Medical devices class 2 injection molding part production plays a crucial role in the healthcare industry, providing essential components that support various patient care needs. Class 2 medical devices, defined by moderate to high risk, include products like syringes, diagnostic tools, and blood pressure monitors—each requiring strict precision and high safety standards. Injection medical molding is a fundamental process for manufacturing these parts, enabling consistency and exactness in their design and functionality. This precision ensures that each medical device meets necessary performance expectations. Furthermore, the regulations surrounding Class 2 devices are essential for maintaining quality, ensuring that each part aligns with regulatory guidelines to provide safe, effective care for patients relying on these critical medical tools. The medical devices class 2 injection molding part process uses medical-grade plastics to mold moderate-risk devices like syringes and contact lenses.
Low-Volume to High-Volume Production Capabilities
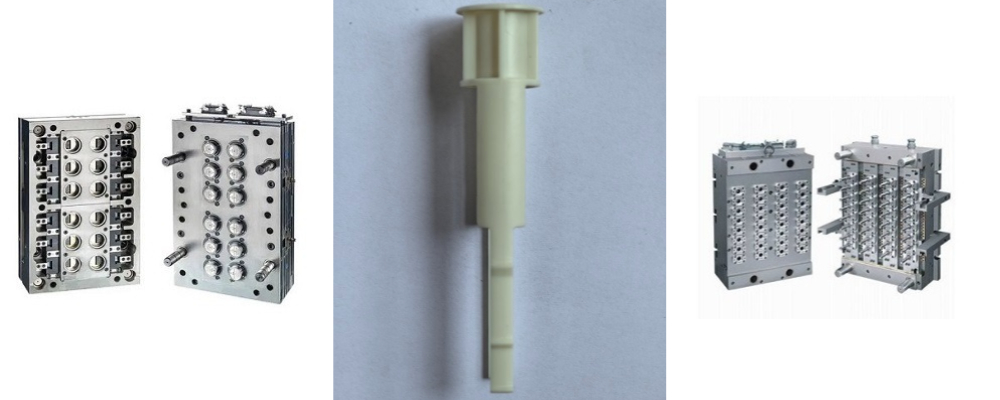
Attributes | Details |
---|---|
Place of Origin | Dongguan, Guangdong, China |
Brand Name | LY Medical Injection Mold |
Product Name | Medical Devices Class 2 Injection Molding Part |
Molding Method | Injection Mold |
Mold Life | 250,000-300,000 Sheets |
Surface Treatment | Polishing |
Size | Custom Size |
Shape | Custom Shape |
Color | Custom Color |
Drawing Format | 2D/(PDF/CAD)3D(IGES/STEP) |
Design Software | UG, PROE, CAD, SOLIDWORK, etc |
Service | OEM Plastic Injection Molding Products |
Tolerance | +/-0.02mm |
Certification | ISO9001:2015 |
Sales Unit | Single Item |
What are Medical Device Classifications: Medical Devices Class 2 Injection Molding Part
The FDA’s classification system for medical devices is foundational in the medical industry, as it categorizes devices based on the level of risk they pose to patients. Each class—Class I, Class II, and Class III—comes with unique regulatory requirements to ensure the safety, quality, and effectiveness of medical devices. For medical devices class 2 injection molding part production, adhering to these classification standards is essential to meet FDA compliance. Below is an overview comparing the risk levels, regulatory controls, and examples for each classification level:
Device Class | Risk Level | Examples | Regulatory Requirements |
---|---|---|---|
Class I | Low Risk | Bandages, non-electric wheelchairs | General controls |
Class II | Moderate to High Risk | Syringes, blood pressure cuffs | General controls and special controls |
Class III | High Risk | Pacemakers, implanted defibrillators | General controls, special controls, and PMA* |
*PMA: Premarket Approval
Class I Devices: Representing low-risk devices, Class I includes products like bandages and non-electric wheelchairs. These devices are subject to general controls, which involve basic standards such as labeling and good manufacturing practices. Most Class I devices do not require FDA review before going to market.
Class II Devices: For medical devices class 2 injection molding part production, Class II devices are categorized as moderate to high risk. They require both general and special controls to meet performance and safety standards, addressing more specific risks than Class I devices. Injection-molded parts used in syringes and blood pressure monitors fall under this classification, where consistency and reliability are paramount.
Class III Devices: These devices, including pacemakers and defibrillators, carry the highest risk and require stringent controls. They undergo premarket approval (PMA), a rigorous process to ensure safety and effectiveness.
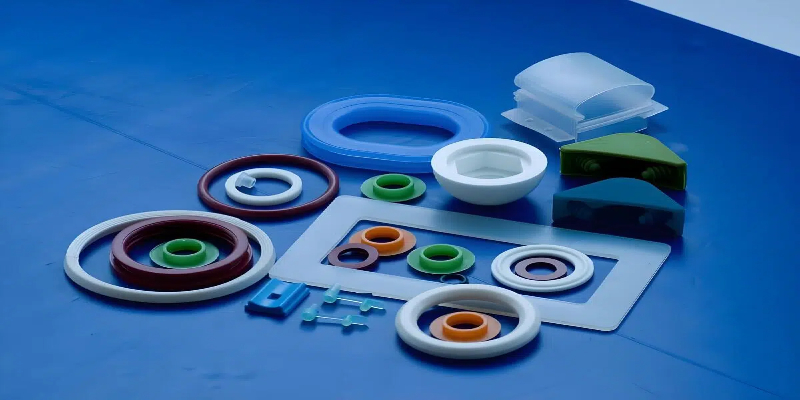
Correct classification is crucial for regulatory compliance. Manufacturers must ensure each medical device class 2 injection molding part meets the specific standards of Class II to avoid risks to patients and ensure alignment with FDA guidelines. This system enables both patient safety and the smooth approval process for high-quality medical device components.
What Defines a Class 2 Medical Device?
Medical devices classified as Class 2 are considered to pose a moderate to high risk to patient health and safety, especially when these devices are designed for sustained contact with the body. These devices play essential roles in diagnostics, treatment, and patient care, requiring both precision in their design and strict adherence to FDA regulations to ensure they meet safety standards. Medical devices class 2 injection molding parts production is fundamental for achieving the reliable quality needed in these products.
Class 2 medical devices fill a wide range of healthcare needs and must comply with general and special controls as mandated by the FDA. This ensures that the devices perform as expected without compromising patient safety or effectiveness. Special controls include specific guidance documents, mandatory performance standards, and, in some cases, post-market surveillance.
Characteristics of Class 2 Medical Devices
The defining features of Class 2 medical devices include:
- Moderate to High Risk: Class 2 devices generally carry more risk than Class 1 devices due to the nature of their interactions with the human body. These risks may arise from sustained contact with tissues, biological fluids, or other critical areas, necessitating higher safety standards.
- Sustained Body Contact: Many Class 2 devices, such as contact lenses and syringes, are designed to interact with the body for extended periods, directly affecting the patient’s health. This characteristic requires that manufacturers of medical devices class 2 injection molding part components adhere to material biocompatibility and safety requirements.
- Regulatory Controls: While Class 2 devices do not demand the rigorous Premarket Approval (PMA) required for Class 3 devices, they must still meet both general and special controls. This includes FDA’s 510(k) clearance process, where manufacturers demonstrate that their device is as safe and effective as an already legally marketed device.
Examples of Class 2 Medical Devices
Class 2 medical devices span a variety of healthcare applications. Injection-molded parts are especially important in the production of these devices, as they contribute to the devices’ durability, functionality, and safety. Examples of Class 2 medical devices include:
- Blood Pressure Cuffs: These diagnostic tools use an injection-molded part in the cuff assembly, ensuring durability and consistent performance under repeated use.
- Syringes: Used for administering medications, syringes are critical Class 2 devices. The medical devices class 2 injection molding part production process ensures the safe production of barrels and plungers, meeting stringent standards for sterility and precision.
- Powered Wheelchairs: Mobility devices like powered wheelchairs require high-quality molded components to maintain structural integrity and provide reliable, safe movement for users.
- Contact Lenses: Injection-molded parts are essential in the manufacturing of contact lenses, which have sustained contact with delicate eye tissues. Class 2 classification ensures biocompatibility and comfort for users.
- Diagnostic Tools: Equipment used in medical diagnostics, such as ultrasound wands and probes, often relies on injection-molded parts. These parts must meet Class 2 safety requirements for accuracy, sterility, and durability.
Regulatory Expectations and Compliance Standards for Class 2 Devices
For manufacturers of medical devices class 2 injection molding part components, compliance with FDA regulations is a primary concern. The FDA imposes specific requirements to ensure that Class 2 devices are both safe and effective. Key regulatory requirements include:
- 510(k) Clearance Process: Most Class 2 devices require 510(k) clearance, which involves submitting data to show that a new device is substantially equivalent to a device already on the market. This process helps ensure that each new device poses no additional risk and performs its intended function effectively.
- General and Special Controls: While general controls include standards for labeling, quality, and post-market reporting, special controls target risks specific to Class 2 devices. For example, contact lenses must meet strict biocompatibility requirements, while powered wheelchairs must meet specific mechanical safety standards.
- Material Biocompatibility: Injection-molded parts used in Class 2 medical devices must meet biocompatibility standards, which means they should not induce any adverse reaction in the body. This requires careful selection of medical-grade plastics and strict adherence to ISO 10993 standards.
- Post-Market Surveillance: The FDA requires some Class 2 devices to undergo post-market monitoring to collect real-world data on performance and any potential risks. This helps ensure that products continue to meet safety standards after they enter the market.
By meeting these standards, medical devices class 2 injection molding part manufacturers can support the development of high-quality, safe products that aid in patient care. The combination of regulatory compliance and precision manufacturing helps provide patients and healthcare professionals with reliable tools that meet critical medical needs.
Key Injection Molding Standards for Class 2 Medical Devices: Medical Devices Class 2 Injection Molding Part
Manufacturing a medical devices class 2 injection molding part requires compliance with several stringent ISO standards that ensure the quality, safety, and biocompatibility of each part. These standards set essential guidelines for production environments, material quality, and processes, which are critical for protecting patient health and meeting regulatory requirements. The following are the key ISO standards that apply to Class 2 medical device injection molding:
ISO 13485: Quality Management System for Medical Devices
ISO 13485 is the foundational quality management standard for medical device plastic manufacturing, specifically tailored to the regulatory requirements of the healthcare industry. For medical devices class 2 injection molding part production, ISO 13485 ensures that each step in the manufacturing process is consistently documented and controlled to meet high-quality standards.
- Key Requirements: ISO 13485 requires that manufacturers establish a comprehensive quality management system (QMS) that outlines quality controls, risk management processes, and methods for ensuring consistent, reproducible quality in every product. For injection molding, this includes controls over the entire molding process, from material selection to finished part inspection.
- Importance for Class 2 Devices: Since Class 2 devices carry moderate to high risk, adherence to ISO 13485 helps ensure that all manufacturing practices align with safety protocols and quality requirements. This reduces the likelihood of defects, contamination, or other issues that could compromise patient safety.
ISO 10993: Biocompatibility Standards for Materials Used in Medical Devices
ISO 10993 is a critical standard that outlines biocompatibility testing for medical device materials. Since Class 2 devices often have sustained contact with body tissues or fluids, biocompatibility is essential in medical devices class 2 injection molding part production. ISO 10993 specifies methods to evaluate whether materials will react adversely when they come into contact with biological tissues.
- Testing Requirements: ISO 10993 consists of several parts that cover different testing protocols, including cytotoxicity, sensitization, irritation, and systemic toxicity. These tests help ensure that materials used in injection-molded parts do not induce harmful biological responses when used in or on the body.
- Relevance for Injection Molding: For Class 2 devices, biocompatible materials are non-negotiable. Manufacturers must select medical-grade plastics like polypropylene or silicone and verify their compatibility with ISO 10993 testing. Meeting this standard is critical to ensure that products such as syringes, blood pressure cuffs, and other injection-molded parts are safe for patient use.
ISO 14644: Cleanroom Standards to Prevent Contamination During Production
ISO 14644 addresses cleanroom standards for controlled environments, essential in the production of medical devices that require sterility and minimal contamination. Medical devices class 2 injection molding part production often takes place in cleanroom environments to prevent contamination that could compromise the safety of devices used in sensitive medical settings.
- Cleanroom Classification: ISO 14644 outlines the classification of cleanrooms based on the number of particles present in the environment. Class 2 device manufacturers often use ISO Class 7 or Class 8 cleanrooms to ensure that contaminants such as dust and airborne particles are minimized.
- Contamination Control: In a cleanroom, airflow, surfaces, and personnel must adhere to strict contamination control protocols. This ensures that injection-molded parts, especially those intended for sustained contact with the body, are manufactured in a sterile environment, reducing the risk of infections or other complications.
Ensuring Compliance with Key Standards
Compliance with ISO 13485, ISO 10993, and ISO 14644 is essential for manufacturers aiming to produce safe and effective injection molding for class ii medical products components. Meeting these standards involves a comprehensive approach to quality control, material safety, and environmental management, creating a manufacturing process that is both efficient and compliant with regulatory requirements. By adhering to these standards, manufacturers can confidently deliver Class 2 medical device components that meet the high expectations of healthcare providers and regulatory bodies alike.
Material Selection for Class 2 Injection Molded Parts: Medical Devices Class 2 Injection Molding Part
In the production of medical devices class 2 injection molding part components, selecting the right materials is vital to ensuring the safety, performance, and reliability of each device. Class 2 medical devices often have sustained contact with body tissues or fluids, which means that the materials used must meet stringent biocompatibility, durability, and safety standards. Medical-grade plastics are typically chosen for their unique properties, each suited to different applications within Class 2 devices. Here are some of the most common materials used in injection molding for these parts:
Importance of Medical-Grade Plastics
The use of medical-grade plastics in medical devices class 2 injection molding part production provides several critical advantages:
- Biocompatibility: Materials must be safe for human contact and comply with standards like ISO 10993, ensuring that they do not cause adverse reactions.
- Durability: Medical devices often need to withstand repeated use without degrading or breaking, especially in clinical settings. This durability is essential for maintaining device functionality and safety over time.
- Resistance to Environmental Factors: Many Class 2 devices are exposed to varying conditions, such as sterilization processes, moisture, or chemicals. Therefore, choosing materials resistant to these factors helps extend the device’s lifespan and reliability.
Commonly Used Materials in Class 2 Device Injection Molding
Different materials bring unique properties to Class 2 medical devices. Below are some of the most frequently used medical-grade plastics for injection molding these components.
Polypropylene (PP) for Moisture Resistance
Polypropylene is a popular choice in medical devices class 2 injection molding part manufacturing because of its excellent moisture resistance and durability. Polypropylene is used in devices where water or body fluids are present, as it maintains stability without warping or breaking down under moisture exposure.
- Applications: Common applications include syringes, lab equipment, and medical tubing.
- Advantages: In addition to moisture resistance, polypropylene offers a good balance of strength and flexibility, making it ideal for disposable devices or components that require regular sterilization.
- Sterilization Compatibility: Polypropylene can withstand certain sterilization methods, such as autoclaving and chemical sterilization, without losing its structural integrity.
Silicone for Flexibility and Biocompatibility
Silicone is widely used in medical devices class 2 injection molding part production, particularly where flexibility and biocompatibility are paramount. Its soft and adaptable nature makes it an ideal choice for devices that require regular bending or manipulation.
- Applications: Silicone is commonly used in catheters, flexible tubing, and seals that need to conform to the human body.
- Advantages: The material is highly biocompatible, non-toxic, and hypoallergenic, making it safe for prolonged contact with body tissues.
- Temperature and Chemical Resistance: Silicone is resistant to extreme temperatures and many chemicals, allowing it to undergo rigorous sterilization without degradation.
Polycarbonate (PC) for Impact Resistance and Transparency
Polycarbonate is a versatile material frequently chosen in the production of medical devices class 2 injection molding part components due to its impact resistance and transparency. Polycarbonate’s toughness makes it suitable for parts that need to withstand physical stress while allowing visibility, essential in devices where monitoring or observing internal processes is required.
- Applications: Polycarbonate is often used in blood pressure monitoring devices, housings for diagnostic tools, and containers requiring clear visibility.
- Advantages: Beyond impact resistance, polycarbonate’s optical clarity provides healthcare professionals with a view of device components or fluids inside, essential for applications that require accurate monitoring.
- Durability in Harsh Environments: Polycarbonate’s chemical resistance also allows it to endure disinfectants and other chemicals, making it reliable for use in healthcare settings where sterilization is routine.
In the medical devices class 2 injection molding part production, selecting the right material is crucial for achieving safety, functionality, and durability. Each of these materials—polypropylene, silicone, and polycarbonate—brings unique properties that suit different medical device applications. By carefully choosing the appropriate plastic, manufacturers can create Class 2 medical device components that meet rigorous industry standards, enhancing the quality and reliability of the devices healthcare providers and patients depend on.
Injection Molding Process for Class 2 Medical Devices
Producing a medical devices class 2 injection molding part requires a meticulous, regulated process to ensure each component meets the high standards of quality, precision, and sterility necessary for medical applications. The medical injection molding process for Class 2 devices follows a series of carefully controlled steps, often conducted within a cleanroom environment to eliminate the risk of contamination. Below is a detailed overview of the injection molding process for Class 2 medical devices, highlighting the importance of precision and consistency throughout each stage.
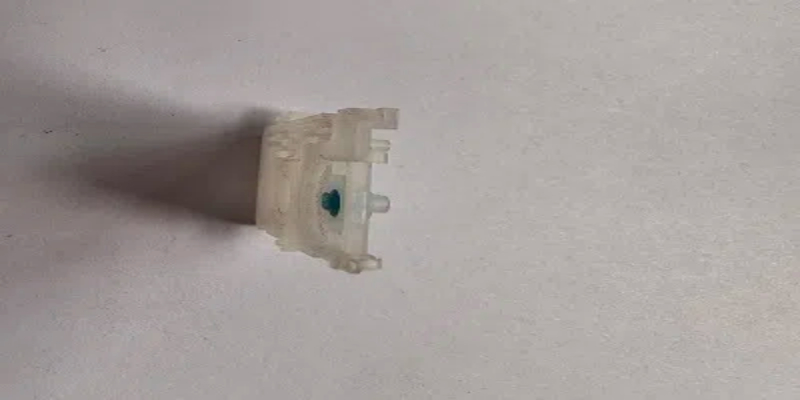
Step-by-Step Overview of the Injection Molding Process for Class 2 Devices
Mold Preparation and Tooling:
- The process begins with the preparation of the injection mold, which is typically crafted from hardened steel to withstand high production volumes. Each mold is customized to form the medical devices class 2 injection molding part precisely.
- The precision medical mold is divided into two halves: the cavity side (A-side), where plastic is injected, and the core side (B-side), which shapes the opposite side of the component.
Material Selection and Preparation:
- Medical-grade plastic pellets, such as polypropylene, silicone, or polycarbonate, are selected for their properties and are thoroughly dried to remove moisture. Moisture can lead to defects in the finished parts, so material preparation is critical.
Injection of Plastic Material:
- The dried plastic pellets are fed into the injection medical molding machine’s hopper, where they are heated and melted to a controlled, uniform temperature. This ensures the plastic flows evenly into the mold.
- The molten plastic is then injected into the mold cavity under high pressure, filling all details and corners of the mold precisely to form the medical devices class 2 injection molding with accuracy.
Cooling and Solidification:
- Once the mold cavity is filled, the injected plastic cools and solidifies within the mold. The cooling process is carefully timed and monitored to ensure the part retains its shape and meets dimensional specifications.
- Cooling time varies based on the material and the thickness of the part, with thicker sections often requiring extended cooling periods.
Ejection of the Part:
- After the plastic has fully solidified, the mold opens, and ejector pins push the finished medical devices class 2 injection molding part out of the mold.
- Ejection must be done with care to avoid damaging the delicate structure of Class 2 medical device components, which often feature intricate designs and small details.
Quality Control and Inspection:
- Each medical devices class 2 injection molding part is thoroughly inspected to ensure it meets strict quality standards. This includes checking for dimensional accuracy, surface quality, and any potential defects.
- Parts are sampled and tested at regular intervals to verify that they meet regulatory and performance requirements.
Importance of Precision and Consistency in Producing Medical-Grade Parts
In Class 2 medical device manufacturing, precision and consistency are paramount. Each medical devices class 2 injection molding part must adhere to exacting dimensions to fit and function seamlessly within the final medical device. Consistency in manufacturing processes reduces the risk of defects, ensures repeatability, and contributes to overall patient safety. Furthermore, maintaining precision allows manufacturers to minimize waste and optimize production efficiency, which is especially crucial in high-volume manufacturing.
Cleanroom Injection Molding Requirements to Ensure Contamination-Free Products
Since many Class 2 medical devices come into direct contact with patients or bodily fluids, producing each part in a cleanroom environment is essential to prevent contamination. Cleanrooms are controlled spaces that adhere to ISO 14644 standards, ensuring that particle levels are kept within acceptable limits.
- Air Filtration and Control: Cleanrooms for medical devices class 2 injection molding part production use HEPA filters and maintain positive air pressure to minimize airborne particles.
- Surface and Equipment Sterilization: Equipment, medical molds, and tools are regularly sterilized to eliminate any risk of contamination.
- Personnel Protocols: Operators working in cleanrooms follow strict protocols, wearing gowns, gloves, and masks to prevent contamination from skin or hair.
Producing medical devices class 2 injection molding part components within a cleanroom environment ensures the parts are free of contaminants that could compromise patient safety or product efficacy. By combining precise, consistent manufacturing practices with cleanroom standards, manufacturers can reliably produce high-quality Class 2 medical device components that meet stringent regulatory requirements and deliver consistent, safe performance in healthcare applications.
Regulatory Requirements for Class 2 Injection Molded Parts: Medical Devices Class 2 Injection Molding Part
Manufacturers of medical devices class 2 injection molding part components must adhere to strict regulatory requirements to ensure that each device meets the high safety and performance standards necessary for healthcare applications. Class 2 medical devices are subject to specific controls by the FDA, including the Premarket Notification 510(k) process and adherence to additional special controls to ensure that each device functions effectively and safely.
Overview of FDA’s Premarket Notification 510(k) Process for Class 2 Devices
The FDA’s Premarket Notification 510(k) process is a key regulatory requirement for bringing most Class 2 medical devices to market. Through this process, manufacturers must submit documentation that demonstrates a new medical devices class 2 injection molding part is substantially equivalent to an existing device that has already been cleared by the FDA. Substantial equivalence means that the new device is as safe and effective as a legally marketed predicate device.
- Purpose of the 510(k) Process: The 510(k) pathway ensures that new Class 2 devices meet established safety and performance benchmarks. By comparing a new device to an existing product, the FDA can assess its safety without the need for a lengthy, full-scale clinical trial. This process significantly reduces time-to-market, allowing manufacturers to introduce innovations while still complying with rigorous standards.
- Documentation Requirements: Manufacturers must provide a comprehensive report in the 510(k) submission, detailing the device’s specifications, materials, intended use, testing protocols, and performance data. This includes any unique aspects of the medical devices class 2 injection molding part and proof that it matches the safety and functionality of the predicate device.
- Risk and Mitigation Strategies: In addition to proving equivalency, manufacturers must also identify any potential risks associated with the device and outline mitigation strategies to ensure patient safety. These risk assessments help the FDA verify that the product’s design and materials align with healthcare standards.
Special Controls and Compliance with Regulatory Standards for Device Safety and Performance
In addition to the 510(k) process, Class 2 medical devices must meet specific special controls that apply to their particular risk profile. These special controls are designed to address known risks associated with Class 2 devices and go beyond general regulatory requirements. They may include performance standards, labeling requirements, biocompatibility testing, and post-market surveillance.
- Performance Standards: Each medical devices class 2 injection molding part must meet certain performance standards, which can vary based on the device’s intended function. For example, components like syringes or blood pressure cuffs must perform reliably under repeated use, often requiring testing for mechanical strength, durability, and sterility.
- Labeling Requirements: Labeling for Class 2 devices includes clear instructions for use, warnings, and safety information. For medical devices class 2 injection molding part components, labeling must also indicate the device’s intended use and any handling or storage requirements to maintain safety and functionality.
- Biocompatibility Testing: Class 2 devices frequently undergo ISO 10993 biocompatibility testing to confirm that materials do not cause harmful reactions when in contact with the body. This testing is essential for injection-molded parts that may be used in devices such as syringes or diagnostic tools, which come into sustained contact with patients.
- Post-Market Surveillance: The FDA may require manufacturers to conduct post-market surveillance for certain Class 2 devices to monitor real-world performance and detect any long-term safety issues. This helps ensure that the medical devices class 2 injection molding part continues to meet safety standards after reaching the market, contributing to a broader understanding of device performance and patient outcomes.
- Compliance Audits and Quality System Regulations (QSR): Manufacturers of Class 2 devices must establish and maintain a quality management system in compliance with FDA’s Quality System Regulations (21 CFR Part 820). This regulation requires a structured approach to manufacturing, including controls over design, production, testing, and validation processes. Compliance audits are periodically conducted by the FDA to verify that manufacturers are consistently meeting these requirements.
Ensuring Compliance for Medical Devices Class 2 Injection Molding Part Production
For manufacturers, achieving and maintaining regulatory compliance for medical devices class 2 injection molding part production involves integrating robust quality controls at every stage of the design, production, and testing processes. Adhering to the 510(k) process, applying special controls, and implementing a comprehensive quality management system ensures that each injection-molded part aligns with FDA standards, allowing for safe, effective use in medical applications.
Compliance with these regulations not only protects patient safety but also builds confidence in the product’s reliability and effectiveness, supporting manufacturers in meeting both industry and patient needs in a highly regulated environment. By following these guidelines, manufacturers of Class 2 injection molded parts can successfully bring innovative, high-quality medical device components to market while ensuring adherence to FDA and international standards.
Applications of Injection Molded Parts in Class 2 Medical Devices: Medical Devices Class 2 Injection Molding Part
Injection molding is essential for the production of medical devices class 2 injection molding part components, providing a high level of precision, cost-effectiveness, and scalability to meet the demands of the healthcare industry. Class 2 medical devices, which are moderate- to high-risk products, rely on injection-molded parts for their critical functionalities. These parts are designed to meet stringent safety and performance standards, ensuring reliability and safety in patient care.
Examples of Injection Molded Components Used in Class 2 Devices
Injection molding allows manufacturers to create a wide variety of components used in Class 2 medical devices. Each part serves a specific function, from delivering medication to enabling diagnostics, and must meet strict biocompatibility and durability standards.
- Syringes: Injection-molded parts play a crucial role in syringe production, including the syringe barrel, plunger, and seal components. These parts must maintain a smooth, frictionless motion to ensure precise dosing and ease of use. Using injection molding, manufacturers can produce millions of identical, high-quality syringes at a low cost, essential for large-scale healthcare needs.
- Housings for Diagnostic Tools: Many diagnostic devices, such as blood glucose monitors and blood pressure cuffs, incorporate injection-molded housings that protect sensitive electronics and sensors. These housings need to be durable, lightweight, and sometimes transparent, allowing healthcare providers to monitor measurements without interference. Medical devices class 2 injection molding part production ensures that housings are both strong and biocompatible, reducing any risk to patients.
- Tubing and Connectors: Flexible tubing and connectors are widely used in medical devices for transporting fluids, gases, or medications. Injection-molded parts allow for the mass production of consistent, reliable tubing that remains flexible, durable, and resistant to kinking. These precision medical components are particularly important in devices like IVs, oxygen delivery systems, and dialysis machines, where reliability and precision are essential.
- Disposable Medical Components: Injection molding is ideal for producing disposable components, which are widely used in Class 2 medical devices to reduce the risk of contamination. Examples include caps, stoppers, and valve covers that form secure seals in fluid or medication delivery systems. Disposable parts are especially important in infection control, as they can be safely discarded after a single use.
Benefits of Injection Molding in Producing High-Quality, Cost-Effective Parts for Mass Production
The injection molding process offers several advantages that make it ideal for manufacturing medical devices class 2 injection molding part components at scale. This method enables the production of complex shapes with precise tolerances, providing reliable and consistent quality with each piece.
- Cost-Effectiveness: Injection molding is highly efficient for large production runs, allowing manufacturers to produce thousands or millions of identical parts with minimal variation. This scalability makes it possible to supply healthcare providers with the high volumes of parts they need while keeping costs manageable.
- High Precision and Consistency: Medical devices, especially Class 2 devices, require precision to perform reliably and safely. Injection molding can produce intricate designs with tight tolerances, which are essential for parts like syringes or diagnostic tool housings. This precision minimizes the risk of malfunctions or variations in performance, ensuring that each part meets regulatory standards and performs as expected.
- Material Versatility: Injection molding supports a wide range of medical-grade materials, including biocompatible plastics like polypropylene, silicone, and polycarbonate. This flexibility allows manufacturers to select materials with properties suited to specific device requirements, such as chemical resistance, flexibility, or transparency, further enhancing device safety and functionality.
- Reduced Waste and Sustainability: Injection molding allows for optimized material usage, reducing waste. Excess plastic from the production process can often be recycled, aligning with the industry’s push toward sustainable practices without compromising the quality of medical devices class 2 injection molding part components.
- Fast Production Times: Injection molding allows rapid production cycles, with parts created in seconds to minutes. This speed enables manufacturers to meet urgent healthcare demands quickly, such as during pandemics or high-demand periods, where consistent and reliable medical supplies are essential.
The applications of injection molding in Class 2 medical device production are vast, ranging from syringes and tubing to complex diagnostic tool housings. Each medical devices class 2 injection molding part is produced with precision and care, ensuring that it meets the necessary regulatory standards for safety, biocompatibility, and durability. By utilizing injection molding, manufacturers are able to supply the healthcare industry with high-quality, cost-effective components at scale, ultimately enhancing patient care and supporting critical medical treatments and diagnostics.
Key Considerations for Wholesale Medical Devices Class 2 Injection Molding Parts
The wholesale purchase of medical devices class 2 injection molding parts requires careful evaluation to ensure compliance with regulatory, material, manufacturing, and quality standards. Class II devices present moderate to high risk to patients and users, necessitating stricter controls than Class I devices. Since these components are used in critical medical applications, they must meet FDA, ISO, and GMP (Good Manufacturing Practices) requirements.
Manufacturers must also ensure biocompatibility, sterilization compatibility, and precision molding techniques to maintain patient safety and device effectiveness. Additionally, suppliers should have a proven track record, the capacity for large-scale production, and stringent quality control measures to avoid defects and inconsistencies. Below is a detailed breakdown of the key aspects buyers must evaluate when sourcing Class II medical injection molding parts.
Regulatory Compliance and Certification
Regulatory compliance is the foundation of purchasing Class II medical injection molded parts. These devices must meet specific legal and safety requirements to be used in healthcare settings. Buyers must verify that manufacturers hold the necessary certifications to ensure regulatory approval, quality control, and product traceability.
Key Certifications and Regulatory Requirements:
FDA 510(k) Clearance
- Most Class II medical devices require 510(k) clearance, proving that the new device is substantially equivalent to an existing legally marketed device.
- This process involves safety, functionality, and biocompatibility testing, ensuring the product meets established medical standards.
ISO 13485 Certification
- This international quality standard ensures that manufacturers maintain a medical-grade quality management system (QMS).
- It requires risk management, process validation, and continuous improvement, ensuring the consistent production of high-quality medical components.
ISO 10993 Compliance
- This standard covers biocompatibility testing to assess how materials interact with human tissue.
- Cytotoxicity, sensitization, and irritation testing must be conducted to ensure materials are safe for long-term or short-term patient contact.
Good Manufacturing Practices (GMP) & 21 CFR Part 820
- These regulations define strict production controls for medical devices, ensuring consistent manufacturing, packaging, and documentation.
- Full traceability is required, allowing recalls if defects are discovered.
Without these regulatory assurances, a manufacturer’s products may be legally unusable, unsafe, or rejected during audits.
Material Selection and Biocompatibility
Material selection is a critical factor in the performance and safety of Class II medical injection molded parts. The chosen materials must be biocompatible, durable, and resistant to sterilization processes. Medical device plastics must not release harmful chemicals, degrade over time, or react with bodily fluids.
Key Considerations for Material Selection:
Biocompatibility
- Materials must be non-toxic, non-reactive, and hypoallergenic for safe patient contact.
- Compliance with ISO 10993 testing ensures the material does not cause irritation, toxicity, or immune responses.
Sterilization Compatibility
Many Class II devices require sterilization before use. The selected material must withstand:
- Gamma radiation (for single-use syringes and IV components).
- Autoclaving (for reusable components like surgical instruments).
- Ethylene oxide (EtO) gas (for sensitive plastics that cannot endure high heat).
Chemical Resistance
- The plastic must resist degradation when exposed to drugs, disinfectants, and bodily fluids.
- Materials like polycarbonate (PC), polypropylene (PP), and polyetheretherketone (PEEK) are commonly used for their stability and strength.
Mechanical Strength and Durability
- Some Class II medical components, such as injection ports or connectors, experience mechanical stress and require impact-resistant plastics.
- Polyethylene (PE) is often used for flexible applications, while acrylonitrile butadiene styrene (ABS) provides toughness.
Selecting the wrong material can lead to device failure, patient injury, or regulatory rejection.
Precision and Quality Control in Manufacturing
Medical injection molding requires high precision and defect-free production to ensure consistent functionality. Minor flaws in syringe barrels, catheter tips, or diagnostic housings could lead to device malfunction, contamination, or patient harm.
Key Aspects of High-Quality Manufacturing:
Tight Tolerances
- Many Class II devices demand extremely tight tolerances to ensure proper fit and function.
- Syringe barrels require exact inner diameter tolerances to ensure smooth plunger movement.
Cleanroom Manufacturing
- ISO Class 7 or Class 8 cleanrooms are often required for molding, assembly, and packaging to prevent contamination.
- Cleanroom molding minimizes particulate matter, bacteria, and dust, ensuring device sterility.
Automated Quality Inspection
- Advanced manufacturers use robotic vision systems to detect dimensional defects, surface irregularities, or contamination.
- 100% inspection policies ensure that every part meets specifications before packaging.
Process Validation and Lot Traceability
- FDA regulations require complete batch traceability, meaning each manufactured part can be tracked through the supply chain.
- Manufacturers must keep records for quality audits and potential recalls.
A lack of precision and quality control can result in regulatory violations, product recalls, or patient harm.
Supplier Reliability and Production Capacity
Finding a reliable manufacturer is essential for consistent, high-quality, and scalable production of Class II medical injection molded parts. A supplier’s ability to meet demand, maintain consistency, and provide regulatory documentation is crucial.
Key Factors in Supplier Selection:
Industry Experience
- The manufacturer should have proven expertise in Class II medical injection molding.
- Case studies, customer references, and FDA registration help verify their credibility.
Scalability and Production Capacity
- The supplier should accommodate both small prototype batches and large-scale orders.
- Multi-cavity molds and high-speed automation increase efficiency and lower costs.
Regulatory Documentation and Support
A trustworthy supplier provides complete documentation, including:
- Material compliance reports (ISO 10993, USP Class VI).
- Batch testing results.
- Process validation reports.
Supply Chain Stability
- A reliable raw material supply ensures consistent production.
- Manufacturers with multiple production facilities reduce risk during supply chain disruptions.
Working with an unreliable supplier may result in delivery delays, defective products, or non-compliance with regulatory audits.
When purchasing medical devices class 2 injection molding parts, buyers must ensure that manufacturers comply with strict FDA and ISO regulations, use high-quality biocompatible materials, maintain precision manufacturing, and offer reliable scalability. Without these assurances, patient safety, regulatory compliance, and product reliability are at risk. Careful evaluation of certifications, materials, quality control processes, and supplier reliability will lead to safer and more effective medical devices.
Mechanical and Chemical Properties in Medical Devices Class 2 Injection Molding Part Material Selection
When manufacturing Class 2 medical devices using injection molding technology, the selection of medical-grade plastic materials is crucial to ensuring safety, functionality, and durability. The mechanical and chemical properties of these materials directly influence the performance, reliability, and compliance of the final product. Mechanical properties like hardness, flexibility, stiffness, and weight determine whether a device can withstand physical stress, repeated use, or wear and tear. Similarly, chemical properties, particularly resistance to cleaning agents, sterilization processes, and bodily fluids, ensure the device remains sterile, intact, and functional over time. Understanding and optimizing these properties is essential for producing high-quality, long-lasting medical devices that meet FDA and ISO 13485 standards.
To fully grasp the role of mechanical and chemical properties in material selection for Class 2 medical device injection molding parts, we will explore the following key aspects:
Mechanical Properties: Ensuring Structural Integrity and Performance
Mechanical properties define how a material responds to physical forces, ensuring that the medical device functions effectively under real-world conditions. Selecting materials with the right balance of strength, flexibility, and durability is critical for both disposable and reusable medical components.
Hardness: Resistance to Indentation and Wear
Hardness determines a material’s resistance to deformation, scratching, or indentation, which is essential for load-bearing components like syringe plungers, catheter hubs, and surgical instrument handles. High-hardness materials such as polycarbonate (PC) or PEEK ensure long-term durability and prevent surface damage that could compromise the device’s function or hygiene.
Flexibility: Maintaining Functionality Under Stress
Flexibility measures a material’s ability to bend without breaking, which is crucial for components that require movement, such as tubing connectors, soft medical grips, or inhaler mouthpieces. Thermoplastic elastomers (TPEs) offer a balance of softness and elasticity, ensuring comfortable use and patient safety.
Stiffness: Structural Stability and Load Resistance
Stiffness refers to a material’s resistance to bending under force. A balance between stiffness and flexibility is necessary for devices like diagnostic casings, infusion pump enclosures, and handheld medical instruments. Materials like polyetherimide (PEI) and ABS provide sufficient rigidity to maintain dimensional stability while preventing excessive brittleness.
Weight: Impact on Usability and Patient Comfort
Lightweight materials are essential for wearable medical devices and handheld equipment. Polymers like polypropylene (PP) and polycarbonate (PC) offer high strength-to-weight ratios, ensuring ease of use without compromising durability. This is particularly important for portable diagnostic tools and ergonomic medical devices.
Chemical Properties: Ensuring Longevity and Biocompatibility
Chemical properties define a material’s ability to resist degradation when exposed to harsh sterilization methods, disinfectants, and biological fluids. In medical applications, these properties ensure the device remains safe, sterile, and functional over its intended lifespan.
Chemical Resistance: Withstanding Harsh Cleaning Agents
Medical devices must endure frequent cleaning and sterilization using alcohol-based disinfectants, hydrogen peroxide, and autoclaving. Materials like polypropylene (PP) and polyether ether ketone (PEEK) resist corrosion, chemical breakdown, and discoloration, ensuring long-term usability.
Biocompatibility: Safe Interaction with the Human Body
Materials used in Class 2 medical devices must comply with ISO 10993 biocompatibility standards, ensuring they do not cause toxic reactions, irritation, or infections. Medical-grade polyethylene (PE), polycarbonate (PC), and TPEs are commonly chosen for their non-toxic and hypoallergenic properties.
Resistance to Bodily Fluids and Drug Compatibility
Devices like IV connectors, catheters, and insulin pens come into direct contact with blood, saliva, or medication formulations. Fluoropolymers (e.g., PTFE) and silicone elastomers resist chemical interactions and degradation, preventing contamination or compromised performance.
Selecting the right material for Class 2 medical device injection molding parts requires careful consideration of both mechanical and chemical properties. While mechanical strength ensures the device can handle physical stress, movement, and repeated use, chemical resistance guarantees longevity against sterilization, bodily fluids, and medical chemicals. By choosing materials that offer the best combination of these properties, manufacturers can create high-performance, durable, and compliant medical devices that meet the highest safety and regulatory standards.
Aesthetics and Usability Considerations in Medical Devices Class 2 Injection Molding Part
The aesthetics and usability of medical devices class 2 injection molding parts play a crucial role in patient experience, acceptance, and overall device functionality. As Class II medical devices often involve direct patient interaction, their appearance, comfort, and ease of use must be carefully considered during the injection molding process.
A well-designed medical device should not only function reliably but also provide a visually appealing and ergonomic experience. Materials such as colorable polycarbonate and flexible silicone contribute to both durability and comfort. Additionally, advanced plastic molding technologies enable the creation of customized, ergonomic, and user-friendly designs. Below are key factors that manufacturers must consider to enhance the aesthetics and usability of Class II medical injection molded parts.
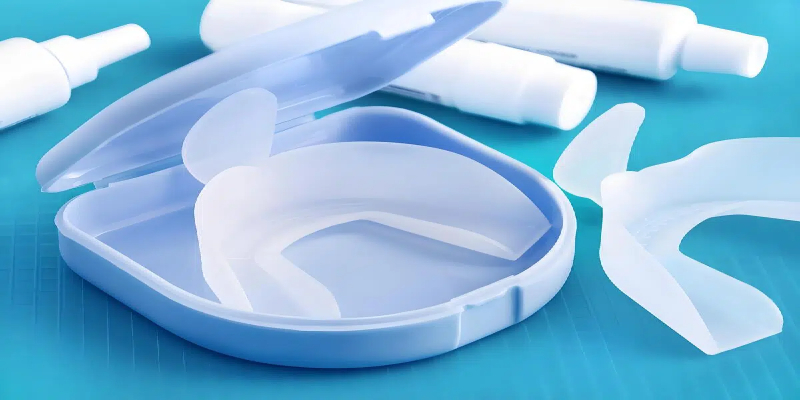
Aesthetic Considerations in Medical Injection Molding
Aesthetics play an important role in the design of medical devices that are externally visible or frequently used by patients. Patients are more likely to accept and use devices that look modern, sleek, and non-intimidating. Additionally, color, texture, and surface finish contribute to the overall perceived quality of the product.
Key Factors in Aesthetic Design:
Color and Customization
- Certain plastics like polycarbonate (PC) and acrylonitrile butadiene styrene (ABS) can be color-matched to blend with the patient’s skin tone or provide a more attractive appearance.
- Devices such as prosthetic covers or orthopedic braces benefit from customizable colors that make them look more natural or stylish.
Surface Finish and Texture
- Smooth, polished finishes improve the feel and hygiene of devices like insulin pens and inhalers.
- Matte or textured surfaces can reduce glare and fingerprints, enhancing the grip and usability of handheld devices.
Material Transparency and Opacity
- Clear polycarbonate or acrylic is used in diagnostic devices, allowing users to see internal components or fluid levels.
- Opaque or frosted finishes provide a sleek, high-end look while concealing internal electronics or mechanisms.
Aesthetic improvements increase user confidence and encourage patient compliance, especially for wearable or frequently used medical devices.
Usability and Ergonomics in Medical Injection Molding
Beyond aesthetics, usability is essential for patient comfort, ease of operation, and long-term adherence to medical treatment. Medical devices should be designed to be intuitive, lightweight, and ergonomically optimized to minimize discomfort or fatigue.
Key Usability Considerations:
Ergonomic Design for Comfort
- Handheld medical devices like glucose meters, auto-injectors, and blood pressure monitors should have a comfortable grip and be easy to hold for extended periods.
- Contoured shapes and soft-touch coatings improve user interaction and reduce strain during repeated use.
Material Flexibility and Skin Comfort
- Silicone and thermoplastic elastomers (TPEs) are commonly used in wearable medical devices, such as CPAP masks and prosthetic liners, due to their softness and adaptability to body contours.
- Flexible materials reduce irritation and pressure points, making devices more comfortable for prolonged wear.
Ease of Operation and Accessibility
- Medical devices should feature simple mechanisms, large buttons, and clear labeling for users of all ages.
- Injection-molded parts can incorporate raised textures, Braille, or color-coded indicators to aid visually impaired users.
Usability-focused designs enhance patient independence and reduce reliance on healthcare providers, making medical treatments more accessible.
Impact of Plastic Injection Molding Technology on Aesthetics and Usability
Medical injection molding technology allows for greater design flexibility, enabling the production of devices that are both visually appealing and user-friendly. This technology supports complex geometries, multi-material molding, and advanced surface finishes to enhance both function and form.
Advantages of Injection Molding for Aesthetic and Usability Enhancement:
Complex Geometries and Customization
- Injection molding enables the production of lightweight yet durable components with intricate curves, grips, and functional features.
- Multi-shot molding allows soft-touch coatings and multiple textures in a single part.
Integration of Functional Features
- Injection-molded parts can be designed with built-in hinges, snap fits, and overmolded grips, eliminating the need for additional assembly.
- Devices such as insulin pumps and diagnostic kits benefit from seamless, user-friendly enclosures.
Cost-Effective Mass Production
- High-volume injection molding ensures consistent quality and precision, making aesthetically and ergonomically superior devices more affordable and widely available.
Plastic injection molding thus provides the ideal balance between aesthetic appeal, usability, and cost-efficiency, ensuring that Class II medical devices meet both functional and patient-centric design goals.
The production of medical devices class 2 injection molding parts must carefully consider both aesthetics and usability to improve patient acceptance, comfort, and ease of use. Materials like polycarbonate for aesthetics and silicone for comfort enhance the overall user experience, while advanced injection molding technologies allow for ergonomic and visually appealing designs. By prioritizing these factors, manufacturers can create medical devices that are not only safe and effective but also patient-friendly and widely accepted in healthcare settings.
Medical Devices Class 2 Injection Molding Part: Prototype Design and Expanded Production Considerations
The development of Class 2 medical devices through injection molding technology requires a well-structured approach from prototype design to full-scale production. During the prototype phase, factors such as material selection, biocompatibility, and functional validation play a crucial role in ensuring product safety and regulatory compliance. As production scales up, manufacturers must address process efficiency, quality control, and cost-effectiveness while adhering to strict FDA and ISO 13485 standards. The success of this transition depends on precision engineering, automation, and advanced validation techniques.
To fully understand the key aspects of designing prototypes and expanding production for Class 2 medical injection-molded parts, we will explore the following critical areas:
Key Considerations in Medical Device Prototype Design
During the prototype phase, the primary goal is to develop a functional, safe, and regulatory-compliant design that can be efficiently manufactured at scale. This requires a balance of material properties, manufacturability, and usability.
Material Selection and Biocompatibility
- Choosing the right medical-grade plastics (e.g., polycarbonate, PEEK, and medical-grade silicone) ensures strength, flexibility, and chemical resistance.
- Materials must comply with ISO 10993 biocompatibility standards to prevent allergic reactions or toxicity.
Design for Manufacturability (DFM)
- Components should be designed to minimize complex geometries while maintaining functionality.
- Features like uniform wall thickness and draft angles reduce molding defects and ensure smooth ejection from molds.
Functional Testing and Validation
- Prototypes must undergo rigorous mechanical stress tests, chemical resistance evaluations, and sterility assessments.
- Rapid prototyping methods, such as 3D printing, can accelerate design iterations before investing in full-scale molding.
Challenges and Strategies for Scaling Up Production
Transitioning from prototype to mass production presents challenges related to cost efficiency, process control, and regulatory adherence. A structured strategy ensures that scaling up maintains product consistency and safety.
Injection Molding Process Optimization
- High-precision molds are essential to achieving tight tolerances and defect-free production.
- Process variables such as temperature, pressure, and cooling time must be monitored and controlled to prevent defects like warping or sink marks.
Quality Control and Compliance
- Implementing real-time quality control measures, including automated inspection systems, ensures consistent product performance.
- Compliance with ISO 13485 (Quality Management System for Medical Devices) and FDA 21 CFR Part 820 is mandatory for regulatory approval.
Cost Efficiency and Supply Chain Management
- Material sourcing strategies should prioritize consistent supply of medical-grade resins.
- Using automated injection molding processes and lean manufacturing principles can reduce waste and enhance efficiency.
Development Prospects for Medical Devices Class 2 Injection Molding Parts
The market for Class 2 medical devices is expected to grow significantly due to advances in material science, automation, and personalized healthcare solutions. Future developments will focus on enhanced biocompatibility, smart medical devices, and sustainable manufacturing methods.
Smart and Connected Medical Devices
- Integration of IoT-enabled sensors in injection-molded parts will enhance real-time patient monitoring.
- Advances in miniaturization will allow for more compact and efficient medical devices.
Sustainable and Biodegradable Materials
- The industry is shifting toward biodegradable and recyclable polymers to reduce environmental impact.
- New materials like biocompatible PLA (polylactic acid) and bioresorbable polymers offer promising alternatives.
Advanced Manufacturing Technologies
- AI-driven process control will improve production accuracy and reduce defects.
- 3D printing hybridization with injection molding will enable faster customization and prototyping.
Developing Class 2 medical devices through injection molding requires a structured approach from prototype design to large-scale production. By prioritizing material selection, regulatory compliance, and process optimization, manufacturers can ensure high-quality, cost-effective, and innovative medical products. The future of the industry lies in smart, biocompatible, and sustainable solutions, driving the next generation of medical device advancements.
Surface Treatment Processes for Medical Devices Class 2 Injection Molding Part
The surface treatment of medical devices class 2 injection molding parts is a critical step in ensuring biocompatibility, durability, hygiene, and functionality. Since Class II medical devices involve moderate to high risks, their surfaces must meet strict regulatory and performance requirements. Proper surface treatment can enhance aesthetics, improve wear resistance, reduce bacterial adhesion, and optimize device performance.
Different surface treatment techniques are used depending on the material, intended use, and regulatory requirements of the device. These processes include polishing, texturing, coating, plasma treatment, laser marking, and sterilization-friendly finishes. Below is a detailed breakdown of the commonly used surface treatment methods in medical injection molding technology.
Polishing and Surface Smoothing
Polishing is an essential process to ensure that medical devices have smooth, non-porous surfaces. A highly polished surface reduces bacterial adhesion, enhances appearance, and improves patient comfort, especially for implantable or skin-contact devices.
Polishing Techniques:
- Mechanical Polishing: Uses abrasive tools to remove imperfections and create a smooth finish.
- Chemical Polishing: Involves chemical baths to dissolve rough surfaces and create a uniform, glossy finish.
- Ultrasonic Polishing: Uses high-frequency vibrations to polish delicate components with complex geometries.
Highly polished surfaces are ideal for syringes, inhalers, catheters, and prosthetic components, where a friction-free experience is necessary.
Texturing for Grip and Aesthetics
Texturing enhances both functionality and aesthetics by improving grip, tactile feedback, and visual appeal. It is especially useful for handheld devices, surgical instruments, and wearables.
Common Texturing Methods:
- Laser Texturing: Uses precision lasers to engrave microscopic patterns on the surface, improving grip and reducing glare.
- Etching and Sandblasting: Creates matte, non-slip textures, enhancing usability for surgical tools and ergonomic grips.
- Molded-In Textures: Achieved by modifying the mold surface, ensuring consistent texture across mass-produced parts.
A well-textured surface improves comfort, control, and user experience, particularly for devices requiring precise handling and repeated use.
Coating and Surface Modification
Coatings enhance the performance, safety, and durability of medical injection molded parts by adding protective layers. These coatings can increase wear resistance, reduce bacterial growth, or provide lubrication for moving parts.
Types of Coatings:
- Antimicrobial Coatings: Silver-ion or nano-coatings that prevent bacterial growth, used in catheters, syringes, and wound care devices.
- Hydrophilic and Hydrophobic Coatings:
- Hydrophilic coatings attract water, reducing friction in catheters and guidewires.
- Hydrophobic coatings repel liquids, preventing contamination and biofilm formation.
- PTFE (Teflon) Coatings: Create a low-friction, non-stick surface, used for surgical instruments and tubing.
- Biocompatible Coatings: Used in implantable medical devices to prevent immune reactions.
Surface coatings extend the lifespan and safety of Class II medical devices, making them more hygienic and efficient.
Plasma Treatment for Adhesion and Sterility
Plasma treatment is a high-tech surface modification process that enhances adhesion, sterilization, and biocompatibility. It is commonly used before bonding, printing, or coating medical plastic parts.
Benefits of Plasma Treatment:
- Improves Adhesion: Ensures better bonding of coatings, adhesives, and inks on polymer surfaces.
- Sterilization Enhancement: Removes contaminants, organic residues, and bacteria, making it ideal for single-use medical devices.
- Enhances Hydrophilicity: Improves lubrication and liquid interaction in devices like contact lenses and diagnostic strips.
Plasma treatment is widely used for microfluidic devices, surgical tubing, and diagnostic equipment, ensuring superior performance and safety.
Laser Marking for Identification and Traceability
Laser marking is a permanent, non-toxic, and wear-resistant method for labeling and tracking medical devices. Since Class II medical devices must meet FDA’s Unique Device Identification (UDI) requirements, laser marking provides an efficient and tamper-proof labeling solution.
Advantages of Laser Marking:
- Permanently Engraves Serial Numbers, QR Codes, and Logos.
- Does Not Fade, Rub Off, or Wear Out Over Time.
- Complies with Medical Regulations for Device Identification and Traceability.
Medical devices such as surgical instruments, insulin pens, and IV components benefit from laser marking, ensuring regulatory compliance and product authentication.
Sterilization-Resistant Finishes
Medical devices must endure repeated sterilization without degrading or losing their surface integrity. Proper surface treatments can enhance heat, chemical, and radiation resistance to ensure long-term device sterility and safety.
Sterilization-Compatible Surface Treatments:
- Heat-Resistant Polymers: Polycarbonate (PC) and Polyetheretherketone (PEEK) can withstand autoclaving.
- Chemical-Resistant Coatings: Protect devices from disinfectants and alcohol-based cleaners.
- Gamma Radiation-Stable Materials: Ensures plastic integrity after sterilization via gamma rays.
Sterilization-resistant finishes are essential for reusable medical devices, such as surgical tools, diagnostic equipment, and monitoring devices.
Surface treatment is a critical step in manufacturing medical devices class 2 injection molding parts to ensure durability, safety, hygiene, and usability. Techniques such as polishing, texturing, coatings, plasma treatment, laser marking, and sterilization-resistant finishes enhance both functionality and regulatory compliance. By implementing these processes, manufacturers can create high-quality, reliable, and patient-friendly medical devices that meet industry standards and improve healthcare outcomes.
FAQs about Medical Devices Class 2 Injection Molding Part
Class 2 medical devices are moderate- to high-risk products that have sustained contact with the body or perform essential diagnostic or therapeutic functions. Examples include blood pressure cuffs, syringes, catheters, and powered wheelchairs. These devices often have injection-molded parts for durability and precision. Blood pressure cuffs, for instance, use molded housings to protect electronic sensors, while syringes rely on molded barrels and plungers for precise dosing. Additional examples are contact lenses, which require biocompatible molded materials, and diagnostic tools like blood glucose monitors, which have injection-molded casings. Each of these devices requires adherence to strict regulatory standards, such as biocompatibility, durability, and safety, to ensure they function safely and effectively.
The Harmonized System (HS) code for injection molding parts generally falls under HS code 84771000. This code classifies machinery and components for processing plastic materials, including parts for injection molding machines. The code is crucial for international trade as it ensures accurate classification for customs and tariff purposes, simplifying the import and export process. Using the correct HS code for injection molding parts not only ensures compliance with global trade regulations but also helps companies avoid delays or additional fees due to misclassification. Manufacturers of medical devices and other industries often use HS code 84771000 to streamline shipping and documentation when sourcing or distributing injection-molded components globally.
A Class 2 device is a medical device that presents moderate to high risk to patient health and safety, requiring more regulatory control than Class 1 devices. These devices often have direct or sustained contact with the body or play a critical role in diagnostics or treatment. To ensure safety and effectiveness, Class 2 devices must comply with general controls and special controls, such as performance standards, biocompatibility testing, and labeling requirements. They are also commonly subject to the FDA’s 510(k) clearance process, which requires manufacturers to demonstrate that their device is substantially equivalent to an already approved product. Examples of Class 2 devices include diagnostic tools, infusion pumps, and dental instruments. The additional regulatory requirements for Class 2 devices help ensure these products meet strict quality and safety standards essential in healthcare settings.
Injection molding produces a wide range of components across industries, particularly in medical, automotive, and consumer goods. A common example in the medical field is the syringe, where injection-molded parts include the barrel, plunger, and stopper, each designed for precision and biocompatibility. In diagnostics, molded housings protect sensitive electronics in devices like blood glucose monitors. Automotive applications include molded knobs, buttons, and interior panels, while in consumer goods, items like plastic casings for electronics or household items like kitchen utensils are typical injection-molded parts. The injection molding process provides consistency and efficiency, enabling high-volume production of durable, complex shapes. Its versatility in material selection—such as polypropylene, silicone, and polycarbonate—allows manufacturers to produce parts with specific properties like flexibility, transparency, or chemical resistance, tailored to each industry’s needs.
An injection molded part typically consists of several key features that ensure functionality and manufacturability. These parts include the main body, which forms the core structure, and ribs that provide additional strength without increasing weight. Bosses serve as mounting points for fasteners or other components. Snap fits or living hinges are integrated for assembly flexibility. Gates and runners are pathways through which molten material flows into the mold, while vents help release trapped air. Draft angles are essential for easy removal of the part from the mold. In Class II medical devices, such as syringes or catheters, precise molding is critical to ensuring product safety, sterility, and compliance with FDA regulations. Features like sealing surfaces and fine tolerances must be maintained to meet medical standards. Advanced materials, such as medical-grade polypropylene or polycarbonate, are often used to ensure biocompatibility.
Medical devices are categorized by the FDA into Class I, II, and III, depending on the risk they pose to patients and the level of regulatory control required.
Class I devices are low-risk and subject to general controls, such as bandages, stethoscopes, and tongue depressors. They usually do not require premarket approval (PMA) and have minimal regulatory requirements.
Class II devices present a moderate risk and require special controls, such as performance standards, post-market surveillance, and possibly FDA clearance via the 510(k) process. Examples include syringes, catheters, and infusion pumps.
Class III devices are high-risk and require the most stringent regulations, including premarket approval (PMA). These devices sustain or support life, such as pacemakers, artificial heart valves, and implantable defibrillators.
Injection molded parts are commonly found in Class II devices, where precision and material compliance are essential.
An example of Class II medical equipment is a syringe used for drug delivery. Syringes fall under Class II because they have direct patient interaction and must meet sterility and performance requirements to minimize risks. Other common examples include catheters, infusion pumps, blood pressure monitors, and dental handpieces.
Many injection molded parts are used in Class II devices, particularly for housings, fluid channels, and connectors. For instance, plastic needle hubs, syringe barrels, and catheter components are often injection molded from medical-grade plastics such as polycarbonate or polypropylene. These parts require high precision in molding to ensure functionality, durability, and compliance with FDA special controls, including biocompatibility and sterility assurance. Proper mold design is critical in ensuring that the parts meet tight tolerances and do not introduce contaminants into medical environments.
Class II medical devices typically require FDA clearance rather than approval. Most Class II devices go through the 510(k) premarket notification process, where the manufacturer must demonstrate that the device is substantially equivalent to a legally marketed device (predicate) in terms of safety and effectiveness. This process does not require full premarket approval (PMA), which is reserved for high-risk Class III devices.
For injection molded Class II medical parts, FDA clearance ensures the material and design meet regulatory standards, such as ISO 13485 for quality management and ISO 10993 for biocompatibility. Manufacturers must follow Good Manufacturing Practices (GMP) under 21 CFR Part 820 to ensure consistency, sterility, and traceability. While Class II devices do not need extensive clinical trials like Class III devices, they must meet specific labeling, testing, and post-market surveillance requirements.
Yes, a syringe is classified as a Class II medical device by the FDA. Syringes are considered moderate-risk devices because they have direct patient contact and must meet safety, sterility, and performance requirements to prevent contamination or incorrect dosing.
Syringes consist of injection molded parts, such as the barrel, plunger, and needle hub, typically made from medical-grade polypropylene or polycarbonate. The molding process must be highly precise to ensure airtight sealing, smooth plunger movement, and accurate dosage delivery.
Since syringes are regulated under Class II, manufacturers must obtain FDA 510(k) clearance before marketing them. This involves demonstrating that the syringe is substantially equivalent to an existing approved device. Additionally, syringes must comply with ISO 13485 (quality systems) and ISO 10993 (biocompatibility testing) standards to ensure patient safety.
The main difference between Class I and Class II medical devices is the level of regulatory control and associated risk.
Class I devices are low-risk and subject to general controls such as labeling, good manufacturing practices (GMP), and registration. They do not require FDA clearance and include items like bandages, examination gloves, and manual wheelchairs.
Class II devices pose moderate risk and require special controls, such as 510(k) clearance, performance testing, and sometimes post-market surveillance. Examples include syringes, catheters, and infusion pumps.
For injection molded parts, Class II devices demand higher precision and material compliance than Class I devices. They often require sterile manufacturing conditions, biocompatible plastics, and rigorous quality control processes to ensure safety and performance in medical applications.
FDA clearance for medical devices primarily refers to the 510(k) premarket notification process, required for Class II devices. This process ensures that a new medical device is substantially equivalent to an already legally marketed device. Unlike premarket approval (PMA) required for Class III devices, 510(k) clearance is faster and less expensive.
For injection molded Class II medical parts, manufacturers must demonstrate that the material, design, and functionality meet regulatory standards such as ISO 10993 for biocompatibility and ISO 13485 for quality management systems. The device must also comply with FDA’s Quality System Regulation (QSR) under 21 CFR Part 820 to ensure consistent manufacturing quality.
While FDA clearance is required for Class II devices, some exempt devices do not need a 510(k) submission but must still comply with labeling, manufacturing, and reporting requirements.
Approximately 43% of all medical devices are classified as Class II, according to FDA data. This category includes a wide range of devices, such as syringes, catheters, diagnostic tools, and surgical instruments, which require moderate regulatory controls.
Many injection molded components are used in Class II medical devices, including plastic housings, syringe barrels, connectors, and tubing components. These parts must meet FDA material and safety requirements, undergo quality testing, and, in most cases, obtain 510(k) clearance before reaching the market.
Class II devices balance innovation and patient safety, requiring special controls like biocompatibility testing, sterility validation, and performance testing to prevent risks associated with improper function or contamination.
You can identify an injection molded part by looking for key characteristics such as parting lines, ejector pin marks, and gate locations. These indicate where the plastic flowed into the mold and where the part was ejected. Consistent wall thickness, smooth finishes, and high repeatability also suggest injection molding.
In Class II medical devices, injection molded parts must meet strict tolerances and biocompatibility standards. For example, syringe barrels have precise inner diameters for smooth plunger movement, and catheter components require ultra-smooth finishes to minimize irritation.
The cost of an injection molded part varies significantly based on factors such as material selection, part complexity, mold design, production volume, and secondary operations.
Material Costs – Medical-grade plastics, such as polycarbonate, polypropylene, or PEEK, can cost between $2 to $50 per pound, depending on biocompatibility requirements and regulatory compliance.
Mold Costs – A simple aluminum mold may cost $5,000 to $20,000, while a high-precision, multi-cavity steel mold for Class II medical devices can range from $50,000 to $200,000.
Per-Part Cost – For high-volume production (100,000+ units), each part can cost between $0.10 to $5.00, with lower costs per unit at higher volumes. Smaller production runs (under 10,000 parts) result in higher per-unit prices.
Post-Processing & Sterilization – Additional costs arise from sterilization, assembly, and quality control, particularly for Class II medical devices, which require tight tolerances and FDA compliance.
Ultimately, economies of scale and mold durability are key factors in cost efficiency.
Class I medical devices are low-risk products that require minimal regulatory oversight. These include bandages, stethoscopes, tongue depressors, and non-sterile gloves. Unlike Class II devices, which need 510(k) clearance, most Class I devices are exempt from premarket approval.
Key attributes of Class I devices:
Simple Design: No electrical components or complex mechanisms.
Minimal Risk: Poses no significant harm to patients.
Basic Performance Standards: Must meet general safety and labeling requirements under FDA 21 CFR regulations.
Since injection-molded medical parts often require precise performance (like syringe barrels or inhaler casings), they are typically Class II, ensuring higher safety and sterility standards.
Syringes are usually Class II medical devices, not Class I, due to their moderate risk and requirement for strict performance standards. Class II designation applies because:
They penetrate the skin, posing an infection risk.
They require FDA 510(k) clearance to demonstrate safety.
Sterility is critical, requiring rigorous quality control.
However, some non-sterile syringes (without needles) may be Class I if they pose minimal risk. In contrast, injection-molded IV connectors, insulin syringes, and prefilled syringes are all Class II, ensuring compliance with strict ISO 13485 and FDA 21 CFR Part 820 standards.
Class II ME (Medical Electrical) Equipment refers to electrical medical devices with moderate risk, requiring additional safety measures under IEC 60601-1 standards. These include patient monitors, infusion pumps, and defibrillators, often incorporating injection-molded enclosures and housings for insulation and durability.
Key characteristics:
Double Insulation: Prevents electric shocks by eliminating the need for a ground connection.
Leakage Current Control: Ensures low electrical leakage to protect patients.
Biocompatible Enclosures: Uses injection-molded medical-grade plastics resistant to sterilization processes.
Unlike Class I ME equipment (simple devices like electric thermometers), Class II ME devices require more advanced safety protections to ensure patient and operator safety.
For Class II medical devices, performance standards refer to the regulatory benchmarks set by the FDA and international bodies (ISO, ASTM) that ensure device safety, durability, and effectiveness. These standards apply to injection-molded medical components like IV connectors, inhalers, and diagnostic test kits.
Key performance requirements include:
Material Safety (ISO 10993): Ensuring biocompatibility and non-toxicity for patient safety.
Dimensional Accuracy & Tolerances: Maintaining precise specifications for functionality.
Sterilization Compatibility (ISO 11135, 11137): Ensuring resistance to ethylene oxide (EtO) or gamma radiation sterilization.
Mechanical & Chemical Resistance: The part must withstand temperature changes, moisture, and repeated use without degradation.
Unlike Class III devices, which undergo full clinical trials, Class II devices must meet FDA-recognized standards to demonstrate safe and effective performance.
Class III medical devices face the strictest regulatory requirements due to their high risk. These include:
Premarket Approval (PMA): Unlike Class 2 devices that require 510(k) clearance, Class 3 devices must undergo a full scientific review to demonstrate safety and effectiveness.
Clinical Trials: Extensive human clinical studies are required to prove long-term safety and efficacy.
Risk Management & Biocompatibility Testing: Materials must undergo ISO 10993 biocompatibility testing to confirm they are safe for human implantation or prolonged use.
Manufacturing Process Validation: The FDA and ISO 13485 require stringent quality control, documentation, and process validation for production.
Post-Market Surveillance: Continuous monitoring and reporting of device performance, failures, or adverse effects is mandatory.
While Class II injection-molded parts (like inhaler housings or syringe barrels) require performance testing, Class III devices have much stricter material and durability requirements, ensuring long-term reliability inside the human body.
The primary difference between Class 2 and Class 3 medical devices is their level of risk and regulatory requirements. Class 2 devices are moderate-risk medical products that require FDA 510(k) clearance, demonstrating substantial equivalence to an already approved device. Examples include syringes, IV tubing, and blood pressure cuffs, which are often made using injection molding. These devices must meet performance and biocompatibility standards but do not require extensive clinical trials.
Class 3 devices, on the other hand, are high-risk, life-sustaining, or implantable medical products, such as pacemakers, artificial heart valves, and implantable defibrillators. These require premarket approval (PMA), extensive clinical testing, and stricter post-market surveillance. While injection molding is used in both classifications, Class 3 devices often require implant-grade materials like PEEK or medical-grade silicone, ensuring long-term biocompatibility. The higher regulatory burden for Class 3 devices reflects their critical role in patient survival.
In the European Union (EU) classificatio, a Type 2a medical device (or Class IIa) is a medium-risk device that is intended for short-term use (less than 30 days) inside the body or for diagnostic purposes. These include infusion pumps, blood pressure monitors, and diagnostic imaging devices. Many injection-molded components, such as disposable syringes, inhalers, and catheter connectors, fall under this category. These devices must comply with Medical Device Regulation (MDR) 2017/745 and require a Notified Body to assess their safety before they can be sold in the EU. Unlike Class IIb devices, which present higher risks (e.g., ventilators), Class IIa devices undergo a less stringent certification process but still require documented risk management and performance testing. In medical injection molding, biocompatibility, sterilization compatibility, and material selection are critical factors to ensure compliance with regulatory standards.
A Type 3 medical devic typically refers to a Class III medical device, which has the highest risk classification under FDA regulations. These devices sustain or support life, are implanted, or present potential high risks to patients. Unlike Class 2 injection-molded parts, which are used in diagnostic and therapeutic equipment, Class 3 devices include items like implantable pacemakers, artificial heart valves, and deep brain stimulators. These devices require premarket approval (PMA), extensive clinical trials, and rigorous regulatory oversight to ensure safety and efficacy. In contrast, Class 2 injection-molded parts, such as syringe barrels, IV connectors, and inhaler housings, require FDA 510(k) clearance, demonstrating that they are substantially equivalent to existing devices. The primary difference is the level of risk and regulatory scrutiny, with Type 3 devices undergoing the most stringent evaluation.
In networking, Layer 2 devices operate at the data link layer of the OSI model, such as switches and bridges. However, in the context of medical devices, Layer 2 can refer to embedded microcontrollers and communication modules within a Class 2 medical device that manage data transmission. These devices facilitate secure and reliable communication between sensors, monitoring systems, and hospital networks. For instance, a wireless infusion pump or a patient monitoring system may incorporate Layer 2 networking components to ensure real-time data exchange without interference. These networking capabilities must comply with HIPAA regulations and FDA cybersecurity guidelines to protect patient data. In injection-molded Class 2 medical devices, such as wearable health monitors or diagnostic equipment, embedded Layer 2 components ensure smooth operation and connectivity, enabling seamless integration with hospital IT infrastructure.
Extrusion molding is a continuous process that forces heated plastic through a die to create long, uniform profiles. It is commonly used for medical tubing, catheters, and IV lines requiring consistent diameters and flexibility. Unlike injection molding, which produces discrete parts, extrusion allows for endless lengths of tubing that can be cut to size. Medical extrusion often involves co-extrusion, where multiple materials are layered for specialized properties like antimicrobial coatings. Precision control ensures uniform wall thickness, smooth surfaces, and biocompatibility, meeting FDA and ISO 10993 standards. This process is essential for fluid management in medical applications, ensuring sterile and durable tubing solutions.
The injection molding process for Class 2 medical devices involves material selection, mold design, machine settings, quality control, and regulatory compliance. First, medical-grade polymers like polycarbonate or polypropylene are chosen for biocompatibility. The mold, designed to FDA and ISO standards, consists of an A-side and B-side, ensuring precision. The injection unit melts and injects plastic into the mold, followed by controlled cooling to prevent defects. The ejection system carefully removes the part without damage. Finally, rigorous quality control tests, including dimensional inspection, biocompatibility assessment, and sterilization validation, ensure compliance with FDA regulations for safe medical device use.
In medical device injection molding, the A-side (cavity side) is the portion of the mold that typically forms the external surface of the part, providing fine details and aesthetics. The B-side (core side) contains ejector pins and moving components that help form internal structures like threads, ribs, or undercuts. For medical parts like syringes or inhaler housings, the A-side often includes surface texturing or branding, while the B-side ensures precise structural integrity. Understanding A/B mold design is crucial for optimizing part functionality, ensuring smooth ejection, and preventing defects like flash or warping in medical components.
Injection molded medical parts can be joined using various techniques, depending on material compatibility and functional requirements. Ultrasonic welding is widely used for assembling components like IV connectors and catheter hubs, ensuring a strong, leak-proof bond. Adhesive bonding with medical-grade cyanoacrylates or UV-curable adhesives provides reliable connections for parts requiring flexibility. Snap-fit assemblies allow for tool-free assembly, commonly found in medical device housings. Overmolding combines multiple materials, such as soft elastomers over rigid plastics, improving grip and comfort in surgical instruments. Solvent bonding chemically fuses compatible plastics, ensuring seamless joins. Each method must comply with FDA regulations and ISO 10993 biocompatibility standards to ensure patient safety and durability in medical environments.
Clamping – The mold is securely closed by the clamping unit, ensuring it remains sealed under high pressure.
Injection – Medical-grade plastic pellets are heated and injected into the mold cavity at high pressure.
Cooling – The molten plastic solidifies within the mold, forming the final shape of the medical component.
Ejection – The mold opens, and the finished part is pushed out using ejector pins.
Post-Processing – The part may undergo secondary processes such as trimming, sterilization, or assembly.
Each step is critical in producing high-precision medical components like syringe barrels, IV connectors, and catheter hubs. Careful process control ensures compliance with FDA and ISO 13485 standards, ensuring the final product meets regulatory requirements for safety and functionality.
Injection molding is widely used in manufacturing Class 2 medical devices, creating precise and reliable components. Common products include syringes, inhalers, IV connectors, surgical instrument handles, diagnostic device housings, blood collection tubes, and catheters. These devices require strict biocompatibility, sterilizability, and durability, making injection molding an ideal process. Medical-grade plastics like polycarbonate, polyethylene, and polypropylene ensure chemical resistance and mechanical strength. Additionally, multi-shot and overmolding techniques allow for the integration of different materials, such as rubberized grips on surgical tools. The ability to produce high volumes with consistent quality makes injection molding the preferred method for disposable and reusable medical components. Manufacturers follow regulatory guidelines, including FDA 21 CFR Part 820 and ISO 13485, to ensure that each part meets industry standards for patient safety and device performance.
The thickness of an injection molded part in Class 2 medical devices varies based on function, material, and regulatory requirements. Generally, thickness ranges from 0.5 mm to 4 mm for medical components, ensuring structural integrity while minimizing material use. Thin-walled parts, around 0.5 mm to 1.5 mm, are common in disposable syringes, inhaler housings, and IV catheter components to ensure lightweight and cost-effective production. Thicker parts, around 2 mm to 4 mm, provide durability for reusable medical devices like surgical instrument handles or diagnostic equipment casings. Maintaining consistent wall thickness is critical to preventing defects like warping, sink marks, or uneven cooling. Design engineers must optimize thickness based on the specific polymer used, such as polycarbonate for impact resistance or polypropylene for flexibility, ensuring compliance with FDA and ISO 13485 standards for medical device manufacturing.
An injection molding machine consists of several key components, each playing a crucial role in producing high-quality medical device parts. The hopper stores and feeds plastic resin into the machine, ensuring a consistent supply of raw material. The barrel and screw melt and mix the plastic, providing uniform heating before injection. The injection unit pushes the molten plastic into the mold cavity under high pressure. The mold itself is a precision-engineered tool that shapes the medical device component, designed to meet FDA regulations. The clamping unit holds the mold tightly closed during injection and cooling, ensuring dimensional accuracy. The cooling system solidifies the plastic, preventing defects like warping. Finally, the ejection system removes the finished part. Each of these components is essential to producing Class 2 medical device parts with high precision, durability, and compliance with strict medical industry standards.
Extrusion and injection molding are both plastic manufacturing processes but differ significantly. Extrusion continuously pushes melted plastic through a die to create long, uniform profiles, such as tubing used in medical devices. Injection molding, on the other hand, injects molten plastic into a mold cavity, producing complex three-dimensional parts like enclosures for medical equipment, syringe components, and inhaler housings. Injection molding allows for precise control of part geometry and intricate designs, which are crucial for Class 2 medical devices requiring tight tolerances and biocompatibility. Unlike extrusion, injection molding can create detailed features, internal cavities, and multiple component assemblies, making it ideal for complex medical parts that require strict regulatory compliance.
Contact our professional team now for a same-day quote and risk-free project evaluation. Benefit from ISO 8 cleanrooms, advanced machines, and 12-hour fast response in medical injection molding.