ISO Certified FUJIU Medical Injection Mold is a trusted leader in the medical plastic parts manufacturing industry, with over 50 years of expertise in designing and producing high-quality injection-moulded components for medical applications. As a prominent China medical plastic parts suppliers and exporter, the company excels in producing custom plastic solutions that meet the stringent demands of the medical field, particularly in the global market. FUJIU Medical Injection Mold’s commitment to precision and reliability ensures that every product is made from medical-grade plastic materials, guaranteeing safety and performance. Their medical equipment parts plastic mould for sale further reflects their capability to meet the varied needs of manufacturers. ISO certification underscores their dedication to upholding the highest standards of quality in production, making them a preferred partner for medical device manufacturers worldwide. This longstanding reputation and adherence to global industry standards make FUJIU a key player among leading medical plastic parts exporters. FUJIU Medical Injection Mold, a trusted medical plastic parts exporter, specializes in high-quality parts for Class 1, 2, and 3 medical devices.
Low-Volume to High-Volume Production Capabilities
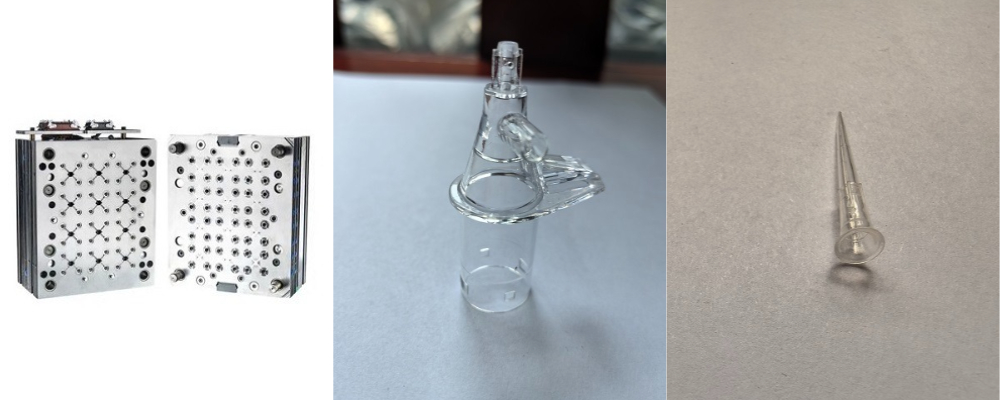
Attributes | Details |
---|---|
Place of Origin | Dongguan, Guangdong, China |
Brand Name | LY Medical Injection Mold |
Product Name | Medical Molding |
Technology | Injection Molding |
Plastic Material | ABS/PP/PS/PE/PVC/PA6/PA66.....etc |
Mold Life | 300000~1000000 Shots |
Certification | ISO9001/TS16949/QS/ISO14001 |
Surface Treatment | Polishing, Etching, Texture, Plating, Painting |
Color/Size | Custom |
Tolerance | 0.01-0.1mm |
Drawing Format | .igs/.stp/.x-t/.step/.stl/.sldprt/.dwg/.dxf |
Quality Control | Process Inspection and Final Inspection before Shipment |
Sales Unit | Single Item |
Facilities and Processes: A Leading Medical Plastic Parts Exporter
Our state-of-the-art facilities are designed to meet the highest standards required for medical device manufacturing. As a prominent medical plastic parts exporter, we work closely with plastic medical device manufacturers, employing advanced technologies and stringent processes to ensure the production of top-quality medical plastic components.
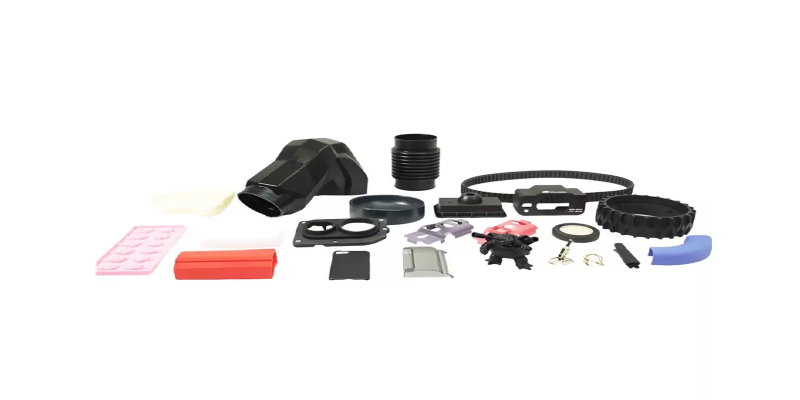
Facilities Provided by a Leading Medical Plastic Parts Exporter
Injection Moulding Machines
- Located within a Class 7 cleanroom, these machines are designed to meet the strictest hygiene and safety standards required for medical manufacturing.
- The cleanroom environment ensures that no contaminants can affect the precision and integrity of the moulding process, which is crucial for producing high-quality medical moulded products.
Cleanroom Features
- The facility is equipped with four laminar flow cabinets, which are used for assembling delicate medical parts in a contaminant-free environment.
- These cabinets maintain a sterile atmosphere, crucial for ensuring the quality and safety of the finished products.
Order Quantity
- We operates with a minimum order quantity of 1000 units, allowing for efficient mass production while ensuring high-quality standards are maintained across all orders.
Processes Provided by a Leading Medical Plastic Parts Exporter
As a trusted medical plastic parts exporter, We offers a comprehensive range of services to meet the unique needs of the medical industry. These services ensure that each project is executed with precision, efficiency, and the highest standards of quality.
Product Design
- We employs advanced 3D CAD software to create detailed and accurate designs for medical plastic components.
- This technology allows for rapid iteration and refinement, ensuring that all design requirements are met before proceeding to production.
Rapid Prototyping
- Using rapid prototyping techniques, We creates models that are used for quick testing and validation.
- This service allows clients to evaluate designs early in the process, reducing risks and saving time before full-scale production.
Tool Design
- We specializes in custom-designed tools tailored to specific product requirements.
- These tools are crafted to ensure precision and efficiency in the manufacturing process, improving product consistency.
Pre-production Sampling
- Before beginning full-scale production, We provides pre-production sampling to ensure the design meets all functional and aesthetic requirements.
- This step helps in identifying potential issues early on, ensuring a smooth transition to mass production.
Manufacture
- We have full-scale production capabilities, allowing them to handle high-volume orders while maintaining consistent quality.
- Their extensive manufacturing infrastructure ensures the ability to produce large quantities of medical plastic parts with reliability and speed.
Markets Supplied by a Leading Medical Plastic Parts Exporter
As a trusted medical plastic parts exporter and a recognized plastic injection medical parts exporter, We serves a wide range of industries that require high-quality plastic components for their specialized applications. Their expertise spans multiple markets, ensuring that each product meets the unique demands of the sector.
Medical Device
- We supplies components for a wide variety of medical devices, including diagnostic tools, surgical instruments, and other essential healthcare equipment.
- Their precise manufacturing ensures that medical-grade standards are met for safety and functionality.
Ear, Nose, and Throat (ENT)
- Our manufactures medical plastic parts used in ENT devices, such as hearing aids, nasal aspirators, and other instruments critical for ENT care.
- The company’s ability to produce small, precise components ensures the optimal performance of ENT products.
Dental
- Serving the dental industry, We produces durable and hygienic plastic parts for dental instruments, including mouthpieces, handpieces, and orthodontic devices.
- The company’s focus on quality ensures that these parts meet the highest standards for patient safety and comfort.
Veterinary
- We extends its services to the veterinary market by providing medical plastic components for animal care, including surgical tools, diagnostic devices, and pet health products.
- Their reliable manufacturing processes ensure that veterinary products are both safe and effective.
Harm Reduction
- We also involved in the harm reduction market, supplying plastic components for products such as needle exchange kits and safe-use equipment.
- Their experience in this area allows them to provide high-quality, durable solutions that support public health initiatives.
Plastic Materials Used by a Leading Medical Plastic Parts Exporter
As a trusted medical plastic parts exporter, We utilizes a wide range of high-performance plastic materials to meet the stringent requirements of the medical industry. These materials are carefully selected for their durability, safety, and ability to withstand the demanding conditions of medical applications.
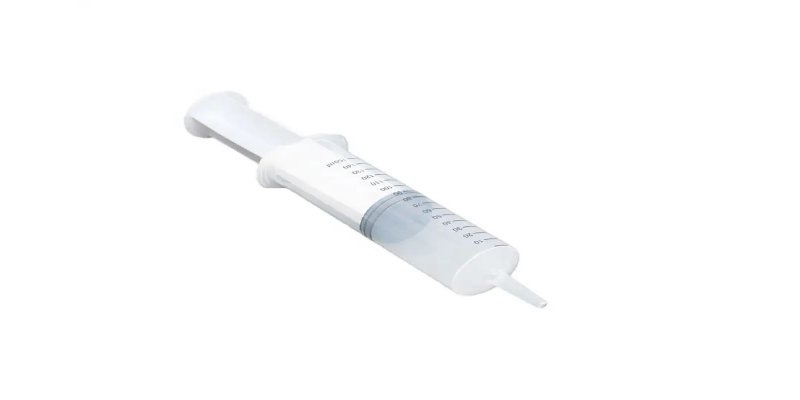
Polypropylene (PP)
- Polypropylene is a versatile material commonly used in medical devices due to its excellent chemical resistance and ability to withstand sterilization.
- It is lightweight, non-toxic, and ideal for disposable medical products such as syringes and test tubes.
Polyethylene Terephthalate Glycol (PETG)
- PETG is favored for its clarity, strength, and ease of thermoforming, making it ideal for medical packaging and diagnostic equipment.
- Its high impact resistance and recyclability also make it an environmentally friendly option for various medical products.
Low-density Polyethylene (LDPE)
- LDPE is used in medical applications that require flexibility and ease of processing, such as tubing, packaging films, and medical bags.
- Its low density ensures it remains lightweight while offering reliable performance in various healthcare settings.
Flexible and Rigid Polyvinyl Chloride (PVC)
- Both flexible and rigid PVC are commonly used in medical devices like IV tubing, catheters, and blood bags, as well as rigid components for surgical instruments.
- PVC’s versatility, ease of molding, and durability make it a popular choice for medical plastic parts.
High-density Polyethylene (HDPE)
- HDPE is known for its high strength-to-density ratio, making it ideal for applications that require toughness and impact resistance, such as medical containers and equipment.
- It is also resistant to corrosion and chemicals, ensuring the safety and integrity of medical components.
Cellulose Acetate (CA)
- Cellulose acetate is a biodegradable plastic commonly used in the production of medical filters, membrane materials, and surgical components.
- Its biocompatibility makes it a safe choice for use in medical devices that come in direct contact with the human body.
Nylon
- Nylon is used in medical applications that require high strength, durability, and wear resistance, such as surgical sutures, mesh implants, and drug delivery systems.
- Its versatility and ability to withstand autoclaving make it suitable for both disposable and reusable medical devices.
Our careful selection and expertise in processing these materials ensure that every product meets the rigorous standards required in the medical field, reinforcing their reputation as a reliable medical plastic parts exporter.
Benefits of Choosing a Leading Medical Plastic Parts Exporter & Suppliers
As a leading medical plastic parts exporter & suppliers , We offers significant advantages to clients in the medical industry. These key benefits highlight their commitment to quality, safety, and precision in producing medical plastic components.
Reliable, Refined Injection Moulding Process
- We employ a highly refined injection moulding process, ensuring consistent and precise manufacturing for medical applications and medical molding.
- This process allows for the production of complex shapes and small parts, meeting the demanding specifications of medical devices and ensuring reliable performance in critical healthcare environments.
Expertise in Medical Components
- With decades of experience, we have specialized knowledge in plastic injection moulding for medical components, including custom medical molding components.
- Their deep understanding of the regulatory and functional requirements of the medical industry ensures that every product is designed and manufactured to meet the highest standards of safety and performance.
High Precision and Quality Control
- We are committed to achieving high precision in every product they manufacture, from components to precision mold medical applications. Rigorous quality control procedures are in place to ensure that every part meets exact specifications.
- This attention to detail guarantees product consistency and compliance with international standards, making them a trusted partner for medical device manufacturers.
Class 7 Cleanroom
- The manufacturing process is carried out in a state-of-the-art Class 7 cleanroom, which meets ISO 14644-1 standards for cleanliness and contamination control.
- The cleanroom is equipped with HEPA filters and stainless steel surfaces, creating a sterile environment that ensures the integrity and safety of all medical plastic components produced.
Applications of a Leading Medical Plastic Parts Exporter
As a trusted medical plastic parts exporter, we provide critical components for various medical applications. Our use of high precision tools for medical device manufacturing ensures that our high-quality plastic parts meet the demands of essential medical devices, guaranteeing functionality, safety, and precision.
Medical Devices
- Stopcock Connectors: Our manufactures stopcock connectors used in medical tubing systems, ensuring leak-free connections for safe fluid management during surgeries and treatments.
- Caps: High-performance caps are produced for sealing medical containers, ensuring sterility and preventing contamination in products like vials, syringes, and diagnostic kits.
- Flow Regulators: We creates flow regulators for controlling the flow of gases and liquids in medical equipment, ensuring accurate delivery in critical medical procedures.
- Valves: Precision-engineered valves are used in devices such as infusion pumps and respirators, where exact flow control is essential for patient care.
- Clips: Our manufactures clips used in medical devices for securing components such as tubing, wires, or dressings, providing reliability and ease of use in clinical settings.
These products are essential for maintaining the highest standards of care and ensuring the effective functioning of medical devices in hospitals, clinics, and other healthcare facilities.
Key Characteristics of an Excellent Medical Plastic Parts Exporter
An excellent medical plastic parts exporter must possess a variety of qualities that contribute to their ability to deliver high-quality, reliable products. These characteristics span from having strong research and technical development capabilities to offering customer-centric services. Each aspect plays a crucial role in ensuring the production of medical plastic parts that meet stringent regulatory standards and exceed customer expectations. In this answer, we will explore the essential qualities a medical plastic parts exporter should have, including powerful research capabilities, in-depth technical expertise, high product quality, and customer-focused service concepts. These characteristics ensure that exporters are equipped to meet the growing demands of the medical device industry while maintaining the highest standards of quality and innovation.
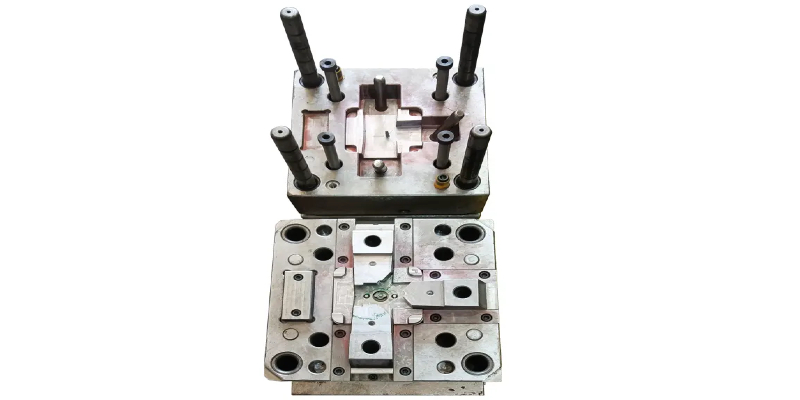
Strong Research Capabilities and Technical Expertise
An excellent medical plastic parts exporter should have a robust research and development (R&D) team with a strong focus on innovation and continuous improvement. R&D capabilities are critical because they allow the exporter to stay ahead of industry trends and technological advancements, ensuring the production of cutting-edge medical plastic parts. In-depth technical expertise allows the company to understand complex medical device requirements and develop precise solutions tailored to various applications.
Research capabilities enable the medical plastic parts exporter to explore new materials, technologies, and manufacturing techniques. This is particularly important for the medical field, where new materials are constantly being developed to improve device safety, performance, and patient outcomes. By investing in R&D, a trusted exporter can not only provide standard parts but also customize solutions to meet specific needs, enhancing their competitiveness and the quality of their products.
High Comprehensive Quality Standards
Another key feature of a top-tier medical plastic parts exporter is their commitment to high-quality standards. The medical industry demands the highest level of precision and reliability, as any defect in a medical plastic part can have serious consequences for patient safety and device performance. A comprehensive quality control system ensures that every part produced meets or exceeds the necessary standards for biocompatibility, durability, and functionality.
Quality assurance measures should be integrated at every stage of the production process, from material selection to final product testing. This includes stringent processes for sterilization, contamination prevention, and thorough inspections of each batch. By adhering to international certifications like ISO 13485 and FDA guidelines, a medical plastic parts exporter ensures that their products meet regulatory requirements and are safe for use in Class 1, 2, and 3 medical devices. FUJIU Medical Injection Mold, for example, prioritizes high-quality standards to guarantee the precision and safety of the medical parts they export.
Customer-Centric Service Concept
An exceptional medical plastic parts exporter places great emphasis on customer satisfaction by adopting a customer-centric service concept. This means that the exporter is focused on understanding the unique needs and challenges of each customer, providing tailored solutions, and offering support at every stage of the process. A customer-focused approach ensures that the exporter not only delivers quality products but also builds strong, long-lasting relationships with clients.
This approach involves clear communication, quick response times, and the flexibility to adapt to changing customer demands. For example, an exporter might offer assistance in product design, offer prototyping services, or collaborate on optimizing manufacturing processes. A strong after-sales support system, including troubleshooting and technical assistance, is also essential for ensuring customer satisfaction. FUJIU Medical Injection Mold exemplifies this customer-centric philosophy, providing ongoing support and guidance to clients throughout the product lifecycle.
Advanced Manufacturing Capabilities
Advanced manufacturing capabilities are essential for a medical plastic parts exporter, as they ensure that the parts produced are not only precise but also scalable for large-volume production. Technologies like injection molding, extrusion, and 3D printing allow exporters to produce complex parts with high accuracy and consistency, all while maintaining cost-effectiveness.
Modern manufacturing facilities equipped with state-of-the-art machinery ensure the production of high-quality medical plastic parts. This includes the use of automated systems for precise molding and injection, which reduces human error and increases efficiency. Advanced manufacturing capabilities also enable the exporter to produce parts in a range of materials, ensuring that the medical devices meet all necessary functional and regulatory standards. With the ability to scale production efficiently, a medical plastic parts exporter like FUJIU Medical Injection Mold can serve large-scale medical device manufacturers reliably.
Regulatory Compliance and Certifications
A reliable medical plastic parts exporter must maintain strict compliance with industry regulations and possess the necessary certifications to guarantee product safety and reliability. Regulatory compliance is particularly critical in the medical field, where manufacturers must meet rigorous requirements to ensure patient safety and the effectiveness of medical devices.
Certifications like ISO 13485, ISO 9001, and FDA approvals are essential for demonstrating that the exporter adheres to global standards. These certifications cover aspects like quality management, product traceability, and design controls. By ensuring compliance with these regulations, the exporter can reassure their clients that the parts they provide are safe and meet all legal and industry standards. This level of certification also ensures that the medical plastic parts exporter is trusted and recognized within the global medical industry.
Innovation in Material Science
Innovation in material science is another crucial factor for an exceptional medical plastic parts exporter. As new materials are developed to meet the specific needs of medical devices, an exporter must keep pace with these advancements to offer the most suitable options. Medical plastics must meet various requirements, such as biocompatibility, resistance to harsh environments, and the ability to withstand sterilization methods like autoclaving or gamma irradiation.
An exporter who invests in exploring and developing new materials, such as high-performance thermoplastics like PEEK or medical-grade polypropylene, can provide medical device manufacturers with innovative solutions. By staying at the forefront of material science, a medical plastic parts exporter can offer a wider range of options for different medical applications, ensuring that clients have access to the most advanced and reliable materials for their products.
An excellent medical plastic parts exporter must have a multifaceted approach to meet the diverse and demanding needs of the medical industry. From having strong research capabilities and technical expertise to adhering to high-quality standards and maintaining customer-centric service, each characteristic plays a pivotal role in ensuring that the exporter provides top-quality medical plastic parts. By investing in advanced manufacturing, regulatory compliance, and innovation, a trusted medical plastic parts exporter can maintain its competitive edge while continuing to meet the highest standards of safety, performance, and customer satisfaction. FUJIU Medical Injection Mold exemplifies these qualities, providing reliable, high-quality plastic parts for medical devices worldwide.
How an Excellent Medical Plastic Parts Exporter Ensures Timely Supply and Supply Security
In the competitive and highly regulated medical industry, ensuring the timely supply and security of medical plastic parts is crucial for maintaining smooth production, regulatory compliance, and patient safety. An excellent medical plastic parts exporter must implement a comprehensive strategy that includes supply chain management, production efficiency, quality control, and risk mitigation. This article explores the key aspects that contribute to achieving these objectives, ensuring that customers receive high-quality medical plastic parts without disruptions.
Robust Supply Chain Management
A well-structured supply chain is the backbone of a reliable exporter. Ensuring seamless procurement, logistics, and distribution helps prevent delays and supply shortages.
- Diversified Supplier Network: Partnering with multiple raw material suppliers reduces the risk of dependency on a single source, ensuring continued production.
- Efficient Logistics Planning: Utilizing advanced logistics strategies, including multiple shipping routes and warehouses in key locations, prevents delays caused by transportation issues.
- Real-Time Inventory Monitoring: Implementing digital tracking systems for inventory management enables proactive restocking and quick responses to demand fluctuations.
Advanced Production and Manufacturing Efficiency
Efficient manufacturing processes are essential for maintaining a steady supply of medical plastic parts while meeting industry standards.
- Automated Production Lines: Leveraging automation improves precision, reduces production time, and minimizes human error, ensuring high-quality and timely manufacturing.
- Lean Manufacturing Practices: Eliminating waste, optimizing resources, and streamlining workflows enhance production speed and cost-effectiveness.
- Capacity Planning: Regularly assessing production capacity and upgrading facilities as needed ensures the ability to meet high-volume demands without delays.
Strict Quality Control and Compliance
Medical plastic parts must meet stringent regulatory and quality standards to ensure safety and reliability. Maintaining strict quality control measures is vital for consistent and timely supply.
- Comprehensive Testing Protocols: Conducting material inspections, dimensional accuracy checks, and performance testing ensures that all parts meet industry requirements.
- Certifications and Compliance: Adhering to international medical standards such as ISO 13485 and FDA regulations guarantees product reliability and global market acceptance.
- Traceability Systems: Implementing batch tracking and documentation helps quickly address potential defects and recalls, reducing risks associated with supply disruptions.
Risk Management and Contingency Planning
Unexpected challenges such as raw material shortages, geopolitical issues, and production failures can threaten supply security. A proactive approach to risk management is essential.
- Backup Production Facilities: Establishing alternative production sites or outsourcing to reliable partners helps mitigate risks caused by local disruptions.
- Emergency Stock Reserves: Maintaining a buffer stock of critical medical plastic parts ensures continuity during supply chain disruptions.
- Scenario Planning and Crisis Response: Developing strategies for different risk scenarios allows exporters to react swiftly to unforeseen events, minimizing supply interruptions.
Strong Customer Relationship and Communication
Building trust and maintaining transparent communication with clients help anticipate demand and prevent supply chain issues.
- Demand Forecasting Collaboration: Working closely with customers to predict order requirements helps optimize production planning and inventory management.
- Flexible Order Fulfillment: Offering customized supply solutions, including priority production and expedited shipping, ensures that urgent needs are met.
- 24/7 Customer Support: Providing continuous support and real-time updates helps clients manage their supply chain effectively.
By integrating these strategic elements, an excellent medical plastic parts exporter can ensure both timely supply and supply security, ultimately supporting the reliability and efficiency of the global healthcare industry.
FAQs about Medical Plastic Parts Exporter
The United States holds the title of the largest exporter of medical devices worldwide. The country houses numerous well-established companies and is a leader in medical technology innovation. Based on data up to recent years, the U.S. medical device market is not only expansive in terms of domestic sales but is also highly active in international trade. Companies like Medtronic, Johnson & Johnson, and Abbott Laboratories are just a few of the noteworthy American enterprises that contribute to the country’s position as a global leader in medical device exports.
Several types of plastics are used extensively in the medical industry due to their versatility, biocompatibility, and durability. Some of the commonly used plastics include Polyvinyl Chloride (PVC), Polyethylene (PE), Polypropylene (PP), Polystyrene (PS), and Polycarbonate (PC). These materials are chosen based on their specific properties that make them suitable for a range of medical applications such as disposable syringes, intravenous bags, catheters, implantable devices, and diagnostic equipment housings. Each plastic type offers unique advantages such as chemical resistance, clarity, toughness, and ease of sterilization.
Determining the “best” plastic for medical devices largely depends on the specific application and the performance requirements of the device. However, Polyetheretherketone (PEEK) is often considered one of the top-performing polymers in the medical field. PEEK boasts excellent mechanical properties, high chemical resistance, and biocompatibility, making it suitable for a wide variety of medical devices including implants and surgical instruments. Its robustness under sterilization conditions further enhances its suitability for repeated use scenarios. Additionally, plastics like Polycarbonate (PC) and Polypropylene (PP) are widely used for disposable or less demanding medical applications due to their favorable balance of properties and cost-effectiveness.
The medical injection molding market is growing rapidly due to the increasing demand for high-quality medical devices and parts. In 2020, the global medical injection molding market was valued at approximately $9 billion and is expected to grow at a compound annual growth rate (CAGR) of around 7% from 2021 to 2028. The rise in chronic diseases, the need for more advanced medical devices, and the growing demand for minimally invasive procedures drive this growth. As a trusted medical plastic parts exporter, FUJIU Medical Injection Mold contributes to this booming market by manufacturing precision plastic parts for various medical applications, including surgical instruments, diagnostic equipment, and drug delivery systems. This market’s expansion is expected to continue, driven by ongoing advancements in medical technology and the increasing use of plastic parts in medical devices.
Medical-grade plastic is produced through a specialized process designed to meet stringent quality and safety standards. The process begins with selecting high-quality raw plastic materials, such as polyethylene, polypropylene, polycarbonate, or medical-grade PVC, depending on the specific requirements of the medical device. These materials are then subjected to injection molding or extrusion, forming them into the desired shape. During manufacturing, the plastic undergoes rigorous testing for biocompatibility, chemical resistance, and durability to ensure it meets medical industry standards. For applications like medical devices and implants, the plastic is sterilized and thoroughly checked for impurities to ensure it is safe for human contact. FUJIU Medical Injection Mold follows these strict protocols, ensuring that the medical plastic parts they export meet global quality standards for use in Class 1, 2, and 3 medical devices.
The cost of injection molding per hour can vary widely depending on several factors, such as the complexity of the mold, the type of plastic material used, and the equipment’s setup and maintenance costs. On average, the cost of injection molding ranges from $50 to $150 per hour. For high-volume production, such as in medical device manufacturing, costs can be lower due to economies of scale. However, more complex molds, such as those required for precision medical parts, may increase the cost. The expertise and reliability of a medical plastic parts exporter like FUJIU Medical Injection Mold ensure that production is efficient, helping to keep costs down while maintaining high standards of quality and precision for medical components. Other factors, such as mold design and tooling, will also influence the final price.
Plastic production costs depend on several factors, including the type of plastic material, production volume, part complexity, and the manufacturing method used. For medical plastic parts, costs can range from a few cents per part for low-complexity items made from common materials, to several dollars per part for high-performance materials used in medical devices. For injection molding, costs typically include the material cost, mold cost (which can be expensive upfront), labor, energy, and machine operation costs. Additionally, quality control, testing, and packaging for medical-grade plastic parts add to the cost. At FUJIU Medical Injection Mold, these factors are carefully managed to ensure competitive pricing for medical device manufacturers while maintaining high quality. By optimizing production and using advanced technologies, medical plastic parts exporters can offer a balance between cost-efficiency and precision.
In general, injection molding tends to be cheaper than CNC (Computer Numerical Control) machining, especially when producing large quantities of parts. Injection molding has a higher initial setup cost due to mold creation, but once the mold is made, the cost per part decreases significantly with high-volume production. This makes injection molding a cost-effective choice for mass production, especially for medical plastic parts. CNC machining, on the other hand, is more suitable for lower-volume production and parts with high complexity or tight tolerances. While CNC machining allows for more flexibility in part design, it typically takes longer per part, increasing the cost. As a reliable medical plastic parts exporter, FUJIU Medical Injection Mold offers injection molding solutions that help keep production costs low, making it an ideal choice for manufacturers in the medical industry.
Injection molding can be both inexpensive and expensive, depending on the production scale, part complexity, and materials used. For high-volume production, injection molding is generally considered cost-effective due to lower per-unit costs after the mold is created. The initial setup for injection molding, which includes mold design and tooling, can be expensive, but for large production runs, the cost per unit drops significantly. Conversely, for small production runs, injection molding can be less cost-effective compared to other methods, like 3D printing or CNC machining, because of the high initial setup costs. As a medical plastic parts exporter, FUJIU Medical Injection Mold optimizes production efficiency, making injection molding an economical choice for manufacturers needing reliable, high-quality medical components at scale, particularly for Class 1, 2, and 3 devices.
Yes, medical-grade plastic is designed to meet strict safety and biocompatibility standards, ensuring it is safe for use in medical applications. These plastics are tested for their resistance to biological reactions, chemical stability, and their ability to withstand sterilization methods commonly used in medical environments. Medical-grade plastics are non-toxic, free from harmful chemicals, and durable under harsh conditions, making them ideal for use in devices that come into direct contact with the human body, such as syringes, IV components, and surgical tools. FUJIU Medical Injection Mold ensures that all exported plastic parts are compliant with regulatory standards, providing peace of mind to manufacturers and healthcare professionals relying on high-quality, safe medical components.
Medical-grade plastic is made from a variety of materials, each selected based on its specific properties and suitability for different medical applications. Common materials include medical-grade polyethylene (PE), polypropylene (PP), polycarbonate (PC), polystyrene (PS), and medical-grade PVC. These materials are chosen for their biocompatibility, durability, and resistance to chemicals, which are crucial for ensuring the safety and performance of medical devices. Some medical-grade plastics are engineered to be transparent for easy monitoring of fluids or sterilization procedures, while others are designed to be flexible or rigid depending on the intended use. FUJIU Medical Injection Mold works with these materials to produce high-quality, reliable medical plastic parts that meet the rigorous standards required in the medical device industry.
The best plastic for medical use depends on the specific requirements of the application, such as biocompatibility, chemical resistance, and durability. Some of the most commonly used plastics in medical devices include medical-grade polyethylene (PE), polypropylene (PP), polycarbonate (PC), and PEEK (Polyether Ether Ketone). PE and PP are often used for items like syringes and IV bags due to their chemical resistance and flexibility. Polycarbonate is used for transparent medical devices like drug delivery systems and diagnostic equipment due to its clarity and strength. PEEK is ideal for high-performance medical implants, as it offers excellent durability and resistance to wear. FUJIU Medical Injection Mold utilizes a range of medical-grade plastics to create reliable parts for various medical device applications, ensuring the highest quality standards are met.
Contact our professional team now for a same-day quote and risk-free project evaluation. Benefit from ISO 8 cleanrooms, advanced machines, and 12-hour fast response in medical injection molding.