Medical plastic parts play an essential role in driving innovation and improving healthcare delivery. These components are critical for a wide array of applications, including surgical instruments, bone implants, diagnostic devices, and medical packaging. Their lightweight, durable, and sterilizable properties make them indispensable in modern medical practices. Behind the seamless integration of these parts into life-saving equipment is the expertise of a medical plastic parts supplier, whose ability to deliver precision, quality, and compliance ensures the highest standards of healthcare safety and efficacy.
High-quality medical plastic parts suppliers are at the forefront of advancing medical device technology. By leveraging state-of-the-art manufacturing processes such as medical injection molding, cleanroom production, and advanced material selection, these suppliers help produce reliable components that meet strict regulatory requirements. Their expertise not only supports the creation of innovative devices but also ensures durability and biocompatibility, which are crucial for both patient safety and long-term device functionality.
Selecting a dependable medical plastic parts supplier is a pivotal step for healthcare companies. Reliable suppliers, ensure adherence to certifications like ISO 13485:2016, employ cutting-edge technologies, and collaborate closely with clients to meet specific medical needs. This partnership is key to achieving consistent production quality and addressing the unique challenges of the medical industry. In particular, China medical plastic parts suppliers are increasingly recognized for their ability to provide innovative, cost-effective solutions such as injection molding for medical devices and labs. FUJIU Medical Injection Mold, a top medical plastic parts supplier, delivers innovative, cost-effective injection molding for medical devices and labs.
Low-Volume to High-Volume Production Capabilities
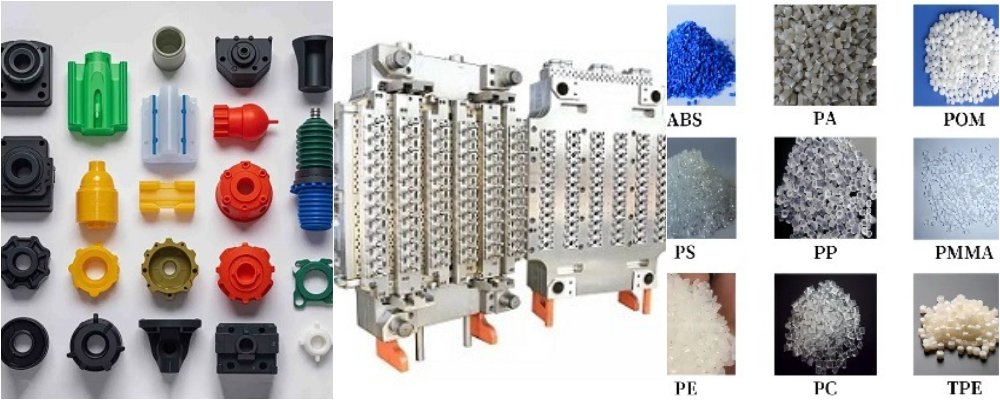
Attributes | Details |
---|---|
Place of Origin | Dongguan, Guangdong, China |
Brand Name | LY Medical Injection Mold |
Product Name | Medical Plastic Parts |
Molding Mode | Plastic Injection Mold |
Processing Service | Molding, Cutting |
Model | Customized |
Size | Customized |
Structure | Customized |
Color | Customized |
Plastic Material | PA66/PC/PE/PVC/PMMA/PP/ABS/ASA/TPU/POM etc |
Surface Treatment | Polishing, Etching, Texturing, Plating, Painting |
Mold Life | 300000~1000000 Shots |
Service | OEM ODM Customization |
Mold Frame | European Standard, World Standard, According to Customer Requirements |
Logo | Customized Logo Acceptable |
Features | High Precision |
Certification | ISO9001/ISO13485 |
Packaging | Plastic Bag Packaging or Packaging According to Customer Requirements |
Transportation | By Sea or Air According to Customer Requirements |
The Role of Medical Plastic Parts in Healthcare
How Medical Plastic Parts Enhance Healthcare
Medical plastic parts have revolutionized healthcare by offering unique benefits that traditional materials like metal or glass cannot match. Lightweight yet highly durable, these materials provide the strength needed for medical applications while reducing the strain on healthcare professionals and patients. Their sterilizable nature ensures they meet stringent hygiene standards, making them ideal for use in environments where safety and cleanliness are paramount.
The involvement of a medical plastic parts supplier is crucial in ensuring these materials meet the highest performance and compliance standards. Suppliers not only deliver precision-manufactured components but also work closely with healthcare organizations to create parts tailored to complex medical needs.
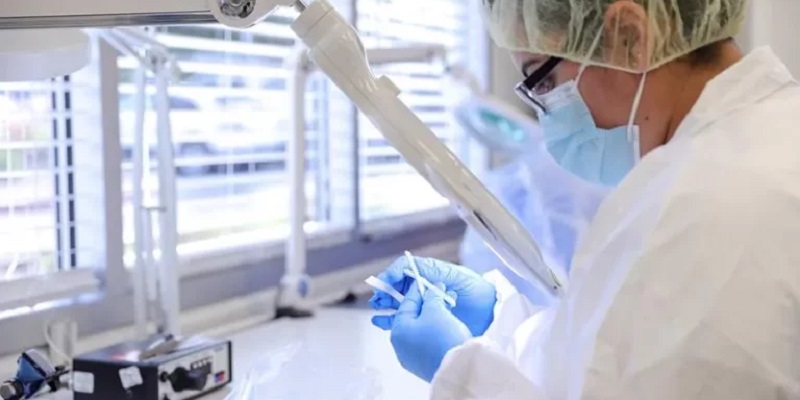
Key Benefits of Medical Plastics
- Lightweight Design: Plastic components reduce the overall weight of medical devices, enhancing portability and ease of use in clinical and surgical settings. Lightweight devices are especially beneficial in wearable technology and portable diagnostic tools.
- Durability: Medical-grade plastics resist wear and tear, maintaining their integrity under rigorous use. This property ensures longer device lifespans and reduced maintenance costs.
- Sterilization Compatibility: Many medical plastics can endure various sterilization methods, such as autoclaving, chemical treatments, and radiation, ensuring they remain safe for repeated use in sterile environments.
The expertise of a medical plastic parts supplier ensures these benefits are optimized in every component they deliver, empowering manufacturers to meet healthcare’s demanding standards.
Applications of Medical Plastic Parts in Healthcare
Medical plastic parts have diverse applications across various healthcare sectors, enabling innovation and improving patient outcomes. Below are some of their most common uses:
- Bone Implants:
Advanced plastics such as PEEK and UHMWPE are frequently used in orthopedic implants. These materials are biocompatible, durable, and lightweight, making them ideal for joint replacements, spinal implants, and fracture fixation devices. - Diagnostic Tools:
Plastic components form the backbone of diagnostic equipment like blood analyzers, imaging systems, and handheld devices. Their lightweight nature and adaptability allow for the production of intricate designs necessary for precision diagnostics. - Surgical Instruments:
Plastics are used in surgical tools due to their ability to withstand sterilization and resist corrosion. Instruments made from plastic are lighter and easier to handle, which can improve surgical precision and reduce fatigue. - Medical Packaging:
Sterilizable plastic packaging ensures the safe transport and storage of medications, implants, and instruments. Features like tamper resistance and transparency make plastics ideal for medical packaging solutions.
The Role of the Medical Plastic Parts Supplier
A reliable medical plastic parts suppliers plays an integral role in bringing these applications to life. By leveraging cutting-edge technologies like injection molding and cleanroom production, suppliers deliver precision-engineered parts that align with medical standards. Their knowledge of material science and manufacturing processes ensures that every component, from bone implants to surgical tools, meets stringent performance and safety criteria.
Collaboration with a trusted medical plastic parts supplier is essential for healthcare organizations seeking innovative and compliant solutions that support the growing demands of modern medicine.
Key Features to Look for in a Medical Plastic Parts Supplier
Ensuring Quality and Compliance
A reliable medical plastic parts supplier must prioritize quality and compliance to meet the stringent standards of the healthcare industry. Certifications such as ISO 13485:2016 ensure that the supplier adheres to internationally recognized quality management practices for medical devices. Furthermore, suppliers must ensure that their materials and processes comply with biocompatibility standards, guaranteeing that medical components are safe for use in clinical settings.
Regulatory compliance is non-negotiable. A trustworthy supplier must demonstrate an in-depth understanding of regional and global medical device regulations, ensuring that all parts meet the necessary requirements. This focus on quality and compliance not only enhances patient safety but also helps manufacturers avoid costly delays and recalls.
Comprehensive Production Capabilities
The production capabilities of a medical plastic parts supplier are a key determinant of their ability to deliver on complex healthcare projects. A versatile supplier should offer the following:
- Injection Molding Expertise: The cornerstone of medical plastic manufacturing, allowing for the creation of precise and intricate components.
- Cleanroom Manufacturing: Facilities certified to ISO Class 7 or 8 standards to minimize contamination risks during production.
- Prototyping Services: Fast and efficient prototyping capabilities to validate designs and functionality before mass production.
- Scalability: The ability to efficiently manage both small-scale and large-scale production runs without compromising quality.
Suppliers with robust production capabilities can seamlessly adapt to the evolving needs of healthcare manufacturers.
Innovation and Adaptability
Innovation and adaptability are vital traits of a competitive plastic medical parts supplier. Advanced technologies and processes not only enhance efficiency but also open the door to new possibilities in medical device plastic manufacturing. Below is an overview of the cutting-edge technologies suppliers may offer:
Technology | Benefits | Applications |
---|---|---|
3D Printing | Rapid prototyping, cost-effective for low-volume production. | Custom implants, surgical guides. |
Moldflow Simulation | Simulates mold filling processes to optimize design and reduce production defects. | Complex injection-molded components. |
Micro Injection Molding | Enables the creation of miniature parts with high precision and consistency. | Catheters, diagnostic devices. |
Material Selection Tools | Helps in choosing biocompatible and sterilizable plastics tailored to specific medical applications. | Bone implants, surgical tools. |
An innovative supplier with these capabilities can provide custom solutions tailored to the unique needs of healthcare applications, ensuring a competitive edge.
Why These Features Matter
Selecting a medical plastic parts supplier with strong quality, production, and innovation capabilities ensures a smooth manufacturing process and superior end products. Such a supplier not only delivers high-quality components but also serves as a valuable partner in overcoming industry challenges. This collaboration is critical for healthcare manufacturers aiming to meet the demands of safety, reliability, and cost-efficiency in their medical devices.
Spotlight on Leading Medical Plastic Parts Suppliers
FUJIU Medical Injection Mold: A Leader in Innovation and Quality
At FUJIU Medical Injection Mold, we bring over 20 years of excellence as a third-generation, employee-owned company. Every team member is a stakeholder, fueling our passion for innovation, quality, and collaboration. We specialize in OEM contract manufacturing for the medical device industry, producing high-precision plastic consumables for equipment and diagnostic kits. From initial design to production, we partner with clients using advanced medical injection molding technologies. Equipped with Class 8 clean rooms and adhering to ISO 13485, FDA, and global standards, we ensure the highest quality control. Our unique blend of family values and employee empowerment sets us apart, guaranteeing a sustainable future for our team and clients worldwide.
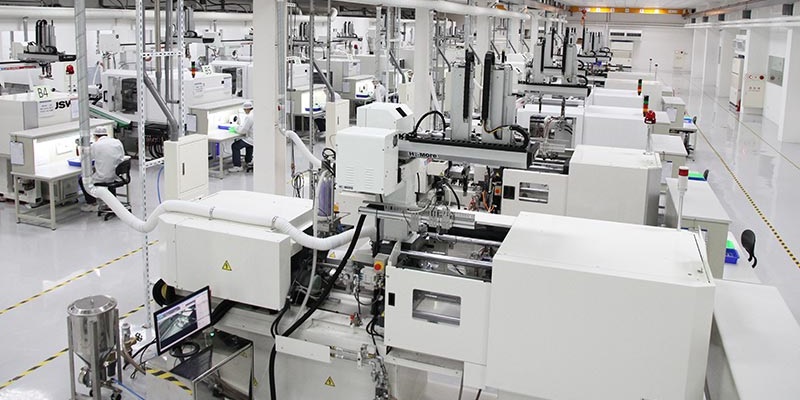
Key Offerings:
- LSR Injection Molding: This technique utilizes liquid silicone rubber, a versatile two-component elastomer that undergoes a curing process to develop its end-use properties. The ability to create high-quality components with outstanding performance characteristics makes LSR injection molding particularly suitable for medical applications.
- Tissue Grinders and Medical Containers: These products are essential for diagnostics and specimen handling, showcasing the company’s expertise in crafting specialized tools for laboratory and clinical use.
- Injection Molding and Cleanroom Production: FUJIU Medical Injection Mold excels in producing components in an ISO-certified cleanroom environment, minimizing contamination risks and ensuring compliance with stringent medical standards.
Innovation and Career Opportunities:
At FUJIU Medical Injection Mold, our mission is to be more than just a manufacturer—we strive to be a trusted partner in your success. Specializing in custom precision medical molds and injection-molded plastic products, we are dedicated to delivering exceptional value and unparalleled service to the medical industry.
Other Notable Medical Plastic Parts Suppliers
Beyond FUJIU Medical Injection Mold, several other medical plastic parts suppliers are making significant contributions to the industry. These companies are renowned for their specialized offerings and commitment to quality.
1. Suppliers of Sterilization-Resistant Plastics:
Companies producing sterilization-resistant plastics cater to the demanding requirements of surgical environments. Their products, capable of withstanding repeated sterilization cycles, are used in devices such as surgical instruments and trays.
2. Diagnostic Component Specialists:
Suppliers focused on diagnostic tools play a crucial role in advancing healthcare technologies. They produce precision-molded parts for imaging systems, blood analyzers, and portable diagnostic devices, ensuring accuracy and reliability in medical assessments.
3. Surgical Tool Manufacturers:
Precision is vital in the development of surgical tools. Suppliers specializing in this area utilize advanced injection molding and cleanroom production techniques to craft lightweight, durable, and sterilizable instruments that enhance surgical efficiency and safety.
The Impact of a Reliable Medical Plastic Parts Supplier
A dependable plastic medical parts suppliers is an essential partner in the healthcare ecosystem. Whether it’s FUJIU Medical Injection Mold with its focus on bone implants and diagnostics or other suppliers delivering sterilization-resistant and precision-engineered tools, these companies drive innovation and ensure the highest standards of quality.
By selecting the right supplier, healthcare organizations can access tailored solutions that meet their unique needs, contributing to improved patient care and operational efficiency in the medical field.
Why Choosing a Reliable Medical Plastic Parts Supplier Matters
The Critical Role of a Medical Plastic Parts Supplier in Healthcare Outcomes
A dependable medical plastic parts supplier is integral to achieving superior healthcare outcomes. The precision and quality of plastic components directly impact the safety, effectiveness, and reliability of medical devices. Whether it’s a diagnostic tool, surgical instrument, or bone implant, ensuring these devices perform as intended can make a life-saving difference.
1. Ensuring Precision and Safety
High-quality suppliers leverage advanced manufacturing technologies like injection molding and micro-fabrication to create components with exact tolerances. This level of precision is critical in medical devices where even the smallest error can compromise patient safety. Additionally, reliable suppliers ensure that all materials used are biocompatible and meet stringent medical standards, reducing the risk of adverse reactions or device failures.
2. Minimizing Contamination Risks
Cleanroom manufacturing is a hallmark of a trusted plastic injection molding medical parts supplier. By adhering to ISO Class 7 or Class 8 cleanroom standards, suppliers minimize contamination risks during production. This is particularly important for devices used in sterile environments, such as catheters or surgical implants. The use of sterilization-resistant plastics further ensures that these devices maintain their integrity through repeated cleaning cycles.
The Importance of Collaboration with a Medical Plastic Parts Supplier
The relationship between healthcare manufacturers and a medical plastic parts supplier goes beyond transactional. It is a collaborative partnership that drives innovation and problem-solving for unique medical challenges.
1. Tailored Solutions for Specific Applications
Every medical application comes with its own set of challenges, from regulatory requirements to functional demands. Reliable suppliers work closely with manufacturers to design and produce components that meet these specific needs. For example:
- Custom materials: Suppliers can recommend and source specialized plastics, such as PEEK or PPSU, for applications requiring high heat resistance or biocompatibility.
- Functional enhancements: Collaborating with suppliers allows manufacturers to incorporate features like improved durability, flexibility, or sterilizability into their designs.
2. Support for Design and Development
A dependable medical plastic parts supplier contributes expertise during the design and prototyping stages. Advanced technologies such as Moldflow simulation and 3D printing allow for iterative testing and refinement, ensuring the final product meets both regulatory and performance standards. This collaboration accelerates time-to-market while minimizing costly revisions.
Why It Matters: Long-Term Impact on Healthcare
The influence of a reliable medical plastic parts supplier extends far beyond production. These suppliers play a pivotal role in enhancing patient safety, reducing healthcare costs, and fostering innovation. Manufacturers who partner with trusted suppliers gain access to high-quality components that elevate their devices and ensure compliance with global standards.
Investing in such a partnership not only benefits healthcare organizations but also contributes to better patient outcomes and a more efficient healthcare system. A collaborative approach ensures that suppliers and manufacturers work hand-in-hand to meet the ever-evolving demands of the medical industry.
Opportunities in the Medical Plastics Industry
Expanding Career Horizons with a Medical Plastic Parts Supplier
The medical plastics industry is growing at an unprecedented pace, driven by advancements in healthcare and the increasing demand for innovative medical devices. A career with a medical plastic parts supplier presents numerous opportunities for skilled professionals to contribute to life-saving technologies while advancing their own professional development.
Growing Demand for Skilled Professionals
As the medical plastics industry continues to evolve, there is an increasing need for talent across a variety of roles. Suppliers are investing in their workforce to meet the complex demands of healthcare innovation, creating exciting career opportunities for professionals in areas such as:
- Design and Development: Specialists who can conceptualize and refine components that meet both functional and regulatory requirements are in high demand. Roles in CAD design, prototyping, and simulation modeling are critical for developing medical precision parts.
- Engineering and Manufacturing: Engineers and technicians play a key role in implementing advanced manufacturing techniques such as injection molding, micro-fabrication, and cleanroom production. Their expertise ensures the consistent quality and efficiency of production processes.
- Quality Assurance: Ensuring compliance with strict medical standards, quality assurance professionals safeguard the safety and reliability of products. These roles require attention to detail and knowledge of industry certifications such as ISO 13485:2016.
This growing demand highlights the critical role of a medical plastic parts supplier in fostering talent to meet industry challenges.
How Leading Suppliers Like FUJIU Medical Injection Mold Drive Workforce Development
Suppliers such as FUJIU Medical Injection Mold lead the way in creating a dynamic and innovative work environment. By focusing on workforce development, FUJIU Medical Injection Mold enables employees to thrive while contributing to groundbreaking medical solutions.
1. Training and Development Programs
Leading suppliers invest in robust training programs to equip their employees with the latest skills in medical plastics manufacturing. From mastering advanced tools like 3D printing to understanding cleanroom protocols, these programs empower workers to excel in their roles.
2. Collaborative Innovation
Employees are encouraged to collaborate across disciplines, driving innovation in product design and manufacturing. FUJIU Medical Injection Mold fosters a culture of creativity where team members contribute to solving complex healthcare challenges through tailored solutions.
3. Career Progression Opportunities
Suppliers like FUJIU Medical Injection Mold offer clear pathways for career advancement. Employees can progress from entry-level roles to leadership positions, supported by ongoing mentorship and professional development initiatives.
Examples of Career Paths in the Industry
The medical plastics industry offers diverse and rewarding career opportunities. Below are some examples of roles available with a medical plastic parts supplier:
- Product Development Engineer: Focuses on designing new components and improving existing ones using cutting-edge technologies.
- Manufacturing Technician: Operates advanced machinery in cleanroom environments to produce high-quality medical plastic parts.
- Quality Control Specialist: Ensures products meet stringent healthcare standards through rigorous testing and certification processes.
- Supply Chain Manager: Manages procurement and logistics to ensure timely delivery of raw materials and finished products.
- Regulatory Compliance Officer: Ensures all manufacturing processes adhere to local and international medical regulations.
The Future of Careers with a Medical Plastic Parts Supplier
The medical plastics industry is not just about creating components; it is about shaping the future of healthcare. A career with a medical plastic parts supplier offers individuals the chance to contribute to life-changing innovations while developing skills that will remain in demand for years to come.
By joining injection molding medical industry leaders like FUJIU Medical Injection Mold, professionals can become part of a dynamic workforce that is revolutionizing healthcare through precision, quality, and innovation. For those looking to make a meaningful impact, the medical plastics industry is a field filled with opportunity and promise.
The Role of Wholesale Medical Plastic Parts Suppliers in Healthcare
Wholesale Medical Plastic Parts Suppliers: A Critical Link in the Supply Chain
Wholesale medical plastic parts suppliers are indispensable to the healthcare industry, providing a steady supply of essential components that power medical devices and tools. These suppliers act as a bridge between manufacturers and end-users, ensuring that large-scale production needs are met efficiently without compromising quality. Their role in the supply chain ensures that hospitals, laboratories, and healthcare facilities have access to reliable medical device components.
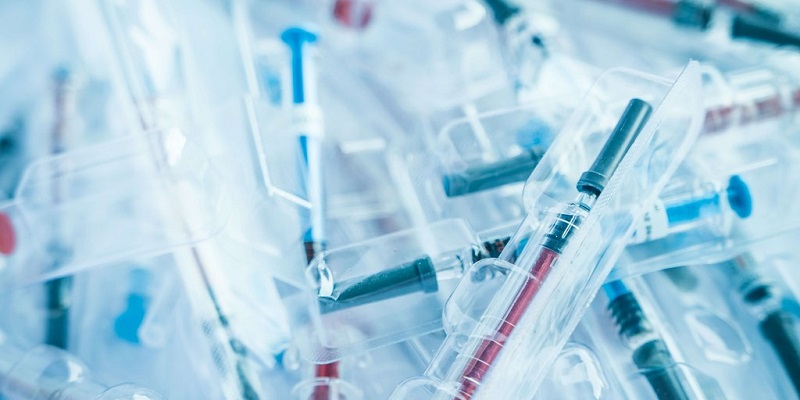
Key Contributions of Wholesale Suppliers
- Scalability:
Wholesale suppliers are equipped to handle large-volume orders, making them ideal partners for manufacturers that produce medical devices on a mass scale. Their ability to deliver bulk quantities ensures consistency in production, allowing manufacturers to meet the growing demands of the healthcare sector. This scalability is achieved by collaborating closely with a medical plastic parts supplier, ensuring a seamless flow of high-quality components. - Cost Efficiency:
By sourcing and distributing medical plastic parts in bulk, wholesale suppliers significantly reduce the per-unit cost of components. This cost efficiency benefits manufacturers, enabling them to produce affordable medical devices without compromising on quality. End-users, such as healthcare providers, also benefit from reduced costs, which ultimately improve patient access to advanced medical solutions. - Compliance Assurance:
Compliance with strict healthcare regulations is a critical requirement in the medical plastics industry. Wholesale medical plastic parts suppliers partner with a medical plastic parts supplier network to ensure all components meet international standards like ISO 13485:2016. This commitment to compliance guarantees that the supplied parts are safe, reliable, and suitable for use in life-saving medical applications.
Impact on Healthcare Innovation
Wholesale medical plastic parts suppliers play a vital role in enabling innovation in medical device manufacturing. By providing timely access to a variety of materials, including sterilization-resistant plastics and biocompatible components, these suppliers help manufacturers design and produce advanced medical technologies. This collaboration fosters a healthcare ecosystem that prioritizes patient safety, device reliability, and cost-effectiveness.
Wholesale medical plastic parts suppliers are not just providers of bulk components; they are strategic partners in driving efficiency, affordability, and innovation in the healthcare industry. Through their close collaboration with a medical plastic parts supplier, they ensure that the industry continues to deliver groundbreaking solutions that improve lives worldwide.
How to Choose the Right Medical Plastic Parts Supplier for Your Needs
How Plastic Medical Equipment Components Suppliers Support Advanced Healthcare
Plastic medical equipment components suppliers play a pivotal role in the healthcare industry by delivering high-quality, precision-engineered parts essential for medical devices. Their expertise ensures that every component, whether used in diagnostic equipment, surgical tools, or life-support machines, meets the highest standards of safety and performance.
By collaborating with a medical plastic parts supplier network, these suppliers bridge the gap between raw material providers and device manufacturers, ensuring that the end product is both functional and compliant with healthcare regulations. Their contributions directly influence the effectiveness of medical devices and the outcomes they provide for patients.
Key Features of Reliable Suppliers
1. Expertise in Precision Engineering
Reliable suppliers excel in producing components that meet the exact specifications required for flawless performance. From intricate parts in ventilators to durable housings for diagnostic machines, their engineering capabilities ensure every component is consistent, reliable, and ready for real-world use. By partnering with a medical plastic parts supplier, these suppliers gain access to specialized materials that further enhance product quality.
2. Collaboration with Manufacturers
Trusted plastic medical equipment components suppliers work closely with manufacturers to understand their specific needs and challenges. This collaboration often extends to co-developing tailored solutions for complex applications. By leveraging their network of medical plastic parts supplier partnerships, they can source specialized plastics, such as biocompatible or sterilization-resistant materials, and incorporate them into highly customized components.
3. Focus on Innovation
Leading suppliers stay ahead of the curve by adopting advanced technologies like 3D printing, which enables rapid prototyping of new designs, and Moldflow simulation, which optimizes the manufacturing process. These technologies ensure that components are produced efficiently and to the exact specifications required for cutting-edge medical devices. Their innovation helps manufacturers stay competitive and respond quickly to changing industry demands.
The Importance of Selecting the Right Supplier
Choosing a reliable plastic medical equipment components supplier is critical for manufacturers seeking to produce high-performing medical devices. A dependable supplier ensures that components meet all technical, regulatory, and functional requirements while maintaining cost-efficiency and scalability. Their collaboration with a medical plastic parts supplier network ensures access to top-quality materials and manufacturing expertise, which directly impacts the safety and reliability of the final device.
Selecting the right supplier not only enhances device quality but also strengthens the entire supply chain, supporting the healthcare industry’s mission to deliver life-saving solutions. Reliable suppliers are more than just providers; they are partners in innovation, driving advancements that improve patient care and support global health initiatives.
Essential Standards for Medical Plastic Parts Suppliers in Injection Molding
Medical plastic parts suppliers in the injection molding industry must adhere to stringent standards to ensure the safety, reliability, and quality of their products. Here are the key standards:
ISO 13485 – Quality Management Systems for Medical Devices
This international standard specifies the requirements for a quality management system specific to medical devices. Suppliers must demonstrate their ability to consistently meet regulatory and customer requirements, focusing on risk management, traceability, and documentation throughout the production process.
ISO 10993 – Biocompatibility Testing
This set of standards ensures that medical-grade materials used in injection molding are safe for contact with human tissues or bodily fluids. Suppliers must perform cytotoxicity, sensitization, and irritation tests to confirm material safety.
FDA Compliance
For products distributed in the U.S., suppliers must meet FDA standards. This includes registering as a medical device manufacturer and ensuring compliance with 21 CFR Part 820, which outlines the quality system regulations for medical devices.
USP Class VI Certification
This certification ensures that the plastics used in medical devices meet stringent biocompatibility requirements. Testing includes toxicity, systemic injection, and implantation studies.
ISO 14644 – Cleanroom Standards
Medical injection molding often requires manufacturing in controlled environments. ISO 14644 sets standards for cleanroom classifications, ensuring minimal contamination during production.
Sterilization Compatibility Standards
Suppliers must ensure their products are compatible with common sterilization methods such as autoclaving, ethylene oxide (EtO), and gamma radiation. This is crucial for maintaining product integrity and safety.
EU MDR and CE Marking (For European Markets)
Suppliers catering to the European market must comply with the European Medical Device Regulation (EU MDR) and obtain CE marking to demonstrate conformity with health and safety requirements.
ISO 9001 – General Quality Management Systems
Although not specific to medical devices, ISO 9001 is often a baseline for ensuring consistent production quality and continuous improvement in processes.
Environmental Standards
Regulations like RoHS and REACH ensure that materials used are free of hazardous substances and comply with environmental safety guidelines.
By adhering to these rigorous standards, medical plastic parts suppliers ensure their products are safe, compliant, and suitable for use in the healthcare industry.
Challenges and Solutions for Medical Plastic Parts Suppliers
Strict Regulatory Compliance
- Challenge: Suppliers must meet stringent standards like ISO 13485, FDA regulations, and biocompatibility tests, which demand significant time and resources.
- Solution: Invest in robust quality management systems, maintain proper documentation, and undergo regular audits to ensure compliance with healthcare regulations.
Material Selection and Availability
- Challenge: Medical-grade materials must be safe, durable, and compatible with sterilization processes. Supply chain disruptions can hinder access to these materials.
- Solution: Establish partnerships with reliable material distributors, maintain a diversified inventory, and implement a proactive supply chain management strategy.
Rising Production Costs
- Challenge: Advanced technologies, skilled labor, and raw materials contribute to high manufacturing costs.
- Solution: Optimize processes using automation, energy-efficient equipment, and lean manufacturing techniques to reduce overheads and improve efficiency.
Technological Advancements
- Challenge: Keeping pace with innovations like micro-molding, bioresorbable materials, and complex geometries can be overwhelming.
- Solution: Invest in R&D, provide ongoing training for staff, and collaborate with experts to integrate advanced technologies into production.
Customization Demands
- Challenge: Clients often require highly specialized designs, increasing complexity and development time.
- Solution: Develop flexible manufacturing processes and leverage CAD/CAM systems to quickly adapt to custom specifications while maintaining high quality.
Global Competition
- Challenge: Competing with low-cost suppliers from other regions while maintaining quality and delivery timelines.
- Solution: Focus on superior quality, faster lead times, and value-added services such as design consulting and post-production support to stand out.
Environmental Concerns
- Challenge: Increasing demand for sustainable manufacturing and the reduction of plastic waste.
- Solution: Use recyclable and bio-based polymers, implement waste reduction programs, and promote sustainability certifications to meet eco-friendly standards.
By addressing these challenges with proactive strategies, medical plastic parts suppliers can thrive in a competitive and highly regulated industry.
FAQs about Medical Plastic Parts Supplier
Medical devices use a variety of plastics tailored for their unique properties and compliance with strict healthcare standards. Common types include:
Polycarbonate (PC): Known for its strength, transparency, and sterilization resistance, it is used in components like syringes, blood oxygenators, and IV connectors.
Polypropylene (PP): Highly durable and steam-sterilization resistant, ideal for reusable medical tools and lab equipment.
Polyethylene (PE): Lightweight and chemically resistant, commonly found in tubing and containers.
Polyvinyl Chloride (PVC): Widely used for flexible applications such as catheters, IV bags, and tubing.
Polysulfone (PSU) and Polyetherimide (PEI): High-temperature plastics used in surgical instruments and diagnostic devices.
These materials are biocompatible, sterilizable, and tailored to meet the safety and performance standards of medical-grade plastics. Selecting the right plastic depends on the device’s intended use, sterilization method, and mechanical or chemical resistance requirements.
Medical implants demand advanced plastics that offer biocompatibility, mechanical strength, and long-term stability. Common plastics used include:
PEEK (Polyether Ether Ketone): Often used for spinal implants, bone plates, and dental implants due to its excellent biocompatibility, sterilization resistance, and mechanical properties.
UHMWPE (Ultra-High-Molecular-Weight Polyethylene): Preferred for joint replacements like knees and hips because of its wear resistance and durability.
Silicone Elastomers: Used for soft implants like breast implants and pacemaker leads, offering flexibility and biocompatibility.
PMMA (Polymethyl Methacrylate): Known for its optical clarity, it is often used in intraocular lenses and cranial implants.
These plastics are designed to remain stable within the body over time, ensuring patient safety and device functionality. The choice of material depends on the implant’s purpose and the specific physiological environment in which it will be used.
FUJIU Medical Injection Mold is headquartered in China, where it operates as a leading manufacturer specializing in precision medical injection molding. The company is located in a strategic industrial hub, providing easy access to global supply chains and advanced technology. FUJIU’s headquarters serves as the center for its research and development (R&D), production, and quality control processes. With a state-of-the-art facility, the company ensures high standards in the production of medical-grade injection-molded components, such as syringes, IV connectors, and diagnostic equipment. FUJIU’s location also supports its international expansion and ability to serve clients across North America, Europe, and other regions. The company prides itself on offering both high-quality products and reliable customer service, which has contributed to its reputation in the medical manufacturing industry.
The market for medical injection molding is vast and growing rapidly, driven by the increasing demand for high-quality medical devices, healthcare products, and equipment. Injection molding is used to produce a wide variety of components, from surgical instruments to diagnostic devices, drug delivery systems, and medical packaging. The medical injection molding market is primarily influenced by advancements in healthcare technologies, an aging global population, and a rising emphasis on precision and sterilization in medical device production. Key sectors within the medical injection molding market include pharmaceuticals, biotechnology, diagnostics, and surgical tools. Furthermore, regulatory requirements for medical devices are strict, which makes medical injection molding particularly valuable for ensuring compliance with safety and quality standards. With the rising focus on cost-effective manufacturing solutions, medical injection molding offers an efficient way to produce large volumes of complex parts while maintaining high precision. The market is expected to continue its upward trajectory as innovations in medical technology and materials evolve.
Medical-grade plastics like polycarbonate (PC), polypropylene (PP), polyethylene (PE), and polyetheretherketone (PEEK) are widely used due to their durability, biocompatibility, and sterilization capabilities. Among these, polycarbonate is a top choice for its strength and transparency, making it ideal for surgical instruments, oxygen masks, and housings for medical devices. Polypropylene is often used for disposable syringes and containers due to its resistance to chemicals and high temperatures. PEEK, on the other hand, is highly favored in implants and orthopedic devices for its unmatched combination of mechanical strength and biocompatibility. The “best” plastic often depends on the intended application, the sterilization method, and regulatory requirements. Medical plastic part suppliers work closely with manufacturers to identify and provide the most suitable material for a specific application, ensuring compliance with medical standards while optimizing performance.
Medical-grade plastics are specialized polymers certified for use in healthcare applications. These materials include polycarbonate, polypropylene, polyethylene, polyetheretherketone (PEEK), and medical-grade polyvinyl chloride (PVC). They undergo rigorous testing to meet biocompatibility standards outlined by regulatory agencies like the FDA and ISO 10993. These certifications ensure that the plastics are non-toxic, hypoallergenic, and safe for prolonged contact with human tissue or fluids. Often referred to as “medical polymers” or “biomedical plastics,” they are engineered to withstand sterilization processes like autoclaving, ethylene oxide (EtO) gas, and gamma radiation. Suppliers of medical-grade plastics play a vital role in ensuring that manufacturers have access to certified, high-quality materials that meet the stringent demands of the healthcare industry.
Plastic is a cornerstone material for many medical supplies due to its versatility, cost-efficiency, and sterilization capabilities. Common medical products made from plastics include syringes, IV bags, catheters, surgical gloves, and blood collection tubes. Polypropylene is used in disposable syringes and medication vials, while polycarbonate finds applications in surgical instruments and diagnostic devices. High-density polyethylene (HDPE) is often used in tubing and containers for pharmaceuticals. Flexible PVC is a popular choice for IV bags and oxygen masks due to its softness and durability. Medical plastic part suppliers provide precision-engineered components for high-tech applications like implants, prosthetics, and diagnostic equipment housings. These plastic supplies are critical in ensuring patient safety, efficiency in healthcare delivery, and compliance with rigorous medical standards.
Starting a medical supply business involves several steps. Begin by conducting market research to identify demand and competition in your target area. Develop a comprehensive business plan outlining your niche, product offerings, and pricing strategy. Obtain the necessary licenses and certifications, including FDA registration for distributing medical-grade materials or devices. Establish partnerships with reliable suppliers specializing in medical-grade plastics and other materials. Invest in an inventory management system and create a secure e-commerce platform or storefront for distribution. Compliance with healthcare regulations and maintaining a robust quality assurance system is essential. Networking with healthcare providers and attending industry trade shows can help build your client base. Strong relationships with medical plastic part suppliers ensure that you have consistent access to high-quality products, setting a solid foundation for long-term success.
Medical-grade polymers are non-toxic and specifically designed for safe use in healthcare settings. They undergo stringent biocompatibility testing to ensure they do not cause adverse reactions when in contact with human tissues or fluids. Regulatory standards, such as ISO 10993 and FDA guidelines, assess these plastics for cytotoxicity, sensitization, and irritation. Materials like polypropylene, polycarbonate, and polyethylene are commonly used due to their safety and durability. For applications like implants, biocompatible materials like PEEK are preferred for their long-term stability and non-toxic nature. It’s important to source these polymers from certified medical plastic part suppliers to guarantee compliance with regulatory requirements. Proper sterilization and quality control further ensure the safety of these materials in healthcare applications.
The highest quality plastic for medical applications depends on the intended use. Polyetheretherketone (PEEK) is often considered one of the highest-quality plastics due to its exceptional mechanical strength, chemical resistance, and biocompatibility. It is frequently used in implants and prosthetics. Polycarbonate is another high-grade plastic valued for its transparency, impact resistance, and sterilization capabilities, making it suitable for diagnostic devices and surgical instruments. Medical-grade silicone, though technically an elastomer, is also regarded as high-quality for its flexibility and hypoallergenic properties in devices like catheters and seals. When selecting high-quality plastics, partnering with a reputable medical plastic part supplier ensures consistent access to materials that meet stringent healthcare industry standards.
Contact our professional team now for a same-day quote and risk-free project evaluation. Benefit from ISO 8 cleanrooms, advanced machines, and 12-hour fast response in medical injection molding.