Multi component injection molding medical technology combines two or more materials or colors into a single molded part during one production cycle. This advanced process is ideal for creating complex, high-quality components with unmatched precision, versatility, and efficiency. In the medical industry, multi component injection molding medical applications are transforming the manufacturing landscape. The technology addresses critical demands for biocompatible, durable, and high-performance medical devices. From catheters and implants to surgical tools and diagnostic equipment, this process enables the production of intricate designs with superior material properties. By integrating multiple materials, manufacturers achieve enhanced functionality, reduced assembly steps, and significant cost savings, making multi component injection molding medical essential for modern healthcare innovations. Its ability to meet stringent regulatory standards further highlights its growing importance in medical device production. Multi-component injection molding medical combines multiple materials or colors into one part, optimizing design, function, and performance for medical devices.
Low-Volume to High-Volume Production Capabilities
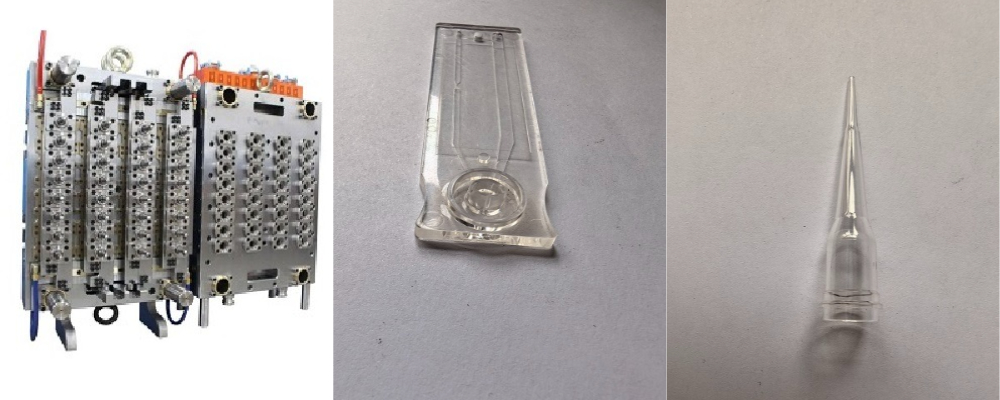
Attributes | Details |
---|---|
Place of Origin | Dongguan, Guangdong, China |
Brand Name | LY Medical Injection Mold |
Product Name | Medical Injection Mold |
Plastic Processing | Polypropylene, ABS, Polyvinyl Chloride, Polyethylene |
Process | Injection Molding |
Size | Customized Size |
Color | Customized Color |
Mold | Customizable |
Shape | Customized Shapes |
Certification | ISO9001 |
Tolerance | 0.02mm-0.05mm |
Drawing Format | STEP/STP/IGS/XT/STL/CAD/PDF/DWG and Others |
Mold Life | 500000 shots |
Service | OEM |
Workshop | ISO13485 cleanroom |
Operation Language | English/Chinese or Others |
Sales Unit | Single Item |
Multi Component Injection Molding Medical Technology
Multi component injection molding medical technology provides highly advanced solutions for the production of precision medical devices. By combining multiple materials or colors in a single production cycle, this process enhances the functionality and performance of medical components, which is especially important in the healthcare sector where reliability and quality are critical.
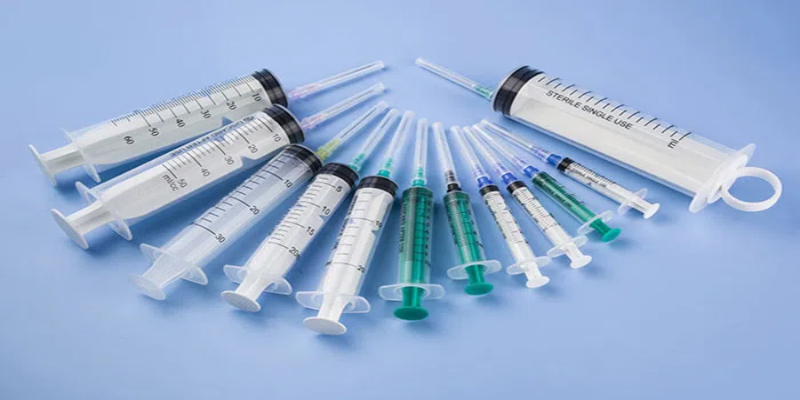
Key Features of the Technology
The multi component injection molding medical process offers tailored solutions for medical applications using high-performance machines. These machines are designed for versatile configurations, allowing manufacturers to produce both single-use and reusable medical devices. The ability to combine multiple materials in one cycle reduces production time, lowers costs, and ensures high accuracy and repeatability, making it an ideal choice for mass production of medical devices.
Processes Used
Several advanced processes are employed in multi component injection molding medical to improve the functionality and versatility of the final product:
- Core Back and Turning Mold Technology: This technique creates multi-material layers within a part, providing strength and functionality where needed. It allows the incorporation of different materials for the outer and inner layers of the product, improving overall performance, especially for medical components that require durability and biocompatibility.
- Sandwich and Interval Injection Molding: By injecting materials in specific intervals, this process creates parts with enhanced material properties in one step. This is ideal for products requiring layered materials, such as medical implants, which may need a hard core for strength and a softer outer layer for comfort or flexibility.
- Overmolding for Ergonomics: This process involves adding a softer material layer over a hard substrate. It is commonly used for creating ergonomic medical devices, such as surgical tools or handles, ensuring comfort while maintaining strength and precision.
Materials Commonly Used
A variety of specialized materials are used in multi component injection molding medical to ensure the final product meets medical standards:
- Polyetheretherketone (PEEK): Known for its strength, chemical resistance, and biocompatibility, PEEK is often used in implants and surgical tools.
- Polycarbonate (PC): A transparent, tough material that is used in medical devices that require clarity, such as diagnostic equipment and protective covers.
- Silicone: Highly flexible and compatible with biological tissues, silicone is widely used in catheters, tubing, and other medical applications where flexibility is key.
- Polypropylene (PP): Durable and resistant to various stresses, polypropylene is commonly used in medical packaging, syringes, and joint replacements.
These materials, combined with multi component injection molding medical technology, enable the production of complex, high-quality medical devices that meet the strict standards of the healthcare industry.
Benefits of Multi Component Injection Molding Medical Applications
The multi component injection molding medical technology offers a range of advantages that are crucial for the production of high-quality, durable medical devices. These benefits include precision, cost-effectiveness, high-volume reproducibility, and the ability to customize products to meet the complex demands of the medical industry.
Precision and Accuracy
One of the standout benefits of multi component injection molding medical is its ability to produce medical devices with exceptional precision and accuracy. Medical components, especially those used in critical applications such as implants or surgical tools, require tight tolerances to ensure proper function and safety. This technology guarantees that the final product meets the stringent dimensional and functional requirements necessary in medical applications. It is ideal for devices where small tolerances can significantly impact the performance and safety, such as catheters, syringes, and diagnostic equipment.
Cost-Effectiveness
The multi component injection molding medical process also delivers substantial cost savings. By combining multiple steps, such as material insertion and molding, into a single cycle, manufacturers can significantly reduce labor costs, minimize material waste, and streamline production time. This process eliminates the need for separate assembly or secondary operations, making it more efficient than traditional molding methods. Additionally, the ability to use multiple materials in one shot reduces the cost of material handling and transportation, further lowering overall manufacturing expenses.
High-Volume Reproducibility
Another significant advantage of multi component injection molding medical is its capacity for high-volume reproducibility. Once the production process is set up, it can produce thousands of identical medical components with minimal variation. This is particularly important in the medical industry, where consistency and uniformity are essential. Whether it’s for mass-produced medical supplies like syringes or for more specialized devices such as diagnostic tools or implants, this technology ensures that each part meets the same high-quality standards.
Customizability
The multi component injection molding medical process allows for exceptional customizability. This flexibility supports the creation of complex geometries, multiple material layers, and ergonomic designs. For instance, medical devices such as surgical instruments, ergonomic handles, and implants can be tailored to fit specific design needs, including incorporating soft-touch surfaces for better grip or creating multi-functional components with varying material properties. The ability to combine different materials with unique properties in a single part opens up possibilities for creating more advanced, patient-friendly, and functional medical devices.
Leading Suppliers and Machines in Multi Component Injection Molding Medical
The multi component injection molding medical industry is driven by a select group of suppliers and advanced machines designed to produce high-quality, precise, and cost-effective medical devices.
How to Choose a Supplier for Multi-Component Injection Molding Medical
Selecting the right supplier for multi-component injection molding in the medical industry is a critical decision that directly impacts product quality, regulatory compliance, and manufacturing efficiency. This decision should be made with careful consideration of several factors such as experience in medical manufacturing, technological capabilities, regulatory expertise, and cost efficiency. A qualified supplier should have a deep understanding of medical-grade materials, cleanroom environments, and the complexities of multi-component molding. Below are several key aspects to consider when choosing a supplier for multi-component injection molding medical.
Experience and Expertise in Medical Manufacturing
When choosing a supplier for multi-component injection molding medical, one of the most important factors is their experience in the medical field. Suppliers with experience in medical device manufacturing understand the stringent regulatory requirements, high-quality standards, and precision necessary for medical components. Look for suppliers that specialize in medical-grade injection molding, particularly those familiar with the challenges of multi-component processes, which often involve combining multiple materials or colors in a single product. Experience in working with the FDA and ISO 13485 certifications ensures that the supplier can meet the specific standards required for medical devices.
Technological Capabilities
Another critical consideration is the supplier’s technological capabilities. Multi-component injection molding requires advanced equipment and specialized machinery to inject different materials into molds either simultaneously or sequentially. Suppliers should have the necessary tooling, machines, and automated systems to handle the complexities of medical multi-component molding. Verify that the supplier’s machines can accommodate the material properties required for medical-grade devices, whether they involve high-performance thermoplastics, elastomers, or biocompatible materials. Additionally, check if they employ up-to-date technology for precision, mold design, and process optimization, which are crucial in producing high-quality medical parts.
Regulatory Compliance and Certifications
In the medical industry, compliance with regulatory standards is non-negotiable. A reliable supplier for multi-component injection molding medical should have the appropriate certifications such as ISO 13485 (for medical device quality management systems) and adherence to FDA regulations. These certifications indicate that the supplier is capable of manufacturing medical components that meet safety, quality, and performance standards. Suppliers who prioritize regulatory compliance will also have the necessary documentation, validation procedures, and testing protocols to ensure that every part produced is safe, sterile, and meets medical standards.
Manufacturing Capabilities and Production Volume
The ability to handle both small and large production runs is another key factor in choosing a supplier for multi-component injection molding. Some medical devices may require small, custom batches for specialized applications, while others may need large-scale production for widespread distribution. The supplier should be flexible enough to manage varying production volumes efficiently, ensuring high-quality output with consistent results. A good supplier will also have experience with low-to-high-volume production, helping to scale up or down based on your business needs, without compromising on quality or lead times.
Material Expertise and Innovation
Multi-component injection molding medical often involves the use of a variety of materials, including bio-compatible, sterilizable, and high-performance plastics. Choosing a supplier with material expertise is essential to ensure the correct selection of materials for specific medical applications. The supplier should be able to recommend materials with the right physical properties, such as strength, flexibility, and biocompatibility, that meet the demands of your medical device. Suppliers with a strong track record in material innovation can help you stay ahead in the market by offering new material solutions, whether it’s for enhancing device performance or improving cost-efficiency.
Quality Control and Testing Procedures
In the medical field, quality control is paramount. A good supplier for multi-component injection molding should have robust quality assurance processes in place, including detailed testing procedures throughout the manufacturing cycle. Look for suppliers that conduct stringent in-process inspections, material testing, and post-production validation. Testing methods, including functional testing, sterilization compatibility, and durability testing, should be part of their process to ensure that the parts meet medical standards. Additionally, ask about the supplier’s traceability and documentation practices, as these are essential for ensuring that products are consistently produced to the required specifications.
Cost and Lead Time Efficiency
While quality should be the primary focus, cost and lead time efficiency are also important factors in selecting a supplier for multi-component injection molding medical. A reputable supplier should offer competitive pricing while still ensuring that all quality and regulatory standards are met. Request detailed quotes that include material, tooling, and production costs, and assess how well the supplier can meet your required timelines. Look for suppliers that can streamline their processes to reduce lead times without sacrificing quality or compliance. An efficient supplier will help you reduce overhead costs and improve your time-to-market.
Customer Support and Communication
Effective communication and customer support play a significant role in a supplier relationship. Choosing a supplier who is responsive, transparent, and proactive in addressing any concerns or questions can greatly enhance your experience. A supplier that understands the importance of clear communication will provide timely updates on production progress, testing results, and any challenges encountered. Moreover, suppliers who offer technical support and consultation can provide valuable insights during product development, ensuring that your multi-component injection molding medical projects proceed smoothly from start to finish.
Choosing a supplier for multi-component injection molding medical involves evaluating their expertise in medical manufacturing, technological capabilities, regulatory compliance, material knowledge, and production flexibility. By considering these aspects and ensuring alignment with your needs, you can select a supplier that will deliver high-quality, compliant, and efficient solutions for your medical device manufacturing requirements.
FUJIU Medical Injection Mold
FUJIU Medical Injection Mold is a leading player in the multi component injection molding medical sector, with a strong focus on high-performance materials. Our company is known for its expertise in manufacturing precision medical components from specialized thermoplastics. FUJIU Medical Injection Mold’s materials are engineered to meet the strict biocompatibility and durability requirements of medical applications.
- High-Performance Plastics: FUJIU Medical Injection Mold offers a broad range of engineering plastics such as PEEK (Polyetheretherketone), which is widely used for medical implants, as well as other materials like PEI and PBT. These materials are specifically chosen for their resistance to heat, chemicals, and wear, which is essential for the long-term performance of medical devices. FUJIU’s precision mold medical services ensure that these materials are utilized to their fullest potential, creating durable and reliable components for the medical industry.
- Customized Solutions: FUJIU Medical Injection Mold also provides tailored solutions for suppliers requiring high-quality, precision medical components. Our company’s injection medical molding services are ideal for applications that demand excellent mechanical properties and biocompatibility, such as surgical instruments, joint replacements, and diagnostic equipment.
Other Notable Players
- Medical Injection Molding Companies: Various specialized medical molding companies focus on niche markets, such as catheter production, implant molding, or diagnostic tool manufacturing. These companies often work with leading OEMs (original equipment suppliers) to provide custom, high-quality medical molding solutions that meet stringent regulatory standards.
- Technological Innovations: Many of these companies are incorporating automation, digitalization, and advanced control systems into their molding processes, making it easier to optimize production and reduce errors. Automation in multi-component injection molding helps minimize human error, speed up production times, and ensure consistent quality across high volumes of medical parts.
Applications of Multi Component Injection Molding Medical
Multi component injection molding medical technology has revolutionized the production of medical devices by enabling the creation of complex parts that combine different materials or colors in a single production cycle. This innovative process enhances the functionality, durability, and precision of medical devices, addressing the diverse needs of healthcare professionals and patients. From diagnostic tools to advanced surgical equipment, multi-component injection molding is integral to various medical applications.
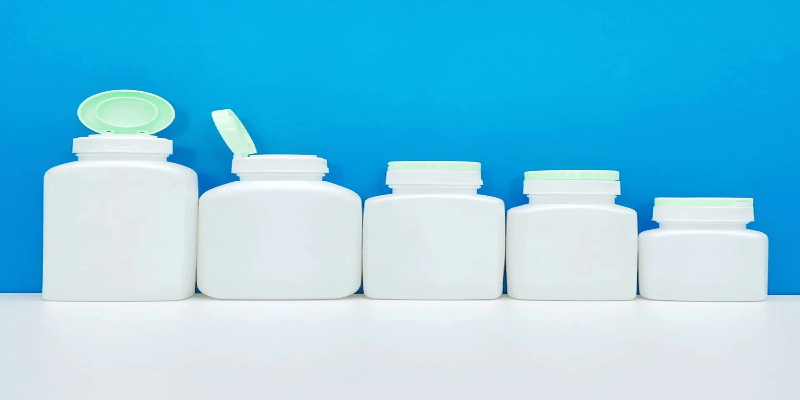
Diagnostic Equipment
One of the key applications of multi component injection molding medical is in the manufacturing of diagnostic equipment. Devices like petri dishes, test tubes, and syringes benefit from the ability to integrate multiple materials into a single part. For instance, a syringe could have a hard outer casing made of polypropylene for structural integrity, while the internal components, such as seals or gaskets, can be made from a softer, more flexible material like silicone to ensure a secure, leak-free seal.
Additionally, blood bags often utilize multi-material injection molding to combine materials that offer both flexibility and durability. The inner layer might be composed of a material that maintains the sterility and safety of the contents, while the outer layer could be made from a stronger, more resilient material to withstand transport and storage conditions. This combination of materials enhances both performance and safety for patients, making multi component injection molding medical a crucial technology for producing high-quality diagnostic tools.
Implants and Prosthetics
Multi component injection molding medical is also widely used in the production of implants and prosthetics, where precision and biocompatibility are paramount. For example, joint replacements often use PEEK (Polyetheretherketone), a high-performance thermoplastic known for its strength, durability, and biocompatibility. In combination with silicone or other soft materials, manufacturers can produce multi-component parts that mimic the natural movement of joints while providing the necessary mechanical strength for long-term use.
These materials are carefully selected to meet the specific needs of the medical application. PEEK is frequently used in spinal implants, while silicone is employed in applications such as breast implants, ensuring that each material performs optimally based on its intended function. By utilizing multi component injection molding medical, manufacturers can produce complex, highly customized implants and prosthetics that meet stringent medical standards, improving patient outcomes and enhancing comfort.
Surgical Tools
Surgical tools are another key area where multi component injection molding medical technology shines. Many surgical instruments require the integration of both hard and soft materials to ensure ease of use, comfort, and safety. For example, ergonomic handles are often overmolded with soft, rubber-like materials to improve grip and reduce fatigue during long surgical procedures. The inner structure of these tools may be made from more rigid materials like stainless steel or high-performance plastics, providing the necessary strength and durability.
The multi-material molding process allows for the creation of tools with multiple layers, each serving a distinct purpose. The hard, durable components ensure the longevity of the tool, while the soft, ergonomic parts improve the user experience. With multi component injection molding medical, manufacturers can design surgical tools that are both functional and comfortable, contributing to better surgical outcomes.
Wearable Medical Devices
In the growing field of wearable medical devices, multi component injection molding medical plays an essential role in the production of devices that integrate both hard and soft materials. Devices such as smartwatches, insulin pumps, and wearable heart monitors require components that are not only durable but also comfortable and easy to wear for extended periods.
The ability to combine different materials in a single part allows for the creation of wearables with soft, skin-friendly surfaces for comfort, while the internal components can be made from tougher, more rigid materials to ensure durability and reliability. For instance, the outer casing of a wearable device may be produced from a soft-touch elastomer, while the internal components like batteries, sensors, and circuits could be molded from durable plastics or metals. This integration of materials allows for the development of wearables that are both functional and comfortable, meeting the increasing demand for non-invasive medical monitoring devices.
Medical Multi-Component Molding: A Key to Advancing Healthcare Devices
What is Medical Multi-Component Molding?
Multi component injection molding medical is a revolutionary process that plays a crucial role in the production of advanced healthcare devices. By combining two or more materials or colors in a single molding cycle, this technique creates complex, durable, and high-performance medical components that meet the stringent demands of the healthcare industry. The ability to integrate different materials, such as rigid plastics, elastomers, and biocompatible substances, allows for the creation of parts with unique properties like flexibility, strength, and chemical resistance—all in one unified component.
Benefits of Medical Multi-Component Molding
In the realm of medical devices, medical multi-component molding is particularly beneficial for producing intricate devices that require multiple functional attributes. For example, multi-component molding can combine hard materials for structural strength with soft, flexible materials for improved ergonomics or better patient comfort. This is ideal for surgical tools, prosthetics, and wearable devices that require a balance between rigidity and flexibility.
Streamlining the Manufacturing Process
Moreover, medical multi-component molding enables the integration of features like tactile grips, soft seals, and complex geometric shapes into a single part, eliminating the need for secondary operations like assembly or bonding. This not only reduces manufacturing time but also enhances the performance and reliability of medical devices. By streamlining the production process, manufacturers can achieve higher output and maintain strict quality control over every batch, ensuring that medical multi-component molding plays a pivotal role in delivering high-quality, safe, and effective healthcare solutions.
The Future of Medical Device Manufacturing
Through this innovative molding technique, the medical industry can create a new generation of devices that are more efficient, comfortable, and functional, meeting both patient needs and regulatory standards. Medical multi-component molding has truly opened up new possibilities for the design and production of advanced medical devices, positioning it as an essential technology in modern healthcare manufacturing.
Automation and Turnkey Solutions in Multi Component Injection Molding Medical
As multi component injection molding medical continues to evolve, automation plays a critical role in improving efficiency, precision, and scalability. The use of fully automated production systems and customized solutions has transformed the way medical devices are manufactured, offering significant benefits in terms of cost savings, quality control, and production speed. These technologies are helping medical manufacturers meet the increasing demand for high-quality, complex parts that are produced in large volumes.
Fully Automated Production Systems
One of the most significant advancements in multi component injection molding medical is the introduction of fully automated production systems. These systems are designed to streamline the production process, reduce the need for human intervention, and minimize the risk of errors, ensuring that each part meets stringent medical industry standards.
By automating the entire production cycle, manufacturers can ensure the consistent delivery of multi component injection molding medical devices that meet strict regulatory requirements, such as those from the FDA or ISO standards. These automated systems are especially critical in producing high-precision medical components, such as implants, diagnostic devices, and surgical tools, where even the slightest variation can affect performance and safety.
Customized Solutions
In addition to automated production systems, multi component injection molding medical also benefits from customized solutions that cater to the unique needs of plastic medical device manufacturers. Consulting services provided by leading companies help optimize production processes, increase operational efficiency, and enhance automation. These solutions are tailored to the specific requirements of each client, addressing challenges such as material selection, mold design, and cycle time optimization.
Customized solutions can also extend to the development of new materials that are better suited for multi component injection molding medical applications. For example, medical device manufacturers may require specific biocompatible materials or those with enhanced properties like chemical resistance, flexibility, or strength. Consultants work closely with manufacturers to create solutions that improve the overall quality of medical components while maintaining cost-effectiveness.
Furthermore, enhanced automation can be integrated into existing systems to boost performance, reduce scrap rates, and ensure consistent quality over long production runs. Through tailored advice and technical expertise, manufacturers can leverage multi component injection molding medical technology to create innovative, high-quality medical devices that meet the growing demand for precision, reliability, and safety in the healthcare industry.
Working Principle of Multi-Component Injection Molding Medical
Multi-component injection molding medical is an advanced manufacturing technique that enables the creation of highly specialized, multi-functional parts used in medical devices. This process involves injecting two or more different materials into a single mold, either sequentially or simultaneously, to produce a single medical component with integrated features. The working principle behind multi-component injection molding combines various materials with distinct properties, such as rigid and flexible polymers, to create components that meet the complex demands of the medical industry. The following sections will outline the key steps and technical aspects of the process.
Mold Design and Material Selection
The first step in the multi-component injection molding medical process is designing the mold and selecting the appropriate materials for each component. The mold design must be carefully crafted to accommodate multiple cavities and channels for each material, ensuring that they can be injected in a controlled manner. Each cavity must be designed with specific material properties in mind, such as biocompatibility, strength, or flexibility. Material selection is crucial, as medical devices often require materials that are both durable and safe for patient contact. For example, rigid materials like polycarbonate or PEEK might be used for structural parts, while elastomers or silicone could be chosen for components that need flexibility or a soft-touch feel.
Injection and Overmolding Process
Once the mold and materials are selected, the multi-component injection molding process begins with the injection phase. The first material is injected into the mold, filling the cavity with molten plastic or resin under high pressure. After the initial material has cooled and solidified to a degree, the second material is injected into the mold in a separate cavity or overmolded onto the first material. This process can be done in one shot (simultaneously) or in separate stages (sequentially), depending on the complexity of the design and materials used. In medical applications, this overmolding technique allows for the integration of different textures, colors, and functionalities into a single component, reducing the need for secondary operations and assembly.
Mold Clamping and Material Curing
During multi-component injection molding, the mold is clamped tightly to maintain its shape and ensure accurate material flow. The clamping force used in medical-grade molding must be precise to avoid deformation of delicate components while ensuring that each material flows into the designated cavities. Once the materials are injected, they undergo curing or cooling, depending on whether thermoplastic or thermoset materials are used. In the case of thermoplastics, the material hardens as it cools, while thermosetting materials undergo a chemical reaction that hardens the material in place. The precise control of the curing or cooling phase is crucial for maintaining the structural integrity of the multi-material component.
Ejecting and Post-Processing
After the materials have been injected, solidified, and cured, the next step is to eject the completed part from the mold. The mold opens, and the part is carefully removed using automated ejector pins or robotic systems. Depending on the complexity of the design, additional post-processing steps may be required, such as trimming excess material, cleaning, sterilization, or additional functional testing. Medical components often require extra care during post-processing to ensure they meet the strict standards of quality, safety, and sterility. For instance, syringe plungers, multi-material catheters, or implantable devices may undergo sterilization and quality inspections to ensure compliance with regulatory guidelines.
Benefits and Advantages of Multi-Component Injection Molding in Medical Manufacturing
The working principle of multi-component injection molding medical allows manufacturers to achieve several benefits that are especially valuable in the medical industry. By combining multiple materials in a single molding cycle, manufacturers can create parts with enhanced performance, such as improved ergonomics, durability, or biocompatibility. Additionally, the process helps reduce production time and costs by eliminating the need for secondary operations like assembly or part bonding. For instance, multi-component molding can combine soft-touch grips with rigid structural components in one piece, improving device functionality and patient comfort. It also enables the creation of more complex designs with intricate geometries, which is often required for modern medical devices like drug delivery systems, surgical tools, and diagnostic equipment.
Key Challenges and Considerations
While the working principle of multi-component injection molding medical offers many advantages, it also presents unique challenges. One of the primary challenges is achieving proper material bonding between the different layers or components. The selection of materials that adhere well to each other and the proper control of injection pressure and mold temperature are critical factors for ensuring strong, reliable bonds between materials. Additionally, the process requires precision in material flow management and timing to avoid defects like short shots, overflows, or misalignment. Manufacturers must also carefully consider regulatory standards and quality assurance processes, as any defects in multi-component parts can lead to failures in medical device performance or safety.
The working principle of multi-component injection molding medical enables the creation of high-performance, multi-functional parts used in medical devices by combining multiple materials in a single molding cycle. This process offers significant advantages in terms of design flexibility, production efficiency, and cost-effectiveness. By understanding the steps involved, from mold design to material selection and post-processing, manufacturers can ensure the production of safe, reliable, and innovative medical components that meet the rigorous demands of the healthcare industry.
Types of Multi-Component Injection Molding in Medical Applications
Multi-component injection molding is revolutionizing the medical industry by enabling the production of complex, multi-material medical devices with enhanced functionality, durability, and patient safety. This process allows for the integration of different materials or colors in a single molding cycle, eliminating the need for assembly while improving product performance. Various types of multi-component injection molding techniques are employed based on the medical device’s requirements, including material properties, structural integrity, and biocompatibility. Below are the primary types of multi-component injection molding used in medical applications, each offering distinct advantages for specific healthcare products.
Overmolding
Overmolding is a multi-component injection molding technique where a secondary material is molded over a base material (substrate) to create a single integrated medical device.
- Application in Medical Devices: This method is commonly used in surgical instrument handles, catheter tips, and syringe grips, where a soft-touch material (like TPE) is overmolded onto a rigid plastic core (like PP or PC) to enhance grip, comfort, and usability.
- Advantages: Improves ergonomics, provides chemical resistance, and enhances patient safety by creating seamless, durable structures.
Co-Injection Molding
Co-injection molding involves injecting two different materials into the same mold during a single cycle, typically forming a layered or encapsulated structure.
- Application in Medical Devices: Used in medical housings, diagnostic equipment casings, and multi-layered syringes, where an inner core material is surrounded by an outer shell for strength and sterilization compatibility.
- Advantages: Enhances mechanical strength, improves material efficiency, and allows for barrier properties in medical packaging.
Multi-Shot Injection Molding
Multi-shot molding utilizes two or more injection units to sequentially inject different materials into the mold, producing a precisely bonded, multi-material medical component.
- Application in Medical Devices: Common in dual-color medical buttons, multi-layered tubing, and wear-resistant orthopedic components, where different materials provide both structural integrity and functional enhancements.
- Advantages: Creates high-precision, multi-functional medical devices without requiring additional bonding or assembly.
Insert Molding
Insert molding is a specialized form of multi-component injection molding where a pre-fabricated part (such as metal or electronic components) is placed into the mold before injecting plastic.
- Application in Medical Devices: Frequently used for implantable medical devices, needle hubs, and electronic sensor encapsulation, where metal or bioelectronic inserts need to be permanently integrated with plastic casings.
- Advantages: Enhances device durability, simplifies assembly, and ensures precise alignment of critical medical components.
Hard-Soft Combination Molding
This technique involves molding a combination of rigid and flexible materials within the same process to achieve an optimal balance of strength and comfort.
- Application in Medical Devices: Used in respiratory masks, flexible joints in prosthetics, and medical-grade tubing, where a rigid structure requires flexible, patient-friendly contact points.
- Advantages: Increases patient comfort, improves device flexibility, and maintains structural stability.
Rotary/Transfer Molding
Rotary or transfer molding involves rotating the mold between different injection stages to allow for multiple materials to be added without contamination.
- Application in Medical Devices: Found in multi-chamber syringes, drug delivery systems, and diagnostic test components, where different plastic materials must be accurately positioned for proper function.
- Advantages: Improves production efficiency, enhances material bonding, and enables complex medical part designs.
Multi-component injection molding is an indispensable technology in modern medical manufacturing, enabling high-precision, multi-material, and functional integration in life-saving devices. Techniques like overmolding, co-injection molding, and multi-shot molding are key to producing ergonomic, durable, and biocompatible medical components. As medical technology advances, multi-component injection molding will continue to drive innovation in safer, more efficient, and patient-friendly medical devices.
Difference Between Multi-Component Injection Molding Medical and Secondary Molding
In the medical manufacturing industry, two prominent molding techniques often come up when producing medical device components: multi-component injection molding medical and secondary molding. Although both processes involve the use of molds to form plastic components, they differ significantly in terms of process flow, material usage, and the types of applications they serve. Understanding these differences is crucial for selecting the right technique depending on the requirements of the medical device being produced. The following sections will delve into these differences from various perspectives.
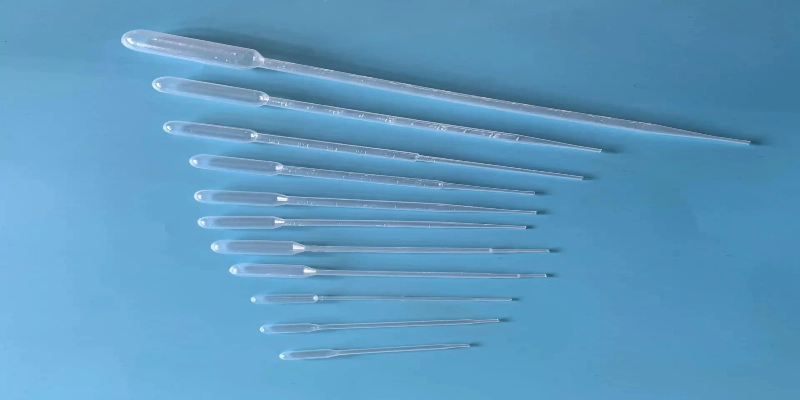
Process Flow: Simultaneous vs. Sequential
One of the most significant differences between multi-component injection molding medical and secondary molding lies in the flow of the molding process itself. In multi-component injection molding, multiple materials or colors are injected into the mold simultaneously or sequentially in one molding cycle. This means that the entire part is formed in a single step, with different materials being injected into the same mold cavity at different times or all at once, depending on the design. This process eliminates the need for additional assembly steps, as the components are integrated into a single, unified part.
In contrast, secondary molding involves multiple stages. A component is first molded using one material, and then the part is subjected to a secondary molding process where a second material is added, typically through overmolding or insert molding. This requires multiple molding cycles, often with manual assembly steps, to create the final part. Secondary molding is often used when a part needs to incorporate a different material or functionality that can’t be achieved in a single cycle.
Material Usage and Integration
The material usage and integration methods in multi-component injection molding medical differ notably from secondary molding. In multi-component injection molding, two or more materials, each with specific properties (e.g., flexibility, rigidity, biocompatibility), are combined during a single molding cycle. This allows for the integration of different material types into one cohesive part. For instance, a medical device may use rigid materials for structural integrity and soft elastomers for parts that need to be flexible or provide a soft-touch feel, such as syringe handles or catheter grips.
On the other hand, secondary molding typically involves a primary material being molded first, followed by a secondary material added afterward. For example, a rigid plastic component may be molded, and then a flexible rubber-like material is overmolded to create a grip or seal. Secondary molding is often used to add additional features or to modify the surface properties of a part but is more labor-intensive and time-consuming compared to the integrated, one-step process of multi-component molding.
Production Efficiency and Cost
In terms of production efficiency, multi-component injection molding medical is generally more efficient compared to secondary molding. Since all materials are injected into the mold in a single cycle, the process tends to be faster, reducing both the cycle time and the need for manual handling or additional assembly. This is particularly advantageous in high-volume production, where minimizing steps and automation can significantly lower overall manufacturing costs.
In contrast, secondary molding requires multiple molding cycles and additional steps like part handling, trimming, and assembly, which adds to the time and cost of production. This can be a disadvantage in terms of production efficiency, especially in medical device manufacturing, where speed, precision, and cost-effectiveness are essential. However, secondary molding might still be used when more complex features are needed that cannot be achieved with a single molding cycle.
Design Flexibility and Complexity
Another notable difference is the design flexibility and complexity of the parts that can be produced. Multi-component injection molding medical allows for the creation of highly intricate, multi-functional components in a single step. This technique is ideal for designing parts that require varying material properties within one device, such as parts that need different textures, flexibility, or color coding. This allows for more complex, integrated designs like syringe plungers with a rigid core and a soft, flexible outer layer, or surgical instruments that combine multiple materials for improved grip and performance.
On the other hand, secondary molding may have limitations in design complexity as it requires multiple steps to integrate different materials. The complexity of the design can be constrained by the need for precise alignment between the primary and secondary materials, and achieving seamless bonding between layers may require more design and process control.
Application in Medical Devices
The choice between multi-component injection molding medical and secondary molding often depends on the specific requirements of the medical device being produced. Multi-component injection molding is ideal for medical components that require multiple materials with different properties in a single, unified part. Examples include dual-material grips for surgical instruments, over-molded seals for medical connectors, and multi-layered drug delivery systems. This process is ideal for creating compact, high-performance components that are lightweight, cost-effective, and meet the stringent demands of medical applications.
Secondary molding, while more labor-intensive, is often used for components that need a specific feature or modification after the primary molding cycle. Examples include adding a soft, flexible coating to a rigid plastic part or adding a second material to enhance durability or biocompatibility. Secondary molding may be used in cases where a medical component needs to be customized or when the required material properties cannot be achieved in a single molding cycle.
Regulatory Compliance and Quality Control
Both multi-component injection molding medical and secondary molding must adhere to strict regulatory requirements, particularly in medical device manufacturing. However, multi-component molding tends to offer a higher level of control over quality, as it eliminates the need for additional assembly and reduces the risk of contamination or errors between molding steps. By creating a fully integrated part in one cycle, manufacturers can ensure that all components meet the necessary quality standards and are compliant with regulations such as ISO 13485 and FDA guidelines.
In secondary molding, additional handling and assembly steps increase the risk of quality control issues. Parts may require additional testing, validation, and documentation to ensure they meet medical standards. However, many manufacturers have developed effective systems to manage these steps, and secondary molding is still widely used for medical applications that require more complex material combinations.
Multi-component injection molding medical and secondary molding differ significantly in terms of process flow, material usage, production efficiency, and application suitability. Multi-component injection molding offers an efficient, cost-effective, and integrated solution for creating high-performance, multi-material medical components in a single molding cycle. In contrast, secondary molding is better suited for applications that require adding a secondary material or feature to an existing part, often involving more labor-intensive steps. Both techniques have their place in medical device manufacturing, and the choice between them will depend on factors such as design complexity, material requirements, and production volume.
Challenges and Solutions for Multi-Component Injection Molding in Medical Applications
Multi-component injection molding is a transformative technology in medical manufacturing, allowing the seamless integration of multiple materials into a single medical device. While this process offers significant advantages—such as enhanced functionality, material bonding, and cost efficiency—it also presents several challenges. Issues related to material compatibility, process complexity, precision control, regulatory compliance, and cost management must be carefully addressed to ensure high-quality medical products. The following sections outline the key challenges in multi-component injection molding for medical applications and the corresponding solutions to overcome them.
Material Compatibility and Bonding Issues
Multi-component injection molding often requires the use of different plastics, elastomers, or even metal-plastic combinations, which may not naturally adhere to one another. Improper bonding can lead to delamination, mechanical failure, or product defects, compromising medical device safety.
- Solution:
- Careful selection of compatible material combinations (e.g., thermoplastic elastomers with rigid plastics).
- Use of adhesion-promoting surface treatments or chemical bonding agents.
- Employing optimized mold designs to facilitate better material interlocking and adhesion.
Complex Mold and Process Design
The precision required in multi-component injection molding for medical devices adds complexity to mold design and process control. Differences in cooling rates, shrinkage, and flow behavior between materials can result in warping, misalignment, or defective parts.
- Solution:
- Utilize computer-aided engineering (CAE) simulations to predict material behavior and optimize mold design.
- Implement high-precision molding machines with multi-axis rotation and automated process control.
- Use advanced hot runner systems to maintain consistent temperature and minimize defects.
Precision and Tolerance Control
Medical devices require exceptionally tight tolerances, often within microns, to meet strict industry standards. The integration of multiple materials in a single mold increases the risk of dimensional inaccuracies and process variability.
- Solution:
- Implement real-time process monitoring using sensors and automated feedback systems.
- Utilize micro-molding technologies for small and intricate medical components.
- Conduct rigorous quality control with 3D scanning and laser measurement to verify dimensions.
Sterilization and Biocompatibility Challenges
Medical devices must comply with FDA, ISO 10993, and other regulatory standards to ensure patient safety. Some materials used in multi-component molding may degrade under sterilization or cause adverse biological reactions.
- Solution:
- Select medical-grade biocompatible materials that withstand gamma radiation, ethylene oxide, or autoclaving.
- Conduct extensive material testing for chemical resistance and bio-inertness.
- Use medical cleanroom environments to prevent contamination during molding.
High Initial Tooling and Production Costs
The development of multi-component molds involves high tooling costs, requiring specialized machinery and advanced mold-making expertise. For low-volume medical production, this can pose a significant financial barrier.
- Solution:
- Optimize mold design for longevity and scalability, ensuring long-term cost efficiency.
- Consider modular mold systems that allow flexibility in part modifications.
- Evaluate cost-benefit trade-offs between multi-component molding and alternative methods like insert molding or additive manufacturing.
Regulatory Compliance and Validation
The medical industry is highly regulated, and multi-component injection molding requires strict validation to meet ISO 13485, FDA, and GMP standards. Failure to comply can result in product recalls or legal challenges.
- Solution:
- Implement a comprehensive validation process, including IQ, OQ, and PQ (Installation, Operational, and Performance Qualification).
- Maintain detailed documentation and process traceability through digital monitoring systems.
- Work closely with regulatory agencies to ensure compliance throughout development and production.
Multi-component injection molding plays a critical role in advancing medical device manufacturing, offering unmatched precision, material integration, and design flexibility. However, challenges related to material bonding, mold complexity, precision control, sterilization, cost, and regulatory compliance must be effectively managed. By leveraging advanced engineering techniques, quality control measures, and strategic material selection, manufacturers can ensure that multi-component injection molding for medical applications remains a reliable, efficient, and compliant production method for next-generation medical devices.
FAQs about Multi Component Injection Molding Medical
Design for Manufacturability (DFM) in injection molding refers to the practice of designing parts in a way that they are easy, cost-effective, and efficient to produce using injection molding techniques. DFM involves a set of principles that aim to optimize the design of a product to make the manufacturing process smoother, faster, and less expensive while maintaining the required quality and performance. This concept is especially critical in medical device manufacturing, where tight tolerances, high-quality standards, and biocompatibility are essential. In DFM, engineers focus on aspects such as material selection, wall thickness, part geometry, and draft angles to ensure that the mold can be manufactured easily and parts can be produced without defects. For instance, complex designs may be simplified to minimize the number of mold components, reducing production time and cost. In the medical industry, DFM is crucial because it ensures that devices like syringes, catheters, and surgical instruments are produced efficiently while meeting regulatory requirements for safety and performance.
Multi-cavity injection molding is a method in which multiple identical parts are created within a single injection mold during one cycle. In contrast to single-cavity molds, which only produce one part per cycle, multi-cavity molds are designed to produce several parts simultaneously, thereby increasing production efficiency and reducing cycle time. This process is commonly used when manufacturing large quantities of the same part, such as medical devices like syringes, vials, or diagnostic equipment components. The key benefit of multi-cavity molding is its ability to produce more parts at once, significantly boosting throughput and reducing per-part production costs. This is especially valuable in industries like medical device manufacturing, where high-volume, cost-efficient production is essential. Furthermore, multi-cavity injection molding ensures consistency in part quality, as all parts are made under the same conditions and in the same mold. By using specialized molds, manufacturers can produce high-quality, precise medical components in a more time- and cost-effective manner, meeting the stringent requirements of the medical industry.
Multi injection molding (or multi-component injection molding) is a process in which two or more different materials or colors are injected into a single mold during one cycle to create a multi-material part. This method allows for the production of complex parts with varying material properties, such as combining hard and soft materials or different colors, all within the same mold.
The multi injection molding process typically involves several steps:
Material Preparation: Different materials, such as thermoplastics, elastomers, or composites, are selected based on the required properties of the final product. Each material may have a distinct injection point within the mold.
Injection: The first material is injected into the mold cavity, where it fills the designated areas. After the first layer solidifies, the mold rotates or opens to allow the injection of the second material.
Molding: The second material is injected, often over the first, creating a multi-layered or co-molded part.
Cooling and Ejection: Once the materials have cooled and solidified, the part is ejected from the mold.
This technique is highly beneficial in medical applications, such as the creation of ergonomic handles for surgical tools or multi-material implants that combine biocompatible polymers with stronger materials. It allows manufacturers to create parts with enhanced functionality, performance, and comfort, reducing assembly time and the need for additional post-processing steps.
Injection molding is widely used in the medical industry to produce a broad range of high-precision, reliable, and biocompatible products. The versatility and cost-effectiveness of injection molding make it an ideal manufacturing technique for medical devices that require strict quality control and regulatory compliance.
Some common medical products made by injection molding include:
Syringes: Used for administering injections, syringes are produced with high precision to ensure they meet stringent safety standards.
Catheters: Essential for minimally invasive procedures, catheters are made with flexible, biocompatible materials to ensure patient safety and comfort.
Implants: Joint replacements, dental implants, and other types of implants are often manufactured using injection molding. The process allows for the use of high-performance materials like PEEK (Polyetheretherketone) and silicone, which are both durable and biocompatible.
Diagnostic Devices: Products such as test tubes, Petri dishes, and blood bags are manufactured using injection molding to ensure precise dimensions and contamination-free surfaces.
Surgical Tools: Molding allows for the production of intricate, ergonomic designs in surgical instruments that require biocompatibility and strength.
Wearable Medical Devices: Modern wearable devices that track health metrics, such as glucose monitors and heart rate monitors, are also produced using injection molding, combining hard and soft materials to ensure functionality and comfort.
Injection molding ensures these products are manufactured efficiently, consistently, and to the highest standards, essential for the medical field’s rigorous demands. The ability to produce complex shapes, ensure sterile conditions, and use various materials makes it indispensable in medical device manufacturing.
Medical injection molding is a manufacturing process used to produce high-precision plastic medical components, devices, and equipment. It involves injecting molten thermoplastic materials into a mold cavity, where they cool and solidify into the desired shape. Multi-component injection molding takes this a step further by using two or more materials or colors in a single molding cycle. This technique allows for the production of complex, multi-material parts without secondary assembly, improving efficiency and product performance. It is widely used for medical devices like syringes, IV connectors, catheters, and implantable components. The process ensures high precision, repeatability, and compliance with strict medical industry regulations, such as ISO 13485 and FDA requirements. The advantages of multi-component injection molding in the medical sector include enhanced functionality, reduced assembly time, and minimized contamination risks, making it a preferred choice for advanced healthcare applications.
The medical injection molding market has been experiencing steady growth, driven by the increasing demand for high-quality medical devices and disposable healthcare products. In particular, multi-component injection molding is gaining traction due to its ability to produce complex, multi-material parts in a cost-effective manner. As of recent estimates, the global medical injection molding market is valued at several billion dollars and is expected to grow at a CAGR of 5–8% over the next decade. Factors contributing to this growth include the rising aging population, advancements in medical technology, and increasing healthcare expenditures. The demand for high-precision, biocompatible, and lightweight medical components further propels the adoption of multi-component injection molding. Key players in the industry are investing in automation, cleanroom manufacturing, and innovative material solutions to meet stringent regulatory standards and enhance production efficiency, making it a lucrative sector within the medical manufacturing landscape.
The lifespan of injection-molded medical components depends on factors such as material selection, environmental conditions, and usage intensity. Typically, medical-grade injection-molded products are designed for either single-use or long-term applications. Single-use items, like syringes and IV components, are disposed of after one use to maintain sterility and prevent infections. On the other hand, multi-use medical devices, such as surgical instrument handles and orthopedic implants, can last for years, provided they are made from high-performance materials like PEEK or medical-grade silicone. The durability of the injection mold itself is also a crucial factor—high-quality steel molds used in multi-component medical injection molding can produce millions of parts before requiring replacement. Proper mold maintenance, including routine cleaning and wear monitoring, extends mold life, ensuring consistent quality and cost-efficiency in medical device production.
The number of cavities in an injection mold varies based on production requirements, part complexity, and material selection. In medical multi-component injection molding, cavity configurations range from single-cavity molds for low-volume, highly specialized components to multi-cavity molds producing thousands of parts per cycle. High-volume medical devices, such as syringe plungers, catheter components, and IV connectors, often use multi-cavity molds to maximize efficiency and reduce per-unit costs. Some molds can have up to 128 cavities, significantly improving production throughput. Multi-component injection molding may require more complex mold designs, such as rotary or transfer molds, to accommodate different materials or colors within the same cycle. The choice of cavity configuration is influenced by factors like cycle time, material flow, and quality control requirements, ensuring that medical components meet stringent safety and performance standards.
The cost of medical injection molding per hour depends on various factors, including machine size, mold complexity, material selection, and labor costs. In general, standard injection molding machines cost between $50 to $500 per hour to operate, with specialized medical-grade machines, such as those used in multi-component molding, being on the higher end. Additional costs arise from cleanroom manufacturing requirements, regulatory compliance, and validation testing in the medical industry. Advanced multi-component injection molding processes, which involve multiple materials or colors, require specialized equipment and tooling, increasing the overall cost. However, these costs are offset by reduced assembly steps, improved product integrity, and lower waste production. While the upfront investment in multi-component medical injection molding can be substantial, its long-term efficiency and cost savings make it an attractive choice for medical device manufacturers.
Injection molding, particularly in the medical sector, is highly profitable due to the growing demand for precision-molded components. Multi-component injection molding further enhances profitability by reducing manufacturing steps, improving product quality, and minimizing material waste. Medical device manufacturers benefit from economies of scale, as high-volume production lowers per-unit costs. Additionally, advancements in automation and process optimization contribute to cost efficiency. Profitability is influenced by factors such as initial tooling costs, material expenses, machine operation costs, and regulatory compliance. While the initial investment in multi-component injection molding can be high, the ability to produce durable, high-performance medical components with minimal assembly makes it a lucrative choice. Companies investing in this technology can achieve significant long-term returns, especially in high-demand areas like drug delivery systems, surgical tools, and diagnostic equipment.
Injection molding and casting are both manufacturing processes used to create medical components, but they differ significantly. Injection molding involves injecting molten thermoplastic or thermosetting materials into a mold under high pressure, allowing for fast, precise production of complex medical parts. In contrast, casting is a slower process where liquid material, such as silicone or metal, is poured into a mold and allowed to solidify naturally. While both methods are used in medical manufacturing, injection molding is preferred for high-volume production of plastic medical devices due to its efficiency, repeatability, and ability to create intricate multi-component designs. Casting is generally used for low-volume, custom medical parts that require flexibility, such as prosthetic components. Multi-component injection molding provides advantages over casting by enabling the seamless integration of different materials, enhancing product functionality, and improving overall manufacturing speed.
Injection molding and injection compression molding (ICM) share similarities but differ in processing techniques and applications. In traditional injection molding, molten material is injected into a mold cavity at high pressure, ensuring detailed and consistent part formation. Injection compression molding, on the other hand, involves injecting material into a partially closed mold, then applying additional compression to distribute the material evenly. This technique reduces internal stress, enhances mechanical properties, and is useful for precision components. In medical multi-component injection molding, ICM can be beneficial for producing thin-walled, high-strength medical parts with improved dimensional stability. While standard injection molding is more commonly used for high-volume medical devices like syringes and catheters, ICM is preferred for specialized applications requiring enhanced material properties, such as high-performance lenses, surgical implants, and diagnostic device housings.
Injection molding, particularly in the medical sector, is a highly specialized process that requires expertise in mold design, material selection, and process control. While basic injection molding can be straightforward, multi-component injection molding adds complexity due to the need for precise coordination of multiple materials, colors, or functions within a single molding cycle. Achieving high-quality medical components involves stringent process validation, adherence to regulatory standards, and maintaining cleanroom conditions. The use of automated systems and advanced software aids in process optimization, making it more efficient but still requiring skilled engineers to oversee production. Training and experience are crucial for ensuring that medical injection molding meets strict safety and performance requirements. Though advancements in technology have streamlined many aspects of the process, mastering medical multi-component injection molding remains a challenging but highly rewarding field.
Injection molding, especially in the medical industry, can be costly due to the high initial investment in molds, regulatory compliance, and specialized equipment. Multi-component injection molding further increases expenses as it requires advanced molds, multi-material handling systems, and precise process control. However, despite the high upfront costs, this method proves cost-effective over time due to high production efficiency, reduced assembly requirements, and minimal material waste. The cost per part decreases significantly with high-volume production, making it an economical choice for large-scale medical device manufacturing. Factors like material selection, machine operation costs, and mold longevity also influence overall expenses. While medical injection molding may be expensive initially, its long-term benefits in quality, consistency, and production efficiency make it a highly viable investment for medical manufacturers looking to produce complex, multi-functional components.
Molding is a broad manufacturing process in which a material is shaped using a mold, while injection molding is a specific type of molding that involves injecting molten material into a mold under high pressure. In medical multi-component injection molding, multiple materials or colors are injected into a single mold in one cycle, allowing for the production of complex, multi-functional medical components. Traditional molding methods, such as compression molding or rotational molding, are often slower and less precise than injection molding. Injection molding is preferred in the medical field because it ensures high precision, repeatability, and compliance with stringent regulatory standards. Multi-component injection molding enhances efficiency by integrating multiple materials without requiring additional assembly, making it ideal for producing advanced medical devices like dual-material syringe plungers, soft-touch catheter grips, and complex surgical instrument handles.
Injection molding and reaction injection molding (RIM) differ primarily in materials and processing methods. Traditional injection molding involves melting thermoplastics and injecting them into a mold under high pressure, where they cool and solidify. In contrast, RIM uses thermosetting polymers that undergo a chemical reaction inside the mold to harden. RIM is commonly used for lightweight, impact-resistant components, whereas injection molding is ideal for high-precision medical applications. Multi-component injection molding in the medical field allows for the integration of different materials in one cycle, such as combining rigid and flexible polymers for improved functionality. RIM is less common in medical applications due to longer curing times and limited material choices. However, multi-component injection molding excels in producing intricate medical parts like over-molded grips, dual-material surgical handles, and multi-layer tubing, ensuring high strength, sterility, and performance in medical environments.
Thermoforming (or thermo molding) and injection molding differ in how they shape plastic materials. Thermoforming involves heating a plastic sheet until it becomes pliable, then shaping it using a mold and applying vacuum or pressure. It is commonly used for large, thin-walled parts such as medical trays, packaging, and housings for medical devices. Injection molding, on the other hand, injects molten plastic into a mold to create highly detailed, repeatable components with complex geometries. Multi-component injection molding enhances this process by combining different materials or colors in a single molding cycle. This technique is essential in the medical field for producing precise, multi-functional parts like dual-material tubing connectors, ergonomic surgical handles, and multi-layered drug delivery devices. While thermoforming is more suitable for simpler, large-surface-area parts, injection molding is preferred for high-precision, durable, and multi-material medical components.
The future of injection molding, particularly in the medical industry, is being shaped by automation, sustainability, and advanced material science. Multi-component injection molding is expected to play a crucial role in the development of next-generation medical devices by integrating multiple materials and functionalities into a single component. Innovations such as bioresorbable plastics, antimicrobial coatings, and smart polymers will enhance medical device performance and patient safety. Additionally, advancements in digital twin technology and AI-driven process optimization will improve efficiency, reduce defects, and minimize material waste. 3D printing is also being integrated with injection molding for rapid prototyping and customized medical device production. As the demand for minimally invasive and patient-specific medical solutions grows, multi-component injection molding will continue to evolve, enabling the production of more complex, lightweight, and highly functional medical components with improved precision and biocompatibility.
Metal injection molding (MIM) is gaining momentum in the medical field due to its ability to produce complex, high-strength metal components with tight tolerances. The future of MIM, especially in multi-component medical applications, will see the integration of biocompatible metals like titanium and stainless steel for producing surgical instruments, orthopedic implants, and dental components. Advancements in nano-particle-infused feedstocks and hybrid metal-plastic injection molding will enhance functionality and durability. Additionally, additive manufacturing and MIM are being combined to create highly customized, patient-specific implants with improved mechanical properties. The medical industry’s increasing demand for lightweight, corrosion-resistant, and high-precision components will drive innovation in MIM. The integration of multi-component MIM with traditional plastic injection molding will further expand possibilities, allowing for the creation of hybrid metal-polymer medical devices with enhanced performance and reduced manufacturing costs.
The hardest plastics used in medical injection molding include polyether ether ketone (PEEK), polycarbonate (PC), and ultra-high molecular weight polyethylene (UHMWPE). PEEK is one of the most durable and high-performance thermoplastics, widely used in medical applications such as spinal implants, orthopedic components, and dental prosthetics due to its exceptional mechanical strength and biocompatibility. Multi-component injection molding can integrate PEEK with softer materials like silicone to create ergonomic, high-strength medical devices. Polycarbonate is also a tough plastic, used for surgical instruments and medical housings due to its impact resistance and clarity. UHMWPE is commonly used in joint replacements due to its extreme wear resistance and low friction properties. The selection of a hard plastic depends on the application, required sterilization methods, and long-term performance, making multi-component injection molding a valuable technique for combining rigid and flexible materials in a single medical device.
The primary purpose of injection molding in the medical industry is to produce high-precision, durable, and cost-effective components at scale. Multi-component injection molding enhances this process by integrating multiple materials, eliminating the need for secondary assembly, and improving product functionality. This is particularly useful in medical applications where different textures, mechanical properties, or biocompatible materials are required in a single part. Injection molding ensures consistency, sterility, and compliance with stringent medical regulations, making it essential for manufacturing surgical instruments, drug delivery devices, and implantable components. By utilizing multi-component technology, medical manufacturers can create products with improved ergonomics, reduced weight, and enhanced durability, contributing to better patient outcomes and streamlined production processes. The ability to mass-produce intricate medical components with high accuracy makes injection molding a cornerstone of modern medical manufacturing.
Injection molding falls under mass production and precision manufacturing, as it enables the large-scale production of highly detailed, repeatable plastic and metal components. In the medical sector, multi-component injection molding is considered an advanced manufacturing technique because it combines different materials, colors, or functionalities in a single process. This method allows for the creation of medical devices with enhanced features such as soft-touch grips, integrated seals, and multi-layered structures. Injection molding is a key part of cleanroom manufacturing, ensuring that medical products meet stringent sterility and regulatory requirements. It is used in high-volume manufacturing of disposable medical components like syringes, IV connectors, and inhalers, as well as durable items like surgical instrument handles and implantable devices. Its ability to achieve complex geometries with high precision makes it an essential process in medical manufacturing.
Injection molding machines are expensive due to their complexity, precision requirements, and ability to process high-performance materials. Multi-component injection molding machines are even more costly because they require specialized tooling, advanced automation, and precise material control to combine multiple materials in a single cycle. In the medical field, additional expenses come from cleanroom requirements, regulatory compliance, and validation testing to ensure product safety and sterility. High-quality medical injection molds, typically made from hardened steel, can cost hundreds of thousands of dollars due to their durability and precision. The integration of robotic automation, AI-driven quality control, and process monitoring systems further increases costs. However, despite the high initial investment, these machines provide significant cost savings in the long run by improving efficiency, reducing waste, and enabling high-volume production of complex medical components with consistent quality.
Pros and Cons of Injection Molding in Medical Applications
Pros:
Precision & Consistency: Multi-component injection molding ensures tight tolerances, crucial for medical devices.
Material Versatility: It allows combining multiple materials, enhancing product functionality.
Reduced Assembly Needs: Producing complex parts in one process reduces assembly time and costs.
Sterilization Compatibility: Many medical-grade plastics used in injection molding are resistant to sterilization methods like autoclaving and gamma irradiation.
Cons:
High Initial Costs: Tooling costs for multi-component molding are significant.
Complex Mold Design: Requires specialized molds and machinery.
Material Compatibility Issues: Some materials do not bond well, requiring additional processing.
Limited Design Changes: Once the mold is created, modifications are expensive.
Despite the challenges, multi-component injection molding is a game-changer for high-precision medical components.
The two primary injection molding processes in medical applications are:
1. Multi-Component Injection Molding:
Combines two or more materials in a single mold cycle.
Common in medical devices requiring different textures, functionalities, or biocompatibility.
Used for catheter handles, syringes with soft grips, and over-molded surgical tools.
2. Micro Injection Molding:
Focuses on producing extremely small medical parts (less than 1g).
Ideal for precision components like hearing aids, microfluidic devices, and drug delivery systems.
Requires specialized machinery with tight process control.
Both processes enhance medical device innovation, offering precision, durability, and material integration benefits.
3D injection molding refers to an advanced technique where complex three-dimensional medical components are molded using a combination of multi-material layering and intricate mold designs.
Benefits:
Enables seamless integration of different medical-grade plastics.
Produces ergonomic designs, such as prosthetic components and surgical grips.
Reduces post-processing and enhances biocompatibility.
Applications:
Medical implants with integrated antimicrobial surfaces.
Custom-fit orthodontic devices.
Wearable medical sensors with embedded electronics.
Unlike traditional multi-component molding, 3D injection molding allows more freedom in part geometry while maintaining high precision and sterility.
While injection molding is a top choice for mass production, other technologies may be better depending on the application:
Additive Manufacturing (3D Printing):
Better for prototyping and patient-specific medical devices.
Enables rapid iteration without expensive tooling.
Used for customized implants and anatomical models.
Liquid Silicone Rubber (LSR) Molding:
Ideal for soft, flexible medical components like seals and valves.
Offers excellent biocompatibility and durability.
CNC Machining:
Preferred for ultra-high precision metal parts.
Used for surgical instruments and implants where plastics aren’t suitable.
Injection molding remains dominant for high-volume production, but these alternatives provide unique advantages for specific medical applications.
PVC (Polyvinyl Chloride) injection molding is widely used in medical applications due to its biocompatibility, chemical resistance, and cost-effectiveness.
Applications in Medical Devices:
IV tubing and blood bags.
Catheter components.
Oxygen masks and breathing devices.
Advantages:
Can be soft or rigid, making it versatile.
Compatible with sterilization processes.
Transparent grades are useful for fluid monitoring.
Challenges:
Some concerns over plasticizers (like phthalates) used to soften PVC, which may require medical compliance testing.
Not as durable as high-performance plastics like PEEK or PPSU.
PVC injection molding remains a cost-effective and widely used technique for disposable and flexible medical components.
The demand for medical injection molding has been growing significantly due to:
Increased Demand for Disposable Medical Devices:
Surge in single-use syringes, IV components, and diagnostic equipment post-pandemic.
Advancements in Multi-Component Molding:
More complex, ergonomic, and functional designs are being created without assembly.
Biocompatible & Sterilizable Plastics:
Rising preference for polymer-based medical devices over metals due to cost and regulatory advantages.
Market Outlook:
Expected to grow at 7-10% CAGR in the next decade.
Growth in minimally invasive surgical tools, drug delivery systems, and wearables is fueling demand.
Multi-component molding is particularly crucial for next-gen medical devices that integrate different materials for enhanced performance.
In multi-component injection molding for medical devices, the cavity and core are two essential parts of the mold that define the final product’s shape and functionality.
The cavity is the mold section that forms the outer surface of the medical component. It determines the external geometry, texture, and overall appearance. In medical applications, such as syringe barrels or diagnostic device casings, the cavity ensures smooth surfaces and precise detailing to meet strict hygiene and biocompatibility standards.
The core is the counterpart that shapes the internal structure of the molded part. It ensures accurate hollow spaces, channels, and intricate details, crucial for devices like catheter components or multi-layered implants. In multi-component molding, the core plays a key role in material bonding and alignment, especially when combining hard and soft materials for ergonomic grips or sealing features.
A well-designed cavity and core system ensures high precision, durability, and functionality in medical device production.
In multi-component injection molding, multiple materials are combined in a single mold to create complex, functional medical devices. However, insert molding is a distinct process where a pre-made component (often metal or another material) is placed into the mold before injection to create a hybrid part.
In standard multi-component injection molding, materials are injected in successive stages to form a seamless product, such as a dual-material surgical grip or a multi-layer catheter tip. This process improves functionality, comfort, and chemical resistance without requiring assembly.
In contrast, insert molding is often used when integrating metal components, electronics, or reinforced structures within plastic medical devices. A common example is the metal needle hub in syringes, where the metal insert is over-molded with plastic for durability and precise alignment.
Both methods are essential in modern medical manufacturing, offering enhanced product performance, biocompatibility, and design efficiency.
Contact our professional team now for a same-day quote and risk-free project evaluation. Benefit from ISO 8 cleanrooms, advanced machines, and 12-hour fast response in medical injection molding.