Medical molding factories are pivotal in the healthcare industry, providing the foundation for producing essential medical devices and components. China medical molding factories, in particular, focus on creating high-quality, reliable products that meet the stringent requirements of the medical field. By employing advanced manufacturing techniques and maintaining strict compliance with regulatory standards, these factories ensure that every product is both safe and effective for patient care. Precision is a hallmark of their operations, enabling the production of components with tight tolerances and consistent quality. Medical Molding Factories include cleanroom and non-cleanroom manufacturing offering injection blow molding & Injection blow molding. Additionally, China medical molding factories leverage cutting-edge technologies to streamline production and minimize errors, reinforcing their critical role in improving healthcare outcomes. Their expertise in innovation and compliance drives advancements in modern medical device manufacturing, making them integral to the global healthcare supply chain.
Low-Volume to High-Volume Production Capabilities
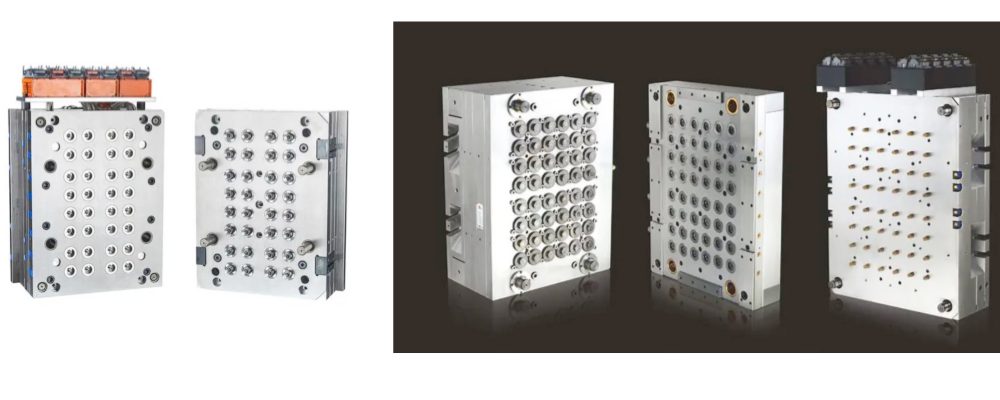
Attribute | Description |
---|---|
Type | Plastic Injection Molding, Custom Mold Manufacturing, Injection Mold Plastic Components |
Brand Name | LY Medical Injection Mold |
Place of Origin | Dongguan, Guangdong, China |
Shaping Mode | Plastic Injection Mould |
Materials Supported | ABS, PC, Nylon, PA66, PP, PMMA, PSU, PCTG, TPE, TPU, PBT, Acetal, PVC, CPVC, Acrylic |
Cavity Options | Single Cavity, Multi-Cavity |
Runner Options | Hot Runner, Cold Runner |
Mold Life | 250,000 - 500,000 shots |
Tolerance | 0.003mm - 0.05mm |
Surface Finishes | Polish, Etched, Texture, Sandy, MT, SPI, Smooth, Glossy |
Applications | Medical Devices |
Certifications | ISO9001 |
MOQ | 1 piece (for molds), 1000 pieces (for parts) |
Logo Customization | Customer Logo Acceptable |
Packaging | 5-ply carton, protects products from scratches |
Delivery | By Sea or Express |
Lead Time | 7-14 days |
Service | OEM/ODM, Customized Molding Services |
Processing Techniques | Moulding, Cutting, Injection Machining, CNC Machining |
Key Features | High Precision, Durable Molds, Custom Colors, Medical-Grade Materials |
Medical Molding Factories: What is Medical Molding?
Medical molding is a specialized manufacturing process integral to the production of critical healthcare components. It involves shaping medical-grade plastics into precise, high-quality parts that meet strict industry standards. This process ensures that the medical devices produced are safe, durable, and reliable, making it an essential element in modern healthcare manufacturing. Medical molding factories play a pivotal role by employing advanced techniques and stringent quality controls to create components that improve patient outcomes and support healthcare innovations.
Types of Molding Processes Used in Medical Molding Factories
Medical molding factories utilize various advanced molding processes to meet diverse healthcare needs, including:
- Injection Molding
Injection molding is one of the most commonly used techniques in medical molding factories. It involves melting medical-grade plastics and injecting them into a mold to create components with high precision and consistent quality. This process is ideal for producing large volumes of complex medical parts, such as syringes, diagnostic tools, and surgical instruments. - Overmolding
Overmolding adds additional layers of material onto an existing component to enhance its functionality and durability. Medical molding factories often use overmolding to improve grip, add insulation, or increase the resilience of parts. This technique is frequently applied to handheld devices and tools that require ergonomic and durable designs. - Insert Molding
Insert molding incorporates pre-formed components, such as metal or other materials, into a plastic molded part. Medical molding factories rely on this technique to produce hybrid components, combining the strength of metal with the flexibility of plastic. It is commonly used in producing surgical instruments and implantable devices. - Liquid Silicone Injection Molding
Liquid silicone injection molding is a specialized process where silicone is heated to a liquid state and then molded into precise shapes. This method is widely used by medical molding factories to create flexible and biocompatible components such as catheters, seals, and tubing. Its ability to produce small, intricate parts makes it invaluable for prototyping and low-volume production.
Through these diverse techniques, medical molding factories ensure the creation of highly specialized medical devices tailored to meet rigorous healthcare standards. Their expertise in these processes underscores their importance in the medical industry.

Medical Molding Factories Quality Assurance Standards
In the context of Medical Molding Factories, Quality Assurance (QA) standards are critical for ensuring that the products manufactured meet the necessary regulatory, safety, and performance requirements. The following is a detailed description of QA standards typically followed in these facilities:
Medical molding factories must adhere to strict regulatory standards to ensure the safety and effectiveness of medical devices. Key regulatory bodies include:
- FDA (Food and Drug Administration) in the United States
- ISO (International Organization for Standardization), specifically ISO 13485, which outlines the requirements for a quality management system (QMS) in the medical device industry
- CE Marking for markets in the European Union
- MDSAP (Medical Device Single Audit Program) for multinational regulatory compliance
These regulations help ensure the products meet safety and effectiveness standards for medical applications.
Material Selection and Traceability
- Raw Materials: The materials used in medical molding are critical to the performance and safety of the final product. Factories must source biocompatible materials such as medical-grade plastics that are safe for direct or indirect contact with patients.
- Traceability: QA standards mandate that the factory maintains full traceability of raw materials, lot numbers, and batch production records. This ensures that if a problem arises with a product, it can be traced back to the source.
Process Validation and Control
- Molding Process: The molding process must be validated to ensure that it consistently produces parts that meet the required specifications. This involves confirming the correct temperature, pressure, cycle times, and material handling during production.
- Control of Environmental Conditions: Factors such as temperature, humidity, and cleanliness must be controlled to prevent contamination and ensure consistent product quality. Cleanrooms may be required depending on the medical device being produced.
- Statistical Process Control (SPC): Continuous monitoring of the molding process using SPC techniques helps identify potential issues before they result in non-compliant products.
Inspection and Testing
- Visual Inspection: Molding products are thoroughly inspected for any visible defects, such as cracks, bubbles, or deformation.
- Dimensional Testing: QA involves measuring the molded products against the specified dimensions to ensure they meet the design requirements. This may include the use of coordinate measuring machines (CMM).
- Functional Testing: Some medical products may require specific functional testing, like pressure testing or load testing, to ensure they perform as expected in real-world conditions.
- Biocompatibility Testing: For products in direct contact with the human body, biocompatibility tests such as cytotoxicity, irritation, and sensitization tests are conducted to ensure the materials are safe.
Inspection of Secondary Operations
Some medical molding processes involve secondary operations such as:
- Assembly: Assembled components must also be inspected for proper fit and function.
- Packaging: Medical products must be packaged in a way that prevents contamination and ensures sterile conditions, if necessary. Packaging materials should meet specific medical packaging standards.
Quality assurance in medical molding factories is a multifaceted process that involves strict adherence to regulatory standards, effective material control, process validation, testing, and documentation practices, as well as ongoing training, audits, and continuous improvement efforts. This rigorous QA system ensures that the products are safe, effective, and suitable for use in medical applications.
Medical Molding Factories: FUJIU Medical Injection Mold and Its Role in Medical Manufacturing
FUJIU Medical Injection Mold stands out as a prominent leader among medical molding factories, offering unparalleled expertise in the production of medical devices. Known for its dedication to precision and quality, FUJIU Medical Injection Mold integrates precision mold medical expertise to provide essential solutions that meet the stringent demands of the medical industry. Our advanced capabilities and commitment to compliance ensure that we remain a trusted partner in the manufacturing of critical healthcare components.
FUJIU Medical Injection Mold Factory
FUJIU Medical Injection Mold is at the forefront of precision medical molding, with state-of-the-art manufacturing facilities designed to meet the highest industry standards. Our factories are equipped with advanced machinery and technology to handle a wide variety of medical-grade plastics, ensuring that every component meets stringent quality requirements.
We pride ourselves on our ISO-certified manufacturing processes, guaranteeing consistent and reliable results across all stages of production. Our team of experts, equipped with extensive material knowledge, works diligently to ensure precise tolerances and flawless finishes for each medical device component.
Key Features of FUJIU Medical Injection Mold Factory:
- Advanced Manufacturing Equipment: Our factories use the latest technology for precise and efficient molding, ensuring optimal performance for every part.
- ISO-Certified Standards: With ISO certification, we maintain the highest standards in quality, safety, and compliance, giving you peace of mind for your medical products.
- Expert Material Knowledge: We specialize in a wide range of medical-grade plastics, offering tailored solutions for your specific needs.
- Fast Turnaround: With rapid prototyping and quick sample delivery, we help you get your products to market faster.
- Low Minimum Order Quantities (MOQ): Our flexible MOQ options support businesses of all sizes, making us the ideal partner for both small and large-scale production runs.
Join over 8,700 medical innovators who trust FUJIU for their medical injection molding needs and elevate your manufacturing process with our precision and dedication to quality.
Commitment to Compliance
Compliance is a cornerstone of FUJIU Medical Injection Mold’s operations. Our company adheres strictly to FDA regulations and holds ISO 13485 certification, demonstrating its commitment to maintaining the highest quality standards. These certifications signify that the products manufactured in their facilities are safe, reliable, and meet all necessary regulatory requirements. Medical molding factories that prioritize compliance, like FUJIU Medical Injection Mold, play a vital role in ensuring patient safety and enhancing the reliability of medical devices.
Why Choose FUJIU Medical Injection Mold?
FUJIU Medical Injection Mold’s reputation among medical molding factories is built on a foundation of precision, compliance, and versatility. By consistently delivering high-quality components and adhering to rigorous medical molding requirements, we have established ourselves as a trusted partner in the medical industry. Whether producing small-scale prototypes or large-scale device components, FUJIU Medical Injection Mold remains at the forefront of innovation, making a significant impact on healthcare advancements.
FUJIU Medical Injection Mold stands out as a leading provider of precision medical molding solutions, offering a range of compelling reasons to choose us for your manufacturing needs:
Precision Molding for Accurate Tolerances
At FUJIU, precision is paramount. Our advanced injection molding technology ensures that every part is produced to the highest tolerances, meeting stringent medical device requirements while maintaining consistency throughout production.
Fast Prototyping and Quick Turnaround
We understand the importance of speed in the medical device industry. FUJIU offers fast sample production and rapid delivery, enabling you to move from concept to market faster than ever before.
Comprehensive Medical Device Assembly
Beyond injection molding, FUJIU also provides full assembly services, streamlining your manufacturing process. We handle everything from component production to final assembly, ensuring seamless integration for your medical devices.
Exceptional Customer Service
We prioritize clear communication and exceptional customer support throughout every stage of the manufacturing process. From initial consultations to post-production assistance, our team is dedicated to ensuring your satisfaction.
Choose FUJIU Medical Injection Mold to elevate your manufacturing process with unmatched precision, fast delivery, and top-tier service.
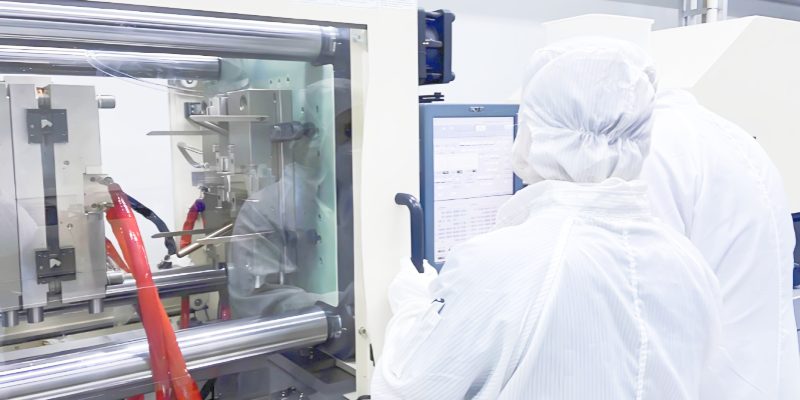
Key Features of Medical Molding Factories
Medical molding factories rely on a combination of advanced technology, precise machinery, and controlled environments to produce medical devices that meet the highest standards of quality and safety. These features are crucial for ensuring the production of reliable, durable, and effective medical components that are compliant with stringent regulatory requirements. Additionally, processes like medical components precision cleaning are vital for maintaining the integrity and sterility of these parts. Below are the key aspects that define the capabilities of medical molding factories.
Advanced Equipment and Technology
One of the defining characteristics of medical molding factories is the use of advanced equipment and technology. Modern molding machines play a critical role in ensuring the accuracy and efficiency required in the production of medical devices. These machines, which can range from electric to hydraulic to hybrid models, allow manufacturers to create components with high precision and repeatability, ensuring that each part meets strict regulatory standards.
- Electric Machines: These machines are known for their energy efficiency, speed, and precision. They are often used in medical molding factories for the production of small, intricate components that require tight tolerances. Electric machines provide consistent results, making them ideal for producing high-volume, high-precision parts such as syringes and diagnostic tools.
- Hydraulic Machines: Hydraulic molding machines are typically used for large, heavy parts. They offer greater force and are well-suited for molding larger medical components like implantable devices and surgical instruments. These machines provide the necessary pressure to create complex parts, making them ideal for medical component molding while maintaining excellent quality.
- Hybrid Machines: Hybrid machines combine the best features of electric and hydraulic systems, offering both energy efficiency and the power needed for large-scale production. Medical molding factories use hybrid machines to achieve a balance between precision and high tonnage, making them suitable for producing a wide range of medical components with varying complexity.
In addition to the machine types, medical molding factories must also ensure that they have the right machinery for large-scale production or for creating smaller, more detailed components. High-tonnage machines are ideal for mass production of standard medical parts, while precision machines are used for producing more intricate components that require meticulous detail.
Clean Room Manufacturing
Another critical feature of medical molding factories is clean room manufacturing, a controlled environment designed to minimize contamination and ensure the highest standards of sterility and quality during production. Clean rooms are essential for manufacturing medical devices, as they help prevent particulate contamination, bacteria, and other foreign matter from affecting the production of medical components.
- ISO Class 7 and Class 8 Clean Rooms: These are the standards of cleanliness required in medical device manufacturing. An ISO Class 7 clean room allows for only 352,000 particles per cubic meter of air, while an ISO Class 8 clean room allows for a higher level of contamination but is still suitable for many types of medical device production. These controlled environments ensure that the molded parts are sterile and free from contaminants, making them safe for use in medical applications.
Medical molding factories employ these clean rooms to manufacture devices such as syringes, catheters, surgical tools, and implants, where sterility is paramount. The clean room environments are equipped with specialized air filtration systems, humidity control, and strict protocols for entry and exit, ensuring that all aspects of the production process meet the required cleanliness standards.
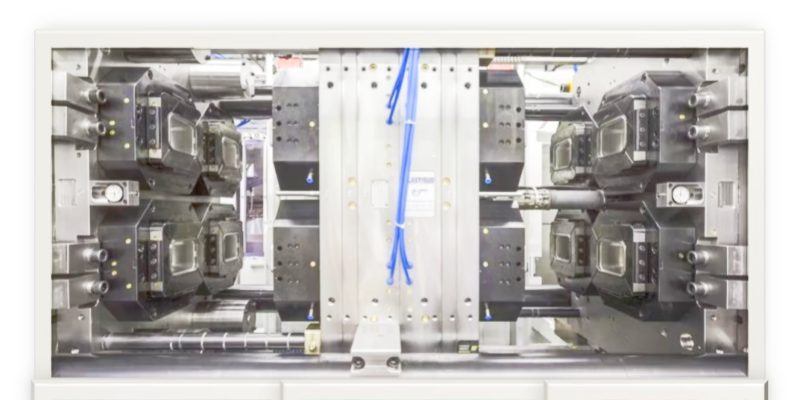
Medical Molding Factories: Medical Products Directory
In the world of medical device manufacturing, medical molding factories play a crucial role in producing a wide array of essential products used in healthcare settings. These factories specialize in precision molding processes that ensure medical components meet the highest standards of quality, safety, and functionality. The Medical Products Directory provides a comprehensive list of common medical items that are typically produced in molding factories. Additionally, medical device plastic manufacturing techniques are employed to produce high-quality plastic components for medical devices. Below are some key examples of products that are molded using advanced molding techniques, such as injection molding, overmolding, and liquid silicone molding.
Syringes
Syringes are among the most common medical devices produced by medical molding factories. These high-precision, disposable tools are essential in delivering medication or fluids in medical procedures. Syringes require the use of injection molding, a process that allows for the production of consistent, sterile, and accurate components. The injection molding process ensures that the syringes have the required dimensions, tight tolerances, and smooth surfaces necessary for safe and efficient use.
In addition to creating syringes, medical molding factories also produce components such as needles and plungers, all designed to meet strict FDA and ISO standards for safety and reliability. The precision and repeatability of injection molding make it the ideal method for manufacturing syringes in high volumes while maintaining consistent quality.
Implants
Implants are another critical category of medical products produced in medical molding factories. These products range from custom surgical implants, such as knee and hip joint replacements, to spinal implants and dental implants. Molding factories use advanced techniques like insert molding and overmolding to create complex, durable implants that meet the specific needs of patients.
Implants must be crafted from materials that are biocompatible, durable, and resistant to body fluids and stress. Materials like PEEK (Polyetheretherketone) are commonly used in implant production due to their strength and resistance to wear, making them suitable for long-term use in the human body. Medical molding factories ensure that implants meet stringent regulatory standards and are manufactured under controlled conditions to guarantee their safety and effectiveness.
Diagnostic Equipment
Diagnostic Equipment includes products like petri dishes, test tubes, and diagnostic kits. These components are often molded for precision and durability, as they play a key role in medical testing, research, and analysis. Medical molding factories specialize in creating such equipment with exact measurements and high clarity to ensure proper function and reliable results in laboratory and clinical environments.
For example, petri dishes must be produced with smooth surfaces and exact dimensions to allow for proper culture growth in microbiology studies. Test tubes and diagnostic kits also require similar precision to ensure that medical professionals can rely on the equipment during testing procedures. Medical molding factories use injection molding and blow molding processes to manufacture these products at scale, ensuring they meet the necessary standards for medical applications.
Catheters and Tubing
Catheters and tubing are essential medical components used for a variety of procedures, including intravenous (IV) insertion, urinary drainage, and feeding. These flexible components are typically made using liquid silicone molding, a process that involves the injection of liquid silicone rubber (LSR) into molds to create flexible, biocompatible parts.
The use of liquid silicone injection molding in medical molding factories allows for the creation of soft, flexible, and durable medical devices that are safe for prolonged contact with the human body. These components are made to withstand exposure to bodily fluids, high temperatures, and sterilization processes, making them ideal for use in sensitive medical applications.
Medical Molding Factories: Why Partner with a Medical Molding Factory?
Partnering with medical molding factories provides several significant advantages for companies in the healthcare industry. From cost-efficiency and regulatory compliance to scalability and quality control, these factories offer critical services that help streamline production while maintaining the highest standards of safety and quality.
Cost-Efficiency
One of the primary reasons to partner with medical molding factories is the cost-efficiency they offer. These factories often utilize highly automated processes that can reduce production costs, particularly in high-volume manufacturing. Automated machinery and streamlined workflows ensure that large quantities of medical components can be produced quickly and with minimal labor costs.
Additionally, by partnering with experienced molding factories, companies can avoid the costs associated with purchasing expensive molding equipment and maintaining in-house production. Medical molding factories have the necessary machinery, expertise, and experience to produce medical products at a much lower cost compared to setting up an internal operation. This enables companies to allocate their resources elsewhere, such as in research and development or marketing, while still benefiting from affordable production.
Regulatory Compliance
In the highly regulated medical industry, regulatory compliance is essential. Partnering with medical molding factories that are experienced in producing medical-grade products ensures that all manufactured components meet the stringent industry regulations. These factories are well-versed in the requirements set by regulatory bodies such as the FDA and CE mark certification. This expertise helps ensure that all products comply with safety standards and quality control guidelines required for medical devices to be sold and used in different regions.
Medical molding factories are equipped with the necessary systems to track and document each step of the manufacturing process. This documentation is crucial for demonstrating compliance during audits and inspections. By partnering with certified and compliant factories, companies can avoid the risks of non-compliance, which could lead to costly fines, delays, or product recalls.
Scalability
Another major advantage of working with medical molding factories is their scalability. Whether a company needs to produce small prototypes or scale up to high-volume manufacturing, molding factories have the flexibility and resources to accommodate these changing needs. From the initial design stage to mass production, these factories can scale production volumes efficiently while maintaining consistency in product quality.
For companies that need to quickly transition from prototype to full-scale production, medical plastic molding factory provide an ideal solution. These factories often have the infrastructure and experience to handle the complexities of scaling production without compromising on the quality or precision required for medical devices. This scalability is crucial for companies that want to bring their products to market faster, without sacrificing the necessary quality standards.
Quality Control
Maintaining quality control is a top priority in the production of medical devices, and medical molding factories, including medical injection molding factory, excel in this area. These factories employ rigorous testing protocols throughout the entire manufacturing process to ensure that all products meet the highest standards of quality. From initial raw material inspections to final product testing, molding medical factories use state-of-the-art equipment and techniques to monitor and verify product quality.
This level of continuous monitoring and testing is essential in the medical industry, where even minor defects can lead to significant consequences for patient safety. By partnering with medical plastic molding factories, companies can be confident that their products will meet the exact specifications and regulatory requirements. This ensures that medical devices perform reliably in real-world applications and reduces the likelihood of costly recalls or legal liabilities.
The Importance of Material Selection in Medical Molding Factories
Material selection is a crucial step in the production of medical devices, as it directly impacts the functionality, safety, and durability of the final product. Medical molding factories must carefully choose the appropriate materials to meet the strict demands of the medical industry, where factors such as biocompatibility, strength, flexibility, transparency, and chemical resistance are paramount. Using the right material ensures that medical products perform as expected in real-world conditions, reduce the risk of adverse reactions, and comply with regulatory standards.
Biocompatibility and Safety
In medical molding, biocompatibility refers to the material’s ability to function within the human body without causing any harmful reactions. It is crucial for materials to be safe when used in medical applications, especially for implants, devices that come into contact with bodily fluids, or anything that might be inserted into the body. Medical molding factories must choose materials that not only meet biocompatibility standards but also maintain their integrity and functionality over time in the body. This helps prevent complications such as inflammation or toxicity, which can compromise patient safety.
Strength and Durability
Medical devices often face mechanical stresses, especially implants and surgical tools, so the materials selected must be strong and capable of withstanding prolonged wear and tear. Materials used in medical molding factory must exhibit strength and durability to ensure that they perform reliably over time, even in challenging environments. The strength of a material ensures that devices like surgical instruments, orthopedic implants, and diagnostic equipment retain their structural integrity and don’t fail under use.
Flexibility and Transparency
In certain medical applications, such as tubing, seals, and gaskets, flexibility is a critical property. Medical molding factories often use materials that can be molded into flexible components that retain their shape but are also adaptable to different forms and functions. Additionally, in some applications, like diagnostic devices or containers, transparency is necessary for visibility, allowing healthcare professionals to see the contents of the medical product.
Chemical Resistance
Medical devices may be exposed to harsh cleaning chemicals, sterilization processes, or bodily fluids, which makes chemical resistance an essential material property. Medical molding factories need to choose materials that are resistant to corrosion, degradation, and wear when exposed to such substances. Materials with high chemical resistance help extend the lifespan of medical devices and prevent the breakdown of materials that could compromise their functionality or safety.
Medical Molding Factories: Common Medical-Grade Materials Used in Molding
Medical-grade materials are specially formulated to meet the stringent safety, durability, and biocompatibility requirements needed for medical applications. These materials are often used in molding processes for items such as medical devices, implants, packaging, and other healthcare products. Below are some common medical-grade materials used in molding:
Medical-Grade Silicone
- Properties: Flexible, biocompatible, resistant to high temperatures, non-reactive with body tissues.
- Applications: Silicone is commonly used for medical tubing, seals, gaskets, and implants. It is also used in the production of prosthetics, catheters, and baby products like pacifiers.
- Molding Process: Silicone molding involves injection molding or compression molding, where the material is heated and injected into molds to form the desired shapes. Liquid silicone rubber (LSR) is often used for precision molding.
Polycarbonate (PC)
- Properties: Transparent, impact-resistant, heat-resistant, lightweight, and durable.
- Applications: Polycarbonate is used for manufacturing surgical instruments, medical device housings, diagnostic equipment, and eyewear lenses.
- Molding Process: Polycarbonate is typically molded through injection molding processes, where the material is heated to a molten state and injected into molds under high pressure.
Polyethylene (PE)
- Properties: Flexible, durable, resistant to chemicals, and has low moisture absorption.
- Applications: Medical-grade polyethylene is often used for orthopedic implants, such as hip and knee replacements, and surgical drapes. It is also used for packaging medical devices.
- Molding Process: Polyethylene is commonly molded using injection molding and extrusion processes. For orthopedic applications, ultra-high molecular weight polyethylene (UHMWPE) is used due to its excellent wear resistance.
Polypropylene (PP)
- Properties: Chemical-resistant, lightweight, rigid, and resistant to fatigue.
- Applications: Polypropylene is used for syringes, drug packaging, medical trays, and surgical instruments. It is often chosen for its chemical resistance and the ability to withstand sterilization processes.
- Molding Process: Polypropylene is typically molded using injection molding, blow molding, or thermoforming processes to create medical device parts or containers.
Polyvinyl Chloride (PVC)
- Properties: Versatile, transparent, resistant to chemicals, and can be made flexible or rigid.
- Applications: Flexible medical-grade PVC is often used in medical tubing, blood bags, and IV bags, while rigid PVC is used for medical device enclosures and components.
- Molding Process: PVC can be molded using injection molding, blow molding, or extrusion processes. Flexible PVC is made by adding plasticizers during processing.
Titanium
- Properties: Biocompatible, corrosion-resistant, lightweight, and strong.
- Applications: Titanium is commonly used in implants such as dental implants, joint replacements, and bone screws. It is also used in surgical instruments.
- Molding Process: Titanium is typically not molded in the same way as plastics due to its high melting point. Instead, it is often formed by casting, forging, or machining into precise shapes for medical applications.
Stainless Steel (Medical-Grade)
- Properties: Corrosion-resistant, durable, and strong. Medical-grade stainless steel is also highly resistant to wear and fatigue.
- Applications: Stainless steel is widely used for surgical tools, implants (such as stents), and orthopedic devices due to its strength and biocompatibility.
- Molding Process: Stainless steel is typically shaped using casting, forging, or machining rather than molding due to its physical properties.
Acrylonitrile Butadiene Styrene (ABS)
- Properties: Rigid, impact-resistant, durable, and can be sterilized.
- Applications: ABS is commonly used in medical device housings, diagnostic equipment, and parts of medical devices like monitors and ventilators.
- Molding Process: ABS is often molded using injection molding, where it is melted and injected into molds to create precise components.
Polytetrafluoroethylene (PTFE)
- Properties: Non-stick, chemical-resistant, and can withstand high temperatures.
- Applications: PTFE is used for components that need to be resistant to chemicals or high friction, such as seals, gaskets, and coatings for surgical instruments.
- Molding Process: PTFE is typically processed through compression molding, ram extrusion, or machining. It is usually in the form of a solid resin or powder that is shaped into the desired form before being sintered at high temperatures.
Polyetheretherketone (PEEK)
- Properties: Biocompatible, wear-resistant, and able to withstand high temperatures.
- Applications: PEEK is used in spinal implants, joint replacements, and other orthopedic devices. It is also used in surgical instruments.
- Molding Process: PEEK is molded using injection molding, where it is heated until molten and injected into molds to form precise parts.
Polyurethane (PU)
- Properties: Flexible, durable, abrasion-resistant, and can be made into both rigid and flexible forms.
- Applications: Polyurethane is used in medical devices like catheters, wound care products, and as coatings for surgical tools.
- Molding Process: Polyurethane is often processed through injection molding, casting, or extrusion, depending on the desired flexibility and form.
Medical-grade materials are selected based on their unique properties, including biocompatibility, durability, flexibility, and resistance to sterilization processes. The molding techniques used to shape these materials depend on their physical characteristics, with injection molding being the most common method for plastics, while metals like titanium and stainless steel are typically cast or machined into shape. These materials and their molding processes are crucial to ensuring the functionality, safety, and reliability of medical devices and equipment.
The selection of materials for molding depends on the specific medical application and the desired properties. Some of the most commonly used materials in medical molding factories include:
- PEEK (Polyetheretherketone): Known for its exceptional strength, biocompatibility, and resistance to high temperatures and chemicals, PEEK is widely used in the production of implants and prosthetics. PEEK is ideal for medical devices that need to endure physical stress, such as knee and hip implants, while offering a high degree of compatibility with human tissue.
- Silicone: With its flexibility and biocompatibility, silicone is frequently used in medical molding for components like catheters, seals, tubing, and gaskets. Silicone’s resistance to extreme temperatures and its ability to conform to various shapes make it ideal for applications that require both flexibility and durability. Liquid silicone injection molding is commonly used to create these parts, ensuring precision and performance.
- Polypropylene: This versatile material is used in the production of syringes, medical containers, and test tubes. Polypropylene offers excellent chemical resistance, is lightweight, and provides sufficient strength for medical applications that involve storage or transportation of fluids and other substances. Its transparency and ease of molding make it an attractive choice for producing medical-grade containers and consumables.
FAQs about Medical Molding Factories
Medical molding is a specialized manufacturing process used to create medical devices, components, and products by shaping materials, such as plastics, rubbers, and silicones, into specific forms. This process plays a vital role in the production of high-quality, precise medical items used in healthcare applications. The most common molding techniques used in the medical industry include injection molding, overmolding, and insert molding. These methods allow for the production of complex shapes with high precision, ensuring that medical products are functional, durable, and compliant with regulatory standards. Medical molding is used for manufacturing items like syringes, surgical implants, diagnostic tools, and tubing. The key advantages of medical molding are its ability to produce high volumes of parts with tight tolerances, reduced waste, and cost efficiency. Additionally, medical molding factories must adhere to strict industry regulations and certifications, such as FDA and ISO 13485, to ensure the safety and quality of the products they manufacture.
Molding in pharmacy refers to the process of shaping or forming pharmaceutical products, such as tablets, capsules, and suppositories, using molding techniques. This method is commonly used to create uniform, consistent, and high-quality dosages of medications that are easy to administer to patients. For example, tablet molding involves compressing powder or granules into a solid form, while capsule molding involves filling gelatin or other material casings with powdered drugs. Additionally, suppository molding is used to create medications in the form of solid masses that are intended to be inserted into body cavities. This molding process ensures that each dose of medication is accurately formulated and shaped, allowing for precise control over the delivery of the drug. Pharmaceutical molding plays a significant role in improving the efficiency of drug production, reducing waste, and ensuring that medications are produced in a sterile and consistent manner, meeting all necessary industry standards and regulations.
The number of molding machines in use around the world varies widely, as it depends on the industry, company size, and production needs. In the context of medical molding factories, the number of machines typically reflects the scale and capacity of the factory. Injection molding machines, which are one of the most commonly used machines for manufacturing medical devices, come in various sizes and configurations to meet different production requirements. These machines range from small desktop models to large, high-tonnage units capable of producing complex medical parts in large volumes. There are also specialized molding machines such as liquid silicone injection molding machines for flexible components like catheters or multi-shot molding machines for creating devices with multiple materials. The total number of molding machines used in medical molding factories can reach into the thousands globally, as companies continuously invest in new technology to meet the growing demand for medical products. These machines are integral to ensuring that medical devices are produced with the highest precision, consistency, and compliance with industry standards.
The medical injection molding market is a rapidly growing segment within the healthcare and manufacturing industries. As of recent market reports, the global medical injection molding industry is valued at approximately USD 10–12 billion, with a projected compound annual growth rate (CAGR) of 6–8% over the next decade. This growth is driven by the increasing demand for precision-engineered medical components that meet stringent regulatory standards. Key products manufactured through medical injection molding include syringes, surgical instruments, implants, catheters, and diagnostic device components.
The demand for disposable medical devices has surged, particularly in light of increased awareness of infection control and hygiene, especially post-COVID-19. Moreover, advancements in polymer science have enabled the development of biocompatible and durable materials that are ideal for medical applications. Cleanroom molding is another significant contributor to market growth, as it ensures contamination-free production environments required for healthcare-grade components.
North America leads the market due to its advanced healthcare infrastructure and high demand for minimally invasive medical devices. However, Asia-Pacific is emerging as a key player, fueled by growing healthcare investments and the availability of cost-effective manufacturing solutions. The combination of innovation, regulatory compliance, and growing demand positions the medical injection molding market for sustained expansion.
Injection molding in the medical field is highly profitable due to the unique demands and value of healthcare-grade components. Medical devices and components often require stringent precision, durability, and compliance with international standards such as ISO 13485. These high standards allow manufacturers to charge premium prices, especially for specialized products like surgical tools, diagnostic components, and implants.
The profitability of medical injection molding is enhanced by the scalability of the process. Once the mold is created, the cost per unit decreases significantly with higher production volumes. This makes the method ideal for manufacturing large quantities of single-use items, such as syringes and catheter components, which are in constant demand.
While initial investments in tooling, cleanroom facilities, and regulatory compliance are high, these costs are quickly offset by the long-term benefits of mass production. Advanced technologies, such as micro-injection molding and multi-material molding, have further improved profitability by enabling the production of complex parts with minimal material waste.
The growing global healthcare market, aging populations, and the rise of chronic diseases have fueled consistent demand for medical devices, ensuring injection molding remains a lucrative field. Companies that invest in innovation, automation, and regulatory expertise can achieve substantial profit margins.
When it comes to medical injection molding, several countries excel due to their advanced technology, quality standards, and cost-effectiveness.
United States: The U.S. is a global leader in medical injection molding, known for its innovation, regulatory compliance, and high-quality standards. Companies in the U.S. specialize in producing complex medical devices and components, supported by cutting-edge technology and cleanroom manufacturing.
Germany: Renowned for precision engineering, Germany is another top player in medical injection molding. The country’s focus on research and development ensures the production of advanced devices, particularly for surgical tools and diagnostic equipment.
China: While primarily known for cost-effective manufacturing, China has made significant advancements in medical injection molding. Its ability to scale production and adopt biocompatible materials has made it a competitive option for medical-grade components.
Japan: Japan’s expertise in robotics and automation makes it a key player in producing intricate medical components with exceptional precision.
Each country has unique advantages. The U.S. and Germany excel in quality and innovation, while China offers cost-effective solutions for high-volume production. Japan and other technologically advanced nations contribute by focusing on precision and automation, crucial for complex medical applications.
The cost of injection molding per hour in the medical field varies significantly based on machine size, cleanroom requirements, material complexity, and location. On average, the hourly cost ranges between $100 and $300 for standard operations, but cleanroom environments can increase this to $500 or more per hour due to stringent contamination controls and specialized equipment.
Factors influencing these costs include:
Machine Size: Smaller machines (50–100 tons) typically cost around $100–$150 per hour, while larger machines (500+ tons) can exceed $300 per hour.
Cleanroom Operations: Medical-grade injection molding often requires ISO-certified cleanrooms to ensure sterility, adding significant overhead costs.
Material Costs: Biocompatible materials such as medical-grade polymers are more expensive than standard thermoplastics, further raising the hourly cost.
Labor and Automation: Skilled labor is necessary to maintain quality standards, and automation can reduce costs in the long term but involves high upfront investments.
Despite the higher costs, the ability to mass-produce critical medical components like syringes, implants, and catheter parts makes the process highly cost-effective for high-volume production. By leveraging economies of scale, medical injection molding ensures competitive pricing for healthcare products without compromising quality.
While injection molding is the gold standard for mass-producing medical components, alternative manufacturing methods may be better for specific applications:
3D Printing (Additive Manufacturing): Ideal for prototyping or creating complex, custom medical components such as patient-specific implants. It is highly versatile and eliminates the need for expensive molds.
Compression Molding: Suitable for large, simple medical parts or components made from thermosetting materials like silicone, often used in medical gaskets or seals.
Blow Molding: Better for producing hollow medical components such as IV bags or oxygen masks.
Micro-Machining: Offers precision for small, intricate parts, particularly for surgical instruments or minimally invasive devices.
Each alternative has advantages depending on production volume, part complexity, and material requirements. However, injection molding remains superior for high-volume, cost-effective production of uniform medical components.
In the medical field, the hardest plastics for injection molding are those with high mechanical strength, chemical resistance, and biocompatibility. Some examples include:
PEEK (Polyether Ether Ketone): Known for its exceptional strength, thermal stability, and biocompatibility, PEEK is widely used in implants and surgical instruments. However, its high melting point and viscosity make it challenging to mold.
Ultem (Polyetherimide): Ultem is used in medical devices requiring high mechanical strength and sterilization resistance. Its stiffness and processing temperatures make it complex to mold.
PTFE (Polytetrafluoroethylene): Commonly known as Teflon, PTFE is difficult to injection mold due to its high melting point and low flow characteristics.
Polycarbonate: While easier to mold than PEEK, polycarbonate poses challenges due to its susceptibility to thermal degradation.
These materials are challenging to process but are crucial for medical applications requiring precision, durability, and compliance with regulatory standards.
Injection molding tooling for the medical industry is expensive due to the high precision, quality, and durability required to meet regulatory and functional standards. The cost of a medical mold can range from $50,000 to $500,000 or more, depending on complexity.
Reasons for high tooling costs include:
Material Quality: Molds are made from hardened steel or aluminum to withstand the high pressures of injection molding and ensure longevity.
Precision Engineering: Medical components demand tight tolerances, requiring advanced machining techniques like CNC milling and EDM.
Cleanroom Compatibility: Molds must meet cleanroom standards, adding extra costs for surface finishes and contamination prevention.
Regulatory Compliance: Medical molds undergo rigorous testing to ensure compliance with FDA and ISO 13485 standards, increasing production time and costs.
Multi-Cavity Design: Molds with multiple cavities are common in medical production to increase efficiency but add complexity and expense.
Despite the high upfront cost, these molds enable mass production of consistent, high-quality medical components, making them a valuable long-term investment.
Injection molding is popular in the medical field due to its ability to produce high-quality, precise, and cost-effective components at scale. Key advantages include:
Precision: It allows for tight tolerances and complex geometries, essential for devices like implants, diagnostic tools, and surgical instruments.
Scalability: The process is ideal for mass production, reducing the per-unit cost of items such as syringes and catheter components.
Material Versatility: Medical injection molding supports a wide range of biocompatible materials, including PEEK, polycarbonate, and silicone, to meet diverse healthcare needs.
Sterility: Molding in cleanroom environments ensures that components are free from contamination, a critical factor in healthcare.
Regulatory Compliance: Injection molding processes can be designed to adhere to FDA and ISO 13485 standards, making it easier to meet regulatory requirements.
Its combination of efficiency, reliability, and adaptability makes injection molding the preferred choice for producing essential medical devices.
The demand for medical injection molding is steadily rising due to advancements in healthcare technology and the growing need for precision-manufactured medical devices. Factors driving this demand include:
Increasing Chronic Diseases: The global rise in chronic illnesses has led to higher demand for devices like insulin pumps, inhalers, and diagnostic tools.
Aging Population: An older demographic requires more medical interventions, increasing the need for syringes, surgical tools, and implantable devices.
Disposable Medical Devices: Single-use items, such as catheters and IV connectors, are in high demand to prevent healthcare-associated infections (HAIs).
Technological Advancements: Innovations in materials and molding techniques, such as micro-injection molding, have expanded the scope of medical applications.
The global medical injection molding market is projected to grow significantly in the coming years, making it a cornerstone of the healthcare manufacturing sector.
The future of injection molding in the medical field is bright, driven by continuous innovation and expanding healthcare needs. Key trends include:
Micro-Injection Molding: The growing demand for smaller, more precise components will drive advancements in micro-molding for applications like minimally invasive surgical tools.
Biodegradable Materials: Increased focus on sustainability will lead to the adoption of eco-friendly and biodegradable polymers in medical injection molding.
Automation: The integration of robotics and AI in molding processes will improve efficiency, reduce costs, and ensure consistent quality.
Customized Solutions: Personalized medicine will require injection molding to produce patient-specific implants and devices.
Emerging Markets: The expansion of healthcare infrastructure in developing regions will fuel demand for cost-effective medical components.
With its ability to adapt to evolving healthcare challenges, injection molding will remain a vital part of medical device manufacturing.
Injection molding, including its use in the medical field, has environmental challenges but also opportunities for sustainability. The primary environmental concern lies in the use of plastic materials, many of which are non-biodegradable. Single-use medical components, such as syringes, catheters, and IV tubes, contribute to medical waste, which is difficult to recycle due to contamination risks.
However, the injection molding process itself is relatively energy-efficient compared to other manufacturing methods. Modern injection molding machines use advanced technology to reduce energy consumption and material waste. Additionally, thermoplastics commonly used in medical applications can be recycled under certain conditions, provided they are uncontaminated.
Efforts to mitigate environmental impact in medical injection molding include:
Biodegradable Materials: Innovations in polymers have led to the development of biocompatible and biodegradable materials, reducing long-term waste.
Energy-Efficient Machines: Newer molding machines are designed to consume less energy, contributing to lower carbon footprints.
Waste Reduction: Techniques like micro-molding reduce material usage while maintaining high precision.
Circular Economy Initiatives: Manufacturers are exploring closed-loop systems for recycling medical-grade plastics.
While injection molding has environmental drawbacks, ongoing advancements and sustainability initiatives are helping to reduce its ecological footprint, especially in critical sectors like healthcare.
Injection molding tools and components in the medical field are designed to last for extensive periods, depending on the application and material used. For molds used in production, the lifespan can range from 500,000 to several million cycles, depending on the mold material and maintenance practices.
Factors influencing the longevity of injection molding in the medical industry include:
Mold Material: Steel molds, commonly used in medical injection molding, have longer lifespans compared to aluminum molds. Hardened steel molds can last for millions of cycles with proper care.
Usage Frequency: High-volume production molds in medical settings may wear out faster but are engineered for durability under repeated use.
Maintenance Practices: Regular cleaning, polishing, and repairing of molds are crucial to maintaining their lifespan in cleanroom environments.
Component Materials: The durability of medical components depends on the plastic material. For example, PEEK and polycarbonate parts are highly durable and resistant to wear.
With proper management, injection molding tools can sustain production for years, ensuring consistent quality and cost-effectiveness in the manufacture of medical devices.
Metal injection molding (MIM) is poised for significant growth in the medical industry due to its ability to produce highly complex and precise metal components. MIM combines the design flexibility of plastic injection molding with the strength and durability of metals, making it ideal for medical applications such as surgical tools, orthopedic implants, and dental components.
Key trends shaping the future of MIM in the medical field include:
Biocompatible Materials: Metals like titanium and stainless steel, which are commonly used in MIM, are biocompatible and ideal for implants and surgical instruments.
Customization: The demand for patient-specific medical devices is driving innovation in MIM to create complex, personalized components with minimal machining.
Miniaturization: Advances in MIM technology enable the production of smaller, more intricate parts required for minimally invasive surgeries and diagnostic devices.
Sustainability: MIM generates less material waste compared to traditional machining, aligning with the industry’s push for eco-friendly solutions.
Additive Manufacturing Synergies: The integration of 3D printing with MIM processes is expected to accelerate prototyping and enhance the development of complex medical parts.
With its versatility and precision, metal injection molding is set to play an increasingly critical role in the evolution of the medical device industry.
Contact our professional team now for a same-day quote and risk-free project evaluation. Benefit from ISO 8 cleanrooms, advanced machines, and 12-hour fast response in medical injection molding.