OEM medical plastic parts play a critical role in modern healthcare, offering solutions that enhance the functionality and safety of medical devices. Guaranteed quality custom OEM medical plastic parts and components excelling in the creation of medical device solutions. As the demand for precision and innovation in medical device manufacturing continues to grow, the need for high-quality, customizable plastic components has never been more vital.OEM medical plastic parts are integral in the creation of a wide range of medical products, from diagnostic tools to surgical instruments. OEM medical plastic parts supplier companies lead the way by providing superior-quality medical supplies that meet stringent regulatory standards. Their expertise in manufacturing durable, biocompatible plastic components ensures the production of reliable devices that contribute to improved patient outcomes and more efficient healthcare solutions.
Low-Volume to High-Volume Production Capabilities
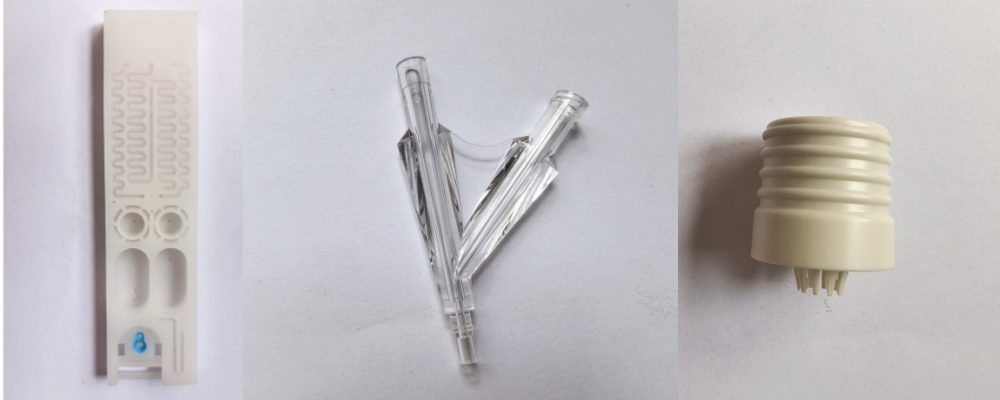
Attribute | Description |
---|---|
Product Name | OEM Medical Plastic Parts |
Place of Origin | Dongguan, Guangdong, China |
Brand Name | LY Medical Injection Mold |
Material Options | ABS, PA66, PP, PC, PMMA, PSU, PCTG, TPE, TPU, PBT, HDPE, Acrylic, Nylon |
Processing Services | Injection Molding, CNC Machining, Cutting, Rapid Prototyping, Assembly, Packaging |
Applications | Medical devices, custom plastic components |
Mold Life | Up to 500,000 shots |
Key Features | - High precision (up to 0.005mm) |
- Advanced technology for rapid prototyping | |
- Wide material and customization options | |
- Tailored services for OEM and ODM clients | |
Customization Options | - Colors: Custom colors |
- Surface Finishes: Texture, smooth, glossy, silk printing, vacuum coating, etc. | |
- Sizes: Customer-specific dimensions | |
Tolerance | 0.005mm - 0.05mm |
Drawing Formats Accepted | STEP, STP, IGS, X-T, STL, CAD, PDF, DWG, and others |
Production Process | Injection molding, deburring, assembly, packaging |
Certifications | ISO9001 |
MOQ | 1 pcs |
Languages Supported | English, Japanese, Spanish, French, Chinese |
Packaging | - Anticorrosive paint and plastic wrap for rust prevention |
- Durable polywood boxes for shipping | |
Delivery Time | Customizable depending on project |
What is OEM Medical Plastic Parts
- Definition and Examples:
OEM medical plastic parts refer to custom-designed plastic components manufactured specifically for use in medical devices and equipment. These include items like precision syringes, diagnostic equipment housings, surgical tool handles, and implantable device components. - Role in Modern Medical Products:
- Provide essential functionalities in devices requiring sterile and precise operations.
- Commonly used in disposable products like IV tubing and long-term solutions like orthopedic implants.
Why Choose Plastic for Medical Devices?
- Advantages of Plastics:
- Lightweight: Easy to handle during medical procedures.
- Cost-Effective: Enables mass production at lower costs without compromising quality.
- Durable: Offers resistance to chemicals and wear, ensuring longevity in critical applications.
- Biocompatible: Suitable for use in direct patient care, meeting safety standards.
- Replacement of Traditional Materials:
- Replaces heavier materials like glass and metal, reducing strain during use.
- Provides enhanced flexibility and customization options.
Both OEM medical plastic parts and OEM plastic medical parts play a transformative role in modern healthcare, ensuring innovation, safety, and accessibility in medical device manufacturing.healthcare delivery.
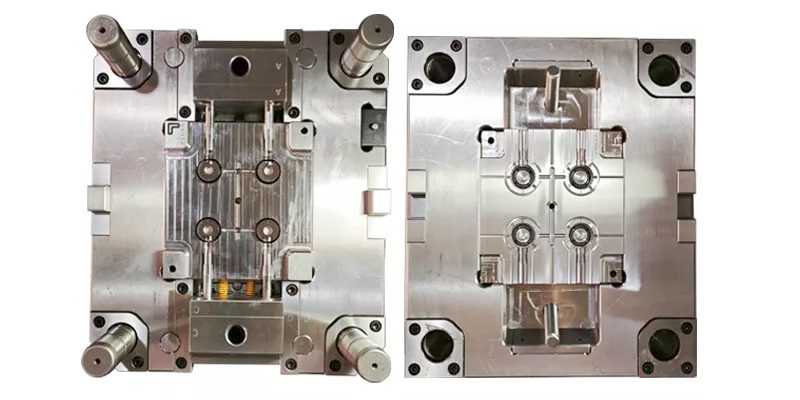
Materials Used in OEM Medical Plastic Parts
Common Medical-Grade Plastics
- Polypropylene (PP):
- Known for its durability and resistance to sterilization, polypropylene is commonly used in items such as syringes and sample collection containers. It is resistant to a wide range of chemicals, making it suitable for disposable medical devices.
- Polyethylene (PE):
- This plastic has high impact resistance, which makes it ideal for prosthetics and implants. Its versatility and chemical resistance allow it to be used in products that come into direct contact with the body.
- Polycarbonate (PC):
- Transparent and impact-resistant, polycarbonate is the preferred material for surgical instruments and medical device housings. Its clarity ensures precision in medical procedures while maintaining durability and strength.
- Polystyrene (PS):
- Cost-effective and easy to mold, polystyrene is widely used in packaging and lab equipment. It provides a safe, sterile, and low-cost solution for medical disposable products, including petri dishes and test tubes.
- Acrylic:
- Ideal for applications requiring high clarity, acrylic is commonly used in microscope slides and protective covers for medical devices. Its optical transparency makes it a top choice for diagnostic tools.
Safety and Compliance
- Regulatory Requirements:
OEM medical plastic parts must meet stringent regulatory standards for biocompatibility and sterility. These materials are tested to ensure they do not cause adverse reactions when in contact with patients. - Autoclavability and Resistance:
Many of the plastics used in OEM medical plastic parts, like polypropylene and polycarbonate, are autoclavable, meaning they can withstand high-temperature sterilization. Additionally, they are resistant to chemicals and heat, ensuring reliability in medical settings.
OEM Medical Plastic Parts Factory
An OEM medical plastic parts factory specializes in manufacturing custom plastic components for the medical industry. These factories ensure that products meet high-quality standards, offering specialized services in designing, molding, and assembling OEM plastic medical parts. An OEM plastic medical parts factory ensures compliance with medical-grade requirements, focusing on durability, precision, and biocompatibility in every product produced, making them a key source for high quality medical plastic parts. By working with a trusted OEM manufacturer, companies can ensure their medical devices are both safe and effective for use in patient care.
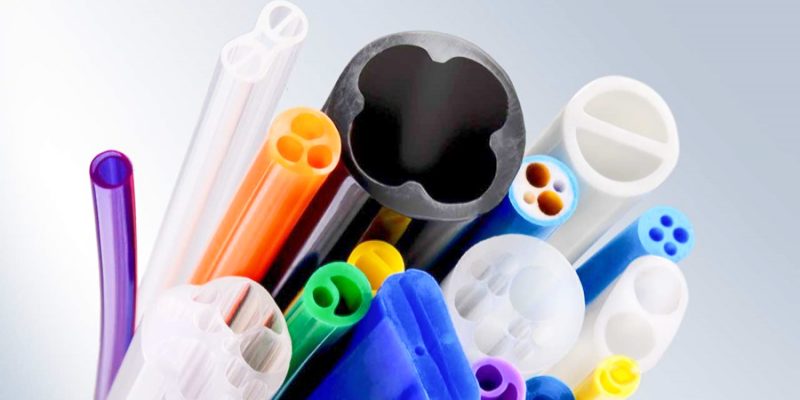
OEM Medical Plastic Parts in a Range of Materials
OEM medical plastic parts are custom-manufactured components that are produced for medical applications, using various types of materials tailored to meet specific requirements. These parts are often made by Original Equipment Manufacturers (OEMs), who specialize in creating high-quality components that are integrated into medical devices, diagnostic instruments, surgical tools, and other healthcare products. The range of materials used in the production of OEM medical plastic parts is diverse, offering unique properties that ensure the functionality, safety, and durability of the devices in which they are used.
The selection of material for OEM medical plastic parts depends on various factors, including the intended application, regulatory requirements, and the mechanical properties needed for the specific device. Common materials used include thermoplastics, thermosets, and elastomers, each offering distinct benefits. Thermoplastics such as polycarbonate (PC), polypropylene (PP), and polyvinyl chloride (PVC) are widely chosen for their ease of molding, strength, and clarity. Polycarbonate, for example, is often used in transparent medical parts such as blood filters and IV connectors due to its high-impact resistance and optical clarity.
Thermosetting plastics like epoxy and phenolic resins are also used in medical applications for their excellent heat resistance and durability. These materials are commonly used for parts that need to withstand higher temperatures or harsh sterilization processes. Elastomers, such as silicone and thermoplastic elastomers (TPE), are frequently chosen for their flexibility, biocompatibility, and ability to provide a tight seal in medical devices. Silicone, in particular, is valued for its ability to maintain its properties in a wide range of temperatures, making it ideal for products like seals, gaskets, and tubing in medical devices.
Manufacturing Processes for Medical Plastic Parts
The manufacturing process for OEM medical plastic parts typically involves precision molding techniques such as injection molding, extrusion, and blow molding. Injection molding is particularly common because it allows for the production of highly detailed and consistent parts at large volumes. In this process, molten plastic is injected into a mold under high pressure, cooling and solidifying to form the final part. The accuracy and repeatability of injection molding make it ideal for producing complex shapes with tight tolerances that are often required in medical applications.
Other methods, such as extrusion, are used for continuous production of parts with consistent cross-sectional profiles, such as tubing and pipes, which are essential components in many medical devices. Blow molding, while not as common as injection molding, is used to create hollow parts like bottles and containers used in medical packaging. Each of these processes ensures that OEM medical plastic parts meet the necessary quality and performance standards required for medical use.
Regulatory Considerations for Medical Plastic Parts
Manufacturers of OEM medical plastic parts must adhere to strict regulatory standards to ensure that their products are safe, effective, and compatible with medical devices. The materials used must meet the biocompatibility requirements set by international standards such as ISO 10993, which evaluates the potential biological risks associated with materials used in medical devices. Additionally, OEMs must follow good manufacturing practices (GMP) to ensure that the production process is consistent and that the parts meet quality assurance protocols.
In addition to biocompatibility testing, medical plastic parts must also meet industry-specific certifications such as CE marking in Europe, FDA approval in the United States, and ISO 13485 certification, which ensures that medical device manufacturers adhere to quality management standards. These certifications are essential for the commercialization of medical devices and their acceptance in different markets worldwide.
Benefits of Using OEM Medical Plastic Parts
The use of OEM medical plastic parts offers numerous benefits to both manufacturers and end users. One of the primary advantages is the ability to tailor the material properties to meet the specific needs of the application. For instance, certain plastics offer superior strength and resistance to chemical degradation, while others provide flexibility and comfort for patient use. Additionally, plastics can be molded into complex shapes, allowing for intricate designs that are both functional and ergonomic.
Another significant advantage is cost-effectiveness. Medical plastic parts are often more affordable than their metal or ceramic counterparts, especially when produced at scale using injection molding. The lightweight nature of plastic also reduces shipping costs and makes handling and assembly easier. Furthermore, plastic parts are often more resistant to corrosion and wear, enhancing the longevity and reliability of medical devices.
OEM medical plastic parts are crucial components in the medical device industry, offering a wide variety of materials, manufacturing processes, and customization options that ensure the safety, durability, and performance of medical devices. By leveraging the right materials and adhering to regulatory standards, manufacturers can create high-quality parts that meet the rigorous demands of healthcare applications.
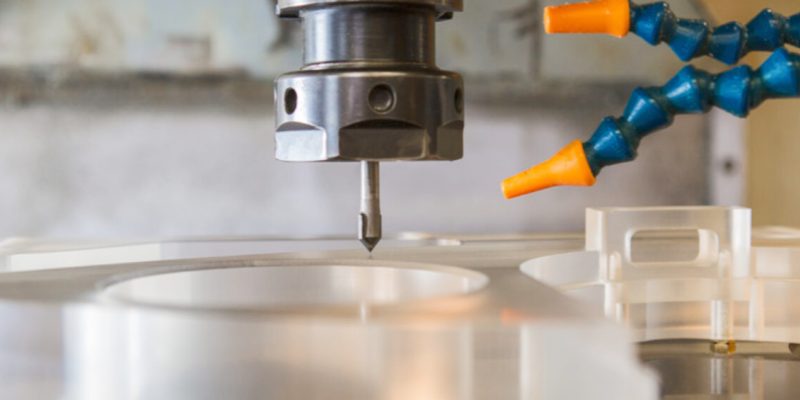
OEM Medical Plastic Parts Engineering
OEM medical plastic parts engineering involves the design, development, and manufacturing of plastic components specifically for medical applications. This field requires a deep understanding of materials science, manufacturing processes, and regulatory requirements, as medical devices rely on these parts to ensure functionality, safety, and patient well-being. The engineering of medical plastic parts is a highly specialized area, as these components must meet stringent standards to be used in life-critical environments, such as hospitals, clinics, and surgical centers.
Design Considerations in OEM Medical Plastic Parts Engineering
The design of OEM medical plastic parts is guided by several critical factors, including material properties, functionality, regulatory requirements, and manufacturability. A key design consideration is biocompatibility, as materials must not cause adverse reactions when in contact with human tissue or bodily fluids. Engineers often refer to biocompatibility standards such as ISO 10993 to select materials that are safe for use in medical applications.
In addition to biocompatibility, the design must consider the mechanical properties of the plastic materials. Medical parts may need to withstand specific stresses, such as pressure, temperature fluctuations, or chemical exposure. For instance, surgical instruments may require high-strength plastics that are resistant to wear, while flexible tubing needs materials that can bend and stretch without breaking or leaking.
The intended use of the part also influences the design. For example, components in disposable medical devices, such as syringes or catheters, need to be designed for single-use functionality and cost-efficiency. On the other hand, parts used in implantable devices must be designed for long-term use and must endure harsh sterilization processes without degrading or losing their effectiveness.
Manufacturing Processes in OEM Medical Plastic Parts Engineering
The manufacturing processes used in OEM medical plastic parts engineering are designed to produce parts that meet the required precision, consistency, and performance standards. Common manufacturing methods include:
- Injection Molding: Injection molding is the most widely used method for producing OEM medical plastic parts. The process involves injecting molten plastic into a mold under high pressure, allowing for the precise and efficient production of complex parts. Injection molding is particularly well-suited for producing high volumes of parts with intricate designs, such as connectors, housings, and fluid control devices.
- Extrusion: Extrusion is used to create continuous profiles, such as tubing, rods, or films. This method involves forcing heated plastic through a die to form a specific shape. Extrusion is ideal for producing long, uniform parts that are often used in diagnostic devices, drug delivery systems, and surgical instruments.
- Blow Molding: Medical blow molding is typically used for creating hollow parts, such as bottles and containers used in medical packaging. In this process, a molten tube of plastic is inflated inside a mold to form the final shape. Although less common than injection molding, blow molding can be used for certain medical applications where hollow components are needed.
- Compression Molding: In compression molding, plastic material is placed into a mold cavity and then heated and compressed to form the final part. This process is typically used for thermosetting plastics and is ideal for producing parts that require excellent heat resistance and dimensional stability.
- 3D Printing: With advances in additive manufacturing, 3D printing has become an increasingly popular method for creating prototypes and low-volume production parts in medical applications. It allows for rapid prototyping, custom designs, and even on-demand production of parts with complex geometries.
Each of these processes offers unique advantages, and the choice of method depends on the part’s complexity, the material being used, the required production volume, and other factors. OEM engineers must assess the most suitable method to ensure that the medical parts meet both performance and cost targets.
Regulatory Compliance and Quality Assurance
Given the critical role that medical devices play in patient care, ensuring that OEM medical plastic parts comply with regulatory standards is a key aspect of the engineering process. Manufacturers must adhere to various regulations depending on the region in which the product will be sold. For example, in the United States, medical plastic parts must comply with FDA regulations for medical devices, while in Europe, they must meet the requirements of the CE marking.
In addition to regulatory compliance, OEM engineers must follow Good Manufacturing Practices (GMP) to ensure that medical parts are produced consistently and to the highest quality standards. This includes maintaining proper documentation, ensuring traceability, conducting regular inspections and testing, and implementing robust quality control procedures. Engineers use various testing methods, including tensile testing, chemical resistance testing, and biocompatibility testing, to ensure that the parts meet the required specifications.
Innovation and Future Trends
As the healthcare industry continues to evolve, OEM medical plastic parts engineering is also advancing. New materials are being developed to meet emerging needs, such as biodegradable plastics for single-use medical devices or advanced antimicrobial plastics to reduce infection risks. Additionally, the integration of smart technologies into medical devices is leading to new engineering challenges, such as incorporating sensors, microelectronics, and wireless capabilities into plastic components.
The future of OEM medical plastic parts engineering will likely see further advancements in material science, manufacturing processes, and regulatory standards. Innovations in 3D printing, for example, could allow for more customizable and complex parts to be produced at lower costs, making personalized medicine a reality. Engineers will continue to push the boundaries of what is possible in order to create more effective, efficient, and patient-friendly medical devices.
OEM medical plastic parts engineering plays a crucial role in the development of medical devices that are safe, effective, and reliable. The process involves careful consideration of material selection, manufacturing techniques, regulatory compliance, and quality assurance to ensure that medical plastic parts meet the highest standards of performance and safety. With ongoing innovations and advancements, the field is set to continue evolving, driving improvements in patient care and medical technology.
The Manufacturing Process of OEM Medical Plastic Parts
Design and Development
- Client Collaboration:
- Work closely with clients to understand their specific needs for OEM medical plastic parts.
- Customize solutions to align with the unique requirements of various medical devices.
- Precision Prototyping:
- Utilize advanced CAD software to accurately transform client concepts into detailed prototypes.
- Ensure that OEM medical plastic parts are designed with exact specifications for optimal functionality and reliability.
- Iterative Feedback:
- Incorporate client feedback throughout the design process to refine and perfect OEM medical plastic parts.
- Conduct multiple design iterations to achieve the highest level of precision and performance.
Custom Plastic Injection Molding
- Versatility in Production:
- Capable of producing complex and intricate designs required for diverse medical applications.
- Support both high-volume and low-volume manufacturing, catering to the scalability needs of OEM medical plastic parts.
- Advanced Molding Techniques:
- Implement state-of-the-art injection molding technologies to ensure consistency and quality in OEM medical plastic parts.
- Utilize precision medical molding to achieve tight tolerances and superior surface finishes.
- Application Examples:
- Manufacture components such as tissue grinders, specimen containers, cytology funnels, and other essential medical supplies.
- Ensure each part meets stringent medical standards and regulatory requirements.
Quality Assurance
- Cleanroom Manufacturing:
- Conduct production in controlled cleanroom environments to maintain sterility and prevent contamination.
- Adhere to Good Manufacturing Practices (GMP) to ensure the highest quality of OEM medical plastic parts.
- Process Validation:
- Implement rigorous validation processes to verify that manufacturing methods meet all regulatory and quality standards.
- Continuously monitor and validate processes to maintain consistency in OEM medical plastic parts production.
- Stringent QC Checks:
- Perform comprehensive quality control (QC) inspections at every stage of production.
- Utilize advanced testing methods to ensure the reliability and durability of OEM medical plastic parts before they reach the client.
OEM Plastic Medical Parts Supplier
- Supplier Expertise:
- Partner with experienced OEM medical plastic parts suppliers who possess in-depth knowledge of medical device manufacturing.
- Ensure that suppliers have the necessary certifications and expertise to produce high-quality OEM medical plastic parts.
- Comprehensive Services:
- Provide end-to-end solutions, including design, molding, assembly, and quality assurance for OEM medical plastic parts.
- Offer flexibility in production processes to accommodate varying client demands and regulatory standards.
- Commitment to Quality:
- Focus on delivering reliable and durable OEM medical plastic parts that meet or exceed industry standards.
- Maintain strong communication and collaboration with clients to ensure satisfaction and successful product outcomes.
- Innovation and Reliability:
- Invest in continuous improvement and innovation to enhance the quality and functionality of OEM medical plastic parts.
- Ensure timely delivery and consistent quality to support the critical needs of the injection molding medical industry.
By following these detailed steps, an OEM medical plastic parts supplier ensures the production of high-quality, reliable, and compliant OEM medical plastic parts that are essential for advancing healthcare solutions.
Applications of OEM Medical Plastic Parts
Key Medical Products
- Centrifuge Bottles for Lab Diagnostics:
- OEM medical plastic parts are fundamental in producing centrifuge bottles used in laboratory diagnostics for separating components like plasma and cells.
- These bottles are designed to be durable, leak-proof, and compatible with various laboratory centrifuge systems.
- Urine Sedimentation Systems for Urinalysis:
- Urine sedimentation systems manufactured using OEM medical plastic parts allow for precise analysis in urinalysis tests.
- These systems are made with high-quality, sterile plastics that ensure accurate and contamination-free results.
- Disposable Cytology Funnels:
- OEM medical plastic parts enable the creation of disposable cytology funnels that facilitate the safe collection and preparation of cellular samples.
- Their single-use design minimizes the risk of cross-contamination while maintaining efficiency during laboratory procedures.
Innovative Solutions
- Hemodrop Blood Dispensers:
- Blood dispensers crafted using OEM medical plastic parts offer innovative solutions for safely handling and dispensing small volumes of blood.
- These dispensers reduce the risk of pathogen exposure while ensuring precise dosing for diagnostic use.
- Tissue Grinders:
- Tissue grinders made with OEM medical plastic parts are used in research and clinical applications to process both soft and tough tissue samples.
- Their robust yet lightweight design allows for efficient sample preparation without compromising sterility.
Role in Medical Supplies
- Integration into Healthcare Settings:
- OEM medical plastic parts are indispensable in various medical supplies used across diagnostic labs, surgical environments, and research facilities.
- Their versatility supports applications ranging from sample handling to patient care, contributing to the overall efficiency and safety of healthcare operations.
OEM Medical Parts Mold: Precision and Efficiency
- What is an OEM Medical Parts Mold?
- OEM medical parts mold refers to the specialized molds used in the production of precise and high-quality medical plastic components.
- These molds are designed for repeatability, ensuring consistent dimensions and performance across large-scale manufacturing.
- Applications of OEM Medical Parts Mold:
- Used to create complex components like syringe barrels, catheter parts, and diagnostic instrument casings.
- Designed with advanced techniques to ensure smooth finishes, tight tolerances, and compatibility with medical-grade plastics.
- Importance of OEM Medical Parts Mold Suppliers:
- A reliable OEM medical parts mold supplier ensures the production of molds that meet regulatory requirements for medical devices.
- Their expertise supports industries in maintaining quality assurance, reducing production time, and enabling cost-effective solutions.
Benefits of Partnering with an OEM Manufacturer for OEM Medical Plastic Parts
Expertise and Reliability
- Industry Leaders with Proven Experience:
- Companies exemplify the expertise required in crafting high-quality OEM medical plastic parts through decades of experience.
- Their ability to design, prototype, and produce innovative medical supplies ensures compliance with stringent global healthcare standards.
- Specialized Knowledge in Medical Applications:
- OEM manufacturers possess deep knowledge of industry requirements, such as sterility, biocompatibility, and regulatory compliance.
- This expertise enables them to produce medical components like diagnostic instrument casings, syringes, and catheter parts with unmatched precision.
- Consistent Quality Assurance:
- Partnering with an OEM manufacturer ensures every piece meets rigorous quality control standards, resulting in reliable and safe products for healthcare applications.
Cost-Effectiveness and Efficiency
- Reduced Operational Costs:
- Outsourcing the production of OEM medical plastic parts to specialized manufacturers significantly reduces the overhead of in-house operations, such as machinery investment and workforce training.
- Streamlined production processes minimize waste and optimize resource use.
- Scalable Manufacturing Solutions:
- OEM manufacturers offer the flexibility to scale production based on demand, accommodating both small-batch requirements for niche applications and large-scale production for high-demand medical supplies.
- Faster Time to Market:
- With access to advanced technologies like injection molding and cleanroom manufacturing, OEM manufacturers can accelerate the production cycle, enabling healthcare providers to deliver critical supplies promptly.
Access to Innovation and Customization
- Tailored Solutions for Unique Needs:
- OEM manufacturers collaborate closely with clients to create custom designs for OEM medical plastic parts, addressing specific needs in medical devices and equipment.
- This level of customization ensures optimal functionality and usability of the final product.
- Integration of Cutting-Edge Technologies:
- Many OEM manufacturers invest in the latest production techniques, such as additive manufacturing and precision mold medical, to enhance product innovation and meet evolving healthcare demands.
By partnering with a reliable OEM manufacturer, businesses can ensure that their OEM medical plastic parts are produced efficiently, cost-effectively, and to the highest standards, ultimately supporting the healthcare industry’s mission to provide safe and effective solutions.
Custom OEM Medical Plastic Parts
Custom OEM medical plastic parts are specially designed and manufactured components tailored to meet the unique needs of specific medical applications. These parts are created by Original Equipment Manufacturers (OEMs) for use in a wide variety of medical devices, ranging from diagnostic tools to implantable devices, and everything in between. The demand for custom plastic parts in the medical industry is growing as medical devices become more specialized, complex, and patient-centered. Custom parts provide the flexibility to design solutions that meet precise functional, regulatory, and aesthetic requirements.
Importance of Customization in OEM Medical Plastic Parts
Customization in OEM medical plastic parts is essential because medical devices have unique specifications that off-the-shelf solutions may not adequately address. Every part must meet stringent functional, regulatory, and safety standards while also considering the specific needs of the patient and healthcare professionals. Customization allows manufacturers to:
- Meet Specific Functional Requirements: Some medical devices require parts with unique shapes, dimensions, and properties to fulfill their intended function. For example, custom plastic parts might need to be flexible, durable, lightweight, or able to withstand harsh sterilization processes. OEMs can choose materials that ensure the part functions optimally in specific environments, such as high-precision surgical instruments, flexible tubing, or wearable medical devices.
- Ensure Biocompatibility: Custom parts must often comply with biocompatibility standards to ensure that the materials do not cause harm when in contact with human tissue. Using specialized materials like medical-grade silicone, polyurethane, or polycarbonate allows engineers to customize parts that are safe for patient interaction, whether for short-term or long-term use.
- Achieve Cost Efficiency: While some generic components may be less expensive upfront, custom parts can be more cost-effective in the long run. By creating parts tailored to the exact specifications needed, manufacturers avoid the inefficiencies of using standardized parts that may require additional modification or fail to meet specific requirements. Furthermore, custom components can be manufactured in bulk using injection molding or other cost-efficient processes, lowering the per-unit cost in high-volume production.
- Improve Patient Comfort and Safety: For patient-facing devices, such as catheters, prosthetics, or infusion pumps, customization allows for design considerations that enhance comfort, usability, and safety. For example, a custom molded plastic part might be designed to fit the natural contours of the body, reducing irritation or discomfort, or to create a secure seal that prevents leakage in critical medical applications.
Materials for Custom OEM Medical Plastic Parts
The selection of materials is one of the most crucial aspects of designing custom OEM medical plastic parts. The materials chosen must fulfill functional requirements such as durability, strength, flexibility, transparency, and resistance to sterilization. Additionally, medical plastics must comply with strict biocompatibility and safety standards. Some of the most commonly used materials for custom medical plastic parts include:
- Polycarbonate (PC): Polycarbonate is often chosen for its strength, impact resistance, and optical clarity, making it an ideal choice for transparent components in medical devices such as blood filters, IV connectors, and diagnostic equipment. It also has good heat resistance, making it suitable for sterilization.
- Polyethylene (PE): Polyethylene is commonly used in applications where flexibility and resistance to chemicals are important, such as in flexible tubing and medical bags. It is also known for being lightweight and durable.
- Polypropylene (PP): Polypropylene is a cost-effective plastic that is used in applications requiring chemical resistance and sterilization capabilities. It is commonly used in medical packaging, syringes, and diagnostic devices due to its ease of manufacturing and ability to withstand autoclaving.
- Medical-Grade Silicone: Silicone is a versatile material that is biocompatible, flexible, and capable of withstanding a wide range of temperatures. Custom silicone parts are commonly used in applications such as seals, gaskets, tubing, and wearable medical devices like sensors or pacemakers.
- Thermoplastic Elastomers (TPE): TPE combines the elasticity of rubber with the processability of thermoplastics. It is often used in applications requiring flexibility, comfort, and durability, such as in patient-contact surfaces and seals for medical devices.
- Acrylic (PMMA): Acrylic is a transparent plastic that offers excellent optical clarity and is often used in parts that require high visibility, such as in medical imaging devices and display panels for diagnostic equipment.
- Ultem (PEI): Ultem is a high-performance plastic known for its strength, dimensional stability, and resistance to high temperatures. It is ideal for critical applications such as sterilization and long-term use in medical devices like ventilators and sterilization trays.
Design and Engineering Process for Custom OEM Medical Plastic Parts
The design and engineering process for custom OEM medical plastic parts involves several key stages to ensure that the final product meets functional, safety, and regulatory requirements. Here’s a breakdown of the typical process:
- Initial Consultation and Requirement Gathering: The process begins with an in-depth discussion between the manufacturer and the medical device company. During this phase, the design team reviews the medical application, its functional requirements, the regulatory standards, and any specific challenges or needs (such as biocompatibility, durability, or sterilization).
- Material Selection: Based on the requirements gathered, the team selects the most suitable materials for the part. The material choice must meet criteria such as strength, flexibility, transparency, and biocompatibility, as well as being cost-effective for mass production.
- CAD Modeling and Prototype Development: Once the material is selected, the design team creates a computer-aided design (CAD) model of the part. This model allows the engineering team to visualize the design in three dimensions and make adjustments to optimize functionality, manufacturability, and cost. After CAD modeling, a prototype is often produced using 3D printing or CNC machining to test fit, functionality, and performance.
- Testing and Iteration: The prototype undergoes rigorous testing to ensure it meets all the functional and safety requirements. This includes testing for biocompatibility, mechanical properties, resistance to sterilization, and performance under real-world conditions. Based on the results, adjustments may be made to the design to improve performance or address any issues.
- Manufacturing and Production: After the design is finalized and the prototype is validated, the part moves into the production phase. The most common manufacturing method for custom OEM medical plastic parts is injection molding, which allows for high-volume production of precise parts with minimal variation. Other methods like extrusion or blow molding may be used depending on the part’s shape and functionality.
- Quality Control and Regulatory Compliance: During the manufacturing process, stringent quality control procedures are in place to ensure that the parts meet both internal quality standards and regulatory requirements. This includes routine inspections, testing, and certification to ensure compliance with FDA and ISO standards.
Applications of Custom OEM Medical Plastic Parts
Custom OEM medical plastic parts are used in a wide range of applications within the medical device industry. Some common examples include:
- Diagnostic Equipment: Components for medical imaging devices, diagnostic instruments, and lab equipment, where clarity, precision, and durability are essential.
- Surgical Instruments: Custom plastic handles, housings, and grips for surgical tools, designed to be lightweight, ergonomic, and resistant to sterilization.
- Implantable Devices: Custom parts for pacemakers, stents, and prosthetics, which require biocompatibility and long-term durability.
- Drug Delivery Systems: Syringes, inhalers, and infusion pumps with precision-engineered components that ensure safety, accuracy, and reliability.
- Patient Monitoring Devices: Custom plastic components for wearable sensors, blood pressure cuffs, and ECG electrodes that offer comfort, flexibility, and ease of use.
Custom OEM medical plastic parts are critical in the development of safe, effective, and patient-friendly medical devices. By selecting the appropriate materials, employing advanced design and manufacturing processes, and ensuring regulatory compliance, custom plastic parts contribute to the overall functionality, performance, and success of medical devices. The ability to customize parts allows manufacturers to create solutions that meet specific medical needs, providing a competitive edge in the rapidly evolving healthcare market.
FAQs about Oem Medical Plastic Parts
A medical OEM (Original Equipment Manufacturer) is a company that designs, manufactures, and supplies medical devices or components that are then branded and sold by another company. Essentially, medical OEMs produce the critical parts or entire products which other companies may market under their own brand names. This is particularly prevalent in the medical industry where precision, reliability, and regulatory compliance are paramount. Medical OEMs often specialize in various fields like surgical instruments, diagnostic equipment, prosthetics, and more, ensuring that their products meet stringent healthcare standards and certifications.
The best plastic for medical devices depends on the specific application and requirements, but common choices include Polycarbonate (PC), Polyethylene (PE), and Polypropylene (PP). Each type of plastic offers distinct advantages. For example, Polycarbonate is highly durable and transparent, making it ideal for use in medical containers and device housings. Polyethylene is often chosen for its flexibility and resistant properties, suitable for tubing and disposables. Polypropylene is widely used due to its strong chemical resistance and sterilization capabilities. Ultimately, the choice of plastic will be guided by factors such as biocompatibility, mechanical properties, sterilization method, and regulatory approval.
OEM plastic refers to the plastic materials used by Original Equipment Manufacturers in the production of parts or products. These plastics are selected based on the requirements of the end product and the specific needs of the application. In the context of medical devices, OEM plastic must adhere to strict regulatory standards and exhibit properties such as biocompatibility, durability, sterility, and resistance to chemicals and radiation. OEM plastic manufacturers often work closely with medical device companies to ensure that the materials meet all necessary performance and safety criteria.
Medical grade plastic is specifically engineered to meet the rigorous standards required for medical devices and equipment. Common types of medical grade plastics include Polycarbonate (PC), Polyethylene (PE), Polypropylene (PP), Polytetrafluoroethylene (PTFE), and Polyetheretherketone (PEEK). These materials are characterized by their high performance, biocompatibility, and ability to withstand various sterilization processes. Each type of medical grade plastic is chosen based on its unique properties and suitability for different medical applications, ranging from surgical instruments and implants to diagnostic devices and disposables. The term “medical grade” ensures that the plastic is safe for use in the human body or in medical environments, meeting regulatory standards set by organizations such as the FDA and ISO.
In the medical field, many supplies are made from plastic due to its versatility, durability, and ease of sterilization. Common examples include syringes, IV tubes, catheters, blood bags, and disposable gloves. Additionally, plastic is used in medical devices such as diagnostic test tubes, petri dishes, and surgical instruments. Polycarbonate and polypropylene are often used for implantable devices and prosthetics. These plastics are chosen for their non-reactivity, transparency, and ability to withstand various sterilization processes such as autoclaving and gamma radiation.
An OEM (Original Equipment Manufacturer) typically produces parts or components that are integrated into a final product by another company, which markets it under its own brand. In the medical field, an OEM might manufacture specialized surgical tools, implants, or components for diagnostic equipment. A manufacturer, on the other hand, handles the entire production process, including assembly, and often sells the finished products directly to consumers or other businesses. For example, a manufacturer might produce and sell complete medical devices, while an OEM may provide components for those devices.
OEM stands for “Original Equipment Manufacturer.” In the context of the medical industry, this term refers to companies that design and produce components or products used in medical devices or equipment, often for other companies to market under their brand name. These products could include diagnostic instruments, implantable devices, and surgical instruments. OEMs are essential in providing high-quality, specialized parts that meet strict regulatory standards for medical applications.
Hospitals use various types of plastic to ensure safety, efficiency, and hygiene. Common plastics include polyvinyl chloride (PVC), often used in IV bags, tubing, and blood bags; polypropylene (PP), used in syringes and medical containers; and polyethylene (PE), commonly used in disposable gloves and medical wraps. Polycarbonate is used in equipment that needs durability and transparency, such as surgical instruments, while silicone is widely used for flexible products like catheters and seals. These plastics must meet stringent medical-grade standards to ensure they are biocompatible and safe for patient use.
The four main types of plastic commonly used in the medical field are polyethylene (PE), polypropylene (PP), polyvinyl chloride (PVC), and polystyrene (PS). Polyethylene is often used for packaging, gloves, and medical wraps due to its flexibility. Polypropylene is used in syringes and medical containers due to its chemical resistance and heat tolerance. PVC is essential for medical tubing, IV bags, and blood bags. Polystyrene is commonly used for laboratory dishes and medical packaging due to its clarity and low cost. Each plastic type is selected based on its properties for specific medical applications.
Medical-grade plastics are identified through rigorous certification processes and compliance with regulatory standards such as ISO 10993 and USP Class VI. These plastics undergo extensive testing for biocompatibility, ensuring they do not cause adverse reactions when in contact with body tissues or fluids. Additionally, medical-grade plastics must withstand sterilization processes like autoclaving or gamma radiation without degrading. Suppliers usually provide documentation proving that their plastics meet the necessary medical-grade standards. In many cases, the plastic will be labeled or specified as medical-grade in product specifications or regulatory filings.
Contact our professional team now for a same-day quote and risk-free project evaluation. Benefit from ISO 8 cleanrooms, advanced machines, and 12-hour fast response in medical injection molding.