Injection molding plays a crucial role in modern manufacturing, particularly in the production of medical devices. This method allows manufacturers to produce precise, high-quality medical components at scale, meeting the stringent demands of the healthcare industry. Medical device injection molding has revolutionized the way critical components like syringes, catheters, and surgical instruments are created, ensuring accuracy, durability, and biocompatibility. Precision mold medical techniques are particularly vital in this process, ensuring that each part is manufactured to the highest standards of precision and quality. By utilizing advanced technologies, medical injection molding factories can deliver cost-effective and reliable solutions for both large-scale production and custom medical applications. In this blog, we’ll explore key players in the industry, focusing on the capabilities of medical molding, the crossover with automotive injection molding, and the latest technological advancements in the field of medical injection molding factories. FUJIU Medical Injection Mold is a trusted medical injection molding factory, offering high-precision plastic molding for medical devices and components.
Medical Injection Molding at the Medical Injection Molding Factory
Medical injection molding is a manufacturing process that involves injecting molten material, typically plastic or metal, into a mold to create medical components. This technique enables the production of highly detailed, precise, and complex parts that meet the strict demands of the medical industry. In a medical injection molding factory, the process ensures high-quality outcomes while maintaining efficiency and reducing waste.
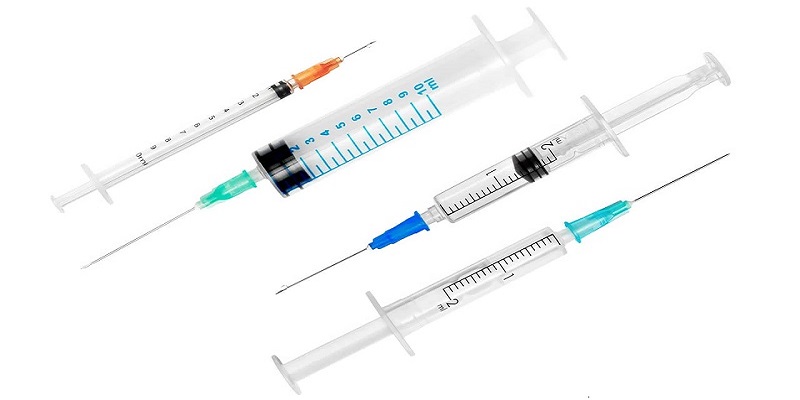
Advantages of Medical Injection Molding
Medical injection molding offers several key advantages that make it the preferred manufacturing process for producing high-quality, reliable, and cost-effective medical devices and components. From tight tolerances and intricate designs to scalability and the use of biocompatible materials, this process addresses the diverse needs of the medical industry. Below, we will explore these advantages in greater detail.
Precision and Tight Tolerances
One of the most significant advantages of medical injection molding is its ability to produce components with high precision and tight tolerances. In the medical industry, where accuracy is critical, this capability ensures that each part fits together seamlessly, performs its intended function, and complies with stringent regulatory standards.
Detailed Description: Medical devices and components often require intricate details and high precision to perform specific functions. Injection molding achieves this by using advanced machinery that precisely controls the injection of molten plastic into molds, ensuring that the finished parts meet exact specifications. This precision is crucial for medical applications where even the slightest deviation could result in failure or safety concerns. The ability to maintain tight tolerances over high-volume production runs makes injection molding an ideal choice for medical manufacturers.
Cost-Effectiveness for High-Volume Production
Medical injection molding is highly cost-effective, particularly when producing large quantities of components. The process minimizes material waste, reduces labor costs, and optimizes production efficiency, making it a viable option for manufacturers aiming to meet the high demand for medical devices at a competitive cost.
Detailed Description: For high-volume production, medical injection molding offers significant cost savings. Once the mold is designed and set up, the cost per unit decreases as the production scale increases. This makes it an efficient choice for creating large quantities of medical devices like syringes, catheters, and surgical instruments. The automation of the injection molding process reduces manual labor and operational costs, further improving profitability for manufacturers. As the healthcare industry continues to grow, the ability to produce high-quality medical devices at scale and at a reduced cost is a critical factor in the success of many manufacturers.
Scalability and Flexibility
Another advantage of medical injection molding is its scalability, which allows manufacturers to adjust production volumes easily based on market demands. Whether it’s a small batch for prototype testing or a large-scale production run, the injection molding process can accommodate both without significant changes to the setup or workflow.
Detailed Description: Medical injection molding is incredibly flexible and adaptable, making it suitable for various production requirements. When production needs change, manufacturers can scale up or down without incurring significant delays or extra costs. For example, if a manufacturer needs to increase the number of units due to a rise in demand for a particular medical device, the process can be adjusted accordingly without compromising the quality of the product. This scalability ensures that manufacturers can respond quickly to changing market conditions, while still maintaining efficiency and high standards of quality control.
Biocompatibility and Material Selection
The materials used in medical injection molding, such as medical-grade plastics and silicones, are biocompatible, meaning they do not cause harm or adverse reactions when in contact with the human body. This is particularly important for medical devices that interact directly with patients, such as implants, drug delivery devices, and surgical tools.
Detailed Description: Medical injection molding utilizes a range of biocompatible materials that meet the safety and performance standards required for medical applications. Materials like polycarbonate, polypropylene, and medical-grade polyethylene are commonly used, as they are durable, safe, and resistant to sterilization methods like autoclaving. These materials are chosen for their ability to maintain their integrity and performance under medical conditions, ensuring that devices made from them are both safe and effective. By selecting the right materials, manufacturers can ensure that the final products meet both regulatory requirements and patient safety standards.
Medical injection molding stands out as an ideal manufacturing process due to its precision, cost-effectiveness, scalability, and the use of biocompatible materials. These advantages make it a reliable and efficient choice for producing high-quality medical devices and components in the healthcare industry. As medical technology continues to advance, injection molding will remain a crucial process for manufacturers looking to meet the increasing demand for safe, reliable, and cost-effective medical products.
Materials Used in Medical Injection Molding
Medical injection molding uses a wide range of materials depending on the specific requirements of the medical device. Medical injection molding polymers, a specialized category of polymers designed for medical applications, are increasingly being used due to their tailored properties, such as enhanced strength, biocompatibility, and resistance to harsh sterilization processes. The selection of materials in medical device injection molding factories is critical, as it directly impacts the performance, safety, and quality of the final product.
Common Materials Used in Medical Injection Molding
Medical-grade plastics are the backbone of most medical injection molding processes. Some of the most widely used materials include:
- Polyethylene (PE): This plastic is known for its durability, flexibility, and resistance to chemicals, making it suitable for a wide variety of medical components such as surgical instruments, containers, and packaging.
- Polypropylene (PP): Polypropylene is another versatile material often used in medical applications due to its resistance to chemical and biological contaminants. It is frequently used in the production of diagnostic devices, syringes, and medical packaging.
- Polycarbonate (PC): Known for its strength, transparency, and impact resistance, polycarbonate is commonly used in devices that require clear components, such as blood oxygenators and surgical trays.
- Silicones: Silicones are often used for their flexibility, resistance to temperature variations, and biocompatibility. They are ideal for products that need to be flexible and elastic, such as seals, tubing, and implants.
- Thermoplastics: Other thermoplastic materials, like polyamide (nylon), polystyrene (PS), and acrylonitrile butadiene styrene (ABS), are also utilized in medical injection molding. These materials offer varying degrees of strength, flexibility, and transparency, making them suitable for a wide range of applications, from diagnostic tools to medical device housings.
- Medical Injection Molding Polymers: These specialized polymers are designed specifically for medical applications. They are formulated to offer properties like enhanced strength, biocompatibility, and resistance to sterilization methods. Some examples include polyetheretherketone (PEEK) and ultrahigh-molecular-weight polyethylene (UHMWPE), which are used in demanding applications such as implants and prosthetics.
Key Characteristics to Consider When Selecting Materials
When selecting materials for medical injection molding, several key characteristics must be considered to ensure the material is suitable for the intended application and meets medical standards. These include:
- Biocompatibility: The material must be compatible with human tissue and body fluids without causing adverse reactions. This is crucial for components that will have direct contact with patients, such as implants, catheters, or surgical tools.
- Durability: Medical devices often need to withstand wear and tear over time, including exposure to sterilization methods like autoclaving, gamma radiation, or ethylene oxide (EtO) sterilization. Therefore, the material must have high resistance to chemical degradation, abrasion, and fatigue.
- Sterilization Resistance: Since many medical devices need to be sterile, the material chosen must be capable of enduring harsh sterilization processes without compromising its properties or safety. This includes resistance to high temperatures, chemicals, and radiation.
- Strength and Flexibility: Depending on the application, medical devices may require materials that are either flexible (e.g., tubing, seals) or strong (e.g., structural components, implants). Materials should be selected based on the mechanical properties needed for the specific device.
- Transparency: Some medical devices, such as diagnostic tools or drug delivery devices, require transparent materials for easy visualization of fluids or internal components. Polycarbonate, for example, is often selected for this property.
- Regulatory Compliance: Materials used in medical injection molding must meet regulatory standards such as those set by the U.S. Food and Drug Administration (FDA), ISO 13485, and other global standards. This ensures that the materials are safe for use in medical applications and that the final product meets strict quality and safety requirements.
The materials chosen for medical injection molding play a vital role in the performance, safety, and reliability of medical devices. Understanding the specific requirements of each application is crucial for selecting the right materials, ensuring that the final product meets both medical and regulatory standards.
Medical Injection Molding Factory: Automotive Injection Molding and its Cross-Industry Applications
Automotive injection molding is a widely used manufacturing process that involves creating parts by injecting molten materials, typically plastics or metal, into molds. This process is crucial in producing durable, high precision medical components required in the automotive industry. Interestingly, the technologies developed in the automotive sector have significant crossover with the medical industry, offering numerous advantages for medical device manufacturing.
Overview of Automotive Injection Molding and its Cross-Industry Applications
Automotive injection molding is commonly used to produce components such as dashboard parts, interior trims, exterior panels, and various mechanical components. The precision and efficiency of the process have made it indispensable in the automotive sector. These same capabilities, however, are also valuable in plastic medical device manufacturing. The techniques developed for automotive parts, such as high-speed production and precise molding, have been adapted to meet the stringent requirements of medical devices, leading to high-performance components that also meet medical industry standards.
In a medical injection molding factory, the same advanced technology used for automotive applications can be applied to create critical medical components. For instance, plastic parts that need to endure high pressure, mechanical stress, or exposure to chemicals can benefit from the innovations in automotive molding. The shared focus on precision and quality assurance makes the adaptation of automotive molding techniques for medical applications highly effective.
Benefits of Automotive Molding Techniques for Medical Applications
The automotive industry’s experience with injection molding offers several key benefits that can be leveraged in medical device production:
- High Durability: Automotive parts are designed to withstand harsh environments, heavy usage, and mechanical stress. These characteristics make automotive molding techniques ideal for producing medical components that require similar durability, such as orthopedic devices, surgical instruments, and diagnostic tools.
- Heat Resistance: Many automotive components are subjected to extreme temperatures, and the materials used in automotive molding are specially designed to resist high heat. In the medical field, this heat resistance is critical for devices that will be exposed to autoclaving processes or require high-performance polymers to withstand varying temperatures in medical environments.
- Precision: Automotive injection molding emphasizes precision, ensuring that each part fits perfectly within the larger system. This high level of accuracy is also crucial in medical device manufacturing, where even the smallest deviation can affect the functionality of the device and patient safety.
Examples of Automotive Injection Molding Companies that Provide Medical Molding Services
Several automotive injection molding companies have expanded their operations to include medical molding services. These companies are able to leverage their deep expertise in high-precision, high-performance manufacturing techniques to provide solutions for medical device manufacturers.
Role of Medical Injection Molding Factory in the Medical Industry: Applications and Impact
Medical injection molding plays a crucial role in the production of various medical devices and components, thanks to its precision, scalability, and cost-effectiveness. Medical injection molding factories are responsible for manufacturing high-quality, durable components that are essential for the functioning of modern medical technology. From diagnostic equipment to surgical instruments and patient monitoring devices, the products created by these factories are integral to providing reliable and effective healthcare solutions. Investing in a medical injection molding business for sale offers a unique opportunity to contribute to this critical industry while tapping into its growing demand and innovative potential. Below, we explore the diverse applications of medical injection molding products and their role in the medical industry.
Diagnostic and Laboratory Equipment
Medical injection molding is extensively used in the production of diagnostic equipment, which requires precise and reliable components to ensure accurate results. Components such as test tubes, beakers, pipettes, and sample containers are manufactured using medical-grade plastics. These products must meet strict regulatory standards to ensure they are safe for use in diagnostic testing environments.
In addition to basic laboratory supplies, medical injection molding factories also produce parts for advanced diagnostic machines, such as blood analyzers and molecular diagnostic equipment. These devices rely on intricate and highly durable components made from biocompatible materials that can withstand sterilization and provide consistent performance over time.
Surgical and Patient Monitoring Equipment
Another important application of medical injection molding is in the production of surgical instruments and patient monitoring devices. Surgical tools like forceps, scissors, and clamps often require injection-molded plastic parts that are both lightweight and durable. Injection molding allows for the production of these components with high precision, ensuring they function effectively during procedures.
Patient monitoring equipment, such as heart rate monitors, infusion pumps, and thermometers, also rely on medical injection molding. The accuracy and reliability of these devices are paramount, and the components created by medical injection molding factories ensure that these systems remain functional, safe, and durable in critical medical settings.
Implants and Prosthetics
Medical injection molding is increasingly used in the production of implants and prosthetic components. These devices need to be tailored to the specific needs of individual patients, which makes the flexibility of injection molding particularly advantageous. For example, custom implants such as orthopedic joint replacements or dental implants require parts that are both biocompatible and capable of withstanding the stress placed on them by the human body.
Injection molding allows medical manufacturers to produce these complex components in a cost-effective manner while maintaining the high-quality standards necessary for such critical applications. The use of medical-grade plastics ensures that implants and prosthetics are safe for implantation and provide long-term functionality.
Drug Delivery Systems
Medical injection molding also plays a vital role in the production of drug delivery systems. These systems, which include devices such as insulin pens, inhalers, and syringes, are essential for patients who require ongoing medical treatment. The components involved in drug delivery systems must be designed with great precision to ensure proper dosage, ease of use, and safety.
Injection molding is used to create both the outer casings and the internal mechanisms of these devices. The materials used are often designed to be biocompatible and resistant to corrosion, ensuring that the devices can safely handle medications and perform reliably over time.
Personal Protective Equipment (PPE)
Personal protective equipment (PPE) is crucial in healthcare settings to ensure the safety of medical professionals and patients. Injection molding is used to produce various types of PPE, including face shields, goggles, and respirators. These items need to be lightweight, comfortable, and durable, which is made possible through the use of medical-grade plastics and injection molding technology.
Medical injection molding factories produce high-quality PPE components that meet safety standards and offer maximum protection in healthcare environments. The precision of injection molding ensures that these components are manufactured to fit securely, providing the necessary protection to prevent the spread of infectious diseases.
Medical injection molding factories are integral to the healthcare industry by providing a wide range of high-quality, reliable products used across various medical applications. From diagnostic equipment and surgical instruments to drug delivery systems and PPE, the precision and versatility of medical injection molding ensure that these products meet the highest standards of safety, performance, and durability. The widespread use of injection-molded medical products in the industry highlights their importance in improving patient care, ensuring healthcare professionals have access to the best tools, and helping to drive innovation in medical technology.
Medical Injection Molding Factory: Insert Molding in Medical Device Manufacturing
Medical device plastic injection molding factory is a highly specialized process used in manufacturing that involves the molding of plastic around pre-existing components, such as metal or electronic inserts. This process allows for the creation of more complex and functional parts by integrating different materials into a single component. Insert molding has become an essential technique in the production of various medical devices due to its ability to combine diverse materials and improve the overall functionality of medical components.

Definition of Insert Molding
Insert molding, in its simplest form, refers to the process where a pre-formed material (typically metal, ceramic, or electronic components) is placed into a mold, and then plastic is injected around it. Once the plastic cools and solidifies, it forms a finished part that includes both the insert and the molded plastic. This process is widely used for creating parts that require the combination of plastic’s lightweight and versatility with the durability and conductivity of metal or the precision of electronic components.
In a medical injection molding factory, insert molding is often utilized to produce medical components that require both structural integrity and specialized functions. For example, inserts may be used in parts like surgical instruments, diagnostic devices, and implantable devices, where the combination of materials can provide the needed strength, precision, and functionality.
Applications in the Medical Field
Insert molding has numerous applications in the medical device manufacturing sector, enabling the production of highly functional and precise components. Some common applications include:
- Diagnostic Tools: Medical devices like thermometers, blood glucose monitors, and diagnostic test strips often require the integration of metal or electronic inserts. Insert molding allows manufacturers to combine medical-grade plastics with conductive materials or sensors, resulting in devices that are both durable and capable of performing specialized tasks.
- Pacemakers and Infusion Pumps: In devices such as pacemakers or infusion pumps, insert molding is crucial for combining plastics with electronic components. This integration ensures that the device functions properly while maintaining biocompatibility, which is vital for patient safety. The precision of insert molding ensures that each part fits perfectly, reducing the likelihood of failure and ensuring long-term reliability.
- Surgical Instruments: Many surgical tools require the combination of metal inserts for strength and plastic components for comfort and functionality. Insert molding is ideal for producing these types of tools, as it ensures that the parts are securely integrated, reducing the need for additional assembly and improving overall efficiency in manufacturing.
Advantages of Insert Molding in Medical Device Manufacturing
Insert molding provides a number of benefits in the medical device industry, making it a preferred manufacturing technique for complex medical components:
- Enhanced Functionality: By integrating metal or electronic components directly into the molded plastic part, insert molding enables medical devices to offer superior functionality. This is particularly important in medical devices that require both strength and the integration of electronics, such as diagnostic equipment, pacemakers, and infusion pumps.
- Reduced Assembly Time: One of the most significant advantages of insert molding is the reduction in assembly time. Since the insert and the plastic are molded together in a single process, there is no need for secondary assembly operations. This not only speeds up production but also reduces the likelihood of errors, leading to more consistent product quality.
- More Complex Designs: Insert molding allows for the creation of more intricate and complex designs that would be difficult or impossible to achieve with traditional molding techniques. The ability to combine different materials within a single part allows for greater flexibility in design, making it easier to meet the demanding specifications required by medical devices.
Injection Molding Medical Industry Factories: The Role of Medical Factories
Injection molding has become a pivotal process in the medical industry due to its ability to produce high-quality, precise, and biocompatible components. China medical molding factories specializing in injection molding are equipped with cleanroom environments and advanced technologies to ensure the production of components that meet stringent industry standards, such as ISO 13485. These factories play a crucial role in enabling the manufacturing of medical devices like surgical tools, diagnostic equipment, catheters, and infusion pumps.
The controlled environment of China medical molding factories minimizes contamination risks and ensures product integrity, which is vital for applications where hygiene and sterility are paramount. With their expertise in injection molding, these factories contribute significantly to the production of medical devices that meet the highest standards of safety and quality, ensuring that these products are safe for use in sensitive healthcare settings.
Precision and Consistency in Medical Component Production
Medical factories use state-of-the-art equipment and specialized molding techniques, such as multi-shot injection molding and insert molding, to produce components with tight tolerances and high precision. These processes not only enhance the mechanical properties and performance of medical devices but also ensure that each part is consistent and reliable. The use of high-quality medical-grade materials like silicones, thermoplastics, and medical-grade plastics in injection molding medical industry factories allows for superior part durability, biocompatibility, and ease of sterilization. By maintaining strict process controls, these factories can deliver components that meet the exacting requirements of medical applications, from small, intricate parts to larger, complex assemblies.
The Role of Cleanroom Environments in Medical Injection Molding Factories
Cleanroom environments within medical plastic injection molding factories are designed to maintain strict cleanliness levels necessary for the production of medical components. These environments are essential to prevent particle contamination, ensuring that the final products are safe for use in medical applications. The cleanroom setting also supports the use of specialized molding techniques that require precise temperature, pressure, and material control. This enables manufacturers to produce components with consistent quality and reliability. By investing in cleanroom technologies, medical injection molding factories can maintain the highest standards of product quality, reduce the risk of defects, and ensure compliance with industry regulations like ISO 13485.
Benefits of Medical Injection Molding Factories to the Healthcare Industry
The presence of specialized medical injection molding factories brings significant benefits to the healthcare industry. These factories allow for the mass production of medical components that are critical to patient care, such as syringes, diagnostic tools, and surgical devices. The ability to scale production while maintaining high quality ensures that medical devices are readily available to meet growing demands. Additionally, medical molding factories often offer custom molding solutions to healthcare providers, enabling the creation of specialized components tailored to specific applications. This not only supports innovation but also enhances patient outcomes by providing reliable, high-performance medical devices.
Choosing the Right Medical Injection Molding Factory
When selecting a medical injection molding factory, it is crucial to choose one that aligns with the specific requirements of your project. The right factory can help ensure that your medical devices meet stringent quality, safety, and regulatory standards, while also being produced in a cost-effective and timely manner. This decision should take into account the factory’s capabilities, certifications, experience, and the quality of its production processes. Below are key factors to consider when choosing a medical injection molding factory.
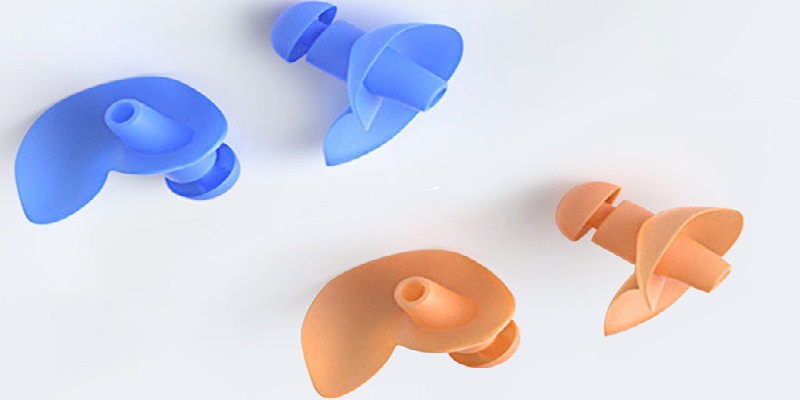
Experience and Expertise in Medical Injection Molding
The factory’s experience in the medical industry is one of the most important factors to consider. Medical devices often require highly specialized production methods, including strict adherence to regulatory standards and precision in design. A factory with a proven track record in medical injection molding will be better equipped to handle the complexities and challenges of medical device manufacturing.
Look for a factory with experience in producing medical-grade devices and components. This includes familiarity with the use of biocompatible materials and an understanding of sterilization processes and techniques. An experienced factory will have the capability to handle high-precision molding, which is essential for medical devices that demand tight tolerances and intricate features.
Certifications and Regulatory Compliance
Regulatory compliance is vital in the medical device manufacturing process, and the factory should have the necessary certifications to demonstrate that it adheres to the industry’s rigorous standards.
- FDA Approval: Ensure that the factory is compliant with the U.S. Food and Drug Administration (FDA) regulations, especially if you plan to market your products in the United States.
- ISO 13485 Certification: This is a standard for quality management systems in the medical device industry, ensuring that the factory has robust procedures in place for quality control and production.
- CE Marking: If your products are intended for the European market, the factory should be able to meet the requirements for CE marking, which confirms that the devices meet the European Union’s safety, health, and environmental protection standards.
Certifications ensure that the factory adheres to the proper medical device manufacturing standards and guarantees product safety, quality, and reliability.
Production Capabilities and Technologies
The factory’s technical capabilities and equipment are crucial in determining its ability to meet your specific manufacturing needs. Some key production capabilities to look for include:
- Advanced Injection Molding Equipment: Check whether the factory uses state-of-the-art injection molding machines that can produce high-quality, high-precision medical components.
- Material Handling: The ability to handle and process medical-grade plastics, silicones, and other materials commonly used in medical device production is essential.
- Prototyping and Customization: A factory that offers rapid prototyping services and can tailor their solutions to your specific requirements is a significant advantage, especially for medical devices that require custom designs.
Assessing the factory’s equipment and technology ensures that they can meet the high standards required in medical device production.
Quality Control and Testing Processes
Quality control is critical when manufacturing medical devices due to the direct impact these products have on patient health and safety. The chosen factory must have a stringent quality management system in place.
- In-Process Quality Control: The factory should have regular inspections during each stage of the injection molding process to ensure parts meet specifications.
- Final Product Testing: The factory should conduct rigorous testing of final products to verify that they meet regulatory standards and function properly in medical applications.
- Certifications for Quality Control: Look for factories with ISO 9001 certification or similar quality control standards, which ensure consistent product quality.
A factory with strong quality control measures will ensure that each medical component produced is reliable, safe, and compliant with relevant standards.
Cost-Effectiveness and Lead Times
Cost and production efficiency are important when choosing a medical injection molding factory, particularly for projects that involve mass production. However, the focus should not solely be on the lowest price; instead, consider the overall value the factory offers.
- Competitive Pricing: Evaluate the factory’s pricing structure based on the complexity and volume of your medical device production.
- Timely Delivery: It is essential that the factory can meet your deadlines without compromising on quality. Delays in production can have serious repercussions, especially in the medical industry.
- Cost-Effective Manufacturing: A factory that can optimize its processes for high-volume production while maintaining quality standards will help reduce costs per unit.
When selecting a factory, consider both the price and the ability to deliver high-quality products on time, as this directly affects the overall success of your project.
Communication and Customer Support
Effective communication is vital for a successful partnership with a medical injection molding factory. Clear communication ensures that the factory understands your project requirements and can provide timely updates on production progress.
- Customer Support: Choose a factory that offers excellent customer support, with representatives who are knowledgeable about the medical industry and can help resolve issues quickly.
- Collaborative Approach: A factory that works closely with your team to understand the unique requirements of your medical device will ensure a smoother manufacturing process and better final products.
Strong communication and support are key to ensuring a successful and efficient collaboration between you and the medical injection molding factory.
Choosing the right medical injection molding factory is a critical decision that can significantly impact the quality, safety, and success of your medical devices. By evaluating factors such as experience, certifications, production capabilities, quality control, cost, and communication, you can select a factory that is best equipped to meet your specific needs. Ensuring that the factory adheres to strict medical standards and provides reliable, high-quality products will help ensure the success of your medical injection molding applications.
Industry Regulations and Standards for Medical Injection Molding Factory
Medical injection molding factories play a critical role in producing high-quality, precise medical components used in various applications, such as diagnostic devices, surgical instruments, and implants. Given the vital nature of these products, strict industry regulations and standards must be followed to ensure the safety, effectiveness, and reliability of medical injection molded products. Below, we explore the key regulations and standards that medical injection molding factories must adhere to in their production processes to ensure compliance and high-quality output.
ISO 13485: Quality Management for Medical Devices
One of the most important industry standards for medical injection molding factories is ISO 13485, which specifies the requirements for a quality management system (QMS) in the manufacturing of medical devices. This standard ensures that manufacturers consistently produce medical devices and components that meet both customer requirements and regulatory obligations. ISO 13485 emphasizes risk management, traceability, documentation, and design controls, all of which are critical in the production of medical injection molding products.
By adhering to ISO 13485, medical injection molding factories can ensure that their products are safe, effective, and manufactured in compliance with international regulations. The certification of this standard is often required by regulatory bodies such as the FDA (Food and Drug Administration) for medical device manufacturing.
FDA Regulations for Medical Devices (21 CFR Part 820)
In addition to ISO 13485, medical injection molding factories that manufacture medical devices for the U.S. market must also comply with FDA regulations, particularly 21 CFR Part 820, which outlines the quality system requirements for medical device manufacturers. This regulation ensures that medical devices are produced under consistent and controlled conditions, with a focus on quality assurance and compliance with health and safety standards.
Key elements of 21 CFR Part 820 include requirements for process validation, device history records, production and process controls, and design controls. By following these regulations, medical injection molding factories can guarantee that their products meet the FDA’s stringent standards for safety and efficacy.
Biocompatibility Standards (ISO 10993)
For medical injection molding products, particularly those that come into direct or indirect contact with the human body, biocompatibility is a major concern. ISO 10993 is a set of standards that provides guidelines for evaluating the biocompatibility of medical devices. This includes testing for potential toxicity, irritation, and sensitization caused by materials used in medical products.
Medical injection molding factories must use materials that are biocompatible, meaning they do not pose a risk to patients when used in medical devices. Compliance with ISO 10993 ensures that the materials used in manufacturing injection-molded medical products will not cause harmful reactions when exposed to body tissues or fluids, ensuring the safety of the final product.
CE Marking and EU Medical Device Regulation (MDR)
For medical injection molding factories that manufacture products for the European market, compliance with the EU Medical Device Regulation (MDR) is mandatory. The MDR outlines the requirements for medical devices sold in the EU, including stringent rules for design, production, and post-market surveillance.
To demonstrate compliance with the MDR, manufacturers must obtain the CE marking for their products. This mark indicates that the product meets the essential safety and performance requirements set out by EU regulations. The CE marking is required for a wide range of medical devices, including those produced using medical injection molding.
RoHS and REACH Compliance
In addition to medical-specific regulations, medical injection molding factories must also adhere to environmental standards such as RoHS (Restriction of Hazardous Substances) and REACH (Registration, Evaluation, Authorization, and Restriction of Chemicals). These regulations limit the use of hazardous materials, such as lead, cadmium, and mercury, in medical products and ensure that harmful substances are not present in the materials used in medical injection molding.
By complying with RoHS and REACH, medical injection molding factories help reduce the environmental impact of medical device production and ensure that the products are safe for patients and healthcare providers.
GMP (Good Manufacturing Practice)
GMP guidelines are another essential set of standards that medical injection molding factories must follow. These practices ensure that manufacturing processes are conducted in controlled environments and that products are consistently produced according to predefined specifications. GMP encompasses various aspects of production, including material control, equipment maintenance, training, and proper documentation.
Compliance with GMP ensures that medical injection molding products are produced with the highest standards of hygiene, quality, and safety, minimizing the risk of defects or contamination.
Medical injection molding factories must adhere to a wide range of industry regulations and standards to ensure that their products meet the strict requirements for safety, quality, and performance. By following guidelines such as ISO 13485, FDA regulations, biocompatibility standards, and CE marking, these factories can guarantee that their medical injection molding products are reliable, safe for use, and in full compliance with global regulatory requirements. Compliance with these standards is essential for maintaining the trust of healthcare professionals, patients, and regulatory bodies in the medical devices produced.
FAQs about Medical Injection Molding Factory
The largest injection molding company in the world is Engel Austria, a global leader in the design and manufacturing of injection molding machines and technology. Engel is known for producing highly advanced injection molding machines that cater to a wide range of industries, including automotive, medical, packaging, and consumer goods. With a strong global presence, Engel operates in over 85 countries and has been recognized for its innovative technology, such as the use of all-electric machines and advanced automation systems that improve efficiency and precision. Alongside Engel, other notable large injection molding companies include Arburg and Husky Injection Molding Systems, which also lead the industry in terms of size and technology. These companies provide state-of-the-art machines that are crucial in the manufacturing of high-quality components, contributing significantly to the growth of industries such as medical device manufacturing and automotive production.
BMP Medical, a leading global provider of medical solutions and devices, is headquartered in Shenzhen, China. BMP Medical is well-known for its focus on innovation and high-quality manufacturing in the medical industry. The company specializes in the design and production of a wide range of medical products, including syringes, infusion sets, surgical instruments, and diagnostic tools. Shenzhen, known as a hub for technology and manufacturing, offers BMP Medical access to cutting-edge technologies, skilled labor, and efficient production capabilities. The company also operates manufacturing facilities and R&D centers in different parts of the world, allowing them to maintain a global presence. As a result, BMP Medical has become a significant player in the medical device industry, known for its high standards and commitment to delivering reliable medical solutions worldwide.
Medical injection molding is a specialized manufacturing process that involves injecting molten materials such as medical-grade plastics, silicones, or thermoplastics into molds to produce precise medical components. This process is widely used in the production of medical devices such as syringes, catheters, diagnostic tools, and surgical instruments. The main advantages of medical injection molding include high precision, scalability, and the ability to produce complex designs in large quantities. One of the key reasons why this method is popular in the medical field is that it ensures the production of components that meet strict quality standards, including biocompatibility and sterility. Medical injection molding factories operate under strict regulations to maintain cleanroom environments, preventing contamination and ensuring that products are safe for medical use. The use of specialized materials, such as medical-grade plastics, ensures that the final components are safe, durable, and reliable. Additionally, the scalability of injection molding allows manufacturers to meet the growing demand for medical devices worldwide while keeping production costs efficient.
The market for medical injection molding is significant and rapidly growing due to the increasing demand for precision components in medical devices. The medical industry relies heavily on injection molding to produce a wide range of components, including surgical instruments, diagnostic devices, drug delivery systems, and implants. The market is driven by the demand for high-quality, biocompatible, and sterile components, especially as the healthcare sector continues to expand globally. Innovations in healthcare, particularly in personalized medicine and minimally invasive procedures, have further contributed to the growth of the medical injection molding market. The increasing adoption of 3D printing technologies and automation in manufacturing processes is also influencing this market. Overall, the medical injection molding market is projected to grow steadily, offering opportunities for medical device manufacturers and suppliers of injection molding services.
The hourly rate for injection molding varies depending on several factors, including the complexity of the part, the materials used, and the location of the manufacturer. On average, injection molding machine rates range from $50 to $150 per hour. However, for specialized processes like medical injection molding, the rates can be higher due to the need for precision, strict quality control, and regulatory compliance (such as FDA certifications and ISO standards). Additionally, mold creation costs, material costs, and the need for cleanroom environments can increase the overall cost. Custom medical injection molding services that require specialized materials (such as biocompatible plastics) or advanced processes (like multi-material molding or overmolding) will also have higher rates. For high-volume production, the hourly rate per unit tends to decrease, as setup costs are amortized over a larger number of parts.
Injection molding can be highly profitable, particularly in high-volume production runs. The profitability of medical injection molding is driven by its ability to produce high-precision components with minimal material waste, ensuring cost-efficiency over time. Once the molds are created, the production of parts can be automated, reducing labor costs. For medical device manufacturers, injection molding provides a reliable, repeatable process that meets stringent regulatory standards, such as those imposed by the FDA and ISO 13485. This means manufacturers can maintain consistent product quality, which is crucial in the medical industry. However, initial investment in high-quality molds, machinery, and specialized materials can be expensive, which makes it important for companies to target markets with high demand for precision medical devices. In general, medical injection molding can be a very profitable venture with the right equipment, expertise, and market focus.
Injection molding can be a rewarding career, particularly for those interested in manufacturing, engineering, and the medical field. With the increasing reliance on injection molding for producing high-precision medical components, skilled professionals in this industry are in high demand. Careers in injection molding range from machine operators and technicians to design engineers and quality control specialists. The growth of the medical device industry and the ongoing advancements in injection molding technology provide job stability and opportunities for career growth. Additionally, many companies offer competitive salaries, benefits, and the chance to work on innovative projects that contribute to healthcare. For individuals who enjoy working with machinery, problem-solving, and ensuring the highest standards of quality and safety, a career in medical injection molding can be both lucrative and fulfilling.
While injection molding is an excellent manufacturing process, especially for producing high-precision, complex parts in high volumes, other manufacturing techniques may be more suitable for certain applications. For example, 3D printing (additive manufacturing) can be better for rapid prototyping, creating complex geometries, or low-volume production runs, as it does not require molds and can produce intricate designs. Blow molding is ideal for producing hollow parts, such as bottles or containers, while compression molding can be better for making parts from thermosetting plastics or larger, less complex parts. Additionally, for industries that require specialized coatings or finishes, die casting or forging may offer advantages. Ultimately, the “better” option depends on the specific requirements of the product, including production volume, material choice, part complexity, and cost-effectiveness. However, for high-volume, precise, and durable medical parts, injection molding remains a top choice.
Contact our professional team now for a same-day quote and risk-free project evaluation. Benefit from ISO 8 cleanrooms, advanced machines, and 12-hour fast response in medical injection molding.