The turning of medical parts plays a crucial role in the medical device industry, where precision and accuracy are of utmost importance. Medical devices require the highest standards of quality, as even the smallest imperfections can impact patient safety and device performance. CNC machining, particularly the turning process, is essential in the manufacturing of medical parts due to its ability to produce high-precision components. This process involves rotating a material while a cutting tool shapes it, allowing manufacturers to create complex, intricate designs needed for medical implants, surgical tools, and diagnostic equipment. In addition to CNC turning, medical injection molding is another vital process in the production of medical parts, ensuring that components are produced with the same level of precision and reliability. The turning of medical parts, alongside injection molding, ensures consistent, reliable production of components that meet stringent regulatory standards, making it vital for the creation of functional and safe medical devices. Turning of medical parts ensures precise production of complex components for medical devices, adhering to strict FDA and industry standards.
What Are Mechanical Turned Parts?
Turning of medical parts is the process of using machines to create precision components for medical devices and instruments. These parts are often small and complex and must meet strict FDA guidelines and industry standards. When choosing a machine shop to turn medical parts, it is important to make sure they meet the requirements of ISO 9001 and ISO 13485. ISO 9001 ensures that machine shops adhere to regulatory requirements and provide high-quality turning services. ISO 13485 provides quality management system specifications for medical device manufacturers.
Mechanical turned parts are components produced through the process of CNC turning, where a rotating material is shaped by a cutting tool. These parts are essential for creating high-precision components that meet the rigorous demands of the medical sector. CNC turning allows for the creation of complex geometries, tight tolerances, and smooth finishes, which are critical for medical applications such as orthopedic implants, dental tools, and surgical instruments. Mechanical turned parts can be made from a variety of materials, including metals, plastics, and biocompatible materials, ensuring compatibility with medical standards and patient safety.
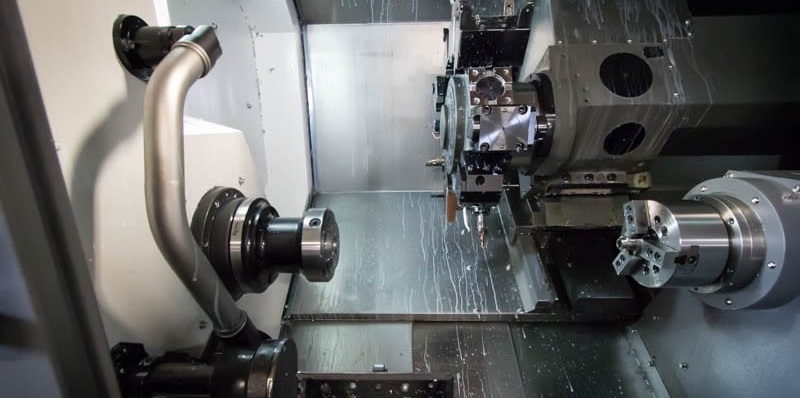
Types of Turning of Medical Parts
- CNC (computer numerical control) machinesThese machines use software to create precise components. They are often used to make parts for diagnostic equipment, such as MRI and CT scanners.
- Swiss lathe turning machinesThese machines use computer technology to create consistent parts. They can move along multiple axes, which makes them ideal for creating long, slender parts. Swiss lathes can also perform multiple operations at once, which can reduce production time.
- CNC turn millsThese machines are a good choice for parts that require high accuracy and a smooth exterior surface finish. For example, a CNC turn mill can be used to machine hip cups, which are made from cobalt chrome and implanted into the pelvis.
Turning of Medical Parts: What is CNC Turning?
CNC turning is a subtractive manufacturing process that is widely used in the production of precise and complex parts, particularly in the medical device industry. This process involves using computer numerical control (CNC) machines to rotate a workpiece while a cutting tool shapes it. The turning of medical parts requires the utmost precision, as even the smallest deviations can affect the functionality and safety of the final product.
Definition
CNC turning is a highly automated process where a rotating material is shaped by a cutting tool. The tool moves along various axes, removing material to create the desired shape. The turning of medical parts uses this process to achieve the exact specifications required for devices such as implants, surgical instruments, and diagnostic equipment. The use of computer-controlled machines ensures that the parts are made to exact tolerances, essential for medical applications.
How it Works
In the medical cnc machining turning, the material—typically a metal, plastic, or other specialized material—is secured on a spindle that rotates at high speed. A cutting tool is then applied to remove material in a precise manner, shaping the part according to the design. The CNC machine is controlled by software that ensures every movement of the tool is accurate and repeatable, making it ideal for creating complex geometries needed in medical devices. The rotating motion allows for efficient cutting, and multiple axes of movement enable intricate shaping of the parts.
Turning of Medical Parts: Importance of CNC Turning in the Medical Device Industry
The turning of medical parts using CNC technology is integral to the production of high-quality medical devices. In the medical device industry, precision, accuracy, and reliability are paramount, as even the smallest deviation from design specifications can have significant consequences for patient safety and device performance. CNC turning offers several key benefits that make it an ideal method for manufacturing medical plastic components.
Precision and Accuracy
One of the primary advantages of CNC turning in the medical device industry is its ability to produce parts with extremely tight tolerances. Medical devices require a high level of precision, especially for components that will be implanted in the human body or used in surgical procedures. The wholesale medical device injection molding using CNC machines ensures that parts are manufactured to exact specifications, with tolerances often measured in micrometers. This high degree of precision is critical for ensuring that medical devices function properly and safely, as even slight inaccuracies could lead to device malfunction or complications for patients.
Complex Geometry
Another critical aspect of the turning of medical parts is its ability to create complex and intricate geometries. Medical implants, surgical tools, and diagnostic equipment often require shapes that are not easily achievable with traditional manufacturing methods. CNC turning allows for the production of highly detailed and geometrically complex parts, such as orthopedic implants, dental devices, and micro-components for minimally invasive surgeries. The precision of CNC turning, alongside the use of precision mold medical techniques, ensures that even the most complex designs can be faithfully reproduced, ensuring functionality and ease of use in medical procedures.
Material Variety
CNC turning is versatile in terms of the materials it can accommodate. In the medical device industry, manufacturers use a variety of materials, including metals (such as titanium and stainless steel), plastics, and biocompatible materials. The turning of medical parts allows for the machining of these materials to produce components that meet the required performance standards. For example, CNC turning can be used to create implants that need to withstand high stress and corrosion, as well as components made from biocompatible materials that will interact safely with human tissue. This flexibility is crucial for creating a wide range of medical devices tailored to specific medical needs.
Consistency
Consistency is another important factor in the turning of medical parts. Plastic medical device manufacturing often requires the production of parts in large quantities while maintaining the highest standards of quality. CNC turning ensures that each component produced is identical to the others, meeting strict regulatory requirements and maintaining high quality throughout production. This uniformity is essential for ensuring that every medical device functions reliably and safely, particularly when they are used in critical medical procedures or implanted in patients.
Turning of Medical Parts: Applications of CNC Turning in Medical Device Manufacturing
CNC turning plays a pivotal role in the manufacturing of plastic medical devices, enabling the production of components with high precision, complex geometry, and material versatility. The turning of medical parts is utilized in a variety of medical applications, ranging from surgical tools to implants and diagnostic equipment. Below are some of the key applications where CNC turning is crucial in the production of medical devices.
Surgical Tools
The turning of medical parts is essential in the production of precision surgical tools, such as handles, blades, and other components that require meticulous craftsmanship. CNC turning ensures that each part is manufactured to exact specifications, providing the necessary sharpness, durability, and ergonomics required in a surgical setting. For instance, the handles of surgical instruments often feature intricate designs for comfort and functionality, and CNC turning is used to achieve this high level of precision. Additionally, blades for various surgical tools—such as scalpels or bone saws—are produced using CNC turning to ensure sharp, smooth, and consistent cutting edges.
Implants
CNC turning plays a crucial role in the production of medical implants, including orthopedic implants like hip and knee joints, dental implants, and custom-made implants for various other applications. These implants must meet strict medical standards, as they are used in the human body and must ensure long-term safety, stability, and comfort. The turning of medical parts is employed to produce these implants with the necessary geometry, strength, and biocompatibility. For example, hip and knee joint implants require intricate designs and precise dimensions to match patient-specific needs, and CNC turning can create these customized components with high accuracy. The use of CNC turning also allows manufacturers to work with various biocompatible materials, ensuring that the implants integrate seamlessly with human tissue.
Prosthetics
In prosthetic device manufacturing, CNC turning enables the creation of parts for custom prosthetic limbs and other assistive devices. Prosthetics need to be designed to fit the unique requirements of individual patients, and the turning of medical parts is a perfect solution for manufacturing such highly personalized components. Using CNC turning, manufacturers can create complex shapes, such as joint components, connectors, and prosthetic limb attachments, with great precision. This ensures that the prosthetics function properly, providing patients with the mobility and comfort they need. The ability to work with different materials, including lightweight alloys and high-strength polymers, further enhances the customization and functionality of prosthetic devices.
Microdevices
In the medical field, microdevices are essential for minimally invasive surgeries and diagnostic procedures. The turning of medical parts at the micro-level is critical for producing small, intricate components that require extreme precision. CNC turning allows for the creation of micro components, such as small surgical tools, diagnostic sensors, and tiny implants, with accuracy to the micron level. These components are often used in minimally invasive surgeries where small incisions are made, and the ability to manufacture these parts with precision is vital for the success of such procedures. The precise turning process ensures that the microdevices are functional, reliable, and safe for patient use.
Medical Device Enclosures
CNC turning is also used in the production of enclosures and housings for various medical devices, including diagnostic equipment, pacemakers, and heart pumps. The enclosures are critical to ensuring the protection and proper functioning of these devices. For example, pacemaker housings must be durable and biocompatible while ensuring the protection of the delicate electronic components inside. The turning of medical parts allows for the manufacturing of these enclosures with the required strength, tight tolerances, and smooth finishes. Additionally, CNC turning ensures the production of lightweight enclosures without compromising the protection or performance of the medical devices. In conjunction with CNC turning, medical enclosure molding process is also used to create these housings in a more efficient, high-volume production setting. This molding process enables the creation of intricate designs and specialized features, ensuring that the enclosures meet both functional and safety standards required in medical device manufacturing.
Turning of Medical Parts: Benefits of Using CNC Turning for Medical Parts
The turning of medical parts using CNC (Computer Numerical Control) machining brings several significant benefits that contribute to the high quality, efficiency, and versatility required in the medical device industry. From meeting stringent regulatory standards to enabling rapid prototyping, CNC turning plays a vital role in producing medical components that are precise, reliable, and customizable. Below are some of the key benefits of using CNC turning for medical parts.
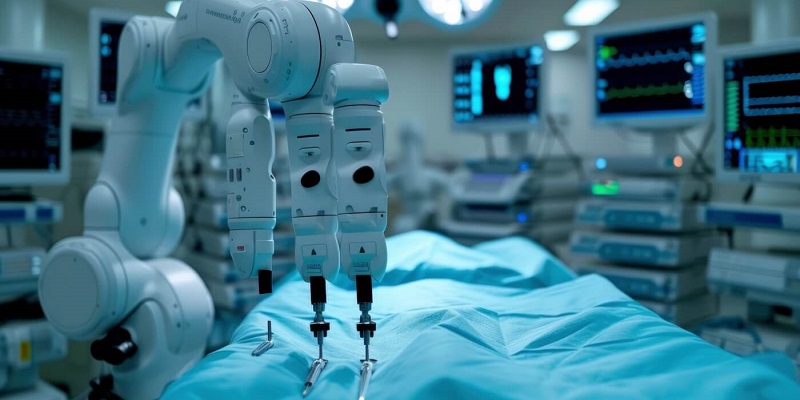
High-Quality Standards
One of the most significant advantages of using CNC turning for medical parts is the ability to meet high-quality standards. CNC machining ensures that medical components are produced with exceptional precision, adhering to strict regulatory and quality requirements, such as ISO 13485, which is specifically designed for medical device manufacturing. This standard emphasizes the importance of consistent quality management, ensuring that all medical parts, from implants to surgical instruments, are produced to the highest specifications. The turning of medical parts with CNC ensures tight tolerances and a high level of accuracy, essential for ensuring the safety, functionality, and reliability of medical devices.
Customization
CNC turning provides a high degree of flexibility, allowing for patient-specific or custom-designed parts. The turning of medical parts is particularly valuable for manufacturing custom implants, prosthetics, and surgical instruments that are tailored to individual patient needs. For example, CNC turning can produce orthopedic implants, such as hip or knee replacements, that are specifically designed to fit the patient’s anatomy. In addition, prosthetic devices can be personalized to match the unique measurements and functionality required by the patient. This level of customization enhances the overall effectiveness of medical treatments and improves patient outcomes, making CNC turning an indispensable tool in the production of individualized medical solutions.
Speed and Cost Efficiency
CNC turning is known for its speed and cost efficiency, especially when it comes to rapid prototyping and low-volume production. In the medical device industry, the need for quick prototyping is critical, as new devices or parts must be tested and modified quickly to meet clinical requirements. CNC turning allows manufacturers to produce prototypes rapidly, enabling engineers to make adjustments and refine designs before moving to full-scale production. Furthermore, CNC turning is cost-effective for low-volume runs, which is particularly beneficial when producing specialized medical parts or small batches. The ability to produce high-quality components in smaller quantities without sacrificing precision or consistency makes CNC turning a practical solution for the medical industry.
Scalability
Another key benefit of CNC turning for medical parts is its scalability. CNC machines are highly versatile, capable of handling both low-volume and high-volume production runs efficiently. Whether manufacturing a single, custom-designed component or producing large quantities of standard medical parts, CNC turning can scale to meet production demands. This scalability ensures that manufacturers can respond to market needs effectively, producing medical parts in the required quantities without compromising quality or increasing costs. Additionally, as the medical device industry continues to grow, the ability to scale production without the need for significant retooling or equipment changes makes CNC turning an attractive option for long-term manufacturing needs.
Turning of Medical Parts: Challenges and Limitations in CNC Turning for Medical Parts
While the turning of medical parts using CNC machining offers numerous benefits, there are also several challenges and limitations associated with the process. These challenges must be carefully considered to ensure the production of high-quality, reliable medical precision components. Below are some of the key challenges encountered during the CNC turning of medical parts.
Material Selection
One of the main challenges in the turning of medical parts is the selection of suitable materials. Certain materials commonly used in medical devices, such as titanium, cobalt-chromium alloys, and high-strength polymers, can be difficult to machine due to their hardness, strength, or unique properties. Some materials may require specialized tools or machining techniques to achieve the required precision and surface finish. For instance, titanium and its alloys are widely used in orthopedic implants, but they require high cutting forces and specialized tools to prevent overheating and maintain cutting efficiency. Additionally, some materials may be prone to wear and tear on the cutting tools, leading to increased maintenance costs and potential production delays. Proper material selection and preparation are crucial in ensuring that the turning of medical parts results in high-quality, functional components.
Complexity of Designs
The turning of medical parts often involves complex designs that must meet stringent requirements for functionality, aesthetics, and safety. Highly intricate and detailed components, such as orthopedic implants, surgical tools, and microcomponents for minimally invasive surgery, require advanced turning techniques to achieve the desired shape, size, and finish. These complex designs may involve varying diameters, intricate contours, and tight tolerances, which can push the limits of traditional CNC turning. As a result, specialized turning strategies, multi-axis machines, and post-processing techniques may be required to achieve the necessary level of detail and precision. The complexity of designs can also increase production time, leading to higher costs and the potential for errors if not carefully managed.
Cost
While CNC turning offers significant advantages in terms of precision and efficiency, the cost of producing high-precision medical parts can be a limitation, especially for small batch production. The specialized equipment, tooling, and skilled labor required to ensure the high standards necessary for medical devices can drive up production costs. Additionally, complex parts that require advanced machining techniques or multi-step processes can be costly to produce, particularly when small quantities are involved. This can present a challenge for manufacturers who need to balance the cost of production with the need for high-quality, reliable parts. While the speed and efficiency of CNC turning help mitigate costs, the expense of materials, tooling, and labor remains an ongoing consideration, especially when producing custom or low-volume parts.
Regulatory Compliance
The turning of medical parts must also meet rigorous regulatory standards set by authorities such as the FDA (Food and Drug Administration) in the United States or the EU’s medical device regulations. Compliance with these standards ensures that medical devices are safe and effective for patient use. Achieving regulatory compliance often involves extensive testing, documentation, and quality control measures to verify that every part meets the required specifications. For example, the FDA’s 21 CFR Part 820 regulations require manufacturers to implement a robust quality management system, track traceability of components, and ensure that all parts are produced in a controlled environment. The need to adhere to these strict guidelines can add complexity and cost to the CNC turning process, as manufacturers must invest in quality control systems and ensure that all processes are well-documented and traceable.
Mechanical Turned Parts for the Medical Sector: Manufacturer of Turning of Medical Parts
In the medical industry, precision is critical, and turning of medical parts play a significant role in ensuring the highest standards of quality, safety, and functionality. Manufacturers of turned components for the medical sector are responsible for producing highly intricate and precise parts that meet stringent regulatory requirements. These mechanical turned parts are used in a variety of medical applications, including implants, surgical tools, prosthetics, and medical devices.
Role of Manufacturers in the Production of Turned Components for the Medical Sector
Manufacturers of turned components for the medical sector are tasked with not only producing parts with exceptional accuracy but also ensuring that these parts comply with various regulatory standards. These standards, such as ISO 13485 for quality management systems and FDA guidelines for medical devices, set out the stringent requirements that manufacturers must adhere to. From the selection of raw materials to the final inspection of finished parts, manufacturers must ensure that every step of the production process is carefully controlled and documented. This includes maintaining traceability, conducting thorough testing, and implementing rigorous quality control measures to ensure that mechanical turned parts meet the medical sector’s needs for safety, reliability, and performance.
Manufacturer of Turned Components for the Medical Sector
Manufacturers of turned components for the medical sector play a crucial role in producing high-precision parts that are essential for medical devices and equipment. Turning is a machining process used to shape materials, typically metals and plastics, by rotating the workpiece while a cutting tool is applied to it. This technique is particularly well-suited for creating cylindrical or complex geometries, which are often required in medical devices like surgical tools, implants, prosthetics, and diagnostic instruments.
A key aspect of manufacturing turned components for the medical sector is ensuring the highest standards of quality and precision. These components must meet stringent regulatory requirements, such as FDA guidelines in the U.S. or ISO 13485 certifications, which govern the safety and performance of medical devices. The materials used, including biocompatible alloys or medical-grade plastics, must be precisely machined to ensure reliability, durability, and safety in their intended medical applications.
Manufacturers of turned components often work closely with medical device designers and engineers to ensure the parts are not only technically sound but also customizable for specific patient needs, such as in orthopedic implants or prosthetics. This collaboration helps in achieving optimal functionality, comfort, and fit for the end user. Additionally, with advancements in CNC (Computer Numerical Control) machining, manufacturers can produce these components at scale, ensuring both cost-efficiency and consistency in the production of medical devices.
Why Choose FUJIU Medical Injection Mold as Medical Parts Turning Manufacturer
FUJIU Medical Injection Mold is the ideal choice for medical parts turning due to our comprehensive, ISO-certified solutions tailored to your needs. We combine speed, flexibility, and uncompromising quality to ensure precision production of medical components, utilizing cutting-edge technology in an ISO 8 cleanroom. Our full-service approach—from product development and in-house tooling to secondary operations—streamlines your production process under one roof, reducing time to market.
With a global supply chain across 10 regions and expertise in procurement, logistics, and project management, we ensure seamless execution of even the most complex projects. Our focus on cost-effective solutions, powered by advanced DFM strategies, enhances productivity while lowering costs. FUJIU delivers reliability, innovation, and value, making us your trusted partner for precision medical manufacturing.
Applications of Mechanical Turned Parts in the Medical Sector
Mechanical turned parts are integral to a vast array of medical applications, ensuring precision, durability, and reliability.
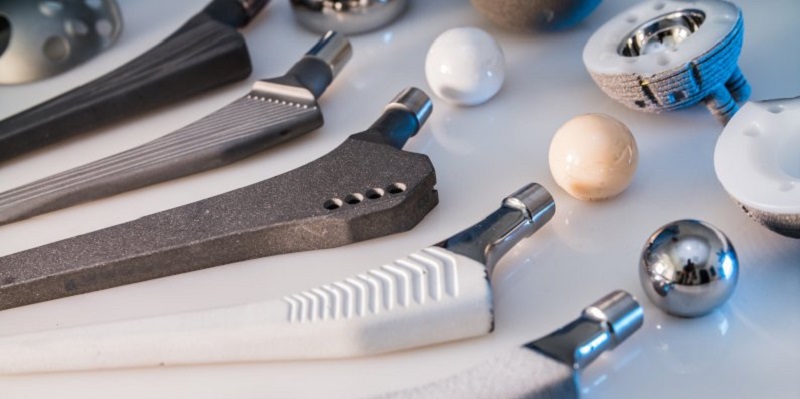
Orthopedic Implants and Surgical Instruments
- Orthopedic Implants: Turned components form the foundation of orthopedic devices like hip, knee, and spinal implants. These parts are made from biocompatible materials such as titanium and stainless steel, offering the strength and precision required for long-term patient use.
- Surgical Instruments: High-precision turning techniques produce critical tools like forceps, scissors, scalpel handles, and drill bits, where accuracy directly impacts surgical outcomes.
Prosthetic Devices
- Prosthetic limbs and components rely on turned parts for their customizable design and precise fit. CNC turning allows for the fabrication of lightweight, durable parts that can withstand daily wear and tear while maintaining comfort and functionality for the patient.
Medical Devices and Diagnostic Equipment
- Turned parts are essential in producing housings, enclosures, and connectors for devices like pacemakers, heart pumps, ventilators, and blood analyzers. These components must meet exact specifications to protect sensitive electronics and ensure device reliability.
Micro-Machining for Minimally Invasive Tools
- The rise of minimally invasive surgeries has driven demand for micro-turned components, such as those used in catheters, endoscopes, and laparoscopic instruments. These parts require extreme precision at small scales to ensure functionality and patient safety.
Drug Delivery Systems
- Devices like insulin pumps and inhalers incorporate turned parts in their mechanisms. Precision machining ensures these systems deliver accurate doses of medication.
Dental and Ophthalmic Devices
- In dental applications, turned components are used for drills, braces, and implants. Similarly, ophthalmic equipment like laser surgical systems and lens manufacturing tools depend on high-precision mechanical parts.
Sterilization-Ready Components
- Turned parts used in medical applications often require compatibility with sterilization processes like autoclaving and chemical disinfection. Manufacturers ensure parts are made from materials that can withstand these processes without degradation.
Robotics in Surgery
- Advanced surgical robots utilize turned parts for joints, arms, and tool holders. The precision of these components enables robots to perform intricate procedures with enhanced accuracy and minimal invasiveness.
Regulatory Compliance and Customization
- Beyond manufacturing precision, the expertise of turned component manufacturers ensures adherence to strict regulatory requirements, such as ISO and FDA standards. Customization capabilities further allow for tailoring components to meet specific medical needs.
By leveraging advanced CNC turning techniques, manufacturers deliver parts that meet the demanding requirements of the medical sector, ensuring patient safety, product durability, and optimal performance across a wide range of applications.
FAQs about Turning of Medical Parts
CNC, or Computer Numerical Control, refers to the use of computer software to control machinery for manufacturing processes, including milling, turning, and drilling. In the medical field, CNC technology is crucial for producing highly precise, custom parts for medical devices. CNC machines use digital designs to create parts with tight tolerances and complex geometries, which are necessary for medical implants, surgical instruments, prosthetics, and diagnostic equipment. CNC machining in the medical field is favored because of its high level of precision and repeatability. For example, it is used to create orthopedic implants like knee or hip replacements, as well as components for pacemakers, dental tools, and even surgical instruments like forceps or scalpels. These components need to meet strict regulatory standards and must be manufactured with exceptional accuracy to ensure patient safety and device effectiveness. Additionally, CNC technology allows for the production of patient-specific or custom-designed parts, making it invaluable for personalized medical treatments and procedures.
Selling a medical device idea can be a complex and challenging process, requiring not only a solid concept but also a deep understanding of the healthcare industry, regulatory requirements, and intellectual property protections. The first step is to ensure that your idea is unique and has market potential. You should conduct thorough research to identify the target audience and determine the potential need for the device. Consider talking to medical professionals, conducting surveys, or attending industry conferences to gather feedback. Once you’ve validated the concept, the next step is to protect it legally by filing for patents or trademarks, ensuring that no one can steal your idea. After securing intellectual property, you can either pursue developing the device yourself or find investors or partners interested in bringing the product to market. You can sell the idea by pitching it to medical device manufacturers, licensing the rights to a company, or partnering with investors to fund the development process. Networking with professionals in the healthcare and medical device industries, along with attending trade shows and events, can significantly increase your chances of success.
Becoming a medical device inventor involves a combination of creativity, technical knowledge, and perseverance. The journey starts with identifying a problem in the healthcare field that can be solved with a new or improved device. A successful medical device inventor must have a keen understanding of both medical needs and technological solutions. Often, inventors are inspired by personal experiences, medical professionals, or patients who face challenges with current devices. After identifying the need, the next step is to develop a concept and create a prototype. Collaborating with engineers, designers, and medical professionals will help refine the idea and make it functional. It’s crucial to understand regulatory requirements, such as FDA approval processes in the U.S., and ensure that the device meets industry standards. The invention should be safe, effective, and reliable, and the inventor must be prepared for testing, validation, and potentially, trials. A key part of becoming a medical device inventor is networking with professionals in the field and seeking partnerships with manufacturers or investors to fund the development and production stages.
Creating a new medical device is a multifaceted process that involves research, development, regulatory approval, and often substantial financial investment. The first step in making a new medical device is identifying a healthcare need that current solutions do not address effectively. Once a need is recognized, the inventor should develop a concept or prototype and begin the design process, which may require collaboration with engineers, designers, and medical professionals. The next step is to refine the prototype through testing to ensure safety and effectiveness. This may involve several iterations and adjustments based on feedback and test results. Alongside development, it’s essential to consider regulatory requirements and prepare for certifications, such as FDA approval in the U.S. or CE marking in Europe. Each market has its own set of regulatory standards, and compliance is crucial for bringing the device to market.
In medical terminology, “turning inward” is often referred to as inversion. Inversion describes the movement where a body part, typically a limb or structure, rotates inward toward the midline of the body. For instance, in the context of the foot, inversion involves the sole turning to face medially, which is common in conditions like sprained ankles when the foot rolls inward. Similarly, in the eye, inversion could describe an inward turning of the eyelid or the misalignment of the eye in a condition like esotropia.
This inward rotation is clinically significant as it relates to biomechanics, muscle function, and joint health. In prosthetics and orthotics, for example, ensuring the appropriate degree of inversion and eversion (outward turning) is crucial for restoring proper gait mechanics. Understanding the implications of inversion helps in designing medical parts like braces, orthopedic devices, and corrective footwear to accommodate or correct this movement.
CNC stands for Computer Numerical Control. In the context of medical parts, CNC machining is a precision manufacturing process where medical components are fabricated using computer-controlled tools. CNC is vital for producing medical devices such as prosthetics, implants, and surgical instruments, which require extreme accuracy and consistent quality.
CNC technology allows for the creation of complex shapes and designs needed for ergonomic and functional medical components. For instance, in orthopedic implants like hip joints or knee replacements, CNC machining ensures tight tolerances and surface smoothness, which are critical for biocompatibility and patient comfort. Similarly, CNC processes are used to craft customized braces, dental implants, and parts for robotic surgical systems. The ability of CNC to work with a wide range of materials, from metals like titanium to high-grade polymers, makes it indispensable in modern medical device manufacturing.
Contact our professional team now for a same-day quote and risk-free project evaluation. Benefit from ISO 8 cleanrooms, advanced machines, and 12-hour fast response in medical injection molding.