Custom medical molding components are essential in the production of medical devices and instruments, where precision and reliability are paramount. The medical industry demands high-quality, durable components that meet strict regulatory standards. Custom molding allows manufacturers to design parts tailored to specific medical applications, ensuring the highest performance and safety. These components are often made from biocompatible materials and undergo stringent testing to meet regulatory requirements. Companies like FUJIU Medical Injection Mold specialize in providing custom medical molding components and precision mold medical components, offering solutions that enhance the functionality of medical devices. With advanced technologies and customized services, the production of these components plays a critical role in advancing healthcare technologies. FUJIU Medical Injection Mold delivers custom medical molding components, crafting precise, FDA-compliant parts for diverse medical applications.
Low-Volume to High-Volume Production Capabilities
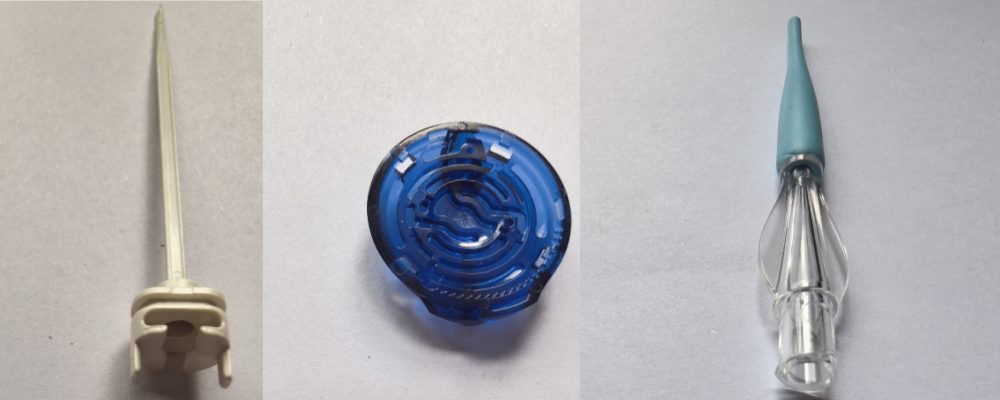
Attribute | Details |
---|---|
Material Options | PP, PC, ABS, PA6, PA66, ASA, TPU, POM, PE, PVC, PMMA, Nylon, Delrin, PET, PEEK, Silicone, Aluminum, Brass, Steel, etc. |
Plastic Molding Type | Injection Molding |
CNC Machining | Available (Micro Machining, Drilling, Milling, Wire EDM, Rapid Prototyping) |
Surface Treatments | Polishing, Etching, Texture, Electroplating, Painting, Anodizing, Brushing, Sandblasting |
Mold Materials | P20, 718, 738, NAK80, S136, 45#, 50#, Hardened Metals |
Certifications | ISO9001, TS16949, QS, ISO14001 |
Mold Life | 300,000 to 10,000,000 shots |
Cavity Options | Single Cavity, Multiple Cavity |
Customizability | Fully Customizable (Shapes, Sizes, Colors, Surface Treatments) |
Tolerance | 0.005 to 0.1mm |
MOQ | 1 piece |
Applications | Medical Equipment |
Warranty | 2 Year |
Delivery Time | 7 to 20 Days |
Packaging | Inner plastic bags, outer carton boxes, customized packaging available |
Processing Services | Molding, CNC Machining, Cutting |
Additional Features | Rapid Prototyping, Durable Mold Design, Multi-Functionality |
Custom Medical Molding Components Suppliers: What to Look For
Choosing the right supplier for medical plastic parts is crucial to ensuring the success of your medical device manufacturing process. A reliable supplier will provide high-quality components that meet regulatory standards and perform optimally in medical applications.
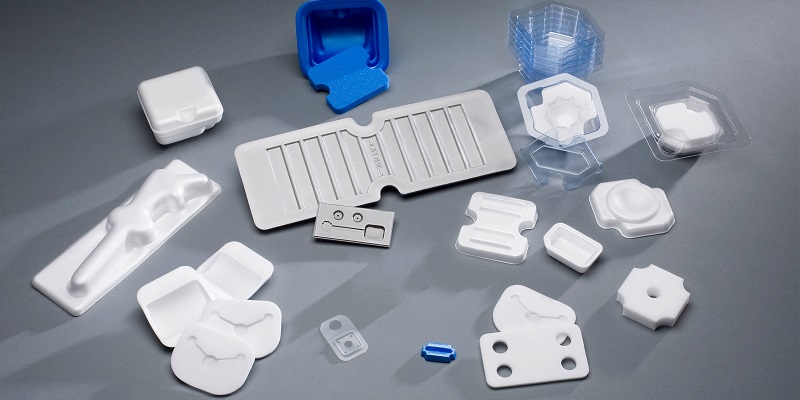
Here are key factors to consider when selecting a supplier for custom medical molding components:
Key Factors in Choosing a Reliable Supplier
- Expertise in the medical industry: A supplier with experience in medical molding is better equipped to handle the complex needs of medical devices, such as precision, durability, and compliance with regulations.
- Technology and capabilities: The supplier should have advanced molding technologies and the capacity to produce custom medical molding components to exact specifications, ensuring high-quality results.
- Customer support and collaboration: Strong communication and collaboration throughout the process are essential to ensure the customized plastic injection molding medical parts meet your needs.
- Supply chain management: A reliable supplier should have efficient logistics and delivery systems in place to avoid delays in production.
Quality Assurance and Certification Requirements
- ISO certifications: Ensure that the supplier has ISO certifications, such as ISO 13485, which demonstrates their commitment to producing medical-grade components that meet industry standards.
- FDA compliance: The supplier should adhere to the U.S. Food and Drug Administration’s regulations for medical device components, ensuring the parts are safe for medical use.
- Material traceability: A trustworthy supplier will provide full traceability of materials used, ensuring that the components are made from biocompatible, medical-grade materials.
- Testing and validation: The supplier should have robust testing processes in place, including functional testing and medical molding validation, to confirm that the custom medical molding components meet performance standards. Medical molding validation ensures that each molding process, from material selection to final product, consistently meets regulatory requirements and safety standards.
The Importance of Experience in the Medical Industry
- Knowledge of regulatory requirements: Suppliers with experience in medical molding are more likely to be familiar with the complex regulatory requirements, such as FDA 21 CFR Part 820, and can ensure compliance throughout the production process.
- Proven track record: An experienced supplier will have a portfolio of successfully completed projects and a history of delivering custom medical molding components on time and within budget.
- Expert advice: With years of experience, a supplier can offer valuable guidance on material selection, medical mold design, and other technical aspects to optimize the custom molding process.
- Ability to solve complex challenges: Experienced suppliers are more capable of handling challenging molding projects, such as high-precision medical components or designs requiring specialized molding techniques.
How to Evaluate a Supplier’s Ability to Meet Custom Requirements
- Capabilities in customization: Ensure that the supplier has the ability to produce custom medical molding components based on your specific design requirements, such as part size, material, and functionality.
- Production flexibility: A supplier should be able to adapt to changes in design or production schedules without compromising on quality or timelines.
- On-time delivery and capacity: Evaluate the supplier’s track record for meeting deadlines and their production capacity to handle your project’s scale.
- Quality control processes: Verify that the supplier has robust quality control processes in place, from prototype to full production, to ensure the final product meets your custom specifications.
By considering these factors, you can select a supplier for custom medical molding components that will meet your needs and ensure the success of your medical device production.
Why Choose FUJIU Medical Injection Mold for Custom Medical Molding Components?
FUJIU Medical Injection Mold is an excellent choice for custom medical molding components due to its comprehensive capabilities and commitment to quality. As an ISO-certified supplier, it offers end-to-end solutions, from product development and design to in-house tooling and advanced manufacturing processes, ensuring speed and flexibility without compromising quality.
The company leverages cutting-edge technology, including operations in an ISO 8 cleanroom, to deliver precision and reliability. Its agile supply chain reduces delivery cycles and accelerates time to market, while rigorous inspections ensure compliance with the highest industry standards.
With a global presence across 10 regions, FUJIU provides seamless project execution through expertise in procurement, quality, and logistics. Its value-added supply chain and Design for Manufacturability (DFM) strategies enhance productivity and reduce production costs, making it a cost-effective and reliable partner for producing high-quality custom medical molding components.
Custom Medical Molding Components Catalog: A Comprehensive Overview
A comprehensive catalog of custom plastic injection molding medical parts offers manufacturers a wide array of parts and solutions tailored to the needs of the medical industry. These components are vital for ensuring the reliability and functionality of medical devices, which require precise and high-performance parts. When exploring a custom medical molding components catalog, it is essential to understand the types of components available, their features, and how to navigate the catalog to find the right part for your specific application.
Types of Custom Components Available for Medical Molding
- Injection Molded Parts: Injection molding is a widely used technique in the production of medical parts, offering the ability to produce high volumes of consistent, precise components. Common examples include housings for medical devices, tubing, and connectors.
- Precision Medical Components: These are custom components designed to meet strict tolerances and regulatory requirements. Examples include seals, housings, and specialized medical connectors. They are made from biocompatible materials to ensure safety and efficacy.
- Customizable Mold Components: These components are often tailored to meet specific design requirements for custom medical molding. Examples include tapered date stamps, puller pins, and bushings, which are essential for mold functioning, preventing flash, and ensuring ease of operation.
- Medical Device Components: These parts are specifically designed for use in medical devices such as implants, surgical instruments, and diagnostic equipment. They may include parts like clips, housings, and precision moldings required for specialized devices.
Features and Benefits of Various Components
- Medical Injection Molding Parts:
- High precision and repeatability
- Capability for large-scale production
- Wide range of material options, including medical-grade plastics
- Suitable for complex shapes and geometries
- Precision Medical Components:
- Exact tolerances for critical applications
- Made from biocompatible materials like medical-grade silicone and thermoplastics
- Sterilizable and resistant to harsh environments
- Designed to meet regulatory standards like FDA and ISO
- Customizable Mold Components:
- Versatile and adaptable to different mold designs
- Can be customized for unique applications, such as specific sizes or functionalities
- Made from durable, corrosion-resistant materials
- Improve the overall performance and efficiency of the molding process
- Medical Device Components:
- Customized to the specific needs of medical devices
- High quality and safety standards to ensure compliance with regulations
- Precise designs for critical applications in healthcare
- Made from materials that support sterilization and patient safety
How to Navigate a Custom Medical Molding Catalog to Find the Right Part
When reviewing a custom medical molding components catalog, it’s essential to know how to navigate it effectively to find the right parts for your project. Here are some steps to follow:
- Identify the Required Component Type: Begin by narrowing down the type of component you need, whether it’s an injection-molded part, a precision medical component, or a customizable mold part.
- Review Material Options: Ensure that the materials listed meet your requirements for biocompatibility, strength, and sterilization capabilities.
- Check for Regulatory Compliance: Verify that the components comply with industry regulations, such as ISO 13485 or FDA requirements.
- Consult with the Supplier: Reach out to the supplier to discuss your needs and confirm that the components will meet your design specifications and manufacturing processes.
By following these steps, you can efficiently navigate a custom medical molding components catalog and select the parts that best suit your medical device production needs.
Custom Large Medical Plastic Parts: Key Considerations for Customization of Custom Medical Molding Components
When it comes to custom large plastic medical parts, precision, quality, and functionality are of utmost importance. These components are crucial for the performance and safety of medical devices, and the customization process must be carefully managed to ensure that they meet the specific needs of healthcare applications. Custom medical molding components, especially those in large sizes, face unique challenges during design and manufacturing.
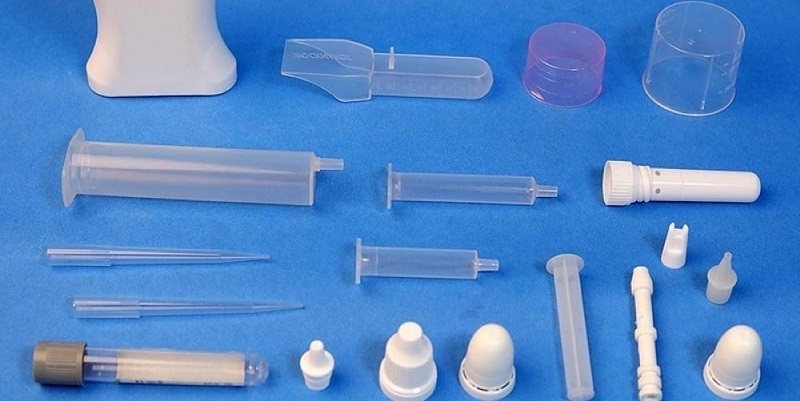
Importance of Precision and Quality in Large Medical Plastic Parts
The need for precision in large medical plastic parts cannot be overstated. These parts often serve critical functions in medical devices such as diagnostic equipment, surgical instruments, or life-saving apparatus. The components must meet stringent tolerances to ensure their proper fit and functionality within the device. High-quality standards are necessary to guarantee that the parts are durable, reliable, and safe for use in medical environments.
- Precision is crucial for ensuring that large medical parts function as intended in complex medical systems.
- Consistent quality is required to meet the rigorous standards set by regulatory bodies.
- Compliance with safety standards is essential to ensure the medical devices are safe for patient use.
- High durability is needed, as these components must withstand regular sterilization processes and various environmental conditions.
Materials Used for Custom Large Plastic Parts
The choice of materials for custom large medical plastic parts plays a significant role in determining their performance and safety. Materials must not only meet the functional requirements of the device but also adhere to stringent biocompatibility standards to avoid any adverse effects on patients.
- Biocompatible Plastics: Materials like medical-grade polypropylene, polycarbonate, and PEEK (Polyetheretherketone) are commonly used in the production of large plastic parts. These materials are designed to be safe for patient contact and can endure sterilization processes.
- Durable and Sterilizable: The materials selected must withstand the harsh conditions of sterilization and be resistant to wear and tear over time.
- Chemical Resistance: Some medical devices may be exposed to various chemicals during sterilization or operation, so the material must be chemically resistant.
- Customizable for Performance: Materials can be tailored to meet specific requirements such as flexibility, impact resistance, or transparency.
Challenges in Designing and Manufacturing Large-Scale Medical Parts
Designing and manufacturing large medical plastic parts comes with its own set of challenges. These parts often require specialized tools, molds, and techniques to ensure high quality and accuracy. Some of the key challenges include:
- Mold Design Complexity: Designing molds for large parts requires careful consideration of material flow, cooling, and shrinkage. The design must ensure even pressure distribution to prevent defects in the final part.
- Precision Tolerances: Large parts may require exceptionally tight tolerances, which can be challenging to achieve while maintaining cost-efficiency.
- Material Selection: The larger the part, the more important it is to choose the right material to ensure both safety and functionality.
- Handling and Transport: Once molded, large medical parts require careful handling, transport, and storage to prevent damage before they are assembled into medical devices.
Examples of Large Medical Plastic Parts Used in Healthcare
Custom large medical plastic parts are used in a wide range of healthcare applications. These components must be durable, precise, and often meet regulatory standards for patient safety. Some common examples include:
- Medical Device Housings: Large housings for medical devices like diagnostic machines, ventilators, and infusion pumps. These parts need to provide protection for the internal components while also allowing for easy sterilization.
- Surgical Instrument Handles: Large plastic handles for surgical instruments that require ergonomic designs for ease of use by healthcare professionals.
- Medical Bed Frames: Custom molded plastic parts used in hospital beds, which must be durable, easy to clean, and resistant to harsh cleaning agents.
- Diagnostic Equipment Components: Large plastic components for devices like X-ray machines or MRI scanners, where precision and stability are crucial for the accuracy of the readings.
Custom medical molding components for large medical plastic parts require a combination of expertise in material science, design, and manufacturing processes to ensure that these parts meet the stringent standards of the medical industry. By addressing the challenges of large-scale molding and selecting the right materials, manufacturers can produce high-quality, reliable components that are essential to healthcare innovation.
Custom Medical Molding Components and Custom Large Medical Plastic Parts Service: Tailored Solutions for Healthcare
Custom medical molding components and custom large medical plastic parts services provide essential solutions for the healthcare industry. These services are designed to meet the specific needs of medical devices, ensuring that components are precisely manufactured and meet the highest standards of quality and functionality. Working with a reliable service provider is crucial to the success of any medical molding project, particularly when it comes to custom large plastic parts.
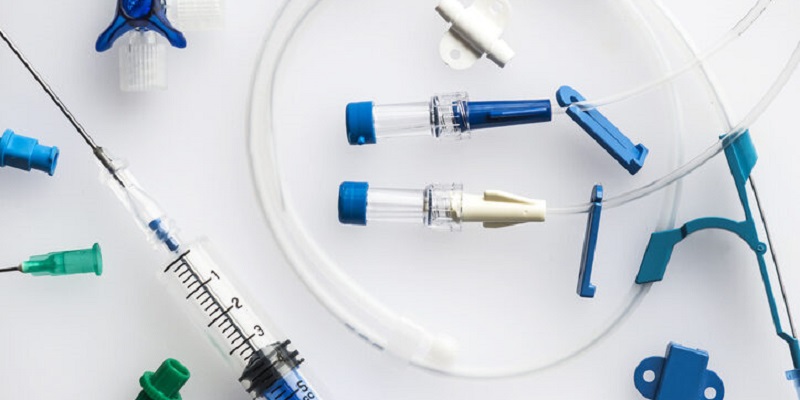
What a Custom Large Medical Plastic Parts Service Involves
A custom large medical plastic parts service is a comprehensive process that includes several stages, from design to manufacturing and quality assurance. It involves close collaboration between the medical device company and the service provider to ensure the final product meets all technical and regulatory requirements.
- Design: The initial step involves creating a detailed design for the medical part. This phase requires deep understanding of both the medical application and the manufacturing capabilities.
- Prototype Development: A prototype is created based on the design to evaluate its functionality, fit, and performance.
- Molding: The custom molding process is tailored to produce large plastic parts with high precision, using specialized equipment to ensure accuracy.
- Testing and Quality Assurance: Custom large medical plastic parts undergo rigorous testing to ensure they meet industry standards for safety, performance, and biocompatibility.
Customization Options (e.g., Design, Material Selection, Molding Techniques)
Customization is a critical aspect of creating medical parts that are perfectly suited for their intended use. There are several areas in which customization can be applied:
- Design Customization: The design process can include features like ergonomic handles, complex shapes, or integration points for other components. It also includes considerations like weight, ease of use, and the part’s function in the medical device.
- Material Selection: The materials used in custom large medical plastic parts must meet high standards for biocompatibility, durability, and resistance to sterilization methods. Materials like medical-grade polypropylene, polycarbonate, and PEEK can be selected based on the part’s intended use.
- Molding Techniques: Various molding techniques can be used for custom medical molding components, including medical injection molding, medical blow molding, and compression molding. Each technique offers unique benefits depending on the complexity and size of the part.
The Benefits of Working with Experienced Service Providers in the Medical Field
Working with experienced service providers for custom medical molding components and large plastic parts offers several key advantages:
- Expert Knowledge of Medical Standards: Experienced providers have a deep understanding of the regulatory and safety standards required for medical devices, ensuring the parts meet compliance.
- Improved Design and Prototyping Capabilities: Professionals in the field offer advanced design and prototyping services, ensuring faster development and reduced time to market.
- Cost-Efficiency: Experienced manufacturers can optimize the production process, resulting in better cost management for large-scale production.
- High-Quality Manufacturing: Reliable service providers have access to the latest technology and equipment, ensuring high-quality parts with tight tolerances.
Case Studies or Examples of Large Plastic Parts in Medical Applications
Here are some examples of large custom plastic parts used in the medical field, highlighting the importance of precision and customization:
- Surgical Equipment Handles: Large plastic handles used in surgical instruments must be ergonomically designed and durable. Custom medical molding components are used to create handles that provide both comfort and functionality for healthcare professionals.
- Medical Device Enclosures: Enclosures for diagnostic machines or patient monitoring devices often require large plastic parts that provide protection for the internal components while remaining lightweight and durable. These parts must be precisely molded to fit complex designs.
- Hospital Bed Components: Custom large plastic parts, such as frames or casings for hospital beds, need to be strong, easy to clean, and resistant to chemicals. Customization ensures that the parts meet the functional and safety requirements of healthcare environments.
- Diagnostic Machine Housings: Large plastic housings for diagnostic equipment, such as CT scanners or ultrasound machines, need to be both sturdy and aesthetically designed to fit into medical environments. Custom medical molding components offer the flexibility to meet these specific needs.
Through custom medical molding components and services for large medical plastic parts, healthcare companies can create reliable, durable, and safe products for medical professionals and patients alike. These tailored solutions ensure that medical devices meet the highest standards for performance, safety, and regulatory compliance.
Custom Medical Molding Components: Customized Medical Instrument Product Component Injection Molding: Ensuring Precision and Performance
Customized medical instrument product component injection molding plays a crucial role in the healthcare industry, ensuring that medical instruments are manufactured with the highest level of precision, durability, and safety. By utilizing advanced injection molding techniques, manufacturers can create components that meet strict regulatory standards and perform reliably in critical medical applications.
Introduction to Customized Medical Instrument Product Component Injection Molding
Injection molding is a highly effective manufacturing process used to produce intricate and precise components for medical instruments. Customized medical instrument product component injection molding is tailored to meet the specific needs of medical devices, which require components that are not only accurate but also biocompatible and durable.
This process involves injecting molten material into a pre-designed mold, allowing the creation of complex shapes with high precision. It is particularly suitable for producing components that require consistent quality and tight tolerances, which are essential for medical applications where failure is not an option.
The Process of Creating Customized Components for Medical Instruments
Creating customized components for medical instruments using injection molding involves several detailed steps, from initial design to final production:
- Design and Prototype: The first step is designing the component based on the specific requirements of the medical device. A prototype is created to evaluate the functionality, fit, and performance of the component before mass production.
- Mold Design and Fabrication: Once the design is finalized, a mold is created to shape the component. This mold must be precise, as even slight errors can affect the performance and safety of the medical instrument.
- Injection Molding: The molten plastic material is injected into the mold at high pressure, filling every detail of the cavity. Once cooled, the part is removed from the mold, and any excess material is trimmed away.
- Post-Processing and Quality Control: After molding, the components undergo post-processing steps, such as polishing, cleaning, and sterilization, to meet the industry of medical moloding requirements. The components are then subjected to rigorous quality control measures, including dimensional checks, testing for durability, and verifying biocompatibility.
Key Factors Influencing Quality
Several key factors play a significant role in ensuring that customized medical molding components meet the demanding requirements of the medical industry:
- Mold Design: The accuracy of the mold design directly impacts the quality of the final product. A well-designed mold ensures that the injection process can produce components with precise dimensions and a consistent finish.
- Material Choice: The material used in the injection molding process must be carefully selected to meet medical standards. Biocompatible materials, such as medical-grade plastics like PEEK or polycarbonate, are commonly used for components that come into contact with the human body.
- Tolerances: Tight tolerances are crucial in medical device manufacturing. Custom medical molding components must be produced to exact specifications to ensure proper function and safety, particularly for critical applications like implants or surgical instruments.
- Manufacturing Process: The process itself, including the pressure and temperature at which the injection occurs, plays a role in the final part’s integrity. A controlled, consistent process ensures high-quality, defect-free components.
How Injection Molding Meets the Demands of Medical Instrument Manufacturers
Injection molding is an ideal solution for medical instrument manufacturers because it offers several benefits:
- Precision and Consistency: Injection molding allows for the mass production of identical parts with tight tolerances, ensuring that each component meets the high standards required in medical applications.
- Customization: The ability to customize the design, material, and size of components makes injection molding highly versatile, allowing manufacturers to create parts that are tailored to the specific needs of medical devices.
- Efficiency and Scalability: Once the mold is created, injection molding enables the rapid production of large quantities of components, reducing manufacturing costs and time to market.
- Quality Control: Injection molding allows for precise control over the manufacturing process, ensuring that parts meet regulatory requirements and pass rigorous quality checks.
Customized medical instrument product component injection molding is a vital process for creating medical device components with the necessary precision, functionality, and compliance. It provides an efficient, scalable, and reliable way to produce high-quality medical components that meet the stringent demands of the healthcare industry.
Advantages of Medical Plastic Injection Molding in Custom Medical Molding Components
Medical plastic injection molding offers numerous benefits, making it a key method for producing custom medical molding components:
Ideal Mechanical Properties: This process enables the production of parts with excellent impact and heat resistance, ensuring durability and maintaining material integrity during repeated sterilization.
Reduced Risk of Breakage: Components are manufactured under high pressure, enhancing their strength and resistance to wear, crucial for medical applications.
Quality and Regulatory Compliance: High-quality medical-grade materials and stringent quality controls ensure compliance with FDA regulations, guaranteeing the safety and reliability of medical products.
Precision Manufacturing: The process supports high-volume, precision production, enabling the consistent manufacture of large quantities of medical parts without compromising quality.
Cost-Effective: By producing large batches efficiently, the per-unit cost decreases, making it a financially viable option for medical device manufacturers.
Wide Range of Material Selection: A variety of medical-grade materials can be used to meet specific requirements, providing flexibility in design and functionality.
These advantages highlight the effectiveness of medical plastic injection molding in creating reliable, high-quality, and cost-efficient custom medical molding components.
FAQs about Custom Medical Molding Components
Custom medical molding components are specifically designed and manufactured parts used in medical devices and equipment. These components are made through injection molding, a process where molten material is injected into a mold to create intricate shapes with high precision. The key benefits of custom medical molding components include their ability to meet the strict regulatory standards of the healthcare industry, their adaptability to the unique design requirements of medical devices, and their role in ensuring the safety and functionality of the devices.
Custom medical molding components are crucial because they provide medical device manufacturers with the ability to create complex, biocompatible parts that are critical for the proper functioning of medical equipment. These parts include everything from surgical instrument components to components for diagnostic tools, implants, and more. Precision and reliability are essential in the medical field, as even the smallest defect can have serious consequences.
The choice of material for custom medical molding components is critical because it directly impacts the safety, durability, and performance of the medical device. The most commonly used materials in medical molding include medical-grade plastics such as:
Polycarbonate: Known for its strength, transparency, and high impact resistance, polycarbonate is widely used in the production of medical device components that require visibility and durability.
Polyethylene (PE): This material is commonly used for its flexibility and biocompatibility, especially in devices that require soft, flexible parts like tubing or seals.
Polyetheretherketone (PEEK): A high-performance plastic known for its excellent strength, chemical resistance, and biocompatibility, making it ideal for implants and long-term medical applications.
Silicone: Used for components requiring flexibility and biocompatibility, such as gaskets, seals, and prosthetic parts.
The material selection process is influenced by the component’s function, the regulatory standards for medical devices, and the specific environment in which the component will be used. Manufacturers must ensure that the chosen material meets both safety standards and the performance requirements of the device.
A sprue in injection molding is the channel through which molten material flows into the mold cavity. In custom medical molding components, sprues are critical to ensuring precise filling of complex geometries, such as ergonomic handles or small medical applicators. Proper design and trimming of sprues are essential to avoid defects, maintain part quality, and comply with stringent FDA standards for medical devices.
Custom injection molding involves designing and producing plastic parts tailored to specific applications. In the context of custom medical molding components, this process creates specialized parts like orthopedic housings or dental device components. It offers precision, flexibility in materials, and scalability, ensuring the parts meet medical-grade standards and complex requirements like biocompatibility and durability.
The best materials for molds are typically steel or aluminum due to their durability and precision. For custom medical molding components, steel molds are preferred because they withstand high-volume production while maintaining tight tolerances. This is essential for creating components like dropper assemblies or impellers that meet stringent medical industry standards.
Materials used in injection molding for custom medical molding components include biocompatible plastics like polycarbonate, polypropylene, and PEEK. These materials are chosen for their durability, sterilizability, and compliance with FDA regulations, making them ideal for producing reliable and safe medical devices.
3D printing excels in prototyping and low-volume production, but for custom medical molding components, injection molding is better for high-volume runs, consistent quality, and meeting FDA standards. Injection molding also provides superior material properties and precision, crucial for medical-grade parts.
For high-volume, consistent production of custom medical molding components, injection molding is unmatched. Alternatives like compression molding or 3D printing may work for specific low-volume or less-complex applications, but they lack the precision and scalability required for medical-grade components.
For custom medical molding components, injection molding is more cost-effective for large production runs due to lower per-part costs and scalability. However, for prototyping or small batches, 3D printing can be cheaper due to lower upfront tooling costs.
Contact our professional team now for a same-day quote and risk-free project evaluation. Benefit from ISO 8 cleanrooms, advanced machines, and 12-hour fast response in medical injection molding.