Precision machining for medical plays a critical role in the manufacturing of high-quality, reliable medical components, ensuring they meet stringent safety and performance standards. This specialized process involves the use of advanced technologies to create precise and customized parts, such as surgical instruments, implants, and medical devices. The demand for accuracy and durability in medical applications makes precision machining indispensable for the healthcare industry. China has emerged as a global leader in medical precision machining, offering cutting-edge manufacturing capabilities and highly skilled labor. With state-of-the-art facilities and a strong focus on innovation, China is a key supplier of precision medical components for industries worldwide. China medical precision machining excels globally, offering precise CNC services for medical implants, surgical tools, and equipment.
Low-Volume to High-Volume Production Capabilities
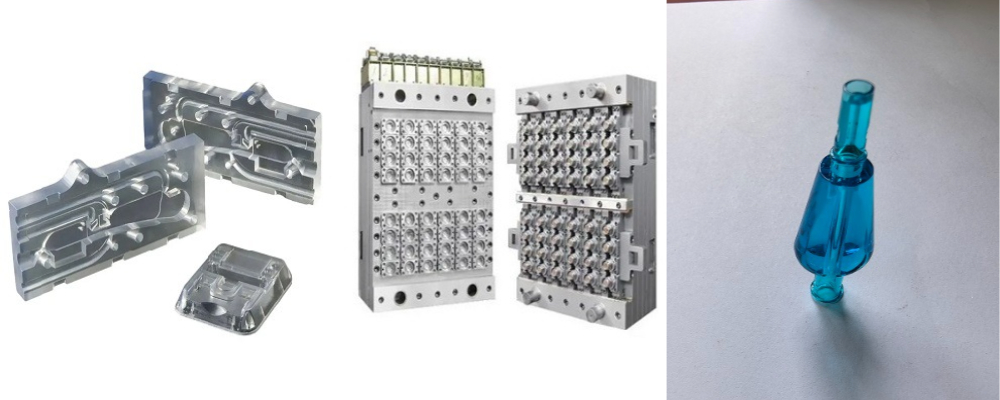
Attributes | Details |
---|---|
Place of Origin | Dongguan, Guangdong, China |
Brand Name | LY Medical Injection Mold |
Product Name | Medical Precision Machining |
CNC Machining or Not | CNC Machining |
Machining Type | Broaching, Drilling, Etching/Chemical Machining, Laser Machining, Milling, Other Machining Services, Turning, Wire Cutting, Rapid Prototyping |
Micro Machining or Not | Micro Machining |
Process | CNC Machining + Deburring |
Device | CNC Machining Center |
Surface Treatment | Customized |
Color | Customized |
Size | Customized |
Length | Customized |
Service | OEM ODM |
Logo | Customized Logo Acceptable |
Certification | ISO9001 |
Tolerance | 0.005mm |
Application | Medical Equipments |
Payment | L/C, D/A, D/P, T/T, Western Union, MoneyGram, paypal |
Selling Units | Single item |
Packing Details | According to Customer Requirements |
Port | According to Customer Requirements |
China Medical Precision Machining: What is CNC Medical Machining?
Defining CNC Machining in the Medical Industry
CNC (Computer Numerical Control) medical machining refers to the use of automated machining processes, controlled by computers, to create highly precise and intricate medical components. This technology is pivotal in the medical industry, as it allows manufacturers to produce parts with extreme accuracy, consistency, and customization. CNC medical machining is used to craft a variety of medical components such as surgical instruments, orthopedic implants, dental devices, and components for medical devices like pacemakers and hearing aids.
In China medical precision machining, CNC technology is utilized to produce parts from a range of biocompatible materials, including metals such as titanium and stainless steel, as well as medical-grade plastics. The precision offered by CNC ensures that these parts meet stringent regulatory standards, including those set by the FDA and ISO 13485, making it indispensable in the production of medical devices.
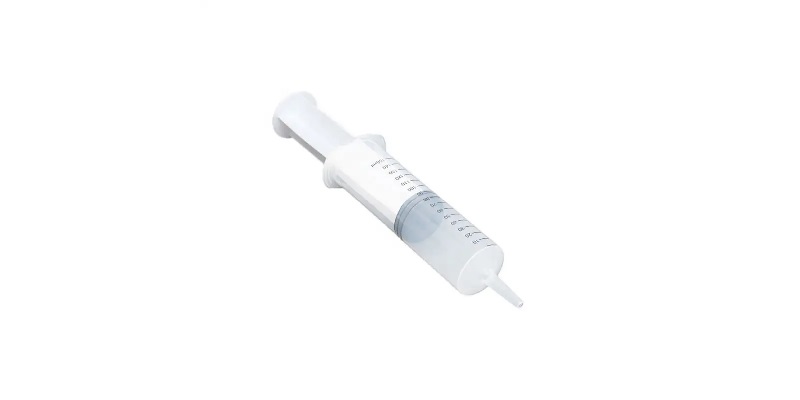
Types of CNC Machining Techniques Used in Medical Manufacturing
Several CNC machining techniques are employed in the medical industry, each suited for different types of medical components. Common techniques include:
- CNC Milling: This process involves the use of rotating cutters to remove material from a workpiece, creating detailed and complex shapes. CNC milling is used for manufacturing precision components such as surgical tools and joint replacement parts.
- CNC Turning: Used to create cylindrical components, CNC turning is essential for producing parts like bone screws, pins, and rods, which require perfect roundness and tight tolerances.
- Micromachining: This technique is used for producing extremely small components, often less than a millimeter in size. It’s especially important for creating delicate parts used in medical devices like stents or microsurgical tools.
China Medical Precision Machining: Key Advantages of CNC in Medical Machining
High Precision and Accuracy
One of the most significant advantages of China medical precision machining is its ability to achieve incredibly high precision. CNC machines are capable of working to tolerances as tight as a few microns, ensuring that each medical part meets strict dimensional requirements.
Customization Capabilities
Medical CNC machining allows for the production of highly customized medical components. Whether it’s designing a personalized implant or creating a specialized surgical tool, CNC technology can accommodate custom specifications to meet the unique needs of patients and healthcare professionals.
Faster Production Times
Another key benefit of CNC medical machining is its efficiency. The automation of the manufacturing process reduces human error and significantly speeds up production times. This is particularly valuable in the medical industry, where time-sensitive components need to be produced quickly and accurately.
Capability to Handle Complex Geometries and Tight Tolerances
CNC machines can handle intricate designs and complex geometries that traditional manufacturing methods may struggle with. This capability is crucial when producing components like orthopedic implants, which require precise fitment, and custom medical devices that need to work seamlessly within the human body. With CNC machining, medical manufacturers can ensure that even the most complex designs are created with exceptional accuracy.
China Medical Precision Machining: Applications of CNC Medical Machining
Surgical Instruments
CNC medical machining plays a crucial role in the creation of complex surgical instruments, where precision and reliability are paramount. Surgical tools such as scissors, forceps, scalpels, and scalpels need to be manufactured with incredibly tight tolerances to ensure they function properly during critical procedures. CNC machines allow manufacturers to produce these tools with high accuracy, ensuring that they meet strict medical standards.
In China medical precision machining, CNC technology is extensively used to manufacture intricate and complex surgical instruments. These tools require precise edges, custom angles, and smooth finishes, all of which are achievable with CNC machinery. For example, surgical scissors need to be sharp, finely honed, and durable to perform delicate procedures without causing damage to tissues. CNC machining ensures these parts are made with consistent quality, reducing the risk of errors during surgery.
Orthopedic Components
CNC machining is widely used in the production of orthopedic components, which require high levels of precision for effective performance. Custom implants, bone screws, joint replacement parts, and spinal components are often made with CNC technology. CNC machining allows for the production of complex geometries, such as interlocking components for joint replacements or screws that need to fit precisely into bone structures.
Materials such as titanium, stainless steel, and PEEK (Polyetheretherketone) are commonly used in orthopedic components because of their biocompatibility, strength, and resistance to wear. CNC machines can work with these materials to produce high-strength components that are durable and safe for use within the human body. China medical precision machining has become a global leader in producing these critical parts, ensuring that orthopedic components meet the highest medical standards.
Dental Devices
The dental industry has also greatly benefited from CNC medical machining. CNC machines are used to create highly customized dental devices, such as implants, crowns, bridges, and dental prosthetics. These devices require the highest level of precision to ensure that they fit perfectly in the patient’s mouth and function as intended. Through CNC machining, dental labs can create individualized solutions that meet the needs of each patient, from the shape of the tooth to the materials used.
CNC technology also supports the use of 3D scanning and CAD modeling, which further enhances the customization of dental devices. For example, using CAD software, manufacturers can create accurate digital models of the patient’s dental structure, which can then be translated into a precise CNC machining process. This customization ensures that dental implants, crowns, and bridges are made to perfectly match the unique contours of the patient’s mouth.
Prosthetics
CNC machining is revolutionizing the field of prosthetics by enabling the production of highly customized prosthetic parts, including limbs, joints, and other devices. Patients can receive personalized prosthetics that are perfectly suited to their individual needs, both in terms of fit and function. With China medical precision machining, the ability to design and manufacture custom prosthetics using CNC technology is becoming more accessible.
The integration of 3D scanning and CAD modeling further enhances the customization process. These tools allow for precise measurements and designs based on a patient’s specific body measurements, ensuring that the prosthetic is a perfect match. Additionally, CNC machining enables the production of lightweight and durable prosthetic parts, ensuring that they not only fit well but are comfortable and functional.
Medical Devices (Housings, Components)
CNC machining is widely used in the production of components for various medical devices, such as pacemakers, hearing aids, respirators, and diagnostic equipment. These devices require precise components that meet stringent regulatory requirements for safety and performance. With CNC technology, manufacturers can produce the fine, intricate parts required for medical devices with exceptional precision.
In China medical precision machining, the focus is on using biocompatible materials such as medical-grade stainless steel, titanium, and specialized plastics. These materials ensure that the components are both safe for use in medical devices and capable of withstanding the conditions they will encounter in medical environments. Additionally, combining CNC machining with precision mold medical techniques allows for the efficient production of highly accurate and compliant parts, meeting strict industry standards, including FDA approval, to ensure the devices are reliable, safe, and effective for medical use.
China Medical Precision Machining: Materials Used in CNC Medical Machining
Types of Materials for Medical Components
In CNC medical machining, the selection of materials plays a crucial role in the functionality, durability, and safety of medical components. The materials used must meet high standards of quality and biocompatibility, ensuring that they are safe to be implanted in the human body or used in medical devices. China medical precision machining excels in utilizing a range of materials that are specifically chosen for their strength, resistance, and compatibility with medical applications.
- Biocompatible Metals: Metals such as titanium, stainless steel, Inconel, and Hastelloy are widely used in CNC medical machining due to their biocompatibility, meaning they do not elicit an adverse reaction when in contact with human tissue. Titanium, for instance, is favored for its strength, lightness, and ability to resist corrosion, making it ideal for orthopedic implants, dental components, and prosthetics. Stainless steel is another commonly used metal in medical applications due to its durability and resistance to corrosion, making it suitable for surgical instruments and implants. Inconel and Hastelloy, high-performance alloys, are used in more demanding applications like implants that need to withstand high stresses or extreme conditions.
- Plastics and Composites: PEEK (Polyetheretherketone), UHMWPE (Ultra-high-molecular-weight polyethylene), and various medical-grade polymers are also essential materials in CNC medical machining. PEEK, in particular, is valued for its excellent mechanical properties, chemical resistance, and biocompatibility, making it ideal for manufacturing spinal implants, surgical instruments, and other devices that require strength and flexibility. UHMWPE is commonly used in joint replacements, especially hip and knee implants, due to its wear resistance and low friction properties. Medical-grade polymers are used in a variety of applications, including medical device housings, seals, and tubes, because they can be easily molded into complex shapes while maintaining safety and durability.
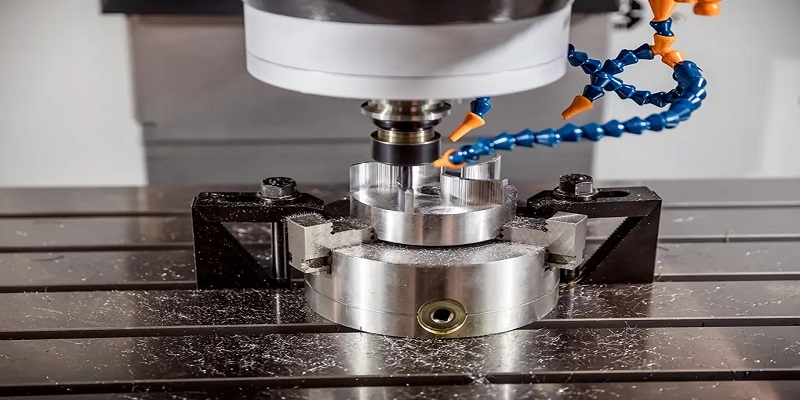
Why Material Selection is Crucial
The selection of the right material in China medical precision machining is a critical step in ensuring the safety and effectiveness of medical components. Medical-grade materials must meet specific criteria to ensure they are compatible with the human body, withstand long-term wear and stress, and perform under demanding conditions.
- Durability and Corrosion Resistance: Medical components, particularly those used in implants or surgical tools, must be durable enough to withstand the stresses and strains of the human body. For example, orthopedic implants must endure mechanical forces, while dental implants must maintain their strength over years of chewing and grinding. Materials like titanium and Inconel are chosen because of their ability to resist corrosion, even when exposed to bodily fluids, ensuring that the medical device remains intact and functional over time.
- Compatibility with the Human Body: The materials used in CNC medical machining must not only be durable but also biocompatible, meaning they should not provoke an immune response when they come into contact with the body. Metals like titanium are widely used because they are not only strong but also highly biocompatible, ensuring they will not cause rejection or adverse reactions in patients. Additionally, medical polymers like PEEK and UHMWPE are chosen for their ability to integrate smoothly with body tissues and fluids without causing inflammation or irritation.
- Compliance with Medical-Grade Standards: It is essential to adhere to strict standards when selecting materials for medical components, such as FDA regulations and ISO 13485 certifications. These standards ensure that materials used in medical machining are safe, reliable, and effective for their intended medical purpose. China medical precision machining is known for its expertise in ensuring that all materials meet or exceed international medical standards, ensuring the highest level of patient safety and performance in medical devices.
Benefits of Choosing China Medical Precision Machining Factory for Medical Product
China medical precision machining has established itself as a global leader in the field of medical manufacturing, owing to its advanced technological capabilities and high production capacity. The country’s development in CNC machining technologies enables manufacturers to produce extremely precise medical components that meet the stringent requirements of the healthcare industry. With its state-of-the-art facilities and equipment, China has become a hub for wholesale precision medical machining, offering manufacturers access to some of the latest and most efficient CNC machining techniques available and making it a prime destination for medical device production.
High Manufacturing Capabilities and Cutting-edge Technology
China’s ability to mass-produce medical components with exceptional precision makes it a trusted partner for global medical device companies. CNC machining factories in China leverage advanced technologies such as 3D printing, micromachining, and multi-axis CNC machining, enabling them to produce complex medical devices, surgical instruments, implants, and diagnostic equipment with tight tolerances. These capabilities ensure that China can meet the high accuracy required for ensuring patient safety and functionality in critical healthcare applications.
Skilled Workforce with Expertise in Medical-grade Precision Machining
One of the primary advantages of choosing a China medical precision machining factory is the country’s highly skilled workforce. Technicians and engineers in China are trained in the latest CNC machining techniques and possess deep knowledge of medical-grade standards. This expertise enables factories to create intricate parts while adhering to international regulatory standards, ensuring the production of safe, high-quality medical components that meet the strictest quality and regulatory requirements.
Cost-effectiveness and Competitive Pricing
Another compelling reason to choose a China medical precision machining factory is its cost-effectiveness. Thanks to China’s large-scale manufacturing operations and lower labor costs, Chinese CNC machining factories offer competitive pricing compared to Western markets. By outsourcing production to China, medical device manufacturers can reduce production costs without compromising quality. This affordability is especially beneficial for high-volume production of precision medical components such as implants, surgical instruments, and diagnostic devices.
Large-scale Production Capabilities Without Compromising Quality
China’s large-scale production capabilities make it an attractive option for both small and large medical device manufacturers. Despite offering lower production costs, China medical precision machining factories are able to maintain the highest standards of quality, ensuring that every component meets regulatory requirements like FDA or ISO 13485. These factories are equipped to handle large quantities of high-precision parts while maintaining consistency in quality, offering a reliable manufacturing solution for medical companies seeking to optimize their production processes.
Advanced Facilities and Certifications
Many Chinese medical machining factories are equipped with advanced facilities and hold key certifications, ensuring compliance with global medical standards. ISO certifications such as ISO 9001 and ISO 13485 validate that the factories adhere to quality management systems and regulatory standards specific to the medical industry. These certifications provide assurance to international medical device manufacturers that the produced components meet the required safety and quality benchmarks.
Furthermore, many factories also hold ITAR (International Traffic in Arms Regulations) registration, which is crucial for manufacturers producing sensitive medical components for international markets or defense-related applications. ITAR compliance guarantees that sensitive technologies are handled in line with stringent export controls, further enhancing the trust and reliability of Chinese CNC machining factories.
Choosing a China medical precision machining factory offers numerous benefits, including cutting-edge technology, skilled labor, cost-effectiveness, and adherence to international quality standards. These advantages make Chinese CNC machining factories a prime destination for global medical device production, ensuring the creation of high-precision components that meet the rigorous demands of the healthcare industry.
China Medical Precision Machining: The Role of CNC Machining in Improving Medical Device Quality
Precision in Design and Manufacturing
One of the core strengths of China medical precision machining lies in its ability to produce medical components with unparalleled precision and consistency. CNC (Computer Numerical Control) technology is at the forefront of this capability, allowing for the accurate and efficient production of highly complex medical parts.
CNC machining ensures that medical devices, from surgical instruments to implants, are produced to exact specifications. With a high degree of control over every aspect of the machining process, manufacturers in China can create parts with tight tolerances and intricate geometries that would be difficult or impossible to achieve using traditional machining methods. This precision ensures that medical devices function as intended, offering reliability and safety to healthcare professionals and patients alike.
Quality Control and Testing
In the context of China medical precision machining, maintaining the highest standards of quality control is essential for ensuring that medical devices are both safe and effective. To achieve this, manufacturers rely on advanced quality control processes and testing systems.
- Importance of Rigorous Quality Control Processes: Leading CNC machining facilities in China utilize comprehensive quality management systems to ensure every component meets the highest standards. Tools like OASIS (Open Architecture Software for Integrated Systems) and CAD/CAM systems are often used to monitor and control the manufacturing process in real-time. These systems allow for the integration of design specifications with manufacturing capabilities, minimizing the risk of errors and deviations from the original design. By utilizing these advanced technologies, manufacturers can ensure that each part adheres to strict medical standards and regulations.
- Ensuring the Safety and Performance of Medical Devices through Continuous Process Improvement: Beyond initial quality control, China medical precision machining places a strong emphasis on continuous process improvement to enhance the safety and performance of medical devices over time. By analyzing data collected during production, manufacturers can identify areas for improvement and implement corrective measures. For instance, any potential issues related to material defects, machining inaccuracies, or design flaws can be detected early, reducing the risk of faulty products reaching the market. In some cases, medical injection molding is also integrated into the process, allowing for the creation of complex parts with high precision and consistency.
This focus on continuous improvement helps maintain high levels of consistency in production, which is crucial in the medical industry, where the slightest deviation can lead to catastrophic consequences. By maintaining rigorous quality standards throughout the manufacturing process, CNC machining ensures that medical devices are reliable, safe, and compliant with all necessary regulations, including FDA and ISO certifications.
China Precision Medical Machining Factory
A China precision medical machining factory plays a crucial role in the global healthcare industry by offering state-of-the-art manufacturing capabilities to produce high-quality medical components. These medical precision machining factories are equipped with advanced CNC machining technology and specialized tools to produce parts with exceptional precision and consistency. They serve as manufacturing hubs for a wide range of medical applications, including surgical instruments, orthopedic implants, dental devices, and prosthetics.
China’s factories are renowned for their ability to handle complex designs and tight tolerances, which are essential in the production of medical components. Many of these facilities are ISO 13485-certified, ensuring compliance with international standards for medical device manufacturing. In addition, they often have advanced testing and quality control processes in place, such as non-destructive testing, surface finish inspection, and 3D dimensional verification. These factories leverage economies of scale to offer competitive pricing while maintaining high-quality standards, making them an attractive option for companies worldwide.
China Precision Medical Machining Supplier
A China precision medical machining supplier is a key partner for companies that require high-quality medical components. These suppliers are typically manufacturers that specialize in producing medical-grade parts using advanced CNC machining techniques. A key advantage of working with Chinese suppliers is their ability to provide custom solutions tailored to the specific needs of clients, whether it’s for a unique medical device or a high-volume production run. Additionally, they often provide competitive medical precision machining quotes, ensuring a balance between cost and quality for businesses.
These suppliers offer a broad range of machining services, including milling, turning, grinding, and micro-machining, all of which are crucial for producing parts with intricate designs and tight tolerances. Whether producing titanium implants, stainless steel surgical instruments, or medical device housings, China precision medical machining suppliers use cutting-edge technology and materials to deliver parts that meet the highest standards of performance and biocompatibility.
The Role of CNC Machining in Prototyping and Product Development in China Medical Precision Machining
CNC machining plays a critical role in prototyping and product development in the medical industry, offering unparalleled precision, flexibility, and efficiency. The ability to quickly produce high-quality, intricate components is essential in the fast-paced medical field, where prototyping new products or refining existing designs is common. China medical precision machining has become a global leader in this regard, providing advanced CNC machining capabilities that help medical device manufacturers develop products that meet strict industry standards. Below, we explore the key aspects of CNC machining’s role in medical product prototyping and development, focusing on its contribution to rapid prototyping, design optimization, material selection, and cost efficiency.
Rapid Prototyping for Medical Device Development
One of the most significant advantages of China medical precision machining is its ability to facilitate rapid prototyping. CNC machining enables medical device manufacturers to quickly produce functional prototypes from digital designs, which is essential in the iterative product development process.
- CNC machines can produce prototypes with precise geometry, allowing designers to test and refine designs before committing to large-scale production. This is crucial in the medical industry, where a device’s functionality and safety must be thoroughly tested.
- In China, advanced CNC machining technologies like 5-axis milling and micromachining help accelerate prototyping cycles, significantly reducing time-to-market for new medical products.
Design Flexibility and Optimization
CNC machining also supports the continuous optimization of medical device designs, making it easier to test various iterations and achieve the best possible performance.
- With China medical precision machining, manufacturers can quickly modify prototypes to improve design elements such as fit, function, and ease of use. This flexibility is essential in medical device development, where minor design adjustments can significantly affect the device’s efficacy and patient safety.
- CNC machines allow for the testing of different materials and geometries to determine the optimal combination, particularly in complex medical products like surgical instruments, implants, and diagnostic tools.
Material Selection and Biocompatibility Testing
China’s advanced CNC machining facilities offer a wide variety of materials that meet the biocompatibility and durability requirements for medical products. This ensures that prototypes and final products are both functional and safe for medical use.
- CNC machining in China allows for the use of materials such as titanium, stainless steel, medical-grade plastics, and ceramics, which are frequently used in medical devices due to their strength, durability, and biocompatibility.
- This wide selection of materials, combined with China’s expertise in medical-grade machining, ensures that prototypes can undergo rigorous testing to verify the materials’ performance in real-world conditions, leading to better product development outcomes.
Cost Efficiency in Prototyping and Production
Another major benefit of China medical precision machining in prototyping and product development is its cost-effectiveness. Due to China’s lower labor costs and large-scale manufacturing capabilities, CNC machining for medical devices is often more affordable compared to other countries.
- Prototyping and product development typically involve high upfront costs due to the need for rapid design changes and multiple iterations. China’s cost-effective production allows medical device companies to perform multiple design iterations at a fraction of the cost, making it easier to refine products without overspending.
- This cost efficiency is especially beneficial for startups or smaller medical device companies that need to maximize their budgets while ensuring high-quality, reliable prototypes.
Precision and Quality Control in the Medical Industry
CNC machining is renowned for its ability to produce highly precise components, which is essential in the medical industry, where the smallest deviations can affect a product’s safety and effectiveness.
- China’s medical precision machining facilities adhere to international standards such as ISO 13485 to ensure that prototypes meet rigorous medical device quality requirements. CNC machines can achieve tolerances as tight as ±0.001 mm, ensuring that medical components like surgical instruments, implants, and diagnostic devices are manufactured to exact specifications.
- This high level of precision is crucial in medical prototyping, as it ensures that designs are accurately translated into functional parts that can be tested and optimized for patient safety and device performance.
China medical precision machining plays a pivotal role in prototyping and product development within the medical industry. By offering rapid prototyping, design flexibility, material variety, cost efficiency, and superior precision, CNC machining in China enables medical device manufacturers to accelerate product development while maintaining the highest standards of quality and safety. With advanced technology and skilled workforce capabilities, China continues to be a leading global partner in the development of medical devices that meet the ever-evolving needs of the healthcare sector.
Workshop Requirements for China Medical Precision Machining
In the realm of medical precision machining, workshops must adhere to rigorous requirements to produce high-quality components that meet the healthcare industry’s exacting standards. These requirements span various aspects, from environmental controls to equipment and quality management systems. China’s medical precision machining industry has developed state-of-the-art facilities that comply with international standards, enabling manufacturers to produce critical components such as surgical tools, implants, and diagnostic devices. This article breaks down the essential workshop requirements, highlighting why they are vital for ensuring excellence in medical precision machining.
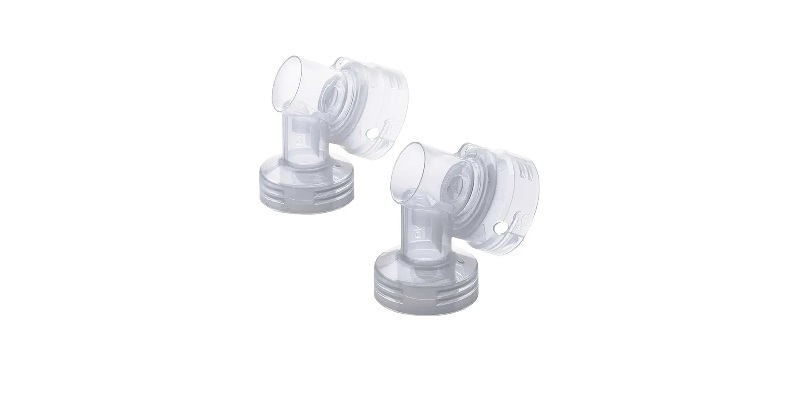
Cleanroom Environment for Contamination Control
Maintaining a clean and controlled environment is a critical requirement for any medical precision machining workshop.
Medical components often need to be manufactured in environments free of contaminants, as these could compromise product safety and performance. Cleanroom standards, typically ranging from ISO 8 to ISO 5, are essential for processing sensitive materials and parts used in surgeries or implants.
Workshops in China that specialize in medical precision machining are equipped with air filtration systems, anti-static flooring, and controlled humidity and temperature. These features prevent contamination and maintain dimensional accuracy during machining. Components are often cleaned and packaged in sterile conditions to ensure compliance with global healthcare regulations.
Advanced Equipment and Technology
High-quality medical precision machining relies on the use of advanced, high-precision equipment.
Workshops must be equipped with cutting-edge machinery capable of achieving the tight tolerances and intricate geometries required for medical components. These machines should also support multi-axis operations and automation for efficiency and consistency.
China’s workshops often use 5-axis CNC machines, electrical discharge machining (EDM), and laser cutting systems to produce complex medical parts. These facilities integrate CAD/CAM software to ensure precise designs are translated into flawless components. Automated systems reduce human error, while advanced metrology tools like coordinate measuring machines (CMMs) verify accuracy.
Strict Quality Control Processes
Robust quality management systems are non-negotiable for medical precision machining workshops.
Workshops must follow stringent quality control protocols to ensure that all components meet regulatory and customer standards. Compliance with certifications like ISO 13485 and FDA requirements is a hallmark of quality-focused operations.
In China, medical machining workshops perform in-process inspections, final part testing, and material traceability checks. Advanced inspection equipment, including optical comparators and surface roughness testers, ensures that every part meets the required specifications. Detailed documentation and certifications accompany each batch of parts to guarantee regulatory compliance.
Skilled Workforce and Training
A highly skilled workforce is essential for maintaining the precision and reliability of medical machining operations.
Technicians and engineers in medical precision machining workshops must possess deep expertise in machining, material science, and quality control. Ongoing training ensures they stay updated on the latest technologies and techniques.
China’s leading workshops invest in training programs for their employees, emphasizing precision manufacturing, equipment maintenance, and regulatory compliance. Skilled machinists work closely with engineers to optimize designs for manufacturability, ensuring efficient production without compromising quality.
Regulatory Compliance and Documentation
Workshops must adhere to local and international regulatory standards to produce medical components suitable for global markets.
Compliance with standards such as ISO 13485, FDA requirements, and EU Medical Device Regulations (MDR) ensures that medical components are safe, reliable, and biocompatible.
Chinese workshops often align their processes with these standards, ensuring that every aspect of production, from material sourcing to final inspections, meets the necessary regulations. Comprehensive documentation, including certificates of conformance and inspection reports, accompanies each shipment, providing customers with confidence in product quality.
Material Handling and Storage
Proper material handling and storage practices are vital to preserve the quality of medical-grade materials.
Medical components often use materials like titanium, stainless steel, or PEEK, which require careful handling to avoid contamination or damage. Workshops must have dedicated storage and handling protocols to maintain material integrity.
In China, medical machining workshops store materials in temperature- and humidity-controlled environments. Dedicated storage areas prevent cross-contamination, while traceability systems ensure each material batch is properly logged and tracked. This ensures that only certified materials are used for production.
Lean Manufacturing and Efficiency
Optimizing production processes is essential for maintaining cost-effectiveness while meeting quality standards.
Lean manufacturing principles help workshops minimize waste, reduce costs, and improve efficiency. This is especially important in the competitive field of medical precision machining.
Many Chinese workshops implement lean manufacturing practices, such as just-in-time production, to reduce inventory costs and streamline operations. Advanced production planning tools and automation further enhance efficiency, allowing workshops to deliver high-quality components on tight deadlines.
China’s medical precision machining workshops meet stringent requirements through a combination of advanced technology, skilled labor, and robust quality control processes. By adhering to global standards and leveraging efficient production methods, these workshops deliver high-quality, reliable medical components that support the healthcare industry worldwide.
FAQs about China Medical Precision Machining
For China medical precision machining, the cost of 5-axis CNC machining typically ranges between $50 to $150 per hour. The pricing is influenced by factors such as machine complexity, labor costs, and the materials being machined. In the medical industry, 5-axis CNC machining is favored for its ability to produce intricate geometries with micron-level precision, essential for surgical tools and implants.
Additionally, medical-grade materials like titanium or stainless steel, commonly used in medical machining, can increase operational costs. High-end facilities with certifications like ISO 13485 may charge a premium for ensuring compliance with international medical standards.
In China, CNC machining costs range from $10 to $50 per hour, depending on the complexity of the project and the type of CNC machine used. For medical precision machining, the cost may be higher, between $30 to $80 per hour, due to the advanced equipment, certified cleanroom environments, and rigorous quality controls required for medical components.
The lower labor costs in China contribute to competitive pricing, but high-precision parts, such as those for surgical instruments or implants, demand additional expenses for material sourcing and compliance with certifications like ISO 13485 or FDA standards.
Precision machining costs for China medical precision machining vary widely, typically ranging from $20 to $100 per hour. The costs depend on factors such as material type, machining complexity, and surface finish requirements. For medical-grade components like implants or surgical tools, the cost is higher due to the use of biocompatible materials and the need for stringent quality assurance.
Facilities specializing in medical precision machining may charge premiums for their expertise, cleanroom environments, and compliance with standards like ISO 13485 or GMP. Bulk production can reduce per-unit costs, but initial setup and testing expenses for medical parts remain significant.
CNC machines typically consume between 3 to 15 kWh per hour, depending on the type and size of the machine. For China medical precision machining, 5-axis or high-precision machines used for medical components generally consume more energy due to their advanced features and higher operational loads.
In medical manufacturing facilities, energy use is optimized by combining efficient machine operation with cleanroom environmental controls. On average, the electricity cost per hour ranges from $0.50 to $2 in China, depending on regional electricity prices and the machine’s efficiency.
For China medical precision machining, the precision level can reach tolerances of ±0.002 mm (2 microns) or better, particularly when using advanced 5-axis CNC machines. Such high precision is essential for medical devices like implants and surgical instruments, where even the smallest deviation can affect functionality and patient safety.
This level of accuracy is achieved through state-of-the-art equipment, specialized tooling, and adherence to strict quality standards such as ISO 13485. Regular calibration and inspection further ensure the consistency of precision in medical machining.
The cost of CNC cutting varies depending on factors like material, machine type, and project complexity. For China medical precision machining, CNC cutting is relatively cost-effective compared to other countries, with rates typically ranging from $30 to $80 per hour. However, the expense may increase for medical applications due to the need for high-precision cutting, certified materials, and compliance with regulations like ISO 13485.
Although CNC cutting for medical components involves additional costs, its precision, efficiency, and ability to handle complex designs make it an essential investment for producing reliable medical devices.
The biggest disadvantage of CNC machining in China medical precision machining is the high initial investment and operational costs. Advanced machines like 5-axis systems required for medical parts are expensive to purchase and maintain. Furthermore, meeting medical standards such as ISO 13485 and GMP involves additional expenses for certifications, cleanrooms, and quality assurance processes.
While CNC machining offers exceptional precision and efficiency, these costs may be a barrier for smaller companies or low-volume production runs. However, the long-term benefits of reliability and compliance often outweigh these initial drawbacks in the medical industry.
In China’s medical precision machining industry, the highest accuracy is achieved through ultra-precision CNC machining, which can attain tolerances as tight as ±0.0001 inches (±2.5 microns). This level of accuracy is often used for intricate components such as microfluidic devices, surgical implants, and robotic surgery tools. Advanced techniques like diamond turning and high-speed 5-axis machining allow manufacturers to meet these precision levels, crucial for medical applications. China’s access to cutting-edge technology and its robust supply chain has positioned it as a leading player in producing high-accuracy medical components at competitive prices, catering to global demand.
In China, high-end CNC machines for medical precision machining can achieve tolerances as tight as ±0.001 mm (1 micron). This precision is essential for critical medical components such as orthopedic implants and surgical instruments. Chinese manufacturers invest in advanced multi-axis CNC machines and quality control systems to meet the strictest requirements. The ability to maintain such tight tolerances consistently makes China a trusted supplier for global medical device companies, especially for components requiring perfect dimensional accuracy and biocompatibility.
The hourly rate for CNC milling in China typically ranges from $20 to $50, depending on the complexity of the part, material, and the specific requirements of the medical industry. Medical precision machining often incurs higher rates due to the need for advanced equipment, strict quality assurance, and compliance with international standards like ISO 13485. Despite the higher standards, China remains competitive due to lower labor costs and economies of scale, making it an attractive option for companies seeking cost-effective manufacturing of medical components.
For medical precision machining in China, micron tolerances typically range from ±1 to ±10 microns, depending on the complexity and application. Parts like surgical implants and diagnostic device components often require tighter tolerances to ensure functionality and compliance with regulatory standards. Chinese manufacturers achieve these tolerances using advanced CNC machines, specialized tooling, and rigorous quality control processes. The ability to consistently produce high-precision parts with such tolerances has solidified China’s position as a leader in the medical machining sector.
China’s top medical precision machining providers use ultra-precision CNC machines from globally renowned brands like Mazak, DMG Mori, and HAAS, or high-quality domestic alternatives such as those from Fanuc and Makino. These machines, equipped with multi-axis capabilities, can achieve tolerances down to ±1 micron, ensuring the highest accuracy for medical components. Additionally, many Chinese manufacturers integrate real-time monitoring systems and temperature-controlled environments to maintain precision, making their machining processes among the most accurate in the industry.
The smallest machining tolerances achieved in China’s medical precision machining industry are typically around ±1 micron. This level of precision is often required for components like micro-surgical tools, catheter connectors, or implants with intricate features. Advanced CNC machining, combined with EDM (electrical discharge machining) and laser micromachining, enables manufacturers to achieve such tolerances. Chinese companies have invested heavily in these technologies, allowing them to produce parts that meet stringent medical device standards while remaining cost-effective.
In China’s medical precision machining industry, tolerances for precision machining typically range from ±0.01 mm to ±0.0005 mm, depending on the component and its application. Surgical instruments and implants often demand the tightest tolerances to ensure proper fit, function, and patient safety. Chinese manufacturers use advanced metrology tools, such as coordinate measuring machines (CMMs), to verify that every part meets the required specifications. This strict adherence to tolerances is critical for maintaining the quality and reliability of medical devices.
For medical precision machining in China, processes like CNC milling and electrical discharge machining (EDM) are among the most accurate. EDM is particularly effective for creating intricate geometries and features with tight tolerances, often required for medical implants or micro-scale components. CNC milling, especially with 5-axis machines, is ideal for producing complex shapes with high precision. The accuracy of these processes is further enhanced by the use of advanced software and quality control systems, ensuring they meet the demanding requirements of the medical industry.
CNC milling for medical precision machining in China can be expensive due to the specialized equipment, skilled labor, and strict quality control involved. Medical components require biocompatible materials like titanium or stainless steel, which are challenging to machine and costly. The complexity of designs, combined with tight tolerances, increases machining time and tool wear. Additionally, compliance with international certifications such as ISO 13485 and FDA regulations adds to operational costs. However, China’s ability to optimize production efficiency and leverage economies of scale helps mitigate these costs, making it a competitive option globally.
Contact our professional team now for a same-day quote and risk-free project evaluation. Benefit from ISO 8 cleanrooms, advanced machines, and 12-hour fast response in medical injection molding.