Clean room injection molding is essential for producing contamination-free, high-quality medical components. In medical device manufacturing, maintaining a sterile and controlled environment is critical to ensure the safety and effectiveness of the products. This process is widely used in the production of medical devices, drug delivery systems, and surgical instruments, where even the smallest particle contamination can compromise functionality and patient safety. Clean room injection molding ensures that these components meet rigorous quality standards by controlling variables such as airborne particles, temperature, and humidity. Furthermore, it aligns with strict regulatory standards, including FDA and ISO requirements, which are crucial for ensuring that medical products meet both safety and performance criteria.
What is clean room injection molding?
Clean room injection molding is a specialized manufacturing process designed to produce contamination-free components in a controlled, sterile environment. Unlike traditional injection molding, which does not impose strict controls on air quality or particulate levels, clean room injection molding takes place in environments that are meticulously regulated for air cleanliness, temperature, and humidity. This ensures that foreign particulates are kept at bay, which is essential for sensitive applications like medical device production, where contamination could compromise the functionality and safety of the product.
Key Goals of Clean Room Injection Molding
The primary goal of clean room injection molding is to minimize contamination. This is achieved by creating a sterile environment where the presence of airborne particles is minimized. The process is designed to eliminate the risk of foreign particulates that could adversely affect the quality of the medical components being produced.
Another key goal is to maintain product integrity. Clean room injection molding is crucial for preserving the quality of components used in sensitive medical applications. By controlling the manufacturing environment, this process ensures that the components meet the highest standards for cleanliness and performance, which is especially important in the medical industry, where precision and hygiene are paramount.
Additionally, clean room injection molding ensures compliance with regulatory standards. It adheres to ISO clean room classifications and meets FDA requirements, which are essential for ensuring that medical devices and components are safe, effective, and compliant with industry regulations.
Clean rooms are classified according to ISO standards, ranging from ISO 5 to ISO 8, based on the cleanliness of the environment. ISO 5 represents the most stringent level, allowing only a very limited number of particles in the air, making it suitable for the most critical production steps, such as molding implantable medical devices. ISO 6 through ISO 8 represent progressively less stringent levels, where higher particle counts are permitted, but they are still suitable for many medical device manufacturing processes. These classifications ensure that the environment is appropriately controlled for the specific manufacturing needs of the product being produced.
Clean Room Injection Molding Requirements
Clean room injection molding is a specialized manufacturing process designed to produce high-quality, contamination-free components for industries such as medical devices, pharmaceuticals, and biotechnology. This process requires stringent controls and specific requirements to maintain sterility, precision, and compliance with regulatory standards. Below are the key requirements for clean room injection molding:
Clean Room Classification
- ISO Certification: Clean rooms must meet ISO 14644-1 standards, typically ISO Class 7 or Class 8, depending on the application.
- Airborne Particulate Control: The clean room must control particulate levels to specified limits:
- ISO Class 7: Maximum 352,000 particles per cubic meter at 0.5 µm.
- ISO Class 8: Maximum 3,520,000 particles per cubic meter at 0.5 µm.
- Positive Pressure: Maintain higher air pressure inside the clean room to prevent unfiltered air from entering.
Environmental Controls
- Temperature: The environment must maintain consistent temperatures, typically between 18–24°C (64–75°F), to ensure material stability and operator comfort.
- Humidity: Relative humidity is controlled, typically between 40–60%, to reduce static electricity and prevent material degradation.
- Air Exchange Rate: Clean rooms require frequent air changes (e.g., 60–90 air changes per hour) using HEPA or ULPA filters.
Equipment Requirements
- Clean Room-Compatible Machines: Injection molding machines must be designed to operate in clean room environments, minimizing particulate emissions and heat generation.
- Enclosed Systems: Equipment, such as dryers and conveyors, must have sealed systems to prevent contamination during material handling.
- Non-Corrosive Materials: All equipment surfaces in contact with materials or products should be made from stainless steel or other non-corrosive materials.
Material Handling
- Medical-Grade Polymers: Use biocompatible and sterilizable materials such as PEEK, polycarbonate, and polyethylene.
- Contamination Prevention: Materials must be stored in sealed containers and transferred to molding machines using closed systems to prevent contamination.
- Pre-Drying: Certain polymers require pre-drying to remove moisture and ensure optimal processing.
Personnel Protocols
- Gowning Procedures: Workers must wear specialized garments, including coveralls, gloves, masks, goggles, and hairnets, made from non-linting and antistatic materials.
- Hygiene Practices: Personnel must follow strict hygiene protocols, including handwashing and using designated clean room entry procedures.
- Access Control: Entry to the clean room is restricted to trained and authorized personnel only.
Clean room injection molding is an intricate process that requires meticulous attention to environmental controls, equipment design, material handling, and quality assurance. By adhering to these requirements, manufacturers can produce reliable, sterile, and high-quality components that meet the demands of the healthcare and pharmaceutical industries.
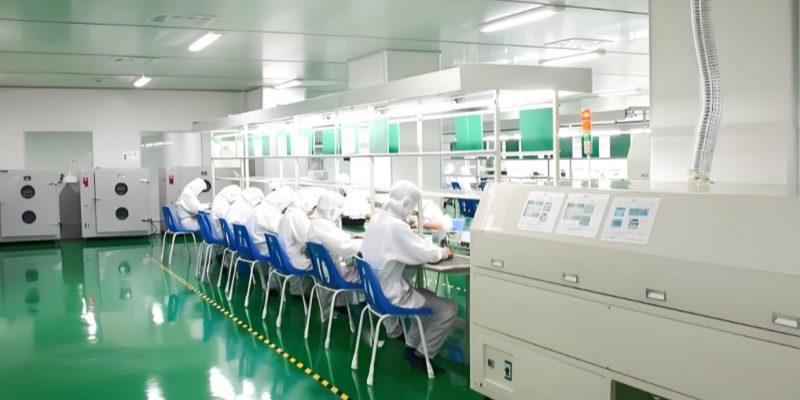
Cleanroom Molding Materials for Medical Use
Cleanroom molding is a highly specialized process designed to meet the stringent requirements of medical and pharmaceutical industries. The materials used for cleanroom molding are carefully selected to ensure compliance with regulatory standards, biocompatibility, and performance in sterile environments. Below is a detailed description of cleanroom molding materials and their key characteristics for medical use.
Key Material Requirements
Medical-grade materials used in cleanroom molding must meet the following requirements:
- Biocompatibility: Materials must not cause any adverse biological reactions when in contact with human tissues or fluids.
- Sterilizability: They must withstand sterilization processes such as autoclaving, gamma irradiation, or ethylene oxide (EtO) exposure without degradation.
- Chemical Resistance: The materials must resist degradation or leaching when exposed to cleaning agents, bodily fluids, or pharmaceuticals.
- Mechanical Integrity: High strength and durability are critical to ensure functionality in medical applications like surgical tools, implants, or drug delivery systems.
- Low Particle Generation: Materials must minimize particulate shedding to maintain cleanroom standards and prevent contamination.
Common Materials Used in Cleanroom Molding
Medical-Grade Thermoplastics
Thermoplastics are widely used due to their versatility, lightweight nature, and ease of molding into complex geometries. Common options include:
- Polycarbonate (PC):
- High impact resistance and transparency.
- Excellent for surgical instruments, blood oxygenators, and IV connectors.
- Polypropylene (PP):
- High chemical resistance and sterilizability.
- Used for syringes, vials, and diagnostic components.
- Polyethylene (PE):
- Low particle generation and high durability.
- Ideal for tubing and disposable medical devices.
- Polyetheretherketone (PEEK):
- Exceptional mechanical properties and biocompatibility.
- Common in orthopedic implants and dental devices.
Silicone Elastomers
- Advantages: High flexibility, temperature resistance, and biocompatibility.
- Applications: Catheters, seals, and prosthetics.
Thermoplastic Elastomers (TPEs)
- Advantages: Combine the properties of thermoplastics and rubber, offering flexibility and durability.
- Applications: Medical tubing, gaskets, and seals.
Fluoropolymers (e.g., PTFE, FEP, PFA)
- Advantages: High chemical resistance, low friction, and inertness.
- Applications: Coatings for guidewires and surgical instruments.
Materials used in cleanroom molding for medical applications must possess specific physical and chemical properties to ensure the functionality, durability, and biocompatibility of the products. Common materials include medical-grade plastics and engineering plastics such as polycarbonate (PC), polypropylene (PP), and polyethylene (PE).
These materials need to meet cleanroom standards while also offering excellent chemical resistance, low friction, thermal stability, and moldability. For example, certain medical-grade plastics are designed to be UV-resistant and aging-resistant, which is essential for long-term use in medical devices.
Materials such as polypropylene (PP) are commonly used in the production of disposable medical devices like syringes and infusion lines, while polycarbonate (PC) is often used for transparent medical device casings, such as monitoring equipment housings.
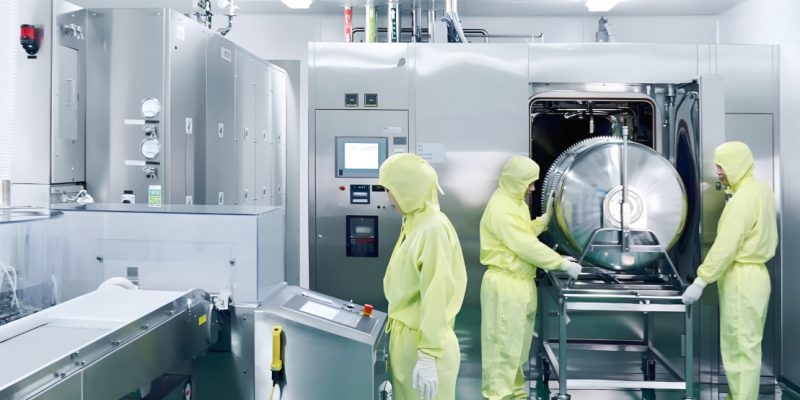
Medical Cleanroom Molding Services
The cleanroom medical molding services are specialized manufacturing processes designed to meet the rigorous quality and sterility standards required for medical device production. These services encompass the entire process, from material selection to molding and post-processing, ensuring products are made in a controlled cleanroom environment.
Steps in Medical Cleanroom Molding Services
The process typically involves precise control over every step, from initial design and mold making to injection molding and quality testing. Production usually occurs in ISO Class 7 or higher cleanrooms to ensure a contaminant-free manufacturing environment.
Medical cleanroom molding services follow a highly controlled and precise workflow to ensure the production of high-quality and sterile components. Below is a detailed description of the process:
Initial Planning and Design
- Requirement Gathering: Work closely with clients to understand product specifications, intended applications, and regulatory requirements.
- Material Selection: Select medical-grade materials based on biocompatibility, durability, and sterilization compatibility.
- Mold Design: Use advanced CAD software to design precision molds, accounting for tight tolerances and complex geometries.
Prototyping and Testing
- Prototype Development: Create prototypes using rapid tooling or 3D printing for initial evaluation.
- Design Validation: Conduct functional and dimensional tests to verify the prototype meets performance standards.
- Revisions: Refine the design based on test results and client feedback.
Cleanroom Preparation
- Cleanroom Setup: Ensure the environment complies with ISO Class 7 or 8 standards, including air filtration and temperature controls.
- Equipment Sterilization: Clean and sterilize all equipment and tools to eliminate contamination risks.
- Personnel Preparation: Staff follow strict gowning and hygiene protocols to maintain sterility.
Injection Molding Process
- Material Preparation: Prepare and sterilize the selected medical-grade polymers for molding.
- Molding Operation: Use injection molding, micro-molding, or overmolding techniques to produce components with precise specifications.
- Real-Time Monitoring: Continuously monitor critical parameters such as pressure, temperature, and cycle times to ensure consistent quality.
Post-Molding Operations
- Trimming and Finishing: Remove excess material, flash, or gates to achieve the required dimensions and surface finish.
- Secondary Processes: Perform additional operations like assembly, bonding, or surface texturing if required.
- Sterilization: Apply appropriate sterilization methods (e.g., gamma radiation, EtO, or autoclaving) to ensure product sterility.
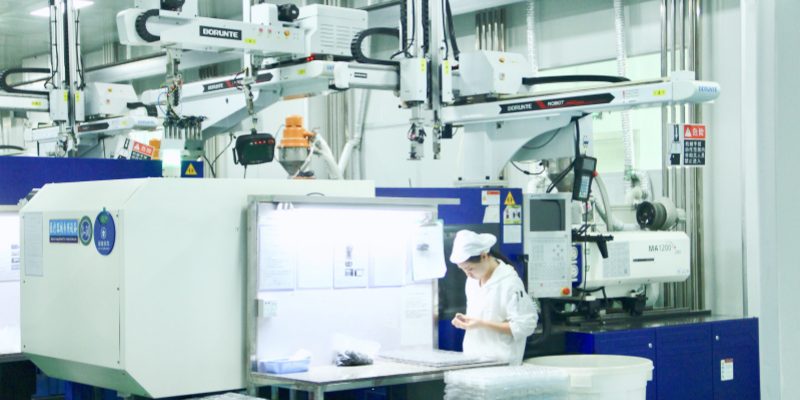
Medical Molding in a Class 7 Clean Room
Class 7 cleanrooms are designed to meet stringent air cleanliness and particle contamination limits, making them ideal for high-precision medical device manufacturing. Medical molding products in such environments ensures that products remain free of bacterial contamination and other pollutants.
Characteristics of Class 7 Clean Rooms for Medical Molding
Class 7 cleanrooms, as defined by ISO 14644-1, are controlled environments specifically designed to minimize particulate contamination, making them ideal for medical molding applications. These cleanrooms ensure sterility, compliance, and precision in the production of medical-grade components. Below are their key characteristics:
Particle Count Standards
Class 7 cleanrooms allow a maximum of:
- 352,000 particles (≥0.5 µm) per cubic meter of air.
- 83,200 particles (≥1.0 µm) per cubic meter.
- 2,930 particles (≥5.0 µm) per cubic meter.
This low particulate level is maintained using advanced filtration and cleaning protocols.
Air Filtration System
- High-Efficiency Particulate Air (HEPA) filters remove 99.97% of particles larger than 0.3 µm, ensuring clean airflow.
- Laminar airflow systems maintain uniform, unidirectional airflow to minimize turbulence and prevent particle buildup on surfaces.
- Air change rates typically range from 60 to 90 changes per hour, constantly refreshing the air to maintain cleanliness.
Environmental Controls
- Temperature is carefully regulated, typically between 18–24°C (64–75°F), to ensure worker comfort and material stability.
- Humidity is controlled at 40–60% to prevent static electricity and maintain the quality of sensitive materials.
- Positive air pressure prevents unfiltered air from entering the cleanroom, further reducing contamination risks.
Personnel Protocols
- Personnel must wear specialized cleanroom garments, including coveralls, gloves, face masks, goggles, and hoods, made from non-linting and antistatic materials.
- Workers follow strict hygiene procedures, such as handwashing and gowning in a designated anteroom before entering the cleanroom.
- Access is restricted to trained and authorized personnel to reduce contamination risks.
Equipment Requirements
- Equipment used in Class 7 cleanrooms is sterilized and designed for low particulate emissions.
- Molding machines and tools are made from non-corrosive materials like stainless steel to ensure hygiene and durability.
- Machinery is often equipped with enclosed systems to prevent particulate release during operation.
Cleaning and Maintenance
- Regular cleaning protocols using approved solvents or disinfectants are in place to remove particles and microbial contamination.
- Cleaning methods are validated to ensure they meet ISO standards and regulatory requirements.
- Continuous monitoring systems track particle levels, temperature, humidity, and pressure to maintain compliance.
Class 7 cleanrooms limit the number of particles in the air to 352,000 per cubic meter, which is suitable for manufacturing medical devices such as surgical instruments, infusion bags, and syringes.
Class 7 cleanrooms are critical for medical molding processes, providing the controlled conditions necessary to produce high-quality, sterile, and compliant components for the healthcare industry. Their advanced filtration, environmental controls, and strict protocols ensure the reliability and safety of the final products.
Why Class 7 Clean Rooms are Ideal for Medical Molding
Class 7 cleanrooms provide a controlled, sterile environment that meets the stringent requirements of medical molding processes. These cleanrooms ensure the production of high-quality, contamination-free medical components, which are essential for healthcare and pharmaceutical applications. Below are the reasons why Class 7 cleanrooms are ideal for medical molding:
Controlled Contamination Levels
- Class 7 cleanrooms maintain strict particulate contamination limits (e.g., a maximum of 352,000 particles per cubic meter at 0.5 µm).
- These controlled environments prevent airborne particles and microorganisms from contaminating medical-grade materials and products, ensuring sterility and safety.
Compliance with Regulatory Standards
- Class 7 cleanrooms adhere to ISO 14644-1 standards, ensuring particle count levels meet international requirements.
- They also comply with FDA regulations, Good Manufacturing Practices (GMP), and ISO 13485 standards, all of which are critical for medical device manufacturing.
Sterility for Critical Applications
- The sterile environment minimizes microbial contamination, making it ideal for manufacturing components used in invasive procedures, implantable devices, and pharmaceutical applications.
- The sterility provided by Class 7 cleanrooms enhances patient safety by ensuring that components remain uncontaminated during production.
Support for Precision Molding
- Medical molding processes often require tight tolerances and consistent quality. Class 7 cleanrooms ensure environmental stability, such as regulated temperature, humidity, and airflow, which are critical for precision manufacturing.
- The clean environment reduces the risk of defects or inconsistencies in molded parts, ensuring uniformity across high-volume production.
Advanced Air Filtration
- High-Efficiency Particulate Air (HEPA) filters in Class 7 cleanrooms remove 99.97% of airborne particles larger than 0.3 µm, providing a constant supply of clean air.
- Laminar airflow systems maintain a uniform air distribution, minimizing turbulence that can disrupt particle control during sensitive molding processes.
Protection of Medical-Grade Materials
- Medical-grade polymers, such as PEEK, polycarbonate, and polyethylene, are highly sensitive to environmental contamination. Class 7 cleanrooms prevent material degradation by maintaining a clean and controlled environment.
- The cleanroom conditions also ensure that materials remain compatible with post-production sterilization methods like gamma radiation or ethylene oxide.
Class 7 cleanrooms provide an appropriate level of cleanliness for most medical device molding processes without being excessively costly or complex, making them ideal for high-volume production.
Class 7 cleanrooms provide the ideal conditions for medical molding, ensuring sterility, precision, and compliance. Their advanced contamination controls, environmental stability, and alignment with regulatory standards make them indispensable for the production of critical medical components.
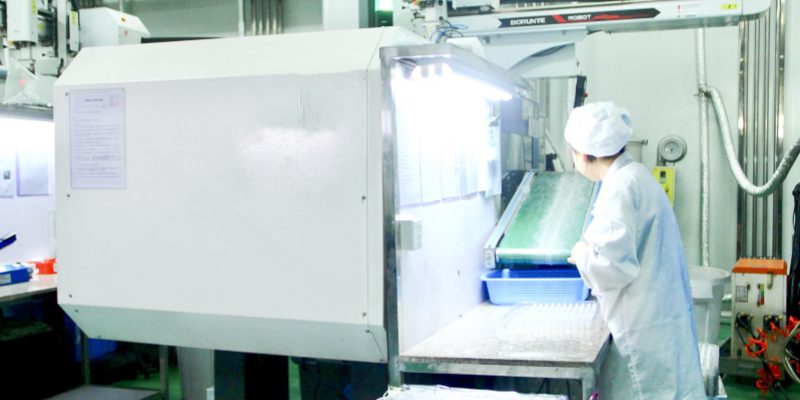
Precision Cleanroom Molding for Medical Devices
Precision cleanroom molding is a high-precision manufacturing technique used in the production of medical devices, ensuring exacting product dimensions and consistency. This process is particularly critical for the manufacturing of complex medical device structures.
Importance of Precision in Cleanroom Molding for Medical Devices
Precision in molding ensures the functionality and reliability of medical devices. This is especially important for devices that require extremely high precision, such as pacemakers, artificial joints, and other critical medical instruments where even the smallest deviation can have significant consequences. In such cases, precision mold medical processes are essential to achieve the necessary accuracy and quality.
Precision is a critical aspect of cleanroom molding for medical devices due to the stringent requirements for safety, functionality, and compliance in the healthcare industry. Medical devices are often used in life-critical applications, where even the smallest manufacturing defect can lead to serious consequences. Below are the key reasons why precision in cleanroom molding is essential:
Ensures Patient Safety
- Medical devices, such as syringes, catheters, and implantable components, must meet exact specifications to function safely and reliably.
- Any deviation in dimensions, material composition, or performance can compromise the safety of patients, leading to potential harm.
- Precision molding minimizes risks by producing components with consistent quality and accurate dimensions.
Supports Regulatory Compliance
- Precision is required to meet strict medical manufacturing standards, including ISO 13485, FDA regulations, and Good Manufacturing Practices (GMP).
- Accurate and consistent manufacturing ensures that medical devices pass rigorous validation, testing, and certification processes mandated by regulatory bodies.
Facilitates Biocompatibility
- Medical devices often come into direct contact with human tissues, blood, or other bodily fluids.
- Precision molding ensures that the material properties remain consistent, preventing unintended reactions, contamination, or degradation that could affect biocompatibility.
Achieves Tight Tolerances
- Many medical devices require extremely tight tolerances, sometimes within microns, to ensure proper fit and functionality.
- For example, components like surgical instruments, diagnostic tools, or drug-delivery devices rely on precise dimensions to function seamlessly without errors.
Maintains Sterility Standards
- Precision in cleanroom molding ensures that parts are free from defects, such as cracks, burrs, or particulate contamination, which could compromise sterility.
- The use of precise molding techniques in a controlled cleanroom environment reduces the risk of contamination during production.
Enables Miniaturization of Devices
- Many modern medical devices are miniaturized to support minimally invasive procedures, such as microfluidics, endoscopic tools, and implantable devices.
- Precision molding techniques, like micro-molding, are essential for manufacturing these small, intricate components with high accuracy.
Precision in cleanroom molding is indispensable for the production of high-quality, reliable, and compliant medical devices. It ensures patient safety, regulatory compliance, and superior device performance while supporting innovation and efficiency in the healthcare industry. By maintaining tight tolerances and adhering to strict quality standards, precision molding helps deliver life-saving solutions with the highest levels of reliability and trust.
Techniques in Precision Cleanroom Molding for Medical Devices
Precision cleanroom molding for medical devices employs advanced techniques to meet the stringent requirements of accuracy, sterility, and reliability. These methods ensure the production of high-quality medical-grade components for critical healthcare applications. Below are the key techniques used:
1. Injection Molding
Injection molding is a widely used method for producing high-precision plastic components by injecting molten polymer into a mold cavity under high pressure. This technique supports complex geometries, ensures tight tolerances, and is suitable for high-volume production. It is commonly used for syringes, housings, and surgical instrument parts.
2. Micro-Molding
Micro-molding specializes in creating extremely small components with dimensions as small as a few microns. It achieves exceptional detail and accuracy, making it ideal for applications like microfluidics, minimally invasive surgical tools, and implantable devices.
3. Overmolding
Overmolding involves molding a layer of material over an existing component to create multi-functional or multi-material parts. This technique reduces assembly steps and enhances functionality, such as adding ergonomic grips or seals to medical devices like handles and instruments.
4. Insert Molding
Insert molding integrates metal or plastic inserts into a molded component during the manufacturing process. It produces durable, integrated components with features such as threaded inserts or embedded sensors, commonly used in surgical devices and diagnostic tools.
5. Two-Shot Molding
Two-shot molding involves the sequential injection of two different materials into the same mold, creating a single component with integrated multi-material features. This technique reduces production time and is often used for medical devices requiring soft-touch surfaces or seals.
6. Liquid Silicone Rubber (LSR) Molding
LSR molding is used to produce flexible and durable components by injecting liquid silicone rubber into molds. This technique is ideal for biocompatible components like catheters, gaskets, and implantable devices, offering thermal stability and resistance to chemical degradation.
7. Gas-Assisted Injection Molding
Gas-assisted injection molding introduces pressurized gas into the mold cavity to create hollow sections in thick parts. This reduces material usage, weight, and the risk of warping, making it suitable for lightweight medical device housings and ergonomic grips.
8. Hot Runner Systems
Hot runner systems use heated channels to deliver molten plastic to the mold cavity, eliminating the need for traditional runners. This approach reduces waste, improves consistency, and shortens cycle times, making it essential for high-precision, high-volume medical molding.
9. Cleanroom-Compatible Mold Design
Molds for cleanroom molding are specifically designed to minimize contamination and ensure precision. Features include polished surfaces, optimized venting systems to prevent air traps, and easy-to-clean designs.
10. Process Monitoring and Automation
Advanced monitoring systems and automation ensure precision and consistency during production. Real-time sensors track parameters like temperature and pressure, while automation minimizes human interaction, reducing contamination risks.
11. Quality Control and Validation
Strict quality control techniques are used to ensure that components meet medical device standards. Methods include dimensional analysis, visual inspections, and process validation protocols like IQ/OQ/PQ (Installation Qualification, Operational Qualification, Performance Qualification).
12. Ultrasonic Welding for Assembly
Ultrasonic welding is used to assemble precision-molded components without adhesives or fasteners. This technique ensures sterile, strong bonds and is commonly employed for multi-part medical devices such as diagnostic equipment and surgical tools.
Precision cleanroom molding techniques are essential for producing high-quality medical devices that meet the strict demands of the healthcare industry. These methods ensure sterility, consistency, and compliance while enabling the creation of innovative and reliable solutions for critical medical applications.
Precision cleanroom molding typically involves the use of advanced automated equipment to precisely control injection pressure, temperature, and speed. Detailed mold design is also a key factor in achieving high precision in the final product.
Clean Room Injection Molding Kits
Clean room injection molding kits are compact, customizable systems designed to enable small-scale or specialized production in a controlled environment. These kits are essential for projects that require high-precision molding, especially in industries like medical device manufacturing, where contamination-free processes are critical. Clean room injection molding kits provide a practical solution for companies or research institutions that need to produce small quantities of components while maintaining strict cleanliness standards.
Description of Clean Room Injection Molding Kits
Clean room injection molding kits are composed of several key components that are tailored for high-precision production. These components include specialized tools, precision molds, and high-quality resin materials that are selected based on the specific needs of the project. The tools in these kits are designed for precise control over the molding process, ensuring that parts are formed to exact specifications. The molds are often custom-designed to meet the unique requirements of the product being produced, while the resin materials are chosen to meet stringent quality and cleanliness standards.
These kits are particularly well-suited for small-scale or custom production needs, where high-volume, large-scale equipment is not necessary. They offer the flexibility to experiment with different designs and materials, which is essential for prototyping and specialized manufacturing.
Typical Uses of Clean Room Injection Molding Kits
Clean room injection molding kits are versatile tools that are widely used across various industries for different applications, especially where cleanliness and precision are critical. These kits are essential in fields such as medical device manufacturing, pharmaceuticals, and aerospace engineering, where contamination control and high-quality results are paramount.
Prototyping New Designs
One of the most common uses of clean room injection molding kits is for prototyping new designs. In product development, particularly in industries like medical devices or pharmaceuticals, it is crucial to test designs early in the process to assess their functionality and quality. Clean room environments ensure that prototypes are produced without contamination, which is critical when the components will undergo further testing or clinical trials. By using these kits, designers can quickly produce functional prototypes in a sterile setting, minimizing the risk of contamination and ensuring the final product meets stringent quality standards. This ability to prototype in a controlled environment helps to expedite the design validation process and reduce time to market.
Custom Manufacturing of High-Precision Parts
Clean room injection molding kits are also widely used for custom manufacturing of high-precision parts, particularly for specialized applications. Industries such as medical device manufacturing often require components with exact specifications to meet regulatory and performance standards. These parts might be small, intricate, and need to perform under strict conditions, such as being free from contaminants that could compromise their function or safety.
For example, in the production of surgical instruments, drug delivery systems, or diagnostic equipment, these kits enable manufacturers to produce components that meet the exacting standards of the industry while adhering to cleanliness requirements. Clean room injection molding kits allow for the production of these critical components on a smaller scale, making them an ideal solution for custom or low-volume production runs.
Low-Volume Production for Specialized Markets
Another typical use of clean room injection molding kits is for low-volume production of specialized parts. Many industries, including medical, aerospace, and electronics, often require components in smaller quantities, especially during the development or testing phase. Clean room injection molding kits enable companies to produce high-quality parts in these lower volumes without the need for a full-scale manufacturing facility.
For instance, a company developing a new type of medical implant might need to produce only a limited number of components for initial trials or clinical testing. With a clean room injection molding kit, they can produce these components in a controlled, sterile environment, ensuring that they meet the necessary quality standards without the high cost of large-scale production.
Manufacturing for Highly Regulated Industries
Clean room injection molding kits are critical for manufacturing components for highly regulated industries, such as medical devices, pharmaceuticals, and biotechnology. These industries are subject to rigorous standards, including FDA regulations and ISO certifications, which require that components be produced in sterile environments to prevent contamination. Clean room injection molding kits offer a cost-effective solution for producing small batches of components while ensuring that the manufacturing process meets these regulatory requirements.
For example, when producing parts for implantable medical devices, clean room injection molding kits ensure that the components are free from dust, particles, or other contaminants that could compromise the safety and effectiveness of the device. By using these kits, manufacturers can maintain compliance with industry regulations while producing high-quality parts for critical applications.
Research and Development
In research and development (R&D) settings, clean room injection molding kits play a crucial role in exploring new materials, techniques, and product designs. R&D teams often need to create specialized parts or conduct tests on prototypes under controlled conditions to better understand how they will behave in real-world applications. Clean room injection molding kits allow researchers to carry out these experiments while maintaining a high level of cleanliness and minimizing contamination risks.
For example, in the development of new drug delivery systems, researchers may need to create prototype components using specific polymers or materials. Clean room injection molding kits provide the necessary tools to produce these parts under sterile conditions, enabling the researchers to gather valuable data for further development.
Short-Run and Custom Orders for Clients
Clean room injection molding kits are also used for fulfilling short-run and custom orders from clients who need specialized parts produced quickly and in small quantities. Whether for replacement parts, limited-edition products, or custom modifications, these kits offer flexibility and precision to meet the specific requirements of clients.
For instance, a company that designs custom medical equipment may receive an order for a batch of specialized components that are not part of their regular product line. Using a clean room injection molding kit, the company can efficiently produce the components in a clean, controlled environment, ensuring that they meet both the client’s specifications and the necessary cleanliness standards.
Benefits of Clean Room Injection Molding Kits
Clean room injection molding kits provide a unique solution for businesses and research teams that need to perform high-quality, contamination-free injection molding without the expense and complexity of a full-scale clean room setup. These kits offer several key benefits, making them an attractive option for startups, smaller companies, and specialized projects. Below, we explore these benefits in detail, highlighting their advantages, as well as some potential drawbacks.
Accessibility for Specialized Projects
One of the primary benefits of clean room injection molding kits is their accessibility for specialized projects. These kits allow smaller businesses, research teams, or universities to access clean room production capabilities without investing in a large, complex clean room facility. For startups or organizations with limited resources, these kits make it possible to carry out high-precision, contamination-free molding on a smaller scale. This accessibility opens up opportunities for innovation, experimentation, and prototyping in industries such as medical device manufacturing, pharmaceuticals, and aerospace engineering.
For example, a small medical device startup can use a clean room injection molding kit to produce small batches of custom components, such as syringe parts or surgical instrument handles, before scaling up to full production. This can be a crucial step in the early stages of product development, allowing companies to test designs and make adjustments before committing to large-scale manufacturing, especially when working with prototype medical equipment molds.
Lower Investment Compared to Full Clean Room Setups
Another significant advantage of clean room injection molding kits is the lower investment required compared to setting up a full clean room facility. Constructing and maintaining a traditional clean room involves significant costs, including building a controlled environment, installing specialized filtration systems, and adhering to regulatory standards. For many companies, especially those just starting out, these costs can be prohibitive.
Clean room injection molding kits offer a more affordable option by providing the necessary tools, molds, and equipment in a compact, ready-to-use package. This makes it easier for companies to enter clean room manufacturing without bearing the high upfront costs of constructing a full clean room. As a result, businesses can still produce high-quality, sterile components for prototyping, research, and low-volume production while keeping their investment manageable.
Ideal for Prototyping and Custom Manufacturing
Clean room injection molding kits are particularly valuable for prototyping and custom manufacturing. In industries such as medical devices, aerospace, and consumer electronics, companies often need to create small quantities of customized or specialized parts to test new designs, conduct research, or meet specific client needs. These kits enable manufacturers to produce high-quality prototypes without waiting for large-scale production or incurring excessive costs.
For instance, a research team developing a new drug delivery device might use a clean room injection moulding kit to produce precise, small-batch components for clinical trials or testing. This flexibility allows companies to iterate on their designs quickly and efficiently, without the long lead times and cost barriers associated with traditional injection molding processes.
Maintaining High-Quality Standards
Despite the smaller scale of production, clean room injection kits help businesses maintain high-quality standards in their products. These kits are designed to operate within controlled environments, ensuring that molded components are free from contamination. For industries such as medical device manufacturing, where product quality and sterility are critical, these kits provide a practical solution for producing defect-free components.
The integration of features like HEPA filters, laminar flow hoods, and anti-static measures ensures that the production environment meets industry standards for cleanliness, even in smaller, more portable setups. By using these kits, manufacturers can consistently produce high-precision, contamination-free parts that meet the regulatory requirements for industries like healthcare and pharmaceuticals.
Flexibility and Scalability
Clean room injection molding kits are highly flexible and scalable, allowing businesses to adjust their production capabilities based on current needs. Whether a company is producing a small batch of custom parts for a specific project or scaling up production for a larger run, these kits can be adapted to accommodate various production volumes and product types. This flexibility is especially valuable for companies that need to quickly pivot or scale their operations in response to changing market demands.
For example, a startup company in the medical device sector may initially use a clean room injection molding kit to produce a small number of components for prototype testing. As the product gains market acceptance, the company can scale up production with minimal investment, using the same clean room injection molding kit to meet higher demands.
Regulatory Compliance and Certification
Clean room injection molding kits are designed to help companies adhere to the stringent regulatory compliance standards required in industries like medical device manufacturing, pharmaceuticals, and biotechnology. These industries are subject to strict regulations, such as FDA guidelines, ISO standards, and Good Manufacturing Practices (GMP), which demand the highest levels of cleanliness and product integrity.
By utilizing clean room injection molding kits, companies can ensure that their products meet the necessary regulatory standards for sterility and precision. These kits help streamline the manufacturing process by providing the necessary equipment and tools to maintain compliance with these critical standards, reducing the risk of product recalls or legal issues down the line.
Reducing Financial Barriers to Clean Room Production
One of the key advantages of clean room injection molding kits is their ability to reduce the financial barriers to clean room production. Full-scale clean room facilities require significant capital investment, not just in physical infrastructure, but also in ongoing operational costs such as personnel, maintenance, and regulatory audits. Clean room injection molding kits, on the other hand, offer a more cost-effective solution for companies that need clean room capabilities on a smaller scale.
This reduced financial commitment makes it easier for businesses to enter specialized markets, such as medical device or pharmaceutical manufacturing, without the burden of large capital expenditures. It also allows companies to experiment with new designs or processes without committing to a large-scale manufacturing setup.
Potential Drawbacks
While injection molding in clean room kits offer many advantages, they do have some limitations. One potential drawback is the limitation in production volume. While these kits are perfect for low-volume production, prototyping, and small-scale custom manufacturing, they may not be suitable for mass production runs that require high throughput. As production volumes increase, the need for more advanced systems or full-scale clean room setups may arise.
Another potential limitation is the capacity of the kit’s equipment. Some specialized molds, materials, or production processes may require more advanced tools than what is available in a clean room injection molding kit. In such cases, businesses may need to upgrade their equipment or transition to a larger-scale clean room facility as their needs evolve.
Case Study: Startups Using Clean Room Injection Molding Kits
A real-world example of the effectiveness of clean room injection molding kits can be seen in startups in the medical device sector. For instance, a company developing a new type of wearable drug delivery system used a medical injection moulding cleanroom kit to produce small batches of components for testing. The flexibility of the kit allowed the company to produce prototypes quickly and make adjustments to the design based on early-stage feedback from clinical trials. By using the kit, the company was able to avoid the high costs of building a full-scale clean room facility, allowing them to bring their product to market faster and more affordably.
Cost of Clean Room Injection Molding
The cost of clean room injection molding can vary significantly depending on several factors, including the initial setup, operational expenses, and compliance requirements. Producing high-quality, contamination-free components in a controlled environment requires specialized equipment, facilities, and strict adherence to regulatory standards, which all contribute to the overall cost.
Factors Affecting Costs
Initial Setup
The initial setup for medial injection moulding cleanroom involves several key expenses. One of the major costs is the design and construction of an ISO-compliant clean room facility. Clean room environments must adhere to strict ISO standards, such as ISO 14644, which define the permissible levels of airborne particles. Constructing a clean room that meets these standards requires specialized materials, precise airflow systems, and significant investments in infrastructure.
Additionally, the procurement of specialized equipment is essential for maintaining the required cleanliness levels in the facility. Equipment such as HEPA filters, laminar flow systems, and other air purification systems are crucial for controlling the air quality and preventing contamination during the medical injection molding process. These systems are often costly but necessary to ensure that the manufacturing environment remains sterile and meets industry standards.
Operational Expenses
Operational expenses are another important factor in the cost of clean room injection molding. These include maintenance costs for the equipment, the labor required to operate and monitor the clean room, and the consumption of materials used in the molding process. Clean rooms require regular maintenance to ensure that equipment such as HEPA filters and laminar flow systems are functioning properly. This maintenance can be costly, particularly for larger or more complex systems.
Labor costs can also add up, as medical plastic injection moulding cleanroom requires highly trained personnel to operate the equipment and monitor the environment. These workers must follow strict protocols to ensure that contamination is minimized, which often requires additional training and expertise. Material costs are another consideration, as high-quality, specialized resins and other materials are used in the process to meet the cleanliness and performance standards required for medical and other sensitive applications.
Compliance Costs
Compliance with industry regulations adds another layer of cost to clean room injection molding. Companies must undergo regular audits and certifications to ensure that they meet ISO, FDA, and other relevant regulatory standards. These audits can be expensive and time-consuming, as they require extensive documentation, testing, and validation to demonstrate compliance.
In addition to regulatory audits, companies must invest in ongoing validation processes to maintain certifications and ensure that their clean room environments remain compliant with the required standards. This includes performing regular testing and monitoring of environmental conditions, such as particulate levels, temperature, and humidity, to ensure consistent quality throughout the production process.
Comparison: Clean Room Injection Molding vs. Traditional Molding
Below is a comparison of the costs between clean room injection molding and traditional molding methods:
Factor | Clean Room Injection Molding | Traditional Molding |
---|---|---|
Initial Setup Cost | High (ISO-compliant facilities, specialized equipment) | Low (standard molding equipment) |
Operational Expenses | High (maintenance, labor, material costs) | Lower (less specialized equipment) |
Compliance Costs | High (regulatory audits, certifications, ongoing validation) | Minimal (no need for regulatory audits or certifications) |
Labor Requirements | Highly skilled labor, specialized training | Standard labor with less training required |
Material Quality and Cost | High-quality, specialized materials | Standard materials, lower cost |
Production Volume | Low to medium (small-scale, custom production) | High (mass production) |
As the table shows, clean room injection molding tends to have higher initial setup, operational, and compliance costs compared to traditional molding. However, it is necessary for producing high-precision, contamination-free components, particularly for industries such as medical devices, where compliance with strict standards is essential. Traditional molding, on the other hand, is more cost-effective for mass production of non-critical components where cleanliness and contamination control are less of a concern.
Clean Room Injection Molding for Sale
The market for clean room injection molding systems offers a variety of solutions designed to meet the growing demand for contamination-free, high-quality manufacturing. Whether for small-scale custom production or larger, more complex applications, clean room injection molding systems for sale are available in various configurations to suit different operational needs. These systems range from modular setups for rapid deployment to complete, fully integrated clean room medical molding solutions for high-precision manufacturing in regulated environments.
Market Availability of Clean Room Molding Systems
One of the key trends in the clean room injection molding market is the availability of modular clean rooms. These systems are designed for quick setup and scalability, allowing manufacturers to establish a controlled environment with minimal time and effort. Modular clean rooms are often pre-fabricated, meaning they can be assembled and installed quickly, providing flexibility for businesses that need to adapt to changing production demands. Additionally, these systems can be expanded as needed to accommodate growing production volumes or evolving regulatory requirements.
Another popular option is complete systems that come with integrated HEPA filtration and advanced environmental controls. These systems are designed to ensure that the clean room environment meets the strictest standards for particulate control, air quality, and humidity, making them ideal for sensitive applications such as medical device manufacturing. The advanced controls in these systems help regulate factors like airflow, temperature, and particle count, ensuring optimal conditions for injection molding processes.
Features to Evaluate When Purchasing Clean Room Injection Molding Systems
When purchasing clean room injection molding systems, there are several key features to consider to ensure that the system meets the specific needs of your business.
- ISO Certification Compliance
One of the most important factors when selecting a clean room injection molding system is whether it complies with ISO standards, particularly ISO 14644, which defines clean room classifications based on allowable particulate levels. The system should meet the necessary clean room classification requirements (ISO 5, ISO 6, etc.) for the intended application, whether for medical devices, pharmaceuticals, or other sensitive products. Ensuring compliance with these standards is crucial for meeting regulatory requirements and ensuring product quality. - Adaptability for Diverse Applications
Clean room injection molding systems should be adaptable to a wide range of applications, from medical device manufacturing to industrial and electronic components. The flexibility of the system allows manufacturers to handle various materials, product sizes, and production volumes. Systems that can easily be reconfigured or upgraded to meet changing needs provide significant value, especially for companies involved in research and development or small-batch production. - Integrated Systems for Efficiency and Precision
Many clean room medical injection molding systems for sale come as fully integrated solutions, combining the injection molding machine with the clean room environment and necessary filtration systems. These integrated systems help streamline production by ensuring that all components work together efficiently. The seamless integration of systems improves both operational efficiency and precision in the manufacturing process. Advanced controls allow for real-time monitoring of critical parameters, such as air quality, temperature, and mold pressure, ensuring consistent and reliable production of high-quality components.
Clean Room Injection Molding
Clean room injection molding is increasingly used in contract manufacturing services, offering businesses a way to produce high-quality, contamination-free components without the need for substantial capital investments in clean room facilities. Contract manufacturers specializing in cleanroom medical injection molding provide a unique advantage by managing the complexities of clean room environments while ensuring adherence to strict industry standards and regulations.
Explanation of Contract Manufacturing Services in Clean Room Settings
Clean room contract manufacturing services allow companies to outsource the production of components in highly controlled environments, such as clean rooms, without having to build or maintain their own facilities. These services typically include the design and production of precision components, using clean room injection molding techniques, that meet the stringent quality and cleanliness standards required for industries like medical devices, pharmaceuticals, and aerospace.
Contract manufacturers that offer clean room injection molding provide end-to-end solutions, from initial product development and prototyping to full-scale production. These services often include access to specialized equipment, tools, and materials that are essential for producing contamination-free products, as well as a skilled workforce trained in maintaining the strict protocols of clean room environments.
Key Benefits of Clean Room Contract Manufacturing
- Access to High-Grade Facilities Without Capital Investments
One of the primary benefits of clean room contract manufacturing is that it provides access to high-grade, ISO-compliant clean room facilities without requiring companies to invest in the infrastructure themselves. Establishing and maintaining a clean room facility is a significant capital expense, and many smaller companies or those with fluctuating production volumes may not have the resources to invest in this. Contract manufacturing allows these businesses to leverage the expertise and facilities of established clean room operators, reducing overhead costs while maintaining the required cleanliness standards. - Expertise in Tooling, Materials, and Compliance
Clean room injection molding is a specialized process that requires knowledge of precise tooling, specialized materials, and regulatory compliance. Contract manufacturers have the necessary expertise to ensure that the production process meets the required technical and regulatory standards. This includes selecting the appropriate materials, such as medical-grade plastics, that comply with FDA and ISO certifications, and using specialized tools and equipment designed for contamination-free production. - Flexibility to Scale Production Based on Demand
Clean room contract manufacturing services offer flexibility to scale production volumes according to demand. This is particularly beneficial for companies involved in product development or those with variable or seasonal production needs. Contract manufacturers can adjust their production capacity quickly, allowing businesses to respond to market changes without the need for significant upfront investment in additional manufacturing capacity. This flexibility ensures that companies can produce components in the necessary quantities, whether it’s for small-scale prototyping or large-scale production runs.
Industries Leveraging Clean Room Contract Manufacturing
Several industries rely heavily on clean room contract manufacturing to produce high-quality, contamination-sensitive components. Among the key sectors are:
- Medical Devices
The medical device industry requires the highest levels of cleanliness and precision, as even small amounts of contamination can jeopardize patient safety. Clean room injection molding is essential for the production of medical devices such as surgical instruments, implants, and diagnostic equipment. Contract manufacturers help companies in this sector by providing access to ISO-compliant clean rooms and ensuring that all components meet strict regulatory standards, such as those set by the FDA and ISO 13485. - Aerospace Engineering
Aerospace components must meet strict performance and safety standards, and cleanroom molding medical ensures that parts are produced without contamination that could affect their function or integrity. Clean room contract manufacturers specializing in aerospace parts can produce high-precision components such as sensors, connectors, and valves that are critical to the safety and performance of aircraft. These components often need to adhere to both regulatory and material performance standards, which clean room environments help maintain. - Pharmaceuticals
The pharmaceutical industry also benefits from clean room contract manufacturing services, particularly for the production of drug delivery systems, medical packaging, and sterile components. Clean room injection molding is essential for ensuring that pharmaceutical components are free from contamination, which is critical in ensuring the efficacy and safety of drugs and treatments. Contract manufacturers in the pharmaceutical industry must comply with rigorous standards, such as Good Manufacturing Practices (GMP), and the clean room environment plays a vital role in meeting these requirements.
Clean Room Injection Molding: Medical Device Cleaning Services in Clean Room Facilities
In clean room facilities, medical device cleaning services play a critical role in ensuring that components meet the highest standards of sterility and quality. These services are essential for the medical device manufacturing process, especially when the devices are intended for sensitive applications where contamination could compromise patient safety or device functionality. Cleaning medical devices in controlled environments helps minimize contamination risks and ensures compliance with stringent industry regulations.
Importance of Cleaning Medical Devices in Controlled Environments
The primary importance of cleaning medical devices in controlled environments is to ensure sterility and eliminate any risk of contamination. In industries like healthcare, even the smallest particle or microorganism can lead to severe consequences. Medical devices, especially those that are implanted or come into direct contact with the human body, must be free from contaminants to ensure patient safety. Clean room environments offer a sterile setting where particles, bacteria, and other harmful elements are strictly controlled.
Additionally, cleaning medical devices in clean room environments helps maintain regulatory compliance. The FDA, ISO, and other regulatory bodies require medical devices to meet certain cleanliness and sterility standards. These standards ensure that medical products are safe and effective. By performing cleaning procedures in clean room facilities, manufacturers can meet the necessary requirements for certification and avoid costly compliance failures. Regular validation and auditing in these controlled environments further ensure that all cleaning processes are in line with regulatory expectations.
Common Cleaning Techniques
To meet the demanding cleanliness standards required for medical devices, a range of cleaning techniques are employed in clean room environments:
- Ultrasonic Cleaning for Intricate Components
Ultrasonic cleaning is a commonly used method for cleaning intricate or delicate medical components. This technique uses high-frequency sound waves to create tiny bubbles in a cleaning solution, which gently remove contaminants from the surfaces of medical devices. Ultrasonic cleaning is particularly effective for cleaning parts with complex geometries, small crevices, or porous surfaces, ensuring thorough sterilization without damaging the components. - Chemical Disinfection for Robust Sterilization
For devices requiring more robust sterilization, chemical disinfection is often employed. In this process, medical devices are submerged in or sprayed with specific disinfecting chemicals, which eliminate harmful microorganisms. This method is especially useful for cleaning devices made of durable materials that can withstand the strong chemicals used for disinfection, ensuring that devices remain sterile and safe for use. - Sterile Packaging Performed Under Controlled Conditions
After cleaning, medical devices are often packaged in sterile conditions to maintain their cleanliness. Sterile packaging is performed within the clean room to ensure that the packaging material does not introduce contaminants. This is a critical step in preventing microbial contamination during transportation or storage, especially for devices intended for surgical use or other sensitive medical applications.
Role of Clean Room Injection Molding in Reducing Contamination Risks During Production
Clean room injection molding plays a key role in reducing contamination risks during the production of medical devices. By manufacturing components in a clean room environment, injection molding processes are able to maintain high levels of sterility, ensuring that components are free from contaminants before they undergo cleaning and sterilization. The controlled conditions of the clean room help prevent the introduction of particles, dust, or other foreign materials into the molded parts.
In clean room injection molding, the materials used are also specifically chosen to meet the rigorous requirements of medical applications. For example, medical-grade plastics are often employed, which are formulated to resist contamination and degradation during the molding process. Additionally, the precision of clean room injection molding reduces the likelihood of defects, such as particulates or surface imperfections, which could otherwise compromise the cleanliness or performance of the medical device.
By integrating clean room injection molding with medical device cleaning services, manufacturers can ensure a consistent, high-quality production process that minimizes contamination risks at every stage, from initial molding to final packaging. This combination of practices allows medical devices to meet the strict cleanliness and sterility standards required for patient safety, regulatory compliance, and overall device performance.
Clean Room Injection Molding: Injection Moulding Tool Manufacturers for Clean Rooms
Injection molding tools used in clean room environments are critical components in the manufacturing process, ensuring that high-quality, defect-free products are produced consistently under sterile conditions. These tools are designed to meet the stringent requirements of clean room protocols, allowing for the precise and contamination-free production of sensitive components, particularly in industries such as medical devices and pharmaceuticals. Manufacturers of injection molding tools for clean rooms play a vital role in providing equipment that aligns with the cleanliness and regulatory standards required for these high-stakes applications.
Role of Precision Tools in Clean Room Injection Molding
Precision tools are indispensable in clean room injection molding because they directly impact the quality of the final product. In clean room environments, even minor defects or contamination can compromise the integrity of the molded parts, which is especially critical in sectors such as medical device manufacturing. Precision tooling ensures that the injection molding process is carried out with high accuracy, producing components that meet exact specifications without introducing defects, particulates, or surface imperfections.
These tools are designed to work within controlled environments, where air quality, temperature, and humidity are carefully regulated to prevent contamination. The molds themselves must be made to high tolerances, ensuring that each part is produced with minimal variation. High-precision tooling also allows for repeatable processes, which are essential for high-volume production of consistent parts required in industries like medical devices and pharmaceuticals.
Characteristics of Reliable Tooling
When selecting injection molding tools for clean room environments, it’s essential to consider certain characteristics to ensure reliability and compatibility with strict clean room protocols.
Durability for Extended Usage
Injection molding tools used in clean room settings must be highly durable to withstand extended use without compromising their functionality. The constant cycle of molding, cleaning, and maintenance can place significant stress on the tools, so they must be manufactured from high-quality materials, such as hardened steel or other corrosion-resistant alloys. This durability ensures that the tools maintain their precision and performance over a long lifespan, reducing the need for frequent replacements and minimizing downtime in the manufacturing process.
Compatibility with Clean Room Protocols
Tooling used in medical molding in a clean room must be compatible with the strict protocols governing clean room environments. This includes the ability to withstand cleaning and sterilization processes without degrading or introducing contaminants. Tools must be designed to be easily cleaned and maintained to avoid the accumulation of dust, particles, or other foreign materials that could compromise the sterility of the environment. Additionally, the design and materials of the tooling should support airflow patterns and other clean room-specific requirements.
Customizability for Specific Design Needs
Reliable injection molding tools are often customizable to meet specific design needs for various applications. In clean room injection molding, the ability to customize tooling ensures that molds can be tailored for different parts or products, whether it’s for the production of medical devices, drug delivery systems, or other specialized components. Customization may include features such as intricate cavity designs, multi-cavity molds, or specialized gating systems to enhance production efficiency, precision, and quality.
Examples of Industries Requiring Medical-Grade Injection Moulding Tools
Injection molding tools for clean rooms are essential in several industries that demand the highest standards of cleanliness, precision, and regulatory compliance. Below are examples of industries that rely on medical-grade injection molding tools:
- Surgical Instrument Production
Surgical instruments must meet extremely high standards of precision and sterility. Tools used in the manufacturing of these instruments must be capable of producing components with the tightest tolerances to ensure they function correctly in medical procedures. Clean room injection molding tools allow for the mass production of surgical instruments while maintaining the highest quality and cleanliness standards. Custom tools may be used for creating complex parts with intricate geometries, such as surgical forceps or scalpels, which require both accuracy and sterilization. - Drug Delivery Systems
Drug delivery systems, such as insulin pens, inhalers, and injection devices, are critical to patient care and must be manufactured in contamination-free environments. Clean room injection molding tools are essential for producing these components, as they must ensure the safe, effective delivery of medication without risk of contamination. The tools used in these processes are designed for the precise molding of medical-grade plastics and must comply with strict regulatory standards, including those set by the FDA and ISO. The customization of molds for different types of drug delivery devices helps ensure that each device performs reliably and safely.
Clean Room Injection Molding: Advantages of Clean Room Injection Molding
Clean room injection molding offers numerous advantages for industries that require precise, contamination-free manufacturing, especially in fields like medical devices, pharmaceuticals, and aerospace. By leveraging the controlled environment of a clean room, manufacturers can minimize contamination risks, ensure regulatory compliance, and produce high-quality components with greater efficiency. Below are some key benefits of utilizing clean room injection molding.
These services minimize contamination risks, enhance production efficiency, and ensure the final product’s biocompatibility and functionality, which is particularly crucial for sensitive medical devices and instruments.
Reduced Contamination Risks: Controlled environments ensure sterility and reduce particulate contamination.
High Precision and Quality: Advanced molding techniques deliver reliable, consistent components.
Regulatory Compliance: Services tailored to meet stringent healthcare industry standards.
Scalability: Efficient production for both small-volume prototyping and high-volume manufacturing.
Benefits of Utilizing Clean Room Injection Molding
Contamination Control
One of the most significant advantages of clean room injection molding is its ability to prevent contamination during the manufacturing process. Clean room environments are specifically designed to control the presence of particulates, dust, and microorganisms, which are common sources of defects in molded parts. By maintaining a sterile environment with controlled air quality and airflow patterns, clean rooms significantly reduce the risk of contamination, ensuring that no foreign particles interfere with the production of medical devices, surgical instruments, or other sensitive components. The controlled environment of clean room injection molding plays a crucial role in enhancing patient safety and product reliability. In medical applications, even the smallest particle of contamination can jeopardize the effectiveness or safety of a device, leading to potential health risks. Clean room injection molding ensures that the molded components are free from harmful contaminants, thereby safeguarding patient health and improving the overall reliability of the final product. Additionally, the process allows for consistent, high-quality results, ensuring that every part meets exact specifications.
Regulatory Compliance
Clean room injection molding is essential for meeting the rigorous regulatory standards imposed by organizations such as the FDA, ISO, and GMP. These standards require manufacturers to adhere to specific cleanliness levels and quality control measures to ensure the safety and efficacy of medical products, drugs, and other sensitive components. In industries like healthcare and pharmaceuticals, regulatory compliance is non-negotiable, as failure to meet these standards can result in legal liabilities, product recalls, and delays in the supply chain. The clean room environment helps ensure compliance with these standards by maintaining strict control over particulate levels, temperature, humidity, and air pressure. This reduces the risk of non-compliance and the associated legal or supply chain delays. By using clean room injection molding, manufacturers can avoid costly regulatory failures and ensure that their products are consistently manufactured to meet the highest industry standards.
Quality Improvements
Clean room injection molding also offers quality improvements by ensuring that parts are produced with high precision and consistency. The controlled environment eliminates variables that might otherwise affect the molding process, such as dust or humidity, which can cause defects or variations in the final product. As a result, clean room injection molding enables the consistent production of high-precision components that meet the exact specifications required for critical applications. Additionally, clean room injection molding allows for the production of intricate and complex parts that require tight tolerances. These parts are often found in sensitive industries, such as medical device manufacturing, where the smallest defect can compromise functionality. The combination of advanced molding technology and the clean room environment ensures that each component is made to the highest standards, reducing the need for rework or waste and improving overall production efficiency.
Clean Room Injection Molding: Future Trends in Clean Room Injection Molding
As industries like medical devices, pharmaceuticals, and aerospace continue to demand higher levels of precision, sterility, and efficiency in manufacturing, the field of clean room injection molding is evolving rapidly. Emerging trends in clean room injection molding point to advances in sustainability, automation, and flexibility, which will drive the future of high-precision, contamination-free manufacturing. Below, we explore the key trends that are shaping the future of this essential manufacturing process.
Growing Focus on Sustainable Materials for Medical Manufacturing
One of the most significant trends in clean room injection molding is the growing focus on sustainable materials. As environmental concerns rise and regulatory bodies impose stricter guidelines on waste and resource consumption, manufacturers are increasingly turning to eco-friendly materials for producing medical components. These materials include biodegradable plastics, recycled materials, and bio-based polymers, which offer a more sustainable alternative to traditional petroleum-based plastics. The adoption of sustainable materials in clean room injection molding allows companies to reduce their environmental footprint while maintaining the required levels of sterility and safety for medical products. By integrating materials that meet both environmental and regulatory standards, manufacturers can help minimize waste and promote sustainability in the medical device and pharmaceutical sectors, where product quality and safety are paramount.
Increasing Integration of Automation and Robotics to Reduce Human Error
Another emerging trend is the increasing integration of automation and robotics into clean room injection molding processes. Automation and robotics technologies are being increasingly implemented to streamline the production process, improve precision, and reduce the likelihood of human error. These innovations help ensure that the injection molding process remains consistent and efficient, especially when working with high-precision medical components that require exacting standards. Automated systems can control variables such as mold temperature, injection speed, and pressure with high accuracy, reducing the risk of defects or inconsistencies in the final product. Furthermore, robots can be used to handle delicate components, minimizing the potential for contamination during handling. This trend also supports the growing demand for faster production cycles, higher throughput, and more cost-effective manufacturing, without compromising the stringent requirements of clean room environments.
Adoption of Modular Clean Room Designs for Flexibility and Cost Savings
As industries evolve, the need for modular clean room designs has become more prominent. Modular clean rooms offer flexibility and cost savings by allowing manufacturers to quickly scale their facilities to meet production demands or regulatory requirements. These modular units can be easily expanded, reconfigured, or moved, making them ideal for businesses that require adaptability and efficiency in their manufacturing processes. For clean room injection molding, modular clean rooms provide manufacturers with the ability to customize their production environment to suit the specific needs of the products being made. Whether it’s a small-scale production run of highly specialized medical devices or a larger batch of standard components, modular clean rooms offer the flexibility to adjust capacity without the high capital costs of constructing a permanent facility. This trend also helps reduce lead times and provides a more cost-effective approach for companies looking to enter new markets or respond to changing demand.
FAQs about Clean Room Injection Molding
Clean rooms are classified into different ISO levels based on the maximum allowable particle concentration in the air. The classification follows the ISO 14644-1 standard, which is widely used in industries such as medical manufacturing. ISO levels range from ISO 1 (the cleanest) to ISO 9 (the least clean). In medical applications, the most commonly used clean room classifications are ISO 5 to ISO 8.
ISO 5 Clean Rooms: These are among the cleanest environments used in medical device manufacturing, especially for critical applications like implantable devices and surgical instruments. In ISO 5, the air can contain a maximum of 3,520 particles (0.5 microns) per cubic meter.
ISO 6 to ISO 8 Clean Rooms: These levels are used for general medical manufacturing and assembly. For example, ISO 7 clean rooms are suitable for packaging sterile products, while ISO 8 rooms are typically used for processes requiring moderate contamination control.
Each ISO level requires specific controls on air cleanliness, temperature, humidity, and personnel protocols to minimize contamination. Higher levels, such as ISO 5, require more stringent measures, including advanced filtration systems like HEPA filters and a higher number of air changes per hour (ACH).
For medical applications, choosing the right ISO level depends on the product’s contamination sensitivity. For instance, sterile medical devices require ISO 7 or higher environments to ensure compliance with FDA and EU MDR regulations, safeguarding patient safety.
Clean rooms have strict requirements to ensure a controlled environment for manufacturing and assembly, especially in the medical field. The following are the primary requirements for clean rooms:
Air Quality and Filtration: Clean rooms rely on HEPA (High-Efficiency Particulate Air) filters to remove 99.97% of particles as small as 0.3 microns. For higher ISO levels like ISO 5, ULPA (Ultra-Low Penetration Air) filters may also be used. Regular air changes, ranging from 20 to over 600 per hour depending on the ISO level, maintain low particle levels.
Temperature and Humidity Control: Consistent temperature and humidity are vital to prevent condensation, material degradation, and static electricity. For medical clean rooms, humidity is often maintained between 30–50%, while the temperature is kept between 20–22°C.
Personnel Protocols: Personnel must follow strict gowning procedures, including wearing sterile gloves, face masks, and cleanroom suits. Entry is controlled through airlocks and gowning rooms to prevent contamination.
Material Handling: Materials entering the clean room must undergo cleaning or sterilization to ensure they do not introduce contaminants.
Monitoring and Maintenance: Regular monitoring of air quality, particle levels, and equipment is required. Certification of clean rooms must adhere to standards like ISO 14644 and regulatory requirements such as FDA CFR 21 Part 11 for medical applications.
These requirements ensure that clean rooms provide a sterile environment essential for producing high-quality medical devices and meeting strict regulatory standards.
The concept of a clean room revolves around creating a controlled environment where contamination from particles, microorganisms, and chemical vapors is minimized. This is particularly important in the medical field, where even minor contamination can compromise patient safety and product effectiveness.
In a clean room, the environment is engineered to limit the number of airborne particles. This is achieved using advanced air filtration systems like HEPA or ULPA filters, which continuously filter the air to remove dust, bacteria, and other contaminants. The airflow is often designed as laminar flow, moving uniformly to prevent turbulence that might disturb settled particles.
Clean rooms are categorized by ISO 14644-1 standards, ensuring that specific cleanliness levels are met. Medical applications rely on clean rooms to manufacture sterile devices like catheters, surgical instruments, and implantable devices. The concept also extends to controlling temperature, humidity, and electrostatic discharge, which could affect sensitive medical materials.
Personnel and equipment inside the clean room are also regulated to minimize contamination. Workers wear gowning attire, and strict protocols ensure that no external contaminants are introduced. This concept is critical in the medical industry to maintain sterility, comply with regulatory requirements like the FDA and EU MDR, and ensure patient safety.
The FDA has specific requirements for cleanrooms, especially in the medical and pharmaceutical industries, to ensure product sterility and safety. These requirements are largely based on Good Manufacturing Practices (GMP) guidelines and are designed to prevent contamination in the production of sterile drugs, medical devices, and biologics.
Key aspects of FDA cleanroom requirements include air quality and filtration systems, such as HEPA or ULPA filters, to maintain air cleanliness. The classification of the cleanroom (e.g., ISO 5, ISO 7) determines the allowable particle limits per cubic meter of air. Additionally, cleanrooms must maintain controlled airflow with positive or negative pressure differentials, depending on the type of product being manufactured. Positive pressure is used to keep contaminants out, while negative pressure is required for hazardous material handling.
Regular environmental monitoring is another critical requirement. This includes monitoring for airborne particles, microbial contamination, temperature, and humidity levels. Surfaces, personnel, and equipment must also be routinely tested for contamination. Cleaning protocols and validation of sterilization processes must be documented and followed strictly.
The FDA also mandates personnel training for cleanroom behavior, gowning procedures, and handling sterile materials. All cleanrooms must be validated and regularly recertified to ensure they comply with FDA guidelines. Non-compliance may result in product recalls, facility shutdowns, or other regulatory actions.
In the medical field, cleanroom requirements ensure that products such as injectable drugs, surgical instruments, and implantable devices are manufactured in conditions that meet stringent sterility and quality standards.
Basic cleanroom requirements focus on controlling the environment to limit contamination, which is critical in medical and pharmaceutical industries. These requirements ensure that cleanrooms maintain specific cleanliness levels according to their classification, such as ISO 5, ISO 7, or ISO 8.
Air Filtration: Cleanrooms must use HEPA (High-Efficiency Particulate Air) or ULPA (Ultra-Low Penetration Air) filters to remove airborne particles. The filtration system must ensure the required particle count levels are maintained for the cleanroom’s classification.
Airflow: Proper airflow patterns, such as unidirectional (laminar) flow, help to prevent the buildup of particles and maintain consistent air cleanliness.
Air Pressure Differentials: Cleanrooms often maintain positive air pressure to keep contaminants out or negative pressure for areas dealing with hazardous substances.
Environmental Monitoring: Continuous monitoring of particle counts, microbial contamination, temperature, and humidity is required to ensure a controlled environment.
Personnel Hygiene: Personnel entering the cleanroom must follow strict gowning protocols, including wearing gloves, face masks, shoe covers, and sterile gowns.
Cleaning and Maintenance: Surfaces, walls, equipment, and flooring must be cleaned and disinfected regularly to maintain sterility.
Restricted Access: Only trained and authorized personnel are allowed to enter cleanrooms to limit potential contamination.
By maintaining these requirements, cleanrooms provide a controlled environment essential for manufacturing sterile medical products, conducting clinical research, or compounding pharmaceuticals.
Cleanroom protocols are designed to maintain sterility and prevent contamination, especially in medical and pharmaceutical environments. Following the dos and don’ts is essential for maintaining cleanroom compliance and ensuring product safety.
Dos:
Follow Gowning Procedures: Wear cleanroom-approved gloves, gowns, masks, and shoe covers. Ensure that all garments are properly fitted and free from damage.
Wash Hands: Always sanitize your hands thoroughly before entering the cleanroom.
Move Deliberately: Slow, controlled movements help minimize particle generation.
Keep the Cleanroom Clean: Use approved cleaning agents to disinfect surfaces regularly.
Handle Materials Properly: Use sterile techniques when transferring materials in and out of the cleanroom.
Monitor Environmental Conditions: Ensure temperature, humidity, and air pressure are within acceptable ranges.
Log All Activities: Maintain accurate records of cleaning, testing, and maintenance activities.
Don’ts:
No Personal Items: Avoid bringing unauthorized items, such as phones, jewelry, or pens, into the cleanroom.
Avoid Excess Movement: Do not run or make sudden movements that may disturb airflow.
Don’t Touch Without Gloves: Do not touch sterile surfaces or equipment with bare hands.
No Eating or Drinking: Food, beverages, and chewing gum are strictly prohibited.
Do Not Lean: Avoid leaning on walls or equipment to prevent contamination.
Avoid Opening Doors Unnecessarily: Frequent entry and exit disturb airflow and may introduce contaminants.
By adhering to these dos and don’ts, personnel can help maintain the controlled environment required for medical and pharmaceutical production.
The ISO 14644 standard provides comprehensive guidelines for cleanroom design, classification, and operation. It establishes air cleanliness levels based on particle counts and specifies testing and monitoring procedures to ensure compliance.
Cleanrooms are classified from ISO 1 to ISO 9, with ISO 1 being the cleanest. For example, an ISO 5 cleanroom allows a maximum of 3,520 particles ≥0.5 µm per cubic meter, while an ISO 8 cleanroom permits up to 3,520,000 particles of the same size. These classifications are critical for industries like healthcare, where sterility and precision are paramount.
ISO guidelines also emphasize airflow control, requiring unidirectional (laminar) flow in high-class cleanrooms to prevent particle accumulation. Other key aspects include environmental monitoring (for temperature, humidity, and microbial contamination) and the use of HEPA or ULPA filters for air purification.
In the medical field, ISO guidelines are vital for manufacturing sterile products, such as injectables, surgical instruments, and implantable devices. Compliance ensures that the risk of contamination is minimized, enhancing patient safety and meeting regulatory requirements. Cleanrooms must also undergo certification and regular maintenance to remain compliant with ISO standards.
Yes, cleanrooms must be certified to meet specific cleanliness and operational standards, such as those outlined in ISO 14644 or GMP guidelines. Certification ensures that a cleanroom’s design, construction, and performance meet the necessary requirements for its intended application.
Certification involves a series of tests, including particle count testing, airflow velocity and direction measurements, air change rate calculations, and pressure differential checks. Environmental conditions, such as temperature, humidity, and microbial contamination levels, are also evaluated.
In the medical and pharmaceutical industries, certification is critical to ensure that cleanrooms are suitable for manufacturing sterile products. Regulatory bodies, such as the FDA, require cleanrooms to be certified and validated before they can be used in production. Certification must also be renewed periodically or whenever significant changes are made to the cleanroom, such as new equipment installation or layout modifications.
Failure to certify a cleanroom can result in regulatory non-compliance, product recalls, or compromised patient safety. Therefore, cleanroom certification is an essential step in maintaining quality assurance and meeting industry standards.
ISO 9 cleanrooms are the least stringent classification under the ISO 14644 standard and are essentially equivalent to typical uncontrolled environments, like regular indoor air. ISO 9 cleanrooms do not require advanced air filtration systems, such as HEPA filters, and they allow higher levels of particulate matter compared to other cleanroom classifications.
In an ISO 9 cleanroom, the allowable particle count is significantly higher than for stricter classifications. The particle limits for ≥0.5 µm particles are up to 35,200,000 particles per cubic meter, which is much higher compared to ISO 8 or stricter classes. Because of its minimal requirements, ISO 9 environments are rarely used for critical medical or pharmaceutical applications that require sterility or highly controlled conditions. Instead, they may serve as an anteroom or buffer zone for higher-class cleanrooms.
While not common in medical applications, if used in a healthcare setting, ISO 9 cleanrooms still need to follow basic cleanroom principles like restricted access, personnel gowning, and regular cleaning to ensure cleanliness above standard environments.
The microbial limit in a cleanroom depends on its classification and the application. Microbial contamination is measured in terms of colony-forming units (CFU), representing viable microorganisms.
For instance:
ISO 5 (Class 100): Maximum of 1 CFU per cubic meter in air samples.
ISO 7 (Class 10,000): Maximum of 10 CFU per cubic meter in air samples.
ISO 8 (Class 100,000): Maximum of 100 CFU per cubic meter in air samples.
Microbial limits are critical for maintaining sterility in environments used for manufacturing medical devices, pharmaceuticals, or sterile compounds. Surface contamination is also monitored, with stricter limits in higher-class cleanrooms. Proper cleaning protocols, sterilization of equipment, and environmental monitoring are vital for controlling microbial contamination.
In medical applications, exceeding microbial limits can lead to product recalls, regulatory non-compliance, and risks to patient safety. Therefore, cleanrooms must implement robust microbial monitoring and control strategies.
Class 3 cleanrooms (equivalent to ISO 3 under ISO 14644) are ultra-clean environments with extremely low allowable particulate levels. These cleanrooms are designed for highly sensitive applications, such as manufacturing implantable medical devices, microelectronics, or conducting advanced research.
Key requirements include:
Airborne Particle Control: Class 3 cleanrooms allow only 35 particles ≥0.5 µm per cubic meter. This requires advanced air filtration systems, typically using ULPA filters with nearly 100% efficiency.
Unidirectional Airflow: Air must flow in a laminar, single-direction pattern to minimize particle buildup.
Air Changes: High air change rates (600 or more per hour) to maintain constant cleanliness.
Environmental Monitoring: Continuous monitoring of particles, temperature, humidity, and microbial contamination is essential.
Strict Gowning: Personnel must wear full-body suits, gloves, masks, and goggles to prevent contamination.
Class 3 cleanrooms are used in critical medical applications where even microscopic contamination can compromise product integrity and safety.
ISO 8 cleanrooms are common in the medical and pharmaceutical industries for less critical processes such as the assembly or packaging of non-sterile medical devices. These cleanrooms have less stringent requirements compared to ISO 5 or ISO 7 classifications but still provide a controlled environment.
Key requirements include:
Airborne Particle Limits: ISO 8 allows 3,520,000 particles ≥0.5 µm per cubic meter.
Air Changes per Hour (ACH): A minimum of 20 air changes per hour is required.
HEPA Filtration: Air must pass through HEPA filters to reduce airborne particles.
Environmental Monitoring: Particle levels, temperature, humidity, and microbial contamination must be monitored regularly.
Restricted Access and Gowning: Personnel must wear appropriate protective clothing such as shoe covers, gloves, and lab coats.
ISO 8 cleanrooms are used in the manufacturing of certain medical products where sterility is not critical but contamination control is still necessary.
Cleanroom protocol refers to the set of procedures and rules that must be followed to maintain the cleanliness and integrity of a cleanroom environment. Protocols are essential in medical and pharmaceutical cleanrooms to prevent contamination and ensure product safety.
Key cleanroom protocols include:
Gowning Procedures: Personnel must wear cleanroom-specific garments, including gloves, masks, goggles, and shoe covers, to prevent contamination from hair, skin, or clothing fibers.
Hygiene Practices: Thorough hand washing and sanitization before entering the cleanroom are mandatory.
Movement Restrictions: Personnel must move slowly and deliberately to minimize particle generation.
Material Handling: All materials entering the cleanroom must be sterilized or cleaned.
Environmental Monitoring: Continuous monitoring ensures particle levels, air pressure, and microbial contamination remain within acceptable limits.
Restricted Access: Only authorized and trained personnel can enter the cleanroom.
Adhering to these protocols ensures cleanrooms meet their intended purpose of providing a controlled environment for sensitive medical and pharmaceutical applications.
U.S. cleanroom standards are governed by ISO 14644, FDA regulations, and GMP requirements. These standards provide guidelines for cleanroom classification, design, operation, and maintenance. Cleanroom classifications range from ISO 1 to ISO 9, depending on allowable particle counts.
The FDA also requires cleanrooms used in pharmaceutical and medical manufacturing to comply with GMP. This includes strict environmental controls, such as HEPA filtration, air pressure differentials, and robust cleaning protocols.
In addition, cleanrooms must be validated and certified regularly to ensure compliance with these standards. Non-compliance can result in regulatory action, product recalls, or compromised patient safety.
A Class 100 cleanroom, also referred to as an ISO 5 cleanroom under ISO 14644 standards, requires a high rate of air changes per hour (ACH) to maintain cleanliness. Typically, 240 to 600 air changes per hour are necessary depending on the cleanroom’s size and the process taking place. This means that the entire volume of air within the cleanroom is replaced 240 to 600 times in an hour.
The purpose of these frequent air changes is to continuously remove airborne contaminants and maintain the strict particle limits for ISO 5 environments. In medical applications, such as the production of sterile pharmaceuticals or implantable medical devices, maintaining Class 100 conditions is critical to prevent contamination.
The high ACH is achieved through the use of unidirectional airflow systems (laminar flow) combined with HEPA (High-Efficiency Particulate Air) filtration to remove particles as small as 0.3 microns. These systems are supported by rigorous environmental monitoring, including particle counters and pressure differentials, to ensure compliance. Failure to maintain the required air changes could lead to contamination, compromising the sterility of medical products and patient safety.
The primary difference between a cleanroom and a non-cleanroom lies in the level of control over environmental factors such as airborne particles, microbial contamination, temperature, humidity, and pressure. Cleanrooms are highly controlled environments that adhere to strict standards, such as ISO 14644 or GMP (Good Manufacturing Practices), while non-cleanrooms are standard spaces with no specialized control mechanisms.
In a cleanroom:
Air Quality: Cleanrooms use HEPA or ULPA filters to achieve specific particle limits (e.g., ISO 5 allows only 3,520 particles ≥0.5 µm per cubic meter).
Pressure Differentials: Cleanrooms maintain positive or negative pressure to control contamination risks.
Environmental Monitoring: Conditions are constantly monitored to ensure compliance with regulatory standards.
Restricted Access: Personnel must follow strict gowning and hygiene protocols.
Non-cleanrooms lack these controls and are not suitable for processes requiring sterility. For example, cleanrooms are essential for manufacturing sterile medical devices, injectable drugs, and implants, while non-cleanrooms are used for general activities that do not require stringent contamination control.
The controlled environment of a cleanroom ensures patient safety by minimizing contamination risks in the production of sensitive medical and pharmaceutical products.
A buffer room and a cleanroom serve distinct but complementary purposes within a controlled environment facility, particularly in medical and pharmaceutical applications.
Buffer Room: A buffer room is a transitional space situated between a cleanroom and an uncontrolled area (e.g., a warehouse or corridor). Its purpose is to minimize the risk of contamination by creating an intermediate zone where personnel and materials can be prepared before entering the cleanroom. Buffer rooms maintain a moderate level of cleanliness (e.g., ISO 8) and are often used for gowning, material transfer, or airlock systems.
Cleanroom: A cleanroom, by contrast, is a highly controlled environment with stricter cleanliness standards (e.g., ISO 5, ISO 6, or ISO 7). It is designed for critical processes like sterile drug compounding, surgical instrument manufacturing, or cell culture work, where contamination control is vital.
The buffer room acts as a protective barrier, reducing the likelihood of contaminants entering the cleanroom. While both spaces are part of a contamination control strategy, cleanrooms have much stricter requirements for particle count, airflow, and environmental monitoring.
Cleanrooms are designed to control contamination and create an environment with precisely regulated airborne particle levels, temperature, humidity, and pressure. In the medical and pharmaceutical fields, cleanrooms are used to ensure the sterility and quality of products, such as injectable drugs, implantable medical devices, and diagnostic equipment.
Key purposes of cleanrooms include:
Sterile Manufacturing: Ensuring that drugs, biologics, and medical devices meet regulatory sterility standards.
Patient Safety: Preventing contamination that could lead to infections or product failures.
Regulatory Compliance: Meeting ISO, FDA, and GMP standards for manufacturing processes.
Research Integrity: Providing a controlled environment for sensitive experiments in biotechnology and healthcare research.
By eliminating or controlling contamination sources such as particles, microorganisms, and chemical residues, cleanrooms enable high-quality production and research in critical healthcare applications.
The leakage rate in a cleanroom refers to the amount of air that escapes through walls, ceilings, or other structural elements. It is an important factor in maintaining pressure differentials and ensuring that the cleanroom remains contaminant-free. A low leakage rate is critical for cleanrooms that operate with positive or negative pressure.
For cleanrooms, acceptable leakage rates are determined during validation and certification. For example:
Positive Pressure Cleanrooms: Designed to keep contaminants out by maintaining higher pressure inside than outside. Leakage rates must be minimal to ensure the pressure differential is maintained.
Negative Pressure Cleanrooms: Used for hazardous material handling, where the pressure inside is lower than the surrounding areas to contain contaminants.
The leakage rate is tested using smoke tests or pressure decay methods. Proper sealing, high-quality construction materials, and regular maintenance help minimize leakage.
A cleanroom is a highly controlled environment designed to meet specific cleanliness standards, such as those defined by ISO 14644, while a controlled room has broader control over environmental factors but does not adhere to strict particle count or microbial contamination limits.
Cleanroom: Controls airborne particles and microorganisms to a specific standard (e.g., ISO 5 or ISO 7). Used in medical and pharmaceutical applications requiring sterility.
Controlled Room: Focuses on maintaining environmental conditions like temperature and humidity but may not have advanced filtration or particle monitoring.
For example, a cleanroom is used for aseptic drug manufacturing, while a controlled room may be used for packaging or storage where sterility is less critical.
A cleanroom is a controlled environment designed to minimize contamination by airborne particles, microorganisms, and chemical vapors. It is used in industries like healthcare, pharmaceuticals, biotechnology, and medical device manufacturing. Cleanrooms are equipped with systems to filter air, control temperature, humidity, and pressure, ensuring a sterile environment suitable for sensitive medical operations or research.
Key qualifications for a cleanroom include:
Air Filtration Systems: High-efficiency particulate air (HEPA) or ultra-low particulate air (ULPA) filters remove contaminants from incoming air.
Controlled Airflow: Laminar or unidirectional airflow is critical to reducing turbulence and preventing cross-contamination.
Environmental Controls: Parameters such as humidity, temperature, and pressure are tightly regulated to maintain sterility and prevent microorganism growth.
Personnel Protocols: Individuals working in cleanrooms must wear proper gowns, gloves, masks, and footwear to reduce contamination.
Particle Monitoring: Regular monitoring ensures compliance with established cleanliness levels.
Cleanrooms are classified according to ISO standards, based on the number of allowable particles per cubic meter. These classifications ensure that the environment meets the specific needs of medical production, such as sterile drug compounding or surgical equipment manufacturing.
An ISO 6 cleanroom is classified under ISO 14644-1 standards, allowing no more than 35,200 particles per cubic meter of air for particles ≥0.5 microns. This level of cleanliness is typically required in pharmaceutical compounding, sterile medical device production, and healthcare-related research.
Requirements for an ISO 6 cleanroom include:
Filtration System: Must use HEPA or ULPA filters to remove 99.99% of airborne particles ≥0.3 microns.
Air Changes: The cleanroom should have 180–240 air changes per hour to ensure consistent removal of contaminants.
Personnel and Gowning: Workers must follow strict gowning procedures, wearing sterile gloves, face masks, coveralls, and boots.
Pressure Control: Positive pressure (higher than surrounding areas) is maintained to prevent contaminated air from entering the room.
Surface Cleanliness: Surfaces must be smooth, easy to clean, and resistant to particle accumulation. Cleaning should occur frequently using sterilizing agents.
Monitoring Systems: Regular particle count monitoring and microbial testing ensure compliance with ISO 6 standards.
In medical settings, ISO 6 cleanrooms are commonly used in aseptic filling of injectable drugs or assembly of sterile instruments.
ISO 7 cleanrooms, also referred to as Class 10,000 cleanrooms, allow up to 352,000 particles per cubic meter of air for particles ≥0.5 microns. This classification is suitable for pharmaceutical processes like drug preparation, compounding, and packaging of non-sterile medical devices.
Key standards for ISO 7 cleanrooms include:
Air Filtration: HEPA filters capable of capturing 99.97% of particles ≥0.3 microns are mandatory.
Air Changes Per Hour: The room should achieve 60–90 air changes per hour to maintain cleanliness.
Gowning Procedures: Workers must wear gloves, masks, shoe covers, and hairnets to minimize contamination risks.
Environmental Controls: Temperature and humidity must be regulated to ensure product integrity and prevent microbial growth.
Surface and Equipment Cleanliness: Materials must be easy to clean and resistant to corrosion or particle generation. Cleaning schedules should be strictly followed.
Particle Monitoring: Regular testing ensures that particle counts remain within ISO 7 limits, especially for critical operations like compounding sterile preparations.
ISO 7 cleanrooms are widely used in medical environments for tasks such as the production of prosthetics, wound care products, or diagnostic tools.
A non-classified cleanroom, also called a non-classified controlled environment, does not meet the stringent particle count requirements of ISO 14644-1 standards. While it might still have some level of environmental control, it is unsuitable for critical medical or pharmaceutical operations requiring sterility.
Key characteristics of non-classified cleanrooms include:
Limited Filtration: The environment may use basic air conditioning or filtration systems but lacks HEPA or ULPA filters.
Minimal Contamination Control: There are no specific protocols for controlling airborne particles, microbial contamination, or personnel movements.
Applications: Non-classified rooms may be used for non-critical tasks like packaging, assembly of non-sterile devices, or storage of materials where sterility is not required.
No Certification: These environments are not tested or certified according to ISO standards.
Non-classified cleanrooms are inappropriate for processes involving sterile medical devices, pharmaceutical drugs, or surgical tools. Instead, they serve secondary purposes where ISO-classified cleanrooms are unnecessary.
An ISO 5 cleanroom, also referred to as Class 100 under older standards, allows no more than 3,520 particles per cubic meter of air for particles ≥0.5 microns. This level of cleanliness is critical in medical environments requiring ultra-high sterility, such as operating theaters, pharmaceutical aseptic filling, or production of injectable drugs.
Requirements for an ISO 5 cleanroom include:
Advanced Air Filtration: ULPA filters are typically required to remove 99.999% of particles ≥0.1 microns.
Air Changes: These rooms require 240–480 air changes per hour to maintain particle-free conditions.
Strict Protocols: Personnel must undergo rigorous gowning procedures, including sterile gloves, masks, hooded coveralls, and boots.
Positive Pressure: The cleanroom is maintained at a higher pressure to prevent unfiltered air from entering.
Surface Cleanliness: All materials and surfaces must be non-porous and easy to sterilize. Routine cleaning with disinfectants is required to prevent microbial contamination.
Real-Time Monitoring: Continuous monitoring of particle counts and microbial contamination is mandatory to ensure compliance.
ISO 5 cleanrooms are essential in critical healthcare applications, including the preparation of intravenous medications, cell therapy products, and sterile surgical implants.
Contact our professional team now for a same-day quote and risk-free project evaluation. Benefit from ISO 8 cleanrooms, advanced machines, and 12-hour fast response in medical injection molding.