In the rapidly evolving healthcare industry, the demand for customized precision medical apparatus components has become increasingly crucial. These components play a pivotal role in ensuring that medical devices function with high accuracy and reliability, directly impacting patient care. The precision and customization of these parts are essential for creating medical equipment that meets specific patient needs, as well as for adapting to the latest technological advancements. Customized Precision Medical Apparatus Components create medical devices and implants to meet exact medical parts manufacturing. Medical device assemblers play a critical role in this process, ensuring that these customized components are accurately integrated into the final product. By allowing for tailored solutions, customized precision medical apparatus components enhance the effectiveness of treatment, optimize patient safety, and improve overall healthcare outcomes. As medical technology continues to advance, the importance of precision and customization in device manufacturing remains central to achieving better results in patient care and medical procedures.
Low-Volume to High-Volume Production Capabilities
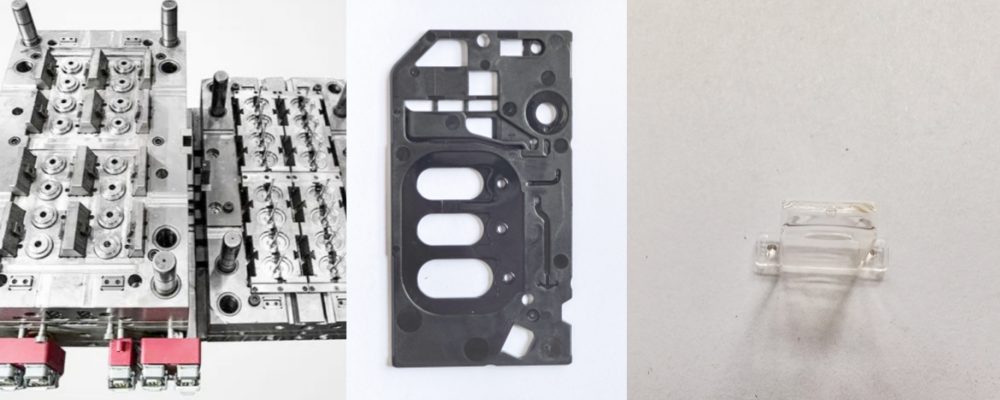
Attribute | Description |
---|---|
Product Name | Customized Precision Medical Apparatus Components |
Place of Origin | Dongguan, Guangdong, China |
Brand Name | LY Medical Injection Mold |
Material Options | Aluminum, Brass, Bronze, Copper, Hardened Metals, Precious Metals, Stainless Steel, Steel Alloys, Polymer |
Processing Services | CNC Machining, Injection Molding, Milling, Turning, Drilling, Broaching, Etching, Laser Machining, Wire EDM, Rapid Prototyping |
Applications | Medical devices, spare parts for medical apparatus |
Precision and Tolerance | ±0.001mm to ±0.1mm |
Customization Options | - Surface Finish: Polishing, anodizing, coating, PVD, plating, powder coating |
- Colors: Red, Green, Blue, Silver, Black, Gold, Custom | |
- Sizes: As per customer’s drawing | |
Drawing Formats Accepted | 2D (PDF, CAD, DWG, DXF), 3D (IGES, STEP, STL, VDA) |
QC Control | 100% dimension inspection |
CNC Capabilities | 3/4/5-axis CNC turning and milling, micro machining |
Certifications | ISO9001, ISO9000:2015, IATF16949:2016 |
Sample Availability | Free samples for new customers; lead time: 5 days |
MOQ | 1 pcs |
Packaging | - Inner: OPP bags |
- Outer: Durable cartons or custom packaging per client requirements | |
Key Selling Points | - High precision and quality assurance |
- Versatile material options | |
- Advanced machining techniques | |
After-Sale Service | Online support; global reach and customer assistance |
What Are Customized Precision Medical Apparatus Components?
Customized precision medical apparatus components are specialized parts designed and manufactured to meet the exact specifications needed for medical devices. These components are crucial for ensuring that medical apparatus operate effectively and safely. Medical molding is often used in the production of these parts, as it enables high precision and ensures that the components meet the strict standards required in the healthcare industry. Below are key aspects of these components:
Definition and Examples
- Implants: These are precision-engineered components designed to be surgically inserted into the body, such as joint replacements or dental implants. Each implant is created to fit the specific anatomy of the patient, ensuring optimal function and comfort.
- Surgical Tools: Customized surgical instruments are crafted to enhance the precision and efficiency of medical procedures. Examples include scalpels, forceps, and scissors that are tailored to meet the needs of a particular surgery or procedure.
- Diagnostic Equipment Parts: These components are designed for diagnostic devices like MRI machines, ultrasound systems, and blood analyzers. Customization ensures these parts align with the performance standards required for accurate diagnosis and patient safety.
Importance of Tailored Designs
- The customization of customized precision medical apparatus components allows manufacturers to meet the unique needs of both medical professionals and patients. A medical plastic components manufacturer plays a critical role in this process, ensuring that custom designs are produced to meet the specific requirements of each medical application. Custom designs ensure that medical devices are compatible with specific procedures, improving both usability and effectiveness.Custom designs ensure that medical devices are compatible with specific procedures, improving both usability and effectiveness.
- Tailored designs are essential in addressing variations in patient anatomy and medical conditions, ensuring that devices work as intended and contribute to better clinical outcomes.
- Additionally, customized components enhance the reliability and safety of medical equipment, reducing the likelihood of malfunction or complications during use.
The role of customized precision medical apparatus components in healthcare is vital, as it ensures the creation of devices that are both patient-specific and technologically advanced.
Customized Precision Medical Apparatus Components Manufacturing Specifications
The manufacturing of customized precision components for medical apparatus requires a high degree of accuracy, strict adherence to standards, and the ability to meet unique client specifications. Below is a detailed description of the key aspects involved in this process:
1. Material Selection
- Biocompatibility: All materials must be biocompatible to ensure they are safe for human contact and do not cause adverse reactions.
- Corrosion Resistance: Materials like stainless steel, titanium alloys, and high-performance plastics (e.g., PEEK) are commonly used to withstand sterilization processes and prolonged use.
- Mechanical Properties: Strength, flexibility, and durability are critical to ensure functionality and reliability.
2. Design and Engineering
- Custom Designs: Each component is tailored to meet specific requirements, including size, shape, and performance metrics.
- CAD Modeling: Advanced Computer-Aided Design (CAD) software is used to create detailed 3D models for precise visualization and adjustments.
- Finite Element Analysis (FEA): Ensures structural integrity and performance under operational conditions.
3. Manufacturing Processes
- Precision Machining: Techniques like CNC milling, turning, and grinding ensure micron-level accuracy.
- Additive Manufacturing (3D Printing): For complex geometries, rapid prototyping, or lightweight structures.
- Injection Molding: Used for high-volume production of plastic components.
- Surface Treatments: Anodizing, passivation, or polishing for enhanced durability and aesthetic quality.
4. Quality Assurance and Compliance
- ISO Certification: Compliance with ISO 13485 for medical device manufacturing.
- Inspection Standards: Coordinate Measuring Machines (CMM), optical comparators, and laser scanners for dimensional verification.
- Regulatory Compliance: Adherence to FDA, CE, and other regional regulations for medical devices.
5. Packaging and Delivery
- Sterile Packaging: Components are packaged in a sterile environment to prevent contamination.
- Custom Labeling: Includes detailed product information, lot numbers, and barcodes for traceability.
- Global Logistics: Secure and timely shipping to meet client deadlines.
6. Client Collaboration
- Prototyping and Testing: Iterative development cycles with client feedback to refine the design and functionality.
- Technical Support: Ongoing consultation to ensure the components meet operational needs and regulatory requirements.
This comprehensive approach ensures the delivery of high-quality, reliable, and innovative components tailored to the needs of the medical industry.
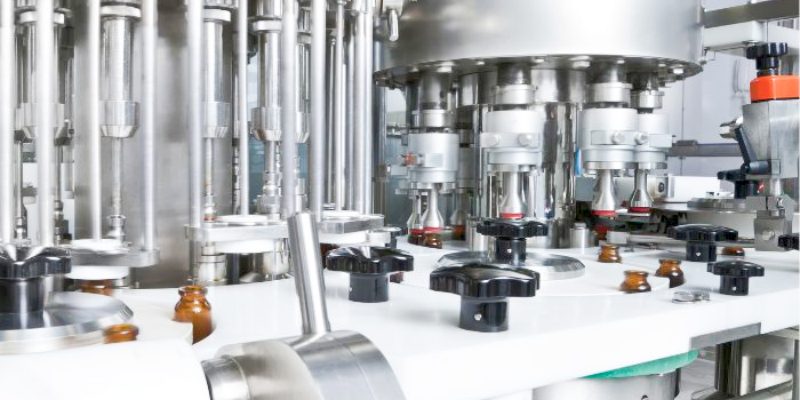
Cost of Customized Precision Medical Apparatus Components
Manufacturing customized precision medical apparatus components is a highly specialized process that involves numerous factors influencing the overall cost. Here is a detailed breakdown:
Material Selection
- Biocompatible Materials: Medical components require materials that are safe for human interaction, such as titanium, stainless steel (316L), cobalt-chromium alloys, and medical-grade polymers like PEEK or PTFE.
- Cost of Metals: Titanium and cobalt-chromium alloys are expensive due to their biocompatibility and resistance to corrosion.
- Cost of Polymers: High-performance plastics are more affordable but require precise manufacturing techniques.
- Ceramics: Used for implants or high-wear parts, ceramics are costly due to their hardness and processing requirements.
- Impact on Cost: Material prices range widely, from $50/kg for stainless steel to over $300/kg for advanced polymers like PEEK.
Design Complexity
- Customization Needs: Highly intricate designs demand advanced machining capabilities, such as multi-axis CNC or micromachining.
- Prototypes can cost between $5,000 and $50,000, depending on the complexity and number of revisions.
- A simplified design can reduce machining time and tooling requirements, lowering costs.
- Impact on Cost: Complex geometries with tight tolerances (+/- 0.001 mm) increase costs due to longer production times and specialized machinery.
Manufacturing Techniques
- CNC Machining: For precision and high repeatability.
- Costs range from $50 to $200 per hour, depending on the complexity and material.
- Additive Manufacturing (3D Printing): Suitable for low-volume production and complex designs.
- Prototyping starts at $1,000 per part, with costs decreasing for batch production.
- Injection Molding: Ideal for high-volume production of plastic components.
- Tooling cost: $10,000–$50,000.
- Per-unit cost: As low as $1 for large quantities.
- Surface Finishing: Processes like anodizing, passivation, or polishing add $20–$50 per part, depending on requirements.
Quality Assurance and Testing
- Inspection Processes: Dimensional verification using CMMs, laser scanners, or optical microscopy.
- Testing costs start at $500 per batch but can exceed $5,000 for extensive validation.
- Regulatory Compliance: Documentation and testing to meet FDA, CE, and ISO 13485 standards.
- Compliance and certification costs can range from $10,000 to $100,000, depending on the complexity of the device.
Production Volume
- Low-Volume Manufacturing: For specialized components or prototypes, costs are higher due to tooling and setup expenses spread over fewer units.
- Typical per-unit costs: $100–$5,000.
- High-Volume Manufacturing: Allows for economies of scale, significantly reducing per-unit costs.
- Typical per-unit costs: $1–$100.
Labor and Expertise
- Engineering and Design Costs: Initial design and prototyping require skilled engineers, costing $50–$150/hour.
- Machining Operators: Skilled machinists command wages of $40–$80/hour.
- Post-Production Support: Includes packaging, sterilization, and customer service, adding 10–20% to the overall cost.
Supply Chain and Sourcing
- Sourcing Specialized Materials: Importing rare or high-grade materials increases costs due to tariffs and shipping fees.
- Lead times and material scarcity can further impact costs.
- Logistics: Packaging for sterility and secure shipping adds $5–$50 per unit.
Regulatory and Legal Compliance
- Documentation: Creating technical files, risk management reports, and clinical evaluations for regulatory approval.
- Costs range from $20,000 to $100,000 depending on the region and device complexity.
- Testing: Biocompatibility, mechanical performance, and sterilization validation cost $5,000–$20,000 per test cycle.
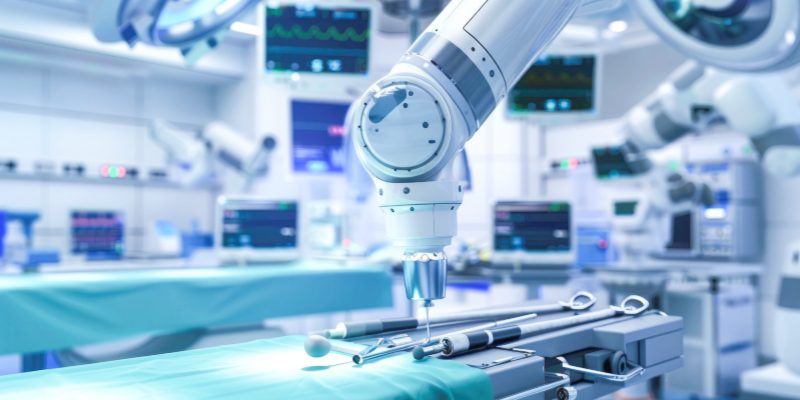
Advantages of Customized Precision Components in Medical Devices
The use of customized precision medical apparatus components brings several significant advantages to the healthcare industry, particularly in the development of medical devices that require exact specifications. Here are six key benefits of using customized components:
- Enhanced Performance
Customized precision parts play a vital role in improving the functionality of medical devices. By tailoring each component to meet the exact requirements of the device, they ensure optimal performance, whether it’s for surgical tools, implants, or diagnostic equipment. These components are designed to integrate seamlessly, resulting in more efficient and effective medical applications. - Durability and Reliability
High-quality materials and precise engineering make customized precision medical apparatus components more durable and reliable. In medical devices, where failure can have serious consequences, the longevity and consistent operation of these components are crucial. Customized parts are built to withstand the rigors of medical environments, from high-stress surgeries to constant use in diagnostic tools. - Improved Patient Outcomes
Customization ensures that injection molding medical devices fit the unique needs of individual patients. Whether it’s a customized implant or a tool designed for a specific procedure, precision components help improve the effectiveness of treatments. This tailored approach leads to better recovery times, fewer complications, and overall enhanced patient outcomes. - Increased Safety
The precision and quality of customized components reduce the risk of device failure. By focusing on exact specifications, manufacturers can ensure that medical devices are safer and more reliable, directly protecting patients during use. - Cost Efficiency Over Time
Although customized components may have higher upfront costs, their long-term reliability and performance can lead to significant cost savings. Reduced need for replacements, fewer complications, and the enhanced lifespan of medical devices help healthcare providers save money over time. - Better Regulatory Compliance
Medical devices need to meet stringent regulatory standards. Customized precision medical components are manufactured to comply with medical industry regulations, ensuring that devices are safe, effective, and meet the required certifications. This adherence to regulatory standards reduces the risk of costly recalls and ensures patient safety.
Precision Medical Molds and Plastic Parts Customized
One of the key areas where customized precision medical apparatus components truly shines is in the creation of precision medical molds and plastic parts customized for medical devices. These molds and plastic components are designed with high precision to meet the demanding requirements of the medical field. Whether it’s for creating complex shapes, ensuring tight tolerances, or ensuring compatibility with other device components, precision medical molds and plastic parts customized are crucial for maintaining the integrity, functionality, and safety of medical devices.
- Custom Molds for Specific Applications
Medical molds are precisely designed to meet the unique needs of medical devices, from implantable devices to diagnostic equipment. Customization ensures that the mold fits the exact specifications required for functionality and safety. These molds are created to adhere to strict medical molding requirements, which include high precision, biocompatibility, and durability to ensure that the final product meets industry standards and performs as intended in medical applications. - Plastic Parts Tailored to Medical Needs
Medical-grade plastics must meet rigorous standards, such as biocompatibility, durability, and sterility. Customized plastic parts ensure that these materials are tailored to the specific requirements of medical devices, whether it’s for surgical instruments, diagnostic equipment, or disposable tools. The customization process guarantees both quality and performance.
Customized precision medical apparatus components offer a wide range of advantages that are essential for the advancement of medical technology, improving patient care, and ensuring the effectiveness of medical treatments and devices.
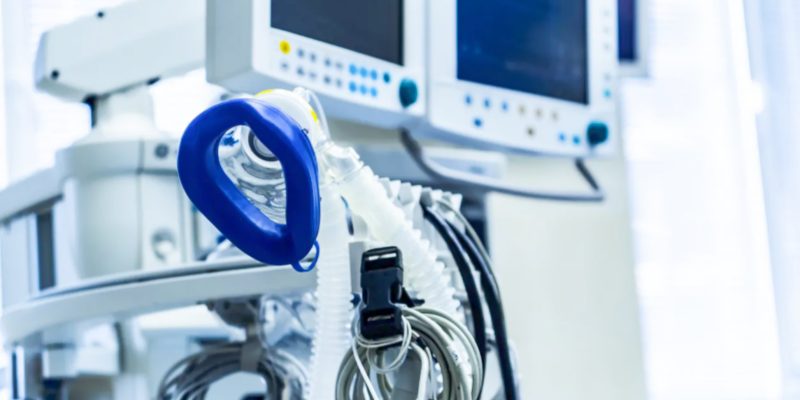
Applications of Customized Precision Medical Apparatus Components
Customized precision medical apparatus components are essential across various medical fields, providing advanced solutions for improving patient care, enhancing surgical precision, and ensuring the accuracy of diagnostic equipment. Below are some key applications of these components:
- Surgical Instruments
Precision surgical tools, such as biopsy cutters and reamers, are designed with high accuracy to ensure minimal patient risk and maximize procedural effectiveness. These customized precision medical apparatus components are tailored to fit specific surgical needs, enhancing the efficiency and safety of operations. - Diagnostic Equipment
In the realm of diagnostic medicine, customized precision medical apparatus components are used to manufacture critical parts for machines like MRI scanners, CT machines, and blood analyzers. Custom components ensure that these complex devices operate with the precision necessary for accurate diagnostics, leading to better patient outcomes and more effective treatments. - Implants and Prosthetics
Customized precision components are crucial in the creation of implants and prosthetics, including spinal implants, cranial screws, and dental prosthetics. Each of these components must be carefully crafted to match the specific anatomical needs of the patient, ensuring proper fit and function. These customized precision machining for medical components play a significant role in restoring mobility and improving the quality of life for patients. - Laboratory Devices
Laboratory equipment, such as DNA analysis machines and fluid flow systems, also relies on customized precision medical apparatus components. The high level of precision required in these devices ensures accurate test results, which are critical in fields like genetics, pathology, and biochemistry. Tailored components help achieve the necessary sensitivity and reliability for scientific and medical research.
Through these applications, customized precision medical apparatus components contribute significantly to advancements in medical technology and healthcare services, ensuring that devices function optimally and meet the unique needs of patients.
Finding Customized Precision Medical Apparatus Components Near Me
When searching for customized precision medical apparatus components, selecting local suppliers can offer several advantages, ensuring you get high-quality parts when you need them most. Here’s how to find the right suppliers:
- Why Choose Local Suppliers?
- Faster Delivery: Proximity to local suppliers means quicker shipping and reduced lead times. This is especially important in the medical field, where time is often of the essence.
- Convenient Consultations: Working with a local supplier allows for direct communication and in-person consultations. This can facilitate faster problem-solving and ensure the customized precision medical apparatus components meet your specific needs.
- Quality Checks: Local suppliers often provide hands-on quality control, ensuring that the components are tested and meet strict standards before delivery.
- Tips for Finding the Right Supplier
- Research and Reviews: Look for suppliers with strong reputations in precision medical manufacturing. Online reviews, case studies, and recommendations from industry professionals can guide you to trusted local vendors.
- Industry Certifications: Ensure the supplier has the necessary certifications, such as ISO 13485, which ensures the components meet international quality standards for medical devices.
- Visit the Facility: If possible, visit the supplier’s facility to inspect their manufacturing processes. This gives you confidence that the customized precision medical apparatus components are being made with the highest standards of precision and care.
Materials Used in Customized Precision Medical Components
When manufacturing customized precision medical apparatus components, the selection of materials is critical to ensure both performance and patient safety. These materials are carefully chosen based on the specific requirements of the medical device, whether for implants, surgical tools, or diagnostic equipment.
Certifications and Quality Standards
The manufacturing of customized precision medical apparatus components must adhere to strict industry standards to ensure safety, quality, and compliance with regulatory requirements. Key certifications and quality standards include:
- ISO 13485: This is an international standard for quality management systems in the medical device industry. It ensures that manufacturers meet regulatory requirements for medical devices and consistently produce products that are safe and effective.
- RoHS Compliance: The Restriction of Hazardous Substances (RoHS) directive limits the use of certain hazardous materials in electrical and electronic equipment. Manufacturers of medical components must ensure their products are RoHS compliant to meet environmental safety standards.
- FDA Regulations: In the U.S., medical components must comply with the Food and Drug Administration (FDA) regulations. This includes meeting requirements for design, production, and testing of medical devices, ensuring that the customized precision medical apparatus components are safe for use in patient care.
These certifications help guarantee that the components are manufactured to the highest standards of quality and reliability, making them suitable for critical medical applications.
Customized Precision Medical Apparatus Components Machining
Customized machining of precision components for medical apparatus involves highly specialized processes to produce parts that meet stringent requirements for accuracy, durability, and biocompatibility. Below is an overview of the critical elements in this field:
Materials Used in Medical Machining
- Metals: Titanium, stainless steel (316L, 304), cobalt-chromium alloys, and aluminum are common due to their strength, corrosion resistance, and biocompatibility.
- Polymers: High-performance plastics such as PEEK, UHMWPE, and PTFE for lightweight and flexible designs.
- Ceramics: Used for components requiring exceptional hardness and wear resistance (e.g., dental or orthopedic implants).
Key Machining Techniques
CNC Machining
- Turning and Milling: For producing intricate geometries with tight tolerances.
- Multi-axis CNC: Enables complex designs with fewer setups, increasing efficiency.
- Micromachining: Precision machining at micro and nano scales for delicate and small components.
Electrical Discharge Machining (EDM)
- Ideal for hard-to-machine materials or intricate designs requiring extreme accuracy.
Additive Manufacturing (3D Printing)
- For rapid prototyping and creating lightweight, complex geometries that traditional machining can’t achieve.
Laser Cutting and Drilling
- Ensures clean edges and high precision for delicate parts.
Precision and Tolerance
- High Tolerance Standards: Medical machining typically requires tolerances as tight as ±0.001 mm.
- Surface Finish: Achieved through polishing, grinding, or electrochemical machining to ensure smooth surfaces critical for functionality and hygiene.
Customization Capabilities
- Client-Specific Designs: Tailored to meet unique specifications for various applications, including surgical tools, prosthetics, and diagnostic equipment.
- Prototype to Production: Scalable processes to transition seamlessly from prototype to full-scale production.
Quality Assurance
- Inspection Techniques: Advanced metrology tools like CMM, laser scanners, and optical microscopes verify precision.
- Regulatory Compliance: Adherence to ISO 13485, FDA, and CE standards ensures safety and reliability.
Advantages of Custom Medical Machining
- Unmatched Precision: Critical for patient safety and device functionality.
- Flexible Solutions: Ability to adapt designs for specific medical needs.
- Enhanced Efficiency: Multi-axis machining and automation reduce production time and costs.
The machining of customized precision medical apparatus components represents a vital intersection of technology, material science, and engineering. It ensures the creation of components that not only meet the rigorous demands of the medical field but also enhance patient care and treatment outcomes.
FAQs about Customized Precision Medical Apparatus Components
Precision medicine involves tailoring medical treatments to individual characteristics of patients. Its key components include:
Genomics and Biomarkers: Identifying genetic variations and biomarkers for targeted therapies.
Data Analytics: Using AI and big data to analyze patient information.
Personalized Diagnostics: Advanced imaging and lab tests for precise diagnoses.
Patient Stratification: Grouping patients based on risk factors or predicted responses.
Targeted Therapies: Developing drugs and interventions specific to a patient’s profile.
Collaborative Research: Integrating findings from genomics, proteomics, and clinical data.
Diagnostic Equipment: Includes MRI machines, X-ray systems, and CT scanners.
Therapeutic Equipment: Devices like infusion pumps, ventilators, and dialysis machines.
Monitoring Equipment: ECG monitors, blood pressure monitors, and pulse oximeters.
Surgical Equipment: Tools like scalpels, endoscopes, and robotic surgical systems.
Durable Medical Equipment (DME): Wheelchairs, crutches, and hospital beds.
OEM stands for Original Equipment Manufacturer. In the medical field, it refers to companies that produce devices, components, or parts, which are then rebranded and sold by another company. For instance, a company might design and manufacture a specific medical sensor, but it is integrated into another company’s device and marketed under that brand. OEMs are critical for maintaining quality and innovation in medical device production.
Identify a Need: Research unmet clinical needs or inefficiencies in current practices.
Concept Development: Brainstorm and design a prototype addressing the identified need.
Regulatory Understanding: Learn about FDA/CE mark approval processes for compliance.
Testing and Validation: Conduct preclinical and clinical trials for safety and efficacy.
Manufacturing: Partner with an OEM or set up facilities for production.
Market Launch: Develop marketing strategies and distribute to healthcare providers.
Continuous Improvement: Gather feedback and refine the product.
Contact our professional team now for a same-day quote and risk-free project evaluation. Benefit from ISO 8 cleanrooms, advanced machines, and 12-hour fast response in medical injection molding.