FUJIU Medical Injection Mold is a leading supplier of high precision tools for medical device manufacturing, recognized for its commitment to quality and innovation. With decades of expertise, the company specializes in medical molded plastics solutions and medical molding that meet the rigorous demands of the medical sector. These tools are essential for precision mold medical applications, ensuring reliability and efficiency in manufacturing processes, making them indispensable for producing cutting-edge medical devices. Our product portfolio includes tweezers, cutters, and other high-precision instruments designed to support intricate operations required in the healthcare industry. By adhering to stringent quality standards, we have established itself as a trusted partner for manufacturers seeking superior tools to enhance their production capabilities and deliver optimal results in medical technology. High precision tools for medical device manufacturing essential for medical molded plastics solutions, efficiency manufacturing processes.
Low-Volume to High-Volume Production Capabilities
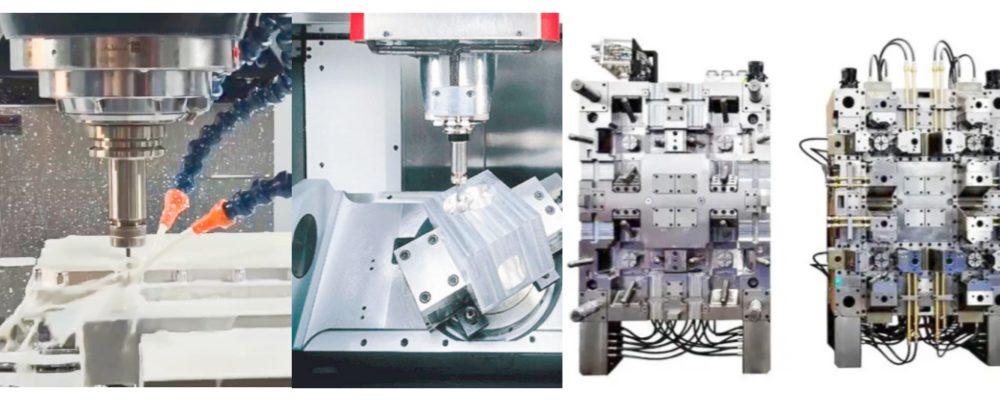
Attribute | Description |
---|---|
Type | High Precision CNC Machining Parts, Medical Machinery Components |
Brand Name | LY Medical Injection Mold |
Place of Origin | Dongguan, Guangdong, China |
Materials Supported | Aluminum, Brass, Bronze, Copper, Hardened Metals, Precious Metals, Stainless Steel, Carbon Steel, Steel Alloys, ABS, POM |
CNC Machining Capabilities | CNC Milling, Turning, Drilling, Broaching, Laser Machining, Wire EDM, Rapid Prototyping |
Micro Machining | Available |
Machining Precision | 0.01mm - 0.02mm |
Surface Treatments | Polishing, Plating, Heat Treatment, Galvanized, Chrome Plating, Custom Finishes |
Certifications | CE, ISO13485, TUV, OHSAS |
Shelf Life | 2 Years |
Applications | Medical Devices, Surgical Instruments, Operation Rooms, Surgical Applications, Medical Equipment Maintenance |
Instrument Classification | Class II |
Packaging | Carton Box, Customized Packaging Options |
Services | OEM/ODM, One-Stop Machining-Assembly, Customization |
Key Features | High Precision, Customizability, Durable Materials, Wide Material Compatibility |
High Precision Tools for Medical Device Manufacturing Processes
Medical device manufacturing demands extraordinary precision, reliability, and adherence to stringent regulatory standards. High-precision tools are critical in this domain to meet the exacting requirements of functionality, safety, and biocompatibility. These tools enable manufacturers to produce intricate components with tight tolerances, ensuring that devices perform as intended and meet industry-specific quality benchmarks.
Key Aspects of High-Precision Tools in Medical Device Manufacturing
1. Micromachining Tools
- Purpose: Micromachining is essential for creating small and complex components used in devices like catheters, stents, and implants.
- Techniques: CNC (Computer Numerical Control) micromachining and laser micromachining allow for sub-micron accuracy.
- Applications: These tools are widely used in the production of microfluidic devices, surgical instruments, and precision diagnostic equipment.
2. Laser Processing Equipment
- Purpose: Lasers provide a non-contact method for cutting, welding, drilling, and marking delicate materials.
- Advantages:
- Ability to process a wide range of materials, including metals, polymers, and ceramics.
- High precision and minimal thermal impact on the material.
- Applications: Used in engraving serial numbers on surgical tools, drilling holes in catheters, and welding titanium implants.
3. Additive Manufacturing (3D Printing) Tools
- Purpose: Additive manufacturing enables the creation of complex geometries that are difficult or impossible to achieve with traditional methods.
- Technologies:
- Selective Laser Sintering (SLS)
- Stereolithography (SLA)
- Direct Metal Laser Sintering (DMLS)
- Applications: Prototyping and production of patient-specific implants, surgical guides, and components for medical devices.
4. Inspection and Metrology Equipment
- Purpose: Ensuring accuracy during and after manufacturing is crucial for medical devices. Inspection tools provide precise measurements to verify adherence to specifications.
- Types:
- Coordinate Measuring Machines (CMM)
- Optical and laser-based systems
- X-ray and CT scanning for internal structure analysis
- Applications: Quality assurance for implants, precision surgical instruments, and other critical components.
5. High-Precision Molding Tools
- Purpose: Injection molding tools are used to produce plastic and silicone components with exceptional detail and consistency.
- Capabilities:
- Micro-molding for creating features as small as a few microns.
- Multi-cavity molds for high-volume production.
- Applications: Manufacturing drug delivery devices, diagnostic cartridges, and surgical instrument handles.
6. Surface Finishing Tools
- Purpose: Surface finishing ensures biocompatibility and enhances device performance.
- Techniques:
- Electro-polishing for creating ultra-smooth surfaces.
- Sandblasting and chemical etching for texture control.
- Plasma treatments for surface modification.
- Applications: Used to finish surgical instruments, stents, and prosthetics.
7. Advanced Material Processing Tools
- Purpose: Specialized tools are required to process advanced materials like bioresorbable polymers and shape-memory alloys.
- Techniques:
- High-speed machining for brittle materials.
- Precision grinding for ceramics and glass.
- Applications: Fabrication of bioresorbable scaffolds, pacemaker components, and orthopedic implants.
Benefits of High-Precision Tools in Medical Device Manufacturing
- Enhanced Product Quality: Improved accuracy ensures the functionality and reliability of devices.
- Regulatory Compliance: Precision tools help manufacturers meet rigorous standards like ISO 13485 and FDA requirements.
- Scalability: Advanced tools support both prototyping and high-volume production.
- Material Versatility: Adaptability to work with diverse materials like metals, polymers, ceramics, and composites.
High-precision tools are indispensable in medical device manufacturing, enabling the production of innovative, life-saving devices. With advancements in technology, these tools continue to push the boundaries of what is possible, ensuring that medical devices are safe, reliable, and effective for end-users. The integration of these tools with automation, AI, and IoT further enhances the efficiency and capabilities of modern manufacturing processes.
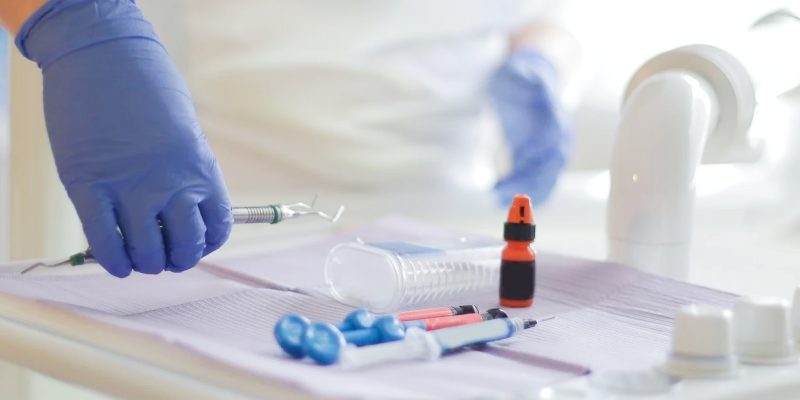
Classifications of High Precision Tools for Medical Device Manufacturing
The manufacturing of medical devices demands an extraordinary level of precision, given the critical importance of ensuring patient safety and product efficacy. High precision tools are essential for producing components with tight tolerances, complex geometries, and superior surface finishes. Below is a detailed classification of high precision tools commonly used in medical device manufacturing:
Machining Tools
These tools are used to shape and finish materials to exact specifications, typically with tolerances in the micron range.
- CNC Milling Machines: Used for producing complex 3D geometries in materials like metals and plastics. They are crucial for creating surgical instruments and prosthetic components.
- CNC Turning Machines: Ideal for cylindrical parts like catheters, guidewires, and screws for implants.
- Micro-Machining Tools: Include micro-drills, end mills, and laser cutters for ultra-small components such as stents and sensors.
Laser-Based Tools
Lasers provide non-contact, high-precision processing, making them indispensable in medical device manufacturing.
- Laser Cutting: For cutting intricate patterns in metals, polymers, and ceramics, such as in stent manufacturing.
- Laser Welding: Ensures strong, precise welds for assembling components like pacemakers and surgical instruments.
- Laser Drilling: Creates micro-holes in components such as filters and infusion devices.
Additive Manufacturing Tools
Also known as 3D printing, these tools enable the production of complex, custom, and lightweight medical devices.
- Stereolithography (SLA): For creating highly detailed prototypes and biocompatible components.
- Selective Laser Sintering (SLS): Used for producing durable parts, such as orthopedic implants, directly from powdered materials.
- Direct Metal Laser Sintering (DMLS): Facilitates the production of high-strength metal components, like titanium implants.
Metrology and Inspection Tools
Precision in manufacturing requires equally precise tools to measure and inspect components.
- Coordinate Measuring Machines (CMMs): For verifying the dimensions and geometries of components with extreme accuracy.
- Optical and Electron Microscopes: Essential for inspecting micro-features and surface finishes.
- Surface Profilometers: Measure surface roughness and texture, ensuring compliance with strict medical standards.
Molding and Forming Tools
These tools are critical for producing plastic and composite components in medical devices.
- Injection Molding Machines: For manufacturing disposable medical components like syringes, tubing connectors, and housings for electronic devices.
- Compression Molding Tools: Used for components requiring high mechanical properties, such as prosthetics and orthopedic supports.
- Blow Molding Machines: Produce hollow components like blood collection tubes and IV fluid containers.
Grinding and Polishing Tools
For achieving smooth, burr-free surfaces, grinding and polishing are indispensable processes.
- Cylindrical Grinders: For shafts and other rounded components used in surgical tools.
- Centerless Grinders: Ideal for producing flawless surfaces on catheters and guidewires.
- Ultrasonic Polishers: Provide precision finishing for intricate parts, ensuring biocompatibility and smooth surfaces.
Ultrasonic and Electrical Discharge Machining (EDM) Tools
These specialized tools are used for materials and designs that are difficult to machine using conventional methods.
- Wire EDM: Cuts complex shapes in hard metals like titanium and stainless steel.
- Sinker EDM: Produces intricate cavities and molds, especially for implantable devices.
- Ultrasonic Machining: Drills and shapes brittle materials, such as ceramics, used in dental and orthopedic applications.
Bonding and Assembly Tools
For final assembly, precise bonding and joining methods are critical.
- Robotic Assembly Systems: Ensure repeatability and precision in assembling small and delicate components.
- Adhesive Dispensing Machines: For uniform application of medical-grade adhesives in devices like catheters and sensors.
- Hot Bar Reflow Soldering Tools: Used for electronic device assembly, ensuring strong electrical connections.
By leveraging the right tools, manufacturers can achieve unparalleled accuracy, quality, and efficiency in producing advanced medical devices.
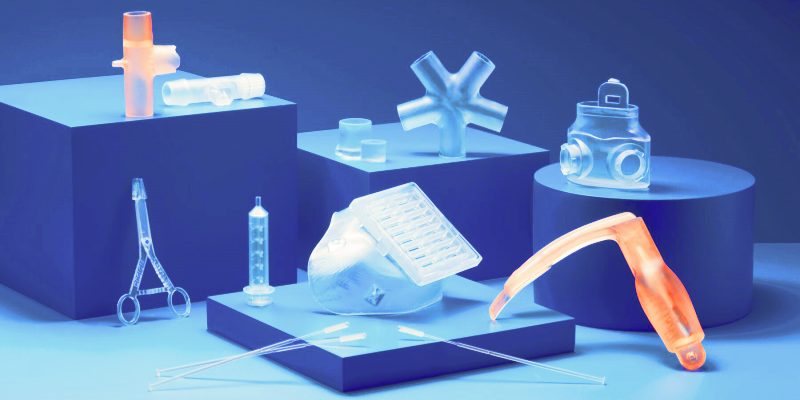
Why Need High Precision Tools for Medical Device Manufacturing
High precision tools are essential for medical device manufacturing for several reasons, driven by the stringent quality, safety, and regulatory requirements of the healthcare industry. Here’s an overview of why precision matters:
Patient Safety
- Medical devices often interact directly with or are implanted in the human body. Any inaccuracies in their dimensions or function can lead to serious health risks, such as device failure, tissue damage, or incorrect medical readings.
Regulatory Compliance
- Medical devices are subject to rigorous standards from regulatory bodies like the FDA (U.S.), CE (Europe), and others. Precision in manufacturing ensures adherence to these strict specifications and minimizes the risk of non-compliance.
Functional Performance
- Medical devices must perform reliably and consistently. For example, surgical tools, prosthetics, and diagnostic equipment require exacting dimensions to function as intended. High precision minimizes variability and ensures optimal performance.
Miniaturization of Devices
- Modern medical technology increasingly relies on miniaturized devices, such as micro-needles, stents, and laparoscopic instruments. Producing such tiny components with exact tolerances necessitates high-precision tools.
Material Sensitivity
- Medical device materials often include specialized metals, polymers, and ceramics that require careful handling to maintain their properties. High-precision tools ensure accurate shaping and processing without compromising material integrity.
Custom and Complex Designs
- Devices such as implants, orthotics, and prosthetics are often customized for individual patients. High-precision manufacturing ensures that complex and personalized designs meet exact specifications.
Cost Efficiency
- Precision tools reduce waste by minimizing errors and material defects. They also enhance production efficiency by maintaining consistent quality, reducing the need for rework or corrections.
Longevity and Durability
- Precise manufacturing ensures tighter tolerances and better assembly, which can enhance the durability and lifespan of medical devices. This is crucial for implants or devices that remain in the body for extended periods.
Advancement in Medical Technology
- High-precision tools enable innovations in medical technology, such as robotics, minimally invasive surgery tools, and advanced diagnostic devices, which require exceptional manufacturing accuracy.
Reputation and Market Competitiveness
- Manufacturers with the capability to produce high-precision medical devices are seen as reliable and advanced. This builds trust with healthcare providers and gives a competitive edge in the market.
High precision tools in medical device manufacturing are not just a preference but a necessity to meet the critical demands of patient safety, regulatory compliance, and technological advancement.
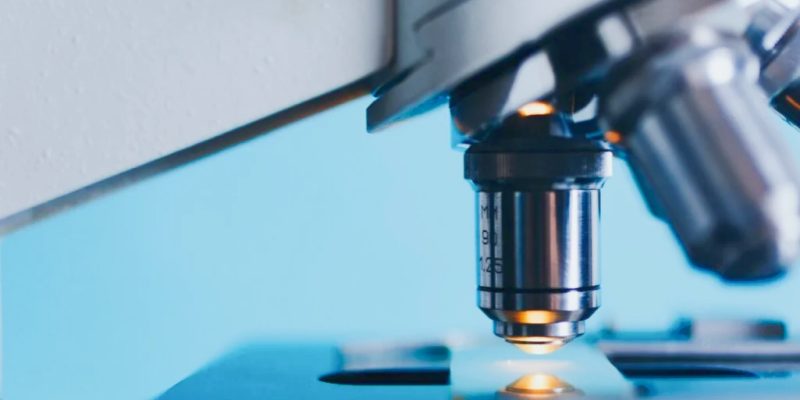
About Medical Molded Plastics Solutions and High Precision Tools for Medical Device Manufacturing
- Founded decades ago, we have become a global leader in providing high precision tools for medical device manufacturing, specializing in molds for the medical sector and serving clients in the healthcare, biotech, and pharmaceutical industries.
- The company specializes in creating tools tailored to the exacting demands of the medical sector, ensuring unparalleled accuracy and durability.
- With a focus on innovation, We incorporates cutting-edge technology and medical molded plastics solutions into its design and manufacturing processes to support the creation of advanced medical devices.
- Services include product customization, technical support, and training to help manufacturers optimize their production processes.
Advisory Board
- We collaborate with industry experts, medical professionals, and researchers to ensure its products, including high quality medical plastic parts, align with the latest healthcare standards and advancements.
- The advisory board, comprising experienced engineers and medical molded plastics solutions, plays a pivotal role in refining the company’s high precision tools for medical device manufacturing.
- Partnerships with international associations and certification bodies ensure compliance with global regulatory standards, reinforcing our commitment to excellence.
Products: High Precision Tools for Medical Device Manufacturing in Molded Plastics Solutions
Tweezers
- High Precision Tweezers: Designed for delicate tasks in medical device assembly, these tools are essential for any medical device assembler. They include high precision tools for medical device manufacturing and specialized options such as Ceramic, Plastic, and ESD-Coated Tweezers.
- Customizations: Tweezers with replaceable tips, pre-assembled kits, and gold-plated models to meet specific requirements in high precision tools for medical molded plastics solutions.
Cutters and Pliers
- Precision Cutting Tools: Featuring Tungsten Carbide and TEK-ME Carbon Steel hand tools for exceptional performance in cutting and shaping medical molded plastics solutions.
- Specialized Options: Includes cable cutters and hairspring cutters for intricate and delicate applications.
Probes and Spatulas
- Microspatulas: Perfect for handling small samples in medical and research settings.
- ESD-Safe Designs: Prevent static interference, ideal for sensitive medical device components.
Scalpels and Blades
- Industrial Trimming Knives: High-precision blades for trimming materials in tight or complex areas.
- Retractable Models: Offer safety and convenience for precision cuts in sterile environments.
Workbench Accessories
- Enhanced Efficiency Tools: Circuit Board Holders, Sticky Swabs, Wire Strippers, and Solvent Dispensers to support clean and precise work environments.
Testers and Visual Inspection Tools
- Advanced Inspection Devices: Smart tweezers, magnifying LED lamps, HD inspection systems, and digital microscopes ensure quality control in high precision tools for medical device manufacturing.
- These tools guarantee exceptional accuracy in evaluating and verifying components.
Media and Educational Resources: High Precision Tools for Medical Device Manufacturing in Molded Plastics
- Stay updated with the latest developments in high precision tools for medical device manufacturing, including insights for plastic medical device manufacturers, through our news portal.
- Regular announcements cover new product launches, innovative technologies, and industry trends to keep manufacturers informed and ahead in the medical device sector.
- Access a comprehensive library of resources, including detailed product catalogs and technical datasheets for all high precision tools for medical molded plastics solutions.
- These downloadable materials provide in-depth specifications, usage instructions, and customization options to support decision-making for manufacturers.
Applications and Markets: Leveraging High Precision Tools for Medical Device Manufacturing in Molded Plastics Solutions
Medical Devices
- We specializes in providing high precision tools for medical device manufacturing, designed to meet the rigorous demands of the healthcare industry.
- These tools are essential for assembling intricate components of medical devices, ensuring safety, reliability, and compliance with industry standards.
Life Sciences
- Advanced instruments such as medical molded plastics solutions and microspatulas are used in microscopy, laboratory research, and sample preparation.
- Their precision supports critical tasks in pharmaceutical and biotechnology applications.
Electronics
- Precision tweezers, cutters, and inspection tools aid in assembling and maintaining delicate electronic circuits.
- These tools ensure accuracy and minimize damage to sensitive components, making them indispensable for high-tech electronics manufacturing.
Watchmaking & Jewelry
- The company offers a range of high-quality tweezers and cutters designed specifically for the fine detailing required in watchmaking and jewelry crafting.
- These tools ensure precision in handling small parts and intricate designs.
Beauty Industry
- Our instruments, including ESD-coated tweezers and precision scissors, are widely used in cosmetic applications such as eyelash extensions and nail art.
- Their durability and precision cater to the beauty industry’s demand for high-quality tools.
By serving diverse markets with its range of high precision tools formedical molded plastics solutions manufacturing, we demonstrates its versatility and commitment to excellence across multiple industries.
FAQs about High Precision Tools for Medical Device Manufacturing
GMPs, or Good Manufacturing Practices, for medical devices are a set of regulations and guidelines provided by regulatory bodies like the FDA (Food and Drug Administration) to ensure products are consistently produced and controlled according to quality standards. These practices minimize risks involved in any pharmaceutical production and ensure products’ safety, efficacy, and quality. GMPs for medical devices cover various aspects, including manufacturing processes, facility design, documentation, quality control, and personnel training. Compliance with GMPs ensures that medical devices meet specific requirements and can be safely used by consumers.
Enterprise Resource Planning (ERP): Manages day-to-day activities like accounting, procurement, project management, and supply chain operations.
Product Lifecycle Management (PLM): Helps manage the entire lifecycle of a product from inception, through engineering design and manufacturing, to service and disposal.
Quality Management Systems (QMS): Ensures compliance with regulations, tracks quality metrics, controls documentation, and manages corrective actions.
Computer-Aided Design (CAD): Facilitates the design and development of the medical devices.
Manufacturing Execution Systems (MES): Monitors and controls production on the shop floor.
These software solutions help streamline operations and maintain compliance with stringent medical regulations.
MMT medical refers to Micro-Machining Technology (MMT) used in the medical device industry. It involves the use of advanced machining and manufacturing techniques to produce micro-scale components and intricate features required for medical devices. These components are often critical for the functionality of devices like minimally invasive surgical instruments, implants, and diagnostic equipment. MMT allows for high precision, tight tolerances, and the ability to work with various materials, including metals, polymers, and ceramics. This technology is crucial for producing smaller, more complex medical devices that cater to the growing demand for miniaturized and less invasive medical solutions.
Quality in the medical device industry refers to the overall measures taken to ensure medical devices are safe, effective, and perform as intended. This involves adhering to standards and regulations set by governing bodies such as the FDA or ISO (International Organization for Standardization). Key aspects of quality in this industry include:
Design Control: Ensuring the device meets user needs and intended uses through careful planning, design verification, and validation.
Risk Management: Identifying and mitigating risks associated with the device throughout its lifecycle.
Supplier Quality Management: Ensuring that materials sourced from suppliers meet required standards.
Production and Process Control: Monitoring and controlling manufacturing processes to maintain quality and consistency.
Post-market Surveillance: Monitoring the performance of the device once it is on the market to detect any issues that may arise.
Maintaining high quality in medical device manufacturing is critical to ensuring patient safety and regulatory compliance.
The five main components of Good Manufacturing Practices (GMP) are:
Personnel: Ensuring staff are properly trained, qualified, and follow hygiene practices to prevent contamination.
Premises and Equipment: Facilities and equipment must be designed, maintained, and cleaned to minimize risks to product quality and patient safety.
Documentation: Accurate and thorough record-keeping ensures traceability, accountability, and compliance.
Production Processes: Standardized and validated procedures are critical for consistent and quality outcomes in medical device manufacturing.
Quality Control: Ongoing monitoring, testing, and review processes ensure the finished products meet predefined standards.
These components are critical in maintaining the safety, efficacy, and quality of medical devices.
The purpose of GMP regulations for medical devices is to ensure that devices are consistently produced and controlled according to quality standards. GMPs aim to:
Minimize risks associated with manufacturing, such as contamination, defects, or errors that could harm patients.
Ensure compliance with regulatory standards, maintaining trust and market access.
Provide a framework for continuous quality improvement.
Ultimately, GMP regulations help protect patients by ensuring medical devices are safe, effective, and reliable, reducing risks associated with device failure or adverse events.
GMP and ISO 13485 differ in scope and focus:
GMP (Good Manufacturing Practices): GMP is a regulatory requirement enforced by government agencies, such as the FDA. It focuses on the manufacturing, storage, and quality control processes to ensure safety and efficacy in regulated industries, including medical devices.
ISO 13485: ISO 13485 is an internationally recognized quality management standard specific to medical devices. It provides a framework for a quality management system but is not a regulatory requirement.
While GMP emphasizes compliance with laws and regulations, ISO 13485 focuses on establishing best practices for quality management systems, facilitating global trade and standardization.
Products falling under GMPs in the medical field include:
Medical Devices: Instruments, apparatuses, implants, and in vitro diagnostic devices.
Pharmaceuticals: Prescription drugs, over-the-counter medications, and vaccines.
Biologics: Cell and gene therapies, blood products, and biosimilars.
Combination Products: Devices incorporating drugs or biologics, such as drug-eluting stents.
Nutraceuticals and Dietary Supplements: While not universally regulated, some jurisdictions require GMP compliance for these products.
GMPs ensure these products are consistently manufactured to meet quality and safety standards, protecting end-users and patients.
High precision tools in medical device manufacturing ensure that the complex designs and strict tolerances required for devices like implants, catheters, and surgical instruments are met. Common tools include CNC machines, laser cutters, micromachining equipment, and precision molding machines. These tools are often equipped with advanced automation and real-time monitoring systems to enhance accuracy and repeatability. Precision is critical to meet regulatory standards, ensure patient safety, and reduce manufacturing defects. Laser technologies are particularly effective for cutting and welding small, delicate components, while injection molding is commonly used for high-volume production of plastic medical devices.
Good Manufacturing Practices (GMPs) for medical devices are a set of regulatory guidelines that ensure products are consistently produced and controlled to meet quality and safety standards. GMPs cover all aspects of manufacturing, including equipment maintenance, employee training, and quality assurance processes. The goal is to ensure devices are safe for use and perform as intended. In the U.S., GMPs for medical devices are governed by 21 CFR Part 820, which outlines requirements for design controls, process validation, and product labeling.
A Quality Management System (QMS) for medical devices is a structured framework that ensures devices meet regulatory and customer expectations. It encompasses processes such as risk management, corrective actions, and continuous improvement. QMS is integral to regulatory compliance, especially with standards like ISO 13485, which is tailored for medical devices. An effective QMS helps manufacturers streamline production, reduce errors, and maintain consistent quality.
The Code of Federal Regulations (CFR) Title 21 is the primary U.S. regulatory framework for medical devices. Specifically, Part 820 outlines the Quality System Regulation (QSR), which includes design controls, production processes, and post-market surveillance. Compliance with the CFR ensures devices meet safety, efficacy, and quality standards.
Yes, GMPs are required by law for medical device manufacturing in most countries. In the U.S., the FDA enforces these requirements under 21 CFR Part 820. Non-compliance can lead to product recalls, legal penalties, or even facility shutdowns.
ISO 13485 is the global standard for medical device quality management systems. It provides a comprehensive framework for designing, developing, and manufacturing medical devices. The standard emphasizes risk management, process validation, and regulatory compliance.
Medical device manufacturing uses software such as CAD (Computer-Aided Design) for device prototyping, ERP (Enterprise Resource Planning) for resource management, and MES (Manufacturing Execution Systems) for production tracking. Validation software ensures processes meet regulatory standards.
Medical practices frequently use EMR (Electronic Medical Records) systems like Epic and Cerner. These systems streamline patient data management, scheduling, billing, and compliance. Telemedicine platforms and practice management software are also widely used.
Durable Medical Equipment (DME) software manages inventory, compliance, and billing for suppliers of equipment like wheelchairs, oxygen systems, and hospital beds. It integrates with insurance systems for efficient claim processing.
Wearable medical devices are the fastest-growing segment, driven by advancements in health monitoring technologies like smartwatches and fitness trackers. These devices enable real-time data collection and remote patient monitoring.
Diagnostic devices, such as imaging systems (MRI, CT scanners) and monitoring devices (ECG machines, blood pressure monitors), are in high demand due to the rising prevalence of chronic diseases and the need for early diagnosis.
Implantable medical devices, such as orthopedic implants, cardiovascular stents, and pacemakers, generate the most revenue. These devices are high-cost, high-impact solutions for critical health conditions.
Regulatory Compliance: Constantly evolving regulations require substantial investment in processes and documentation.
Cost Pressures: Balancing innovation with affordability is a major hurdle.
Supply Chain Disruptions: Delays in sourcing raw materials and components can hinder production timelines.
The medical device industry is highly profitable, with margins often exceeding 20%. Growth is driven by technological innovations, regulatory approvals, and expanding global healthcare infrastructure.
Commonly used medical devices include thermometers, stethoscopes, blood pressure monitors, and glucose meters. These devices are essential for routine diagnostics and chronic disease management.
The United States is the largest supplier, contributing significantly to global exports. It leads in R&D, innovation, and the production of high-value medical technologies.
Technological Advancements: AI, IoT, and robotics are revolutionizing device functionality.
Aging Population: An older demographic increases demand for healthcare solutions.
Chronic Diseases: Rising cases of diabetes, cardiovascular issues, and cancer drive demand.
Emerging Markets: Expanding healthcare infrastructure fuels growth in developing countries.
Contact our professional team now for a same-day quote and risk-free project evaluation. Benefit from ISO 8 cleanrooms, advanced machines, and 12-hour fast response in medical injection molding.