The healthcare industry increasingly relies on plastic materials for the production of medical devices, offering essential benefits like durability, cost-effectiveness, and versatility. High-quality medical plastic parts are crucial for advancing healthcare technologies, ensuring safety, precision, and reliability in patient care. These components are integral to the functionality of various medical devices, from surgical instruments to diagnostic equipment. The manufacturing of these parts requires strict adherence to quality standards, as the reliability of medical devices directly impacts patient outcomes. Precision molding medical processes are key to producing these high-quality parts, ensuring the accuracy and performance needed for safe, effective use. As such, focusing on the production of high-quality medical plastic parts is vital to meeting the evolving needs of modern healthcare systems. High-quality medical plastic parts from FUJIU Medical Injection Mold, a leading China medical plastic parts factory, provide FDA-compliant durability, sterilization tolerance, and enhanced device performance.
Why High Quality Medical Plastic Parts Are Essential for Patient Safety
In the healthcare industry, the importance of high quality medical plastic parts cannot be overstated. These parts are integral to the safe and efficient operation of medical devices, and their quality directly impacts patient safety. Medical plastic components are used in everything from surgical tools to diagnostic machines, and even slight defects in these parts can lead to malfunction or failure.
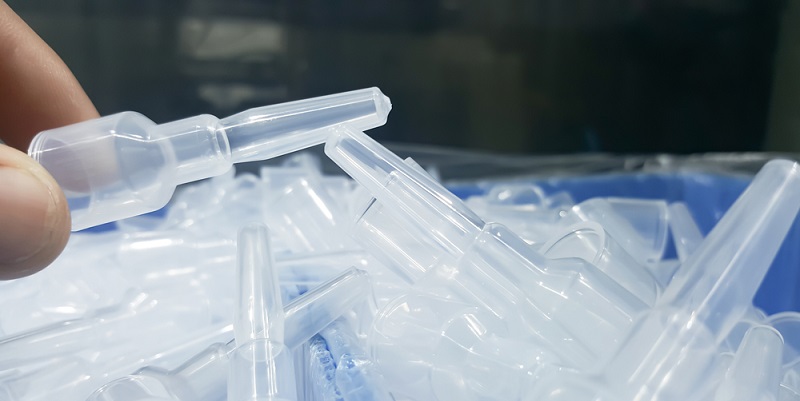
Factors That Affect Patient Safety
- Material Integrity: High quality medical plastic parts are manufactured with materials that are durable, resistant to wear, and able to withstand harsh environments such as sterilization processes.
- Precision Manufacturing: High precision is crucial to ensure that medical devices function correctly. Even minor deviations in plastic components can result in misalignment or malfunction, affecting patient care.
- Chemical Resistance: Medical devices must often resist exposure to various chemicals, such as disinfectants or medications. Low-quality plastic parts may degrade, impacting the safety of the device.
- Regulatory Compliance: High quality medical plastic parts must meet stringent regulatory standards to ensure they are safe for use in medical settings. Failure to comply with these standards could jeopardize patient health.
The reliability of these materials is essential to ensure that medical devices perform their intended function without compromising the safety of patients. The critical role of medical plastic parts high quality extends far beyond the production floor and into patient care, emphasizing the need for rigorous quality control and adherence to industry standards.
Key Features of High Quality Medical Plastic Parts
High quality medical plastic parts are characterized by several essential features that ensure they meet the stringent requirements of the healthcare industry. These features not only enhance the performance of medical devices but also ensure patient safety and regulatory compliance. The following are the key features that define high quality medical plastic parts:
Durability and Longevity
- Resistance to Wear and Tear: High quality medical plastic parts are designed to withstand repetitive use without degrading. This durability ensures that the parts maintain their functionality over time, reducing the risk of malfunctions or failures.
- Impact Resistance: Medical devices often need to endure physical stress. High quality plastic components are engineered to resist cracks, breaks, or deformation when subjected to pressure or impact.
- Temperature Resistance: Many medical applications involve exposure to high or low temperatures, such as during sterilization. High quality medical plastic parts can endure these temperature variations without losing their structural integrity.
- Chemical Resistance: Medical devices are frequently exposed to a variety of chemicals, including disinfectants, drugs, and bodily fluids. High quality medical plastic parts are resistant to chemical degradation, ensuring they maintain their functionality in diverse environments.
Precision and Accuracy
- Tight Tolerances: High quality medical plastic parts are manufactured with precision to meet the exact specifications of the medical device. This ensures that each part fits perfectly within the device, minimizing the risk of operational failure.
- Consistency: Manufacturing processes for high quality medical plastic parts ensure consistency in every batch, so each part exhibits the same high standard of performance. Consistent quality reduces variability in device performance.
- Custom Molded Shapes: Many medical devices require custom shapes or designs, and high quality plastic parts are capable of being molded with complex geometries to meet these specific needs.
Regulatory Compliance
- ISO Standards Compliance: High quality medical plastic parts are produced in compliance with international standards, such as ISO 13485, which ensures that medical devices are designed, developed, and manufactured with a focus on safety and quality.
- FDA Approval: Many medical plastic parts need to meet FDA (Food and Drug Administration) requirements. High quality parts are often tested and approved for use in medical devices to ensure safety and effectiveness.
- Biocompatibility: High quality medical plastic parts are manufactured from biocompatible materials, meaning they do not cause adverse reactions when in contact with the human body, such as in implants or surgical instruments.
Ease of Sterilization
- Autoclave Compatibility: Medical devices often require sterilization to ensure they are free of harmful pathogens. High quality medical plastic parts are designed to withstand autoclave processes, ensuring that they remain safe for use even after repeated sterilization cycles.
- Non-porous Surface: High quality medical plastic parts often have smooth, non-porous surfaces that prevent the growth of bacteria and other pathogens, further enhancing patient safety.
High quality medical plastic parts are indispensable in the healthcare industry. Their durability, precision, compliance with regulations, and ability to withstand sterilization are essential to ensuring that medical devices function reliably and safely in a wide range of medical applications.
Types of High Quality Medical Plastic Parts Used in Healthcare
High quality medical plastic parts are integral to a wide range of healthcare applications. These parts must meet strict regulatory standards, ensuring that they provide safety, durability, and functionality in medical devices. The following are some common types of high quality medical plastic parts used in healthcare settings:
Injection-Molded Plastic Parts
- Syringe Components: High quality medical plastic parts are essential for manufacturing syringes, where precision and cleanliness are critical. These components are made from biocompatible plastic materials to ensure safety during injection or fluid transfer.
- Catheters: Catheters often require custom-shaped plastic parts that need to be both flexible and durable. High quality plastic is used to ensure the catheters maintain their integrity under varying pressures and during prolonged use.
- IV Connectors: These parts need to withstand constant fluid exposure and high-pressure conditions. High quality medical plastic parts are used to ensure secure connections and minimize the risk of leaks or failure during fluid transfer.
- Prosthetic Components: Prosthetic devices rely on high-quality plastic parts that are lightweight, durable, and comfortable for the user. These components often require customization to ensure proper fit and function.
Extruded Plastic Parts
- Tubing: Medical tubing is commonly made from high quality medical plastic parts, ensuring it is flexible, durable, and resistant to chemical exposure. This type of plastic part is essential for medical devices such as oxygen masks, IV systems, and respiratory equipment.
- Filtration Components: High quality extruded plastics are used to create filtration membranes for devices like dialysis machines or air purifiers. These parts need to maintain their filtration integrity over time while being resistant to chemical and biological contaminants.
Molds and Housing Units
- Device Casings: Many medical devices, such as portable monitors, diagnostic machines, and surgical instruments, require sturdy housing to protect sensitive electronics and internal components. High quality medical plastic parts are used to mold these casings, providing both strength and insulation.
- Protection Covers: Many medical devices require protection from dust, moisture, and contaminants. High quality plastic parts are used to create protective covers for devices like surgical instruments, diagnostic equipment, and patient monitoring systems.
Implantable Medical Devices
- Orthopedic Implants: High quality medical plastic parts are used in orthopedic devices such as joint replacements and bone anchors. These materials must be biocompatible and capable of withstanding the mechanical stresses of the body.
- Dental Implants: For dental applications, high quality plastics are used in crowns, bridges, and dentures. These parts need to be both durable and comfortable while ensuring biocompatibility with the body’s tissues.
The versatility of high quality medical plastic parts allows for their integration into a wide range of healthcare applications, from basic tools to complex, life-saving devices. As the healthcare industry continues to evolve, the demand for high-precision medical components will only grow, emphasizing the need for consistent quality and innovative manufacturing techniques.
How High Quality Medical Plastic Parts Are Manufactured
The manufacturing of high-quality medical plastic parts involves a series of precise and highly controlled processes to ensure that each component meets stringent safety, performance, and regulatory standards. Medical device assemblers play a critical role in this process, ensuring that each part is carefully constructed, assembled, and tested to the highest specifications. These parts must be produced with extreme attention to detail, as even slight variations can affect the functionality and safety of medical devices. Below are the key steps involved in the manufacturing of high quality medical plastic parts.
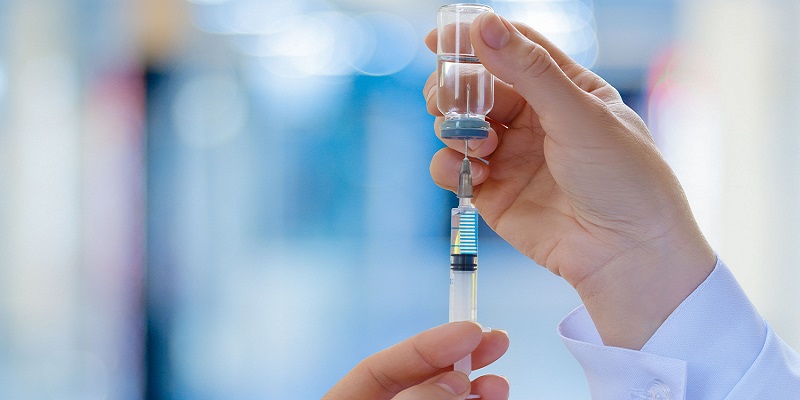
Material Selection and Preparation
- Choosing Biocompatible Plastics: High-quality medical plastic parts are made from materials that are biocompatible, meaning they do not cause adverse reactions when in contact with the human body. Common materials include medical-grade polypropylene, polycarbonate, and polyethylene. Both polypropylene and polycarbonate are widely used in medical devices class 2 injection molding parts, ensuring the required strength, durability, and safety for medical applications.
- Ensuring Material Purity: The plastics used in medical applications must be free from contaminants that could affect their performance or safety. This requires careful sourcing of materials and rigorous quality control processes during the material preparation phase.
- Additives for Strength and Durability: Some medical plastic parts may require additives such as stabilizers or plasticizers to improve their strength, flexibility, or resistance to temperature and chemicals. These additives must be carefully controlled to avoid any negative impact on the safety or function of the final product.
Manufacturing Processes
- Injection Molding: This is one of the most common methods used for producing high quality medical plastic parts. In injection molding, plastic is heated until it becomes molten, then injected into a mold under high pressure. This medical injection molding process allows for the production of complex, precise shapes with tight tolerances.
- High precision: Injection molding allows for the creation of parts with exceptional detail and accuracy, which is critical in medical device plastic manufacturing.
- Repeatability: This method ensures that each part is made consistently, meeting the same specifications in every cycle.
- Fast Production: Medical injection molding is efficient, allowing for high-volume production while maintaining product quality.
- Extrusion: For certain applications, such as medical tubing or filters, extrusion is used to form plastic parts. In extrusion, heated plastic is forced through a mold to create continuous shapes. This method is commonly used to create flexible components like tubing for IV systems and catheters.
- Blow Molding: For hollow medical parts such as bottles or fluid containers, blow molding is employed. This process involves inflating a heated plastic tube into a mold to form the desired shape. It is highly effective for creating parts that need to hold liquids or gases under pressure.
Post-Manufacturing Processes
- Quality Control and Inspection: After the parts are molded, they undergo rigorous inspection to ensure they meet medical device standards. This includes testing for dimensional accuracy, strength, and resistance to environmental factors such as temperature and chemicals.
- Dimensional inspections: High quality medical plastic parts must meet precise specifications, which are verified through automated inspection systems.
- Sterilization: Many medical plastic parts require sterilization, and the chosen materials and manufacturing methods must ensure that the components can be sterilized without compromising their integrity.
- Cleaning and Packaging: Once the parts have passed inspection, they are carefully cleaned to remove any manufacturing residues. Cleanliness is essential in medical device plastic manufacturing to avoid contamination. The parts are then packaged in sterile, protective containers to maintain their integrity before use.
Testing and Certification
- Biocompatibility Testing: High quality medical plastic parts must undergo biocompatibility testing to ensure they are safe for use in the human body. This testing is often performed in compliance with ISO 10993 standards.
- Performance Testing: In addition to biocompatibility, the parts must be tested for their ability to perform under the expected conditions. This includes tests for durability, resistance to wear, and the ability to function effectively over time.
- Regulatory Approval: Manufacturers must ensure that high quality medical plastic parts meet all necessary regulatory requirements, including FDA approval in the U.S. or CE marking in Europe, before they can be used in medical devices.
By following these rigorous processes, manufacturers can produce high quality medical plastic parts that meet the highest standards of safety, reliability, and performance, ensuring that medical devices function as intended and support positive patient outcomes.
Regulatory Standards and Certification for High Quality Medical Plastic Parts
The manufacturing of high quality medical plastic parts is governed by a set of stringent regulatory standards and certification processes to ensure that the final products are safe, effective, and reliable for use in healthcare applications. Compliance with these standards is crucial to meet both industry requirements and patient safety considerations. Below are the key regulatory standards and certification processes for high quality medical plastic parts.
Key Regulatory Standards for Medical Plastic Parts
- ISO 13485: This standard specifies the requirements for a quality management system (QMS) in the medical device industry. It ensures that manufacturers of high quality medical plastic parts maintain a high level of consistency in their production processes, allowing for continuous improvement in product quality.
- FDA Approval (21 CFR Part 820): In the United States, medical devices, including those with plastic components, must comply with the Food and Drug Administration (FDA) regulations. This includes requirements for the design, manufacturing, and testing of high quality medical plastic parts to ensure safety and effectiveness for medical use.
- ISO 10993: This is a series of standards that focus on the biological evaluation of medical devices. It assesses the biocompatibility of the materials used in medical devices, including plastics, to ensure they do not cause adverse reactions when in contact with the body.
- European CE Marking: For products sold in the European Union, CE marking is required to demonstrate that high quality medical plastic parts comply with the European Medical Device Regulation (MDR) or In-vitro Diagnostic Regulation (IVDR). This certification confirms that the product meets all safety and performance requirements.
Certification Processes for Medical Plastic Parts
- Biocompatibility Testing: Before high quality medical plastic parts are certified for medical use, they must undergo biocompatibility testing to ensure that they are safe for contact with human tissues. This testing evaluates potential toxicity, allergic reactions, and other harmful effects that could arise from prolonged exposure.
- Sterilization Validation: Many medical plastic parts, such as syringes or surgical instruments, need to be sterilized before use. Manufacturers must validate the sterilization process to ensure that the parts remain free of harmful microorganisms after sterilization. This is particularly important for parts that come into direct contact with the patient.
- Design and Process Validation: High quality medical plastic parts undergo thorough validation processes to confirm that they meet both the functional and safety requirements of the medical devices they are used in. This involves rigorous testing to ensure that the parts perform as intended under various conditions.
By adhering to these regulatory standards and certifications, manufacturers can ensure that their high quality medical plastic parts are safe for use in medical devices, enhancing patient safety and meeting industry expectations. Compliance with these regulations also facilitates global market access, allowing manufacturers to sell their products in different countries and regions.
Innovations in High Quality Medical Plastic Parts
The field of medical device manufacturing is continuously evolving, and innovations in high quality medical plastic parts play a crucial role in enhancing the performance, safety, and efficiency of medical devices. Advances in material science, manufacturing techniques, and design integration have led to significant improvements in the capabilities of medical plastic parts. High quality medical plastic parts factories are at the forefront of these innovations, employing cutting-edge technologies to produce components that meet the stringent requirements of the healthcare industry. These innovations are pushing the boundaries of what is possible in healthcare applications and offering new solutions for patient care.
Advanced Materials for High Performance
- Bio-degradable Plastics: The development of bio-degradable plastics for use in medical applications is a major innovation. These materials are designed to degrade safely within the body, reducing the risk of long-term complications from implanted devices.
- High-Performance Polymers: New polymers with enhanced properties, such as improved heat resistance, strength, and flexibility, are being used in high quality medical plastic parts. Materials like PEEK (Polyetheretherketone) are being used in applications requiring high-performance characteristics, such as spinal implants and joint replacements.
- Anti-Microbial Plastics: The introduction of anti-microbial plastics is a breakthrough in medical plastic parts manufacturing. These materials help reduce the risk of infections by inhibiting the growth of harmful bacteria on the surface of medical devices, such as surgical instruments and catheters.
- Smart Polymers: A growing area of innovation is the use of smart polymers that respond to environmental stimuli like temperature, pH, or humidity. These materials can be used for drug delivery systems or devices that require adaptive functionality, improving treatment outcomes.
Innovations in Manufacturing Processes
- 3D Printing (Additive Manufacturing): 3D printing technology has revolutionized the production of high quality medical plastic parts. This method allows for the creation of highly complex, custom-designed components with greater precision and at a faster turnaround. It is especially beneficial for prosthetics, custom implants, and surgical tools.
- Micro-Molding: The use of micro-molding techniques has enabled the creation of smaller, highly intricate plastic parts that are essential for miniaturized medical devices, such as micro-sensors, drug delivery systems, and diagnostic tools.
- Multi-Material Molding: This innovation allows for the integration of different materials into a single part, offering unique functionality. For example, combining soft and hard plastics in a single injection-molded part can create devices that are both durable and flexible, ideal for wearable medical devices like glucose monitors or heart rate sensors.
- Laser Engraving and Marking: Laser engraving is increasingly used in the medical plastics industry to mark parts with detailed serial numbers, barcodes, or logos. This innovation improves traceability and enhances product safety, especially for single-use medical devices.
Design Innovations for Improved Functionality
- Ergonomic Design: The design of high quality medical plastic parts has evolved to focus more on ergonomics. Devices such as surgical instruments, prosthetics, and diagnostic tools are now designed with user comfort and ease of use in mind, improving both the effectiveness of the device and the patient’s experience.
- Integration of Electronics: Many high quality medical plastic parts now integrate sensors, microchips, or other electronic components directly into the plastic material. This innovation enables the creation of “smart” medical devices that can monitor patients in real-time, providing continuous feedback and improving the overall effectiveness of treatments.
- Flexible Packaging Solutions: Advances in flexible plastic packaging, such as for sterile medical devices, allow for better protection and longer shelf life. Innovations in multi-layer plastic films are used to package medical devices in a way that ensures they remain sterile until they are used, without compromising the strength or integrity of the packaging.
These innovations in high quality medical plastic parts are enhancing the design, functionality, and safety of medical devices. By continuously evolving materials, manufacturing processes, and design techniques, the healthcare industry can continue to improve patient care and create more advanced, effective solutions for medical challenges.
How to Choose Medical-Grade Plastics for High-Quality Medical Plastic Parts
Selecting the right medical-grade plastic is essential for producing high-quality medical plastic parts that meet performance, safety, and regulatory requirements. The choice depends on factors such as biocompatibility, sterilization tolerance, mechanical strength, and resistance to chemicals and heat. Here’s a guide to choosing the appropriate materials and an introduction to commonly used medical-grade injection molding materials.
Factors to Consider When Choosing Medical-Grade Plastics
- Biocompatibility: Ensure the plastic meets ISO 10993 and FDA standards for safe use in medical applications.
- Sterilization Resistance: Select materials that can endure methods like autoclaving, gamma radiation, or chemical sterilization without degradation.
- Chemical Resistance: Opt for plastics that resist disinfectants, body fluids, and other chemicals encountered in medical environments.
- Mechanical Properties: Consider durability, flexibility, or rigidity based on the application, such as implants, surgical tools, or diagnostic devices.
- Processing Needs: Ensure the material is compatible with the injection molding process for efficient production.
Common Medical-Grade Injection Molding Materials
Polycarbonate (PC):
Known for its excellent strength, optical clarity, and impact resistance. It is widely used for surgical instruments, diagnostic equipment, and medical housing.
Advantages: Withstands autoclaving and gamma radiation, offers transparency for diagnostic tools, and maintains durability under stress.
Polypropylene (PP):
A lightweight, flexible plastic with high chemical and moisture resistance. Commonly used for syringes, lab containers, and medical packaging.
Advantages: Cost-effective, highly resistant to sterilization processes, and recyclable for disposable medical products.
Polyethylene (PE):
Available in low (LDPE) and high (HDPE) density forms, it is used for tubing, containers, and flexible medical components.
Advantages: Biocompatible, resistant to chemicals, and offers flexibility for specific medical applications.
Polysulfone (PSU):
A high-performance polymer with exceptional thermal and chemical resistance. Used in sterilizable components like surgical trays and dialysis parts.
Advantages: Withstands repeated autoclaving, highly durable, and maintains mechanical integrity in harsh conditions.
Thermoplastic Elastomers (TPE):
Combines elasticity and strength, ideal for seals, gaskets, and wearable devices. Offers a soft-touch feel for improved patient comfort.
Advantages: Flexible, biocompatible, and retains properties after repeated sterilization.
Polyetheretherketone (PEEK):
A high-performance material used in implants and critical medical applications. Renowned for its strength, thermal stability, and chemical resistance.
Advantages: Biocompatible, withstands sterilization, and is lightweight yet extremely durable, making it ideal for orthopedic implants.
Acrylonitrile Butadiene Styrene (ABS):
Used in non-critical medical device housings, offering strength and ease of processing.
Advantages: Cost-effective and versatile for general medical applications.
Choosing the right material for high-quality medical plastic parts involves balancing biocompatibility, durability, sterilization resistance, and application-specific requirements. Polycarbonate, polypropylene, polyethylene, polysulfone, TPE, PEEK, and ABS are commonly used medical-grade plastics, each offering unique properties to meet the diverse needs of medical device manufacturing.
Requirements for the Production Workshop and External Environments for High-Quality Medical Plastic Parts
Producing high-quality medical plastic parts requires a meticulously controlled production environment to meet stringent healthcare standards and ensure product safety and reliability. Below are the key requirements for the production workshop and external environments:
Clean Room Standards
- ISO Certification: The production area must meet ISO 14644 standards, typically ISO Class 8 (100k) or Class 7 (10k), depending on the application.
- Air Filtration: HEPA filtration systems should be installed to maintain controlled particulate levels, ensuring a contaminant-free environment.
- Positive Pressure Systems: Maintain positive air pressure to prevent external contaminants from entering the clean room.
- Sterility Protocols: Regular sterilization and cleaning of equipment and surfaces are essential to maintain a hygienic workspace.
Temperature and Humidity Control
- Stable Temperature: Maintain consistent temperatures to ensure the optimal performance of materials like polycarbonate, polypropylene, or PEEK, which are sensitive to thermal changes.
- Humidity Levels: Low humidity is crucial to avoid material degradation, especially for polymers prone to moisture absorption, like nylon or TPE.
Contamination Prevention Measures
- Personnel Hygiene: Require employees to wear cleanroom attire, including gloves, masks, and gowns, to minimize contamination risks.
- Restricted Access: Limit entry to authorized personnel and ensure strict adherence to cleanroom protocols.
- Material Handling: Use sealed containers to transport raw materials and prevent exposure to dust or moisture.
Quality Control and Monitoring
- Real-Time Monitoring: Use sensors and automated systems to continuously track environmental conditions like air quality, temperature, and humidity.
- Inspection Systems: Implement high-precision inspection tools, such as optical and CMM (Coordinate Measuring Machines), to ensure part accuracy.
- Regular Audits: Conduct periodic audits of the production environment to ensure compliance with medical industry regulations like FDA and ISO 13485.
External Environmental Considerations
- Proximity to Suppliers: Locate production facilities near raw material suppliers to ensure timely delivery and reduce contamination risks during transport.
- Waste Management: Establish systems for handling and disposing of production waste in compliance with environmental regulations.
- Energy Efficiency: Implement energy-efficient systems to support sustainability and reduce production costs while maintaining environmental standards.
Producing high-quality medical plastic parts requires a cleanroom production workshop meeting ISO standards, strict environmental controls, contamination prevention measures, robust quality monitoring, and efficient external logistics. These requirements ensure the final products meet stringent safety, regulatory, and performance standards, essential for medical applications.
Requirements for Manufacturers During the Production of High-Quality Medical Plastic Parts
Manufacturers of high-quality medical plastic parts must meet strict standards and provide specific conditions to ensure product safety, reliability, and compliance with regulatory requirements.
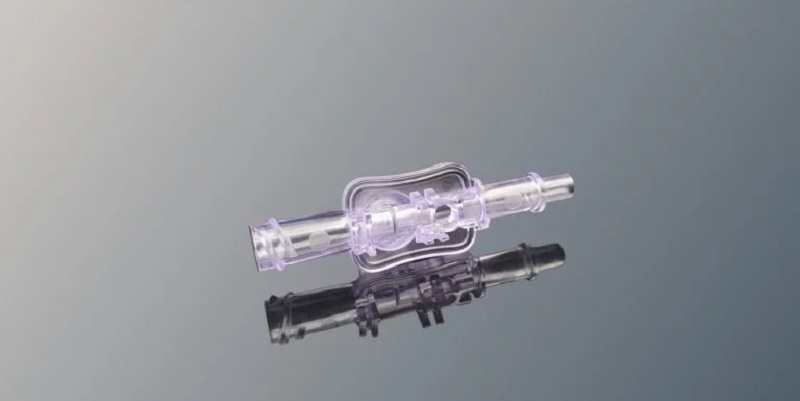
Below are the key requirements and conditions manufacturers should fulfill:
Regulatory Compliance
- Certifications: Manufacturers must comply with ISO 13485 for medical device quality management systems and FDA regulations to ensure the production process meets global standards.
- Material Testing: All materials must be certified as biocompatible according to ISO 10993 and other relevant standards.
- Traceability: Maintain thorough records of materials, processes, and products to ensure traceability for regulatory audits and recalls.
Advanced Manufacturing Equipment
- Precision Injection Molding Machines: Use state-of-the-art machines capable of producing components with tight tolerances, high precision, and repeatability.
- Specialized Tools: Provide tooling solutions optimized for medical-grade materials, such as micro-molding tools for intricate parts.
- Automated Systems: Implement automation for material handling, inspection, and packaging to reduce human error and contamination risks.
Stringent Quality Control Processes
- Inspection Standards: Employ advanced quality inspection systems, such as optical metrology, coordinate measuring machines (CMM), and in-process monitoring, to ensure parts meet exact specifications.
- Defect Prevention: Use mold flow analysis and simulation tools to identify and eliminate potential defects during production.
- Cleanroom Production: Ensure components are manufactured and assembled in ISO-certified cleanrooms to prevent contamination.
Skilled Workforce and Training
- Technical Expertise: Employ skilled engineers and technicians trained in medical injection molding, material science, and regulatory requirements.
- Ongoing Training: Provide regular training sessions to ensure the workforce stays updated on the latest technologies and standards in medical plastic manufacturing.
- Safety Protocols: Train employees in cleanroom protocols and contamination prevention.
Reliable Supply Chain Management
- Certified Material Suppliers: Partner with suppliers who provide certified medical-grade plastics, such as polycarbonate (PC), polypropylene (PP), or PEEK, to ensure consistent quality.
- Inventory Management: Maintain a robust inventory system to avoid shortages of critical materials and ensure uninterrupted production.
- Timely Delivery: Establish strong logistics to meet deadlines and maintain consistent product availability for customers.
Commitment to Sustainability
- Eco-Friendly Practices: Use sustainable materials where possible and minimize waste through recycling and efficient production practices.
- Energy Efficiency: Implement energy-saving technologies and renewable energy sources in production facilities.
- Compliance with Environmental Laws: Adhere to regulations for waste management and environmental impact reduction.
Manufacturers of high-quality medical plastic parts must adhere to strict regulatory standards, invest in advanced equipment, ensure rigorous quality control, employ a skilled workforce, manage a reliable supply chain, and commit to sustainability. By providing these conditions, manufacturers can produce safe, durable, and compliant medical plastic components that meet the high demands of the healthcare industry.
Personnel Involved in the Production Process of High-Quality Medical Plastic Parts and Their Requirements
The production of high-quality medical plastic parts involves a multidisciplinary team with specific expertise to ensure the manufacturing process meets stringent industry standards. Below are the key personnel involved and the requirements they must fulfill:
Design Engineers
Role:
- Create precise designs and specifications for medical plastic parts, focusing on functionality, manufacturability, and compliance with regulatory standards.
- Use CAD software and simulation tools to develop molds and ensure the components meet application needs.
Requirements:
- Expertise in medical device design and proficiency with software like SolidWorks or AutoCAD.
- Knowledge of material properties, such as biocompatibility and sterilization resistance.
- Familiarity with ISO 13485 standards and FDA regulations.
Process Engineers
Role:
- Develop and optimize the injection molding process to ensure consistent quality and efficiency.
- Monitor machine parameters, troubleshoot production issues, and improve cycle times.
Requirements:
- In-depth knowledge of injection molding machines, materials, and processing techniques.
- Problem-solving skills to address defects or inefficiencies during production.
- Certification in scientific molding (e.g., RJG Master Molder) is highly valued.
Quality Control Specialists
Role:
- Inspect and test components to ensure they meet specified tolerances and regulatory standards.
- Implement quality assurance processes to identify and eliminate defects.
Requirements:
- Proficiency in quality control tools like coordinate measuring machines (CMM) and optical inspection systems.
- Strong understanding of ISO 13485 and statistical process control (SPC).
- Attention to detail and a commitment to upholding product quality.
Cleanroom Technicians
Role:
- Operate in ISO-certified cleanrooms to handle and assemble medical plastic parts without contamination.
- Ensure compliance with hygiene protocols and maintain the cleanliness of the production environment.
Requirements:
- Training in cleanroom operations and contamination prevention.
- Adherence to strict hygiene practices, including wearing protective equipment.
- Familiarity with cleanroom classifications (ISO 7 or ISO 8) and associated protocols.
Maintenance Technicians
Role:
- Maintain and repair molding machines and tools to ensure uninterrupted production.
- Perform routine checks to prevent machine downtime and ensure consistent output.
Requirements:
- Technical expertise in injection molding equipment and mold maintenance.
- Strong problem-solving skills and the ability to work under time constraints.
- Certification in equipment maintenance or relevant technical training.
Regulatory and Compliance Specialists
Role:
- Ensure that all production activities and components comply with medical industry regulations, such as FDA guidelines and ISO standards.
- Handle documentation, audits, and certifications.
Requirements:
- Expertise in regulatory frameworks like ISO 10993, ISO 13485, and FDA 21 CFR Part 820.
- Strong organizational skills to manage documentation and audits.
- Attention to detail to ensure adherence to compliance requirements.
The production of high-quality medical plastic parts involves design engineers, process engineers, quality control specialists, cleanroom technicians, maintenance technicians, and regulatory specialists. Each team member must meet strict requirements related to technical expertise, regulatory knowledge, and operational precision to ensure the final products meet the high demands of the medical industry.
Key Considerations When Choosing to Customize High-Quality Medical Plastic Parts
Customizing high-quality medical plastic parts requires careful attention to ensure that the final products meet strict industry standards and specific application requirements. Below are the essential factors to consider:
Material Selection
- Biocompatibility: Ensure the selected material is certified for safe use in medical applications (e.g., ISO 10993 or FDA-approved).
- Durability: Choose materials resistant to wear, impact, and environmental stress, such as polycarbonate (PC) or PEEK.
- Sterilization Tolerance: Verify that the material can withstand sterilization processes like autoclaving, gamma radiation, or chemical cleaning.
Precision and Design Requirements
- Tight Tolerances: Confirm that the manufacturer can meet the precision required for your application, especially for parts used in critical devices like implants or surgical tools.
- Custom Geometry: Ensure the design accommodates complex shapes or micro-scale dimensions as needed.
- Prototyping: Request prototypes to validate the design and functionality before mass production.
Manufacturer Expertise
- Industry Experience: Choose a manufacturer with a proven track record in producing high-quality medical plastic parts for the healthcare sector.
- Compliance with Standards: Ensure the manufacturer adheres to ISO 13485 and FDA regulations.
- Technological Capability: Look for advanced facilities equipped with precision injection molding machines and cleanroom manufacturing.
Production Environment
- Cleanroom Manufacturing: Verify that the parts will be produced in ISO-certified cleanrooms to prevent contamination.
- Environmental Control: Ensure the production environment maintains controlled temperature, humidity, and particle levels.
Scalability and Cost
- Volume Requirements: Confirm the manufacturer can scale production to meet your demand, whether for low-volume prototypes or high-volume orders.
- Cost Transparency: Ensure clear communication of costs, including tooling, materials, and production, to avoid hidden charges.
Quality Assurance
- Inspection Processes: Ensure the manufacturer employs rigorous quality control measures, such as optical inspection and dimensional testing.
- Traceability: Choose a partner who provides full traceability for materials and processes.
- Regulatory Documentation: Confirm that the manufacturer offers comprehensive documentation to support regulatory submissions.
When customizing high-quality medical plastic parts, focus on selecting biocompatible materials, ensuring precision in design, partnering with experienced manufacturers, verifying cleanroom production, evaluating scalability, and ensuring stringent quality control. These considerations will help ensure that the customized parts meet the highest standards of safety, performance, and regulatory compliance.
FAQs about High Quality Medical Plastic Parts
When selecting the best medical grade plastic for a specific application, it is important to consider the material’s properties and how they align with the requirements of the medical device. The best medical grade plastic typically needs to meet rigorous biocompatibility, durability, and regulatory standards to ensure safety and performance. Some of the most commonly used medical-grade plastics include:
Polycarbonate (PC): Known for its high impact resistance, transparency, and ability to withstand sterilization, polycarbonate is frequently used in devices like surgical instruments, IV components, and diagnostic equipment.
Polyethylene (PE): This material is widely used due to its flexibility, chemical resistance, and ease of molding. It is commonly found in tubing, catheters, and prosthetic components.
Polypropylene (PP): Polypropylene is valued for its chemical resistance, low density, and stability during sterilization. It is often used in disposable medical devices such as syringes and specimen containers.
Polyetheretherketone (PEEK): This high-performance plastic is known for its strength, chemical resistance, and biocompatibility, making it ideal for implantable devices like spinal implants and joint replacements.
The best medical-grade plastic is chosen based on the specific needs of the device, including factors like mechanical strength, transparency, resistance to sterilization, and biocompatibility.
Medical grade plastic refers to plastics that meet strict standards for use in medical applications, ensuring they are safe, durable, and capable of withstanding the demands of healthcare environments. These plastics are specially formulated to be biocompatible, meaning they do not cause harmful reactions when in contact with the human body. While the term “medical grade plastic” is commonly used, several specific types of medical plastics are categorized based on their properties and intended use.
Some of the most common medical grade plastics include:
Medical-Grade Polycarbonate (PC): Known for its clarity, impact resistance, and ability to be sterilized, polycarbonate is often used for medical devices that require both strength and transparency.
Medical-Grade Polypropylene (PP): This plastic is often used in disposable devices due to its excellent chemical resistance and ability to withstand high temperatures without degrading.
Medical-Grade Silicone: Frequently used in medical applications that require flexibility, such as tubing, seals, and implants, silicone is known for its biocompatibility and resistance to extreme temperatures.
Medical-Grade Nylon: Used for surgical instruments, syringes, and other medical tools, nylon is valued for its strength, wear resistance, and ability to endure harsh sterilization processes.
In general, the term “medical grade” refers to any plastic that has been tested and certified to meet regulatory standards such as ISO 10993 for biocompatibility, ensuring that the material is safe for use in direct or indirect contact with the human body.
Hospitals use a variety of high-quality medical plastics to create durable, sterile, and biocompatible parts. Common plastics include polycarbonate (PC) for surgical instruments and diagnostic devices, polypropylene (PP) for syringes and containers, and polyethylene (PE) for tubing and medical storage solutions. Polyvinyl chloride (PVC) is widely used for flexible medical bags and tubing, while acrylonitrile butadiene styrene (ABS) is employed in medical device housings. These plastics are chosen for their resistance to chemicals, sterilization methods, and mechanical stress. High-quality medical plastics must meet regulatory standards to ensure they are safe for patient use. Their versatility makes them indispensable for applications like implants, surgical tools, and diagnostic equipment, where precision and reliability are paramount.
Medical-grade polymers are specialized plastics designed for healthcare applications, meeting stringent safety, biocompatibility, and regulatory standards. These materials include polycarbonate (PC), polyethylene (PE), polypropylene (PP), and silicone elastomers. They are used to manufacture high-quality medical plastic parts such as syringes, implants, and surgical instruments. Medical-grade polymers undergo rigorous testing for biocompatibility (ISO 10993) to ensure they do not cause adverse biological reactions. They are also resistant to sterilization methods like autoclaving, chemical cleaning, and gamma radiation. The polymers’ durability, lightweight nature, and ability to be molded into complex shapes make them ideal for high-precision medical components, ensuring safety and effectiveness in critical healthcare applications.
High-density polyethylene (HDPE) is a versatile, durable plastic widely used in medical applications due to its strength, chemical resistance, and biocompatibility. HDPE is a type of polyethylene characterized by a high strength-to-density ratio, making it suitable for producing medical-grade containers, tubing, and protective barriers. It is resistant to moisture, chemicals, and impacts, which makes it ideal for medical storage solutions like specimen containers and sharps disposal bins. HDPE is lightweight, easy to sterilize, and can be processed through injection molding, extrusion, or blow molding. Its use in high-quality medical plastic parts ensures durability and compliance with safety standards for patient care.
Yes, medical-grade plastics are specifically engineered to be safe for healthcare use. These plastics undergo stringent testing for biocompatibility, ensuring they do not cause allergic reactions, toxicity, or irritation when in contact with patients. They are designed to meet regulatory requirements, such as ISO 10993 for biological evaluation and FDA guidelines for medical devices. Medical-grade plastics, including polycarbonate (PC), polypropylene (PP), and polyethylene (PE), are used in applications like syringes, surgical instruments, and implants. Their resistance to sterilization processes, durability, and precision in manufacturing ensure they maintain safety and reliability in critical medical environments.
Contact our professional team now for a same-day quote and risk-free project evaluation. Benefit from ISO 8 cleanrooms, advanced machines, and 12-hour fast response in medical injection molding.