Injection molding medical devices is a pivotal process transforming the healthcare industry. This advanced manufacturing technique allows the production of high-quality, precise, and reliable medical components, ranging from syringes to complex surgical instruments. The ability to create intricate designs with tight tolerances ensures these devices meet stringent medical standards, facilitated by precision mold medical techniques that guarantee accuracy and consistency in each part.
The process is highly cost-efficient, making it suitable for large-scale production while minimizing material waste. Compliance with FDA regulations is another critical aspect, ensuring the safety and reliability of the medical devices produced. Whether for disposable products or long-term implants, injection molding medical devices delivers durability, sterility, and consistency, making it an indispensable solution in modern healthcare manufacturing. Injection molding medical devices uses medical-grade materials to create precise, sterile components for equipment, tools, and diagnostic devices.
What Is Injection Molding Medical Devices?
Medical injection molding devices is a specialized manufacturing process that shapes medical-grade plastics into precise, functional components. This method involves heating plastic materials, such as thermoplastics or silicone, to a molten state and injecting them into a custom-designed mold. Once cooled and solidified, the material takes the exact shape of the mold, resulting in highly accurate and detailed medical parts.
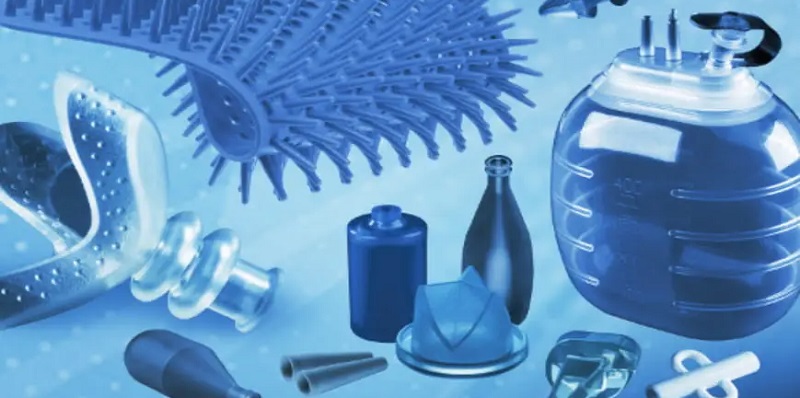
Features of Injection Molding Medical Devices
Injection molding medical devices stands out due to its unique features:
- Durability: Components produced are robust and long-lasting, essential for both single-use and reusable devices.
- Sterility: Materials and processes support strict hygienic requirements, including cleanroom production.
- Customization: Allows the creation of complex geometries tailored to specific medical applications.
- Mass Production Efficiency: Ideal for high-volume manufacturing with consistent quality across batches.
Examples of Injection Molding Medical Devices
Injection molding enables the production of a variety of medical devices used in healthcare settings:
- Syringes and needle hubs.
- Catheters and multi-lumen tubing.
- Surgical tools such as scalpels and forceps.
- Implants like pacemaker components and joint replacements.
This process provides a reliable, scalable, and cost-effective solution for producing medical devices, meeting both functional and regulatory standards.
Types of Injection Molding Medical Devices Processes
Injection molding medical devices involves various specialized processes, each suited to different medical applications. The choice of method depends on factors such as the material requirements, design complexity, and functionality needed for the medical device. Below are the key processes used in the production of medical devices through injection molding.
Plastic Injection Molding
Plastic injection molding is the most common and versatile process used in the manufacturing of medical devices. The process involves heating medical-grade plastic to a molten state and injecting it into a precisely designed mold. Once cooled, the plastic solidifies into the desired shape, ensuring high accuracy and durability.
Applications of Plastic Injection Molding in Medical Devices:
- Test tubes: Used for sample collection and laboratory analysis.
- Petri dishes: Commonly used in laboratories for growing cultures and samples.
- Blood bags: Designed for safe and efficient storage and transport of blood.
- Syringes and Needle Hubs: Widely used in injections and intravenous therapies.
Insert Molding
Insert molding is a technique where metal parts or other components are inserted into a mold before the plastic is injected. The molten plastic then encapsulates the inserted parts, creating a single, integrated component. This process is particularly useful for creating medical devices that require both metal and plastic components for functionality and strength.
Applications of Insert Molding in Medical Devices:
- Connectors: Used for medical equipment requiring secure connections.
- EKG Leads: Essential for heart monitoring equipment.
- Needles: Commonly used in various types of syringes and injection systems.
- Surgical Tools: Devices that require both a plastic handle and metal blade or tip.
Overmolding
Overmolding involves applying one material over another to create a multi-layered, functional component. This process is ideal for medical devices that require enhanced ergonomics, strength, or a combination of properties such as softness on the outside with rigidity inside. Overmolding improves the performance and user experience of medical devices.
Applications of Overmolding in Medical Devices:
- Ergonomic Grips: For surgical tools, making them more comfortable and easy to use.
- Multi-layer Catheters: Offers added flexibility, durability, and resistance to kinks.
- Handlebar Covers: On medical devices, providing a soft, cushioned grip for comfort and control.
- Drug Delivery Systems: Where soft, flexible outer layers are required for patient comfort.
Liquid Silicone Injection Molding
Liquid silicone injection molding (LSR) is used to create soft, flexible, and durable medical devices. In this process, liquid silicone rubber is injected into molds and then cured to form stable, flexible parts. Liquid silicone molding for medical devices is particularly beneficial for creating components that require high precision, flexibility, and biocompatibility, making it essential for applications in healthcare where safety and performance are critical.
Applications of Liquid Silicone Injection Molding in Medical Devices:
- Seals and Gaskets: For preventing leaks and ensuring sterility in medical devices.
- Tubing: Used in various types of medical equipment requiring flexibility and strength.
- Catheters: Silicone’s flexibility makes it ideal for creating catheters used in various medical procedures.
- Valves: In devices where precise, flexible movement is required for fluid control.
Thin Wall Molding
Thin wall molding focuses on creating device walls thinner than 1mm, balancing structural integrity and patient comfort. Materials like LCP, polypropylene, nylon, silicone, and metals are used, depending on the application. This technique is common in wearable devices, micro-surgical tools, and invasive equipment such as catheter ablation tools and endoscopes.
Gas-Assisted Injection Molding
Gas-assisted injection molding addresses sink marks caused by uneven cooling in traditional molding. By introducing nitrogen gas through channels, this method hollows thicker sections and applies pressure to ensure smooth, structurally sound parts without visual blemishes. It is ideal for creating complex components but is less suitable for designs with sharp corners.
3D Printing
While not injection molding, 3D printing supports the process by producing prototypes for testing and, in some cases, creating molds from plastic or metal. Though current technology lacks the precision for narrow tolerances, 3D-printed molds are useful for certain applications in medical device manufacturing.
Metal Injection Molding (MIM)
MIM is used for small medical parts requiring strength and flexibility. A metal powder is combined with a plastic binder to form feedstock, injected into molds, and debound through various processes, leaving nearly 100% dense metal components. This technique is ideal for parts demanding high maneuverability and mechanical properties.
Each of these medical injection molding processes plays a crucial role in the manufacturing of reliable, high-quality medical devices that meet the strict standards of the healthcare industry.
Materials Used in Injection Molding Medical Devices
The selection of materials for injection molding medical devices is critical to ensuring that the final products meet the strict regulatory standards, safety requirements, and performance expectations of the healthcare industry. Various materials offer distinct benefits, allowing manufacturers to choose the most appropriate one based on the device’s function, durability, and environmental considerations. Below are some of the most commonly used materials in injection molding medical devices.
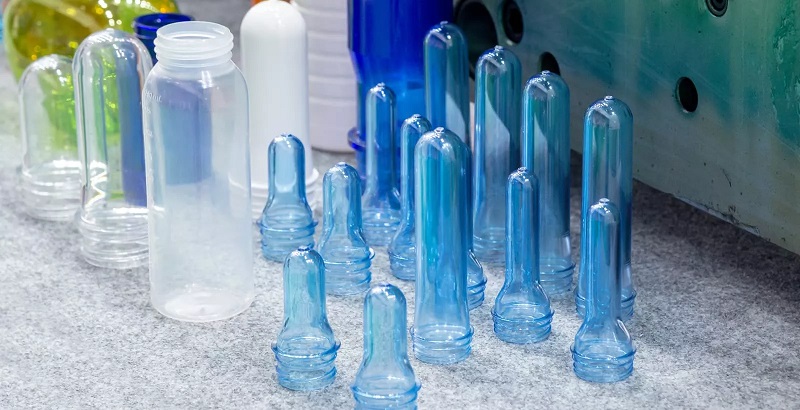
PEEK (Polyetheretherketone)
PEEK is a high-performance thermoplastic known for its exceptional strength, chemical resistance, and ability to withstand high temperatures. It is often used in medical devices that require high mechanical strength and resistance to harsh environments, making it an ideal material for implants and surgical instruments.
Benefits of PEEK in Medical Applications:
- Biocompatibility: Safe for implantation in the human body.
- Thermal Stability: Can endure high temperatures during sterilization processes.
- Chemical Resistance: Resists degradation from chemicals, bodily fluids, and other harsh substances.
- High Strength: Suitable for load-bearing implants such as spinal fusion devices and dental implants.
Polyethylene (PE)
Polyethylene is one of the most widely used materials in injection molding medical devices due to its versatility and durability. It is particularly well-suited for creating flexible and impact-resistant parts such as containers, tubing, and connectors. Polyethylene’s low cost also makes it ideal for disposable medical devices.
Benefits of Polyethylene in Medical Applications:
- Durability: Resistant to impact, making it suitable for a variety of medical applications.
- Low Friction: Ideal for devices requiring smooth, easy movement.
- Chemical Resistance: Resists corrosion and degradation from bodily fluids and medications.
- Flexibility: Offers great flexibility for items such as tubing and catheter components.
Polycarbonate (PC)
Polycarbonate is a transparent, high-impact plastic that is frequently used for medical devices that require clarity and strength. It is commonly used in devices such as oxygenators, masks, and protective covers. Polycarbonate’s transparency makes it useful in applications where visibility of the contents or inner workings of the device is necessary.
Benefits of Polycarbonate in Medical Applications:
- Transparency: Allows for easy visualization of fluids or substances inside devices like oxygenators.
- Impact Resistance: Highly resistant to shattering and breakage, providing strength and durability.
- Heat Resistance: Can withstand the heat of sterilization processes.
- High Dimensional Stability: Maintains structural integrity during use.
Silicone
Silicone is a highly flexible, biocompatible material that is often used in medical devices requiring a high degree of flexibility and comfort, such as catheters, seals, and gaskets. Medical grade silicone for molding is specially designed to meet the stringent requirements of medical applications, ensuring that components are safe, reliable, and durable. Silicone is also known for its ability to withstand extreme temperatures and its resistance to chemical breakdown, making it ideal for medical applications requiring long-term durability and safety.
Benefits of Silicone in Medical Applications:
- Biocompatibility: Perfect for medical implants and devices in direct contact with human tissue.
- Flexibility: Its softness and pliability make it ideal for applications requiring comfort, such as catheters and seals.
- Temperature Resistance: Suitable for devices that must endure both high and low-temperature extremes.
- Chemical Inertness: Does not react with bodily fluids or medications.
Polystyrene (PS)
Polystyrene is a low-cost, versatile plastic often used for medical devices that require clarity, such as diagnostic equipment and laboratory items. It is commonly used in the production of petri dishes, culture trays, and diagnostic parts. While it is not as durable as some other materials, its transparency and ease of molding make it a popular choice for disposable medical items.
Benefits of Polystyrene in Medical Applications:
- Cost-Effective: A low-cost material, ideal for disposable items like petri dishes and culture trays.
- Clarity: Transparent nature allows for easy inspection of contents, useful in diagnostic and laboratory devices.
- Ease of Molding: Can be easily shaped into complex forms for medical applications.
- Rigid Structure: Provides structural stability for items that don’t require high impact resistance.
The materials used in injection molding medical devices are chosen carefully to meet specific performance, regulatory, and safety requirements. Each material has unique benefits that make it suited for particular medical applications, whether for disposable items, implants, or surgical instruments. Choosing the right material is essential to ensuring that the final product performs reliably under medical conditions while adhering to strict health and safety standards.
How to Choose the Right Materials for Injection Molding Medical Devices
Selecting the appropriate material for injection molding medical devices is crucial to ensure performance, safety, and functionality. Here’s how to make the right choice:
- Durability and Strength
Medical devices must be made from materials that resist breaking and shattering to avoid inconveniences or risks during critical moments. Opt for materials like high-strength polymers that align with the device’s specific durability requirements. - Operating Conditions
Consider the environment where the device will be used. For parts subjected to high temperatures or repeated sterilization, choose heat-resistant materials like polypropylene. For parts requiring flexibility and abrasion resistance, polycarbonate is ideal. - Ease of Use
Focus on the end-user experience. Lightweight, ergonomic materials are essential for tools like surgical instruments, ensuring functionality and comfort without compromising sterilization requirements.
By evaluating these factors, you can select the most suitable materials to meet the unique demands of medical device applications.
Injection Molding Medical Devices: Injection Molding PET Plastic Medical Devices
Injection molding medical devices using polyethylene terephthalate (PET) is a highly effective method for producing durable and clear medical components. PET, a versatile thermoplastic polymer, is widely used in various industries, but its unique properties make it especially well-suited for medical applications. The process involves melting PET resin and injecting it into a custom mold under high pressure, allowing the material to take the exact shape of the mold once cooled and solidified. This method ensures high precision, durability, and clarity in the production of medical devices.
Applications of Injection Molding PET Plastic Medical Devices
PET is commonly used in the production of medical devices that require transparency, strength, and sterility. Some of the most common applications include:
- Syringe Barrels: PET is used for producing clear and durable syringe barrels, allowing easy visualization of the fluid inside.
- Fluid Containers: PET’s chemical resistance and clarity make it ideal for producing containers that store fluids for medical treatments.
- Diagnostic Vials: PET is also used in the creation of vials used for blood samples, urine tests, and other diagnostic purposes, providing a sterile and reliable container for samples.
- Medical Packaging: PET is used in the packaging of sterile medical components, offering clarity and durability while ensuring the safety and integrity of the contents.
Advantages of Injection Molding PET Plastic Medical Devices
Using PET for injection molding medical devices offers numerous benefits, making it an excellent choice for the production of disposable medical products. The key advantages include:
- Biocompatibility: PET is biocompatible, meaning it is safe for use in medical applications where it may come into contact with bodily fluids or tissues. This makes it ideal for products like syringes and diagnostic vials.
- Chemical Resistance: PET is resistant to a wide range of chemicals, including bodily fluids, sterilizing agents, and pharmaceutical compounds. This makes it particularly suitable for fluid storage containers and products that need to withstand exposure to harsh substances.
- Recyclability: PET is highly recyclable, contributing to environmentally sustainable practices in the medical device industry. It can be reused to produce new medical components, reducing waste and the carbon footprint.
- Transparency: PET’s excellent clarity makes it ideal for medical devices like syringes and diagnostic vials, where it is essential to see the contents of the container. This clarity ensures that healthcare professionals can easily monitor fluid levels, identify substances, and perform accurate medical procedures.
- Durability: PET’s strength and durability make it suitable for medical devices that must endure handling, transportation, and sterilization without compromising their integrity.
The use of PET in injection molding for medical devices combines the benefits of biocompatibility, chemical resistance, and recyclability, making it an optimal material for producing a wide range of medical products, particularly those that are disposable or require clarity and strength.
Benefits of Injection Molding Medical Devices
Injection molding is a highly effective manufacturing process for medical devices, offering numerous advantages that contribute to high-quality, cost-efficient production. Whether producing a small batch of prototypes or large-scale runs of disposable products, medical molded devices ensures compliance with regulatory standards, precision, and flexibility. Below are the key benefits of using injection molding for medical device manufacturing.
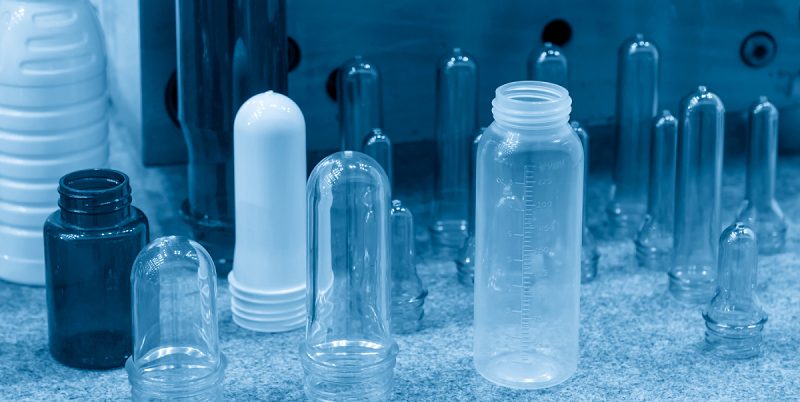
Regulatory Compliance
One of the most important advantages of injection molding medical devices is its ability to meet stringent regulatory standards, particularly those set by the U.S. Food and Drug Administration (FDA). The medical device industry is governed by strict regulations to ensure patient safety, and injection molding is highly effective in ensuring compliance with these guidelines.
- FDA Compliance: Injection molding medical devices allows manufacturers to meet FDA requirements for medical-grade materials, cleanroom standards, and manufacturing processes.
- Sterility Assurance: The molding process, along with subsequent sterilization, ensures that devices like syringes and catheters are produced in a sterile environment.
- Quality Control: Advanced quality control measures, such as inspection systems and batch traceability, are easily integrated into the injection molding process to ensure compliance with regulatory standards.
- Traceability: Injection molding provides the ability to trace the entire production process, which is crucial for meeting industry standards and providing accountability in case of product recalls.
Cost Efficiency
Cost efficiency is a significant benefit of molded medical devices, especially when it comes to reducing material waste and minimizing labor costs. The process is highly automated, which allows for faster production times and lower costs per unit.
- Reduced Material Waste: Injection molding uses precise amounts of material, which minimizes waste. This is particularly important when working with expensive medical-grade plastics.
- Labor Cost Reduction: The automation of injection molding systems reduces the need for manual labor, lowering overall labor costs while maintaining consistent product quality.
- Energy Efficiency: The molding process is energy-efficient compared to other manufacturing methods, contributing to lower overall production costs.
- Low Cost for High Volumes: Once the mold is created, the cost per unit decreases significantly with higher production volumes, making injection molding ideal for mass production of disposable medical devices like syringes and vials.
High Precision
Injection molding medical devices ensures high precision and repeatability, which is crucial for creating medical components that must meet strict specifications. The process can achieve tight tolerances and fine details that are necessary for parts used in critical medical applications.
- Tight Tolerances: Injection molding can achieve tolerances as tight as ±0.001 inches, ensuring that medical devices are produced with consistent dimensions.
- Complex Geometries: The process allows for the creation of intricate, complex shapes that are often required for medical devices, such as multi-lumen catheters or surgical tools.
- Consistent Quality: The automated nature of injection molding ensures that each part is identical, maintaining consistency and reliability across large production runs.
- Reduced Risk of Defects: The precision of the molding process reduces the risk of defects, which is critical when producing devices that must function perfectly for patient safety.
Scalability
Injection molding medical devices is highly scalable, making it suitable for both small-scale production runs and large-scale manufacturing. This scalability is a key advantage for medical device manufacturers who may need to transition from prototyping to full-scale production without significant changes in their production processes.
- Prototyping and Low-Volume Production: Injection molding can be used for prototyping medical devices, allowing manufacturers to test designs and functionality before committing to mass production.
- Mass Production: Once the design is finalized, wholesale medical injection molding allows for seamless scaling to mass production, enabling the manufacture of millions of units without compromising quality. This process is ideal for large-scale runs of medical devices, ensuring efficiency and consistency while maintaining the high standards required in the healthcare industry.
- Flexibility for Design Changes: Injection molding allows for easy adjustments to the mold design, which makes it easier to accommodate changes in product specifications or new product features.
- Faster Time to Market: With the ability to quickly transition from prototype to full-scale production, manufacturers can get their medical devices to market faster, meeting urgent demands.
Wide Range of Compatible Materials
Compared to other manufacturing processes, injection molding has one of the widest selection of materials. While some materials are not suitable for use in the medical industry, there are still many materials that meet the various requirements and regulations of the industry.
Excellent Strength, Durability and Mechanical Properties
Injection molded parts are very strong and durable. They can also withstand vibrations, shocks and harsh environments. Some are also heat-resistant, which means they can be easily sterilized repeatedly through an autoclave without any damage.
Injection molding medical devices offers significant benefits, including regulatory compliance, cost efficiency, high precision, and scalability. These advantages make it the ideal choice for producing a wide range of medical products, from high-precision surgical instruments to cost-effective disposable devices.
Injection Molding Medical Devices: Injection Molding Specialists for Medical Devices
Injection molding specialists play an essential role in producing high-quality medical devices, combining technical expertise with state-of-the-art technology. These experts manage every aspect of the injection molding process to ensure precision, reliability, and compliance with strict regulatory standards. Below, we explore the responsibilities, key services, and advantages of working with injection molding specialists for medical devices.
Role of Injection Molding Specialists for Medical Devices
Specialists in injection molding medical devices oversee the entire production process, from concept to delivery. Their expertise ensures that all aspects of manufacturing align with the unique requirements of the medical industry.
- Ensuring Precision: Specialists leverage advanced machinery and software to create accurate molds and maintain tight tolerances in the final products.
- Regulatory Compliance: With in-depth knowledge of FDA and other regulatory standards, they ensure that all materials and processes meet required safety and quality guidelines.
- Optimizing Efficiency: Specialists streamline workflows to reduce production time and costs without compromising quality.
- Risk Mitigation: By applying rigorous quality control measures, they reduce the likelihood of defects and ensure consistent output.
Key Services Provided by Injection Molding Specialists
Injection molding specialists for medical devices offer a range of services tailored to meet the specific needs of medical device manufacturers. These services include:
- Custom Mold Design and Tooling
specialists use advanced CAD/CAM software to create molds that meet the precise specifications of medical devices. The medical mold design process involves developing durable, high-precision molds capable of withstanding repeated production cycles, ensuring consistent quality and reliability for critical medical components. This attention to detail is crucial for meeting regulatory standards and ensuring the functionality of medical devices. - Prototyping and Validation Processes
Specialists create prototypes for testing and validation, allowing manufacturers to evaluate the functionality and design of medical devices before full-scale production. This step minimizes risks and ensures product performance. - Cleanroom Production Capabilities
To meet sterility requirements, many specialists operate in ISO-certified cleanrooms. This ensures that devices such as syringes, catheters, and surgical tools are manufactured in contamination-free environments. - Material Selection Guidance
Specialists help manufacturers choose the best medical-grade materials, such as PEEK, silicone, or polycarbonate, to meet specific application needs.
Why Choose Injection Molding Specialists?
Collaborating with injection molding specialists for medical devices offers significant advantages, including expertise, efficiency, and innovation. These professionals bring the following benefits to medical device projects:
- Knowledge of Materials: Specialists understand the unique properties of medical-grade plastics and help select the most suitable material for durability, biocompatibility, and performance.
- Expertise in Regulatory Standards: Their familiarity with FDA, ISO, and other global standards ensures compliance throughout the production process.
- Access to Advanced Technologies: Specialists utilize cutting-edge technologies, such as 3D printing for rapid prototyping and robotics for precision manufacturing.
- Comprehensive Project Management: They manage all stages of production, from mold design and testing to mass production and delivery, ensuring efficiency and quality at every step.
Injection molding specialists are indispensable for ensuring the success of medical device manufacturing, combining technical knowledge with a commitment to delivering reliable and compliant products.
Compliance Requirements for Injection Molding Medical Devices
Ensuring compliance is a critical aspect of manufacturing injection molding medical devices, as the medical industry is highly regulated. Adhering to these standards guarantees safety, effectiveness, and reliability in medical applications. Key compliance factors include:
FDA Regulations
The FDA mandates strict standards for the cleanliness and sterility of medical devices, including implantable devices, instruments, and components. Materials used in injection molding must meet these criteria, ensuring they are safe for medical use. Additionally, the injection molding process and facilities must often pass FDA audits to achieve medical-grade approval.
ISO Certification
Compliance with ISO standards, particularly ISO 13485:2016, is essential for medical device manufacturing. This certification ensures that quality management systems meet medical industry requirements. Depending on the device, additional standards such as ISO 10993 for biocompatibility or compliance with Class I, II, or III requirements may be necessary.
By adhering to these regulations, manufacturers can ensure that their injection-molded medical devices meet the stringent demands of the healthcare sector.
Why FUJIU Medical Injection Mold is a Top Choice for Injection Molding Medical Devices
FUJIU Medical Injection Mold stands out as a leading manufacturer in injection molding medical devices due to its comprehensive solutions, advanced technology, and commitment to quality.
- Full-Service Solutions
From product design and development to in-house tooling and secondary operations, FUJIU provides end-to-end support under one roof, streamlining the manufacturing process. - Speed and Flexibility
Their agile supply chain adapts to changing demands, ensuring faster delivery cycles and reduced time to market, ideal for dynamic medical industry requirements. - Uncompromising Quality
ISO-certified production ensures adherence to the highest standards, with rigorous inspections guaranteeing reliable and safe medical components. - Advanced Technology
FUJIU employs cutting-edge equipment and ISO 8 cleanroom facilities for precision and reliability in medical device manufacturing. - Global Expertise
With operations in 10 regions and expertise in procurement, logistics, and quality control, FUJIU ensures smooth project execution on a global scale. - Cost-Effective Solutions
Their DFM (Design for Manufacturing) strategies and value-driven supply chain reduce production costs without compromising quality.
For manufacturers seeking precision, reliability, and efficiency, FUJIU Medical Injection Mold offers unparalleled expertise and solutions in the medical device industry.
FAQs about Injection Molding Medical Devices
Injection molding is an essential manufacturing process for producing a wide range of high-precision products, especially in the medical industry. This technique involves melting plastic materials and injecting them into molds to create detailed and durable components. In medical device manufacturing, injection molding is used to produce various items, including:
Syringes and Needle Components: Syringe barrels, plunger rods, and needle hubs are commonly made using injection molding. The high precision required for these items ensures safe and reliable use in healthcare settings.
Catheters: Both single-lumen and multi-lumen catheters, used in medical procedures, are manufactured through injection molding. The process allows for the integration of different materials for flexibility and strength.
Surgical Instruments: Components like handles, grips, and casings for surgical tools are produced using injection molding, providing the necessary durability and sterility.
Diagnostic and Lab Equipment: Items such as petri dishes, test tubes, and diagnostic vials are often molded using medical-grade plastics. The precision of the molding process ensures that these products meet rigorous standards for accuracy and safety.
Implants and Prosthetics: In some cases, medical implants such as joint replacements and dental devices are also produced using injection molding techniques, utilizing biocompatible materials for patient safety.
The versatility and precision of injection molding make it an ideal solution for creating complex and high-quality medical devices.
The medical injection molding market is a rapidly growing sector due to the increasing demand for high-quality, precise, and cost-effective medical devices. The market is driven by several factors, including technological advancements, the aging population, and a rising global healthcare expenditure. Here’s an overview of key market trends:
Growing Demand for Disposable Medical Devices: Disposable products, such as syringes, catheters, and diagnostic tools, account for a significant portion of the medical injection molding market. As healthcare providers focus on reducing cross-contamination risks, the demand for single-use, sterile medical devices has increased.
Aging Population: The aging population worldwide has led to an increase in the prevalence of chronic diseases, which in turn drives demand for medical devices like joint implants, pacemakers, and diagnostic equipment. Injection molding is a cost-effective method to produce these devices in large volumes.
Regulatory Compliance and Innovation: Stringent regulations like those from the FDA and ISO push the industry toward higher standards for medical device safety and performance. As a result, manufacturers are turning to injection molding specialists who can meet these compliance requirements while ensuring consistent product quality.
Cost-Effectiveness and Scalability: Medical injection molding is an attractive solution for manufacturers looking to reduce costs. The automation of the injection molding process minimizes labor costs, while the ability to produce high volumes of parts with consistent quality makes it ideal for large-scale manufacturing.
With these factors driving growth, the medical injection molding market is expected to continue expanding in the coming years. Manufacturers are constantly innovating to meet the needs of the healthcare industry, and injection molding remains a vital technology for producing high-precision, cost-effective medical devices.
Medical injection molding is a process used to produce high-precision components for medical devices. It involves injecting molten medical-grade plastic or silicone into a custom-designed mold under high pressure. This process is specifically tailored for medical applications, adhering to strict standards for biocompatibility, hygiene, and safety. Commonly produced items include surgical instruments, implantable devices, and diagnostic components. The method ensures consistency, tight tolerances, and the ability to scale production, which are critical for medical applications.
Injection molding is widely used to create a range of medical products. Examples include syringes, catheter tips, diagnostic device housings, drug delivery system components (e.g., insulin pens), surgical instrument grips, and implantable devices. These products require precise manufacturing to meet stringent regulatory standards and ensure safety and reliability in medical settings. The process allows for the production of both single-use and reusable medical parts, accommodating a variety of material and design needs.
While the largest injection molding companies may vary depending on specific criteria, some leading companies involved in medical injection molding include Medtronic, Johnson & Johnson, and Flex. These companies utilize extensive injection molding operations to produce components for their medical devices. On a global scale, injection molding service providers like Nypro (a Jabil subsidiary) specialize in medical manufacturing, making them significant players in the industry.
The cost of an injection mold for medical devices ranges widely depending on complexity, size, material, and production requirements. Simple molds may cost between $5,000 and $20,000, while complex, high-precision molds for medical applications can reach $50,000 to $500,000 or more. The higher costs in medical injection molding are due to the need for cleanroom compatibility, strict regulatory compliance, and material considerations.
Injection molding is expensive due to several factors:
Tooling Costs: Precision-engineered molds require significant investment.
Regulatory Compliance: Medical-grade products must meet strict standards.
Material Costs: Medical-grade plastics and silicones are more costly.
Operational Costs: Cleanroom production environments and quality assurance increase expenses. These factors combine to ensure high-quality, consistent production suitable for critical medical applications.
Alternatives to injection molding include:
3D Printing: Ideal for prototyping or low-volume production, offering design flexibility.
Compression Molding: Suitable for simpler, larger parts.
Blow Molding: Best for hollow medical devices like containers. Each alternative has specific applications and limitations. For large-scale production of high-precision medical parts, injection molding is often superior, but alternatives like 3D printing are gaining popularity for rapid development.
An injection molding job involves operating machines that produce plastic or silicone parts by injecting molten material into molds. In medical manufacturing, this role includes maintaining cleanroom conditions, monitoring equipment, and ensuring quality control. Employees may be responsible for setting up machines, troubleshooting issues, and performing inspections to ensure parts meet regulatory standards for medical use.
The primary purpose of injection molding in medical device production is to create high-precision, high-quality components at scale. The process allows manufacturers to produce complex shapes with tight tolerances, ensuring reliability and safety. It supports the use of biocompatible materials, essential for medical applications, while enabling cost-effective mass production of both single-use and reusable medical parts.
Contact our professional team now for a same-day quote and risk-free project evaluation. Benefit from ISO 8 cleanrooms, advanced machines, and 12-hour fast response in medical injection molding.