Injection molding is a widely used manufacturing process in which melted plastic is injected into a mold to create precise, durable parts. This process is essential in the injection molding medical industry, where high accuracy and the use of FDA-approved materials are crucial for producing medical-grade components. The ability to consistently create complex, sterile, and reliable parts at scale makes injection molding an ideal solution for medical device manufacturers. Key players in the injection molding medical industry have contributed significantly to advancing medical molding technology. Their expertise ensures the production of high-quality components used in everything from surgical instruments to diagnostic tools, driving efficiency and safety in medical device manufacturing. The injection molding medical industry produces precise, durable devices using techniques like two-shot, blow, and insert molding for various applications.
Low-Volume to High-Volume Production Capabilities
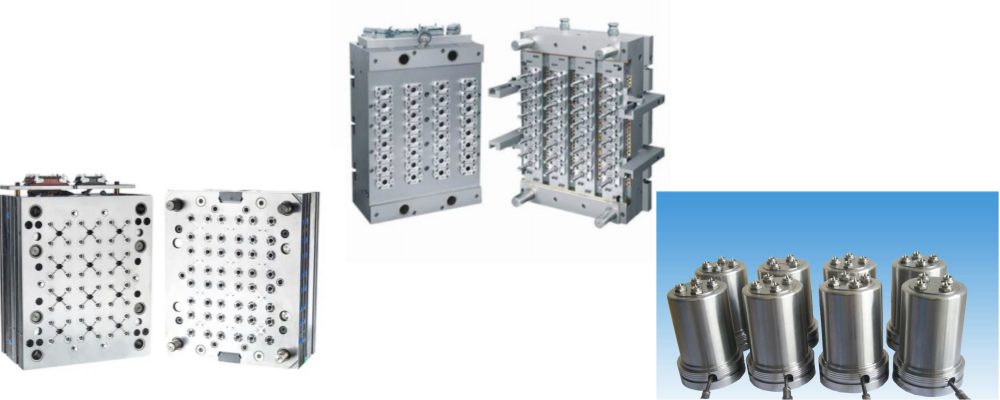
Attribute | Details |
---|---|
Shaping Mode | Plastic Injection Mould |
Product Types | Medical products (e.g., syringes, medical trash cans), custom silicone molds |
Mold Materials | High-quality steel options such as P20, S50CH13, NAK80, 718, S136, 2738, and 2316 ensure long-lasting durability. |
Material Compatibility | Supports diverse plastics including ABS, PA66, PC, ASA, TPU, POM, PS, PE, PVC, PP, PMMA, Acetal, and Acetron. |
Mold Life | Mold lifespans range from 30,000 shots to over 10,000,000 shots, depending on material and application. |
Tolerance | Ensures precision with tolerances ranging from ±0.01 mm to ±0.1 mm. |
Surface Treatment | Available treatments include polishing, etching, texturing, electroplating, painting, and logo engraving. |
Processing Methods | Advanced manufacturing techniques such as CNC milling, CNC lathe operations, drilling, and precision molding. |
Core Components | Incorporates critical components like bearings, motors, pumps, gears, PLCs, pressure vessels, and engines. |
Applications | Ideal for medical devices |
Certification and Compliance | Compatible with 2D/3D/CAD/DWG/STEP files; Non-disclosure agreements available for proprietary designs. |
MOQ (Minimum Order Quantity) | Flexible MOQ starting from 1 piece for prototypes or 10 pieces for bulk production. |
Delivery Time | Standard production delivery within 7-8 working days, with expedited options available. |
Product Features | - High durability with long mold life |
- Eco-friendly and efficient production methods | |
- Precision manufacturing for complex designs | |
- High adaptability for various industries and applications | |
- Fast prototype turnaround with sample production available | |
- OEM service accepted for customized product names, model numbers, and packaging | |
- Custom design options for unique shapes, sizes, and applications | |
- High productivity with consistent quality assurance | |
Inspection Standards | 100% quality inspection with strict adherence to precision requirements. |
What Is Injection Molding Medical Industry
Medical injection molding is a specialized process in the injection molding medical industry that involves melting medical-grade plastic resins and injecting them into a precisely designed mold. This method allows manufacturers to produce highly accurate, consistent, and complex parts that are essential for medical applications. Once the plastic has been injected into the mold, it is cooled and hardened to form the desired shape, creating parts that meet strict quality standards. Precision is critical in this process, as medical components often require tight tolerances to ensure their functionality and safety. Compliance with FDA and ISO standards is mandatory, as the parts produced must meet rigorous health and safety regulations, including sterility and durability.
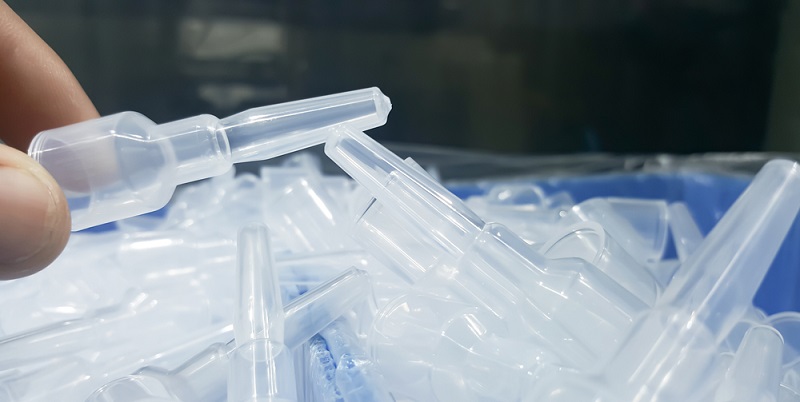
Key Materials Used in Medical Injection Molding
In the injection molding medical industry, a variety of materials are utilized to meet the specific requirements of medical devices. These include:
- PEEK (Polyetheretherketone): Known for its superior strength and high resistance to chemicals, heat, and radiation, PEEK is often used in surgical implants and other critical medical devices.
- Polypropylene (PP): Polypropylene is a versatile, lightweight material that is highly resistant to chemicals and is commonly used for medical components such as syringes, diagnostic devices, and containers.
- Polystyrene (PS): This material is known for its excellent impact resistance and dimensional stability, making it ideal for use in diagnostic tools like Petri dishes and test tubes.
- Silicone: Silicone is often used in medical applications that require flexibility and biocompatibility, such as catheters, seals, and tubing. Its ability to withstand sterilization and its non-reactive properties make it essential for many medical products.
- Polyethylene (PE): Polyethylene (PE) is a versatile, durable medical-grade plastic polymer composed of thousands of ethylene polymers, giving it impressive tensile strength and rigidity. PE is also highly compatible with biological tissues and can withstand harsh environmental conditions, including sterilization. Thanks to these properties, PE is widely used in the medical field for manufacturing joint prostheses, connectors, tubing, pharmaceutical containers, and more.
- Polycarbonate (PC): Polycarbonate (PC) is transparent and has excellent mechanical properties. It’s tough, flexible, and resistant to abrasion, breakage, and temperature. Polycarbonate is also highly compatible with bodily tissues, making it ideal for manufacturing various medical equipment, from clear masks to protective gear and oxygenators.
These materials offer the necessary performance and regulatory compliance required in the injection molding medical industry, ensuring that products meet the safety and performance standards required for medical use.
Key Considerations for Selecting Medical Injection Molding Materials
Selecting the right materials for medical injection molding is crucial to ensure the functionality, safety, and longevity of the final products. Below are the primary factors to consider:
Material Properties
- Strength and Durability: The material must meet the strength requirements of the intended application to avoid cracking or breaking during use. Toughness and long-term performance are critical, particularly for parts subject to mechanical stress.
- Flexibility: For applications like tubing and connectors, materials must offer flexibility without sacrificing durability.
- Transparency: In applications where visibility is necessary, such as diagnostic tools, materials should possess high optical clarity.
- Chemical and Temperature Resistance: Materials must withstand exposure to sterilization processes (e.g., autoclaving or chemical sterilization) and resist degradation when exposed to harsh chemicals, heat, or moisture.
Regulatory Compliance
- FDA Standards: Medical-grade plastics must meet FDA regulations for sterility, safety, and cleanliness to ensure they are suitable for healthcare use. Non-compliant materials are not permissible for medical applications.
- ISO Certification: Materials and manufacturing processes should comply with ISO standards, particularly ISO 13485 for medical devices and ISO 10993 for biocompatibility. Additional ISO certifications may apply depending on the device class (I, II, or III).
Sterility Requirements
- Sterilization Compatibility: Materials must maintain their properties after sterilization processes like gamma radiation, ethylene oxide (EtO) sterilization, or autoclaving.
- Antimicrobial Additives: Incorporating antimicrobial additives during the molding process can prevent microbial growth on the surface, reducing the need for frequent sterilization and extending the product’s lifespan.
Operational Conditions
- Environmental Tolerance: Materials must endure the specific operating environment, including exposure to vibrations, corrosive substances, or repeated stress, without degradation.
- User-Centric Design: Components like surgical instruments must be lightweight, ergonomic, and functional, while disposable products like drug delivery systems must balance durability with cost-effectiveness.
Manufacturing Compatibility
- Molding Method Compatibility: Different manufacturing techniques—such as injection molding, insert molding, overmolding, and micro molding—require specific material properties. It is crucial to select materials that are compatible with the chosen production method to avoid defects or inefficiencies during manufacturing.
By thoroughly evaluating these considerations, manufacturers can ensure the selection of materials that meet the functional, regulatory, and environmental requirements of medical injection molding applications.
Common Applications of Injection Molding Medical Industry
Medical Devices and Components
Injection molding plays a pivotal role in the injection molding medical industry by producing high-precision medical devices and components. Medical devices such as syringes, catheters, surgical instruments, and joint replacements are commonly manufactured using this process. The precision mold medical technology ensures that these devices meet strict tolerances, which is critical for their functionality in medical settings. For example, syringes must be produced with high accuracy to ensure the proper dosage of medication, while catheters require consistency in size and shape to avoid complications during procedures. Injection molding also ensures repeatability in mass production, meaning that each part is consistently manufactured to the same high standards. This level of precision and consistency is essential for ensuring the safety, reliability, and effectiveness of medical devices in patient care.
Diagnostic and Testing Equipment
In addition to medical devices, injection molding is also extensively used in the production of diagnostic and testing equipment. Components such as diagnostic testing kits, Petri dishes, and test tubes are produced using injection molding techniques that ensure high quality and precision. These items often require FDA-approved materials to meet safety standards and are typically manufactured in sterile environments to prevent contamination. The molding process allows for the creation of complex shapes and fine details necessary for diagnostic tools, ensuring they function effectively in critical applications. For example, Petri dishes and test tubes need to have precise dimensions to accurately hold and incubate samples, while diagnostic kits must maintain the integrity of the materials used to detect medical conditions. By adhering to strict quality controls, the injection molding medical industry ensures that these critical components meet the regulatory standards required for medical use.
Personal Protection Equipment (PPE)
Injection molding is also widely used in the production of personal protection equipment (PPE), which has become increasingly important in the healthcare industry, particularly in response to the COVID-19 pandemic. Items such as face shields, masks, and protective covers are made using injection molding techniques that ensure they are durable, comfortable, and provide adequate protection for medical staff and patients alike. The use of FDA-approved materials in the molding process guarantees that PPE components are safe and reliable for use in healthcare settings. Injection molding allows for the rapid production of these essential items at scale, ensuring that they meet both quality and regulatory standards. With the ability to produce parts quickly and efficiently, the injection molding medical industry has been instrumental in meeting the growing demand for protective gear in medical environments.
Injection Molding Medical Industry: Types of Injection Molding Used in Medical Manufacturing
Plastic (Regular) Injection Molding
Plastic injection molding involves melting plastic polymers at high temperatures to create sterile and contaminant-free medical equipment. By reshaping the plastics in aluminum or steel molds, manufacturers can produce precise and customized medical devices that meet the highest standards of hygiene.
Liquid Silicone Injection Molding
Liquid silicone injection molding involves heating silicone to a liquid state and then molding it into various shapes, making it a versatile solution for developing medical products. Silicone, a plastic polymer, is specifically designed to meet the needs of the medical industry. However, it’s important to note that silicone molds may not be as durable as aluminum or steel molds, making this technique more suitable for small quantities and initial prototyping stages.
Insert Molding
In the injection molding medical industry, insert molding is a highly effective process that combines metal and plastic components within the same mold to create a single, unified part. This technique is commonly used in the production of medical devices such as needles and surgical instruments. The insert molding process involves placing a metal part (such as a needle or metal screw) into a mold, where it is then surrounded by molten plastic. The plastic hardens, bonding seamlessly with the metal, forming a strong, durable part. This is especially useful in medical applications where components must exhibit both strength and flexibility. Insert molding ensures that the metal parts, which provide structural integrity, are securely integrated into the device, while the plastic parts contribute to functionality, ergonomics, and safety. This technique is ideal for complex medical devices that require a combination of materials to perform different functions in a single component, making it essential for a medical plastic components manufacturer.
Overmolding and Two-Shot Molding
Another important process in the injection molding medical industry is overmolding, which involves creating a polymer layer over an existing substrate, such as a metal or plastic part. This technique is often used to produce ergonomic, multi-material components that require a combination of hardness and flexibility. For example, surgical handles and drug delivery devices are commonly manufactured using overmolding. In the case of surgical handles, overmolding allows for the creation of soft, comfortable grips on the hard, durable base of the instrument. The resulting multi-material part offers improved performance and user comfort while maintaining the necessary strength for medical use. Multi component injection molding medical plays a crucial role in this process by enabling the production of complex, multi-material parts that are essential for high-performance medical devices. Another related technique, two-shot molding, involves injecting two different materials into the same mold in two separate stages, further enhancing the design and functionality of complex machining medical parts. This allows for even more intricate designs that provide both performance and aesthetic benefits in medical devices.
Micro Molding for Precision Components
Micro molding is a specialized technique within the injection molding medical industry, used to create tiny, intricate components that require the highest levels of precision. This process is essential for manufacturing small, complex parts that are commonly used in medical devices such as microfluidic devices and diagnostic tools. Micro molding allows manufacturers to produce parts with fine details, such as thin walls, intricate channels, and small-scale features that would be impossible to achieve with traditional molding techniques. These components are critical for devices used in advanced diagnostics, where even the smallest error could compromise performance. For example, microfluidic devices, which are used for analyzing small fluid samples, require precision-engineered parts to accurately control the flow of liquids at a microscopic scale. Micro molding ensures these components are made with the necessary accuracy and consistency to meet stringent medical standards.
The Advantages of Injection Molding Medical Industry
Cost-Effectiveness
One of the most significant advantages of injection molding in the medical industry is its cost-effectiveness, particularly in high-volume production. Once the initial mold is created, the cost per part decreases dramatically as the number of parts produced increases. This is because the process allows for mass production, where multiple parts are created simultaneously, optimizing both time and resources. Automated molding systems further enhance this advantage by reducing labor costs, increasing the speed of production, and minimizing human error. The automation ensures that the molding process is both efficient and consistent, which helps manufacturers maintain a competitive edge in the market. For those looking to enter this sector, a medical injection molding business for sale offers a pathway into an industry that balances innovation with high-volume, cost-effective production. As a result, injection molding plays a pivotal role in the production of cost-effective medical components, from syringes to surgical instruments, all while meeting the high standards required for medical-grade products.
Precision and Repeatability
In the injection molding medical industry, precision and repeatability are paramount, as even minor deviations in part dimensions can compromise the safety and functionality of medical devices. High precision is essential for producing components that need to fit together seamlessly or function within strict tolerances. Medical applications, such as catheters, diagnostic equipment, joint replacements, and those assembled by the medical device assembler, demand parts that are produced to exact specifications in every cycle. Injection molding ensures that each part is created with the same level of precision, thanks to the high repeatability of the process. This ability to meet tight tolerances guarantees consistent part quality, which is crucial for the reliability of medical devices. Additionally, the injection molding medical industry has developed advanced technologies and techniques to monitor and maintain the precision of each part produced, ensuring that the strictest standards of quality control are met.
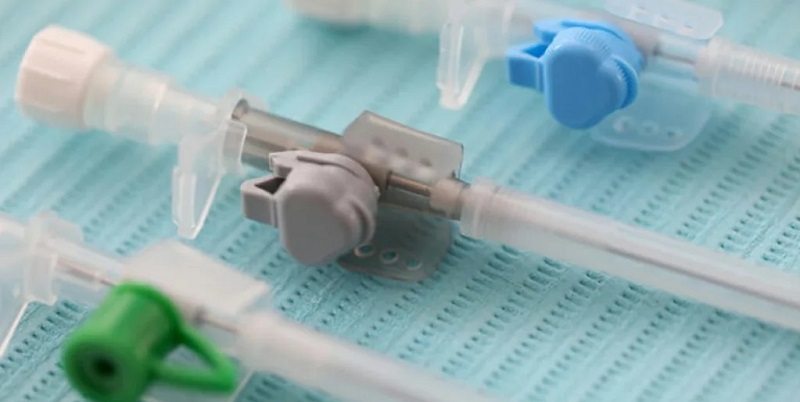
Compliance with Regulations
The injection molding medical industry operates within a highly regulated environment, where products must comply with stringent FDA and ISO standards. These regulations ensure that medical components are safe, clean, and sterile before they are used in patient care. Injection molding plays a key role in this process by enabling the production of components that meet these standards. The use of FDA-approved materials and adherence to specific manufacturing processes help ensure that the final product is safe for medical use. Furthermore, clean room injection molding operations are conducted in controlled environments that play a critical role in preventing contamination and ensuring sterility. These controlled environments are essential for maintaining the integrity of the manufacturing process, ensuring that medical products are free from harmful pathogens or particulate matter, which is crucial for patient safety.
Innovations in Injection Molding Medical Industry
Advancements in Materials and Technologies
The medical injection molding industry has witnessed significant advancements in both materials and technologies, enabling the production of increasingly complex and functional medical devices. OEM medical injection molding plays a crucial role in the use of biocompatible materials for implants and surgical devices. These materials are designed to interact safely with the human body, reducing the risk of adverse reactions. PEEK (Polyetheretherketone), for example, is a high-performance polymer used in medical implants due to its excellent mechanical properties, biocompatibility, and resistance to high temperatures. Similarly, medical-grade silicone is often used for devices like catheters and seals due to its flexibility, durability, and biocompatibility. As a result, the injection molding medical industry can now create implants, joint replacements, and surgical instruments that meet the highest standards of safety and performance.
Additionally, insert molding and overmolding have become key technologies for creating advanced, multi-functional medical parts. Insert molding combines metal or other materials with plastic components, allowing for the production of devices that require both strength and flexibility, such as surgical instruments or needles. Overmolding involves creating a second layer of material over an existing part, improving ergonomics and functionality. This technique is commonly used in products like surgical handles or drug delivery devices, where comfort, precision, and multi-material integration are essential. By incorporating these technologies, the injection molding medical industry is pushing the boundaries of what is possible in medical device manufacturing, enabling the creation of more intricate, high-performance products.
Sustainability and Waste Reduction
Sustainability has become a critical focus in the injection molding medical industry, as manufacturers look for ways to reduce their environmental impact while maintaining the efficiency and cost-effectiveness of production. One important approach is the integration of sustainable practices such as recycling scrap materials generated during the molding process. These materials can often be reprocessed and reused, reducing the need for new raw materials and minimizing waste. In addition, some companies in the medical molding sector have implemented closed-loop systems, where excess plastic and defective parts are collected, cleaned, and reintroduced into the production process. This not only helps reduce waste but also lowers production costs.
Furthermore, the development of biodegradable materials is gaining traction in the injection molding medical industry, especially for disposable medical devices. These materials break down more easily in the environment, offering a more eco-friendly alternative to traditional plastics. By embracing these sustainable practices and materials, companies in the medical molding sector are contributing to environmental preservation while still delivering the high-quality, reliable products needed for healthcare applications. As the demand for sustainability grows, the injection molding medical industry continues to innovate and evolve, balancing environmental responsibility with the critical need for medical device reliability and performance.
Sustainability and Environmental Impact in the Medical Injection Molding Industry
LCA Injection Molding Medical Industry
Life Cycle Assessment (LCA) is becoming an increasingly important tool in the injection molding medical industry, helping manufacturers evaluate the environmental impact of their products from creation to disposal. By considering factors like energy consumption, raw material use, carbon footprint, and waste production, LCA provides a comprehensive understanding of the environmental effects of medical device production. Manufacturers can use LCA to identify opportunities for minimizing waste, reducing energy usage, and selecting more sustainable materials. For example, companies are now utilizing LCA to compare the ecological impact of different polymers used in medical devices, ensuring that the materials chosen are not only cost-effective and durable but also environmentally responsible. As the industry embraces more sustainable practices, LCA serves as a guiding framework for making decisions that align with environmental goals while meeting the high standards of safety and quality required in medical applications.
Injection Molding Medical Device Industry: Focus on Sustainability
The injection molding medical device industry is making strides in reducing its environmental footprint, with a growing emphasis on using sustainable processes and materials. Beyond LCA, industry players are turning to more eco-friendly materials, including biodegradable plastics and recycled resins, to manufacture medical devices. Innovations like 3D injection molding and micro-molding are also enabling manufacturers to use fewer raw materials while increasing production efficiency. Additionally, advances in energy-efficient molding systems and automation are helping to lower energy consumption and reduce emissions during the production process. This shift towards sustainability in the injection molding medical device industry not only benefits the environment but also helps companies meet regulatory requirements and consumer demand for environmentally responsible products. The continuous development of these practices ensures that the industry remains aligned with global sustainability goals while still delivering safe and reliable medical devices.
Essential Requirements for the Injection Molding Medical Industry
Manufacturer Requirements
To succeed in the injection molding medical industry, manufacturers must meet stringent regulatory and operational requirements to ensure the quality and safety of their products.
- Cleanroom Standards:
Manufacturing medical components requires a controlled environment to prevent contamination. Cleanrooms, typically certified to ISO 7 or ISO 8 standards, are essential. These facilities must control particulate levels, temperature, humidity, and air pressure to meet medical-grade cleanliness requirements. Laminar airflow systems and High-Efficiency Particulate Air (HEPA) filters are often used to maintain these standards. - Quality Management Systems (QMS):
A robust QMS certified under ISO 13485 is mandatory for medical device manufacturers. This ensures consistent production processes, traceability of materials, and compliance with international standards. Manufacturers must document and validate every stage of production, from material selection to final inspection. - Good Manufacturing Practices (GMP):
Adherence to GMP is critical. This involves maintaining hygienic facilities, training personnel in sterile handling techniques, and conducting routine inspections. GMP-compliant facilities are regularly audited by regulatory bodies to ensure ongoing compliance. - Regulatory Compliance:
Manufacturers must comply with region-specific regulatory standards, such as the FDA’s 21 CFR Part 820 for Quality System Regulation in the United States or the EU Medical Device Regulation (MDR). These regulations cover design controls, risk management, and post-market surveillance. - Advanced Manufacturing Techniques:
Cutting-edge equipment and technologies, such as micro-molding, two-shot molding, and insert molding, are often required to produce complex and precise medical components. Manufacturers must also integrate automated systems to ensure accuracy and reduce human error.
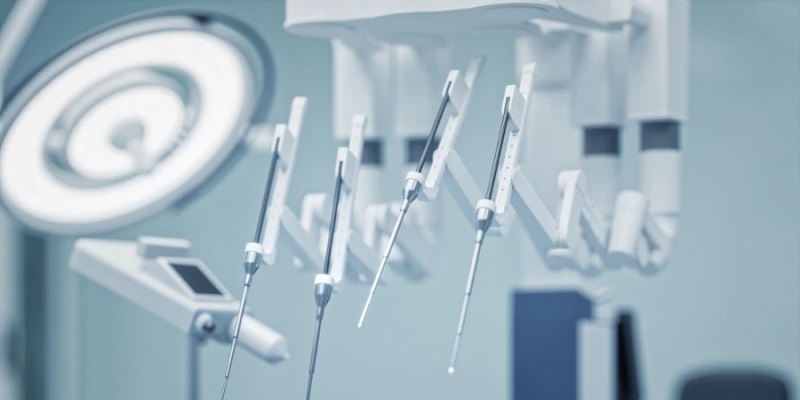
Product Standards
Products created through medical injection molding must meet high standards to be suitable for medical applications.
- Material Compliance:
Medical-grade plastics, such as polycarbonate, polypropylene, and PEEK, must meet biocompatibility standards like ISO 10993 and USP Class VI. These materials are selected for their ability to withstand sterilization processes and their chemical resistance, ensuring they are safe for use in medical settings. - Dimensional Accuracy and Precision:
Medical components require exacting tolerances, often within microns. Injection-molded parts must undergo rigorous inspection, including Coordinate Measuring Machine (CMM) analysis and in-line optical inspection, to ensure compliance with specifications. - Sterilization Compatibility:
Products must be compatible with common sterilization methods, such as gamma radiation, ethylene oxide, and autoclaving. This ensures that components remain functional and safe for use after sterilization. - Regulatory Certifications:
Finished products must comply with the FDA’s 510(k) process in the U.S. or CE marking requirements in Europe, indicating they meet safety and performance standards. Products must also pass biocompatibility testing and adhere to standards for mechanical performance, chemical resistance, and longevity. - Application-Specific Testing:
Certain medical devices, such as catheter components or diagnostic equipment parts, undergo additional tests specific to their applications. This may include fluid dynamics testing, tensile strength testing, or environmental stress crack resistance analysis.
By meeting these comprehensive manufacturer requirements and stringent product standards, the injection molding medical industry ensures the production of safe, reliable, and high-quality medical components essential for healthcare applications.
Step-by-Step Process in the Injection Molding Medical Industry
The injection molding process in the medical injection molding industry involves a series of precise steps to ensure the production of high-quality, functional medical components. Below is a detailed breakdown of the process:
Medical Part Design and Engineering
The process begins with defining the specifications of the medical part to be manufactured. Engineers collaborate to create a detailed design that includes all necessary dimensions, functional requirements, and performance criteria. Advanced computer-aided design (CAD) software is used to develop a blueprint, ensuring that the part meets all regulatory and application standards.
Mold Tool Customization and Fabrication
The next step is to fabricate a custom mold tool that corresponds to the part design. The mold is crafted using strong, durable metals, such as stainless steel or aluminum, to withstand high temperatures and prolonged use. Precision is critical in mold fabrication, as any imperfections can compromise the quality of the final parts.
3D Prototyping
A three-dimensional prototype of the medical part is created using CAD software. This prototype is an essential step in evaluating the design’s functionality, weight, geometry, and other key parameters. If any issues are identified, adjustments are made to the design, and another prototype is produced to ensure it meets all requirements.
CNC Machining
CNC machining is employed to refine the prototype and the mold, ensuring flawless dimensions and surface finishes. This computer-controlled process removes excess material and corrects irregularities, delivering a precise mold and medical part prototype.
Injection Molding
Once the mold and part design are finalized, the actual injection molding process begins. The selected medical-grade plastic is heated until it reaches a molten state. The molten plastic is then injected into the custom mold under high pressure. After injection, the mold is cooled to solidify the plastic, forming the desired medical component. The part is then removed, inspected, and prepared for further processing or sterilization.
By following these systematic steps, the injection molding medical industry ensures the production of reliable, precise, and application-specific medical components.
Contact our professional team now for a same-day quote and risk-free project evaluation. Benefit from ISO 8 cleanrooms, advanced machines, and 12-hour fast response in medical injection molding.