Liquid silicone molding for medical devices, is a type of medical molding, has become a crucial process in the medical device industry, delivering components that meet strict safety and performance standards. Liquid Silicone Molding for Medical Devices widely used in manufacturing critical-function components used in medical devices industry Liquid silicone rubber (LSR), the primary material used in this process, offers unmatched biocompatibility, making it ideal for applications requiring direct contact with human tissue or bodily fluids. Its unique properties—such as flexibility, resilience, and the ability to withstand sterilization—make it an indispensable material in medical device manufacturing. Additionally, precision mold medical techniques in liquid silicone molding provide the accuracy necessary for intricate designs, ensuring high-quality, reliable parts for devices like respiratory masks, implants, and surgical tools. This combination of safety, adaptability, and precision underlines LSR’s vital role in advancing healthcare solutions.
Low-Volume to High-Volume Production Capabilities
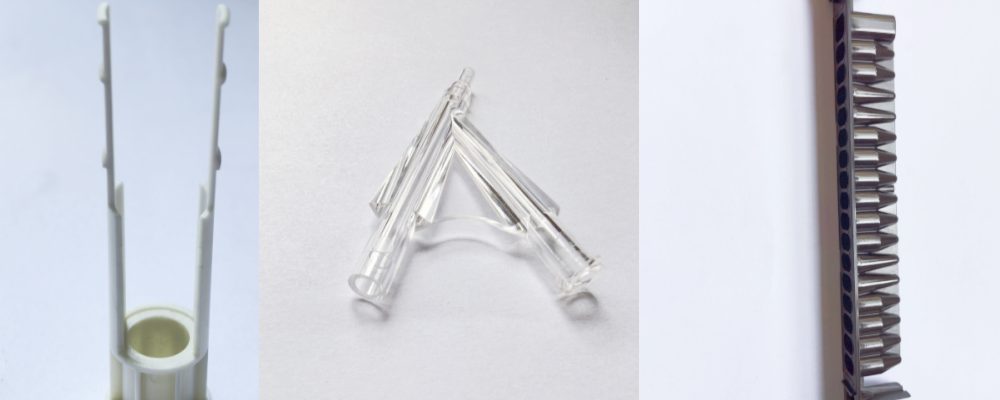
Attribute | Details |
---|---|
Material | Medical-grade liquid silicone rubber (LSR), RTV silicone rubber, platinum-cured silicone. |
Place of Origin | Dongguan, Guangdong, China |
Brand Name | LY Medical Injection Mold. |
Hardness Range | Shore 25A ± 2 to 50A. |
Tensile Strength | Ranges from ≥ 2.8 MPa to ≥ 5.0 MPa. |
Elongation | ≥ 500%. |
Tear Strength | ≥ 10 KN/m to ≥ 25 N/mm. |
Viscosity | 19,000 ± 2,000. |
Mixing Ratio | 1:1 (for two-component silicone). |
Curing Time | 8–12 hours. |
Working Time | 60 minutes. |
Features | High strength, high temperature resistance, low temperature resistance, weather resistance, aging resistance, UV resistance, flame retardant, antistatic, high crystallinity (HCPP), eco-friendly, and compliance with international standards (ISO 9001:2015). |
Applications | Medical devices |
Appearance | Transparent, translucent, customizable color options. |
Processing Methods | Injection molding, extrusion molding, hot melt molding, handmade. |
Product Forms | Liquid two-component silicone, custom shapes and designs. |
Compliance | ISO 9001:2015 certification, food-grade, medical-grade. |
Performance Characteristics | High durability, excellent flexibility, exceptional clarity, and weather resistance. |
Customization Options | Custom colors, shapes, and sizes available upon request. |
Delivery and Service | Fast delivery, high-quality products, excellent communication, and perfect service. |
Why Use Liquid Silicone Molding for Medical Devices?
High Resistance and Biocompatibility
Liquid silicone molding for medical devices offers distinct advantages, making it an optimal choice for creating safe, durable, and biocompatible medical components. One of the primary benefits of using liquid silicone rubber (LSR) is its hypoallergenic nature, which is essential for medical devices that come into direct contact with sensitive tissues and bodily fluids. LSR’s high resistance to chemicals and contaminants ensures that devices remain stable and safe, even in environments that may otherwise cause material degradation.
Exceptional Durability
LSR demonstrates exceptional durability, allowing it to withstand repeated sterilization cycles without losing its flexibility or integrity. This durability is critical for devices that require longevity and reliability, such as implantable devices and syringe stoppers. Furthermore, liquid silicone molding for medical devices allows for complex, precision designs, which is invaluable for creating specialized components like respiratory masks and medical valves. The precision offered by this process also ensures minimal variance in mass production, guaranteeing consistent quality and safety across all manufactured parts.
Liquid Silicone Molding for Medical Devices Molds
In Liquid Silicone Molding (LSM), the mold is a critical component of the process, shaping the silicone material into the desired form for medical devices. These liquid medical silicone molds are highly specialized and designed to meet the stringent requirements of the medical industry. They must ensure that the final product is accurate, safe, and capable of withstanding various sterilization processes.
Types of Molds Used in Liquid Silicone Molding for Medical Devices
- Single-Cavity Molds:
- Definition: Single-cavity molds are designed to produce one part at a time. These are typically used for low-volume or custom medical devices.
- Application: Ideal for specialized, complex parts such as implantable devices, catheters, or seals where precision and individual quality control are critical.
- Multi-Cavity Molds:
- Definition: Multi-cavity molds can produce multiple parts simultaneously within one cycle. This is ideal for high-volume production runs.
- Application: Used for high-demand medical products like tubing, valves, and gaskets that require consistent mass production.
- Cold Runner Molds:
- Definition: These molds use a cold runner system to direct the liquid silicone into the cavities. The material remains cooler and solidifies after the injection.
- Application: Common for molding thin-walled parts like medical gaskets or O-rings, where tight tolerances and high-speed production are necessary.
- Hot Runner Molds:
- Definition: Hot runner molds use heated channels to keep the silicone material in its liquid state until it enters the mold cavity. This results in less waste and more precise molding.
- Application: Typically used for creating complex parts like microfluidic devices, catheters, or valves that need fine details.
- Prototype Molds:
- Definition: These molds are used to create a small number of samples or prototypes for testing and validation. They are often made from softer materials like aluminum or 3D printed components.
- Application: Ideal for developing new medical products, conducting feasibility studies, or running small batches for initial testing.
Mold Materials for Liquid Silicone Molding in Medical Devices
- Steel Molds: Steel is often used for high-precision, durable molds that can withstand the heat and pressure of the molding process. Steel molds are ideal for large production runs and offer high durability and longevity.
- Aluminum Molds: Aluminum is lighter and more cost-effective than steel, making it a good choice for prototype molds or small-volume production runs. However, it may wear out faster than steel molds.
- High-Performance Alloys: In some cases, specialized alloys may be used for molds that require excellent resistance to high temperatures and corrosive materials, especially for medical devices that involve complex or multi-step molding.
Design Considerations for Medical Device Molds
- Precision:
- Medical device molds need to be highly precise to ensure that the final part meets strict regulatory standards for accuracy and consistency. The mold design will incorporate tight tolerances to guarantee that dimensions are within specified limits.
- Ease of Demolding:
- Since the medical parts produced by LSM may have intricate features or soft silicone, the mold must be designed for easy release of the parts. This could involve designing ejector pins or using release agents to minimize damage to delicate components.
- Ventilation:
- Proper ventilation is crucial to allow for the release of trapped air during the molding process. Vent holes must be strategically placed in the mold to avoid defects such as bubbles or voids in the final product.
- Cavity and Gate Design:
- The cavity design must accurately reflect the shape and features of the medical device. The gate system (where silicone enters the mold) must be strategically positioned to avoid part defects and ensure uniform material flow.
- Material Compatibility:
- The mold material must be compatible with liquid silicone rubber (LSR). It must withstand the temperatures required for curing and not react negatively with the silicone. Additionally, molds must be designed to ensure that high-quality parts are produced without defects like warping, flash, or incomplete filling.
Advantages of Custom Molds for Medical Devices
- Precision and Quality Control:
- Custom molds allow for higher precision and greater control over the final product. This is essential in the medical industry, where parts like implants, tubing, and catheters must meet strict safety and regulatory standards.
- Scalability:
- Custom molds can be designed to produce a range of quantities, from low-volume prototypes to high-volume production runs. This flexibility is essential when introducing new medical devices or scaling production based on demand.
- Material Optimization:
- Custom molds can be optimized to use specific types of liquid silicone rubber (LSR), ensuring that the resulting product is both cost-effective and meets the required biocompatibility, sterilization, and durability standards for medical devices.
- Design Flexibility:
- Molds can be customized to produce complex geometries and fine details in medical devices. This allows manufacturers to create innovative medical components that meet the evolving needs of healthcare applications.
Mold Maintenance
- Regular maintenance and cleaning are essential to preserve the integrity of the mold and the quality of the molded parts. Over time, molds can wear out or accumulate silicone residues, which may affect the final product. Routine inspections, cleaning, and possible repair or retooling help ensure the longevity of the mold and consistency of production.
Molds in Liquid Silicone Molding (LSM) are fundamental to the production of high-quality medical devices. The design and materials of the mold are tailored to produce precise, biocompatible, and durable components that meet stringent regulatory standards. Whether for low-volume custom devices or high-volume production, the use of advanced mold designs ensures the consistency, accuracy, and performance of medical products like tubing, catheters, and implants. Proper mold design and maintenance are key to ensuring that the devices are safe, effective, and of the highest quality.
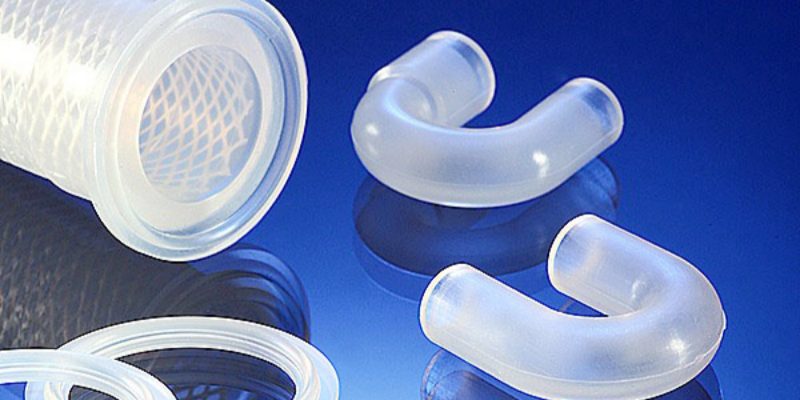
What are Liquid Silicone Molding for Medical Devices Use
Liquid Silicone Molding (LSM) is a highly versatile manufacturing process used to produce medical devices that require biocompatibility, precision, durability, and flexibility. LSM uses liquid silicone rubber (LSR), a material known for its excellent properties in medical applications, such as non-toxicity, high temperature resistance, and compatibility with sterilization processes.
Implants
- Uses: LSM is widely used for manufacturing implantable devices, including breast implants, joint replacements, and surgical meshes. These devices require high biocompatibility, flexibility, and strength to perform well within the human body.
- Benefits: LSR’s softness and elasticity make it suitable for parts that need to conform to the body’s movements, reducing the risk of irritation and ensuring long-term functionality.
Medical Tubing
- Uses: Medical tubing made from LSR is used in a variety of applications, such as catheters, IV lines, oxygen tubes, and dialysis tubing. The flexible nature of liquid silicone allows these tubes to bend and twist without breaking.
- Benefits: LSR tubing is biocompatible, flexible, and can be sterilized through methods like autoclaving or gamma radiation, making it ideal for use in sterile medical environments.
Seals and Gaskets
- Uses: LSM is used to manufacture seals, gaskets, and O-rings that are used in medical equipment and devices. These components ensure airtight or watertight seals in medical devices such as syringes, IV bags, and pumps.
- Benefits: LSR is resistant to temperature extremes, moisture, and chemical exposure, which makes it reliable for preventing leaks and contamination in medical devices.
Surgical Tools
- Uses: Silicone is used in the production of handles or grips for surgical tools such as scalpels, forceps, and scissors. The material’s flexibility and slip-resistant properties make it ideal for creating ergonomic handles that provide a firm grip during delicate procedures.
- Benefits: Medical-grade silicone provides a non-slip surface that enhances safety during surgery. It also allows for easy cleaning and sterilization of tools.
Medical Valves
- Uses: Valves made from liquid silicone are used in medical devices such as heart valves, insulin pumps, and pressure-regulating devices.
- Benefits: Silicone valves offer precise control over fluid flow and pressure while maintaining biocompatibility. Their flexibility also enables them to function under varying conditions without losing effectiveness.
Diagnostic Devices
- Uses: LSM is used to produce components for diagnostic devices, including biosensors, test strips, and diagnostic kits. The material is used to create small, precise parts that are essential for diagnostic tests.
- Benefits: Silicone’s biocompatibility, ability to form intricate shapes, and capacity for sterilization make it a preferred material for in-vitro diagnostic applications.
Wound Care and Dressing
- Uses: Liquid silicone is used in the production of wound care devices, including wound dressings, bandages, and scar treatment sheets. These medical products require a material that is soft, flexible, and gentle on the skin.
- Benefits: LSR is gentle on the skin, making it ideal for wound care and scar management. It is also non-irritating and provides a moisture barrier to protect wounds from contaminants.
Microfluidic Devices
- Uses: Microfluidic devices, which are used in laboratories for handling small amounts of fluids, are often made from liquid silicone. These devices are critical in applications such as point-of-care diagnostics, drug testing, and genetic testing.
- Benefits: LSR is ideal for creating small-scale, high-precision channels in microfluidic devices, enabling accurate fluid control and the ability to run tests on minute quantities of samples.
Orthopedic Braces and Supports
- Uses: Liquid silicone is used to produce orthopedic braces, splints, and supports. These devices help in the treatment and rehabilitation of bone fractures, joint dislocations, and soft tissue injuries.
- Benefits: LSR offers the necessary elasticity and comfort needed for orthopedic applications. It also has excellent shock absorption properties, providing effective protection and support to injured areas.
Dental Products
- Uses: Liquid silicone is used in the production of dental devices, such as mouthguards, dentures, dental impression materials, and orthodontic devices.
- Benefits: Silicone’s biocompatibility, flexibility, and moldability make it ideal for dental applications, ensuring a comfortable fit and safe use in the oral cavity.
Peristaltic Pumps
- Uses: Peristaltic pumps used in medical devices, such as infusion pumps, chemotherapy pumps, and blood pumps, are made using silicone tubing. The pumps help deliver controlled doses of fluids or drugs.
- Benefits: The flexibility and resistance to crushing of silicone tubing ensure that these pumps function reliably without compromising the safety of the fluid being administered.
Advantages of Liquid Silicone Molding in Medical Devices
- Biocompatibility: LSR is safe for prolonged contact with the human body and doesn’t trigger adverse reactions, making it ideal for implantable and surgical devices.
- Sterilization Resistance: Silicone can withstand repeated sterilization processes, such as autoclaving or gamma radiation, without degrading or losing its properties, ensuring the safety of the device.
- Durability: Liquid silicone is highly resistant to wear and tear, temperature fluctuations, and chemicals, ensuring that medical devices made from it have a long service life.
- Flexibility and Comfort: For devices that require flexibility, such as catheters or wound dressings, silicone provides a soft, flexible alternative that is comfortable for patients and conforms to body contours.
- Precision: Liquid silicone can be molded into precise shapes, making it ideal for creating detailed components like microsensors, valves, and tubing used in medical applications.
Liquid Silicone Molding (LSM) plays a crucial role in the production of a wide variety of medical devices that require precision, biocompatibility, and durability. From implants to tubing, wound care products, and diagnostic devices, LSM enables the creation of medical components that meet the strict standards of the healthcare industry. Its benefits, such as flexibility, biocompatibility, and sterilization resistance, make it an ideal material for medical applications that prioritize patient safety and device reliability.
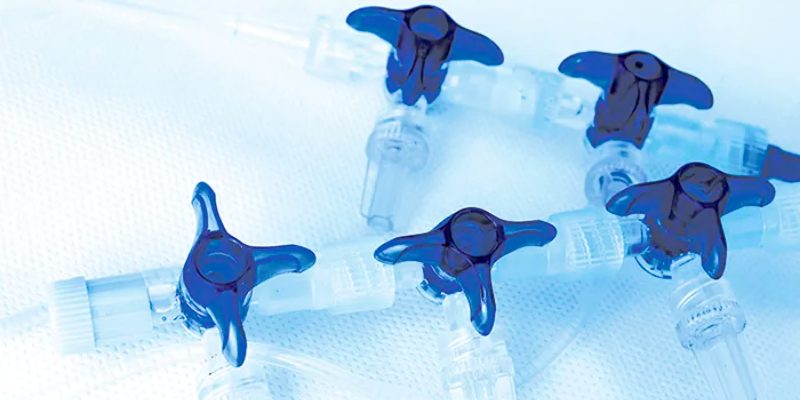
Advantages of Liquid Silicone Molding for Medical Devices
- Biocompatibility
LSR is non-toxic and biocompatible, making it suitable for medical applications that require direct or prolonged contact with the human body, such as implants, catheters, and prosthetics. - Durability
LSR is highly durable and resistant to wear, chemicals, and extreme temperatures, ensuring that medical devices maintain their performance over time, even under harsh conditions. - Sterilization Resistance
Liquid silicone can endure multiple sterilization methods, including autoclaving, gamma radiation, and ethylene oxide sterilization, without losing its properties, making it ideal for reusable medical devices. - Flexibility and Comfort
LSR is flexible and elastic, providing comfort and ease of use in medical devices that need to conform to the body, such as catheters, wound dressings, and prosthetic components. - Precision Manufacturing
LSM allows for the production of highly precise and intricate components with tight tolerances, making it ideal for manufacturing complex medical parts like valves, seals, and microfluidic devices. - No Post-Molding Processing
LSR self-cures during the molding process, which means there is minimal need for additional post-processing steps, leading to reduced production time and cost. - Chemical and Moisture Resistance
Silicone has excellent resistance to a wide range of chemicals, oils, and moisture, making it suitable for medical devices exposed to harsh environments, like drug delivery systems and wound care products. - Non-Allergenic
LSR is non-allergenic and does not leach harmful substances into the body, making it a safe choice for patients with sensitivities, particularly for long-term or implantable medical devices. - Sustainability
Liquid silicone molding is an environmentally friendly process, as silicone is a stable, non-toxic material that can be recycled, contributing to more sustainable manufacturing practices in the medical field. - Cost-Effective for High-Volume Production
While the initial setup cost for LSM can be high, the process is cost-effective for large-volume production, as it offers fast cycle times and reduces material waste, making it ideal for mass-producing medical devices.
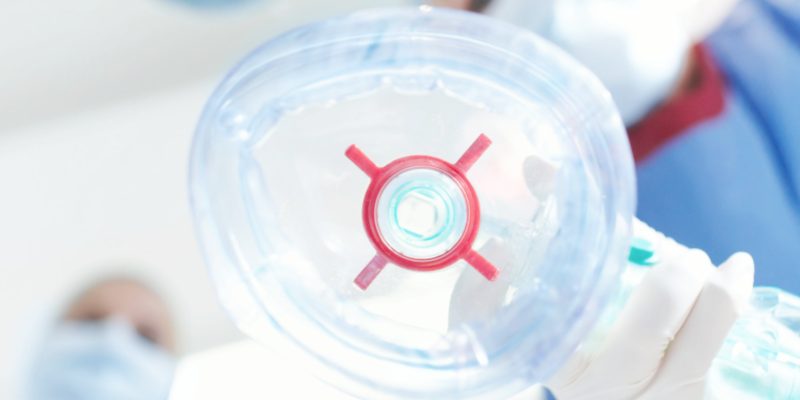
Medical Grade Liquid Silicone Rubber (LSR) and its Qualities
In liquid silicone molding for medical devices, medical-grade liquid silicone rubber (LSR) is a specialized material, is a type of medical grade silicone for molding, rigorously tested and certified to meet stringent FDA and ISO standards. Unlike standard silicone, which is used in a variety of consumer applications, medical-grade LSR undergoes extensive biocompatibility testing to ensure it is safe for use in critical healthcare environments. This certification guarantees that the material is suitable for devices requiring direct contact with body tissues or fluids, offering both safety and performance.
Purity and Safety
Medical-grade LSR is exceptionally pure and free from harmful contaminants, which is crucial for devices like implantable medical products, syringe stoppers, and catheter components. Its chemical and physical stability also means it resists degradation from sterilization processes, a necessary quality for reusable medical tools.
flexibility and precision
Furthermore, liquid silne molding for medical devices allows manufacturers to create highly precise, adaptable designs. This adaptability makes LSR ideal for producing complex medical parts such as valves, respiratory masks, and surgical instruments, where both flexibility and precision are essential. Overall, medical-grade LSR’s superior compliance and versatility support a wide range of applications in healthcare, making it a key material in advancing medical technology.
Costs of Liquid Silicone Molding for Medical Devices
When evaluating the costs of medical device liquid silicone molding, it’s essential to consider a variety of factors that contribute to the total expense. The initial design phase, for instance, is crucial, as it requires precise Computer-Aided Design (CAD) files and prototyping to refine the mold for medical-grade accuracy. Prototyping, often involving 3D printing, allows for early testing and modifications, ensuring that the mold meets specific tolerances and design requirements before final production. This phase alone can impact costs significantly but is key to achieving a reliable final product.
The choice of materials also affects the overall cost. Medical-grade molds typically use durable materials, such as pre-hardened steel or beryllium copper, to withstand extensive production runs and maintain quality under stringent medical standards. Custom mold pricing can range widely: single-cavity molds may start at around $500, while more intricate, multi-cavity, or complex molds can reach up to $20,000, especially when high-precision and larger molds are required.
In terms of long-term value, liquid silicone molding for medical devices proves to be cost-effective, particularly for high-volume production. While the upfront investment may be significant, the low per-unit production cost and high output rate make it ideal for medical manufacturers. This approach not only reduces material waste but also ensures consistent product quality, further enhancing the cost-efficiency of liquid silicone molding over time.
Top Providers of Liquid Silicone Molding for Medical Devices
Choosing the right provider for medical liquid silicone molding is essential to ensure high-quality, safe, and compliant products. Each of these companies brings specialized expertise and resources that cater specifically to the needs of the medical device industry, with robust production capabilities that support a wide range of medical applications.
FUJIU Medical Injection Mold is well-regarded for its use of advanced injection molding technology within ISO Class 8 cleanrooms, making it a trusted partner for producing high-precision components such as respiratory masks and fluid management parts. I focuses on the adaptability of silicones for various medical applications, offering high-quality, biocompatible materials tailored to meet complex medical device requirements.FUJIU Medical Injection Mold provides a range of medical-grade silicone solutions and emphasizes customizable overmolding and plasma etching, enhancing component durability and reliability. FUJIU Medical Injection Mold known for its Class I, II, and III component production, specializes in closed-loop, microprocessor-controlled systems to deliver accurate and repeatable results in highly regulated environments.
Selecting ISO-certified manufacturers is vital, especially for medical components that fall under regulatory classifications. ISO certifications ensure that the company maintains stringent quality control and adheres to rigorous safety standards, which are crucial for Class I (low risk), Class II (moderate risk), and Class III (high risk) medical devices. Partnering with experienced, certified providers in liquid silicone molding for medical devices assures not only compliance with regulatory standards but also optimal performance, safety, and reliability in medical applications.
Liquid Silicone Molding for Medical Devices for Sale: Finding the Best Option
When looking for lsr medical silicone injection molding, it’s essential to prioritize quality, reliability, and compliance with medical standards. Finding the best option means identifying a provider who can meet specific medical requirements and deliver consistent, high-quality results. Quality liquid silicone rubber (LSR) molding solutions should be produced in ISO-certified cleanrooms to minimize contamination risks and ensure a sterile environment suitable for sensitive medical components.
Cleanroom Facilities
To choose the right provider, start by evaluating their cleanroom facilities. An ISO Class 7 or 8 cleanroom environment is recommended for most medical applications, as this setup prevents particulate contamination and protects the biocompatibility of the silicone parts. Providers like Donatelle, SIMTEC, and Specialty Manufacturing offer cleanroom facilities that comply with these standards, making them strong options for medical-grade silicone molding.
Collaborative Design Support
Another key factor is collaborative design support. Many top providers work closely with clients from the initial design phase through to prototyping, production, and testing. Collaborative design support ensures that the final product meets both functional and regulatory standards. A provider who offers robust design assistance, such as early-stage prototyping and mold adjustments, can be invaluable in refining complex precision medical components device.
Quality control processes
Quality control processes are critical. The best providers employ stringent, multi-phase quality checks, ensuring each component meets specifications and regulatory guidelines. This includes post-molding inspections for accuracy and cleanliness, as well as testing to confirm biocompatibility and performance. When considering liquid silicone molding for medical devices for sale, look for providers who prioritize quality assurance, ISO certification, and transparent quality control practices. These factors will help ensure that your medical device components are safe, reliable, and compliant.
Innovations and Custom Solutions in Liquid Silicone Molding
Liquid silicone molding for medical devices has advanced with innovations and custom solutions that enhance the material’s functionality and expand its applications in the medical field. Specialized techniques such as overmolding and plasma etching have become essential for creating high-performance, multi-functional medical components.
Overmolding
Overmolding involves applying a layer of silicone over existing materials like plastic or metal, resulting in a final product with enhanced grip, flexibility, or added insulation. This technique is particularly useful in producing ergonomic handles for surgical instruments, soft-touch surfaces, and seals that prevent contamination in medical devices.
Plasma etching
Plasma etching is another innovative solution that has gained popularity for its ability to improve silicone adhesion on various surfaces, creating a durable bond between silicone and other materials. In medical devices, plasma etching is commonly used to add waterproof or protective barriers to implants or electronic components. This process not only extends the lifespan of the device but also protects against biofluid infiltration, a crucial factor for implantable devices.
Custom solutions
Custom solutions in liquid silicone molding for medical devices are also enabling the development of tailored components that meet specific healthcare needs. For example, protective coatings developed through custom silicone molding processes can shield sensitive electronic implants from moisture, ensuring safe and stable functionality within the body. Similarly, custom seals can be engineered to prevent biofluid leakage in devices like catheters, valves, and fluid management systems. These custom solutions are highly beneficial in applications requiring superior barrier protection, biocompatibility, and reliability.
By leveraging these advanced techniques, providers of liquid silicone molding for medical devices can deliver components that meet complex medical demands, ensuring better outcomes and broader applications in healthcare technology.
How Liquid Silicone Molding is Made for Medical Devices
Liquid Silicone Molding (LSM) is a manufacturing process commonly used to create medical devices that require biocompatible, flexible, and durable components. This method is especially suited for producing precision parts like tubing, gaskets, valves, seals, and implants, which need to meet strict safety standards. LSM uses liquid silicone rubber (LSR), a versatile material that is highly favored in the medical industry due to its superior biocompatibility and sterilization capabilities.
Key Steps in Liquid Silicone Molding for Medical Devices
- Material Preparation:
- The process begins with preparing the liquid silicone rubber (LSR), a two-component material that consists of a silicone base and a curing agent (often referred to as the catalyst). These components are mixed in precise ratios to achieve the desired properties of the final product.
- Mold Design:
- A mold is designed, often using high-precision CNC machining, to create the shape of the desired medical device component. The mold is typically made from aluminum or steel to withstand the high temperatures and pressures used during the process. The mold must also be designed to ensure precision and consistent quality, as medical devices are required to meet stringent regulatory standards.
- Injection:
- The prepared liquid silicone is then injected into the mold using an injection molding machine. The machine uses high pressure to inject the liquid silicone into the cavities of the mold. This step ensures that the silicone fills every part of the mold, creating the intricate shapes and features required for medical devices.
- Curing:
- Once the silicone is injected into the mold, it undergoes a curing process (also called vulcanization), where heat is applied to the mold. The curing process causes the liquid silicone to solidify, forming the final shape of the device. This is a critical step as the material needs to fully cure to achieve its required strength, elasticity, and biocompatibility. The temperature and time are carefully controlled during this step.
- Cooling and Demolding:
- After curing, the mold is allowed to cool before the part is removed (demolded). This ensures the silicone maintains its shape and dimensional accuracy. Depending on the design, the part may need to be trimmed or have excess silicone removed.
- Post-Processing:
- After the part is demolded, post-processing may be required, such as trimming excess material, cleaning, or applying a surface treatment to ensure the part meets the required specifications. Additional operations such as coloring or insertion of other components (e.g., metal parts) may also be performed at this stage.
- Sterilization and Packaging:
- For medical devices, ensuring that the final product is sterile is crucial. After post-processing, the molded parts undergo a sterilization process, which could involve autoclaving or gamma radiation, depending on the device’s intended use. Once sterilized, the devices are then packaged in clean rooms to prevent contamination before shipping.
The production of liquid silicone molding for medical devices involves a multi-step process that ensures both precision and compliance with stringent medical standards. This meticulous process starts with Computer-Aided Design (CAD), where the initial design and specifications for the medical component are established by a medical molding engineer. The digital blueprint helps to visualize the mold’s structure and confirm its functionality. Next, a prototype is often produced, commonly using 3D printing or a soft tooling method, allowing engineers to test the mold’s fit, dimensions, and performance before moving on to final production.
Once the design is finalized, the molding takes place in an ISO-certified cleanroom. Cleanrooms are essential for maintaining a controlled, contaminant-free environment, especially critical for medical components that will come into contact with the human body. Liquid silicone rubber (LSR) is injected into the mold using precise injection molding equipment. This machinery is often microprocessor-controlled, enabling closed-loop feedback that maintains consistent temperatures, pressures, and injection speeds throughout the process. This control ensures that each molded component meets the exact specifications required for medical injection molding applications.
Various molding methods are employed in liquid silicone molding for medical devices. Injection molding is the most common, allowing for high precision and the ability to produce complex geometries. Compression molding is another technique used for simpler designs or high-consistency rubber (HCR) applications. Both methods benefit from the precision of microprocessor-controlled systems, which help to maintain tight tolerances and produce uniform components across large production runs.
This combination of rigorous design, cleanroom manufacturing, and advanced molding technology enables liquid silicone molding for medical devices to achieve the highest standards of quality, safety, and reliability, making it ideal for components that must perform consistently under demanding conditions.
Choosing the Right Liquid Silicone Molding Solution for Medical Needs
Cost
The cost is a significant consideration in choosing a liquid silicone molding solution. While it might be tempting to opt for the lowest-cost option, it’s vital to ensure that cost-saving does not come at the expense of quality and reliability. Analyzing the total cost of ownership, which includes not just the initial investment but also long-term maintenance and potential downtime costs, can provide a clearer picture of the actual expenses involved.
Quality
Quality is paramount when producing medical devices. High-quality liquid silicone rubber (LSR) ensures that the molded parts meet stringent medical standards and perform reliably under various conditions. It is essential to look for molding solutions that offer precise and consistent quality control processes. This guarantees that each component produced meets the necessary specifications and requirements.
Certifications
Certifications are crucial in the medical industry. Solutions that comply with international standards such as ISO 13485 can provide an extra layer of confidence. These certifications indicate that the molding process adheres to industry best practices and regulatory requirements, thus ensuring that the products are safe for medical applications.
Supplier Expertise
The expertise of the supplier can significantly impact the success of liquid silicone molding for medical devices. Experienced suppliers bring a wealth of knowledge and technological capabilities, enabling them to provide valuable insights and innovative solutions. Working with a supplier who understands the unique challenges and requirements of the medical industry can result in better quality, more efficient production, and tailored solutions that meet specific needs.
The importance of high-quality liquid silicone rubber (LSR) molding in supporting safe and effective medical device production cannot be overstated. The key considerations outlined—cost, quality, certifications, and supplier expertise—form the foundation of making an informed decision. By carefully evaluating these factors, companies can ensure that they choose the right liquid silicone molding solution that not only meets their medical device needs but also contributes to the overall success and reliability of their products. Leveraging the benefits of liquid silicone molding for medical devices can lead to enhanced performance, greater patient safety, and improved outcomes in healthcare applications.
Key Consideration | Description |
---|---|
Cost | Analyze total cost of ownership, considering initial investment, maintenance, and potential downtime costs, without compromising quality. |
Quality | Ensure high-quality LSR that meets stringent medical standards and guarantees consistent quality control for reliable performance. |
Certifications | Select solutions that comply with international standards (e.g., ISO 13485) to ensure products meet regulatory and safety requirements. |
Supplier Expertise | Choose suppliers with experience and knowledge in the medical industry to access innovative, tailored solutions and efficient production. |
This table encapsulates the vital aspects that should be considered when choosing liquid silicone molding for medical devices, ensuring safety, reliability, and performance.
FAQs on Liquid Silicone Molding for Medical Devices
Liquid silicone molding for medical devices can be purchased through specialized manufacturers and suppliers who provide high-quality, medical-grade components. These suppliers often operate within ISO-certified cleanrooms to ensure a contaminant-free environment essential for medical applications. When choosing a supplier, consider factors such as their experience with medical applications, certifications, and cleanroom capabilities, as well as their ability to provide custom molding options and design support. FUJIU Medical Injection Mold, for example, offers tailored solutions that meet stringent regulatory standards such as FDA and ISO 13485 compliance. Additionally, you may want to inquire about bulk pricing and support for high-volume orders, as many suppliers, including FUJIU, typically offer cost-effective solutions for larger production runs. Online sourcing platforms dedicated to medical supplies or direct inquiries to silicone manufacturers can also be helpful starting points in identifying the right partner for your specific needs.
Creating liquid silicone molding for medical devices involves a precise, multi-step process. It starts with designing the mold using Computer-Aided Design (CAD) software to define the exact specifications and dimensions of the medical device part. The design then moves into the prototype phase, where early testing with soft tooling or 3D printing helps confirm that the mold meets requirements before mass production. During actual production, liquid silicone rubber (LSR) is injected into the mold in a cleanroom environment, ensuring the components remain sterile and free from contaminants. Injection molding machines, often controlled by microprocessors, maintain strict temperature and pressure conditions to guarantee consistency and precision. Finally, each component undergoes a thorough inspection to ensure it meets all regulatory and quality standards. Manufacturers may also perform additional steps, such as plasma etching or overmolding, to enhance the durability and performance of the final product, making it suitable for medical use.
While liquid silicone and medical silicone may seem similar, there are essential differences. Liquid silicone, also known as liquid silicone rubber (LSR), is a versatile material used in a variety of applications, including non-medical products. Medical silicone, however, refers to silicone that has been specially formulated and tested to meet strict biocompatibility and safety standards. Medical silicone is rigorously certified to ensure it’s safe for contact with human tissue and bodily fluids, meeting FDA, ISO 10993, or ISO 13485 standards. While both forms of silicone share qualities such as durability, flexibility, and resistance to temperature, medical silicone undergoes extensive testing for biocompatibility, purity, and chemical stability. This makes it suitable for applications in the medical field, such as implants, catheter components, and syringes, where safety and compliance are paramount.
Medical devices primarily use high-quality medical-grade silicones, including liquid silicone rubber (LSR) and high-consistency rubber (HCR). LSR is commonly used for injection molding processes, creating parts that are precise, biocompatible, and resistant to sterilization procedures. This type of silicone is ideal for manufacturing complex components, like seals, syringes, and respiratory masks. High-consistency rubber (HCR), another popular silicone, is used for compression molding and produces durable parts needed in medical devices with more straightforward designs. Both types undergo rigorous biocompatibility testing to ensure they’re safe for direct contact with the body or bodily fluids. Medical-grade silicones are designed to meet stringent regulatory standards, making them reliable and safe for sensitive healthcare applications. These silicones offer durability, flexibility, and hypoallergenic properties, which are critical for the safety and longevity of medical devices.
The cost of liquid silicone injection molding varies depending on several factors, including the complexity of the mold, the quality of materials, and the production volume. On average, a basic single-cavity mold for liquid silicone molding may start at approximately $500 for simpler designs. However, more complex molds, especially those with multi-cavity configurations or requiring intricate features, can cost anywhere from $5,000 to $20,000 or more. High-volume production typically reduces the per-unit cost, making liquid silicone injection molding a cost-effective solution for manufacturers who require large quantities. Additional considerations, such as the use of medical-grade materials, customizations, and ISO-certified cleanroom manufacturing, can also impact the overall cost. While the initial setup costs may seem high, liquid silicone injection molding remains an economical choice for large production runs due to the durability and consistency it provides.
Yes, medical-grade silicone is a highly specialized form of silicone that meets strict regulatory standards for use in medical applications. It is a biocompatible material, meaning it is safe for prolonged contact with the human body without causing adverse reactions. Medical-grade silicone is commonly used in the production of a variety of medical devices and components, including catheters, implants, gaskets, surgical tools, and tubing.
Medical-grade silicone undergoes thorough testing to ensure it meets the required safety and performance standards set by regulatory bodies such as the FDA (Food and Drug Administration) in the U.S. or ISO (International Organization for Standardization). This testing ensures that the material is non-toxic, non-reactive, and resistant to degradation over time, even when exposed to bodily fluids or extreme temperatures.
Contact our professional team now for a same-day quote and risk-free project evaluation. Benefit from ISO 8 cleanrooms, advanced machines, and 12-hour fast response in medical injection molding.