Machining plays a vital role in the medical industry, where precision and quality are non-negotiable. Medical parts, ranging from surgical instruments to prosthetics, demand exceptional accuracy to meet stringent healthcare standards. As with medical injection molding, this is where machining medical parts also becomes essential, ensuring components are manufactured to exact specifications. Advanced technologies, such as CNC machining, have revolutionized the production process by delivering unparalleled precision, consistency, and efficiency. These cutting-edge solutions enable the creation of intricate designs and complex geometries that were once considered impossible. The importance of machining medical parts extends beyond functionality; it also ensures patient safety and enhances the performance of medical devices. As the industry evolves, the demand for innovative machining techniques continues to grow. Machining medical parts uses precise CNC processes to create implants, surgical tools, and device components with tight tolerances and high accuracy.
Low-Volume to High-Volume Production Capabilities
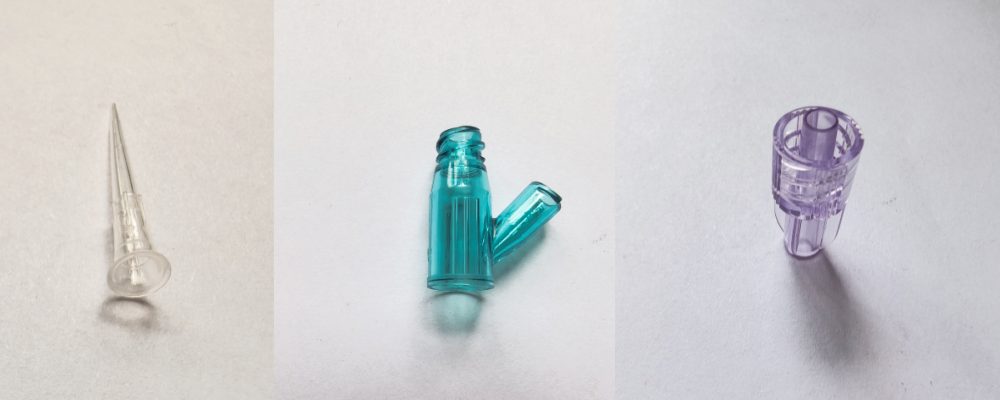
Attribute | Details |
---|---|
Product Name | Machining Medical Parts |
CNC Machining or Not | CNC Machining |
Material Capabilities | Aluminum, Brass, Copper, Bronze, Stainless Steel, Steel Alloys, Hardened Metals, Precious Metals, POM, ABS, PA, PC |
Micro Machining | Available |
Place of Origin | Dongguan, Guangdong, China |
Type | Broaching, Drilling, Milling, Turning, Laser Machining, Etching, Wire EDM, Rapid Prototyping |
Brand Names | LY Medical Injection Mold |
Applications | Medical devices,Medical equipment |
Surface Treatments | Anodizing, Nickel Plating, Zinc Plating, Powder Coating, Polishing, Painting, Brushing |
Process Techniques | Laser cutting, NCT cutting, bending, welding, stamping, deburring, assembly |
Tolerance | +/-0.01mm to +/-0.2mm |
Industry Standards | ISO 9001, ISO 9001:2015 |
Lead Time | 10-35 days for mass production |
MOQ | 1 Piece |
Key Features | Precision manufacturing, durable materials, corrosion resistance, custom designs |
OEM/ODM Services | Accepted |
What Are Machined Medical Parts?
Machining medical parts refers to the precise manufacturing process used to create essential components for healthcare applications. This process relies on advanced techniques, such as CNC machining and precision mold medical, to produce parts with tight tolerances and high-quality finishes. Below are detailed explanations of key categories of machined medical parts and their significance.
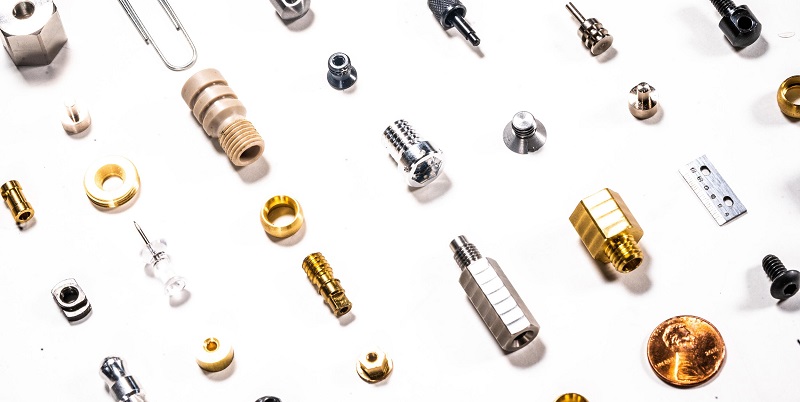
Definition and Examples of Medical Parts Created Through Machining
- Machined medical parts are custom components crafted to meet the exacting demands of the medical industry.
- These parts include surgical tools, medical device components, and implants that require precise dimensions and exceptional durability.
- Examples include biopsy cutters, ventilator casings, and titanium joint implants.
Types of Machined Medical Parts
Surgical Tools
Machining medical parts ensures that surgical tools are reliable and effective for critical procedures. Examples include:
- Scalpels: Manufactured to provide sharpness and consistency for surgical precision.
- Scissors: Designed with ergonomic features to enable surgeons to perform delicate tasks.
- Biopsy Cutters: Engineered with high precision to extract tissue samples safely.
Medical Devices
Medical component machining is essential for producing parts for diagnostic and treatment equipment. Examples include:
- CT Scanner Components: High-accuracy machining ensures smooth operation and imaging precision.
- MRI Table Parts: Customized components crafted to withstand electromagnetic interference.
- Ventilator Housings: Durable, lightweight casings to protect sensitive internal mechanisms.
Prosthetics and Implants
The development of prosthetics and implants depends heavily on machining medical parts, which enables customization and functionality. Examples include:
- Custom Titanium Implants: Used for joint replacements and bone repairs, requiring exact measurements.
- Orthopedic Hardware: Plates, screws, and pins crafted to fit individual patient needs.
The Importance of Machining in Medical Manufacturing
- Precision and Accuracy: Critical for ensuring patient safety and device performance.
- Customization: Medical component machining allows for tailored solutions based on unique patient requirements, ensuring the creation of customized precision medical apparatus components for optimal fit and functionality.
- Material Versatility: Handles a wide range of materials, such as titanium, stainless steel, and advanced polymers.
- Regulatory Compliance: Supports the production of parts that meet stringent medical industry standards and medical molding requirements, ensuring safety and regulatory adherence.
By combining advanced technology and expertise, machining medical parts continues to drive innovation and improve healthcare outcomes worldwide.
Processes Used in Machining Medical Parts
The production of high-quality medical parts requires advanced processes to meet the stringent demands of the healthcare industry. Machining medical parts involves specialized techniques to achieve the precision, durability, and reliability essential for medical applications. Below are the key processes used in creating medical machined components.
CNC Machining
CNC machining is the cornerstone of manufacturing in the medical industry due to its accuracy and adaptability. This process, known as high quality precision medical CNC machining, is widely used for machining medical parts and offers the flexibility to handle various materials and designs.
- 5-Axis Milling
- Used for creating complex geometries in medical parts, such as surgical instruments and prosthetic joints.
- Enables precision in creating curved surfaces and multi-directional cuts in a single setup.
- CNC Turning
- Ideal for producing cylindrical components like catheters and bone screws.
- Medical CNC machining ensures dimensional accuracy and smooth finishes, which are critical for medical applications where functionality and safety are paramount.
- EDM (Electrical Discharge Machining)
- Essential for intricate designs, such as those in implantable devices and micro-surgical tools.
- Provides precision cutting in hard-to-machine materials like titanium and stainless steel.
Micromachining
Micromachining is indispensable for producing small-scale, highly detailed parts required in modern medical devices.
- Applications
- Dental tools with precise cutting edges for effective treatment.
- Inserts for cardiac devices, ensuring reliability in life-saving equipment.
- Advantages
- Allows the creation of components with extremely tight tolerances.
- Supports the production of lightweight, compact machined medical components.
Deburring
Deburring ensures that machined medical components meet safety and quality standards by removing sharp edges and surface imperfections.
- Importance in Medical Parts
- Provides smooth finishes for tools and implants to avoid tissue damage.
- Ensures medical-grade cleanliness by eliminating burrs where contaminants might collect.
- Methods
- Manual deburring for delicate components requiring a personal touch.
- Automated deburring for consistency in high-volume production.
How These Processes Benefit Machined Medical Components
- Precision and Repeatability: Critical for consistent performance in medical devices.
- Material Adaptability: Can handle advanced materials like titanium, PEEK, and stainless steel.
- Compliance with Standards: Ensures machined medical components meet stringent healthcare regulations.
By leveraging these processes, machining medical parts continues to support innovation in medical device manufacturing, ensuring reliable and efficient solutions for healthcare needs.
Materials Used for Machining Medical Parts
The choice of materials is critical in machining medical parts, as they must meet strict healthcare standards for biocompatibility, strength, and reliability. Various metals and plastics are used to manufacture components that ensure safety and performance in medical applications.
Metals
- Titanium
- Widely used for implants like hip replacements and dental screws due to its biocompatibility.
- Known for corrosion resistance, making it ideal for long-term use inside the human body.
- Stainless Steel
- Common in surgical tools and equipment for its durability and resistance to heat and sterilization.
- Provides excellent strength, ensuring tools remain sharp and reliable during use.
- Inconel and Aluminum
- Inconel: Offers high strength at elevated temperatures, suitable for specialized medical devices.
- Aluminum: Lightweight and corrosion-resistant, often used in diagnostic equipment and housings.
Plastics
- PEEK and Ultem
- PEEK (Polyether Ether Ketone): A sterilizable, high-performance polymer used for spinal implants and endoscopic components.
- Ultem: Known for its resistance to creep and excellent dielectric properties, making it ideal for electronic medical devices.
- Medical-Grade Silicone and High-Performance Polymers
- Silicone is highly flexible and biocompatible, used in catheters and prosthetic components.
- Other advanced polymers offer tailored solutions for lightweight, sterilizable medical parts.
CNC Machined Parts for Medical Applications
CNC machining plays a pivotal role in creating high-quality components from these materials. Below are examples of how CNC machined parts for medical are used:
Applications
- Implants: CNC machining ensures precise fitting and durability in orthopedic and dental implants.
- Surgical Instruments: Delivers accuracy in scalpel blades, forceps, and other tools.
- Diagnostic Equipment Components: Produces intricate parts for CT scanners, MRI machines, and ventilators.
Advantages of CNC Machined Parts for Medical
- Unmatched Precision: Enables the creation of complex geometries with micrometer-level accuracy.
- Material Versatility: Can process metals and plastics, meeting various medical requirements.
- Repeatability: Ensures consistent quality for large-scale production of medical devices.
Key Considerations for Material Selection in Machining Medical Parts
- Biocompatibility: Materials must be safe for contact with human tissues.
- Strength and Durability: Components must withstand sterilization, wear, and long-term use.
- Lightweight Properties: Essential for devices that require portability or implantable components.
By combining the right materials with advanced machining techniques, the production of reliable and innovative medical parts continues to advance healthcare technologies.
Applications of CNC Machining in Machining Medical Parts
CNC machining is integral to modern healthcare, enabling the production of highly accurate and reliable medical components. The versatility of this technology supports a wide range of applications, from life-saving tools to cutting-edge diagnostic equipment. Below are the key applications of CNC machining in machining medical parts.
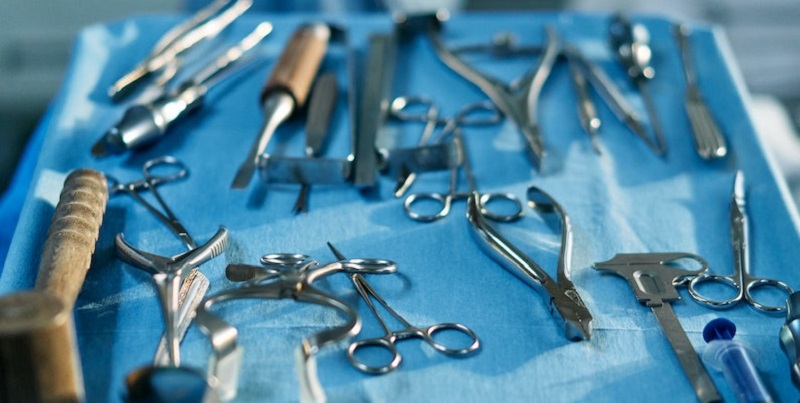
Surgical Tools
- Precision Instruments: CNC machining produces tools, ensuring razor-sharp edges for ophthalmic surgeries.
- Trocar Systems: Designed for minimally invasive procedures, trocars require exact specifications for safe and effective operation.
- Ligation Devices: These tools are essential for surgical procedures involving blood vessel ligation and rely on flawless manufacturing for proper functionality.
Implants and Prosthetics
- Customization: CNC machining allows for the production of custom-made parts tailored to individual patient needs using 3D scanning and CAD modeling.
- Applications: From titanium joint replacements to cranial plates, machining medical parts ensures biocompatibility and durability in implants.
- Orthopedic Solutions: Screws, plates, and pins are precisely machined to secure bone fractures effectively.
Diagnostic Equipment
- CT Scanner Collimators: CNC machining is used to create collimators, which control X-ray beams for clear imaging.
- MRI Table Components: Lightweight and non-magnetic materials are precision-machined for MRI-compatible components.
- X-Ray Machine Anodes: The production of these critical parts ensures optimal functionality and heat resistance.
Medical Prototypes
- Rapid Prototyping: CNC machining facilitates the quick production of prototypes, enabling innovation and testing in medical device development.
- Iterative Design: Engineers can refine designs for cnc medical parts before mass production, ensuring accuracy and functionality.
- Cost-Efficiency: Producing prototypes through CNC machining minimizes waste and speeds up the development process.
Dental Tools and Devices
- Orthodontic Solutions: CNC machining creates precise tools and brackets for orthodontic treatments, ensuring patient comfort and effectiveness.
- Dental Implants: Customized implants and abutments are machined for optimal fit and durability.
- Specialized Instruments: Tools like drills and probes are produced to meet the high precision required in dental surgeries.
How CNC Machining Enhances Medical Applications
- Unparalleled Accuracy: Ensures the tight tolerances necessary for sensitive medical applications.
- Material Flexibility: Supports the use of advanced materials like titanium, stainless steel, and PEEK for diverse needs.
- Reliability: Delivers consistent quality across cnc medical parts and large-scale production runs.
By supporting innovation and precision, CNC machining remains a cornerstone in the development and production of high-quality medical tools and devices, enhancing healthcare outcomes worldwide.
Choosing a Machine Shop for Machining Medical Parts
Selecting the right machine shop for machining medical parts, such as medical parts mold factories, is critical to ensuring the quality, reliability, and safety of the final product. A reputable shop must meet stringent industry standards, possess advanced equipment, and demonstrate expertise in the medical field. Below are key considerations when choosing a machine shop for machining medical parts.
Certifications to Look For: ISO 9001, ISO 13485
- ISO 9001 Certification: Ensures that the machine shop follows a well-defined quality management system (QMS), guaranteeing consistency in manufacturing processes.
- ISO 13485 Certification: Specifically tailored for the medical device industry, this certification assures that the machine shop adheres to strict regulations regarding medical product safety and performance.
- Other Certifications: Look for additional certifications like FDA registration, which indicates compliance with medical device manufacturing regulations.
Experience in Machining for the Medical Field
- Industry Knowledge: A machine shop with experience in machining medical parts will be familiar with the specific requirements and standards for medical devices, implants, and surgical tools.
- Previous Projects: Consider the shop’s track record of successfully completing projects for the medical industry, ensuring they have a solid understanding of the unique challenges involved in manufacturing medical components.
- Regulatory Compliance: A shop experienced in the medical field will understand and comply with FDA regulations, European CE standards, and other global requirements.
Advanced Equipment and Technology
- Swiss Machining: For high-precision, small-diameter parts, Swiss machining is ideal. It is often used for cnc machining medical parts, especially for components like catheters and dental tools that require tight tolerances.
- 5-Axis CNC Machines: These machines enable the machining of complex geometries with high precision, making them indispensable for parts like implants, surgical tools, and diagnostic equipment components.
- Other Technologies: Evaluate whether the shop uses the latest machining technology, such as laser cutting, EDM (Electrical Discharge Machining), or micromachining, which are crucial for producing intricate medical components.
Quality Assurance Processes
- Inspection and Testing: A reliable machine shop should implement comprehensive quality control measures, including dimensional checks, material testing, and surface finish inspections.
- Traceability: Ensure the shop maintains full traceability for each batch of parts, allowing for detailed documentation of the materials, processes, and results.
- Failure Analysis: The shop should have procedures in place for identifying and addressing any issues that arise during production, ensuring that all cnc machining medical parts meet the required safety and performance standards.
When selecting a machine shop for machining medical parts, it’s essential to prioritize certifications, industry experience, advanced equipment, and robust quality assurance practices. These factors ensure that the machine shop can consistently produce high-quality, compliant medical components that meet the rigorous demands of the healthcare industry.
Advantages of CNC Machining for Machining Medical Parts
CNC machining offers significant benefits in the production of medical parts, especially in high-precision applications where quality and reliability are paramount. Below are the key advantages of machining medical parts using CNC technology.
Precision and Repeatability for High-Stakes Applications
- Tight Tolerances: CNC machining, using high precision tools for medical device manufacturing, is known for its ability to maintain extremely tight tolerances, which is critical for machining medical parts used in life-saving applications.
- Consistency: CNC machines can repeat the same process with the same accuracy, ensuring that each part produced meets the required specifications. This repeatability is crucial for high-stakes applications such as surgical tools, implants, and diagnostic devices.
- Complex Geometries: CNC machining excels at creating intricate and complex geometries that are often required in medical device manufacturing, such as custom implants or diagnostic equipment components.
Compatibility with Biocompatible Materials
- Material Selection: CNC machining is compatible with a wide range of biocompatible materials, such as titanium, PEEK, and medical-grade stainless steel, which are often used in medical parts for their strength and compatibility with the human body.
- Versatility: Whether the application requires corrosion resistance, lightweight properties, or bio-compatibility, cnc medical parts manufacturing can accommodate a variety of materials to ensure the part’s functionality and safety.
- Surface Finishing: CNC machining also provides excellent control over surface finishes, ensuring that parts meet stringent standards for smoothness and sterility, crucial for medical devices that must be safely implanted or come into direct contact with the human body.
Rapid Prototyping and Production Flexibility
- Faster Development Cycles: CNC machining enables rapid prototyping, which is particularly beneficial in the medical field where fast development of new devices or surgical tools is essential. By quickly creating prototypes, manufacturers can test, refine, and iterate designs more efficiently.
- Customization: CNC machining allows for the production of highly customized machining medical parts, enabling medical professionals to receive tailored solutions that meet the unique needs of their patients.
- Adaptability: Whether you need a single prototype or a large production run, CNC machining offers the flexibility to handle both low and high-volume production. This adaptability is vital for medical parts that may vary in size and complexity.
Cost-Effective for Low and High-Volume Production
- Reduced Waste: CNC machines are highly efficient, reducing material waste and ensuring that only the necessary amount of material is used. This contributes to lower production costs and minimizes the environmental impact.
- Economical for Various Production Scales: CNC machining can be cost-effective for both small and large production runs. For cnc medical parts manufacturing, it is an ideal option for both low-volume, high-precision needs, as well as larger-scale production where cost per unit is a concern.
- Automation: Many CNC machines are automated, reducing the need for manual labor and allowing for higher efficiency in production. This automation helps keep costs low while maintaining consistent quality in the manufacturing of medical components.
The advantages of CNC machining for machining medical parts are clear: it offers unmatched precision, material compatibility, rapid prototyping, and cost efficiency. These benefits make CNC machining an essential technology in cnc medical parts manufacturing, supporting the production of safe, reliable, and innovative medical devices that meet the strict demands of the healthcare industry.
Key Considerations for Selecting Materials in Machining Medical Parts
Choosing the right materials for machining medical parts is critical to ensuring their safety, durability, and functionality. The selection process depends on specific application requirements, including biocompatibility, chemical resistance, radiation resistance, and sterilization compatibility. Here are the key considerations:
Long-Term Contact Applications
Medical parts in long-term contact, such as implants like pacemakers, prosthetics, and artificial joints, must be strong, durable, and biocompatible. Metals like titanium and stainless steel are ideal for their non-toxic properties and compatibility with human tissue. Plastics such as PE, PU, PET, and acrylic are also viable options.
Chemical Resistance
Medical devices like surgical tools and diagnostic equipment require materials resistant to cleaning agents and sterilization chemicals. Stainless steel, titanium, aluminum, and resins like PC and PEEK provide excellent chemical durability.
Radiation Resistance
Devices exposed to X-rays or MRI radiation, like diagnostic tools, must resist degradation. Titanium and plastics like ABS, PU, and PEEK are radiation-resistant materials.
Sterilization Compatibility
Frequent exposure to sterilization methods necessitates materials that withstand high temperatures and corrosive chemicals. Stainless steel, titanium, and plastics like PEEK, PC, and ABS perform well under these conditions.
Drug Delivery Devices
Materials for drug dispensers, such as tubes and syringes, must prevent static adhesion to ensure precise dosages. Antistatic metals like stainless steel and titanium, or polymers like polypropylene, ABS, and acrylic, are suitable.
Artificial Joints
Artificial joint materials need high strength, biocompatibility, and wear resistance. Common options include titanium, stainless steel, cobalt-chromium alloys, and plastics like UHMWPE, PEEK, and PTFE.
Prosthetics
Prosthetic components must balance durability, lightweight properties, and impact resistance. Materials like titanium, aluminum, ABS+PC, PMMA, and PEEK are commonly used based on the prosthetic’s design and application needs.
By carefully assessing the requirements of each medical application, manufacturers can select the most suitable materials to ensure precision and reliability in machining medical parts.
Essential Materials for Machining Medical Parts
When it comes to machining medical parts, the choice of material is critical to meeting the stringent demands of the medical industry.
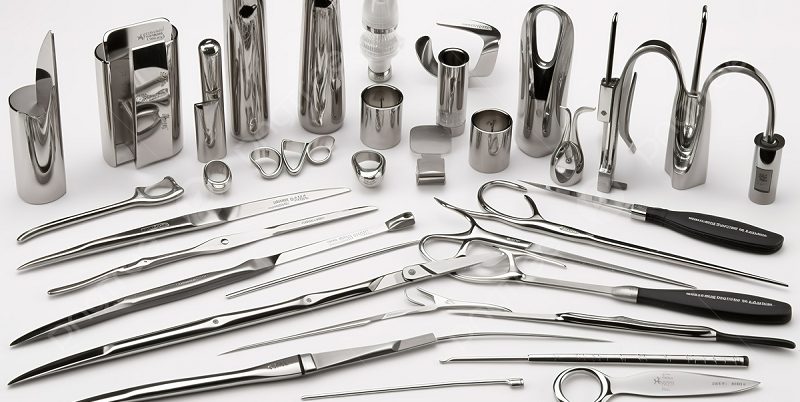
Here’s how five key materials play vital roles in medical CNC machining:
Titanium
Titanium is a top choice for medical applications due to its excellent biocompatibility, corrosion resistance, and lightweight nature. It is commonly used in implants like artificial joints, pacemakers, and prosthetics, as well as in surgical instruments. CNC machining allows for the precise shaping of titanium into intricate components required for medical devices.
Stainless Steel
Known for its strength, chemical resistance, and durability, stainless steel is widely used in surgical tools, orthopedic screws, and diagnostic equipment. CNC machining ensures tight tolerances and smooth finishes, making stainless steel suitable for sterilizable and reusable medical components.
Invar
Invar, an alloy with a very low coefficient of thermal expansion, is utilized in medical devices that require dimensional stability across temperature changes. CNC machining enables the production of highly precise Invar components, often used in imaging equipment and other sensitive instruments.
Kovar
Kovar is a nickel-cobalt alloy known for its excellent thermal expansion properties, making it ideal for applications that involve sealing glass or ceramic components. In medical CNC machining, Kovar is used for devices requiring airtight seals, such as diagnostic equipment and electronic enclosures.
Inconel
Inconel, a nickel-based superalloy, is highly resistant to extreme temperatures and corrosion. It is used in manufacturing parts for radiation-exposed medical equipment, as well as surgical tools that demand exceptional durability. CNC machining enables the fabrication of complex Inconel components with high precision.
Each of these materials brings unique advantages to machining medical parts, ensuring that the resulting components meet the medical industry’s rigorous standards for safety, reliability, and performance.
Expert Tips for Designing CNC Machined Medical Parts
Designing CNC machined medical parts requires careful planning to ensure efficiency, functionality, and compliance with stringent medical standards. Here are detailed tips for optimal design:
Simplify the Design
Streamlining the design enhances manufacturability, reduces costs, and improves precision. Key approaches include:
- Simplifying Geometry: Remove unnecessary features that complicate machining.
- Standard Features: Incorporate chamfers, radii, and fillets to ease tooling and improve durability.
- Material Optimization: Minimize material usage while maintaining structural integrity.
- Tool Accessibility: Design with clear access for cutting tools to avoid machining complexities.
Use Bright Colors
Bright colors improve part identification, traceability, and usability. They distinguish prototypes, functional test parts, or different versions of a design. However, color selection must account for:
- Compatibility with sterilization processes.
- Resistance to high temperatures and harsh chemicals.
- Maintaining biocompatibility for safe medical applications.
Enhance Visual Appeal
Aesthetic designs with vibrant colors help products stand out in the market and improve usability. Key features like buttons and ports should be highlighted for user convenience. Visual appeal should complement practicality, ensuring the design remains functional and purpose-driven.
Optimize for Portability
Portability is vital for medical components used across various clinical settings. Achieve this by:
- Using lightweight materials like aluminum.
- Incorporating ergonomic designs for ease of use.
- Designing products that are simple to disassemble and transport.
Ensure Easy Maintenance
Durability and ease of maintenance are critical for long-term safety and functionality.
- Use robust, easy-to-clean materials to reduce maintenance frequency.
- Design for simple accessibility to facilitate efficient repairs.
- Integrate monitoring systems to detect potential issues early for timely intervention.
By following these tips, manufacturers can achieve designs that enhance the performance, usability, and reliability of CNC machined medical parts, meeting the industry’s high standards.
Requirements for Participants and Experts in CNC Machining Medical Parts
CNC machining for the medical industry is a highly specialized field that requires participants and experts to meet strict standards to ensure the safety, reliability, and precision of medical components. Below are the detailed requirements for individuals and organizations involved in machining medical parts:
Expert Knowledge in Medical Standards
Participants must have a comprehensive understanding of medical industry standards such as ISO 13485 for medical device quality management and FDA regulations for medical components. Experts need to be familiar with material biocompatibility, sterilization requirements, and the tolerances required for life-critical components.
Technical Proficiency in CNC Machining
Experts should possess advanced skills in CNC programming, operation, and troubleshooting. This includes experience with CAD/CAM software, understanding of machining techniques, and the ability to achieve precise tolerances and complex geometries.
Material Expertise
A thorough knowledge of medical-grade materials like titanium, stainless steel, PEEK, and other biocompatible polymers is essential. Participants must understand how these materials behave under machining processes and ensure they meet application-specific requirements.
Cleanroom Manufacturing Compliance
For some medical parts, machining must occur in a cleanroom environment to avoid contamination. Experts must adhere to strict cleanliness protocols and ensure that equipment and materials meet sterility standards.
Quality Assurance Capabilities
Participants should be skilled in implementing and managing rigorous quality assurance processes, including:
- In-process inspections using tools like CMM (Coordinate Measuring Machines).
- Surface finish testing to meet medical-grade smoothness.
- Compliance documentation to validate conformity with regulatory requirements.
Problem-Solving and Innovation Skills
Medical machining often involves unique challenges, such as creating custom implants or advanced surgical tools. Participants must demonstrate problem-solving abilities and the capacity for innovative design and machining solutions.
Understanding of Sterilization and Durability
Experts must design and machine parts that can withstand repeated sterilization processes, such as steam, chemical, or radiation sterilization. This requires precise material selection and surface treatment knowledge.
Collaboration and Communication Skills
CNC machining for the medical industry involves cross-disciplinary collaboration with designers, engineers, and healthcare professionals. Effective communication ensures that the manufactured parts meet functional and clinical requirements.
Commitment to Continuous Learning
The medical field is constantly evolving with new technologies and regulatory updates. Participants must stay informed about advancements in materials, machining techniques, and medical regulations to maintain a competitive edge.
By meeting these stringent requirements, participants and experts in machining medical parts can contribute to the production of reliable, high-quality medical components that meet industry demands and improve patient outcomes.
Limitations of CNC Machining Medical Parts
CNC machining is a vital manufacturing method in the medical field, known for its precision and reliability. However, it has certain limitations that must be considered during the design and production process. Below are the key challenges associated with machining medical parts:
Complexity of Shapes
CNC machining excels at creating parts with simple to moderately complex geometries. However, it struggles with highly intricate shapes involving undercuts, deep cavities, or internal features that standard cutting tools cannot easily access. Producing such designs may require specialized tooling, additional operations, or alternate methods, increasing production time and costs.
Material Limitations
Although CNC machines handle common medical materials like titanium, aluminum, and plastics, certain materials, such as ceramics or heat-sensitive polymers, pose machinability challenges. These materials may require advanced equipment, special tooling, or slow machining speeds to avoid deformation, affecting accuracy and efficiency.
Limited Production Speed
CNC machining is slower than other methods like injection molding or additive manufacturing when producing large volumes of medical components. The precision required for complex designs further increases machining time, making it less suitable for high-volume production under tight timelines.
Size Limitations
The capacity of a CNC machine depends on its size, which determines the maximum dimensions of parts it can process. Very large or bulky medical components may exceed the machine’s capabilities, requiring alternative manufacturing methods like casting or 3D printing.
Surface Finishing Requirements
While CNC machining achieves high precision, it may not always meet the stringent surface finish standards required for medical parts. Additional processes, such as polishing, anodizing, or coating, are often necessary to achieve the desired finish, adding time and cost to the production cycle.
Operator Skills and Training
The effectiveness of CNC machining depends on skilled operators capable of programming, operating, and maintaining the machines. Training and retaining qualified personnel can be a challenge, especially with the increasing complexity of medical device manufacturing and a shortage of skilled CNC technicians.
By understanding these limitations, manufacturers can optimize processes, select appropriate materials, and balance production methods to meet the specific needs of machining medical parts while maintaining quality and cost-efficiency.
The Future of CNC Machining Medical Parts: Innovations and Trends
The future of CNC machining medical parts is promising, with advancements in technology driving innovation and improving the safety, efficiency, and personalization of medical devices. Here’s a detailed look at the key trends shaping its future:
Enhanced Automation and Digitalization
Automation is becoming central to medical CNC machining, with robotics, artificial intelligence (AI), and machine learning (ML) streamlining tasks like material handling, tool changes, and machining operations. This reduces production time, enhances productivity, and minimizes errors.
Integration with digital technologies like CAD, CAM, and simulation tools will further improve workflows, enabling faster prototyping, real-time quality control, and iterative design optimization. Real-time data monitoring and feedback will ensure higher precision and adherence to stringent medical standards.
Customization and Personalization
CNC machining will increasingly support the production of patient-specific devices, such as implants, prosthetics, and surgical tools. Advanced imaging technologies like 3D scanning and medical imaging will allow anatomical data to be directly translated into customized device designs, improving patient outcomes and satisfaction.
Regulatory Compliance
As regulatory requirements for medical devices become more rigorous, CNC machining processes will adapt to ensure compliance. This includes maintaining traceability, validation, and documentation throughout production, ensuring consistent quality and repeatability.
Miniaturization
Demand for miniature and micro-machined medical devices will grow, particularly for minimally invasive surgeries and targeted drug delivery. CNC machining will be vital for producing these highly precise components, enabling breakthroughs in personalized medicine and diagnostics.
Advanced Materials
New biocompatible and durable materials will emerge as materials science advances. CNC machining will evolve to handle these materials, supporting the development of innovative devices with improved strength, safety, and functionality.
Integration with 3D Printing
The synergy of CNC machining and 3D printing will unlock new possibilities, combining the precision of machining with the design freedom of additive manufacturing. This integration will allow for the production of complex, patient-specific medical parts with optimized performance and reduced production timelines.
By embracing these advancements, CNC machining will remain a cornerstone of medical manufacturing, driving innovation and improving healthcare outcomes.
FAQs about Machining Medical Parts
CNC (Computer Numerical Control) machining is commonly used in the production of various medical devices due to its precision and adaptability. Examples of medical devices created using CNC machining include surgical instruments, orthopedic implants, dental implants, custom prosthetic components, and parts for diagnostic equipment. This technology ensures that the devices meet stringent quality and regulatory standards, which is critical for patient safety and efficacy. The accuracy of CNC machining also allows for the creation of highly complex devices that may be tailored to the specific needs of individual patients.
CNC, or Computer Numerical Control, plays a significant role in healthcare by enabling the precise manufacturing of medical devices and equipment. In healthcare, CNC machines are used to fabricate items such as surgical tools, implants, and other medical hardware. These machines are controlled by computers to execute exact movements and produce parts with high accuracy. The reliability and precision afforded by CNC machining help to ensure that medical devices meet strict regulatory standards and perform as required in critical healthcare applications.
Machining parts involves the process of shaping raw material into a desired final form using controlled material removal techniques. This is achieved through various machining processes such as cutting, drilling, milling, and turning. The term “machined parts” refers to the components produced through these processes, often using CNC machines for enhanced precision and repeatability. Machined parts are essential in numerous industries including automotive, aerospace, and medical, where accurate and reliable parts are crucial for performance and safety.
Medical equipment manufacturing is the process of designing, producing, and assembling medical devices and tools used in healthcare settings. This field encompasses a broad range of products including diagnostic machines, surgical instruments, life support systems, and medical imaging devices. The manufacturing process often involves strict regulatory compliance to ensure that the equipment is safe and effective for use in medical practice. High-quality materials, advanced technologies like CNC machining, and rigorous testing are commonly employed to meet the demanding standards required in the healthcare industry.
In the medical field, CNC stands for Computer Numerical Control, a technology used to manufacture precision components for medical devices and equipment. CNC machines utilize computer-driven instructions to cut, shape, and fabricate parts with high accuracy. These machines are essential in producing items such as surgical instruments, orthopedic implants, prosthetics, and dental components.
CNC machining is crucial in the medical industry due to its ability to meet stringent quality standards and produce components with complex geometries. Materials like titanium, stainless steel, and medical-grade plastics are commonly machined to ensure biocompatibility and durability. CNC technology enables rapid prototyping and large-scale production of medical parts, ensuring consistency and reliability in life-critical applications. Its precision and ability to produce intricate designs make CNC machining a cornerstone in modern medical manufacturing.
When a part has been machined, it means it has undergone a manufacturing process in which material is removed from a raw workpiece to achieve a desired shape, size, and finish. Machining involves techniques such as cutting, drilling, milling, or turning using tools like lathes, mills, or CNC machines.
In the context of medical parts, machining ensures the precise dimensions and tolerances required for medical devices. For instance, surgical tools, dental implants, or prosthetic components often need to meet exact specifications for safety and functionality. A machined part undergoes additional quality control checks to verify compliance with industry standards. The machining process is essential for creating components that meet the strict requirements of the medical field, including biocompatibility, durability, and sterile finishes.
Machined components are parts or products manufactured through machining processes that remove material from a workpiece to achieve specific dimensions, tolerances, and surface finishes. These components are often made using CNC machines, lathes, mills, or drills, depending on the complexity and application.
In the medical field, machined components include items like surgical instruments, orthopedic implants (e.g., joint replacements), dental crowns, and prosthetic parts. These components are crafted from biocompatible materials like titanium, stainless steel, or medical-grade plastics. Precision is paramount, as these components often interact with the human body, requiring strict adherence to design specifications and high-quality surface finishes to ensure safety and effectiveness.
Machined components are integral to the medical industry, as they ensure the functionality and reliability of medical devices, supporting both healthcare providers and patients.
CNC stands for Computer Numerical Control, a technology used in manufacturing to control machining tools via computer programming. CNC machines follow pre-programmed instructions to cut, shape, and form materials into precise components.
In the medical industry, CNC machining is critical for creating high-quality parts like surgical tools, implants, and diagnostic equipment. The process ensures exceptional accuracy and repeatability, which is vital for medical devices that require exact specifications and biocompatibility. CNC programming allows manufacturers to produce complex geometries and detailed designs that are difficult to achieve manually.
By automating the machining process, CNC technology reduces errors, improves efficiency, and supports rapid production, making it essential for producing reliable and safe medical components.
The cost of machining a part depends on several factors, including material type, complexity of design, tolerances, surface finish requirements, and production volume. For medical parts, the need for high precision, biocompatible materials (e.g., titanium or medical-grade plastics), and stringent quality standards can increase costs.
On average, custom machining costs can range from $50 to $200 per hour for labor and machine operation. A simple part may cost $100–$300, while complex medical components requiring intricate designs or exotic materials can exceed $1,000 per part. Additional factors like setup fees, tooling costs, and post-machining processes (e.g., polishing or sterilization) also influence the final price.
For small production runs or prototypes, costs may be higher due to setup and programming expenses. Larger production volumes typically lower the per-unit cost through economies of scale. A detailed quote from a machining provider helps clarify specific costs.
In machining, ECM stands for Electrochemical Machining, a non-traditional process used to remove material by anodic dissolution. This technique is especially suited for creating intricate shapes, high-precision parts, and components from hard-to-machine materials without introducing mechanical stress.
For medical applications, ECM is valuable in producing parts like surgical instruments, implants, and precision tools with complex geometries and fine finishes. It’s often used for materials such as titanium or stainless steel, which are challenging to machine conventionally. The process involves no direct contact between the tool and the workpiece, reducing wear and ensuring consistent results.
ECM is ideal for the medical field due to its ability to achieve tight tolerances, smooth finishes, and burr-free edges, all of which are critical for biocompatibility and functionality in medical devices. The process is highly efficient for high-volume production of precision components.
Contact our professional team now for a same-day quote and risk-free project evaluation. Benefit from ISO 8 cleanrooms, advanced machines, and 12-hour fast response in medical injection molding.