Blow molding has become a cornerstone in the medical industry, revolutionizing the way high-quality plastic components are manufactured. Medical blow molding produces durable, leak-resistant components for healthcare, ensuring quality with advanced cleanroom technologies. This advanced technique involves shaping medical-grade plastics into hollow parts, enabling the creation of durable and precise devices. Medical blow molding is particularly vital for producing items like fluid containers, diagnostic equipment, and respiratory devices, meeting stringent healthcare standards. Its significance lies in its ability to deliver lightweight, flexible, and cost-effective solutions while maintaining sterility and functionality. Innovation and customization further enhance medical blow molding, allowing manufacturers to meet diverse and complex medical requirements. By adapting to emerging technologies, this process continues to play a critical role in ensuring efficient, safe, and tailored healthcare solutions.
Low-Volume to High-Volume Production Capabilities
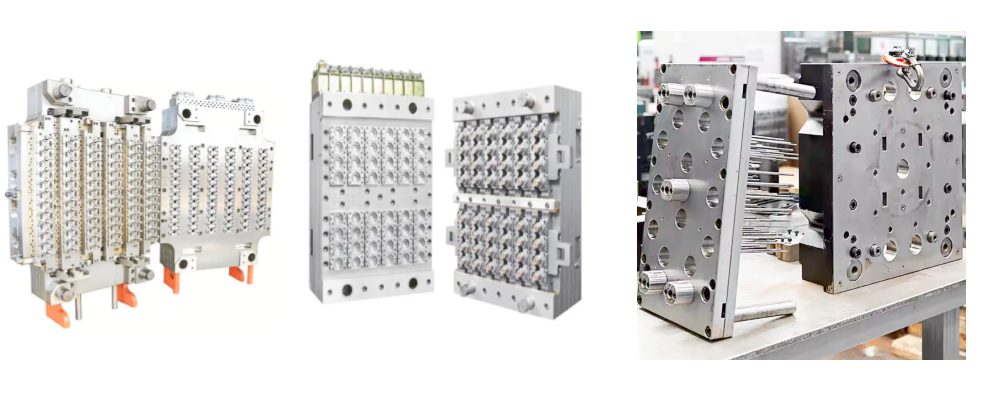
Attribute | Details |
---|---|
Shaping Mode | Injection Mould, Extrusion Blow Moulding |
Materials Processed | ABS, PC, PVC, HDPE, PP, PE, EVA, PA, TPE, TPU, Nylon, POM, PS |
Clamping Force (kN) | 280 - 600 |
Automation | Fully Automatic |
Extruder Motor Power (kW) | 45 - 55 |
Air Consumption (m³/min) | 0.33 - 1.6 |
Key Selling Points | Easy to Operate, Automatic Functionality, Eco-Friendly, Lightweight |
Core Components | PLC, Engine, Bearing, Gearbox, Motor, Pressure Vessel, Pump |
Color Options | White, Green, Black, Gray, Natural, or Custom Colors |
Customization | Tailored designs, customizable size, and color options |
Certification | ISO9001, ISO13485:2016, IATF16949:2016 |
MOQ (Minimum Order Quantity) | 1 Piece |
Packaging | Wooden Case, Plastic Bag with Carton |
After-Sales Services | Commissioning and training, free spare parts, video technical support, online support |
Sample Availability | Free Samples Available |
Application | Medical Containers, Hospital Bed Boards |
Brand Name | LY Medical Injection Mold |
Origin | Dongguan, Guangdong, China |
Design File Formats | STP, IGS, PDF, CAD, DWG, STEP |
What Is Medical Blow Molding?
Medical blow molding is a specialized manufacturing process used to create hollow plastic parts for medical applications. It is a technique that combines the advantages of plastic extrusion and the shaping power of air pressure to produce parts with consistent quality and complex geometries. This process is crucial in the production of a variety of medical components, ranging from containers to medical devices and diagnostic equipment. The medical blow molding process is not only efficient but also offers high precision, making it an essential technology in the healthcare industry.
The Medical Blow Molding Process
The medical blow molding process involves several key steps. It begins with the extrusion of a heated plastic tube, known as a “parison.” The parison is placed into a mold, and air is blown into it, causing the plastic to expand and take the shape of the mold cavity. In this process, medical molding engineers are essential in ensuring the mold design is accurate, the material properties are suitable, and the process is optimized to achieve uniform wall thickness and complex shapes. Once the part has cooled and hardened, it is removed from the mold and undergoes quality checks before being used in medical applications.
One of the main reasons for the widespread adoption of medical blow molding is its ability to produce large quantities of uniform parts with minimal waste. This is particularly beneficial in the medical industry, where precision and reliability are paramount. The hollow nature of many medical devices, such as bottles, vials, and surgical instruments, is a direct result of this process.
Medical Blow Molding Applications
Medical blow molding is used in a variety of medical applications, including the production of containers, medical devices, diagnostic equipment, and packaging. For instance, blow molding is commonly used to create plastic bottles and containers for pharmaceutical products, intravenous (IV) bags, and even components for diagnostic equipment such as blood collection tubes. Medical devices like respiratory masks and certain types of surgical instruments are also manufactured using medical blow molding techniques. These parts often require intricate designs, and blow molding is ideal for creating such components efficiently and accurately.
The versatility of the medical blow molding process enables manufacturers to design parts with different wall thicknesses and various material properties, which are critical for medical applications. Additionally, this technique allows for the integration of features like threaded necks for closures or precise nozzles for dispensing.
Medical Blow Molding for Medical Products
- Precision: Medical blow molding ensures that each part is produced to the exact specifications required. This precision is essential in the medical field, where even small variations can compromise the functionality or safety of the product.
- Cleanliness: The blow molding process can be controlled in a way that minimizes contamination, making it suitable for applications where sterility is important. Many medical blow molding systems include features for cleanroom production, which is critical for creating products used in healthcare environments.
- Durability: Medical molding products made through blow molding are typically robust and durable. The materials used in the process can withstand harsh conditions, such as sterilization, which is vital for medical applications that need to endure multiple uses or high-stress environments.
- Customization: Blow molding offers significant flexibility in terms of design. Manufacturers can customize the shape, size, and even the color of the products, which is particularly useful when creating medical devices that need to meet specific functional or aesthetic requirements.
- Cost-Effectiveness: Once the mold is created, medical blow molding allows for the mass production of identical parts, which reduces manufacturing costs in the long run. This is particularly beneficial for producing large quantities of medical items such as containers, diagnostic equipment, or medical tools.
Medical Blow Molds: Specialized Tools for Precision Manufacturing
Medical blow molds are custom-designed tools that play a critical role in the medical blow molding process. These molds are used to shape the parison into the desired form. Medical blow molds are typically made from high-quality steel and are engineered to meet the stringent standards required in the medical industry. The molds can be highly complex, often incorporating features that allow for precise molding of intricate shapes, such as vent holes or fine details on the surface of medical devices.
Because the integrity of medical products is paramount, medical blow molds must be manufactured to extremely tight tolerances. They are also designed to handle high-temperature and high-pressure conditions, ensuring the finished products meet all safety and performance standards. As medical blow molding continues to advance, the technology behind these molds has become more sophisticated, incorporating advanced cooling systems and automated features to improve both efficiency and precision.
Medical blow molds are essential for creating high-quality medical devices and components. Without them, it would be difficult to achieve the consistency and reliability that are necessary in medical manufacturing.
Medical blow molding is a highly efficient and effective process for creating hollow plastic components used in the medical industry. The process is particularly well-suited for manufacturing medical containers, devices, and diagnostic equipment, with the added benefits of precision, cleanliness, durability, and customization. With the continued development of advanced blow molding techniques and molds, this process will undoubtedly remain a critical part of medical device plastic manufacturing used the technique to develop durable and sterile oxygen masks for emergency medical care. Another example involves the production of leak-proof IV fluid bags that withstand rigorous handling during hospital transport.
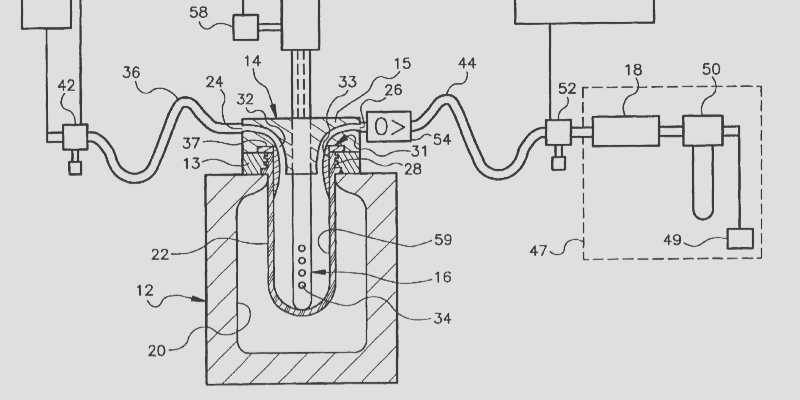
Medical Blow Molding Technologies
Medical blow molding technologies are a cornerstone of modern healthcare manufacturing, enabling the creation of precise, reliable, and innovative medical devices and packaging solutions. These technologies combine advanced engineering, material science, and automation to meet the rigorous demands of the medical industry. Below, we explore the technological aspects that define this field.
Technological Innovations in Medical Blow Molding
Micro-Blow Molding:
- Allows the production of ultra-small, intricate components, essential for minimally invasive devices and microneedle arrays.
- Utilizes high-precision molds and micro-extrusion systems.
- Features real-time monitoring for defect-free production at a microscopic scale.
Multi-Layer Blow Molding:
- Enables the production of containers with multiple material layers.
- Provides enhanced barrier properties to protect sensitive pharmaceuticals from oxygen and moisture.
- Advanced co-extrusion technologies ensure seamless integration of layers for durability.
Biocompatible Material Technologies:
- Focuses on polymers like medical-grade polypropylene (PP), polyethylene (PE), and thermoplastic elastomers (TPEs).
- Utilizes cutting-edge compounding methods to enhance material properties like sterility, flexibility, and compatibility with bodily tissues.
Automation and Robotics:
- Incorporates automated blow molding machines equipped with robotics for mold handling, material feeding, and quality inspection.
- Reduces human intervention to ensure contamination-free production.
- Advanced software integration for remote monitoring and predictive maintenance.
Precision Control Systems
Medical blow molding heavily relies on precision control technologies to meet strict tolerances required for medical applications:
- Computerized Process Control: Ensures real-time adjustments in temperature, pressure, and cooling cycles.
- In-Mold Sensors: Monitor parameters like wall thickness and structural integrity during production.
- Vision Systems: Employ AI-driven inspection systems to detect defects such as micro-cracks and inconsistencies.
Sustainable Technologies in Medical Blow Molding
- Energy-Efficient Machinery: Advanced servo-driven systems minimize energy consumption during production cycles.
- Recyclable Materials: Technologies enabling the use of eco-friendly and recyclable polymers while maintaining medical-grade quality.
- Waste Reduction: Precision trimming and scrap reprocessing systems ensure minimal material wastage.
Future Directions in Medical Blow Molding Technologies
- 3D Blow Molding: Combining 3D printing and blow molding for rapid prototyping of complex medical devices.
- Smart Materials: Development of shape-memory polymers and bioactive materials for advanced medical applications.
- Digital Twins: Simulating blow molding processes virtually to optimize performance and reduce downtime.
- Sustainability Focus: Enhanced technologies for incorporating biodegradable plastics into medical manufacturing.
Medical blow molding technologies are at the forefront of healthcare innovation, enabling the production of critical devices and components with unparalleled precision and reliability. Through continuous advancements, these technologies are driving the future of medical manufacturing, ensuring safer and more efficient healthcare solutions.
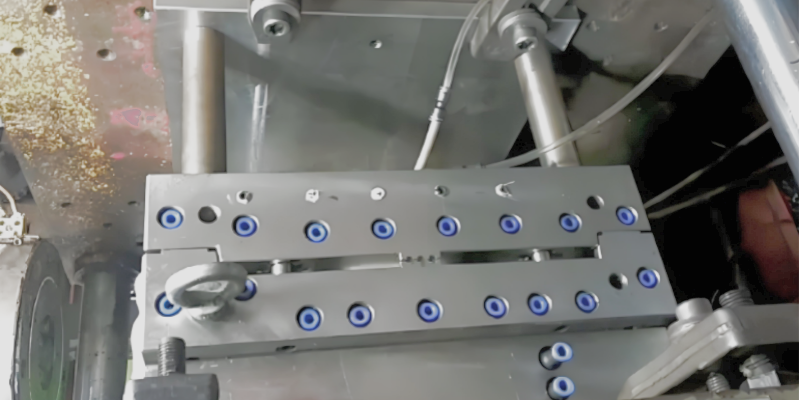
Types of Medical Blow Molding in the Medical Industry
Medical blow molding is a vital process in the manufacturing of plastic components for the healthcare industry. There are several types of blow molding techniques used to create different types of medical products. Each type of blow molding has its own set of characteristics, making it ideal for specific applications in the medical field. Below are six common types of blow molding used in the medical industry, each with distinct benefits and applications.
Extrusion Blow Molding
Characteristics:
Extrusion blow molding is one of the most widely used types of blow molding in the medical industry. This process involves extruding a hollow tube of molten plastic, which is then inflated inside a mold to form the desired shape. The process is ideal for producing large containers or parts with complex shapes. Extrusion blow molding can also create multi-layer structures, which is useful for products that require barrier properties, such as protecting sensitive pharmaceutical contents.
Applications:
Extrusion blow molding is commonly used to produce fluid containers such as IV bags, pharmaceutical packaging, and medical bottles. This technique is particularly beneficial for creating large-volume products like fluid containers that require durability, strength, and ease of use. It is also used for packaging medical products that need extra protection from environmental factors, such as oxygen or moisture, due to the multi-layer capabilities of this technique.
Extrusion blow molding can accommodate various types of resins, allowing manufacturers to tailor the material properties to meet the specific requirements of the medical application. This includes ensuring that the material is compatible with medical-grade standards and can withstand sterilization processes.
Injection Blow Molding
Characteristics:
Injection blow molding is a process that combines injection molding with blow molding. The process starts with the injection of molten plastic into a mold to form a preform. This preform is then transferred to a blow mold, where it is inflated to the final shape. The key advantage of injection blow molding is its ability to produce parts with seamless neck and base formations. This process produces minimal waste, making it a highly efficient method for medical device production.
Applications:
Injection blow molding is commonly used for creating precise medical bottles, diagnostic containers, and pharmaceutical packaging. It is particularly well-suited for applications that require highly consistent dimensions, such as containers that must have exact sealing capabilities. The process also enables the creation of complex shapes with high-quality finishes, which is critical for products like medical bottles, where a smooth, uniform surface is essential for both functionality and safety.
The high precision of injection blow molding also makes it ideal for producing small, intricate components for diagnostic equipment or single-use medical devices. Its low-waste production makes it an environmentally friendly choice for mass production of medical items.
Injection Stretch Blow Molding
Characteristics:
Injection stretch blow molding is a variation of injection blow molding that involves stretching the plastic preform both vertically and horizontally to enhance its mechanical properties. This stretching process results in thinner walls, higher transparency, and improved strength compared to traditional blow molding methods. Injection stretch blow molding is ideal for producing containers that need to be strong yet lightweight. It also allows for better control over the material’s molecular structure, resulting in products with higher durability.
Applications:
Injection stretch blow molding is often used to manufacture PET containers for medical storage solutions, including pharmaceutical bottles, IV fluid bags, and diagnostic sample containers. The enhanced mechanical properties and clarity of the final product make it particularly useful for items that require visibility for content inspection, such as pharmaceutical products that must be carefully monitored.
In addition, injection stretch blow molding can be used to create medical packaging solutions that require both strength and aesthetic appeal. The high clarity of the containers produced by this method is especially useful when the contents need to be visible or inspected, such as in the case of medical samples or medicines.
Blow Mold for Medical Packaging
Characteristics:
A blow mold for medical packaging is designed specifically to meet the stringent requirements of the healthcare and pharmaceutical industries. These molds are built with precision to ensure that the final products meet strict regulatory standards, such as FDA guidelines for medical products. The molds used in medical blow molding for packaging are often made from high-quality, durable materials that can withstand repeated sterilization processes without degradation.
Applications:
Blow molds for medical packaging are used to produce a wide variety of packaging components, including bottles, vials, containers, and packaging for pharmaceuticals and medical devices. These molds are designed to create items that are airtight, tamper-proof, and capable of withstanding rigorous handling conditions, including transport, storage, and sterilization.
Medical packaging plays a crucial role in the safety and efficacy of medical products, and blow molds for medical packaging are essential for ensuring that these products meet the necessary safety standards. The precision of the blow molding process ensures that the packaging fits the medical products securely, protecting them from contamination and damage.
Compression Blow Molding
Characteristics:
Compression blow molding combines elements of both compression molding and blow molding. In this process, plastic is heated and compressed into a mold cavity. Once the material is set, air is blown into the mold to form the final shape. This technique is used for making complex shapes and is especially good for producing thicker-walled medical parts.
Applications:
Compression blow molding is used for creating medical parts such as surgical trays, diagnostic devices, and certain types of medical containers that require thicker walls. It is ideal for parts that must withstand higher mechanical stress or sterilization conditions.
Two-Part Blow Molding
Characteristics:
Two-part blow molding involves using two different types of materials for different parts of a product. This method allows manufacturers to create components that require different properties, such as hard outer surfaces with softer inner layers, or multi-material designs that offer unique functionality. This process provides more flexibility in design compared to other blow molding techniques.
Applications:
Two-part blow molding is used in the production of medical devices where different material properties are necessary, such as drug delivery systems or surgical instruments that require both rigidity and flexibility. The ability to combine multiple materials in one product makes this technique particularly useful for creating multi-functional medical parts.
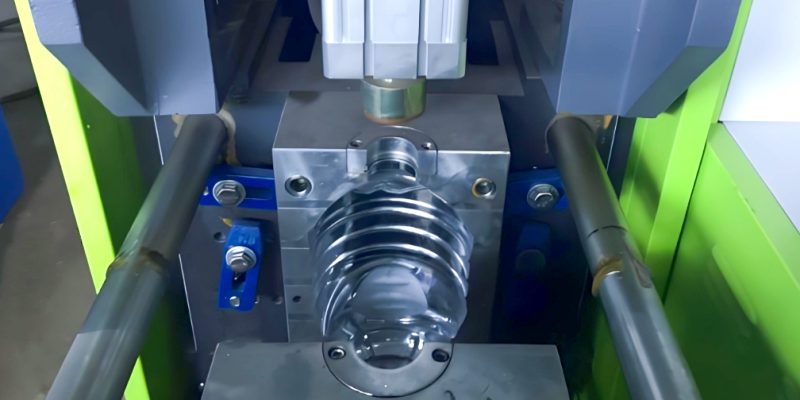
Advantages of Medical Blow Molding for Applications
Medical blow molding is a highly versatile and efficient process used to create various plastic components essential to the healthcare industry. The process provides significant advantages in terms of production efficiency, product design flexibility, material compatibility, regulatory compliance, and cost-effectiveness. Below, we will explore five key benefits of blow molding specifically for medical applications, highlighting how this process supports the creation of reliable, high-quality medical products.
High-Volume Production with Consistent Quality
Advantage:
One of the major benefits of medical blow molding is its ability to produce high volumes of medical products with consistent quality. Once the mold is designed, blow molding allows for rapid, repeatable production. This is essential in the medical field, where products need to be produced in large quantities without compromising on the quality or safety of each item. From packaging and containers to complex medical devices, blow molding ensures that every unit produced meets the necessary specifications and performance standards.
How It Works:
Medical blow molding achieves consistent quality through automated machinery that controls variables like pressure, temperature, and material flow, reducing human error and variability. This is especially crucial for medical products that must meet strict requirements for accuracy and functionality. For instance, pharmaceutical packaging like IV bags or pill containers must be uniform in size and shape to ensure proper sealing and safety. By using high-precision blow molding, manufacturers can maintain uniformity in every product produced, making it easier to meet stringent medical regulations.
Ability to Produce Complex Shapes and Lightweight Designs
Advantage:
Medical blow molding is uniquely suited for producing complex shapes and lightweight designs. The process can create intricate components, such as bottles with threaded caps, intricate medical device housings, or containers with complex geometric features. Additionally, medical blow molding allows for the creation of thin-walled structures, making it ideal for producing lightweight products that are easy to handle, transport, and dispose of—critical attributes for medical consumables.
How It Works:
Blow molding uses pressurized air to inflate molten plastic inside a mold, allowing for the formation of detailed designs. The flexibility of this process allows manufacturers to create custom shapes that would be difficult or impossible to achieve with other manufacturing techniques. In medical applications, lightweight and complex parts are often required to minimize user fatigue and reduce shipping costs. For example, injection stretch blow molding can be used to produce clear PET containers for medical storage that are not only lightweight but also strong and transparent, ensuring both durability and visibility for easy inspection of contents.
Compatibility with Medical-Grade Thermoplastics (e.g., PE, PP, PET)
Advantage:
Another significant advantage of medical blow molding is its compatibility with a wide range of medical-grade thermoplastics. Materials such as polyethylene (PE), polypropylene (PP), and polyethylene terephthalate (PET) are commonly used in medical products due to their excellent chemical resistance, biocompatibility, and sterilization properties. Medical blow molding can accommodate these materials, ensuring that products are safe, durable, and effective in their intended medical applications.
How It Works:
The versatility of medical blow molding allows manufacturers to select the best thermoplastic material for each product’s specific needs. For example, PE is often used for making flexible packaging for medical devices and sterile packaging due to its excellent resistance to moisture and sterilizing agents. PP is chosen for medical containers and components that require higher chemical resistance and strength. PET, known for its clarity and strength, is commonly used in medical containers like blood bags or diagnostic sample vials, where transparency and durability are essential. By selecting the appropriate material, manufacturers can enhance the functionality of medical products while ensuring they meet the regulatory and performance standards required for medical use.
Compliance with Regulatory Standards (e.g., FDA, ISO Certifications)
Advantage:
Medical blow molding is an ideal process for ensuring that medical products meet the strict regulatory standards required in the healthcare industry. Compliance with FDA regulations and ISO certifications is essential for ensuring the safety, efficacy, and quality of medical devices and packaging. Blow molding is well-suited to produce products that comply with these standards due to its precision and control over manufacturing processes.
How It Works:
To meet regulatory requirements, manufacturers must ensure that medical products are produced in controlled environments, using materials that are safe for use in healthcare. Medical blow molding facilities are typically certified to meet industry standards, such as ISO 13485 (Quality Management Systems for Medical Devices) or ISO 9001 (Quality Management Systems). This ensures that the production process is thoroughly controlled and audited, minimizing the risk of defects. Products created through medical blow molding, such as drug packaging or surgical tools, are tested for compliance with various safety protocols, including sterility, material integrity, and performance under pressure or temperature variations.
Cost-Effectiveness Through Low-Pressure Machinery and Reduced Waste
Advantage:
Medical blow molding is a cost-effective method for producing high-quality medical products due to its low-pressure machinery and reduced material waste. Compared to other manufacturing processes, such as injection molding, blow molding can offer significant savings in energy costs and raw materials. This makes it an attractive option for manufacturers who need to produce large quantities of medical items, such as disposable medical devices or packaging, while maintaining tight cost controls.
How It Works:
Blow molding uses lower pressure compared to other molding methods, resulting in reduced energy consumption and a more efficient use of materials. This lower-pressure setup minimizes the amount of plastic required to produce each part, reducing material waste. Additionally, the process can produce parts with thin walls, which further conserves materials. For medical product manufacturers, this reduction in waste is not only cost-effective but also aligns with sustainability goals by decreasing the environmental footprint. Moreover, the speed and efficiency of blow molding allow manufacturers to meet high demand without significantly increasing production costs.
Medical Product Blow Molding Mould: Essential Tools for Precision Manufacturing
Characteristics:
A medical product blow molding mould is a specialized tool used to form the shape of medical devices and packaging during the blow molding process. These molds are crafted with precision to ensure that the final product meets the high standards required for medical applications. They are often made from durable materials like steel or aluminum to withstand the pressures of repeated use while maintaining exacting tolerances. The design of the mold must accommodate the specific needs of the product, including intricate features, smooth surfaces, and compatibility with medical-grade thermoplastics.
Applications:
Medical product blow molding molds are used to create everything from fluid containers to surgical instrument housings. These molds are designed to ensure uniformity and precision in each product, helping manufacturers maintain the high standards required in medical production. For example, a mold used for medical bottles may include a precisely engineered neck for secure sealing, or a mold for an IV bag may be designed to ensure even wall thickness for strength and durability.
Benefit:
The high precision of medical product blow molding molds ensures that each medical product is manufactured to exact specifications. This is critical for products like sterile medical devices or pharmaceutical containers, where even minor deviations can affect performance or safety. Well-designed molds facilitate consistent production, ensuring that each product is uniform, reliable, and compliant with medical industry regulations.
Custom Blow Molding for Specialized Medical Applications
Medical blow molding has evolved as a critical technology for the production of highly specialized medical products. Custom blow molding offers tailored solutions for medical devices and components that require unique shapes, materials, and designs to meet specific medical needs. This process allows manufacturers to address the growing demand for custom medical products, ranging from intricate medical device housings to containers for medical nutrition. Below, we delve into the advantages of medical custom blow molding, exploring its applications and the ability to create specialized, user-friendly, and functional products.
Tailored Solutions for Unique Medical Devices and Components
Advantage:
One of the primary benefits of medical custom blow molding is its ability to provide tailored solutions for highly specialized medical devices and components. This process enables manufacturers to create products that meet the precise specifications required for different medical applications, such as surgical instruments, diagnostic tools, or drug delivery systems. Medical custom blow molding allows for the production of unique shapes, sizes, and features, ensuring that each product fits the specific needs of healthcare providers and patients.
How It Works:
In medical custom blow molding, the design and molding process are closely aligned with the intended medical application. Custom molds are created based on detailed specifications, allowing manufacturers to produce parts that fit within the complex requirements of the medical field. This could include the production of complex geometries, multi-chamber designs for drug delivery, or the incorporation of features such as smooth, ergonomic surfaces for easy handling. The flexibility of the custom blow molding process enables the creation of specialized components that meet exact functional, regulatory, and safety standards. For example, custom molds might be used to produce orthopedic implants or diagnostic equipment casings that require both durability and precision.
FUJlU Medical injection Mold: Excellence in Custom Medical Blow Molding
At FUJlU Medical injection Mold, we specialize in delivering high-precision custom medical blow molding solutions tailored to meet the demanding needs of the healthcare industry. Our expertise in injection molding and blow molding technologies ensures the production of high-quality medical components and devices that adhere to the strictest industry standards. By combining advanced manufacturing techniques with unparalleled attention to detail, we support healthcare providers, laboratories, and medical researchers in their pursuit of excellence.
Uncompromising Precision
Precision is the cornerstone of medical device manufacturing. At FUJlU Medical injection Mold, we utilize state-of-the-art blow molding technologies to create components with exceptionally tight tolerances. Our processes ensure that every product meets the rigorous specifications required for critical medical applications, including surgical instruments, diagnostic tools, and fluid collection systems.
Key precision-focused practices include:
- Advanced mold design for consistent part accuracy.
- Real-time quality control systems for defect detection.
- Precision trimming and finishing for flawless end products.
Adherence to Regulatory Standards
We recognize the importance of compliance with industry standards such as ISO 13485 and FDA regulations. Our custom medical blow molding solutions are developed with strict quality assurance protocols to ensure patient safety and device efficacy.
Features of our regulatory-focused approach:
- Routine audits and inspections to maintain compliance.
- Material traceability to meet documentation requirements.
- Sterilization-ready production for cleanroom compatibility.
Enhanced Product Reliability
Our custom medical blow molding services are designed to produce reliable and durable components that can withstand the demands of various medical environments. Whether it’s a critical surgical tool or a diagnostic device, FUJlU Medical injection Mold ensures consistent performance under diverse conditions.
Key reliability-enhancing measures include:
- Material selection optimized for strength and biocompatibility.
- Multi-layer blow molding for added durability and barrier properties.
- Rigorous testing procedures to validate product integrity.
Advanced Manufacturing Capabilities
Our expertise in both injection and blow molding allows us to manufacture complex medical components with intricate geometries. FUJlU Medical injection Mold employs cutting-edge machinery and innovative techniques to produce high-volume orders efficiently without compromising quality.
Technological highlights:
- Micro-Blow Molding: For ultra-small, precise components.
- Multi-Material Integration: Combines materials for enhanced functionality.
- Automation: Streamlined production with robotics and IoT monitoring.
Supporting Innovation in Medical Technology
As a forward-thinking company, FUJlU Medical injection Mold is committed to supporting the development of next-generation medical devices. We work closely with clients to translate their designs into manufacturable solutions, enabling the creation of groundbreaking products that improve patient care.
Innovative capabilities include:
- Compatibility with advanced materials such as biopolymers.
- Design consultation to optimize manufacturability.
- Rapid prototyping for faster product development cycles.
At FUJlU Medical injection Mold, we are dedicated to driving advancements in medical technology through precision and innovation. Our custom medical blow molding services enable healthcare providers and manufacturers to deliver reliable, high-quality solutions that positively impact patient outcomes. With a focus on quality, compliance, and cutting-edge manufacturing, we are your trusted partner in medical device production.
Case Study: Blow Molding for Protein Powder Containers Used in Medical Nutrition
Example:
A great example of custom blow molding in the medical field is the production of protein powder containers for medical nutrition. These containers are often used to package specialized nutritional products for patients with specific medical needs, such as those recovering from surgery or dealing with malnutrition. The need for safe, secure, and easy-to-use containers is paramount, as these products must not only preserve the quality of the nutrition but also be designed for ease of use by patients with limited dexterity or mobility.
How It Works:
Custom blow molding is employed to produce protein powder containers with features that enhance usability and functionality. For instance, these containers might be designed with wide mouths for easy filling and dispensing of powder, a secure sealing system to ensure product safety, and a lightweight yet durable construction to withstand the rigors of transport and handling. Additionally, blow molding allows for the creation of these containers in a variety of materials, including medical-grade polyethylene (PE) or polypropylene (PP), which are safe for contact with food and capable of maintaining product integrity. In-mold labeling or decoration can also be incorporated to display clear instructions, nutritional information, and branding, making it easier for patients and healthcare professionals to identify the product and use it correctly.
Integration of In-Mold Decoration for Branding and User-Friendly Designs
Advantage:
Another advantage of medical custom blow molding is the integration of in-mold decoration (IMD) for branding and user-friendly design elements. In the medical industry, product labeling and branding are not only critical for marketing but also for ensuring patient safety and product traceability. In-mold decoration involves the incorporation of labels, logos, or user instructions directly into the product during the molding process, eliminating the need for additional labeling or stickers. This feature is particularly valuable for products that require high levels of hygiene or those that are sterilized and packaged for single-use.
How It Works:
In-mold decoration can be applied during the blow molding process, where a pre-printed label or graphic is inserted into the mold cavity. The heat from the molding process bonds the decoration directly to the surface of the product, resulting in a permanent, smudge-proof, and tamper-proof label. This process is particularly important for medical products that need to provide clear information, such as dosage instructions for medical containers or detailed care instructions for surgical tools. For example, in custom blow molding for medical devices, instructions for use, barcodes, or even safety warnings can be directly incorporated into the molded product. This not only simplifies the production process but also enhances the overall user experience by providing easy-to-read information that will not degrade or wear off over time.
Characteristics:
A medical custom blow mold is a specialized tool designed to produce precisely engineered medical products. These medical molds are created with extreme attention to detail to ensure that the final product meets the strict standards required for medical applications. The custom mold is crafted based on the specific design and functional requirements of the medical product, whether it’s for a surgical device, diagnostic container, or pharmaceutical packaging. Medical custom blow molds are typically made from durable materials such as steel or aluminum, ensuring they can withstand the high pressures and temperatures involved in the blow molding process.
Applications:
Medical custom blow molds are used in a variety of applications across the medical field. These molds are integral to the production of a wide range of medical devices and components, such as fluid bags, medical bottles, surgical instrument housings, and diagnostic containers. For instance, a custom blow mold may be designed to produce a specific type of IV fluid bag, where the mold’s shape and features ensure optimal function, such as controlled flow or secure sealing. Another application could be the production of sterile containers for vaccines or injectable medications, where the design of the mold ensures the containers are both airtight and easy to handle.
Benefit:
The use of medical custom blow molds ensures that each product is manufactured to precise specifications, guaranteeing functionality, safety, and compliance with medical standards. Custom molds allow manufacturers to achieve highly specialized features that are critical in the medical industry, such as tamper-evident closures, precise neck formations, and ergonomic handles. This level of precision is essential for products that must perform reliably in life-saving medical applications.
Custom Blow Molding for Medical Industry: Meeting Specialized Needs
Characteristics:
Custom blow molding for the medical industry refers to the use of tailored blow molding processes to produce specialized medical products. This process includes the design and manufacture of custom molds that are specific to the medical application at hand. Custom blow molding enables the creation of products that not only meet the technical requirements of the medical field but also address specific patient needs, such as ease of use, safety, and comfort.
Applications:
Custom blow molding for the medical industry is used to create a wide array of medical products, including respiratory devices, drug delivery systems, medical packaging, and diagnostic equipment. One key application is the production of customized oxygen masks, where the blow medical injection molding process ensures a perfect fit for patients’ faces, enhancing comfort and minimizing leakage. Another example is the creation of specialized containers for medical-grade liquids, where custom blow molding ensures that the containers are not only functional but also meet the sterilization and chemical resistance requirements of medical products.
Benefit:
By employing custom blow molding for the medical industry, manufacturers can produce products that are specifically designed for the unique needs of the healthcare sector. This customization ensures the final product performs optimally, adheres to safety standards, and is tailored for specific medical applications, making it an indispensable solution for the production of high-quality medical products.
Leading Medical Blow Molding Companies
The medical blow molding industry is driven by innovative companies dedicated to producing high-quality components and devices. These companies play a crucial role in advancing healthcare through precise and efficient manufacturing.
FUJIU Medical Injection Mold renowned for its advanced technology in medical molding, combining high-cavitation systems with automation for optimal production.
- Capabilities:
We excels in injection blow molding, delivering seamless and precise components with exceptional surface finishes. We expertise ensures consistent quality across large production runs. - Key Applications:
Our products include medical bottles, diagnostic equipment, and fluid containers. For example, we developed durable, tamper-proof medical bottles that comply with ISO and FDA standards, ensuring the safe transport of sensitive liquids. - Advantages:
We focus on automation minimizes human intervention, reducing contamination risks and production times. This approach also enhances cost-effectiveness for our clients.
China Medical Product Blow Molding Mold: Pioneering Innovation
China has emerged as a key player in the development of china medical product blow molding mold, leveraging cost-effective manufacturing and technological expertise to meet global demands.
- Overview:
Chinese manufacturers excel in creating molds tailored for the medical sector. These molds are designed to produce high-precision components while maintaining affordability. - Advantages:
By using state-of-the-art CNC machining and advanced design software, these companies produce durable molds that ensure consistent product quality. This makes them ideal for applications such as sterile packaging, medical storage containers, and fluid transfer systems. - Case Example:
A Chinese manufacturer developed a specialized blow mold for syringes with integrated safety caps, reducing needle-stick injuries in healthcare environments.
Medical Blow Molding: Industry Impact and Leading Players
The global medical blow molding industry is shaped by companies that prioritize innovation, precision, and regulatory compliance. Firms like FUJIU and Aptyx are setting benchmarks for quality and efficiency, while China’s mold manufacturers provide cost-effective solutions without compromising on standards.
- Industry Impact:
These companies contribute to better patient care by producing reliable, high-performance medical components. Their advancements also streamline healthcare supply chains, ensuring timely availability of critical products. - Research Highlight:
Studies show that firms investing in automation and sustainable materials are leading the way in medical blow molding, offering solutions that balance performance with environmental responsibility.
Leading companies in the medical blow molding sector are at the forefront of healthcare innovation. Through their dedication to precision, sustainability, and customization, they ensure that the medical industry continues to benefit from reliable and cost-effective solutions.
Materials Used in Medical Blow Molding
Materials play a critical role in the success of medical blow molding processes. The selection of appropriate materials ensures the production of safe, durable, and functional medical components. Below is an overview of the most common thermoplastics used and their unique benefits for medical applications.
Common Thermoplastics in Iso Certified Blow Molder Medical
- Polyethylene (PE):
Polyethylene is a widely used material in medical blow molding due to its durability and impact resistance. It is particularly suitable for producing medical containers that require flexibility and toughness, such as fluid bottles and sterile packaging. Its excellent chemical resistance ensures the safe containment of medical solutions. - Polypropylene (PP):
Known for its versatility, polypropylene is another popular choice in the medical industry. Its ability to withstand high-temperature sterilization processes makes it ideal for applications requiring repeated use or autoclaving. PP is commonly used for diagnostic tools, syringe barrels, and other components requiring clarity and strength. - Polyethylene Terephthalate (PET):
PET is favored for its high clarity and transparency, making it suitable for diagnostic containers and test kits. Its lightweight nature and resistance to breakage add to its popularity in medical applications. Additionally, PET’s recyclability aligns with the growing emphasis on sustainability in healthcare manufacturing. Medical injection molders frequently choose PET for components where clarity and recyclability are essential.
Importance of Injection Blow Molding for Medical Industry
In medical blow molding, only medical-grade thermoplastics are used to ensure safety and compliance. These materials must meet stringent FDA and ISO standards, ensuring biocompatibility, sterility, and resistance to contamination. Medical-grade plastics also undergo rigorous testing to confirm their suitability for sensitive applications such as drug delivery systems and diagnostic equipment.
China Medical Product Blow Molding Mould Factory: A Leader in Material Expertise
China Medical Product Blow Molding Mold Factory
China Medical Product Blow Molding Mould Factory: A Leader in Material Expertise
China’s manufacturing sector is known for its expertise in creating high-quality molds tailored to the specific demands of medical blow molding. A China medical product blow molding mould factory focuses not only on mold design but also on material compatibility, ensuring the use of FDA-approved thermoplastics for reliable and consistent output. This expertise extends to thermoplastic injection molding medical, providing a range of materials suitable for the medical industry.
- Material Selection Expertise:
Factories in China, such as Shenzhen Weidagao Mould, specialize in optimizing materials for durability and performance. They conduct extensive material testing to align with medical standards and ensure compatibility with various molding techniques. - Case Study:
A leading china medical product blow molding mould factory collaborated with a pharmaceutical company to produce sterile packaging for IV fluids using polyethylene. This partnership ensured optimal material utilization and compliance with global regulations.
China Medical Product Blow Molding Mould: A Focus on Quality
China Medical Product Blow Molding Mould
Chinese manufacturers, renowned for cost-effective solutions, excel in producing china medical product blow molding mould designs. These molds support a variety of thermoplastics, offering flexibility for medical manufacturers worldwide.
- Applications:
From diagnostic containers made of PET to sterilizable PP syringe barrels, Chinese molds are integral to a wide array of medical products. - Advantages:
Chinese molds are known for their durability and precision, ensuring minimal material wastage during the blow molding process. Their adaptability to different thermoplastics provides a competitive edge in meeting diverse industry needs.
The choice of materials in medical blow molding significantly impacts the quality and functionality of the final product. With a focus on FDA-approved, medical-grade thermoplastics like PE, PP, and PET, the industry ensures compliance with stringent safety standards. Meanwhile, Chinese factories continue to lead in innovation, offering high precision medical molds optimized for these materials, as demonstrated by the contributions of china medical product blow molding mould factory leaders. This blend of material excellence and advanced molding techniques drives progress in medical manufacturing globally.
FAQs about Medical Blow Molding
Blow molding is categorized into three main types, each suited for specific applications, including medical manufacturing. These types are:
Extrusion Blow Molding (EBM):
Process: Molten plastic is extruded as a hollow tube (parison), which is then enclosed in a mold. Air is blown into the parison, inflating it to the mold’s shape.
Applications in Medicine: Commonly used for producing medical containers, such as IV solution bottles, specimen containers, and urine collection bottles.
Advantages: Ideal for large hollow parts, cost-effective for high-volume production, and compatible with various materials like polyethylene and polypropylene.
Injection Blow Molding (IBM):
Process: A preform is created using injection molding, then transferred to a blow mold where it is inflated.
Applications in Medicine: Used for smaller, high-precision containers like vials, ampoules, and dropper bottles.
Advantages: Offers high precision, uniform wall thickness, and a smooth finish, making it ideal for sterile medical packaging.
Stretch Blow Molding (SBM):
Process: Similar to IBM but includes an additional step where the preform is stretched axially and radially before blow molding.
Applications in Medicine: Suitable for producing lightweight, durable, and clear containers, such as pharmaceutical bottles and IV fluid containers.
Advantages: Increases material strength and clarity, reduces weight, and improves barrier properties.
Each type of blow molding has unique advantages, allowing manufacturers to meet the diverse requirements of the medical field.
Blow molding involves four key stages, each critical to producing high-quality components, especially for medical applications:
Plasticization and Parison/Preform Creation:
Extrusion Blow Molding (EBM): A molten plastic tube (parison) is extruded.
Injection Blow Molding (IBM) and Stretch Blow Molding (SBM): A preform is created by injecting molten plastic into a mold.
Medical Application: Preforms or parisons are crafted with precise dimensions for uniform wall thickness, crucial for sterile containers like vials or IV bottles.
Mold Clamping:
The parison or preform is placed inside a two-part mold. The mold is clamped shut, encapsulating the material.
Medical Application: Cleanroom operations ensure that this step is contamination-free.
Blowing and Shaping:
Compressed air is blown into the parison or preform, inflating it to take the shape of the mold. In SBM, this step includes stretching the material for enhanced strength and clarity.
Medical Application: This stage ensures the final product has the required shape, size, and properties, such as for pharmaceutical bottles or oxygen masks.
Cooling and Ejection:
The molded part is cooled within the mold to solidify its shape. Once cooled, the mold is opened, and the part is ejected.
Medical Application: Cooling is carefully controlled to avoid defects, ensuring components meet strict medical quality standards.
These stages combine to produce sterile, precise, and reliable medical containers and components, vital for healthcare use.
An alternative to blow molding for medical applications is injection molding, particularly when precision and intricate designs are required. Injection molding is better suited for creating solid medical components such as syringes, surgical instruments, and implants. It offers tight tolerances and the ability to use advanced biocompatible materials.
Another alternative is rotational molding (rotomolding), which is suitable for creating hollow structures like medical storage tanks. Although slower than blow molding, rotomolding can produce seamless and durable parts with uniform wall thickness, making it a viable option for certain medical applications.
Thermoforming is also a potential alternative, especially for producing large, thin-walled medical trays or packaging. While it lacks the 3D complexity of blow molding, thermoforming is cost-effective for low to medium-volume production.
For custom or small-scale medical components, 3D printing (additive manufacturing) is gaining popularity. It allows for rapid prototyping and the creation of intricate geometries that traditional blow molding cannot achieve.
These alternatives are chosen based on factors such as material requirements, production volume, and the complexity of the medical part being produced. While blow molding is ideal for producing lightweight, hollow medical items like bottles or containers, these alternatives offer more flexibility for specialized applications.
Blow molding has several disadvantages, particularly in medical applications, where precision and material standards are critical:
Limited Precision: Blow molding is less precise compared to other manufacturing methods like injection molding. It is challenging to achieve tight tolerances required for medical devices.
Material Restrictions: While suitable for producing hollow components, blow molding cannot handle materials like PEEK or certain medical-grade polymers that require high precision.
Wall Thickness Variation: The process often results in uneven wall thickness, which may compromise the durability and performance of medical containers or devices.
High Initial Costs: Blow molding machinery and tooling involve significant upfront investment, which may not be cost-effective for low-volume medical production.
Complex Shapes: It is less effective for producing intricate or multi-part medical devices. The process is ideal for hollow shapes, limiting its applications to items like bottles or containers.
Sterility Concerns: While possible, maintaining sterility during blow molding can be challenging without additional post-processing or cleanroom environments.
Despite these disadvantages, blow molding remains an efficient choice for producing large volumes of simple, hollow medical components. For more complex or high-precision applications, alternatives like injection molding or 3D printing are often preferred.
Injection blow molding (IBM) and stretch blow molding (SBM) are two distinct processes, each with specific applications in the medical field:
Injection Blow Molding (IBM): This process involves creating a preform through injection molding, which is then transferred to a blow mold where it is inflated to form the final shape. IBM is commonly used for smaller medical containers like vials, bottles, or ampoules. The process ensures high precision and uniform wall thickness, making it suitable for sterile medical packaging.
Stretch Blow Molding (SBM): This technique also begins with an injection-molded preform, but the preform is stretched lengthwise and then inflated in the blow mold. The stretching process enhances the material’s strength and clarity, making SBM ideal for producing lightweight yet durable medical containers such as IV solution bottles.
Key Differences:
Orientation: SBM stretches the material, improving strength and reducing weight. IBM does not stretch the preform.
Applications: SBM is better for larger or clear containers, while IBM is preferred for small, precise medical items.
Material Strength: SBM results in stronger and more durable products due to the biaxial stretching process.
Both processes are widely used in medical manufacturing, with the choice depending on the specific requirements of the product.
An example of blow molding in the medical field is the production of IV solution bottles and single-use medical containers. These hollow plastic containers are essential for storing and dispensing sterile fluids like saline or medication in hospitals and clinics.
Another common example is urine sample bottles or specimen containers, which require precise dimensions and reliable seals to ensure sample integrity. Blow molding efficiently produces these items in large quantities, maintaining cost-effectiveness and quality.
Blow molding is also used to create oxygen masks, a critical component in respiratory care. These masks require lightweight, flexible materials and uniform wall thickness, which blow molding can provide.
For these medical applications, blow molding ensures consistent quality, sterility, and durability, making it an indispensable process in healthcare manufacturing.
Injection molding is widely used in the medical field for producing precision-engineered components and devices. Examples include:
Syringes and Needle Hubs: Disposable syringes are manufactured with tight tolerances to ensure safe and accurate medication delivery.
Surgical Instruments: Handles, grips, and certain components of minimally invasive surgical tools are created using injection molding for precision and durability.
Implantable Devices: Biocompatible materials like PEEK are injection-molded to create parts for orthopedic and dental implants.
Diagnostic Tools: Components of diagnostic devices, such as casings for glucose monitors or lab equipment, are made using this method.
Catheter Components: Small, intricate catheter parts require the precision and consistency injection molding provides.
Injection molding ensures high-quality, sterile, and cost-effective production for medical devices, meeting stringent regulatory standards.
The key differences between blow molding and rotomolding (rotational molding) in medical applications are:
Process:
Blow molding uses air to inflate heated plastic into a mold, creating hollow items like bottles.
Rotomolding rotates molds filled with plastic powder, forming seamless, hollow structures like medical storage tanks.
Precision:
Blow molding provides higher precision for smaller items like IV bottles.
Rotomolding produces larger, less detailed parts with uniform wall thickness.
Applications:
Blow molding is ideal for lightweight, disposable containers.
Rotomolding is used for durable, large-scale items like hospital furniture or equipment casings.
Both methods serve specific needs in healthcare but differ in precision and product type.
The medical molding process involves manufacturing precise, sterile components for healthcare using methods like injection molding, blow molding, or compression molding. The process is tailored to meet stringent regulatory standards such as ISO 13485. Steps include:
Material Selection: Biocompatible and sterilizable materials, such as PEEK, polycarbonate, or medical-grade silicone, are chosen.
Tooling: High-precision molds are designed to ensure exact dimensions and tolerances.
Molding: The chosen method, such as injection molding, shapes the material into the desired form.
Cleanroom Operations: Components are often produced in cleanrooms to prevent contamination.
Post-Processing: Sterilization, assembly, and quality checks are performed to meet medical standards.
This process is vital for producing items like surgical tools, implants, and diagnostic device components.
In the medical field, the two most common types of injection molding processes are thermoplastic injection molding and micro-injection molding. These methods cater to the unique requirements of medical devices, including precision, durability, and biocompatibility.
Thermoplastic Injection Molding:
This process involves melting medical-grade thermoplastics, such as polycarbonate or PEEK, and injecting them into molds to create components. It is commonly used for producing surgical instruments, diagnostic device housings, and disposable items like syringes. Key advantages include scalability, material versatility, and the ability to create complex geometries with tight tolerances. This method is particularly suited for high-volume production, making it cost-effective for mass-producing medical devices.
Micro-Injection Molding:
This specialized process is used for manufacturing extremely small, intricate components with high precision. Micro-injection molding is essential for producing minimally invasive surgical tools, catheter components, and parts for implantable devices. The process ensures consistent quality for components as small as a few millimeters, with tolerances measured in microns.
Both processes are critical in the medical industry for addressing the diverse needs of healthcare applications, from large-scale production to specialized precision components.
In gynecology, “molding” refers to the shaping or alteration of the fetal head during delivery as it adapts to the shape of the birth canal. This is a natural and temporary process that occurs during labor, particularly in vaginal births. The bones of a baby’s skull are not fully fused, allowing the head to compress slightly to pass through the mother’s pelvis.
Key Aspects of Molding in Gynecology:
Physiological Mechanism: The overlapping of cranial bones, such as the frontal and occipital bones, facilitates this process.
Impact on Delivery: Molding reduces the diameter of the fetal head, aiding its passage through the birth canal.
Post-Birth Recovery: The baby’s head typically returns to its normal shape within a few days to weeks after birth.
Molding is an essential aspect of childbirth and is usually harmless. However, in some cases, excessive molding may indicate complications, such as cephalopelvic disproportion, requiring medical intervention.
Advantages:
Precision: Injection molding provides tight tolerances and repeatability, essential for medical devices like implants and diagnostic tools.
Material Versatility: It supports a wide range of biocompatible materials, such as PEEK and medical-grade silicones.
Scalability: Ideal for high-volume production, reducing per-unit costs for disposable items like syringes.
Sterility: Can be performed in cleanroom environments to maintain sterility, critical for healthcare applications.
Complex Designs: Enables the creation of intricate geometries, reducing the need for assembly.
Disadvantages:
High Initial Costs: Tooling and setup expenses are significant, making it less cost-effective for low-volume production.
Material Restrictions: Some materials, like certain thermosets, are incompatible with injection molding.
Lead Time: Designing and manufacturing molds can take weeks to months, delaying production.
Environmental Impact: Use of non-biodegradable plastics contributes to medical waste.
Specialized Equipment: Medical-grade injection molding requires advanced machinery and expertise, increasing operational costs.
Despite these challenges, injection molding remains indispensable for producing high-quality medical devices at scale.
Injection stretch blow molding (ISBM) is a two-stage process commonly used in the medical field to create lightweight, durable, and clear containers. It involves injecting plastic into a preform, which is then heated, stretched, and inflated to form the final product. This process is often used for producing IV solution bottles, sterile fluid containers, and pharmaceutical packaging.
Process Steps:
Injection Molding: A preform is created by injecting molten plastic into a mold.
Heating and Stretching: The preform is reheated and stretched axially using a core rod.
Blow Molding: Compressed air inflates the preform into the desired shape within a blow mold.
The stretching step enhances material strength and clarity, making ISBM ideal for medical packaging that requires durability and transparency.
An example of injection blow molding in the medical field is the production of small vials and ampoules for storing pharmaceutical products. These items require precise dimensions, uniform wall thickness, and high clarity to ensure proper containment and visibility of medications.
Injection blow molding is also used to manufacture sterile dropper bottles, commonly used for eye or ear medications. These bottles need to meet stringent regulatory standards, which injection blow molding achieves by providing consistency and quality.
The process is highly efficient for producing these medical-grade components at scale, ensuring compliance with healthcare requirements while maintaining cost-effectiveness.
Blow molding is widely used in the medical field due to its efficiency in producing lightweight, hollow, and sterile components in high volumes. It is particularly advantageous for manufacturing medical packaging and fluid storage containers. This process offers several benefits tailored to healthcare needs:
Cost-Effective Mass Production: Blow molding allows for the production of large quantities of items like IV solution bottles, reducing per-unit costs.
Sterility: Medical blow molding can be performed in cleanroom environments, ensuring the sterility of products. This is critical for items that come into direct contact with bodily fluids or medication.
Lightweight and Durable Products: The process creates thin-walled containers that are lightweight yet strong, ideal for transporting and storing medical fluids.
Customizable Designs: Blow molding supports a variety of shapes and sizes, accommodating specific medical applications such as specimen containers, urine collection bottles, and oxygen masks.
Material Versatility: Compatible with medical-grade plastics like PET and polypropylene, which are biocompatible and sterilizable.
Blow molding remains a cornerstone of medical manufacturing for its ability to deliver reliable, cost-effective solutions while meeting stringent regulatory requirements.
Rotational molding, or rotomolding, is a process used in the medical field to create large, hollow, seamless components with uniform wall thickness. It is particularly suited for applications requiring durability, such as medical storage tanks, hospital furniture, and casings for medical equipment.
Process Steps:
Loading the Mold: A pre-measured amount of powdered plastic, typically a medical-grade polymer, is placed inside a mold.
Heating and Rotation: The mold is heated in an oven while rotating along two axes. The molten plastic coats the interior of the mold evenly, forming the desired shape.
Cooling: The mold is cooled to solidify the plastic, ensuring consistent wall thickness.
Demolding: The finished part is removed from the mold for inspection and finishing.
Advantages for Medical Use:
Seamless Design: Eliminates weak points, ensuring durability for items like hospital storage units.
Uniform Thickness: Prevents structural weaknesses in medical tanks or containers.
Large Part Capability: Ideal for producing bulky items like patient transport carts or large medical device housings.
Material Compatibility: Can use FDA-approved, biocompatible plastics.
Rotomolding is slower than other processes like injection molding, but its ability to create durable and seamless components makes it invaluable in medical manufacturing.
The medical molding process involves producing high-quality, sterile components and devices for healthcare applications. It relies on precision molding techniques such as injection molding, blow molding, or compression molding to meet strict regulatory standards like ISO 13485 and FDA requirements.
Key Steps in the Medical Molding Process:
Material Selection: Biocompatible materials such as medical-grade PEEK, silicone, or polycarbonate are chosen for their durability and compatibility with sterilization methods.
Tooling: Custom molds are created to achieve the exact dimensions and tolerances required for medical devices.
Molding: The selected process (e.g., injection molding) shapes the material into the desired form under controlled conditions.
Cleanroom Production: Components are often manufactured in cleanroom environments to prevent contamination.
Post-Processing: Includes sterilization, quality testing, and assembly, ensuring that the final products meet healthcare standards.
This process is used to create a wide range of medical devices, from syringes and implants to diagnostic components and surgical tools, ensuring safety, precision, and reliability.
Injection stretch blow molding (ISBM) is a specialized process used in the medical field to produce lightweight, durable, and clear plastic containers. It combines injection molding and blow molding with an additional stretching step, enhancing material strength and clarity.
Applications in Medicine:
IV Solution Bottles: Lightweight, sterile containers for fluids.
Pharmaceutical Packaging: High-clarity bottles for liquid medications.
Diagnostic Containers: Precision-molded containers for laboratory samples.
Key Steps:
Injection Molding: A preform is created using medical-grade plastic.
Stretching: The preform is reheated and stretched both axially and radially to improve mechanical properties.
Blow Molding: Compressed air inflates the stretched preform into its final shape.
This method is favored for its ability to produce strong, clear, and sterile containers essential for medical use.
A prime example of injection blow molding in the medical field is the production of sterile vials for pharmaceutical storage. These vials require high precision to ensure proper sealing and sterility, making injection blow molding an ideal manufacturing method.
Other examples include:
Dropper Bottles: Used for eye or ear medications, requiring uniform dimensions and clear walls.
Ampoules: Small, precise containers for liquid medications.
Sterile Sprayer Bottles: Used for wound cleaning or disinfectant application.
Injection blow molding ensures consistent quality and compliance with medical standards, making it indispensable for healthcare packaging.
Contact our professional team now for a same-day quote and risk-free project evaluation. Benefit from ISO 8 cleanrooms, advanced machines, and 12-hour fast response in medical injection molding.