CNC machining, or Computer Numerical Control machining, plays a crucial role in the medical industry by enabling the production of high-precision, custom medical devices. Medical CNC machining offers advanced manufacturing capabilities, allowing for the creation of intricate and personalized components such as surgical tools, implants, and prosthetics. Precision is paramount in this field, as medical devices must meet stringent safety standards and function seamlessly within the human body. This process allows for the customization of implants and tools to better suit individual patient needs, significantly improving patient outcomes. Medical CNC Machining offers speed and precision produce high-grade surgical instruments, components for medical machines. Additionally, precision mold medical components are vital in ensuring the accuracy and functionality of various medical devices. In this blog, we will explore various medical CNC machining jobs and how they contribute to innovations in healthcare, driving efficiency and accuracy in medical applications.
Low-Volume to High-Volume Production Capabilities
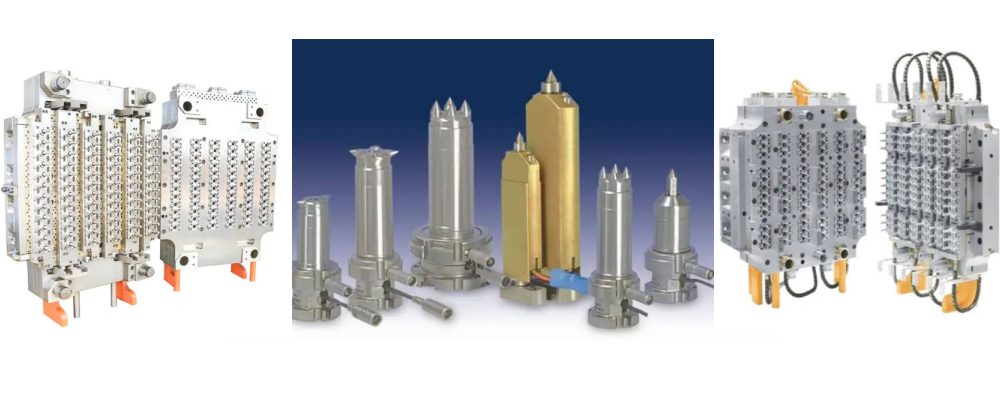
Attribute | Description |
---|---|
Type | Medical CNC Machining |
Brand Name | LY Medical Injection Mold |
Place of Origin | Dongguan, Guangdong, China |
Materials Supported | Aluminum, Brass, Bronze, Copper, Hardened Metals, Precious Metals, Stainless Steel, Steel Alloys, Titanium, POM |
CNC Machining Capabilities | CNC Turning, Milling, Drilling, Broaching, Laser Machining, Etching, Wire EDM, Rapid Prototyping |
Micro Machining | Available |
Equipment | 3/4/5 Axis CNC Machining Centers |
Surface Treatments | Anodizing, Powder Coating, Plating, Polishing, PVD Coating, Nickel Plating, Zinc Plating, Chrome Plating |
Tolerance | +/-0.01mm |
Certifications | ISO9001:2008, TS16949 |
Applications | Medical Devices |
MOQ | 1 Piece, Small Orders Accepted |
Delivery Time | 7-15 Days |
Packaging | PE Box, PVC Box, Corrugated Box, Custom Packaging |
Processing Service | CNC Machining, Milling, Turning, Grinding, EDM Wire Cutting |
Customization | OEM/ODM Services, Customer-Specific Materials and Dimensions |
Features | Rapid Prototyping, Heat Treatment Supported, High Precision |
What is Medical CNC Machining?
Definition of CNC Machining
CNC (Computer Numerical Control) machining is an advanced manufacturing process that uses computers to control machine tools like lathes, mills, routers, and grinders. In the medical industry, medical CNC machining is employed to create high-precision parts and components essential for medical applications. The process involves translating CAD (Computer-Aided Design) models into machine instructions, ensuring that each part is fabricated to the exact specifications required. This level of precision is critical in the medical field, where small deviations can result in serious consequences. Additionally, medical molding is often used alongside CNC machining to create intricate components that require specific shapes or materials, further enhancing the customization and precision needed in medical devices.
Common Processes in Medical CNC Machining
The medical CNC machining process involves several key techniques to produce various medical components:
- Cutting: Using rotating tools to cut through materials, creating parts with complex geometries required for surgical tools or implants.
- Milling: This involves the use of a rotating tool to remove material from a workpiece, often used in the creation of custom prosthetics or orthopedic implants.
- Turning: CNC turning, or the turning of medical parts, involves rotating the workpiece against a cutting tool, ideal for cylindrical medical components such as needles or tubing.
- Drilling: Drilling is used to create precise holes in materials for parts like screws or joints used in implants and other medical devices.
- Grinding: CNC grinding ensures that parts have smooth finishes and the required precision, especially important for implants or medical devices that interact with human tissue.
- Polishing: Polishing removes any rough edges or surface imperfections, essential in ensuring the smoothness of medical device components to avoid irritation or injury when implanted.
Benefits of Medical CNC Machining
High Accuracy and Consistency
One of the main advantages of CNC machining for medical is its ability to achieve high accuracy. CNC machines operate with precise control, ensuring that every part meets the exact specifications. This is crucial for medical devices, where even slight variations can result in malfunctions or complications. For example, surgical instruments must have exact measurements for functionality and safety.
Cost-Effective for Small and Large Production Runs
CNC machining is particularly advantageous for both low-volume and mass production. Whether it’s producing a small batch of custom implants or a large order of standardized surgical tools, medical CNC machining ensures cost-efficiency without compromising quality. For example, producing a custom-made prosthetic limb may be more cost-effective through CNC machining than traditional methods, reducing overall healthcare costs.
Flexible Material Choices
The flexibility in material selection is another key benefit. CNC machining can work with a wide range of materials, such as medical-grade stainless steel, titanium, PEEK (Polyether ether ketone), and other specialized plastics and alloys. This enables the production of diverse medical devices tailored to specific patient needs. For instance, titanium implants, which are biocompatible and strong, can be easily manufactured using CNC machining, ensuring high performance and patient safety.
Precision and Customization for Medical Applications
The precision of medical CNC machining also allows for the customization of medical devices and components to meet the unique needs of individual patients. For example, dental implants, which require precise dimensions to fit a patient’s jaw, can be customized using CNC machining to ensure a perfect fit, improving both functionality and comfort. This ability to personalize products based on patient-specific requirements is revolutionizing healthcare by ensuring better treatment outcomes.
Reduced Production Time and Increased Efficiency
Another benefit of CNCmachining medical is the reduction in production time. By automating the manufacturing process, CNC machines can produce components at a much faster rate compared to traditional methods. This is especially beneficial in medical fields where time-sensitive procedures, like surgeries requiring implants, need to be carried out promptly. For example, CNC machining can produce a batch of surgical instruments in a fraction of the time it would take with manual labor, thus improving hospital workflow and reducing waiting times for patients.
Quality Control and Reliability
Quality control is an essential aspect of medical CNC machining, particularly in the medical industry, where product failure can result in severe consequences. CNC machines are capable of producing highly consistent parts that meet stringent quality standards. Additionally, the integration of advanced inspection systems during the machining process ensures that every component is checked for accuracy and performance. For example, implantable devices like hip replacements undergo rigorous testing to meet safety and regulatory standards, ensuring that they will function correctly and last as required.
Challenges of Medical CNC Machining
Despite its numerous advantages, medical device machining does come with some challenges. One major difficulty is the need for specialized materials that meet strict medical regulations, such as biocompatibility and sterilization standards. Additionally, the cost of advanced CNC machines can be high, particularly for smaller manufacturers or healthcare facilities. However, these costs can be offset by the long-term benefits, such as reduced labor costs and increased production speed, making CNC machining a viable option for medical device manufacturing.

Medical CNC Machining: Materials Used in CNC Medical Machining
Metals Used in Medical CNC Machining
Medical CNC machining relies heavily on specific metals that provide the necessary strength, durability, and biocompatibility for medical applications. Stainless steel is one of the most commonly used metals due to its excellent corrosion resistance, making it ideal for surgical instruments and implants that need to withstand exposure to bodily fluids. Stainless steel is also known for its strength and longevity, which is critical in medical devices that must perform under stress for extended periods.
Titanium is another popular metal choice in medical CNC machining. It is known for its high strength-to-weight ratio and exceptional resistance to corrosion, which makes it perfect for implants, such as joint replacements, dental implants, and spinal devices. Additionally, titanium is biocompatible, meaning it integrates well with human tissue, reducing the risk of rejection by the body. The ability to machine titanium to precise specifications ensures that these implants fit perfectly and function effectively in medical treatments.
Medical-grade alloys, such as titanium alloys and cobalt-chromium alloys, are also commonly used in CNC machining for medical applications. These materials are specifically designed to meet the demands of the medical field, providing not only durability but also resistance to wear, making them ideal for devices that require high-performance over long periods.
Plastics Used in Medical CNC Machining
In addition to metals, medical CNC machining also utilizes advanced plastics that are capable of withstanding high temperatures and harsh chemical environments. PEEK (Polyether Ether Ketone) is one such plastic that offers exceptional strength and stability at elevated temperatures, making it ideal for components used in medical devices, such as orthopedic implants and surgical instruments. PEEK is also known for its biocompatibility, making it a popular choice for implants and devices that need to be in contact with human tissue.
Another commonly used plastic in medical CNC machining is PEI (Polyetherimide), which has excellent chemical resistance and dimensional stability. PEI is used in medical applications where the components may be exposed to cleaning chemicals, autoclave sterilization, or other harsh environments. Its high strength and resistance to impact make it a reliable material for devices that need to maintain structural integrity over time, such as housings for diagnostic equipment or protective covers for surgical tools.
These high-performance plastics allow manufacturers to create lightweight yet durable components for a wide variety of medical devices, reducing the overall weight of the equipment without compromising on strength or safety.
Ceramics and Composites in Medical CNC Machining
Ceramics are another important material used in medical CNC machining. Ceramics, such as alumina and zirconia, are valued for their exceptional hardness, wear resistance, and biocompatibility. These materials are frequently used in dental implants, bone substitutes, and other medical devices that require high strength and resistance to degradation over time. Ceramics also offer the advantage of being non-reactive with bodily fluids, which makes them ideal for long-term use in the body without causing adverse reactions.
In addition to ceramics, composite materials are gaining popularity in the medical CNC machining industry. Composites like carbon fiber-reinforced polymers and glass fiber composites are used in specialized applications where lightweight yet strong materials are required. These composites combine the best characteristics of different materials to achieve superior performance in specific medical applications, such as prosthetics or orthopedic implants. The ability to tailor composite materials to meet the precise requirements of a medical device or implant ensures optimal performance and longevity.
For example, carbon fiber-reinforced polymers are frequently used in prosthetic limbs, as they are strong, lightweight, and flexible. This allows for the creation of prosthetics that closely mimic the movement and function of a natural limb, improving comfort and mobility for the wearer.
Custom Material Choices for Specialized Medical Applications
The versatility of medical CNC machining in working with a wide range of materials allows for the creation of highly specialized devices tailored to meet the unique requirements of different medical fields. For example, some medical devices require radio-opaque materials that can be easily detected in X-ray imaging. In such cases, materials like barium sulfate-filled plastics are used to make components that will not interfere with medical imaging processes while still providing the necessary structural strength.
Similarly, for applications that require electromagnetic shielding, materials like mu-metal or conductive plastics are selected to ensure that medical devices such as pacemakers and diagnostic equipment are protected from electromagnetic interference. This level of customization is only possible through the use of advanced CNC machining techniques, which can work with a diverse range of materials to create highly specialized parts.
Biocompatibility and Regulatory Considerations
When selecting materials for medical CNC machining, biocompatibility is a key factor that cannot be overlooked. Medical devices and implants must meet stringent standards to ensure they do not cause harm when in contact with the human body. Materials like titanium, PEEK, and certain ceramics are chosen for their proven track record of being safe for implantation, reducing the risk of rejection or adverse reactions.
Furthermore, regulatory standards, such as ISO 13485 for medical devices, require manufacturers to ensure that the materials used in medical CNC machining are not only biocompatible but also meet specific performance and quality criteria. These standards help ensure that the materials used will function as intended throughout their life cycle in the human body.
Cost-Effectiveness and Material Selection
Choosing the right materials for medical CNC machining also plays a crucial role in cost-effectiveness. While high-performance metals like titanium and specialized plastics like PEEK can be expensive, the ability to manufacture medical devices with precision using CNC machining reduces waste and ensures that parts are produced to exact specifications. This reduces the need for extensive post-processing and rework, ultimately lowering the cost of production. Additionally, the high efficiency and low material waste associated with CNC machining processes help optimize production costs without compromising on quality or performance.
In cases where cost is a significant concern, manufacturers may opt for alternative materials such as stainless steel or PEI, which offer a good balance of strength, durability, and cost-effectiveness for less critical applications. The availability of a wide range of materials ensures that manufacturers can meet the demands of different medical applications while adhering to budget constraints.
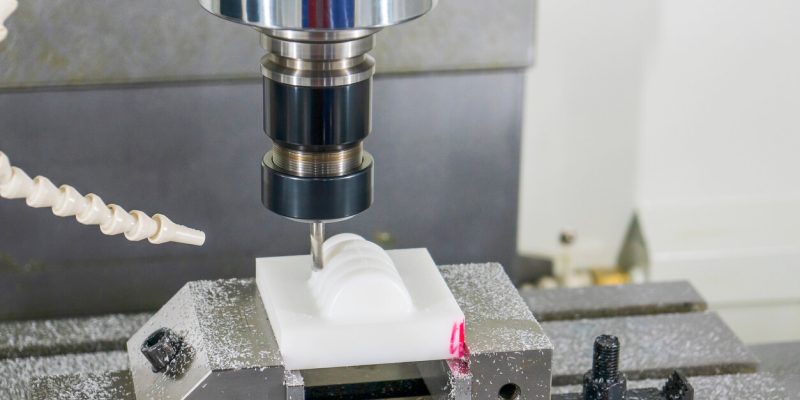
Key Applications of CNC Machining Medical
Surgical Tools
One of the most critical applications of medical CNC machining is in the production of surgical tools. Tools like scalpels, forceps, retractors, and instruments for minimally invasive surgeries require extreme precision to ensure safety and effectiveness during operations. CNC machining allows for the consistent production of these tools with tight tolerances and sharp edges, ensuring that they meet the stringent standards required for medical use. The ability to create complex geometries and intricate designs using CNC machining makes it ideal for producing specialized instruments that are essential in delicate surgeries, such as those in neurosurgery or ophthalmology. Moreover, CNC machining offers the advantage of quick production cycles, which is essential when hospitals need to replenish their surgical tool inventory swiftly.
Medical Devices and Components
Medical CNC machining is also widely used in manufacturing various medical devices and components. This includes critical components for devices such as pacemakers, diagnostic tools, and ventilator components. For example, pacemakers need to be made from biocompatible materials and require exceptional precision to function correctly within the human body. CNC machining ensures that these components are manufactured to the highest standards, ensuring long-term reliability and safety. Additionally, components for diagnostic equipment like MRI machines and CT scanners are also made using CNC machining, where precision and durability are paramount. The versatility of CNC machining allows manufacturers to work with a wide variety of materials to create components that meet medical regulatory standards and enhance device performance.
Implants
In the medical industry, implants play a crucial role, and medical machining is vital in their creation. Orthopedic implants, such as joint replacements, dental implants, and spinal implants, require a high degree of customization to fit individual patient needs. CNC machining ensures that each implant is designed and manufactured to the exact specifications, minimizing the risk of complications and improving patient outcomes. For instance, a CNC-machined orthopedic implant can be designed to match the unique anatomy of a patient’s joint, ensuring optimal fit and function. CNC machining’s ability to handle various materials, such as titanium and stainless steel, makes it ideal for producing durable and biocompatible implants.
Prosthetics
The development of prosthetics is another significant application of medical CNC machining. Prosthetic limbs and devices are often customized to meet the specific needs of patients, ensuring enhanced comfort and performance. CNC machining allows for the precise creation of these custom parts, from the socket that fits the patient’s residual limb to the components that simulate the natural movement of the body. For example, a custom-designed prosthetic limb made with CNC machining can be fitted more comfortably, improving the patient’s mobility and quality of life. CNC machining’s flexibility enables manufacturers to create prosthetics that incorporate a variety of materials, including lightweight alloys and flexible plastics, further enhancing the prosthetic’s functionality and comfort.
Enclosures and Housings
Another essential application of medical CNC machining is the creation of enclosures and housings for medical devices. Devices like MRI machines, CT scanners, and lab analyzers require durable and precise enclosures to protect their sensitive internal components. CNC machining provides the high precision needed to create these housings with the exact measurements required to shield the devices from external impacts while ensuring easy access for maintenance and repair. The ability to machine complex geometries, including ventilation systems and cable channels, is crucial for designing enclosures that are both functional and protective. Furthermore, medical CNC machining allows manufacturers to use a wide range of materials, from stainless steel to specialized plastics, to meet the various requirements of medical device housings. In addition to machining, medical enclosure molding plays a significant role in creating customized housings. This process allows for the mass production of enclosures with intricate details and tight tolerances, which is critical for the manufacturing of medical devices that require both protection and precision in design.
Microdevices
Medical CNC machining is also used to produce microdevices such as biosensors, diagnostic systems, and wearable health technology. These microdevices often require extreme precision to function effectively, as even the slightest deviation in size or shape can cause malfunctions. CNC machining allows for the creation of tiny, complex components with high accuracy, making it ideal for the production of microdevices. For instance, CNC machining is used to produce biosensors that monitor various health parameters like blood sugar levels, heart rate, and oxygen saturation. These devices are critical in providing real-time data that can improve patient care and enable early diagnosis. Additionally, wearable health technology, such as fitness trackers and smartwatches, also benefits from the precision and customization offered by medical CNC machining. This enables the production of lightweight, comfortable, and durable devices that continuously monitor the wearer’s health.
Medical CNC Machining Components
Medical CNC (Computer Numerical Control) machining plays a vital role in the healthcare industry by manufacturing precise, high-quality components used in medical devices, implants, and surgical tools. These components require extreme precision, reliability, and biocompatibility to meet strict medical standards and regulations.
Key Features of Medical CNC Machining Components
- High Precision
Medical components often demand tight tolerances, typically in the range of ±0.001 mm. CNC machining ensures consistent accuracy, which is critical for implants and devices that interact with the human body. - Biocompatible Materials
Common materials include titanium, stainless steel, cobalt-chromium alloys, and medical-grade plastics like PEEK and UHMWPE. These materials are chosen for their strength, durability, and compatibility with the human body. - Complex Geometries
Medical components often have intricate designs, such as those required for orthopedic implants or minimally invasive surgical tools. CNC machines can handle complex shapes and surface finishes with ease. - Surface Finishing
Advanced surface treatments such as polishing, anodizing, and coating are applied to CNC-machined parts to ensure smoothness, durability, and corrosion resistance, particularly for implants and tools used in sterile environments.
Applications of Medical CNC Machining Components
- Surgical Instruments
CNC machining produces scalpels, forceps, clamps, and other precision tools used in surgeries. These tools must be sharp, ergonomic, and easy to sterilize. - Orthopedic Implants
Components like hip and knee replacements, spinal implants, and screws for bone fixation are manufactured using CNC machining. The biocompatibility and mechanical strength of these parts are crucial for patient safety and functionality. - Dental Implants and Tools
Dental applications include crowns, bridges, abutments, and surgical guides. CNC machining ensures that these components fit precisely and are durable enough to withstand long-term use. - Cardiovascular Devices
CNC machining is used to create parts for pacemakers, stents, and heart valves, which require exceptional precision and reliability. - Diagnostic Equipment
High-precision components for MRI machines, CT scanners, and other diagnostic tools are also manufactured using CNC machining.
Medical CNC machining is a cornerstone of modern healthcare manufacturing, providing the precision, reliability, and scalability needed for cutting-edge medical devices and implants. Its versatility and continual advancements ensure its essential role in meeting the evolving demands of the medical industry.
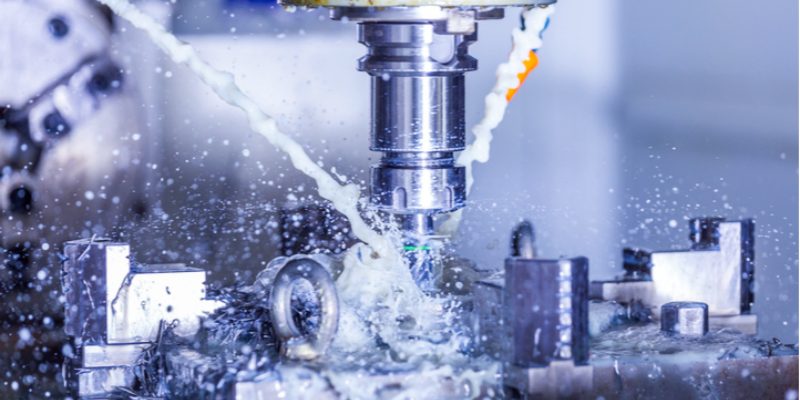
Medical CNC Machining Methods
Medical CNC machining employs a variety of advanced techniques to manufacture high-precision components for medical devices, implants, and surgical tools. These methods are tailored to meet the stringent requirements of the healthcare industry, including tight tolerances, biocompatibility, and complex geometries. Below is an overview of the primary CNC machining methods used in the medical field.
CNC Milling
CNC milling is one of the most widely used machining methods in the medical industry.
- Process: A rotating cutting tool removes material from a workpiece to create the desired shape. The process can handle complex geometries and tight tolerances.
- Applications:
- Orthopedic implants (e.g., knee and hip replacements)
- Surgical instruments
- Dental components (e.g., crowns, abutments)
- Advantages:
- High precision and repeatability
- Ability to machine complex 3D shapes
- Versatility in materials
CNC Turning
CNC turning is ideal for producing cylindrical or symmetrical components.
- Process: The workpiece rotates while a stationary cutting tool removes material to shape the part.
- Applications:
- Bone screws
- Pins and rods for orthopedic fixation
- Catheter components
- Advantages:
- High-speed production of round components
- Excellent surface finishes
- Cost-efficient for high-volume production
Swiss CNC Machining
Swiss machining is a specialized form of CNC turning, particularly suited for small and intricate components.
- Process: The workpiece is held and guided by a collet close to the cutting tool, providing superior stability and precision.
- Applications:
- Micro-surgical instruments
- Stent components
- Miniature screws and pins
- Advantages:
- Exceptional precision for small parts
- Capability to produce complex, detailed designs
- Minimal material waste
5-Axis CNC Machining
5-axis machining offers unmatched versatility and precision by allowing the cutting tool to move along five different axes simultaneously.
- Process: The additional axes enable the machining of intricate shapes and undercuts without repositioning the workpiece.
- Applications:
- Complex implants (e.g., spinal cages, cranial plates)
- Advanced surgical tools
- Custom prosthetics
- Advantages:
- Ability to create highly complex geometries
- Reduced production time due to fewer setups
- Enhanced surface finishes
Electrical Discharge Machining (EDM)
EDM is used to produce extremely fine details and features in hard materials.
- Process: Material is removed by electrical discharges (sparks) between a workpiece and an electrode, which does not involve direct contact.
- Applications:
- Intricate surgical instruments
- Mold-making for medical device components
- Components with narrow tolerances and fine features
- Advantages:
- High precision and accuracy
- No mechanical stress on the workpiece
- Capability to machine extremely hard materials
Laser Machining
Laser machining uses focused laser beams to cut, drill, or engrave materials with precision.
- Process: The laser beam heats and vaporizes material to create the desired shape or feature.
- Applications:
- Micro-hole drilling in surgical tools
- Cutting of biocompatible materials
- Surface engraving for part identification
- Advantages:
- Non-contact process reduces contamination risks
- High precision for micro-sized features
- Ability to process delicate and thin materials
Micro-Machining
Micro-machining techniques are specifically designed for producing miniature components with high precision.
- Process: Specialized tools and processes are used to achieve extremely small features.
- Applications:
- Micro-surgical instruments
- Components for minimally invasive devices
- Tiny screws and fasteners
- Advantages:
- Sub-micron level accuracy
- High-quality surface finishes
- Suitable for highly detailed designs
Waterjet Cutting
Waterjet cutting uses a high-pressure stream of water mixed with abrasive materials to cut through various materials.
- Process: The high-pressure waterjet erodes the material to achieve the desired shape.
- Applications:
- Cutting implants from raw materials
- Shaping medical-grade plastics and metals
- Creating prototypes for testing
- Advantages:
- No thermal distortion or heat-affected zones
- Environmentally friendly with minimal waste
- Suitable for a wide range of materials
Additive Manufacturing Integration
Though not strictly CNC machining, additive manufacturing (3D printing) is increasingly combined with CNC machining to produce medical components.
- Process: A part is initially 3D-printed and then refined using CNC machining for better precision and surface quality.
- Applications:
- Custom prosthetics
- Patient-specific implants
- Complex surgical guides
- Advantages:
- Combines speed of 3D printing with precision of CNC machining
- Reduces material waste
- Supports highly complex designs
Each CNC machining method in the medical field serves specific purposes, allowing manufacturers to create components with unmatched precision, reliability, and quality. As technology advances, these methods will continue to evolve, supporting the development of innovative medical devices and improving patient care.
Medical CNC Machining: The Role of CNC Machining in Medical Testing
Precision Testing Tools in Medical CNC Machining
One of the most significant roles of medical CNC machining is the creation of precision testing tools used in diagnostic equipment and lab analyzers. Precision is crucial in medical testing, as even the smallest error can lead to incorrect diagnoses and ineffective treatments. CNC machining offers unparalleled accuracy in crafting tools like test tubes, syringes, pipettes, and blood vials that are essential in diagnostic procedures. The high precision of CNC machining ensures that these tools are produced to exact specifications, which helps guarantee consistent performance in diagnostic labs.
Moreover, medical CNC machining is used to produce components for testing devices such as thermometers, glucometers, and other diagnostic machines. These devices rely on accurate sensors and components to deliver precise results, making the role of CNC machining essential in ensuring that each part functions optimally. For instance, components such as sensors and probes, which require intricate details and exact measurements, are fabricated with the utmost accuracy using CNC technology.
Customization for Nursing and Testing Needs
Another critical aspect of medical CNC machining is its ability to provide customized solutions tailored to specific nursing and testing needs. Medical professionals often require specialized tools and equipment to carry out unique diagnostic tests or manage patients with specific conditions. CNC machining allows manufacturers to design and produce bespoke components that meet these needs, ensuring the highest standards of performance.
For example, CNC machining can be used to create customized surgical instruments that are designed to meet the precise demands of a particular procedure. Whether it’s the length of a needle or the angle of a scalpel, CNC technology enables customization to meet exacting requirements. Additionally, nursing tools, such as specialized forceps, clamps, and retractors, can be made using CNC machining for precise functionality and ease of use in patient care settings.
Customized components for testing equipment can also be created through medical CNC machining. For example, if a new diagnostic machine requires a unique component for better performance or ease of use, CNC machining can rapidly produce a prototype and subsequent production units tailored to the specific design and functional needs of the device. This adaptability is essential in the fast-paced world of medical testing, where new technologies and needs arise frequently.
High-Volume Production and Efficiency
Another advantage of medical CNC machining in medical testing is its ability to support high-volume production while maintaining quality. Once a design has been finalized, CNC machines can replicate the production of components with a high level of consistency and speed, making it possible to meet the demands of large-scale testing operations. This is particularly important for medical testing facilities that need to produce large quantities of diagnostic tools, such as blood tests or urine collection devices, with minimal lead time.
High-volume production also reduces the overall cost per unit, making these specialized tools more affordable. CNC machining can mass-produce diagnostic and testing components with minimal human intervention, which helps reduce errors and increases operational efficiency. This combination of high-volume production and precision makes medical CNC machining indispensable in the medical testing industry.
Material Considerations for Testing Equipment
The materials used in medical CNC machining for testing tools are crucial for maintaining both functionality and safety. For diagnostic tools that come into contact with patients, biocompatibility is a key consideration. Stainless steel, medical-grade plastics, and ceramics are commonly used in CNC machining because of their resistance to corrosion and their ability to withstand sterilization processes like autoclaving. These materials ensure that diagnostic equipment remains sterile and safe for repeated use in various medical environments.
For example, the use of stainless steel in test tubes and syringes ensures that the equipment is durable, resistant to breakage, and free from contamination. Plastics like PEEK (Polyether Ether Ketone) are favored for diagnostic equipment components that need to be lightweight yet chemically resistant. These materials provide a balance of strength, biocompatibility, and resistance to wear, ensuring that medical CNC machining parts remain functional over time.
Adaptability to Emerging Medical Testing Technologies
As medical testing technologies evolve, medical CNC machining plays an essential role in adapting to these changes. With the development of new diagnostic methods, such as point-of-care testing and wearable health technology, CNC machining enables manufacturers to produce the custom components required to support these advancements. Whether it’s the tiny sensors used in biosensors or the specialized enclosures for portable diagnostic devices, medical CNC machining allows manufacturers to keep pace with innovations in medical technology, including customized precision medical apparatus components.
For example, in the development of wearable health technology, CNC machining is used to create the small, intricate parts needed for devices like glucose monitors, heart rate monitors, and blood oxygen sensors. These devices must be both compact and precise, which makes CNC machining a perfect fit for producing their components. With the continued advancement of personalized medicine and real-time diagnostics, medical CNC machining will continue to be at the forefront of producing components that enable these cutting-edge technologies.
Improved Safety and Reliability of Testing Equipment
In medical testing, reliability and safety are paramount. A failure in testing equipment can lead to serious consequences, including misdiagnosis or incorrect treatment. With medical CNC machining, manufacturers can ensure that each part meets stringent safety standards by using high-quality materials and precision fabrication methods. The repeatability of CNC machines means that each component is produced with exact consistency, reducing the chance of defects and increasing the overall reliability of medical testing devices.
For instance, in blood test analyzers, even the smallest malfunction or error in the manufacturing process can lead to faulty readings. By using medical CNC machining, manufacturers can ensure the consistent quality of components such as test chambers or fluidic paths. This results in more accurate test results, which is crucial for the health and safety of patients. Furthermore, CNC machining helps reduce the likelihood of contamination, as parts are made to precise tolerances and undergo thorough quality control checks.
Medical CNC Machining for the Medical Industry
Revolutionizing Healthcare Manufacturing
CNC machining for the medical industry has revolutionized the way medical devices and components are manufactured. With its ability to produce highly precise and intricate parts, CNC machining allows for the creation of customized solutions tailored to the specific needs of medical applications. The high precision achieved by CNC machines is essential for ensuring that medical precision components and devices meet strict regulatory standards and perform reliably in clinical settings. Whether for surgical instruments, implants, or diagnostic tools, CNC machining for the medical industry ensures that every component is crafted to the exact specifications required for optimal performance.
Precision and Customization
CNC machining for medical devices offers an unparalleled level of precision and customization, both of which are crucial for the development of functional, effective, and safe medical devices. With CNC machining and high precision tools for medical device manufacturing, medical device manufacturers can produce highly intricate parts that meet exacting specifications, whether for implantable devices, prosthetics, or surgical tools. The customization aspect of CNC machining is particularly important in the production of bespoke medical devices, such as custom implants or tailored prosthetics, which need to fit the individual needs of patients.
CNC machining’s ability to create parts with high repeatability and consistency makes it ideal for mass production of medical devices as well. For example, in the case of pacemakers, ventilator components, or stents, CNC machining ensures that each part is produced to the same high standard, reducing the risk of defects and ensuring that the devices perform reliably in life-critical applications.
Furthermore, CNC machining allows for the production of multi-material medical devices, incorporating components made from different materials such as stainless steel, titanium, ceramics, and plastics. This versatility is crucial for creating complex medical devices with multiple functions or requiring biocompatibility and strength.
Meeting the Demands of the Healthcare Sector
Medical CNC machining services are tailored to meet the specific needs of healthcare providers, device manufacturers, and research institutions. These services offer a wide range of solutions, from rapid prototyping to mass production of precision components for medical devices. With the increasing demand for innovative medical technologies, CNC machining services play a crucial role in delivering high-quality, cost-effective solutions that meet the evolving needs of the healthcare sector.
One of the key features of medical CNC machining services is their ability to provide customized parts and rapid prototyping. This is especially valuable in the development of new medical technologies, where quick turnaround times and the ability to test and refine designs are essential for successful product development. Whether it’s a new type of diagnostic equipment, surgical instrument, or implantable device, CNC machining services allow manufacturers to bring ideas to life quickly and efficiently.
Additionally, medical CNC machining services ensure that all components are manufactured to the highest standards of quality and precision. Service providers often follow rigorous quality control procedures, ensuring that every part meets FDA and ISO standards for medical devices. This adherence to strict regulations is vital for ensuring the safety and effectiveness of medical products and maintaining the trust of healthcare professionals and patients alike.
Key Benefits of CNC Machining for Medical Devices and Services
The integration of CNC machining into the production of medical devices offers several significant benefits that contribute to the advancement of healthcare technology:
Unmatched Precision
CNC machining allows for the production of microscopic components with exceptional precision, ensuring that medical devices perform as intended without compromising on safety or functionality.
Cost-Effectiveness
CNC machining is cost-effective, particularly for small to medium production runs. It reduces the need for expensive tooling and molds, which is particularly beneficial for medical device manufacturers who need to create complex parts with minimal waste.
Versatility
The ability to use a variety of materials, including metals, plastics, and composites, makes CNC machining incredibly versatile. Medical device manufacturers can tailor components to meet specific needs, whether it’s for biocompatibility, strength, or lightweight performance.
Rapid Prototyping and Design Iteration
CNC machining is ideal for rapid prototyping, enabling manufacturers to quickly test and modify designs. This is essential in the medical field, where device testing and iterations must be completed swiftly to meet market demands.
Enhanced Production Efficiency
Once the design is finalized, CNC machining can produce large quantities of parts with minimal human intervention, ensuring consistent quality and reliability in every product.
Limitations of Medical CNC Machining
While CNC machining offers unparalleled precision and reliability for the production of medical components, it also has some limitations that manufacturers must consider. These challenges can impact the efficiency, cost, and feasibility of certain medical applications.
High Initial Costs
- Problem: CNC machines and their supporting software are expensive to purchase and maintain.
- Impact: The high upfront investment can increase the cost of medical components, especially for smaller production runs or custom devices.
- Mitigation: Spreading costs over large production volumes or leveraging contract manufacturing services can help offset expenses.
Material Constraints
- Problem: Not all materials are suitable for CNC machining. Some biocompatible materials, such as ceramics, are difficult to machine due to their brittleness.
- Impact: Limited material options may restrict the design and functionality of medical devices.
- Mitigation: Exploring alternative manufacturing methods (e.g., additive manufacturing or EDM) for challenging materials.
Complexity and Geometrical Limitations
- Problem: While CNC machines can handle complex designs, certain geometries, such as deep internal cavities or sharp undercuts, are challenging or impossible to machine.
- Impact: Design restrictions may require adjustments that compromise the ideal functionality of medical components.
- Mitigation: Combining CNC machining with other technologies, such as 3D printing or multi-axis machining, can address some of these challenges.
Time-Intensive for Prototyping
- Problem: Although CNC machining is efficient for production, it may not be the fastest option for initial prototyping due to programming and setup times.
- Impact: Delays in prototyping can slow down the development cycle for new medical devices.
- Mitigation: Rapid prototyping methods like 3D printing can be used for preliminary testing, followed by CNC machining for final precision.
Waste Generation
- Problem: CNC machining is a subtractive process, which generates significant material waste, especially when working with expensive medical-grade materials.
- Impact: Waste increases costs and environmental concerns, particularly for high-value materials like titanium.
- Mitigation: Optimizing machining paths and using near-net-shape materials can reduce waste.
Medical CNC machining is a cornerstone of modern medical manufacturing, but it is not without limitations. Understanding these challenges and employing strategies to mitigate them ensures that manufacturers can produce high-quality components efficiently and cost-effectively. Combining CNC machining with other manufacturing techniques and innovations can further enhance its capabilities, meeting the evolving demands of the healthcare industry.
FAQs about Medical CNC Machining
A CNC machine (Computer Numerical Control) in the medical field refers to a high-precision manufacturing tool that is used to create components for medical devices, surgical instruments, and implants. These machines are controlled by a computer program, allowing them to produce complex parts with exceptional accuracy and consistency. CNC machining is used in medical applications to manufacture a wide range of items, including surgical instruments, prosthetics, orthopedic implants, and diagnostic equipment.
In the medical field, CNC machines can process various materials such as stainless steel, titanium, plastics, ceramics, and composites, which are essential for ensuring the safety and functionality of medical devices. These machines are capable of executing processes like cutting, milling, turning, and grinding with high precision. One of the primary benefits of CNC machining in medicine is the ability to customize components to meet the unique needs of individual patients, especially for items like custom implants and prosthetics.
CNC machining in the medical industry also supports rapid prototyping and the manufacturing of small or large production runs with minimal variation in quality. This makes CNC machines crucial for the development of innovative medical technologies and the efficient production of life-saving devices.
In healthcare, CNC (Computer Numerical Control) refers to a technology used for precision manufacturing of medical devices and components. CNC machines are automated systems that use computer programs to control the movements of tools in manufacturing equipment. These machines are utilized in healthcare to produce highly accurate and specialized parts for medical devices, surgical tools, diagnostic equipment, and implants.
One key benefit of CNC in healthcare is its ability to meet the stringent requirements for biocompatibility, sterility, and accuracy. CNC machining ensures that medical products, such as scalpels, surgical forceps, and joint implants, are made with the exact measurements required to ensure patient safety and device functionality.
The use of CNC machines in healthcare also extends to the rapid prototyping of new medical devices, enabling manufacturers to quickly test and refine designs before full-scale production. This leads to faster development cycles for innovative medical solutions. CNC technology is also widely used for manufacturing precision parts for diagnostic machines like MRI scanners and CT machines, enhancing the accuracy and performance of medical imaging and testing.
CNC machining is widely used to manufacture a variety of surgical instruments that require high precision and reliability. Some of the most common surgical instruments made by CNC machining include:
Scalpels: CNC machines are used to cut high-quality scalpel blades with the exact dimensions and sharpness needed for surgical procedures.
Forceps: Surgical forceps, which are used to grasp, hold, or manipulate tissue during surgery, are made with CNC machines for precision and strength.
Retractors: Surgical retractors help surgeons expose underlying tissues and organs by gently pulling back the skin or muscles. These instruments are crafted with fine tolerances using CNC.
Needles: CNC machining produces precision needles for injections, sutures, and biopsy procedures.
Surgical drills and cutting tools: CNC machining is also employed in creating surgical tools like drills and cutting blades for procedures like bone surgery or tissue removal.
The use of CNC technology ensures that these surgical instruments meet the exact specifications required for safe and effective use in medical environments. Additionally, CNC machining allows for customization of instruments to meet the needs of specific surgical procedures or patient requirements.
Furthermore, CNC machining contributes to the mass production of surgical tools, maintaining consistency across all manufactured items while reducing production costs. This is especially important for hospitals and clinics that require high-volume production of medical instruments.
In the pharmaceutical industry, CNC stands for Computer Numerical Control, just as it does in other sectors. CNC technology in pharmaceuticals is used primarily for precision manufacturing and processing of equipment, tools, and components for drug production, packaging, and laboratory testing. CNC machines are widely used in the creation of molds and components for pharmaceutical packaging machines, tablet press machines, and capsule filling systems.
CNC technology helps improve the production of pharmaceutical equipment by allowing manufacturers to create highly intricate parts with minimal tolerance errors. This is essential in producing machinery that must adhere to the stringent standards set by pharmaceutical regulators like the FDA. CNC machines also help ensure that pharmaceutical tools, such as pipettes, measuring instruments, and vials, are produced accurately to maintain the integrity of drug formulations and dosing.
In addition to equipment manufacturing, CNC machining is also utilized for the production of precise lab testing tools, such as biosensors, which are used for pharmaceutical research and quality control. The use of CNC technology in this context allows pharmaceutical companies to optimize production efficiency, reduce waste, and maintain high-quality standards across their operations.
Contact our professional team now for a same-day quote and risk-free project evaluation. Benefit from ISO 8 cleanrooms, advanced machines, and 12-hour fast response in medical injection molding.