The medical component molding creates strong, durable equipment and precise measurements meeting the highest possible standards. Medical component molding is a vital manufacturing process used to produce high-precision plastic parts for medical devices. This technique involves shaping materials, usually thermoplastics, through injection molding to create components that meet stringent medical industry standards. The process ensures the production of intricate, durable, and sterile parts that are essential in medical procedures. Precision mold medical components are crucial, as even minor deviations can affect the performance and safety of medical devices. Furthermore, regulatory compliance is critical, with medical components needing to meet FDA and other health-related certifications. Ensuring quality through each step of production, from design to final product, guarantees that devices perform reliably in critical healthcare environments.
Low-Volume to High-Volume Production Capabilities
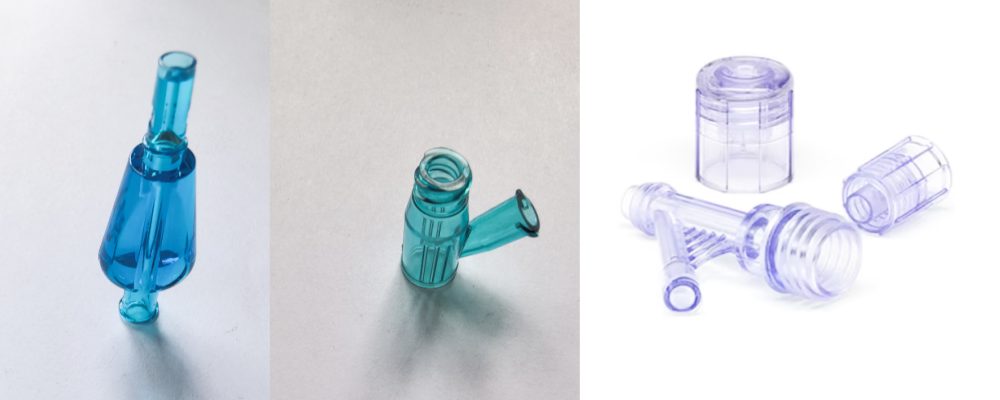
Attribute | Description |
---|---|
Shaping Mode | Plastic Injection Mould |
Place of Origin | Dongguan, Guangdong, China |
Brand Name | LY Medical Injection Mold |
Processing Service | Moulding, Plastic Molding Service, Custom Molding, Precision Molding |
Tolerance | 0.005mm - 0.1mm |
Materials | A wide range of medical-grade materials, including PP (Polypropylene), ABS (Acrylonitrile Butadiene Styrene), PC (Polycarbonate), ABS+PC, Nylon, Delrin, PMMA (Polymethyl Methacrylate), PET (Polyethylene Terephthalate), PVC (Polyvinyl Chloride), PEEK (Polyether Ether Ketone), and more. |
Customized Surface Process | Surface treatments including Polishing, Die Casting, Brushing, Anodizing, Plating, Electroplating, and more to enhance the aesthetics and performance of the components. |
Molding Type | Injection Molding, capable of producing precise, complex medical components with excellent repeatability and performance. |
Molding Complexity | Suitable for complex, multi-cavity molds, with capabilities to produce intricate designs and structures tailored to medical device requirements. |
Packaging | Inner Packaging: Opp Bags; Outer Packaging: Cartons. Custom packaging options available upon request to ensure safe transport and handling. |
Production Capacity | High-volume production capacity for medical components, ensuring timely delivery for large orders while maintaining stringent quality control standards. |
Application | Used in the manufacturing of medical devices, including but not limited to surgical instruments, diagnostic devices, drug delivery systems, and other medical applications. |
Molding Process Features | Precision molding with high repeatability, allowing for consistent and reliable production of medical components that meet strict regulatory standards. |
Compliance | Meets international medical standards and regulations, such as ISO 13485 (Quality Management Systems for Medical Devices), ensuring safety and reliability in medical applications. |
Lead Time | Fast lead times for prototyping and production, with flexibility in response to urgent or large-volume orders. |
Quality Control | Rigorous quality control at every stage, including material inspection, molding process checks, and final product inspection to meet medical industry standards. |
What Is Medical Component Molding
Medical component molding is a critical manufacturing process for producing plastic parts used in medical devices. It involves shaping materials, usually thermoplastics, through injection molding to create components that are crucial for the functioning of medical equipment. These parts must be designed with precision to ensure proper performance, safety, and compliance with strict healthcare regulations. The components produced in this process can range from simple connectors to complex, multi-part systems, all of which need to meet the highest standards for quality and functionality.
Importance of Precision and Regulatory Compliance in Medical Device Production
In medical component molding, precision is essential to ensure that each part meets the required specifications. Any deviation in size, shape, or structural integrity can result in device malfunction, affecting patient safety. Additionally, medical devices must comply with a variety of regulatory standards to ensure they are safe for use. These include:
- FDA regulations: Medical components must meet strict FDA guidelines for medical device production.
- ISO certifications: Manufacturers must ensure their molding processes adhere to quality management standards.
- Material compatibility: The materials used in molding must be compatible with medical applications, ensuring patient safety.
- Sterilization readiness: Many medical components require the ability to withstand sterilization processes without degradation.
The combination of precision and regulatory compliance is what makes molding medical parts components a specialized and essential process in the healthcare industry. At FUJIU Medical Injection Mold, we ensure that our molding services meet these rigorous standards, providing reliable and high-quality products for the medical sector.
Medical Component Molding Industry
The medical component molding industry focuses on the design, manufacturing, and production of precision-molded parts and components used in healthcare applications. This industry is a critical segment of the broader medical device sector, playing a vital role in creating products that meet stringent quality, safety, and performance standards.
Technologies
- Injection Molding: The most common method, using medical-grade plastics to create components with high precision and repeatability.
- Micro-Molding: For producing extremely small and intricate parts, such as those used in minimally invasive surgeries or microfluidics.
- Overmolding: Combines different materials into a single component, often used for ergonomic medical tools or multi-material devices.
- Cleanroom Molding: Ensures the production of sterile components in controlled environments to meet regulatory standards.
Materials Used
Medical component molding utilizes biocompatible and FDA-approved materials such as:
- Thermoplastics: Polypropylene (PP), polyethylene (PE), and polycarbonate (PC).
- Elastomers: Silicone and thermoplastic elastomers (TPEs) for flexible parts.
- Bio-Resorbable Polymers: Used for temporary implants or drug-delivery applications.
Regulatory Compliance
The industry is highly regulated, adhering to ISO 13485 standards for quality management systems in medical device manufacturing. Components must also meet FDA or EU MDR (Medical Device Regulation) requirements to ensure safety and efficacy.
Trends and Innovations
- Sustainability: Increasing use of recyclable and biodegradable materials.
- Automation: Advanced robotics for precision and efficiency in production lines.
- Customization: Demand for patient-specific devices, leading to more tailored molding processes.
- Miniaturization: Growth in micro-molding to support less invasive medical technologies.
The medical component molding industry is indispensable to healthcare innovation, ensuring the production of high-quality, reliable components that support patient care and safety.
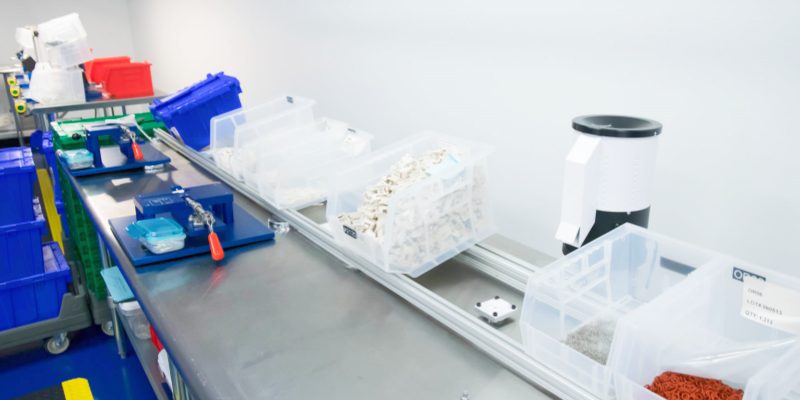
Medical Component Molding Process
The medical component molding process involves the production of precision parts and devices using advanced molding techniques tailored to meet stringent medical and regulatory standards. Here’s a step-by-step breakdown:
Material Selection
- Medical-Grade Materials: Selection of biocompatible materials like thermoplastics (e.g., polycarbonate, polypropylene) or elastomers (e.g., silicone, TPE).
- Regulatory Compliance: All materials must meet ISO 10993 standards and FDA or EU MDR requirements for safety, sterility, and compatibility.
Mold Design and Development
- CAD Modeling: Computer-aided design (CAD) is used to create precise digital prototypes of the mold.
- Tooling Fabrication: High-precision tools (usually made of hardened steel or aluminum) are manufactured to create the mold cavities.
- Multi-Cavity Molds: For high-volume production, molds with multiple cavities are developed to produce multiple parts simultaneously.
Molding Process
- Injection Molding: A common method where molten material is injected into a mold under high pressure, cooled, and ejected.
- Micro-Molding: Used for extremely small or intricate parts, such as those for minimally invasive devices.
- Overmolding: Combines two or more materials, ideal for ergonomic or multi-functional components.
- Compression Molding: Suitable for elastomeric materials, such as silicone parts.
Cleanroom Manufacturing
- Sterile Environment: Components are molded in ISO Class 7 or 8 cleanrooms to prevent contamination.
- Air Filtration Systems: Ensure a controlled environment free from particles, bacteria, and other contaminants.
Quality Control and Testing
- Dimensional Inspection: Parts are inspected for size, shape, and tolerance accuracy using tools like CMM (Coordinate Measuring Machines).
- Functional Testing: Ensures components perform as intended, such as flow testing for IV connectors.
- Material Testing: Biocompatibility and sterilization resistance are tested to meet medical standards.
Secondary Processes
- Assembly: Combining molded components into complete devices, such as syringes or inhalers.
- Surface Finishing: Polishing or texturing to meet aesthetic and functional requirements.
- Printing and Marking: Adding labeling or unique identifiers using laser marking or pad printing.
Packaging and Sterilization
- Specialized Packaging: Sealing in medical-grade pouches or trays to maintain sterility.
- Sterilization: Methods like ethylene oxide (EtO), gamma radiation, or autoclaving to ensure safe use in clinical environments.
Regulatory Documentation
- Traceability: Full documentation to track materials, processes, and inspections.
- Compliance: Adherence to ISO 13485 standards and FDA guidelines for medical device production.
The medical component molding process is highly specialized, integrating advanced technologies, stringent quality controls, and regulatory compliance to produce reliable, safe, and effective components for healthcare applications.
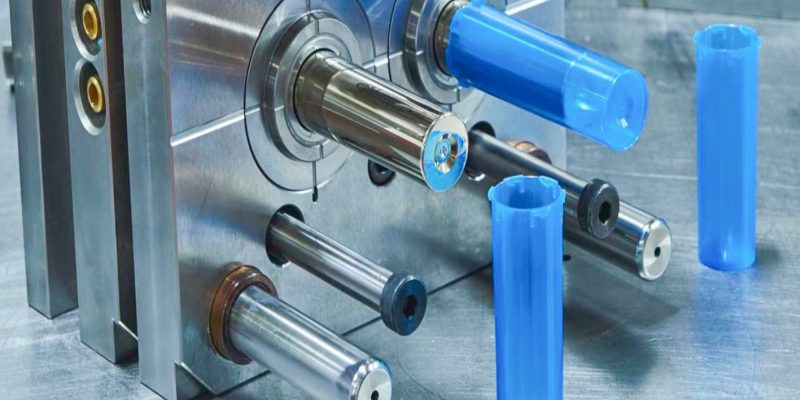
Application of Medical Component Molding
Medical component molding plays a crucial role in producing precise, reliable, and biocompatible parts for various healthcare applications. Here are the primary areas where medical component molding is applied:
Medical Devices
- Surgical Instruments: Handles, grips, and other components for scalpels, forceps, and laparoscopic tools.
- Diagnostic Devices: Components for blood analyzers, test kits, and imaging equipment.
- Wearable Devices: Parts for glucose monitors, blood pressure cuffs, and health trackers.
Drug Delivery Systems
- Syringes: Precise plastic molding for single-use syringes.
- Inhalers: Complex parts for metered-dose inhalers and dry powder inhalers.
- Auto-Injectors: High-precision components for epinephrine or insulin delivery pens.
Implants and Prosthetics
- Temporary Implants: Bioresorbable polymer components for orthopedic or drug delivery applications.
- Prosthetics: Molded silicone and polymer parts for artificial limbs and other prosthetic devices.
- Dental Implants: Small, durable components used in orthodontics and restorative dentistry.
Catheters and Tubing
- IV Catheters: Precisely molded connectors and hubs for fluid and medication delivery.
- Urinary Catheters: Flexible and smooth tubing for comfort and safety.
- Cardiovascular Devices: Molded parts for stents, guide wires, and heart valve delivery systems.
Packaging and Storage
- Sterile Packaging: Molded containers and trays for storing medical instruments and implants.
- Single-Use Containers: Disposable vials, caps, and closures for pharmaceutical products.
- Reagent Reservoirs: Custom containers for diagnostic and research applications.
Custom Applications
- Patient-Specific Devices: Molded parts for tailored medical implants or custom surgical tools.
- Minimally Invasive Surgery Tools: Micro-molded components for precision and reduced tissue damage.
- Diagnostic Consumables: Lab-on-a-chip devices and cartridges for rapid testing.
Laboratory and Research Equipment
- Microfluidic Devices: Molded parts for handling small liquid volumes in biological research.
- Assay Kits: High-precision components for chemical and biological testing systems.
Medical component molding supports applications across medical devices, drug delivery, implants, and diagnostics. Its ability to create high-quality, biocompatible, and cost-effective components makes it indispensable in advancing healthcare technologies.
What Is Medical Component Molding Cost
The cost of medical component molding can vary widely depending on several factors that influence the complexity and scale of production. Medical device manufacturers must consider these factors when determining the budget for their component molding projects. Below are the key elements that can impact the overall cost of medical component molding:
Key Factors Influencing the Cost of Medical Component Molding
- Complexity of the Design: More intricate and detailed designs require more advanced tooling and precise molding techniques, which can drive up the cost.
- Material Selection: Different materials have varying costs, with high-performance medical-grade plastics or composites being more expensive than standard materials.
- Tooling and Equipment: Custom molds for medical components, especially those requiring high precision, often require significant investment in tooling and machinery.
- Production Volume: Larger production volumes typically reduce the cost per unit, while smaller production runs may lead to higher costs due to setup fees and mold wear.
How Material Choices Impact Overall Costs
The material selected for medical component molding can significantly influence both the cost and quality of the final product. Some materials are more expensive than others due to their superior properties, regulatory approvals, and manufacturing requirements. Key factors include:
- Biocompatibility: Materials used in medical components must be biocompatible to avoid reactions with the human body, which can raise material costs.
- Sterilization Resistance: Materials that can withstand repeated sterilization processes, such as autoclaving, are typically more expensive.
- Durability: High-performance plastics that offer better durability, resistance to wear, and structural integrity tend to be priced higher than standard plastics.
- FDA Approval: Medical-grade materials that have been approved by regulatory bodies, such as the FDA, are more costly but necessary for medical device manufacturing.
These factors collectively determine the total cost of producing medical components through molding, and understanding them helps manufacturers optimize both cost-efficiency and compliance with medical industry standards.
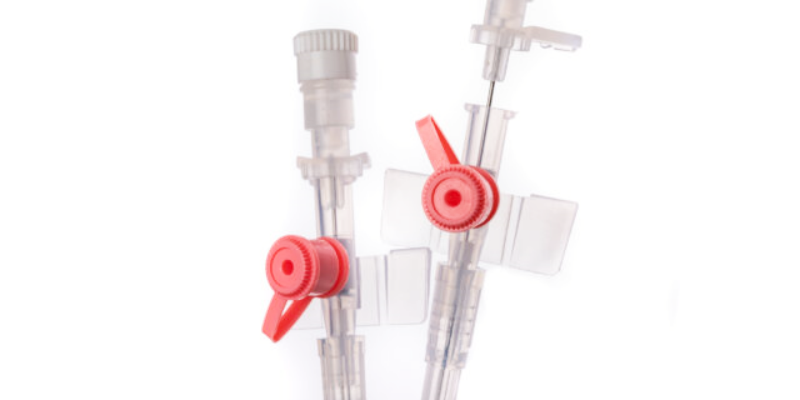
Medical Component Molding and Its Role in Healthcare
Medical component molding plays a crucial role in the production of essential parts for the healthcare industry. The precision and quality required for medical devices demand advanced molding techniques to produce components that ensure both safety and effectiveness. This process is integral to developing products that support medical professionals in diagnosing, treating, and monitoring patients. Medical component molding ensures that critical parts meet the highest standards of durability, functionality, and compliance with regulatory requirements.
Importance of Medical Molding in Producing Critical Components
Medical molding allows for the creation of components that are vital to the proper functioning of medical devices. The importance of this process lies in its ability to manufacture parts with:
- High precision: Ensures that parts fit together perfectly and perform reliably.
- Durability: Components are built to withstand wear, stress, and extreme conditions in medical environments.
- Compliance with health regulations: Medical precision components must meet strict industry standards such as FDA approvals and ISO certifications.
- Sterilization compatibility: Many components must be capable of being sterilized to prevent contamination.
By using medical component molding, manufacturers are able to produce components that are both safe and effective, supporting the healthcare industry in providing high-quality patient care.
Overview of Molding Methods
Several molding techniques are used to produce medical components, each suited to specific types of parts and production requirements. These methods include:
- Injection Molding: The most commonly used method for medical component molding, allowing for high precision and the production of complex shapes. It is ideal for mass production and can use a wide range of materials.
- Insert Molding: This process combines plastic with metal inserts to create stronger and more durable components. It is often used for devices that require both plastic and metal parts, such as surgical tools or connectors.
- Micro Molding: Used for producing extremely small, high-precision parts, typically in applications such as diagnostic devices or small medical implants. Micro molding can create parts with tolerances as tight as a few microns.
These methods each have their strengths and are selected based on the needs of the medical device being produced, ensuring that the final product meets the required specifications for safety, functionality, and regulatory compliance.
Medical Device Plastic Components Injection Moulding: A Specialized Approach of Medical Component Molding
Medical device plastic components injection moulding is a highly specialized approach within the broader field of medical component molding. This technique is used to manufacture plastic parts that are essential for the functionality and safety of medical devices. The process involves injecting molten plastic into precisely designed molds to form components with high accuracy, suitable for use in critical medical applications.
How This Method Ensures Precision and Adherence to Regulatory Standards
Medical device plastic components injection moulding is designed to ensure high levels of precision and compliance with regulatory standards that are essential in the healthcare industry. The factors that contribute to its effectiveness in maintaining these standards include:
- High precision: Injection moulding allows for the production of parts with tight tolerances, ensuring that each component is consistent and fits within the required specifications.
- Material traceability: The use of FDA-approved medical-grade materials ensures that every part meets the strict requirements for safety, performance, and biocompatibility.
- Sterility compliance: Components produced through this method can be designed to withstand sterilization processes like autoclaving, ensuring that the parts remain sterile and safe for medical use.
- Regulatory adherence: Medical device plastic components injection moulding is performed in compliance with various regulatory standards such as ISO 13485, ensuring that the manufacturing process meets the required safety and quality levels for medical devices.
These factors make this molding technique ideal for producing critical components that must meet the highest standards of safety and performance.
Examples of Devices Produced Using This Technique
Medical device plastic components injection moulding is used to produce a wide range of medical devices. Some of the most common examples include:
- Syringes: Plastic syringes used for injections and fluid administration.
- Implants: Components such as joint replacements or dental implants made from biocompatible plastics.
- Diagnostic tools: Components for devices like thermometers, blood glucose monitors, and portable diagnostic instruments.
- Surgical instruments: Parts such as handles for scalpels and forceps made using injection molding for precision and durability.
- Patient monitoring equipment: Components used in medical monitors for tracking vital signs.
These examples highlight the versatility of medical device plastic components injection moulding in producing essential parts for various types of medical devices. Each part must meet the required standards for safety, durability, and functionality, making this method crucial for the healthcare industry.
Medical Component Molding: Choosing the Right Medical Injection Molding Companies
Choosing the right company for medical component molding is crucial to ensuring the success of medical device production. The right partner will not only meet the required technical specifications but also ensure that components adhere to strict regulatory standards. When selecting a medical injection molding company, manufacturers should consider a number of factors that can impact both the quality and cost-effectiveness of their components.
How to Select a Reliable Company for Medical Component Molding
Selecting a reliable company for medical component molding requires a thorough evaluation of the company’s capabilities, reputation, and expertise in the medical device industry. Key considerations include:
- Experience and Specialization: Look for a company with extensive experience in medical component molding. They should have a proven track record of producing medical-grade components and understanding the specific needs of the healthcare industry.
- Expertise in Advanced Molding Techniques: Ensure the company is proficient in specialized molding methods such as micro molding, insert molding, and cleanroom molding, which are essential for producing precise and sterile components.
- Technical Capability: The company should be equipped with advanced machinery capable of meeting the complex needs of medical device production, such as multi-cavity molds and high-precision injection systems.
- References and Case Studies: Check the company’s history of successful projects and its ability to deliver parts on time and within budget. Look for customer testimonials or case studies related to similar projects.
Services Offered by Medical Injection Molding Companies
Medical injection molding companies typically offer a range of medical injection molding services designed to cover every step of the production process, from concept to final product. These services include:
- Prototyping: Many companies provide prototyping services, which are essential for testing designs and verifying the fit and functionality of medical components before full-scale production begins. Prototypes allow for early detection of any issues, reducing the risk of errors during mass production.
- Production: The core service of any injection of medical molding company is the mass production of plastic components. Companies should be able to produce high volumes of parts while maintaining consistency and meeting the required specifications for each part.
- Cleanroom Molding: Cleanroom molding is crucial in the medical industry, where sterility is a top priority. A reputable molding company should offer cleanroom production environments to prevent contamination during the manufacturing process, supported by medical components precision cleaning. Cleanrooms are especially important for parts that will be used in invasive medical procedures or implanted in the human body.
Considerations for FDA Compliance and Regulatory Requirements
Medical component molding is highly regulated, and any medical device or part must comply with strict FDA guidelines and other industry standards to ensure patient safety and product reliability. When choosing a medical injection molding company, the following factors must be considered:
- FDA Compliance: The company must follow Good Manufacturing Practices (GMP) and ensure that all components meet FDA approval requirements. Companies should have experience working with FDA-regulated products and should be able to provide documentation of compliance.
- ISO Certification: Companies should be ISO 13485 certified, which ensures that their quality management systems meet the standards required for the production of medical devices.
- Material Traceability: A reliable company should maintain full traceability of the materials used in production to ensure that the medical components are produced with FDA-approved materials. This ensures that all parts meet regulatory standards for biocompatibility and safety.
- Validation and Testing: The molding company should conduct thorough testing, including mechanical, thermal, and chemical validation, to ensure that the medical components meet safety, durability, and performance standards.
By selecting a company that offers a comprehensive range of services and adheres to stringent regulatory requirements, manufacturers can ensure that their medical components are produced to the highest standards, which is critical in the healthcare industry.
Medical Plastic Parts Molding: Essential for Quality Medical Devices in Medical Component Molding
Medical plastic parts molding is an essential aspect of medical component molding, playing a crucial role in the production of high-quality medical devices. It allows for the creation of plastic components used in everything from diagnostic tools to surgical instruments. These components must meet stringent performance, safety, and regulatory standards to ensure their reliability and effectiveness in healthcare applications. The process of molding plastic parts for medical devices requires precision, quality control, and expertise to guarantee that each component can withstand the demanding environments in which they will be used.
Overview of Medical Plastic Parts Molding and Its Importance in the Medical Industry
Medical plastic parts molding involves the use of specialized molding techniques, such as injection molding, to produce plastic components for medical devices. The importance of this process lies in its ability to create precise, durable, and biocompatible parts necessary for the safe and effective operation of medical devices. These molded components can range from small parts, like connectors and needles, to larger components, such as housings for medical equipment.
The role of medical plastic parts molding is critical in ensuring that the medical devices function as intended while maintaining safety standards. Many medical devices rely on complex, high-precision plastic components to perform specific functions, and molding is the most effective and reliable way to manufacture these parts at scale.
Materials Commonly Used for Medical Plastic Parts Molding
The selection of materials is crucial in medical plastic parts molding, as medical components must meet strict requirements for performance, safety, and regulatory compliance. Some of the most commonly used materials in this process include:
- Polycarbonate (PC): Known for its clarity, strength, and impact resistance, polycarbonate is widely used for components that require high durability and transparency, such as medical device housings and diagnostic equipment.
- Polypropylene (PP): A versatile and cost-effective material, polypropylene is often used for medical components that require chemical resistance, low moisture absorption, and high sterility.
- Polyethylene (PE): This material is often used for low-cost, single-use components, such as syringes and packaging, because of its flexibility, biocompatibility, and ease of sterilization.
- Polymethyl methacrylate (PMMA): Also known as acrylic, PMMA is used for optical components due to its clarity and ability to withstand sterilization processes.
- Medical-grade nylon: Nylon is used in components requiring flexibility and wear resistance, such as tubing and surgical instruments.
These materials are selected based on the specific requirements of the medical devices they will be used in, including biocompatibility, strength, flexibility, and resistance to sterilization.
How It Ensures Durability, Flexibility, and Compliance with Healthcare Standards
Medical plastic parts molding ensures the creation of components that meet the demanding performance and safety standards of the healthcare industry. Key factors that contribute to the success of medical plastic parts molding include:
- Durability: The materials used in medical plastic parts molding are selected for their ability to withstand wear, stress, and harsh conditions, ensuring that components perform reliably over time.
- Flexibility: Many medical devices require components that can bend, stretch, or conform to specific shapes. Molding techniques allow for the production of flexible parts that maintain their integrity under various conditions, such as catheters and surgical tools.
- Compliance with regulatory standards: Medical plastic parts molding ensures that components meet strict FDA guidelines and international standards, such as ISO 13485, which govern the production of medical devices. The use of certified medical-grade materials ensures that components are safe for use in healthcare settings.
- Sterilization compatibility: Molding techniques are designed to produce components that can withstand common sterilization methods, such as autoclaving, without compromising their integrity or functionality.
Through the use of advanced molding techniques and careful material selection, medical plastic parts molding guarantees the production of high-quality, reliable medical components that are crucial for patient care and medical procedures.
FAQs about Medical Component Molding
Medical molding refers to the process of manufacturing plastic components used in medical devices through molding techniques such as injection molding, compression molding, and blow molding. The primary purpose of medical molding is to create high-precision, biocompatible parts that meet the stringent standards required for medical applications. These parts can include anything from syringes, catheters, and surgical instruments to diagnostic devices and implants.
The process typically involves heating medical-grade plastics to a molten state and injecting them into molds that shape the components. Once cooled and solidified, the components are carefully inspected for quality, including testing for durability, biocompatibility, and sterility compatibility. Medical molding plays a crucial role in ensuring that medical devices function properly and safely in clinical settings. It is a highly regulated industry where every part must meet standards set by regulatory bodies like the FDA and ISO. As such, precision, material selection, and adherence to these standards are critical factors in producing reliable medical components.
There are three primary types of molding techniques used in the manufacturing of medical components: injection molding, compression molding, and blow molding. Each technique has its own applications and benefits depending on the type of component being produced.
Injection Molding: This is the most commonly used molding technique in the medical industry. It involves injecting molten plastic into a mold under high pressure. Injection molding is ideal for producing parts with complex shapes and high precision, making it perfect for items like syringes, connectors, and small diagnostic devices. The process is highly efficient for high-volume production runs.
Compression Molding: In compression molding, a preheated material is placed into a mold cavity, and pressure is applied to shape it. This technique is particularly useful for larger parts, such as gaskets, seals, and custom plastic parts used in medical equipment. It is often used for thermosetting plastics that harden under heat and pressure, providing a durable end product.
Blow Molding: This method is primarily used to produce hollow parts such as bottles and containers. Blow molding involves melting plastic and inflating it into a mold, creating hollow components that are lightweight yet strong. In the medical field, blow molding is often used for producing disposable containers and certain types of medical packaging.
Each of these molding techniques offers unique advantages, with selection depending on factors such as the material, complexity of the part, and production volume required.
In medical terms, molding refers to the shaping of an infant’s head during childbirth. As the baby passes through the birth canal, the soft bones of the skull overlap slightly to facilitate delivery. This process is normal and temporary, with the head typically returning to a rounder shape shortly after birth. Molding is especially common in vaginal deliveries and rarely indicates any medical concern. However, excessive or uneven molding might require attention to rule out underlying complications, such as cephalhematoma or craniosynostosis.
Caput Succedaneum: Swelling of the scalp caused by pressure during labor.
Cephalhematoma: A collection of blood beneath the periosteum, confined to a specific bone.
Overlapping Cranial Bones: Normal adaptation of skull bones during vaginal delivery.
Subgaleal Hemorrhage: Bleeding under the scalp’s aponeurotic layer, often due to birth trauma.
These types describe common variations or complications of head molding during childbirth and are managed based on severity.
In the pharmaceutical industry, molding involves shaping materials into specific forms, often for creating medical devices or dosage forms. For example, molding is used to manufacture tablet molds, prefilled syringes, or inhalers. The process ensures precision, hygiene, and compliance with medical standards. Injection molding, a common technique, allows for the creation of complex shapes using materials like polymers or plastics, crucial for drug packaging and delivery systems. Pharmaceutical molding focuses on accuracy, sterility, and safety to meet regulatory requirements.
Contact our professional team now for a same-day quote and risk-free project evaluation. Benefit from ISO 8 cleanrooms, advanced machines, and 12-hour fast response in medical injection molding.