In healthcare, maintaining the highest standards of cleanliness and sterility is critical. Medical components precision cleaning plays a vital role in achieving this, as it is specifically designed to eliminate contaminants that could compromise patient safety. By thoroughly removing particles, residues, and pathogens from medical instruments, components, and medical molding, this cleaning process helps prevent healthcare-associated infections and ensures compliance with stringent healthcare standards. Beyond safety, medical components precision cleaning contributes to the longevity and optimal functionality of medical devices, reducing wear and tear caused by accumulated debris. Ultrasonic medical components precision cleaning is critical for cleaning of medical components is globally leading solutions. Advanced cleaning technologies, such as ultrasonic and automated systems, are now integral to this process, providing efficient, effective solutions that meet the complex needs of the medical industry.
Low-Volume to High-Volume Production Capabilities
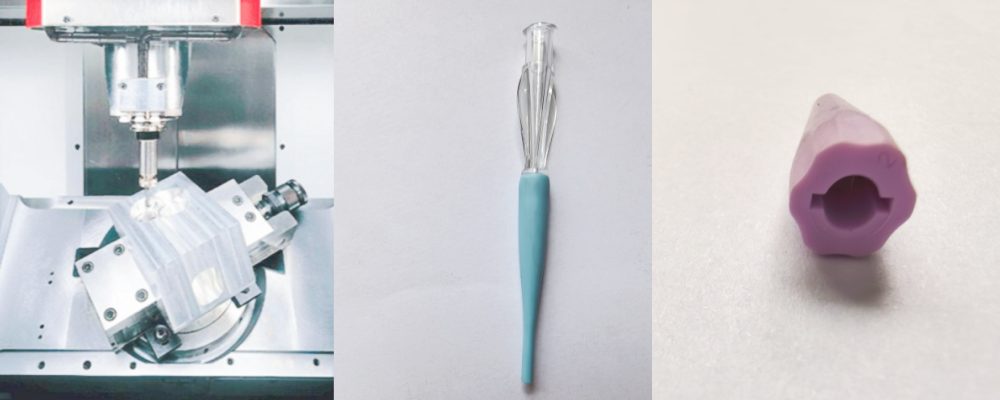
Attribute | Details |
---|---|
Product Range | Customized medical components, precision tubing, cannula needles, CNC machining parts, and plastic/metal medical device components. |
Materials | Aluminum, Brass, Bronze, Copper, Hardened Metals, Precious Metals, Stainless Steel, Steel Alloys, Iron, Titanium Alloy (e.g., Ti-6Al-4V), PEEK, Elastomers, Polyurethane. |
Manufacturing Capabilities | CNC Machining, Micro Machining, Broaching, Drilling, Etching/Chemical Machining, Laser Machining, Milling, Turning, Wire EDM, Rapid Prototyping, Extrusion, Moulding. |
Tolerance | +/- 0.01mm |
Applications | Medical devices,cardiology drainage systems,steerable catheters |
Surface Treatments | Anodizing, Nickel plating, Zinc plating, Polishing, Custom Surface Treatments. |
Certifications | ISO9001, ISO13485:2003 |
Delivery Time | 7–15 days |
Customization Options | Sizes, Colors, Materials, and Shapes tailored to customer needs. |
Manufacture Environment | Standard Class 10 or Class 10,000 Cleanroom depending on the product. |
Processes Offered | Moulding, Cutting, Machining-Assembly, Custom OEM/ODM services. |
Special Features | High-precision engineering, durable materials, multi-functional processing, fast delivery, excellent customization options. |
Product Examples | - CNC Aluminum Parts for Aerospace and Medical Devices |
- Polyurethane Medical Tubing | |
- Precision Stainless Steel Cannula Needles | |
- Customized Injection Molds. |
Why Medical Components Precision Cleaning Matters
Preventing Healthcare-Associated Infections (HAIs)
In healthcare, medical components precision cleaning is critical for infection prevention. Contaminated medical equipment can harbor bacteria, viruses, and other pathogens that pose significant risks to patients. Thorough cleaning protocols help prevent the spread of these infections, which are often linked to improperly sanitized medical devices. By removing all traces of contaminants, precision cleaning serves as an essential measure in controlling HAIs, ensuring that healthcare facilities provide a safer environment for both patients and staff.
Regulatory Compliance and Standards
Medical components precision cleaning also plays a vital role in meeting stringent regulatory standards set by agencies such as the FDA, CDC, and other health authorities. These organizations mandate rigorous guidelines for cleaning and sterilizing medical instruments to ensure public safety. Failure to comply with these standards can lead to severe penalties, including costly recalls and reputational damage. Precision cleaning allows healthcare providers to adhere to these regulations, ensuring that each instrument and component meets the highest safety and cleanliness standards.
Enhancing Equipment Longevity and Performance
In addition to infection control and compliance, medical components precision cleaning is essential for maintaining equipment functionality and durability. Accumulated contaminants can lead to wear and tear, reducing the lifespan of medical instruments and impairing their effectiveness. By thoroughly removing residues and particles, precision cleaning minimizes abrasive interactions that can degrade devices over time. This process not only extends the lifespan of medical components but also enhances their performance, reducing the need for frequent repairs or replacements.
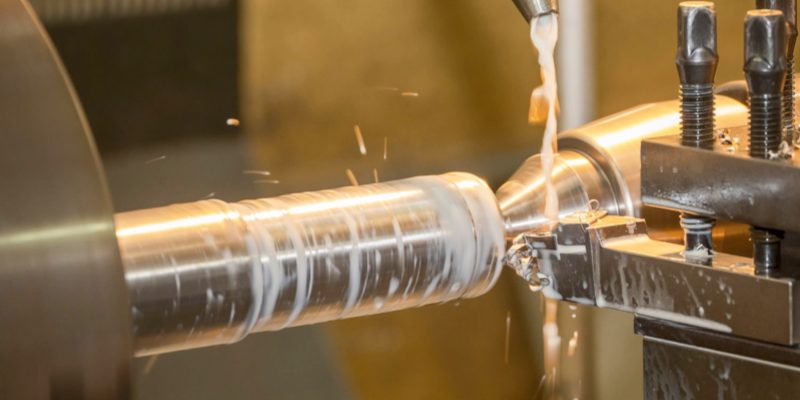
Ultrasonic Medical Components Precision Cleaning Systems
Ultrasonic cleaning systems are widely used in the medical device industry for precision cleaning, especially for components that require thorough decontamination and sterilization. These systems utilize high-frequency sound waves (typically between 20 kHz and 40 kHz) to generate microscopic bubbles in a cleaning solution. When these bubbles collapse, they create a high-energy effect known as cavitation, which effectively removes contaminants, debris, and residues from intricate surfaces and hard-to-reach areas of medical components. This process is particularly valuable for cleaning delicate and complex medical devices without causing damage.
How Ultrasonic Cleaning Works for Medical Components
- Cavitation Process: The ultrasonic cleaner generates high-frequency sound waves that create rapid pressure changes in the liquid medium. These pressure changes form tiny bubbles (cavitation bubbles), which implode upon collapsing. The implosion creates intense microscopic scrubbing forces, breaking apart and dislodging contaminants on the surface of medical components.
- Cleaning Solution: An appropriate cleaning solution is used in ultrasonic cleaning to enhance the cavitation process. The solution may contain detergents, solvents, or enzymes, depending on the type of contamination (organic, inorganic, or biological matter). The solution is typically heated to improve cleaning efficiency.
- Precision and Delicacy: Ultrasonic cleaning is ideal for medical components due to its ability to clean fine details without causing mechanical stress or damage to delicate parts. It can clean intricate geometries, including lumens in catheters, surgical instruments, and microcomponents of implants, which are difficult to clean by traditional methods.
- Time Efficiency: The ultrasonic cleaning process is relatively quick, typically taking from a few minutes to half an hour, depending on the level of contamination and size of the components. This efficiency makes it ideal for medical facilities with high volumes of device reprocessing.
Applications in Medical Device Manufacturing and Reprocessing
- Surgical Instruments: Ultrasonic cleaning systems are extensively used to clean surgical tools, including forceps, scissors, and scalpels, removing blood, tissue, and other residues.
- Implants: Ultrasonic cleaners help decontaminate implantable devices, such as joint replacements, stents, and dental implants, ensuring they are free of microbial contamination before they are sterilized.
- Endoscopes and Catheters: Medical devices like endoscopes, catheters, and other instruments with internal channels benefit from ultrasonic cleaning because it can reach deep into their lumens, ensuring thorough decontamination.
- Microcomponents: Ultrasonic cleaning is especially beneficial for cleaning tiny medical components, such as sensors, needles, and valves, which require highly detailed attention to cleanliness.
Benefits of Ultrasonic Cleaning for Medical Devices
- Thorough Cleaning: The cavitation process is highly effective at removing even microscopic contaminants, biofilm, and residues, ensuring medical devices meet stringent cleanliness standards.
- Non-Abrasive: Ultrasonic cleaning is a non-abrasive method, preventing any mechanical damage to sensitive components, which is crucial in medical device manufacturing.
- Efficiency: It provides a fast and consistent cleaning process, which is especially useful in environments that handle large volumes of medical equipment.
- Reachability: Ultrasonic waves can clean hard-to-reach areas of medical components that might be challenging for traditional cleaning methods, such as small grooves or channels in instruments.
- Regulatory Compliance: Ultrasonic cleaning ensures that medical components meet regulatory requirements for cleanliness, including standards set by the FDA, ISO, and other health authorities.
Challenges and Considerations
- Cost: Ultrasonic cleaning systems can be expensive, particularly for high-quality units designed for medical device cleaning. However, the investment is often justified by the thoroughness and efficiency of the cleaning process.
- Maintenance: The cleaning solution needs to be regularly replaced and monitored for optimal performance, as contaminants can degrade the solution over time.
- Compatibility: It’s important to ensure the ultrasonic cleaning system is compatible with the materials used in the medical components, as some materials may be sensitive to ultrasonic energy.
Ultrasonic medical components precision cleaning systems offer significant advantages in terms of effectiveness, efficiency, and precision, making them ideal for the medical device industry. These systems ensure that components are thoroughly cleaned and decontaminated, meeting high standards of hygiene and safety. With the ability to clean complex, delicate devices, ultrasonic cleaning is an essential tool for both manufacturing and reprocessing medical equipment.
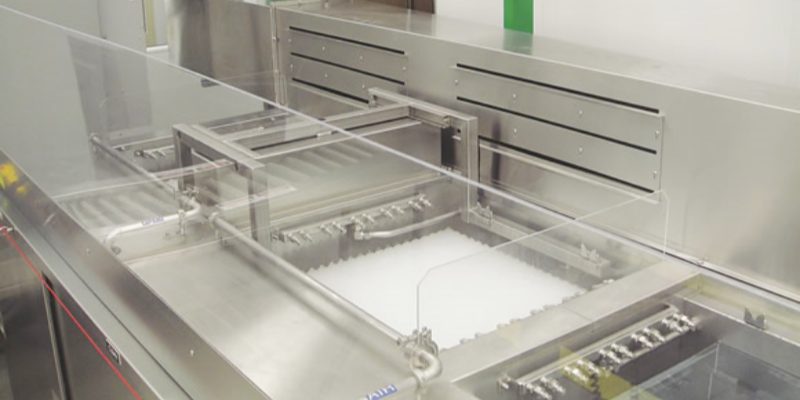
Controlling Medical Components Precision Cleaning Methods
Effective cleaning of medical components is critical to ensure that they are free of contaminants, such as bacteria, viruses, and residues, before use. Precision cleaning methods, especially in the medical device industry, require rigorous controls to ensure that devices meet stringent cleanliness standards. Below are key methods for controlling the precision cleaning of medical components.
Ultrasonic Cleaning
Ultrasonic cleaning is one of the most effective precision cleaning methods, often used in medical device reprocessing and manufacturing. It involves the use of high-frequency sound waves (ultrasound) to create cavitation bubbles in a cleaning solution. When these bubbles collapse, they generate energy that removes contaminants from the surfaces of medical components.
- Control Parameters:
- Frequency: Typically between 20 kHz and 40 kHz, depending on the size and delicacy of the components.
- Temperature: Cleaning solutions are often heated to enhance cleaning efficiency.
- Solution Composition: The choice of cleaning solution (e.g., detergents or enzymes) is controlled to ensure compatibility with the components and effective removal of contaminants.
- Cleaning Time: Proper exposure time is critical to ensure thorough cleaning without damaging sensitive components.
- Equipment Calibration: Regular calibration of ultrasonic cleaners ensures consistent performance.
High-Pressure Water Jets
High-pressure water jets use pressurized water to blast contaminants off surfaces. This method is often used for cleaning larger components or those with intricate internal channels, such as endoscopes or surgical instruments.
- Control Parameters:
- Water Pressure: The pressure must be optimized to remove debris without damaging the components.
- Water Temperature: Warm water can increase the effectiveness of the cleaning process.
- Spray Pattern: Ensuring even distribution across the component to ensure all surfaces are cleaned thoroughly.
- Flow Rate: Maintaining the appropriate flow rate helps ensure that contaminants are effectively dislodged.
Automated Spray and Soak Cleaning
Automated spray and soak cleaning systems use a combination of spraying cleaning solutions on medical devices and soaking them in the solution for a predetermined period. This method is ideal for cleaning both external and internal surfaces of devices with complex geometries.
- Control Parameters:
- Soak Time: The length of time the components are exposed to the cleaning solution is closely monitored to prevent over- or under-cleaning.
- Spray Intensity: The force and angle of the spray must be controlled to ensure effective cleaning without damaging fragile parts.
- Cleaning Solution Composition: Solutions with specific detergents, enzymes, or solvents are chosen based on the type of contamination being removed.
Dry Ice Blasting
Dry ice blasting is a non-abrasive cleaning method in which solid carbon dioxide (dry ice) pellets are accelerated and shot at high speeds to remove contaminants from surfaces. This method is often used for cleaning medical devices with sensitive or intricate parts.
- Control Parameters:
- Pellet Size: The size of the dry ice pellets affects the cleaning power and the potential for damage to components.
- Pressure Settings: The pressure used to propel the dry ice must be carefully controlled to ensure effective cleaning without damaging delicate parts.
- Cleaning Duration: The time the dry ice is applied to the device must be optimized to achieve effective cleaning.
Chemical Vapor Deposition (CVD) and Plasma Cleaning
CVD and plasma cleaning methods are used to remove microscopic contaminants from surfaces of medical components. These methods use gaseous chemicals or ionized gases to interact with the surface, removing organic and inorganic residues.
- Control Parameters:
- Pressure and Temperature: Both the temperature and pressure of the cleaning chamber must be carefully controlled to ensure optimal interaction with contaminants.
- Chemical Composition: The choice of gases or chemicals used must be tailored to the specific type of contamination being removed.
- Process Time: The duration of the cleaning process must be monitored to avoid overexposure to the cleaning medium, which could damage sensitive components.
Visual Inspection and Monitoring
After cleaning, visual inspection plays a key role in controlling the cleaning process. It ensures that the components are free from visible contamination and meets the cleanliness standards required for medical use.
- Control Parameters:
- Inspection Tools: Tools like magnifying glasses, borescopes, or microscopes are used to inspect hard-to-reach areas for cleanliness.
- Acceptable Cleanliness Standards: Regulatory standards such as ISO 13485 or FDA requirements must be adhered to, which define acceptable levels of contamination.
Automated Cleaning Validation Systems
To ensure consistency, cleaning validation is an essential part of medical device reprocessing. Automated cleaning systems can be integrated with sensors to monitor the cleanliness of the devices in real-time.
- Control Parameters:
- Validation Protocols: Automated systems are programmed to follow predefined cleaning protocols and adjust parameters as necessary to ensure thorough cleaning.
- Real-Time Monitoring: Sensors detect factors such as contamination levels, temperature, and solution concentration to provide ongoing validation during the cleaning process.
Environmental Control
Environmental factors such as humidity, temperature, and air quality also influence cleaning effectiveness and the post-cleaning process. For example, after cleaning, medical components need to be properly dried and stored in controlled conditions to avoid contamination.
- Control Parameters:
- Drying Time and Temperature: Drying parameters need to be optimized to ensure that moisture does not affect the component or promote microbial growth.
- Storage Conditions: Devices should be stored in clean, controlled environments to avoid recontamination.
Controlling medical components precision cleaning is crucial for maintaining the safety and efficacy of medical devices. By implementing carefully controlled cleaning methods, manufacturers and healthcare providers can ensure that their devices meet stringent regulatory standards and are safe for use. Precision cleaning systems like ultrasonic cleaners, automated spray systems, and chemical cleaning methods, combined with thorough validation and monitoring, ensure that contaminants are effectively removed without compromising the integrity or functionality of the medical components.
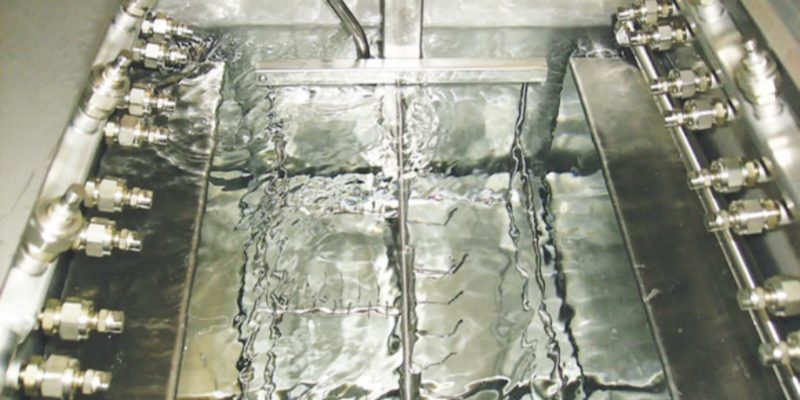
Medical Components Precision Cleaning Process
The precision cleaning process for medical components is essential to ensure that devices are free of contaminants, residues, and biohazards, making them safe for patient use. This process typically involves several stages, including pre-cleaning, cleaning, rinsing, drying, and validation. Each step is meticulously controlled to ensure the cleanliness, safety, and regulatory compliance of medical devices. Below is an overview of the typical stages involved in the precision cleaning process for medical components:
Pre-Cleaning
Pre-cleaning is the initial stage where large particles and visible contaminants are removed from the surface of the medical components. This step helps prevent these particles from interfering with the subsequent cleaning process.
- Methods:
- Wiping with absorbent materials
- Rinsing with water or a mild detergent solution
- Pre-soaking in a cleaning solution to loosen contaminants
- Importance: Helps reduce the load of contamination and ensures the cleaning agents are more effective during the main cleaning phase.
Cleaning
Cleaning is the core process where contaminants, such as dirt, oils, biological residues, and other particulates, are removed from the medical components. Various cleaning methods may be used depending on the complexity of the components and the type of contamination.
- Common Methods:
- Ultrasonic Cleaning: Uses high-frequency sound waves to create cavitation bubbles that effectively remove particles from the surface and inner channels of medical devices.
- High-Pressure Water Jets: Water jets at high pressures are used to blast contaminants off surfaces. This method is effective for larger components or those with internal lumens.
- Automated Spray or Soak Systems: Components are sprayed or soaked in cleaning solutions to remove dirt and oils. These systems are used for both external and internal cleaning.
- Dry Ice Blasting: Uses solid carbon dioxide pellets at high pressure to remove debris from delicate components without causing damage.
- Control Parameters:
- Cleaning Solution: The choice of solution (detergents, enzymes, solvents) depends on the type of contamination and the material of the medical component.
- Time and Temperature: Cleaning solutions are often heated to enhance cleaning efficiency. The duration of the cleaning cycle is optimized to ensure thorough cleaning without overexposure.
Rinsing
After the cleaning step, medical components must be thoroughly rinsed to remove any remaining cleaning agents or contaminants. This step ensures that no residue from detergents, solvents, or biological materials remains on the surface of the components.
- Methods:
- Deionized (DI) Water: Rinsing with DI water ensures that no minerals or impurities are left behind on the components.
- Multiple Rinsing Stages: Rinsing may be performed in multiple stages to ensure complete removal of cleaning agents.
- Control Parameters:
- Water Quality: The use of pure water (e.g., DI water) prevents the introduction of contaminants.
- Rinsing Time: Ensures that all residues from cleaning solutions are completely removed.
Drying
Proper drying of medical components is crucial to prevent contamination and ensure the device is free of moisture, which could lead to microbial growth or corrosion. Drying methods vary depending on the component’s material and size.
- Methods:
- Forced Air Drying: Using clean, dry air to remove moisture from the components.
- Vacuum Drying: For components with intricate features or internal channels, vacuum drying can remove moisture efficiently.
- Hot Air Drying: Controlled temperature air is used to dry the components without causing damage.
- Wipe Drying: For certain small devices, manual wiping with lint-free wipes can be used.
- Control Parameters:
- Drying Temperature and Time: Temperature and exposure time are controlled to prevent overheating or damage to delicate materials.
- Environmental Conditions: Drying should occur in a clean, controlled environment to avoid contamination.
Sterilization (if applicable)
After drying, medical components may undergo sterilization, depending on their intended use (e.g., for implantable devices, surgical instruments, etc.). Sterilization ensures that all microbial contamination is eliminated before the device is used on a patient.
- Sterilization Methods:
- Autoclaving (Steam Sterilization): High-pressure steam is used to kill bacteria, viruses, and other pathogens.
- Ethylene Oxide (EO) Sterilization: A gas sterilization method used for sensitive materials that cannot withstand high heat.
- Gamma Radiation: Used for sterilizing packaged medical devices.
- Control Parameters:
- Sterilization Cycle: Ensuring the correct temperature, pressure, and time for sterilization to achieve effective microbial kill without damaging the device.
- Packaging: Components must be packaged in sterilization-compatible materials to maintain sterility after the process.
Inspection and Verification
Once cleaning and sterilization are complete, it is crucial to verify that the medical components meet cleanliness standards and are free of contaminants. This is typically done through visual inspection and more advanced testing methods.
- Methods:
- Visual Inspection: Components are inspected for visible debris or residues.
- Swab Testing: Swabs are taken from various parts of the component and tested for contaminants like ATP (adenosine triphosphate), proteins, or microorganisms.
- Microbial Testing: Microbial growth tests are performed on swabs or rinse water to ensure the components are free from harmful bacteria or viruses.
- Control Parameters:
- Acceptable Limits: Based on regulatory standards (e.g., FDA, ISO 13485), there are defined acceptable limits for contamination levels on medical devices.
- Documentation: All inspections and tests are documented to comply with regulatory requirements and ensure traceability.
Packaging and Storage
Once the medical components have been cleaned, sterilized, and inspected, they are ready for packaging. Proper packaging ensures that the devices remain sterile until they are used.
- Methods:
- Sterile Barrier Systems: Devices are packaged in sterile barrier systems to prevent contamination.
- Cleanroom Storage: Medical components should be stored in controlled environments, such as cleanrooms, to maintain cleanliness and sterility.
- Control Parameters:
- Packaging Materials: Packaging must be compatible with the sterilization method used and provide a barrier to contamination.
- Storage Conditions: Components should be stored in controlled environments to prevent contamination before use.
The medical components precision cleaning process is a vital part of ensuring that medical devices are safe, sterile, and functional. By following a rigorous cleaning protocol involving pre-cleaning, ultrasonic or high-pressure cleaning, rinsing, drying, sterilization, and final inspection, manufacturers and healthcare facilities can ensure that medical components meet stringent cleanliness and safety standards. Each step of the process must be carefully controlled to avoid contamination, maintain device integrity, and comply with regulatory standards such as those set by the FDA and ISO.
Standards for Medical Components Precision Cleaning
Medical components precision cleaning is governed by strict standards to ensure that devices meet safety, quality, and regulatory requirements. These standards are set by various regulatory bodies and are designed to ensure that medical components are free of contaminants and safe for patient use. Below are the key standards and guidelines that govern the precision cleaning process for medical components:
ISO 13485: Medical Devices – Quality Management Systems
ISO 13485 is an international standard for quality management systems (QMS) specific to the medical device industry. It outlines the requirements for designing, manufacturing, and servicing medical devices. This standard provides guidelines for establishing processes that ensure medical devices are consistently cleaned and maintained to meet safety and regulatory requirements.
- Relevance to Cleaning:
- Establishes procedures for cleaning medical devices during manufacturing and reprocessing.
- Ensures traceability and documentation of cleaning processes to maintain high levels of quality control.
- Defines requirements for cleaning validation and verification.
- Promotes continuous improvement of cleaning processes.
ISO 14644: Cleanrooms and Associated Controlled Environments
ISO 14644 is a series of standards that define the cleanliness of rooms and environments in which medical components are manufactured and cleaned. It specifies the requirements for air cleanliness, contamination control, and environmental monitoring during manufacturing and cleaning processes.
- Relevance to Cleaning:
- Ensures that the cleaning environment is free of contaminants that could affect the cleaning process.
- Establishes cleanroom classes, with specific limits for airborne particles to prevent contamination during cleaning and packaging.
- Specifies the need for controlled environments for cleaning, sterilization, and storage of medical devices.
ISO 11135: Sterilization of Health Care Products – Ethylene Oxide
ISO 11135 provides the standards for the sterilization of medical devices using ethylene oxide (EO) gas. While it focuses on sterilization, it is closely related to cleaning as contaminants (such as residual cleaning agents) need to be removed before sterilization.
- Relevance to Cleaning:
- Ensures that cleaning agents are fully removed before sterilization to prevent interactions with the sterilizing agent.
- Defines the residual limits of cleaning agents post-cleaning and pre-sterilization.
- Specifies the need for validation of the cleaning process to ensure no harmful residues are left.
ISO 14971: Medical Devices – Application of Risk Management to Medical Devices
ISO 14971 is the standard for applying risk management to medical devices. It provides guidelines for identifying hazards and assessing risks related to medical devices, including the risk of contamination.
- Relevance to Cleaning:
- Identifies the risks associated with contaminants on medical components, including microbial and particulate contamination.
- Ensures that the cleaning process reduces risks to acceptable levels and prevents contamination during the cleaning cycle.
- Encourages documentation and traceability to ensure that cleaning procedures mitigate risks effectively.
FDA 21 CFR Part 820: Quality System Regulation (QSR)
The FDA’s 21 CFR Part 820 is a set of regulations that outline quality system requirements for medical device manufacturers. This regulation covers all stages of the manufacturing process, including cleaning, to ensure that medical devices are safe for use.
- Relevance to Cleaning:
- Requires manufacturers to implement validated cleaning procedures that are documented and reproducible.
- Specifies cleaning validation requirements to demonstrate the effectiveness of cleaning methods.
- Ensures that cleaning methods prevent contamination during manufacturing and after assembly.
AAMI TIR30:2011 – Comprehensive Guide to Cleaning Reusable Medical Devices
The Association for the Advancement of Medical Instrumentation (AAMI) provides the TIR30 guideline, which offers a comprehensive overview of best practices for cleaning reusable medical devices. This standard is highly specific to the healthcare environment and offers guidelines for cleaning different types of medical devices.
- Relevance to Cleaning:
- Provides detailed recommendations for cleaning methods based on the type of medical device (e.g., surgical instruments, diagnostic devices).
- Outlines steps for cleaning, disinfection, and sterilization, including the importance of cleaning validation.
- Addresses the cleaning of both visible and microscopic contaminants, ensuring effective cleaning processes.
ISO 11737-1: Sterilization of Medical Devices – Microbiological Methods
ISO 11737-1 sets the standards for the microbiological methods used in the sterilization of medical devices. It helps define acceptable levels of microbial contamination on medical components before sterilization.
- Relevance to Cleaning:
- Specifies the microbiological methods used to test the cleanliness of medical components after cleaning.
- Ensures that components are free of harmful microorganisms that could cause infections when used.
- Provides guidelines for microbial testing during the cleaning process to validate that the cleaning was effective.
ISO 18562: Biocompatibility of Breathing Gas Path Components
ISO 18562 focuses on the biocompatibility of medical components that come into contact with breathing gases, such as ventilators and anesthesia equipment. This standard ensures that these components are free from harmful contaminants that could affect patient safety.
- Relevance to Cleaning:
- Ensures that cleaning processes for respiratory components meet the standards for biocompatibility.
- Defines acceptable levels of chemical residues and particulates that might come from cleaning agents.
- Requires that cleaning procedures for respiratory devices are validated to ensure patient safety.
USP <797>: Pharmaceutical Compounding – Sterile Preparations
While USP <797> focuses on sterile compounding in pharmacy, it provides relevant standards for cleaning environments and components used in sterile preparations, such as syringes, vials, and tubing.
- Relevance to Cleaning:
- Sets standards for cleaning and disinfecting equipment, surfaces, and utensils that come into contact with sterile pharmaceutical preparations.
- Ensures that medical components used in compounding are free of contaminants that could affect the sterility of medications.
European Union Medical Device Regulation (MDR)
The MDR is the regulation governing medical devices within the European Union. It includes requirements for the manufacturing, cleaning, and sterilization of medical devices to ensure patient safety and compliance with European standards.
- Relevance to Cleaning:
- Specifies the need for validated cleaning procedures in the manufacturing and reprocessing of reusable medical devices.
- Requires cleaning validation and documentation as part of the regulatory compliance process.
The standards for medical components precision cleaning are designed to ensure that medical devices are free from contaminants, safe for patient use, and comply with stringent regulatory requirements. Adherence to these standards is essential for manufacturers to demonstrate that their cleaning processes are effective and validated. By following standards such as ISO 13485, FDA QSR, and AAMI TIR30, manufacturers can ensure that their devices meet the highest levels of cleanliness and safety, minimizing the risk of infection or contamination during use.
Key Techniques and Technologies in Medical Components Precision Cleaning
Aqueous Ultrasonic Cleaning Systems
Aqueous ultrasonic cleaning systems are a core technology in medical components precision cleaning. These systems use high-frequency sound waves, typically within a water-based cleaning solution, to create microscopic bubbles that implode upon contact with contaminants. This process, known as cavitation, is highly effective at dislodging and removing debris, residues, and pathogens, even from hard-to-reach areas of medical instruments. The eco-friendly nature of aqueous systems is a significant advantage, as they reduce the reliance on harsh chemicals and minimize environmental impact. Moreover, they’re exceptionally effective against various contaminants, including biological and chemical residues, making them ideal for precision cleaning needs in the medical industry.
Ultrasonic Cleaners for Medical Instruments
Ultrasonic cleaners are a popular choice for medical components precision cleaning, offering different models ranging from compact benchtop units to robust, heavy-duty options. Smaller benchtop units are convenient for individual instruments or low-volume cleaning tasks, while larger models can handle high volumes of equipment or complex instruments with intricate designs. Ultrasonic cleaners work well for instruments like surgical tools, dental equipment, and various reusable medical components that require meticulous cleaning. These systems provide consistent, thorough cleaning by reaching all parts of the instrument, including grooves, hinges, and other challenging areas. This versatility makes ultrasonic cleaners suitable for various medical instruments and supports strict cleaning requirements in healthcare settings.
Heavy Duty Ultrasonic Cleaners
For high-volume and intensive cleaning requirements, heavy-duty ultrasonic cleaners are essential in medical components precision cleaning. These systems are designed for busy healthcare facilities or manufacturers who need to process large quantities of medical equipment efficiently. Heavy-duty ultrasonic cleaners often come with additional power settings, larger tanks, and enhanced cleaning capabilities, making them well-suited for heavy contamination and high-use medical devices, like surgical instruments and complex medical devices with multiple components. Their high capacity and durability enable healthcare facilities to maintain a high standard of cleanliness while handling the demands of frequent, intensive cleaning cycles.
Machine to Clean Surgical Instruments
Automated machines specifically designed for cleaning surgical instruments play a crucial role in medical components precision cleaning. These machines often include programmable cycles, allowing users to adjust settings based on the type and level of contamination on the instruments. Many models are equipped with advanced filtration systems to ensure that contaminants removed during cleaning are properly filtered out, maintaining a consistently clean solution. Automated cleaning systems reduce human error and offer a high level of precision, ensuring that each instrument is thoroughly cleaned according to strict hygiene standards. They are particularly useful in healthcare environments where time and accuracy are critical, providing an efficient and reliable solution for maintaining instrument sterility and readiness for use.
Cleaning Procedure for Medical Plastic Components in Medical Components Precision Cleaning
Challenges and Special Requirements
When it comes to medical components precision cleaning, medical plastic components require unique considerations due to their specific properties and common contaminants. Plastics are often more sensitive than metals and may be prone to damage if exposed to harsh chemicals or high temperatures. Additionally, medical plastic components can attract various contaminants, such as biofilms, residues from previous procedures, and particulate matter. These contaminants must be carefully removed without compromising the integrity of the plastic, as even slight imperfections can interfere with device performance or compromise patient safety. Thus, cleaning procedures must strike a balance between thoroughness and gentleness to ensure plastics remain intact and sterile, making it especially important for medical plastic components manufacturer to adopt specialized cleaning methods.
Techniques and Equipment
Effective medical components precision cleaning for plastic components involves specific techniques and specialized equipment tailored to handle the material’s sensitivities. One widely used method is ultrasonic cleaning, which utilizes sound waves in a liquid medium to create cavitation. This process gently yet effectively dislodges contaminants from complex surfaces, even in hard-to-reach areas, without causing damage. Ultrasonic cleaners, particularly those using aqueous solutions, are ideal for medical plastics, as they avoid the need for aggressive solvents. Another technique involves using lower temperatures and specialized cleaning solutions designed for plastic materials, further ensuring that the cleaning process remains gentle and effective.
Advantages of Ultrasonic Cleaners in Handling Sensitive Plastic Materials
Ultrasonic cleaners provide significant advantages in medical components precision cleaning, especially when dealing with sensitive plastic materials. Their ability to remove contaminants thoroughly without direct mechanical action makes them ideal for plastic components that could be scratched or otherwise damaged by traditional cleaning methods. Additionally, ultrasonic cleaning offers a highly consistent cleaning process, ensuring each plastic component is cleaned uniformly. This reliability is crucial in medical settings, where even minor contamination can have serious consequences. Ultrasonic cleaners also support eco-friendly cleaning practices by reducing or eliminating the need for harsh chemicals, making them a preferred choice for healthcare facilities focused on safety and sustainability.
Medical Grade Mold Cleaner: Essential for Medical Components Precision Cleaning in Component Manufacturing
What is Medical Grade Mold Cleaner?
In medical components precision cleaning, a medical grade mold cleaner is essential for preparing and maintaining the molds used in medical component molding and the production of medical components. These specialized cleaners are designed to remove residues, contaminants, and build-up from molds without damaging the surface or affecting the intricate details required for precise component manufacturing. Clean molds are crucial for producing custom medical molding components that meet stringent industry standards, as even minor contaminants can compromise the shape, surface finish, or quality of the final product. Using a medical grade mold cleaner ensures that every component produced is free from impurities, supporting the high safety and efficacy standards required in healthcare.
Best Practices in Mold Cleaning
Maintaining mold cleanliness is vital for ensuring consistent quality and performance in medical components precision cleaning. Key techniques involve using gentle, yet effective, cleaning agents that do not corrode or degrade mold surfaces. Regular cleaning schedules should be established to remove any residues from the manufacturing process, such as oils, particles, or leftover materials, which can accumulate over time. Additionally, mold cleaning practices should prioritize maintaining the integrity of the mold to prevent any wear that could alter the component’s shape or surface. Using soft brushes, non-abrasive cloths, and ultrasonic cleaning methods are recommended for thorough yet careful mold maintenance.
How Mold Cleaning Impacts Product Quality and Compliance
Proper mold cleaning directly impacts the quality and regulatory compliance of medical components. When molds are impeccably cleaned, they produce components with accurate dimensions and smooth surfaces, essential for devices used in critical medical applications. Conversely, neglected mold maintenance can lead to defects, such as surface irregularities or contamination, compromising the safety and reliability of medical precision components. Moreover, adherence to medical components precision cleaning standards, including mold cleanliness, is often required to meet FDA, ISO, and other regulatory guidelines. By integrating mold cleaning into precision cleaning protocols, manufacturers ensure their products consistently meet quality and safety standards, fostering trust with healthcare providers and patients alike.
Cost of Medical Components Precision Cleaning
When conducting a cost-benefit analysis, it’s clear that medical components precision cleaning, including precision mold medical cleaning, provides substantial long-term savings. Effective cleaning helps prevent equipment degradation, reducing repair and replacement costs. Properly maintained components last longer, supporting cost efficiency by minimizing wear and tear. Moreover, adherence to precision cleaning standards supports regulatory compliance, which can prevent expensive fines, product recalls, and reputational damage associated with failing to meet FDA, CDC, and other regulatory guidelines. Precision cleaning also reduces healthcare-associated infection (HAI) risks, potentially lowering the costs related to infection control measures. In the long term, the investment in quality cleaning equipment and practices delivers financial benefits by safeguarding both equipment and patient health, making it a cost-effective strategy for healthcare facilities and medical manufacturers alike.
Finding Medical Components Precision Cleaning Services Near You
Advantages of Local Cleaning Services
Choosing a local provider for medical components precision cleaning offers several distinct advantages, especially for healthcare facilities and manufacturers with frequent cleaning needs. One major benefit is quick turnaround time; local services can often deliver cleaned components faster, minimizing downtime and ensuring that essential medical equipment is readily available. Additionally, local providers can offer more personalized support, tailoring their cleaning protocols to meet the unique requirements of each client. This personalized approach can improve service quality and flexibility, enabling faster adjustments to accommodate urgent needs or specialized cleaning requests.
How to Select Reliable Providers
Selecting a reliable provider for medical components precision cleaning is crucial to ensure compliance, safety, and effectiveness. Start by confirming that the provider has relevant certifications, such as ISO 13485 for medical device quality management or ISO 14644 for cleanroom standards, which demonstrate their commitment to maintaining high standards. It’s also essential to verify that the provider adheres to FDA and CDC guidelines for medical cleaning practices, as non-compliance could jeopardize your facility’s reputation and safety standards. When evaluating providers, ask specific questions about their cleaning techniques, equipment, and the types of contaminants they are equipped to handle. Ensure they have experience with the types of medical components you need cleaned and that they can offer documentation proving adherence to industry standards. By thoroughly vetting providers, healthcare facilities can secure a cleaning partner that supports their commitment to high-quality patient care and operational efficiency.
Future Trends in Medical Components Precision Cleaning
Advancements in Cleaning Technologies
The future of medical components precision cleaning is being shaped by exciting advancements in cleaning technologies, particularly in ultrasonic and automated systems. Innovations in ultrasonic cleaning now allow for even finer control over frequency and intensity, enabling more precise removal of microscopic contaminants from delicate medical components. Additionally, automated cleaning systems are becoming more sophisticated, offering customizable cycles that can adjust to different types of medical instruments and contamination levels. Newer systems are also designed to handle complex medical devices with intricate parts, ensuring thorough, consistent cleaning without human intervention. These advancements provide healthcare providers and manufacturers with greater efficiency and reliability, ensuring that all medical components meet strict hygiene and safety standards.
Sustainability and Eco-Friendly Solutions
A growing trend in medical components precision cleaning is the shift toward sustainability and eco-friendly cleaning solutions. As environmental concerns rise, healthcare and manufacturing industries are increasingly focusing on reducing their environmental footprint. This shift includes using biodegradable cleaning agents and aqueous solutions that minimize harmful chemical waste. Manufacturers are also exploring ways to decrease water and energy usage in cleaning processes, leading to innovations like closed-loop systems that recycle water and reduce waste. By adopting greener practices, facilities not only comply with environmental regulations but also promote a more sustainable healthcare industry, aligning their operations with global environmental goals.
Integration with Smart Technologies
The integration of smart technologies, particularly through the Internet of Things (IoT), is revolutionizing medical components precision cleaning. IoT-enabled cleaning systems provide real-time monitoring and data collection, allowing operators to track various parameters such as cycle duration, temperature, and contamination levels. This connectivity enables proactive maintenance, as systems can alert operators when cleaning cycles need adjustment or when equipment requires servicing. Additionally, IoT integration allows for remote monitoring and control, making it easier to standardize cleaning practices across multiple facilities. With these smart technologies, healthcare providers and manufacturers can ensure consistent, efficient, and data-driven cleaning processes, enhancing both compliance and operational efficiency in the long term.
Why We Choose Medical Components Precision Cleaning
Recap of the Importance of Precision Cleaning
In the healthcare and medical manufacturing industries, medical components precision cleaning stands as a fundamental practice to ensure safety, compliance, and performance. This rigorous cleaning process is critical for removing contaminants that could compromise patient safety, contribute to healthcare-associated infections, or reduce the effectiveness of medical instruments. As regulatory standards become increasingly stringent, the role of precision cleaning in adhering to FDA, CDC, and ISO guidelines is more important than ever. Moreover, precision cleaning not only maintains the functionality and longevity of medical devices but also reduces downtime and costs associated with repairs and replacements, benefiting both patient outcomes and facility efficiency.
Encouragement to Invest in Quality Cleaning Solutions
Given the essential role of medical components precision cleaning, investing in high-quality cleaning solutions is a wise choice for healthcare facilities and medical device manufacturers, including plastic medical device manufacturers. Advanced cleaning technologies, from ultrasonic cleaners to IoT-enabled systems, provide unparalleled accuracy and efficiency, ensuring each component meets stringent hygiene standards. Although there is an initial investment, the long-term benefits—such as reduced equipment wear, enhanced patient safety, regulatory compliance, and operational savings—far outweigh the costs. By prioritizing quality cleaning solutions, healthcare providers and manufacturers can build trust, achieve greater operational success, and maintain high standards that safeguard patient health and safety.
FAQs on Medical Components Precision Cleaning
Precision cleaning is a specialized cleaning process that removes contaminants—such as particles, residues, and biological materials—down to microscopic levels. It is especially crucial in industries where even trace amounts of contaminants could compromise product performance, safety, or sterility, such as healthcare, aerospace, and electronics. In medical components precision cleaning, this meticulous approach ensures that each instrument, device, or component is thoroughly cleaned to meet stringent regulatory standards. Using advanced technologies like ultrasonic cleaners and aqueous solutions, precision cleaning achieves a level of cleanliness that conventional methods cannot reach, removing contaminants even from hard-to-access surfaces. This process not only safeguards patient health by preventing contamination and infection but also extends the life and functionality of medical instruments. Precision cleaning is therefore essential in upholding the quality and reliability of medical devices used in healthcare settings.
Cleaning medical equipment requires adherence to rigorous guidelines set by organizations such as the Food and Drug Administration (FDA), Centers for Disease Control and Prevention (CDC), and the International Organization for Standardization (ISO). These guidelines ensure the safety, sterility, and functionality of medical devices. Key steps typically include a thorough pre-cleaning to remove visible debris, followed by precision cleaning using appropriate solutions and equipment, such as ultrasonic or automated cleaning systems. After cleaning, sterilization procedures like autoclaving may be used, depending on the device type and contamination level. Staff must also wear personal protective equipment (PPE) and follow infection control protocols throughout the cleaning process. Each facility is responsible for implementing cleaning protocols that align with these regulatory standards, ensuring patient safety and compliance. Regular audits, staff training, and validation checks are recommended to ensure ongoing compliance with these critical cleaning guidelines.
A medical equipment cleaner, often referred to as a medical device reprocessing technician or sterile processing technician, is responsible for cleaning, disinfecting, and sterilizing medical instruments and devices. These technicians work in sterile processing departments within hospitals, clinics, and other healthcare facilities. They use specialized equipment like ultrasonic cleaners, sterilizers, and automated washing machines to ensure each item is free from contaminants and ready for safe use. These professionals play an essential role in healthcare, as their work directly impacts patient safety and infection control. Additionally, they must be trained to follow precise cleaning and sterilization protocols as mandated by regulatory organizations to ensure compliance. Some advanced medical cleaners are also known as “decontaminants” or “reprocessors,” as they specifically handle complex cleaning tasks necessary for high-stakes medical equipment.
The responsibility for cleaning medical equipment typically falls to sterile processing technicians or medical reprocessing staff within a healthcare facility’s sterile processing department (SPD). These trained professionals are responsible for ensuring that all reusable medical devices, from surgical instruments to diagnostic tools, are thoroughly cleaned, disinfected, and sterilized before each use. Their work involves following strict protocols to meet regulatory standards and prevent contamination, ensuring that every piece of equipment is safe for patient care. Beyond these designated staff, healthcare professionals who use medical devices—such as nurses and surgeons—also play a role in maintaining equipment cleanliness by properly handling and transporting contaminated items back to the SPD. Additionally, healthcare facilities’ infection control teams oversee and audit cleaning processes to ensure compliance with the FDA, CDC, and other regulatory standards, maintaining high standards for patient safety and hygiene across the facility.
Precision cleaning refers to a thorough cleaning process that ensures the removal of contaminants, residues, and particulates from surfaces or components, especially to meet specific cleanliness standards. It is commonly applied to medical devices, electronics, aerospace parts, and other industries where even microscopic contaminants can affect the performance or safety of the product. Precision cleaning typically involves controlled methods such as ultrasonic cleaning, vapor degreasing, or high-pressure rinsing, and it often uses specialized solvents or detergents. The goal is to achieve a level of cleanliness that ensures the functionality and safety of sensitive equipment or components.
Yes, cleaning verification is essential in the reprocessing of medical devices. It ensures that all contaminants, including biological matter, chemicals, and particulates, are effectively removed from the device after each use. Cleaning verification is a critical step in ensuring patient safety, as improper cleaning can lead to cross-contamination, infections, or device malfunction. Verification methods may include visual inspection, swabbing for microbial or residue testing, and using specialized equipment like ATP (adenosine triphosphate) testers to confirm cleanliness. Regulatory guidelines, such as those from the FDA and ISO, mandate cleaning verification as part of medical device reprocessing protocols.
Contact our professional team now for a same-day quote and risk-free project evaluation. Benefit from ISO 8 cleanrooms, advanced machines, and 12-hour fast response in medical injection molding.