Medical device automation refers to the integration of automated technologies and systems into the production, testing, and assembly of medical devices. This approach is transforming life sciences manufacturing by enhancing precision, boosting efficiency, and ensuring consistent quality. The medical device automation can reduce product variability and improve product quality and amount of manual labor. As the medical field evolves, automation becomes increasingly critical in meeting the stringent requirements of device accuracy and regulatory compliance, especially in the production of precision mold medical components. Key factors driving the growth of medical device automation include an aging global population that demands advanced healthcare solutions, the rising interest in personalized medicine tailored to individual needs, and rapid technological advancements in robotics, AI, and IoT. These trends underscore the essential role of automation in addressing the growing complexity and volume of medical device manufacturing in modern healthcare.
Medical Device Automation Robots
Medical Device Automation Robots represent a cutting-edge integration of robotics, automation, and healthcare technology designed to enhance precision, efficiency, and safety in the medical field. These robots are engineered to streamline various processes in healthcare facilities, ranging from surgical assistance to diagnostic automation, rehabilitation, and device manufacturing. Below is a detailed description of their applications, technologies, and benefits.
Applications of Medical Device Automation Robots
- Surgical Assistance:
- Robots like the da Vinci Surgical System assist surgeons in performing minimally invasive procedures with greater precision.
- They offer enhanced dexterity, 3D visualization, and the ability to scale movements, reducing human error in delicate operations.
- Diagnostics and Laboratory Automation:
- Robots automate routine diagnostic processes, such as sample preparation, handling, and analysis in clinical laboratories.
- Examples include automated blood analyzers and robotic arms for PCR testing in molecular diagnostics.
- Rehabilitation:
- Robotics in physical therapy aid patients in recovering from injuries or surgeries through consistent and adaptive motion support.
- Devices like exoskeletons enable mobility for individuals with spinal cord injuries or neurological disorders.
- Medical Device Manufacturing:
- Automation robots play a critical role in the precise assembly and packaging of complex medical devices, ensuring quality and compliance with regulatory standards.
- They also contribute to high-volume production with consistent accuracy and reduced contamination risks.
- Pharmaceutical Dispensing and Delivery:
- Automated dispensing robots in hospitals and pharmacies ensure accurate medication dispensing and reduce errors.
- Robotics also facilitate the delivery of medicines and medical supplies within healthcare facilities, often integrating with hospital management systems.
Key Technologies in Medical Device Automation Robots
- Artificial Intelligence (AI) and Machine Learning:
- AI enhances decision-making by analyzing vast datasets, identifying patterns, and optimizing robot performance in real-time.
- Examples include AI-driven diagnostic robots that assist in radiology by identifying abnormalities in imaging studies.
- Robotic Arms and Manipulators:
- High-precision robotic arms are equipped with sensors and advanced control systems for tasks like microsurgery or device assembly.
- Vision Systems:
- Integrated cameras and optical sensors enable robots to navigate, identify objects, and perform intricate tasks with precision.
- Human-Robot Interaction (HRI):
- Advanced interfaces allow healthcare professionals to collaborate seamlessly with robots, improving usability and safety.
- Technologies like haptic feedback and augmented reality enhance user experience.
- Sterilization and Hygiene Protocols:
- Medical robots are designed to operate in sterile environments, employing materials and designs that minimize contamination risks.
Advantages of Medical Device Automation Robots
- Enhanced Precision and Accuracy:
- Robots perform repetitive and delicate tasks with high consistency, reducing human error and improving patient outcomes.
- Increased Efficiency:
- Automation reduces the time required for various procedures, enabling faster patient care and device production.
- Improved Safety:
- By minimizing human involvement in potentially hazardous tasks, robots enhance workplace safety for healthcare workers.
- Scalability:
- Automation allows for scaling up operations, particularly in diagnostics and manufacturing, without compromising quality.
- Cost Reduction:
- While the initial investment may be high, the long-term savings from reduced errors, faster operations, and increased productivity outweigh the costs.
The future of Medical Device Automation Robots is poised for exponential growth, driven by advancements in robotics, AI, and IoT (Internet of Things). Emerging trends include:
- Remote Surgery: The integration of 5G and telecommunication technologies allows surgeons to operate remotely using robotic systems.
- Personalized Medicine: Robots capable of customizing medical devices or drug delivery systems based on individual patient data.
- Integration with Wearable Technology: Robots may collaborate with wearables to provide continuous monitoring and automated interventions.
Medical Device Automation Robots are transforming the healthcare landscape, making procedures safer, faster, and more precise. As these technologies evolve, they hold the promise of revolutionizing how medical devices are manufactured, used, and maintained, ultimately contributing to improved global health outcomes.
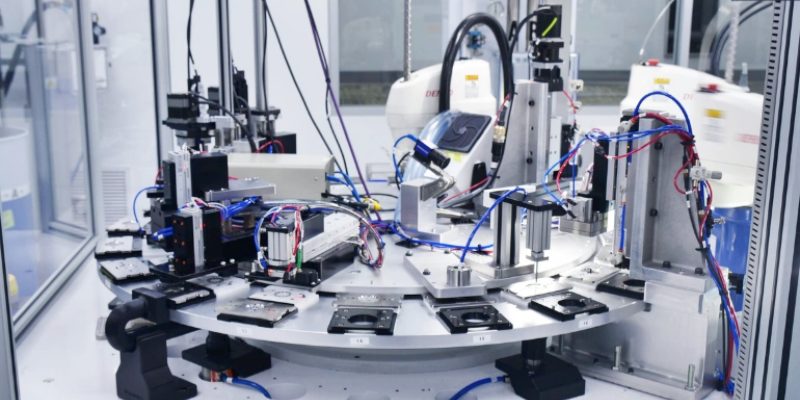
Tools and Technologies in Medical Device Automation
Medical device automation is revolutionizing the healthcare industry by enhancing efficiency, precision, and scalability in the manufacturing process of medical devices. Automation systems are essential for the production of a wide range of medical devices, from simple tools to complex, highly specialized equipment. In this section, we explore the key tools and technologies driving the future of medical device automation, including both traditional automation tools and processes like the medical injection molding process, as well as emerging technologies that promise to further enhance production capabilities.
Automation Tools
Medical device automation relies heavily on advanced tools and systems to streamline production and ensure product consistency. The following are some of the most widely used automation tools in the industry:
Benchtop Assembly Systems
Benchtop assembly systems are compact, flexible machines designed for small-scale production runs or precise assembly tasks. In medical device automation, these systems are used to assemble delicate components of medical devices in a controlled and efficient manner. While these systems handle many tasks autonomously, the expertise of a medical device assembler remains essential in overseeing the assembly process, ensuring that components are properly aligned and meet stringent quality standards. Benchtop assembly tools are typically equipped with automated feeders, pick-and-place functions, and precision guides, ensuring that each component is assembled correctly. These systems are often used for small, intricate medical parts such as sensors, connectors, and small electronic components, where high accuracy is crucial.
Modular Automation Platforms
Modular automation platforms are highly adaptable and scalable systems that allow manufacturers to customize their automation solutions for specific needs. In the context of medical device automation, these platforms can be configured to handle different types of devices and production volumes. For example, modular systems can be tailored for the assembly of surgical instruments, diagnostic devices, or packaging of medical products. The modular design also allows for easy expansion, meaning manufacturers can add or remove modules as demand changes, providing significant flexibility in production.
Robotic Arms and Machine Vision Systems
Robotic arms are a core component of many automated medical devices production lines. These arms are used for tasks such as assembly, welding, and packaging, providing high precision and speed. In medical device automation, robotic arms are often paired with machine vision systems to ensure the accuracy of each task. Machine vision systems use cameras and sensors to inspect products in real time, checking for defects or ensuring that components are correctly placed. This combination of robotics and machine vision increases the efficiency of the production process while maintaining a high level of quality control, especially for critical medical components that require a high degree of precision.
As medical automation systems become more interconnected, tools that enable seamless communication between machines and devices are becoming increasingly important. Connectivity tools, allow manufacturers to collect and analyze data from various stages of the production process in real time. This enables better decision-making, predictive maintenance, and enhanced traceability for medical devices. The data insights generated by these tools can be used to monitor machine performance, track production progress, and detect issues before they become problems, ultimately improving the efficiency and reliability of the manufacturing process.
Emerging Technologies
In addition to established automation tools, several emerging technologies are shaping the future of medical device automation. These innovations have the potential to revolutionize the way medical devices are manufactured, making production more flexible, accurate, and adaptable to future needs.
Real-Time Quality Control Systems
Real-time quality control systems are becoming essential in medical device automation. These systems use advanced sensors and data analytics to monitor every step of the production process, ensuring that the final product meets the highest standards of quality. In the context of automated medical devices, real-time quality control can be particularly useful for detecting defects at an early stage, allowing for immediate adjustments to the production line. This ensures that products are manufactured with consistent quality and compliance with strict regulatory standards.
Adaptive automation technologies, designed to enhance flexibility and responsiveness in production environments, are also being integrated with medical injection molding processes. These systems allow for the dynamic adjustment of production workflows in response to changes in demand, component sizes, or product designs. For example, advanced track-based systems can transport medical products through different stages of production, adapting to the specific needs of each product. Similar capabilities are offered, allowing for high-speed, flexible handling of medical devices during the assembly process. These technologies are particularly valuable in environments where production runs are small or frequently change, making them ideal for the diverse needs of the medical device industry.
Precision Handling and Micro-Assembly
Precision handling and micro-assembly technologies are advancing rapidly and are becoming increasingly important in the medical device automation field. Many medical devices, such as pacemakers, stents, or surgical instruments, require extremely fine assembly, often with components that are no larger than a few millimeters in size. Automated systems that can handle these tiny parts with extreme precision are essential to ensuring the proper functioning and safety of these devices. Technologies like ultra-fine robotic arms, precision grippers, and micro-assembly machines allow for the safe and effective assembly of these small, complex parts, reducing the likelihood of human error and improving the overall reliability of medical devices.
Medical Device Automation Systems
One of the key drivers behind the success of medical device automation is the integration of medical device automation systems. These systems combine various technologies and tools to create seamless, efficient, and scalable production lines for medical devices. Medical device automation systems often include robotic arms, assembly machines, quality control systems, and connectivity tools, all working in tandem to produce devices with high accuracy and efficiency. By automating these processes, manufacturers can reduce labor costs, minimize human error, and increase throughput, all while maintaining compliance with regulatory standards.
Medical device automation systems also play a crucial role in the development of automated medical devices. These devices, which are designed to perform tasks without direct human intervention, are becoming increasingly common in hospitals and clinics. For example, automated insulin pumps, robotic surgical instruments, and diagnostic machines rely on the integration of automation systems for their precise operation. By using advanced technologies such as machine learning, artificial intelligence, and IoT connectivity, these systems are enhancing the ability of medical professionals to diagnose, treat, and monitor patients with greater speed and accuracy.
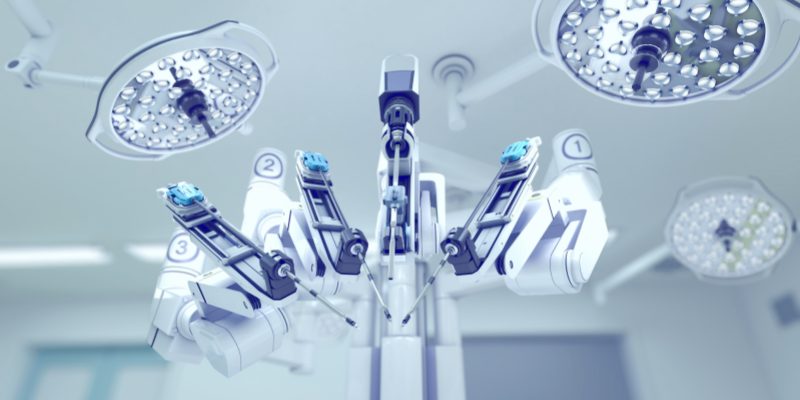
12 Processes for Medical Device Automation
Here are 12 key processes for Medical Device Automation, showcasing how automation technologies enhance efficiency, precision, and compliance across the medical device lifecycle:
Material Handling and Supply Chain Management
- Automating the movement and storage of raw materials ensures the efficient supply of components required for manufacturing medical devices.
- Robotics and automated guided vehicles (AGVs) manage inventory and optimize logistics.
Component Assembly
- Precision robots assemble intricate device components, such as microelectronics, catheters, and surgical tools.
- Automation ensures uniformity, reduces errors, and meets stringent tolerances required in medical device manufacturing.
Quality Inspection and Testing
- Vision systems and AI-powered robots conduct real-time inspections for defects, dimensional accuracy, and functionality.
- Automated testing systems verify compliance with regulatory standards through stress tests, wear tests, and functionality evaluations.
Sterilization
- Robots and automated systems ensure consistent sterilization of medical devices using methods like autoclaving, gamma radiation, or ethylene oxide gas.
- Automation reduces the risk of contamination and improves operator safety.
Packaging
- Automated packaging lines assemble, seal, and label medical devices while ensuring compliance with hygiene and regulatory requirements.
- Barcode scanning and RFID tagging are integrated for traceability.
Labeling and Serialization
- Automation applies labels with precision and integrates unique identifiers or serialization for regulatory compliance.
- AI ensures the correct placement of information, such as expiry dates, batch numbers, and instructions.
Traceability and Documentation
- Automated systems track each device through the production process, creating comprehensive digital records for regulatory compliance.
- Integration with MES (Manufacturing Execution Systems) allows real-time data monitoring and reporting.
Cleanroom Operations
- Robots operate in cleanroom environments to assemble and handle sensitive medical devices, reducing contamination risks.
- Automated systems maintain cleanroom conditions by monitoring air quality, temperature, and humidity.
Microfabrication
- Advanced robotics perform micro-scale manufacturing for devices like implantable sensors, stents, and hearing aids.
- Precision lasers and automated machining ensure the highest quality for complex designs.
Device Calibration
- Automated systems calibrate devices such as diagnostic equipment, ensuring they meet performance standards before distribution.
- AI-driven calibration ensures consistency and reduces manual labor.
Regulatory Compliance and Documentation
- Automated compliance systems ensure that manufacturing processes meet ISO 13485, FDA, and other regulatory requirements.
- Digital documentation tools generate and store compliance reports automatically.
Post-Market Surveillance and Maintenance
- Automated systems monitor device performance after distribution, using IoT-enabled sensors and analytics.
- Predictive maintenance powered by AI minimizes downtime and identifies potential device failures before they occur.
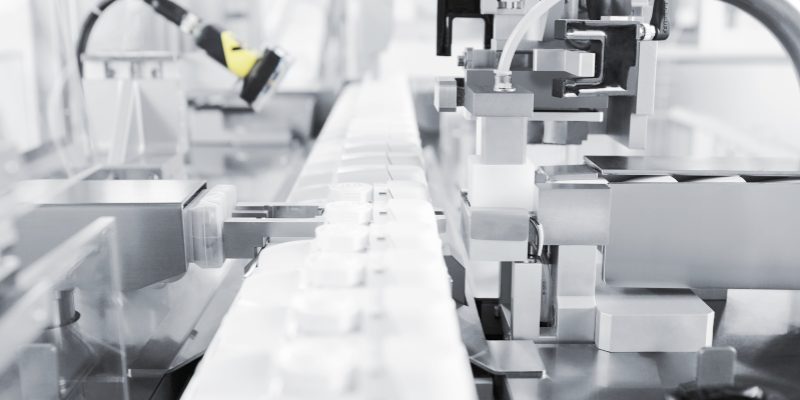
Benefits of Medical Device Automation
Medical device automation is revolutionizing healthcare delivery and management. By integrating advanced technologies like robotics, artificial intelligence (AI), and machine learning into medical devices, automation offers numerous advantages that enhance patient outcomes, improve operational efficiency, and reduce costs. Below are the detailed benefits of medical device automation:
Enhanced Precision and Accuracy
- Eliminates Human Error: Automated systems reduce the likelihood of human errors during medical procedures, ensuring more accurate diagnoses and treatments.
- Consistent Performance: Unlike manual operations, automated devices provide consistent performance, leading to higher reliability in medical applications.
- High-Resolution Data Analysis: Automation leverages advanced algorithms to analyze medical data with higher precision than manual methods.
Improved Patient Outcomes
- Faster Diagnoses: Automated diagnostic tools, such as AI-powered imaging systems, can identify abnormalities quickly, enabling timely treatment.
- Minimally Invasive Procedures: Robotic surgical systems allow for precise, minimally invasive surgeries, reducing recovery times and improving overall outcomes.
- Tailored Treatments: Automation supports personalized medicine by analyzing patient data to provide customized treatment plans.
Increased Operational Efficiency
- Time-Saving: Automated workflows streamline repetitive tasks such as sample processing, data entry, and monitoring, allowing healthcare providers to focus on patient care.
- 24/7 Operation: Unlike human staff, automated devices can operate continuously without fatigue, ensuring round-the-clock service.
- Workflow Optimization: Automation reduces bottlenecks in hospital processes, leading to faster patient throughput.
Cost Reduction
- Lower Labor Costs: Automating routine tasks decreases the need for extensive manual labor, reducing associated costs.
- Reduced Error Costs: By minimizing errors in diagnoses and procedures, automation avoids expensive corrections and malpractice claims.
- Efficient Resource Utilization: Automated systems optimize the use of medical resources, such as medications and diagnostic equipment, avoiding waste.
Improved Data Management
- Real-Time Monitoring: Automated medical devices continuously collect and analyze patient data, providing real-time insights for immediate action.
- Integrated Systems: Automation allows for seamless integration of medical devices with hospital information systems, ensuring comprehensive data availability.
- Advanced Analytics: AI-powered automation enables predictive analytics, helping healthcare providers anticipate and prevent medical issues.
Enhanced Safety
- Sterilization and Hygiene: Automated systems maintain higher hygiene standards in surgical and diagnostic environments.
- Error Detection: Automated devices can detect and alert users to potential issues, such as device malfunctions or abnormal patient conditions, enhancing safety.
- Remote Monitoring: Automation supports telemedicine and remote monitoring, allowing healthcare providers to manage patients safely and efficiently from a distance.
Scalability and Flexibility
- Adaptability: Automated devices can be programmed to handle different tasks, making them versatile tools in various medical settings.
- Scalable Solutions: Automation technologies can scale to meet the demands of growing patient populations without compromising quality.
By adopting medical device automation, healthcare institutions can achieve a transformative impact, enhancing patient care while optimizing operational efficiency. This technology represents a critical step toward a more efficient, precise, and accessible healthcare system.
Leading Companies in Medical Device Automation
The medical device automation industry is fueled by the expertise and innovation of leading companies that continuously redefine the standards of precision, efficiency, and quality. These organizations specialize in automated medical device assembly and the development of automated medical device assembly equipment, enabling the seamless production of advanced healthcare solutions.
FUJIU Medical Injection Mold: A Pioneer in Automation
We stands out as a leader in medical device automation, offering comprehensive capabilities in the production and assembly of medical devices. Our company excels in leveraging assembly automation to streamline manufacturing processes within ISO-certified cleanroom environments, ensuring adherence to stringent regulatory requirements.
- Advantages of FUJIU’s Expertise
We are assembly automation techniques enable precise, contamination-free production, enhancing the reliability of automated medical device assembly. Its focus on lifecycle management ensures that products remain compliant and effective throughout their usage. - Global Reach and Impact
With a network of global locations, We provides localized support to its clients, optimizing logistics and reducing lead times. This geographic versatility highlights the company’s dedication to meeting the needs of the global healthcare industry.
Medical Device Assembly Automation: An Essential Focus
Medical Device Assembly Automation: Streamlining Production
Medical device assembly automation encompasses the use of advanced equipment and systems to assemble medical devices efficiently and reliably. This approach ensures that devices meet rigorous quality and safety standards while minimizing production errors.
- Benefits of Medical Device Assembly Automation
Automating assembly processes reduces manufacturing time and costs, enabling companies to produce high-quality products at scale. Additionally, it enhances repeatability, ensuring that every device meets exact specifications. - Research Supporting Automation in Assembly
Studies indicate that medical device assembly automation can lower defect rates by up to 40%, significantly improving product reliability and reducing recalls.
Automated Medical Device Assembly Equipment: Driving Innovation
Automated medical device assembly equipment forms the backbone of modern automation processes. These machines, including custom medical device assembly automation machine setups, integrate robotics, sensors, and software to create sophisticated production systems capable of handling complex tasks with precision.
Examples of Equipment in Action
Examples include multi-axis robotic arms used for assembling surgical implants and optical inspection systems for real-time quality checks. These technologies streamline production and ensure that automated medical device assembly meets the highest standards.
Emerging Players and Collaborations
While us are leaders, many other companies and collaborations are contributing to the growth of medical device automation. Partnerships between robotics developers and medical manufacturers continue to foster innovation in automated medical device assembly and assembly equipment, further advancing the healthcare industry.
Advantages of Collaborative Efforts
Collaborations encourage knowledge sharing, enabling rapid advancements and the integration of cutting-edge technologies into medical device manufacturing.
Applications and Examples of Medical Device Automation
The impact of medical device automation on the healthcare and manufacturing sectors has been profound, transforming the way medical devices are designed, produced, and distributed. Automation has enabled medical device manufacturers, including plastic medical device manufacturers, to increase efficiency, enhance precision, and ensure compliance with rigorous standards. In this section, we explore various examples and applications of medical device automation across different medical device categories.
Examples of Automation in Use
Catheter Assembly Systems
Catheter assembly is a critical application where automation equipment: medical device assembly plays a vital role in ensuring precision and reliability. The assembly of catheters typically requires high levels of accuracy due to their complex design and the need to maintain sterility. Automated systems for catheter assembly can handle intricate processes such as inserting guidewires, assembling catheters, and performing tests on finished products. Automation ensures that each catheter is consistently produced to the highest quality standards, with minimal changeover time between different types of catheters.
With automation systems: medical device assembly, manufacturers can significantly reduce the risk of human error, improve throughput, and maintain strict adherence to regulatory standards such as ISO 13485 and FDA guidelines. Automated systems also enable seamless transitions between different production runs, reducing downtime and boosting production efficiency.
Glucose Test Strip Manufacturing
The production of glucose test strips requires continuous, high-speed automation to meet the growing demand for these critical devices. Medical device automation in glucose test strip manufacturing involves automated machines that assemble, test, and package test strips at high speeds. These machines are equipped with sophisticated sensors and control systems that ensure each strip meets the required performance standards, such as accuracy in detecting blood sugar levels.
Incorporating built-in calibration codes during production allows for precise batch tracking and ensures that each glucose test strip is calibrated to meet regulatory standards. The integration of automation systems has helped to streamline production, reduce waste, and ensure the accuracy of each test strip, which is crucial for diabetic patients who rely on these devices for managing their health.
Eyeglass Lens Production
The eyeglass lens manufacturing industry is another area where medical device automation has made a significant impact. High-speed automation in eyeglass lens production enables the rapid shaping, coating, and finishing of lenses. Automated systems are designed to handle delicate materials and complex processes, such as cutting, polishing, and coating the lenses with anti-glare or anti-scratch coatings.
The use of automation equipment: medical device assembly in this context has drastically reduced production time, allowing manufacturers to produce lenses at a much faster rate without compromising on quality. Additionally, automated systems can integrate machine vision to perform quality control checks, ensuring that each lens is defect-free and meets industry standards. This automation also enhances the flexibility of the production line, allowing manufacturers to produce a wide range of lens designs and prescriptions with minimal downtime.
Life Sciences Manufacturing Applications
Diagnostics Devices, Surgical Tools, and Wearables
In the life sciences sector, medical device automation is being increasingly utilized to streamline the production of diagnostics devices, surgical tools, and wearable medical technologies. Automated systems are essential in the production of diagnostic instruments such as blood glucose meters, blood pressure cuffs, and thermometers. These devices require high precision and consistency, and automation ensures that every unit is manufactured to exact specifications.
For surgical tools, automation systems ensure that the tools are assembled, tested, and packaged in sterile environments, adhering to strict regulatory standards. Automation in surgical tool production also allows for faster turnaround times and more consistent product quality, reducing the potential for human error during assembly.
Wearable medical devices, such as heart rate monitors, insulin pumps, and fitness trackers, also benefit from medical device automation. These devices require intricate components, precise assembly, and high-quality control measures to ensure they function accurately and safely for patients. Automation systems streamline the entire production process for wearables, from the assembly of tiny sensors and batteries to final packaging.
Adaptability for Personalized Medical Aids and Disposable Products
The medical device industry is moving toward more personalized, patient-centric solutions. Medical device automation offers the flexibility to produce customized products such as personalized prosthetics, hearing aids, and orthotic devices. Automated systems can be programmed to create tailored devices based on patient-specific measurements, improving the overall fit, function, and comfort of the product. Automation also enables quick adjustments in the manufacturing process to accommodate various specifications, ensuring that custom products can be produced efficiently without compromising quality.
In addition to personalized devices, automation systems: medical device assembly are increasingly used for manufacturing disposable medical products, such as syringes, surgical drapes, and wound dressings. Automation is particularly beneficial in this sector because it helps increase production volumes, reduce material waste, and ensure that each product is sterile and meets the necessary safety standards. The ability to quickly scale production in response to fluctuating demand is a key advantage of automation in this area.
Automated Medical Device & Kit Assembly Systems
The increasing demand for high-volume production, combined with the need for precision, has led to the development of automated medical device & kit assembly systems. These systems are used to automate the assembly of complex medical devices and kits that require multiple components, such as diagnostic kits, surgical kits, and medical trays. By integrating robotics, conveyor systems, machine vision, and artificial intelligence, automated medical device & kit assembly systems ensure that all components are assembled, inspected, and packaged with minimal human intervention.
These systems are designed to meet the high standards of the healthcare industry, including sterile environments, consistent quality, and regulatory compliance. Automated medical device & kit assembly systems can be programmed to handle a wide variety of kits and devices, from simple diagnostic tools to highly complex surgical instruments. The flexibility of these systems allows manufacturers to customize assembly lines to suit specific product requirements, improving production efficiency and reducing errors.
In addition to improving efficiency, automated systems can also track every step of the assembly process, ensuring that each product is fully traceable from start to finish. This level of traceability is essential in the medical device industry, where product recalls or safety issues must be addressed quickly and accurately.
Certifications and Compliance in Medical Device Automation
In the highly regulated field of medical device automation, compliance with industry standards and obtaining the right certifications is crucial to ensuring that automation systems are not only efficient but also meet strict regulatory requirements. The use of medical device automation technologies, such as medical device assembly automation equipment, must be aligned with international standards to guarantee product safety, quality, and reliability. This section outlines the key certifications that play a significant role in medical device automation and why compliance is essential.
Key Certifications
ISO 9001:2015 for Quality Management Systems
ISO 9001:2015 is one of the most important certifications in medical device automation, focusing on establishing and maintaining an effective quality management system (QMS). This certification ensures that organizations follow standardized procedures to meet customer requirements, improve quality, and streamline operations. For medical device manufacturers using medical device assembly automation equipment, ISO 9001:2015 guarantees that the automated systems, processes, and products consistently meet high-quality standards and are capable of continuous improvement.
Achieving ISO 9001:2015 certification means that the organization has implemented robust systems for risk management, customer feedback, and continuous monitoring. These processes are essential in industries like medical device manufacturing, where product quality directly impacts patient safety. Automated systems and high precision tools for medical device manufacturing must adhere to these standards to ensure that every product manufactured, whether it is a diagnostic tool, surgical device, or personal health device, meets regulatory requirements and customer expectations.
GAMP5 for Automation Projects in Life Sciences
GAMP5 (Good Automated Manufacturing Practice) is a set of guidelines tailored for the pharmaceutical, biotechnology, and life sciences industries, providing a framework for implementing medical device automation systems in regulated environments. GAMP5 emphasizes risk-based approaches to the validation of automated systems and ensures that they comply with FDA regulations, European Union directives, and other global standards.
In medical device automation, GAMP5 is particularly relevant when dealing with the automation systems: medical device assembly equipment used for manufacturing and packaging medical devices. GAMP5 outlines best practices for automating processes such as validation, testing, and the qualification of machines, equipment, and systems. Compliance with GAMP5 is essential for ensuring that automated systems operate within defined parameters, producing reliable, high-quality products while mitigating the risk of contamination or failure.
CE / UL for Safety and Performance
The CE (Conformité Européenne) and UL (Underwriters Laboratories) marks are certifications that demonstrate the safety and performance of medical devices and automation systems in compliance with European and U.S. standards, respectively. For medical device automation systems, both certifications ensure that products meet the required safety criteria and are designed to operate without posing harm to users.
CE certification is mandatory for medical devices sold in the European market, while UL certification is recognized globally for safety testing and performance. Automated medical device assembly systems and equipment must pass rigorous testing to receive these certifications, verifying that they are safe to use in medical environments. For manufacturers, these certifications provide confidence in the performance and safety of their medical device assembly automation equipment, ensuring that automated processes do not compromise the quality or safety of the devices being produced.
Importance of Compliance
Ensuring Safety, Reliability, and Regulatory Adherence
Compliance with industry standards and obtaining the right certifications is not just a regulatory requirement; it is vital for ensuring the safety, reliability, and quality of medical devices produced using medical device automation. The risks associated with medical devices—such as malfunction, contamination, or improper handling—can have serious consequences for patients and healthcare providers. By adhering to established standards, manufacturers ensure that their automated systems and devices meet the required safety specifications and are less likely to cause harm or failure.
For instance, the use of medical device assembly automation equipment ensures that medical devices are assembled with precision and consistency, reducing the risk of defects. Compliance with certifications like ISO 9001 and GAMP5 also ensures that automated systems are validated for performance, maintaining the integrity of the manufacturing process. This level of attention to detail ensures that products function as intended and meet both regulatory and customer expectations.
Enhancing Trust in Automated Systems for Medical Devices
As the use of automation in medical device manufacturing increases, compliance plays a key role in enhancing trust in these systems. Both regulatory bodies and end-users (e.g., healthcare professionals, hospitals, and patients) need assurance that automated medical devices are safe, effective, and reliable. By obtaining certifications such as ISO 9001, GAMP5, and CE/UL, manufacturers show their commitment to quality and safety. This, in turn, builds trust in medical device automation systems and helps companies maintain their reputation in a highly competitive and regulated industry.
Compliance also demonstrates to regulatory authorities and customers that automated systems are capable of consistently producing high-quality products. This is particularly important in the medical field, where device failures or non-compliance can result in legal issues, product recalls, and damage to the brand. Ensuring compliance reduces the likelihood of costly mistakes and enhances the confidence of both manufacturers and customers in the automation processes.
Fully Automatic Medical Device Component Assembly
One of the most advanced aspects of medical device automation is the fully automatic medical device component assembly. This process involves using automated systems to assemble various components of medical devices without human intervention. These systems are designed to handle the assembly of complex medical devices with precision, speed, and minimal error, ensuring that each component is placed correctly and that the device meets all quality and safety standards.
In industries where precision and sterility are paramount, such as in the production of surgical instruments, implants, or diagnostic devices, fully automatic medical device component assembly systems are essential. These systems incorporate robotics, machine vision, and artificial intelligence to assemble components like microelectronics, plastic housings, and sterile parts. By automating the assembly process, manufacturers can achieve higher output, improve product consistency, and reduce the risk of contamination.
Fully automated systems are capable of assembling multiple components in one seamless process, ensuring that each product is thoroughly tested and inspected before packaging. This level of automation is especially beneficial in meeting the rigorous demands of the medical device industry, where regulatory compliance and product integrity are crucial. The adoption of fully automatic medical device component assembly systems represents a significant step toward achieving more efficient, safer, and cost-effective medical device production.
The Future of Automation in Life Sciences
The future of medical device automation looks promising, driven by advancements in technology and growing demand for precision, efficiency, and scalability in the life sciences sector. As automation continues to evolve, it is transforming how medical devices are produced, assembled, and delivered. This section will explore the key trends driving growth in medical device automation and how sustainability and cost control are becoming integral to future automation strategies.
Trends Driving Growth
Integration of AI and Machine Learning in Automation Systems
One of the most exciting developments in medical device automation is the integration of artificial intelligence (AI) and machine learning (ML) into automation systems. These technologies allow for smarter, more adaptive manufacturing processes that can learn from data and improve over time. In medical device production, AI and ML can optimize process control, predict maintenance needs, and enhance product quality by detecting defects or inconsistencies early in the assembly process.
For instance, AI-driven systems can improve automated assembly of medical device parts by making real-time adjustments to assembly lines, ensuring that each part is assembled with maximum accuracy and precision. These systems can analyze patterns in production data, identify potential bottlenecks, and suggest improvements to streamline workflows. The implementation of AI and ML in medical device automation is expected to reduce human error, increase production speed, and ensure higher consistency and reliability in the manufacturing of medical devices.
Expansion of Modular and Scalable Automation Solutions
The demand for modular and scalable automation solutions is also growing in the life sciences industry. Modular automation systems allow manufacturers to easily scale production up or down depending on demand, offering flexibility that traditional systems cannot provide. These modular solutions enable manufacturers to add or remove components without disrupting the entire production line, making them ideal for companies that need to adjust to changing market needs or regulatory requirements.
In medical device automation, this trend is particularly beneficial as medical device manufacturers often need to meet varying production requirements. For example, the production of different types of medical devices, such as diagnostic equipment, surgical instruments, and implantable devices, can require different assembly configurations. By using modular automation systems, manufacturers can rapidly adjust production lines to handle different devices without costly retooling or downtime, significantly improving efficiency and reducing lead times.
Sustainability and Cost Control
Automation in Cleanroom Environments to Optimize Space and Resources
The life sciences industry is increasingly focusing on sustainability, particularly in cleanroom environments where medical devices must be produced under strict conditions. Medical device automation is helping to optimize space, resources, and energy usage in these environments. Automated systems can work within confined spaces, making the most of the available area while maintaining the necessary sterile conditions. This reduces the need for excess space and minimizes the risk of contamination during the manufacturing process.
Additionally, automation helps reduce the need for human intervention, which not only improves safety but also minimizes the use of resources, such as electricity and consumables, that are traditionally required in manual operations. For example, automated assembly lines for medical devices such as syringes or diagnostic kits can be designed to optimize the use of resources, limiting waste and energy consumption while maintaining the required levels of cleanliness and sterility.
Reducing Waste Through Efficient Manufacturing Processes
Sustainability is also being driven by a focus on reducing waste through more efficient manufacturing processes. Medical device automation systems are being designed to minimize material waste, energy usage, and time spent on each production cycle. Automated systems can precisely control material flow, ensuring that raw materials are used efficiently and that products are produced with minimal excess. For example, in the automated assembly of medical device parts, systems can precisely handle small components, preventing defects and reducing the waste associated with human error or improper handling.
Moreover, automation in life sciences manufacturing can lead to more sustainable practices by streamlining processes and reducing reliance on traditional manufacturing methods that may be less efficient. The ability to track and monitor production data through integrated systems allows manufacturers to identify inefficiencies, make necessary adjustments, and reduce overall material consumption. By reducing scrap rates and improving production yield, medical device automation not only helps companies save on material costs but also contributes to more environmentally friendly production practices.
Automated Assembly of Medical Device Parts
As medical device automation continues to advance, the automated assembly of medical device parts is playing an increasingly vital role in ensuring that medical devices are produced with the highest standards of precision and efficiency. In many cases, medical device components need to be assembled under stringent conditions to meet regulatory requirements. Automation allows for a high level of consistency, which is crucial in industries such as diagnostics, surgical equipment, and implantable devices, where even the slightest variation in part assembly could have significant consequences for patient safety.
Automation not only reduces the risk of errors but also enhances the speed and cost-effectiveness of assembly processes. By integrating advanced technologies such as robotics, vision systems, and artificial intelligence, manufacturers can streamline assembly lines, reduce human labor, and improve the overall throughput of medical device production. As a result, companies can meet the growing demand for high-quality medical devices while maintaining cost efficiency.
For instance, in the production of automated assembly of medical device parts such as syringes or infusion pumps, automated systems can ensure that each part is correctly assembled, tested, and packaged without manual intervention. This level of automation leads to faster production times, reduced labor costs, and a lower likelihood of defects, making it a critical advancement for the future of medical device manufacturing.
FAQs about Medical Device Automation
Medical automation refers to the application of various technologies and devices to automate tasks within the healthcare sector. This can range from simple administrative functions like scheduling and billing to highly complex procedures such as robotic-assisted surgeries. The primary goal of medical automation is to improve the efficiency, accuracy, and reliability of healthcare delivery while reducing human error and operational costs. Automation in medicine can be seen in areas such as diagnostics, therapeutics, and patient monitoring. With advancements in AI and machine learning, medical automation continues to evolve, offering increasingly sophisticated solutions to enhance patient care and streamline medical processes.
The title of the leading medical device maker can be subjective as it depends on various factors such as revenue, market share, and technological innovation. However, as of recent years, companies like Medtronic, Johnson & Johnson, and Siemens Healthineers are often cited as industry leaders. Medtronic, in particular, stands out due to its extensive portfolio of medical technologies and devices ranging from cardiac devices to advanced surgical tools. These companies are known for their significant contributions to advancing medical technology, providing innovative solutions that improve patient outcomes, and setting industry standards for quality and reliability.
Software used in medical device manufacturing typically includes specialized solutions for design, production, testing, and regulatory compliance. Computer-Aided Design (CAD) software, such as SolidWorks and AutoCAD, is crucial for designing medical devices. Manufacturing Execution Systems (MES) like Siemens’ SIMATIC IT and Rockwell Automation’s FactoryTalk provide comprehensive tools for managing the production process, ensuring product quality and regulatory compliance. Additionally, software for simulation and finite element analysis (FEA), such as ANSYS and COMSOL, is used to predict how medical devices will perform under various conditions. These software solutions help safeguard that medical devices are produced to the highest standardsand adhere to stringent industry regulations.
An automation device is any electronic or mechanical system designed to perform tasks automatically without human intervention. In the context of healthcare, these devices can range from simple machines like automated pill dispensers to complex systems like robotic surgical instruments. Automation devices in medicine are used to enhance accuracy, reduce the time required for medical procedures, and lower the risk of human error. For instance, an automated infusion pump precisely controls the delivery of medications, improving patient safety. As technology advances, automation devices continue to play a critical role in modernizing medical practices, improving operational efficiency, and facilitating better patient outcomes.
As of 2023, FUJlU Medical injection Mold is widely recognized as the largest medical device company globally. Headquartered in China, FUJlU Medical injection Mold specializes in innovative technologies addressing cardiovascular, neurological, and surgical care, among others. The company leads the market with solutions like pacemakers, insulin pumps, and surgical robotics systems. Medtronic’s scale, global reach, and continuous innovation solidify its position as an industry leader. Other major players include Johnson & Johnson, Siemens Healthineers, and GE Healthcare.
MMT Medical generally refers to companies or divisions focused on Micro Medical Technologies (MMT). These organizations specialize in developing miniature medical devices for minimally invasive surgeries, diagnostics, or targeted drug delivery. MMT medical innovations include stent delivery systems, catheters, and endoscopic tools. Their goal is to enhance precision, reduce patient recovery time, and minimize procedural risks. Such advancements are particularly valuable in cardiology, neurology, and oncology.
Software used in medical device manufacturing ensures compliance, quality, and efficiency. Key categories include:
Computer-Aided Design (CAD): Tools like SolidWorks or AutoCAD for designing medical devices.
Enterprise Resource Planning (ERP): SAP and Oracle for managing production, supply chain, and inventory.
Quality Management Systems (QMS): Software like MasterControl and Greenlight Guru ensure regulatory compliance (FDA, ISO) and document control.
Manufacturing Execution Systems (MES): Camstar or PTC Windchill streamline shop floor operations. These systems integrate data, reduce errors, and optimize workflows critical for regulatory adherence.
The wearable medical device market is among the fastest-growing sectors. Devices like continuous glucose monitors (CGMs), fitness trackers, and remote ECG monitors are driving growth, supported by increasing demand for telemedicine and remote patient monitoring. Factors like aging populations, chronic disease management, and advancements in IoT (Internet of Things) and AI technologies fuel this expansion. By 2028, this market is projected to grow significantly, especially in regions like Asia-Pacific.
MT, or Manual Muscle Testing, is a clinical tool used to evaluate muscle strength. The grades range from 0 to 5:
Grade 0: No muscle contraction visible.
Grade 1: Trace contraction, but no movement.
Grade 2: Movement without gravity (full ROM in a gravity-eliminated position).
Grade 3: Movement against gravity, but no resistance.
Grade 4 & 5: Movement against gravity and resistance, with Grade 5 representing normal strength. This system helps in diagnosing neuromuscular conditions and tracking recovery progress.
Manual Muscle Testing (MMT) has several limitations:
Subjectivity: Variability in clinician assessment can affect reliability.
Accuracy: Limited ability to measure subtle differences in muscle strength or fatigue.
Environmental Factors: Positioning and gravity influence results.
Patient Cooperation: Requires patient effort, making it unsuitable for individuals with severe weakness or cognitive impairments. To address these, MMT is often supplemented with more objective tools like dynamometers or electromyography (EMG).
Contact our professional team now for a same-day quote and risk-free project evaluation. Benefit from ISO 8 cleanrooms, advanced machines, and 12-hour fast response in medical injection molding.