Our company specializes in medical device injection mold manufacturing, providing high-quality solutions for the healthcare industry. With decades of experience in working with medical-grade materials, we ensure that all of our products meet stringent FDA compliance standards. We focus on producing durable, precise, and functional medical components, such as diagnostic disposables, surgical instruments, and orthopedic devices. By integrating medical molded plastics solutions, we enhance the performance and reliability of these components, ensuring they meet the critical demands of the healthcare sector. Our key features include ISO-certified cleanrooms, ensuring a sterile environment for production, and expert capabilities in designing molds for Class I, II, and III medical devices. Our commitment to medical device injection mold excellence is demonstrated through a strong focus on Design for Manufacturability (DFM), allowing us to optimize every stage of the molding process for superior performance and efficiency. Medical device injection mold enables precise, cost-effective production of components like catheter locks and diagnostic kits using diverse materials.
Low-Volume to High-Volume Production Capabilities
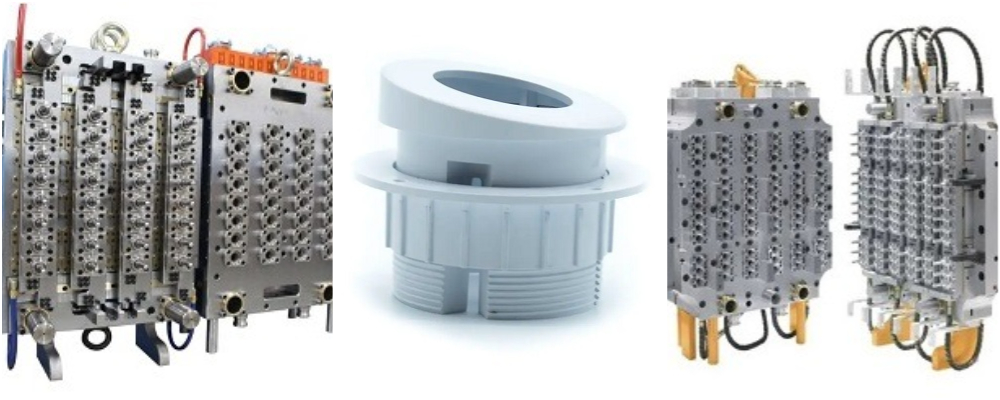
Attributes | Details |
---|---|
Place of Origin | Dongguan, Guangdong, China |
Brand Name | LY Medical Injection Mold |
Product Name | Medical Device Injection Mold |
Molding Mode | Plastic Injection Mold |
Model | Customized |
Quality | ROHS Standard |
Size | According to Your Drawing |
Structure | According to Your Drawing |
Color | Customized |
Cavity | According to Customer Requirements, Single Cavity or Multi-cavity |
Product Material | Plastic |
Surface Treatment | Texture (MT Standard), High Gloss Polishing |
Service | OEM ODM Customization |
Design Software | UG/CAD |
Mold Base | European Standard, World Standard, According to Customer Requirements |
Application | Medical, Laboratory Areas |
Packing Details | Safe and Properly Packed Cardboard Box |
Supply Capacity | 2000 Pieces Per Month |
Services Offered in Medical Device Injection Mold
Our company offers a wide range of specialized services in medical device injection mold manufacturing, each designed to meet the complex needs of the medical industry. Below, we highlight the key services we provide, showcasing how each one benefits our clients and enhances product development.
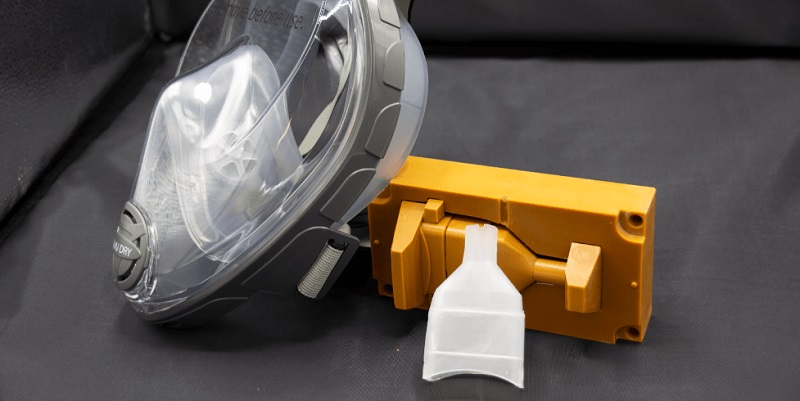
Injection Mold Design
One of the core services we provide is medical device mold design. We use advanced 3D simulation software to create precise mold prototypes, allowing for accurate testing and optimization before actual production. This approach ensures that the final product meets stringent tolerances, which is crucial for medical devices that require high precision for both functionality and safety. The simulation helps identify potential issues early in the design phase, reducing production errors and costs. Additionally, by focusing on performance during the design phase, we ensure that molds will deliver superior part quality, durability, and repeatability over time.
Tooling
Our tooling services are essential for producing high-quality medical device injection mold components. We provide custom mold fabrication for a variety of complexities, from simple parts to intricate designs. Our expertise includes creating molds that can withstand the demands of high-volume production while maintaining high precision. We also specialize in insert and overmolding tools, which are key for multi-material projects. Insert molding allows for the seamless integration of metal and plastic, while overmolding combines materials to create ergonomic, user-friendly products. These services improve the performance, aesthetics, and durability of medical devices, which are critical for ensuring patient safety and comfort.
Blow Molding
Blow molding in the context of medical device injection mold is a specialized manufacturing process used to create hollow, uniform, and often intricate components essential in medical applications. This process involves heating a plastic preform or parison, inflating it within a mold using compressed air, and forming it into the desired shape. Blow molding is particularly valuable for producing single-construction hollow parts, such as fluid containers, reservoirs, or complex tubing systems, commonly used in medical devices. The key advantage of this method lies in its ability to produce consistent wall thickness across the part, ensuring structural integrity and compliance with medical standards. However, achieving minimal wall thickness variation is a decisive factor for the feasibility of this process, as it impacts the strength, functionality, and regulatory compliance of the final product. Medical blow molding offers an economical solution for high-volume production while maintaining the precision and quality demanded in the medical field.
Post-Processing
Post-processing is an integral part of the medical device injection mold manufacturing process. After parts are molded, they often require additional steps such as kitting, assembly, and part decoration. Kitting involves organizing individual components into kits for easy assembly, which is especially important for medical devices that need to be packaged and sterilized. Assembly services ensure that complex parts are joined correctly, while part decoration enhances the device’s appearance and function, such as adding labels or improving grip surfaces. These post-processing services are designed to ensure that the final product is ready for use and meets all regulatory and customer requirements.
Automation
Incorporating medical device automation into the medical device moulds process improves both efficiency and consistency. Robotic systems, such as cobots (collaborative robots), are used to automate tasks like part removal, inspection, and packaging. Automation reduces human error, minimizes labor costs, and speeds up production. By integrating automated systems into the injection molding process, we can maintain consistent quality across large batches of medical devices while reducing production time. This is particularly important in the medical field, where precision and repeatability are crucial for ensuring the safety and effectiveness of each product.
Seven Types of Medical Device Injection Mold Processes
Plastic injection molding is one of the most widely used methods in medical device mold msker production. Our plastic molding services include various techniques such as thin-wall molding, gas-assisted molding, and LSR (Liquid Silicone Rubber) molding. Thin-wall molding is ideal for producing lightweight, compact medical components, reducing material costs while maintaining strength. Gas-assisted molding uses pressurized gas to create hollow parts, offering superior surface quality and reducing material usage. LSR molding is perfect for creating flexible, high-performance parts for medical devices such as gaskets and seals. These techniques provide high precision, high-volume production, and the ability to meet diverse medical device requirements.
Thin Wall Injection Molding
Thin wall injection molding focuses on creating lightweight medical components with minimal wall thickness, such as syringe barrels and medical housings. This method reduces material usage while maintaining structural integrity and is ideal for high-volume production of disposable medical devices
Gas-Assisted Injection Molding
Gas-assisted injection molding involves injecting a gas (usually nitrogen) into the molten plastic to hollow out thick sections of a part. This process is excellent for producing lightweight and strong components, such as ergonomic medical handles or complex enclosures, with reduced material consumption and cycle time.
Overmolding
In the field of medical device mould production, insert and overmolding offer several benefits for medical moulded products. Insert molding allows for the integration of metal components into the mold, which is especially useful in producing complex medical parts that require both plastic and metal. This approach eliminates the need for secondary assembly operations, streamlining the manufacturing process and reducing overall costs. Overmolding, on the other hand, involves molding one material over another, such as adding a soft, ergonomic layer to a hard plastic component. This is particularly beneficial for improving the functionality and user comfort of medical devices, such as surgical tools or handles for diagnostic equipment.
Liquid Silicone Rubber (LSR) Injection Molding
LSR injection molding processes medical-grade silicone into flexible and biocompatible parts, such as catheters, seals, and valves. This method is valued for its precision, ability to produce intricate designs, and suitability for devices requiring flexibility and sterilization.
High Consistency Rubber (HCR) Injection Molding
HCR injection molding uses high-viscosity silicone materials to create durable and heat-resistant parts. It is commonly employed for producing seals, gaskets, and medical tubing that demand resilience under high-stress conditions.
Metal Injection Molding (MIM)
Metal injection molding allows for the production of small, highly precise metal parts used in surgical tools, orthopedic implants, and dental components. This process offers the advantage of creating complex geometries that are difficult to achieve through traditional metalworking methods.
Plastic Injection Molding
Plastic injection molding is the most versatile and widely used process for medical device components. It can process a range of medical-grade thermoplastics to produce high-precision parts such as diagnostic test kits, IV components, and protective housings, all while ensuring cost efficiency and scalability.
Each of these injection molding techniques addresses specific requirements in the medical device industry, enabling the production of safe, reliable, and high-quality components tailored to diverse applications.
Materials & Applications in Medical Device Injection Mold
Our expertise in medical device injection mold manufacturing extends to a wide range of materials and applications, each carefully chosen to meet the exacting standards of the medical industry. Below, we outline our specialized capabilities in materials, their applications, and how they contribute to the successful production of medical devices.
Materials
Materials play a critical role in the medical device injection mold process, and we work with a variety of plastics and composites to meet different performance and regulatory requirements. The choice of material can influence everything from the functionality of the device to its compliance with medical standards.
Common Materials
Some of the most common materials used in medical device injection mold production include Polypropylene (PP), Polyethylene (PE), and Polycarbonate (PC). These materials are widely used in medical device manufacturing due to their affordability, durability, and ease of processing. Polypropylene is commonly chosen for its chemical resistance and low moisture absorption, making it ideal for medical devices that require sterilization. Polyethylene, on the other hand, is known for its toughness and versatility, often used in disposable medical products like syringes and tubing. Polycarbonate, with its high transparency and impact resistance, is frequently selected for diagnostic components such as imaging equipment and protective medical casings.
Specialty Materials
In addition to common materials, we specialize in higher-performance materials like Polyetheretherketone (PEEK), Silicone, and Polystyrene (PS), which are often required for high-stakes medical applications. PEEK is highly valued for its strength, resistance to heat, and biocompatibility, making it ideal for surgical implants and orthopedic devices. Silicone is chemically inert, flexible, and biocompatible, which makes it suitable for medical devices such as gaskets, seals, and flexible tubing. Polystyrene is often used for its ease of processing and ability to create high-quality finishes, frequently seen in diagnostic disposables like Petri dishes and test tubes.
Applications
The medical device injection mold process is used to manufacture a broad spectrum of medical components, from simple diagnostic tools to complex surgical devices. Below are some key applications where our capabilities are essential.
Medical Instruments
Our medical device injection mold services are widely used in the production of medical instruments such as scalpels, pacemaker components, and surgical tools. These products require exceptional precision, strength, and biocompatibility to ensure they perform reliably in sensitive environments. For example, scalpel handles often undergo injection molding with materials like Polycarbonate for strength and Polypropylene for resistance to wear. Pacemaker components, made using advanced materials like PEEK, need to meet strict electrical and mechanical performance criteria to ensure patient safety.
Diagnostic Disposables and Imaging Components
Medical device injection mold is frequently employed in the production of diagnostic disposables such as syringes, test tubes, and imaging components like X-ray casings. These devices need to be sterile, durable, and resistant to chemicals and temperature fluctuations. For example, medical-grade syringes are commonly molded using Polypropylene (PP), ensuring they are both cost-effective and capable of withstanding sterilization without degrading. Imaging components, including those used in MRI or CT machines, require high-impact resistance and excellent surface finishes, which can be achieved through the injection molding process using Polycarbonate (PC).
Drug Delivery Systems and Orthopedic Devices
Medical device injection mold processes are also critical for manufacturing drug delivery systems, such as inhalers and infusion pumps, as well as orthopedic devices like joint replacements and spinal implants. These applications require materials that are strong, biocompatible, and capable of withstanding the wear and tear of daily use. For instance, Polyetheretherketone (PEEK) is often chosen for orthopedic implants due to its exceptional durability and ability to mimic bone in terms of mechanical properties. Drug delivery systems, often made with materials like Silicone, must be flexible and capable of safely interacting with pharmaceutical substances.
Neonatal Care and Cardiovascular Components
In neonatal care and cardiovascular products, medical device injection mold techniques are crucial for creating components that ensure the safety and well-being of vulnerable patients. Neonatal care devices such as incubators, monitors, and feeding tubes require careful attention to both functionality and comfort. For these applications, flexible, biocompatible materials like Silicone are often used to ensure the devices do not cause harm to infants. Similarly, cardiovascular products such as stents, catheters, and heart valves must be manufactured to extremely tight tolerances, often with materials like PEEK or Polycarbonate, ensuring both strength and flexibility.
Technical Highlights in Medical Device Injection Mold
The medical device injection mold process is built upon several key technical strengths that ensure the highest quality, precision, and compliance with regulatory standards. These technical highlights are crucial in ensuring that every medical device produced is functional, safe, and reliable for patient care. Below, we dive deeper into each of these technical highlights, highlighting the key factors, benefits, and examples of how they apply to medical device manufacturing.
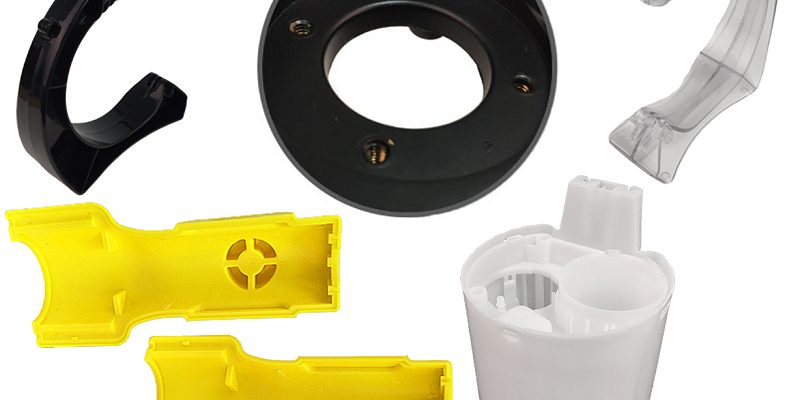
Precision Manufacturing
One of the most important features of the medical device injection mold process is precision manufacturing. Medical devices must meet stringent quality standards, and this begins with the ability to maintain tight tolerances throughout the molding process. Precision manufacturing ensures that each component is produced with exact dimensions, contributing to the overall performance and safety of the device.
Benefits of Precision Manufacturing
Tight Tolerances for Correct Component Fit
Tight tolerances in medical device injection molding are crucial to ensuring that components fit together perfectly. Components that don’t meet these exact specifications may not function as intended, leading to potential malfunctions or failures. This precision guarantees that medical parts, such as joints or surgical tools, align accurately when assembled, reducing the risk of defects that could compromise the performance of the medical device. In the medical field, even a slight variation in component dimensions can lead to significant consequences, such as improper fitting or alignment, which can endanger patient safety.
Ensuring Functional and Mechanical Integrity
Medical components like implants, pacemakers, and diagnostic devices must maintain both functional and mechanical integrity under pressure. Tight tolerances are essential for ensuring that these devices will not only fit together properly but also endure the mechanical stresses they will face during use. For example, a surgical tool must maintain its shape and durability even after repeated use in a high-pressure environment. Achieving these mechanical requirements is possible only through precise molding, ensuring longevity and minimizing the risk of failure in critical applications.
Ergonomic Design Requirements
Beyond just mechanical functionality, many medical devices also need to meet ergonomic requirements to ensure user comfort and ease of use. For instance, surgical tools and implants must be designed to fit comfortably in the hand or body. Precise molding ensures that these parts have the right shape, weight, and texture, which are essential for their effective use in medical procedures. Inaccurate designs could lead to discomfort or difficulty in handling, which may affect the performance of medical professionals and patient outcomes.
Prevention of Medical Risks through Accurate Design
Inaccurate components can result in significant medical risks. For example, an incorrectly molded pacemaker could fail to function as intended, jeopardizing the health of the patient who relies on it. Similarly, a poorly designed surgical tool could lead to complications during an operation. By using advanced techniques in medical device injection molding, manufacturers can ensure that each part meets precise standards, reducing the risk of malfunctions and improving patient safety.
Advanced CAD and Simulation Tools for Precision
Achieving these tight tolerances is made possible by modern computer-aided design (CAD) and simulation tools. These technologies allow manufacturers to create highly accurate models of medical precision components before they are produced. CAD helps in designing parts with complex geometries, while simulation tools predict how the mold will behave during the injection process. This predictive capability enables manufacturers to fine-tune the designs and adjust the process before production begins, ensuring that the final components meet the required specifications consistently.
Consistency with Complex Geometries
Medical device injection molding can achieve precision even with complex geometries. Complex parts, such as multi-component assemblies or intricate interior features, require molds that can maintain consistency throughout the production process. Advanced molding techniques ensure that these complex designs are accurately reproduced in every batch, providing reliable and consistent results across large production volumes. This consistency is especially important in the medical industry, where even small deviations from the ideal design can result in significant risks to the patient’s health.
Example of Precision in Action: A pacemaker casing, which requires perfect alignment for internal components like batteries and circuits, must be molded with extreme precision. A slight deviation could lead to device failure, jeopardizing patient safety. Therefore, precision manufacturing is a crucial aspect of medical device injection mold for such critical devices.
Regulatory Compliance
Regulatory compliance is a cornerstone of the medical device injection mold industry. Medical devices must comply with several rigorous standards set by organizations like the U.S. Food and Drug Administration (FDA) and international standards such as ISO 13485. These regulations govern everything from the design of the device to its manufacturing process, ensuring that each part meets the necessary criteria for patient safety and effectiveness.
Benefits of Regulatory Compliance
Ensuring Safety for Medical Devices
Regulatory compliance ensures that medical devices are safe for use in healthcare settings. Adhering to industry regulations such as FDA and ISO standards ensures that the devices meet rigorous safety criteria, protecting patients and healthcare providers from potential harm. This assurance is essential in maintaining trust in medical technology, as safety is always a top priority in healthcare.
Facilitating Market Entry
Compliance with regulatory standards such as FDA regulations is crucial for medical devices to enter various markets. For example, FDA approval is required for a device to be sold and used in the U.S. market. Similarly, compliance with European CE marking standards allows medical devices to be sold in the European Union. Regulatory compliance simplifies the process of obtaining approvals and entering multiple regions, thereby enhancing global reach.
Adherence to International Standards
Regulatory compliance guarantees that medical devices meet internationally recognized standards. For instance, ISO certifications ensure that the devices are manufactured under high-quality management systems. This adherence to global standards helps create consistency in product quality and performance, which is particularly important for the reputation of manufacturers.
Building Customer Trust
ISO certifications and other regulatory approvals reassure customers that medical devices are made to high standards. Customers, including healthcare professionals and hospitals, seek reliable and high-quality products, and compliance with regulatory requirements provides peace of mind. This trust can lead to stronger relationships with end-users and healthcare organizations.
Improved Quality Control
Regulatory compliance necessitates strict quality control measures throughout the manufacturing process. This includes documenting procedures, conducting regular audits, and ensuring that products undergo thorough testing before reaching the market. Such robust quality assurance systems improve the consistency and reliability of medical devices.
Reduced Risk of Legal Issues
By adhering to regulatory requirements, manufacturers reduce the risk of legal challenges and liability. Failure to comply with regulations can result in product recalls, fines, and legal actions. By staying compliant, manufacturers safeguard their business against potential legal issues while ensuring the continued availability of their products in the marketplace.
Example of Regulatory Compliance: A manufacturer creating orthopedic implants must validate the device through IQ/OQ/PQ (Installation Qualification, Operational Qualification, and Performance Qualification) processes. This ensures that the device meets the regulatory standards for both safety and performance. Such compliance is critical for devices implanted into patients’ bodies, where failure can have severe consequences.
Cleanroom Operations
To ensure the highest level of sterility and contamination control, medical device injection mold processes often take place in cleanroom environments. These controlled areas are classified based on the number of particles allowed per volume of air, with ISO 7-rated cleanrooms being commonly used for the manufacturing of medical devices.
Benefits of Cleanroom Operations
Reduced Risk of Contamination
One of the primary benefits of cleanroom operations is the significant reduction in the risk of contamination during the molding process. Cleanrooms are specially designed environments with controlled levels of airborne particles, temperature, humidity, and other variables that could compromise the quality of medical products. This is especially crucial for devices used in sterile environments, such as surgical instruments, implants, or drug delivery systems. Maintaining a contamination-free environment ensures the final product is safe for use in sensitive medical applications.
Safe Handling of Sensitive Materials
Cleanroom operations provide the necessary environment to safely handle sensitive materials such as Silicone, PEEK (Polyetheretherketone), and other advanced polymers. These materials have unique properties that can be easily compromised by contamination or environmental factors. For example, PEEK, used in medical implants, requires very specific temperature and humidity conditions to maintain its strength, durability, and biocompatibility. Cleanrooms ensure these materials remain in optimal condition throughout the molding process.
Compliance with Regulatory Standards
Cleanroom operations help manufacturers comply with strict regulatory standards, such as those set by the FDA and ISO. These standards ensure that medical devices are manufactured in environments that minimize the risk of contamination and guarantee the safety and efficacy of the products. The controlled environment of a cleanroom allows manufacturers to meet these regulatory requirements, which is essential for obtaining certifications and approvals for medical devices.
Improved Product Quality and Reliability
By preventing contamination and ensuring that sensitive materials are handled under the right conditions, cleanroom operations enhance the overall quality and reliability of medical devices. Devices produced in cleanrooms are more consistent in terms of performance, durability, and compliance with safety standards. This leads to fewer defects and a lower rate of product recalls, which is crucial in the medical industry, where the stakes are high.
Reduced Risk of Product Failures
The use of cleanroom operations significantly reduces the risk of product failures due to contamination during manufacturing. Even small particles of dust or other foreign substances can cause defects in critical components like implants, syringes, or pacemaker components. Cleanrooms ensure that such particles do not interfere with the manufacturing process, resulting in higher-quality products that are more reliable in the long run.
Support for High-Precision Molding
Cleanroom environments are ideal for high-precision molding processes that require tight tolerances and consistency, especially in the production of precision mold medical devices. For medical devices that need to fit together perfectly or perform specific functions (such as drug delivery systems or diagnostic tools), the sterile and controlled conditions of a cleanroom enhance the precision of the molding process. This leads to higher-performance parts with fewer defects, which are essential for the proper functioning of medical devices.
Example of Cleanroom Use: For example, medical devices like stents or catheters that are inserted into the human body must be produced in ISO 7 cleanrooms to avoid contamination. Any external particles could cause infections or device failure, so a cleanroom ensures that only the highest levels of cleanliness are maintained during the manufacturing process.
Automation
Automation plays a vital role in the medical device injection mold process, enhancing both efficiency and consistency. The use of robotic systems, including cobots (collaborative robots) and End-Of-Arm Tools (EOAT), allows for highly automated, precise movements during production.
Benefits of Automation
Reduction in Human Error
One of the primary benefits of automation in the production of medical devices is the significant reduction in human error. Automated systems perform repetitive tasks with precision, eliminating inconsistencies that can occur with manual labor. This is especially important in the medical device industry, where even small errors can lead to defects that compromise the safety and effectiveness of the device. Automation ensures that each product meets the required specifications consistently, reducing the risk of errors that could affect patient outcomes.
Increased Production Speeds
Automation dramatically increases production speeds, allowing manufacturers to produce large quantities of medical devices in less time. Automated machinery and robotic systems can work continuously without the need for breaks or shift changes, making production runs faster and more efficient. For high-demand medical products like syringes, which require large volumes to be produced quickly, automation ensures that production meets market demand without sacrificing quality or reliability.
Consistent Quality Across Production Runs
With automation, manufacturers can ensure consistent quality across large production runs. Automated systems are programmed to follow precise instructions and can maintain tight tolerances throughout the manufacturing process. This ensures that every product, whether it’s a syringe, pacemaker, or diagnostic tool, is produced to the same high standard. Consistency is critical in the medical device industry, where even slight variations in a device’s dimensions or functionality can lead to failure in critical applications.
Minimization of Manual Labor Costs
Automation also reduces the reliance on manual labor, significantly lowering labor costs in the production process. Robots and automated machines can handle tasks that would typically require multiple human workers, such as assembly, inspection, and packaging. By reducing the need for human intervention, manufacturers can focus their resources on more complex tasks, while still benefiting from a streamlined, cost-effective production line. This cost efficiency is particularly important in industries like medical device manufacturing, where profit margins can be tight.
Enhanced Scalability and Flexibility
Automation allows manufacturers to scale their production processes up or down as needed, providing greater flexibility to meet changing market demands. For plastic medical device manufacturers, this means they can quickly adjust production volumes for high-demand products, such as syringes or diagnostic devices, without compromising on quality. Automated systems can be reprogrammed or adapted to produce different products with minimal downtime, making the production process more adaptable to fluctuating market needs.
Improved Product Traceability and Compliance
Automated systems are equipped with data collection capabilities that track every step of the production process. This provides manufacturers with valuable information on product quality and production efficiency, making it easier to identify issues and ensure compliance with regulatory standards. For medical devices, which are subject to stringent regulatory requirements, having a comprehensive record of production data helps maintain traceability and supports efforts to meet FDA, ISO, and other certification standards. Automation ensures that every device is produced according to the required specifications, which is crucial for maintaining safety and quality.
Example of Automation in Action: For high-precision components like pacemaker housings, cobots can be used to handle delicate parts in a safe and efficient manner. These robotic systems can perform tasks such as assembling small components or performing in-line inspections without the risk of contamination, ensuring that each piece meets the required standards.
Prototyping
Prototyping is an essential step in the medical device injection mold process, especially when developing new devices or refining existing ones. Functional prototypes allow for testing, validation, and iterative design improvements before moving to full-scale production.
Benefits of Prototyping
Early Identification of Potential Issues
Prototyping plays a crucial role in identifying potential issues with the design, materials, or manufacturing processes early in the development phase. By creating a prototype, manufacturers can test the functionality of the design, uncover any flaws, and make necessary adjustments before mass production begins. This early detection helps avoid costly revisions during later stages of production, saving time and resources.
Design Flaws Identification
A functional prototype allows manufacturers to identify any design flaws that could negatively affect the performance, safety, or functionality of the medical device. Whether it’s issues related to ergonomics, assembly, or the interaction between components, prototyping provides a tangible representation of the design, making it easier to pinpoint problems that may be overlooked during theoretical design phases.
Streamlining FDA Approval
For medical devices that require FDA approval, prototyping can significantly streamline the approval process. A tangible, functional prototype allows regulatory bodies to evaluate the device’s performance, safety, and usability more effectively. This model serves as a reference for demonstrating compliance with regulatory requirements and accelerates the review and approval process by providing a real-world example of the device.
Material and Manufacturing Process Evaluation
Prototyping also allows manufacturers to evaluate the materials and manufacturing processes to be used in final production. By testing different materials and production methods, manufacturers can determine which combinations offer the best performance, durability, and cost-effectiveness for the medical device. This iterative process ensures that the final product will meet the necessary standards for quality and performance.
Cost and Time Efficiency
Using prototypes can help reduce costs in the long term by identifying issues early, thus preventing expensive changes or delays once production has begun. Additionally, prototyping can shorten the overall development timeline by enabling faster iteration and testing of various design versions, leading to quicker time-to-market for the medical device.
Enhancing Collaboration and Communication
Prototypes serve as a valuable communication tool among design teams, engineers, stakeholders, and regulatory bodies. By providing a physical model, prototypes make it easier for everyone involved to understand the design intent and functionality. This enhances collaboration and ensures that all parties are aligned on the project’s goals and specifications.
Example of Prototyping Use: When designing a new type of surgical tool, the initial prototypes may be used for real-world testing to ensure the device’s ergonomic design and mechanical performance are suitable for use in an operating room. Through rapid prototyping, manufacturers can make adjustments before committing to large-scale production, reducing time to market and enhancing product success.
Benefits of Partnering in Medical Device Injection Mold
Partnering with a specialized manufacturer in the medical device injection mold process offers several key benefits. These advantages span from scalable production options to high-quality assurance, ultimately ensuring that medical devices are manufactured efficiently, with a focus on performance, cost, and regulatory compliance. Below, we detail each benefit of partnering for medical device injection mold manufacturing.
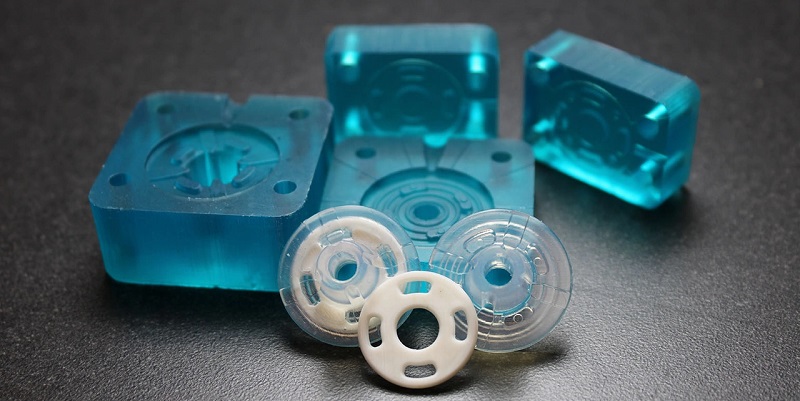
Scalability
Scalability is a significant advantage when partnering with a medical device injection mold provider. The ability to scale production from small batch prototypes to full-scale mass production allows companies to meet fluctuating market demands while maintaining high-quality standards.
- Flexibility: Allows manufacturers to adjust production volumes based on demand.
- Prototype to Mass Production: Small batches can be produced for testing, followed by large-scale production.
- Adaptability: Enables rapid scaling when FDA approval or market growth demands increased production.
A startup company developing a new wearable medical device may begin by manufacturing a few hundred units for clinical trials. Once the device gains FDA approval, the manufacturer can easily scale up production to thousands or even millions of units without sacrificing quality. This flexibility allows the company to adapt to the market and grow its customer base.
Cost Efficiency
One of the primary advantages of partnering with a medical device injection mold provider is cost efficiency. The use of injection molding reduces both material waste and labor costs, contributing to the overall cost-effectiveness of the manufacturing process.
- Automation: Reduces labor costs by minimizing manual operations.
- Precision: Ensures minimal material waste and higher efficiency.
- Affordable Devices: Cost savings can be passed on to end consumers.
In the production of plastic surgical instruments, automated molding machines can produce large quantities of high-quality parts with minimal labor. By using the exact amount of material needed for each part, manufacturers reduce waste, making the production process more cost-effective. This allows the cost of each unit to be lowered, enabling hospitals and healthcare providers to afford essential medical devices in high volumes.
High-Quality Assurance
Ensuring the highest quality is a fundamental part of the medical device injection mold process. Quality assurance includes in-line inspections, advanced testing labs, and strict adherence to industry standards to guarantee that the medical devices meet all necessary regulatory and safety requirements.
- In-line Inspections: Detects defects early in the process, reducing the risk of faulty products.
- Testing Labs: Validates durability and performance through stress and functional tests.
- Consistency: Ensures all components are molded and assembled according to specifications.
Medical devices like insulin pumps or pacemakers require absolute precision and reliability. During the medical device injection mold process, each unit undergoes continuous inspection to ensure that the components are correctly molded and assembled. Any deviation from the design specifications is immediately detected and corrected, ensuring that only high-quality devices are released to the market.
End-to-End Support
Another major benefit of partnering with a medical device injection mold manufacturer is the end-to-end support they offer, ranging from design consultation to full-scale production. This holistic support system ensures a seamless transition from the conceptualization of the device to its final production and distribution.
- Comprehensive Assistance: Experts provide guidance through every stage, from design to full-scale production.
- Design for Manufacturability (DFM): Optimizes designs for cost, quality, and ease of production.
- Turnkey System Transfer: Manages the entire production line and logistics for manufacturers.
A medical company developing a new surgical instrument can rely on their molding partner to not only provide the injection molds and tooling but also help with product design optimization and prototyping. As the device moves toward mass production, the partner can continue to provide testing, validation, and logistics support. This comprehensive service streamlines the entire development process, saving time and reducing the need for multiple suppliers.
Customization and Innovation
Customization is another crucial benefit of partnering with a medical device injection mold provider. These companies offer the ability to create highly specialized designs and incorporate innovative features into the devices, allowing manufacturers to meet the unique needs of healthcare providers and patients.
- Innovative Solutions: Offers customized features like multi-material molding, specialized coatings, and ergonomic designs.
- Enhanced Functionality: Helps improve user experience and patient outcomes.
- Unique Features: Incorporates a combination of materials for durability and comfort.
In the production of surgical tools, a manufacturer may require a combination of hard and soft materials to create a handle that is both durable and comfortable. Through insert molding or overmolding, these manufacturers can create components that offer both strength and ergonomics in a single part, resulting in a more effective and user-friendly medical device.
Regulatory Expertise
Partnering with an experienced medical device injection mold provider also provides access to their regulatory expertise. Ensuring compliance with FDA, ISO, and other industry regulations is essential for the successful approval and market release of medical devices.
- Navigating Regulations: Helps manufacturers comply with FDA and ISO standards.
- Reduced Approval Delays: Ensures all components meet safety and efficacy standards.
- Guidance Through Validation: Assists with IQ/OQ/PQ protocols and other necessary validations.
The complexities of regulatory approval can be daunting, but working with a partner who is well-versed in medical device standards helps navigate these challenges. A medical device injection mold provider ensures that every part of the manufacturing process complies with necessary regulations, from material selection to final production. This reduces the likelihood of delays in approval or costly revisions later in the process.
Medical Device Product Molds: Examples and Benefits
When it comes to medical devices, medical device injection mold is critical for ensuring the precision, safety, and functionality of the final product. Plastic medical device mold design plays a crucial role in creating reliable and efficient medical tools that meet stringent regulatory requirements. Below, we explore the various aspects of molds examples in medical devices, the benefits of using plastic medical device molds, and the impact these molds have on the quality and success of medical products.
Key Benefits of Medical Device Product Molds
Precision
One of the primary benefits of medical device product molds is their ability to create intricate, complex designs with tight tolerances. Precision is vital in the medical industry, where even the smallest deviation can compromise the functionality and safety of a device. For instance, surgical tools like scalpels or forceps require molds that ensure exact sharpness and ergonomic designs to function correctly and safely. The ability to manufacture with high precision guarantees that medical devices perform as intended.
Reproducibility
Molds provide a consistent and repeatable process for manufacturing parts. Reproducibility is particularly important in medical device production, where high volumes of identical parts are needed. Whether producing syringes or pacemaker components, using molds ensures that each unit produced has the same exact dimensions, shape, and functionality. This consistency is essential for patient safety, regulatory compliance, and product reliability.
Durability
Medical device product molds are designed to endure high production volumes and multiple cycles. High-quality molds can withstand many production cycles without degradation, which is beneficial in keeping costs low over the long term. For example, molds used in mass production of diagnostic kits or surgical instruments are made to last, providing a cost-effective manufacturing process while ensuring that the parts meet the same high standards throughout their lifecycle.
Molds Example in Medical Device: Precision and Performance
Medical device molds are often required to produce parts that not only meet strict quality standards but also exhibit high performance in real-world applications. The role of a mold extends beyond simply shaping a part—it also ensures that the part performs as required, especially under challenging conditions.
Examples of Molds in Medical Devices
Plastic medical device molds are commonly used to create components such as syringe bodies, IV connectors, or inhaler housings. These molds must be designed with precision to guarantee the integrity of the components, ensuring that they meet safety and performance standards. For example, molds used to manufacture pacemaker cases or insulin pumps need to accommodate both the device’s external structure and internal components while ensuring that the device meets medical-grade sterilization and safety standards.
Material Compatibility
Plastic medical device molds are often made to accommodate specific materials, such as polypropylene (PP), polyethylene (PE), or silicone. These materials are chosen for their biocompatibility, strength, and performance in medical environments. Using the right material ensures that the final product will function correctly and safely for patients, meeting regulatory standards. For example, polypropylene is commonly used in syringes, while silicone is chosen for parts that require flexibility and sealing capabilities.
Advantages of Plastic Medical Device Molds
Plastic medical device molds offer several advantages when it comes to manufacturing a wide range of medical products. These advantages make them an ideal choice for producing functional, durable, and cost-effective components.
Cost-Effectiveness
Plastic is generally less expensive than metals and other materials, which makes plastic medical device molds a cost-effective choice for manufacturers. The cost savings are particularly noticeable in high-volume production runs, where the price per unit can significantly drop. For example, plastic syringes or drug delivery components produced using injection molds offer excellent functionality while keeping production costs low.
Customization
Plastic molds are highly versatile, enabling the production of custom shapes and complex geometries. This customization is crucial in the medical device industry, where devices often require unique forms for ergonomic or functional purposes. For example, custom-designed plastic molds can create components with snap-fits, locking mechanisms, or ergonomic grips to improve both usability and performance.
Biocompatibility
Many plastics used in medical device molds are biocompatible, meaning they can be safely used in direct contact with patients or sensitive medical applications. This is a critical requirement for devices like catheters, surgical tools, or implants that come into direct contact with human tissue. By using biocompatible materials, manufacturers ensure the safety of medical devices for the end-users.
Challenges in Using Plastic Medical Device Molds
Despite the numerous benefits, plastic medical device molds come with certain challenges that need to be addressed during the design and production phases.
Material Limitations
Not all plastic materials are suitable for all medical applications. For instance, some plastics may not have the necessary resistance to high temperatures, harsh chemicals, or other medical environment conditions. This can lead to material degradation or failure over time. Selecting the right plastic for the right application is essential to avoid such issues. For example, some plastics used in medical molding may not withstand prolonged exposure to heat sterilization, which is a common requirement for surgical tools.
Surface Finish Issues
Achieving the necessary surface finish for medical devices can be challenging with plastic molds. Some plastic molds require additional post-processing steps, such as polishing or coating, to achieve the desired smoothness or sterility. Medical devices like syringes, for example, require a very smooth surface to ensure ease of use and patient comfort. Any roughness in the surface can lead to issues like irritation or difficulty in operation.
Complexity in Design
The complexity of certain medical devices can make medical mold design more intricate and time-consuming. Devices with complex internal structures or those requiring multi-material molding are particularly challenging. For instance, creating molds for components like infusion pumps requires detailed attention to how different materials (e.g., rubber seals and plastic housings) interact and how the mold can accommodate these components. The increased complexity can lead to longer production times and higher costs.
Molds Examples in Medical Devices: Specialized Designs
Specialized medical device product molds are often required for devices that fulfill very specific purposes. These molds are designed to create parts that must meet high standards of precision, biocompatibility, and performance.
Micro-Molds
Used for producing miniature components like pacemaker parts or stents, micro-molds ensure extreme precision and accuracy at small scales. These molds are critical for devices that require highly detailed features in tight spaces.
Multi-Shot Molds
These molds are used for creating components that need multiple materials in a single part. For example, a medical device may require a soft rubber seal combined with a rigid plastic housing. In medical rubber molding, multi-shot molding ensures that these materials are perfectly combined in a single piece, enhancing the device’s functionality, durability, and ease of use. This process is crucial in the medical industry, where precision and performance are paramount for device reliability and patient safety.
Biocompatible Molds
Specialized molds are also created for medical devices that will be in prolonged contact with the human body, such as implants or surgical instruments. These molds ensure that the device meets both the required functional specifications and biocompatibility standards.
FAQs about Medical Device Injection Mold
Medical injection molding refers to the process of creating parts or components for medical devices using injection molding technology. In this process, plastic or other materials are injected into a mold to form precise, complex shapes that are required for medical applications. Medical injection molding is essential for producing high-quality, reliable parts that meet strict regulations and safety standards, such as those from the FDA and ISO. This process is widely used in the medical industry to create components for devices such as syringes, pacemakers, diagnostic equipment, surgical tools, and drug delivery systems. The main advantages of medical injection molding include its ability to produce high-precision, high-volume parts efficiently. Additionally, the process can accommodate a variety of medical-grade materials, such as polypropylene, polyethylene, silicone, and specialized materials like PEEK (Polyetheretherketone) for devices that require high performance and durability. The molding process ensures that each part is consistent and accurate, which is crucial in medical applications where safety and functionality are paramount.
Injection molding is a manufacturing process used to produce a wide variety of parts by injecting molten material into a pre-designed mold. This process can be used with a variety of materials, such as plastics, metals, or ceramics. Once the material is injected into the mold, it cools and solidifies into the shape of the mold, after which the finished part is ejected. Injection molding is a popular method for mass-producing complex and intricate parts with high precision. The process begins by heating the material to its melting point, and then injecting it into a mold cavity under high pressure. After cooling, the solidified part is removed from the mold. This process is highly efficient for high-volume production and is capable of creating complex geometries with tight tolerances. It’s widely used across various industries, including automotive, electronics, consumer goods, and medical devices, due to its versatility, speed, and cost-effectiveness. Injection molding can produce parts with detailed features, such as thin walls, intricate textures, or multi-material combinations, making it ideal for applications requiring high performance and precision.
The injection molding process requires specialized equipment to perform each step, ensuring high precision and efficiency. The core pieces of equipment involved in injection molding include:
Injection Molding Machine: This machine is responsible for injecting the molten material into the mold. It consists of two main components: the injection unit, which melts and injects the material, and the clamping unit, which holds the mold in place under pressure during injection.
Molds: The molds are custom-designed tools that determine the shape of the finished part. They are typically made of steel or aluminum and consist of two halves that are clamped together to form the cavity into which the molten material is injected.
Extruder: In some processes, an extruder is used to prepare the material before injection. It ensures that the material is heated to the correct temperature and is fed into the injection unit.
Cooling System: After the material is injected into the mold, it needs to cool down before being ejected. The cooling system is responsible for ensuring the mold cools at a controlled rate to prevent warping or defects in the final part.
Robotic Arm: In modern injection molding operations, robotic arms are often used to automatically remove the molded parts from the machine and place them on conveyors or into packaging systems.
This combination of equipment allows injection molding to be a highly efficient process for producing large quantities of complex parts with tight tolerances.
An injection mold is a tool used in the injection molding process to shape molten material into a solid part. Injection molds are essential for producing high-volume, precise, and consistent parts for a wide range of industries, including automotive, electronics, consumer products, and medical devices.
The primary use of an injection mold is to create complex parts with detailed features, such as thin walls, undercuts, or textured surfaces, that would be difficult or impossible to achieve through other manufacturing methods. Injection molds are often custom-designed to meet the specific requirements of the part being produced, ensuring that it fits within the exact specifications needed for its intended use.
Injection molds are especially critical in industries where high-quality, durable, and cost-effective parts are required. In medical device manufacturing, for example, molds are used to produce parts for syringes, surgical tools, pacemakers, and diagnostic equipment. These molds must be manufactured to extremely high tolerances to ensure the parts meet stringent regulatory standards and perform as intended. Molds can be made from materials such as steel or aluminum, depending on the complexity and material requirements of the parts being produced.
Injection mold validation for medical devices ensures the mold consistently produces parts that meet stringent regulatory requirements. The process typically involves three stages: Installation Qualification (IQ), Operational Qualification (OQ), and Performance Qualification (PQ).
IQ verifies that the mold, machine, and supporting systems are installed and functioning as specified.
OQ tests the mold under varied operating conditions to ensure it meets design specifications. Parameters like temperature, pressure, and cycle times are validated.
PQ evaluates the mold’s ability to produce acceptable parts in a production-like setting. Statistical sampling ensures consistency and compliance with quality standards.
Validation requires rigorous documentation, adherence to ISO 13485 or FDA guidelines, and comprehensive testing. Proper validation minimizes risks, ensures patient safety, and confirms that the mold will perform reliably under production conditions.
Injection molding is a specific type of molding process that injects molten material (usually plastic or thermoplastics) into a precision mold under high pressure. It is highly suitable for complex geometries and high production volumes, particularly in medical devices requiring intricate designs and consistent quality.
Molding, in general, refers to shaping materials into desired forms, encompassing various techniques such as compression molding, blow molding, and rotational molding. Each method suits different materials and applications.
For medical devices, injection molding is often preferred for its precision and ability to meet strict regulatory standards. It ensures tight tolerances, biocompatibility, and the production of parts like syringes, implants, and surgical tools. Other molding methods may lack the precision or versatility required for medical-grade components.
Injection-molded medical device components often have distinct characteristics:
Consistent Quality: Injection molding creates parts with uniform dimensions and smooth finishes, critical for medical applications.
Visible Features: Look for ejector pin marks, parting lines, or slight weld lines, indicating where the material met during molding.
Complex Shapes: Injection molding allows for intricate geometries, undercuts, and integrated features such as threaded inserts or hinges.
Material Identification: Often, plastics like polypropylene (PP) or polycarbonate (PC), common in medical devices, are used.
Mass Production Evidence: High-volume items like IV connectors, syringes, or catheter components are typically injection molded.
For medical devices, regulatory markings, serial numbers, or validation stamps may also signify the part was injection molded in a compliant facility.
“Mould” and “mold” are regional spellings of the same term, used interchangeably.
Mold is the preferred spelling in American English.
Mould is the British English variant.
Both terms refer to the tooling used in manufacturing processes like injection molding. In medical device contexts, the difference is purely linguistic, with no impact on meaning. Regardless of the spelling, molds or moulds for medical devices must meet strict design and manufacturing standards to ensure biocompatibility, precision, and compliance with regulations.
Injection molds for medical devices are expensive due to precision requirements, material selection, and engineering complexity. Factors driving costs include:
High-Quality Materials: Medical molds use durable steel or aluminum to withstand high pressures and ensure longevity.
Precision Engineering: Mold cavities must meet tight tolerances to ensure device functionality and regulatory compliance.
Validation Costs: Rigorous IQ, OQ, and PQ testing adds to expenses.
Customization: Each mold is tailored to specific medical device designs, often with complex geometries.
Tool Life: Longevity and accuracy over millions of cycles justify upfront costs.
The investment is necessary to ensure high-volume, consistent production of critical medical components like catheters, syringes, and implants, meeting regulatory and safety standards.
What is the injection mold validation procedure?
Injection mold validation for medical devices ensures the mold consistently produces parts that meet stringent regulatory requirements. The process typically involves three stages: Installation Qualification (IQ), Operational Qualification (OQ), and Performance Qualification (PQ).
IQ verifies that the mold, machine, and supporting systems are installed and functioning as specified.
OQ tests the mold under varied operating conditions to ensure it meets design specifications. Parameters like temperature, pressure, and cycle times are validated.
PQ evaluates the mold’s ability to produce acceptable parts in a production-like setting. Statistical sampling ensures consistency and compliance with quality standards.
Validation requires rigorous documentation, adherence to ISO 13485 or FDA guidelines, and comprehensive testing. Proper validation minimizes risks, ensures patient safety, and confirms that the mold will perform reliably under production conditions.
What is the difference between injection molding and molding?
Injection molding is a specific type of molding process that injects molten material (usually plastic or thermoplastics) into a precision mold under high pressure. It is highly suitable for complex geometries and high production volumes, particularly in medical devices requiring intricate designs and consistent quality.
Molding, in general, refers to shaping materials into desired forms, encompassing various techniques such as compression molding, blow molding, and rotational molding. Each method suits different materials and applications.
For medical devices, injection molding is often preferred for its precision and ability to meet strict regulatory standards. It ensures tight tolerances, biocompatibility, and the production of parts like syringes, implants, and surgical tools. Other molding methods may lack the precision or versatility required for medical-grade components.
How to tell if something is injection molded?
Injection-molded medical device components often have distinct characteristics:
Consistent Quality: Injection molding creates parts with uniform dimensions and smooth finishes, critical for medical applications.
Visible Features: Look for ejector pin marks, parting lines, or slight weld lines, indicating where the material met during molding.
Complex Shapes: Injection molding allows for intricate geometries, undercuts, and integrated features such as threaded inserts or hinges.
Material Identification: Often, plastics like polypropylene (PP) or polycarbonate (PC), common in medical devices, are used.
Mass Production Evidence: High-volume items like IV connectors, syringes, or catheter components are typically injection molded.
For medical devices, regulatory markings, serial numbers, or validation stamps may also signify the part was injection molded in a compliant facility.
What is the difference between mould and mold?
“Mould” and “mold” are regional spellings of the same term, used interchangeably.
Mold is the preferred spelling in American English.
Mould is the British English variant.
Both terms refer to the tooling used in manufacturing processes like injection molding. In medical device contexts, the difference is purely linguistic, with no impact on meaning. Regardless of the spelling, molds or moulds for medical devices must meet strict design and manufacturing standards to ensure biocompatibility, precision, and compliance with regulations.
Why are injection molds so expensive?
Injection molds for medical devices are expensive due to precision requirements, material selection, and engineering complexity. Factors driving costs include:
High-Quality Materials: Medical molds use durable steel or aluminum to withstand high pressures and ensure longevity.
Precision Engineering: Mold cavities must meet tight tolerances to ensure device functionality and regulatory compliance.
Validation Costs: Rigorous IQ, OQ, and PQ testing adds to expenses.
Customization: Each mold is tailored to specific medical device designs, often with complex geometries.
Tool Life: Longevity and accuracy over millions of cycles justify upfront costs.
The investment is necessary to ensure high-volume, consistent production of critical medical components like catheters, syringes, and implants, meeting regulatory and safety standards.
What products are injection moulded?
Injection molding is widely used in medical devices for its precision and efficiency. Common products include:
Syringes: Disposable and reusable.
Catheters: Used in cardiovascular and urological procedures.
Surgical Instruments: Handles, clips, and blades.
Implants: Orthopedic and dental applications.
IV Connectors: Fittings and valves for intravenous therapy.
Diagnostic Components: Test kits and sample containers.
These items require biocompatible materials, strict dimensional control, and smooth finishes to ensure safety and efficacy in medical applications.
Injection molding is ideal for producing medical devices when:
High Precision is Needed: Complex shapes with tight tolerances are required.
Large Volumes are Demanded: High production efficiency reduces per-unit costs.
Material Selection is Critical: Biocompatible plastics like PP or PC can be processed.
Consistency is Key: Injection molding ensures uniformity across batches.
Regulatory Compliance is Mandatory: Meets ISO 13485 or FDA standards.
Applications include disposable items like syringes, intricate surgical tools, and patient-specific implants. It is chosen when quality, scalability, and cost-effectiveness are critical.
Contact our professional team now for a same-day quote and risk-free project evaluation. Benefit from ISO 8 cleanrooms, advanced machines, and 12-hour fast response in medical injection molding.