Medical device plastic manufacturing plays a crucial role in the healthcare industry, with plastic medical device manufacturers providing materials essential for a wide range of medical applications, from MRI casings to plastic syringes and prosthetics. These materials are specifically engineered to meet stringent standards, ensuring patient safety and performance. The key characteristics of medical-grade plastics include biocompatibility, malleability, and hardness, allowing them to be used in highly precise applications. Additionally, these plastics must be compatible with advanced manufacturing processes, such as injection moulding and 3D printing, to create complex and reliable medical devices. The versatility and reliability of medical-grade plastics are what make them indispensable in the development of innovative healthcare solutions. Medical device plastic manufacturing uses biocompatible thermoplastics to produce durable, sterilization-resistant devices like syringes and surgical implants.
Low-Volume to High-Volume Production Capabilities
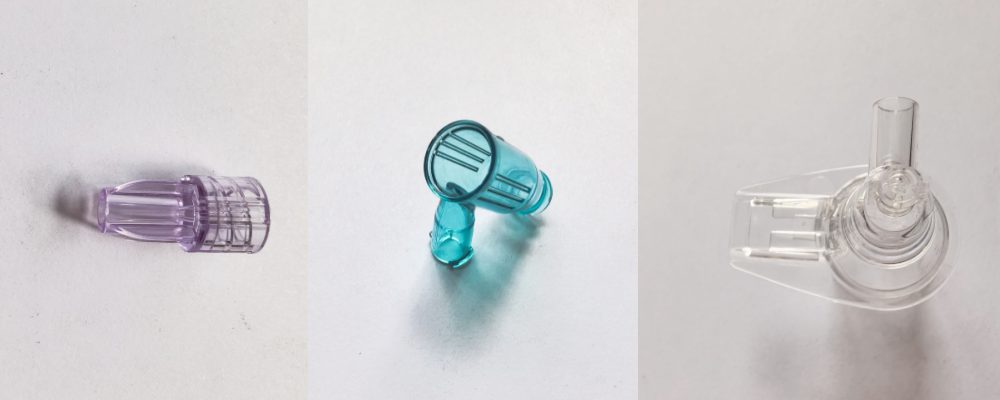
Attribute | Details |
---|---|
Processing Service | Moulding, Cutting |
Place of Origin | Dongguan, Guangdong, China |
Brand | LY Medical Injection Mold |
Plastic Molding Type | Injection Molding, Rotational Molding |
Materials Used | ABS, PA66, PP, PC, PMMA, PSU, PCTG, TPE, TPU, PBT, PE, ASA, Rubber |
Applications | Medical Devices |
Customization Options | - Size: Fully customized to client drawings |
- Color: Grey, custom colors, or client request | |
- Surface Finish: Custom textures, polishing, spray painting, etc. | |
Quality Standards | - ISO 9001 certified - 100% professional inspection |
Tolerance | ±0.003mm to ±0.01mm |
Applications | - Medical equipment, enclosures, sterile products, and skin prick test prong applicators |
Product Features | - Material Capability: Rubber, plastic |
- Durability: IP54-rated enclosures for harsh conditions | |
- OEM and ODM services available | |
- High accuracy for complex medical and industrial applications | |
- Flexible design, production, and shipping solutions | |
Lead Time | - Production: 7-30 days |
- MOQ: 1 to 10,000 pieces | |
Packaging Options | Plastic bags, cardboard boxes, wooden cases |
Safety of Medical Grade Plastics in Medical Device Plastic Manufacturing
The safety of medical-grade plastics is a critical consideration in medical device plastic manufacturing, ensuring that devices are safe for patient use and function effectively. These materials are subjected to rigorous testing and regulations to guarantee their biocompatibility and resistance to contaminants.
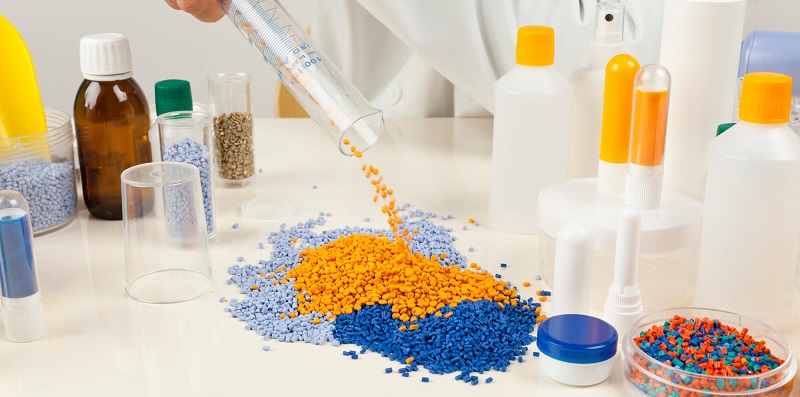
Biocompatibility Standards
Medical grade plastics must meet strict biocompatibility standards, ensuring they do not cause adverse reactions when in contact with body tissues. Medical molded plastics solutions are particularly important in plastic medical device manufacturing, where devices like syringes, implants, and catheters are inserted into or come into direct contact with the human body. These solutions ensure that the materials used are safe, durable, and meet the highest standards for medical applications.
Chemical Resistance and Durability
Medical plastics must be resistant to chemicals, fluids, and temperatures that are common in medical environments. This ensures that the materials retain their strength and integrity under various conditions, which is crucial in the production of devices used in critical medical procedures.
Sterilization Compatibility
A key aspect of safety in medical plastics is their compatibility with sterilization processes. Medical plastics used in the manufacturing of medical devices must be able to withstand sterilization methods such as autoclaving, without degrading or releasing harmful substances.
Plastic Medical Device Manufacturing Considerations
In plastic medical device manufacturing, the safety of the final product is deeply linked to the selection of appropriate plastics and production techniques. Plastic injection molding medical parts companies, for example, specialize in precise control over the final product’s shape and characteristics, ensuring that the devices produced meet the required safety standards. This manufacturing process allows for high levels of precision and consistency, critical for producing medical devices that must adhere to strict regulatory requirements.
Compliance with Regulatory Guidelines
Medical device plastic manufacturing must adhere to stringent regulatory guidelines, such as those set by the FDA and ISO, to ensure the safety of medical devices. Compliance with these standards is essential for preventing risks to patients and ensuring the reliability of medical devices throughout their lifecycle.
The safety of medical-grade plastics is fundamental in the medical device plastic manufacturing process. The use of precision mold medical techniques in this process helps achieve high accuracy and consistency, ensuring that the final products meet both regulatory requirements and the highest standards of patient care.
Common Types of Thermoplastics in Medical Injection Moulding for Medical Device Plastic Manufacturing
Thermoplastics are widely used in medical device plastic manufacturing due to their ability to be molded into precise shapes, ensuring the reliability and functionality of medical devices. In medical injection moulding, thermoplastics offer flexibility, durability, and a wide range of properties, making them ideal for diverse medical applications. In addition, medical device automation further enhances the efficiency and consistency of the medical injection molding process, enabling high-volume production of precise and reliable medical components.
Polypropylene (PP)
Polypropylene is a lightweight and chemically resistant plastic, often used in the production of medical devices such as syringes, containers, and diagnostic equipment. Its resistance to chemicals and moisture makes it ideal for medical environments where cleanliness and sterilization are paramount.
Polycarbonate (PC)
Polycarbonate is known for its strength and impact resistance, making it suitable for medical device plastic manufacturing. It is commonly used in the production of medical equipment like respiratory devices, IV connectors, and optical components. Polycarbonate can also be molded into transparent forms, which is essential for devices requiring clear viewing.
Polyvinyl Chloride (PVC)
Polyvinyl chloride is widely used in medical plastic medical device manufacturing due to its versatility and cost-effectiveness. It is often found in the production of blood bags, tubing, and other flexible medical components. PVC can be formulated in soft or rigid forms, depending on the application.
Acrylonitrile Butadiene Styrene (ABS)
ABS is known for its toughness and durability, making it ideal for use in medical devices like surgical instruments, casings, and housings for diagnostic equipment. It is easy to process and provides excellent strength and impact resistance, ensuring long-lasting performance in medical applications.
High-Density Polyethylene (HDPE)
HDPE is a rigid, strong plastic that is resistant to impact and chemicals, making it suitable for medical devices requiring durability and chemical resistance. It is commonly used for containers, medical packaging, and even certain implants.
Polymethyl Methacrylate (PMMA)
PMMA, also known as acrylic, is often used in medical device plastic manufacturing for its clarity and optical properties. It is frequently used in the production of medical optical devices like lenses, as well as in implants and other applications where clear visibility is crucial.
Injected Molded Foam Manufacturing Medical Devices
The foam manufacturing of injection molding medical devices is a growing trend in the medical device industry. This process involves creating lightweight, durable, and flexible foam components that are injected into molds to form medical devices. The foam material offers excellent cushioning, insulation, and support properties, which makes it ideal for use in devices like orthotics, prosthetics, and protective covers for sensitive medical equipment.
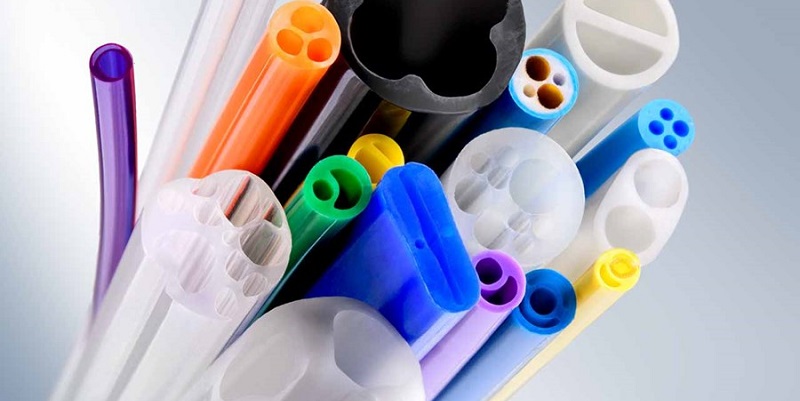
The combination of injection moulding and foam materials allows for the creation of devices that are not only functional but also comfortable and lightweight, essential for patient comfort and ease of use. This method is becoming increasingly popular in medical device plastic manufacturing due to its versatility and ability to produce complex geometries at a lower cost.
The use of thermoplastics in medical device plastic manufacturing, including the innovative use of injected molded foam, plays a pivotal role in the development of safe, effective, and patient-friendly medical devices.
Keys to Successful Medical Device Plastic Manufacturing Through Injection Molding
The success of medical device plastic manufacturing through injection molding depends on precision, material integrity, and adherence to strict regulatory requirements. Below are the key aspects that contribute to a successful process:
Mold Design for Accuracy and Functionality
Mold design is a foundational element in the injection molding process. The initial part design, developed using CAD software, must be optimized to meet the specific requirements of injection molding. The mold must account for factors such as shrinkage, wall thickness, and draft angles to ensure that the final product matches the intended fit and functionality. In some cases, certain intricate features may require design modifications, as not all geometries can be effectively produced through injection molding. A well-designed mold guarantees dimensional accuracy, efficient production, and long-term reliability.
Material Selection for Compliance and Performance
Careful material selection is crucial in medical device plastic manufacturing to meet the healthcare industry’s rigorous standards. Materials must comply with FDA regulations and ensure:
- Biocompatibility: Safe interaction with the human body without adverse effects.
- Sterilizability: Ability to withstand sterilization methods such as autoclaving, gamma irradiation, or ethylene oxide (ETO).
- Durability: Resistance to mechanical stress, chemicals, and environmental factors.
The injection molding process offers access to a broad range of thermoplastic and thermoset materials, allowing manufacturers to select the most suitable option for specific medical applications.
ISO Class 8 Cleanroom for Contamination Control
Maintaining a clean production environment is essential to producing high-quality medical devices. Injection molding for medical applications often takes place in ISO Class 8 cleanrooms, which are designed to minimize contamination risks. These cleanrooms comply with ISO 14644 standards for air cleanliness, including strict control of particles, bioburden, and electrostatic discharge (ESD).
Additionally, controlled environment spaces with temperature regulation and pressurization are used for processes like part decoration, assembly, and packaging, ensuring that the final product meets safety and sterility requirements.
Process Validation to Ensure Consistency and Quality
Process validation is a critical aspect of medical device plastic manufacturing. This method involves collecting and analyzing data throughout the design and production stages to establish scientific evidence that the injection molding process consistently produces high-quality parts. Process validation ensures:
- Safe and reliable products that meet performance specifications.
- Reduction in scrap rates and waste.
- Prevention of part failures in the field.
- Compliance with regulatory and application requirements.
For medical devices, where patients’ lives are at stake, process validation is indispensable in guaranteeing that every part meets the highest standards for safety, precision, and performance.
By focusing on optimized mold design, careful material selection, contamination-free production environments, and rigorous process validation, manufacturers can achieve success in medical device plastic manufacturing. These keys ensure the consistent delivery of safe, durable, and high-quality plastic components essential to the medical industry.
Advantages of Medical Device Plastic Manufacturing Through Injection Molding
Medical device plastic manufacturing through injection molding offers a wide range of advantages, making it the preferred choice for producing high-quality, reliable, and cost-effective medical components. Below are the key benefits of this process from multiple aspects:
Unparalleled Accuracy and Consistency
Injection molding ensures exceptional precision and consistency, allowing manufacturers to produce parts with tight tolerances and identical specifications. This level of accuracy is critical in the medical field, where even minor deviations can impact device functionality and patient safety.
Design Flexibility for Complex Components
The injection molding process offers unmatched design flexibility, enabling engineers to create intricate and custom components with minimal tooling changes. This adaptability is essential for developing innovative and unique medical devices to meet the evolving demands of healthcare applications.
Cost-Effective for High-Volume Production
While the initial tooling costs can be significant, injection molding becomes highly cost-effective for large-scale production. Once the mold is in place, manufacturers can produce high quantities of parts quickly and efficiently, significantly lowering unit costs and making it ideal for mass production.
Accelerated Time to Market
Injection molding streamlines the production process, reducing the time needed to manufacture medical devices. This rapid production capability enables companies to bring new and life-saving devices to market faster, giving healthcare providers access to critical innovations sooner.
Regulatory Compliance with FDA-Approved Materials
Meeting strict regulatory requirements is essential in medical device plastic manufacturing. Injection molding supports the use of FDA-approved materials, ensuring that components comply with safety, quality, and performance standards right from the start.
Biocompatibility for Patient Safety
Medical devices often require direct contact with the human body. Injection molding allows for the use of biocompatible materials that are safe, non-toxic, and sterilizable without degrading their properties. This ensures patient safety while meeting a variety of medical application needs.
Scalability for Flexible Production Volumes
Injection molding is highly scalable, making it suitable for both low-volume prototype development and high-volume production runs. This flexibility enables manufacturers to adapt to varying market demands and production needs efficiently.
Reduction in Material Waste
Compared to other manufacturing processes, injection molding generates minimal material waste. The ability to optimize material usage not only reduces production costs but also supports sustainability efforts, aligning with the industry’s focus on environmentally friendly manufacturing practices.
Post-Processing Versatility
Injection molded parts can undergo a variety of post-processing operations, including assembly, machining, laser marking, pad printing, and surface treatments. These processes enhance the functionality, appearance, and precision of medical components to meet specific device requirements.
Enhanced Structural Integrity and Performance
Injection molding produces parts with exceptional structural integrity, ensuring they can withstand mechanical stress, sterilization, and the demands of their intended medical application. This durability enhances long-term performance and reduces the likelihood of defects or failures.
Medical device plastic manufacturing through injection molding combines precision engineering with advanced manufacturing technology. Its benefits—ranging from accuracy and cost-effectiveness to scalability and regulatory compliance—make it a cornerstone of medical device production. By enabling engineers to create complex, biocompatible components at scale, injection molding accelerates innovation and ensures life-saving medical devices reach the market faster and with uncompromising quality. As the healthcare industry continues to evolve, injection molding will remain at the forefront of shaping the future of medical device manufacturing.
Quality and Safety Standards in Medical Device Plastic Manufacturing
Ensuring quality and safety in medical device plastic manufacturing requires a multifaceted approach, encompassing strict adherence to regulatory guidelines, advanced testing protocols, and robust manufacturing processes. Below are the key aspects that manufacturers focus on to guarantee the safety, reliability, and performance of medical plastic products:
Compliance with Regulatory Standards
Medical plastic manufacturers operate under stringent regulatory frameworks, including international standards such as ISO 13485 for medical devices and Good Manufacturing Practice (GMP) guidelines. These standards mandate precise controls over production processes, ensuring that every stage—from material selection to final product assembly—meets consistent quality benchmarks. Regulatory compliance guarantees that medical plastic products are safe, effective, and suitable for healthcare use.
Material Selection and Biocompatibility Testing
The materials used in medical device plastic manufacturing must be biocompatible to ensure they do not cause adverse reactions when in contact with the human body. Manufacturers conduct biocompatibility testing in accordance with standards like ISO 10993 to evaluate cytotoxicity, sensitization, and irritation. This ensures that plastics are non-toxic, hypoallergenic, and free from harmful contaminants.
Rigorous Quality Control and Testing
Quality control in medical plastic manufacturing involves a series of rigorous tests to ensure durability, safety, and performance. Common testing processes include:
- Sterilization Testing: Ensures products can withstand sterilization methods like autoclaving, gamma irradiation, or ethylene oxide (ETO) without compromising structural integrity.
- Material Durability Testing: Verifies that the plastics can endure mechanical stress, temperature fluctuations, and chemical exposure under real-world medical conditions.
- Contaminant Analysis: Identifies and eliminates foreign particles or chemical residues that could pose risks to patients.
Adherence to Good Manufacturing Practices (GMP)
GMP guidelines require manufacturers to establish controlled, clean production environments to minimize contamination risks. These practices include proper facility design, equipment maintenance, employee training, and documentation to ensure consistent quality. Every product batch undergoes thorough inspection and validation to comply with industry requirements.
Traceability and Documentation
Medical plastic manufacturers maintain detailed traceability records for all materials, components, and processes involved in production. This ensures that any potential quality issue can be quickly identified, traced to its source, and resolved. Comprehensive documentation is also vital for regulatory audits and maintaining transparency in the manufacturing process.
Continuous Improvement and Innovation
To stay at the forefront of safety and quality, manufacturers invest in research and development, seeking innovative materials and processes that enhance product performance. Advanced technologies like automated quality inspection systems and cleanroom manufacturing further elevate the precision and reliability of medical plastic products.
By implementing these measures, medical device plastic manufacturing ensures that products consistently meet the high safety and quality standards demanded by the healthcare industry. This rigorous approach safeguards patient well-being while enabling the production of reliable, high-performance medical devices.
Sustainable Practices in Medical Device Plastic Manufacturing to Reduce Environmental Impact
The environmental impact of medical device plastic manufacturing can be significantly reduced through a combination of sustainable practices, innovative technologies, and material efficiency.
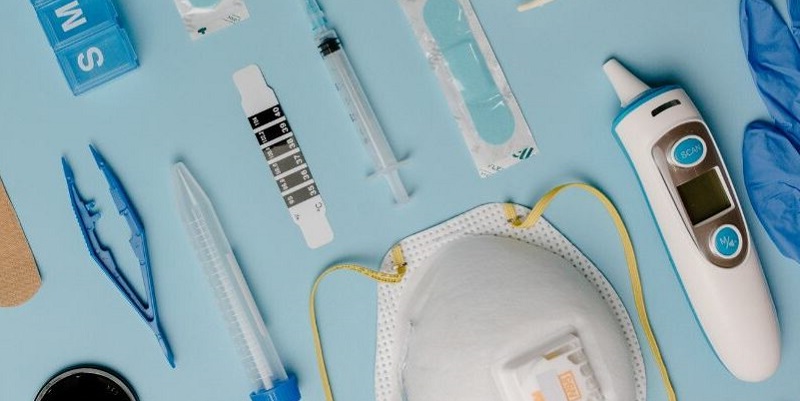
Below are detailed measures that can help minimize the ecological footprint of plastic-based medical products:
Adopting Biodegradable and Recyclable Materials
Traditional plastics used in medical devices, such as PVC and polyethylene, often pose disposal challenges due to their non-biodegradable nature. By incorporating biodegradable polymers, such as polylactic acid (PLA) or polyhydroxyalkanoates (PHA), manufacturers can create products that naturally break down over time. Recyclable thermoplastics are another viable solution, as they can be reprocessed into new medical components without compromising quality. Material innovations ensure that plastics are more sustainable while maintaining their safety and performance standards.
Implementing Closed-Loop Recycling Systems
A closed-loop recycling process minimizes waste by reintroducing used medical plastic components back into the production cycle. This system involves collecting, sterilizing, and recycling plastic medical products to produce new devices. Although medical plastics require stringent hygiene measures, advanced recycling technologies such as pyrolysis or mechanical recycling can ensure high-grade output suitable for reuse.
Reducing Plastic Usage Through Design Optimization
Optimizing the design of medical devices can significantly decrease plastic consumption. Manufacturers can adopt lightweighting techniques to reduce material usage without compromising functionality. Multi-functional components and modular designs also help minimize the overall need for separate plastic parts, further reducing environmental impact.
Utilizing Renewable Energy in Manufacturing
Transitioning to renewable energy sources, such as solar or wind power, can lower the carbon footprint of medical device plastic manufacturing processes. Energy-efficient production equipment, combined with clean energy sources, helps reduce greenhouse gas emissions, contributing to overall sustainability.
Enhancing Product Lifecycle Management
Manufacturers can improve the environmental impact of medical plastic products by considering the entire product lifecycle—from material sourcing to end-of-life disposal. Implementing take-back programs allows medical facilities to return used products for recycling or repurposing. Additionally, adopting life cycle assessments (LCAs) can help identify areas for improvement in environmental performance.
Promoting Sustainable Supply Chain Practices
Partnering with suppliers that prioritize sustainable practices is essential for reducing the environmental impact of medical plastic production. This includes sourcing raw materials responsibly, minimizing transportation emissions, and ensuring compliance with environmental standards.
By adopting these measures, the medical device plastic manufacturing industry can balance its operational needs with environmental responsibility, fostering a sustainable future while maintaining the integrity and safety of essential medical products.
The Evolution of Medical Device Plastic Manufacturing and the Role of Medical Injection Molding
The medical device plastic manufacturing industry, driven by advancements in injection molding, has played a transformative role in modern healthcare. The development of medical plastics and their applications has evolved significantly over the decades, leading to safer, more efficient, and cost-effective medical solutions. Below is a historical overview of the industry’s evolution, highlighting key developments:
Early Innovations: Transition from Metals to Plastics
In the early 20th century, medical devices were primarily made of metals and glass. These materials, while durable, were heavy, costly, and difficult to sterilize. The introduction of thermoplastics in the mid-20th century marked a turning point, offering a lightweight, flexible, and sterilizable alternative. Polymers such as polyethylene (PE) and polystyrene (PS) became early materials for medical applications, ushering in the initial phase of medical device plastic manufacturing.
The Rise of Injection Molding in the Medical Field
Injection molding technology became widely adopted in the 1940s and 1950s due to its ability to produce high-quality plastic components with unmatched precision and consistency. This innovation allowed medical manufacturers to mass-produce disposable devices like syringes, tubing, and connectors efficiently. By the 1960s, medical-grade plastics such as polypropylene (PP) and polyvinyl chloride (PVC) emerged, further expanding the range of applications.
Biocompatibility and Sterilization: Medical Plastics in the 1970s–1980s
As the medical industry advanced, the need for biocompatible materials that could safely interact with the human body became paramount. The 1970s and 1980s saw the development of specialized medical plastics such as silicone, polycarbonate (PC), and polyurethane (PU). These materials were sterilizable and non-toxic, making them suitable for implants, surgical instruments, and devices like catheters. Injection molding became a key process for shaping these complex, high-performance plastics into precise components.
The Disposable Revolution and Infection Control
The AIDS epidemic in the 1980s and rising concerns about infection control drove a surge in demand for single-use medical devices. Injection-molded disposable plastics provided a solution to minimize contamination risks and improve patient safety. Devices like single-use syringes, IV tubing, and surgical instruments became industry standards, highlighting the vital role of medical device plastic manufacturing.
Technological Advancements in the 21st Century
In recent decades, technological advancements have further refined medical injection molding processes. Innovations include:
- Micro-Injection Molding: Enables the production of miniature components for advanced medical devices such as implants, hearing aids, and surgical tools.
- Cleanroom Manufacturing: Ensures contamination-free production environments, meeting strict ISO standards for medical-grade plastics.
- Material Science Breakthroughs: The development of biocompatible and bioresorbable polymers, such as polylactic acid (PLA) and polyetheretherketone (PEEK), has revolutionized applications in implants and drug delivery systems.
Sustainability and the Future of Medical Plastics
Today, the industry is focused on balancing innovation with sustainability. Efforts to develop recyclable and biodegradable plastics, as well as adopting closed-loop manufacturing processes, reflect the growing demand for environmentally friendly solutions. Advances in 3D printing and precision molding are opening new frontiers in patient-specific implants and prosthetics, pushing medical device plastic manufacturing into a new era.
The evolution of medical device plastic manufacturing has been a story of innovation, precision, and adaptation to the healthcare industry’s ever-changing needs. From replacing metals with early thermoplastics to today’s biocompatible, sustainable solutions, injection molding has been at the heart of this transformation. As technology continues to advance, medical injection molding will remain a driving force in shaping safer, more efficient, and cutting-edge medical devices for the future.
Future Innovations in Medical Device Plastic Manufacturing
The future of medical device plastic manufacturing is evolving as the healthcare sector seeks innovative ways to address environmental concerns while advancing technology. Below are several key areas where plastics are expected to play a transformative role in the medical field:
Sustainable and Recyclable Materials
With growing scrutiny over the environmental impact of disposable medical plastics, manufacturers are exploring sustainable alternatives. Materials like polyolefins are emerging as replacements for traditional polyvinyl chloride (PVC), which is more difficult to recycle. These new materials improve recyclability, reduce medical waste, and provide a greener solution for disposable items such as syringes, catheters, and packaging. The adoption of sustainable plastics will help balance the demand for single-use medical devices with environmental responsibility.
Advances in 3D Printing Technologies
3D printing is revolutionizing medical device plastic manufacturing by enabling the rapid production of specialized medical tools, implants, and prosthetics. This technology has several promising applications:
- Custom Medical Implants: Healthcare providers can design and manufacture patient-specific implants, ensuring better fit and functionality. Customization reduces recovery times and improves patient outcomes.
- Remote Manufacturing: In remote or underserved areas, 3D printing provides access to critical medical tools and devices. Plastics used in these printers are lightweight, durable, and cost-effective, offering on-demand manufacturing capabilities.
- Training and Research Applications: 3D printing allows for the creation of realistic bone, organ, and tissue models. These plastic models are invaluable in medical training environments, helping surgeons practice procedures and researchers study complex anatomy before actual surgeries.
Development of Biocompatible and Smart Plastics
Advances in material science are leading to the creation of biocompatible plastics that interact safely with the human body. These plastics can be used in long-term implants, drug delivery systems, and bioresorbable stents, which dissolve over time after serving their purpose. Additionally, smart plastics—capable of responding to environmental conditions like temperature or pH—are opening new avenues in diagnostics and treatment delivery.
Reduction of Medical Waste Through Circular Economy Models
Manufacturers are adopting circular economy principles, where plastic medical devices are designed for reusability or recyclability. Future processes may include closed-loop recycling systems that reclaim and repurpose plastics from disposable products, significantly reducing landfill contributions.
Improved Performance in Medical Devices
High-performance plastics will continue to replace traditional materials like metals in medical devices due to their durability, lightweight properties, and flexibility. These materials are ideal for minimally invasive surgical tools, wearables, and portable medical devices, enhancing both patient comfort and treatment outcomes.
The future of medical device plastic manufacturing lies in sustainable practices, advanced technologies like 3D printing, and innovative materials that meet both medical and environmental needs. These developments will drive efficiency, improve patient care, and reduce the ecological footprint of plastic-based medical products.
FUJIU Medical Injection Mold – Medical Device Plastic Manufacturing Factory
At FUJIU Medical Injection Mold, we are proud to be a leading provider of innovative and reliable plastic manufacturing solutions for the medical industry. With over 20 years of expertise in ISO-certified medical injection molding, we specialize in the production of high-quality, precision medical device components. Our comprehensive services cover everything from mold design to automated assembly, ensuring that we meet the unique needs of every healthcare application.
As the demand for medical devices continues to grow, efficient, cost-effective production methods become increasingly crucial. Medical injection molding stands out as one of the most economical and effective ways to manufacture plastic parts used in medical devices. FUJIU Medical Injection Mold leverages cutting-edge technology, including state-of-the-art machinery and automated quality inspection systems, to produce plastic components that adhere to the highest safety and performance standards.
Expertise in Custom Solutions
Our in-house design for manufacturability (DFM) expertise allows us to create custom solutions tailored to the specific requirements of each medical device. We understand the complexities involved in medical device production and work closely with our clients to develop cost-efficient, reliable, and functional plastic parts.
Wide Range of Medical-Grade Resins
We offer a diverse selection of medical-grade resins, carefully chosen to meet the stringent safety and efficacy standards demanded by the medical industry. Whether for diagnostic, therapeutic, or surgical applications, our materials are selected for their durability, biocompatibility, and compliance with global regulations.
Reliable and High-Quality Production
Our advanced medical injection molding processes, combined with automated inspection systems, ensure that every part produced is of the highest quality. From prototyping to mass production, we guarantee reliable service and superior product consistency, making us the preferred partner for medical device manufacturers worldwide.
FUJIU Medical Injection Mold is your one-stop solution for all your medical device plastic manufacturing needs. Trust our experience and commitment to quality to deliver precision-engineered components that support better healthcare outcomes.
FAQs about Medical Device Plastic Manufacturing
Medical equipment made of plastic includes a wide variety of items, such as syringes, catheters, IV bags, surgical instruments, and diagnostic devices. Plastics are favored in the medical field due to their versatility, cost-effectiveness, and ability to be molded into complex shapes. Additionally, plastic is lightweight, durable, and can be designed to be disposable or reusable. This makes plastic an ideal material for creating single-use items that need to be sterile, as well as more permanent fixtures in healthcare settings. Other common examples include tubing, protective gloves, inhalers, and various types of containers used for storing samples and medications.
Biocompatibility: The plastic must be non-toxic and not cause any adverse reaction when in contact with the human body.
Sterilizability: The material should be able to undergo sterilization processes (like autoclaving, gamma radiation, or chemical sterilization) without degrading.
Durability: Medical plastics need to withstand the mechanical stresses and strains during their use, ensuring they do not crack or break.
Chemical Resistance: The material should resist degradation when exposed to various chemicals, including cleaning agents, bodily fluids, and pharmaceutical substances.
Medical devices made of polymers include a wide spectrum ranging from everyday items to advanced technology instruments. Some of the most common devices include disposable gloves, syringes, IV bags, catheters, tubing, and wound dressings. Advanced devices such as heart valves, orthopedic implants, and artificial organs also utilize polymers for their biocompatibility and flexibility. Additionally, diagnostic devices, dental products, and even components of MRI machines and other imaging equipment often incorporate polymers. The versatility of polymers, their safety, and their compatibility with various sterilization methods make them indispensable in modern medical technology.
The headquarters of BMP Medical is located in Gardner, Massachusetts, USA. BMP Medical specializes in the production of custom plastic medical devices, leveraging their location to serve the healthcare industry effectively. Their headquarters is strategically positioned to offer logistical advantages, ensuring efficient distribution and service within the medical sector. The company’s facilities in Gardner are equipped with advanced manufacturing technologies, supporting their mission to provide high-quality, reliable medical products and components to their clients.
High-density polyethylene (HDPE) is indeed used in medical device manufacturing, valued for its chemical resistance, durability, and biocompatibility. This thermoplastic material is particularly suitable for single-use devices and components, such as specimen containers, trays, and tubing. Its non-reactive surface makes it ideal for applications requiring cleanliness and resistance to contamination.
HDPE’s ease of processing allows for cost-effective production of medical devices with precise tolerances. It is also lightweight, making it an excellent choice for portable medical devices or components that must be easily handled by healthcare professionals. Moreover, its high resistance to impact and moisture ensures the integrity of products even under demanding storage and transportation conditions.
Although HDPE is not as commonly used as other plastics like polycarbonate or polypropylene for high-performance devices, its reliability in specific applications makes it a key material in medical plastics. Its compatibility with sterilization methods further enhances its usability in the healthcare sector.
Contact our professional team now for a same-day quote and risk-free project evaluation. Benefit from ISO 8 cleanrooms, advanced machines, and 12-hour fast response in medical injection molding.