Medical enclosure molding is a vital process in the manufacturing of medical devices, ensuring that the external casings are both durable and precise. The enclosures protect delicate internal components and help maintain the functionality of medical equipment in various environments. Precision is paramount, as even the smallest defect can compromise the safety and performance of the device. Medical injection molding companies play a significant role in this process by using advanced techniques and materials to meet strict regulatory standards. Through medical enclosure molding, manufacturers can produce high-quality, cost-effective enclosures that meet the rigorous demands of the healthcare industry. Additionally, medical molding services further enhance this process by providing customized solutions that meet specific design requirements, enabling manufacturers to produce enclosures tailored to unique medical devices. This molding technique is essential for creating reliable and secure medical devices. Medical enclosure molding uses aluminum tooling and versatile materials to create durable, cost-effective enclosures with high design flexibility.
Low-Volume to High-Volume Production Capabilities
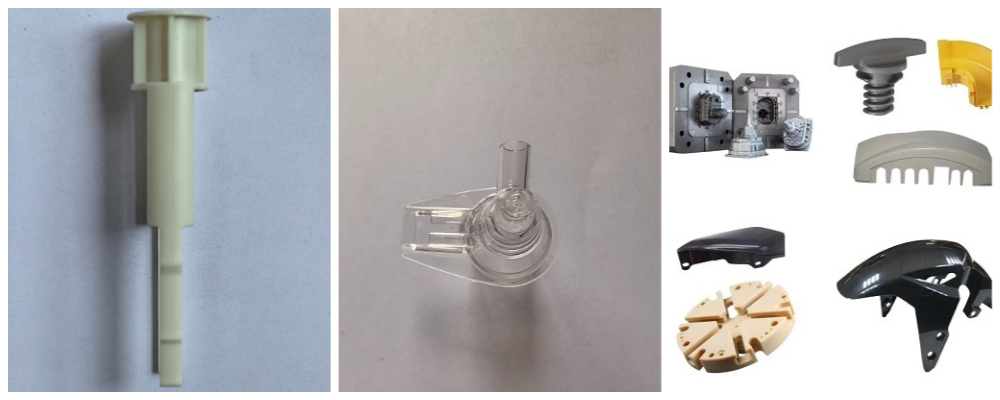
Attributes | Details |
---|---|
Place of Origin | Dongguan, Guangdong, China |
Brand Name | LY Medical Injection Mold |
Product Name | Medical Enclosure Molding |
Material | Plastic |
Plastic Material | ABS/PP/PS/PE/PVC/PA6/PA66.....etc. |
Application | Medical Industry |
Color | Customized |
Size | Customized |
Model | Customized |
Logo | Customer Logo |
Mold Life | According to Customer Requirements |
Surface Treatment | Texture, Polishing, Painting, Plating, Sandblasting, etc. |
Process | Silicone Molding/Vacuum Casting |
Drawing Format | .igs/.stp/.xt/.step/.stl/.sldprt/.dwg/.dxf |
Certification | ISO |
Process | Thermoforming, Processing, Extrusion, Coating |
Processing Service | Molding, Cutting |
Minimum Order Quantity | 1 Piece |
Packing | Carton |
What is Medical Enclosure Molding?
Medical enclosure molding refers to the process of creating the external casings for medical devices using injection molding techniques. This method involves injecting molten plastic or other suitable materials into a mold to form the desired shape and structure of the device’s enclosure. The goal of medical enclosure molding is to produce durable, lightweight, and secure enclosures that can withstand the rigors of medical environments while ensuring the safety and protection of sensitive internal components.
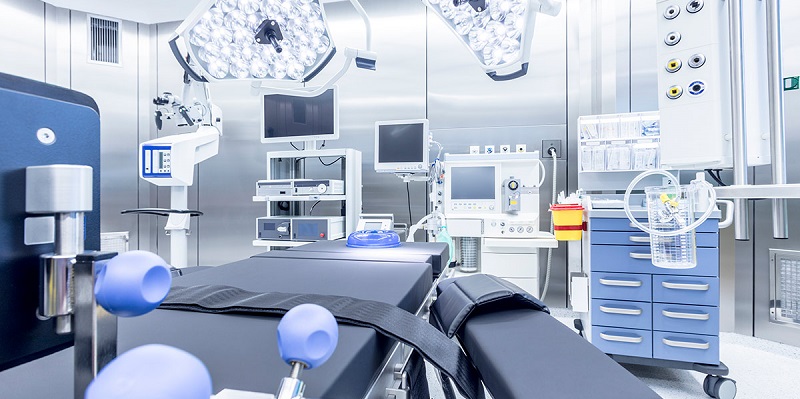
Materials Used in Medical Enclosure Molding
The materials selected for medical enclosure molding are critical for the performance and safety of the medical device. Some commonly used materials include:
- Thermoplastics like polycarbonate, ABS, and polypropylene, known for their strength and ease of molding.
- Medical-grade resins that meet the strict regulatory standards for medical devices.
- Antimicrobial materials for devices intended for frequent contact with patients or healthcare providers.
- Polyurethane and nylon for devices requiring flexibility and impact resistance.
Key Benefits of Medical Enclosure Molding
- Precision Manufacturing: Ensures exact tolerances to meet industry standards for device performance and safety.
- Customization: Offers the ability to create unique shapes, sizes, and features for different medical device types.
- Cost-effectiveness: The efficiency of injection molding allows for high-volume production at a lower cost per unit.
- Regulatory Compliance: Medical enclosure molding can be performed using materials that comply with FDA and ISO standards for medical devices.
By using medical enclosure molding, manufacturers can produce enclosures that not only protect sensitive electronics and components but also contribute to the overall performance and reliability of medical devices in various healthcare settings.
Medical Enclosure Molding Cost: Factors to Consider
The cost of medical enclosure molding can vary depending on several factors, all of which play a crucial role in determining the final price of production. Understanding these factors is essential for businesses to optimize their enclosure medical device plastic manufacturing process and budget effectively.
Material Selection
The type of material chosen for the molding process significantly impacts the overall cost. Medical-grade plastics such as polycarbonate, ABS, and polypropylene may have different pricing based on factors like material availability, durability, and suitability for the intended application. More specialized materials, like antimicrobial plastics or FDA-approved resins, tend to be more expensive. The choice of material also affects factors like mold wear, production time, and the need for additional post-processing.
Complexity of Design
The complexity of the enclosure design is another key factor influencing the cost of medical enclosure molding. Designs with intricate features, such as detailed surface textures, thin walls, or multi-part components, require more advanced molds and longer cycle times. More complex designs can increase production time, tooling costs, and the risk of defects, which adds to overall costs. Simple, straightforward designs typically incur lower molding costs due to faster production times and less detailed medical molding requirements.
Tooling and Mold Costs
Creating the mold for medical enclosure molding is a significant upfront expense. Tooling costs depend on factors like mold size, material, and the number of cavities in the mold. Medical mold designed for high-volume production are typically more expensive but offer cost savings over time due to their durability and ability to produce large quantities of parts in a short period. The need for prototype molds or adjustments during the design process can further increase costs.
Production Volume and Lead Time
The scale of production also plays a major role in determining the cost of medical enclosure molding. Larger production runs tend to reduce the per-unit cost because the initial setup and mold costs are spread over more units. On the other hand, small production batches or custom orders may result in higher costs per unit due to the increased setup time and lower economies of scale. Additionally, tight lead times can increase costs as expedited production may require additional labor or resources to meet deadlines.
By considering these factors, businesses can better estimate the cost of medical enclosure molding and make informed decisions that balance quality, efficiency, and budget constraints.
Medical Enclosure Molding: A Key Aspect of Medical Device Production
Medical enclosure molding plays a vital role in the production of medical devices, providing the necessary external protection for sensitive internal components. The casing or enclosure of a medical device not only ensures safety but also contributes to the device’s overall functionality and longevity. Utilizing precision mold medical techniques in the molding process is essential, as it ensures that the enclosures are crafted with the highest accuracy, directly impacting the device’s performance and meeting regulatory standards.
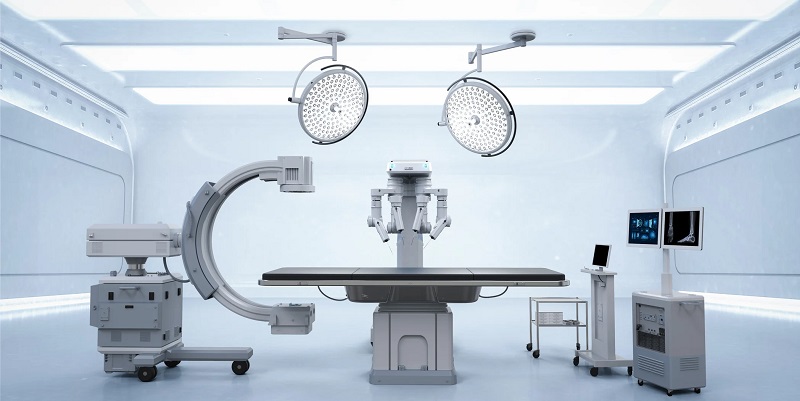
Protecting Sensitive Components
One of the main functions of medical enclosures is to protect the delicate electronics and other internal components from external factors, such as moisture, dust, and physical damage. This is especially important in medical devices, where reliability and safety are paramount. Medical enclosure molding allows manufacturers to create enclosures that are airtight, waterproof, and resistant to impact, ensuring that the device operates effectively under varying conditions.
Compliance with Regulatory Standards
Medical devices are subject to stringent regulations, particularly in industries like healthcare and pharmaceuticals. Enclosures produced through medical enclosure molding must meet FDA standards and other regulatory requirements to ensure that the devices are safe for use. These regulations may dictate the types of materials that can be used, the mold design, and even the processes involved in production. Meeting these standards is essential for manufacturers who aim to get their products to market and maintain consumer trust.
Customization and Design Flexibility
Medical enclosure molding offers a high level of customization, allowing manufacturers to design enclosures that meet the specific needs of the medical devices. Custom shapes, sizes, and features can be incorporated into the mold to accommodate unique device functionalities. Whether it’s creating enclosures with multiple compartments, specific mounting points, or integrated cooling systems, the design flexibility of medical enclosure molding makes it a versatile solution for a wide range of medical applications.
Enhancing Durability and Longevity
Durability is a crucial factor in medical device enclosures, as these devices often need to perform reliably over long periods of time, even under harsh conditions. The materials used in medical enclosure molding, such as high-impact plastics and specialized resins, ensure that enclosures are robust enough to withstand wear and tear. This contributes to the overall longevity of the medical device, reducing the need for replacements and minimizing downtime in critical healthcare settings.
Medical enclosure molding is not just about creating a protective shell for medical devices; it is a key component of the device’s performance, compliance, and long-term reliability. This process plays a crucial role in ensuring that medical devices are both functional and safe for use in real-world medical applications.
Sealing Plans for Water-Resistant Medical Enclosure Molding
When designing a medical device enclosure, formulating a sealing plan to prevent water intrusion requires a comprehensive evaluation of several critical factors. Here’s a detailed explanation of the key considerations:
Chemical Compatibility
Medical devices often operate in environments where they are exposed to cleaning agents, disinfectants, or harsh chemicals. The materials used for the enclosure and sealing must resist degradation when in contact with these substances. Incompatible materials can crack, swell, or lose their sealing ability, compromising the enclosure’s integrity and functionality.
Durability and Strength
The enclosure and its sealing elements must withstand physical stresses such as impact, vibration, or pressure changes. Materials should be robust enough to maintain a secure seal over the device’s lifecycle, even in demanding conditions. This is particularly important for portable or wearable medical devices that endure frequent handling.
UV Exposure and Resistance
Devices used in outdoor settings or those exposed to sunlight must have UV-resistant materials. UV radiation can cause materials to become brittle, discolored, or degraded over time, potentially leading to seal failure and water ingress.
Electrical Conductivity or Insulative Properties
Depending on the device’s requirements, the enclosure materials and sealing plan must either block or allow electrical conductivity. For devices requiring electrical isolation, seals and materials must have excellent insulative properties. Conversely, devices needing grounding or shielding may require conductive materials.
Overall System Cost
The sealing solution should balance performance with cost-efficiency. Premium sealing materials or designs might improve durability and resistance but could also increase production costs. Manufacturers must evaluate whether higher initial costs result in long-term savings by reducing maintenance, repairs, or replacements.
Part Weight
In applications like portable or wearable medical devices, reducing part weight is critical for user comfort and convenience. Lightweight materials that do not compromise strength or sealing effectiveness are preferred to ensure the device remains practical without sacrificing protection.
Desired Product Performance
The sealing plan must align with the overall performance goals of the medical device. For instance, the required IP (Ingress Protection) rating determines the level of water and dust resistance needed. Factors like thermal resistance, noise dampening, or flexibility may also influence the choice of sealing methods and materials.
By thoroughly considering these aspects, designers can create a reliable sealing plan that ensures the medical device enclosure protects against water intrusion while meeting all performance and regulatory requirements.
Medical Enclosure Molding: Insert Molding Electronics for Medical Devices
Insert molding is a crucial technique used in medical enclosure molding, especially when integrating electronic components into the enclosures of medical devices. This process combines the precision of injection molding with the need to secure sensitive electronic parts within a protective casing. Insert molding allows manufacturers to incorporate various electrical components, such as wires, connectors, and circuit boards, directly into the molded part during production.
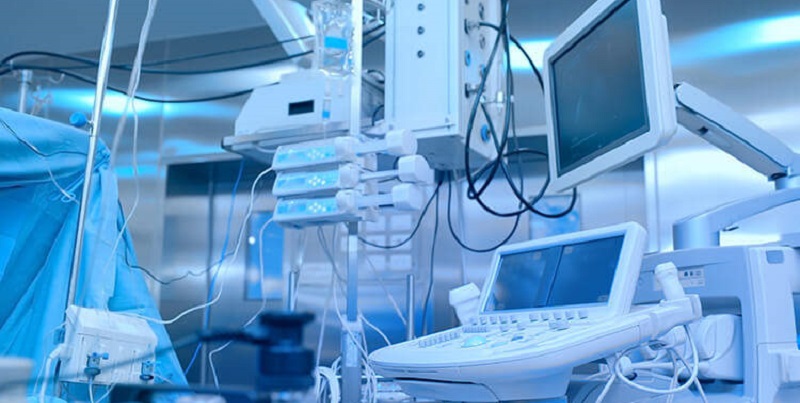
Benefits of Insert Molding for Medical Devices
Insert molding offers numerous advantages in the production of medical device enclosures, particularly when it comes to electronics integration. Some key benefits include:
- Improved Reliability: By embedding electronic components directly into the molded part, insert molding eliminates the need for additional assembly steps, reducing the risk of component misalignment or failure.
- Space Efficiency: This method allows for compact designs, which is crucial in medical devices where minimizing size and maximizing functionality are key.
- Enhanced Durability: The electronic components become securely encased within the material, providing additional protection against mechanical stress, moisture, and contaminants.
- Cost Savings: The ability to integrate electronics during the medical injection molding process can reduce the overall cost of production by eliminating the need for manual labor or secondary operations.
Application of Insert Molding in Medical Enclosures
In medical device production, insert molding is used to create enclosures for devices that require embedded electronics, such as pacemakers, infusion pumps, diagnostic equipment, and handheld medical devices. The integration of sensitive electronic components during medical enclosure molding ensures that they are protected from external factors like heat, moisture, and physical shock, which is critical for maintaining the integrity of the device.
By utilizing insert molding, manufacturers can create enclosures that not only protect the device but also streamline the overall production process, ensuring higher efficiency, lower costs, and enhanced product performance.
Medical Enclosure Molding and Medical Equipment Casings Molding: Ensuring Protection and Performance
Medical enclosure molding and medical equipment casings molding are integral processes in the production of medical devices, ensuring both protection and performance. These enclosures serve as the first line of defense for sensitive internal components, such as electronics and mechanical parts, and play a critical role in the safety and effectiveness of medical equipment.
Protection from External Hazards
Medical enclosures must safeguard the internal workings of medical devices from various external hazards, such as moisture, dust, and physical damage. The integrity of these enclosures is vital for maintaining the reliability of the device. Medical enclosure molding, when performed with high precision, ensures that the casing forms a durable barrier that protects against environmental factors while remaining lightweight and functional. Medical equipment casings molding achieves similar outcomes, allowing for the creation of robust, high-performance protective covers that can withstand harsh conditions in both clinical and non-clinical settings.
Regulatory Compliance and Performance Standards
Both medical enclosure molding and medical equipment casings molding must comply with rigorous industry standards. These standards ensure that enclosures meet the necessary safety and quality benchmarks required by regulatory bodies such as the FDA. The molding process must adhere to specifications that guarantee the device’s protection, while also ensuring that the device continues to perform optimally throughout its lifespan. The selection of suitable materials and molding techniques plays a vital role in achieving this balance between protection and performance.
Precision Engineering for Optimal Performance
In plastic medical device manufacturing, the precision of the molding process is key to the overall performance of the device. Whether for enclosures or equipment casings, medical enclosure molding and medical equipment casings molding allow for exact tolerances and detailed designs that are crucial for the accurate functioning of the device. Properly molded enclosures contribute to the smooth operation of the device, with components securely housed and properly aligned within the casing.
Together, medical enclosure molding and medical equipment casings molding ensure that medical devices are both well-protected and fully functional, delivering the necessary performance for healthcare professionals and patients alike.
FAQs about Medical Enclosure Molding
Medical molding refers to the specialized manufacturing process used to create components and enclosures for medical devices. This process is primarily used for producing parts that require high precision, reliability, and compliance with strict regulatory standards. Medical molding often involves injection molding, where molten material—typically medical-grade plastics or thermoplastics—is injected into molds to create the desired shape. These molds are designed to meet the specific needs of the medical industry, ensuring that the final product is safe, durable, and suitable for use in healthcare environments. The molded parts can range from external enclosures that protect sensitive internal components to intricate device components such as housings, connectors, or fluidic channels. Medical molding is vital because it ensures that medical devices are safe for patients, provide proper protection to sensitive electronics, and meet FDA and other regulatory standards. The precise nature of medical molding is crucial for the production of devices used in critical applications like diagnostics, patient monitoring, and surgical equipment.
The term “molding” refers to a broad category of manufacturing processes where material is shaped into a predetermined form by pouring or injecting it into a mold. While “molding” is a general term, “injection molding” is a specific type of molding that involves injecting molten material into a mold cavity under high pressure. The key difference between the two lies in the method of shaping the material.
Injection molding is typically used for mass production of high-precision components, and it is highly popular in industries like medical device manufacturing, automotive, electronics, and consumer products. It offers several advantages over traditional molding techniques, including high production speed, consistency, and the ability to create complex shapes with tight tolerances. In contrast, traditional molding methods (such as compression molding or rotational molding) may be used for larger parts or materials that are not suitable for injection molding. These methods often involve less precision and may be used for products that do not require the same high standards of accuracy or complexity as those in the medical field.
In the context of medical enclosure molding, injection molding is favored due to its ability to produce small, precise, and highly complex parts required in medical devices, ensuring both functionality and safety.
The cost of an injection molding machine varies widely depending on its size, capabilities, and technology. For medical enclosure molding, machines designed for high precision and cleanroom environments typically range from $50,000 to $500,000 or more.
Small-scale benchtop units used for prototyping may cost between $5,000 and $20,000, but they are unsuitable for large-scale medical manufacturing. Advanced units with features like multi-material molding, robotic integration, or FDA-compliant production systems fall into the higher price bracket.
Additionally, cleanroom compliance for medical molding can add significant costs. Air filtration systems, controlled environments, and automation further raise the price. For medical-grade enclosures, investing in a high-quality unit ensures repeatable accuracy, consistent product quality, and compliance with strict regulatory standards. Manufacturers should also account for maintenance and auxiliary equipment like molds, which may cost $10,000 to $100,000 per mold.
Injection molding is costly due to tooling, precision, and compliance requirements. For medical enclosure molding, the process involves designing and manufacturing custom molds, often crafted from durable materials like steel or aluminum. These molds, which can cost $10,000 to $100,000, are built to endure high pressure and maintain microscopic tolerances.
Cleanroom environments and regulatory compliance add further costs. Medical-grade materials, such as biocompatible plastics, are often more expensive than standard materials. Additionally, rigorous quality control, including inspections, testing, and certifications, contributes to higher operational expenses.
Advanced machinery capable of maintaining tight tolerances and sterility is another factor. While initial costs are high, injection molding is cost-effective for large production volumes, as the per-part price decreases significantly after tooling investment. The high upfront cost ensures reliability and compliance with healthcare standards, critical for medical enclosures.
The timeline for injection molding in medical enclosures depends on factors like part complexity, material, and production scale. A single injection molding cycle for a standard enclosure typically takes 30 seconds to 2 minutes, including injection, cooling, and ejection.
However, the full process, from concept to production, is much longer. Designing and manufacturing the mold may take 8 to 12 weeks due to precision requirements and cleanroom standards. Once the mold is ready, testing and validation, including sample runs and quality inspections, may add several weeks.
For large-scale production of medical enclosures, lead times can be streamlined due to automation and continuous production. However, cleanroom protocols, material sourcing, and regulatory compliance may extend timelines. Despite its initial duration, injection molding remains efficient for producing high-quality, compliant medical enclosures in large quantities.
Contact our professional team now for a same-day quote and risk-free project evaluation. Benefit from ISO 8 cleanrooms, advanced machines, and 12-hour fast response in medical injection molding.