Medical grade silicone for molding plays a critical role in the manufacturing of safe and effective medical devices. This specialized silicone offers unmatched biocompatibility, durability, and flexibility, making it an ideal material for devices that come into direct contact with human tissue. The high quality of medical grade silicone ensures it can endure sterilization processes and resist bacterial growth, crucial for patient safety. Its application spans various healthcare needs, from surgical instruments to custom-fit prosthetics. Given the stringent requirements in medical device production, the importance of using reliable, high-quality silicone cannot be overstated. medical molding silicone thus enables manufacturers to produce devices that meet strict health and safety standards. Medical grade silicone for molding is crucial for safe, biocompatible medical devices, ideal in dental, surgical, and consumer healthcare applications.
Low-Volume to High-Volume Production Capabilities
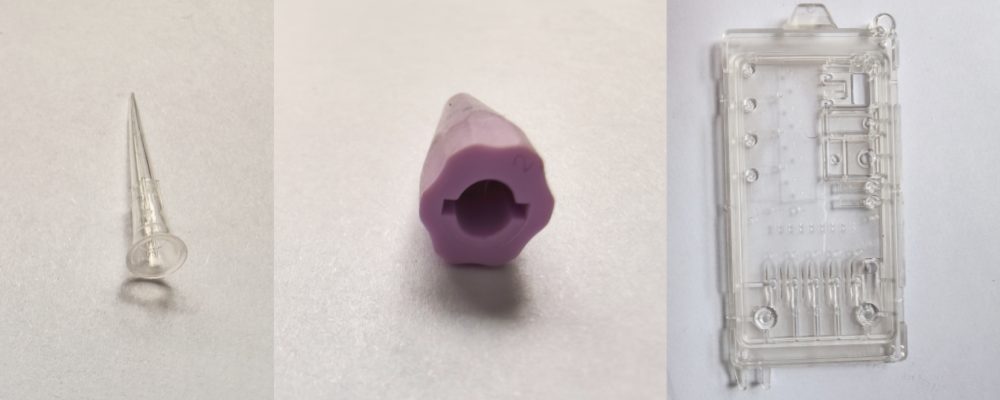
Attribute | Details |
---|---|
Purity | 99% |
Material | Medical Grade Silicone |
Appearance | Customizable shapes |
Hardness | 5~80 Shore A |
Features | High strength and resilience, eco-friendly, durable, high transparency, no yellowing |
Applications | Mold making, medical products, mask breathing tubes, catheters, electronics potting glue |
Color Options | Colorless, pale yellow, transparent, white, red, black, and customizable |
Processing Service | Moulding, injection molding |
Certification | FDA, MSDS, ROHS, LFGB, ISO 9001:2015 |
Shelf Life | 24 months |
MOQ | 1 piece |
Packaging | Custom options available |
Brand | LY Medical Injection Mold |
Place of Origin | Dongguan, Guangdong, China |
What is Medical Grade Silicone Molding
Medical grade silicone for molding has become essential in the production of medical devices and components due to its unique properties and safety profile. This material is favored in the healthcare industry because it meets stringent biocompatibility standards, offers superior durability, and can be sterilized repeatedly without degrading. Let’s delve into what makes medical grade silicone for molding a standout choice, including its unique qualities, the characteristics of liquid silicone rubber (LSR), and the key differences between medical grade silicone and standard silicone.
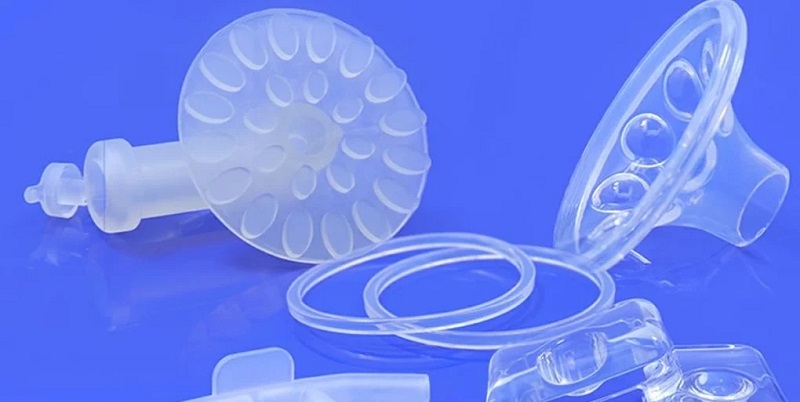
What Is Medical Grade Silicone Made Of?
What Is Silicone Made Of?
Silicone is a synthetic polymer made from a combination of silicon, oxygen, carbon, and hydrogen. The primary ingredient, silicon, is derived from silica (silicon dioxide), commonly found in sand or quartz. Here is a breakdown of the production process and composition:
Base Material: Silicon
- Silicon is extracted from silica through a high-temperature reduction process using carbon in an electric furnace.
- This results in pure silicon, which forms the backbone of silicone.
Chemical Transformation
- The pure silicon is reacted with methyl chloride at high temperatures to produce methylchlorosilanes.
- These compounds are separated and purified to extract dimethyldichlorosilane, the primary building block of silicone.
Polymerization
- Dimethyldichlorosilane undergoes hydrolysis to form silanols, which are then condensed into polydimethylsiloxane (PDMS), the most common form of silicone.
Final Composition
- Silicone is made up of a flexible polymer chain of alternating silicon and oxygen atoms, with organic groups (like methyl or phenyl groups) attached to the silicon atoms.
- Fillers, stabilizers, and other additives can be introduced to modify its properties, depending on the intended application.
Medical Grade Silicone Made Of
Medical grade silicone is a highly purified form of silicone, engineered to meet stringent safety and performance standards for use in medical applications. It is composed primarily of polydimethylsiloxane (PDMS), but its production involves additional steps and considerations to ensure biocompatibility and safety.
Base Material
- Similar to general silicone, medical grade silicone begins with silicon derived from silica.
- The silicon is converted to PDMS, ensuring high purity by removing contaminants and volatile compounds.
Additives and Fillers
- Medical grade silicone may include biocompatible fillers such as silica particles to enhance mechanical properties.
- Any additives used must comply with medical safety regulations and be non-toxic, ensuring they do not leach or degrade under medical conditions.
Cross-Linking Agents
- To achieve the desired consistency and durability, medical grade silicone undergoes cross-linking using agents such as platinum catalysts, which are safe and non-toxic.
Purity and Testing
- Medical grade silicone is subjected to extensive purification and quality testing to remove impurities, volatiles, and by-products.
- It must meet standards such as ISO 10993 or USP Class VI for biocompatibility, ensuring it does not cause adverse reactions in the human body.
Variants
- Medical grade silicone can be produced in different forms, such as Liquid Silicone Rubber (LSR), high-consistency rubber (HCR), or room-temperature vulcanizing (RTV) silicone, depending on the application.
Definition and Unique Qualities of Medical Silicone
Medical silicon molding is a specialized type of silicone that has been formulated and tested to be safe for use in medical applications. Unlike standard silicones, medical grade silicone is subjected to rigorous testing to ensure it meets high biocompatibility standards, which means it can safely interact with human tissue without causing adverse reactions. This is crucial for applications in medical implants, tubing, and other devices that come into contact with the human body. Medical grade silicone’s stability under a range of temperatures, its inert nature, and its resistance to chemical degradation make it a highly reliable material in both short-term and long-term medical use.
One of the standout qualities of medical grade silicone is its flexibility. This allows it to be shaped into complex forms, making it ideal for molding applications. Whether creating precise components for surgical devices or producing customized implants, medical grade silicone’s ability to retain its shape and properties over time makes it a preferred material in the healthcare sector.
Key Characteristics of Silicone Rubber Molding in Medical Devices for Molding Applications
Liquid Silicone Rubber (LSR) is a specific type of medical grade silicone for molding that is highly valued for its versatility in creating detailed and complex parts. LSR is a two-part platinum-cured elastomer that, once molded, forms a flexible, durable, and biocompatible product. The liquid form of LSR allows it to flow easily into intricate molds, ensuring accurate reproduction of details, which is crucial in medical devices where precision is required. To achieve this level of accuracy, precision mold medical techniques are employed, enabling the production of custom components that meet the strict demands of the healthcare industry. These precision molding methods ensure that every part, from implants to surgical tools, adheres to the highest standards of safety, performance, and reliability.
In medical molding applications, LSR offers several advantages:
- High Precision and Stability: The liquid medical injection molding process for LSR enables the creation of small, detailed parts with tight tolerances, an essential requirement in medical devices.
- Biocompatibility: LSR is non-toxic and hypoallergenic, making it safe for direct and prolonged contact with human tissues.
- Durability and Resistance: LSR molded products are resistant to extreme temperatures, UV exposure, and various chemicals, providing longevity and reliability in harsh medical environments.
Additionally, LSR’s low compression set ensures that molded parts maintain their shape and functionality, even after repeated use. This makes it ideal for components like seals, valves, and gaskets used in medical equipment, where consistency is critical.
How Medical Grade Silicone Differs from Standard Silicone in Safety, Purity, and Durability
The term “medical grade silicone for molding” specifically refers to silicone that has been produced and tested to meet rigorous safety and quality standards, differentiating it significantly from standard or commercial silicone. Medical grade silicone undergoes strict testing for purity, ensuring that it contains no harmful contaminants that could cause adverse reactions in the body. Unlike standard silicone, which may be suitable for industrial or consumer products, medical grade silicone is designed with patient safety as a priority.
Several key factors distinguish medical grade silicone:
- Safety Standards: Medical grade silicone must meet specific regulatory standards, such as ISO 10993 and FDA compliance, which mandate thorough testing for biocompatibility and toxicity.
- Purity: Medical silicone is manufactured in cleanroom environments to avoid contamination, ensuring it is free from potentially harmful substances that could interact negatively with human tissues.
- Enhanced Durability: Medical silicone is engineered to withstand sterilization methods like autoclaving, ensuring it remains safe and effective after multiple uses. Standard silicone, however, may degrade or lose its properties when exposed to these conditions.
Medical grade silicone for molding not only provides unmatched safety and reliability but also supports the high precision and customization required in the healthcare industry. Its unique properties make it an indispensable material for applications ranging from implantable devices to reusable medical instruments, solidifying its role in modern medical technology.
Benefits of Medical Grade Silicone for Molding Applications
Medical grade silicone for molding offers numerous benefits that make it highly suitable for producing medical devices and components. Its unique qualities, including flexibility, durability, and biocompatibility, ensure that it meets the strict requirements of the healthcare industry. Below, we explore the specific benefits of medical grade silicone for molding in detail.
Benefits | Description |
---|---|
Flexibility | Medical grade silicone for molding provides exceptional flexibility, allowing it to be molded into complex shapes and maintain elasticity. This is essential for items such as tubing, seals, and other devices that need to conform to precise shapes and movements. |
Durability | Designed to withstand repeated use, medical silicone remains strong and intact over time. Its durability is especially critical in applications where devices are exposed to mechanical stress, ensuring longevity and consistent performance. |
High-Temperature Resistance | Medical grade silicone for molding withstands high temperatures, making it suitable for sterilization methods such as autoclaving. This resistance ensures that molded components can endure repeated cleaning cycles without degrading. |
Chemical and Bacterial Resistance | Resistant to various chemicals and bacteria, medical grade silicone protects against contamination, a vital feature in the sterile environments of medical applications. It helps maintain a safe and uncontaminated environment for patients. |
Water Repellence | This material naturally repels water, which prevents moisture build-up, crucial in medical devices that must stay dry to maintain their function and integrity. The water-repellent properties make it ideal for use in respiratory and wound care applications. |
Non-Allergenic Properties | Medical grade silicone is hypoallergenic, reducing the risk of allergic reactions. This biocompatibility makes it safe for use in prolonged contact with human skin and tissues, as seen in devices such as implants and respiratory masks. |
Long-Term Stability | Medical grade silicone for molding maintains its properties over long periods, making it suitable for devices that require durability and a stable, unchanging structure. Its stability is crucial for products like prosthetics and implants. |
Minimal Compression Set | Medical silicone retains its shape under pressure, meaning it has a low compression set. This characteristic is ideal for seals and gaskets that must maintain their structure and function under continuous or repeated compressive forces. |
Example: Silicon Medical Face Mask Molding Machine
A silicone medical face mask molding machine is an excellent example of how medical grade silicone for molding is applied in critical healthcare settings. These machines mold silicone masks that need to meet strict requirements for patient safety, comfort, and durability.
- Precision and Flexibility: The machine uses liquid silicone rubber (LSR) to mold face masks that are highly flexible, ensuring a snug yet comfortable fit on patients’ faces.
- Durability and Safety: Masks produced with medical grade silicone are resistant to bacteria, chemicals, and high temperatures, allowing for safe and repeated sterilization without compromising material integrity.
- Biocompatibility: The masks are hypoallergenic, making them suitable for patients with sensitive skin and ensuring safe, non-irritating contact with facial tissues.
Medical grade silicone for molding has revolutionized the production of medical devices, bringing safety, flexibility, and durability to a range of applications that prioritize patient health and comfort. The combination of these benefits makes medical grade silicone an essential material in the healthcare industry, particularly for products that demand precision, longevity, and biocompatibility.
Types of Medical Grade Silicone for Molding
Medical grade silicone for molding can be divided into several types, each suited to specific applications in the healthcare industry. These types vary in their curing processes, flexibility, biocompatibility, and durability, allowing manufacturers to select the best option for each medical application. Here’s an overview of the primary types of medical grade silicone for molding and the advantages they offer in medical device manufacturing.
Room Temperature Vulcanizing (RTV) Silicone
Room Temperature Vulcanizing (RTV) silicone is a type of silicone that cures at room temperature, providing a convenient option for applications that don’t require high-temperature curing. RTV silicone is typically available as a two-part system (base and curing agent) that, when mixed, initiates a chemical reaction to form a durable, rubbery material.
- Properties: RTV silicone has excellent flexibility and good mechanical properties, making it ideal for molds that need to maintain precise shapes while also being soft and pliable. It’s resistant to high temperatures and many chemicals, ensuring it can perform well under demanding medical conditions.
- Applications: RTV silicone is commonly used in creating custom molds for medical components, such as prosthetics, dental impressions, and other applications that require a highly flexible material. Because it cures without the need for specialized equipment, it is often chosen for custom medical prototypes and smaller production runs.
- Advantages: The ease of use and flexibility of RTV silicone make it a popular choice for medical injection molding applications. It also has good biocompatibility, although it’s typically used for external devices or short-term applications rather than long-term implants. The room-temperature curing process makes it especially useful in applications where high-temperature curing would be impractical or could damage other components.
Liquid Silicone Rubber (LSR)
Liquid Silicone Rubber (LSR) is one of the most versatile and widely used forms of medical grade silicone for molding. LSR is a two-part platinum-cured elastomer that, when mixed and injected into molds, cures to form a flexible, durable material that is ideal for complex and high precision medical components.
- High Flexibility and Precision Molding Capabilities: LSR is known for its exceptional flexibility and its ability to be molded into intricate shapes with tight tolerances. This precision makes it suitable for small, detailed components that require accurate reproduction, such as seals, gaskets, and connectors in medical devices.
- Biocompatibility: LSR is highly biocompatible, making it safe for direct contact with human tissues. It is also hypoallergenic and resists bacterial growth, which is essential for medical applications that need to ensure patient safety.
- Applications: LSR is frequently used in the production of medical devices that require consistent performance and durability, including respiratory masks, catheter components, and other devices in continuous contact with skin or mucous membranes.
- Advantages: The liquid medical injection molding process for LSR allows for high production speeds and minimizes material waste. Its ability to withstand repeated sterilization and its resistance to extreme temperatures and chemicals make it ideal for high-demand medical environments.
Platinum-Cured Silicone
Platinum-cured silicone, also known as addition-cure silicone, is a type of medical grade silicone for molding that undergoes a curing process involving a platinum catalyst. This curing process results in a pure, high-quality silicone that offers superior durability, making it highly suitable for sensitive medical applications.
- Enhanced Purity and Safety: Platinum-cured silicone is free from the byproducts associated with other curing methods, such as tin-cured silicone, which can release harmful residues. This purity is especially critical in medical applications where direct contact with body tissues or fluids is involved.
- Benefits in Medical Applications: Platinum-cured silicone is extremely biocompatible and is suitable for long-term implants, including pacemakers, breast implants, and other devices that must remain in the body for extended periods. It is also resistant to breakdown from body fluids and chemical exposure, ensuring that it retains its properties over time.
- Applications: This type of silicone is commonly used in devices that require a high degree of purity and stability, including implants, drug delivery systems, and sensitive diagnostic equipment.
- Advantages: Platinum-cured silicone’s high purity, stability, and hypoallergenic properties make it the preferred choice for critical medical applications. It also offers excellent durability under repeated sterilization, making it suitable for devices that must be used multiple times or remain in the body for long durations.
Each type of medical grade silicone for molding provides unique benefits, allowing manufacturers to select the best material based on the specific requirements of the medical device. Room Temperature Vulcanizing (RTV) silicone, Liquid Silicone Rubber (LSR), and platinum-cured silicone each bring distinctive advantages in terms of flexibility, precision, durability, and safety, ensuring that they meet the diverse needs of modern medical technology.
Where to Buy Medical Grade Silicone for Molding
Purchasing medical grade silicone for molding requires careful consideration of supplier quality, certifications, and product reliability. Given the strict requirements for medical devices, it is essential to source medical silicone from reputable suppliers to ensure that the materials meet all necessary regulatory standards. Below are recommended sources and essential tips to guide you through purchasing medical grade silicone for molding.
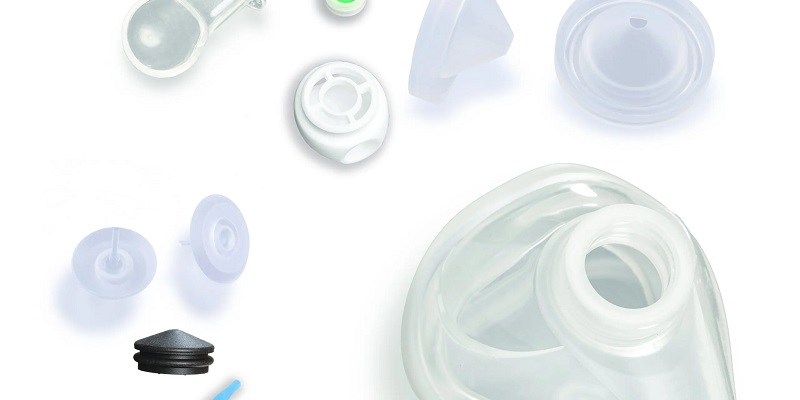
Recommended Suppliers and Sources for Medical Grade Silicone
There are several well-established suppliers and online platforms where you can purchase medical grade silicone for molding. These suppliers typically offer a range of medical silicone types, including Liquid Silicone Rubber (LSR), Room Temperature Vulcanizing (RTV) silicone, and platinum-cured silicone, each suited for various medical applications.
- Specialty Suppliers: Companies that specialize in silicone products, and provide high-quality medical grade silicone options. These suppliers are known for their rigorous quality controls and adherence to industry standards, offering LSR and RTV silicone in different formulations ideal for medical applications.
- Medical-Grade Material Distributors: Distributors like FUJIU Medical Injection Mold supply medical-grade materials tailored for healthcare applications. Our companies focus on biocompatible products and can provide extensive documentation and support for regulatory compliance, making reliable choices for purchasing medical silicone.
- Online Platforms: Online platforms may offer a selection of medical grade silicone for molding. While these platforms provide convenience, it is important to carefully review the specifications, certifications, and seller ratings to ensure that the silicone meets medical-grade standards.
When purchasing from any supplier, prioritize companies that provide thorough product information, safety certifications, and technical support to assist with regulatory requirements.
Medical Silicone Molding Company
For those looking to purchase molded products or partner with a company that provides medical molding services, working with a medical silicone injection molding company can be advantageous. Medical molding companies are specialized in producing high-quality silicone components for healthcare applications and often have in-house expertise in material selection, regulatory compliance, and manufacturing standards.
- Top Medical Molding Companies: Companies like FUJIU Medical Injection Mold is widely recognized for their medical molding expertise. We offer end-to-end services, from designing and prototyping to full-scale production of silicone parts for medical devices. Our company use FDA-compliant materials and are well-versed in ISO standards, making them ideal partners for custom medical-grade silicone molding projects.
- Benefits of Working with Specialized Molding Companies: Our companies understand the unique requirements of the healthcare industry, such as biocompatibility, sterilization compatibility, and traceability. We also often provide post-molding services like assembly, packaging, and sterilization, ensuring that molded parts are ready for clinical use.
Tips for Selecting Trusted Sellers and Verifying Material Certifications
When buying medical grade silicone for molding, especially for applications that require high reliability, following these tips can help ensure that you are getting materials that meet the strictest quality standards:
- Check for Certifications: Always verify that the silicone meets ISO 10993 biocompatibility standards and, where relevant, is FDA-compliant. These certifications indicate that the silicone has passed extensive testing for safe use in medical applications.
- Request Documentation: Reputable suppliers provide detailed technical data sheets (TDS) and certificates of analysis (COA) to verify the material’s properties, including biocompatibility, temperature resistance, and durability. Be wary of suppliers who cannot provide such documentation, as these materials may not meet medical-grade standards.
- Evaluate Supplier Reputation: Research the supplier’s reputation within the medical industry. Look for suppliers or companies that are widely recognized and have established partnerships with medical device manufacturers. Customer reviews, case studies, and industry recognition are strong indicators of a supplier’s credibility.
- Ask About Traceability: For medical applications, traceability is key. A trustworthy supplier will have traceability protocols to track batches and provide information about the manufacturing process, which is crucial in case of recalls or material assessments.
Following these guidelines and choosing reliable sources can ensure that the medical grade silicone for molding you purchase meets the high demands of the healthcare industry. This approach not only promotes product quality but also aligns with regulatory requirements for safe and effective medical devices.
Best Medical Grade Silicone for Molding
Selecting the best medical grade silicone for molding depends on specific requirements like durability, flexibility, biocompatibility, and compatibility with particular molding processes. Below is a comparison of top-rated medical silicone products and brands, highlighting key factors to consider when choosing the most suitable silicone for medical applications.
Brand/Product | Cost | Durability | Flexibility | Compatibility with Molding Processes | Description |
---|---|---|---|---|---|
Dow Corning Silastic® LSR | Moderate to High | Excellent | High | Liquid Injection Molding (LIM) | Known for exceptional flexibility and durability, Silastic® LSR is widely used in devices that require precise detailing, such as catheters and respiratory devices. |
Wacker Elastosil® M4600 | High | Excellent | High | Liquid Injection Molding (LIM), Compression Molding | A premium LSR product, Elastosil® M4600 offers excellent biocompatibility and low compression set, making it suitable for long-term implants and applications with rigorous durability requirements. |
Momentive Silopren® LSR 7000 | Moderate | Very Good | High | Liquid Injection Molding (LIM) | Silopren® LSR 7000 is highly resistant to chemicals and bacteria, ideal for medical applications that need strong resistance to sterilization processes. Suitable for complex, high-precision parts. |
Shin-Etsu KE-2090 | Moderate | Good | Moderate | Room Temperature Vulcanizing (RTV), Compression Molding | KE-2090 provides reliable durability and is particularly suitable for medical prototypes or short-run production due to its ease of use at room temperature. |
NuSil MED-4850 | High | Exceptional | High | Liquid Injection Molding (LIM), Extrusion | MED-4850 offers unmatched purity and stability, often chosen for long-term implantable devices due to its platinum-cured composition, which ensures high biocompatibility and durability. |
Key Factors to Consider When Selecting Medical Grade Silicone for Molding
When selecting the best medical grade silicone for molding, several critical factors come into play:
- Cost: Medical grade silicone varies significantly in price based on brand, composition, and curing process. Higher costs often reflect enhanced purity, durability, and compliance with stringent medical standards, making these materials better suited for long-term implants or devices requiring frequent sterilization.
- Durability: For medical applications that involve long-term use or repeated sterilization, durability is essential. Brands like Dow Corning and NuSil are renowned for high-durability silicones, often selected for implantable devices and reusable components.
- Flexibility: Silicone’s flexibility is crucial for applications where the material must conform to specific shapes or allow for patient movement. Liquid Silicone Rubber (LSR) products, such as Silopren® LSR 7000 and Elastosil® M4600, provide high flexibility, making them ideal for tubing, seals, and other components in continuous contact with skin or tissue.
- Compatibility with Molding Processes: Not all medical grade silicones are suitable for every molding process. LSR is often used in Liquid Injection Molding (LIM) for high-volume production of intricate parts, while RTV silicone is preferred for small-scale or prototype production due to its room-temperature curing capabilities. Knowing the ideal process compatibility ensures efficient production and optimal material performance.
This table serves as a guide to selecting the best medical grade silicone for molding, helping manufacturers choose the most appropriate silicone to meet the unique demands of the healthcare industry.
Medical Grade Silicone for Molding Cost Factors
Understanding the cost factors associated with medical grade silicone for molding is essential for manufacturers in the healthcare industry, where budgets must balance both quality and regulatory compliance. The price of medical grade silicone for molding is influenced by several elements, including the type of silicone, curing process, order quantity, and specific manufacturing requirements. Below, we examine these factors in detail to provide insights into managing costs effectively when sourcing medical grade silicone.
Overview of Cost Considerations
The cost of medical grade silicone for molding is primarily determined by three main factors:
- Material Type: Different types of medical grade silicone—such as Liquid Silicone Rubber (LSR), Room Temperature Vulcanizing (RTV) silicone, and platinum-cured silicone—have varying price points. LSR, for example, is often preferred for high-precision, high-volume applications and tends to be more expensive due to its exceptional properties like flexibility, durability, and biocompatibility. Platinum-cured silicone, known for its purity and safety in long-term medical use, also comes at a premium cost, particularly for applications requiring implant-grade silicone. RTV silicone, while generally more affordable, may be limited to certain applications, often in prototyping or short-run production due to its room-temperature curing process.
- Curing Process: The curing process directly affects both production costs and time. Platinum curing, common for LSR and high-grade silicones, is an expensive process due to the materials involved and the superior quality it delivers, ensuring minimal impurities and enhanced biocompatibility. Tin-cured silicones, while more affordable, are generally not suitable for medical applications due to potential safety concerns. Medical manufacturers often rely on platinum-cured silicone, particularly for applications where material purity and patient safety are paramount. The curing process may also affect the level of specialized equipment and energy required, influencing overall costs.
- Quantity: Order quantity plays a significant role in cost management. Larger orders typically lower the per-unit cost due to economies of scale. This is especially true for high-volume production in the medical field, where consistent and large-scale demand justifies bulk orders. Conversely, smaller orders, such as for prototyping or initial testing, may have a higher per-unit cost due to setup fees, minimum order requirements, and the absence of bulk pricing discounts. Manufacturers often negotiate bulk pricing with suppliers to optimize costs in long-term production.
Insights on Pricing for Small vs. Bulk Orders
Understanding the differences in pricing for small and bulk orders is crucial when planning production budgets for injection molding medical devices.
- Small Orders: Small-volume orders are common for prototypes, product testing, and limited production runs. However, these orders generally come with a higher price per unit due to initial setup costs and the lack of volume discounts. Custom formulations or specialty grades of medical grade silicone for molding can further increase the per-unit cost in small orders. Additionally, suppliers may impose minimum order quantities (MOQ), so smaller projects might require careful budgeting to account for these minimums.
- Bulk Orders: For high-demand medical applications, such as disposable medical devices, bulk ordering significantly reduces the cost per unit. Bulk orders benefit from reduced material costs, labor efficiencies, and streamlined production processes. Suppliers often offer discounted rates on larger quantities, making bulk orders more economical for long-term production. For example, when manufacturing thousands of units of medical-grade tubing or seals, the cost savings from bulk orders can be substantial, benefiting both the manufacturer and the end customer by reducing overall production expenses.
Additional Factors Influencing Overall Costs
Aside from material type, curing process, and order quantity, several additional factors impact the overall cost of medical grade silicone for molding:
- Custom Formulations: Some medical applications may require silicone with specific properties, such as increased resistance to chemicals or enhanced flexibility. Custom formulations add to material costs due to additional processing, testing, and certification requirements.
- Compliance and Certifications: Medical-grade silicone products must meet stringent standards, such as ISO 10993 for biocompatibility and FDA requirements. Ensuring compliance with these standards adds costs related to testing, documentation, and quality assurance.
- Shipping and Logistics: For manufacturers relying on global suppliers, shipping and logistics can significantly impact costs, especially for bulk orders that require specialized storage or handling due to the sensitive nature of medical grade silicone.
So, the cost factors associated with medical grade silicone for molding are multifaceted and require careful planning to manage effectively. By understanding material types, curing processes, order quantities, and other influencing factors, manufacturers can make informed decisions that balance cost efficiency with the high-quality standards required in the medical industry.
Applications of Medical Grade Silicone for Molding
Medical grade silicone for molding has transformed healthcare manufacturing due to its versatility, durability, and biocompatibility. Its applications span a broad range of medical devices and equipment, from surgical instruments to wound care products, where silicone’s unique properties meet strict health and safety requirements. Below, we explore various applications where medical grade silicone for molding is essential.
Medical Device Silicone Molding
Silicone rubber molding is one of the most critical uses of medical grade silicone in healthcare, serving a wide range of medical devices that require precision, durability, and patient safety. Medical silicone rubber is particularly suited to molding applications that demand detailed customization and tolerance to extreme sterilization processes, which are common in medical settings.
- Surgical Instruments: Many surgical instruments, especially those requiring soft yet durable grips, are manufactured using silicone rubber molding. The silicone provides a non-slip, ergonomic grip that helps surgeons maintain control, even during lengthy procedures. Silicone’s resistance to high temperatures also allows these instruments to be sterilized repeatedly without degradation, making it a valuable material in operating rooms.
- Catheters and Tubing: Catheters and tubing are common applications for medical silicone rubber due to silicone’s biocompatibility and flexibility. Molding silicone into these shapes creates smooth, comfortable devices that can remain in the body for extended periods, such as urinary catheters or intravenous lines. Medical grade silicone for molding catheters is ideal because it resists bacterial growth, maintains flexibility, and can withstand continuous contact with bodily fluids.
- Respiratory Masks and Seals: Silicone molding is essential for producing respiratory masks and sealing components used in ventilators and other respiratory aids. These products benefit from the hypoallergenic properties of medical silicone, ensuring that they remain comfortable against the skin while forming a tight seal to optimize respiratory support. The durability of medical silicone also allows these products to endure multiple sterilization cycles.
Specialized Uses for Medical Silicone in Sensitive Equipment, Wound Care Products, and Patient Support Devices
Medical silicone’s non-allergenic, moisture-resistant, and durable properties make it ideal for applications in sensitive equipment and patient-care products, where patient safety and comfort are paramount.
- Sensitive Diagnostic Equipment: Medical grade silicone is frequently used in diagnostic equipment, such as ultrasound probes and sensors, which require safe materials that interact with sensitive bodily tissues. Molding provides a seamless finish and smooth surface that minimizes irritation, ensuring patient comfort during diagnostic procedures.
- Wound Care Products: Wound care dressings and bandages often incorporate silicone to prevent adhesion to the wound, which aids in pain-free dressing changes and faster healing. Medical silicone is flexible, breathable, and forms a gentle, non-stick barrier that helps maintain a sterile environment over the wound area. This application demonstrates how silicone can significantly improve patient care in wound management.
- Patient Support Devices: Silicone molding is also crucial in the creation of patient support devices, such as prosthetics and orthopedic implants. Medical silicone’s flexibility and adaptability allow it to conform to body contours, providing comfort and support where it’s needed most. Prosthetic liners, for instance, use molded silicone to cushion the contact points between the prosthetic and the patient’s skin, preventing chafing and enhancing long-term wearability.
Medical Custom Silicone Molding
Medical custom silicone molding caters to the specific needs of healthcare providers by offering personalized medical molding solutions for unique applications. Custom molding is particularly beneficial in producing components and devices that require precise dimensions and unique designs.
- Custom Prosthetics and Orthotics: Custom silicone molding is used in developing prosthetics and orthotic devices tailored to individual patients. Medical grade silicone for molding allows for high customization, ensuring a perfect fit and improved comfort for users. These custom products can be adjusted to meet specific needs, such as varying thicknesses or flexibility levels for different activities.
- Implantable Devices: Many implantable devices, like pacemaker components and cochlear implants, require custom molding to achieve specific shapes and dimensions that suit patient anatomy. Medical custom silicone molding ensures that the silicone meets biocompatibility and durability requirements necessary for safe, long-term implantation within the human body.
Silicone Bonding Medical Grade Molding
Silicone bonding medical grade molding is essential in creating multi-material devices or securely joining silicone with other components within a medical device. This process expands the potential applications of medical grade silicone by integrating it with other materials without compromising safety or quality.
- Multi-Material Medical Devices: Many advanced medical devices, such as surgical tools and diagnostic equipment, use silicone bonded to metals, plastics, or other materials. Silicone bonding medical grade molding allows silicone to adhere strongly to these materials, combining silicone’s flexibility and biocompatibility with the structural support of other materials. This is crucial for devices that require both rigidity and a comfortable, biocompatible surface.
- Seals and Gaskets in Equipment: Silicone bonding is often used to create seals and gaskets in medical equipment, where silicone must be securely attached to other surfaces. This ensures that the equipment is leak-proof and able to handle various fluids or gasses, as seen in devices like oxygen masks and blood collection systems. The bonding process guarantees a stable connection, preserving the device’s integrity during usage.
Medical grade silicone for molding is an invaluable resource in healthcare, offering unparalleled versatility across a wide array of applications. From custom-fit prosthetics and non-invasive diagnostic tools to durable surgical instruments, medical silicone molding continues to advance patient care and device innovation in the medical industry.
Differences: Silicone, Medical Grade Silicone for Molding, and Food Grade Silicone
Silicone is a versatile polymer widely used across industries due to its flexibility, durability, and resistance to extreme temperatures. Within this category, medical grade silicone and food grade silicone stand out as specialized variants with unique properties tailored to specific applications. While all types of silicone share a similar base composition, their distinctions lie in purity, safety standards, and functional applications.
To help you better understand these materials, this section provides a detailed comparison of standard silicone, medical grade silicone (specifically for molding), and food grade silicone. The comparison is organized across several key factors: composition, safety standards, applications, and regulatory compliance.
Key Differences Between Silicone, Medical Grade Silicone for Molding, and Food Grade Silicone
Aspect | Standard Silicone | Medical Grade Silicone for Molding | Food Grade Silicone |
---|---|---|---|
Composition | General silicone without stringent purification processes. | High-purity silicone, specially treated to meet medical standards. | Purified silicone to meet food safety standards. |
Safety Standards | Not subjected to rigorous safety or health testing. | Compliant with ISO 10993, USP Class VI, and FDA regulations. | Meets FDA and LFGB standards for food safety. |
Applications | Industrial uses (seals, gaskets, adhesives). | Medical devices, implants, and molding for surgical tools. | Kitchenware, baking molds, and food storage products. |
Temperature Resistance | Moderate resistance to temperature extremes. | Excellent resistance to sterilization processes and high temperatures. | High resistance to cooking and freezing temperatures. |
Toxicity and Biocompatibility | May contain fillers or additives unsuitable for sensitive uses. | Non-toxic and biocompatible, suitable for internal and external medical use. | Non-toxic but not suitable for direct implantation. |
Regulatory Compliance | Minimal regulation for general use. | Strict adherence to medical and regulatory standards. | Complies with food contact safety regulations. |
Durability | Standard durability for industrial wear and tear. | Extremely durable, resistant to sterilization chemicals. | Durable enough for repeated exposure to cooking and cleaning. |
Detailed Insights
Composition
- Standard silicone is produced for general industrial purposes without stringent purity controls.
- Medical grade silicone undergoes extensive processing to eliminate impurities, ensuring its safety for medical applications such as implants and surgical tools.
- Food grade silicone is purified to meet food contact safety requirements, though it lacks the precision purity of medical grade.
Safety Standards
- Medical grade silicone adheres to rigorous international standards like ISO 10993 and USP Class VI to ensure biocompatibility and non-toxicity for human use.
- Food grade silicone meets FDA and LFGB requirements, ensuring it is safe for cooking and storage but unsuitable for medical procedures.
Applications
- While standard silicone is commonly used in industrial products like gaskets or adhesives, food grade silicone is seen in kitchen tools. Medical grade silicone dominates in healthcare environments, particularly for precise molding applications where safety is critical.
Temperature and Chemical Resistance
- Medical grade silicone stands out for its exceptional resistance to sterilization and harsh chemicals, making it indispensable in medical molding processes.
This structured comparison highlights why medical grade silicone for molding is essential for healthcare applications, as its unparalleled safety and durability set it apart from other types of silicone.
Can Medical Grade Silicone for Molding Be Made Using 3D Printing?
Yes, medical grade silicone molds can be made using 3D printing, but the process requires specific techniques and considerations to ensure that the final product meets medical standards. The integration of 3D printing with medical grade silicone molding has advanced significantly, allowing for greater customization and precision in producing medical devices and tools.
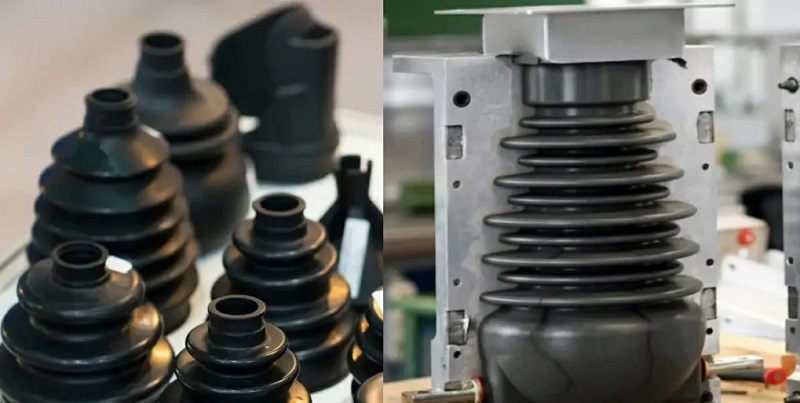
Here is a detailed exploration of the process:
hallenges of 3D Printing Medical Grade Silicone
Medical grade silicone is a viscous material that does not naturally lend itself to conventional 3D printing methods like fused deposition modeling (FDM) or selective laser sintering (SLS). The following challenges must be addressed:
- Material Flow: Silicone’s high viscosity makes it difficult to extrude through standard nozzles.
- Curing Process: Silicone requires curing, often using heat or UV light, which needs to be integrated into the printing process.
- Surface Finish: Achieving a smooth surface, critical for medical applications, can be challenging with layer-by-layer printing.
Technologies Used for 3D Printing Silicone
To overcome these challenges, specialized 3D printing techniques have been developed:
- Direct Ink Writing (DIW): This method extrudes silicone in a controlled manner, allowing for precise deposition of material.
- Liquid Additive Manufacturing (LAM): LAM combines the extrusion of liquid silicone rubber (LSR) with an integrated curing system, making it suitable for creating medical grade molds.
- Vat Polymerization: Some printers use UV-curable silicone resins in a vat polymerization process to build detailed molds.
Steps to Create Medical Grade Silicone Molds via 3D Printing
- Design and Prototyping: CAD software is used to design the mold with exact dimensions.
- Material Selection: Medical grade silicone or compatible materials with ISO 10993 or USP Class VI certifications are chosen.
- Printing Process: Advanced 3D printers equipped for silicone printing are used to create the mold.
- Post-Processing: The mold undergoes curing, polishing, and quality checks to ensure biocompatibility and compliance with medical standards.
Applications of 3D-Printed Medical Grade Silicone Molds
- Custom Medical Devices: 3D printing allows for patient-specific molds to create prosthetics, implants, or surgical tools.
- Rapid Prototyping: Medical manufacturers can quickly prototype and test designs for silicone-based products.
- Complex Geometries: Intricate designs, such as microfluidic channels or advanced surgical molds, can be achieved with 3D printing.
Benefits of Using 3D Printing for Medical Grade Silicone Molding
- Customization: Enables highly tailored designs for individual patient needs.
- Speed: Reduces production time compared to traditional molding methods.
- Cost-Effectiveness: Ideal for small batch production or iterative prototyping.
While 3D printing medical grade silicone molds is feasible, it remains a specialized process requiring advanced equipment and expertise. As technology progresses, the integration of 3D printing and silicone molding is expected to expand further, offering new opportunities in healthcare innovation.
What Kind of Machine Is Needed to Produce Medical Grade Silicone for Molding?
Producing medical grade silicone for molding requires highly specialized equipment designed to handle the material’s unique properties, ensure high purity, and comply with stringent medical standards. These machines must facilitate precision, control, and hygiene throughout the production process. Here is a detailed look at the types of machines typically used:
Liquid Silicone Rubber (LSR) Injection Molding Machines
LSR injection molding machines are the most common equipment for producing medical grade silicone molds. These machines are specifically designed to process Liquid Silicone Rubber, which is a preferred form of medical grade silicone due to its purity and flexibility. Key features include:
- Closed-Loop Systems: Ensures minimal contamination and maintains medical-grade cleanliness.
- Precise Temperature Control: Maintains the exact temperature required for silicone curing.
- Advanced Injection Units: Facilitates consistent and precise material injection for intricate mold designs.
- Servo-Controlled Hydraulics or Electric Drives: Provides accurate control over pressure and speed, essential for molding complex medical parts.
Compression Molding Machines
For some medical applications, compression molding machines may be used. These machines work by compressing silicone under high pressure and heat within a mold cavity. Features include:
- Uniform Pressure Application: Essential for achieving smooth surfaces on medical products.
- Hygienic Design: Equipped with easy-to-clean surfaces and components to maintain medical compliance.
Extrusion Machines
Medical grade silicone products such as tubes, catheters, and seals are often produced using extrusion machines. These machines process silicone into continuous profiles with high precision. Features include:
- Extrusion Heads with Fine Tolerance: Ensures consistent diameter and wall thickness for medical tubing.
- Curing Ovens: Integrated ovens cure the extruded silicone to meet required specifications.
- Cleanroom Compatibility: Designed to operate in cleanroom environments to prevent contamination.
Mixing and Dispensing Machines
Medical grade silicone production often starts with the preparation of the silicone material. This involves machines capable of mixing silicone with curing agents or additives while ensuring a homogeneous blend.
- Static or Dynamic Mixers: Blend silicone components without introducing impurities.
- Automated Dispensing Systems: Delivers the mixed silicone directly to the molding or extrusion machine with precision.
CNC Milling Machines for Mold Fabrication
Before molding, precise medical silicone molds need to be fabricated. CNC milling machines are used to create these molds with the exact specifications required for medical-grade products. These machines offer:
- High Precision: Ensures the mold cavity aligns perfectly with design requirements.
- Versatility: Can handle complex geometries for intricate silicone parts.
Post-Processing and Inspection Equipment
After molding, medical grade silicone products often undergo post-processing and quality inspection. Necessary equipment includes:
- UV or Heat Curing Units: Completes the curing process for consistent material properties.
- Laser Cutters: Refines edges or adds features to molded products.
- Inspection Machines: Includes X-ray scanners, vision systems, and biocompatibility testers to ensure regulatory compliance.
Cleanroom Requirements
Regardless of the machine type, production of medical grade silicone for molding typically occurs in cleanroom environments. These spaces ensure:
- Strict control of air quality to prevent contamination.
- Compliance with ISO 14644 standards, essential for medical device manufacturing.
Summary of Essential Machines
- LSR Injection Molding Machines
- Compression Molding Machines
- Extrusion Machines
- Mixing and Dispensing Machines
- CNC Milling Machines for Mold Fabrication
- Post-Processing and Inspection Equipment
The selection of machines depends on the specific medical application, whether it involves molding, extrusion, or other processing methods. Advanced equipment, coupled with rigorous quality control, ensures that medical grade silicone meets the highest industry standards for safety and performance.
How to Check the Quality of Medical Grade Silicone for Molding?
Ensuring the quality of medical grade silicone for molding is essential for meeting stringent medical industry standards. This involves a comprehensive evaluation of the material’s physical, chemical, and biological properties to verify its suitability for medical applications. Below is a detailed guide on how to check the quality of medical grade silicone for molding:
Verify Compliance with Regulatory Standards
Medical grade silicone must adhere to specific standards that guarantee its safety and functionality for medical use. Key certifications to look for include:
- ISO 10993: Ensures biocompatibility, including cytotoxicity, sensitization, and irritation testing.
- USP Class VI Certification: Confirms the material’s safety for use in medical applications involving direct human contact.
- FDA Approval: Ensures the silicone is approved for use in medical devices within the United States.
Physical Property Testing
To confirm the performance characteristics required for molding, physical tests are conducted:
- Tensile Strength and Elongation: Assesses the material’s ability to withstand stress and deformation.
- Tear Resistance: Evaluates the silicone’s durability, especially for flexible and thin-walled products.
- Compression Set: Measures the material’s ability to return to its original shape after compression.
- Shore Hardness: Determines the silicone’s firmness, which is crucial for specific medical applications.
Chemical Purity and Stability Tests
Purity and stability are critical for ensuring the safety and longevity of medical grade silicone:
- Volatile Content Analysis: Identifies and measures volatile compounds that could pose risks.
- Chemical Resistance Testing: Confirms the material’s resilience against chemicals used in medical environments, such as disinfectants or sterilization agents.
- Thermal Stability: Ensures the silicone can withstand sterilization processes, including autoclaving or UV exposure.
Biocompatibility Testing
Biocompatibility is a cornerstone of medical grade silicone quality checks, involving:
- Cytotoxicity Testing: Evaluates whether the material has toxic effects on living cells.
- Sensitization Testing: Determines whether the material causes allergic reactions.
- Hemocompatibility Testing: Verifies that the silicone is safe for contact with blood, critical for implants or surgical tools.
Dimensional Accuracy and Surface Finish
For molding applications, precision and finish are vital:
- Dimensional Tolerance Testing: Ensures the material maintains tight tolerances during and after molding.
- Surface Smoothness Analysis: Confirms that the silicone’s surface is free from defects that could compromise functionality or safety.
Testing for Contamination
Medical grade silicone must be free from impurities and contaminants:
- Spectroscopy and Chromatography: Detects trace contaminants that may not be visible to the naked eye.
- Particle Analysis: Ensures the material is free of particulates that could compromise cleanliness or function.
Sterilization Compatibility
Since medical silicone often undergoes sterilization, its compatibility with various sterilization methods must be tested:
- Heat Sterilization Tests: Evaluates resistance to high-temperature autoclaving.
- Chemical Sterilization Tests: Confirms resistance to commonly used sterilants like ethylene oxide.
- Radiation Sterilization Tests: Assesses the material’s stability under gamma or electron beam sterilization.
Long-Term Durability Tests
Medical devices often need to function reliably over long periods, necessitating:
- Aging Tests: Simulates prolonged exposure to environmental factors like heat, humidity, and UV light.
- Fatigue Testing: Measures the silicone’s ability to endure repetitive stress.
Independent Laboratory Testing
For a comprehensive assessment, manufacturers often send samples to independent labs specializing in medical material testing. These labs provide detailed reports verifying compliance with all relevant standards.
Quality Assurance Checklist for Medical Grade Silicone for Molding
- Compliance with ISO 10993, USP Class VI, and FDA regulations.
- Physical property testing (tensile strength, tear resistance, etc.).
- Chemical purity and stability verification.
- Biocompatibility testing for safety.
- Dimensional accuracy and smooth surface finish.
- Contamination-free certification.
- Compatibility with various sterilization methods.
- Long-term durability and aging resistance.
Ensuring the quality of medical grade silicone for molding is a rigorous process. Only through thorough testing and certification can manufacturers guarantee that the material meets the safety, performance, and reliability requirements of medical applications.
FAQ about Medical Grade Silicone for Molding
Silicone and medical-grade silicone differ significantly in purity, biocompatibility, and safety standards. Regular or industrial silicone is commonly used in applications like kitchenware, automotive parts, and electronics due to its flexibility and durability. However, it is not designed to meet stringent health and safety standards. Industrial silicone may contain additives or byproducts that could be unsafe in prolonged contact with human tissue.
Medical-grade silicone, on the other hand, is specifically formulated to meet high safety and purity requirements, making it suitable for medical and healthcare applications. This type of silicone undergoes extensive testing and complies with regulatory standards like ISO 10993 and FDA requirements to ensure it’s safe for use in direct contact with human tissue. Medical-grade silicone is typically platinum-cured, which reduces impurities and makes it hypoallergenic and biocompatible. This type is preferred in medical devices, implants, and other sensitive applications that require safe, non-toxic materials.
For molds, especially those used in medical applications, Liquid Silicone Rubber (LSR) and Room Temperature Vulcanizing (RTV) silicone are the most common types. LSR is a platinum-cured silicone that’s favored for its high flexibility, durability, and precision molding capabilities. It’s typically used in injection molding and offers tight tolerance control, making it suitable for producing intricate medical device parts, prosthetics, and components requiring fine detail. LSR is also biocompatible, meaning it’s safe for applications involving contact with human skin or tissue.
RTV silicone, on the other hand, cures at room temperature, making it ideal for molds that don’t require high-temperature equipment. RTV is commonly used in prototyping and smaller production runs due to its ease of handling and versatility. However, RTV is generally used for external or short-term medical applications rather than implants. Both LSR and RTV silicones are flexible, resistant to chemicals, and provide excellent detail reproduction, making them ideal choices for medical-grade silicone molding applications.
Yes, medical-grade silicone is considered safe for use inside the body, particularly for applications requiring long-term implantation. This type of silicone undergoes rigorous testing and must meet strict regulatory standards for biocompatibility, such as ISO 10993 and FDA approvals, which evaluate its compatibility with human tissue and its safety for extended use. Medical-grade silicone is platinum-cured, which reduces impurities and makes it hypoallergenic and highly resistant to bacterial growth, a crucial factor for implants and internal medical devices.
Medical-grade silicone is commonly used in applications like pacemaker leads, cochlear implants, catheters, and prosthetic implants. Its durability and resistance to degradation ensure that it can remain stable and functional inside the body without breaking down. Additionally, medical-grade silicone has a low risk of causing allergic reactions or inflammatory responses, making it ideal for implants and devices intended for continuous contact with bodily fluids and tissues.
Body-safe silicone refers to silicone that has been tested and proven non-toxic, hypoallergenic, and biocompatible for use in contact with human skin or within the body. Medical-grade silicone is the most reliable type of body-safe silicone, as it undergoes extensive testing and meets strict health and safety standards like ISO 10993 and FDA compliance. This testing ensures that the silicone is free from harmful additives or byproducts that could cause irritation, allergic reactions, or toxicity.
In addition to medical-grade silicone, platinum-cured silicone is generally considered body-safe as well. The platinum curing process eliminates impurities that could potentially harm the body, making it suitable for applications in wearable medical devices, implants, and personal care products. Silicone that’s labeled as food-grade is also safe for short-term skin contact but may not meet the rigorous standards needed for medical or long-term applications. When choosing silicone for body-safe uses, it’s essential to verify that it meets appropriate certifications for biocompatibility and safety.
Medical-grade silicone is a highly purified form of silicone that meets stringent biocompatibility and safety standards set by regulatory bodies like the FDA. This silicone is typically used in medical devices and implants, where long-term exposure to human tissues and fluids is expected. It is characterized by its high level of purity, biocompatibility, and resistance to bacteria and degradation. Medical-grade silicone can be in several forms, such as elastomers, gels, or liquids, and is sterilizable through methods like autoclaving, gamma irradiation, or ethylene oxide treatment. Common examples include Dow Corning’s QP1 products and NuSil’s MED-4000 series, which are designed to meet the rigorous demands of medical applications.
For molding applications, high-consistency rubber (HCR) and liquid silicone rubber (LSR) are commonly used types of silicone. Both offer excellent flexibility, durability, and heat resistance, making them suitable for detailed and intricate molds. LSR is often favored for its ability to be easily injected into intricate mold cavities, ensuring high precision and efficiency in production. It is widely used in applications requiring complex geometries, such as medical devices, consumer products, and industrial components. HCR, on the other hand, is typically used for compression molding and extrusions. Medical-grade silicones used for molding are specifically formulated to offer biocompatibility, making them suitable for producing medical devices and components like catheters, syringe stoppers, and gaskets.
Medical-grade silicone is generally considered superior to food-grade silicone in terms of purity, biocompatibility, and overall safety. While both types of silicone are non-toxic and safe for contact with the body, medical-grade silicone undergoes more extensive testing and adheres to stricter regulatory standards. This ensures that it does not cause adverse reactions when used in long-term or implantable medical devices. Food-grade silicone, while safe for cooking and food storage applications, does not necessarily meet the same rigorous biocompatibility standards and may not be suitable for internal body applications. Therefore, while both types are safe for their intended uses, medical-grade silicone offers a higher assurance of safety and performance in medical applications.
Contact our professional team now for a same-day quote and risk-free project evaluation. Benefit from ISO 8 cleanrooms, advanced machines, and 12-hour fast response in medical injection molding.