Injection molding has revolutionized the medical industry by enabling the production of precise, high-quality components essential for modern healthcare. This manufacturing process, including precision mold medical applications, is widely used to create a variety of medical devices and equipment, such as surgical instruments, implants, and diagnostic tools. The precision and consistency of medical injection molding ensure that each product meets stringent regulatory and safety standards. Medical injection molding companies play a vital role in advancing healthcare by offering innovative solutions and ensuring the reliable production of complex medical-grade parts. Their expertise in material selection, process optimization, and quality control drives the creation of components critical to patient safety and medical innovation. This technology continues to shape the future of healthcare through its unmatched precision and efficiency. Medical injection molding applications create precise, high-quality components for devices in surgery, diagnostics, drug delivery, and patient monitoring.
What Are Medical Injection Molding?
Medical injection molding is a specialized manufacturing process that creates high-precision, medical-grade components. The medical injection molding process is widely recognized for its ability to produce complex, sterile, and reliable parts that meet the demands of the healthcare industry. Below, we explore the process and its benefits.
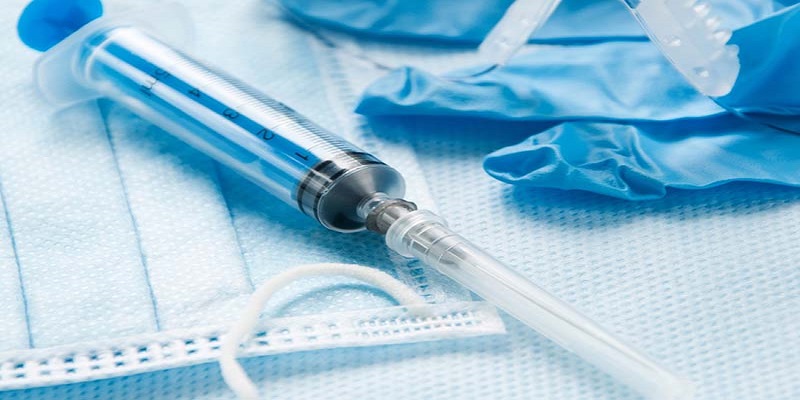
What is the Medical Injection Molding Process
The medical injection molding process involves several precise steps to produce high-quality medical components. Each phase of the process is carefully controlled to ensure that the final products meet the strict requirements for medical devices. This includes using medical-grade thermoplastics, injecting them into molds, and cooling the parts to achieve the desired shape and features. Below, we break down each step of the process to explain how it works and why it’s essential in the medical device industry.
Melting Medical-Grade Plastics
- The process begins with medical-grade thermoplastics, which are heated until they reach a molten state.
- Common materials include polycarbonate, polypropylene, and medical-grade polyethylene.
Injecting into Molds
- The molten material is injected into precision-engineered molds designed to create intricate shapes and features.
- Advanced equipment ensures uniform distribution for consistent part quality, in line with medical mold design standards.
Cooling and Ejecting Finished Parts
- After filling the mold, the material cools and solidifies to form the desired component.
- The finished part is then ejected with minimal waste, maintaining efficiency.
Key Benefits of Medical Injection Molding Applications
Medical injection molding offers several key benefits, making it a preferred manufacturing method for medical device production. The process ensures that components are sterile and free from contaminants, which is essential in medical applications where safety is a top priority. Additionally, metal injection molding medical is highly cost-effective for high-volume production, helping to reduce the cost per unit of each part. Precision and consistency are critical advantages of this process, as the parts produced must meet exacting standards for performance and quality, particularly in life-critical medical applications.
- Sterile and Contaminant-Free Production
- This process operates in controlled environments to ensure compliance with strict medical standards.
- Cost-Effective for High Volumes
- High production efficiency reduces costs per unit, making it ideal for mass production of medical devices.
- Precision and Consistency
- Delivers unparalleled accuracy, essential for components used in critical medical applications.
Common Medical Injection Molding Applications
Medical injection molding applications are essential for creating a wide range of medical devices and components with high precision and sterility. Below is a detailed overview of the common products manufactured using this process and the key aspects that ensure their quality.
Examples of Medical Products Produced Through Injection Molding
Diagnostic Tools
- Petri dishes, test tubes, and specimen containers are molded with exact dimensions for accurate laboratory work.
- Microfluidic devices for advanced diagnostics rely on intricate mold designs to handle minute fluid volumes.
Surgical Equipment
- Instruments such as scalpel handles, clamps, and retractors are made to strict tolerances for reliable use in surgery.
- Orthopedic components, including joint spacers and implant guides, benefit from the process’s biocompatible materials.
Drug Delivery Devices
- Syringes and insulin pens are produced to ensure precise medication dosing.
- Catheters and blood bags are molded from medical-grade materials to maintain sterility during use.
Personal Protective Equipment (PPE)
- Masks, face shields, and respirators are created to meet the protective requirements of healthcare workers.
- Injection molding ensures consistent quality and availability for high-demand items.
Complex Medical Molding Applications in Healthcare
Complex medical molding applications enable the production of advanced, multi-component devices, including:
- Implantable Medical Devices
- Pacemaker housings, artificial joints, and surgical screws require biocompatible and durable designs.
- Integrated Diagnostic Equipment
- Multi-part casings for imaging devices, such as MRI and ultrasound, ensure performance and durability.
- Minimally Invasive Tools
- Specialized components for laparoscopic surgery depend on intricate mold designs and micro-level precision.
Key Considerations in Medical Injection Molding Applications
The production process of medical injection molding must adhere to stringent standards to ensure the creation of high-quality, sterile, and safe medical components. Given the critical role these parts play in healthcare, several key factors must be considered during production to maintain sterility, ensure compliance with regulations, and select the appropriate materials. Below, we explore the key aspects that manufacturers must pay attention to when producing medical components via injection molding, to ensure that the end products meet safety, reliability, and regulatory standards.
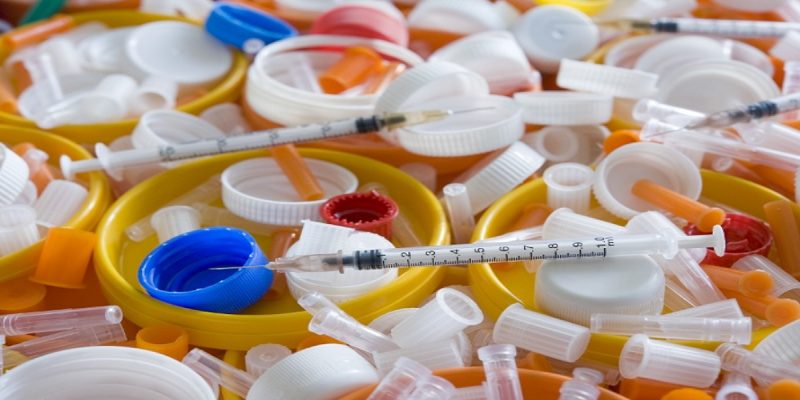
Sterile Environments for Production
In medical injection molding, it is crucial to maintain a sterile environment during the entire manufacturing process to prevent contamination. The production of medical devices and components often takes place in cleanrooms, which are controlled environments designed to minimize airborne particles, dust, and microbial contamination. Cleanrooms are classified based on the level of cleanliness required, with higher classifications necessary for devices that are in direct contact with patients or sensitive internal organs. The air filtration systems in cleanrooms are designed to maintain a sterile atmosphere and ensure that the medical parts produced through clean room injection molding meet stringent sterility requirements. Any contamination, no matter how small, could compromise the functionality or safety of the medical device, making this step a vital part of the medical injection molding process.
Adherence to Regulatory Compliance
Regulatory compliance is one of the most important considerations in the production of medical injection molded parts. Medical devices and components must adhere to a wide range of global standards, including those set by the FDA, ISO 13485, and other international bodies. The FDA sets forth regulations, such as 21 CFR Part 820, which governs good manufacturing practices (GMP) for medical devices in the U.S., ensuring that medical products are consistently produced and controlled to meet safety standards. ISO 13485, an internationally recognized standard, outlines the quality management systems required for manufacturing medical devices, including injection-molded parts. Compliance with these standards ensures that medical devices are manufactured under controlled conditions, thoroughly tested, and documented, with rigorous controls in place to guarantee their safety and efficacy for patient use.
Material Selection for Biocompatibility and Performance
The selection of materials is another critical factor in medical injection molding. Since medical components are often in direct contact with patients, the materials used must be biocompatible and meet stringent safety standards. Common materials for medical injection molding include medical-grade plastics like polycarbonate, polypropylene, and polyethylene, which are specifically chosen for their durability, strength, and ability to be sterilized. Biocompatibility testing, as outlined in standards like ISO 10993, is essential to ensure that the materials will not cause adverse reactions when exposed to bodily fluids or tissues. The chosen material must also meet performance requirements, such as resistance to chemical exposure, mechanical stresses, and sterilization methods, to ensure that the components perform as intended in medical applications.
Consistency and Precision in Production
Medical injection molding applications require extremely high levels of precision and consistency. Even the slightest variations in the production process can lead to defects, which could compromise the safety or effectiveness of the device. Injection molding allows for the mass production of highly intricate parts with tight tolerances, ensuring uniformity across all components. Advanced injection molding machines with precise controls are essential to achieving the desired quality and consistency. Maintaining precision in every step of the process, from the melting of materials to the cooling and ejection of the parts, ensures that the molded components meet exact specifications. This level of precision is crucial for medical applications where component failure can have serious consequences for patient health and treatment outcomes.
In medical injection molding applications, it is vital to pay careful attention to maintaining sterile environments, adhering to regulatory compliance, selecting the right materials, and ensuring precision throughout the production process. These factors collectively guarantee the safety, reliability, and performance of the medical devices and components that are critical to healthcare. By meeting these high standards, manufacturers can ensure that their products serve the needs of healthcare providers and patients while maintaining the highest level of quality and safety.
Benefits of Medical Injection Molding Applications
Medical injection molding applications are integral to the production of high-quality medical components, offering numerous benefits that meet the demanding needs of the healthcare industry. Below are the key advantages of this innovative manufacturing method.
Compliance with Standards
- FDA Regulations
- Ensures that all medical components are manufactured with materials and processes compliant with FDA standards for safety and performance.
- ISO Certifications
- Adherence to ISO 13485 and other global standards guarantees consistent quality and reliability in medical-grade plastics.
Traceability
- End-to-End Component Tracking
- Enables manufacturers to trace every stage of the production process, ensuring complete transparency and accountability.
- Enhanced Safety and Quality Assurance
- Tracking systems help identify and resolve any issues promptly, safeguarding patient safety.
Cost Efficiency
- Low Cost Per Unit
- Ideal for high-volume production, reducing manufacturing costs while maintaining consistent quality.
- Efficient Use of Materials
- Minimal material waste contributes to cost savings and environmental sustainability.
Material Versatility
- Wide Range of Medical-Grade Plastics
- Materials such as polypropylene, polycarbonate, and PEEK (Polyether Ether Ketone) can be used for various applications.
- Biocompatible and Durable Options
- Customizable materials meet specific requirements, such as flexibility, strength, or resistance to sterilization processes.
High Precision
- Tight Tolerances
- Achieves dimensional accuracy critical for applications like surgical instruments, diagnostic tools, and implantable devices.
- Complex Geometries
- Supports intricate designs, making it possible to produce components for advanced medical injection molding applications.
Medical injection molding applications provide unparalleled precision, cost-efficiency, and compliance, making them essential for the development of innovative and reliable medical devices.
Types of Medical Injection Molding Technologies for Medical Injection Molding Applications
Advancements in medical injection molding applications have led to the development of various specialized molding technologies tailored to meet the diverse needs of the healthcare industry. These technologies enable the production of high-quality medical components with precision and efficiency. Below are the key types of medical injection molding technologies:
Thin Wall Molding
- Lightweight Design
- Thin wall molding is used to create medical components that are lightweight yet strong, such as disposable syringes, diagnostic casings, and sample containers, through medical component molding.
- Durability and Precision
- This technique maintains structural integrity while reducing material usage, ensuring cost-effective production for high-volume applications.
- Applications in Medical Injection Molding
- Ideal for devices requiring minimal weight without compromising functionality, such as portable diagnostic equipment.
Insert Molding
- Overmolding for Enhanced Designs
- Insert molding integrates plastics with other materials, such as metals or ceramics, to improve ergonomic or functional properties.
- Improved Durability
- Provides a strong bond between materials, commonly used in surgical instruments, scalpel handles, and diagnostic tool components.
- Applications in Medical Injection Molding
- Perfect for devices that need a combination of material properties, such as strength and comfort in handheld instruments.
Liquid Silicone Injection Molding
- Flexibility for Soft Medical Products
- Medical silicone injection molding excels in producing soft, flexible items like tubing, seals, and catheters, essential for patient comfort.
- Biocompatibility
- Silicone’s biocompatible nature makes it a preferred material for implantable devices and components exposed to bodily fluids.
- Applications in Medical Injection Molding
- Commonly used for flexible connectors, stoppers, and other critical components requiring elasticity and sterilization compatibility.
Medical injection molding applications benefit significantly from these diverse technologies, which cater to various requirements, from lightweight designs to complex, multi-material products. These innovations continue to drive the evolution of healthcare devices, ensuring reliability, precision, and adaptability.
Importance of Medical Grade Plastics in Medical Injection Molding Applications
Medical injection molding relies heavily on medical grade plastics to ensure that the components produced meet stringent safety, performance, and regulatory standards. These plastics are specially formulated to provide the necessary physical, chemical, and biocompatibility properties required for use in medical devices. When selecting medical grade plastics, manufacturers must carefully consider various factors to ensure that the material will not only perform well in the intended medical application but also adhere to industry regulations. Below, we explore why medical grade plastics are chosen for medical injection molding, and what considerations must be made during material selection to ensure the highest quality and safety of medical products.
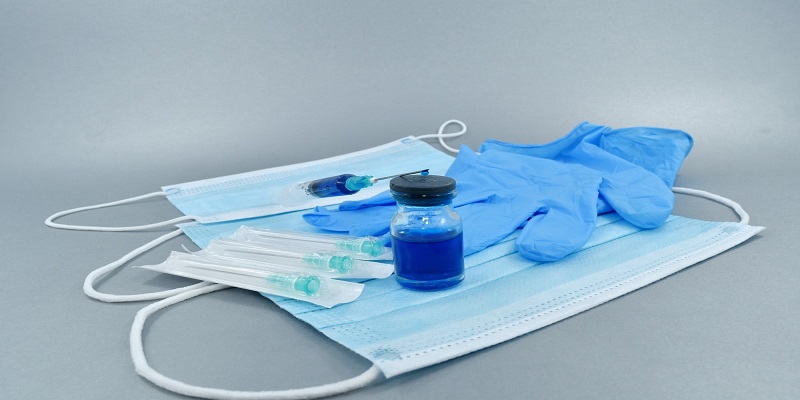
Why Medical Grade Plastics Are Chosen for Medical Injection Molding
Medical grade plastics are specifically designed to meet the demanding requirements of the healthcare industry, offering a combination of mechanical strength, durability, and biocompatibility. One of the primary reasons for using medical grade plastics in injection molding is their ability to be sterilized without losing their integrity. These materials are resistant to harsh cleaning agents, high temperatures, and other sterilization processes like autoclaving, which are essential in medical environments.
Additionally, medical grade plastics are chosen for their precise performance characteristics, such as resistance to chemicals, fatigue, and impact, making them ideal for components that must withstand repeated use in demanding medical environments. The materials used also must meet biocompatibility standards to ensure they do not cause any adverse reactions when in contact with the human body. Whether it’s for surgical tools, diagnostic devices, or drug delivery systems, medical grade plastics ensure that the final products are safe and reliable for patient care.
Factors to Consider When Choosing Medical Grade Plastics
When selecting medical grade plastics for injection molding, several important factors need to be taken into account to ensure that the material is suitable for the intended application. These include:
Biocompatibility and Safety
The most important consideration in choosing a medical grade plastic is biocompatibility, which ensures that the material will not cause any harmful reactions when exposed to human tissue or bodily fluids. The chosen plastic must meet biocompatibility standards such as ISO 10993 to ensure that it is safe for use in medical devices. Materials that are not biocompatible could lead to allergic reactions, toxicity, or other adverse effects, compromising patient health and the overall safety of the device.
Mechanical and Physical Properties
Another crucial factor in selecting medical grade plastics is the material’s mechanical properties, such as strength, flexibility, and resistance to impact or wear. Medical devices often face harsh environments and mechanical stresses, so the chosen plastic must be able to withstand these conditions without degrading. Materials such as polycarbonate, polypropylene, and medical-grade polyethylene are commonly used because of their excellent mechanical properties and high impact resistance.
Chemical Resistance and Durability
Medical components often need to be exposed to a wide range of chemicals, including cleaning agents, disinfectants, and sterilization agents. As such, medical grade plastics must exhibit excellent chemical resistance to prevent degradation over time. Plastics such as PEEK (polyetheretherketone) or PPSU (polyphenylsulfone) are highly resistant to chemicals and can withstand harsh sterilization methods, such as autoclaving. Durability is critical for medical devices that undergo frequent sterilization cycles or long-term use.
Regulatory Compliance and Certifications
Medical grade plastics must comply with a variety of industry standards, including FDA regulations, ISO 13485, and other specific regional or international medical device standards. The material must meet the regulatory requirements for medical use and be certified for safety and performance. This ensures that the plastics used in medical injection molding applications are suitable for creating components that meet legal requirements for medical device manufacturing.
The selection of medical grade plastics for injection molding applications is a highly detailed and crucial part of the manufacturing process. The right material must provide a balance of biocompatibility, mechanical properties, durability, and chemical resistance while adhering to regulatory standards. Manufacturers must take care to ensure that these materials will perform reliably in critical medical applications, ensuring both patient safety and long-term functionality of the medical devices. By carefully considering these factors, manufacturers can ensure that medical injection molding applications deliver high-quality, safe, and effective medical devices for healthcare providers and patients.
Medical Grade Plastics and Their Applications in Medical Injection Molding Applications
Medical injection molding applications rely on high-quality medical-grade plastics to produce durable, biocompatible, and functional components. Each material offers unique properties, making it suitable for specific medical uses. Below is an overview of common medical-grade plastics and their applications.
Polyethylene (PE)
- Wearable Medical Devices
- Frequently used in skin-contact devices due to its lightweight and hypoallergenic properties.
- Joint Prostheses
- High-density polyethylene (HDPE) is used in joint replacements for its strength and wear resistance.
- Applications in Medical Injection Molding
- Ideal for disposable components such as surgical drapes and packaging films.
Polypropylene (PP)
- Sterilized Syringes
- Resistant to heat and chemicals, allowing for repeated autoclave sterilization.
- Medical Containers
- Used for vials, specimen cups, and lab storage due to its durability and non-reactivity.
- Applications in Medical Injection Molding
- Suitable for high-volume production of sterile and lightweight components.
Polyetheretherketone (PEEK)
- Surgical Implants
- Known for its exceptional resistance to heat, chemicals, and mechanical stress, making it perfect for implantable devices.
- High-Performance Components
- Used in spine devices, dental implants, and endoscopic components.
- Applications in Medical Injection Molding
- Widely adopted for long-term use where durability and biocompatibility are critical.
Polycarbonate (PC)
- Protective Equipment
- Commonly used for face shields, goggles, and ventilator housings due to its impact resistance.
- Laboratory Tools
- Found in beakers, pipettes, and diagnostic device housings where clarity and toughness are essential.
- Applications in Medical Injection Molding
- Ensures precision and optical clarity for sensitive medical environments.
Silicone
- Catheters
- The flexibility and biocompatibility of silicone make it ideal for tubing and drainage devices.
- Soft Medical Components
- Often used in seals, stoppers, and components requiring elasticity.
- Applications in Medical Injection Molding
- Ideal for products requiring sterility and comfort, especially in patient-contact applications.
Medical injection molding applications leverage the distinct advantages of these plastics to produce high-quality, reliable components that meet the stringent demands of the healthcare industry. These materials ensure safety, durability, and efficiency in a variety of medical settings.
The Role of Medical Injection Molding Companies in Medical Injection Molding Applications
Medical injection molding companies play a critical role in the success of medical injection molding applications. They bring together advanced technologies, specialized expertise, and stringent compliance measures to deliver high-quality medical components. Below is an overview of their contributions.
Capabilities of Medical Injection Molding Companies
Engineering Expertise
- Utilize advanced engineering tools to design precision molds tailored to specific medical requirements, ensuring they meet the necessary standards for medical molding requirements.
- Ensure molds meet the tolerances necessary for critical applications like implants or diagnostic devices.
Prototyping and Testing
- Offer rapid prototyping services to validate designs and test functionality before full-scale production.
- Ensure prototypes align with medical standards and regulatory requirements.
High-Volume Production
- Employ state-of-the-art machinery to produce components in bulk while maintaining consistent quality.
- Support scalability for projects ranging from small batches to mass production.
Turnkey Solutions
- Comprehensive Services
- Provide end-to-end solutions, including design, material selection, mold fabrication, and delivery of finished products.
- Efficient Processes
- Streamline production timelines by integrating all stages of development within one facility.
- Applications in Medical Injection Molding
- Turnkey services support seamless creation of components for surgical tools, drug delivery systems, and protective equipment.
Traceability Systems
- Full Transparency
- Implement tracking systems that monitor every step of the production process, from raw material to final component.
- Compliance Assurance
- Enable detailed documentation to meet FDA, ISO, and other regulatory requirements.
- Applications in Medical Injection Molding
- Critical for ensuring quality and safety in devices such as catheters, implants, and diagnostic equipment.
Importance of Choosing a Reliable Partner
- Regulatory Knowledge
- A dependable company understands global medical standards and ensures compliance at every stage.
- Customization and Innovation
- Provides tailored solutions for unique medical injection molding applications, leveraging the latest technologies and materials.
- Long-Term Collaboration
- Offers consistent support, ensuring timely delivery and post-production services like sterilization and packaging.
The role of medical injection molding companies is pivotal in driving innovation and maintaining the integrity of medical injection molding applications. Their capabilities and commitment to excellence ensure the delivery of safe, reliable, and high-performing medical components.
Key Questions to Ask When Customizing Medical Injection Molding Applications
Medical injection molding applications are widely used across the healthcare industry to produce precision components, and custom solutions are often needed to meet specific requirements for various medical devices. When working with a manufacturer to customize medical injection molding products, it’s essential to ask the right questions to ensure the product meets your specifications, complies with regulations, and performs reliably in its intended medical application. Below are key considerations and questions you should ask the manufacturer when customizing your medical injection molding products.
Material Selection and Compatibility
When customizing medical injection molding products, selecting the right material is crucial to ensure biocompatibility, durability, and safety. It is important to understand the options available and the characteristics of each material to ensure it fits the intended use.
Key Questions to Ask:
- What types of medical-grade plastics do you recommend for this specific application?
- How do you ensure that the materials used meet the biocompatibility standards for medical devices (e.g., ISO 10993)?
- Are the materials resistant to sterilization processes like autoclaving, and do they maintain integrity under these conditions?
- Can you provide material certifications that prove compliance with relevant regulatory standards?
These questions help you verify that the manufacturer uses appropriate materials that meet the necessary regulatory and safety standards for medical applications.
Compliance with Regulatory Standards and Certifications
Regulatory compliance is critical in the medical industry to ensure that the final products are safe for use in healthcare environments. It’s essential to confirm that the manufacturer is well-versed in the standards required for medical injection molding applications.
Key Questions to Ask:
- How do you ensure compliance with FDA regulations for medical devices?
- Are you certified with ISO 13485, and how do you implement this certification in your manufacturing process?
- Do you follow current good manufacturing practices (cGMP) during production?
- Can you provide documentation of compliance with relevant standards for medical device manufacturing?
Asking these questions ensures that the manufacturer is up to date with the necessary certifications and follows industry guidelines to produce high-quality medical components.
Customization and Design Capabilities
Customization is a major advantage of medical injection molding, and you need to ensure that the manufacturer can meet your specific design requirements while maintaining high-quality production.
Key Questions to Ask:
- Can you work with complex part geometries and achieve the necessary precision for my design?
- What are your capabilities for designing and prototyping custom molds to meet my specific needs?
- How do you handle design changes or iterations during the manufacturing process?
- Can you assist with the integration of specific features, such as overmolding, insert molding, or multi-material molding?
These questions help clarify the manufacturer’s ability to produce parts that meet your exact specifications, including complex designs and custom features.
Production Volume and Lead Time
Understanding the production volume and lead time is important to ensure timely delivery and cost-effectiveness. Whether you need a small batch for prototyping or a large production run, discussing these details early is crucial.
Key Questions to Ask:
- What is your minimum order quantity (MOQ) for custom injection molding products?
- What is the typical lead time for both prototyping and full production runs?
- Can you scale production efficiently if the order volume increases?
- How do you ensure consistency in quality when scaling production?
These questions help manage expectations regarding production timelines and help you plan your supply chain effectively.
Quality Control and Testing Processes
In medical injection molding applications, ensuring consistent quality is vital for patient safety and device performance. Understanding the manufacturer’s quality control and testing processes will provide confidence in the reliability of the product.
Key Questions to Ask:
- What quality control measures do you have in place throughout the production process?
- Do you conduct in-house testing for mechanical properties, biocompatibility, and sterilization resistance?
- How do you ensure part consistency across large production volumes?
- Can you provide reports or documentation of quality testing, including traceability for each batch?
These questions ensure that the manufacturer follows a robust quality assurance process to produce reliable, high-quality medical components.
Cost Considerations and Pricing Transparency
Cost is always an important factor in any manufacturing project. When customizing medical injection molding products, it’s essential to have a clear understanding of the pricing structure and what factors influence costs.
Key Questions to Ask:
- Can you provide a detailed breakdown of the costs involved, including materials, labor, and tooling?
- How does the complexity of the part design impact the overall cost?
- Are there any additional costs for prototypes, mold creation, or modifications to the design?
- Do you offer cost-saving options for high-volume production runs?
These questions help you understand the cost implications and make informed decisions regarding your budget and production scale.
Asking the right questions when customizing medical injection molding products ensures that you choose a manufacturer who can meet your specific needs while adhering to industry standards. From material selection and regulatory compliance to design capabilities and cost considerations, these key questions will help you navigate the customization process successfully and ensure that the final products meet your performance, safety, and regulatory requirements. By addressing these factors early in the process, you can avoid potential pitfalls and achieve a high-quality, customized solution for your medical device needs.
FAQs about Medical Injection Molding Applications
Injection molding is a widely used manufacturing process in the medical industry, known for its precision and efficiency in producing complex and high-quality components. Medical products made by injection molding include:
Syringes and needles
Medical device housings
Surgical instruments and tools
Implantable components
Diagnostic equipment parts
Catheters and IV components
Laboratory consumables such as Petri dishes and test tubes
Protective equipment like face masks and shields
The ability to produce these items with high consistency and tight tolerances makes injection molding an integral process in creating medical products.
Automotive parts, such as dashboards, bumpers, and interior components
Consumer electronics, including casings for phones, laptops, and remote controls
Packaging solutions, such as caps, containers, and lids
Household items like kitchenware, toys, and furniture components
Aerospace components like plastic fasteners and interior fittings
The process is celebrated for its ability to mass-produce detailed parts with consistent quality, making it suitable for a diverse array of products.
A rising need for disposable medical supplies
Growth in minimally invasive surgical procedures requiring precision components
Expansion of diagnostic testing services
Technological advancements leading to innovative medical devices
Stringent regulatory standards promoting high-quality production practices
Overall, the market is expected to see robust expansion, supported by advancements in materials and manufacturing technologies that cater to the evolving needs of the healthcare industry.
High-volume manufacturing of plastic parts across various sectors
Creating intricate components that require consistent and precise dimensions
Producing both small-scale consumables and large-scale industrial products
Prototyping new designs to test and refine product concepts
Achieving high-strength, lightweight parts through advanced materials like composites and high-performance plastics
Whether you are in the automotive, medical, consumer goods, electronics, or aerospace industry, injection molding offers a reliable and scalable solution for manufacturing high-quality parts.
Medical injection molding is a highly specialized manufacturing process used to produce precise, high-quality plastic components for medical devices and equipment. In this process, raw plastic material is melted and injected into a mold under high pressure, allowing it to take the shape of the mold cavity. Medical injection molding is used to create a wide range of medical parts, including surgical instruments, diagnostic equipment, and implants. The process is highly controlled, ensuring that components meet stringent industry standards for quality, biocompatibility, and durability. This method is ideal for producing complex geometries and small to large quantities of parts with consistent precision, making it a key technique in the manufacturing of medical devices used in various healthcare applications.
An injection molding job refers to the tasks involved in the production of plastic components using the injection molding process. This job encompasses various responsibilities, including setting up and operating injection molding machines, selecting appropriate materials, and ensuring that molds are properly prepared and aligned. Technicians and operators monitor the molding process, adjusting temperature, pressure, and injection speed to ensure quality and accuracy in the final product. Injection molding jobs also involve quality control, inspection, and troubleshooting to prevent defects in molded components. This work is crucial in industries like medical device manufacturing, where high precision and reliability are essential to ensuring that parts are safe and functional for patient care. In medical injection molding, adherence to regulatory standards and cleanliness protocols is also a significant part of the job.
The primary purpose of injection molding is to produce high-quality plastic parts in a cost-effective and efficient manner. This process is ideal for manufacturing parts with complex shapes, tight tolerances, and consistent performance, which are essential in industries such as medical device manufacturing. Injection molding allows for the production of parts at a high volume while maintaining precision, making it perfect for creating both small and large quantities of identical components. The purpose of injection molding extends beyond simply producing parts—it also enables manufacturers to select materials based on performance needs, such as biocompatibility for medical applications. Additionally, the ability to integrate multiple features, such as overmolding and insert molding, allows for more functional and reliable medical components that meet stringent safety standards. Ultimately, the purpose of injection molding in medical applications is to produce reliable, cost-effective, and high-quality components that improve patient care and safety.
Contact our professional team now for a same-day quote and risk-free project evaluation. Benefit from ISO 8 cleanrooms, advanced machines, and 12-hour fast response in medical injection molding.