Custom Medical Injection Molding Medical Molding Services
Low-Volume to High-Volume Production Capabilities
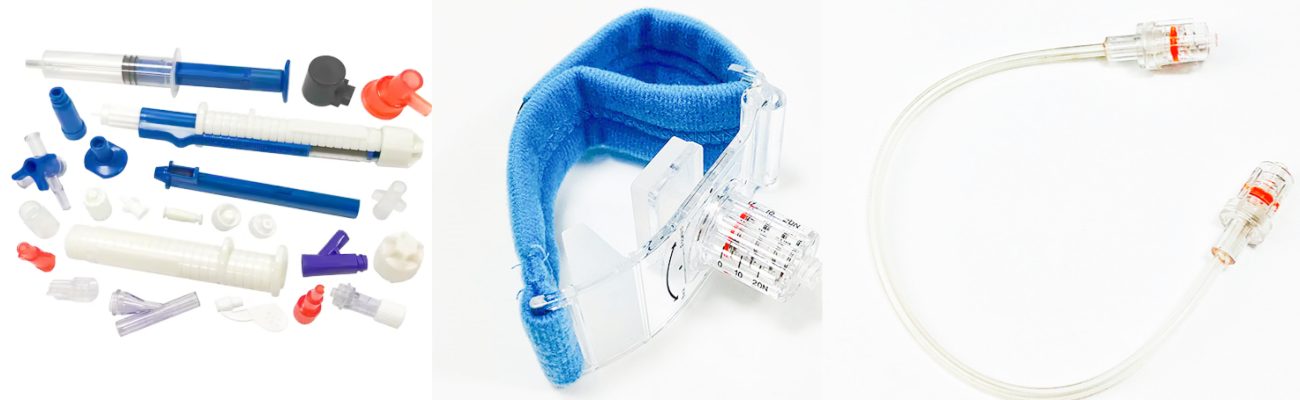
Attribute | Details |
---|---|
Product Name | Medical Injection Molding |
Brand | LY Medical Injection Mold |
Place of Origin | Dongguan, Guangdong, China |
Mold Type | Plastic Injection Mould, Hot Runner / Cold Runner |
Material Options | ABS, PP, PE, PEEK, PC, PMMA, POM, PA66, PVC, etc. |
Surface Finishing | Original, Matte, Polishing, Etched, Texture, Custom Surface |
Color Options | White, Black, Grey, Red, Custom Colors |
Gate Type | Side gate, Sub gate, Pin point gate, Edge gate |
Cavity | Single or Multi cavity |
Mold Life | 30,000 - 700,000 shots (varies by product and type) |
Cycle Time | 30 - 60 seconds |
Mold Precision | ±0.03 mm |
Shaping Mode | Plastic Injection Molding |
Certification | ISO 9001:2008 |
Customization | Custom colors, size, logo, and surface treatment |
Product Application | Medical equipment |
Production Process | CNC, High-speed carving, EDM, Wire cut, Drilling, Injection |
Delivery Time | 30 - 50 days (mold production) |
In the medical industry, a continuous supply of reliable medical devices and their components is essential for effective healthcare delivery. As the demand for these devices grows, we seek efficient and cost-effective methods to produce them. Among various manufacturing processes, medical injection molding process stands out as the most economical and effective way to manufacture medical parts. At FUJIU Medical Injection Mold, we specialize in providing a comprehensive range of medical device solutions tailored specifically for medical applications.
Our in-house expertise in design for manufacturability (DFM) and part processing allows us to create custom solutions tailored to our clients’ needs. We understand that each medical device has unique requirements, and we strive to deliver products that are not only functional but also cost-efficient.
We utilize a wide array of medical-grade resins, ensuring that our products meet the stringent safety and efficacy requirements inherent in the medical industry. Our state-of-the-art machinery, automated quality inspection systems, and scientifically-backed molding processes guarantee reliable service and superior product quality, making favorable medical injection molding services a cornerstone of our operations. FUJIU Medical Injection Molds specializes in medical injection molding, producing high-quality plastic parts from various materials in large quantities, cost-effectively.
What is Plastic Medical Molding?
Plastic medical molding refers to the process of manufacturing medical devices and components using plastic materials through injection molding. This method is crucial in producing a wide range of medical and dental products such as syringes, surgical instruments, implants, catheters, and diagnostic devices. The process involves injecting molten plastic into a mold under high pressure, allowing it to take the shape of the desired component. Due to its precision, cost-efficiency, and ability to produce high volumes of parts with intricate details, plastic medical molding is widely used in the industry. Materials used often include medical-grade plastics, thermoplastic elastomers (TPE), and silicone, which meet strict regulatory standards for biocompatibility and sterilization. The benefits of plastic medical molding include high repeatability, reduced waste, and the ability to produce complex geometries, making it an ideal solution for both low and high-volume production in the medical field.
Injection molding offers exceptional precision, making it ideal for the production of medical components that require tight tolerances and consistent quality. This is particularly important in medical devices where even the smallest deviation can affect performance and safety. With advanced molding technologies, manufacturers can achieve high repeatability, ensuring that every part meets exact specifications. Injection molding is a highly efficient method for mass production, capable of producing large quantities of parts quickly and cost-effectively. Once the mold is created, it can be used to produce thousands or even millions of parts without significant loss in quality. This scalability makes it an excellent choice for medical device manufacturers needing to meet large demand. Injection molding allows for the use of a wide range of materials, including medical-grade plastics, thermoplastic elastomers (TPE), silicone, and composites. This versatility makes it possible to tailor the material properties to the specific needs of the medical application, whether it’s biocompatibility, flexibility, or durability. It also enables the production of multi-material components in one cycle, further enhancing design possibilities. Although the initial cost of creating an injection mold can be high, the overall production cost per unit decreases significantly with high-volume runs. This makes injection molding an attractive option for medical manufacturers, especially when balancing the need for precision and large-scale production. The cost-effectiveness of injection molding also allows companies to remain competitive while maintaining strict regulatory and quality standards. Injection molding is capable of producing components with intricate designs, complex geometries, and advanced features such as thin walls, undercuts, and integrated threads. This capability allows for the production of sophisticated medical devices and components, such as microfluidic systems, syringe bodies, and surgical instruments, that require high precision and functionality. Injection molding is a highly efficient process that minimizes material waste. The method uses just the right amount of material to fill the mold, and excess material (called flash) is typically recycled. This is especially important in the medical industry, where minimizing waste is critical for both cost savings and environmental sustainability. For medical applications, ensuring product sterility and regulatory compliance is critical. Injection molding offers a high degree of control over the manufacturing process, which helps ensure that medical components meet stringent regulatory standards such as ISO 13485, FDA approval, and USP class VI compliance. Additionally, plastic parts produced by injection molding can be sterilized to meet healthcare standards. Injection molding offers relatively short lead times compared to other manufacturing processes. Once the mold is created, parts can be produced quickly, which is advantageous for medical companies needing to bring new products to market fast or respond to urgent demands. Medical-grade plastics and composites used in injection molding offer excellent mechanical properties, including strength, flexibility, and resistance to wear and chemicals. This makes injection-molded components ideal for use in medical devices that must withstand repeated use, exposure to harsh environments, or interaction with bodily fluids. Injection molding offers a high degree of design flexibility, enabling manufacturers to tailor components to the specific needs of healthcare applications. Whether it’s for drug delivery systems, surgical instruments, or diagnostic tools, injection molding can accommodate custom designs, color options, and part integrations, ensuring the final product meets the precise specifications required. Injection molding is a cornerstone technology in the medical industry, offering a range of benefits from precision and efficiency to material versatility and cost-effectiveness. Whether for high-volume production or specialized components, the advantages of injection molding make it an essential process for manufacturing high-quality medical devices that meet the rigorous demands of healthcare professionals and patients.Advantages of Using Injection Molding in the Medical Industry
Precision and Consistency
High-Volume Production
Versatility in Materials
Cost Efficiency
Complex Geometries and Features
Reduced Waste
Sterility and Compliance with Regulations
Shorter Lead Times
Strong Material Properties
Customization and Design Flexibility
Material Versatility in Medical Injection Molding
Medical injection molding can utilize various materials to meet specific application requirements, ensuring that products are not only functional but also compliant with safety regulations. The choice of materials is critical, as each type offers unique properties that cater to different needs within the medical field. Commonly used materials include:
Plastics:
Plastics such as polypropylene, polyethylene, polystyrene, and polyetheretherketone (PEEK) are popular choices in medical applications due to their durability and versatility.
Polypropylene is widely used for its lightweight nature and excellent resistance to chemicals and moisture, making it ideal for items like syringes and packaging.
Polyethylene is favored for its toughness and flexibility, often used in disposable items and medical bags.
Polystyrene offers clarity and ease of molding, which is beneficial for producing components that require visual inspection.
PEEK, known for its high strength and thermal stability, is often employed in more demanding applications, such as implants and surgical instruments.
Thermoplastic Elastomers (TPE):
These materials provide a unique combination of rubber-like elasticity and thermoplastic processability. TPEs are suitable for various medical applications, including grips, seals, and tubing. Their flexibility and resilience enable the production of devices that require a soft touch or need to conform to various shapes, enhancing patient comfort.
Silicones:
Silicone elastomers are renowned for their chemical stability, flexibility, and resistance to extreme temperatures. They are particularly important in the medical field because they support sterilization processes, making them crucial for devices that come into contact with bodily fluids. Silicones are commonly used in applications such as catheters, seals, and various prosthetics, where biocompatibility and safety are paramount.
Metals and Composite Materials:
In certain applications, especially those requiring enhanced strength and durability, metals and composite materials are used. Metals such as stainless steel and titanium are often employed for surgical instruments and implants due to their exceptional strength, corrosion resistance, and longevity. Composite materials, combining various materials to leverage their strengths, are also utilized in specific scenarios, such as orthopedic devices where both strength and lightweight properties are desired.
What Aspects Should Be Considered When Selecting A Medical Injection Molding Supplier?
When selecting a medical injection molding supplier, it’s crucial to consider multiple factors to ensure the supplier can meet the high standards of the medical industry. These factors include:
Selecting the right medical injection molding supplier involves a combination of technical expertise, regulatory compliance, quality control, and efficient logistics. By carefully considering these factors, you can ensure a successful partnership that supports your needs for high-quality, reliable, and cost-effective medical components. FUJIU Medical Injection Molds meets all the critical requirements for selecting a reliable medical injection molding supplier. With extensive experience in the medical industry, we ensure compliance with regulatory standards such as ISO 13485 and FDA requirements, guaranteeing high-quality, reliable products. Our advanced injection molding technology allows us to handle a wide range of materials and produce precision components at both small and large scales. We maintain rigorous quality control processes, ensuring that every product meets stringent medical device standards. Additionally, we support customized services, offering tailored solutions for unique design needs, rapid prototyping, and scalable production. Our expertise in material sourcing, process validation, and risk management further ensures that we deliver consistent, high-quality components that meet the exacting demands of the medical sector. Whether you need low-volume prototypes or high-volume production, FUJIU Medical Injection Molds is equipped to handle all your medical molding requirements.Experience and Expertise
Regulatory Compliance
Quality Control and Assurance
Capabilities and Technology
Material Handling and Sourcing
Cost Efficiency and Lead Times
Scalability
Customer Support and Communication
Risk Management
Location and Logistics
FUJIU Medical Injection Molds
What is Overmolding in Medical Molding?
Overmolding is a specialized form of medical injection molding that involves the process of molding a polymer over a substrate, resulting in a composite part that effectively combines the properties of both materials. This innovative technique not only enhances the functionality of medical devices but also eliminates the need for post-molding assembly. This capability is crucial in maintaining sterility and reducing production time in medical applications.
In the overmolding process, a base substrate—typically made from a thermoplastic material—is first molded into the desired shape. Once this substrate is formed, a second material is molded over it, creating a multi-layered component. This technique is particularly beneficial in the medical industry, where it can be utilized for various applications, such as: Handles on Surgical Instruments: Overmolding allows for the creation of ergonomic handles that improve grip and comfort for healthcare professionals, enhancing usability during surgical procedures. This is essential in medical molding, where device performance and user experience are paramount. Medical Products: Overmolding extends beyond products with metal parts. It can also be applied to create medical components using materials like silicones or thermoplastic elastomers (TPE) overmolded onto thermoplastic substrates. This capability allows for greater design flexibility and functionality in medical devices, ensuring they meet the diverse needs of healthcare settings. Overmolding is more than just layering one material on top of another; it involves complex bonding mechanisms that are critical to the success of the composite part: Chemical Bonds: These bonds form at the molecular level between the overmold material and the substrate. The effectiveness of this bonding is influenced by how well the overmold material wets the surface of the substrate, determined by factors such as temperature, material compatibility, and surface treatment. Mechanical Bonds: The physical geometry at the interface of the substrate and overmold plays a crucial role in establishing mechanical bonds. The design of the substrate can incorporate features such as undercuts or textures that enhance the grip of the overmold material, ensuring a robust connection between the two layers. Several methods are commonly used in the overmolding process, each with unique applications in medical molding: Two-Shot Molding: Also known as double-shot molding, this is a continuous two-step process where a substrate is first molded, and then a different material is overmolded onto it in a single cycle. This method is efficient and effective for producing complex parts with diverse material properties, making it ideal for a variety of medical applications. Pick-and-Place Molding: This method is primarily used for prototyping and low-volume production runs. In this process, pre-molded substrates are manually placed into the molding machine, where they are then overmolded. While not as automated as two-shot molding, this technique allows for quick adjustments and variations during the development phase, providing flexibility in the medical injection molding process. The use of overmolding in medical device manufacturing offers numerous advantages: Reduced Assembly Time: By integrating multiple materials into a single part, overmolding eliminates the need for separate assembly processes, streamlining production and minimizing potential contamination during assembly. Enhanced Functionality: The combination of different materials allows for enhanced features, such as improved grip on handles, flexibility, or resistance to chemicals, contributing to better performance in medical applications. This capability is particularly important in medical molding, where device reliability is critical. Improved Aesthetics: Overmolding enables manufacturers to create visually appealing products by combining colors and textures. This aesthetic enhancement can improve user experience and marketability, crucial factors in the competitive medical device landscape. Cost Efficiency: By reducing assembly time and minimizing the number of parts required, overmolding can lower overall production costs while maintaining high-quality standards, making it a cost-effective solution for manufacturers in the medical industry.The Overmolding Process
Bonding Mechanisms
Types of Overmolding Processes
Advantages of Overmolding in Medical Injection Molding
The Role of Thin Wall Injection Molding in Medical Injection Molding Applications
Medical injection molding is an essential process in the healthcare industry, providing efficient and precise solutions for manufacturing medical devices. One notable technique within this domain is thin wall injection molding, specifically designed to produce thin, lightweight parts that are crucial for a range of medical applications. This method is particularly advantageous for creating small, intricate components that require a high degree of accuracy.
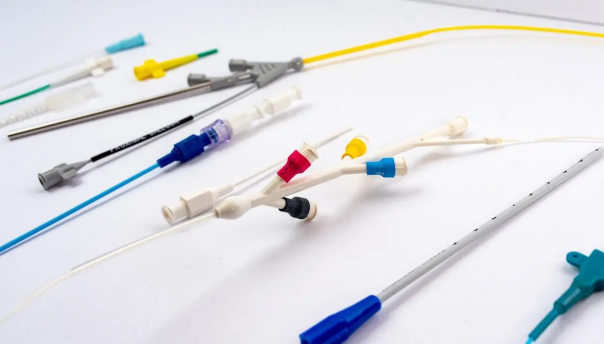
What is Thin Wall Injection Molding?
Thin wall injection molding focuses on producing parts with a wall thickness of less than 1mm, categorizing them as “thin-walled.” This technique is characterized by its ability to create lightweight components while significantly reducing material costs and cycle times. The thinness of the wall plays a critical role in determining the overall size and functionality of the part.
In medical applications, the precision offered by thin wall injection molding is vital. Precision mold medical components must meet tight tolerances and rigorous safety and efficacy standards. The lightweight nature of these parts allows for easier handling and installation, making them ideal for various medical applications, including diagnostic tools and surgical instruments.
Benefits of Thin Wall Injection Molding
The key benefits of thin wall injection molding make it a preferred choice for manufacturers, particularly in high-volume production environments:
Cost Savings: By minimizing the amount of material used in each part, manufacturers can significantly reduce production costs. This is particularly important in the medical field, where budget constraints often play a significant role in the development of new devices.
Faster Cycle Times: The design of thin wall parts allows for quicker cooling times during the injection molding process. This results in shorter cycle times and the ability to produce more parts in less time, enhancing overall production efficiency.
High Precision: Thin wall injection molding is capable of achieving a high degree of precision, which is crucial for the small, complex parts commonly found in medical devices. This precision ensures that each component fits and functions as intended, ultimately contributing to the safety and effectiveness of the device.
Lightweight Design: The lightweight nature of thin wall components can improve the usability and functionality of medical devices. Lighter devices are often easier to handle, transport, and operate, which can enhance patient and clinician experiences.
Applications in Medical Molding
Thin wall injection molding finds a variety of applications within the medical field. Some common uses include:
Small Enclosures for Medical Devices: Many medical devices require protective casings that are both lightweight and durable. Thin wall injection molding allows manufacturers to create these enclosures efficiently and cost-effectively, ensuring they meet the necessary regulatory standards in medical injection molding.
Disposable Medical Supplies: Products such as syringes, cups, and trays often benefit from thin wall designs, as these items are typically produced in high volumes and require low material costs. This is particularly relevant in the context of medical molding, where efficiency and cost-effectiveness are paramount.
Diagnostic Equipment Components: Components used in diagnostic tools, such as housings for sensors and electronic parts, can be effectively manufactured using thin wall injection molding. This ensures they meet the necessary precision standards required in medical applications.
Surgical Instrumentation: Many surgical instruments, including handles and lightweight tools, utilize thin wall injection molding to balance functionality with ease of use. This is essential for improving the performance and handling of devices used in critical medical procedures.
Advancing Medical Injection Molding: The Impact of Gas-Assisted Techniques
In the world of medical injection molding, the demand for precision and quality in plastic components is paramount. One innovative technique that has gained traction in recent years is gas-assisted injection molding. This low-pressure process not only enhances the manufacturing of complex machining medical parts but also addresses many common challenges faced in traditional molding methods. Gas-assisted molding is particularly effective for producing medical precision components that require intricate details, high dimensional accuracy, and smooth surface finishes, ensuring that each part meets the stringent requirements of the medical industry.
What is Gas-Assisted Injection Molding?
Gas-assisted injection molding is a unique process that combines traditional injection molding with the introduction of pressurized gas, typically nitrogen or carbon dioxide. The process begins by heating plastic until it becomes molten and injecting it into a mold. After the initial injection, pressurized gas is introduced into the mold cavity, pushing the molten plastic into the extremities of the mold and allowing for the creation of thicker walls with hollow sections. Once the molding is complete, the gas is vented, and the finished parts are removed from the mold.
This innovative approach is particularly beneficial for producing plastic parts that have large surface areas and require intricate textures and superior surface quality, making it an ideal choice for medical applications.
Advantages of Gas-Assisted Injection Molding
Gas-assisted injection molding offers several significant advantages, especially in the context of medical molding:
Material Cost Savings: By utilizing gas to expand the plastic within the mold, this technique reduces the amount of plastic required for production. This not only decreases material costs but also contributes to more sustainable manufacturing practices.
Decreased Cycle Times: The use of gas allows for quicker filling and cooling times compared to traditional injection molding. As a result, manufacturers can produce more parts in a shorter time frame, enhancing overall productivity.
Improved Part Appearance: Gas-assisted injection molding significantly improves the aesthetics of the finished product. It reduces common defects such as sink marks, blemishes, warpage, and distortion. The pressurized gas helps to pack out the resin evenly, ensuring that the surface quality meets the high standards required in medical injection molding applications.
Reduced Residual Stress: Lower molding pressures result in less residual stress on the finished parts. This not only enhances the durability and performance of the components but also reduces wear and tear on the molds, extending their lifespan and decreasing maintenance costs.
Enhanced Design Flexibility: The ability to create hollow sections and thicker walls allows for greater design flexibility. This is particularly advantageous for medical devices that require lightweight yet robust components, such as surgical instruments and diagnostic equipment.
Applications in Medical Injection Molding
Gas-assisted injection molding is increasingly being used in various applications within the medical industry. Some common uses include:
Medical Device Housings: The process is well-suited for creating lightweight, durable enclosures for medical devices, ensuring that they are both functional and aesthetically pleasing.
Surgical Instruments: The precision offered by gas-assisted injection molding allows for the manufacture of intricate surgical tools that require high levels of accuracy and performance.
Diagnostic Equipment Components: Parts used in diagnostic tools can benefit from the superior surface quality and reduced defects provided by this molding technique.
Fluid Management Systems: Components that require hollow sections, such as tubing connectors and valves, are ideal candidates for gas-assisted injection molding, enabling efficient fluid flow without compromising structural integrity.
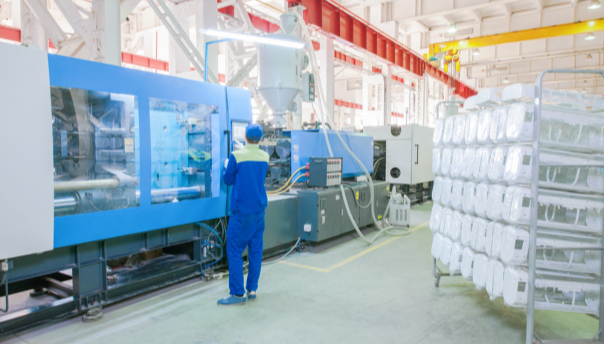
Advantages of LSR Injection Molding in Medical Applications
Medical injection molding is a crucial technology in the healthcare industry, allowing for the precise production of various medical devices and components. One of the innovative methods employed in this field is LSR (Liquid Silicone Rubber) injection molding. This technique utilizes liquid silicone rubber, a versatile two-component elastomer that undergoes a curing process to develop its end-use properties. The ability to create high-quality components with outstanding performance characteristics makes LSR injection molding particularly suitable for medical applications.
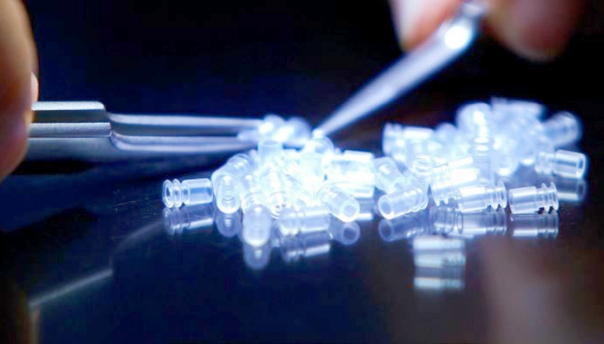
What is LSR Injection Molding
LSR injection molding involves the use of liquid silicone rubber, which requires curing to achieve the desired material properties. The two components of LSR are typically delivered in 5-gallon pails or 55-gallon drums. These components are first poured into a static mixer, where they are combined before being fed into the injection unit. Additional mixing occurs within the injection unit to ensure a homogeneous blend.
The injection process begins when the injection screw pushes the shot, or the specific amount of LSR required, into the mold. One of the unique aspects of LSR injection molding is that the two halves of the mold remain clamped during the curing process, which typically lasts about 30 seconds. This rapid curing time significantly enhances production efficiency compared to high-consistency silicone rubber (HCR), which may require five minutes or more for curing, particularly when using peroxide curing agents. This makes liquid silicone molding for medical devices a particularly valuable process, as it allows for precise, high-quality molding of medical components like seals, gaskets, and other critical parts, all while maintaining fast production cycles.
Advantages of LSR Injection Molding in Medical Applications
LSR injection molding offers several key advantages, particularly in the context of medical molding:
Rapid Cycle Times: The quick curing process associated with LSR injection molding allows for faster production cycles. This efficiency is crucial in high-volume medical applications where timely delivery is essential.
Enhanced Material Properties: LSR can be platinum-cured, which results in materials with superior optical clarity, tensile strength, and tear strength. Platinum-cured silicones are known for their exceptional performance characteristics, making them ideal for demanding medical environments.
Lower Extractables: One of the critical benefits of platinum-cured silicones is their reduced extractables. Extractables are compounds that can leach out of the material, potentially affecting the safety and effectiveness of medical devices. The lower level of extractables in platinum-cured LSR contributes to higher purity, which is essential for many medical applications.
Versatility in Design: LSR injection molding allows for the creation of complex geometries and intricate designs. This versatility is particularly advantageous in the medical field, where components must often meet specific functional and ergonomic requirements.
Biocompatibility: LSR is known for its biocompatibility, making it suitable for direct contact with human tissue. This property is particularly important for medical devices used in implants, prosthetics, and various diagnostic tools.
Applications of LSR Injection Molding in Medical Molding
The benefits of LSR injection molding make it a preferred choice for a variety of applications within the medical industry, including:
Inhaler Spacers: LSR is commonly used to manufacture spacers for asthma inhalers. The combination of rapid production and high purity ensures that these critical components meet stringent regulatory requirements.
Seals and Gaskets: LSR is ideal for producing seals and gaskets that require flexibility and durability. These components are essential for maintaining the integrity of medical devices.
Surgical Instruments: The precision and versatility of LSR injection molding allow for the creation of intricate surgical instruments that require high performance and reliability.
Medical Tubing: LSR can be used to produce flexible and biocompatible tubing for various medical applications, from drainage systems to catheter components.
Diagnostic Equipment: Components used in diagnostic tools, such as sensors and housings, benefit from the clarity and strength of platinum-cured LSR.
Let’s Create Great Things—Get a Quote Today
Contact our professional team now for a same-day quote and risk-free project evaluation. Benefit from ISO 8 cleanrooms, advanced machines, and 12-hour fast response in medical injection molding.
Medical Injection Molding: The Advantages of HCR Injection Molding
In the realm of medical injection molding, the choice of material and processing method can significantly influence the quality and performance of medical devices. One such method, HCR (High-Consistency Rubber) injection molding, utilizes heat-cured silicone rubber to create robust and reliable components that meet the stringent demands of the healthcare industry. Understanding the intricacies of HCR injection molding is essential for manufacturers looking to optimize their production processes.
What is HCR Injection Molding
HCR injection molding involves the use of high-consistency silicone rubber, a material characterized by its gum-like texture. The process begins by heating this raw material to reduce its viscosity, making it easier to inject into molds under high pressure. During the injection cycle, the preheated silicone fills the mold cavity completely, ensuring that intricate designs are accurately replicated.
The preheating stage plays a crucial role in enhancing the flow of the silicone, allowing it to fill the mold more rapidly. However, the higher viscosity of HCR presents challenges during processing, making HCR injection molding generally more complex than LSR (Liquid Silicone Rubber) injection molding.
Benefits of HCR Injection Molding in Medical Applications
Despite its challenges, HCR injection molding offers several advantages that make it a valuable option in medical molding:
Superior Material Properties: HCR silicone can achieve better overall properties compared to LSR. This includes enhanced durability, heat resistance, and mechanical strength, which are critical for medical devices that must withstand rigorous conditions.
Versatility in Design: The ability to mold complex shapes and geometries is one of the key benefits of HCR injection molding. This flexibility is essential for creating components such as gaskets, O-rings, and seals that require precise fit and function.
High-Pressure Processing: The high-pressure injection process allows for the production of denser parts with improved surface finishes. This is particularly beneficial for medical components that must meet strict aesthetic and functional standards.
Adaptability to High Shear Conditions: Although high shear conditions in the mold can lead to varying shrink rates depending on the part’s geometry, skilled manufacturing partners can mitigate these challenges through proper tool design and process optimization.
Wide Range of Applications: HCR injection molding is particularly well-suited for applications requiring a durable and flexible material, making it ideal for producing components such as:
Gaskets: Essential for preventing leaks in medical devices, gaskets produced through HCR injection molding offer reliable sealing properties.
O-Rings: Used in various medical applications, O-rings manufactured from HCR silicone ensure a tight seal and compatibility with different fluids and gases.
Medical Device Components: From housings to seals, HCR silicone is used in various medical devices that demand high performance and reliability.
Importance of Proper Tool Design
The success of HCR injection molding relies heavily on proper tool design and the expertise of the manufacturing partner. Due to the material’s higher viscosity and the complexities involved in the molding process, it is crucial to work with experienced professionals who understand the nuances of HCR silicone.
A well-designed mold can minimize issues related to shrinkage and ensure that parts are produced consistently and to specification. This is especially important in the medical field, where even minor defects can have significant implications for device performance and patient safety.
Harnessing the Power of Medical Injection Molding
In the medical industry, the demand for high-performance components is ever-increasing. Metal injection molding (MIM) has emerged as a key solution for producing durable and intricate metal parts required in various medical applications. This advanced manufacturing process combines powdered metal with a thermoplastic binder, resulting in parts that are not only strong but also capable of intricate designs essential for medical molding.
The Process of Metal Injection Molding
Metal injection molding begins with the careful blending of fine metal powders with a thermoplastic binder. This mixture is then subjected to heat, allowing the metal particles to bond with the binder. The next step involves injecting this material into a precisely designed mold under high pressure. Once the part is formed, the thermoplastic binder is removed, usually through a debinding process, preparing the part for the final sintering stage.
During the sintering process, the part is heated at high temperatures, which compacts the metal and fuses the particles together. This results in a net-shape or near-net-shape part, minimizing the need for extensive post-processing and machining. The precision and efficiency of this method make it an invaluable aspect of medical injection molding.
Key Benefits of Metal Injection Molding in the Medical Field
Metal injection molding offers several compelling advantages that make it particularly suited for medical applications:
Rapid Production: MIM is well-suited for high-volume manufacturing, allowing for quick turnaround times. This efficiency is critical in the medical field, where time-to-market can significantly impact patient care and treatment options.
Complex Designs: The ability to produce intricate shapes is one of the standout features of MIM. This capability enables manufacturers to create components that would be difficult or cost-prohibitive to produce using traditional methods, enhancing the design possibilities in medical molding.
Enhanced Mechanical Properties: Parts produced via MIM are known for their excellent mechanical strength, comparable to that of forged or cast materials. This robustness is essential for components used in surgical instruments and implants, where reliability is paramount.
Material Versatility: MIM can effectively process challenging materials like stainless steels, cobalt-chromium alloys, and titanium alloys. This flexibility makes it a valuable alternative to CNC machining, especially for complex shapes that are often required in medical applications.
Consistency and Quality: MIM ensures high consistency and repeatability, which are crucial for maintaining the rigorous quality standards required in medical devices. This reliability helps to enhance patient safety and device performance.
Applications of Metal Injection Molding in Healthcare
Metal injection molding finds extensive applications across the medical sector, including:
Surgical Tools: MIM is widely used to manufacture surgical instruments that require high precision and strength, ensuring they can withstand the rigors of medical procedures. This is vital in maintaining the integrity of surgical instruments during operations.
Implants: The ability to create custom-shaped implants makes MIM an attractive choice for orthopedic and dental applications, providing patients with tailored solutions that meet their specific anatomical needs.
Connectors and Fasteners: These essential components, critical for assembling medical devices, benefit from the durability and strength that MIM provides. Their reliability ensures that medical devices function as intended without failure.
Diagnostic Instrument Parts: MIM is also utilized to produce parts for diagnostic tools, ensuring they meet the necessary standards for accuracy and reliability. High-quality components are essential for effective diagnosis and patient monitoring.
Key Applications of Plastic Injection Molding in Medical Devices
In the medical and dental industries, plastic injection molding plays a vital role in the production of various devices and components. While the range of plastic devices seems nearly infinite, certain applications consistently demonstrate high demand among injection molding manufacturers. Understanding these key applications helps to illustrate the significance of medical injection molding in providing effective solutions for healthcare.
Test Strips: Millions of chemical test strips are produced each year for use with diagnostic meters. These strips are essential for monitoring cholesterol levels, including HDL, LDL, and triglycerides. Their reliable performance is critical for effective health management, making them a staple product in the medical molding sector.
Catheters: Catheters are thin plastic tubes that serve a wide array of medical applications. Depending on the medical-grade materials and manufacturing processes employed, catheters can be used in various specialties, including cardiovascular, urological, gastrointestinal, neurovascular, and ophthalmic fields. They play a vital role in fluid drainage, drug delivery, and surgical instrument access, underscoring their importance in medical molding.
Biopsy Needles: The prevalence of biopsies in modern medicine means that millions of biopsy needles are produced annually. These needles typically feature a plastic handle, which is crafted using injection molding techniques. The design and manufacturing of these handles must meet stringent regulatory standards to ensure safety and efficacy during procedures.
Check Valves: Check valves are common components used in fluid delivery systems within medical devices. These valves control the flow rates of fluids in applications such as fluid drainage and irrigation. Their precise engineering is crucial for maintaining the desired fluid dynamics in various medical scenarios.
Orthopedic Devices: The orthopedic field benefits significantly from medical injection molding, which is utilized to manufacture a wide range of implants, prosthetic devices, components, and related surgical instrumentation. The ability to produce complex geometries and durable materials makes injection molding an ideal choice for these critical applications.
Urology Pumps: Injection molded plastic urology pumps are vital in treating conditions like incontinence and erectile dysfunction. They are also used in surgical procedures such as endoscopy, highlighting the diverse applications of medical molding technologies in enhancing patient care.
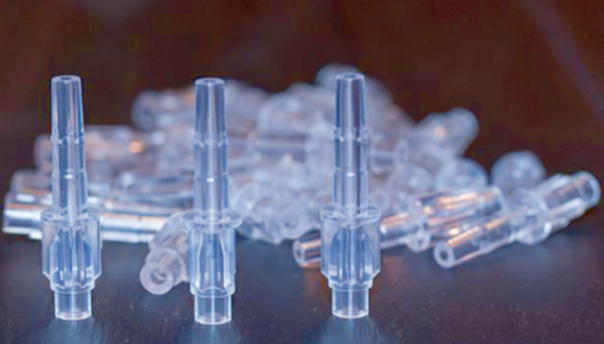
Custom Services by FUJIU Medical Injection Mold
FUJIU Medical Injection Mold is a leading provider of Custom Medical Injection Molding and Medical Molding Services, leveraging decades of expertise in manufacturing plastic components for the medical and pharmaceutical industries. Our services are designed to meet the highest standards of precision, quality, and compliance, enabling us to produce complex medical parts that are often beyond the capabilities of competitors. Below is a detailed description of our capabilities and services:
Certifications and Quality Standards
FUJIU Medical Injection Mold is committed to delivering the highest quality medical components. Our facilities are certified to the following standards:
- ISO 13485:2016: Ensures compliance with medical device quality management systems.
- ISO 9001: Demonstrates our commitment to quality management across all operations.
- AS9100D: Highlights our ability to meet aerospace industry standards, reflecting our precision and reliability.
These certifications underscore our dedication to maintaining rigorous quality control and meeting the stringent requirements of the medical and pharmaceutical industries.
State-of-the-Art Facilities
Our manufacturing capabilities are supported by advanced facilities, including:
- ISO Class 8 and Class 7 Cleanrooms: These controlled environments ensure the production of sterile, contamination-free components, which is critical for medical applications.
- 150,000 Square Feet of Production Space: Our expansive facilities include injection molding, tooling, design, assembly, and warehousing, allowing us to handle projects of any scale with precision and efficiency.
Comprehensive Medical Molding Services
We offer a wide range of Custom Medical Injection Molding services to meet the diverse needs of the medical industry:
Core Services
- Injection Molding: High-precision molding of medical-grade plastics for components such as surgical instruments, diagnostic devices, and drug delivery systems.
- Insert Molding: Combining metal or plastic inserts with molded components to create durable, multi-material parts.
- Overmolding: Adding a secondary layer of material (e.g., TPE or silicone) to improve grip, comfort, or functionality.
- Metal Injection Molding (MIM): Producing small, complex metal parts with high precision for medical devices.
- Post-Molding Services: Including assembly, hot stamping, and heat staking to ensure finished parts meet exact specifications.
Specialized Molding Techniques
- Micro-Molding: Producing extremely small and intricate components for applications like minimally invasive surgical tools or implantable devices.
- Liquid Silicone Rubber (LSR) Molding: Ideal for creating flexible, biocompatible parts such as seals, gaskets, and diaphragms.
- Polyurethane Casting: Offering an alternative to traditional molding for low-volume or specialized applications.
Additional Capabilities
- 3D Printing: Rapid prototyping and low-volume production of medical components.
- Design for Manufacturability (DFM): Our engineers work closely with clients to optimize designs for efficient and cost-effective production.
- Tooling Design and Development: Custom tooling solutions tailored to specific project requirements.
Advantages of Partnering with FUJIU Medical Injection Mold
- Complex Part Manufacturing: Our expertise allows us to produce parts with intricate geometries and tight tolerances that many competitors cannot achieve.
- End-to-End Solutions: From design and prototyping to full-scale production and assembly, we provide comprehensive services under one roof.
- Global Presence: With manufacturing facilities in both the United States and China, we offer flexible and scalable solutions to meet global demand.
- Regulatory Compliance: Our adherence to ISO 13485 and other standards ensures that all components meet the strict requirements of the medical industry.
- Customization: We tailor our services to meet the unique needs of each project, whether it involves prototyping, low-volume production, or high-volume manufacturing.
Commitment to Innovation
FUJIU Medical Injection Mold is at the forefront of medical molding technology, offering:
- Miniaturization: Expertise in micro-molding for increasingly small and complex medical devices.
- Smart Device Integration: Capabilities to incorporate sensors and electronics into molded components.
- Sustainability: Exploring eco-friendly materials and processes to reduce environmental impact.
FUJIU Medical Injection Mold is your trusted partner for Custom Medical Injection Molding and Medical Molding Services. With our advanced facilities, material expertise, and commitment to quality, we deliver precision-engineered components that meet the highest standards of the medical industry. Whether you need standard or cleanroom molding services, we have the capabilities to bring your medical device ideas to life. Partner with us to stay ahead in the competitive medical manufacturing landscape.
Medical Injection Molding: Innovations by FUJIU Medical Injection Mold
At FUJIU Medical Injection Mold, our expertise encompasses every stage of medical molding, ensuring effective production and high-quality outcomes. Our comprehensive support for medical molding projects includes:
Comprehensive Support for Medical Molding Projects
Precision Product Design: We collaborate closely with clients to understand their product requirements and design specifications, ensuring that every detail is meticulously considered.
Material Selection: Choosing the right material is critical for medical devices. We assist clients in selecting the most suitable medical-grade resins based on specific application needs.
Prototyping: Our rapid prototyping capabilities allow clients to visualize and test their designs before full-scale production, enabling early identification of potential issues.
Mold Tooling Fabrication: Once designs are finalized, we design and build molds optimized for efficiency and precision, essential for high-quality manufacturing.
Process Validation: We conduct thorough process validation to guarantee that the injection molding process consistently produces high-quality components. Rigorous testing protocols are employed to ensure that every aspect of production meets industry standards.
Full-Scale Production: Our facilities include cleanroom environments to ensure that all medical molding activities comply with the highest hygiene and safety standards.
Turnkey System Transfer: If required, we facilitate the transfer of turnkey systems to customer facilities, providing training and support to ensure effective operation while maintaining product quality.
Typical Applications of Medical Injection Molding
FUJIU Medical Injection Mold is called upon for a variety of medical applications, showcasing our capabilities in the field of medical injection molding. Some typical applications we handle include:
Multi-Purpose Medical Needles: Designed for reliability and safety across various medical procedures.
Multi-Lumen Catheters: Engineered for precision, critical for effective medical interventions.
Male/Female Luer Locks: Ensuring secure connections in medical devices, enhancing safety and efficacy.
Trocar Handles: Designed for durability and precision in minimally invasive surgeries.
Scalpels and Other Instruments: Expertise extends to the production of sharp, reliable surgical instruments.
Pacemaker Components: Manufactured with critical tolerances for functionality in life-saving devices.
Filters and Patient Electrodes: Vital components for diagnostic and monitoring equipment.
Fetal Monitoring Probes and EKG Hook-up Leads: Ensuring quality and precision for patient monitoring.
Y Connectors and Power Cords: Commonly used in various medical devices, benefiting from our advanced molding techniques.
Injection Mold Tooling Services
In addition to our plastic injection molding services, we offer a comprehensive suite of tooling services:
In-House Mold Toolmaking: We create high-precision molds in-house, allowing for greater control over the production process and timelines.
High Precision Machining: Our advanced machining capabilities ensure that molds are manufactured with high precision, resulting in accurate and consistent part production essential for medical applications.
Rapid Tool Iterations & Modifications: We understand that product designs may evolve, and we offer rapid iterations and modifications to molds to accommodate changes efficiently.
Quick Turnaround Prototyping: Our quick turnaround prototyping services enable clients to test designs and concepts rapidly, facilitating faster time-to-market for new medical devices.
Mold Flow Analysis: We perform mold flow analysis to predict how the molten plastic will behave during the injection process, helping to optimize design and reduce production issues.
Scientific Molding Process Development: Our expertise in scientific molding ensures that the injection molding process is data-driven and optimized for producing consistent and high-quality medical components.
Single Cavity Pre-Production Injection Molds: We provide single cavity molds for pre-production runs, allowing clients to validate their designs before committing to full-scale production.
High Cavitation Hot Runner Mold Systems: Our hot runner mold systems enable high cavitation production, improving efficiency and reducing material waste, making them ideal for high-volume medical manufacturing.
Key Factors in Medical Injection Molding
When it comes to medical injection molding, the success of your project hinges on several critical factors that dictate the choice of materials and the molding processes used. Understanding these factors is essential for creating high-quality medical devices that meet stringent industry standards:
Environment: The intended operating environment of a medical device plays a vital role in material selection. Factors such as exposure to moisture, temperature extremes, and potential chemical interactions must be considered.
Chemical Compatibility: Medical devices often come into contact with various substances, including medications and bodily fluids. Selecting materials that are chemically compatible with these substances is crucial to avoid degradation or contamination, ensuring patient safety and device effectiveness.
Complexity of Finished Part or Device: The intricacy of the design impacts the choice of molding process. More complex shapes may require specialized molding techniques to ensure that all features are accurately reproduced.
Mechanical Function: Understanding how the medical device will function under stress is essential for material selection. Components must withstand physical loads and perform reliably throughout their lifecycle.
Physical Load: Evaluating the physical load that a device will endure helps in determining the appropriate material and manufacturing method. This consideration is especially important for surgical instruments and implants, which must exhibit strength and durability to perform safely and effectively.
Sterilization: Many medical devices require sterilization to ensure safety before use. Materials must be chosen based on their ability to withstand sterilization processes without degrading or losing functionality.
Thermal Conditions: The temperature ranges that the device will encounter can influence material selection and processing techniques. Materials must maintain their integrity and performance in the face of varying thermal conditions, which is critical for devices used in diverse medical environments.
Advanced Molding Capabilities
At FUJIU Medical Injection Mold, we offer a range of plastic injection molding capabilities tailored to meet the unique needs of the medical industry. Our advanced methods include:
Injection Molding: Ideal for producing highly engineered, small precision parts in large volumes, allowing for multicavity options and efficient production.
Blow Molding: An effective technique for creating stand-alone hollow parts, ensuring uniform and economical production of single-constructed hollow pieces.
2-Shot Molding (Two-Shot Molding): This specialized process enables the molding and overmolding of a medical device or component in a single cycle, enhancing aesthetics while offering potential cost savings.
Insert Molding (Overmolding): This technique can eliminate the need for additional assembly and allows for the incorporation of color contrasts within the device, improving visual appeal.
Pad Printing & Screen Printing: We provide printing services for adding logos, labels, or markings directly onto molded parts, ensuring compliance with branding and informational requirements.
Assembly Techniques: Our extensive capabilities include various assembly methods such as annealing, heat staking, ultrasonic welding, and curing, which enhance the integrity and functionality of medical devices.
FAQs about Medical Injection Molding & Medical Molding
What are the health risks in injection molding?
Injection molding, while an efficient manufacturing process, can present several health risks to workers. One of the primary concerns is exposure to hazardous chemicals, including volatile organic compounds (VOCs) released from certain plastics during the melting and molding processes. Prolonged exposure to these fumes can lead to respiratory issues and skin irritations. Additionally, the process can produce fine particles and dust from the materials being processed, which can be harmful if inhaled over extended periods. Furthermore, there is a risk of physical injuries, such as cuts or burns, from handling sharp tools and hot materials. It is essential for facilities to implement proper ventilation systems to minimize exposure to harmful fumes and particles. Regular safety training and monitoring can also help ensure that workers are aware of potential hazards and how to mitigate them. Adopting safety protocols, such as using appropriate personal protective equipment (PPE), is crucial for reducing these risks and promoting a safe working environment.
What is medical injection molding?
Medical injection molding is a specialized manufacturing process used to produce medical devices and components with high precision and strict quality standards. This technique involves injecting molten plastic or other materials into a carefully designed mold that shapes the final product. The medical industry often requires parts to be produced with tight tolerances, ensuring that they function reliably and safely in healthcare applications. Common products manufactured through medical injection molding include syringes, surgical instruments, implants, and diagnostic equipment components. Given the critical nature of these devices, medical injection molding adheres to stringent regulations and standards, such as those set forth by the FDA and ISO certifications. The process also focuses on minimizing contamination risks, which is vital in maintaining the integrity and safety of medical products. By employing advanced technologies and high-quality materials, medical injection molding plays a crucial role in developing innovative solutions that enhance patient care and improve healthcare outcomes.
What is the life expectancy of an injection mold?
The life expectancy of an injection mold can vary significantly based on several factors, including the type of material being molded, the complexity of the mold design, the frequency of use, and the maintenance practices employed. Generally, high-quality molds can last anywhere from 500,000 to over 1 million cycles. However, molds used for high-abrasion materials or in high-volume production scenarios may experience wear and tear more rapidly, potentially shortening their lifespan. To maximize the life expectancy of an injection mold, regular maintenance and proper handling are crucial. This includes routine inspections to identify wear and issues, cleaning the mold after each use to prevent contamination, and making necessary repairs promptly. Additionally, the selection of suitable materials for both the mold and the parts being produced plays a significant role in determining the mold’s longevity. Investing in high-quality materials and employing best practices in mold care can lead to more extended use and better performance, ultimately reducing the cost per part in long-term production.
Does injection molding release fumes?
Yes, injection molding can release fumes during the process. When plastic materials are heated to their melting point for injection, they can emit volatile organic compounds (VOCs) and other hazardous fumes. The composition of the plastic used greatly influences the types and quantities of fumes released. For instance, materials that contain additives, such as colorants or stabilizers, may produce additional fumes when heated. Exposure to these fumes can pose health risks to workers, including respiratory issues and other health problems. To mitigate these risks, it is crucial for manufacturing facilities to have proper ventilation systems in place to effectively remove harmful fumes from the workspace. Additionally, using high-quality materials that produce fewer emissions can help reduce fume generation. Regular monitoring of air quality and implementing safety protocols, such as requiring personal protective equipment (PPE), can further protect workers from exposure to potentially harmful substances during the injection molding process.
What PPE is needed for injection molding?
Personal protective equipment (PPE) is essential in ensuring the safety of workers involved in the injection molding process. Common PPE requirements include safety goggles or face shields to protect against eye injuries from flying particles or hot materials. Additionally, heat-resistant gloves should be worn to prevent burns when handling molds and materials that have been heated to high temperatures. Protective clothing, such as long sleeves and pants made from durable materials, can also help shield workers from potential injuries. In environments where fumes and dust are present, respirators or masks may be necessary to protect against inhalation of harmful substances. Ear protection should be considered in noisy environments to prevent hearing loss from machinery operation. It is vital for employers to provide appropriate training on the correct use of PPE and to ensure that all employees understand the importance of wearing it at all times while working. By adhering to PPE guidelines, facilities can significantly reduce the risk of injuries and promote a safer working environment for injection molding personnel.
What is one disadvantage of injection molding?
One significant disadvantage of injection molding is the high initial cost associated with the design and fabrication of molds. Creating precision molds requires substantial investment in high-quality materials and advanced manufacturing processes. Additionally, the mold-making process itself can be time-consuming, often taking weeks or even months to complete, depending on the complexity of the design. This upfront investment can be a barrier for small businesses or those looking to produce low volumes of products. While injection molding is highly efficient for large production runs and offers the advantage of consistent quality, the economic viability may diminish for smaller-scale operations. Furthermore, once a mold is made, modifications can be costly and challenging, making it essential to get the design right from the outset. Therefore, while injection molding provides numerous advantages in terms of speed and precision for high-volume production, the high initial costs and inflexibility can be a drawback, especially for companies that are testing new product concepts or producing limited quantities.
What are the accidents of injection molding?
Accidents in injection molding can occur due to various factors, primarily related to the machinery and materials involved in the process. One common type of accident is related to equipment malfunction. If the injection molding machine is not properly maintained or operated, it can lead to mechanical failures, which may cause injuries to operators. Additionally, workers can be at risk for burns from hot molten plastic, which is injected at high temperatures. Another potential hazard is the risk of entrapment or crushing injuries if operators are not careful around moving parts or if safety guards are not properly in place. Moreover, there can be slip and fall accidents in the production area due to spilled materials or poor housekeeping. To minimize these risks, companies should implement thorough safety training, maintain equipment regularly, and ensure that proper personal protective equipment (PPE) is used by all workers. Regular safety audits and adherence to industry safety standards can further help in preventing accidents in injection molding environments.
Is injection molding bad for the environment?
Injection molding can have environmental implications, but its impact largely depends on various factors, including the materials used, waste management practices, and the lifecycle of the products manufactured. The process itself generates plastic waste, which, if not managed properly, can contribute to environmental pollution. Furthermore, the production of certain plastics can release harmful chemicals into the atmosphere. However, many companies are increasingly adopting sustainable practices to mitigate these effects. For instance, using recycled materials in the injection molding process can significantly reduce waste. Additionally, advancements in technology have led to the development of more eco-friendly materials that produce fewer emissions. Companies can also minimize their environmental footprint by implementing efficient waste management and recycling programs. While injection molding has its environmental challenges, the industry is evolving to adopt greener practices, and manufacturers are encouraged to explore sustainable materials and methods to lessen their ecological impact.
What are the safety rules for injection molding?
Safety is paramount in injection molding facilities, and several safety rules should be strictly followed to protect workers and ensure a safe working environment. First and foremost, proper personal protective equipment (PPE) must be worn at all times. This includes safety goggles, heat-resistant gloves, and protective clothing to shield against burns or injuries from machinery. Operators should be trained on how to safely operate machinery and understand the potential hazards associated with injection molding. Another critical rule is to maintain clear walkways and work areas to prevent slip and fall accidents. Machinery should be equipped with safety guards to prevent operators from coming into contact with moving parts. Regular maintenance of machines is essential to prevent malfunctions that could lead to accidents. Emergency stops and safety shut-offs must be easily accessible to operators. Lastly, proper handling and storage of materials, as well as effective waste disposal practices, should be implemented to minimize risks. By adhering to these safety rules, injection molding facilities can create a safer workplace for their employees.
Why is injection molding expensive?
Injection molding can be considered expensive for several reasons, primarily related to the initial setup costs and the complexity of the process. One of the main costs is the creation of molds, which require significant investment in high-quality materials and advanced manufacturing techniques. Designing and fabricating a precision mold can take weeks or even months, contributing to the overall expense. Additionally, the machinery used in injection molding is often sophisticated and costly, further increasing the initial investment required for setting up a production line. Moreover, the need for skilled labor to operate these machines and maintain quality control adds to the cost. While injection molding is highly efficient for large production runs and can lower the cost per unit in the long run, the high upfront costs make it less feasible for small batches or prototypes. Therefore, businesses must evaluate the economic implications of injection molding based on their production needs and volume requirements to determine if it is the right choice for their applications.
How many times can an injection mold be used?
The lifespan of an injection mold can vary significantly based on several factors, including the type of material being molded, the complexity of the mold design, and how well the mold is maintained. Generally, high-quality molds can be used for anywhere between 500,000 to over 1 million cycles before they need replacement or extensive repairs. For molds used in precision mold medical applications, where tight tolerances and consistent quality are critical, the lifespan may be influenced by factors such as wear and tear from abrasive materials. Molds that are properly maintained and regularly inspected can last much longer than those that are not cared for. Implementing a regular maintenance schedule, including cleaning, inspections, and necessary repairs, can significantly extend the life of an injection mold. Additionally, the choice of materials and the design of the mold can impact its durability. In short, while molds can have a long lifespan, proper care and material choices are essential to maximize their usage.
What is the contamination of injection molding?
Contamination in injection molding refers to the presence of unwanted substances that can affect the quality and integrity of the molded products. This can occur at various stages of the injection molding process, from the raw material handling to the final product inspection. Common sources of contamination include dust, oils, and foreign particles that may be introduced during the manufacturing process. For instance, if the molding machine or molds are not adequately cleaned, residues from previous materials can mix with new batches, leading to defects such as discoloration or compromised structural integrity. In precision mold medical applications, where product quality is critical, any contamination can result in significant safety and regulatory concerns. To minimize the risk of contamination, strict cleanliness protocols should be established. This includes regular cleaning of machines, molds, and work areas, as well as using filtered air systems and maintaining controlled environments in cleanrooms. Implementing quality control measures, such as in-process inspections and rigorous testing, can further help identify and address contamination issues before they impact production.
How long does injection molding take?
The duration of the injection molding process can vary significantly based on several factors, including the complexity of the part being produced, the type of material used, and the specific design of the mold. Generally, the cycle time for injection molding can range from 15 seconds to several minutes per part. Cycle time includes the entire process, from injection of the molten plastic into the mold to the cooling and ejection of the finished product. For more complex designs, such as those commonly found in precision mold medical applications, the cycle time may be longer due to the additional cooling time required to ensure dimensional stability and quality. Additionally, factors such as mold maintenance, machine setup, and material preparation can influence overall production speed. It’s important to note that while the injection molding process itself may be quick, the design and fabrication of molds can take weeks or even months, depending on their complexity. Therefore, while individual cycles may be short, the total lead time for producing parts can be longer when factoring in the mold creation phase.
What is molding in medical terms?
In medical terms, molding refers to the process of shaping materials, typically plastics or other polymers, into specific forms used for medical devices and components. This process can involve various techniques, with injection molding being one of the most prevalent methods in the healthcare industry. Molding is critical in creating parts that must meet stringent regulatory standards for safety, functionality, and quality. Medical molding applications include a wide array of products, such as syringes, surgical instruments, implants, and diagnostic equipment. The precision and reliability of molded parts are paramount, as they often play a critical role in patient care and outcomes. The term “medical molding” encompasses not only the manufacturing process but also considerations related to material selection, sterilization, and compliance with health regulations. In precision mold medical applications, achieving tight tolerances and high-quality finishes is essential to ensure that the final products perform as intended and meet the necessary safety standards.
Is injection molding easy?
Injection molding is not necessarily an easy process, but it can be highly efficient and effective when properly executed. The complexity of injection molding lies in its multifaceted nature, requiring a thorough understanding of materials, machinery, and design principles. Setting up an injection molding operation involves several steps, including mold design and fabrication, material selection, machine calibration, and process optimization. Each of these aspects demands attention to detail and a strong grasp of engineering and manufacturing concepts. Additionally, while the actual molding process may be straightforward—injecting molten material into a mold—the challenges arise in maintaining quality control, achieving tight tolerances, and minimizing defects. In precision mold medical applications, the stakes are even higher, as any inaccuracies can compromise product safety and effectiveness. Thus, while the injection molding process can be automated for efficiency, it requires skilled operators and engineers to oversee operations, troubleshoot issues, and ensure consistent quality. Ultimately, with the right expertise and preparation, injection molding can be a highly productive manufacturing method, but it is not without its complexities.
How to tell if something has been injection molded?
Identifying whether an object has been made through injection molding involves examining several characteristics of the item. One of the most recognizable features is the presence of mold lines or parting lines, which are often visible along the edges where the two halves of the mold meet. These lines can sometimes be subtle but can usually be felt or seen on the surface of the molded product. Additionally, injection-molded items often have a glossy finish, which is a result of the mold’s polished interior surface. Another telltale sign is the presence of ejector pin marks, which are small indentations left by the pins that help eject the part from the mold. These marks can be found on the surface of the product, typically in less visible areas. The overall uniformity and precision of the part dimensions can also indicate injection molding, as this process produces parts with high consistency and accuracy. Lastly, products made from complex geometries with intricate details are often indicative of injection molding, as this method excels in creating such designs efficiently.
What is the difference between injection and reaction injection molding?
The primary difference between injection molding and reaction injection molding (RIM) lies in the materials and processes used. In traditional injection molding, thermoplastic materials are heated until they become molten, then injected into a mold where they cool and solidify. This method is ideal for producing high volumes of parts with consistent properties and can accommodate a wide range of thermoplastics. In contrast, reaction injection molding involves a chemical reaction between two or more components, such as isocyanates and polyols, which react in the mold to form a thermosetting polymer, typically polyurethane. This process allows for the production of larger and more complex parts while also enabling the incorporation of additives or fillers during the mixing stage. Additionally, RIM is suitable for creating parts with varying densities and excellent surface finishes. While injection molding is typically faster for smaller, high-volume runs, RIM is advantageous for larger components or those requiring lightweight materials with high strength. Both methods have their applications, but the choice depends on the specific requirements of the product being manufactured.
What is the disadvantage of reaction injection molding?
One significant disadvantage of reaction injection molding (RIM) is the longer cycle time compared to conventional injection molding. The chemical reaction that occurs during the RIM process requires time to fully cure before the part can be removed from the mold, which can slow down production rates. This extended cycle time may not be suitable for high-volume applications where rapid production is essential. Additionally, the initial setup costs for RIM can be higher due to the need for specialized molds and materials, which may be a barrier for some manufacturers. Furthermore, RIM can have limitations regarding the materials used; while it is excellent for producing certain thermosetting plastics, it may not accommodate a wide variety of materials like traditional injection molding can. This can restrict design choices and material properties for specific applications. Lastly, managing the chemical reaction during the RIM process can introduce challenges related to quality control, as variations in the mixing ratios or reaction conditions can lead to inconsistencies in the final product. Overall, while RIM offers unique advantages for certain applications, these disadvantages should be carefully considered when choosing the appropriate manufacturing method.
What is the difference between injection molding and molding?
Injection molding and molding are terms that are often used interchangeably, but they refer to different aspects of the manufacturing process. Molding is a broader term that encompasses various methods of shaping materials, including compression molding, blow molding, and injection molding. Injection molding is a specific type of molding where molten material, usually plastic, is injected into a mold cavity under pressure.
The key difference lies in the method of material application. In injection molding, the material is heated until it becomes liquid and then injected into a mold, where it cools and solidifies into the desired shape. This process is highly efficient for producing complex parts with precise dimensions and high repeatability.
In contrast, the term “molding” can refer to any method of forming materials into shapes, including those that do not involve injection. For example, compression molding involves placing a material into a heated mold and applying pressure to shape it, without the injection step. Therefore, while all injection molding is a form of molding, not all molding is injection molding. The choice of method depends on the specific requirements of the part being produced.
Is injection molding the same as injection compression molding?
Injection molding and injection compression molding are related processes but have distinct differences. Injection molding is the more common method in which molten plastic is injected into a mold cavity under high pressure. This method allows for the creation of complex shapes with tight tolerances, making it suitable for high-volume production of plastic parts.
On the other hand, injection compression molding combines elements of both injection and compression molding. In this process, the molten material is injected into a partially open mold, and then the mold is closed to compress the material into the final shape. This method is often used for thermosetting plastics and can be advantageous for producing larger parts with lower internal stresses compared to traditional injection molding.
The primary difference between the two processes lies in the way the material is handled during the molding cycle. While injection molding fills the mold entirely with molten material under pressure, injection compression molding allows for a compression phase that can improve material flow and reduce cycle times for certain applications. Ultimately, the choice between these methods will depend on the specific design requirements and material properties needed for the final product.
What is injection molding in dentistry?
Injection molding in dentistry refers to a specialized application of the injection molding process used to create dental products and components. This method is particularly useful for producing precise and intricate items such as dental crowns, bridges, dentures, and orthodontic devices. In this context, dental materials, often made from thermoplastics or thermosetting resins, are heated until they become molten and then injected into molds designed to replicate the desired dental shapes.
The use of injection molding in dentistry offers several advantages, including high accuracy in producing complex geometries and the ability to create multiple identical parts efficiently. This is especially important in dental applications, where precision is critical for the proper fit and function of dental appliances. Additionally, injection molding allows for the incorporation of specific properties, such as color and translucency, which can enhance the aesthetic appearance of dental products.
Overall, injection molding plays a vital role in modern dentistry, enabling the production of high-quality, durable, and aesthetically pleasing dental components that improve patient outcomes and satisfaction.
What are the four types of molding?
The four main types of molding processes used in manufacturing include injection molding, blow molding, compression molding, and rotational molding.
Injection Molding: This is one of the most common methods, where molten plastic is injected into a mold cavity under high pressure. It is ideal for producing high volumes of precise and complex parts, making it widely used in industries such as automotive, consumer goods, and medical devices.
Blow Molding: This process is primarily used for producing hollow plastic parts, such as bottles and containers. It involves inflating molten plastic inside a mold to form a hollow shape. Blow molding can produce high volumes of lightweight products efficiently.
Compression Molding: In this method, a pre-measured amount of material is placed into an open mold, and pressure is applied to shape the material. Compression molding is often used for rubber and thermosetting plastics and is suitable for producing large parts.
Rotational Molding: This process involves placing a powdered material into a mold that is then heated and rotated along two axes. The powder melts and coats the interior of the mold, forming a hollow part. Rotational molding is commonly used for producing large, hollow products such as tanks and playground equipment.
What is the medical device molding process?
The medical device molding process is a specialized form of injection molding specifically tailored for the manufacturing of medical components and devices. Given the critical nature of medical applications, this process adheres to stringent regulatory standards and focuses on producing high-quality, biocompatible parts.
The process begins with material selection, where manufacturers choose suitable thermoplastics or thermosetting plastics that meet the requirements for safety and functionality. Common materials used in medical molding include polycarbonate, polypropylene, and various silicone compounds.
Once the appropriate material is selected, the molding process itself typically involves the following steps:
Design and Prototyping: Initial designs are created, and prototypes are developed to test form, fit, and function.
Mold Fabrication: High-precision molds are designed and manufactured to produce the desired shapes and features of the medical devices. This step is crucial, as molds must be capable of maintaining tight tolerances to ensure safety and efficacy.
Injection Molding: Molten material is injected into the mold under high pressure. The cooling and solidification phase is carefully controlled to achieve the desired properties in the final product.
Quality Control and Testing: Rigorous inspections and testing are conducted to ensure that the molded components meet regulatory requirements and specifications. This can include tests for dimensional accuracy, strength, and biocompatibility.
Sterilization and Packaging: Many medical devices require sterilization before use, and appropriate packaging is essential to maintain sterility until the product is needed.
What is the market for medical injection molding?
The market for medical injection molding is a vital and growing segment within the medical device manufacturing industry. This market includes the production of precision components for medical equipment, devices, and implants. With advancements in healthcare technology, there is an increasing demand for complex, high-quality parts such as syringes, surgical tools, diagnostics, and drug delivery systems. The medical injection molding market benefits from the need for sterile, reliable, and cost-effective solutions. The growth of the aging global population, coupled with a rising demand for minimally invasive medical procedures, further drives this market. Additionally, regulatory requirements like FDA approval for medical devices necessitate high standards in the manufacturing process. This industry is expected to continue expanding as innovations in medical technologies emerge, offering manufacturers opportunities to innovate with materials like biocompatible plastics and to capitalize on the need for mass production of high-precision medical components.
What is an injection molding job?
An injection molding job refers to a role in the manufacturing process where plastic or other materials are injected into a mold to create a desired shape. This process is widely used for producing high-volume, precise parts in various industries, including medical device manufacturing. In the context of medical injection molding, the job typically involves setting up and operating machines that inject materials such as medical-grade plastics into molds to create components like syringes, catheters, or implants. Workers in this field must ensure the molds are properly maintained, the correct materials are used, and the machines are set to the right specifications. The job also requires attention to detail and an understanding of quality control, as medical components must meet strict regulatory standards. Injection molding jobs may also involve design, troubleshooting, and process optimization to improve efficiency and product quality in the production of medical devices.
How much is an injection mold?
The cost of an injection mold can vary significantly based on the complexity of the design, materials used, and the size of the mold. For medical injection molding, the price is typically higher due to the stringent quality standards and the need for precision. A basic injection mold may cost anywhere from $1,000 to $5,000, while more intricate and specialized molds, such as those required for medical device production, can range from $10,000 to $100,000 or more. Additional costs include mold maintenance, modifications, and testing. The need for sterilization, biocompatibility, and compliance with regulations like ISO 13485 and FDA standards for medical device manufacturing can also increase the cost of the mold. High-quality medical molds often require premium materials like stainless steel, which adds to the overall price. Despite the initial investment, injection molding is a cost-effective solution for high-volume production, as the cost per part decreases significantly with large quantities.
Is injection molding a good career?
Yes, injection molding can be a rewarding career, especially in sectors like medical device manufacturing. As the industry continues to grow, skilled professionals in injection molding are in high demand. Careers in this field offer competitive salaries, job stability, and opportunities for career advancement. Roles include machine operators, mold designers, engineers, quality control specialists, and technicians. For those with a background in mechanical engineering, materials science, or industrial design, injection molding presents an opportunity to work on cutting-edge technologies, such as producing medical devices with intricate designs and high standards. Additionally, medical injection molding requires professionals to adhere to strict regulatory guidelines, offering job security and potential for specialization. With ongoing advancements in automation, robotics, and 3D printing, injection molding professionals can also stay at the forefront of technological progress. Overall, the sector provides diverse career paths and the chance to contribute to important innovations in healthcare.
Let’s Create Great Things—Get a Quote Today
Contact our professional team now for a same-day quote and risk-free project evaluation. Benefit from ISO 8 cleanrooms, advanced machines, and 12-hour fast response in medical injection molding.