Injection molding is a versatile manufacturing process that involves injecting molten material into a precisely designed mold to produce complex and consistent shapes. In the medical industry, the medical injection molding process, often utilizing precision mold medical techniques, is essential for creating a wide range of medical devices, including syringes, implants, and diagnostic tools. This process ensures high precision, reliability, and adherence to strict regulatory standards, making it indispensable for producing components that require exact specifications and safety. The medical injection molding process melts plastic, injects it into molds under pressure, cools it, and forms precise medical devices.
Low-Volume to High-Volume Production Capabilities
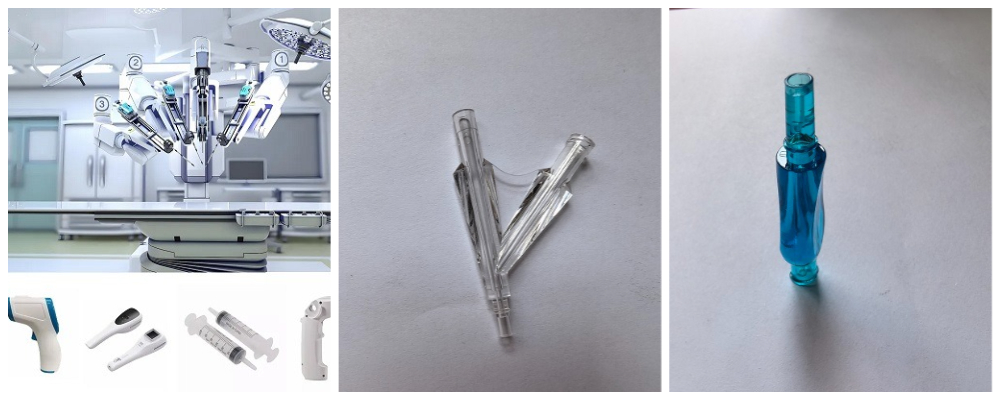
Attributes | Details |
---|---|
Place of Origin | Dongguan, Guangdong, China |
Brand Name | LY Medical Injection Mold |
Product Name | Medical Injection Molding |
Material | Plastic |
Plastic Material | ABS/PP/PS/PE/PVC/PA6/PA66.....etc. |
Application | Medical Industry |
Drawing Format | 2D/(PDF/CAD)3D(IGES/STEP) |
Process | Injection Molding |
Processing Service | Molding, Injection Plastic |
Service | Custom OEM |
Certification | ISO9001 |
Size | Custom Size |
Color | Custom Color |
Logo | Customer Logo |
Shape | Customer Design |
Surface Treatment | Custom Surface Texture |
Features | Durable, High Precision |
OEM/ODM | OEM ODM Available |
Minimum Order Quantity | 1 Piece |
Packing Details | According to Customer Requirement |
What is the Medical Injection Molding Process?
Definition and Basic Principles
Medical Injection Molding Defined
- medical injection molding process is a specialized manufacturing technique used to create precise and complex medical components by injecting molten materials into custom-designed molds.
Basic Principles
- Utilizes high-precision molds to ensure consistency and accuracy in each produced part.
- Involves cycles of material injection, cooling, and medical injection molding process release to achieve high-volume production.
Comparison with Other Manufacturing Processes
- Versus Machining: Unlike subtractive machining, which removes material, injection molding adds material only where needed, reducing waste.
- Versus 3D Printing: Offers higher production rates and better consistency for mass manufacturing compared to additive 3D printing methods.
Significance in Medical Device Production
Precision and Reliability
- Ensures that each medical device meets strict regulatory standards and performance specifications.
Examples of Commonly Molded Medical Devices
- Syringes: High-volume production with consistent dimensions and functionality.
- Implants: Customizable shapes and materials for patient-specific applications.
- Diagnostic Tools: Accurate components for reliable medical diagnostics.
- Disposable Medical Supplies: Cost-effective and hygienic production of items like tubing and connectors.
Medical Injection Manufacturing Process
Material Selection: Choosing biocompatible and durable materials suitable for medical applications.
Mold Design: Creating precise molds that can produce intricate shapes required for medical devices.
Injection: Injecting molten material into the mold under controlled conditions to ensure uniformity.
Cooling: Allowing the material to solidify within the mold to maintain structural integrity.
Post-Processing: Finishing steps such as trimming, sterilization, and quality inspection to meet medical molding requirements.
The injection molding process usually takes between 2 seconds and 2 minutes and has four stages: clamping, injection, cooling, and ejection.
Why the Medical Injection Molding Process is Widely Used in the Medical Industry
The medical injection molding process has become a cornerstone of manufacturing in the medical industry due to its ability to produce strong, durable equipment with exceptional precision, such as OEM medical injection molding for injection molding medical devices. Metal injection molding medical further enhances this process, allowing for the production of components with superior strength and precision. Medical devices require exact dimensions and consistent quality to ensure they meet stringent regulatory and safety standards. The process achieves this by forming components with precise measurements and a high-quality surface finish, crucial for devices such as syringes, surgical instruments, and implantable devices.
A key reason for its popularity is the cleanroom manufacturing environment. Clean room injection molding is conducted in sterile conditions to eliminate bacteria, dust, and other contaminants, ensuring the safety and reliability of the medical products. This cleanliness is vital for devices that come into direct contact with the human body or are used in sensitive procedures.
Moreover, injection molding is cost-effective for mass production, maintaining quality across high volumes. Its ability to combine efficiency, precision, and cleanliness makes it indispensable in medical manufacturing.
The Medical Injection Molding Process: Applications and Examples of Injection Molding Medical Products
Types of Medical Products Manufactured
Syringes
- High precision and consistency in production.
- Ensures accurate dosing and reliable performance.
Catheters
- Custom shapes and sizes for various medical procedures.
- Enhanced flexibility and durability through the medical injection molding process.
Implants
- Biocompatible materials tailored for patient-specific needs.
- Precise manufacturing ensures proper fit and functionality.
Blood Bags
- Durable and sterile packaging solutions.
- Consistent quality to maintain blood integrity.
More
- Includes disposable and reusable medical devices requiring high precision.
Innovative Applications
Smart Medical Devices
- Integration of electronics with molded components.
- Facilitates advanced functionalities and connectivity.
Biodegradable Implants
- Development of implants that safely dissolve after use.
- Reduces the need for additional surgeries.
Personalized Medicine
- Tailoring devices to individual patient specifications.
- Enhances treatment effectiveness and patient comfort.
Advanced Diagnostic Tools
- Improved accuracy through precise molding techniques.
- Enables more reliable diagnostic procedures.
Sustainable Materials
- Use of eco-friendly materials in the medical injection molding process.
- Promotes environmental sustainability in medical manufacturing.
Case Studies
Case Study 1: Enhanced Syringe Production
Utilized the medical injection molding process to improve accuracy. Resulted in reduced manufacturing costs and increased production efficiency.
Case Study 2: Customizable Implants
Employed the medical injection molding process to create patient-specific implants. Achieved higher biocompatibility and better patient outcomes.
Case Study 3: Disposable Blood Bags
Implemented the medical injection molding process for producing sterile blood bags. Ensured durability and compliance with medical standards.
Validation Injection Molding Processes Medical Devices
Ensuring Compliance
Adhering to stringent regulatory standards through validated processes. Guarantees that medical devices meet all necessary safety and quality requirements.
Quality Assurance
Conducting rigorous testing to maintain high standards in the medical injection molding process.
Ensures consistency and reliability of the final products.
Process Optimization
Enhancing efficiency and reliability in the production of medical devices. Utilizes data-driven approaches to refine the medical injection molding process.
Documentation and Traceability
Maintaining comprehensive records for validation of injection medical molding processes medical devices. Facilitates easy tracking and verification during audits and inspections.
Medical Injection Molding Process Techniques
The medical injection molding process is a cornerstone of modern healthcare manufacturing, enabling the precise and mass production of medical components. Including medical component molding, which plays a key role in ensuring the reliability and functionality of healthcare products. Below, we explore the various molding techniques integral to creating these essential devices.
Types of Injection Molding Used in Medical Devices
Regular Plastic Injection Molding
Regular plastic injection molding is a fundamental method in the medical injection molding process, designed to create standard medical components. This process, such as thermoplastic injection molding medical, involves melting thermoplastic materials and injecting them into moldsto form items like syringes, vials, and housings for medical instruments. The use of high precision tools for medical device manufacturing ensures that these components meet the exacting standards required for medical applications. It is widely used for its consistency, speed, and ability to produce complex shapes at a high volume, making it ideal for medical device manufacturing.
Insert Molding
Insert molding combines plastic with other materials, such as metals or electronics, during the medical injection molding process. This technique is ideal for creating hybrid medical devices, like catheters with embedded sensors or surgical tools with integrated metal inserts. It ensures strong adhesion between materials, improving device reliability.
Overmolding
Overmolding enhances the functionality and ergonomics of medical products by layering materials. In the medical injection molding process, this technique is often employed to add soft grips to surgical tools or to create multi-material components like blood analysis devices. It allows manufacturers to combine different properties, such as rigidity and softness, in a single device.
Liquid Silicone Injection Molding
Liquid medical silicone injection molding is pivotal in producing flexible and biocompatible components, such as seals, gaskets, and implantable devices. This specialized technique within the medical injection molding process ensures products meet strict medical-grade standards for safety, durability, and comfort. Its low-temperature curing process makes it suitable for delicate applications.
Injection Molding Process Medical Devices
The injection molding process medical devices production involves several crucial steps tailored to meet the stringent requirements of the healthcare industry:
- Material Selection
Medical-grade plastics, such as polyethylene, polypropylene, and liquid silicone rubber, are chosen for their biocompatibility, chemical resistance, and strength. - Design and Prototyping
Computer-aided design (CAD) and simulation tools are used to create precise molds and prototypes, ensuring optimal fit and functionality. - Mold Fabrication
High-precision molds, often made from steel or aluminum, are crafted to meet the exact dimensions and tolerances required by medical standards. - Injection Molding Execution
During the medical injection molding process, materials are melted, injected, and cooled to form the desired shapes. Advanced machines maintain consistent temperatures and pressure for uniformity. - Quality Assurance
Rigorous testing, including visual inspections and functional assessments, ensures that medical devices meet all regulatory and safety standards.
Advantages of the Medical Injection Molding Process
- Precision and Consistency: The medical injection molding process allows for the production of highly detailed and consistent parts, essential for critical medical applications.
- Scalability: This process can efficiently produce thousands of identical parts, making it ideal for high-demand medical supplies like syringes and surgical instruments.
- Cost-Effectiveness: Once molds are fabricated, the process offers a cost-effective solution for large-scale manufacturing.
- Material Versatility: A wide range of medical-grade plastics and silicones can be used, catering to diverse healthcare needs.
- Durability: Plastics used in injection molding offer exceptional durability, making them ideal for medical applications. These materials can endure harsh environmental conditions, including exposure to high heat, blunt force, and vibration, without cracking or breaking. Additionally, they maintain their shape and integrity even after repeated sterilization cycles in autoclaves, ensuring long-lasting performance in demanding healthcare environments.
- Resistance to Contamination: Medical-grade plastics used in injection molding are highly resistant to contamination. They inherently repel contaminants and require minimal sterilization to maintain sterility. This characteristic enables them to meet stringent FDA standards and regulatory requirements, making them reliable and safe for medical use.
By leveraging the medical injection molding process, manufacturers deliver safe, reliable, and innovative medical devices that improve patient care and advance healthcare technology.
Medical Grade Materials for Medical Injection Molding Process
Medical-grade materials are specially designed to meet the stringent requirements of healthcare applications, offering biocompatibility, durability, and resistance to environmental stress. Here is a breakdown of some of the most widely used materials in medical injection molding:
Polyetheretherketone (PEEK)
PEEK is a premium thermoplastic valued for its resistance to radiation, chemicals, high temperatures, and wear. Its outstanding dimensional stability under stress makes it ideal for surgical implants and other critical medical applications. PEEK’s robustness ensures reliability even in harsh environments, making it a preferred choice for advanced medical devices.
Polyethylene (PE)
Polyethylene is a durable polymer with impressive tensile strength and biocompatibility. Resistant to sterilization and harsh conditions, it is extensively used for joint prostheses, pharmaceutical containers, tubing, and medical connectors, combining reliability with versatility.
Polycarbonate (PC)
Polycarbonate is transparent, tough, and flexible with excellent mechanical properties. Its resistance to abrasion and compatibility with bodily tissues make it perfect for manufacturing protective medical equipment, clear masks, and oxygenators. In medical atomization mask injection molding processing, polycarbonate is often selected for its strength and clarity, ensuring that the masks are both durable and allow for clear visibility during use. This material’s ability to withstand sterilization processes and its biocompatibility make it a reliable choice for medical devices, ensuring safety and effectiveness in treatments.
Polypropylene (PP)
Polypropylene’s resistance to cracking, radiation, and temperature makes it indispensable in healthcare. It is used to manufacture syringes, knee and hip replacements, and connectors, offering durability and precision in life-saving applications.
Silicone
Known for its flexibility and chemical inertness, silicone is widely used in medical-grade products such as catheters, tubing, and connectors. Its biocompatibility and adaptability make it ideal for devices requiring high mechanical performance and tissue compatibility.
Polystyrene (PS)
Polystyrene, while less flexible, offers exceptional dimensional stability and is compatible with body tissues. It is commonly used for creating petri dishes, culture trays, and diagnostic components, ensuring precision and reliability in laboratory settings.
These medical-grade materials ensure safety, reliability, and high performance in the production of medical devices. Each material offers unique properties tailored to specific healthcare applications, enabling the creation of advanced and life-saving medical technologies.
How to Choose the Right Medical Injection Molding Material
Selecting the right material for medical injection molding is crucial for ensuring the functionality, safety, and reliability of the final product. Here are the key factors to consider:
Durability and Strength
In medical applications, materials must be robust to avoid breakage during critical moments. Fragile materials can compromise patient safety and device effectiveness. For applications requiring resistance to shattering, cracking, or mechanical stress, select materials with proven durability, such as polyetheretherketone (PEEK) for implants or polycarbonate (PC) for surgical tools.
Operating Conditions
The material must align with the environmental demands of its application:
- High-Temperature Resistance: For components subjected to repeated sterilization, such as autoclaving, materials like polypropylene (PP) are ideal.
- Flexibility and Wear Resistance: For applications requiring flexibility and durability under stress, such as tubing or connectors, consider materials like silicone or polycarbonate.
Understanding the operational needs of the component ensures reliability in diverse medical settings.
Ease of Use and Ergonomics
The usability of the part plays a significant role in material selection. For instance:
- Ergonomic Design: Surgical instruments should be lightweight and comfortable to handle to enhance performance during procedures.
- Sterilization-Friendly: Materials like polyethylene (PE) or polypropylene (PP) are excellent for devices that require easy sterilization and cleaning.
- Functionality: Choose materials that provide an optimal balance of strength, flexibility, and usability, ensuring that they meet both clinical and practical needs.
By evaluating these factors—durability, operating conditions, and ease of use—you can identify the most suitable medical-grade plastic for your specific application. This approach ensures the safety, reliability, and efficiency of the final medical product.
Integrating Electronics: Insert Molding Electronics in the Medical Injection Molding Process
The integration of electronics through insert molding is revolutionizing the medical device industry. By combining advanced materials with electronic components, this process elevates the functionality and performance of medical devices, seamlessly supporting the medical injection molding process.
What is Insert Molding Electronics?
- Definition and Process
Insert molding electronics is a specialized technique that embeds electronic components, such as sensors, circuits, or wires, into plastic or silicone molded parts during the medical injection molding process. The process ensures that the electronic elements are securely encapsulated, offering protection from environmental factors like moisture, chemicals, and mechanical stress. - Precision and Integration
This method allows precise placement of delicate electronic parts, ensuring they maintain functionality and structural integrity throughout the molding process.
Benefits for Medical Devices
Enhanced Functionality
- Insert molding electronics enables the creation of smart devices, such as diagnostic tools with integrated sensors, capable of providing real-time feedback.
Durability and Protection
- The encapsulation of electronics during the medical injection molding process shields components from wear and tear, ensuring longer device lifespans.
Miniaturization
- This process supports the development of compact and lightweight medical devices, ideal for portable or implantable applications.
Cost-Effectiveness
- By combining multiple steps into one seamless process, manufacturers save time and reduce production costs while maintaining high precision.
By combining the medical injection molding process with insert molding electronics, manufacturers can produce innovative, high-performing medical devices that meet the rigorous demands of modern healthcare.
FAQs about Medical Injection Molding Process
Clamping: The first step involves securing the two halves of the mold together. This is done using a clamping unit that holds the mold under pressure to ensure that it remains closed while the plastic is injected.
Injection: In this step, melted plastic is injected into the mold cavity. The plastic is heated in the injection molding machine until it becomes liquid and is then forced into the mold under high pressure.
Dwelling: After the molten plastic fills the mold, pressure is applied to ensure that all cavities are filled and the plastic conforms to the shape of the mold. This helps in eliminating any defects or incomplete fill.
Cooling: During this stage, the plastic inside the mold is allowed to cool and solidify. The mold remains closed to maintain the shape of the product as the plastic hardens.
Ejection: Once the plastic has sufficiently cooled, the mold is opened, and the finished product is ejected from the mold. The cycle is then repeated for the next part.
Filling: This stage involves injecting the molten plastic into the mold cavity at high pressure and speed, filling it entirely.
Packing: Once the mold is filled, pressure is maintained to allow more material to be packed into the mold to compensate for shrinkage that might occur during cooling.
Cooling: After packing, the material is allowed to cool and harden within the mold, maintaining the shape of the finished part.
Ejection: Once adequately cooled, the mold opens, and the solidified part is ejected. This is crucial to ensure the part keeps its design integrity without deforming.
Medical molding refers to the specialized process of manufacturing medical-grade components using injection molding techniques. It is tailored to meet stringent regulatory and cleanliness standards applicable to medical products. Primarily, it involves using biocompatible and sterilizable materials to produce parts that are safe for direct or indirect contact with the human body. These might include surgical instruments, medical device components, and other healthcare-related items. The process demands precision and often involves cleanroom environments to minimize contamination risks. The materials used are usually subjected to rigorous testing to ensure compliance with medical standards like ISO 13485. This sector of molding is crucial as it contributes to enhanced patient safety, reliability, and efficacy of medical devices.
Injection molding is a detailed process comprising several steps, allowing for the efficient production of plastic parts.
Firstly, the plastic pellets or granules are fed into the hopper of the injection molding machine. The material is then transferred to a barrel where it is heated until it turns into a molten state. This step is crucial as it prepares the material for injection.
Next, the mold closes, and the molten plastic is injected into the mold cavity through a screw or ram. The design of the cavity determines the shape of the finished product. High pressure ensures every nook and cranny of the mold is filled, thereby creating a detailed and precise part.
After filling, the cooling stage begins, wherein the plastic material solidifies within the mold, retaining the cavity’s shape. The mold remains closed during this period to ensure the integrity of the shape.
Once cooled, the ejector pins are activated to expel the solid part from the mold. The cycle then repeats for the next piece, making injection molding an efficient and repeatable process ideal for mass production.
Medical injection molding starts with loading medical-grade polymers into a hopper. These materials are heated in a barrel until molten. The molten material is injected into a pre-designed steel or aluminum mold under high pressure. The mold is engineered to form the exact shape and dimensions of the medical component.
Once inside the mold, the material cools and solidifies. After cooling, the mold opens, and the newly formed component is ejected. This process ensures precision, repeatability, and compliance with stringent medical standards.
Medical-grade polymers used are biocompatible, sterilizable, and tailored for use in devices like IV connectors or surgical instruments. Quality control measures, including dimensional checks and sterilization validations, ensure the end product is safe and functional for medical applications.
The anatomy of medical injection molding includes:
Material: Biocompatible polymers (e.g., silicone or thermoplastics) chosen for sterilizability and performance.
Injection Unit: Melts and injects material into the mold. Precision controls are critical to meet medical specifications.
Mold: A customized cavity designed for specific medical components, like catheter tips or implantable devices.
Clamping Unit: Holds the mold securely, preventing defects during injection.
Cooling System: Ensures the part solidifies quickly and accurately.
Ejector System: Removes the finished part without contamination.
This integrated setup enables mass production of medical-grade components with strict adherence to safety and quality standards, meeting regulatory requirements such as FDA or ISO certifications.
Creating a mold for medical injection molding can take 8 to 16 weeks, depending on the complexity, materials, and regulatory requirements. Medical molds often require advanced features like multi-cavities for high-volume production or intricate designs for specialized components.
The mold-making process includes CAD design, material selection (usually stainless steel for durability), machining, and quality testing. For medical applications, additional time may be needed for compliance checks, such as biocompatibility, sterilization validation, and alignment with ISO 13485 standards.
While time-consuming, this process ensures the mold meets stringent medical safety and precision requirements, crucial for producing sterile and accurate medical devices.
The cost of medical injection molding varies based on factors like mold complexity, material choice, and production volume. A mold for medical components typically costs $10,000 to $100,000 or more due to the high precision required.
Per-part costs can range from $0.10 to $10, depending on the part’s size and complexity. Materials like medical-grade thermoplastics or silicones also influence costs.
Although expensive upfront, injection molding becomes cost-effective for large production runs, as the mold can produce millions of identical components with low variability, ensuring compliance with strict medical regulations.
While both processes shape materials, medical injection molding forms complex, three-dimensional parts like syringes, while extrusion creates continuous shapes, such as tubing. Injection molding uses a mold cavity, enabling intricate designs, whereas extrusion pushes material through a die to produce uniform, linear products.
Medical injection molding suits high-precision components requiring strict tolerances and repeatability, while extrusion is ideal for medical tubing or catheter production. Both processes use medical-grade materials but cater to different design and application needs.
Medical injection molding is a specialized manufacturing process for creating precise, sterile components for medical devices. It uses biocompatible polymers, such as thermoplastics and silicones, ensuring products meet strict health and safety standards.
Applications include producing syringes, implantable devices, and diagnostic tools. The process requires cleanroom conditions to maintain sterility, along with compliance with regulatory standards like FDA and ISO 13485.
This method offers high precision, scalability, and cost-efficiency, making it ideal for producing consistent, high-quality medical components critical to healthcare and patient safety.
Contact our professional team now for a same-day quote and risk-free project evaluation. Benefit from ISO 8 cleanrooms, advanced machines, and 12-hour fast response in medical injection molding.