Injection molding plays a crucial role in the medical industry, providing a cost-effective and efficient solution for manufacturing high-precision components. As the demand for advanced medical devices continues to rise, the need for precise, reliable, and affordable production methods has become increasingly important. The injection of precision mold medical services have proven essential in meeting these demands by offering a streamlined process that ensures consistent quality, fast turnaround times, and the ability to create complex geometries. This technology enables the production of a wide range of medical components, from surgical tools to implantable devices, all while maintaining the high standards required in healthcare applications. By utilizing medical injection molding, manufacturers can meet the stringent regulatory requirements and enhance the safety and reliability of medical products. FUJIU Medical Injection Mold provides medical injection molding services with design support, prototyping, and cost-efficient solutions for precision medical parts.
Low-Volume to High-Volume Production Capabilities
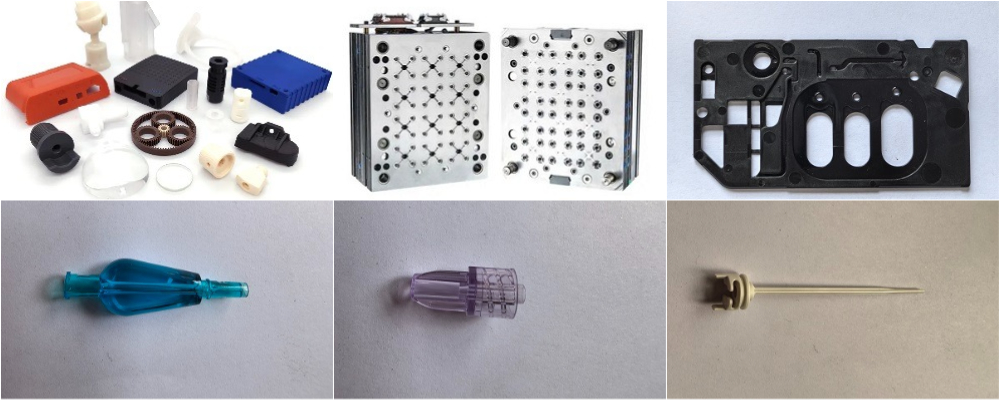
Attributes | Details |
---|---|
Place of Origin | Dongguan, Guangdong, China |
Brand Name | LY Medical Injection Mold |
Product Name | Medical Injection Molding |
Molding Mode | Plastic Injection Mold |
Model | Customized |
Quality | ROHS Standard |
Size | According to Your Drawing |
Structure | According to Your Drawing |
Color | Customized |
Cavity | According to Customer Requirements, Single Cavity or Multi-cavity |
Plastic Material | PP, PC, PS, PA6, POM, PE, PU, PVC, ABS, PMMA etc |
Surface Treatment | Anodizing, Polishing, Powder Coating, Screen Printing, Painting, etc. |
Mold Life | 50,000 to 1,000,000 shots |
Service | OEM ODM Customization |
Design Software | UG/CAD |
Mold Frame | European Standard, World Standard, According to Customer Requirements |
Tolerance | 0.01-0.05mm |
Logo | Customized Logo Acceptable |
Application | Medical, Laboratory Areas |
Features | High Precision |
Certification | ISO9001/ISO13485 |
Supply Capacity | 2000 per Month Pieces |
Packaging | Plastic Bag Packaging or Packaging According to Customer Requirements |
Transportation | By Sea or Air According to Customer Requirements |
What Are Medical Injection Molding Services?
Medical injection molding services refer to the specialized process of using injection molding technology to create precise and high-quality components for medical devices. This advanced manufacturing technique involves injecting melted medical-grade plastic materials into custom-designed molds to produce parts that meet strict healthcare standards. Injection molding is essential for the production of medical devices due to its efficiency, cost-effectiveness, and ability to create complex parts with high precision.
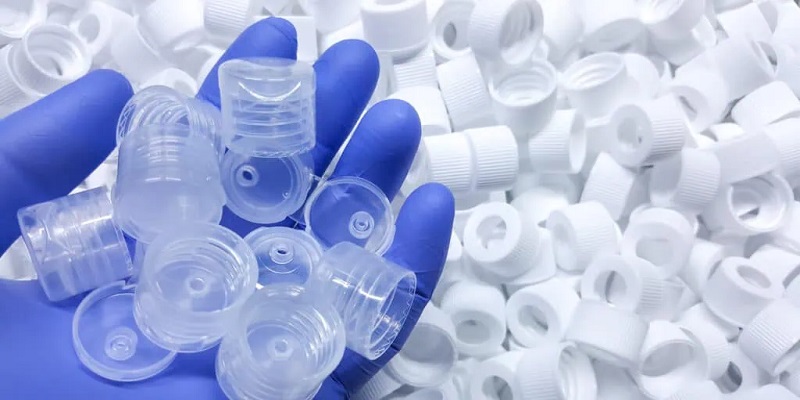
Definition of Injection Molding and Its Significance in Medical Device Manufacturing
Injection molding is a manufacturing process in which molten material, often plastic or metal, is injected under high pressure into a mold cavity to produce parts. In the context of medical devices, medical injection molding services primarily use medical-grade plastics that comply with regulatory standards, ensuring that the resulting components are safe for use in medical environments.
The significance of injection molding in medical device manufacturing cannot be overstated. It enables the production of high-quality components that are precise, consistent, and cost-effective. Medical device manufacturers depend on injection molding to create intricate, durable parts with tight tolerances, which are essential for devices that require high performance and reliability, such as surgical instruments, diagnostic equipment, and implantable devices.
Types of Medical Devices Commonly Produced
Medical injection molding services cater to a wide range of devices and components used in various healthcare applications. Some of the most common medical devices produced using injection molding include:
- Surgical Tools: Precise and durable instruments like scalpels, forceps, and scissors are often manufactured using injection molding. The process ensures that these tools meet strict specifications for functionality and safety.
- Implantable Devices: Components used in implants, such as pacemaker housings, joint replacements, and dental implants, are typically produced through injection molding. The precision required for these devices ensures a better fit and reduces the risk of complications.
- Syringes and Injectors: Disposable syringes and auto-injectors are essential in healthcare settings. Injection molding is widely used to create the complex shapes and fine details required for these devices, ensuring safety and accuracy.
- Catheters: Catheters, used for a variety of medical treatments, require a high degree of precision and quality to ensure they function as intended. Medical injection molding services can produce catheters with intricate designs, fine walls, and specific material properties to prevent infection and complications.
- Diagnostics and Monitoring Devices: Parts for diagnostic tools, such as blood glucose meters, thermometers, and pulse oximeters, are also commonly produced via injection molding. These devices require precise parts for consistent and accurate performance.
Explanation of the Molding Process
The injection molding process for medical components follows a precise series of steps to ensure quality and compliance with medical standards. Here’s a breakdown of the process:
- Material Preparation: Medical-grade plastics are selected based on the requirements of the medical device. These plastics must meet stringent standards for biocompatibility, sterilization, and strength. Materials are typically in the form of pellets before being processed.
- Melting the Material: The pellets are heated to a molten state in the injection medical molding machine. The temperature must be carefully controlled to avoid degradation of the material, ensuring the final product’s integrity.
- Injection into Molds: The molten plastic is injected into a pre-designed mold cavity under high pressure. The mold is typically made from steel or aluminum and is designed to the exact specifications required for the medical device part.
- Cooling and Solidifying: After the material is injected into the mold, it cools and solidifies. The cooling time depends on the size and complexity of the part, as well as the type of material used.
- Finishing: Once the part is removed from the mold, it may require additional finishing steps, such as trimming excess material, polishing, or adding secondary operations like inserting metal components or applying coatings.
The entire process is carefully controlled to ensure that each component meets the necessary quality standards. Medical injection molding services help manufacturers meet regulatory requirements, such as those set by the FDA and ISO, ensuring that the products are safe for medical use.
Medical injection molding services are a vital aspect of the medical device manufacturing industry. By providing precision, efficiency, and scalability, this process enables the production of high-quality medical molding components that are essential to healthcare and patient safety.
Why Choose Medical Injection Molding Services for Your Devices?
Choosing medical injection molding for your devices offers numerous advantages, making it a highly preferred manufacturing method for the medical industry. This process provides unmatched precision, scalability, and cost-effectiveness, while ensuring compliance with stringent regulatory standards. Below are some key reasons why medical injection molding services are essential for producing high-quality medical components.
Precision and Accuracy
One of the most critical requirements for medical devices is precision. Medical injection molding services excel in producing parts with tight tolerances and dimensional consistency, which is essential for the functionality and safety of medical devices. Whether it’s for surgical tools, implants, or diagnostic equipment, the ability to create complex, detailed parts with exact measurements ensures that each device functions as intended and minimizes the risk of failure. The accuracy of the process also reduces the need for post-production modifications, saving time and costs while maintaining high product quality.
Compliance with Industry Standards
The medical industry is highly regulated, and manufacturers must ensure that their products meet various quality and safety standards. Medical injection molding services help ensure that medical components are compliant with key regulatory frameworks, such as the FDA (Food and Drug Administration) requirements for medical devices and ISO 13485 certification for quality management systems. These certifications confirm that the manufacturing process and materials meet the rigorous demands of the healthcare industry, guaranteeing that the end products are safe for patient use and can withstand the stresses and strains of medical applications.
Injection Molding Services for Medical Devices: Scalability
Another significant advantage of using medical injection molding services is scalability. This process allows for the production of both low-volume prototypes and high-volume production runs. Whether you’re developing a new device and need a small batch for testing or you’re scaling up for full commercial production, injection molding is versatile enough to handle all stages of manufacturing. The ability to shift from prototyping to mass production quickly and efficiently makes it an ideal choice for medical device companies looking to launch new products or meet increasing demand.
Cost-Effectiveness
Cost is always a consideration in manufacturing, especially in the medical field where margins can be tight. Medical injection molding services help keep costs low by automating much of the production process. Automation reduces the need for manual labor, leading to lower labor costs and faster production times. Additionally, once the molds are designed and set up, the cost per unit decreases significantly, especially in high-volume production. This makes injection molding a cost-effective solution for producing complex medical parts at scale while maintaining product quality.
Material Versatility
Medical devices require materials that meet specific performance, durability, and biocompatibility requirements. Medical injection molding services offer a wide range of medical-grade materials that can be selected based on the needs of the device. These materials include PEEK (polyether ether ketone), silicone, polypropylene, and others that offer different characteristics such as high resistance to heat, chemical stability, and flexibility. The ability to use a variety of materials ensures that manufacturers can create devices with the necessary properties for their intended medical applications, whether they need strength, flexibility, or biocompatibility.
The advantages of medical injection molding services make it a vital process for the production of medical devices. From precision and regulatory compliance to scalability and cost-effectiveness, injection molding provides the tools needed to produce high-quality, reliable medical components that meet the demands of the healthcare industry. With its material versatility and efficient production capabilities, it is the ideal solution for manufacturers seeking to produce safe and effective medical devices.
Best Medical Injection Molding Services Near Me
When searching for the best medical injection molding services near you, it’s crucial to select a provider that can meet the strict medical molding requirements of the medical industry while offering efficient and reliable service. Choosing a local provider can offer several advantages, from reduced shipping costs to quicker turnaround times. Below are some helpful tips for finding high-quality medical plastic injection molding services and key factors to consider during your search.
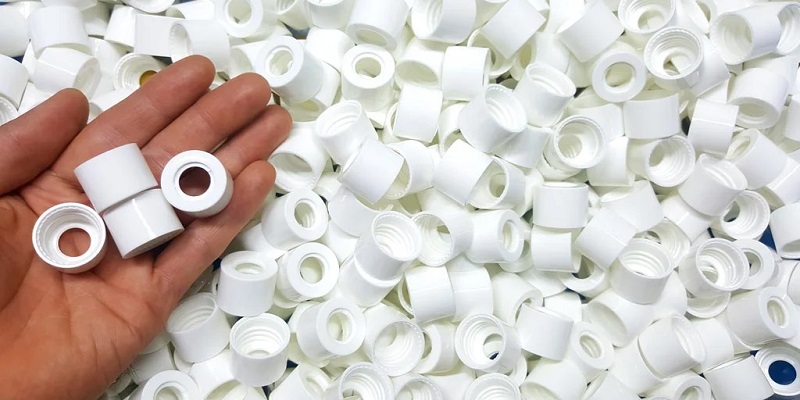
Finding Quality Providers Locally
To locate top-tier medical injection molding services near you, start by conducting online research using specific keywords like “medical injection molding services near me” or “local medical plastic injection molding services.” You can also explore directories or industry-specific websites that list certified and reputable manufacturers. Networking within the medical device manufacturing community, attending trade shows, or consulting with industry associations can also point you toward trusted local providers.
Another effective method is to ask for recommendations from other medical device manufacturers, suppliers, or partners in the healthcare sector. Word-of-mouth referrals often lead to high-quality service providers who have proven track records in meeting the unique needs of medical device production.
Importance of Proximity
The proximity of a medical injection molding services provider plays a significant role in the efficiency and cost-effectiveness of your project. Working with a local supplier offers several key benefits:
- Quick Response Times: Local manufacturers are often more responsive and can handle last-minute changes or urgent orders more swiftly. This is critical in industries like medical device manufacturing, where timelines are often tight.
- Reduced Shipping Costs: By selecting a provider nearby, you can save on expensive shipping and transportation costs. Additionally, local companies are less affected by shipping delays and international customs issues, which can often cause delays for overseas suppliers.
- Easier Communication: Proximity allows for easier communication, including in-person meetings or site visits, ensuring that both you and the provider are aligned on expectations, requirements, and specifications.
Factors to Consider
When evaluating medical plastic injection molding services near you, it’s important to consider several key factors to ensure you’re selecting a high-quality and reliable provider:
Certifications
Certifications are a crucial indicator of a manufacturer’s compliance with industry standards. For medical devices, look for companies that are FDA compliant and ISO 13485 certified. These certifications ensure that the manufacturer follows strict quality management systems and that the products they produce meet regulatory standards for safety and effectiveness. Some providers may also hold additional certifications specific to certain types of medical devices or materials.
Technology and Equipment
Modern technology and state-of-the-art equipment are essential for producing high-quality medical components. When evaluating medical injection molding services, consider whether the provider has advanced machinery capable of handling complex designs and meeting the tight tolerances required for medical devices. The availability of cleanrooms for sterile production environments is also a key consideration, especially for components used in implantable devices or products that require high levels of cleanliness.
Facility Capabilities
A facility’s capabilities play a vital role in the quality and efficiency of the manufacturing process. Some important features to look for include:
- Cleanrooms: Cleanrooms are essential for producing medical components that must be free from contaminants. A provider with certified cleanroom facilities ensures that the parts are produced in a controlled, sterile environment, reducing the risk of contamination.
- High-Volume Production: If you require high-volume production runs, ensure the provider has the capacity and expertise to handle large quantities without compromising quality. Check if they have automated systems that increase production efficiency and consistency.
- Prototyping Capabilities: Many medical injection molding services also offer prototyping capabilities, which are essential when developing new medical devices. Having a local provider that can quickly produce prototypes for testing and validation can significantly speed up the development process.
Customer Reviews and Reputation
Before making a final decision, take the time to review customer testimonials, case studies, and industry reviews. Positive feedback from other medical device manufacturers or healthcare providers is a good indicator that the supplier can deliver high-quality components on time and within budget. Additionally, reach out to past or current customers to gather insights into the provider’s reliability, customer service, and overall performance.
Finding the best medical injection molding services near you involves researching local providers, considering key factors like certifications, technology, and customer reviews, and weighing the benefits of proximity. Whether you are looking for medical plastic injection molding services for prototypes or large-scale production, working with a nearby, certified provider can help streamline your manufacturing process and ensure your medical devices meet the high standards required for healthcare applications.
Materials and Selection Guide for Medical Injection Molding Services
Materials Used in Medical Injection Molding Services
Polypropylene (PP):
Polypropylene is widely used in medical applications due to its excellent chemical resistance, low density, and affordability. It is commonly utilized for syringes, medical containers, and IV components. Its ability to withstand sterilization processes like autoclaving makes it ideal for reusable medical devices.
Polycarbonate (PC):
Renowned for its high impact resistance, clarity, and durability, polycarbonate is used in medical devices requiring transparency and toughness, such as surgical instruments, oxygen masks, and enclosures for diagnostic equipment. It is also biocompatible and can be sterilized without degrading.
Polyethylene (PE):
Offering superior flexibility and chemical resistance, polyethylene is ideal for disposable medical items like tubing, bags, and containers. High-density polyethylene (HDPE) is often used for rigid applications, while low-density polyethylene (LDPE) serves softer, pliable needs.
Thermoplastic Elastomers (TPE):
TPEs are highly versatile, combining the benefits of rubber-like elasticity with the ease of thermoplastic processing. These materials are used for seals, gaskets, and grips on medical devices due to their soft touch and excellent sealing properties.
Polyetheretherketone (PEEK):
PEEK is a high-performance engineering plastic used in demanding applications like implants and surgical instruments. It offers exceptional mechanical strength, chemical resistance, and compatibility with imaging equipment such as MRIs.
Acrylic (PMMA):
Known for its optical clarity and scratch resistance, PMMA is used in applications requiring transparency, such as lenses, blood reservoirs, and diagnostic devices. It is lightweight, biocompatible, and easy to process.
Polyoxymethylene (POM):
Also known as acetal, POM is valued for its strength, stiffness, and low friction. It is used in precision medical components like inhalers, surgical instrument handles, and valve systems.
Selection Considerations for Medical Injection Molding Materials
Biocompatibility:
The material must comply with medical standards such as ISO 10993 or USP Class VI to ensure it is safe for direct or indirect contact with the human body.
Sterilization Compatibility:
Consider whether the material can endure sterilization methods like autoclaving, gamma radiation, or ethylene oxide without compromising its properties.
Mechanical Properties:
Assess the strength, flexibility, and durability required for the specific application to ensure the material meets performance expectations.
Chemical Resistance:
The material should resist degradation when exposed to cleaning agents, bodily fluids, or pharmaceuticals.
Transparency or Opaqueness:
Applications requiring visibility, like diagnostic devices, may necessitate transparent materials, whereas others may benefit from opaque options.
Cost and Processability:
Evaluate the cost-effectiveness of the material and its ease of processing for high-volume production.
Regulatory Compliance:
Ensure the material aligns with regional and international medical device regulations to facilitate market approval.
By carefully considering these materials and selection criteria, FUJIU Medical Injection Mold ensures optimal solutions for diverse medical device manufacturing needs.
How Much Do Custom Medical Injection Molding Services Cost?
The cost of medical injection molding services can vary significantly based on several factors, including the type of material used, the complexity of the parts, the volume of the order, and mold creation costs. Custom injection molding for medical devices requires precision, high-quality materials, and specialized facilities, all of which contribute to the overall price. Below is a breakdown of the key factors affecting the cost of custom injection molding and some tips for cost-saving opportunities.
Overview of the Factors Affecting the Cost of Medical Injection Molding
Material Choice
The type of material chosen for the injection molding process is one of the most significant factors influencing the cost. Medical-grade plastics are specifically designed to meet the stringent requirements of the medical industry. These materials tend to be more expensive than general-purpose plastics due to their specialized properties, such as biocompatibility, durability, and resistance to sterilization methods.
- High-performance materials are typically more costly than standard materials, such as polypropylene or polyethylene.
- Custom compounds or specialized additives for certain medical applications can also drive up material costs.
Part Complexity
The complexity of the part being produced is another key determinant of cost. More intricate designs with fine details, undercuts, or multi-cavity molds require advanced molding techniques and may result in higher production costs. Parts with complex geometries often require additional post-processing, such as trimming or finishing, which can increase the overall cost.
- Simple, straight-forward designs tend to be less expensive.
- Complex components, such as medical implants, surgical instruments, or parts with multiple features, will increase both tooling and production time.
Order Volume
The volume of the order has a direct impact on the cost per unit. In general, higher-volume production runs lead to a lower cost per unit, as the fixed costs of mold creation and machine setup are spread over a larger number of parts. Conversely, small-volume runs tend to have higher costs per unit due to the relatively higher proportion of setup and tooling costs.
- Small runs (e.g., prototyping or low-volume production) tend to be more expensive per unit, as the initial costs of setup and medical mold design must be amortized over fewer parts.
- Large production runs can reduce the unit cost significantly because the same mold can be used to produce a higher number of parts.
Mold Costs
Mold creation is one of the most significant up-front costs in injection molding. The complexity of the mold, the number of cavities, and the materials used for the mold itself (e.g., steel or aluminum) will all impact the overall price. Mold costs are usually a one-time expense, but they can be quite high, especially for custom molds designed for medical devices.
- Simple molds may cost a few thousand dollars, while complex, multi-cavity molds can cost tens of thousands of dollars.
- Long-term use of a mold for high-volume production can help offset the initial mold cost, making it more economical over time.
Breakdown of Cost-Saving Opportunities
Small Runs vs. Large Production Volumes
When evaluating the cost of medical injection molding services, consider how order volume can impact pricing:
- Small Runs: For custom, low-volume runs (e.g., for prototyping or pilot batches), you may face higher per-unit costs due to the upfront expenses associated with tooling and setup. These runs are typically priced based on the costs to set up the machine and produce a small batch, rather than the volume of parts produced.
- Large Runs: For large-scale production, the cost per unit typically decreases significantly. Once the mold is created and machine setup is complete, producing additional parts becomes more cost-efficient. Higher volumes allow the manufacturer to recoup the mold costs and operational expenses over a larger number of parts, resulting in a reduced cost per unit.
High-volume production may qualify for bulk pricing discounts, so it’s worth discussing expected production quantities with the injection molding provider upfront to gain a better understanding of cost efficiencies for larger runs.
Tools for Estimating Custom Injection Molding Costs
To get a clearer idea of what your medical injection molding services project will cost, many companies offer online quote systems where you can input details about the part design, material requirements, and expected production volume to receive an estimated price. These systems can provide a quick estimate based on the initial project scope.
For more precise cost breakdowns, especially for custom medical parts that require specialized materials and processes, it’s often better to consult directly with the molding service provider. They can offer a more detailed estimate based on the specific requirements of your project. Key considerations include:
- Online Quote Systems: Many injection molding companies offer online tools to quickly get an estimate based on part design and specifications.
- Consultation Services: Speaking directly with an experienced engineer or project manager can help identify potential cost-saving strategies, including material suggestions, design optimization, and volume planning.
The cost of medical injection molding services depends on several factors, including material choice, part complexity, production volume, and mold creation expenses. Understanding how these elements interact can help you make informed decisions when planning your medical device production. For smaller runs, you can expect higher unit costs, but for large-scale production, the cost per unit can drop significantly. Utilizing online tools for initial estimates and consulting with experienced professionals can help you navigate the pricing process and identify opportunities for cost savings without compromising on quality.
Popular Medical Injection Molding Services and Techniques
When it comes to medical injection molding services, there are various specialized techniques that allow manufacturers to produce high-precision, high-quality medical components. These techniques are crucial for creating parts that meet the stringent requirements of the healthcare industry, such as biocompatibility, durability, and functionality. Below are some of the most popular medical injection molding techniques used in the production of medical devices.
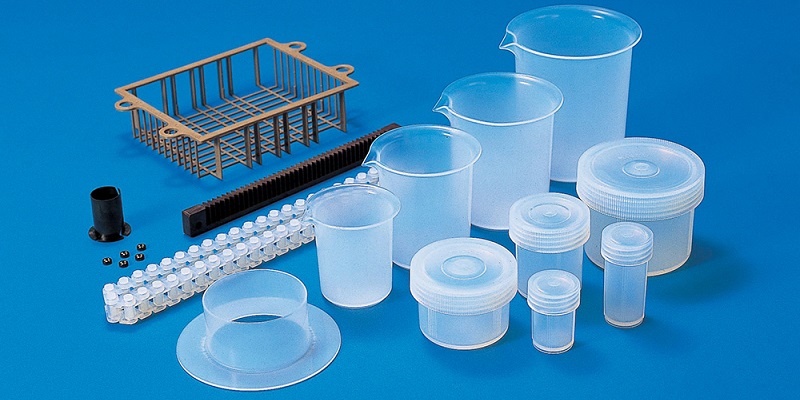
Overmolding
Overmolding is a popular technique used in medical injection molding services to create multi-layered components that offer additional strength, protection, or flexibility. This process involves molding one material over another to combine the benefits of both materials in a single part. Overmolding is ideal for creating devices that require a soft-touch surface, electrical insulation, or shock resistance.
- Improved strength and durability: Overmolding can provide a durable outer layer that protects sensitive inner components from wear and tear.
- Enhanced ergonomics: Medical devices such as surgical handles, grips, or patient contact components can benefit from overmolding, as it provides a comfortable, non-slip surface.
- Flexibility: The ability to combine hard and soft materials in a single part allows manufacturers to produce more complex designs that meet the varying requirements of medical devices.
Insert Molding
Insert molding is a process where metal inserts are placed into a mold and then plastic is injected around the insert to create a seamless, integrated part. This technique is often used in medical injection molding services for producing components that require metal and plastic components to be combined, such as medical device housings, connectors, and handles.
- Strength and integrity: Metal inserts improve the strength of the plastic part, which is essential for parts that need to withstand high stress or pressure.
- Cost-effective: Insert molding allows for the use of inexpensive plastic materials while still achieving the necessary strength and durability of metal.
- Reduced assembly costs: By combining the insert and plastic in one molding process, manufacturers can reduce the need for additional assembly steps, which saves both time and labor costs.
Micro Molding
Micro molding is a highly specialized technique used in medical injection molding services to produce ultra-precise parts with extremely small dimensions. This technique is essential for manufacturing miniature medical components that require tight tolerances and high precision, such as micro-sized catheters, diagnostic equipment components, and implants.
- Ultra-precision: Micro molding is capable of producing parts with extremely fine details, which is crucial for medical devices that require high precision and functionality in small spaces.
- Small-scale applications: This technique is often used for applications where the parts are smaller than 1 millimeter in diameter, such as in microelectronics, drug delivery systems, and surgical tools.
- High efficiency: Micro molding technology allows for fast production of small, high-quality parts with minimal material waste, making it a cost-effective solution for small-scale medical applications.
Liquid Silicone Injection Molding (LSR)
Liquid Silicone Rubber (LSR) injection molding is a popular technique in medical injection molding services used to produce flexible, biocompatible medical components. LSR is ideal for medical applications that require materials that are not only flexible but also resistant to heat, chemicals, and sterilization processes. This makes it suitable for a wide range of medical devices such as catheters, seals, and gaskets.
- Biocompatibility: LSR is highly biocompatible, making it perfect for medical devices that come into contact with the human body, such as catheters, seals, and gaskets.
- Flexibility and durability: LSR parts can be molded to be both flexible and durable, which is essential for devices that need to bend or stretch without losing their integrity.
- Heat and chemical resistance: LSR is highly resistant to heat and chemicals, which makes it ideal for medical devices that need to endure autoclaving and other sterilization methods.
Each of these techniques—overmolding, insert molding, micro molding, and liquid silicone injection molding—offers distinct advantages for medical device production. By leveraging these advanced techniques, medical injection molding services providers can produce highly specialized, high-quality components that meet the demanding requirements of the healthcare industry. Whether you’re designing a small, ultra-precise medical component or creating multi-functional parts, choosing the right molding technique is essential for ensuring the performance, safety, and longevity of your medical device.
Choosing the Best Medical Injection Molding Services Near You
When selecting medical injection molding services near you, it’s essential to evaluate several key factors to ensure that the provider can meet the high standards required for medical device production. The right company should not only have the necessary technical expertise but also a reputation for reliability and quality. Below are some practical steps for assessing medical injection molding companies in your area and ensuring you choose the best one for your needs.
How to Assess the Reputation and Experience of Medical Injection Molding Companies Near You
The reputation and experience of a medical injection molding services provider are critical indicators of their ability to meet the stringent requirements of medical device manufacturing. A company with a solid track record in the medical industry is more likely to understand the unique challenges and regulations involved in producing high-quality, reliable medical components.
- Industry Experience: Look for a provider with a long history of working with medical device manufacturers. Companies that have experience producing FDA-approved devices or parts that meet ISO 13485 standards are more likely to understand the complexities of medical device production.
- Customer Testimonials and Case Studies: Research customer reviews, case studies, and testimonials to understand how the company has worked with other clients in the medical field. Positive feedback from medical device manufacturers or healthcare professionals can give you confidence in their capabilities.
- References: Don’t hesitate to ask for references from previous clients. A reputable company should be able to provide references from companies in the medical field who can speak to the company’s ability to meet deadlines, quality standards, and regulatory requirements.
What types of medical devices do they specialize in?
Understanding the company’s area of expertise can help you determine if they are a good fit for your specific needs. Some medical injection molding services providers specialize in certain types of medical devices, such as diagnostic equipment, surgical instruments, or implantable devices.
- Specialization: A provider that specializes in your type of medical device may have more experience and better capabilities for handling the specific requirements of your project. For example, some companies may have experience working with soft, flexible materials like silicone for catheters, while others may specialize in hard, durable materials for surgical instruments.
- Range of capabilities: Ask if they can handle everything from the design phase to prototyping and mass production. A company with a broad range of capabilities is often better equipped to handle all aspects of your project.
Importance of Facility Tours and Audits for Understanding Their Capabilities
Visiting a company’s facility or conducting an audit can provide valuable insights into their capabilities and overall quality standards. A facility tour allows you to assess the company’s equipment, production environment, and adherence to industry standards firsthand.
- Cleanroom Capabilities: Many medical devices require manufacturing in cleanroom environments to prevent contamination. Ask if the facility is equipped with cleanrooms, and schedule a tour to see if they meet the required cleanliness standards.
- Equipment and Technology: A tour gives you the opportunity to see the quality and state of the equipment the company uses for medical injection molding services. Look for advanced machinery, automated systems, and quality control processes that ensure high precision and consistency.
- Compliance and Standards: During the tour, inquire about the company’s adherence to FDA and ISO standards. A reliable company will be happy to show you their certifications and provide evidence of their compliance with medical industry regulations.
- Production Capacity: Ask about the company’s production capabilities to ensure they can handle both small runs (for prototypes or low-volume production) and high-volume manufacturing without compromising on quality.
Choosing the best medical injection molding services provider near you involves thorough research and careful consideration of key factors such as reputation, experience, certifications, and facility capabilities. By asking the right questions—such as whether the company is ISO 13485 certified, whether they specialize in your type of medical device, and whether they offer full turnkey solutions—you can better assess whether a company is the right fit for your needs.
Advantages of FUJIU Medical Injection Mold for Medical Injection Molding Services
- ISO-Certified Quality Assurance: FUJIU ensures all products meet the highest industry standards through rigorous inspections and ISO-certified production processes.
- Full-Service Solutions: From product design to in-house tooling and secondary operations, FUJIU offers end-to-end manufacturing under one roof, streamlining workflows.
- Agile and Flexible Supply Chain: Their adaptive supply chain reduces delivery cycles, accelerates time to market, and accommodates changing requirements with ease.
- Advanced Technology: With cutting-edge equipment and ISO 8 cleanroom facilities, FUJIU guarantees precision and reliability for high-quality medical components.
- Global Expertise: A robust supply chain across 10 regions, supported by experts in procurement, logistics, and project management, ensures seamless execution.
- Cost-Effective Solutions: FUJIU’s value-added DFM strategies optimize production efficiency, lowering overall costs while maintaining top-tier quality.
FAQs about Medical Injection Molding Services
The cost of injection molding per hour can vary significantly depending on several factors, including the type of machine, its size, and the complexity of the mold being used. On average, the cost can range from $30 to $150 per hour. High-end, specialized machines or those used for complex molds can exceed this range. Additional costs to consider include setup fees, labor, and material costs, which can also impact the overall hourly rate.
Medical injection molding is a specialized process used to manufacture medical-grade plastic components and devices. This method involves injecting molten plastic into a precision mold to create items like syringes, surgical instruments, and other medical devices with high accuracy and consistency. The process must adhere to strict regulatory standards, such as ISO 13485, to ensure the components’ biocompatibility, safety, and reliability. Materials used in medical injection molding are often medical-grade polymers, designed to meet the rigorous demands and specifications of the healthcare industry.
The market for medical injection molding is substantial and continues to grow rapidly, driven by advancements in healthcare, increasing demand for medical devices, and technological innovations. This market encompasses a wide range of products, including diagnostic equipment, surgical tools, and patient care items. North America, Europe, and Asia-Pacific are major contributors to this market, with significant growth observed in emerging economies. The market’s expansion is further supported by an aging population, greater focus on minimally invasive surgeries, and the ongoing development of biocompatible and high-performance medical polymers.
The cost of injection molding per part can vary widely based on several factors such as the complexity of the design, the type of material used, and the volume of production. For simple parts, the cost can be as low as $0.10 to $1.00 per piece for high-volume production. More complex parts with intricate designs or those made from advanced materials can cost several dollars per part. The upfront cost of creating the mold, which can range from $1,000 to $100,000, also affects the per-part cost, making high-volume production more cost-effective over time.
The cost of injection molding for medical applications varies based on factors like material type, mold complexity, and production volume. In medical injection molding services, costs are often higher than standard applications due to stringent regulatory requirements, precision tolerances, and biocompatible materials. The mold creation process, which includes designing and manufacturing the tool, represents a significant upfront investment, often ranging from $10,000 to $100,000 depending on complexity. After the mold is made, per-part costs can decrease substantially with high-volume production. For example, producing thousands of disposable syringes or other medical-grade components can make the per-unit cost competitive. Costs can also fluctuate based on secondary operations like sterilization, cleanroom production, and packaging. By leveraging an experienced medical injection molding provider, companies can optimize costs while ensuring compliance with standards such as ISO 13485 for medical devices.
Injection molding for medical applications can be considered expensive, particularly during the initial stages of mold creation. The tooling cost is a major investment, but it ensures long-term cost efficiency when producing high volumes of consistent, high-quality medical components. The expense stems from the need for advanced machinery, precision engineering, and compliance with medical industry standards, such as FDA and ISO certifications. However, once the mold is created, production costs for each unit become significantly lower. For single-use medical devices or components, the scalability of injection molding often outweighs the upfront expense. Advanced technologies, such as micro-molding for tiny medical parts, may add to the cost due to higher precision requirements. In essence, while the upfront investment is substantial, the long-term scalability and reliability make injection molding a cost-effective solution for the medical sector.
To calculate the hourly rate for an injection molding machine in medical applications, several factors must be considered. These include the cost of the machine, energy consumption, labor, maintenance, and auxiliary equipment like chillers or dryers. For medical molding services, additional costs for operating in a cleanroom environment and regulatory compliance should be factored in.
A simplified calculation involves:
Dividing the machine’s cost by its estimated lifespan in hours (e.g., 10 years at 4,000 hours/year).
Adding operating costs, such as electricity and materials.
Including labor costs and any overhead, such as facility expenses or certifications.
For example, a $250,000 medical-grade molding machine with a lifespan of 40,000 hours results in a base rate of $6.25/hour. Adding $20/hour for energy and labor plus $5/hour for maintenance and cleanroom costs would result in an estimated $31.25/hour. Tailoring this to project-specific needs is essential.
Injection molding can be a rewarding career, especially in the medical field, where precision and innovation are key. Careers in medical injection molding services often involve working with advanced technology, materials, and processes to produce critical components like surgical tools, implants, or diagnostic equipment. The field offers diverse opportunities, including roles in machine operation, tool design, quality control, and regulatory compliance.
With the increasing demand for medical devices and the global focus on healthcare innovation, injection molding professionals with specialized knowledge in medical applications are highly sought after. These roles often require attention to detail, problem-solving skills, and familiarity with industry standards such as ISO 13485 or FDA requirements. A career in this niche also offers job security and growth potential due to the consistent demand for medical-grade products. Pursuing certifications or training in medical injection molding can further enhance career prospects.
Contact our professional team now for a same-day quote and risk-free project evaluation. Benefit from ISO 8 cleanrooms, advanced machines, and 12-hour fast response in medical injection molding.