Precision engineering is essential in the medical field, as it directly impacts the quality, safety, and performance of medical devices. The high accuracy required for surgical instruments, implants, and diagnostic tools ensures better patient outcomes and reduced risks. Medical machined components, such as precision mold medical parts, play a crucial role in this process, enabling the production of intricate and precise components that meet strict industry standards. CNC machining has revolutionized medical device manufacturing by providing a cost-effective and efficient way to produce these parts. Over the years, the growth of medical machined components has been driven by advancements in technology, increasing demand for personalized healthcare solutions, and a greater focus on improving the quality and reliability of medical devices. This evolution continues to shape the future of healthcare. FUJIU Medical Injection Mold provides precision CNC services, delivering custom medical machined components for devices, implants, and instruments.
Low-Volume to High-Volume Production Capabilities
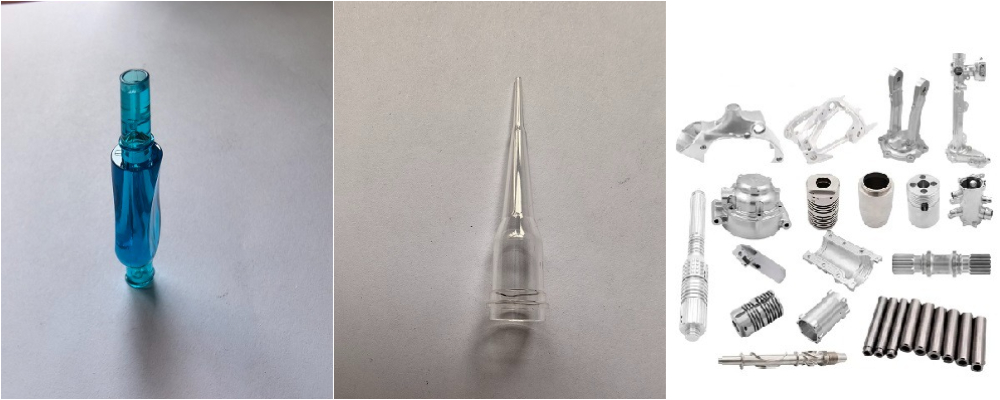
Attributes | Details |
---|---|
Place of Origin | Dongguan, Guangdong, China |
Brand Name | LY Medical Injection Mold |
Product Name | Medical Molding |
Molding Mode | Plastic Injection Molding |
Product Material | Plastic |
Color | Customized |
Size | Customized |
Length | Customized |
Style | Customized |
Service | OEM ODM |
Processing Services | Broaching, Drilling, Milling, Other Processing Services, Turning, Rapid Prototyping |
Features | High Precision |
Logo | Customized Logo Acceptable |
Supplier | Manufacturer |
Design Software | 2D/3D/CAD/DWG//STEP/PDF/UG |
Surface Treatment | Customer Requirement |
Quality Control | 100% Inspection |
Minimum Order Quantity | Small Order Accepted |
Packing Details | Outer Packaging Carton Inner Packaging According to Customer Requirement |
Port | According to Your Requirement |
What Are Medical Machined Components?
Definition and Characteristics of Medical Machined Components
Medical machined components are high precision medical components used in various medical devices, including surgical tools, implants, diagnostic equipment, and prosthetics. These components are typically manufactured using advanced CNC (Computer Numerical Control) machining techniques, which ensure an exceptional degree of accuracy and reliability. CNC machining is essential for producing parts that meet stringent specifications, such as exact dimensions, tight tolerances, and surface finishes. The materials used in these components are often biocompatible metals like titanium, stainless steel, or specialized plastics like PEEK, all of which are carefully selected to ensure durability and safety within the human body.
Importance of Medical Machined Components in Healthcare
Medical machined components are integral to the medical field due to their role in enabling life-saving innovations. For example, these components are crucial for developing precise implants, such as hip and knee replacements, that offer patients longer-lasting solutions and improved mobility. Additionally, surgical tools like scalpels, forceps, and robotic surgical arms are made from these components, ensuring that doctors can perform procedures with extreme precision. As a result, the healthcare sector relies heavily on medical machined components to enhance patient outcomes and contribute to the growing need for customized, high-quality medical solutions.
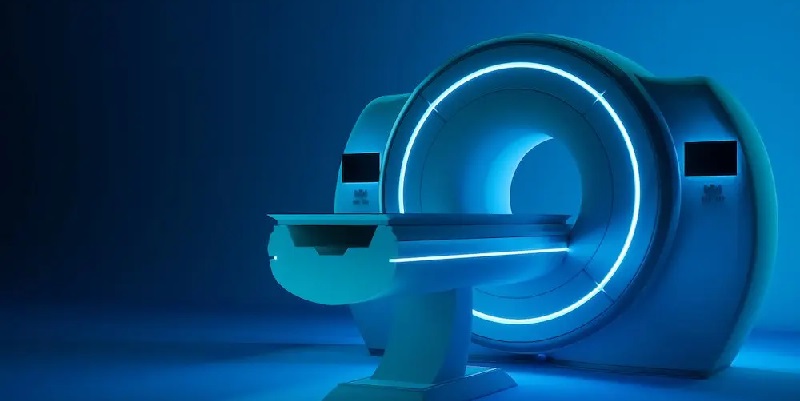
Enabling Life-Saving Innovations
One of the major benefits of medical machined components is their ability to support innovations in medical treatments. These components have enabled breakthroughs such as minimally invasive surgeries, which reduce recovery time and complications for patients. For instance, precision-machined components are critical in robotic surgery, where tiny, accurate parts are required to perform delicate operations. In addition, advancements in personalized medicine, such as custom prosthetics and implants, would not be possible without the precise manufacturing of medical machined components tailored to each patient’s unique needs.
Improving Patient Outcomes
The role of medical machined components extends beyond innovation; they are vital for improving the overall quality of care and patient outcomes. Accurate machining allows for the creation of medical devices that fit the human body perfectly, reducing the likelihood of complications and ensuring longevity. For example, hip and knee implants made from titanium are custom-designed to match a patient’s anatomical structure, providing better functionality and less discomfort. This tailored approach improves the success rate of surgeries and enhances the quality of life for patients.
The Role of Medical Machined Components in Diagnostics
Medical machined components also play a key role in diagnostic devices, such as MRI machines, CT scanners, and X-ray systems. These machines rely on precisely engineered parts, such as rotors, stators, and collimators, to ensure accurate imaging and functionality. Without high-quality machined components, diagnostic devices would be less reliable, potentially leading to misdiagnosis or incorrect treatment plans. The continued development of medical machined components in diagnostic technology is essential for advancing healthcare and enabling early detection of diseases.
Advancements in Manufacturing Techniques for Medical Machined Components
The growing demand for medical machined components has spurred innovation in manufacturing techniques. The integration of AI, robotics, and advanced CAD/CAM systems has significantly enhanced production capabilities. These technologies allow for greater precision, reduced lead times, and the ability to produce small-batch custom components for specific medical needs. The application of these advancements in CNC machining ensures that medical devices are not only functional but also meet the highest standards of safety and quality.
Medical Machined Components: CNC Medical Parts and Their Applications
Overview of CNC Technology in Medical Machining
CNC (Computer Numerical Control) technology has revolutionized the manufacturing of medical machined components by providing a level of precision and repeatability that is essential for medical devices. Integral to high quality precision medical CNC machining, CNC machines operate through automated control, allowing for the highly accurate production of parts with minimal human intervention. This technology plays a crucial role in medical machining, as it can produce components with tight tolerances and complex geometries that are often required in medical applications. The use of high-quality precision medical CNC machining in medical manufacturing allows for faster production cycles, reducing the time needed to bring medical devices from design to market, all while maintaining high standards of quality.
Key Applications of Medical Machined Components
Surgical Tools
One of the most critical applications of medical machined components is in the production of surgical tools. These include items like scalpels, biopsy cutters, and robotic arms. Precision is paramount when manufacturing surgical instruments because even the slightest deviation in size or shape can result in compromised performance during surgeries. CNC machining ensures that these tools meet the exact specifications required for each procedure, whether it’s a simple incision or a complex operation using robotic assistance. The tight tolerances and durability of CNC-machined surgical tools contribute directly to the safety and success of surgeries, improving patient outcomes.
Implants
Medical machined components are also integral in the manufacturing of implants such as hip replacements, knee implants, and titanium bone plates. These implants must be manufactured to precise specifications in order to ensure a proper fit within the human body, as well as to provide long-term functionality and comfort. CNC machining offers the ability to create complex shapes and surfaces for implants, such as the smooth curves of a joint replacement or the intricate structures of a bone plate. The use of high-quality, biocompatible materials like titanium further enhances the effectiveness of these implants, ensuring that they integrate well with human tissue and last for extended periods.
Diagnostic Devices
CNC technology is essential in the production of parts for diagnostic devices, including components for CT scanners, MRI machines, and X-ray systems. These devices rely on precision-engineered parts, such as rotors, stators, and collimators, which are critical for generating accurate readings and ensuring patient safety during diagnostic procedures. The production of medical machined components for diagnostic equipment must meet strict quality and safety standards. By using CNC technology, manufacturers can ensure that these components are crafted with the highest precision, which helps improve the accuracy of diagnostic tests, reduce equipment failure, and contribute to more reliable healthcare outcomes.
Custom Prosthetics
One of the most groundbreaking applications of medical machined components is in the creation of custom prosthetics. Prosthetic devices, including limbs and joints, can be tailored to fit the specific anatomy of individual patients. CNC machining allows for the manufacturing of prosthetics that offer enhanced comfort, functionality, and mobility. By using advanced scanning technology and CAD (Computer-Aided Design), manufacturers can design prosthetic components that match the unique shape and size of a patient’s body. This level of customization leads to prosthetics that fit better and function more naturally, improving the overall quality of life for patients.
Dental Instruments
Dental instruments and implants are another critical area where medical machined components play an essential role. Precision machining is required to produce dental tools, such as drills, scalers, and zirconia-based dental implants. Zirconia is commonly used for dental implants due to its strength, durability, and biocompatibility. CNC machining is used to shape these materials with exceptional accuracy, ensuring that dental implants and tools not only fit perfectly but also function optimally in the harsh conditions of the human mouth. The use of CNC in dental applications has advanced the field of dentistry by improving the quality of implants and tools, which leads to better patient experiences and outcomes.
Benefits of CNC Machining for Medical Applications
Precision and Accuracy
CNC machining offers unparalleled precision and accuracy, which is essential in the production of medical machined components. Parts manufactured using CNC machines can meet tight tolerances, which is critical for medical applications where even minor deviations can result in malfunctions or complications. For example, in the creation of joint replacements, precise dimensions ensure that the implants fit perfectly and function properly, minimizing risks during surgery and improving patient recovery.
Material Versatility
CNC machining allows for the use of a wide range of materials suitable for medical applications. Medical machined components can be crafted from biocompatible metals like titanium, stainless steel, and specialized alloys, as well as high-performance plastics like PEEK. These materials are chosen for their strength, corrosion resistance, and compatibility with the human body. The ability to machine these materials precisely ensures that medical devices are both durable and safe for long-term use inside the human body.
Customization and Scalability
CNC technology also enables the customization of medical machined components, which is particularly important for applications such as custom prosthetics and implants. These devices must be tailored to fit individual patients, and CNC machining allows manufacturers to produce unique parts with high accuracy. Additionally, CNC machining is highly scalable, meaning manufacturers can produce both small batches for specialized devices and large volumes for mass-produced products. This versatility helps meet the diverse needs of the medical industry.
Regulatory Compliance
Another significant advantage of CNC machining in the production of medical machined components is its ability to meet the stringent regulatory standards required by the medical industry. Certifications like ISO 9001 and ISO 13485 ensure that products are manufactured in environments that meet high-quality standards. CNC machining facilities are equipped to adhere to these certifications, ensuring that all components are safe for use in medical applications and comply with the necessary regulatory requirements.
Medical Machined Components: Benefits of CNC Machining in Medical Applications
Precision and Accuracy: Meeting Stringent Medical Industry Standards
The primary advantage of using CNC machining for the production of medical machined components is its unparalleled level of precision and accuracy. Medical devices and components must meet extremely tight tolerances to ensure safety and effectiveness during use. CNC machining offers the ability to produce parts with millimeter-precision, which is critical in medical applications where even minor deviations could lead to significant risks or failures. This high degree of accuracy is essential for applications such as surgical instruments, implants, and diagnostic devices. For example, CNC-machined hip implants are produced to such stringent standards that they fit perfectly within a patient’s body, leading to improved stability, better performance, and a more comfortable fit for the patient. Other medical devices, like biopsy cutters or robotic arms, also require CNC machining for their high-precision production to guarantee that each component meets the necessary specifications. Overall, CNC machining in medical applications provides a level of quality control that manual methods simply cannot match.
Material Versatility: Working with Biocompatible Materials like Titanium, Stainless Steel, and PEEK
CNC machining offers significant material versatility, which is a crucial factor when it comes to manufacturing medical machined components. Unlike traditional manufacturing methods, CNC machining allows manufacturers to work with a wide variety of materials, including biocompatible materials like titanium, stainless steel, and PEEK. Titanium, for example, is highly favored in medical applications due to its excellent strength-to-weight ratio and biocompatibility, making it ideal for implants, bone plates, and other medical devices. Stainless steel, another common material, offers durability and corrosion resistance, making it perfect for surgical tools and other instruments that need to withstand tough environments. PEEK, or polyether ether ketone, is a high-performance plastic that has become increasingly popular for medical applications due to its biocompatibility, mechanical strength, and resistance to chemicals. The ability to use such a diverse range of materials with CNC machining means manufacturers can optimize medical machined components for each specific application, improving the quality, functionality, and longevity of medical devices.
Customization and Scalability: From Small-Batch Prototypes to High-Volume Production
CNC machining offers unparalleled customization and scalability, which is particularly valuable in the medical field where each patient might require a unique device or component. For example, custom prosthetics or implants can be manufactured with precision and accuracy thanks to CNC technology, allowing each device to be tailored to meet the specific anatomical requirements of individual patients. CNC machining provides the flexibility to create customized medical components with highly detailed features, such as the perfect fit of a prosthetic limb or a personalized implant for hip replacements. Moreover, CNC technology is scalable, meaning manufacturers can also produce large volumes of medical components without compromising quality. This scalability is essential in the medical field where mass-produced devices, such as diagnostic components for CT scanners or MRI machines, must still meet rigorous quality standards. CNC machining helps bridge the gap between prototyping small batches and producing high-volume medical components, providing a cost-effective and efficient production method that meets industry standards.
Regulatory Compliance: Adherence to ISO 9001 and ISO 13485 Standards
For medical device manufacturers, compliance with international quality standards such as ISO 9001 and ISO 13485 is essential to ensure that their products meet the highest standards of safety, reliability, and effectiveness. CNC machining plays a key role in helping manufacturers comply with these regulations for medical machined components. With CNC technology, manufacturers can produce parts that not only meet specific medical standards but also ensure consistency, reliability, and quality throughout the production process. This means that every component, whether it’s a surgical tool, implant, or diagnostic device, will be manufactured to the same exacting standards. The ISO certifications require compliance with precise documentation, traceability, and control measures to ensure that every part meets the specifications necessary for medical use. CNC machining facilities, equipped with sophisticated software and quality control measures, offer manufacturers a reliable and efficient solution to meet these regulatory requirements. This ensures that all medical machined components are safe for use, effective in operation, and compliant with regulatory standards, ultimately enhancing patient care and safety.
Key Materials Used in Medical Machined Components
Metals
Titanium: Lightweight and Biocompatible
Titanium is one of the most widely used metals in the production of medical machined components due to its unique combination of properties, including lightweight, strength, and biocompatibility. Titanium’s lightness is an advantage in medical applications, as it reduces the overall weight of medical devices, making them easier to handle, implant, or wear. Its strength allows for the creation of durable and long-lasting components, which is essential in implants like joint replacements or bone plates that must endure the stresses of the human body. Titanium’s biocompatibility ensures that it can be safely implanted into the body without causing adverse reactions. This property makes titanium ideal for medical implants, such as dental implants and hip replacements, where the material must integrate with bone tissue and not induce any immune response. For instance, titanium is commonly used in dental implants, as it bonds effectively with the jawbone, providing a stable and permanent solution for tooth loss.
Stainless Steel: Durable and Corrosion-Resistant
Stainless steel is another essential metal used in the production of medical machined components, offering durability and corrosion resistance. Stainless steel’s strength makes it suitable for surgical instruments and medical devices that require long-term performance under high stress. The corrosion resistance of stainless steel is crucial for devices exposed to bodily fluids, such as surgical tools, as it helps prevent degradation over time. Additionally, stainless steel is easy to sterilize, an important property for medical instruments that must be kept free from contamination. For example, stainless steel scalpels and surgical scissors are common in the medical field due to their ability to maintain sharpness while withstanding repeated use and sterilization processes. Stainless steel is also commonly used in the production of surgical fasteners, pins, and plates, providing reliable performance in critical medical applications.
Special Alloys: Used in Critical Medical Devices
Special alloys are often used in the production of medical machined components where superior performance is needed in specialized applications. These alloys are carefully engineered to meet the specific demands of the medical field, such as increased resistance to wear, fatigue, and extreme conditions. For example, cobalt-chromium alloys are widely used in orthopedic implants due to their excellent wear resistance and strength. Similarly, nitinol, a shape-memory alloy, is used in medical devices such as stents and guidewires because of its ability to return to a predetermined shape when heated. This makes it ideal for applications where precise and reliable functioning is required. Special alloys offer a level of performance that is critical in medical devices that need to operate under high-stress conditions and remain safe for patient use over extended periods.
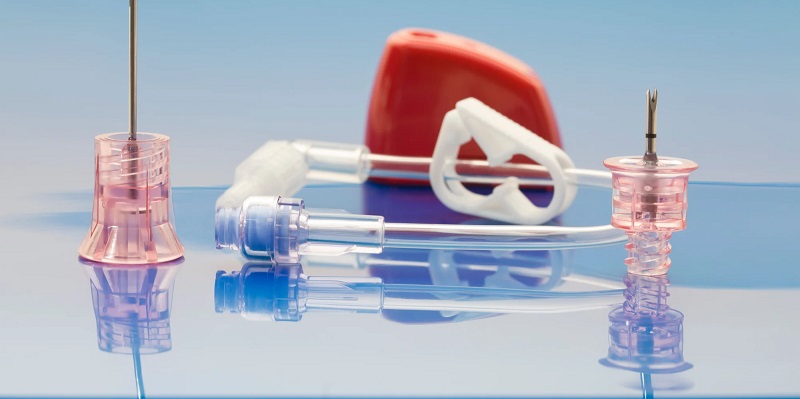
Plastics
PEEK: High Strength and Biocompatibility
PEEK (polyether ether ketone) is a high-performance thermoplastic widely used in the production of medical machined components due to its exceptional strength and biocompatibility. PEEK is a favored material in medical device manufacturing, especially in thermoplastic injection molding medical, because of its ability to maintain high mechanical properties even at elevated temperatures. It is resistant to wear, fatigue, and chemicals, making it a durable option for medical applications. PEEK’s biocompatibility is crucial in applications such as spinal implants, where the material comes into contact with bone and tissue. It does not induce an immune response and is well-tolerated in the human body. Additionally, PEEK’s radiolucency allows for easier imaging in diagnostic procedures, which is particularly useful for implants that need to be monitored over time through X-rays or MRIs.
UHMW and Delrin: Used for Custom Components
UHMW (ultra-high-molecular-weight polyethylene) and Delrin (a type of acetal resin) are two plastics commonly used in the manufacturing of medical machined components that require custom features or non-metallic alternatives. UHMW is known for its extremely low friction, high abrasion resistance, and ability to absorb impact, making it an ideal choice for components such as joint bearings or prosthetic devices. It is also chemically resistant and can be sterilized, which is important for medical applications. Delrin, on the other hand, is a versatile plastic known for its strength, stiffness, and dimensional stability. It is often used in creating custom components like gears, bearings, or housings for medical devices. Both materials offer lightweight alternatives to metals, while still maintaining the mechanical properties required for critical medical applications. For example, Delrin is often used in orthodontic components, where precision and durability are essential.
Medical Machined Components: Challenges and Considerations in Medical Machining
High Precision Demands and Tight Tolerances
One of the most significant challenges in the manufacturing of medical machined components is the need for high precision and tight tolerances. Medical devices often require tolerances in the range of micrometers, as even the smallest deviation can lead to malfunction, patient discomfort, or potential harm. For example, a surgical instrument such as a scalpel needs to maintain a sharp, precise edge, while implants like knee or hip replacements require exact measurements to fit securely within the human body. Achieving such precision requires advanced CNC machining techniques, along with sophisticated measuring tools like CMMs (coordinate measuring machines) to ensure accuracy. These stringent demands for precision often require the use of specialized machinery and highly skilled technicians, increasing both the complexity and cost of production.
Regulatory and Safety Compliance
Another major challenge when producing medical machined components is the need to comply with strict regulatory and safety standards. The medical industry is governed by a range of regulations, including ISO 9001 for quality management and ISO 13485 for medical device manufacturing. These certifications ensure that medical devices are produced under consistent quality control measures that protect patient safety. Compliance with these regulations is essential in gaining approval for medical devices to enter markets, especially for high-risk products like implants or diagnostic equipment. For example, any failure in meeting regulatory standards could result in recalls, legal issues, or, most critically, patient harm. Manufacturers must also adhere to safety standards related to material selection, sterilization, and testing, all of which increase the complexity of the production process for medical machined components.
Environmental Considerations: Minimizing Waste and Using Sustainable Processes
As demand for medical machined components grows, so does the need for sustainable practices in their manufacturing. Environmental considerations are becoming more critical, with a growing focus on minimizing waste and using energy-efficient processes. The machining process often produces waste materials, such as metal shavings or coolant runoff, which must be disposed of responsibly to prevent harm to the environment. Furthermore, the medical industry is increasingly embracing eco-friendly practices, such as using recyclable materials or energy-efficient manufacturing technologies. For example, using biodegradable coolants during CNC machining can reduce harmful chemical waste, while sourcing materials like biocompatible plastics or recycled metals for implants can further enhance the sustainability of the products. Manufacturers are also exploring additive manufacturing (3D printing) technologies as a potential method to reduce material waste during production.
Cost and Production Challenges in Prototyping and Mass Production
Manufacturing medical machined components comes with significant cost and production challenges, especially when transitioning from prototyping to mass production. Developing prototypes for medical devices involves extensive research and design iterations, often requiring custom tooling and small-batch production, which can be expensive. Once a design is finalized, scaling up to mass production involves setting up complex manufacturing processes and ensuring that the high precision required is maintained throughout large volumes of parts. In the case of implants or surgical tools, manufacturers need to produce components with identical specifications in every batch, which is difficult and expensive to achieve. Additionally, the long lead times for prototyping, testing, and validation increase the cost of production. For example, a titanium knee implant prototype may require several months of design, testing, and regulatory approval before mass production can begin, making the entire process cost-intensive. Managing the cost of labor, materials, and equipment while maintaining high-quality standards is a delicate balance that manufacturers must navigate.
Complexities in Material Selection and Customization
Selecting the right materials for medical machined components can also pose a challenge. The materials chosen must meet specific mechanical, chemical, and biocompatibility requirements. For instance, titanium and stainless steel are frequently used for implants, but different alloys or composites may be needed depending on the device’s specific application. Customization adds another layer of complexity, as medical devices are often tailored to individual patient needs. Custom prosthetics or surgical instruments may need to be designed and machined to highly specific dimensions, requiring careful selection of materials and detailed design work. These customized components often require more time and cost to produce, as opposed to standardized parts used in more generic medical devices.
Advanced Technology Integration in Manufacturing
The integration of advanced technologies into the production of medical machined components can offer significant advantages, but it also comes with challenges. Technologies such as automation, robotics, and artificial intelligence are increasingly being used to improve efficiency and precision in medical device manufacturing. High precision tools for medical device manufacturing play a critical role in enhancing the accuracy and quality of these processes. However, integrating these technologies into existing manufacturing systems requires substantial investment in both infrastructure and training. For example, automated systems can improve the speed and accuracy of machining processes, reducing human error and production time. However, they also require careful monitoring to ensure consistent quality. The adoption of new technologies can also involve steep learning curves for technicians and engineers, who must be trained to operate the new systems effectively. While these advanced technologies hold great promise, the upfront investment and integration challenges can be significant.
Medical Machined Components: Plastic Components for Medical Devices
Plastic components play an essential role in the manufacturing of medical device parts, providing significant advantages such as lightweight, cost-effectiveness, and versatility. Plastics are frequently used in medical devices due to their excellent molding capabilities and ability to be customized for a wide variety of applications. These components are essential in devices like syringes, inhalers, diagnostic machines, and drug delivery systems. For example, PEEK (Polyetheretherketone) and UHMW (Ultra-High Molecular Weight Polyethylene) are commonly used for surgical implants and diagnostic equipment due to their strength and biocompatibility. Medical injection molding is a widely used process to produce these plastic components efficiently while maintaining precision and scalability for high-volume production.
Medical Devices Injection Molding Part Names
Injection molding is a key method in producing plastic parts for medical machined components, especially for disposable devices. This process allows manufacturers to produce highly precise and consistent parts, such as:
- Syringes: Plastic syringes are a staple in healthcare, used for injections, and are often made with clear plastic for visibility.
- Catheters: Flexible plastic components that are used in a variety of medical applications, including inserting into veins or other bodily passages.
- IV Components: Components like drip chambers, connectors, and tubing that are crucial for intravenous treatments.
- Needles: Used for injections, often manufactured with biocompatible materials and precision for accurate delivery of medications.
- Valves: For controlling the flow of fluids in medical devices, including those used in respirators or infusion pumps.
These plastic parts must be produced with exceptional accuracy to meet the stringent standards set by regulatory bodies, such as the FDA.
Plastic Parts Optimization for Medical Devices
Optimizing plastic parts for medical devices involves designing components that are not only functional but also reliable and cost-effective. The optimization process often includes several factors such as:
- Biocompatibility: Materials used must not cause adverse reactions when in contact with human tissue or fluids. Materials like PEEK and medical-grade PVC are often chosen for their biocompatibility.
- Durability: Plastic components must withstand long-term use, sterilization processes, and extreme environmental conditions, including temperature and humidity changes.
- Cost-Effectiveness: Injection molding allows for cost-efficient mass production, which is essential for disposable devices like syringes and diagnostic tools.
- Ergonomics: Parts must be designed for easy handling by healthcare professionals, ensuring that devices are user-friendly during patient care.
By considering these factors, manufacturers can optimize the performance and quality of plastic components, ensuring they meet the demanding needs of healthcare environments.
Manufacture of Plastic Components for Medical Equipment
The medical plastic components manufacturer for medical equipment is a highly specialized process that requires attention to detail and expertise in plastic material properties, molding techniques, and medical device regulations. Injection molding is one of the most common techniques used in medical plastics manufacturing, as it allows for high-volume production of precise parts. This process involves injecting molten plastic into a mold, where it cools and solidifies into the desired shape. Key factors influencing the manufacture of plastic components include:
- Material Selection: Choosing the right plastic material is crucial for ensuring the safety, strength, and longevity of medical devices. Popular materials include polypropylene, polyethylene, and polystyrene.
- Sterilization: Most plastic components need to be sterilized before use in medical applications. This can be achieved through methods like autoclaving, which must be considered when selecting materials.
- Regulatory Compliance: The manufacturing process must meet the regulatory standards set forth by bodies like ISO 13485 and the FDA, ensuring that all components are safe for medical use.
This process ensures that medical machined components are reliable and meet the highest standards of safety and performance.
Plastic Medical Equipment Spare Parts
Plastic medical equipment spare parts are critical to maintaining the functionality of medical devices over time. These parts, which can include seals, housings, and functional components, need to be produced to the same high standards as the original equipment. The longevity and performance of these spare parts are essential in ensuring that devices continue to function properly without compromising patient care. Some common examples of plastic spare parts include:
- O-Rings and Seals: Used in various medical devices like pumps and filtration systems to prevent leakage and maintain sterile conditions.
- Casings and Housings: Plastic casings for devices such as infusion pumps or blood pressure monitors, which must be durable and resistant to wear and tear.
- Connectors and Tubing: Plastic connectors and tubing are vital in medical systems that deliver fluids or gases, like ventilators or IV drip systems.
The use of plastic machined components in spare parts offers durability and cost-effectiveness, ensuring that medical equipment remains operational with minimal downtime.
Processes Involved in Manufacturing Medical Machined Components
The production of medical machined components involves several critical processes, each requiring precision, attention to detail, and adherence to strict standards to ensure the safety and efficacy of the final product. Below is a detailed breakdown of these processes and the key considerations at each step.
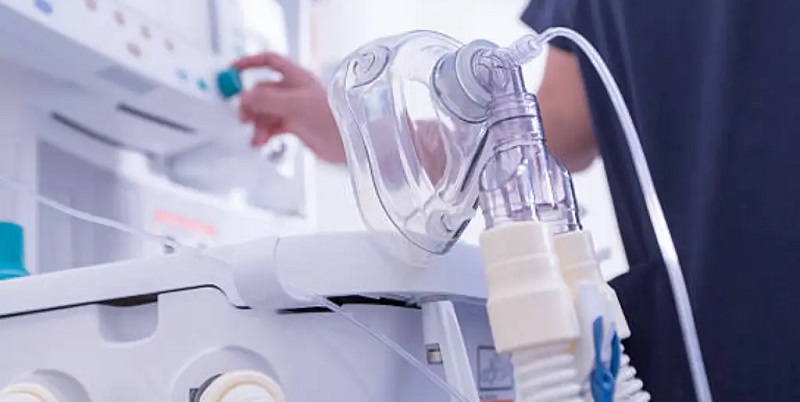
Conceptualization and Design
The journey begins with designing the component based on its intended application, whether for surgical tools, implants, or diagnostic equipment. This includes CAD modeling to create detailed designs and simulations.
Key Considerations:
- Ensure the design meets the functional requirements of the medical device.
- Consider biocompatibility, durability, and weight of materials.
- Use finite element analysis (FEA) to identify potential stress points or weaknesses.
Matters to Address: Poor design can lead to ineffective or unsafe components, so collaboration between engineers and medical experts is essential.
Material Selection
Choosing the right material is vital for biocompatibility, strength, and sterilization requirements. Common materials include stainless steel, titanium, PEEK, and medical-grade polymers.
Key Considerations:
- Verify that materials meet industry standards like ISO 10993 for biocompatibility.
- Ensure the material can withstand sterilization methods, such as autoclaving or chemical disinfection.
Matters to Address: Inappropriate material selection can lead to corrosion, breakage, or adverse biological reactions.
Prototyping
A prototype is created to test the design and functionality before moving into full production. This step often involves CNC machining for precision.
Key Considerations:
- Use prototyping to test for fit, performance, and usability.
- Identify and resolve design flaws at this stage to avoid costly changes later.
Matters to Address: Skipping or rushing this step can result in undetected defects that compromise the final product.
Precision Machining
The actual production involves CNC machining processes like milling, turning, drilling, and grinding to shape the component to exact specifications.
Key Considerations:
- Maintain tight tolerances to ensure compatibility with other parts.
- Implement consistent quality checks during machining.
Matters to Address: Poor machining practices can lead to deviations in dimensions, compromising the component’s performance.
Surface Finishing
After machining, surface treatments such as polishing, anodizing, or coating are applied to improve durability, functionality, and aesthetics.
Key Considerations:
- Ensure the finish meets cleanliness and sterility requirements.
- Choose finishes that enhance wear resistance or reduce friction for moving parts.
Matters to Address: Improper finishing can lead to surface defects, contamination, or reduced component lifespan.
Sterilization and Cleaning
Components are cleaned and sterilized to meet medical standards. This may involve autoclaving, ultrasonic cleaning, or chemical sterilization.
Key Considerations:
- Ensure the component is free from contaminants, debris, or residues.
- Verify that cleaning processes do not degrade the material.
Matters to Address: Inadequate sterilization can result in infections or regulatory non-compliance.
Quality Control and Testing
Process: Rigorous testing is performed to ensure the component meets functional, dimensional, and safety standards. Methods include visual inspection, stress testing, and dimensional analysis using CMM.
Key Considerations:
- Comply with ISO and FDA standards for medical devices.
- Implement traceability to document quality assurance processes.
Matters to Address: Skipping or minimizing quality control can lead to defective products reaching the market, risking patient safety.
Packaging and Distribution
Components are packaged in sterile conditions and prepared for shipping to medical facilities or assembly plants.
Key Considerations:
- Use packaging materials that maintain sterility and prevent contamination.
- Clearly label packaging with information such as lot numbers and expiration dates.
Matters to Address: Improper packaging can compromise sterility and lead to product recalls.
By following these detailed processes, manufacturers can ensure the production of high-quality medical machined components that meet the rigorous demands of the medical industry. Failing to address any of these steps can result in substandard products, jeopardizing patient safety and company reputation.
Key Considerations in Designing Medical Machined Components
Designing medical machined components requires a thorough understanding of various factors to ensure the components meet functional, safety, and regulatory requirements. Below is a detailed exploration of the key considerations, their importance, and the potential consequences of neglecting them.
Ductility
Ductility determines how well a material can deform under stress without breaking, which is critical for components that need to withstand bending or stretching during use.
Consequences of Neglect: Using low-ductility materials can lead to cracking or failure during surgical procedures, posing risks to patient safety and increasing liability for manufacturers.
Design Focus: Select materials like stainless steel or titanium with sufficient ductility to ensure durability and performance.
Tolerance Levels
Tight tolerances ensure components fit seamlessly into medical devices, maintaining functionality and preventing malfunctions.
Consequences of Neglect: Poor tolerance control can lead to misaligned parts, device failures, or compromised precision in surgeries, potentially endangering patient outcomes.
Design Focus: Utilize precision machining technologies like CNC to achieve high accuracy and consistency in tolerances.
Tension Requirements
Components subjected to tension, such as surgical wires or fasteners, must handle the forces applied during use without deformation or breakage.
Consequences of Neglect: Ignoring tension requirements can lead to mechanical failure under stress, causing device malfunction during critical procedures.
Design Focus: Conduct rigorous stress tests and select materials with appropriate tensile strength.
Disposal and Disinfection Requirements
Medical components often require sterilization and disposal methods that align with hospital protocols and regulatory standards.
Consequences of Neglect: Inadequate material selection or design can lead to components that degrade under repeated sterilization or cannot be safely disposed of, increasing contamination risks.
Design Focus: Choose biocompatible materials that can withstand high-temperature sterilization or chemical exposure, and ensure designs facilitate easy cleaning and safe disposal.
Biocompatibility
Components used in implants or devices that come into contact with human tissues must not cause adverse reactions.
Consequences of Neglect: Using non-biocompatible materials can result in allergic reactions, infections, or rejection of the implant.
Design Focus: Opt for materials such as titanium, PEEK, or certain medical-grade polymers that are proven safe for human use.
Regulatory Compliance
Adhering to medical device regulations ensures that components meet industry standards for safety and effectiveness.
Consequences of Neglect: Failure to comply can lead to legal penalties, product recalls, and damage to the manufacturer’s reputation.
Design Focus: Follow guidelines set by regulatory bodies like the FDA or ISO for medical devices.
By addressing these critical aspects in the design of medical machined components, manufacturers can ensure the safety, reliability, and effectiveness of their products. Neglecting these factors not only compromises device performance but also endangers patient health and exposes manufacturers to significant risks.
How to Choose a Precision Machining Production Workshop for Medical Machined Components
Selecting the right precision machining production workshop for medical machined components is a critical decision that impacts the quality, reliability, and compliance of the medical devices being manufactured. Below is a detailed guide on factors to consider during the selection process and why each is important.
Expertise in Medical Machining
Medical components demand high precision, biocompatibility, and compliance with strict regulatory standards. A workshop with specialized experience in medical machining will have the knowledge to meet these requirements.
What to Look For: Check if the workshop has a history of producing parts for medical devices, implants, or surgical instruments and if their team includes engineers familiar with medical-grade materials and processes.
Advanced Equipment and Technology
Precision machining for medical components requires advanced tools like CNC machines, milling machines, and turning centers that ensure high accuracy and consistency.
What to Look For: Ensure the workshop uses modern equipment capable of meeting tight tolerances and intricate designs. Ask about their maintenance schedule to confirm the reliability of their machinery.
Compliance with Regulatory Standards
Medical components must adhere to strict standards such as ISO 13485 for medical devices or FDA regulations for product safety and efficacy.
What to Look For: Verify if the workshop is certified under relevant standards and familiar with documentation and reporting requirements to ensure regulatory compliance.
Material Knowledge and Availability
Medical components require materials like stainless steel, titanium, or PEEK, which must be biocompatible and durable.
What to Look For: Choose a workshop with expertise in machining these materials and access to high-quality material suppliers. Ask if they can provide certifications for material compliance.
Quality Assurance and Inspection Capabilities
The performance of medical components relies on precise manufacturing and thorough inspection to eliminate defects.
What to Look For: Ensure the workshop has robust quality control systems, including advanced metrology tools like coordinate measuring machines (CMM) and surface finish testers. Check for a clear process for defect identification and resolution.
Production Capacity and Flexibility
Whether for prototyping or large-scale production, the workshop must be able to accommodate your project needs without delays.
What to Look For: Evaluate their capacity for low-volume and high-volume production. Discuss lead times and their ability to handle custom orders or urgent requirements.
Reputation and References
A well-regarded workshop with positive client feedback is more likely to deliver reliable results.
What to Look For: Ask for client references, reviews, or case studies. A workshop with a solid reputation in the medical industry demonstrates trustworthiness and expertise.
Cost-Effectiveness
Balancing cost with quality is essential to maintaining competitive pricing while ensuring high standards.
What to Look For: Request detailed quotes and compare them with other workshops. Avoid choosing solely based on cost—focus on value for money by weighing quality and capabilities.
By carefully evaluating these factors, you can select a precision machining production workshop capable of delivering high-quality medical machined components that meet your technical, regulatory, and cost requirements. A reliable workshop ensures the success of your medical devices and contributes to better patient outcomes.
FAQs about Medical Machined Components
Machined components are parts that have been precisely manufactured using various machining techniques such as milling, turning, and drilling. These processes involve the removal of material from a raw material to create parts with specific shapes and sizes. The primary goal is to achieve high accuracy, tight tolerances, and superior surface finishes that meet strict industry standards. In various industries, including automotive, aerospace, and medical sectors, machined components play a crucial role in ensuring the proper function of complex systems. For instance, in the medical field, machined components are used in surgical instruments, implants, diagnostic devices, and prosthetics. These components must adhere to strict quality and safety regulations, ensuring that they perform reliably and safely in critical applications. The use of advanced machining techniques, such as CNC (Computer Numerical Control) machining, allows for the production of intricate, high-precision medical machined components, ensuring optimal functionality and patient safety.
A component of a medical device refers to any individual part or assembly that makes up a complete medical device, contributing to its function and overall performance. These components can range from mechanical elements like gears, screws, and handles, to electronic parts such as sensors and batteries, or even software that controls the device. In medical devices, components must be carefully designed and manufactured to meet stringent regulatory requirements for safety, efficacy, and biocompatibility. Common components include surgical instruments like scalpels, diagnostic parts like CT scanner detectors, and implantable devices such as pacemakers or prosthetic joints. Each component serves a vital role in ensuring the device performs its intended purpose, whether it’s monitoring a patient’s health, aiding in diagnosis, or facilitating a surgical procedure. Components in medical devices often need to withstand extreme conditions like sterilization and contact with bodily fluids, making material selection and precision manufacturing essential.
CNC (Computer Numerical Control) in the medical field refers to the use of computer-controlled machinery to manufacture high-precision components for medical devices. CNC machines operate by following pre-programmed instructions that control the movement of tools to shape materials like metals and plastics. This level of precision is critical in the medical industry, where even the smallest deviations in size or shape could affect the functionality of a medical device. CNC machining is used extensively to create medical machined components, such as surgical instruments, implants, and diagnostic equipment. One of the key advantages of CNC machining in the medical field is its ability to produce complex geometries and maintain high standards of quality and accuracy, which is essential for patient safety. Additionally, CNC technology allows for customization and small-batch production, making it ideal for the creation of patient-specific prosthetics or implants, further advancing personalized medicine.
Medical devices are made from a wide range of materials, selected for their unique properties to meet specific requirements for safety, durability, and performance. Common materials include metals like stainless steel, titanium, and cobalt-chromium alloys, which are favored for their strength, biocompatibility, and resistance to corrosion. Stainless steel, for example, is widely used in surgical instruments and diagnostic devices because it is durable, easy to sterilize, and non-reactive with human tissues. Titanium is often used for implants due to its lightweight and superior biocompatibility, which minimizes the risk of rejection by the body. Other materials include high-performance plastics such as PEEK (Polyetheretherketone) and UHMWPE (Ultra-High Molecular Weight Polyethylene), which are used for implants and prosthetics, offering strength, flexibility, and resistance to wear. Additionally, ceramics and silicone are used in certain medical devices, like dental implants and seals, for their biocompatibility and ability to withstand sterilization processes. Each material is carefully chosen to ensure the safety and effectiveness of the medical device, meeting both regulatory standards and the needs of patients.
Contact our professional team now for a same-day quote and risk-free project evaluation. Benefit from ISO 8 cleanrooms, advanced machines, and 12-hour fast response in medical injection molding.