Medical micro molding is a cutting-edge plastic injection molding technique designed to produce incredibly small and intricate components for medical applications. With the ability to achieve micron-level precision, this process ensures the creation of components essential for advanced healthcare devices. From diagnostic tools to drug delivery systems, medical micro molding, along with extrusion molding medical, supports innovations in minimally invasive medical technologies, enabling better patient outcomes and efficient treatment solutions. As healthcare continues to evolve, the demand for micro components has surged. This growth is fueled by wearable medical devices, robotic-assisted surgeries, and personalized medicine. Medical micro molding plays a critical role in meeting these demands by delivering scalable solutions for high-precision, high-performance medical device manufacturing. Medical micro molding is a high-precision process for creating complex, miniature components for medical devices using advanced polymers.
Low-Volume to High-Volume Production Capabilities
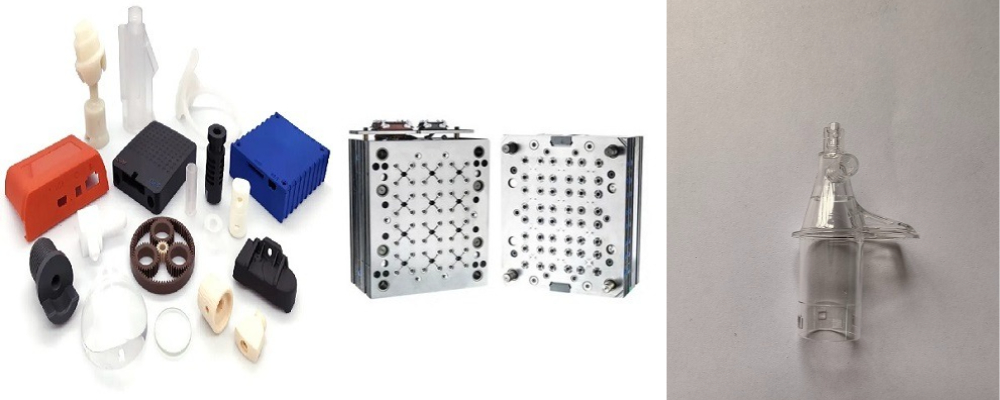
Attributes | Details |
---|---|
Place of Origin | Dongguan, Guangdong, China |
Brand Name | LY Medical Injection Mold |
Product Name | Medical Micro Molding |
Molding Mode | Plastic Injection |
Product Material | Plastic |
Surface Treatment | Anodizing, Polishing, Powder Coating, Screen Printing, Painting, etc. |
Features | High Precision |
Color | Customized |
Size | Customized |
Length | Customized |
Style | Customized |
Service | OEM ODM |
Processing Service | Molding, Cutting |
Logo | Customized Logo Acceptable |
Supplier | Manufacturer |
Quality Control | 100% Inspection |
Minimum Order Quantity | Small Order Accepted |
Packing Details | Outer Packaging Carton Inner Packaging According to Customer Requirement |
Port | According to Your Requirement |
What is Medical Micro Molding
Medical micro molding is a highly specialized manufacturing process used to produce miniature, intricate components for the medical field with micron-level precision. This advanced plastic injection molding technique involves injecting molten polymers into micro-scale molds designed to maintain extremely tight tolerances. It is essential for creating components with the high precision and consistency required for life-saving devices. The process incorporates strict validation measures to ensure all components meet medical-grade standards. Materials used in medical micro molding are carefully selected for their biocompatibility and durability, including high-performance polymers like PEEK and medical-grade silicones. These materials enable the production of safe and effective parts that comply with stringent healthcare regulations.
The applications of medical micro molding span a wide range of healthcare needs, including minimally invasive devices like catheters, implantable systems such as stents, and diagnostic tools like microfluidic chips. Its benefits include unmatched precision, scalability for mass production, and the ability to customize components for specific applications. This process also ensures compliance with medical industry standards, making it essential for producing advanced surgical tools, implants, and diagnostic devices. By combining innovative materials, precise technology, and rigorous quality control, medical micro molding continues to drive innovation and improve outcomes in the healthcare industry.
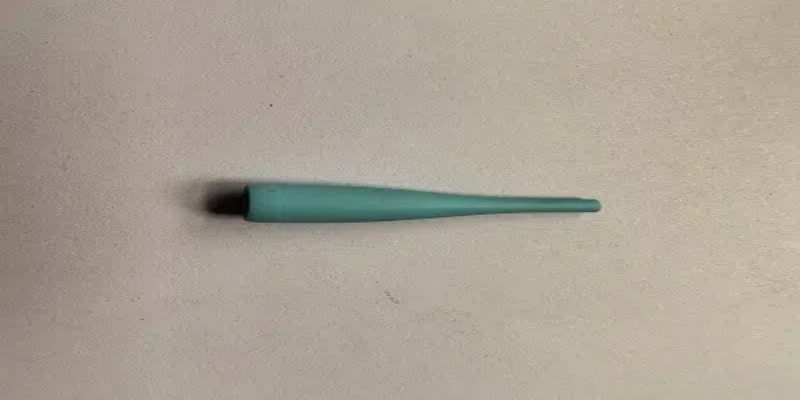
FUJIU Medical Injection Mold Supplier
At FUJIU Medical Injection Mold Supplier, we take immense pride in being more than just a manufacturer—we are your dedicated partner in success. Specializing in custom precision medical molds and injection-molded plastic products, we focus on delivering outstanding value and exceptional service tailored to the medical industry. With over 20 years of expertise in precision mold manufacturing and more than a decade of experience in project and supply chain management, we are uniquely equipped to meet the rigorous demands of the medical sector.
Our capabilities in medical micro molding are second to none. With cutting-edge injection molding technologies, an ISO Class 8 cleanroom, and a fleet of 20 state-of-the-art machines, we ensure the production of micro-scale medical components with unmatched precision and quality. From product development to meticulous mold design, material selection, and efficient production, FUJIU Medical Injection Mold Supplier is committed to advancing healthcare through innovation, integrity, and excellence.
The Role of Medical Micro Molding in Healthcare
Medical micro molding plays a transformative role in the healthcare industry by enabling the creation of highly precise, miniature components essential for advanced medical devices. With its unparalleled ability to meet stringent tolerances and produce complex geometries, this technology is a cornerstone of innovation in modern medicine.
Applications in Medical Devices
Medical micro molding is indispensable for developing a wide range of medical devices. Its precision allows the production of intricate components that drive innovation in diagnostics, treatment, and patient care.
Microfluidic Components for Diagnostics
Medical micro molding enables the production of microfluidic channels and systems used in diagnostic devices, allowing precise control of fluids at microscopic scales.
Soft Mist Inhaler Components
Intricate parts molded through this process ensure consistent and effective delivery of medication via soft mist inhalers.
Catheter Tips for Cardiovascular Applications
Medical micro molding supports the creation of catheter tips, critical for minimally invasive cardiovascular procedures, ensuring optimal flexibility and precision.
Specialized Uses
- Insert-molded battery connectors for cardiac devices.
- Micro-needle arrays for precise drug delivery.
- Thin-wall cannulae for surgeries requiring fine control and accuracy.
- Therapeutic Areas Served
Medical micro molding impacts a broad spectrum of therapeutic fields:
- Cardiology: Devices for minimally invasive heart procedures.
- Neurology: Micro components for neural stimulators and monitoring systems.
- Orthopedics: Surgical tools and implants for precision treatments.
- Urology: Components for diagnostic and therapeutic systems.
- Ophthalmology: Molds used in tools for delicate eye surgeries.
By addressing these diverse applications, medical micro molding continues to drive advancements in healthcare, improving patient outcomes and enabling groundbreaking treatments.
Key Features of Medical Micro Molding
Medical micro molding is defined by its ability to deliver high precision medical components, material versatility, and scalable manufacturing, making it a critical process in modern healthcare device production. These features enable manufacturers to create complex, tiny parts that meet the demanding requirements of medical applications.
Precision and Tolerances
One of the most defining aspects of medical micro molding is its exceptional precision.
- Ultra-Small Components
Components produced through this technology often weigh less than 0.001 grams and can incorporate features as small as a micron, enabling their use in advanced medical devices requiring microscopic precision. - Thin-Wall Molding
Medical micro molding allows for thin-wall molding, achieving wall thicknesses as fine as 0.006 inches. This capability is vital for creating lightweight, flexible components used in minimally invasive surgical tools and diagnostic equipment.
Precision is achieved through meticulous tool design and advanced molding techniques, ensuring consistent quality even for high-volume production runs.
Material Versatility
Medical micro molding supports a wide range of high-performance engineered materials tailored to specific medical applications.
- High-Performance Plastics
Materials like PEEK, Ultem, and other bioresorbable materials, such as PLA, provide durability, biocompatibility, and functionality for medical devices. - Application-Specific Material Selection
Matching materials to the intended use is crucial. For example, bioresorbable polymers are ideal for temporary implants, while PEEK excels in applications requiring high strength and chemical resistance.
This versatility ensures that medical micro molding can meet the diverse needs of healthcare devices, from long-term implants to disposable tools.
Manufacturing Scalability
Scalability is another critical feature of medical micro molding, allowing manufacturers to produce micro components efficiently in large quantities.
- High-Volume Production
Advanced techniques enable the creation of up to 10,000 parts per pound of resin, including runners, without sacrificing quality or precision. - Cost-Effective Manufacturing
The ability to combine precision and volume reduces waste and production costs, making medical micro molding an economical solution for the healthcare industry.
By combining these key features, medical micro molding addresses the growing demand for sophisticated, high-quality medical components, supporting innovations that enhance patient care and treatment outcomes.
Medical Micro Molding: Micro Molding Capabilities and Technologies
Medical micro molding is supported by advanced techniques, complementary services, and rigorous quality control measures, ensuring that the process meets the exacting requirements of medical device plastic manufacturing. These capabilities enable the production of highly complex and precise components for a wide range of applications.
Advanced Molding Techniques
Medical micro molding relies on cutting-edge molding methods to create intricate parts with unparalleled precision and functionality.
Micro Injection Molding
This technique forms the foundation of medical micro molding. It is designed for producing tiny, intricate components with tight tolerances, often measured in microns. The process uses specialized equipment to achieve precision while minimizing material waste.
Two-Shot Molding
Two-shot molding enables the integration of two different materials into a single part. This capability is particularly valuable for components requiring multi-material functionality, such as combining hard and soft polymers for enhanced performance.
Overmolding
Overmolding combines multiple materials or layers to create complex, functional parts. In medical micro molding, overmolding is often used to add soft grips, encapsulate electronics, or bond materials with distinct properties into a single cohesive structure.
Complementary Services
To support the precision and quality required in medical micro molding, manufacturers offer a range of complementary services.
Micro Tooling
Micro tooling is essential for creating the precision medical molds used in the process. High-quality micro tooling ensures that each component is formed with exact dimensions and consistency, even at high production volumes.
Laser Processing
Laser processing provides detailed finishing and post-mold enhancements, such as cutting, engraving, or adding micro-scale features. This step is crucial for refining parts used in delicate medical applications.
Prototyping and Material Testing
In-house prototyping allows manufacturers to rapidly test designs, ensuring their feasibility and performance before full-scale production. Material testing ensures compatibility, durability, and compliance with medical standards.
Inspection and Quality Control
Inspection and quality control are central to medical micro molding, ensuring that all components meet the strict requirements of the healthcare industry.
- Regulatory Compliance
Facilities involved in medical micro molding are often FDA-registered and ISO 13485-certified. These certifications reflect a commitment to adhering to the highest standards for medical device manufacturing. - High-Resolution Metrology
Advanced metrology systems are employed to measure micro-scale features with precision. These tools ensure that each component meets design specifications, avoiding costly errors or rework.
By leveraging these advanced capabilities and technologies, medical micro injection molding continues to set the standard for innovation, precision, and reliability in the production of medical components.
Commonly Used Materials in Medical Micro Molding
In medical micro molding, the selection of materials plays a critical role in achieving the precision, functionality, and safety required for medical applications. These materials must possess unique characteristics such as biocompatibility, durability, and the ability to be molded into intricate shapes with tight tolerances. Below, we explore the most commonly used materials in medical micro molding, categorized by their properties and applications.
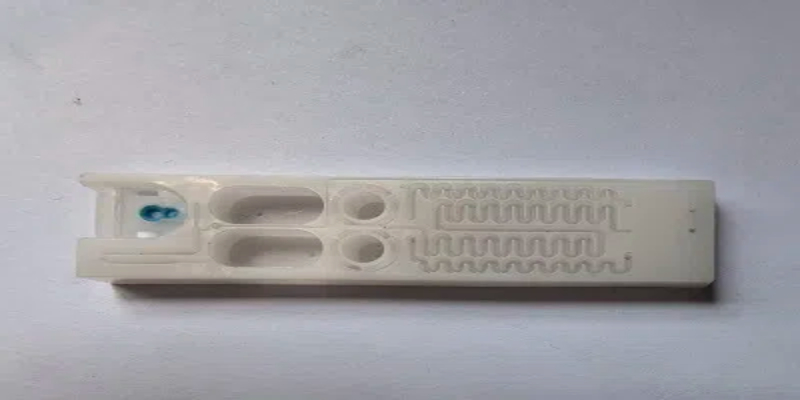
Thermoplastics for Versatility and Precision
Thermoplastics are widely used in medical micro molding due to their versatility and precision. These materials are capable of forming complex geometries and provide excellent mechanical properties.
- Polyethylene (PE): Known for its flexibility and chemical resistance, ideal for tubing and catheter components.
- Polypropylene (PP): Offers high strength and resistance to fatigue, making it suitable for syringes and implantable devices.
- Polycarbonate (PC): Valued for its transparency and impact resistance, used in optical medical instruments and housings.
High-Performance Polymers for Specialized Applications
High-performance polymers excel in demanding medical environments where durability, heat resistance, and biocompatibility are essential.
- PEEK (Polyether Ether Ketone): Frequently used in implants due to its strength and excellent biocompatibility.
- Ultem (Polyetherimide): Withstands high temperatures and sterilization processes, ideal for surgical instruments.
- LCP (Liquid Crystal Polymer): Ensures precision for small, detailed components like microfluidic devices.
Elastomers for Flexibility and Sealing
Elastomers are essential for creating flexible, soft components used in sealing and cushioning applications.
- Silicone Rubber: Commonly used for seals, gaskets, and implantable devices due to its biocompatibility and flexibility.
- TPE (Thermoplastic Elastomers): Combines the characteristics of rubber and plastic, offering flexibility and ease of processing.
Biocompatible Materials for Safety
Medical applications require materials that can safely interact with the human body.
- Medical-Grade Polymers: Specifically certified for biocompatibility to meet regulatory standards.
- Resorbable Polymers: Such as polylactic acid (PLA) and polyglycolic acid (PGA), used in temporary implants and sutures.
Composite Materials for Enhanced Performance
Composite materials combine properties of multiple substances to achieve superior performance in micro molding.
- Reinforced Polymers: Include fillers like glass or carbon fibers to improve strength and rigidity.
- Metal-Polymer Hybrids: Combine the conductivity of metals with the moldability of plastics for advanced medical devices.
By selecting the appropriate material based on the specific application and required properties, medical micro molding enables the creation of innovative, life-saving components that meet the highest industry standards.
Expanding the Scope of Medical Micro Molding
The medical micro molding market is a dynamic and rapidly evolving sector driven by demand for precision, innovation, and scalability. Combining cutting-edge technologies like micro medical molding and micro medical injection molding services, manufacturers cater to the growing needs of the healthcare industry by producing components with incredible accuracy and functionality.
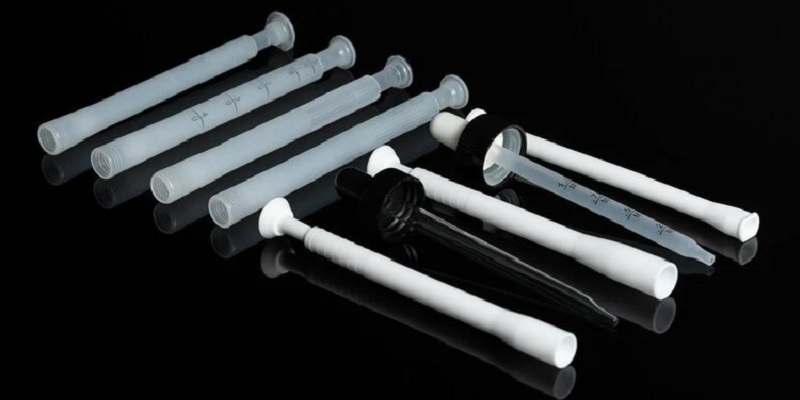
Medical Micro Molding Market
The medical micro molding market has grown significantly in recent years, propelled by advancements in minimally invasive devices, wearable health technologies, and diagnostic tools. The market is characterized by:
Rising Demand for Precision Parts
The increasing complexity of medical devices drives the need for micro-molded components with tolerances as tight as a micron.
Emergence of Bioabsorbable Materials
The use of bioresorbable polymers in temporary implants and drug delivery systems is expanding, further fueling market growth.
Regional Growth Opportunities
North America, Europe, and Asia-Pacific regions are leading in investment and technological advancements, making the market globally competitive.
Medical Micro Molding and Micro Injection Molding Services
These two complementary services form the backbone of producing intricate medical components. While medical micro injection molding focuses on ultra-small, high-precision parts, micro injection molding for medical devices excels in creating components with complex geometries, thin walls, and multi-material designs.
Manufacturers offering both services can meet diverse customer requirements, such as:
- Device Customization: Tailoring designs for specific applications, including catheter tips, needle hubs, and surgical instruments.
- High-Volume Production: Efficient medical molding manufacturing processes enable the production of millions of micro-scale parts with consistent quality.
Medical Micro Molding and Extrusions
Medical devices often combine molded components with extruded parts. Medical micro molding and extrusions work in tandem to deliver comprehensive solutions:
- Tubing Integration: Extrusions like microbore tubing and multilumen shafts are combined with micro-molded connectors or fittings for complete assemblies.
- Advanced Catheter Designs: Micro-molded hubs, tips, and transition points enhance catheter performance while maintaining precision.
Micro Injection Molding for Medical Devices
Micro injection molding is essential for producing a wide variety of medical components, including:
- Drug Delivery Systems: Small, complex parts for inhalers, autoinjectors, and micro-needle arrays.
- Surgical Tools: Components with tight tolerances for minimally invasive procedures.
- Implantable Devices: Biocompatible and bioresorbable parts that integrate seamlessly with the human body.
Medical Micro Plastic Injection Parts
Medical micro plastic injection parts form the core of numerous healthcare solutions. These parts are critical for delivering functionality and durability in life-saving devices:
- Diagnostic Devices: Microfluidic chips and connectors for lab-on-a-chip technologies.
- Cardiovascular Applications: Thin-wall cannulae and catheter components for precise medical interventions.
- Wearable Technologies: Lightweight, compact parts for health monitoring and diagnostic wearables.
This expanded integration of medical micro molding, micro injection molding, and extrusions allows the healthcare industry to push the boundaries of innovation and patient care, making the technology indispensable in modern medical device manufacturing.
Requirements for Medical Micro Molding Production and Manufacturer Qualifications
Medical micro molding demands an advanced production environment and adherence to stringent industry standards to meet the precision, safety, and reliability required in medical applications. The production environment, certifications, and specialized skills play a crucial role in ensuring quality. Below, we explore these requirements in detail, emphasizing the critical factors manufacturers must address to excel in medical micro molding.
Controlled Production Environment
A controlled production environment is essential for medical micro molding to maintain precision, cleanliness, and product integrity.
- ISO-Class Cleanrooms: Manufacturing must take place in an ISO Class 7 or 8 cleanroom to minimize contamination risks. These environments ensure that dust, particulates, and other contaminants are kept at safe levels.
- Temperature and Humidity Control: Maintaining consistent conditions prevents material degradation and ensures accurate molding processes.
- Specialized Equipment: Precision micro molding machines with tight tolerance capabilities and advanced control systems are required to handle the intricate demands of micro components.
Compliance with Regulatory Standards and Certifications
Manufacturers must obtain specific certifications to demonstrate their capability to produce safe, high-quality medical micro molding components.
- ISO 13485 Certification: Demonstrates adherence to medical device quality management systems and regulatory compliance.
- FDA Compliance: Ensures that products meet U.S. Food and Drug Administration requirements for safety and performance.
- Biocompatibility Standards: Materials and processes must comply with ISO 10993 or USP Class VI standards to ensure safety for human contact.
- Environmental Compliance: Adherence to sustainability practices, such as RoHS and REACH, ensures environmentally friendly production processes.
Technical Expertise and Skilled Workforce
Producing medical micro molding components requires highly trained professionals with specialized skills in design, engineering, and manufacturing.
- Material Science Expertise: Knowledge of biocompatible and high-performance polymers is crucial for selecting the right material for each application.
- Precision Engineering Skills: Operators must be skilled in designing molds and running micro injection molding machines to maintain tolerances within microns.
- Quality Assurance Expertise: Manufacturers need robust quality control systems, including advanced metrology tools for inspection and verification of micro-sized components.
Advanced Quality Control and Testing Capabilities
Ensuring product performance and safety is paramount in medical micro molding. Manufacturers must implement rigorous quality control systems.
- Metrology Equipment: Use of high-resolution microscopes and 3D scanners for dimensional analysis of micro components.
- Process Validation: Comprehensive testing and validation of molding processes to ensure repeatability and reliability.
- Sterilization Readiness: Ability to handle sterilization requirements, such as gamma irradiation or autoclaving, depending on the medical application.
Research and Development Capabilities
Continuous innovation is key in medical micro molding. Manufacturers must invest in R&D to stay at the forefront of technology.
- Prototyping Services: Rapid prototyping helps in refining designs and ensuring feasibility before full-scale production.
- Process Optimization: Advanced simulations and testing to optimize material flow, cooling, and other process parameters for high precision.
By adhering to these stringent requirements, manufacturers can meet the complex demands of medical micro molding, ensuring the production of safe, effective, and reliable components for medical applications.
Future of Medical Micro Molding
The future of medical micro injection molding is filled with exciting possibilities, driven by emerging trends, technological advancements, and significant industry growth. As the demand for precise, small-scale components in medical devices grows, new developments are enhancing the capabilities of this specialized manufacturing technique.
Emerging Trends in Medical Micro Molding
One notable trend is the increasing use of bioresorbable materials for implantable devices. These materials dissolve within the body over time, eliminating the need for removal surgeries and reducing the risk of long-term complications. Medical micro molding is ideally suited to shape these delicate, bioresorbable components with the required precision. Additionally, the integration of Medical Micro Molding with additive manufacturing (3D printing) is gaining traction. This combination allows for the creation of complex geometries, where 3D printing handles intricate designs and micro molding ensures high-volume production of precise, consistent parts.
Technological Innovations Shaping the Industry
In terms of technological innovations, advances in micro metrology are enabling more precise measurements of microscopic features, which is essential for meeting the high standards required in medical device manufacturing. Furthermore, high-speed injection molding is evolving, providing faster production cycles while maintaining the precision that medical micro molding demands. The development of ultra-fast lasers for precision detailing is also transforming the industry. These lasers enhance the ability to create highly detailed cuts and finishes on molded components, which is crucial for medical applications that require minute features, such as micro-holes or specialized surface textures.
Industry Growth and Expanding Applications
Wearable Technology and Medical Micro Molding
The demand for wearable technology, such as health monitoring devices, is rapidly growing, and medical micro molding plays a vital role in producing the miniaturized components needed for these devices. From sensors to connectors, medical micro molding ensures that even the smallest parts meet stringent medical requirements while being functional and reliable.
Personalized Medicine and Medical Micro Molding
Personalized medicine is creating a shift in healthcare by focusing on individualized treatments and devices. As a result, there is an increasing need for customized, high-precision components that medical micro molding is ideally suited to manufacture. This includes custom implants, patient-specific tools, and specialized devices tailored to unique medical conditions.
Advanced Diagnostics and Micro Molding
Medical micro molding is also finding expanding applications in advanced diagnostic tools. With the increasing emphasis on early detection and preventative care, medical devices that require intricate, high-precision parts are becoming more common. Micro-molded components are crucial in ensuring the accuracy and reliability of diagnostic devices such as microfluidic chips, sensors, and other miniature systems.
The future of medical micro injection molding holds tremendous potential, as these trends, innovations, and growing applications continue to shape the future of medical technology.
FAQs about Medical Micro Molding
Injection molding, especially for medical micro molding, is challenging to perform at home due to the precise equipment, materials, and expertise required. Medical micro molding involves creating extremely small and intricate parts, often requiring specialized machines capable of high pressure and precise temperature control. While some hobbyists attempt small-scale injection molding at home using manual or desktop machines, producing medical-grade components requires cleanroom environments and strict quality control. Additionally, materials used in medical micro molding, like biocompatible thermoplastics, need precise handling. Home setups rarely meet these standards, making professional facilities the best option for medical-grade injection molding.
Injection molding in medical micro molding involves injecting molten plastic or polymer into a precisely machined mold to form complex, miniature components. The process starts with material preparation, where medical-grade polymers are dried and loaded into the machine. The material is heated and melted in the barrel, then injected into a mold cavity under high pressure. After cooling and solidifying, the mold opens, and the part is ejected. In medical micro molding, advanced technology ensures tight tolerances and consistent quality, essential for devices like catheters, surgical tools, and implantable components. Precision, biocompatibility, and regulatory compliance are central to the process.
In medical micro molding, molding begins with designing a precise mold tailored to the component’s specifications. The mold, often made of hardened steel or aluminum, includes intricate cavities to shape the part. Medical-grade polymer is heated, melted, and injected into the mold under high pressure. The material fills the mold cavities, forming the part’s exact shape. The mold is cooled to solidify the material, after which it opens, and the component is ejected. Post-molding steps include quality checks and surface finishing. Cleanroom environments and tight tolerances are critical in medical applications to ensure biocompatibility and functionality.
The duration of medical micro molding depends on factors like part complexity, material, and machine settings. Typically, a single injection molding cycle can take 10 to 60 seconds. For micro molding, where precision is paramount, cycles may be slightly longer to ensure uniform filling and proper cooling of intricate features. Initial setup, including mold design and production, can take weeks to months. Once the mold is prepared, high production speeds make injection molding efficient for large-scale manufacturing. In medical applications, stringent quality checks may add time, but they are essential for ensuring reliability and safety.
The cost of producing a small injection mold for medical micro molding varies widely, ranging from $5,000 to $50,000 or more. Factors affecting the cost include mold complexity, material, and precision. Medical micro molds require advanced engineering to achieve tight tolerances and biocompatibility, which adds to the expense. Multi-cavity molds, used for high-volume production, are more costly but reduce per-part manufacturing costs. Cleanroom compatibility and validation for medical applications also increase costs. Despite the initial investment, injection molding is cost-effective for producing large volumes of precise, high-quality medical components.
Injection molding, particularly in the medical micro molding sector, can be highly profitable due to the demand for precision components in healthcare. The high initial costs of mold production are offset by low per-part manufacturing costs in large-scale production. Medical applications, such as surgical tools and implantable devices, often command premium prices due to stringent quality requirements. The profitability of injection molding depends on factors like production volume, part complexity, and market demand. Companies that invest in advanced technology and cater to niche medical needs often see significant returns on investment.
Medical micro molding can produce parts as small as a fraction of a millimeter. Advanced injection molding machines are designed to handle extremely fine details and tight tolerances, making it possible to create micro-components for medical devices like sensors, catheters, and implants. Precision is achieved through micro-machined molds, specialized materials, and advanced process control. Parts with intricate features, such as wall thicknesses below 0.1 mm, are achievable. This capability is critical for modern medical technology, enabling the development of minimally invasive devices and complex diagnostic tools.
In medical micro molding, parts can be molded with walls as thin as 0.1 mm or less, depending on the material and design. Achieving such thinness requires advanced machinery, precise mold design, and carefully selected medical-grade polymers with excellent flow properties. Thin-walled molding is often used for components like microfluidic devices, where fine channels and structures are essential for functionality. Maintaining uniformity and avoiding defects like warping or incomplete fills is critical, requiring tight process control. Thin-walled parts are essential in medical applications for reducing size and weight without compromising performance.
Injection molding is generally more cost-effective than machining for producing large volumes of medical micro components. While mold creation is expensive, the low per-part cost in high-volume production offsets this initial investment. Machining, on the other hand, is better suited for low-volume or prototype production due to higher per-part costs and slower production speeds. Injection molding is also superior for creating complex, repeatable designs with tight tolerances, which are critical in medical applications. For long-term projects requiring consistent quality and large-scale production, injection molding is the more economical choice.
The upfront cost of injection molding is high due to mold design and production, which can range from thousands to tens of thousands of dollars. However, the process becomes cost-effective for high-volume production, where the per-part cost decreases significantly. Medical micro molding adds costs for precision, biocompatible materials, and cleanroom operations. Despite these expenses, injection molding’s ability to produce large quantities of high-quality, consistent parts makes it a cost-efficient choice for medical applications. Over time, the initial investment is justified by reduced production costs and high reliability.
Injection molding, especially for medical micro molding, requires specialized knowledge, advanced equipment, and rigorous quality control, making it a complex process. Challenges include designing precise molds, selecting suitable materials, and maintaining consistent production quality. Medical-grade components often require compliance with strict regulatory standards, adding to the complexity. While the process itself is automated, achieving optimal results requires expertise in mold design, material science, and process optimization. For these reasons, injection molding is best left to experienced professionals in well-equipped facilities, particularly for critical applications like medical device manufacturing.
Injection molding is generally a fast process, especially for producing large volumes of small, precise parts, such as in medical micro molding. The actual injection cycle, including material heating, injection, cooling, and ejection, typically takes 10 to 60 seconds per part. However, the overall timeline includes time for mold design and production, which can take weeks or months. For medical micro molding, where high precision and biocompatibility are essential, additional time is required for quality control and regulatory compliance. While the setup is time-intensive, the process is efficient once production begins, making it ideal for high-volume manufacturing.
The five key steps in medical micro molding are:
Material Preparation: Medical-grade polymers are dried and prepared for molding to ensure optimal performance.
Melt Injection: The material is melted and injected into the mold under high pressure.
Filling and Cooling: The molten material fills the mold cavities, cools, and solidifies into the desired shape.
Part Ejection: The mold opens, and the formed part is ejected.
Post-Processing: Includes quality checks, cleaning, and finishing, particularly critical in medical applications to meet stringent standards.
Alternatives to injection molding for medical micro components include:
3D Printing: Suitable for prototyping or small-scale production; offers design flexibility but lacks the speed and cost-efficiency of molding for high volumes.
CNC Machining: Precise and versatile, ideal for low-volume production but more expensive for large runs.
Compression Molding: Suitable for simpler parts but less precise than injection molding.
Cast Molding: Effective for prototypes or small batches but slower and less scalable.
While these alternatives have their uses, injection molding remains the best choice for mass production of intricate, biocompatible medical parts.
While effective for medical micro molding, injection molding has some disadvantages:
High Initial Costs: Mold design and manufacturing require significant investment.
Long Setup Time: Preparing molds and processes takes weeks to months.
Material Limitations: Not all materials are suitable for medical applications.
Defects: Errors like warping or incomplete fills may occur if parameters are not optimized.
Despite these challenges, injection molding is the most efficient and precise method for producing medical micro components at scale.
The four stages in medical micro molding are:
Clamping: The mold halves are securely clamped together.
Injection: Molten material is injected into the mold.
Cooling: The material cools and solidifies in the mold cavity.
Ejection: The mold opens, and the finished part is removed.
These stages ensure precise and consistent production, essential for high-quality medical components.
Key techniques in medical micro molding include:
Thermoplastic Micromolding: Common for medical devices; uses biocompatible polymers.
LIM (Liquid Injection Molding): Ideal for silicone-based components.
Micro-Injection Compression Molding: Combines injection and compression for improved precision.
Insert Micromolding: Embeds pre-made components into the molded part.
These techniques allow for the creation of intricate, miniature medical parts with high precision and biocompatibility.
The three primary types of molding relevant to medical applications are:
Injection Molding: Ideal for high-volume, precise components.
Compression Molding: Used for simpler parts with fewer design complexities.
Blow Molding: Suited for creating hollow parts like medical containers.
For medical micro molding, injection molding is the most effective due to its precision and scalability.
The two most common injection molding processes are:
Thermoplastic Injection Molding: Uses plastic materials that can be melted and reshaped.
Liquid Silicone Rubber (LSR) Molding: Produces flexible, biocompatible parts ideal for medical applications.
Both methods are widely used in medical micro molding, depending on the part’s requirements.
Challenges of medical micro molding include:
Cost: High initial costs for mold design and production.
Defect Risks: Issues like flash or warping can occur without precise control.
Material Restrictions: Not all polymers are suitable for medical use.
Despite these drawbacks, injection molding is the most reliable method for mass-producing intricate, high-quality medical components.
For low-volume or complex prototypes, 3D Printing can be better due to faster setup and greater design flexibility. However, for large-scale production of medical micro components, injection molding remains superior in terms of cost, precision, and scalability.
Compression Molding and Cast Molding are generally cheaper for low-volume or simple designs. However, for medical micro molding, their lack of precision and scalability often make them unsuitable compared to injection molding.
In medical terms, molding refers to the process of shaping materials into specific forms, often for devices or components used in healthcare. Medical micro molding is a specialized subset of this process, designed for creating extremely small, intricate parts with high precision. These components are commonly used in devices like surgical instruments, diagnostic equipment, or implants. The molding process typically involves using biocompatible materials such as medical-grade plastics or silicones to ensure safety and compatibility with human tissues. This technique allows manufacturers to produce components with consistent quality, essential for meeting stringent medical industry standards.
Casting and molding are distinct manufacturing techniques. In casting, a liquid material, such as metal or resin, is poured into a mold and solidifies as it cools. Molding, especially in medical micro molding, involves injecting molten plastic or silicone into a mold under high pressure. The key differences lie in the materials used, the precision achievable, and the scale of production. Molding, particularly injection molding, is ideal for high-volume production of intricate medical components, whereas casting is typically used for larger, less complex parts. Molding offers superior precision, making it indispensable in the medical industry.
Molding is a broad term encompassing various techniques, including compression, blow, and injection molding. Injection molding specifically refers to a process where molten material is injected into a mold under pressure. In medical micro molding, injection molding is preferred for its ability to produce highly detailed and precise components, essential for medical applications. Other molding methods, like compression molding, may lack the precision or efficiency needed for small-scale, intricate medical parts. Injection molding’s versatility and scalability make it a cornerstone process in medical manufacturing.
Infusion molding involves injecting resin into a mold containing pre-placed reinforcing fibers. This process is less common in medical micro molding but can be used for larger composite parts, such as orthopedic supports. The infusion process begins with creating a vacuum within the mold to draw in the resin, ensuring it penetrates the fiber layers. Once infused, the material cures to form a strong, lightweight component. While beneficial for certain applications, its use is limited in medical micro molding, where injection molding better suits the need for precision and biocompatibility.
Insert molding integrates a pre-formed part, like a metal pin or threaded insert, into a molded component during the injection molding process. For medical micro molding, this technique is essential for creating complex components that combine multiple materials or functions. The process involves placing the insert into the mold cavity before injecting molten plastic or silicone, which then solidifies around the insert. Applications include surgical tools or medical device housings that require embedded connectors or enhanced durability.
The medical molding process involves the precision manufacturing of components used in healthcare devices. Medical micro molding focuses on producing extremely small parts with intricate geometries, such as catheter tips or microfluidic channels. The process uses biocompatible materials, ensuring safety and regulatory compliance. Injection molding is the primary method due to its precision, repeatability, and scalability. Quality control, including validation and testing, is a critical aspect, ensuring components meet the rigorous demands of medical applications.
The minimum quantity for injection molding depends on factors like mold cost and part complexity. For medical micro molding, minimum orders often range from a few hundred to several thousand pieces. Smaller batches can be produced, but the high upfront cost of mold creation makes it less economical. For prototypes or low-volume needs, alternative methods like 3D printing may be more cost-effective. However, for large-scale medical device production, injection molding remains the most efficient choice.
The principle of micro injection involves using specialized injection molding machines to produce extremely small, precise parts. In medical micro molding, molten material is injected into molds with micro-scale cavities. The process requires tight control of parameters like temperature, pressure, and cooling to achieve the desired precision and repeatability. This method is essential for creating intricate components used in medical devices, such as micro-valves or connectors, where high accuracy is critical for performance and safety.
Micro casting involves pouring molten material, often metal or ceramic, into molds to create small, detailed parts. While not as common as micro molding in medical applications, it is used for producing durable components like implants or surgical tools. The process includes creating a precise mold, heating the material until it melts, and pouring it into the mold. After cooling, the mold is removed, and the part is finished. Micro casting offers good detail but lacks the scalability and material flexibility of micro molding.
Micro molding is a specialized injection molding process for producing small, intricate parts with high precision. The process involves melting a medical-grade material, injecting it into a micro-scale mold, cooling it, and ejecting the finished part. Tight tolerances and rigorous quality control are critical to ensure the parts meet the stringent standards of medical applications. Micro molding is commonly used to create components like catheter tips, microfluidic devices, or surgical instrument parts.
Injection molding produces a wide range of medical products, including syringe components, catheter parts, microfluidic devices, and implantable components. In medical micro molding, tiny yet essential parts like seals, valves, or connectors are common. The versatility of injection molding allows for the use of biocompatible materials, ensuring these products meet safety and performance standards required in the healthcare industry.
People use injection molding for its efficiency, precision, and scalability. In medical micro molding, the process is ideal for producing intricate, high-quality parts in large quantities. It supports a wide range of materials, including biocompatible plastics and silicones, and offers excellent repeatability. These attributes make injection molding the preferred method for manufacturing medical devices and components that require strict adherence to regulatory standards.
Contact our professional team now for a same-day quote and risk-free project evaluation. Benefit from ISO 8 cleanrooms, advanced machines, and 12-hour fast response in medical injection molding.