Medical mold design plays a crucial role in ensuring the quality and safety of medical devices used in healthcare. Precise medical mold design is relatively vital to ensure that medical products are made accurately as per the required specifications. It involves the development of precise molds that comply with strict industry standards to produce components like surgical tools, diagnostic devices, and implantable products. The importance of precision medical mold design cannot be overstated, as even minor inaccuracies could compromise functionality or patient safety. Furthermore, compliance with medical regulations ensures the molds meet requirements for biocompatibility and sterilization. Resources such as Medical Mold Design PDFs and Injection Mold Design Handbooks provide valuable insights into best practices, material selection, and advanced techniques. These tools guide professionals in creating reliable molds for the medical industry’s demanding applications.
Low-Volume to High-Volume Production Capabilities
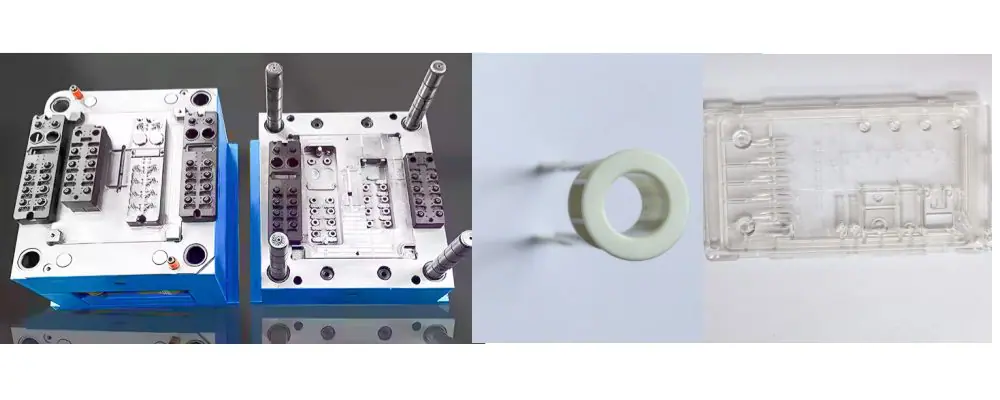
What Is Medical Mold Design?
Medical mold design refers to the specialized process of creating molds used in manufacturing medical-grade components. These molds are critical in producing precise, safe, and effective medical devices and equipment, such as syringes, implants, and diagnostic tools. The field requires expertise in engineering, material science, and compliance with strict medical industry standards. To ensure these standards are met and that the final products are of the highest quality, medical molding services provide the necessary support, translating design concepts into functional molds that better serve the needs of the healthcare industry.
Key Features of Medical Mold Design
- High Precision
Medical mold design prioritizes unparalleled accuracy to ensure that each component functions as intended. Any deviation in dimensions or tolerances could result in defective or unsafe products. Precision also ensures compatibility with other medical device components. - Biocompatibility
The materials used in medical mold design must be biocompatible, meaning they should not cause adverse reactions when in contact with the human body. This is vital for implants, surgical instruments, and other devices that have direct interaction with tissues or fluids. - Sterilization Compatibility
Medical molds are designed to produce components that withstand sterilization processes like autoclaving, gamma radiation, or chemical cleaning. This ensures that medical devices remain safe for repeated use in healthcare environments. - Adherence to Standards
Following guidelines outlined in resources like Plastic Injection Molding Design Guides is crucial. These guides provide best practices for creating molds that meet regulatory standards, ensuring patient safety and effective device performance.
Importance of Medical Mold Design
Medical mold design is fundamental to the healthcare industry, where safety, reliability, and performance are non-negotiable. Without accurate molds, the production of life-saving devices would be compromised. Leveraging resources like Plastic Injection Molding Design Guides equips designers with the knowledge to meet high medical standards. This specialized design process ensures that patients receive the safest and most effective medical solutions possible.
Medical Mold Design Process
The Medical Mold Design Process involves creating molds specifically for manufacturing medical-grade components and devices. These molds must meet stringent requirements for quality, precision, and compliance with medical standards. Below is a detailed step-by-step description of the process:
Requirements Analysis
- Understanding the Product: Collect detailed specifications of the medical device or component to be manufactured, including material, dimensions, tolerances, and surface finishes.
- Regulatory Compliance: Ensure the mold design adheres to relevant medical standards and regulations, such as ISO 13485 or FDA requirements.
- Production Volume: Determine whether the mold is for high-volume production (e.g., multi-cavity molds) or low-volume production (e.g., prototype molds).
Conceptual Design
- Initial Sketches and Layout: Create rough designs of the mold, including the positioning of cavities, gates, runners, and ejection systems.
- Flow Analysis: Use simulation tools to analyze the material flow during injection molding, ensuring uniform fill and minimizing defects like air pockets or weld lines.
Detailed Design
- CAD Modeling: Develop a precise 3D model of the mold using software such as SolidWorks, AutoCAD, or CATIA.
- Cavity and Core Design: Design the cavity and core to meet the exact dimensions and features of the medical component.
- Gate and Runner System: Optimize the gate and runner system for efficient material flow and minimal waste.
- Cooling System: Integrate cooling channels to regulate mold temperature and improve cycle time.
- Ejection Mechanism: Design the ejector pins or plates to ensure the molded parts can be removed without damage.
Validation and Simulation
- Mold Flow Analysis: Conduct advanced mold flow analysis to predict potential issues like shrinkage, warpage, or sink marks.
- Thermal Analysis: Simulate heat transfer to ensure the cooling system maintains consistent temperatures.
- Structural Analysis: Check for mold deformation under pressure during the injection process.
Prototype Manufacturing
- Soft Mold Creation: For prototype or low-volume production, create a soft mold using aluminum or other cost-effective materials.
- Trial Runs: Test the prototype mold with actual material to validate part quality and design accuracy.
Final Mold Fabrication
- Precision Machining: Use CNC machining, EDM (Electrical Discharge Machining), and other techniques to fabricate the mold to the specified design.
- Polishing and Finishing: Apply surface treatments, such as polishing or coating, to achieve the required surface finish and ensure easy demolding.
Testing and Validation
- Injection Molding Trials: Perform test runs to produce sample parts, checking for consistency, precision, and compliance with specifications.
- Dimensional Inspection: Use tools like CMM (Coordinate Measuring Machines) to measure critical dimensions and tolerances.
- Performance Validation: Test the molded parts for mechanical properties, biocompatibility, and any other functional requirements.
Adjustment and Refinement
- Iterative Modifications: Make adjustments to the mold design or machining based on testing results.
- Quality Assurance: Conduct final checks to ensure the mold meets all quality standards and production goals.
Mass Production Readiness
- Documentation: Prepare detailed documentation for mold maintenance, operation guidelines, and quality control.
- Production Setup: Install the mold into the injection molding machine, configure parameters, and begin mass production.
Maintenance and Lifespan Management
- Regular Inspection: Monitor wear and tear, especially in high-precision areas like gates and ejector pins.
- Preventive Maintenance: Schedule cleaning, lubrication, and component replacement to extend mold life.
This systematic approach ensures that the medical mold is reliable, efficient, and capable of producing components that meet the highest medical industry standards.
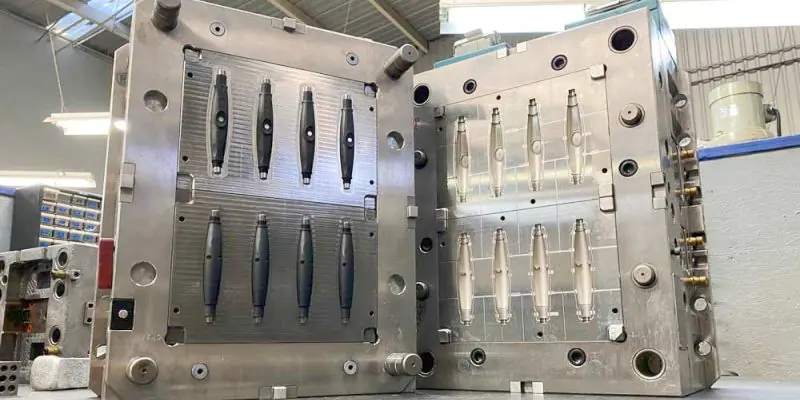
Key Elements of Medical Mold Design
Medical mold design requires careful consideration of various factors to ensure the production of high-quality medical components. These elements play a vital role in determining the efficiency, precision, and reliability of the molds used in manufacturing. Below, we delve into the key aspects that make medical mold design successful.
Medical injection mold design is a subset of medical mold design, focusing specifically on creating molds for the medical injection molding process. This method is widely used for mass-producing medical-grade plastic components. Key considerations include:
Material Selection
- Use of medical-grade thermoplastics, such as polycarbonate (PC), polypropylene (PP), and polyetheretherketone (PEEK).
- Materials must meet FDA or ISO standards for medical use.
Gate Design
- Proper gate placement ensures uniform filling of molds without defects.
- Avoids issues like weld lines or trapped air that compromise product quality.
Surface Finish
- Ensures smooth surfaces for easy sterilization and patient safety.
- Critical for components like syringes or catheter parts that contact human tissues.
Validation and Testing
- Molds must undergo extensive validation to meet medical industry requirements.
- Includes mold flow analysis, dimensional inspections, and performance testing.
Functional Design
Dimensional Accuracy
- Exact dimensions are critical to ensuring that medical components fit and function as intended.
- Tight tolerances prevent issues like misalignment or device failure during use.
Runner Systems
- Effective runner systems facilitate the smooth flow of molten material into the mold cavities.
- Proper design minimizes material wastage and ensures uniform filling.
Ejection Methods
- Ejector pins or other mechanisms must ensure the safe removal of parts without damage.
- Design tools like Mould Design Drawings help visualize and plan ejection systems.
Shape Design
3D Shapes and Precision
- Complex 3D geometries are often required for intricate medical components.
- Accurate shape design is crucial for ensuring functionality and aesthetic appeal.
Surface Finishes
- Surface finishes, such as glossy or textured options, enhance the appearance and usability of medical devices.
- Smooth finishes are essential for devices that require sterilization or contact with tissues.
External Aesthetics
- External appearance must meet medical industry standards for quality and cleanliness.
- High aesthetic value builds trust among end users.
Strength Design
Mold Durability
- Molds must withstand repeated use without warping or deformation.
- The choice of robust materials ensures long-term functionality.
Structural Integrity
- Reinforcements may be added to high-stress areas of the mold to enhance strength.
- Strength design prevents issues such as cracking during high-volume production.
Thermal Design
Cooling System Efficiency
- Efficient cooling systems help maintain consistent temperatures within the mold.
- Optimized thermal regulation reduces cycle times and increases production efficiency.
Medical Device Mold Design
Material Suitability
- Use FDA-approved or ISO-compliant materials for molds that contact sensitive medical-grade plastics.
- Materials must resist wear and tear from high-pressure injection processes.
Sterilization and Safety
- Molds must support components that endure frequent sterilization without degradation.
- Designs should minimize areas prone to bacterial contamination, ensuring safety.
Customizations
- Medical device mold design often requires tailoring molds to specific device needs, such as implants or diagnostic equipment.
- Customization ensures product performance aligns with medical molding requirements.
By integrating these key elements, medical mold design ensures the efficient and accurate production of medical components, meeting the high standards demanded by the healthcare industry.
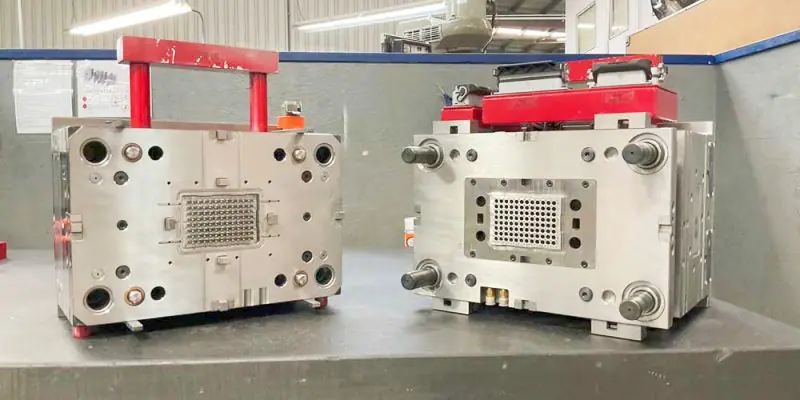
Materials Used in Medical Mold Design
Choosing the right materials is a critical aspect of medical mold design, as the molds must support the production of safe, reliable, and functional medical components. Below is an overview of key materials and their applications in the field.
Thermoplastics and Their Applications
PEEK (Polyetheretherketone)
- Known for its exceptional mechanical strength and chemical resistance.
- Widely used in surgical implants, such as spinal cages and dental components.
- Capable of withstanding high temperatures and sterilization processes.
Polypropylene (PP)
- A lightweight and cost-effective material with excellent chemical resistance.
- Commonly used in the production of sterile syringes, connectors, and lab equipment.
- Ideal for applications requiring durability and reusability.
Polycarbonate (PC)
- Offers high clarity and impact resistance, making it suitable for transparent components.
- Used in medical devices like housings, lenses, and oxygenator parts.
Silicone and Its Role in Medical Applications
Silicone Elastomers
- Known for their flexibility, biocompatibility, and heat resistance.
- Ideal for components like catheters, tubing, and seals.
- Silicone ensures patient safety due to its hypoallergenic properties.
Liquid Silicone Rubber (LSR)
- Commonly used in intricate medical parts due to its precision and molding flexibility.
- Suitable for products requiring high-temperature sterilization, such as gaskets and diaphragms.
Medical Part Mold Tooling Design: Key Considerations
Material Compatibility
- Medical parts mold tooling design must accommodate materials with diverse properties like high melt flow or rigidity. Similarly, liquid silicone molding for medical devices requires careful consideration of material properties to ensure that the silicone’s flexibility and biocompatibility are maintained throughout the molding process.
- Proper tooling ensures compatibility between mold materials and the thermoplastics or silicones used.
Durability Requirements
- Tooling materials must withstand repeated cycles without degradation.
- Hardened steel is often used for long-term molds, while aluminum may be employed for prototyping.
Precision and Complexity
- Molds must achieve tight tolerances to produce highly detailed medical components.
- Designs should account for venting systems to avoid air entrapment during the molding process.
Reference Resources for Material Selection
Resources like Plastic Mould Design Calculations PDF provide essential insights into the properties of materials and their suitability for specific medical applications. These guides help designers calculate mold dimensions, choose materials, and optimize production processes.
By understanding the properties of thermoplastics and silicones, medical mold design ensures the production of components that meet stringent industry standards. Material selection directly impacts the performance, safety, and longevity of medical devices, making it a cornerstone of successful mold design.
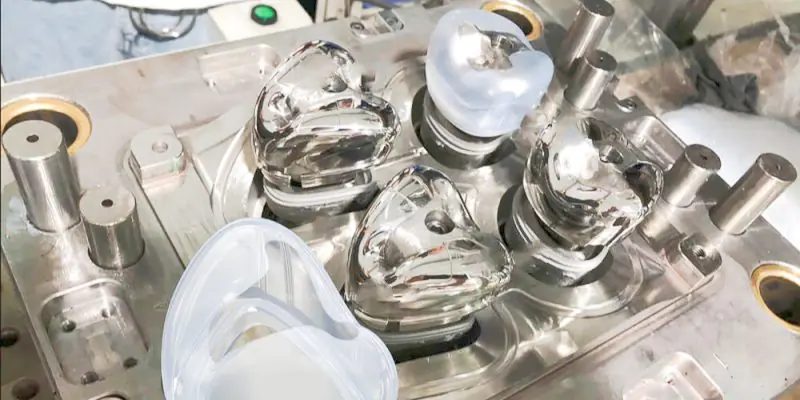
Considerations for Medical Mold Design
Effective medical mold design demands careful planning and precise execution. Designers must address a range of factors to ensure the production of medical components that meet strict standards for safety, functionality, and durability. Below are key considerations for successful medical mold design.
Wall Thickness
Strength and Durability
- Walls must be thick enough to ensure component strength, particularly for devices subjected to mechanical stress.
- Uniform thickness minimizes the risk of warping or structural failure.
Flexibility
- In applications requiring flexibility, such as tubing or diaphragms, thinner walls may be advantageous.
- Consistency in thickness aids in maintaining material flow and reducing defects.
Tolerance and Shrinkage
Material Behavior
- Different materials exhibit unique shrinkage rates during cooling. This must be accounted for in mold design.
- Accurate calculations prevent deviations in the final product’s dimensions.
Tight Tolerances
- Critical for components that need to fit precisely with other parts, such as syringes or connectors.
- Specialized tools, like shrinkage compensation charts, assist designers in achieving high accuracy.
Gate Location
Optimized Flow
- Proper placement of gates ensures uniform material flow, reducing the risk of air entrapment or voids.
- Balanced flow promotes consistent filling across cavities.
Minimized Defects
- Strategic gate positioning avoids weld lines or blemishes on critical functional areas.
- For complex designs, hot runner systems may enhance performance.
Surface Finish
Cost and Functionality
- High-gloss finishes improve aesthetics and are often essential for visible components like housings.
- Textured finishes may enhance grip or reduce glare, depending on the medical application.
Hygiene and Sterilization
- Smooth surfaces are easier to clean and sterilize, a vital requirement for surgical and diagnostic equipment.
Undercut Features
Complex Geometries
- Undercuts may be necessary for specific designs, such as snap-fit mechanisms or intricate features.
- Proper mold planning ensures undercuts do not hinder part ejection.
Cost Efficiency
- Where possible, reducing or eliminating undercuts simplifies the mold design and lowers production costs.
- Alternative approaches, such as collapsible cores, can address complex features without compromising quality.
Medical-Grade Plastic Mold Design and Production: Key Factors
Material Selection
- Use medical-grade plastics that are biocompatible, durable, and capable of withstanding sterilization.
- Examples include polycarbonate for transparency and PEEK for high-performance applications.
Tooling Design
- Tooling for medical-grade plastic mold design and production requires precision to meet strict tolerances.
- Advanced technologies like CNC machining and EDM are commonly used for tooling.
Validation and Testing
- Each mold undergoes rigorous validation to ensure that components meet industry standards.
- Techniques like mold flow analysis and dimensional inspections verify performance and consistency.
By addressing these considerations, medical mold design supports the production of safe, high-quality medical components. Meticulous attention to details like wall thickness, surface finishes, and gate locations ensures optimal functionality and reliability, meeting the demands of the healthcare industry.
Advanced Techniques in Medical Mold Design
In modern medical mold design, advanced techniques are essential for creating high-precision, durable, and functional components that meet the rigorous demands of the healthcare industry. Below are key techniques that elevate the effectiveness and versatility of medical mold design.
Insert Molding
Enhanced Functionality
- Involves embedding secondary components, such as metal inserts, into the mold during the manufacturing process.
- Common in creating reinforced components like threaded connectors or sensors in diagnostic equipment.
Improved Durability
- Combines different materials to achieve a balance of strength, flexibility, and functionality.
- Reduces assembly steps, minimizing production time and cost.
Applications in Medical Devices
- Often used for devices like catheters, surgical instruments, and implanted components where strength and integration are critical.
Overmolding
Multi-Layered Parts
- Allows the creation of components with multiple materials or layers for added durability or ergonomic benefits.
- Commonly used for adding soft-touch surfaces to devices like handles, grips, or syringes.
Seamless Integration
- Ensures a strong bond between different materials, eliminating the need for adhesives or additional assembly steps.
- Results in improved performance and longevity for medical devices.
Medical Applications
- Used in stethoscopes, drug delivery systems, and other devices requiring both rigid and flexible sections.
- Ideal for producing small, intricate parts with exceptional detail and accuracy.
- Supports the manufacturing of hypoallergenic and biocompatible components for sensitive applications.
How Advanced Techniques Transform Medical Mold Design
Customization
- Advanced methods like insert molding and overmolding enable tailored solutions for specific medical needs.
Enhanced Performance
- By combining materials and layers, these techniques ensure better durability, flexibility, and functionality.
Improved Efficiency
- Techniques such as liquid silicone molding streamline production by reducing waste and assembly time, aligning with sustainable practices.
By adopting advanced techniques, medical mold design continues to push boundaries, delivering innovative and reliable solutions for healthcare applications. These approaches not only improve the quality of medical components but also optimize the production process for greater efficiency and cost-effectiveness.
Medical Mold Design Applications
Medical mold design plays a crucial role in the manufacturing of medical devices and components, ensuring precision, biocompatibility, and compliance with stringent regulatory standards. Here are the key applications of medical mold design:
Medical Devices
- Surgical Instruments: Handles, grips, and housings for tools like scalpels, forceps, and scissors.
- Diagnostic Devices: Housings for devices like glucometers, thermometers, and blood pressure monitors.
- Endoscopic Equipment: Parts for minimally invasive surgery tools requiring complex geometries and high precision.
Implantable Devices
- Orthopedic Implants: Molded components for knee, hip, and spine implants made from biocompatible materials.
- Dental Implants: Precision parts for dental crowns, bridges, and orthodontic devices.
- Pacemakers and Stents: Molded casings and components for cardiac devices and vascular implants.
Consumable Medical Products
- Syringes and Needles: Single-use syringes, needle hubs, and other precision-molded parts.
- IV Components: Connectors, drip chambers, and flow regulators for intravenous therapy systems.
- Catheters: Soft, flexible tubing and connectors for various catheter applications.
Medical Packaging
- Sterile Containers: Molded cases for syringes, surgical tools, and medications.
- Blister Packs: Custom molds for packaging pills, capsules, and medical devices.
- Protective Casings: Rigid or flexible packaging for fragile medical components.
Prosthetics and Orthotics
- Limb Prostheses: Custom-designed molds for lightweight, durable artificial limbs.
- Orthotic Braces: Molded components for support devices like knee braces, foot orthoses, and spinal supports.
Wearable Medical Devices
- Fitness and Health Trackers: Casings and components for wearable monitors like heart rate trackers and glucose monitors.
- Hearing Aids: Small, precisely molded housings for hearing aids.
- Insulin Pumps: Molded enclosures and connectors for wearable insulin delivery systems.
Diagnostic and Laboratory Equipment
- Microfluidic Devices: Molds for components in lab-on-a-chip devices used for diagnostics and research.
- Test Tubes and Petri Dishes: Mass production of consumables for labs and medical testing.
- Centrifuge Tubes: Molded parts for precision laboratory use.
Sterilization-Resistant Components
- Autoclave-Safe Parts: Molded components designed to withstand high temperatures and pressures during sterilization.
- Chemical-Resistant Parts: Products molded from materials that resist degradation from sterilizing chemicals.
Rehabilitation and Assistive Devices
- Wheelchair Components: Molded parts for lightweight, ergonomic designs.
- Assistive Technology: Casings and parts for hearing aids, vision aids, and mobility devices.
Customized and Patient-Specific Products
- Dental Aligners: Precision molds for creating patient-specific aligners.
- Custom-Fit Masks: Molds for personalized CPAP masks and oxygen masks.
- Personalized Implants: Molds designed based on individual patient anatomy, often leveraging 3D imaging data.
Pharmaceutical Applications
- Dosage Delivery Devices: Components for inhalers, drug delivery pumps, and pill dispensers.
- Sterile Vials and Ampoules: Molds for pharmaceutical containers used for liquid and powder medications.
Emergency and Critical Care Equipment
- Defibrillator Parts: Casings and connectors for defibrillators.
- Oxygen Masks and Tubing: Molded parts for respiratory support equipment.
- Ventilator Components: Precision parts for life-saving respiratory devices.
Research and Development
- Prototyping: Creating prototype molds for testing new medical device designs.
- Rapid Production: Small-scale production molds for research purposes or clinical trials.
The versatility and precision offered by medical mold design make it indispensable in the healthcare industry, supporting a wide range of applications critical to patient care, diagnostics, and research.
The Art of Medical Mold Design
The Art of Medical Mold Design represents a delicate balance between engineering precision, creativity, and a profound understanding of the healthcare industry’s unique demands. It’s not merely a technical task but an intricate craft that involves innovating for reliability, efficiency, and compliance. Here’s a deep dive into the artistic and technical aspects of medical mold design:
Crafting Precision for Life-Saving Applications
- Tolerance Mastery: Achieving micro-level precision in mold design is vital for creating medical components that fit perfectly into life-critical systems.
- Material Expertise: Selecting mold materials that harmonize with the properties of medical-grade plastics, silicones, or metals ensures durability and biocompatibility.
- Dimensional Accuracy: Creating molds that produce consistent parts, especially for devices like syringes or implants, where even slight variations could have significant consequences.
Harmonizing Function and Aesthetics
- Ergonomic Design: For devices like surgical tools or wearable medical devices, molds must produce components that are not only functional but also comfortable and easy to use.
- Surface Finishes: Achieving perfect polish or texture is critical, as smooth surfaces reduce bacteria accumulation and improve cleaning efficiency in medical environments.
- Design for Patient Comfort: Molds for prosthetics or orthodontic devices must accommodate customization for individual needs, blending technical precision with a patient-centric approach.
Innovative Problem-Solving
- Miniaturization: As medical devices become smaller, designing molds for intricate, micro-sized components demands advanced technology and expertise.
- Complex Geometries: Creating molds for products like stents or microfluidic devices requires mastery of complex shapes and innovative gating systems.
- Multi-Material Integration: Molds are often designed to produce components combining materials like rigid plastics and soft elastomers in a single part.
Aesthetic and Emotional Impact
- Enhancing Trust: The look and feel of medical devices impact patient confidence, and well-designed molds contribute to the visual and tactile quality of the final product.
- Empathy in Design: Mold design reflects care and precision, ensuring devices are safe, effective, and aligned with patient well-being.
The art of medical mold design is a synergy of technical expertise, creative innovation, and unwavering commitment to quality and safety. It’s not just about making molds; it’s about crafting tools that empower medical advancements and improve lives globally.
FAQs about Medical Mold Design
Medical molding is a specialized manufacturing process used to create high-precision plastic components for the healthcare industry. It involves the use of injection molding techniques to produce parts and devices that meet stringent medical standards and specifications. Medical molding is commonly used to manufacture components such as syringes, IV tubes, catheters, and other medical devices that require a high degree of accuracy and consistency. The materials used in medical molding are typically biocompatible and sterilizable, ensuring that they are safe for use in medical applications. This process is critical in ensuring the reliability and effectiveness of medical devices, thereby playing a crucial role in patient care and treatment.
Mold design refers to the process of creating a mold—a cavity or hollow form used to shape materials into specific forms or products through techniques like injection molding, blow molding, or compression molding. In the medical field, mold design is critical for manufacturing precise and sterile components such as syringes, surgical instruments, and medical device housings. The design must consider factors like material compatibility (e.g., biocompatible plastics), part geometry, dimensional tolerances, and cleanroom manufacturing requirements. It also integrates features for efficiency, such as cooling systems, ejection mechanisms, and high durability for repeated production cycles. Since medical components often require exacting standards, mold designs prioritize quality, consistency, and adherence to regulatory requirements (e.g., ISO 13485 or FDA compliance). Proper mold design ensures efficient production of high-quality medical parts, minimizing waste while meeting stringent industry demands.
The cost of a custom mold for medical applications depends on several factors, including the complexity of the design, material requirements, and the intended production volume. On average, custom molds for medical devices range from $10,000 to over $100,000.
Key cost drivers include:
Part Complexity: Intricate designs with tight tolerances and fine details, such as those for catheters or surgical tools, increase costs.
Material: High-performance steel or aluminum is typically used, with hardened steel being more expensive but longer-lasting.
Regulatory Standards: Molds designed for medical devices must meet strict quality and safety standards, adding to engineering and validation costs.
Cavities and Production Volume: Multi-cavity molds for high-volume production are more expensive upfront but reduce per-part cost.
Lead Time: Faster turnaround demands may involve additional costs.
While the initial investment is significant, custom molds are essential for producing consistent, high-quality medical components at scale.
The medical molding process is a specialized form of manufacturing that produces high-precision and sterile components used in medical applications. It primarily involves injection molding, where biocompatible thermoplastics or silicone materials are melted and injected into a pre-designed mold to create parts like syringes, catheters, IV connectors, or surgical instrument components.
Key stages include:
Material Selection: Biocompatible materials such as polycarbonate, polypropylene, or medical-grade silicone are chosen based on the application.
Mold Preparation: Custom molds, often multi-cavity and designed for cleanroom environments, are installed in the molding machine.
Injection: The material is heated, melted, and injected into the mold cavity under high pressure.
Cooling: The molten material solidifies into the desired shape within the mold.
Ejection and Quality Control: The part is removed and undergoes stringent inspections for dimensional accuracy, surface finish, and sterility.
Medical molding often requires cleanroom facilities (Class 7 or Class 8), strict adherence to regulatory standards (e.g., ISO 13485 or FDA requirements), and validation processes to ensure product safety and consistency.
Injection molding theory is based on the principle of converting raw material into a finished product through the application of heat, pressure, and a precisely designed mold. The theory encompasses several physical and mechanical concepts:
Melting and Flow: The material, typically thermoplastic or thermosetting polymer, is melted in the injection unit to a specific viscosity. Proper control ensures uniform flow into the mold cavity.
Injection Pressure and Speed: Material is injected at high pressure to ensure it completely fills the mold cavity, including fine details. The speed of injection is crucial to avoid defects like air traps or incomplete filling.
Cooling and Solidification: The injected material solidifies as it cools in the mold, retaining the shape of the cavity. Effective cooling is essential to maintain dimensional accuracy and reduce cycle times.
Shrinkage Management: Materials contract upon cooling; the mold design compensates for shrinkage to maintain precise dimensions.
Ejection: Once solidified, the part is ejected using mechanisms like ejector pins.
The theory emphasizes optimizing machine settings, material behavior, and mold design to achieve efficiency, accuracy, and quality, especially in applications like medical manufacturing where precision is critical.
Contact our professional team now for a same-day quote and risk-free project evaluation. Benefit from ISO 8 cleanrooms, advanced machines, and 12-hour fast response in medical injection molding.