Medical plastics play a vital role in revolutionizing modern healthcare by offering versatile and cost-effective solutions. Variety of plastic medical devices and components can be made with injection molding by high quality medical molded plastics solutions. These materials are widely used in both single-use and multi-use applications, ensuring hygiene, safety, and improved patient care. Medical plastics have steadily replaced traditional materials like glass and metals due to their durability, flexibility, and lightweight properties.
Low-Volume to High-Volume Production Capabilities
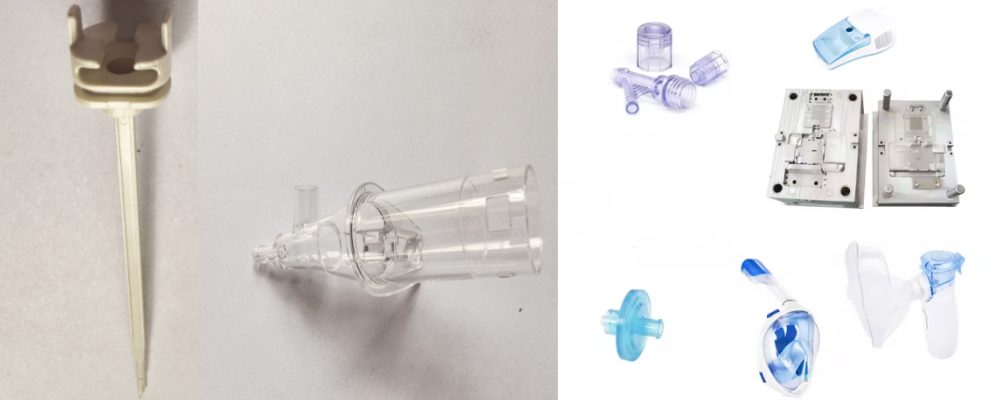
Attribute | Description |
---|---|
Product Name | Medical Molded Plastic Parts |
Brand Name | LY Medical Injection Mold |
Product Type | Injection Molded Plastic Parts |
Main Applications | Medical Devices, Medical Plastic Parts |
Material Options | ABS, PVC, PP, PC, PA66, PEEK, TPE, Nylon, Delrin, PMMA, PET, PVC, PCTG, and other plastics |
Size/Specifications | Customized Size |
Surface Treatment | Polishing, Anodizing, Electroplating, Powder Coating, Passivating, etc. |
Precision/Tolerance | 0.001mm - 0.05mm (specific tolerance based on design requirements) |
Processing Type | Injection Molding, CNC Machining, Milling, Turning, Wire EDM, Electrical Discharge Machining (EDM), Rapid Prototyping, etc. |
Design Software | PROE, UG, CAD, CAM, STEP, IGES, etc. |
Customization Availability | Yes (OEM/ODM Available, Customized Designs) |
Minimum Order Quantity (MOQ) | 1 piece |
Samples | Samples Available |
Lead Time | 2-5 days for sampling, 15-30 days for mass production |
Payment Terms | L/C, T/T, D/P, Western Union |
Packaging | Inner Packaging: Opp Bags; Outer Packaging: Carton |
Certifications | ISO 9001:2008 |
Quality Assurance | 100% based on production drawings or samples |
Manufacturing Process | Molding, CNC Machining, Injection Molding, etc. |
Adjustability/Adaptability | Custom Design, Fully Customizable |
What Are Medical Molded Plastics Solutions
Medical Molded Plastics Solutions refer to specialized plastic components and products designed and manufactured to meet the rigorous demands of the medical and healthcare industries. These solutions involve the use of advanced molding techniques to produce high-quality plastic parts with precision, durability, and reliability, tailored for applications where safety, biocompatibility, and performance are critical.
Key Characteristics of Medical Molded Plastics Solutions
Medical molded plastics solutions are created with a strong emphasis on meeting the stringent standards of the healthcare sector. They include the following defining characteristics:
- Tailored Design for Medical Applications: These solutions are specifically engineered to suit medical environments, from complex surgical instruments to single-use diagnostic tools. They are designed with precision to ensure they meet the functional, mechanical, and aesthetic requirements unique to medical devices.
- Advanced Manufacturing Techniques: Cutting-edge molding processes, such as injection molding, blow molding, or micro-molding, are employed to create intricate and detailed plastic parts. These techniques ensure high consistency and repeatability, which are essential in medical applications.
- Focus on Biocompatibility and Safety: Materials used in these solutions are carefully selected to be biocompatible, non-toxic, and safe for use in direct contact with human tissues, fluids, or drugs. They must also comply with strict medical regulations, such as ISO 10993 or FDA standards.
- Durability and Sterilizability: Medical molded plastics are designed to withstand harsh sterilization processes, such as autoclaving, gamma radiation, or ethylene oxide treatment, without degrading or compromising performance. This ensures they remain safe and effective during use.
- Compliance with Regulatory Standards: These solutions must adhere to globally recognized quality and safety standards, such as ISO 13485 for medical device quality management and other region-specific certifications required by regulatory bodies.
These solutions play a crucial role in advancing healthcare by enabling the production of innovative, cost-effective, and high-performance medical products. Their development is driven by ongoing advancements in material science and manufacturing technologies, ensuring they meet the evolving demands of the medical field.
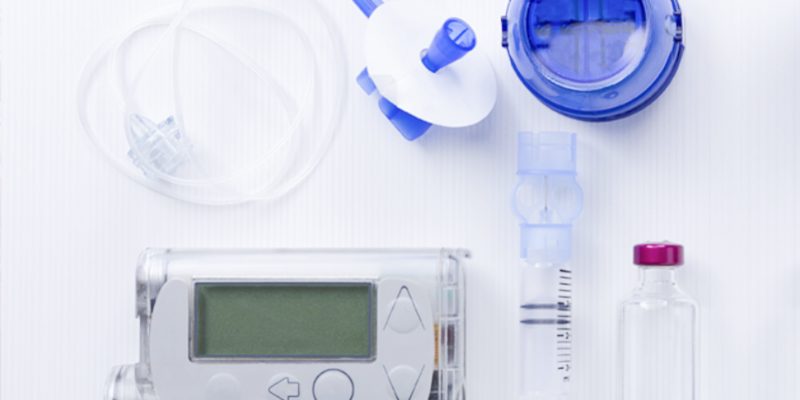
Benefits of Medical Molded Plastics Solutions
Medical molded plastics have revolutionized the healthcare industry, offering a range of benefits that enhance patient care, improve operational efficiency, and drive innovation. Here’s an in-depth look at their advantages:
Biocompatibility and Safety
- Non-Toxic Properties: Medical-grade plastics are designed to be biocompatible, ensuring they do not react negatively with human tissues or bodily fluids.
- Sterilizability: These plastics can withstand various sterilization methods, including autoclaving, gamma radiation, and chemical disinfectants, ensuring a high level of hygiene.
Versatility in Design
- Complex Geometries: Injection molding allows for the creation of intricate designs that are difficult to achieve with traditional materials like metal.
- Customization: Plastics can be tailored to specific medical applications, offering unique shapes, sizes, and functionalities to meet precise requirements.
Lightweight yet Durable
- Ease of Handling: Plastics are lighter than metal or glass, making devices and components easier to transport and use.
- High Strength-to-Weight Ratio: Modern plastics offer exceptional durability, ensuring they can withstand mechanical stress without adding excessive weight.
Cost-Effectiveness
- Mass Production: Injection molding is highly efficient for producing large volumes of medical components, significantly reducing per-unit costs.
- Material Efficiency: Minimal waste is generated during the manufacturing process, making it both economical and environmentally friendly.
Wide Range of Applications
- Disposable Items: Plastics are commonly used in single-use items such as syringes, IV tubes, and surgical gloves, reducing the risk of cross-contamination.
- Reusable Devices: Durable plastics are also employed in instruments like inhalers, insulin pens, and diagnostic tools.
Improved Patient Comfort
- Soft Touch and Flexibility: Plastics can be designed with flexible or soft-touch properties, enhancing patient comfort during use.
- Hypoallergenic Options: Many medical plastics are free from allergens, making them suitable for sensitive patients.
Resistance to Chemicals and Corrosion
- Medical plastics are highly resistant to chemicals, moisture, and corrosion, ensuring longevity and reliability even in harsh environments.
Environmental Benefits
- Recyclability: Many medical plastics are recyclable, aligning with sustainability goals in healthcare.
- Reduced Material Usage: Advanced manufacturing techniques allow for thinner and lighter components, decreasing material consumption without compromising quality.
Enhanced Innovation Potential
- Integration with Technology: Medical plastics enable seamless integration with electronic components for smart medical devices, such as wearable health monitors.
- Rapid Prototyping: Plastics facilitate quick prototyping, accelerating the development of new medical technologies.
Regulatory Compliance
- Medical plastics are manufactured to meet stringent regulatory standards, ensuring they are safe and effective for healthcare use.
Medical molded plastics solutions offer unmatched flexibility, safety, and efficiency, driving advancements across the healthcare sector. Their combination of adaptability, cost-effectiveness, and innovation potential makes them indispensable in modern medical applications.
Types of Medical Molded Plastics Solutions
Medical molded plastics solutions rely on advanced materials tailored to meet the rigorous demands of the healthcare industry. The following are six key types of medical plastics and their unique properties:
Common Thermoplastics
Polycarbonate (PC):
- High impact resistance and excellent heat tolerance.
- Widely used in medical device casings, lenses, and protective gear like face shields.
Polypropylene (PP):
- Steam sterilizable and chemically resistant.
- Ideal for lab containers, syringes, orthotics, and prosthetics.
Polyethylene (PE):
- Biologically inert with high impact resistance.
- Commonly utilized in implants, medical tubing, and joint replacement components.
Acrylonitrile Butadiene Styrene (ABS):
- Known for toughness and a smooth, clean finish.
- Perfect for non-invasive medical tools and diagnostic equipment.
Polyvinyl Chloride (PVC):
- Available in flexible and rigid forms.
- Used in catheters, IV bags, and oxygen masks due to its versatility and affordability.
Polymethyl Methacrylate (PMMA):
- Offers glass-like transparency and scratch resistance.
- Ideal for intraocular lenses and dental implants.
Polyether Ether Ketone (PEEK):
- Resistant to high temperatures and autoclave sterilization.
- Excellent choice for surgical and dental implants.
Thermoplastic Polyurethane (TPU):
- Highly elastic with abrasion resistance.
- Used for flexible components like tubing and wound dressings.
Material Selection Criteria
Biocompatibility: Ensuring materials are non-toxic and safe for patient contact.
Regulatory Compliance: Meeting stringent healthcare standards and certifications.
Durability: Withstanding mechanical stress and wear in critical applications.
Sterilization Methods: Compatibility with methods like steam, radiation, or chemical sterilization.
By leveraging the properties of these specialized materials, medical molded plastics solutions enhance innovation, safety, and efficiency in modern healthcare systems.
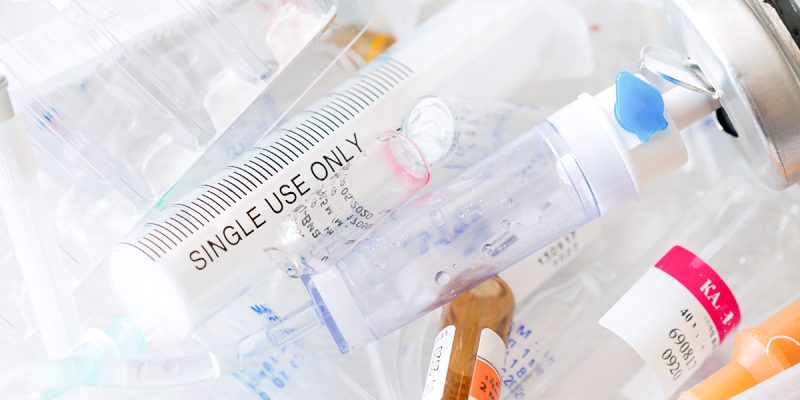
Manufacturing Techniques for Medical Molded Plastics Solutions
Producing medical molded plastics solutions requires advanced manufacturing techniques tailored to meet strict healthcare standards. The following methods highlight key processes and their benefits:
Injection Molding
Process Overview
Liquefied plastic is injected into pre-designed medical molds, forming precise and repeatable shapes.
Ensures consistent quality for even the most intricate medical precision components.
Applications
- Widely used for creating test tubes, surgical tools, syringe bodies, and pacemaker components.
- Essential for mass-producing medical consumables and device casings with exact dimensions.
Advantages
Economies of Scale: Cost-effective for large production runs.
High Precision: Produces complex designs with tight tolerances.
Reduced Waste: Optimized material usage with minimal production scrap.
Secondary Operations
Advanced Techniques
- Sonic Welding: Utilizes high-frequency sound waves to join plastic parts without adhesives.
- Hot Plate Welding: Applies heat to fuse components, ideal for durable medical devices.
- Multi-Shot Molding: Combines different plastics in a single part for added functionality.
Assembly and Over-Molding
- Over-molding integrates multiple materials, enhancing ergonomics and grip for devices like catheters and surgical handles.
- Assembly operations streamline the production of complex, multi-component medical devices.
Clean Room Manufacturing
ISO-Class Environments
- Operates under ISO Class 7 or Class 8 standards to ensure products are free from contaminants.
- Designed for manufacturing contamination-sensitive products, such as implantable devices and IV tubing.
Specialized Benefits
- Protects medical molded plastics solutions from particulate and microbial contamination.
- Essential for maintaining sterility in medical devices used in critical care and surgeries.
The combination of these techniques ensures that medical molded plastics solutions deliver the quality, precision, and safety required in modern healthcare.
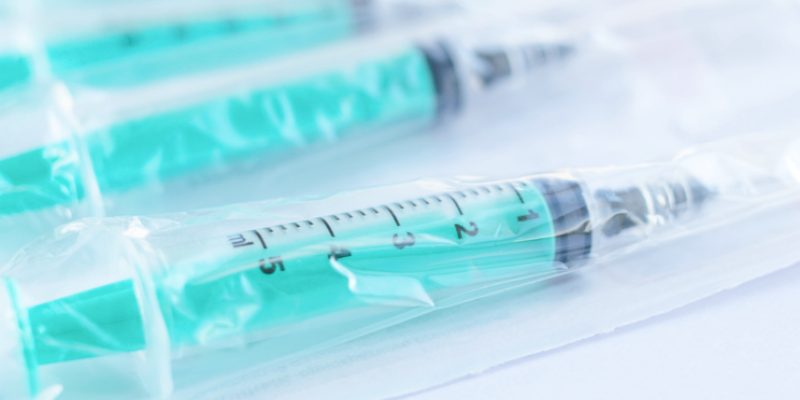
Medical Applications of Medical Molded Plastics Solutions
Medical molded plastics solutions are essential in healthcare, offering versatile, durable, and cost-effective materials for various critical applications. They are key in medical injection molding applications, producing high-precision components like syringes, surgical instruments, and diagnostic tools.Below are the key areas where these plastics are used:
Single-Use Devices
Syringes: Lightweight, sterilizable, and safe for single-use, ensuring patient hygiene.
Catheters: Flexible, biocompatible tubing designed for minimally invasive medical procedures.
Lancets: Precision instruments for blood sampling with sterile and ergonomic designs.
Gloves: Latex-free, hypoallergenic, and disposable to maintain strict hygiene standards.
IV Bags: Made from medical-grade plastics, ensuring durability and compatibility with various fluids.
Advantages
- Disposable nature reduces contamination risks.
- Easy to produce in large quantities using medical molded plastics solutions.
Surgical and Diagnostic Equipment
Surgical Instruments
- Precision-molded plastics ensure durability and sterility in instruments like forceps and retractors.
Biopsy Needles
- Lightweight and strong components enhance diagnostic accuracy.
Diagnostic Test Strips
- Designed for high precision and compatibility with analytical devices for rapid results.
Benefits
- Medical molded plastics solutions provide high precision and reduce overall production costs for these critical devices.
Implants and Prosthetics
Implantable Devices
- Heart Valves: Long-lasting, biocompatible polyethylene components improve patient outcomes.
- Joint Replacements: PEEK-based materials offer excellent strength and flexibility for orthopedic implants.
Custom Prosthetics
- Medical molded plastics solutions allow for personalized designs tailored to individual needs.
Advantages
- Lightweight and durable materials improve patient comfort and mobility.
- Biocompatibility ensures safety for long-term use.
Fluid Management and Tubing
PVC Tubing
- Commonly used in respiratory systems, urology devices, and IV fluid management systems.
Applications in Healthcare
- Supports critical care by safely transporting fluids and gases in medical environments.
Advantages
- Flexible, sterilizable, and chemically resistant materials meet rigorous medical standards.
- Medical molded plastics solutions enhance efficiency in fluid management processes.
These applications demonstrate how medical molded plastics solutions provide innovative, reliable, and cost-effective options for improving healthcare outcomes globally.
Quality Standards and Certifications for Medical Molded Plastics Solutions
Ensuring the safety, reliability, and performance of medical molded plastics solutions requires strict adherence to quality standards and certifications. Below are the critical aspects of these requirements:
Regulatory Compliance
FDA Guidelines
- Products must meet U.S. Food and Drug Administration (FDA) requirements for biocompatibility and material safety.
- This includes rigorous testing for potential toxicity, durability, and sterilization compatibility.
ISO 13485 Standards
- Specifies the quality management systems for medical device plastic manufacturing.
- Focuses on risk management, consistent product quality, and regulatory compliance.
IATF 16949 Certification
- Relevant for manufacturers serving both medical and automotive sectors.
- Emphasizes defect prevention, waste reduction, and continuous improvement for high precision medical molded plastics solutions.
Quality Assurance Processes
Process Validation
- Ensures that production methods consistently yield products meeting predefined specifications.
- Includes rigorous testing during development and production phases.
Traceability
- Full traceability systems are implemented to track materials and processes from sourcing to final delivery.
- Essential for ensuring accountability and addressing potential recalls efficiently.
Statistical Controls
- Continuous monitoring of production metrics to maintain consistent quality across batches.
- Key for minimizing variability in medical molded plastics solutions.
Shot-by-Shot Inspection:
- Critical components undergo individual inspections to detect defects during medical injection molding.
- Advanced imaging and metrology tools ensure precision and compliance with tolerances.
By adhering to these quality standards and certifications, manufacturers of medical molded plastics solutions provide reliable, safe, and compliant products to meet the healthcare industry’s demanding needs.
What Plastic Products Are Manufactured During the Medical Molded Plastics Solutions Process?
During the medical molded plastics solutions process, a wide variety of plastic products are manufactured to meet the specific needs of the healthcare and medical industries. These products are tailored for applications ranging from diagnostics to surgical procedures and patient care. Below is a detailed list of commonly manufactured plastic products:
Medical Device Components
- Inhaler Casings
- Insulin Pens
- Dialysis Machine Components
- Oxygen Masks
- IV Drip Chambers
- Infusion Pumps
Surgical Tools and Accessories
- Scalpel Handles
- Surgical Guides
- Trocars and Cannulas
- Instrument Trays
Patient Care Products
- Bed Pans
- Urine Bags
- Ostomy Bags
- Medical-grade Pill Bottles
- Patient Monitoring Device Casings
Packaging Solutions
- Sterile Packaging for Instruments
- Blister Packs
- Tamper-proof Containers
- Sealable Pouches
Electronic Device Housings
- Covers for Heart Rate Monitors
- Casings for Portable Ultrasound Devices
- Enclosures for Wearable Health Devices
- Parts for Telemedicine Equipment
Prosthetics and Orthotics
- Artificial Limb Components
- Custom Molded Orthotic Inserts
- Plastic Casts for Fracture Support
Laboratory Equipment
- Petri Dishes
- Test Tubes
- Centrifuge Tubes
- Well Plates
Infection Control Products
- Face Shields
- Protective Goggles
- Isolation Gown Components
- Barrier Films
Smart Medical Devices
- Wearable Device Parts
- Sensor Housings
- Components for Smart Pills
Material-Specific Products
- Thermoplastic Products: Durable, lightweight components for general use.
- Silicone-based Products: Flexible, biocompatible items like catheters and seals.
- Bioabsorbable Plastics: Temporary implants that dissolve in the body.
These products are crafted using advanced techniques like injection molding, blow molding, and extrusion, ensuring precision, consistency, and compliance with stringent medical standards. The variety of products demonstrates the versatility and critical role of medical molded plastics in modern healthcare.
Future Trends and Innovations in Medical Molded Plastics Solutions
Medical molded plastics solutions are evolving to meet the demands of modern healthcare while addressing environmental concerns and technological advancements. Below are the key trends shaping the future:
Sustainability
Biodegradable Polymers
- Manufacturers are investing in the development of biodegradable medical plastics to reduce long-term environmental impact.
- These materials decompose safely without compromising sterility or biocompatibility.
Recyclable Plastics
- Focus on producing recyclable plastics that retain durability and functionality.
- Recycling initiatives aim to reduce medical waste in hospitals and clinics.
Green Manufacturing Processes
- Adopting energy-efficient production methods, such as low-energy molding technologies, to enhance sustainability.
- Minimizing emissions while maintaining the high standards required for medical molded plastics solutions.
Advanced Applications
3D Printing
- Revolutionizing the production of customized medical devices, including prosthetics, implants, and surgical guides.
- Enables rapid prototyping and tailored designs, reducing production costs and lead times.
Smart Materials
- Integration of responsive plastics that change properties based on environmental stimuli.
- Examples include drug delivery systems that release medication at controlled rates or diagnostic plastics embedded with sensors for real-time health monitoring.
Nanotechnology Integration
- Incorporating nanomaterials into medical molded plastics solutions for enhanced antimicrobial properties and improved mechanical strength.
- Enables the creation of ultra-light, highly durable devices for advanced medical applications.
Digital Transformation in Manufacturing
AI and Automation
- Smart factories use AI-driven quality control and robotic systems to enhance precision in medical device automation.
- Predictive maintenance tools minimize downtime, ensuring consistent output of medical molded plastics solutions.
Data-Driven Customization
- Leveraging big data to refine designs and optimize production based on patient-specific needs.
- Enhances the development of personalized medical devices.
As sustainability and technology converge, medical molded plastics solutions are poised to lead innovation in healthcare, offering safer, smarter, and more environmentally conscious solutions.
FAQs about Medical Molded Plastics Solutions
The best plastic for medical devices depends on a variety of factors including biocompatibility, durability, and resistance to various chemicals. Commonly used plastics in medical devices include Polycarbonate (PC) for its strength and clarity, Polyethylene (PE) for its flexibility, and Polypropylene (PP) for its chemical resistance. Each of these materials has been tested and proven to perform well in medical settings, making them ideal candidates for a range of medical devices.
BMP Medical is headquartered in Massachusetts, USA. This location provides the company with strategic advantages in terms of logistics, supply chain management, and access to skilled labor. The headquarters is equipped with state-of-the-art facilities that enable BMP Medical to produce high-quality medical devices and components. Their centralized location also ensures efficient distribution to their global customer base.
Alternatives to plastic molding include metal injection molding, ceramic molding, and 3D printing. Metal injection molding is particularly useful for creating strong, durable components that must withstand high levels of stress and wear. Ceramic molding is ideal for heat-resistant and bio-compatible applications. Meanwhile, 3D printing offers the flexibility to produce complex, customized shapes quickly and cost-effectively. Each of these alternatives has specific advantages that can make them suitable for different applications depending on the requirements.
Polyether ether ketone (PEEK) is commonly used in medical implants due to its excellent mechanical properties and biocompatibility. PEEK is known for its high strength, stability, and resistance to degradation inside the human body. Additionally, medical-grade silicone rubber and polyethylene are also used in various implantable devices. These materials are carefully chosen based on their ability to withstand the body’s environment and ensure long-term functionality and safety.
Plastics utilized in medical devices must meet stringent criteria to ensure safety and efficacy:
Biocompatibility: Materials should not induce adverse reactions when in contact with body tissues or fluids, ensuring they are non-toxic, non-carcinogenic, and non-immunogenic.
Sterilization Capability: Plastics must withstand various sterilization methods—such as autoclaving, gamma irradiation, or ethylene oxide treatment—without degrading or losing functionality.
Chemical Resistance: Materials should resist chemicals they may encounter during use or cleaning processes, preventing degradation or harmful interactions.
Mechanical Properties: Plastics must possess appropriate strength, flexibility, and durability to function effectively in their intended medical applications.
Ensuring these requirements are met is crucial for the safe and effective performance of medical devices.
In healthcare, “BMP” commonly stands for Basic Metabolic Panel, a blood test that measures various substances to assess metabolism and organ function. However, in the context of medical manufacturing, “BMP” refers to BMP Medical, a company specializing in plastic injection molding for medical devices.
If referring to Bone Morphogenetic Proteins (BMPs), they are naturally produced in the human body, primarily by osteoblasts, and play a crucial role in bone formation and healing. In the context of BMP Medical, the company operates a state-of-the-art facility in Sterling, Massachusetts, where they produce plastic medical devices and components.
The optimal plastic for injection molding in medical applications depends on specific requirements:
Polyether Ether Ketone (PEEK): Known for its high mechanical strength, chemical resistance, and biocompatibility, making it suitable for implants and other critical medical components.
Polycarbonate (PC): Offers clarity and impact resistance, commonly used in devices like blood oxygenators and IV connectors.
Polypropylene (PP): Valued for its chemical resistance and sterilization capability, often used in syringes and medical containers.
Material selection should consider factors such as biocompatibility, sterilization methods, mechanical demands, and the device’s intended use.
The cost of plastic injection molding in the medical field varies based on several factors:
Tooling Costs: Designing and manufacturing precision molds can be expensive, especially for complex medical components.
Production Volume: High-volume production can reduce per-unit costs, making molding more cost-effective.
Material Selection: High-performance medical-grade plastics like PEEK are more costly than standard materials.
Regulatory Compliance: Adhering to stringent medical standards can add to costs due to necessary testing and validation processes.
While initial investments can be substantial, plastic injection molding offers cost benefits in large-scale production, providing consistent quality and precision essential for medical devices.
Contact our professional team now for a same-day quote and risk-free project evaluation. Benefit from ISO 8 cleanrooms, advanced machines, and 12-hour fast response in medical injection molding.