Medical molding engineering is a specialized field within medical device engineering that focuses on the design, development, and optimization of molds and dies used to manufacture medical devices. A medical molding engineer is responsible for creating precision molds that are crucial in producing high-quality medical components. These components can range from small, intricate parts like syringes to complex devices such as surgical implants and diagnostic tools. The role of a medical molding engineer is vital in ensuring that these components meet stringent industry standards for safety and functionality.
Medical molding engineering plays a critical role in the healthcare industry by enabling the precise, scalable production of medical devices. By ensuring high accuracy in mold design and manufacturing, a medical molding engineer contributes to the production of safe, reliable medical equipment. This field also supports advancements in healthcare technology, fostering innovation that improves patient care and treatment outcomes.
Low-Volume to High-Volume Production Capabilities
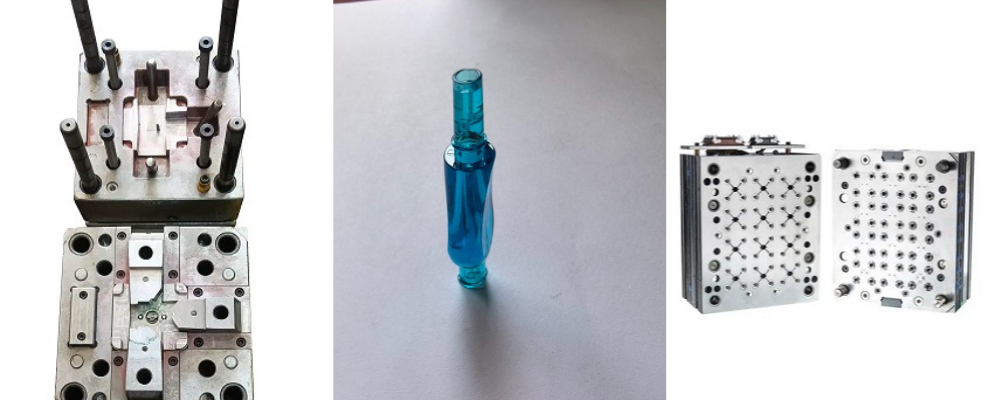
Attributes | Details |
---|---|
Place of Origin | Dongguan, Guangdong, China |
Brand Name | LY Medical Injection Mold |
Product Name | Medical Molding |
Molding Mode | Plastic Injection |
Product Material | Plastic |
Color | Customized |
Size | Customized |
Length | Customized |
Style | Customized |
Service | OEM ODM |
Processing Service | Molding, Cutting |
Features | High Precision |
Logo | Customized Logo Acceptable |
Certification | ISO9001/ISO13485 |
Supplier | Manufacturer |
Design Software | 2D/3D/CAD/DWG//STEP/PDF/UG |
Surface Treatment | Matte, Texture, Polishing, UV Coating, Rubberization, etc. |
Quality Control | Process Inspection and Final Inspection before Shipment |
Packing Details | Outer Packaging Carton Inner Packaging According to Customer Requirements |
Sales Unit | Single Item |
Port | According to Your Requirements |
What is a Medical Molding Engineer?
A medical molding engineer is a specialized professional within the medical device industry, focusing on the design, development, and production of molds and dies used to create medical-grade components. These engineers play a critical role in manufacturing precise, durable, and biocompatible parts that meet the strict standards of healthcare applications. Their expertise spans materials science, process optimization, and regulatory compliance, ensuring that each product—from syringes and catheters to surgical implants and diagnostic tools—meets safety and quality requirements. By combining engineering principles with advanced manufacturing technologies like injection molding, a medical molding engineer helps bring life-saving devices to market efficiently and effectively.
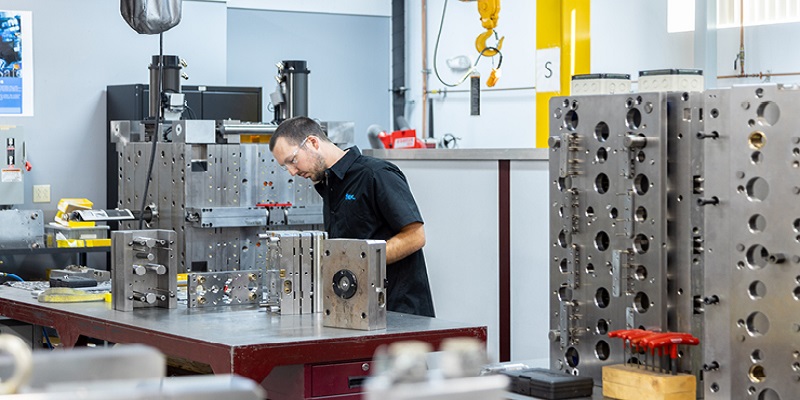
Key Responsibilities of a Medical Molding Engineer
A medical molding engineer plays a critical role in the healthcare manufacturing industry by ensuring that medical devices are produced with precision and quality. Their responsibilities span design, development, testing, collaboration, and regulatory compliance. Here’s an in-depth look at the key areas of their work:
Design and Development
One of the primary responsibilities of a medical molding engineer is creating molds and dies tailored for medical-grade plastics and components. This involves using advanced CAD software to design precision medical mold that meet stringent industry standards. The engineer must consider material properties, component size, and complexity during the design phase. A medical molding engineer also ensures that these molds are optimized for efficiency and durability, enabling high-volume production without compromising on quality.
Testing and Optimization
Before a mold is approved for production, it undergoes rigorous feasibility studies and testing. A medical molding engineer conducts these tests to ensure that the molds and dies meet the required performance, durability, and compliance standards. This includes simulating manufacturing conditions, testing material compatibility, and assessing the long-term reliability of the molds. They also focus on optimizing designs for manufacturability, reducing production costs while maintaining high-quality outcomes.
Collaboration
The work of a medical molding engineer is highly collaborative. They partner with product designers, mechanical engineers, and healthcare professionals to align the medical mold designs with the functional and aesthetic requirements of medical devices. Additionally, they engage with production teams to oversee the fabrication and testing process, ensuring smooth transitions from design to manufacturing. Effective teamwork ensures that the final products meet both technical and regulatory standards.
Compliance and Safety
Regulatory compliance is a cornerstone of the medical device industry. A medical molding engineer ensures that all medical molds and manufacturing processes adhere to strict standards such as those set by the FDA and ISO. This includes verifying material safety, maintaining traceability of design and production processes, and ensuring that the molds are suitable for sterile and contaminant-free environments. By prioritizing compliance, they help ensure patient safety and product reliability.
Essential Skills for Medical Molding Engineers
A medical molding engineer requires a diverse set of technical and soft skills to excel in the specialized field of medical device manufacturing. These skills ensure that they can design and produce high-quality molds and components while maintaining compliance with industry standards. Below is a detailed breakdown of the critical skills that a medical molding engineer must possess:
Technical Proficiency
To succeed as a medical molding engineer, a strong foundation in technical skills is essential. This includes a deep understanding of materials commonly used in medical device plastic manufacturing, such as PEEK (Polyetheretherketone), polypropylene, and silicone. These materials are chosen for their biocompatibility, durability, and ability to withstand sterilization processes.
Proficiency in CAD (Computer-Aided Design) software is also vital. Engineers use these tools to create detailed and precise mold designs that meet exact specifications. Expertise in mold fabrication techniques ensures that these designs can be effectively translated into functional molds for high-volume production. Whether working on injection molding or liquid silicone molding, technical expertise enables the engineer to deliver accurate and reliable results.
Problem-Solving and Critical Thinking
A medical molding engineer often faces complex manufacturing challenges that require innovative solutions. For example, ensuring that a mold is both cost-effective and capable of producing high precision medical components can be a significant hurdle. Engineers must analyze design limitations, identify areas for improvement, and develop practical solutions to enhance manufacturability.
Critical thinking is also crucial when troubleshooting production issues. Engineers must quickly assess the root cause of problems, whether related to material defects or process inefficiencies, and implement corrective measures to maintain production quality.
Communication and Teamwork
Collaboration is a key part of a medical molding engineer’s role, as they work with multidisciplinary teams that include product designers, quality assurance professionals, and healthcare experts. Strong communication skills ensure that everyone involved in the project understands the goals and requirements. Engineers must articulate technical concepts clearly during meetings and presentations to facilitate effective teamwork.
Additionally, documenting processes is essential for regulatory compliance and production continuity. Engineers must create detailed reports, design documentation, and operational guidelines to support both internal teams and external stakeholders.
Regulatory Knowledge
The medical device industry is highly regulated, and a medical molding engineer must have an in-depth understanding of compliance standards such as FDA guidelines and ISO certifications. This knowledge ensures that the molds and components they produce meet stringent safety and performance criteria.
Engineers must stay up-to-date on changes in regulatory requirements, particularly those related to material safety, sterilization, and biocompatibility. By integrating compliance considerations into the design and production process, they help ensure the reliability and safety of medical devices.
Benefits of a Career in Medical Molding Engineering
A career as a medical molding engineer offers numerous advantages, from personal fulfillment to professional growth in a dynamic and impactful field. Below is a detailed exploration of the benefits that make this career path both rewarding and promising.
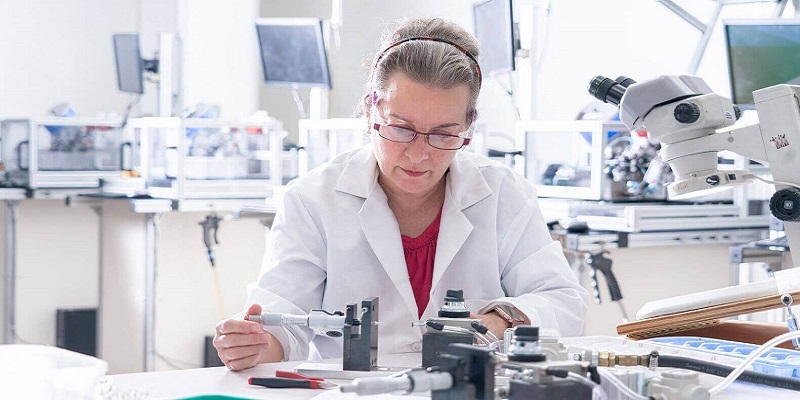
Impact on Healthcare
A medical molding engineer plays a crucial role in developing life-saving devices and technologies. By designing and manufacturing high-precision molds for critical components, such as surgical implants, syringes, and diagnostic equipment, these professionals directly contribute to improving patient outcomes and advancing healthcare.
Their expertise ensures the production of reliable and safe medical devices, which are essential for effective treatment and care. This precision engineering not only enhances device functionality but also builds trust in the medical tools used by healthcare providers.
Growth Opportunities
The demand for skilled medical molding engineers is on the rise due to several factors, including an aging global population and rapid advancements in medical technology. As healthcare systems expand and evolve, the need for innovative medical devices continues to grow, driving opportunities in this specialized field.
The financial prospects are equally attractive, with a median salary range of $80,000–$100,000 annually. Experienced professionals in this field often advance to leadership roles, such as project managers or technical directors, further enhancing their career trajectory.
Innovation and Creativity
Innovation is at the heart of a medical molding engineer’s career. Working with cutting-edge materials and technologies, such as liquid medical silicone injection molding, offers endless opportunities to solve complex challenges. Engineers in this field constantly push the boundaries of what is possible, from developing biocompatible materials to creating molds for minimally invasive surgical tools.
This creativity not only keeps the job intellectually stimulating but also contributes to the advancement of medical science. Every innovation can lead to more effective treatments, safer procedures, and improved quality of life for patients worldwide.
Career Pathways and Education for a Medical Molding Engineer
Becoming a medical molding engineer requires a combination of formal education, specialized training, and practical experience. The career pathways and educational requirements offer a structured yet flexible route into this rewarding profession.
Educational Requirements
To enter the field as a medical molding engineer, a strong educational foundation is essential. A bachelor’s degree in a relevant discipline, such as mechanical engineering, plastics engineering, or biomedical engineering, is typically the minimum requirement. These programs provide the technical and theoretical knowledge needed to design and optimize molds for medical devices.
For professionals aiming to enhance their qualifications, certifications in mold design, CAD software, or industry-specific skills like medical injection molding processes can be highly beneficial. These certifications not only validate expertise but also make candidates more competitive in the job market.
Advanced Training
Aspiring medical molding engineers can benefit greatly from pursuing advanced training tailored to the medical device industry. Specialized graduate programs in bioengineering or mechanical engineering with a focus on medical devices equip students with in-depth knowledge of materials science, regulatory compliance, and precision manufacturing.
Hands-on courses and workshops in mold fabrication, quality assurance, and medical-grade material properties are also advantageous. These programs often include opportunities for internships or cooperative education, providing practical experience alongside academic learning.
Entry and Growth
The career of a medical molding engineer often begins with roles such as tooling or mold technician, where professionals gain hands-on experience in mold fabrication and testing. Over time, they may advance to engineering positions, taking on responsibilities like designing complex molds, optimizing production processes, and ensuring compliance with industry standards.
With additional experience and demonstrated expertise, many engineers progress into managerial or technical leadership roles. These positions allow them to oversee multidisciplinary teams, contribute to high-level project planning, and play a pivotal role in innovation within the medical molding industry.
Challenges in Medical Molding Engineering
The role of a medical molding engineer is both rewarding and demanding, as professionals in this field must navigate a range of challenges to ensure the successful production of medical devices. These challenges stem from the industry’s emphasis on quality, precision, and scalability, all while adhering to rigorous regulatory standards.
Stringent Quality Standards
One of the foremost challenges faced by a medical molding engineer is meeting the stringent quality standards required for medical device manufacturing. Regulatory frameworks like those enforced by the FDA (Food and Drug Administration) in the U.S. and ISO (International Organization for Standardization) globally require thorough documentation and meticulous testing at every stage of production.
Ensuring compliance demands detailed knowledge of material properties, manufacturing processes, and device safety. A medical molding engineer must also stay up to date with changes in regulations and maintain a proactive approach to quality assurance. Failure to meet these high standards can result in device recalls, legal repercussions, and risks to patient safety, making this aspect of the role critically important.
Precision and Scalability
Balancing precision with scalability is another significant challenge in the work of a medical molding engineer. Medical devices often require extremely tight tolerances, especially for components used in implants, surgical tools, and diagnostic equipment. Achieving such precision involves careful design, material selection, and advanced manufacturing techniques like injection molding with liquid silicone or high-performance plastics.
However, this precision must also be maintained when scaling up production for high-volume manufacturing. For instance, items like syringes or catheters are produced in millions, and even a small defect rate can have substantial repercussions. A medical molding engineer must continuously optimize processes to ensure both accuracy and efficiency while keeping production costs manageable.
Navigating Technological and Material Innovations
The evolving nature of technology and materials in the medical field poses additional challenges. As new biocompatible materials and advanced manufacturing techniques emerge, engineers must adapt their skill sets and processes to integrate these innovations effectively. This requires ongoing learning and a commitment to staying ahead of industry trends.
Overcoming the Challenges
Despite these obstacles, the challenges of being a medical molding engineer present opportunities for growth and innovation. By leveraging advanced tools, fostering collaboration, and embracing continuous improvement, professionals in this field can successfully address these challenges and contribute to groundbreaking advancements in healthcare technology.
How a Medical Molding Engineer Can Find the Job They Want
Finding a job as a medical molding engineer requires leveraging a range of strategies and channels to connect with the right opportunities. Below is a detailed explanation of the most effective methods:
Professional Networking
Networking is one of the most powerful tools for finding specialized roles, such as medical molding engineer positions.
- Join Industry-Specific Groups: Participate in professional organizations like the Society of Plastics Engineers (SPE) or the Medical Device Manufacturers Association (MDMA). These groups often provide job boards, mentorship programs, and networking events tailored to the industry.
- Attend Industry Events: Trade shows and conferences, such as MD&M (Medical Design & Manufacturing) or Plastics Industry expos, allow direct interaction with hiring managers, industry leaders, and peers.
- Leverage LinkedIn: Create a professional profile emphasizing skills and achievements in medical molding. Regularly post updates, comment on industry trends, and connect with professionals in medical device manufacturing to expand your network and visibility.
- Ask for Referrals: Reach out to former colleagues, mentors, or contacts who may know of openings. Employee referrals are often prioritized in hiring.
Online Job Portals
Job boards are a convenient way to access a wide range of opportunities, but focusing on industry-specific portals increases the chances of finding relevant roles.
- General Job Boards: Platforms like Indeed, Glassdoor, and Monster list engineering roles across industries. Use keywords such as “medical molding engineer” and set alerts for new postings.
- Specialized Platforms: Explore niche job sites like MedReps (for medical device roles) or Engineering.com (for engineering-specific openings). These often feature roles that align more closely with medical molding expertise.
- Tailor Applications: Customize resumes and cover letters to highlight relevant experience in medical injection molding, regulatory compliance, and project management. A targeted application increases the likelihood of success.
Company Websites
Directly applying to positions on company websites can be highly effective, especially for roles at leading medical device manufacturers.
- Identify Key Employers: Research companies known for medical injection molding or medical device manufacturing, such as Medtronic, Stryker, or Phillips-Medisize.
- Monitor Career Pages: Regularly visit their career sections to stay updated on new job postings. Many organizations list positions on their websites before posting them on job boards.
- Cold Outreach: Even if no current openings are listed, consider reaching out to HR or department heads via email or LinkedIn to express interest. Include a resume and emphasize your relevant expertise in medical molding.
Recruitment Agencies
Recruitment firms specializing in engineering or medical device roles can provide access to exclusive opportunities and streamline the application process.
- Find Specialized Agencies: Look for recruiters with expertise in medical manufacturing or plastics engineering. Agencies like Kelly Engineering or Randstad Engineering often have connections in these fields.
- Build Relationships: Establish a rapport with recruiters by sharing your career goals and expertise. This increases the chances of being recommended for roles that match your skills.
- Leverage Exclusive Listings: Many companies use agencies to fill specialized roles without advertising them publicly. Partnering with a recruiter can open doors to these hidden opportunities.
Continuing Education and Certifications
Furthering your education not only enhances your qualifications but also opens doors to networking and job opportunities through academic and professional affiliations.
- Certifications in Injection Molding: Obtain certifications such as RJG Master Molder or Scientific Injection Molding to demonstrate expertise in advanced molding techniques.
- Medical-Specific Training: Enroll in courses on biocompatibility standards, clean room manufacturing, or ISO 13485 compliance. These skills are highly valued in medical molding.
- Utilize Alumni Networks: Many educational institutions and certification bodies maintain job boards or alumni networks where you can connect with potential employers.
By combining these strategies and dedicating time to each, a medical molding engineer can effectively identify and secure a role that aligns with their skills, interests, and career aspirations.
Key Precautions for a Medical Molding Engineer to Avoid Job Scams
When searching for a job, a medical molding engineer must stay vigilant to avoid fraudulent opportunities. Scammers often target job seekers with fake offers or deceitful practices.
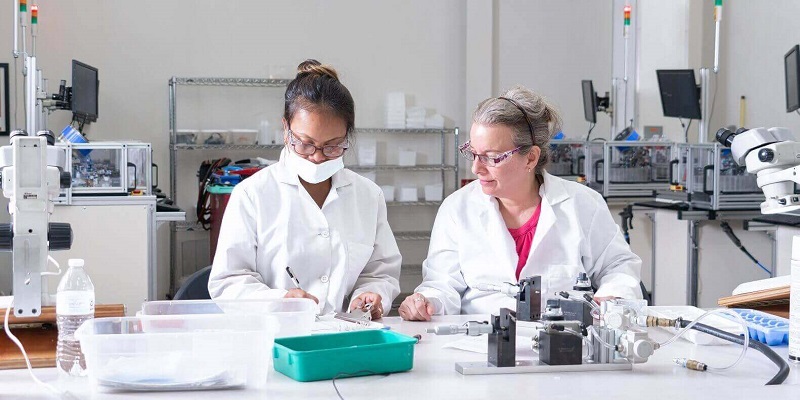
Here are essential precautions to protect yourself:
Verify the Employer’s Legitimacy
Research the company before applying or accepting an offer.
- Check the Company Website: Ensure the website is professional and matches the job description. Fake companies often have poorly designed websites or generic content.
- Look for Reviews: Use platforms like Glassdoor or LinkedIn to check employee reviews and confirm the company’s reputation.
- Verify Contact Details: Reach out using official contact information found on the company’s website, not from unverified sources.
Beware of Requests for Payment or Personal Information
Legitimate employers will never ask for payment or sensitive personal information upfront.
- No Upfront Fees: Avoid offers that require payment for training, certifications, or equipment before you start.
- Secure Personal Data: Be cautious when providing sensitive information like your Social Security Number or bank details. Share these only after verifying the employer and receiving a formal job offer.
Analyze Job Offers Critically
Fake job offers often include unrealistic promises.
- Beware of “Too Good to Be True” Salaries: Scammers lure candidates with offers significantly higher than industry standards. Research typical salaries for a medical molding engineer to set expectations.
- Assess the Job Description: Ensure the description matches the skills and responsibilities of a legitimate medical molding engineer role. Vague or overly broad descriptions are red flags.
Use Trusted Job Search Channels
Rely on verified and reputable platforms for your job search.
- Stick to Recognized Job Boards: Use trusted websites like LinkedIn, Indeed, or Glassdoor. Avoid unknown platforms with minimal credibility.
- Consult Industry-Specific Networks: Job boards of professional associations, such as the Society of Plastics Engineers, are reliable sources for legitimate job postings.
Insist on Professional Communication
Evaluate the professionalism of the recruiter or hiring manager.
- Check Email Domains: Official company emails use verified domains (e.g., @companyname.com). Be wary of generic addresses like Gmail or Yahoo.
- Assess Communication Style: Poor grammar, lack of professionalism, or rushed hiring processes are signs of a scam.
By following these precautions, a medical molding engineer can confidently navigate the job search process and avoid fraudulent schemes while securing legitimate opportunities.
Key Considerations for a Medical Molding Engineer Before Accepting a Job Offer
When a medical molding engineer is ready to accept a job offer, it’s essential to thoroughly evaluate the details to ensure the role aligns with career goals and expectations. Below are critical aspects to consider before finalizing your decision:
Review the Employment Contract
Carefully read the job offer letter and contract to understand the terms of employment.
- Salary and Benefits: Verify that the offered salary matches the agreed amount and review benefits such as healthcare, retirement plans, bonuses, and paid time off.
- Job Role and Responsibilities: Ensure the job description reflects your expectations and the responsibilities discussed during interviews.
- Termination and Notice Period: Understand the terms related to resignation, termination, and notice periods to avoid misunderstandings later.
Evaluate the Work Environment and Culture
Assess whether the company’s work environment aligns with your values and preferences.
- Workplace Policies: Look into company policies regarding flexibility, work-life balance, and professional development opportunities.
- Team Dynamics: If possible, connect with future colleagues or supervisors to gauge the workplace culture and team collaboration.
- Location and Commute: Consider the job’s location and commute time or remote work arrangements, as they can impact job satisfaction.
Understand Career Growth Opportunities
Determine how the position fits into your long-term career goals.
- Training and Development: Ask about opportunities for skill enhancement, certifications, or training in advanced molding technologies.
- Advancement Potential: Inquire about the company’s promotion structure or pathways to leadership roles in engineering or management.
- Exposure to Innovations: Consider whether the company works with cutting-edge medical molding technologies or projects that align with your professional aspirations.
Confirm Regulatory and Compliance Standards
As a medical molding engineer, ensure the company adheres to industry standards and regulations.
- Regulatory Compliance: Verify that the company complies with ISO 13485, FDA regulations, and other standards relevant to medical device manufacturing.
- Quality Assurance: Look into the company’s quality control practices and its commitment to delivering safe, high-quality medical components.
Negotiate if Necessary
Before accepting, discuss any adjustments you may need in the offer.
- Clarify Unclear Terms: If any aspect of the offer is unclear, seek clarification before signing.
- Negotiate Compensation: If the salary or benefits package doesn’t meet your expectations, politely negotiate to reach a mutually agreeable outcome.
- Request Revisions: Ensure any agreed changes are reflected in the final written offer before signing.
By paying attention to these details, a medical molding engineer can confidently accept a job offer, ensuring that it aligns with their professional goals and provides a strong foundation for career growth.
How a Medical Molding Engineer Can Negotiate the Salary They Want When Accepting a Job
When a medical molding engineer decides to accept a job, negotiating for the desired salary is a crucial step. Effective negotiation ensures that compensation aligns with expertise, experience, and market standards. Below are strategies to secure the salary you want:
Research Industry Salary Standards
Understand the average salary range for medical molding engineers to set realistic expectations.
- Use Salary Data Sources: Refer to websites like Glassdoor, Payscale, or industry-specific reports to identify typical salaries for your role, considering location, experience, and company size.
- Benchmark Against Experience: Align your expected salary with your level of expertise, certifications, and any unique skills (e.g., micro-molding expertise or regulatory compliance knowledge).
Highlight Your Value
Demonstrate why you deserve the requested salary by showcasing your skills and achievements.
- Emphasize Unique Qualifications: Discuss certifications, such as RJG Master Molder or ISO 13485 expertise, and how they add value to the company.
- Share Quantifiable Results: Highlight past successes, such as improving production efficiency, reducing defects, or implementing innovative molding techniques.
- Focus on In-Demand Skills: If you have expertise in niche areas like micro-molding or advanced medical-grade materials, emphasize these skills during negotiations.
Strategically Present Your Desired Salary
Approach salary discussions confidently and professionally.
- Start with a Range: Provide a reasonable salary range, with your ideal figure on the higher end. This gives room for negotiation without undervaluing yourself.
- Be Flexible but Firm: Express willingness to negotiate while staying firm about the minimum amount you’re willing to accept.
- Base It on Data: Justify your request by referring to industry averages, cost of living, and the value of your skills to the company.
Consider the Entire Compensation Package
Look beyond salary to evaluate the full offer.
- Assess Benefits: Take into account bonuses, healthcare, retirement contributions, and other perks that may add value to the offer.
- Negotiate Benefits: If the base salary cannot be increased, negotiate additional benefits like relocation assistance, professional development funding, or flexible working arrangements.
Timing and Approach
The way you negotiate can influence the outcome.
- Negotiate After the Offer: Discuss salary only after receiving a formal job offer, showing that the employer values your skills.
- Be Professional and Positive: Approach the conversation respectfully, framing your request as part of ensuring mutual satisfaction.
- Express Enthusiasm: Reinforce your excitement about the role while discussing salary, making it clear that compensation is not your sole motivator.
By preparing thoroughly and negotiating strategically, a medical molding engineer can secure the salary they want while maintaining a positive relationship with the employer.
FAQs about Medical Molding Engineer
A molding engineer is responsible for designing, developing, and optimizing molds and dies used in the manufacturing process. These professionals ensure that molds are efficient, durable, and meet production requirements for quality and precision. Molding engineers work closely with product designers to translate ideas into functional molds, often using advanced CAD software. They also oversee mold testing, troubleshooting, and maintenance to resolve production issues. Additionally, they collaborate with manufacturing teams to streamline operations and implement cost-effective solutions. In industries like medical devices, molding engineers ensure compliance with strict regulatory standards while maintaining high-volume reproducibility.
Medical molding is a specialized manufacturing process used to create precise, sterile components for medical devices and healthcare applications. It involves melting and shaping medical-grade plastics or other biocompatible materials into parts like syringes, catheters, surgical tools, and implants. Medical molding ensures that these products are safe, durable, and compatible with the human body. Techniques like injection molding, overmolding, and insert molding are common in this field. The process requires strict adherence to industry standards, such as FDA and ISO regulations, to ensure product safety and quality for patient care.
A mold engineer designs, develops, and manages molds and dies used in manufacturing. Their role includes creating detailed specifications, conducting feasibility studies, and testing molds to ensure efficiency and precision. Mold engineers are also responsible for troubleshooting production issues, optimizing mold designs for cost-effectiveness, and collaborating with cross-functional teams, including product designers and manufacturing staff. In industries like medical devices, they ensure compliance with stringent regulatory standards and support high-quality, scalable production. The role demands expertise in CAD software, materials science, and mold fabrication techniques, as well as strong problem-solving and communication skills.
A medical design engineer specializes in developing innovative medical devices that improve patient care. They work on creating functional and safe designs for products like diagnostic tools, implants, prosthetics, and surgical instruments. Medical design engineers use their expertise in engineering principles, materials science, and regulatory requirements to develop devices that meet healthcare needs. They collaborate with clinicians, researchers, and manufacturing teams to ensure the products are both effective and manufacturable. Their responsibilities include prototyping, testing, and refining designs to meet industry standards and patient safety requirements, contributing to advancements in healthcare technology.
Molding and casting are both manufacturing techniques used to create parts, but they differ significantly in methods, materials, and applications. For medical molding engineers, understanding these distinctions is vital. Molding involves shaping materials (typically plastics) by injecting or compressing them into a mold cavity under high pressure and temperature. It is commonly used in medical device manufacturing due to its precision, repeatability, and ability to work with biocompatible materials like thermoplastics and silicones.
Casting, on the other hand, involves pouring molten material (usually metals or ceramics) into a mold where it solidifies. Casting is better suited for parts with complex geometries or larger sizes but lacks the precision and speed of molding. Medical molding engineers focus on injection molding for its ability to produce high-quality, intricate medical components with tight tolerances, making it the preferred method in healthcare manufacturing.
A career in injection molding, especially as a medical molding engineer, offers excellent prospects. The medical industry’s demand for precision-engineered components ensures a stable and rewarding career path. Medical molding engineers work on cutting-edge technologies, designing molds for intricate medical devices like implants, surgical tools, and diagnostic equipment. The role combines engineering, material science, and manufacturing expertise, providing opportunities for continuous learning and innovation.
The job offers competitive salaries, especially in the medical field, where stringent quality and regulatory standards elevate the importance of skilled professionals. Additionally, the career has significant growth potential as advancements in materials and technologies, like micro molding and bioresorbable plastics, expand the scope of medical applications. For individuals interested in combining engineering with healthcare impact, injection molding for the medical sector is a fulfilling and challenging career choice.
Contact our professional team now for a same-day quote and risk-free project evaluation. Benefit from ISO 8 cleanrooms, advanced machines, and 12-hour fast response in medical injection molding.