Injection molding plays a pivotal role in the production of medical devices, offering unmatched precision and scalability for creating intricate components. In the healthcare industry, meeting medical molding requirements is critical to ensure devices are safe, effective, and compliant with stringent regulations. Manufacturers, particularly China medical molding factories, prioritize precision, often utilizing advanced precision mold medical techniques to produce parts that meet exact specifications. These factories are adept at selecting materials that guarantee biocompatibility and durability, ensuring that the final products are of the highest quality. Compliance with standards like ISO 13485 and FDA regulations ensures reliability and market acceptance. The entire process is tailored to uphold patient safety and functionality, making precision and quality control essential. Understanding these medical molding requirements allows manufacturers to create devices that not only meet industry demands but also push the boundaries of innovation in healthcare. Medical molding requirements ensure safety and quality by meeting ISO 13485, ISO 10993, ISO 14644, and FDA standards for healthcare components
Low-Volume to High-Volume Production Capabilities
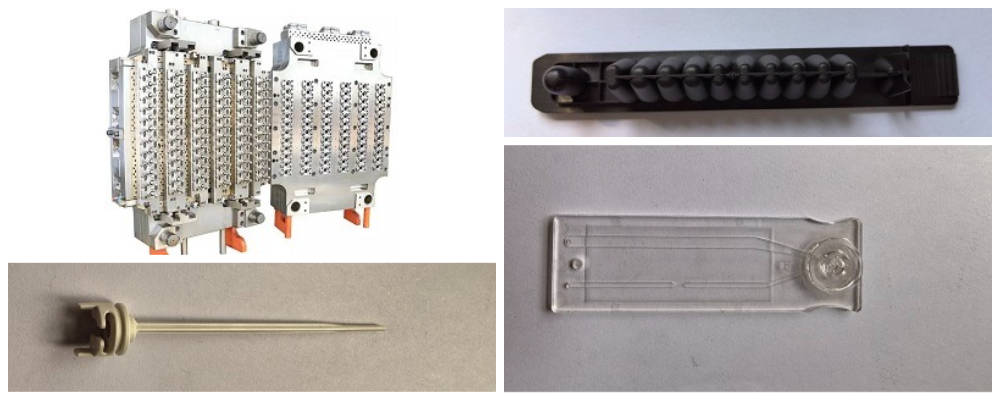
Attributes | Details |
---|---|
Place of Origin | Dongguan, Guangdong, China |
Brand Name | LY Medical Injection Mold |
Product Name | Medical Molding |
Application | Medical Industry |
Shaping Mode | Plastic Injection Mold |
Technology | Hot Pressing |
Material | ABS/PA66/PP/PC/PMMA/PSU/PCTG/TPE/TPU/PBT |
Surface Treatment | Polished, Matte, Smooth, Bright, etc. |
Certification | ISO9001:2015 |
Size | Customized Size |
Color | Customized Color |
Shape | Customized Shape |
Processing Service | Molding, Cutting |
Drawing Format | IGES, STEP, AutoCAD, Solidworks, STL, PTC Creo, DWG, PDF, etc. |
Feature | Environmentally Friendly |
Advantage | High Quality |
Mold Life | According to Customer Requirement |
Minimum Order Quantity | 100 Pieces |
Why Are Medical Molding Requirements Critical in Manufacturing?
Medical molding is an essential process in manufacturing high-quality medical devices, and adhering to medical molding requirements ensures optimal performance, safety, and reliability.
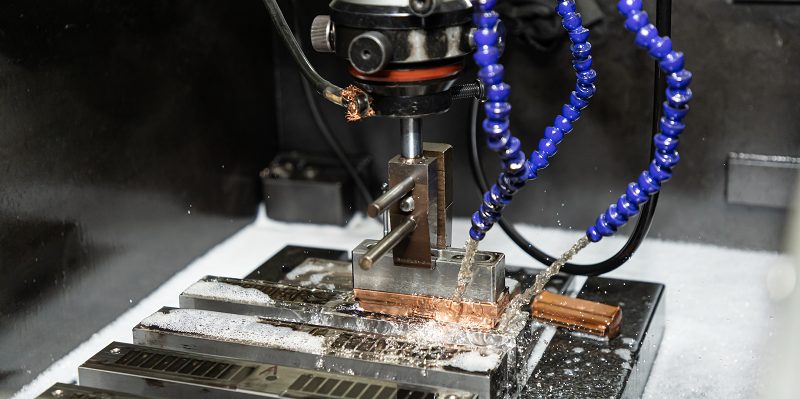
Below are the key reasons why these requirements are critical:
Ensuring Patient Safety and Product Efficacy
- Patient safety is paramount in medical applications. Strict medical molding requirements guarantee that products meet hygiene and sterility standards to minimize risks.
- Precision in molding ensures that components function as intended, contributing to the efficacy of medical devices like surgical tools and implants.
Compliance with Regulatory Standards for Global Market Entry
- Compliance with standards such as ISO 13485, FDA, and CE certification is mandatory for global market entry. These requirements confirm that medical devices meet established safety and quality benchmarks.
- Adhering to medical molding requirements demonstrates a commitment to ethical manufacturing and ensures long-term industry credibility.
Enhancing Product Durability and Biocompatibility
- Materials used in medical molding must be biocompatible to avoid adverse reactions in patients. Selection of high-grade plastics, such as polycarbonate or PEEK, ensures compatibility and longevity.
- Robust design and material precision enhance durability, making devices reliable even under repeated use or extreme conditions.
What is Medical Injection Molding Requirements?
Adhering to medical injection molding requirements involves meticulous attention to detail across the production process. Key aspects include:
- Material Selection: Using certified biocompatible materials suitable for healthcare environments.
- Process Control: Implementing strict quality checks to maintain consistency and precision in molded components.
- Regulatory Documentation: Ensuring all products have complete compliance records to meet regulatory and audit requirements.
Meeting these medical molding requirements is not just about compliance—it’s a commitment to delivering safe and innovative medical solutions that improve patient outcomes worldwide.
Regulatory Standards for Meeting Medical Molding Requirements
Adhering to strict medical molding requirements, including medical molding validation, is essential for producing safe, effective, and compliant medical devices. Regulatory standards provide the framework to ensure consistency, quality, and patient safety. Below are key regulations and standards that shape the medical molding process:
FDA Requirements
The U.S. Food and Drug Administration (FDA) enforces stringent guidelines for medical molding manufacturers to ensure product safety and efficacy. Key aspects include:
- Registration with FDA (21 CFR Part 820): Medical molding facilities must register with the FDA to produce Class I, II, or III devices.
- Quality Management System (QMS) Compliance: QMS implementation is required to maintain consistency in processes and product quality.
- Risk Management Protocols: Risk assessments, Failure Mode and Effects Analysis (FMEA), and thorough documentation are integral to identify and mitigate potential risks.
ISO Standards
Compliance with ISO standards ensures that products meet international benchmarks for quality and safety. Core ISO standards include:
ISO 13485: Medical Devices
A critical standard for quality management systems in medical manufacturing. It focuses on the design, development, and production of medical-grade products. ISO 13485 outlines the requirements for a quality management system (QMS) when producing medical-grade products. It is the most common standard used in medical device manufacturing. ISO 13485 is not limited to plastic injection molding but rather covers the general requirements for all manufacturing technologies that are used to produce medical equipment. This standard was developed to ensure that consistent quality is maintained and that medical devices and equipment are produced in a safe and effective manner.
To achieve these goals, ISO 13485 outlines processes and procedures to manage risk and regulatory compliance while providing mechanisms to continuously improve the QMS whenever a gap or potential for improved performance is noted. The standard defines best practices for documentation, training, traceability, research and design, production, and how to handle non-conformances. For both the part designer and the medical injection molders, there are well-defined responsibilities.
The QSR (Quality System Regulations), also referred to as 21 CFR part 820, as outlined by the FDA, has many parallels with ISO 13485. In the United States, the QSR may be used as a supplement or replacement for the ISO 13485 standard.
ISO 10993: Biological Evaluation of Medical Devices
Ensures biological evaluation and biocompatibility, verifying that materials used in medical molding are safe for patient contact. ISO 10993 focuses primarily on the biocompatibility requirements for medical devices. It encompasses products that are designed to come into direct or indirect contact with the body. The goal of ISO 10993 is to reduce the risk of adverse effects on patients when exposed to materials that include, but are not limited to, injection molded plastics. ISO 10993 compliant materials are non-toxic, do not affect the immune system, or do not potentially cause cancer.
The ISO 10993 standard consists of 23 parts or subsections. This includes processes and procedures for animal welfare requirements, tests for carcinogenicity, reproductive toxicity, in vitro cytotoxicity, and various sterilization techniques. USP (United States Pharmacopeia) Class VI covers similar biocompatibility requirements for plastics and, as such, is sometimes used in place of ISO 10993 or as a supplement. For designers, this standard can play an important role in material selection.
ISO 14644: Cleanrooms & Associated Controlled Environments
Defines cleanroom requirements to control contamination during the molding process, essential for sterile medical devices. ISO 14644 regulates the use of cleanrooms during medical device manufacturing. It defines the various cleanroom classes from Class 1 to Class 9, where Class 1 has the most stringent cleanliness requirements.
In cleanrooms, the amount and size of airborne particles are carefully controlled to reduce the chances of exposing sensitive medical components to these particles. ISO 14644 also outlines specific requirements for designing, manufacturing, and maintaining cleanrooms for optimal performance. Designers may need an injection molder with a Class 7 or Class 8 cleanroom to limit the potential for contamination during manufacturing.
What is Highly Demanding Medical Molding Requirements
The Challenges of Highly Demanding Medical Molding
Meeting the needs of highly demanding medical molding involves navigating complexities that go beyond standard manufacturing. These include:
- Precision Manufacturing: Extremely tight tolerances are required for critical medical components.
- Material Certification: Only biocompatible, high-performance materials are used to meet stringent medical molding requirements for durability and safety.
- Enhanced Traceability: Full documentation and batch traceability are essential for audits and recalls, ensuring product accountability at every stage.
Compliance with these rigorous standards allows manufacturers to meet the demands of highly demanding medical molding, ensuring patient safety, product reliability, and market acceptance.
Medical Device Classifications and Their Impact on Medical Molding Requirements
Understanding medical device classifications is essential for adhering to medical molding requirements, as these classifications dictate the regulatory standards and design considerations for each type of device.
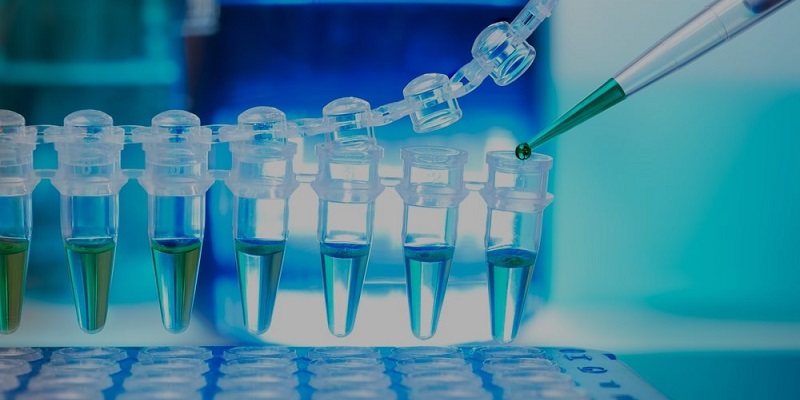
Below is an overview of classifications and their impact:
Classification Based on Potential Risk to Patients
Class I: Low-Risk Devices
- Examples: Bandages, examination gloves, eyeglasses.
- Regulatory Implications: Subject to general controls such as proper labeling and good manufacturing practices (GMP).
- Design Considerations: Simpler manufacturing processes with less stringent testing requirements. Compliance with basic medical molding requirements ensures safety and functionality.
Class II: Moderate-Risk Devices
- Examples: Syringes, surgical gloves, blood pressure monitors.
- Regulatory Implications: Requires additional controls, including performance testing and premarket notification (510(k)) submissions.
- Design Considerations: Emphasis on precision and material selection to meet both performance and biocompatibility standards outlined in medical molding requirements.
Class III: High-Risk Devices
- Examples: Pacemakers, heart valves, implants.
- Regulatory Implications: Subject to the most rigorous controls, including premarket approval (PMA) and clinical testing to validate safety and effectiveness.
- Design Considerations: Advanced manufacturing processes with strict adherence to medical molding requirements, including use of biocompatible materials, sterile environments, and comprehensive traceability protocols.
Regulatory Implications and Design Considerations for Each Class
- Class I: Focuses on cost-efficiency and basic compliance without compromising safety. Low-risk products still require adherence to GMP and consistent manufacturing practices.
- Class II: Demands additional validation and quality assurance measures, requiring tighter tolerances in the molding process and the use of FDA-approved materials.
- Class III: Represents the pinnacle of medical molding requirements, necessitating cutting-edge technologies, cleanroom environments, and rigorous quality control to produce life-sustaining devices.
Each classification plays a critical role in shaping the molding process, ensuring that all medical devices are safe, reliable, and suitable for their intended use. Proper adherence to medical molding requirements at every stage safeguards patient outcomes and supports regulatory compliance.
Material Selection to Meet Medical Molding Requirements
Material selection is a critical aspect of meeting medical molding requirements, as the chosen materials must ensure the safety, reliability, and performance of medical devices. Using medical-grade plastics that comply with regulatory standards is essential for maintaining patient safety and product efficacy. Below is a detailed look at commonly used materials and the factors influencing their selection:
Importance of Using Medical-Grade Plastics
- Regulatory Compliance: Medical-grade plastics meet strict FDA and ISO standards, ensuring they are safe for contact with the human body and compatible with medical applications.
- Enhanced Performance: These materials are specifically engineered to withstand sterilization processes and resist degradation under medical conditions.
Commonly Used Materials and Their Characteristics
Polyetheretherketone (PEEK)
- Characteristics: High resistance to heat, chemicals, and mechanical stress.
- Applications: Often used in surgical implants and high-performance components.
Polypropylene (PP)
- Characteristics: Excellent moisture and chemical resistance, lightweight, and cost-effective.
- Applications: Ideal for disposable syringes, containers, and other non-invasive tools.
Polycarbonate (PC)
- Characteristics: High impact resistance, transparency, and dimensional stability.
- Applications: Commonly used for surgical instruments, connectors, and diagnostic devices.
Silicone
- Characteristics: Highly flexible, durable, and biocompatible.
- Applications: Suited for catheters, seals, and prosthetics.
Polystyrene (PS)
- Characteristics: Rigid, stable, and cost-efficient.
- Applications: Frequently used for diagnostic tools and lab equipment.
Polyethylene (PE)
- Characteristics: Biocompatible, versatile, and widely used in medical applications.
- Applications:It is ideal for manufacturing tubing, containers, and implantable devices.
Perfluoroalkoxy (PFA)
- Characteristics: Known for high thermal resistance, excellent chemical stability, and durability.
- Applications:It is used for catheter coatings and high-temperature labware.
Fluorinated Ethylene Propylene (FEP)
- Characteristics: Features flexibility, transparency, low friction, and chemical resistance.
- Applications:It is applied in medical tubing, wiring insulation, and fluid handling systems.
Factors Influencing Material Choice
Biocompatibility and Sterilization
- Materials must be safe for patient contact, with no adverse biological reactions.
- The ability to endure multiple sterilization methods (e.g., autoclaving, radiation) is essential for meeting medical molding requirements.
Mechanical Strength and Chemical Resistance
- Components must withstand mechanical stress during use and resist degradation from exposure to bodily fluids or cleaning agents.
- High chemical resistance ensures durability in challenging environments, such as operating rooms or laboratories.
Selecting the right material is fundamental to meeting medical molding requirements, ensuring that the final product performs reliably in its intended medical application while adhering to regulatory standards.
Injection Molding Techniques for Meeting Medical Molding Requirements
Various injection molding techniques are employed in the medical industry to meet diverse requirements and ensure compliance with medical molding requirements. These techniques offer precision, scalability, and adaptability to create high-quality components for medical applications.
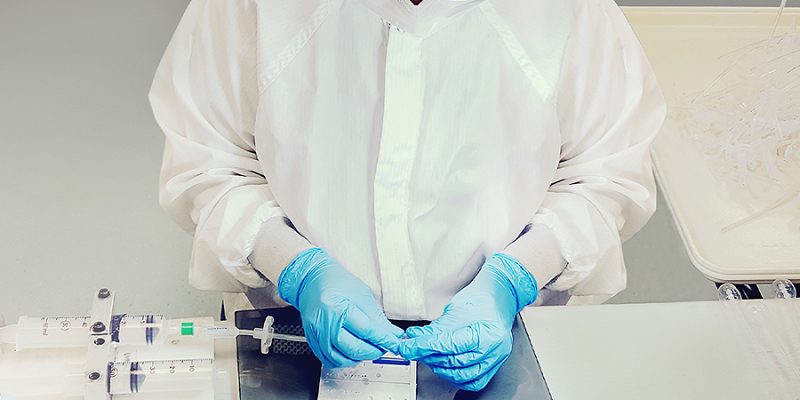
Below are the key techniques used:
Plastic Injection Molding
- Overview: A cost-effective process for producing large volumes of parts with consistent quality.
- Advantages:
- Highly efficient for mass production, reducing unit costs.
- Supports a wide range of medical-grade plastics like polypropylene and polycarbonate.
- Ensures precision in meeting tight tolerances required by medical molding requirements.
- Applications: Commonly used for syringes, diagnostic components, and housing for medical devices.
Insert Molding
- Overview: Combines molded plastic components with pre-fabricated inserts, such as metal or ceramic parts.
- Advantages:
- Increases design versatility by incorporating multiple materials.
- Reduces assembly time and enhances product integrity.
- Applications: Used for surgical instruments, connectors, and devices requiring embedded electronics.
Overmolding
- Overview: Involves molding one material over another to create a single, unified component.
- Advantages:
- Enhances durability and comfort by combining hard and soft materials.
- Improves grip and functionality for medical tools.
- Adheres to medical molding requirements by ensuring seamless integration of materials.
- Applications: Ideal for creating ergonomic handles for surgical devices or protective coverings for electronic components.
Liquid Silicone Injection Molding
- Overview: Specialized for molding flexible and biocompatible materials like liquid silicone rubber (LSR).
- Advantages:
- Exceptional biocompatibility and resistance to extreme temperatures.
- Highly precise for intricate parts and medical components.
- Suitable for sterilization processes, aligning with medical molding requirements for safety and reliability.
- Applications: Used for catheters, seals, and implantable devices.
These techniques, tailored to meet stringent medical molding requirements and supported by high precision tools for medical device manufacturing, ensure that medical devices are manufactured to the highest standards of safety, durability, and performance. Each method is chosen based on the device’s specific application and regulatory needs.
Benefits of Fully Complying with Medical Molding Requirements
Adhering to medical molding requirements provides significant advantages for manufacturers, healthcare providers, and patients. These benefits extend beyond regulatory compliance, fostering trust, enhancing product quality, and improving market competitiveness. Below are six key benefits:
Improved Patient Safety and Trust in Medical Devices
- Ensuring Safety: Compliance with medical molding requirements ensures that materials and manufacturing processes meet stringent safety standards, minimizing the risk of device failure or adverse reactions.
- Building Trust: Reliable, high-quality medical devices foster trust among healthcare providers and patients, reinforcing confidence in the product’s efficacy and safety.
Faster Regulatory Approvals for Market Entry
- Streamlined Compliance: Meeting industry standards like ISO 13485 and FDA requirements expedites regulatory review processes, enabling faster time-to-market.
- Global Acceptance: Adherence to medical molding requirements ensures compliance with international standards, simplifying entry into global markets and expanding opportunities.
Enhanced Product Quality and Long-Term Performance
- Durability: High-quality materials and precision manufacturing result in products that perform consistently over time, meeting rigorous medical use demands.
- Reliability: Devices manufactured under strict medical molding requirements are less prone to defects, reducing the likelihood of recalls and failures.
Cost Efficiency Through Reduced Defects
- Minimized Waste: Stringent quality control reduces manufacturing defects, lowering material waste and production costs.
- Fewer Recalls: Compliance with medical molding requirements mitigates the risk of costly recalls and reputational damage, saving resources in the long run.
Competitive Advantage in the Medical Industry
- Reputation for Excellence: Manufacturers that consistently meet medical molding requirements and produce high-quality medical precision components establish a reputation for producing superior, reliable medical devices.
- Market Differentiation: High standards in manufacturing set compliant companies apart, attracting healthcare providers and industry partnerships.
Adaptability to Future Regulatory Changes
- Proactive Compliance: A solid framework for meeting current medical molding requirements makes it easier to adapt to evolving industry regulations.
- Sustainability: Compliance supports long-term viability and sustainability, ensuring the manufacturer remains competitive in a dynamic market.
By meeting medical molding requirements, manufacturers can deliver safe, reliable, and high-performing medical devices that meet industry needs while fostering trust and innovation in healthcare solutions.
FAQs about Medical Molding Requirements
To work in the field of injection moulding, certain qualifications are typically required, balancing both formal education and hands-on experience. Generally, a high school diploma or equivalent is the minimum educational requirement. Many employers prefer candidates with further education in fields such as engineering, manufacturing technology, or industrial design, often gained through an associate’s degree or a bachelor’s degree program. Technical skills training, which may include learning about mould design, material science, and machine operation, is crucial. Additionally, certifications can bolster one’s qualifications; for example, certifications from the Society of Plastics Engineers can demonstrate specialized competence. Experience in a manufacturing environment can be a valuable asset, as it helps in understanding the nuances of the injection moulding process.
Medical moulding is a specialized process within the injection moulding industry, focusing on producing components and devices used in the healthcare sector. It involves designing and manufacturing medical-grade plastic parts that meet strict regulatory standards and quality requirements. The materials used in medical moulding are often bio-compatible and durable to withstand various sterilization techniques and environmental conditions. This process is utilized to create a wide range of products, including surgical instruments, diagnostic devices, dental components, and custom prosthetics. Precision and consistency are crucial in medical moulding to ensure patient safety and product reliability, necessitating advanced moulding technologies and stringent quality control measures.
The design of medical equipment must adhere to numerous international and national standards to ensure safety, effectiveness, and reliability. One of the primary sets of guidelines comes from the International Organization for Standardization (ISO), with ISO 13485 being particularly significant as it outlines quality management systems for the design and manufacture of medical devices. Compliance with ISO 13485 ensures that products meet both customer and regulatory requirements. In addition, the FDA provides regulations under 21 CFR Part 820, known as the Quality System Regulation (QSR), which governs the production processes within medical device manufacturing in the United States. Key aspects covered include risk management, performance testing, usability engineering, and validation processes. Furthermore, the design process must consider ergonomic factors, electrical safety (IEC 60601), and biocompatibility (ISO 10993) if the device involves human contact.
Injection moulding, like any industrial process, comes with specific safety requirements designed to protect workers and ensure a secure working environment. One crucial aspect is the use of guarding and interlocks on machinery to prevent accidental contact with moving parts. Proper training for operators is essential, covering machine controls, emergency stop procedures, and safety protocols. Personal protective equipment (PPE), such as safety glasses, gloves, and protective clothing, may be required to shield workers from hot materials and moving equipment. Temperature and pressure controls are critical to prevent overheating and bursts, while regular maintenance and inspection of equipment help identify potential hazards early. Ventilation is important to disperse any fumes or particulates that may be emitted during the process, keeping air quality within safe limits. Additionally, adherence to regulatory standards like OSHA in the United States helps ensure compliance with industry safety practices. By implementing these safety measures, the risks associated with injection moulding can be significantly minimized, promoting a safer and more efficient manufacturing environment.
Medical molding often requires certifications to ensure the production of safe and high-quality medical components. One of the most important certifications is ISO 13485, which specifies requirements for a quality management system (QMS) in the design, production, and servicing of medical devices. This standard focuses on regulatory compliance and risk management, emphasizing cleanliness, contamination control, and traceability.
Additionally, cleanroom certifications, such as compliance with ISO 14644 standards, are vital for facilities where medical molding occurs. These standards ensure the control of airborne particles during the manufacturing process. Some medical molding processes also require compliance with FDA 21 CFR Part 820, which governs quality systems for medical devices in the United States.
Obtaining these certifications demonstrates that a manufacturer adheres to stringent controls in material selection, tooling, and molding processes, ensuring the safety and efficacy of the final medical device.
Injection molding for medical applications must meet specific standards to ensure safety, precision, and reliability. The primary standard is ISO 13485, which outlines the quality management system for medical devices. Compliance with this ensures traceability, defect prevention, and regulatory adherence.
Another critical guideline is ISO 14644 for cleanroom environments. This is particularly crucial when molding components that will be used in sterile medical devices. For materials, standards such as USP Class VI certification assess biocompatibility, ensuring the material is safe for contact with the human body.
The FDA 21 CFR Part 820 also applies to U.S.-based manufacturers, focusing on quality systems, validation, and documentation. Molders often adhere to these standards to meet industry and regulatory demands. Additionally, manufacturers may implement Design for Manufacturability (DFM) principles, aligning with these standards to enhance production efficiency while ensuring compliance.
To secure FDA approval for a medical device, manufacturers must demonstrate that the device is safe, effective, and compliant with regulatory standards. The process often begins with determining the device classification (Class I, II, or III), which dictates the level of regulation required.
For Class II and some Class I devices, manufacturers usually need to submit a 510(k) premarket notification to demonstrate that their device is substantially equivalent to a legally marketed predicate device. The submission requires detailed documentation, including design controls, testing results, labeling, and risk assessments.
Class III devices, considered high-risk, typically require a more rigorous Premarket Approval (PMA), which involves clinical testing and extensive safety and efficacy data.
Manufacturers must also comply with FDA Quality System Regulation (QSR), outlined in 21 CFR Part 820, ensuring robust design, production, and documentation practices. Additional requirements include biocompatibility testing and sterility validation.
In most cases, medical devices cannot be legally sold in the U.S. without FDA approval or clearance. Class I devices, which pose minimal risk, are often exempt from premarket notification but must still comply with general controls like labeling and quality system requirements. However, Class II and III devices generally require 510(k) clearance or Premarket Approval (PMA) before they can be marketed.
Selling an unapproved medical device can lead to severe consequences, including product recalls, fines, and legal action. Certain exemptions exist, such as for investigational devices used in clinical studies, but even these must comply with FDA regulations.
In emergency situations, the FDA may authorize unapproved devices under the Emergency Use Authorization (EUA) program. For routine commercialization, however, FDA approval or clearance is essential to ensure the device’s safety and effectiveness for public use.
The timeline for 510(k) clearance can vary, but the FDA typically aims to review submissions within 90 calendar days. However, the actual duration often extends beyond this, depending on the complexity of the device and the completeness of the submission.
Manufacturers must provide detailed documentation, including descriptions of the device, its intended use, design data, and proof of substantial equivalence to a predicate device. If the FDA identifies deficiencies during the review, they may issue requests for additional information, which can delay the process.
Pre-submission consultations with the FDA can help streamline the process by addressing potential issues early. On average, manufacturers should anticipate a timeline of 3 to 6 months for clearance, although more complex devices or incomplete applications can extend this period to a year or longer. Strategic planning and robust documentation are key to minimizing delays.
Contact our professional team now for a same-day quote and risk-free project evaluation. Benefit from ISO 8 cleanrooms, advanced machines, and 12-hour fast response in medical injection molding.