Medical molding services play a crucial role in the production of medical devices and pharmaceutical packaging, ensuring that these products meet the highest standards of quality, safety, and performance. This process involves the use of advanced molding techniques, such as injection molding, blow molding, and compression molding, to create complex components that are used in a wide range of medical applications. China medical molding factories have become key players in this industry, offering cost-effective solutions without compromising on quality. These factories utilize state-of-the-art equipment and skilled professionals to produce high-precision parts for various medical devices. Medical molding services, along with precision mold medical techniques, are essential in maintaining strict adherence to regulatory standards, including those set by the FDA and ISO, ensuring that all products are manufactured with precision and consistency. Whether it’s producing surgical tools, drug delivery systems, or sterile packaging, medical molding services guarantee the functionality and safety of life-saving healthcare products. FUJIU Medical Injection Mold, based in China, provides ISO-certified medical molding services, specializing in precision parts, cleanroom production, and assembly.
Low-Volume to High-Volume Production Capabilities
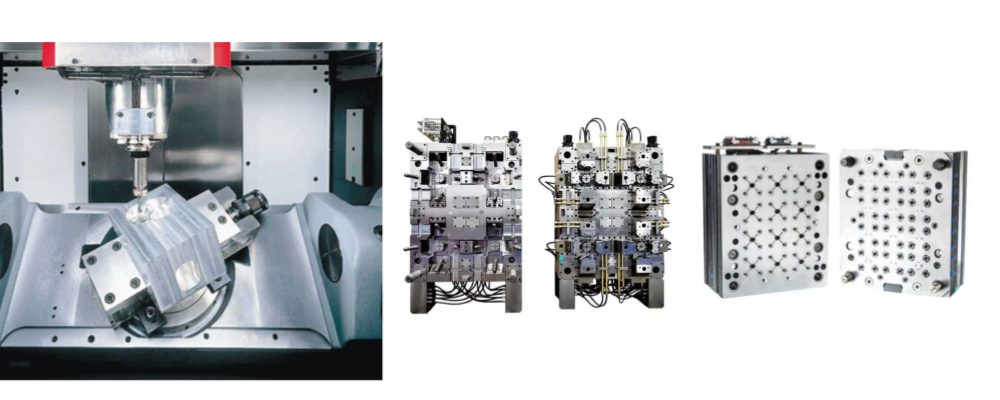
Attribute | Details |
---|---|
Shaping Mode | Medical Molding |
Place of Origin | Dongguan, Guangdong, China |
Brand Names Available | LY Medical Injection Mold |
Materials Used | ABS, PP, PC, PS, PA6, PA66, POM, PE, PU, PVC, PMMA, PSU, PCTG, TPE, TPU, PBT, ASA, Rubber |
Applications | Medical Parts, Medical equipment |
Customization Capabilities | - Size: Fully customized to client requirements |
- Color: Customizable | |
Process and Treatments | - Injection Molding Process: Hot and cold runner options |
- Surface Treatments: Polishing, spray painting, screen printing, UV coating, electroplating, laser carving, sandblasting | |
- Additional Processing Services: Molding, cutting, assembling, customized packing | |
Precision and Accuracy | - Dimensional Accuracy: ±0.02mm |
- Mold Life: 300,000 to 1,000,000 shots | |
- Cavity Configurations: Single, multi, and combination molds (e.g., 1x1, 1+1, 1x2) | |
Certifications | ISO9001-certified manufacturing process |
MOQ (Minimum Order Quantity) | From 1 piece to 500 pieces |
Packing Options | Wooden cases and customizable packaging based on user requirements |
Notable Features | - High-quality material selection ensuring durability and precision |
- Tailored designs meeting both industrial and medical application standards | |
- Specialized options for medical machinery shells and industrial-grade plastic components |
What Are Medical Molding Services?
Medical molding services refer to the specialized use of molding techniques to create precision components for medical devices and pharmaceutical applications. These services are critical for producing high-quality, safe, and functional products that are essential in healthcare settings. The molding process involves the shaping of medical-grade materials into components that meet strict regulatory standards and are durable enough for use in sensitive medical environments. Medical molding services encompass a variety of molding methods, each tailored to meet specific needs in the healthcare industry, such as injection molding, compression molding, and blow molding. These techniques ensure that medical components maintain their performance and integrity, even under challenging conditions.
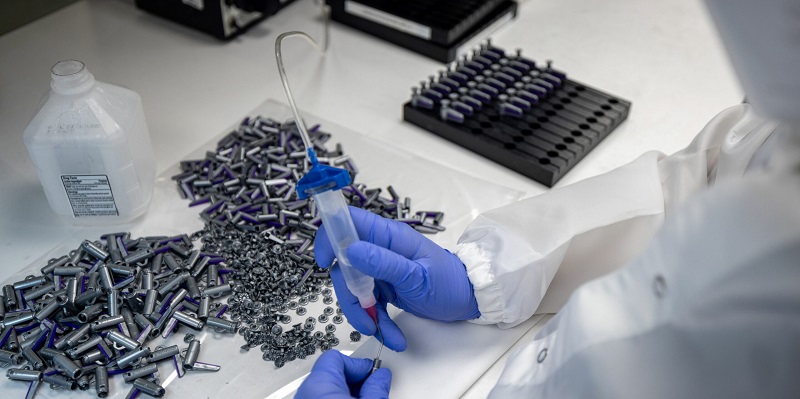
Types of Molding Used in Medical Applications
- Injection Molding: One of the most widely used techniques in medical molding services, injection molding is ideal for producing high-precision parts such as syringes, medical connectors, implants, and small components used in drug delivery systems. This process allows for intricate designs with tight tolerances, making it highly suitable for medical devices that require high levels of accuracy and sterility.
- Blow Molding: Blow molding is employed to create hollow medical products such as bottles, containers, and vials. This method is often used to manufacture medical packaging that needs to be both lightweight and resistant to damage. It allows for the production of containers with uniform wall thickness and a high degree of consistency, critical for packaging pharmaceuticals or creating disposable medical devices.
- Compression Molding: Used for larger medical components, compression molding is especially effective for producing parts like seals, gaskets, and components used in medical equipment. The process involves placing medical-grade material into a heated mold, where it is compressed to form the desired shape. It is ideal for larger, complex parts that require a high degree of durability and resistance to wear and tear.
- Rotational Molding: Rotational molding is often used for creating large, hollow parts in medical applications, such as storage tanks, medical furniture, and certain medical device enclosures. This method is particularly useful when producing large-volume parts with consistent thickness and strength. It allows for the efficient production of complex shapes without the need for high-pressure molding equipment.
Medical molding services ensure that these different molding techniques are applied with precision, resulting in components that meet stringent industry standards and contribute to the overall safety and effectiveness of medical products.
Contract Medical Molding Services
Contract medical molding services are an essential solution for companies looking to outsource the production of medical components and devices. These services allow businesses to focus on product design and development while relying on specialized molding experts to handle manufacturing. By partnering with a contract medical mold provider, companies gain access to advanced molding technologies, high-quality materials, and compliance with strict regulatory requirements. Additionally, the expertise in medical mold design ensures that the molds are tailored to meet precise specifications. Contract manufacturers can offer flexible production capabilities, scaling from prototyping to high-volume manufacturing, ensuring timely delivery and cost-effective production. This partnership is crucial for companies that may not have the in-house capacity or expertise to produce medical components at the required standards.
Medical Device Molding Services
Medical device molding services are specialized processes designed to create high-precision components for medical devices used in various healthcare applications. These services involve advanced molding techniques such as injection molding, overmolding, and multi-shot molding, ensuring the production of durable and reliable devices. With the integration of medical device automation, manufacturers can achieve enhanced efficiency and consistency throughout the production process. Medical device molding services are used to manufacture a wide range of products, including surgical instruments, implants, diagnostic devices, and drug delivery systems. The focus on precision and compliance with industry standards, such as FDA regulations and ISO certifications, ensures that the medical devices produced are safe, effective, and of the highest quality. By utilizing cutting-edge technologies and materials, these services help meet the evolving demands of the healthcare industry.
Medical Plastic Molding Services
Medical plastic molding services play a vital role in the production of plastic components used in medical applications. These services specialize in molding medical-grade plastics that offer excellent biocompatibility, durability, and resistance to harsh sterilization processes. Medical plastic molding services are used to create a variety of products, including syringes, IV bags, tubing, and medical packaging. With the ability to work with materials like polypropylene, polyethylene, and polycarbonate, these services ensure that each product meets the specific requirements for strength, safety, and sterility. The use of medical plastic molding is particularly important in producing single-use devices, which are designed to minimize contamination risks and ensure patient safety. By partnering with a reliable medical plastic molding trader, companies can access high-quality materials and advanced manufacturing solutions, ensuring cost-effective production and timely delivery. Adhering to strict manufacturing standards, medical plastic molding services help to deliver high-quality, cost-effective solutions for the healthcare industry.
Medical Molding Services:Why Medical Molding is Crucial for the Healthcare Industry
High-Precision Manufacturing
Medical molding services are vital to the healthcare industry because they ensure that medical products meet the highest standards of precision and reliability. Medical products, such as surgical instruments, implants, and pharmaceutical packaging, must adhere to strict regulatory standards, such as those set by the FDA and ISO 13485. These regulations guarantee that medical components are safe for patient use, effective, and free from defects. Molding techniques like injection molding, compression molding, and blow molding are capable of producing parts with exceptional accuracy and consistency, meeting these rigorous standards. High-precision medical molding manufacturing is particularly critical for parts like syringes, surgical implants, and medical connectors, where even the smallest deviation could impact their functionality and safety.
Material Efficiency & Sustainability
Another key benefit of medical molding services is material efficiency and sustainability. With growing concerns about environmental impact, many companies are prioritizing eco-friendly manufacturing practices. These companies strive to minimize material waste and ensure that excess materials are recycled. The use of recyclable materials such as polypropylene, polyethylene, and medical-grade silicones not only reduces waste but also makes the production process more sustainable. Additionally, the ability to recycle materials means that manufacturers can maintain a cost-effective production process without compromising product quality. Sustainable practices in medical molding help reduce the environmental footprint of the healthcare industry, which is crucial as demand for medical products continues to grow.
Versatility and Customization
Medical molding services offer exceptional versatility and customization options, which are essential for creating medical products that cater to specific needs. Whether producing simple components like medical caps or complex parts such as drug delivery systems and diagnostic tools, medical molding services provide tailored solutions for each project. Advanced molding techniques, such as two-shot molding and overmolding, allow manufacturers to combine multiple materials into a single part, enhancing functionality and usability. This flexibility allows medical companies to create custom-designed parts that meet the unique specifications of each medical application. Whether for high-volume production or one-off prototypes, medical molding services ensure that healthcare products can be designed to meet exacting requirements for performance, durability, and sterility.
Medical Molding Services:Technologies and Innovations in Medical Molding
Injection Molding for Medical Devices
One of the most significant technologies in medical molding services is high-precision injection molding. This technique ensures that medical components are produced with exceptional accuracy, durability, and sterility—essential qualities for devices that will be used in critical medical environments. For example, OEM medical injection molding allows manufacturers to create parts with intricate details and tight tolerances, ensuring that products like syringes, implants, and medical connectors are not only functional but also meet strict regulatory standards, including those set by the FDA and ISO 13485. In some cases, metal injection molding medical is used to achieve even greater precision and strength, particularly for components that require enhanced mechanical properties. Advanced materials like PEEK (Polyetheretherketone), polypropylene, silicone, and polycarbonate are often used in medical injection molding because of their superior mechanical properties, biocompatibility, and resistance to wear, making them ideal for medical devices that must withstand harsh conditions and provide reliable performance over time.
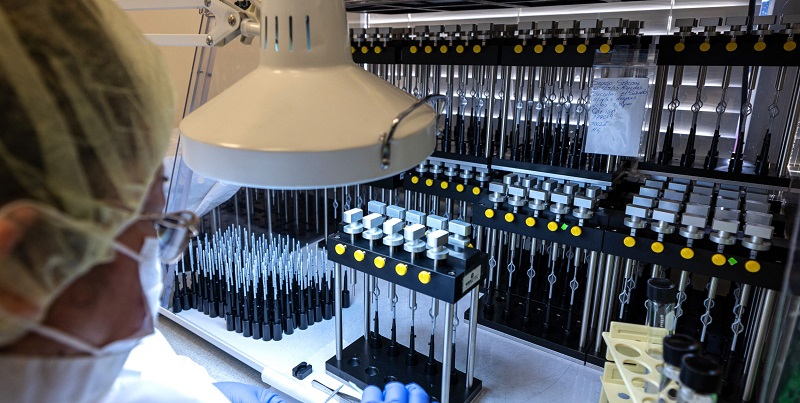
Cleanroom Molding
Cleanroom molding is another important innovation in medical molding services. In the medical industry, the sterility of products is paramount, particularly for devices like syringes, IV bags, and surgical instruments. To ensure that the molding process remains free from contaminants, manufacturers often use controlled environments, such as ISO Class 7 or Class 8 cleanrooms, during the production of medical components. These cleanrooms maintain strict air quality controls to minimize the presence of particulates that could compromise the sterility of medical products. Medical components precision cleaning is often integrated into the molding process to further ensure that all components are free from residues, oils, and particles that could affect their performance or safety. Medical molding services that utilize cleanroom facilities are crucial for ensuring the highest levels of cleanliness and quality control, which is vital in preventing infections or complications during medical procedures. The use of cleanroom environments allows manufacturers to produce medical products that are free from contaminants and meet the stringent requirements for safety and quality in the healthcare industry.
Two-Shot & Overmolding
Advanced molding techniques like two-shot molding and overmolding are revolutionizing the production of complex medical devices. These methods allow for the creation of multi-material products that offer enhanced functionality and performance. In two-shot molding, two different materials are injected into a single mold at different stages to create a single part with integrated features, such as medical devices with built-in grips, seals, or ergonomic components. Overmolding, on the other hand, involves adding a secondary material over an existing part, enhancing its durability or adding extra functionality. These techniques are particularly useful for medical products like drug delivery systems, surgical tools, and diagnostic devices that require multiple materials for enhanced performance. By using two-shot molding and overmolding, medical molding services can create more innovative, durable, and user-friendly medical components, meeting the increasing demand for complex and functional healthcare solutions.
Applications of Medical Molding Services
Common Products Manufactured
Medical molding services are integral to the production of a wide range of critical medical devices and components. Some of the most common products manufactured using these services include surgical instruments, knee and hip implants, syringes, specimen cups, medical packaging, and diagnostic equipment. Precision in molding is essential for the production of these items, as they often require exact specifications and high levels of durability. Surgical instruments, for example, need to be finely crafted to ensure safety and functionality during operations, while knee and hip implants must be designed for long-term performance and biocompatibility. Medical molding services also play a vital role in producing packaging for pharmaceuticals and medical devices, which must comply with regulatory standards to ensure safety and sterility. The versatility of molding technologies enables manufacturers to meet the diverse and demanding needs of the healthcare industry, producing both simple and complex components that contribute to better patient care.
Pharmaceutical Applications
- Production of Pharmaceutical Packaging: Medical molding services play a vital role in the manufacturing of pharmaceutical packaging, including components like bottles, vials, blister packs, closures, and caps. These packaging items are essential for protecting and containing medications while ensuring their safety during storage and transportation.
- Injection Molding in Pharmaceutical Applications: The pharmaceutical industry relies heavily on injection molding to produce high-quality packaging components. This process is particularly useful for creating closures and caps, which are critical for maintaining the integrity of pharmaceutical products. Injection molding allows for the production of precise, durable parts that can meet stringent industry standards.
- Ensuring Safety and Integrity: Components such as closures and caps produced through medical molding services must provide airtight or tamper-proof seals. This is essential to protect pharmaceutical products from contamination, moisture, or degradation. These components help ensure that the medication remains safe and effective throughout its shelf life.
- Complex Shapes and High-Volume Production: Medical molding services enable manufacturers to create a wide range of complex shapes and sizes needed for various pharmaceutical applications. This flexibility is especially important for meeting the demands of high-volume production while maintaining the precision required for pharmaceutical packaging.
- Material Versatility: With the ability to work with a variety of materials, such as medical-grade plastics, medical molding services help produce pharmaceutical packaging that meets the strict regulatory and quality standards of the healthcare industry. The use of these materials ensures that the packaging can withstand sterilization and environmental factors, further enhancing the safety of pharmaceutical products.
Personal Protective Equipment (PPE)
The scope of medical molding services also extends to the production of personal protective equipment (PPE), including masks, face shields, and gloves. During times of high demand, such as the COVID-19 pandemic, the ability to produce large quantities of PPE quickly and efficiently becomes crucial. Medical molding services support the healthcare sector by providing rapid, scalable production of these protective items, ensuring that healthcare professionals and patients have the necessary protection to prevent the spread of infections. The use of injection molding for PPE allows for the creation of high-quality, durable products designed to meet safety standards. Whether producing face shields for frontline workers or surgical gloves for sterile environments, medical molding services help ensure that critical protective gear is available when it’s most needed, contributing to overall public health and safety.
The Importance of MedAccred Certification for Medical Molding Services
What is MedAccred Certification?
MedAccred certification is an industry-recognized accreditation program designed to ensure strict compliance with quality and process standards for critical manufacturing operations, particularly in the medical device sector. It evaluates and certifies manufacturers based on their ability to meet stringent requirements for safety, consistency, and reliability in medical production.
Why is MedAccred Certification Important?
For medical molding services manufacturers, MedAccred certification is a vital benchmark of quality and trustworthiness. It ensures compliance with strict process and product standards, thereby improving product quality and reducing recalls or warranty claims. Certification also strengthens supply chain efficiency by streamlining supplier selection and enhancing overall reliability. Most critically, MedAccred certification helps reduce patient risks and limits OEM liability and litigation risks, offering a safeguard for both manufacturers and healthcare providers. This level of assurance is essential for delivering high-quality medical components that meet regulatory and patient safety demands.
Guide to Medical Grade Materials Used in Medical Molding Services
Medical molding services rely on a variety of high-performance materials to meet the unique requirements of medical devices and components. Each material offers specific properties that make it suitable for different applications in the medical industry.
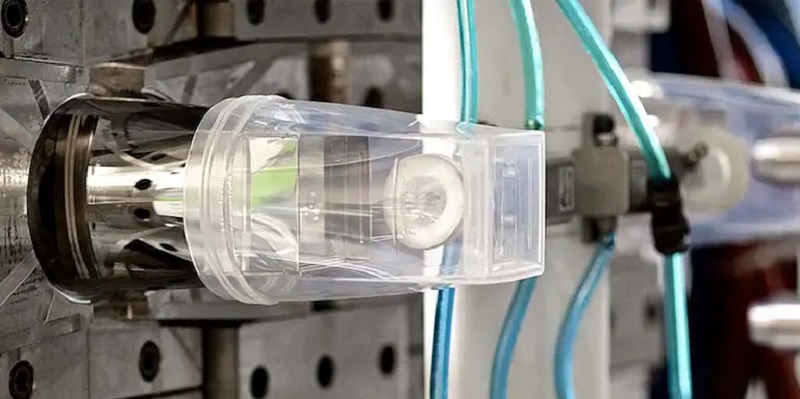
Medical Grade Materials Used in Medical Molding Services
- ABS (Acrylonitrile Butadiene Styrene):
A strong, impact-resistant material, ABS is widely used for durable medical devices such as housings, enclosures, and handheld tools due to its strength and ease of molding. - POM (Polyoxymethylene):
Known for its excellent stiffness and low friction, POM is ideal for precision parts like gears, valves, and drug delivery components. - PMMA (Acrylic):
Offering superior clarity and biocompatibility, PMMA is commonly used for lenses, light guides, and transparent medical components. - LCP (Liquid Crystal Polymer):
LCP provides exceptional strength, chemical resistance, and dimensional stability, making it suitable for micro-molded components used in minimally invasive surgeries. - LSR (Liquid Silicone Rubber):
This material is flexible, biocompatible, and resistant to sterilization processes, making it ideal for seals, gaskets, and implantable devices. - PA (Nylon):
With excellent mechanical strength and chemical resistance, PA is often used in surgical instruments and structural medical parts. - PC (Polycarbonate):
PC is known for its toughness, transparency, and impact resistance, making it suitable for diagnostic equipment, syringes, and housings. - PBT (Polyester):
PBT offers durability and high heat resistance, often used in applications like catheter components and connectors. - PET (Polyethylene Terephthalate):
With excellent barrier properties, PET is commonly used for sterile packaging and fluid delivery systems. - PUR (Polyurethane):
A highly flexible material, PUR is frequently used in tubes, cushions, and wearable medical devices. - TPU/TPE (Thermoplastic Polyurethane/Elastomer):
Offering elasticity, durability, and biocompatibility, TPU/TPE is ideal for flexible medical components like tubing and catheters. - PEEK (Polyetheretherketone):
A high-performance material with exceptional chemical resistance and biocompatibility, PEEK is used for implantable devices and surgical instruments. - PEI (Ultem):
PEI is a high-strength, heat-resistant material often used in sterilization trays and reusable medical devices. - PPE+PS (Polyphenylene Ether – Noryl):
Known for its dimensional stability and chemical resistance, this material is often used in diagnostic and laboratory equipment.
Selection Considerations for Medical Grade Plastics
When selecting medical-grade materials for medical molding services, the following factors should be considered:
- Strength:
Ensure the material provides the required mechanical strength to support the application, such as structural integrity for surgical instruments or durable housings. - Industry Standards:
The material must comply with FDA regulations and other medical industry standards to ensure safety and efficacy. - Operating Conditions:
Evaluate the environmental conditions the material will endure, such as exposure to chemicals, sterilization methods, or extreme temperatures. Materials like PEEK or LCP are ideal for harsh environments. - General Use:
Assess the intended function of the device. For instance, surgical tools should be lightweight and ergonomic, while disposable drug delivery systems require flexibility, transparency, and cost-effectiveness.
By understanding the unique properties of each material and carefully evaluating application-specific requirements, manufacturers can optimize their medical molding services to produce reliable, high-quality medical devices.
Detailed Process of Medical Molding Services for Manufacturing Medical Components
Medical molding services involve a series of well-coordinated steps to ensure high-quality and precision manufacturing of medical components. Each stage is crucial, requiring meticulous planning and execution. Below is a detailed overview of the process:
Product Development and Design
Description:
The process begins with in-depth product research and analysis to optimize the product’s structure and functionality. A reasonable production plan is devised, ensuring the design aligns with manufacturing capabilities and medical application requirements. Custom tools and molds are created based on the product specifications.
Precautions:
- Ensure the design meets regulatory standards like FDA and ISO.
- Involve cross-functional teams for accurate design validation.
- Prioritize functionality and manufacturability during structural optimization.
3D Prototype Injection Molding
Description:
A 3D prototype is created to provide a tangible representation of the design. Feedback is collected, and modifications are made until the customer is satisfied with the prototype.
Precautions:
- Use materials that closely simulate the final product’s properties.
- Thoroughly review the prototype for flaws in design or functionality.
- Confirm all critical dimensions and tolerances before moving to production.
Material Selection
Description:
Experts recommend suitable and economical medical-grade plastics based on the product’s intended use, operating environment, and regulatory compliance requirements.
Precautions:
- Consider biocompatibility, durability, and sterilization resistance.
- Evaluate the material’s suitability for specific medical applications, such as disposable or reusable components.
- Ensure compliance with FDA and ISO standards for medical plastics.
Mold Manufacturing
Description:
Using high-quality steel and advanced equipment, experienced mold manufacturers produce durable, high-precision molds designed to meet production requirements.
Precautions:
- Use high-grade steel to ensure mold longevity and precision.
- Test molds rigorously to identify potential defects early.
- Maintain strict tolerances to ensure the mold produces consistent parts.
Medical Plastic Injection Molding
Description:
Approved prototypes and selected materials are used to produce medical-grade components through plastic injection molding. The process is carried out efficiently to meet the agreed delivery timeline.
Precautions:
- Conduct machine setup checks to avoid defects in production.
- Monitor process parameters such as temperature, pressure, and cycle time.
- Implement in-process quality inspections to ensure consistency.
Secondary Processing
Description:
Additional operations, such as machining, ultrasonic cleaning, liquid filling and sealing, and shrink packaging, are performed to complete the product.
Precautions:
- Ensure cleanliness during all secondary operations, especially for sterile medical devices.
- Validate each secondary process step to prevent contamination or damage.
- Package products according to medical industry standards to maintain sterility and integrity.
By following these detailed steps and adhering to necessary precautions, medical molding services ensure the production of high-quality, reliable medical components that meet stringent industry standards and customer expectations.
FAQs about Medical Molding Services
Medical molding is the process of creating precise and specialized components for medical devices, pharmaceutical packaging, and other healthcare products using molding techniques. This process is crucial in the healthcare industry due to its ability to produce high-quality, sterile, and compliant products. Medical molding services are used for manufacturing a wide range of items, such as syringes, knee implants, IV bags, and medical packaging. The process ensures that components are made with strict adherence to regulatory standards, such as FDA guidelines, to guarantee the safety and effectiveness of the final product. Medical molding typically involves techniques like injection molding, blow molding, compression molding, and overmolding. Each of these methods has specific applications depending on the type of medical product being manufactured. Additionally, medical molding requires the use of medical-grade materials, such as polycarbonate, silicone, and polypropylene, to meet the stringent requirements for biocompatibility, durability, and resistance to sterilization processes.
In medical terms, molding refers to the process of shaping or forming objects, typically used in the context of creating medical devices, equipment, or prosthetics. It can also refer to the technique used to manufacture medical components, ensuring they meet the strict specifications necessary for patient safety and treatment effectiveness. Molding in the medical field requires careful attention to detail and precision, as even small deviations can lead to complications in the use of the devices. In addition to manufacturing medical products, “molding” in a clinical context may also refer to the formation of body parts during certain medical treatments. For example, when a cast is applied to a fractured limb, it “molds” to the shape of the limb to provide support during healing. Furthermore, molding is an essential process in the development of customized medical products such as prosthetics, where the shape must be tailored to an individual patient’s anatomy.
Molding in pharmacy refers to the process of creating molds for pharmaceutical packaging or drug delivery systems. The technique is used to form precise shapes and structures necessary for storing, dispensing, and delivering medications. Common applications of molding in the pharmaceutical industry include the production of blister packs, vials, medical closures, and other components used in drug packaging. The molding process ensures that these components meet strict industry standards for safety, contamination prevention, and sterility. The molds used in pharmaceutical applications are designed to preserve the integrity of medications, protect them from external factors like moisture and air, and ensure that drugs remain effective until their expiration date. Molding in pharmacy can involve various materials, including high-quality plastics, which are selected based on their compatibility with medications and their ability to withstand sterilization processes like autoclaving. These materials must meet rigorous regulatory requirements to ensure that they do not affect the quality or safety of the drugs contained within.
The three main types of molding used in manufacturing are injection molding, blow molding, and compression molding.
Injection Molding: This is the most commonly used molding technique, especially in the medical industry. In injection molding, melted plastic is injected into a mold cavity under high pressure, where it cools and solidifies into the desired shape. This process is ideal for producing precise, complex parts like syringes, surgical instruments, and other medical devices. It is known for its ability to produce high volumes of consistent products with tight tolerances.
Blow Molding: Blow molding is used primarily for creating hollow objects like bottles and containers. In this process, air is blown into a tube of molten plastic inside a mold, expanding it to the shape of the mold. Blow molding is used to produce items such as medical bottles and containers, often used in pharmaceutical packaging.
Compression Molding: Compression molding is used for large-scale items that require more significant size and durability. In this method, plastic is placed into an open mold, and a second mold is pressed down to shape the material. Compression molding is often used for medical equipment components like seals and gaskets, as well as larger items like surgical trays or components of medical furniture. Each molding method has specific applications in the medical industry, offering different benefits based on the requirements of the product being manufactured.
Injection molding for medical applications costs approximately $50 to $150 per hour, depending on several factors. These include machine size, material selection, and the complexity of the medical part being manufactured. Medical molding services often require high precision, cleanroom environments, and specialized materials, such as biocompatible or medical-grade plastics. These added requirements increase operational costs compared to general industrial molding. Additionally, tool maintenance and compliance with regulatory standards, such as ISO 13485, further contribute to the higher hourly rates in medical molding. Costs can escalate when producing complex parts like surgical tools or implantable devices due to stringent quality controls. However, with advancements in technology, efficient automation and optimized processes can help manage costs over the long term, particularly in high-volume production scenarios.
Injection molding for medical applications can be highly profitable when operations are optimized and targeted at niche markets requiring specialized components. The profit margin depends on factors like the complexity of the molded medical parts, material costs, and the scale of production. Medical molding services often command higher prices due to the need for precision, compliance with regulatory standards, and cleanroom manufacturing. While initial investment in high-quality molds and equipment is substantial, these tools often last for millions of cycles, spreading costs over high-volume production. Companies specializing in medical molding frequently focus on critical, high-demand items like drug delivery systems, diagnostic equipment components, or implantable devices. High-quality production paired with strong relationships in the healthcare industry can make injection molding a sustainable and lucrative business, provided manufacturers remain agile in responding to evolving medical technology and regulatory standards.
Numerous companies specialize in injection molding for medical applications, ranging from large, multinational firms to specialized niche manufacturers. These companies often operate in cleanroom facilities to meet stringent healthcare standards. Examples include those that produce parts for surgical instruments, drug delivery devices, and diagnostic equipment. Key players typically emphasize compliance with certifications like ISO 13485 for medical device manufacturing. In addition to producing custom components, many companies offer design consultation, material selection, and prototyping services tailored to medical needs. When choosing a provider, it’s critical to assess their expertise in medical-grade plastics, biocompatibility, and adherence to healthcare industry regulations. Companies with advanced technologies, such as micro-molding or overmolding for medical devices, often stand out in this specialized market.
Injection molding is a rewarding career, particularly in the medical sector, where precision manufacturing has a tangible impact on healthcare. Careers in this field range from machine operation and mold design to quality assurance and engineering. Those working in medical molding services often enjoy opportunities to work with cutting-edge technologies, such as micro-molding and bioresorbable materials. Given the healthcare industry’s growth, skilled professionals in medical injection molding are in high demand. With the right training, individuals can pursue paths in mold-making, process optimization, or project management. Salaries are competitive, especially for specialists with expertise in cleanroom manufacturing or regulatory compliance. Furthermore, the industry offers opportunities for continuous learning, innovation, and advancement, making it an attractive long-term career choice for technically inclined individuals.
In some medical applications, alternatives like additive manufacturing (3D printing) or thermoforming may be better than injection molding, depending on the project’s specific requirements. For low-volume production, prototypes, or highly complex geometries, 3D printing offers significant advantages, including faster lead times and lower upfront costs. Thermoforming, on the other hand, can be more cost-effective for producing large, thin-walled parts such as medical trays or enclosures. Compression molding and liquid silicone rubber (LSR) molding are other viable options for certain medical applications, particularly when flexibility or unique material properties are required. However, injection molding remains the gold standard for high-volume, precision manufacturing due to its efficiency and repeatability. Choosing an alternative depends on the production scale, material needs, and part complexity, but for most medical components, injection molding’s precision and scalability make it the preferred choice.
Injection molding for medical applications is expensive due to the high precision and regulatory requirements involved. The cost of molds, often made of durable steel or aluminum, can range from $10,000 to over $100,000, depending on complexity. In medical molding, additional costs arise from using biocompatible or medical-grade plastics and operating in cleanroom environments to ensure contamination-free production. Compliance with stringent healthcare standards, such as FDA regulations and ISO certifications, further increases costs due to added documentation, testing, and quality assurance measures. Moreover, the design and engineering of molds for medical parts often involve significant time and expertise to ensure flawless performance over millions of cycles. While expensive, these investments ensure the reliability and safety of medical components, which are critical in healthcare settings. Over time, high-volume production helps offset initial costs, making injection molding a cost-efficient solution for large-scale manufacturing.
Contact our professional team now for a same-day quote and risk-free project evaluation. Benefit from ISO 8 cleanrooms, advanced machines, and 12-hour fast response in medical injection molding.