Molding plays a crucial role in the medical device industry by enabling the production of complex, high precision medical components essential for patient safety and device performance. Medical molding solutions are designed to meet stringent regulatory standards while providing the durability and functionality required in critical healthcare applications. These solutions utilize advanced molding techniques to create reliable, consistent, and cost-effective medical devices, from implants to diagnostic tools. Whether it’s the creation of surgical instruments or life-saving medical equipment, medical molding solutions ensure that each product is crafted to the highest standards of quality. By leveraging innovations in materials and molding technologies, these solutions help the medical industry maintain reliability, safety, and efficiency in device manufacturing. Medical molding solutions create durable, precise devices with advanced technologies, including cleanroom, two-color, and DNA-free injection molding.
Low-Volume to High-Volume Production Capabilities
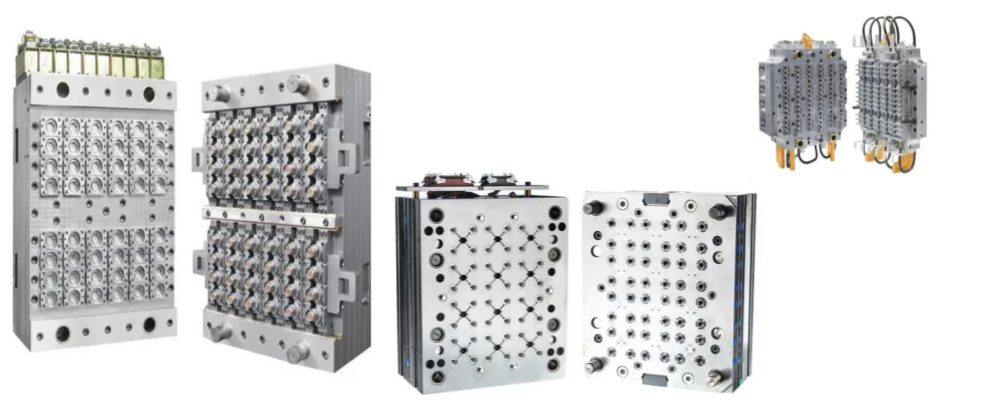
Attribute | Details |
---|---|
Product Name | Medical Molding |
Shaping Mode | Plastic Injection Molding |
Place of Origin | Dongguan, Guangdong, China |
Brand Names | LY Medical Injection Mold |
Product Materials | ABS, PC, PP, PA, PMMA, TPU, TPE, POM, PS, PVC, Nylon |
Mold Materials | P20, 718, NAK80, S316, German and Japan import steel |
Cavity Options | Single Cavity, Multi Cavity |
Runner System | Hot Runner, Cold Runner |
Mold Life | 100K-500K shots |
Precision | Up to 0.005mm |
Applications | Medical devices, digital blood pressure monitors, syringes, medical shells |
Key Features | High-precision molding, fast mold design, customizable mold colors and sizes, efficient production, multi-material compatibility, custom gate types (side gate, pin-point gate, etc.) |
Surface Treatment | Polishing |
Delivery Methods | DHL, FedEx, Shipping |
Injection Rate | 67.7 g/s (varies by model) |
Screw Speed | 1–190 rpm |
Warranty | 2 year (machine and core components) |
Certification | ISO 9001:2008 |
What Are Medical Molding Solutions?
Medical molding solutions refer to the advanced manufacturing techniques used to create components and devices for the healthcare industry. These solutions are essential in producing high-precision, high-performance medical devices that meet the strict regulatory standards for safety and effectiveness. Precision mold medical techniques are often employed within these solutions to ensure the production of highly accurate and customized components, which is critical for devices used in complex medical applications. Medical molding solutions encompass a variety of molding processes, such as injection molding, compression molding, and micro molding, each tailored to specific device requirements.
In the medical field, molding solutions ensure the production of everything from small, intricate parts like catheters and syringes to larger, more complex components like implants and surgical tools. These solutions use medical-grade materials, which are tested for biocompatibility and durability, ensuring the devices will perform reliably in critical environments. Medical molding solutions also focus on optimizing production efficiency, minimizing waste, and ensuring the scalability needed for large production volumes.
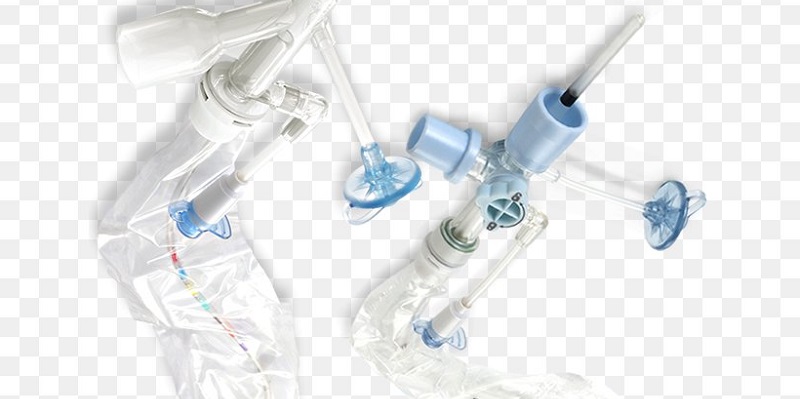
By integrating cutting-edge molding technologies, medical molding solutions play a pivotal role in the creation of devices that are both safe for patients and cost-effective for manufacturers. Whether it’s for a custom-made prosthetic or a mass-produced diagnostic tool, medical molding solutions make it possible to meet the evolving needs of the medical industry with precision and reliability.
Medical Molding Solutions: Key Molding Processes in Medical Device Manufacturing
In plastic medical device manufacturing, various molding processes are used to create high-quality, precise components essential for the functionality and safety of medical devices. The choice of molding process depends on factors such as material, part complexity, production volume, and regulatory requirements. Medical molding solutions include several key molding techniques, each tailored to different types of medical devices and components.
SMC Molding Process
The Sheet Molding Compound (SMC) process is commonly used in the production of strong, lightweight parts for medical devices. SMC molding is ideal for creating large, intricate parts that require high strength and durability, such as housings for medical equipment or structural components in prosthetics. The process involves using a composite material made of resin, fiber, and other additives, which are molded under heat and pressure. SMC molding solutions offer excellent dimensional stability and resistance to chemical and environmental factors, making them ideal for critical medical applications.
SMC Injection Molding
SMC injection molding is another vital process in medical molding solutions, often employed for producing complex parts with high precision. In this method, pre-compounded SMC materials are injected into molds under controlled pressure and temperature. This process allows for the efficient production of high-quality parts with tight tolerances, making it suitable for small to medium-volume runs of medical precision components like connectors, valve components, and housings for diagnostic equipment. The process ensures uniform material distribution and can be adapted to create parts with intricate designs or fine details.
SMC Micro Molding
Smc micro molding is an advanced molding technique used for producing extremely small, highly detailed medical parts, such as micro connectors, miniature sensors, and small surgical instruments. This process is particularly important in the development of devices used in minimally invasive procedures, where precision and reliability are paramount. Smc micro molding solutions enable the production of intricate components with tight tolerances, often in the range of micrometers, using specialized molding equipment designed for very small cavities and delicate materials. This technique ensures that small-scale medical devices perform reliably in critical applications.
Medical Plastic Molding Solutions
Medical plastic molding solutions are widely used in the production of a vast range of medical devices, including syringes, catheters, and diagnostic equipment. The use of medical-grade plastics ensures that products are durable, biocompatible, and resistant to harsh sterilization processes. Medical plastic molding solutions utilize various molding techniques, such as injection molding and compression molding, to produce consistent and high-quality plastic components. The ability to mold plastics into complex shapes and designs allows manufacturers to produce lightweight, cost-effective medical devices while maintaining the highest safety standards.
These molding processes, including SMC and medical plastic molding solutions, play an essential role in the creation of reliable, high-performance medical devices. Whether it’s a simple component or a complex assembly, medical molding solutions ensure that devices are made to stringent standards of safety, precision, and durability.
Types of Medical Molding Solutions
Medical molding solutions are diverse and tailored to meet the specific needs of the healthcare industry. These solutions use different molding techniques to create a wide variety of medical components, from micro-sized parts to large, complex assemblies. The type of medical injection molding process chosen depends on the material requirements, the complexity of the design, and the desired production volume. Each type of molding solution is designed to optimize the functionality, durability, and performance of the end product while adhering to strict regulatory standards.
SMC Injection Molding
SMC injection molding is a versatile medical molding solution widely used for producing durable, high-strength components. This process involves injecting a preheated sheet molding compound into a mold cavity, where it is formed into the desired shape. SMC injection molding is ideal for producing parts that require both high strength and low weight, such as casings for medical devices or components that need to withstand harsh environments.
Micro Molding
Medical micro molding is a specialized form of injection molding used to create extremely small and intricate medical device components. This process is essential for producing micro-scale parts like medical connectors, microfluidic devices, and precision surgical instruments. Micro molding requires highly precise equipment and techniques to achieve tolerances as tight as a few microns, making it a crucial solution for many advanced medical applications.
Compression Molding
Compression molding is another type of medical molding solution used for making large, solid medical components. It involves placing a preheated material into a mold cavity, where it is compressed under heat and pressure to form the final part. This process is commonly used for producing rubber seals, gaskets, and other components that require flexibility and durability.
Overmolding
Overmolding is a process that involves molding one material over another to create a composite part with enhanced properties. In the medical field, overmolding is often used to create handles for surgical instruments or to add soft-touch features to medical device components. This solution allows manufacturers to combine materials with different properties, such as rigid and flexible polymers, to meet the unique needs of the device.
These various types of medical molding solutions, including extrusion molding medical not mentioned, play a critical role in ensuring that medical devices are safe, reliable, and able to perform as intended in critical healthcare environments. Whether producing a tiny, high-precision part or a larger, multi-material component, these advanced molding solutions provide the necessary functionality and durability required in medical device manufacturing.
Medical Molding Solutions: Medical Plastic Molding Solutions in Detail
Medical plastic molding solutions are crucial in the production of high-precision medical components that meet the rigorous standards of the healthcare industry. These solutions are versatile and cost-effective, enabling the creation of medical devices ranging from simple components like syringes to complex systems such as surgical instruments and diagnostic tools. Medical plastic molding solutions ensure that the materials used in the manufacturing process comply with the necessary regulations, such as biocompatibility and durability. Various molding techniques are employed depending on the complexity and function of the device, optimizing production efficiency, and maintaining high-quality standards.
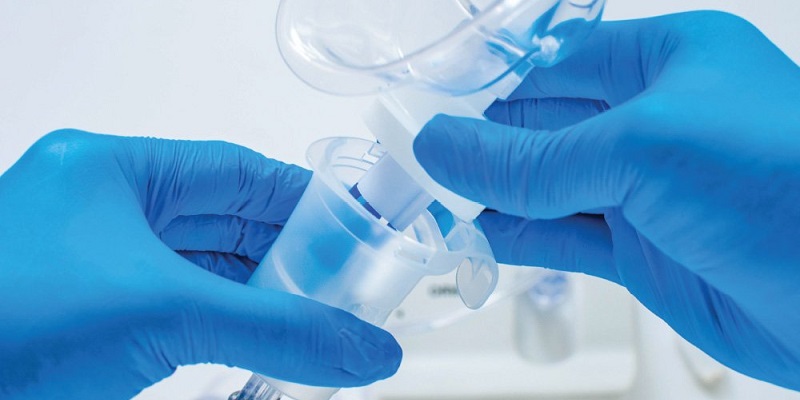
Key Benefits of Medical Plastic Molding Solutions
- Precision and Consistency: Medical plastic molding solutions allow for highly accurate production, ensuring that each part meets strict design specifications with minimal variation.
- Cost-Effectiveness: These solutions enable large-scale production at lower costs, making it easier to meet the high demand for medical devices while maintaining quality.
- Biocompatibility: Medical plastic molding solutions use materials that are biocompatible, ensuring the safety of the device when it interacts with the human body.
- Design Flexibility: The molding processes allow for intricate designs and complex geometries, making them ideal for medical devices that require fine details and tight tolerances.
Medical Plastic Molding Techniques
- Injection Molding: This widely used technique involves injecting molten plastic into a mold cavity under high pressure. It is ideal for producing complex, precise parts with high consistency. Commonly used for syringes, connectors, and housings for medical devices.
- Compression Molding: This technique is used for creating medical components that need to maintain high strength and durability, such as medical equipment housings or large structural parts.
- Extrusion Molding: Extrusion molding is used to produce continuous shapes like tubes, rods, or profiles used in medical applications such as catheters or medical tubing.
- Blow Molding: This method is used for hollow parts such as bottles or blood bags, where the plastic is inflated within a mold to create the desired shape.
Challenges in Medical Plastic Molding Solutions
- Material Selection: The choice of materials is critical, as they must meet stringent requirements for medical use, such as biocompatibility, chemical resistance, and strength.
- Tooling and Mold Design: Creating molds for medical plastic components is a time-consuming and expensive process, especially for highly intricate or custom designs.
- Regulatory Compliance: Medical molding solutions must comply with strict regulatory standards, such as ISO 13485, ensuring the products meet quality and safety standards.
- Production Scalability: Maintaining quality while scaling up production to meet large-volume demands without compromising on precision and performance.
These factors contribute to the overall effectiveness of medical plastic molding solutions, making them a key component of modern medical device manufacturing.
The Future of Medical Molding Solutions
The future of medical molding solutions is poised for innovation, driven by advancements in technology, materials, and manufacturing processes. As the healthcare industry continues to evolve, medical molding solutions will play a critical role in addressing the growing demand for more personalized, efficient, and cost-effective medical devices. These solutions are not only becoming more advanced but also more adaptable to emerging trends in medical technology, such as 3D printing and micro-manufacturing.
Key Factors Shaping the Future of Medical Molding Solutions
- Advances in Material Science: The development of new medical-grade materials, such as biocompatible plastics and biodegradable polymers, will expand the range of medical molding solutions. These materials will allow for safer, more sustainable medical devices.
- Increased Automation and AI Integration: The integration of artificial intelligence (AI) and robotics into the molding process will enhance precision, improve production speed, and reduce human error, making manufacturing even more efficient.
- Customization and Personalization: With the rise of personalized medicine, medical molding solutions will enable the production of custom medical devices tailored to individual patient needs, such as patient-specific implants and prosthetics.
- Sustainability Initiatives: As sustainability becomes a higher priority in the healthcare sector, medical molding solutions will incorporate eco-friendly practices, including the use of recyclable materials and energy-efficient production methods.
The Role of FUJIU Medical Injection Mold in Advancing Future Molding Solutions
At FUJIU Medical Injection Mold, we are a third-generation, employee-owned company with over 20 years of experience in providing OEM contract manufacturing for the medical device industry. We focus on innovation, quality, and collaboration, and our high-precision production of plastic consumables drives the advancement of the industry.
We are committed to pushing forward future molding solutions, particularly in the following key areas:
- Integration of Advanced Technologies: We are incorporating cutting-edge technologies such as automation, robotics, and digitalization through IoT and AI to enhance precision and increase production efficiency.
- Customization and Design Flexibility: By leveraging these technologies, we offer unique packaging solutions that can quickly adapt to evolving consumer demands, providing a higher level of brand differentiation.
- Sustainability Initiatives: We prioritize sustainable practices in our molding projects, including the use of eco-friendly materials and energy-efficient production processes to meet the growing demand for green manufacturing in the market.
- Collaboration and Partnerships: We actively engage in partnerships with other companies and institutions, sharing knowledge, expertise, and resources to develop new technologies and processes. This collaboration accelerates innovation and enhances product quality.
The Evolution of Expertise in Medical Molding Solutions
Expertise in medical molding solutions has evolved significantly over the years, driven by advancements in technology, regulatory demands, and the increasing complexity of medical devices. This evolution can be broken down into several key phases:
Early Development: Basic Molding Techniques
In the early stages, medical molding relied on basic injection molding techniques originally developed for industrial applications. These methods were adapted to produce simple medical products, such as syringes and basic surgical instruments.
- Materials: General-purpose plastics were used, with minimal consideration for biocompatibility.
- Challenges: Limited precision and a lack of advanced quality controls hindered the production of intricate medical devices.
Introduction of Medical-Grade Materials
The development of medical-grade materials, such as biocompatible plastics and silicone, marked a turning point. These materials met stricter safety and performance standards, enabling the production of implants, catheters, and other devices.
- Key Advancements: Use of ISO 10993 and FDA-compliant materials.
- Impact: Allowed manufacturers to produce parts that could safely interact with the human body.
Incorporation of Advanced Injection Molding Technologies
Technological innovations brought precision and versatility to medical molding:
- Multi-Cavity Molding: Enabled high-volume production while maintaining consistent quality.
- Micro-Molding: Allowed for the creation of tiny components for applications like microfluidics.
- Two-Color Molding: Facilitated the integration of multiple materials into a single part, expanding design possibilities.
Cleanroom Manufacturing and Stringent Quality Controls
To meet the healthcare industry’s need for contamination-free products, cleanroom manufacturing became a standard.
- Facilities: Controlled environments with ISO-classified cleanliness levels.
- Practices: Implementation of DNA-free injection molding to prevent contamination in sensitive applications, such as diagnostic tools.
Digital Integration and Rapid Prototyping
Recent years have seen a shift towards digital technologies:
- Computer-Aided Design (CAD): Enhances the precision of mold design.
- Simulation Software: Predicts material flow and reduces defects.
- 3D Printing: Accelerates prototyping, enabling faster design iterations.
Focus on Sustainability and Cost Efficiency
Modern medical molding solutions emphasize reducing waste and optimizing production:
- Recyclable Materials: Incorporating eco-friendly materials.
- Process Efficiency: Automation and lean manufacturing reduce costs and improve output.
The expertise in medical molding solutions has evolved into a highly specialized field, blending material science, advanced manufacturing, and regulatory compliance to produce innovative and reliable medical devices.
Measures Taken by Medical Molding Solutions to Ensure Product Consistency
Ensuring product consistency is critical in medical molding solutions, as even minor deviations can compromise the safety and effectiveness of medical devices. To achieve this, advanced measures are implemented throughout the manufacturing process, focusing on material quality, precision manufacturing, and stringent quality control.
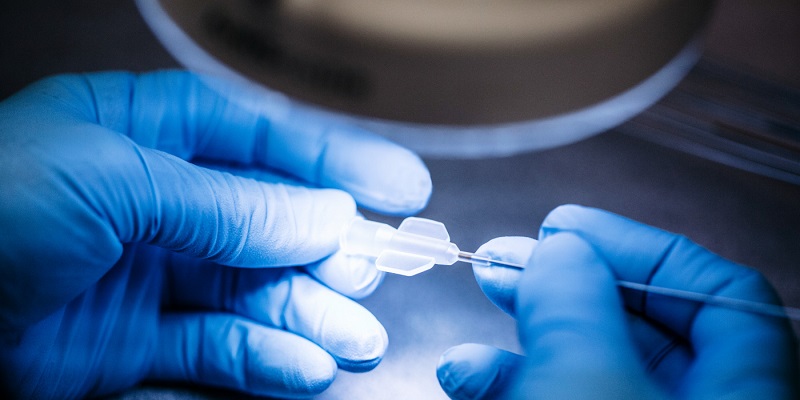
Material Selection and Verification
Medical molding begins with the use of high-quality, biocompatible materials that meet regulatory standards such as ISO 10993 and USP Class VI. Consistency in raw materials is ensured through:
- Supplier Audits: Vetting suppliers to ensure consistent material quality.
- Batch Testing: Verifying that each batch of materials adheres to specifications.
Precision Mold Design and Manufacturing
Consistency starts with precision mold design:
- Computer-Aided Design (CAD): Creates accurate mold designs that meet tight tolerances.
- CNC Machining: Produces molds with exact specifications, ensuring uniformity across production runs.
- Multi-Cavity Molds: Designed to ensure each cavity produces identical parts, even in high-volume production.
Controlled Manufacturing Environment
Cleanroom production is a standard in medical molding solutions to minimize contamination and maintain uniformity. Key features include:
- ISO-Certified Cleanrooms: Controls particulate matter and environmental factors.
- DNA-Free Molding Processes: Prevents biological contamination, critical for diagnostic and implantable devices.
Process Monitoring and Automation
Automation and real-time monitoring enhance consistency by reducing human error and maintaining precise control over production variables:
- Automated Systems: Control injection pressure, temperature, and curing time for uniform results.
- Process Sensors: Continuously measure critical parameters to ensure consistency throughout production.
- Data Analytics: Tracks production metrics to identify and address deviations proactively.
Comprehensive Quality Assurance
Quality checks are integrated at every stage of the manufacturing process:
- First-Article Inspection (FAI): Verifies that initial samples meet all design specifications.
- In-Process Inspections: Conducted during production to detect and correct issues immediately.
- Post-Production Testing: Includes dimensional analysis, material testing, and biocompatibility verification to ensure compliance.
Validation and Regulatory Compliance
Medical molding solutions adhere to strict validation protocols, including:
- Process Validation: Ensures reproducibility and reliability of production processes.
- Regulatory Audits: Regular inspections to maintain certifications like FDA approval or ISO 13485 compliance.
By combining rigorous material selection, advanced manufacturing techniques, and thorough quality control measures, medical molding solutions ensure the consistent production of high-quality, reliable medical devices, meeting the healthcare industry’s demanding standards.
FAQs about Medical Molding Solutions
Medical molding refers to the specialized manufacturing processes used to create precise and high-quality components for medical devices. This process involves using medical-grade materials, often plastics or composites, which are molded into specific shapes and sizes to meet the requirements of various medical applications. Medical molding is crucial in the production of everything from surgical instruments and implants to diagnostic devices and packaging.
There are several types of molding used in the medical industry, including injection molding, compression molding, and micro molding, each designed for specific product needs. Injection molding, for example, is often used for producing small, intricate components with tight tolerances, such as syringes or connectors. The goal of medical molding is to ensure that each part meets stringent regulatory standards for safety, biocompatibility, and durability, while also ensuring cost-effectiveness and scalability for mass production. In short, medical molding is a cornerstone of the medical device manufacturing process, enabling the creation of reliable and safe products for the healthcare industry.
While injection molding is one of the most common methods used in medical molding due to its precision and scalability, there are several alternatives depending on the product requirements, material choice, and production volume. The best alternative to injection molding varies based on specific application needs, but some of the top options include:
Compression Molding: This process is often used for producing larger parts or components that require higher strength. In compression molding, materials are placed in a mold cavity and then compressed to form the desired shape. It is often used for manufacturing rubber parts or thermoset materials in medical devices.
Blow Molding: Used mainly for creating hollow components such as bottles or medical fluid bags, blow molding involves inflating a heated plastic tube inside a mold to form the part. This process is suitable for creating parts with uniform wall thickness and is commonly used for producing packaging for medical supplies.
3D Printing: For rapid prototyping or low-volume production of complex or customized medical devices, 3D printing (or additive manufacturing) is a growing alternative. This method allows for the creation of highly detailed, custom parts in a fraction of the time compared to traditional molding methods. It is especially useful for creating patient-specific implants or devices that require unique specifications.
Rotational Molding: This method is used for producing large, hollow parts like containers and tanks. Rotational molding involves heating a plastic material inside a mold and rotating it to evenly distribute the material. It is an ideal alternative when producing large-volume, durable medical products, such as oxygen tanks or storage containers.
For medical molding solutions, compression molding and cast molding are cost-effective alternatives to injection molding. Compression molding involves placing silicone into a mold cavity and applying heat and pressure to form the desired shape. It is particularly suitable for low-volume production or simple parts with less intricate designs.
Another option is 3D printing, especially for rapid prototyping or producing complex geometries. While 3D printing isn’t always a direct replacement for injection molding, it can significantly reduce costs for small batches or custom designs.
Both methods require less initial investment in tooling compared to injection molding, making them more affordable for certain medical applications. However, they may lack the scalability, precision, or speed of injection molding for high-volume production. The choice of method depends on factors like production quantity, part complexity, and material requirements specific to medical-grade products.
Injection molding can be highly profitable for medical molding solutions due to its efficiency in mass production and the high value of medical-grade products. The profitability depends on factors such as:
Production Volume: The higher the volume, the lower the per-unit cost, increasing profitability.
Tool Longevity: High-quality molds can be reused for thousands of cycles, reducing long-term costs.
Precision and Quality: Medical-grade products command higher prices due to stringent safety and quality standards.
Although the initial investment in molds and machinery is high, the ability to produce intricate, biocompatible components at scale offsets these costs. For example, injection molding is ideal for manufacturing syringes, catheters, or surgical instrument components. With advancements in automation, labor costs are reduced, further boosting profitability. Companies specializing in medical injection molding often achieve strong returns by combining high-volume production with premium pricing.
The cost of a mold for medical injection molding can range from $5,000 to over $100,000, depending on several factors:
Material: High-precision molds for medical-grade silicone or plastic require premium materials, such as stainless steel, to ensure durability and consistency.
Complexity: Intricate designs, micro-features, and multi-cavity molds increase costs due to the precision required.
Tool Life: Medical molds are built to last for thousands or even millions of cycles, contributing to the upfront expense.
Custom Requirements: Molds for medical applications often need compliance with ISO 13485 standards, adding to design and validation costs.
While expensive, these molds ensure high-quality, biocompatible components essential for medical devices. The cost is typically amortized over large production runs, making injection molding cost-effective for high-volume manufacturing of medical parts.
3D printing offers advantages in prototyping and customization, but it is generally not better than injection molding for large-scale medical molding solutions. Here’s why:
Advantages of 3D Printing:
Ideal for creating prototypes, custom parts, or low-volume production with minimal lead times.
Can handle complex geometries that are difficult or expensive to produce with molds.
Advantages of Injection Molding:
More cost-effective for high-volume production, with lower per-unit costs.
Produces parts with superior surface finish, consistency, and strength.
While 3D printing is gaining traction with advancements in biocompatible materials, it currently cannot match the speed, scalability, or cost-effectiveness of injection molding for medical-grade products. Both methods can complement each other, with 3D printing used for prototypes and injection molding for mass production.
For certain medical molding solutions, liquid silicone rubber (LSR) molding and micro-molding may be better alternatives, depending on the application.
LSR Molding:
Ideal for producing high-precision medical components, such as seals, catheters, or implants.
Offers superior biocompatibility and durability compared to standard injection molding materials.
Micro-Molding:
Specifically designed for producing extremely small parts, such as microfluidic devices or surgical instruments.
Ensures precise tolerances required in advanced medical applications.
Additionally, 3D printing can outperform injection molding in cases requiring rapid customization or highly complex geometries. However, for mass production, injection molding remains the most efficient and reliable choice. The “better” solution depends on production needs, part complexity, and the regulatory requirements of the medical industry.
Medical molding solutions are expensive due to the high level of precision, quality, and compliance required. Key factors contributing to the cost include:
Tooling Costs: Molds are made from durable materials like stainless steel to withstand repeated use, and they must be manufactured with micrometer precision.
Material Purity: Medical-grade materials, such as silicone or biocompatible plastics, are more expensive than general-purpose alternatives.
Regulatory Compliance: Meeting standards like ISO 10993 or FDA requirements involves extensive testing, validation, and certification.
Cleanroom Production: Manufacturing often takes place in controlled environments to prevent contamination, increasing operational costs.
R&D Investment: Designing molds for intricate medical components requires advanced engineering and prototyping, which adds to the initial expense.
Despite the upfront costs, molding ensures the production of reliable, high-quality medical components, making it a worthwhile investment for healthcare applications.
Contact our professional team now for a same-day quote and risk-free project evaluation. Benefit from ISO 8 cleanrooms, advanced machines, and 12-hour fast response in medical injection molding.