Medical molding validation is a critical process in the manufacturing of medical devices. It involves verifying that injection molding techniques consistently produce high-quality parts that meet the strict standards of the healthcare industry. This validation ensures that every molded component, from syringes to surgical implants, meets precise specifications for safety, reliability, and performance. The importance of medical molding validation lies in its role in meeting regulatory requirements, such as those set by the FDA, and in ensuring that the final products are safe for patient use. By integrating precision mold medical techniques into the process, manufacturers can achieve even greater accuracy and consistency in the production of medical components. Through rigorous testing and documentation, manufacturers can guarantee that their molding processes deliver dependable and compliant medical devices, reinforcing their commitment to quality and safety. Medical molding validation ensures injection molding meets quality standards, ensuring consistency, stability, and minimal scrap in medical devices.
Low-Volume to High-Volume Production Capabilities
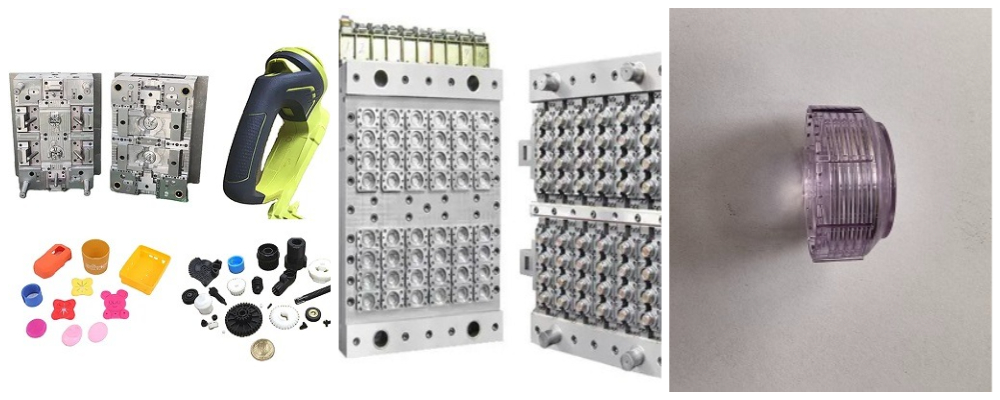
Attributes | Details |
---|---|
Place of Origin | Dongguan, Guangdong, China |
Brand Name | LY Medical Injection Mold |
Product Name | Medical Injection Molding |
Material | Plastic |
Plastic Material | ABS/PP/PS/PE/PVC/PA6/PA66.....etc. |
Application | Medical Industry |
Molding Mode | Plastic Injection Mold |
Technology | Hot Pressing |
Surface Treatment | Custom Surface Texture |
Process | Kiss Cutting |
Hardness | 20~90 Shore A |
Usage | Versatile |
Certification | ISO9001 |
Processing Service | Molding, Cutting |
Size | Accept Customer's Design |
Shape | Custom Shape |
Color | Custom Color |
Logo | Customer's Logo |
Drawing Format | STP STEP IGS CAD |
Features | Durable |
OEM/ODM | OEM ODM Available |
Minimum Order Quantity | 1 Piece |
Packing | Polybag Packing or Packing According to Customer's Needs |
Shipping | By Sea or Air According to Customer's Requirements |
What is Medical Molding Validation?
Medical molding validation refers to the comprehensive process of verifying that injection molding procedures for medical devices consistently produce parts that comply with both quality standards and regulatory requirements. The validation process ensures that every aspect of the molding cycle—from material selection to final product inspection—meets strict specifications that guarantee the safety and effectiveness of the medical devices. This involves both the scientific approach to molding and the documentation needed to prove compliance with regulations set by authorities like the FDA (Food and Drug Administration) or other global standards.
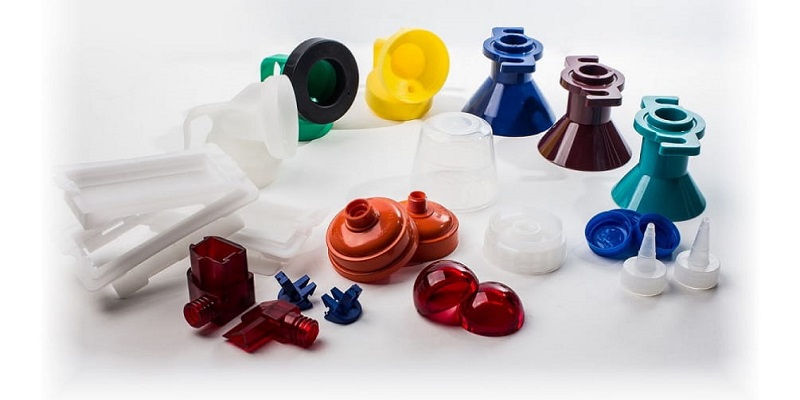
Key Steps in Medical Molding Validation
- Material Selection: Choosing the right medical-grade materials to ensure safety and performance.
- Molding Process Setup: Adjusting molding parameters like temperature, pressure, and timing to achieve consistent results.
- Process Monitoring and Control: Ongoing testing and monitoring to ensure the molding process stays within defined specifications.
- Final Product Testing: Conducting rigorous testing to ensure the molded components meet all quality and regulatory criteria.
Importance of Medical Molding Validation
Medical molding validation not only helps manufacturers produce consistent, high-quality products but also provides a documented trail of compliance that can be critical for regulatory approval and audits. This validation helps mitigate risks related to product failure, patient safety, and potential legal liabilities. It also boosts the efficiency of the manufacturing process by identifying potential issues early, which can save time and reduce costs in the long run.
- Ensures that the manufacturing process is reliable
- Establishes confidence that the process can consistently meet requirements
- Helps avoid delays in the regulatory schedule and time to market
- Is required by law for legally selling molded devices
Benefits of Medical Molding Validation
- Quality assurance: Ensures that parts meet the required specifications and are free from defects.
- Regulatory compliance: Satisfies regulatory bodies’ stringent requirements, preventing costly delays or fines.
- Improved efficiency: Validated processes often lead to fewer production issues and lower scrap rates.
- Risk reduction: Helps to mitigate the risk of recalls, litigation, or safety concerns.
Drawbacks of Medical Molding Validation
- High initial investment: The cost of certification and validation activities can be substantial, especially for small manufacturers.
- Time-consuming: The validation process can take weeks or even months to complete, delaying production timelines.
- Resource-intensive: Requires a dedicated team of experts and resources for testing and documentation.
- Potential for production disruptions: Any flaws found during validation may require modifications, disrupting ongoing production.
Examples of Medical Molding Validation in Practice
- Syringe manufacturing: Ensuring that the molding process produces syringes with precise dimensions and leak-proof seals.
- Orthopedic implants: Validation ensures that implants are made from medical-grade materials with optimal strength and durability.
- Disposable surgical instruments: Molding processes for tools like scalpels and forceps must be validated for safety and precision.
- Diagnostic equipment: Validation of the medical injection molding process for components of devices like blood glucose meters or respiratory machines ensures accurate function and safety.
Medical Molding Validation Process
Medical molding validation is a crucial step in the process of injection molding for medical devices. It ensures that the injection molding process consistently produces parts that meet the stringent requirements set forth by regulatory agencies, such as the FDA. This includes validating not only the equipment and process but also the materials used, the molding conditions, and the final product’s quality.
The validation process for injection molding in medical applications typically involves several stages:
Process Qualification
In this stage, manufacturers ensure that the injection molding process is capable of producing high-quality components that meet all specified tolerances and standards. This includes evaluating the machine settings, molds, materials, and environmental conditions. Each stage of the process, from material selection to molding parameters, is thoroughly documented to confirm that the system operates as expected.
Equipment and Material Validation
For medical device plastic manufacturing, it is critical to validate the equipment and materials used in the molding process. This includes assessing the reliability and performance of the injection medical molding machine, as well as the medical-grade plastics used to make components. The materials must be tested for purity, compatibility with human tissues, and resistance to sterilization methods.
Performance Testing and Documentation
Once the process and equipment are validated, performance testing ensures that the molded components function as intended. This may include tests for strength, durability, biocompatibility, and precision. Thorough documentation is crucial throughout the validation process to demonstrate compliance with industry standards and regulatory requirements.
By thoroughly validating the injection molding process, manufacturers can ensure the safety, reliability, and performance of medical devices, which is essential for patient care and regulatory approval.
Medical Molding Validation Certification
Medical molding validation certification is a formal acknowledgment that a medical device manufacturer has successfully implemented and verified its molding process in compliance with industry standards and regulatory requirements. Achieving certification is a critical step for manufacturers in the medical device industry, as it demonstrates their commitment to quality, safety, and consistency in producing medical components.
This certification process typically involves thorough documentation, including reports on testing results, validation protocols, and evidence that all regulatory criteria have been met. Certification ensures that the production process consistently produces parts that meet the necessary physical, chemical, and mechanical properties required for medical applications.
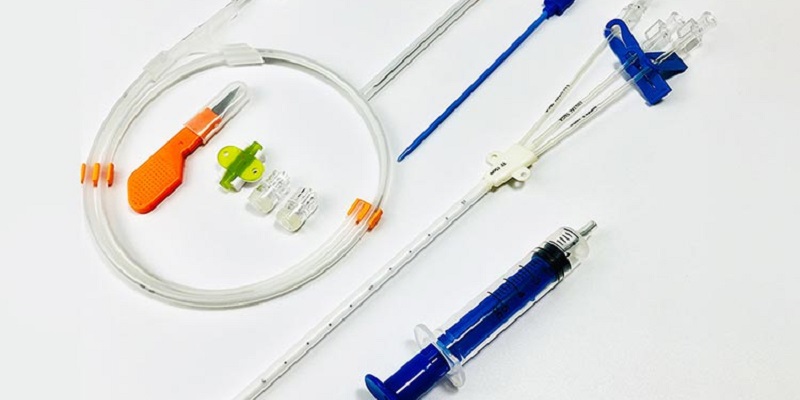
Steps to Obtain Medical Molding Validation Certification
- Process Design and Risk Assessment: The first step involves designing medical molding process to ensure it meets the required specifications for medical-grade materials and products. A detailed risk assessment helps identify potential issues that could affect the safety and performance of the devices.
- Testing and Documentation: Extensive testing is carried out to verify that the molding process consistently meets specifications. This includes mechanical testing, material property validation, and environmental testing. Comprehensive documentation of the testing process is essential for certification.
- Final Validation Report: After testing and adjustments, a final validation report is compiled, which outlines the process controls, test results, and compliance with regulatory requirements. This report is critical for the certification review.
Importance of Certification in Medical Molding Validation
Certification is crucial for gaining trust from regulators, healthcare providers, and end-users. Without certification, a medical plastic device manufacturer may struggle to enter or maintain a foothold in highly regulated markets. Furthermore, it assures patients and medical professionals that the devices are produced to the highest standards of safety and reliability.
By obtaining medical molding validation certification, manufacturers not only comply with the law but also enhance the credibility and reliability of their products in the medical device market.
Medical Molding Validation Costs
Medical molding validation costs refer to the financial investment required to validate the injection molding process for medical devices, ensuring that the parts produced meet regulatory and quality standards. These costs can vary widely depending on factors such as the complexity of the product, the materials used, and the scope of the validation process itself.
The validation process typically involves several stages, including equipment qualification, process design, testing, and documentation. Each of these stages contributes to the overall cost, which may include direct expenses like testing equipment, staff hours, and laboratory fees, as well as indirect costs such as project delays and regulatory audits.
Factors Affecting Medical Molding Validation Costs
- Product complexity: More intricate designs require advanced technology and testing methods, increasing validation costs.
- Material selection: Medical-grade materials are often more expensive and may require additional testing to meet standards.
- Regulatory requirements: The cost of compliance with FDA or international regulations can be significant, especially for high-risk devices.
- Validation scope: A full validation process, including requalification or ongoing process monitoring, adds to the overall cost.
Key Considerations in Medical Molding Validation
The medical molding validation process involves several critical factors to ensure precision, consistency, and quality in the production of medical device components.
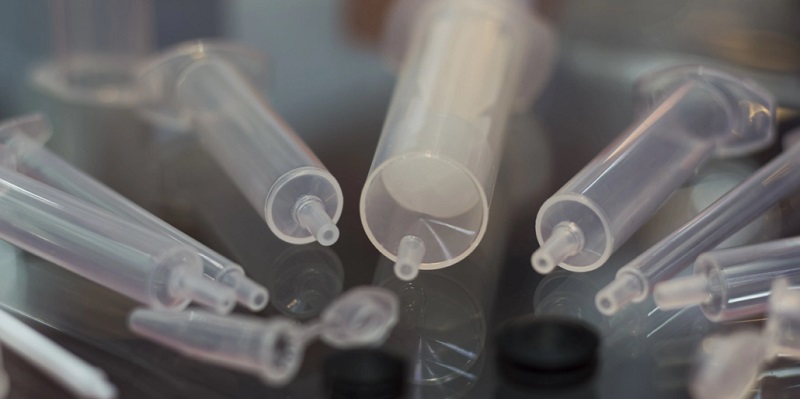
Each of these considerations plays a vital role in achieving reliable and compliant outcomes:
Cooling Circuit Size and the Reynolds Equation
The size of the cooling circuit in the mold must align with the turbulent Reynolds equation to ensure effective heat transfer. Turbulent flow within the cooling system enhances the uniform removal of heat, preventing defects like warping or sink marks. Proper design and validation of the cooling circuit size optimize cycle times and maintain part quality.
Balanced Cooling Through Uniform Line Sizing
Adjusting the size of the cooling lines uniformly ensures balanced cooling throughout the mold. Imbalances can lead to uneven cooling, which may cause dimensional inconsistencies or material stresses. A well-calibrated cooling system is essential for stable and repeatable production.
Inspection Area Location, Lighting, and Cleanliness
The molded product inspection area must be strategically located in a clean, controlled environment. Proper lighting is crucial for accurate visual inspection of defects or surface imperfections. Ensuring cleanliness minimizes contamination risks, particularly for medical-grade components requiring sterility.
Calibration and Documentation of Inspection Equipment
All equipment and technologies used to inspect and accept molded parts must be regularly calibrated and recorded. This includes devices for dimensional measurement, visual inspection, and material testing. Accurate calibration ensures reliable inspection results and compliance with regulatory requirements.
These considerations are integral to a successful medical molding validation process, guaranteeing that all components meet strict quality and performance standards while minimizing production risks.
Regulations and Standards for Medical Molding Validation
Medical molding validation must adhere to established guidelines and standards to ensure compliance, consistency, and safety in medical device manufacturing. Key regulatory and standard frameworks include:
- Global Harmonization Task Force (GHTF) Guidelines
The GHTF, a voluntary international organization, provides comprehensive process validation guidelines for medical devices. These guidelines help manufacturers ensure that molding processes consistently produce components meeting predefined quality and safety standards. They emphasize process qualification (IQ, OQ, PQ), risk management, and documentation. - ISO Standards for Medical Devices
The International Organization for Standardization (ISO) sets global quality standards for medical device manufacturers. Key standards include:- ISO 13485: Specifies requirements for quality management systems specific to medical devices, including validation processes.
- ISO 14971: Focuses on risk management principles for medical devices.
- ISO 10993: Addresses biocompatibility requirements for materials used in medical molding.
Adhering to these regulations ensures that medical molding validation processes meet global safety, quality, and performance expectations, fostering trust and compliance in the medical device industry.
FAQs about Medical Molding Validation
Molding validation is the process of ensuring that an injection molding system consistently produces parts that meet predefined specifications for quality, safety, and regulatory compliance. This process is essential in industries like medical device manufacturing, where precision and reliability are critical. Molding validation involves several steps, including the qualification of the equipment, material testing, process monitoring, and final product testing. Each stage of the process must be documented to demonstrate compliance with industry standards and regulatory bodies such as the FDA.
The goal of molding validation is to guarantee that the molded components not only meet the required specifications but also function as intended in their final application. For medical devices, this often means verifying that the components are biocompatible, durable, and safe for use in critical healthcare environments. Molding validation also helps to identify any potential issues early in the production process, reducing the risk of costly recalls or non-compliance fines. It is an investment in quality assurance, ensuring that the final product is both reliable and safe for patient use.
Medical molding refers to the injection molding process used to manufacture medical devices and components, such as surgical instruments, implants, and diagnostic tools. It involves injecting medical-grade materials, typically plastics or silicone, into molds to create precise and functional parts. Medical molding is a critical part of the medical device industry because it allows manufacturers to produce high volumes of components with tight tolerances, ensuring that the devices are reliable, safe, and functional.
The key to successful medical molding lies in using medical-grade materials that are designed to withstand sterilization, are biocompatible, and meet the stringent regulations set by regulatory bodies like the FDA. The molding process is highly controlled to ensure the consistency and quality of each part produced. With advanced molding technologies, manufacturers can produce complex geometries and intricate designs that are required for modern medical devices. As the medical industry continues to evolve, medical molding plays a pivotal role in developing life-saving devices that meet the highest standards of quality and precision.
Medical molding is a specialized injection molding process for producing components used in medical devices. This process involves using medical-grade plastics, stringent cleanroom conditions, and precise manufacturing controls to meet healthcare industry standards. The medical molding process ensures the biocompatibility, sterility, and performance of the molded parts. Commonly used materials include polycarbonate, polypropylene, and PEEK, chosen for their durability, chemical resistance, and safety.
The process begins with designing a precise mold, often with intricate features, to meet the functional requirements of medical devices. High-quality machinery is employed to maintain consistent conditions, including temperature, pressure, and cycle times. Cleanroom environments (ISO 7 or ISO 8) are often required to prevent contamination. Post-molding processes like sterilization and packaging ensure readiness for medical use. Rigorous quality controls, including dimensional inspection and material verification, are integral to medical molding.
Medical device validation ensures that a device consistently meets its intended purpose and regulatory requirements. For molding processes, this involves validating the design, equipment, and manufacturing processes through a series of documented steps. The process typically includes three stages: Installation Qualification (IQ), Operational Qualification (OQ), and Performance Qualification (PQ).
Installation Qualification (IQ): Verifies that the molding equipment is installed and operating as intended.
Operational Qualification (OQ): Establishes that the process performs reliably under specified operating parameters, such as temperature and pressure.
Performance Qualification (PQ): Demonstrates that the molded parts consistently meet quality and functional requirements under real-world conditions.
Validation also involves risk assessments, material certifications, and biocompatibility testing to meet ISO 13485 or FDA standards. Regular audits and revalidations are performed to maintain compliance. This ensures that the molding process produces medical-grade components reliably.
Verification of injection molding parts ensures they meet the required specifications for medical use. This involves several inspection and testing methods:
Dimensional Accuracy: Using tools like Coordinate Measuring Machines (CMM) to ensure parts adhere to specified dimensions.
Visual Inspection: Checking for surface defects, such as flash, sink marks, or warping.
Material Verification: Confirming the material meets the medical-grade requirements using spectroscopy or other analytical techniques.
Functional Testing: Assessing the part’s performance under simulated usage conditions, including mechanical stress or chemical exposure.
Sterility Testing: Ensuring parts meet sterility requirements for medical applications.
Documentation Review: Cross-verifying the production parameters and lot traceability records.
Advanced techniques, such as CT scanning or X-ray imaging, may be used for complex geometries. Verification ensures compliance with standards like ISO 10993 (biocompatibility) and ISO 13485.
Molding refers to the manufacturing process of shaping raw materials into desired forms using molds. In medical molding, this typically involves injecting molten plastic into a custom-designed mold under high pressure. Once the material cools and solidifies, the finished component is ejected.
Medical molding uses materials and processes tailored to meet the stringent requirements of the healthcare industry. Cleanroom environments and precise equipment are essential to avoid contamination. Different molding techniques, such as injection molding, blow molding, or compression molding, may be used depending on the application.
The primary goal of molding in medical device production is to create precise, high-quality, and biocompatible components, such as syringes, implants, or diagnostic tools, consistently and efficiently.
Plastic quality for medical molding is assessed through a combination of material testing, visual inspections, and functional evaluations:
Material Testing: Verifies properties like tensile strength, chemical resistance, and biocompatibility. Methods include DSC (Differential Scanning Calorimetry) for thermal properties and FTIR (Fourier-Transform Infrared Spectroscopy) for material composition.
Visual Inspection: Identifies defects like discoloration, inclusions, or surface imperfections.
Dimensional Accuracy: Ensures the part meets precise tolerances using tools like CMM.
Functional Testing: Simulates real-world usage, checking durability and performance.
Contamination Check: Ensures parts are free from particulates or microbial contamination, especially for sterile applications.
Certifications: Confirm compliance with regulatory standards like FDA or ISO 10993.
Regular quality checks during and after production ensure the plastic is suitable for medical applications.
Validating a medical molding process ensures it produces consistent, high-quality results that meet regulatory requirements. The process involves:
Define Objectives: Identify critical parameters, such as temperature, pressure, and cycle time.
Risk Assessment: Analyze potential risks and establish mitigation plans.
Installation Qualification (IQ): Verify equipment is installed correctly and meets specifications.
Operational Qualification (OQ): Test the process under different conditions to determine operational limits.
Performance Qualification (PQ): Demonstrate consistent production of quality parts under normal operating conditions.
Documentation: Maintain detailed records of validation steps, including test results and equipment calibrations.
Ongoing Monitoring: Regularly review and revalidate the process to ensure continued compliance.
Validation confirms that the molding process reliably produces parts that meet all medical and regulatory requirements, ensuring patient safety.
Contact our professional team now for a same-day quote and risk-free project evaluation. Benefit from ISO 8 cleanrooms, advanced machines, and 12-hour fast response in medical injection molding.