Medical moulded products are essential components in the production of medical devices, offering reliability and precision for healthcare applications. FUJIU Medical Injection Mold specializes in the cleanroom manufacturing of medical devices, ensuring that all products are produced in a controlled and sterile environment. FUJIU Medical injection Mold specializes in medical moulded products with high precision medical products and assemblies competently. Since its establishment, the company has been focused on delivering high-quality and bespoke solutions for the medical industry. With expertise in medical moulding and precision mold medical solutions, FUJIU Medical Injection Mold is committed to providing durable, precise, and compliant medical moulded products. The company’s mission is to meet the stringent requirements of plastic medical device manufacturers while maintaining the highest standards of safety, quality, and efficiency in all their processes.
Low-Volume to High-Volume Production Capabilities
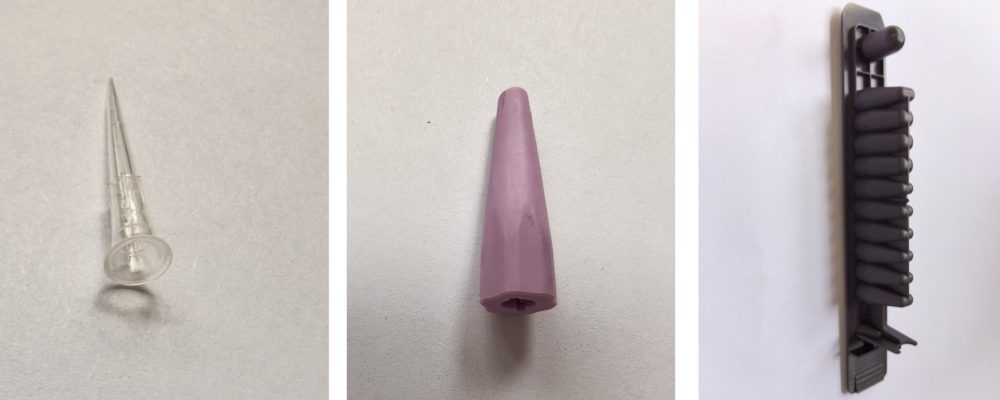
Attributes | Details |
---|---|
Place of Origin | Dongguan, Guangdong, China |
Brand Name | LY Medical Injection Mold |
Product Name | China Medical Molding |
Technology | Injection Molding |
Processing Services | Molding, Cutting |
Color | Customized Color |
Size | Accept Customer's Design |
Shape | Customized Shape |
Service | One-Stop Service |
Feature | Environmentally Friendly |
Advantage | High Quality |
Certification | ISO9001:2008 |
Tolerance | +/-0.01mm / OEM |
OEM | Avaliable |
Selling Units | Single item |
Packing Details | According to Customer's Requirement |
Port | According to Customer's Requirement |
Medical Moulded Products List
Medical moulded products are integral to various medical applications, ensuring the proper functioning of devices used in healthcare settings. These products are designed with precision to meet the high standards required in the medical industry. Injection molding for Class I medical products plays a crucial role in the production of these items, as it ensures consistency, reliability, and precision in manufacturing. Below is a detailed list of the types of injection moulding medical products typically manufactured:
- Syringes: Used for administering injections or drawing fluids. Available in various sizes, syringes are crucial for both medical and emergency applications.
- Dispensers: These are used to accurately measure and dispense liquids or medication in a controlled manner, ensuring proper dosage.
- Spatulas: Commonly used in medical procedures for mixing or applying substances, spatulas come in different shapes and sizes to suit various medical tasks.
- Mixing Bowls: Used for combining materials, mixing bowls are made from non-reactive materials to ensure safe handling of chemicals or medications.
- Catheters and Tubes: These are often used in patient care for medical procedures like inserting fluids into the body.
- Needles: A wide range of needle types, each designed for specific medical uses, including injections, drawing blood, or administering other treatments.
Product Capabilities
Medical moulded products are manufactured with precision to meet various requirements. The product capabilities include:
- Weight: The products can be designed to handle a weight of up to 232g, making them suitable for a variety of applications in the medical field.
- Surface Area: These products can have a surface area up to 120cm², which allows for the creation of larger, complex parts required in medical devices.
Advanced Capabilities in Medical Moulding
In addition to basic moulding techniques, advanced manufacturing capabilities such as over moulding are employed. Over moulding is a process where two or more materials are combined to form a single product, allowing for enhanced functionality, durability, and comfort. This technique is commonly used in products such as syringes with soft-touch handles or medical devices requiring multiple layers of material for performance.
Other advanced capabilities include:
- Multi-material injection moulding: Allows for the creation of products with varying textures and hardness, improving usability and performance.
- High-precision manufacturing: Ensures that all components are accurately produced to meet strict regulatory standards, essential for medical device certification.
- Cleanroom production: All products are manufactured in controlled environments to meet cleanliness and sterility requirements, ensuring safety and compliance with medical standards.
- Customization: Products can be tailored to meet the specific needs of the healthcare sector, offering flexibility in terms of design, material selection, and functionality.
These advanced capabilities enable manufacturers to create highly specialized injection molded medical products designed to meet the demanding needs of the healthcare industry.
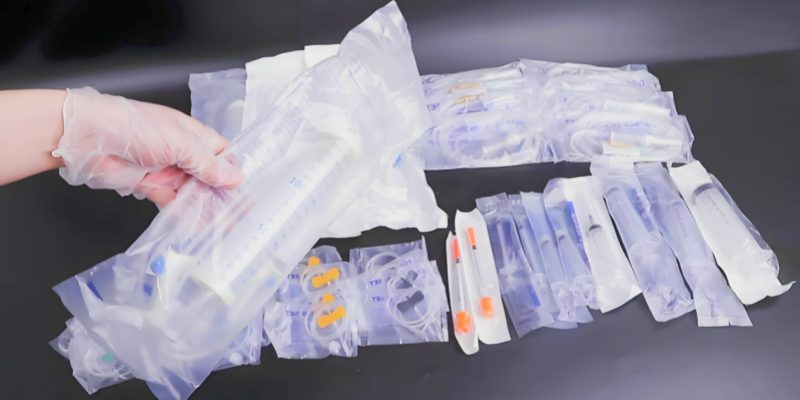
Types of Medical Moulded Products
Medical moulded products are essential components in the healthcare industry, providing precision, durability, and sterility for various medical applications. These products are manufactured using injection moulding, compression moulding, or blow moulding techniques to meet strict regulatory standards. Below are the key types of medical moulded products:
Medical Device Housings and Casings
Medical devices require durable and precisely moulded housings to protect sensitive components. These housings are made from biocompatible plastics such as polycarbonate, ABS, and PEEK to ensure safety and longevity.
- Examples:
- Enclosures for diagnostic devices
- Casings for handheld medical instruments
- Protective covers for surgical tools
Syringes and Injection Moulded Components
Disposable and reusable syringes are among the most common medical moulded products. They are produced through high-precision injection moulding to ensure accuracy and sterility.
- Examples:
- Insulin syringes
- Prefilled syringes
- Needle hubs and plungers
Implants and Prosthetic Components
Certain medical moulded products are used in implants and prosthetic applications. These products require biocompatibility, high strength, and resistance to bodily fluids.
- Examples:
- Joint replacement components (hip, knee, and shoulder implants)
- Dental prosthetics
- Cranial and facial implants
Surgical and Diagnostic Equipment Components
Various surgical and diagnostic tools require moulded plastic parts to ensure lightweight construction, chemical resistance, and precision.
- Examples:
- Handles for surgical instruments
- Housings for endoscopic devices
- Blood analysis and test cartridge components
Medical Tubing and Catheters
Medical-grade tubing and catheters require flexibility, durability, and chemical resistance. These components are moulded from silicone, PVC, and other biocompatible materials.
- Examples:
- IV tubing
- Catheters (urinary, cardiovascular, etc.)
- Respiratory tubing
Pharmaceutical Packaging
Medical moulding is widely used in pharmaceutical packaging to ensure sterility, durability, and controlled dispensing.
- Examples:
- Blister packs for tablets and capsules
- Vials and ampoules for liquid medications
- Inhaler components for respiratory drugs
Personal Protective Equipment (PPE) Components
Injection-moulded plastics are used in the production of PPE for healthcare workers, ensuring safety and durability.
- Examples:
- Face shields
- Respirator masks
- Protective eyewear frames
Laboratory Consumables
Laboratory equipment relies on precision-moulded plastic components that are chemically resistant and disposable.
- Examples:
- Petri dishes
- Pipette tips
- Microcentrifuge tubes
Orthopedic Supports and Braces
Moulded plastic and elastomer-based orthopedic products provide support, stability, and recovery assistance for patients with musculoskeletal conditions.
- Examples:
- Ankle and knee braces
- Wrist splints
- Custom orthotic insoles
Medical moulded products play a vital role in the healthcare industry, ensuring safety, sterility, and efficiency in various applications. The use of advanced moulding techniques and biocompatible materials continues to improve the quality and performance of these essential medical components.
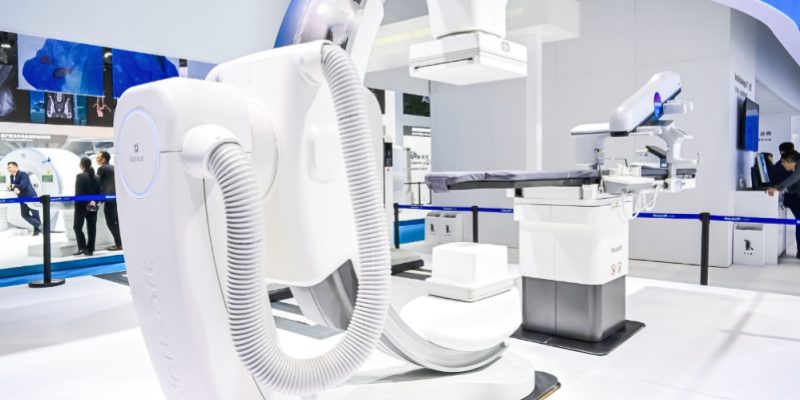
6 Steps of Manufacture Medical Moulded Products
The manufacturing of medical moulded products involves a highly controlled process to ensure precision, sterility, and compliance with medical standards. Below are the six key steps in the production process:
Design and Prototyping
Before mass production begins, a detailed design and prototype must be developed. This step ensures that the product meets medical requirements, regulatory standards, and functional needs.
- Key Activities:
- Creating 3D CAD models
- Performing simulations and stress testing
- Producing rapid prototypes using 3D printing or soft tooling
- Evaluating prototypes for fit, function, and material suitability
Material Selection
Choosing the right material is critical for the performance and safety of medical moulded products. Materials must be biocompatible, sterilizable, and resistant to chemicals and wear.
- Common Materials:
- Polycarbonate (PC) – used for durable housings and surgical tools
- Polyethylene (PE) – used in tubing and disposable labware
- Polypropylene (PP) – used in syringes and containers
- Silicone – used in catheters and implants
- PEEK – used in orthopedic implants due to high strength and biocompatibility
Mould Fabrication
A high-precision mould is created based on the product design. The quality of the mould directly impacts the accuracy and consistency of the final product.
- Key Activities:
- CNC machining and EDM (Electrical Discharge Machining) to shape the mould
- Surface finishing to prevent defects in the final product
- Validation of the mould through trial runs
Moulding Process
The selected material is injected, compressed, or blown into the mould to form the final shape of the product.
- Common Moulding Techniques:
- Injection Moulding: Used for syringes, casings, and PPE components
- Compression Moulding: Used for silicone-based products like catheters
- Blow Moulding: Used for medical bottles and IV fluid containers
- Key Process Parameters:
- Temperature and pressure control to ensure material flow and consistency
- Cycle time optimization to balance quality and efficiency
- Automated quality checks during production
Post-Processing and Sterilization
After moulding, products go through additional processes to meet medical standards and ensure functionality.
- Post-Processing Activities:
- Trimming excess material
- Surface finishing (polishing or texturing)
- Laser marking or engraving for traceability
- Sterilization Methods:
- Gamma Radiation: Used for prepackaged medical devices
- Ethylene Oxide (EtO) Gas: Used for heat-sensitive plastics
- Autoclaving: Used for heat-resistant medical tools
Quality Control and Packaging
Every medical moulded product must pass strict quality control before being packaged and shipped.
- Quality Control Measures:
- Dimensional inspection using precision measuring tools
- Mechanical and chemical resistance testing
- Biocompatibility and sterilization validation
- Compliance checks with regulatory standards (e.g., ISO 13485, FDA guidelines)
- Packaging Considerations:
- Sterile barrier packaging for medical implants and syringes
- Tamper-evident seals to maintain integrity
- Batch coding and tracking for traceability
Manufacturing medical moulded products involves a meticulous step-by-step process, from design to quality control. Each stage ensures that the final product meets the highest standards of safety, durability, and regulatory compliance for use in the healthcare industry.
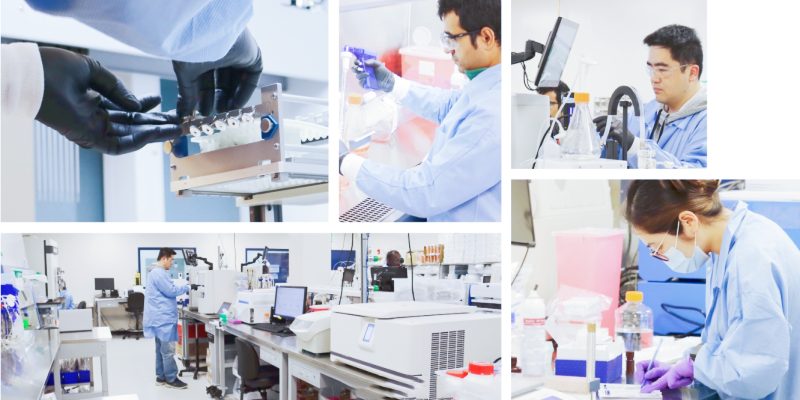
Advantages and Disadvantages of Medical Moulded Products
Medical moulded products play a crucial role in modern healthcare, offering numerous benefits while also posing some challenges. Below is a detailed overview of their advantages and disadvantages.
Advantages of Medical Moulded Products
High Precision and Consistency
Medical moulding techniques, such as injection moulding, produce highly accurate and repeatable components. This ensures uniformity, which is critical for medical devices that require exact specifications.
Cost-Effective Mass Production
Once the mould is created, medical moulding enables high-volume manufacturing at a lower cost per unit. This makes it an efficient choice for disposable medical supplies such as syringes, IV components, and lab consumables.
Biocompatibility and Sterility
Medical-grade plastics used in moulded products are designed to be biocompatible, meaning they do not cause adverse reactions in the human body. Many are also resistant to sterilization methods, such as autoclaving and gamma radiation.
Lightweight and Durable
Compared to metal alternatives, plastic moulded medical products are lighter, making them easier to handle, transport, and use in medical procedures. Despite being lightweight, they offer high durability and impact resistance.
Versatile Design Capabilities
Medical moulding allows for complex geometries and intricate designs that would be difficult or impossible to achieve using other manufacturing methods. This is particularly useful for components in diagnostic devices and surgical tools.
Chemical and Corrosion Resistance
Medical plastics are highly resistant to chemicals, making them suitable for use in harsh environments where exposure to disinfectants, medications, or bodily fluids is common.
Reduced Risk of Contamination
Because moulded medical products are often manufactured in controlled cleanroom environments, the risk of contamination is minimized. This is essential for products used in sterile medical applications.
Disadvantages of Medical Moulded Products
High Initial Tooling Costs
The creation of moulds is expensive, requiring significant investment in precision machining. This high upfront cost can be a barrier for small production runs.
Limited Material Strength Compared to Metals
While medical-grade plastics are durable, they are not as strong as metals. In applications where extreme strength is required, such as orthopedic implants, metal alternatives may be preferred.
Environmental Concerns
Many medical moulded products are disposable, leading to significant medical plastic waste. While some biodegradable alternatives exist, plastic waste management remains a challenge in the healthcare industry.
Sensitivity to Heat and UV Exposure
Certain medical plastics degrade under prolonged exposure to high temperatures or UV light, limiting their use in extreme conditions. This requires careful material selection based on application needs.
Regulatory Compliance and Testing Requirements
Medical moulded products must meet strict regulatory standards (e.g., ISO 13485, FDA guidelines), requiring extensive testing and documentation. This increases the complexity and time required to bring new products to market.
Design Limitations for Specific Applications
While plastic moulding allows for intricate designs, certain applications still require metal components or alternative materials due to strength, heat resistance, or electrical conductivity requirements.
Medical moulded products offer numerous advantages, including cost-effectiveness, high precision, and biocompatibility, making them indispensable in the healthcare industry. However, they also come with challenges such as high initial tooling costs, environmental concerns, and regulatory hurdles. Careful material selection and advanced moulding techniques continue to improve the functionality and sustainability of these essential medical components.
Medical Moulded Products Manufacturers
The medical moulding industry is home to several key manufacturers that specialize in producing high-quality, reliable medical moulded products. These manufacturers play a vital role in the healthcare sector, providing essential components for medical devices that meet stringent regulatory and performance standards. The leading manufacturers in this field are known for their expertise in cleanroom manufacturing, precision moulding, and the use of advanced technology to ensure the highest levels of safety and efficiency.
Key Factors in Choosing Medical Moulded Products Manufacturers
When evaluating injection medical molding products manufacturers, there are several important factors to consider:
- Technology: Leading manufacturers use state-of-the-art machinery, such as modern injection moulding machines (50-150 tonne), to produce highly precise and reliable products.
- Cleanroom Compliance: Cleanroom environments are essential for ensuring that medical products are free from contaminants. Manufacturers that maintain strict cleanroom compliance can guarantee that the products meet required sterility and safety standards.
- Customisation Capabilities: The ability to provide tailored solutions is critical. Many manufacturers offer bespoke medical molding services, allowing for the design and production of medical moulded products that are customized to meet the unique needs of healthcare applications.
- Material Expertise: The use of a wide range of materials is important in producing medical moulded products. Manufacturers must have expertise in working with materials such as medical-grade plastics, elastomers, and thermoplastics to ensure the right material is selected for each product.
- ISO Certifications: ISO certifications, such as ISO 9001:2015 and ISO 13485:2016, are crucial in ensuring that manufacturers adhere to international quality standards. These certifications indicate that the manufacturer follows strict processes to produce molded medical products that meet safety and regulatory requirements.
Importance of ISO Certifications in Manufacturing
ISO certifications play an essential role in ensuring the quality of medical moulded products. These certifications provide assurance to healthcare providers and manufacturers that the production processes follow internationally recognized standards. Some of the key certifications in the industry include:
- ISO 9001:2015: This certification focuses on quality management systems and ensures that manufacturers consistently meet customer requirements and regulatory demands.
- ISO 13485:2016: Specific to the medical device industry, this certification outlines the requirements for a comprehensive quality management system to ensure the consistent design, development, production, and delivery of medical devices.
- ISO 14644: This certification governs the cleanliness of manufacturing environments, ensuring that cleanrooms are maintained to prevent contamination during production.
Manufacturers that hold these certifications are recognized for their commitment to producing high-quality medical moulded products that meet stringent regulatory requirements and are safe for use in healthcare settings.
Custom Medical Moulded Products Company: FUJIU Medical injection Mold
Precision-Engineered Medical Moulding Solutions
FUJIU Medical Injection Mold specializes in the design, development, and manufacturing of high-quality custom medical moulded products. Utilizing advanced injection moulding and blow moulding techniques, we create precise components for medical devices, equipment, and testing instruments. Our commitment to excellence ensures that all products meet FDA approval and stringent quality standards, making us a trusted partner in the medical industry.
Comprehensive Manufacturing Capabilities
We provide a full-service contract manufacturing solution, from initial product design to assembly, packaging, and delivery. Our expertise in medical injection moulding allows us to produce components with exceptional accuracy and reliability, ensuring that your medical products meet the highest performance and safety requirements.
- Design & Prototyping – Rapid development of complex components with minimal lead time
- Custom Injection Moulding – High-precision manufacturing for medical-grade plastic parts
- Assembly & Packaging – Comprehensive solutions to streamline your product development
- Regulatory Compliance – Adherence to FDA, ISO 13485, and industry-specific standards
Cutting-Edge Technology & Expertise
FUJIU Medical Injection Mold operates state-of-the-art cleanroom facilities to manufacture biocompatible plastic components with strict contamination control. Our in-house mould manufacturing and maintenance capabilities allow for fast turnaround times and cost-efficient production. Whether you need small intricate components or large-scale medical parts, our team ensures precision, consistency, and compliance with the highest industry standards.
Why Choose FUJIU Medical Injection Mold?
- Industry-Leading Expertise – Extensive experience in medical-grade plastic injection moulding
- High-Precision Manufacturing – Ability to produce intricate and high-tolerance medical components
- Fast Turnaround & Cost Efficiency – Optimized processes to reduce lead times and moulding costs
- Reliable Quality Control – Rigorous inspection and testing to guarantee product excellence
- End-to-End Solutions – Seamless integration from concept to production, protecting your intellectual property
Partner with Us for Advanced Medical Moulding Solutions
At FUJIU Medical Injection Mold, we are dedicated to delivering efficient, precise, and timely injection moulding solutions for the medical industry. Whether you require custom medical components, complex high-tolerance parts, or large-scale production, our expertise and technology make us the ideal partner for your needs.
Contact us today to discuss your project requirements and receive a tailored quote for your custom medical moulding solutions.
Medical Moulded Products: Advanced Capabilities and Services
Medical moulded products are critical components in the medical device industry, and advanced capabilities are essential for ensuring their performance, safety, and compliance with stringent regulatory standards. Manufacturers specializing in medical moulded products often offer a wide range of services that enhance their ability to produce high-quality, customized solutions for medical device manufacturers. These services ensure that the products not only meet functional requirements but also adhere to the strictest cleanliness and safety protocols.
Advanced Services for Medical Moulded Products
Some of the advanced services offered in the medical moulded products sector include:
- Ultrasonic Welding: Ultrasonic welding is a technique that uses high-frequency sound waves to join two or more materials without the need for adhesives or mechanical fasteners. This is particularly useful in medical moulded products, where hermetically sealed joints are necessary to prevent contamination. The precision of ultrasonic welding ensures that parts are securely bonded without compromising the integrity of sensitive materials, making it ideal for use in medical devices such as syringes or IV bags.
- Drilling, Cutting, Torque Testing: These processes are essential in medical moulded products to ensure that components are manufactured to exacting standards. Drilling is used to create holes for fittings, while cutting ensures that components are shaped to the correct dimensions. Torque testing checks the durability and strength of joints and connections, ensuring that products will function properly under the stresses they will encounter in real-world medical applications.
- 3D Printing: 3D printing offers a versatile and efficient method for creating prototypes and final products in the medical moulded products sector. This technology allows manufacturers to rapidly produce complex, customized medical precision components. 3D printing is especially beneficial for developing low-volume, high-precision parts, which is common in medical devices that require frequent modifications or specialized designs.
Focus on Custom Solutions for Medical Device Manufacturers
A key differentiator for manufacturers of medical moulded products is their ability to provide custom solutions for plastic medical device manufacturers. The medical industry is highly regulated and requires products that not only meet strict performance criteria but also comply with regulatory standards. Custom solutions enable manufacturers to meet these needs by offering:
- Tailored Designs: Medical moulded products manufacturers can design custom products that meet the specific requirements of medical device companies, from precise dimensions to specialized materials and functional features.
- Material Expertise: The ability to select and work with medical-grade materials ensures that the custom solutions provided will be safe, durable, and effective for use in the medical field. Whether it is biocompatibility, chemical resistance, or strength, manufacturers can choose the right materials for each unique product.
- Prototyping and Iteration: With rapid prototyping capabilities, manufacturers can quickly test and iterate designs before final production, ensuring that the final product meets the intended design specifications.
- Scalability: Custom solutions are not only tailored to meet the specific needs of medical devices but are also scalable, allowing manufacturers to increase production volumes as needed without sacrificing quality or precision.
These advanced capabilities and services are essential for ensuring that medical moulded products meet the highest standards of quality, safety, and functionality, providing reliable solutions for the healthcare industry. By offering custom solutions and utilizing state-of-the-art technologies, manufacturers are able to support medical device companies in creating products that improve patient outcomes and enhance healthcare delivery.
Plastic Medical Molded Products: Versatile Solutions for Healthcare
Plastic medical moulded products have become essential in the healthcare industry due to their versatility, durability, and cost-effectiveness. These products play a crucial role in the design and manufacturing of plastic medical devices used in a wide range of medical applications. From administering medications to assisting in surgeries, plastic medical moulded products are integral to the healthcare sector. They are engineered to meet high standards of safety, performance, and regulatory compliance, ensuring their reliability in critical medical situations.
Benefits of Plastic Materials in Medical Device Manufacturing
Plastic materials offer numerous advantages in the production of medical moulded products, making them a preferred choice for manufacturers. The benefits include:
- Durability: Plastic medical moulded products are highly durable, ensuring that they can withstand the rigorous conditions often found in medical environments. These products are resistant to wear, moisture, and chemical exposure, making them ideal for long-term use in both hospitals and clinics.
- Flexibility: Plastics can be easily molded into complex shapes, allowing for the creation of intricate and customized medical components. This flexibility makes them perfect for producing products with precise tolerances and designs.
- Cost-Effectiveness: Plastic materials are typically more affordable than other materials like metal or glass, which helps keep production costs lower. This cost efficiency is critical for manufacturers producing large volumes of medical products, such as syringes or dispensers.
- Biocompatibility: Certain types of medical-grade plastics are designed to be biocompatible, meaning they can safely interact with the human body without causing adverse reactions. This is crucial for products such as implants or medical tubing that are in direct contact with patients.
Commonly Produced Plastic Medical Moulded Products
Plastic medical moulded products are manufactured to meet the specific needs of healthcare professionals and patients. Some of the most commonly produced plastic medical moulded products include:
- Syringes: Plastic syringes are widely used for injecting medications and fluids into the body. They are manufactured in various sizes and capacities to meet the needs of different medical procedures, ensuring precision and ease of use.
- Dispensers: These are used for dispensing medications, liquids, or other materials in a controlled manner. Plastic dispensers are designed for accuracy and are commonly used in hospitals, pharmacies, and clinics.
- Mixing Bowls: Used for preparing medications or combining different substances, plastic mixing bowls are an essential tool in healthcare settings. They are lightweight, durable, and easy to clean, which makes them a preferred choice for medical professionals.
- Needles and Tubes: Plastic moulded products also include medical needles and tubes, which are essential for administering fluids, drawing blood, or other medical treatments. These items are designed for single-use and are manufactured to the highest standards of cleanliness and safety.
- IV Bags and Connectors: Plastic medical moulded products also include IV bags and connectors, which are used for intravenous medication delivery. These items are flexible, allowing for safe and controlled administration of fluids.
These examples highlight the versatility of plastic materials in the production of medical moulded products. From simple items like syringes to more complex devices such as IV bags, plastic medical moulded products meet the diverse needs of the medical community.
Plastic medical moulded products are essential in modern healthcare, offering a reliable, cost-effective, and safe solution for a variety of medical applications. With their advanced manufacturing processes and material advantages, these products continue to play a vital role in improving patient care and medical treatment outcomes.
FAQs about Medical Moulded Products
A moulded product refers to an item that is created through a manufacturing process known as moulding, where materials such as plastics, metals, or ceramics are shaped using a mould. In the context of medical products, moulding is often used to produce highly specialized items that must meet strict standards for safety, precision, and functionality. The process involves heating the raw material until it becomes malleable, then injecting or pouring it into a pre-designed mould, where it cools and solidifies into the desired shape. Moulded products are widely used across many industries, including healthcare, where they are integral to creating medical devices and equipment like syringes, dispensers, and IV bags.
Medical moulded products are crucial in the healthcare sector because they are designed to be durable, biocompatible, and precise. These items can range from small, disposable products to larger, more complex devices used in surgeries or patient care. The moulding process ensures that these products are consistent in quality, which is essential for patient safety. Medical moulded products also offer a high degree of customization, allowing manufacturers to meet the specific needs of healthcare providers and patients.
Medical molding is the specialized process of creating medical devices and products through moulding techniques, primarily using medical-grade plastics. This process is critical in the manufacturing of products that must adhere to strict regulatory standards, as these items are often used in patient care or surgical procedures. The primary goal of medical molding is to produce products that are both functional and safe for human use. These products can range from simple items like syringes and catheters to complex devices such as implants and diagnostic tools.
Medical molding is performed in cleanroom environments to maintain the highest level of hygiene and prevent contamination. The materials used in medical molding are selected for their biocompatibility, ensuring that they are safe to use within the human body or in direct contact with patients. The process also involves precision and attention to detail to ensure that the finished product meets specific performance criteria and regulatory requirements, such as those set by the FDA or ISO standards. Advanced molding technologies, including injection moulding, overmoulding, and multi-material moulding, are often used to create medical moulded products that can withstand rigorous testing and provide optimal performance in real-world medical settings.
In medical terms, molding refers to the process by which an infant’s skull changes shape during childbirth. The human skull is composed of several bones connected by soft, flexible sutures and fontanelles. This allows for a certain degree of flexibility, which is crucial during vaginal delivery. As the baby passes through the birth canal, the skull bones may slightly overlap, compress, or shift to accommodate the narrow passage. This process helps facilitate delivery while protecting the brain.
Molding is most commonly observed in newborns and usually resolves within a few days after birth as the bones gradually return to their normal positions. In cases where excessive or prolonged molding occurs, healthcare professionals may monitor the baby for any underlying conditions, such as craniosynostosis (a premature fusion of skull sutures).
Apart from neonatal molding, the term is also used in orthotics and prosthetics, where custom-fitted medical devices such as braces, splints, or cranial helmets are molded to fit an individual’s body for therapeutic or corrective purposes. Additionally, molding techniques are employed in surgical procedures, particularly in reconstructive surgery, where implants or grafts are shaped to match a patient’s anatomy.
The difference between “molded” and “moulded” is purely linguistic and based on regional spelling preferences. “Molded” is the American English spelling, while “moulded” is the British English version. Both words refer to the same concept: the process of shaping a material into a specific form using a mold.
In medical and healthcare-related applications, molded or moulded materials are often used for prosthetics, orthotics, medical-grade plastics, and surgical implants. For example, molded medical devices such as dental aligners, hearing aids, and orthopedic supports are customized to fit patients precisely.
In pharmaceuticals, molded tablets and capsules ensure accurate dosing and controlled drug release. In biomedical engineering, molded silicone or polymer-based components are used for manufacturing medical tubing, catheters, and respiratory masks. Whether spelled “molded” or “moulded,” the term generally refers to the shaping of medical materials to achieve precision, sterility, and patient compatibility.
A mould product refers to any item that has been shaped using a mould (a cavity or frame) to achieve a specific form. In the medical field, mould products are extensively used in various applications, including medical devices, prosthetics, implants, and pharmaceutical formulations.
Examples of mould products in healthcare include:
Medical-Grade Plastics: Items such as syringes, IV tubing, and catheters are injection-moulded for sterility and precision.
Dental Moulds: Custom dental aligners, retainers, and night guards are manufactured using dental impressions and moulding techniques.
Prosthetics and Orthotics: Limb prosthetics, orthopedic braces, and shoe inserts are made through moulding to ensure a patient-specific fit.
Pharmaceutical Tablets and Capsules: Many medications are compressed and moulded into uniform shapes to ensure accurate dosing and controlled release.
In some cases, mould products also include bioresorbable implants that gradually dissolve in the body, aiding in tissue regeneration. The moulding process ensures these medical items meet stringent safety, biocompatibility, and performance standards.
Molding processes are commonly classified into three main types, particularly in medical manufacturing:
Injection Molding:
The most widely used technique, where molten plastic, silicone, or rubber is injected into a mould cavity under high pressure.
Common in producing syringes, surgical instruments, medical tubing, and IV components.
Compression Molding:
A process where a pre-measured amount of material is placed into a mould and compressed under heat and pressure.
Used for orthopedic shoe insoles, prosthetic components, and some pharmaceutical tablet formulations.
Blow Molding:
Involves inflating a heated plastic tube inside a mould until it takes the shape of the cavity.
Used for manufacturing medical bottles, IV solution containers, and respiratory masks.
Each type of molding is chosen based on factors like material properties, desired product durability, and regulatory compliance in healthcare applications.
Injection molding duration depends on several factors, including material type, part complexity, and mold design. However, in medical manufacturing, cycle times typically range from a few seconds to several minutes per unit.
Key time factors include:
Material Melting & Injection: Molten plastic or silicone is injected into the mold within a few seconds.
Cooling & Solidification: Some medical-grade plastics solidify within 10-30 seconds, while complex parts may require longer cooling.
Mold Opening & Part Ejection: The molded medical device or component is removed, adding another 5-15 seconds.
Quality Inspection: Critical in medical applications, ensuring sterility and precision; this step may add additional time.
For high-volume medical manufacturing, advanced automation can produce thousands of components per hour.
The difference between casting and moulding lies in the technique and material application, particularly in the medical field.
Moulding:
Moulding is a manufacturing process where a material (such as plastic, rubber, or silicone) is shaped using a mould under pressure.
Medical applications include injection-moulded syringes, prosthetic limbs, and pharmaceutical tablets.
Moulding is faster and allows for high-volume production of precision parts, such as IV tubing and surgical instrument handles.
Casting:
Casting involves pouring a liquid material (such as metal, ceramic, or resin) into a mould, which then solidifies.
In healthcare, dental crowns, orthopedic implants, and some custom prosthetics are created using casting.
Casting is useful for making complex, durable medical devices and implants, but it is often slower than moulding.
While both processes shape materials into medical products, moulding is preferred for mass production, whereas casting is often used for customized or high-strength applications.
Molding in the pharmaceutical industry refers to the shaping of drugs, medical devices, and packaging materials using specialized moulding techniques. This process is critical for ensuring precision, sterility, and dosage accuracy in medical treatments.
Key applications include:
Tablet and Capsule Molding: Many medications are compressed into uniform tablets using moulding techniques, ensuring consistent dosing.
Medical-Grade Plastic Components: Syringes, inhalers, and IV connectors are injection-moulded to meet pharmaceutical-grade safety standards.
Blister Packaging: The packaging for tablets and capsules is often thermo-moulded to create protective, tamper-proof containers.
Biodegradable Implants: Some drug delivery systems, such as slow-release implants, are moulded to provide extended medication release.
Molding technology helps maintain pharmaceutical quality control, meeting strict regulatory requirements for medical safety and efficacy.
In medical terms, a mould refers to a structure or device used to shape, support, or replicate a specific part of the body. Medical moulds are used in several contexts, including:
Dental Moulds: Used for creating dental impressions for aligners, retainers, and dentures.
Orthotic & Prosthetic Moulds: Custom-made braces, limb prosthetics, and orthopedic insoles rely on moulding for an exact fit.
Surgical Moulds: Used in reconstructive surgery to shape implants or grafts.
Cranial Helmets: Designed for infants with skull deformities to guide proper head shape development.
Moulds ensure that medical devices and treatments are customized to individual patient needs, improving therapeutic outcomes.
Bone molding refers to the natural or assisted reshaping of bones, often occurring in infants, after fractures, or during corrective orthopedic treatments.
Neonatal Bone Molding: Occurs in newborns as skull bones shift during childbirth but typically return to normal shape within days.
Fracture Healing: After a bone fracture, remodeling occurs as new bone tissue forms, adjusting to mechanical stress over time.
Orthopedic Corrections: Devices like braces or surgical interventions help reshape bones in conditions like scoliosis or limb deformities.
Craniofacial Surgery: Bone grafts and implants are molded to restore facial structure after trauma or congenital disorders.
Bone molding is a critical part of medical treatments for restoring function and aesthetic appearance.
In medical and pharmaceutical industries, the purpose of molding is to create precise, durable, and sterile medical products that improve healthcare outcomes.
Precision Manufacturing: Ensures that medical devices like catheters and syringes meet exact specifications.
Customization: Allows prosthetics, orthotics, and dental appliances to fit patients perfectly.
Mass Production: Enables large-scale production of medical supplies, reducing costs and increasing availability.
Sterility & Safety: Medical-grade plastics and silicone molding prevent contamination, crucial for hospital environments.
Molding plays a vital role in modern medicine by ensuring high-quality, reliable, and patient-specific healthcare solutions.
The most commonly used plastic for injection molding in the medical industry is polypropylene (PP). It is widely preferred because of its excellent chemical resistance, lightweight nature, durability, and low cost. In addition to polypropylene, several other plastic materials are commonly used in medical injection molding, depending on the specific application and required properties.
Other frequently used medical-grade plastics include:
Polycarbonate (PC): Known for its high impact resistance, optical clarity, and heat resistance, it is commonly used in medical devices such as surgical instruments, oxygen masks, and blood filters.
Polyethylene (PE): A versatile plastic used for IV tubing, prosthetic components, and disposable syringes due to its flexibility and chemical resistance.
Polyvinyl Chloride (PVC): Used in the production of catheters, blood bags, and IV solution containers because of its durability and compatibility with sterilization processes.
Acrylonitrile Butadiene Styrene (ABS): Used in medical equipment casings and diagnostic tools because of its toughness and ease of sterilization.
Silicone: Although not a plastic, silicone is commonly injection molded for medical applications such as catheters, respiratory masks, and implants due to its biocompatibility and flexibility.
These plastics are rigorously tested and must comply with strict healthcare regulations to ensure patient safety. Manufacturers choose these materials based on the specific needs of medical applications, considering factors such as sterility, biocompatibility, resistance to chemicals, and the ability to withstand repeated sterilization processes.
Moulding is widely used in medical applications to create precision parts and devices essential for patient care and treatment. Three common objects that can be moulded in the healthcare industry include:
Syringes and IV Components:
Injection molding is the most common method for producing medical syringes and intravenous (IV) components. These devices require precision, sterility, and uniformity to ensure accurate drug administration. Syringes and IV connectors are made from medical-grade plastics such as polypropylene or polyethylene, ensuring safety and compatibility with a variety of medications.
Prosthetic Limbs and Orthopedic Braces:
Custom-moulded prosthetic limbs and orthopedic braces are essential for individuals who have lost limbs or require support for musculoskeletal conditions. These devices are manufactured using molding techniques to ensure a perfect fit and maximum comfort. Silicone and thermoplastic elastomers are commonly used for prosthetic sockets, while rigid plastics are used for orthopedic braces.
Dental Aligners and Retainers:
Moulded dental appliances such as aligners, retainers, and night guards are custom-made for each patient. These are typically made using thermoforming or injection molding to ensure a precise fit that aids in orthodontic treatment. The materials used must be safe for oral use, transparent, and durable to withstand extended wear.
Moulding plays a crucial role in the medical industry by enabling the production of high-quality, patient-specific medical devices that improve treatment outcomes and enhance comfort.
Injection-moulded products have several distinct characteristics that make them identifiable. These features are particularly important in the medical field, where precision and quality control are essential. Here are some key indicators that a product has been made using injection molding:
Seam Lines or Parting Lines:
Injection-moulded products often have thin lines where two halves of the mold meet. These lines, known as parting lines, appear due to the nature of the mold design and are a common feature in plastic medical devices like syringes and IV components.
Ejector Pin Marks:
When an injection-moulded part is ejected from the mold, small circular marks known as ejector pin marks may be visible on the surface. These marks occur due to the pins pushing the solidified plastic out of the mold cavity.
Uniformity in Shape and Texture:
Injection molding ensures that all parts have consistent dimensions and surface finishes. Medical devices such as inhalers, catheters, and diagnostic equipment housings have smooth, repeatable shapes due to the precise nature of the injection molding process.
Gate Marks:
The point where the molten plastic enters the mold cavity leaves a small mark known as a gate mark. This is often found on the edge of medical plastic components and can indicate the injection point used during manufacturing.
By looking for these features, medical professionals and manufacturers can easily identify injection-moulded products and ensure that they meet the necessary quality standards for healthcare applications.
The difference between “injection molded” and “injection moulded” is purely based on regional spelling conventions. Both terms refer to the same manufacturing process but are used in different parts of the world:
Injection Molded: Used in American English (e.g., the United States).
Injection Moulded: Used in British English (e.g., the United Kingdom, Canada, and Australia).
Both spellings are correct, and the choice between them depends on the region’s preferred spelling rules. In medical manufacturing and documentation, consistency in spelling is important to maintain uniformity in communication, especially in international trade and regulatory documentation.
Regardless of spelling, injection molding is a crucial process in the healthcare industry, ensuring the production of sterile, high-quality medical devices that meet strict industry standards.
Yes, silicone can be injection moulded, and it is widely used in medical applications due to its biocompatibility, flexibility, and resistance to heat and chemicals. Medical-grade silicone is a preferred material for various healthcare products because it is non-toxic, hypoallergenic, and can withstand sterilization processes such as autoclaving and gamma radiation.
Common Medical Applications of Silicone Injection Molding:
Medical Implants – Silicone is used in pacemaker casings, breast implants, and artificial heart valves due to its durability and compatibility with human tissue.
Respiratory Masks & Tubing – Many breathing masks, CPAP devices, and ventilator components are made using silicone injection molding.
Catheters & Seals – Soft and flexible silicone is ideal for long-term indwelling catheters and seals in medical devices.
Wearable Medical Sensors – Many biomedical sensors and electrode pads are made from silicone because of its skin-friendly properties.
Why is Silicone Preferred for Medical Use?
Non-reactive & Biocompatible – It does not cause allergic reactions or toxicity.
Heat & Chemical Resistance – Can withstand sterilization without degrading.
Durability – Remains flexible and does not break down over time.
Silicone injection molding is crucial in the medical industry because it ensures precise, sterile, and high-quality medical components that improve patient care and safety.
Advantages of Injection Molding in Medical Applications:
High Precision & Consistency – Injection molding ensures uniformity in medical devices such as syringes, prosthetics, and surgical instruments.
Mass Production Capability – Ideal for producing large quantities of medical components quickly and efficiently.
Material Versatility – Allows for the use of a wide range of biocompatible materials, including polypropylene, polycarbonate, and silicone.
Sterility & Safety – Medical-grade plastics and silicones used in injection molding meet strict industry regulations for patient safety.
Cost-Effective for High Volume – While the initial tooling cost is high, the cost per unit decreases significantly with large-scale production.
Disadvantages of Injection Molding in Medical Manufacturing:
High Initial Tooling Cost – Creating the mold is expensive and requires precise engineering.
Limited Design Changes – Once a mold is created, modifying the design can be costly and time-consuming.
Material Restrictions – Not all materials are suitable for injection molding, limiting choices for some applications.
Production Lead Time – The initial setup and mold manufacturing can take weeks or months before full-scale production begins.
Despite these challenges, injection molding remains the most efficient and reliable method for producing high-quality medical devices on a large scale.
Material Preparation & MeltingMedical-grade plastic or silicone is fed into a heated barrel, where it melts and becomes liquid.
Injection into the MoldThe molten material is injected into a pre-designed mold cavity under high pressure.
Cooling & SolidificationThe molded part is cooled to solidify its shape, ensuring structural integrity.
Ejection of the ProductOnce cooled, the mold opens, and ejector pins push the finished part out.
Quality Control & SterilizationEach part undergoes rigorous inspection to ensure it meets medical-grade specifications and is sterilized before use.
These steps ensure the production of precise, durable, and safe medical components used in healthcare settings.
Molding technology is used to manufacture a variety of medical and pharmaceutical products, including:
Medical Devices & InstrumentsSyringes, IV components, catheters, inhalers, and diagnostic test kits.
Pharmaceutical PackagingBlister packs for tablets, vials for liquid medications, and ampoules.
Orthopedic & Prosthetic ComponentsCustom-molded artificial limbs, knee braces, and spinal supports.
Dental & Maxillofacial ProductsAligners, dentures, night guards, and mouthpieces.
Molded products play a crucial role in the healthcare industry by ensuring precision, sterility, and effectiveness in patient treatments.
Both casting and molding are used in medical manufacturing, but they serve different purposes.
Products Created by Molding:
Injection-Molded Syringes & IV Components – High-volume production of precision plastic parts.
Molded Prosthetic Limbs – Custom-designed for amputees using advanced materials.
Dental Aligners & Night Guards – Thermo-molded for individual patients.
Products Created by Casting:
Orthopedic & Dental Implants – Titanium hip replacements and dental crowns are typically cast rather than molded.
Plaster Casts for Bone Fractures – Used to immobilize broken bones.
Custom-Fitted Hearing Aids – Made by casting molds of a patient’s ear shape.
Casting is generally used for metal and ceramic medical components, while molding is preferred for plastic and silicone-based devices.
Injection molds used in medical manufacturing must be made from durable, high-precision materials to ensure quality and longevity. The most common materials include:
Stainless Steel – Preferred for high-precision medical molds due to its strength and resistance to wear.
Aluminum – Lighter and less expensive than steel, but less durable.
Nickel Alloys – Used for highly detailed molds that require superior heat resistance.
Beryllium-Copper Alloys – Provide excellent heat dissipation for fast cooling times.
These materials are chosen based on production volume, part complexity, and the specific requirements of medical-grade plastics or silicone.
Molding materials vary depending on the medical application, with the most common including:
Medical-Grade Plastics
Polypropylene (PP) – Used for syringes and IV components.
Polycarbonate (PC) – Used for surgical tools and lenses.
Polyethylene (PE) – Found in catheters and tubing.
Silicone & Rubber
Silicone Elastomers – Used for respiratory masks, implants, and wearable sensors.
Thermoplastic Elastomers (TPE) – Used for flexible medical seals and tubing.
Metal (for Casting Applications)
Titanium & Stainless Steel – Used for orthopedic and dental implants.
Each material must comply with biocompatibility and sterility requirements to ensure safety in medical applications.
Contact our professional team now for a same-day quote and risk-free project evaluation. Benefit from ISO 8 cleanrooms, advanced machines, and 12-hour fast response in medical injection molding.