Medical parts injection molds are vital to the production of high-quality, precise medical devices, ensuring accuracy and reliability in the healthcare sector. These molds are extensively used to manufacture critical components like implants, surgical tools, syringes, and diagnostic equipment, all of which demand stringent precision to meet safety and functional standards. By leveraging advanced injection molding technologies, companies in the field ensure that these parts adhere to the strict requirements of medical applications, including biocompatibility, durability, and regulatory compliance. Injection molding companies play a crucial role in this process, providing expertise and innovation to meet industry standards while supporting the mass production of essential medical components with consistent quality and cost-efficiency. Medical parts injection molds create precise, durable, and compliant medical devices by molding medical-grade plastics into customized shapes.
What Are Medical Parts Injection Molds?
Medical parts injection molds are specialized tools used in the injection molding process to create precise, durable, and sterile components for the healthcare industry. These molds are designed to meet the exacting standards required for medical devices, ensuring safety, reliability, and performance.
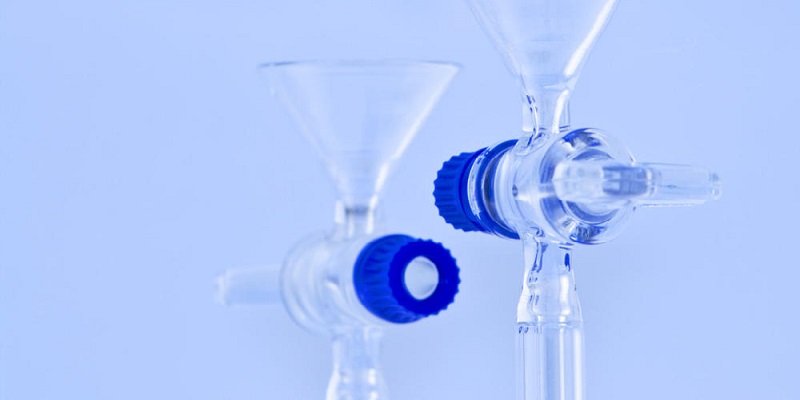
The Role of Medical Parts Injection Molds
- High Precision Manufacturing: Medical parts injection molds enable the creation of intricate components with minimal tolerances, ensuring functionality and compatibility in critical applications.
- Durability and Sterility: The materials used in these medical molds are carefully chosen to support sterilization processes like autoclaving and to maintain structural integrity under demanding conditions.
- Mass Production: Injection molding is ideal for producing large volumes of identical medical parts efficiently and cost-effectively.
Types of Products Made Using Medical Parts Injection Molds
- Surgical Implants: Components like knee and hip implants are manufactured with exceptional accuracy to ensure proper fit and long-term functionality.
- Syringes and Catheters: Disposable medical tools such as syringes and catheters rely on molds that ensure sterility and precise design.
- Laboratory Tools: Items like test tubes, petri dishes, and pipettes are created using molds that emphasize uniformity and clarity.
Piece Medical Device Molds in Medical Parts Injection Molds
3 piece medical device molds are a specific type of injection mold used to produce medical devices with multiple complex components. These molds consist of three separate parts to allow for:
- Complex Geometries: Perfect for devices that require intricate shapes and internal features.
- Ease of Assembly: Designed to produce components that fit seamlessly together in medical devices.
- Enhanced Versatility: Suitable for products like multi-chamber syringes, diagnostic kits, and custom surgical tools.
Medical parts injection molds, including 3 piece medical device molds, are indispensable for ensuring the precision, quality, and scalability of modern medical devices.
Exploring the Types of Medical Molding Processes with Medical Parts Injection Molds
Medical parts injection molds are essential tools used in a variety of molding processes, enabling the production of precise, durable, and high-quality medical components. Below are six key types of medical injection molding processes, each with unique benefits and applications:
Plastic Injection Molding
- Description: This process involves melting plastic polymers and injecting them into medical parts injection molds to form sterile, high-precision components.
- Applications:
- Syringes: Ensuring uniformity and sterility for single-use and reusable syringes.
- Blood Bags: Precision medical molds create secure and durable connections.
- Connectors: Used in tubing and other medical equipment.
Insert Molding
- Explanation: In this method, a secondary material, such as plastic or metal, is overmolded onto an existing component to enhance functionality.
- Common Use:
- Electronics in Medical Devices: For example, circuit boards in diagnostic equipment.
- EKG Hook-Up Leads: Creating secure and durable interfaces.
Overmolding
- Description: This process involves adding a layer of material over an existing part to improve durability, grip, or functionality.
- Example:
- Handles for Surgical Instruments: Provides a non-slip, ergonomic grip to enhance precision and comfort during procedures.
Liquid Silicone Injection Molding (LSR)
- Details: Ideal for producing small runs of flexible, biocompatible components. This process uses liquid silicone, which is injected into specialized molds.
- Applications:
- Tubing: Flexible and durable, suitable for fluid transport in medical applications.
- Catheters: Smooth and sterile surfaces ensure patient safety.
Compression Molding
- Explanation: Plastic or composite materials are placed into a heated mold and compressed to form the desired shape.
- Uses:
- Orthopedic Supports: Producing durable and lightweight braces.
- Prosthetics: Creating custom-fit prosthetic components.
Micro Injection Molding
- Overview: Focuses on producing ultra-small parts with intricate details, essential for modern medical devices.
- Applications:
- Micro Valves: Used in surgical tools and drug delivery systems.
- Miniature Connectors: Crucial in high-tech diagnostic devices.
Role of Plastic Medical Parts Molders
Plastic medical parts molders specialize in creating components using these processes, ensuring consistency, quality, and adherence to regulatory standards. By leveraging medical parts injection molds and advanced techniques, they deliver innovative solutions tailored to the medical industry’s demands.
What is the Cost of Medical Parts Injection Molds
The cost of medical parts injection molds can vary significantly based on several factors, ranging from material selection to mold complexity. Below is a detailed breakdown of the factors influencing costs and the typical pricing ranges for different mold types.
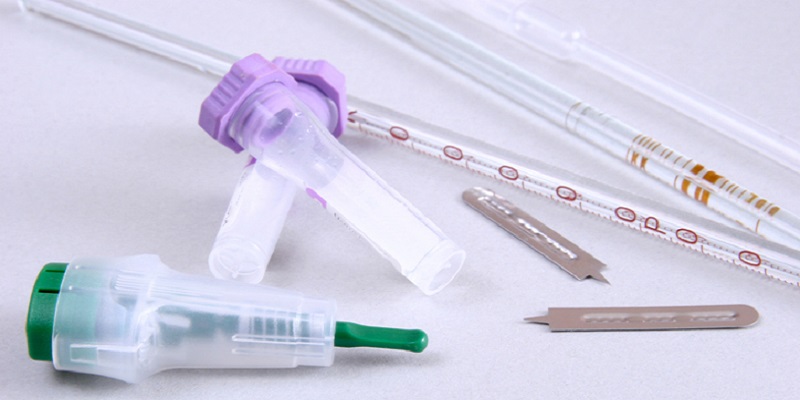
Factors Influencing Costs
Raw Materials
- The cost of the materials used to create the mold, such as hardened steel or aluminum, directly affects pricing.
- Specialized plastics for manufacturing medical precision components increase the overall cost, especially when biocompatibility is required.
Complexity of Mold Design
- Single-Cavity Molds: These molds create one part at a time, making them less expensive but suitable for low-volume production.
- Multi-Cavity Molds: Designed to produce multiple parts simultaneously, these are more complex and costly but reduce per-unit production costs in high-volume scenarios.
Volume of Production
- Low-Volume Production: For smaller quantities, simpler and less expensive molds, such as aluminum molds, may suffice.
- High-Volume Production: Durable steel molds are required for long-term use, increasing upfront costs.
Pricing Breakdown
Single-Cavity Molds:
- Cost: $1,000–$5,000.
- Ideal for small-scale projects or prototypes where lower upfront costs are essential.
Complex or Multi-Cavity Molds:
- Cost: Up to $80,000 or more.
- Best suited for large-scale production where higher initial investments are offset by lower unit costs.
Role of Plastic Mold for Medical Parts
Plastic mold for medical parts is a key component in determining overall costs. These molds, created with precision for applications in healthcare, must meet strict industry standards, which can increase development expenses. Companies specializing in medical parts injection molds ensure cost-effective solutions tailored to production needs while maintaining the required quality for medical devices.
Key Benefits of Medical Parts Injection Molds for Healthcare Manufacturing
Medical parts injection molds provide essential advantages in the production of high-quality medical devices. Their efficiency, precision, and ability to meet stringent industry standards make them a cornerstone of modern medical manufacturing. Below is a detailed exploration of the benefits they offer.
Cost Efficiency
- High-Volume Production Savings: Medical parts injection molds significantly reduce per-unit costs by allowing the production of large quantities of components with minimal material waste.
- Long-Term Investment: Durable molds, such as those made from hardened steel, ensure consistent production over time, optimizing cost efficiency for manufacturers.
Compliance with Industry Standards
- Certifications: Medical molds designed for medical devices adhere to critical certifications like FDA and ISO standards, ensuring safety and reliability.
- Regulatory Assurance: Medical part injection plastic mould designs meet strict guidelines for biocompatibility, dimensional accuracy, and material safety, ensuring usability in healthcare environments.
Precision and Reproducibility
- Consistency Across Batches: Medical parts injection molds provide unparalleled precision, producing identical components with tight tolerances required for critical applications such as implants and surgical tools.
- Adaptability for Complex Designs: Advanced mold-making techniques allow for the creation of intricate geometries, ensuring parts meet specific functional requirements.
Durability and Sterility
- Material Durability: Medical part injection plastic moulds are engineered to withstand high pressures and temperatures, ensuring longevity.
- Sterilization Compatibility: Components produced with these molds are designed to endure sterilization methods like autoclaving, crucial for maintaining hygiene and functionality in medical environments.
Medical parts injection molds, combined with the expertise of manufacturers, deliver cost-effective, precise, and durable solutions for the healthcare sector, ensuring the production of safe and reliable medical devices.
Materials Used in Medical Molding: A Focus on Medical Parts Injection Molds
The materials used in medical parts injection molds are carefully selected to ensure compliance with healthcare standards while meeting the specific requirements of durability, precision, and biocompatibility. Below is a detailed exploration of the most common materials and their applications in medical molding.
Common Plastics in Medical Injection Molding
Polypropylene (PP)
- Characteristics: Lightweight, chemical-resistant, and sterilization-friendly.
- Applications: Used in syringes, pill containers, and disposable medical components due to its robustness and low cost.
- Additionally: It is also commonly used for medical devices class 2 injection molding parts, providing the necessary durability and biocompatibility required for such applications.
Polycarbonate (PC)
- Characteristics: Tough, transparent, and highly resistant to impact.
- Applications: Frequently used in diagnostic tools, such as blood analyzers and protective shields, where visibility and durability are essential.
Silicone
- Characteristics: Flexible, biocompatible, and resistant to temperature fluctuations.
- Applications: Ideal for tubing, seals, and connectors, as it offers exceptional flexibility and sterility.
Material Selection for Medical Parts Injection Molds
The choice of material for medical parts injection molds depends on factors like the device’s functional requirements, exposure to sterilization, and regulatory compliance. By integrating materials such as PEEK or silicone into medical part plastic mould designs,manufacturers ensure the materials used in medical molding.
The creation of 3 piece medical device molds relies heavily on the selection of high-quality materials that meet the stringent demands of medical applications. These materials must ensure durability, precision, and compliance with healthcare standards.
Material Selection for 3 Piece Medical Device Molds
The design and functionality of 3 piece medical device molds require materials tailored for the specific needs of medical devices. Factors influencing material selection include:
- Durability: Ability to withstand repeated use and sterilization.
- Precision: Ensuring tight tolerances for reliable performance.
- Biocompatibility: Compliance with healthcare safety standards to avoid adverse reactions.
By incorporating advanced materials and precise engineering, 3 piece medical device molds facilitate the production of high-quality medical components essential for patient care. production of safe, reliable, and high-performing medical components.
Choosing Manufacturers for Medical Parts Injection Molds
The production of medical parts injection molds is a highly specialized process, as it directly impacts the quality, precision, and safety of critical medical devices. These molds are responsible for shaping plastic components used in various medical applications, from syringes and IV connectors to complex surgical instruments. Given the importance of these devices in the healthcare industry, selecting the right manufacturer for medical parts injection molds is a critical decision. It is essential to ensure that the manufacturer not only has the technical expertise but also adheres to the highest standards of quality control, precision, and compliance with regulatory requirements. Furthermore, clean room environments play an especially important role in the manufacturing of medical components, ensuring that the molds produced are free from contamination and meet stringent safety standards. Below, we will explore the key factors to consider when selecting a manufacturer, with a particular focus on their capabilities regarding clean room standards.
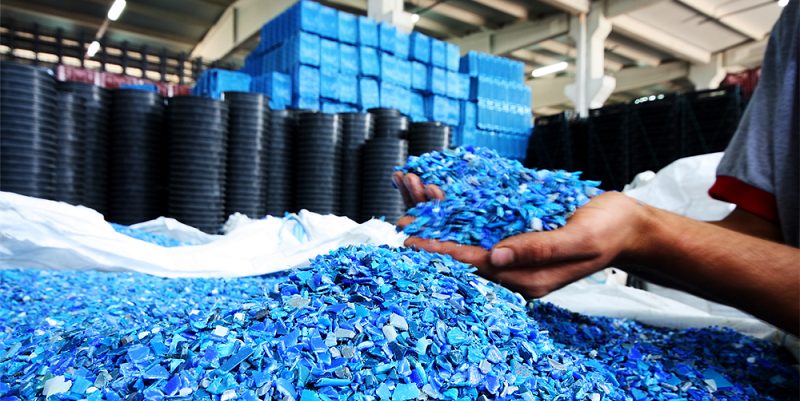
Manufacturer Expertise and Experience
When it comes to the manufacturing of medical parts injection molds, the experience and technical capabilities of the manufacturer are paramount. Medical device molds must adhere to precise specifications and meet strict regulatory standards. Manufacturers with extensive experience in medical molding are better equipped to understand the complexities of the medical industry, including the nuances of materials, mold design, and production processes that ensure the integrity of the medical parts.
Experienced manufacturers often possess the knowledge to create molds that accommodate a variety of medical-grade plastics, which are selected based on their safety, biocompatibility, and durability. Moreover, an experienced manufacturer will have the capabilities to handle intricate mold designs and complex part geometries required for medical devices. It is crucial to select a manufacturer who has expertise in producing molds for medical applications, as this will ensure they are familiar with the high standards for functionality, sterility, and patient safety that medical devices demand.
Quality Control and Compliance
Quality control in the manufacturing of medical parts injection molds is not just about precision—it’s about ensuring that the final product meets the rigorous safety and regulatory standards required in the medical field. The FDA, ISO 13485, and other regulatory bodies impose strict guidelines on medical device manufacturing, including mold production. A trusted manufacturer must follow these regulations to ensure that the molds meet the high standards necessary for medical applications.
Before selecting a manufacturer, ask for detailed information about their quality control processes. This includes their testing protocols, inspection procedures, and their ability to perform rigorous verification of mold dimensions, weight consistency, and material properties. The manufacturer should also have the necessary certifications to prove that they comply with industry-specific standards. For example, ISO 13485 certification indicates that the manufacturer has a quality management system that addresses the safety and regulatory requirements for medical devices. Compliance with such standards minimizes the risk of defects or non-compliant parts entering the production chain, ensuring that the final medical device will function as intended.
Clean Room Standards
The clean room environment is crucial for the production of medical parts injection molds. Clean rooms are specially designed environments where air quality, temperature, humidity, and particulate contamination are strictly controlled to minimize the risk of contamination. In the medical device industry, cleanliness is vital to prevent any particles, dust, or bacteria from contaminating the mold or the plastic materials used to create the medical parts.
A high-quality clean room should comply with ISO Class 7 or better, with strict air filtration systems and positive air pressure to prevent contaminants from entering. These conditions ensure that the medical parts produced in these environments are free from harmful particulates that could compromise the safety or function of the medical device. When selecting a manufacturer, confirm that their clean room facilities meet these standards and that the company conducts regular certifications and inspections to ensure compliance. Manufacturers with in-house clean room environments can maintain greater control over the production process and ensure that the molds meet the highest standards for sterility and contamination-free molding.
Choosing the right manufacturer for medical parts injection molds is a multifaceted decision that requires careful consideration of the manufacturer’s experience, commitment to quality, and adherence to strict regulatory standards. It is essential to select a manufacturer with the technical expertise to handle complex medical molding projects and who follows stringent quality control processes to ensure precision and compliance. Moreover, ensuring that the manufacturer operates under appropriate clean room standards is critical for producing contamination-free molds that meet the safety requirements for medical devices. By prioritizing these factors, you can ensure that the medical parts injection molds will meet the high standards necessary for the manufacture of safe, reliable, and effective medical devices.
Importance of MedAccred Certification in the Production of Medical Parts Injection Molds
MedAccred certification is an essential credential in the manufacturing of medical devices, particularly for medical parts injection molds. This certification is awarded to suppliers who meet stringent standards set by the MedAccred program, a global initiative aimed at ensuring that manufacturers of medical components adhere to the highest quality and compliance standards. In this section, we will explore what MedAccred certification is and why it holds significant importance in the production process of medical parts injection molds, especially in terms of quality assurance, risk mitigation, and regulatory compliance.
What is MedAccred Certification?
MedAccred is a quality system certification program developed by the Medical Device Manufacturers Association (MDMA) and administered by the Performance Review Institute (PRI). The program was specifically designed to evaluate and verify that suppliers in the medical device manufacturing supply chain meet the critical requirements for quality control, traceability, and regulatory compliance.
MedAccred certification focuses on evaluating key processes such as injection molding, heat treatment, coating, and assembly. For manufacturers of medical parts injection molds, MedAccred certification assures that their processes, from design to production, meet the regulatory and safety requirements set by industry standards like ISO 13485, FDA, and other relevant global authorities. The certification process includes rigorous audits and continuous assessments to ensure that suppliers maintain high standards of operational excellence.
Role of MedAccred Certification in the Production Process of Medical Parts Injection Molds
MedAccred certification plays a vital role in ensuring that manufacturers of medical parts injection molds consistently produce high-quality and compliant molds that meet industry standards. Below, we will outline why MedAccred certification is crucial in the production process of these molds.
Ensuring Consistency and Quality
MedAccred certification is a rigorous process that evaluates a manufacturer’s ability to maintain consistency and high quality in their production processes. In the case of medical parts injection molds, even the smallest defect in the mold can have significant implications for the functionality and safety of the final medical device. MedAccred certification ensures that a manufacturer adheres to strict quality control procedures and standards, thereby minimizing the risk of mold defects or contamination. This consistency in production is critical for ensuring that medical devices, such as syringes, surgical tools, and diagnostic equipment, perform reliably in clinical settings.
Mitigating Risk and Enhancing Compliance
The production of medical parts injection molds is subject to numerous regulatory requirements, including those set by the FDA, ISO 13485, and other governing bodies. MedAccred certification helps manufacturers meet these stringent requirements by ensuring their processes are well-documented, auditable, and aligned with regulatory standards. This certification serves as a valuable tool for mitigating risks associated with non-compliance, such as recalls or product failures, by ensuring that all production processes are carefully monitored and controlled.
For manufacturers, MedAccred certification demonstrates their commitment to maintaining compliance with international medical device regulations, which is essential for staying competitive in the global medical market. For customers and stakeholders, it provides confidence that the manufacturer is capable of producing molds that meet the highest standards of quality, reliability, and regulatory adherence.
Building Trust with Clients and Partners
MedAccred certification enhances a manufacturer’s reputation in the highly regulated medical device industry. It signals to clients and business partners that the manufacturer has undergone comprehensive audits and met the rigorous requirements necessary for producing medical-grade molds. This builds trust and fosters long-term relationships, as companies are more likely to partner with suppliers who have MedAccred certification due to the added assurance that the production processes meet industry best practices.
MedAccred certification is a critical factor in ensuring the quality, compliance, and risk management of medical parts injection molds. By validating that manufacturers adhere to strict regulatory standards and maintain high-quality production processes, MedAccred certification not only guarantees the reliability of the molds but also builds trust between manufacturers and their clients. Given the complex and sensitive nature of medical device production, manufacturers with MedAccred certification offer the necessary assurance that their injection molding processes are safe, precise, and compliant with global standards, making it an invaluable credential in the medical molding industry.
Professional Skills and Considerations for Designing Medical Parts Injection Molds
Designing medical parts injection molds requires a high level of skill, precision, and knowledge of both engineering principles and medical device standards. The design process for these molds involves considering factors such as material selection, mold structure, part geometry, and regulatory compliance to ensure that the molds produce high-quality, safe, and reliable medical components. Designers must not only be familiar with injection molding technology but also have an in-depth understanding of the specific requirements of the medical industry. In this section, we will explore the key professional skills designers need and the critical considerations during the design process for medical parts injection molds.
Professional Skills Required for Designing Medical Parts Injection Molds
Designing medical parts injection molds is a highly specialized task that requires a combination of engineering knowledge, creativity, and attention to detail. The skills required for this role extend beyond basic mold design to include a deep understanding of the medical device manufacturing industry’s needs and standards. Below are the key skills that designers need to possess.
Advanced CAD (Computer-Aided Design) Skills
One of the most critical skills for designing medical parts injection molds is proficiency in CAD software. Designers must use CAD tools to create detailed 3D models of the molds, taking into account the dimensions, part geometry, and any features specific to the medical application. Advanced CAD skills enable designers to visualize the mold design, identify potential design flaws, and optimize the design for manufacturing efficiency.
The ability to simulate the injection molding process through CAD software is also essential. This simulation helps designers analyze factors like material flow, cooling time, and mold stress, ensuring that the mold will perform as expected during production.
Knowledge of Material Science
An in-depth understanding of materials is crucial for selecting the appropriate medical-grade plastics for the molds. Medical parts injection molds must be designed with materials that meet strict regulatory standards for safety, biocompatibility, and durability. Designers must be familiar with the properties of various medical-grade plastics, such as their thermal conductivity, strength, and chemical resistance, to ensure that the mold is not only functional but also compliant with medical industry standards.
Expertise in Injection Molding Technology
Designers must also have a solid understanding of injection molding processes, including the mechanics of how the molten plastic is injected into the mold cavity and how the material solidifies. Knowledge of molding techniques such as multi-shot molding, insert molding, and overmolding can help designers create more complex parts that meet specific medical needs. Additionally, expertise in the design of mold cooling channels, vents, and gates is essential for ensuring efficient and effective molding processes.
Key Considerations During the Design Process of Medical Parts Injection Molds
The design process for medical parts injection molds is highly complex, and several factors must be considered to ensure that the molds meet the high standards required in the medical industry. Below are some critical considerations designers should focus on during the design process.
Regulatory Compliance and Quality Standards
Medical parts injection molds must adhere to strict regulatory requirements, including ISO 13485, FDA guidelines, and other international standards governing medical device manufacturing. Designers must ensure that the mold design aligns with these regulations and that all materials used in the process are approved for medical use. Understanding these compliance requirements is essential to avoid delays in production and costly recalls due to non-compliance.
To meet these standards, designers must incorporate quality control features into the mold design. This includes ensuring that the molds are durable, precise, and capable of producing consistent parts without defects. Documentation throughout the design process is also crucial to ensure traceability and auditability for regulatory purposes.
Mold Durability and Longevity
Given the critical nature of medical devices, the molds used to manufacture these parts must be designed to last for thousands of cycles without degradation in performance. Designers should focus on ensuring that the mold materials are durable and resistant to wear and tear. This involves selecting high-quality, wear-resistant materials for the mold cavities and ensuring proper cooling and venting to reduce the risk of mold damage over time.
In addition, the design should account for easy maintenance and repair of the molds, as the ability to keep the molds in good condition will contribute to the overall efficiency of the production process and reduce downtime.
Part Design and Geometric Complexity
Medical parts often have complex geometries due to their intricate designs, which may include small features, undercuts, or delicate structures. Designers need to ensure that the mold design accommodates these complexities while maintaining part integrity. The design should also consider part ejection methods, minimizing stress on the part during removal, and ensuring that no deformation or damage occurs.
Designing for manufacturability is key to ensuring that the final parts are cost-effective to produce and meet quality standards. This may involve simplifying designs where possible or incorporating features such as ribs or gussets to reinforce parts and reduce material usage.
Cleanliness and Sterility
Medical devices often require a high level of cleanliness and sterility. Designers must consider how the mold design will affect the cleanliness of the final part. This includes ensuring that the mold can be easily cleaned and that no contaminants can be introduced during the molding process. The design of the mold should also take into account the need for minimal post-processing to avoid the introduction of foreign particles or contaminants.
Designing medical parts injection molds requires a combination of technical expertise, industry knowledge, and attention to detail. Designers must possess a strong understanding of CAD, material science, and injection molding technology while considering critical factors such as regulatory compliance, mold durability, part design complexity, and cleanliness. By keeping these considerations in mind, designers can create molds that not only meet the stringent requirements of the medical industry but also ensure that the medical devices produced are safe, reliable, and of the highest quality.
Development Process of Medical Parts Injection Molds: Challenges and Milestones
The development of medical parts injection molds has undergone significant evolution since its inception, driven by advances in materials, technology, and regulatory standards. From the early stages of simple mold designs to the highly sophisticated, precision-driven molds used in medical device manufacturing today, the journey has been marked by numerous innovations and challenges. In this section, we will explore the historical development of medical parts injection molds, highlighting key milestones and the challenges that have shaped their evolution.
Early Developments: The Birth of Injection Molding
The roots of medical parts injection molding trace back to the early 20th century, when the injection molding process itself was first introduced. Initially, injection molding was used to produce consumer goods, such as buttons and combs, using materials like Bakelite. However, as the medical field began to demand more precise and reliable components, the need for specialized molds emerged.
During this early period, medical device manufacturers faced limited material options, with most molds made from relatively simple metals. The first medical parts injection molds were used to produce basic components, such as syringes and IV components, but the technology was still in its infancy. The main challenge at this time was the lack of advanced materials that could meet the stringent requirements for medical applications, including durability, biocompatibility, and sterility.
The 1980s and 1990s: Advancements in Material Science and Precision
In the 1980s and 1990s, significant advancements in material science and precision engineering revolutionized the medical parts injection mold industry. The development of high-performance, medical-grade plastics, such as polycarbonate and polyethylene, opened up new possibilities for mold designers. These materials offered better resistance to chemicals, higher strength, and more flexibility, making them ideal for medical device production.
During this period, the rise of Computer-Aided Design (CAD) and Computer-Aided Manufacturing (CAM) technology allowed designers to create far more complex and precise molds. These innovations led to the development of molds capable of producing more intricate parts, such as micro components used in surgical tools, diagnostic devices, and implants. The precision offered by CAD technology also made it easier to ensure that the molds met the stringent regulatory requirements for medical devices.
However, this period was also fraught with challenges. Manufacturers faced increasing pressure to meet the rising demand for high-quality, sterilizable medical parts while complying with stricter regulatory standards. The introduction of ISO 13485, a quality management system standard for medical device manufacturing, added additional complexity to the design and production processes, pushing manufacturers to adopt more rigorous quality control practices.
The 2000s to Present: Sophistication and Regulatory Hurdles
The turn of the 21st century saw the further refinement of injection molding techniques, driven by advancements in automation, robotics, and materials science. These improvements enabled manufacturers to produce highly complex and customized medical components with greater speed and accuracy. The integration of automation into the molding process also helped reduce human error and improve consistency in production.
As the medical device industry grew, so did the complexity of the parts being produced. Today, medical parts injection molds are used to manufacture a wide array of devices, from tiny, intricate components used in diagnostics and surgical tools to large, durable parts used in life-saving equipment like ventilators and infusion pumps. These molds are designed with sophisticated features like multi-cavity molds, hot runner systems, and overmolding to enhance production efficiency and product quality.
Despite these advancements, several challenges remain. As medical devices become increasingly complex and feature intricate designs, manufacturers must contend with difficulties related to mold durability, material compatibility, and precision. The growing demand for customizable solutions has also placed pressure on manufacturers to develop molds capable of handling diverse shapes and sizes.
Challenges Encountered in the Development of Medical Parts Injection Molds
The development of medical parts injection molds has not been without its obstacles. Below, we outline some of the most significant challenges faced during their evolution.
Meeting Stringent Regulatory Requirements
One of the most persistent challenges in the development of medical parts injection molds has been meeting the ever-increasing regulatory requirements set by agencies such as the FDA, European Medicines Agency (EMA), and other global regulatory bodies. These regulations govern everything from the materials used in medical devices to the manufacturing processes, ensuring that products are safe, effective, and free from defects.
Manufacturers have had to continuously adapt their designs and processes to comply with these regulations. For example, molds used in the production of medical devices must meet strict sterilization and biocompatibility standards, which requires ongoing investment in testing, validation, and documentation. The complexity of regulatory compliance can increase costs and lead times for production, presenting challenges for manufacturers, especially in an increasingly globalized market.
Material Innovation and Selection
The evolution of medical-grade materials has been a major milestone in the development of medical parts injection molds, but selecting the right material for each application has always been a challenge. Over the years, medical-grade plastics have become more advanced, offering improved durability, resistance to chemicals, and biocompatibility. However, these materials often come with their own set of challenges, including higher costs, material sourcing issues, and the need for precise control over molding conditions to avoid defects like warping or uneven cooling.
With the constant introduction of new materials, designers must be able to quickly assess their suitability for various applications, including considering factors like moldability, strength, and sterility. Balancing the performance characteristics of the material with the economic realities of production remains a key challenge in the field.
Complex Part Design and Precision
The complexity of medical parts, especially in fields like microsurgery, diagnostics, and implants, has grown significantly over time. Designers face the challenge of creating molds that can produce highly detailed, intricate parts without compromising strength, functionality, or sterility. The need for precision is especially important, as even the slightest error in mold design or manufacturing can result in faulty parts that compromise patient safety.
Achieving the necessary precision often requires the use of advanced mold-making technologies, including multi-cavity molds, hot runner systems, and in some cases, 3D printing to produce prototypes. The challenge here is not only the technical difficulty of creating such molds but also ensuring that they are capable of maintaining their precision and durability over thousands of production cycles.
The development of medical parts injection molds has come a long way, from its humble beginnings to the highly sophisticated molds used in modern medical device production. Advances in materials science, precision engineering, and automation have driven significant progress, but challenges like regulatory compliance, material selection, and precision remain constant. As the medical industry continues to evolve and demand more complex and customized devices, the design and manufacturing of medical parts injection molds will continue to face new hurdles. Despite these challenges, the ongoing innovation in mold technology ensures that medical devices remain safe, effective, and reliable for patients worldwide.
FAQs about Medical Parts Injection Molds
Cavity and Core: These are essentially the male and female parts of the mold, which shape the external and internal surfaces of the molded part.
Runner System: This includes runners and gates that direct the melted plastic into the mold cavity.
Ejector System: This system includes pins and mechanisms to eject the finished part from the mold.
Cooling System: Channels and cooling lines to maintain the proper temperature of the mold.
Guide Pins and Bushings: These ensure precise alignment of the two halves of the mold.
Clamping Plates: These hold the mold together during the injection process.
The cost of an injection molded part depends on several factors, including the complexity of the part, the material used, the size of the production run, and the intricacy of the mold design. For small-scale production, the cost per part can be relatively high due to the initial mold manufacturing expense, which can range from a few thousand to tens of thousands of dollars. However, in high-volume production, the cost per part significantly decreases and can be as low as a few cents to a few dollars per part. Material costs, machine time, labor, and any post-processing required also contribute to the total cost.
Medical molding is a specialized form of injection molding that focuses on producing plastic components and devices used in the medical field. This type of molding adheres to strict standards and regulations for cleanliness, precision, and biocompatibility. Applications of medical molding include the production of syringes, catheters, surgical instruments, implantable devices, and diagnostic tools. It often involves the use of medical-grade plastics and operates in cleanroom environments to prevent contamination. The process also requires thorough validation and verification to ensure that the molded parts meet stringent medical industry requirements.
The lifespan of an injection mold varies widely based on factors such as the mold material, part complexity, maintenance practices, and the type of plastic being injected. Typically, a well-maintained steel mold can produce anywhere from tens of thousands to over a million parts. For high-volume production in industries such as automotive or consumer goods, molds made from hardened steel are commonly used, which can yield a higher number of cycles. Conversely, molds made from less durable materials like aluminum may be suitable for lower volume runs, offering a few thousand to tens of thousands of cycles before requiring refurbishment or replacement. Regular maintenance and care can significantly extend the life and efficiency of the mold.
Contact our professional team now for a same-day quote and risk-free project evaluation. Benefit from ISO 8 cleanrooms, advanced machines, and 12-hour fast response in medical injection molding.