A medical parts mold is a specialized tool used in the manufacturing of medical components. It shapes and forms medical devices and tools by injecting molten plastic into a mold cavity, which then cools to create the desired part. These molds are crafted with precision, particularly in the case of precision mold medical, to ensure the accurate dimensions and properties necessary for medical applications. Medical parts molds play a vital role in ensuring the quality and safety of medical devices. Their precision ensures that each part meets strict regulatory requirements, including FDA and ISO certifications. These molds are used in various medical applications, such as diagnostics, surgical tools, and medical devices, where reliability and consistency are essential for patient safety. Medical parts mold is used in injection molding to create high-quality, precise, lightweight medical devices from plastics, TPE, silicone, or metals.
Medical Parts Mold Price
When considering the cost of a medical parts mold, several key factors come into play that can influence the final price. These factors range from the complexity of the mold to the certifications required for medical-grade production. Understanding these factors is crucial for managing costs while maintaining high standards of quality and compliance.
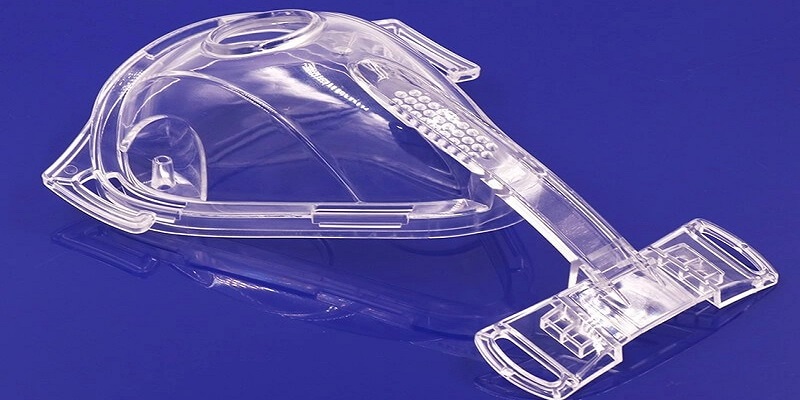
Factors Affecting Price
- Mold Complexity: The design of the medical parts mold is one of the most significant factors in determining price. Complex molds with multiple cavities or intricate features are more expensive to design and manufacture. For example, a multi-cavity mold, which produces several parts at once, will require more advanced technology and precise engineering than a single-cavity mold, driving up the cost.
- Material Used in Mold Construction: The materials used to create the mold also impact the price. Steel molds, for example, are more durable and can withstand high-volume production but are more expensive to produce than aluminum molds, which may be a more affordable option for low to medium-volume production.
- Volume Requirements: The size of the production run affects the cost of the medical parts mold. If you require only prototypes or small batches, the medical mold design and tooling may be simpler and more affordable. However, for large-scale production, higher precision and more durable molds are necessary, leading to increased costs.
- Cleanroom and FDA-Grade Certifications: Medical devices require a high level of cleanliness to meet regulatory standards, so molds must often be produced in a cleanroom environment. Molds that meet FDA standards for medical applications also come with a premium due to the additional testing, certification, and quality control required.
Cost-Saving Tips
- Opting for Modular Designs: Modular mold designs allow manufacturers to reuse components for different parts, reducing overall mold production costs. This design flexibility can lower the cost of creating new molds for different medical parts.
- Leveraging Automation to Lower Labor Costs: Automation in the mold production process can significantly reduce labor costs by streamlining the manufacturing steps. Automated processes, such as the medical injection molding process, can also improve consistency and reduce cycle times, resulting in overall savings in production.
- Partnering with Experienced Manufacturers for Efficient Production: Working with experienced manufacturers who specialize in medical parts molds can help optimize production processes. Their expertise allows for faster prototyping, design adjustments, and quicker turnaround times, ultimately leading to cost savings in both the short and long term. Partnering with these experts also ensures that regulatory compliance and industry standards are met without compromise.
By understanding these factors and tips, you can make more informed decisions when selecting a medical parts mold manufacturer and manage costs effectively while maintaining the highest quality standards.
Leading Medical Parts Mold Manufacturers
When selecting a manufacturer for your medical parts mold, it’s crucial to partner with a company that has a strong reputation and experience in the medical device industry. The quality and precision of the medical parts mold are paramount, especially given the strict regulatory standards for medical products. The following characteristics define top manufacturers in this space, ensuring they meet the highest standards of quality, safety, and compliance.
Characteristics of Top Manufacturers
- Proven Track Record in the Medical Industry: Leading medical parts mold manufacturers have a proven track record of success in producing high-quality medical components. They have experience working with a wide range of medical devices, from diagnostic tools to surgical instruments, ensuring that they are familiar with the unique challenges and requirements of the medical industry. A reputable manufacturer should provide case studies or examples of past projects demonstrating their expertise in creating precise, compliant medical parts.
- ISO Certifications (e.g., ISO 13485 for Medical Devices): Top medical parts mold manufacturers adhere to industry standards such as ISO 13485, which ensures they follow the required quality management systems for the design and manufacture of medical devices. This certification is critical as it demonstrates the manufacturer’s ability to meet stringent regulatory requirements, including the production of devices that must meet FDA guidelines. Manufacturers with this certification are committed to maintaining quality and traceability throughout the production process, which is essential for ensuring the safety and reliability of medical products.
- Use of Advanced Technologies Like Multi-Shot Molding and Insert Molding: Leading medical parts mold manufacturers employ advanced molding technologies to enhance precision, functionality, and efficiency. Multi-shot molding, for example, allows for the injection of different materials into a single mold cavity, enabling manufacturers to create complex, multi-material parts that are crucial for medical devices with multiple functions. Insert molding, which involves placing metal or other components inside the mold before injecting plastic, is also widely used in the medical field to create parts such as connectors, housings, and even needles, offering both strength and durability. Manufacturers that are skilled in these advanced techniques can produce innovative medical parts with superior performance and cost efficiency.
By selecting a manufacturer with these characteristics, you ensure that your medical parts mold is produced by a trusted partner who understands the intricacies of the medical device industry and can meet the necessary regulatory and quality standards.
Medical Parts Mold: Medical Injection Molding Companies
When choosing a medical injection molding company for your medical parts mold, it’s essential to select a partner with specialized expertise in the medical device industry. These companies are responsible for turning design concepts into functional, precise medical components, and their ability to meet strict regulatory standards and quality assurance protocols is crucial.
What Sets Them Apart?
- Expertise in Producing High-Precision Medical Parts: A key differentiator for leading medical parts mold manufacturers is their ability to produce high-precision parts consistently. The medical industry demands strict tolerances and intricate designs that ensure the safety, functionality, and longevity of medical devices. These companies are skilled in creating complex parts such as surgical tools, diagnostic devices, and implantable components that must meet tight dimensional specifications. Advanced technology like scientific molding, high-precision injection medical molding machine, and rigorous testing ensure the accuracy of each part.
- Access to Cleanroom Manufacturing Environments: Many medical injection molding companies maintain cleanroom environments for the production of medical parts molds to meet the stringent requirements of the medical industry. Cleanrooms minimize the risk of contamination and ensure that parts are manufactured in an environment that meets ISO Class 7 or Class 8 standards. This is particularly important for the production of medical components that will be used in sterile environments, such as surgical instruments or diagnostic devices. Cleanroom capabilities ensure that each mold produced complies with regulatory requirements and upholds the safety and performance standards needed in the medical field.
- Ability to Handle FDA and Industry-Specific Compliance: Medical injection molding companies that specialize in medical parts molds are well-versed in meeting FDA regulations and other industry-specific compliance standards. They ensure that all materials, processes, and finished products comply with the FDA’s Good Manufacturing Practices (GMP) and meet all required safety and performance standards. These companies play a critical role in ensuring that the final products are safe for patient use and meet the regulatory guidelines required for approval. A commitment to compliance and traceability ensures that every step of the production process is documented and auditable.
Services Offered
- Prototyping and Tooling: Medical molding companies offer prototyping services that allow clients to test designs before mass production. Using medical parts molds, these companies create functional prototypes that help identify any design flaws or issues early in the development process. The tooling services provided ensure that the molds used for mass production are precisely engineered for efficiency and cost-effectiveness, reducing the time and cost associated with design iterations.
- Mass Production with Traceability Systems: Once prototypes are validated, medical injection molding companies offer mass production services that deliver large quantities of high-quality medical parts molds. Traceability systems are integrated into the production process to monitor and document every part produced. This ensures that all parts are fully traceable from raw material sourcing through to the final product. Traceability is crucial in the medical industry for ensuring accountability, managing recalls, and maintaining compliance with regulatory standards.
- Secondary Processes (e.g., Assembly, Packaging): Medical injection molding companies often offer a full range of secondary services to complement their molding operations. These may include assembly, where individual parts are combined into finished products, and packaging, where products are prepared for shipment under controlled conditions to ensure they remain sterile and free from contamination. These services allow for a streamlined, turnkey solution for manufacturers needing end-to-end support for their medical parts mold production.
Medical Parts Mold: Insert Molding for Electronics in Medical Applications
Insert molding is an essential process in the production of medical parts molds, particularly for medical devices that require integration with electronic components. This process involves embedding metal or other electronic components into plastic during the molding process, creating a single, reliable part that combines both plastic and electronic elements. Insert molding is widely used in medical applications where precision and performance are crucial.
Definition and Process
- Overview of Combining Plastic with Electronic Components: Insert molding is a manufacturing process that involves placing pre-formed metal or electronic components, such as connectors, into a mold cavity, where plastic is then injected around them. Molding definition medical refers to the precise molding process used to create medical device components that meet the stringent requirements of the healthcare industry. The result is a single part that combines the durability of metal or other materials with the versatility and formability of plastic. This process is highly beneficial for medical devices that need to withstand harsh environments, offer high performance, and be reliable in critical applications.
- Examples: EKG Connectors, Pacemaker Components, and Needle Assemblies: Insert molding plays a crucial role in creating complex, high-precision medical components. For example, EKG connectors that interface with monitoring equipment are often produced using insert molding, allowing for the integration of both electronic and plastic parts into a single unit. Similarly, pacemaker components that require electrical leads and housing often use insert molding to achieve both the necessary electronic functionality and biocompatibility. Needle assemblies, used in medical procedures like injections and blood collection, also benefit from insert molding, as it allows for the integration of metal needles and plastic components like hubs or caps, all within one seamless part.
Advantages in Medical Devices
- Improved Durability and Functionality: The combination of plastic with metal or electronic components via insert molding provides significant improvements in the overall durability and functionality of medical devices. For instance, when metals like stainless steel or copper are combined with high-strength plastics, the resulting component offers superior resistance to wear, corrosion, and stress, making it ideal for medical devices that require long-term reliability. This enhanced durability is crucial for devices such as pacemakers or surgical tools, where failure is not an option.
- Reduction of Manual Assembly, Leading to Higher Efficiency and Consistency: One of the key advantages of using medical parts mold insert molding is the reduction of manual assembly. With insert molding, the electronic components are already embedded in the plastic during the molding process, which significantly reduces the need for additional assembly steps. This leads to a more streamlined manufacturing process, reduces labor costs, and enhances consistency and repeatability. For example, the integration of EKG connectors or pacemaker components with minimal manual handling ensures that each part produced meets the same high standards, improving quality control and reducing the risk of human error in the assembly line.
Insert molding also ensures that the components have better adhesion between the plastic and metal or electronic parts, further improving the reliability of the final product. This is especially important in medical applications, where device performance, safety, and durability are non-negotiable.
Benefits of Advanced Medical Parts Mold Manufacturing
The process of advanced medical parts mold manufacturing offers several significant benefits, particularly in ensuring the production of high-quality, reliable, and cost-efficient medical components. High precision tools for medical device manufacturing play a key role in achieving these benefits, as they ensure the accuracy and consistency required for medical devices. Precision, cost efficiency, and compliance with industry standards are essential in the manufacturing of medical devices, which require exacting standards due to their critical application in healthcare.
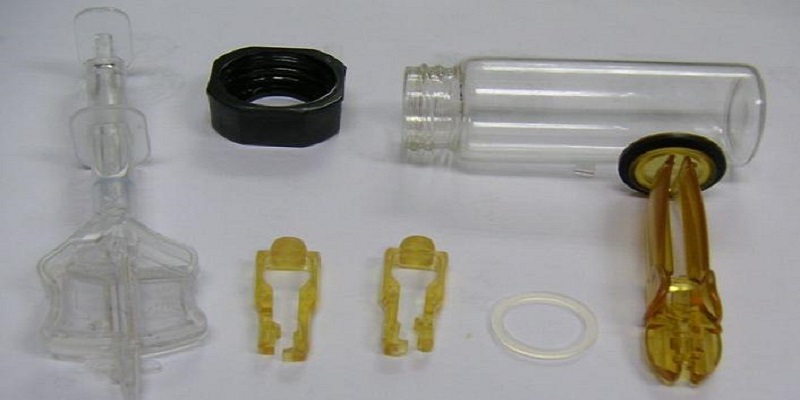
Precision and Reliability
- Importance of Maintaining Tolerances within ±25 Microns: In the medical device industry, the precision of each part is crucial for the safety and functionality of the end product. Medical parts mold manufacturing must ensure that parts are created with extremely tight tolerances, often within ±25 microns, to meet medical molding requirements and ensure proper fit, performance, and compatibility. Whether it’s a surgical instrument, a diagnostic tool, or a pacemaker component, precision in molding ensures that each part functions as intended, without fail. This level of precision is vital to meet the stringent quality standards required by the medical industry, ensuring that even the smallest parts can withstand stress and perform accurately in critical applications.
- Techniques Like Scientific Molding to Optimize Results: One technique used to achieve the required precision in medical parts mold manufacturing is scientific molding. Scientific molding involves closely controlling and optimizing every aspect of the injection molding process, including temperature, pressure, and material flow. By using this data-driven approach, manufacturers can ensure that the molding process is highly consistent, reducing defects and variations in the final parts. Scientific molding also helps to ensure repeatability in mass production, making it an essential technique in the creation of high-quality, reliable medical components that meet regulatory standards.
Cost Efficiency
- Automation to Reduce Cycle Times and Waste: Another benefit of advanced medical parts mold manufacturing is the potential for automation to streamline the production process. Automation reduces the need for manual labor, thereby lowering labor costs and reducing the risk of human error. In addition, automated systems can significantly cut down on cycle times, meaning that more parts can be produced in a shorter amount of time. This is particularly beneficial in high-volume production scenarios, where speed and efficiency are key to meeting demand while maintaining cost-effectiveness. Additionally, automated systems often incorporate advanced monitoring and feedback loops, helping to further reduce material waste by ensuring that each part is produced with minimal scrap or excess material.
- Reusable Molds for Long-Term Savings in High-Volume Production: The use of reusable molds is another important cost-saving strategy in medical parts mold manufacturing. In high-volume production, molds are often used repeatedly, which makes the initial cost of creating a mold more economical over time. By using high-quality, durable molds, manufacturers can achieve significant savings in the long term, as these molds can withstand many cycles of production without degradation in quality. This makes it possible to maintain high consistency and quality across large quantities of parts, while keeping production costs under control.
Compliance and Quality Assurance
- Use of FDA-Approved Materials: Compliance with regulatory standards is a cornerstone of medical parts mold manufacturing. Medical devices and components must adhere to strict regulations set by agencies like the FDA to ensure that the materials used are safe for use in healthcare environments. Advanced molding processes incorporate FDA-approved materials, such as biocompatible plastics and medical-grade metals, to meet these requirements. Using approved materials also ensures that parts are non-toxic, durable, and suitable for their intended medical applications, whether they are inserted into the body, used for diagnostics, or applied in surgical procedures.
- Adherence to ISO and GMP Standards: To ensure consistent quality and safety, manufacturers of medical parts mold components must adhere to international standards such as ISO 13485 for medical devices and Good Manufacturing Practices (GMP). These standards outline the best practices for quality management systems, ensuring that each step of the manufacturing process is thoroughly controlled and documented. By adhering to these rigorous standards, manufacturers can guarantee that the medical parts produced meet the highest levels of quality, safety, and performance. This adherence to global standards is critical in maintaining regulatory compliance and ensuring that devices are safe and effective for use in healthcare settings.
Medical Parts Mold: Medical Parts Plastic Injection Molds
Medical parts plastic injection molds are integral to the production of a wide range of medical components. This specialized molding process involves injecting molten plastic into a mold cavity, where it cools and solidifies into the desired shape. It is one of the most common methods used in the manufacturing of medical devices, including syringes, diagnostic equipment, and surgical tools.
Precision and Versatility in Medical Applications
The use of plastic injection molding for medical parts mold manufacturing allows for the production of highly precise components. Medical parts often require detailed and complex geometries that can be easily achieved with this method. The ability to produce intricate features, such as thin walls, undercuts, and fine details, makes plastic injection molding ideal for creating complex medical devices. Furthermore, the process is capable of producing parts with excellent dimensional accuracy, which is crucial for medical applications where small variations can affect functionality and safety.
Material Selection and Biocompatibility
In the medical industry, the choice of material for medical parts mold manufacturing is critical. Medical-grade plastics, such as polycarbonate (PC), polypropylene (PP), and polyethylene (PE), are commonly used in injection molding due to their durability, biocompatibility, and resistance to sterilization processes. These materials ensure that the final components are not only safe for patient use but also capable of withstanding repeated exposure to harsh medical environments, such as high temperatures and chemical sterilization. The use of biocompatible materials is essential to meet regulatory requirements and to avoid any adverse reactions when the parts are in contact with patients.
High-Volume Production and Cost Efficiency
Another advantage of using plastic injection molds for medical parts mold manufacturing is the ability to produce large quantities of parts efficiently. The process is highly suitable for high-volume production runs, which makes it a cost-effective solution for manufacturers. Once the mold is designed and built, it can be used repeatedly to produce identical parts, allowing for fast production cycles and reduced unit costs. This makes plastic injection molding an excellent choice for mass-produced medical components, such as IV connectors, plastic housings for medical devices, and even components for drug delivery systems.
Precautions for Selecting Medical Injection Molding Materials for Medical Parts Mold
Selecting the right materials for medical parts mold manufacturing is a critical step that directly impacts the safety, performance, and durability of medical devices. This guide outlines key considerations, including biocompatibility, durability, sterilization resistance, chemical stability, thermal stability, regulatory compliance, application-specific functionality, and ease of processing. Each point is detailed to help manufacturers make informed decisions when choosing materials for injection molding in the medical industry.
Biocompatibility:
Biocompatibility is critical to ensure that the materials used in medical parts mold do not cause adverse biological reactions when in contact with human tissue or fluids. Materials should undergo rigorous testing, such as cytotoxicity, sensitization, and irritation assessments, to meet biocompatibility standards like ISO 10993 or FDA guidelines. This ensures patient safety and product reliability for both short-term and long-term medical applications.
Durability:
Medical components are often subjected to repeated use and mechanical stress. The selected material must resist wear, impact, and fatigue to maintain its performance over time. For example, devices like surgical instruments or implants require high mechanical strength and toughness to handle repeated mechanical loading without failure.
Resistance to Sterilization:
Medical parts must endure various sterilization methods, such as autoclaving (high-pressure steam), ethylene oxide gas, gamma radiation, or chemical sterilization. Materials should retain their mechanical, thermal, and aesthetic properties after repeated sterilization cycles to ensure reliability and safety throughout the product’s lifespan.
Chemical Resistance:
Medical devices frequently come into contact with strong disinfectants, cleaning agents, and bodily fluids. The chosen material must be chemically stable to avoid degradation, swelling, or discoloration, which could compromise the functionality or sterility of the medical part. Common materials like polypropylene (PP) or polycarbonate (PC) are often selected for their chemical resistance.
Thermal Stability:
Many medical applications involve exposure to elevated temperatures during sterilization or use. Materials need to have a high heat deflection temperature (HDT) and retain their structural integrity under these conditions. For example, polycarbonate is a popular choice for its thermal stability and ability to withstand autoclave sterilization.
Regulatory Compliance:
Materials must adhere to strict regulatory standards for medical devices. These include ISO certifications, such as ISO 10993 for biocompatibility, and compliance with FDA requirements. Manufacturers must document and validate material properties to meet regional and international regulatory standards, ensuring the product is safe for patient use and meets market requirements.
Functionality and Application Needs:
The material must align with the specific functional requirements of the medical device. For example, transparency may be critical for diagnostic tools, while flexibility is essential for catheters. Understanding the application environment, such as exposure to mechanical forces, chemical agents, or sterilization, helps tailor material selection to meet design and performance goals.
Ease of Processing:
The material should be compatible with the injection molding process to ensure efficient manufacturing. Properties like melt flow rate, shrinkage, and cooling behavior affect mold design and production efficiency. Materials that process easily can reduce cycle times, minimize defects, and improve overall cost-effectiveness in production.
Plastic Materials Used in Medical Device Injection Molding for Medical Parts Mold
Selecting the right plastic materials for medical device injection molding is crucial to ensure the safety, performance, and reliability of the final product. The materials used for medical parts mold manufacturing must meet stringent medical industry standards, including biocompatibility, sterilization resistance, and durability. Below is a detailed introduction to commonly used plastic materials, their characteristics, and their advantages.
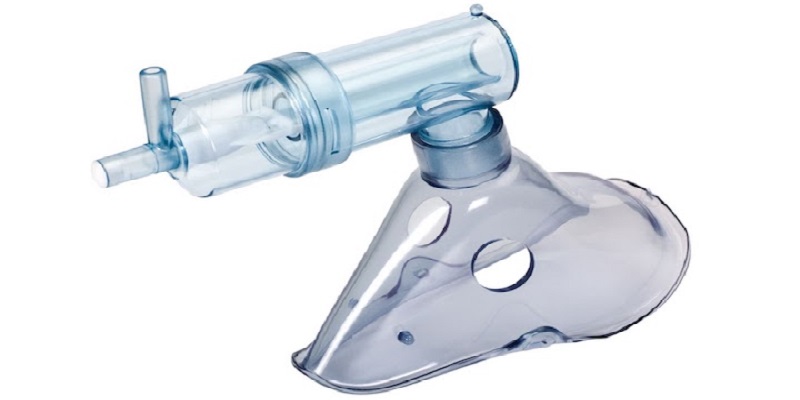
Polycarbonate (PC)
Polycarbonate is widely used in medical parts mold manufacturing due to its excellent strength, transparency, and ability to withstand repeated sterilization processes.
Characteristics of Polycarbonate:
- High impact resistance and durability.
- Excellent optical clarity, making it ideal for transparent medical devices.
- High thermal stability, suitable for autoclave sterilization.
- Lightweight yet strong.
Advantages:
- Durable under mechanical stress and extreme environments.
- Resistant to repeated sterilization without degradation.
- Highly versatile, suitable for a wide range of medical applications, including surgical instruments, diagnostic devices, and drug delivery systems.
Polypropylene (PP)
Polypropylene is a popular choice for disposable and reusable medical devices due to its low cost, chemical resistance, and versatility.
Characteristics of Polypropylene:
- Lightweight and flexible.
- High chemical and moisture resistance.
- Withstands low to moderate thermal exposure.
- Biocompatible and non-reactive.
Advantages:
- Cost-effective for high-volume production.
- Suitable for devices in contact with fluids or chemicals.
- Used in syringes, IV components, and laboratory equipment.
- Recyclable and environmentally friendly.
Polyethylene (PE)
Polyethylene is valued for its flexibility, chemical resistance, and ease of processing in injection molding.
Characteristics of Polyethylene:
- High flexibility and toughness.
- Excellent resistance to chemicals and low moisture absorption.
- Available in different densities (LDPE, HDPE) for varied applications.
Advantages:
- Ideal for tubing, catheter components, and flexible medical parts.
- Biocompatible and safe for patient use.
- Easy to sterilize and process.
Acrylonitrile Butadiene Styrene (ABS)
ABS combines strength, rigidity, and cost-effectiveness, making it ideal for non-critical medical components.
Characteristics of ABS:
- High impact strength and rigidity.
- Easy to mold and process.
- Moderate chemical resistance.
Advantages:
- Affordable and suitable for complex designs.
- Used in equipment housings, enclosures, and non-critical medical parts.
- Can be blended with other materials for enhanced properties.
Thermoplastic Elastomers (TPE)
TPE is preferred for applications requiring flexibility, comfort, and durability.
Characteristics of TPE:
- High elasticity and flexibility.
- Resistant to chemicals and sterilization processes.
- Soft-touch feel and adaptable to various hardness levels.
Advantages:
- Used for seals, gaskets, and wearable medical devices.
- Enhances patient comfort and usability.
- Retains properties after repeated sterilization.
Polysulfone (PSU)
Polysulfone is selected for its superior thermal and chemical resistance, ideal for critical medical applications.
Characteristics of Polysulfone:
- High strength and rigidity.
- Exceptional resistance to high temperatures and harsh chemicals.
- Transparent with good biocompatibility.
Advantages:
- Used for sterilizable components like surgical trays and dialysis parts.
- Maintains integrity under extreme conditions.
- Long service life for durable medical devices.
Polyetheretherketone (PEEK)
PEEK is a high-performance plastic used in demanding medical applications, such as implants.
Characteristics of PEEK:
- Extremely high strength and toughness.
- Excellent thermal and chemical resistance.
- Biocompatible and suitable for long-term implantation.
Advantages:
- Used in orthopedic implants, dental devices, and surgical instruments.
- Withstands sterilization and long-term exposure to body fluids.
- Lightweight and corrosion-resistant.
Advantages for These Materials
- Safety and Biocompatibility: All materials meet stringent regulatory requirements for medical use.
- Durability: Resistant to wear, chemicals, and sterilization, ensuring long-term performance.
- Versatility: Suitable for various applications, from disposable components to critical implantable devices.
- Cost-effectiveness: Many materials allow for economical high-volume production.
- Ease of Processing: Optimized for efficient and precise injection molding processes.
These materials ensure that medical parts molds produce high-quality, reliable medical devices tailored to patient safety and industry standards.
What is Medical Micro Molding in Medical Parts Mold Manufacturing
Medical micro molding is a niche segment within the medical plastic injection molding industry, designed to create extremely small and precise components essential for advanced medical devices. This process involves fabricating parts with microscopic dimensions, often weighing only a fraction of a gram, and with tolerances measured in microns. Medical micro molding plays a critical role in producing components for minimally invasive devices, surgical tools, implants, and drug delivery systems. Its high precision and strict quality control make it indispensable for the medical industry.
Key Considerations in Medical Micro Molding for Medical Parts Mold
Medical micro molding presents unique challenges due to its precision requirements and the small scale of components. Below are four crucial factors to ensure success in this highly specialized process.
Clean Room Meets ISO Standards 100k (ISO Class 8) and 10k (ISO Class 7)
A clean manufacturing environment is essential for medical micro molding to prevent contamination and meet strict medical standards.
- ISO Class 8 and ISO Class 7 Standards:
Micro molding must be performed in clean rooms that comply with ISO Class 8 (100k) and ISO Class 7 (10k) to control particle counts, ensuring a sterile and contaminant-free production process. - Importance of Clean Rooms:
These controlled environments are critical for producing parts used in sensitive applications, such as implants or components in direct contact with bodily fluids. They also minimize risks of defects caused by environmental particles. - Implementation:
Clean rooms should be equipped with advanced filtration systems, proper airflow management, and robust cleaning protocols to maintain sterility throughout production.
Gates and Ejection
The design and execution of gates and ejection systems are pivotal in medical micro molding to ensure precision and avoid damage to micro-sized parts.
- Gate Design:
Gates must be extremely small to suit the micro-scale components. Proper gate placement ensures consistent filling, avoids material degradation, and minimizes stress concentrations on the part. - Ejection System:
Ejection requires delicate handling to avoid deformation or breakage of the tiny components. Special ejection mechanisms, such as vacuum or custom pin systems, are often used to safely remove parts from the mold. - Challenges:
Achieving uniform flow through micro gates while ensuring smooth ejection demands advanced engineering and precision mold design.
Standard Wall Thickness and Size Doesn’t Apply
Unlike traditional injection molding, medical micro molding operates without adhering to conventional wall thickness and size constraints.
- Thin Walls and Small Sizes:
Micro components often have walls that are a fraction of a millimeter thick. Maintaining uniformity and structural integrity is challenging at these scales. - Unique Part Design:
Designers must tailor components for manufacturability, considering flow dynamics, cooling rates, and the properties of the chosen material. Traditional design guidelines often require adaptation or complete revision. - Process Adjustments:
High-precision molding machines with micro-scale capabilities are essential to accommodate the intricate geometries and minute dimensions.
Stretching Complexity
The complexity of medical micro molding extends beyond standard injection molding, requiring a holistic approach to design, material selection, and process control.
- High Precision:
Tolerances in micro molding are often measured in microns, necessitating precise control over every stage of production, from mold fabrication to injection parameters. - Material Behavior:
At micro scales, material behavior, such as flow and shrinkage, becomes less predictable and requires in-depth analysis and testing to achieve optimal results. - Advanced Equipment:
Specialized molding machines with capabilities for extremely high injection pressures and precise temperature control are critical to manage the complexities of micro-scale components. - Application-Specific Designs:
Micro molding often involves creating highly complex geometries for specific applications, such as bioresorbable stents or microfluidic devices, requiring custom solutions and extensive prototyping.
Medical micro molding is an essential technology for producing miniature, high-precision components in medical parts mold manufacturing. This process requires adherence to strict clean room standards, innovative gate and ejection designs, adjustments to conventional molding rules, and advanced techniques to handle its inherent complexity. By addressing these factors, manufacturers can ensure the production of reliable, high-quality micro medical components suited to critical applications.
FAQs about Medical Parts Mold
In the medical industry, the term “mold” typically refers to a “molding” process used to create medical parts or components. While there is no specific “medical” term for mold, the process of molding is essential in manufacturing medical devices and parts. This involves using a mold, which is a hollow cavity or form into which material (usually plastic or metal) is poured or injected to create a specific shape or part. In medical applications, molds are used to produce precise, high-quality components such as surgical instruments, diagnostic tools, and prosthetics. The term “mold” itself can be synonymous with “die” or “form” in this context, referring to the tool used to shape medical parts.
Medical molding refers to the process of creating medical device components and parts using various molding techniques such as injection molding, blow molding, or compression molding. This process is crucial for manufacturing high-precision medical devices that must meet strict safety and regulatory standards. Medical molding is used to create everything from syringes and diagnostic instruments to implantable devices and surgical tools. The materials used in medical molding must be biocompatible, durable, and capable of withstanding sterilization processes. Molding ensures that medical parts have the necessary shape, strength, and functionality while adhering to industry regulations such as FDA approval and ISO certifications. Precision and reliability are critical, as even minor deviations can compromise the safety or effectiveness of medical devices.
The term “molded” in the medical context refers to the process by which materials, usually plastics, are shaped using a mold or die to form medical parts or components. When a medical part is described as “molded,” it means that the component was created through a specific molding process, like injection molding, where material is injected into a mold cavity, then cooled and solidified to form the desired shape. Molding is a standard method for manufacturing a wide range of medical devices because it allows for high precision and the ability to produce complex parts that meet stringent regulatory standards. This molded process ensures that the medical components are consistent, reliable, and ready for use in applications like diagnostics, surgeries, and patient care.
Mold parts refer to the individual components that make up the complete mold used in the molding process. These parts are designed to create the cavity or shape into which the molding material (plastic, metal, etc.) is injected or poured. In the context of medical device manufacturing, mold parts are crucial in shaping components such as surgical instruments, diagnostic tools, and packaging for medical products. The main mold parts include the core, cavity, ejector pins, and sprues. Each part is carefully engineered to ensure precise shaping of the final medical part. Mold parts must be made from high-quality, durable materials that can withstand the high pressures and temperatures involved in molding processes while maintaining their structural integrity over multiple production cycles. The reliability and quality of mold parts directly influence the final product’s consistency, safety, and performance.
Contact our professional team now for a same-day quote and risk-free project evaluation. Benefit from ISO 8 cleanrooms, advanced machines, and 12-hour fast response in medical injection molding.