Medical parts mold companies play a crucial role in the healthcare industry, providing the high-precision components used in medical devices, diagnostics, and surgical instruments. These companies, along with leading medical plastic parts companies, specialize in medical injection molding, a process that ensures both safety and accuracy in the production of critical healthcare products. High-quality medical injection molding is essential for meeting strict regulatory standards, such as FDA requirements, and ensuring the functionality and reliability of medical devices. This blog focuses on highlighting top medical parts mold companies around the world, including those based in regions like China and the USA, helping businesses find reliable partners both locally and globally for their medical manufacturing needs. Medical parts mold companies specialize in precise, efficient injection molding for the medical and pharmaceutical industries, with expertise in product design and assembly.
Low-Volume to High-Volume Production Capabilities
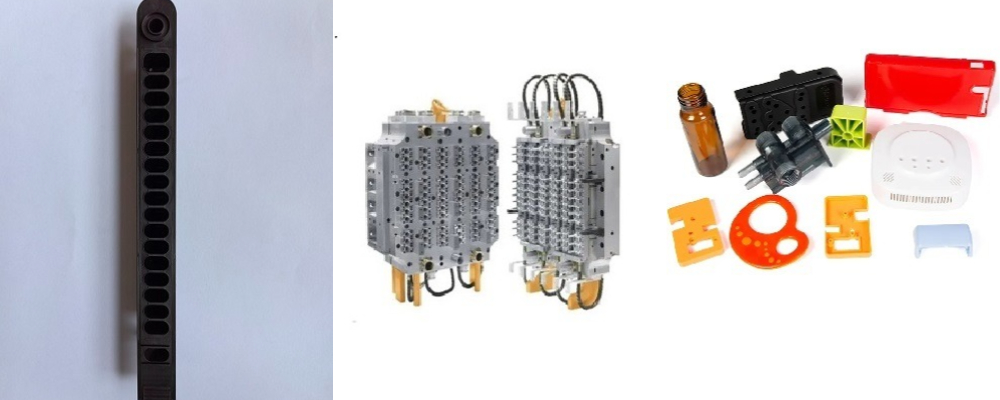
Attributes | Details |
---|---|
Place of Origin | Dongguan, Guangdong, China |
Brand Name | LY Medical Injection Mold |
Product Name | Medical Injection Molding |
Molding Mode | Plastic Injection Mold |
Product Material | Plastic |
Surface Treatment | Custom Surface Texture |
Features | High Precision |
Color | Customized |
Size | Customized |
Length | Customized |
Service | OEM ODM |
Processing Service | Molding, Cutting |
Logo | Customized Logo Acceptable |
Application | Medical Grade |
Certification | ISO9001 |
Tolerance | 0.01-0.05mm |
Packing Details | Outer Packaging Carton Inner Packaging According to Customer Requirement |
Port | According to Your Requirement |
What are Medical Parts Mold Injection and How Do They Work?
Medical injection molding is a specialized manufacturing process used to create high-precision parts for medical devices and components. Unlike standard molding, which is commonly used in automotive and consumer products, medical injection molding requires a higher level of accuracy, clean manufacturing environments, and stringent compliance with regulatory standards to ensure the safety and performance of medical devices.
Medical injection molding involves injecting molten plastic or other materials into a mold to form components that are used in medical devices. Molding definition medical refers to the precise process of shaping materials into parts that meet the high standards required in the healthcare industry. The key difference from standard molding lies in the materials used, the required tolerances, and the environmental controls. Medical parts mold companies must adhere to stringent guidelines to ensure the parts are biocompatible, durable, and able to meet the exacting demands of the healthcare industry.
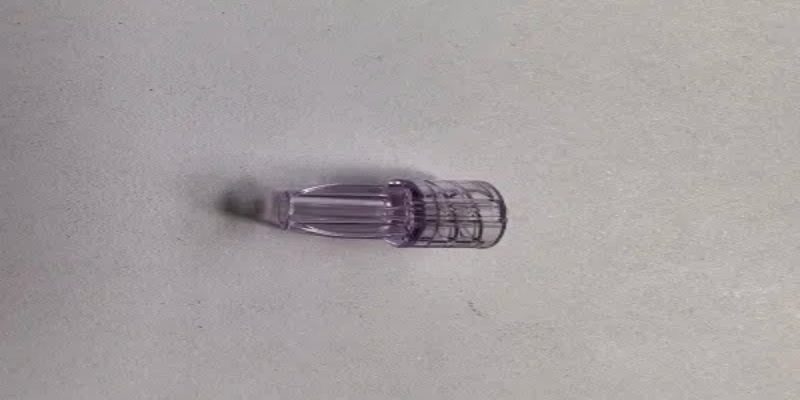
Medical Parts Mold Injection Process
The medical injection molding process begins with the creation of a precise mold, typically made of high-quality steel or aluminum. Materials, including medical-grade plastics and elastomers, are then heated until molten and injected into the mold under high pressure. This process requires the use of advanced technologies such as ISO clean rooms to prevent contamination and to comply with FDA standards for medical devices. An essential component of this process is medical molding validation, which ensures that the molding process itself consistently produces parts that meet all regulatory and safety standards. Medical parts mold companies validate each step of the molding process to ensure the final products are free of defects, meet biocompatibility requirements, and adhere to the necessary quality control measures.
Medical Parts Mold Injection Applications
Medical injection molding is used to create a wide range of components for medical devices. Common applications include:
- Syringes and needles: These require high precision to ensure correct dosing and safety during use.
- Catheters: Molding technology is used to create flexible, biocompatible tubing for use in various medical procedures.
- Diagnostic tools: Including components for blood testing equipment, diagnostic kits, and imaging devices.
- Implants and surgical instruments: Many life-saving implants and tools rely on injection molded components for durability and accuracy.
The high precision and reliability offered by medical parts mold companies are essential for the functionality and safety of these devices. Through advanced molding techniques, these companies ensure that critical medical products meet the demanding standards of the healthcare industry.
Advantages of Medical Parts Mold Injection
Injection molding plays a crucial role in the production of medical plastic products by offering numerous benefits that directly contribute to the effectiveness, cost-efficiency, and quality of medical devices. From customization to material selection, the process ensures that medical products meet stringent standards and perform reliably. Below, we explore these advantages from multiple perspectives to highlight how injection molding improves the manufacturing of medical products.
Customization
Injection molding technology is a highly versatile process, especially when it comes to manufacturing medical plastic products. It allows for a high degree of customization, ensuring that each product meets specific design requirements. This capability is particularly beneficial in producing diverse medical components such as knobs, housings, casings, and wearable medical technologies.
With injection molding, manufacturers can create intricate designs with undercuts, complex geometries, and tailored features that meet the needs of both the medical device and its intended use. This flexibility ensures that various customer requirements can be fulfilled with precision and efficiency, making it a top choice for custom medical device production.
Cost Optimization
One of the most significant advantages of injection molding in medical plastic product manufacturing is cost optimization. By enabling mass production of components in a highly efficient manner, injection molding reduces the overall production cost. The process minimizes material waste and ensures the consistent, high-volume output of medical components.
Additionally, the compact nature of the injection molding process means fewer resources are required, and time-consuming manual labor is reduced. This efficiency not only lowers direct costs for manufacturers but also helps buyers save money across the entire production process, making it an economically viable option for large-scale medical product manufacturing.
Accuracy
When it comes to manufacturing medical devices, accuracy is non-negotiable. Even the slightest flaw in a medical product can have life-threatening consequences. Injection molding provides unmatched precision, ensuring that every component meets strict medical industry standards. Medical parts mold companies specializing in injection molding are equipped to deliver the high levels of accuracy required for medical applications.
Through precise control of the injection molding process, manufacturers can achieve the desired tolerances, ensuring that every medical part functions as intended. This precision is vital for maintaining the reliability and safety of medical devices, where even minor defects can lead to severe consequences.
Material Selection
Injection molding offers a wide range of materials that are ideal for manufacturing medical products. Medical-grade plastics, such as silicone, polycarbonate, polyethylene, and polypropylene, are commonly used in this process. These materials are lightweight, biocompatible, durable, and easily handled, making them perfect for the production of medical devices.
The flexibility in material selection allows manufacturers to choose the best material for each application, ensuring optimal performance and safety for end-users. These materials also meet regulatory standards for biocompatibility, ensuring that medical products are safe for use in the human body or in sensitive medical environments.
Durability
Medical plastic products produced through injection molding are known for their exceptional durability. These components are designed to withstand harsh conditions, vibrations, and demanding environments without compromising their integrity. Durability is especially crucial for medical devices, which must maintain their functionality even under extreme conditions.
Injection-molded medical products are resistant to cracking, breaking, or shattering, ensuring that they perform reliably over an extended period. Whether the product is exposed to wear and tear, sterilization cycles, or fluctuating temperatures, the durability of injection-molded plastic parts ensures they remain operational, reducing the need for frequent replacements and enhancing the product’s lifecycle.
Sterilization
Sterilization is a vital consideration in medical product manufacturing, and injection molding helps improve both the strength and durability of medical devices. When using medical-grade plastics, injection molding ensures that the molded parts can endure rigorous sterilization processes, such as autoclaving, without degradation.
The controlled process of injection molding helps enhance the material’s ability to resist wear and retain its structural integrity, even after repeated sterilization cycles. This is particularly important in the medical field, where devices must meet strict sterilization requirements to ensure patient safety and product effectiveness.
Shortening Time
One of the key benefits of injection molding is its ability to shorten product development time. The technology allows for faster production of prototypes and final products, reducing the time it takes to bring a medical product to market. The high efficiency of injection molding ensures that manufacturers can quickly respond to customer needs, making it ideal for rapidly evolving medical fields.
Furthermore, the precise nature of injection molding helps minimize errors, ensuring that fewer revisions are necessary during the development process. This not only speeds up production but also reduces the likelihood of costly mistakes, allowing medical products to reach the market more quickly and reliably.
Injection molding offers numerous advantages in the production of medical plastic products, from customization and material selection to durability and cost optimization. These benefits make it the preferred manufacturing process for medical device companies that require high-quality, precise, and cost-effective solutions.
Why Choose Medical Parts Mold Companies for Your Medical Device Manufacturing?
Choosing the right medical parts mold company is crucial for ensuring that medical devices meet both safety and performance standards. The healthcare industry demands precision, high-quality materials, and strict regulatory compliance, which only specialized medical parts mold companies can provide. Below are the key reasons why partnering with a reputable medical parts mold company is essential for success in medical device manufacturing.
Precision and Quality
Medical devices, such as syringes, implants, and diagnostic equipment, require exceptional precision to ensure proper functionality and patient safety. Even minor errors in the molding process can result in defects that could jeopardize a patient’s health or the performance of the device. Medical parts mold companies have the advanced tools and technologies needed to create precision mold medical parts with tight tolerances in their medical parts injection molds. These companies invest in high-tech equipment like precision injection molding machines, as well as controlled environments such as ISO clean rooms, to ensure each part is manufactured with accuracy. The result is high-quality, reliable medical components that meet the rigorous demands of the healthcare industry.
Regulatory Compliance
Regulatory standards in the medical field are strict and ever-evolving, requiring manufacturers to meet high levels of compliance. For instance, medical parts mold companies must adhere to FDA regulations for medical devices and ISO certifications, such as ISO 13485, which governs quality management systems for medical device manufacturing. These standards ensure that the manufacturing processes are continually assessed, allowing for early detection of potential issues. cGMP (current Good Manufacturing Practice) is also essential for medical molding to guarantee that devices are produced under controlled conditions. Choosing a company that follows these regulations helps mitigate risks, minimize recalls, and ensure patient safety.
Material Selection
The materials used in medical devices must be safe, durable, and capable of withstanding various physical and chemical stresses. Medical parts mold companies specialize in selecting and using biocompatible materials that comply with healthcare industry standards. Medical-grade plastics, elastomers, and other polymers are commonly used to create components that are resistant to wear, stress, and potential contamination. These materials must also be compatible with sterilization processes, which is critical for many medical products. The use of high-quality materials ensures that the final product is not only functional but also safe for patient use, reducing the risk of complications and enhancing the longevity of the device.
By partnering with experienced medical parts mold companies, manufacturers can ensure that their products meet these stringent requirements, helping to bring safe, effective, and reliable medical devices to the market.
Top Medical Parts Mold Companies & Manufacturer
When selecting a medical parts mold company, it is essential to choose a supplier that excels in precision, compliance, and innovation, particularly in producing OEM medical plastic parts. Several companies across the globe are recognized for their expertise in medical injection molding, offering cutting-edge solutions for a wide range of medical device applications.
FUJIU Medical Injection Mold
FUJIU Medical Injection Mold is a leading provider specializing in OEM contract manufacturing for the medical device industry. With years of experience in producing high-precision plastic consumables, we excel in manufacturing components for diagnostic kits, medical equipment, and other healthcare devices. We operate state-of-the-art Class 8 clean rooms, ensuring a controlled environment that meets stringent industry standards. Additionally, we adhere to ISO 13485, FDA regulations, and other global quality standards, making us a reliable partner for medical device manufacturers. Our commitment to quality control and precise manufacturing ensures the production of safe and effective medical components that meet all necessary regulatory requirements.
At FUJIU Medical Injection Mold, we exemplify the qualities that make medical parts mold companies stand out: precision, compliance with regulations, and the use of advanced technology to produce high-quality medical components. We also offer double injection plastics for medical parts wholesale, further enhancing the customization and durability of components. By partnering with these leaders, manufacturers can ensure that their medical devices meet the highest standards of safety, performance, and reliability.
How to Find the Best Medical Parts Mold Companies Near You
Finding the best medical parts mold companies near you requires a combination of research, networking, and evaluating potential partners based on their expertise, capabilities, and reputation. Here are some key methods to help you identify local medica plastic parts suppliers that meet your medical device manufacturing needs.
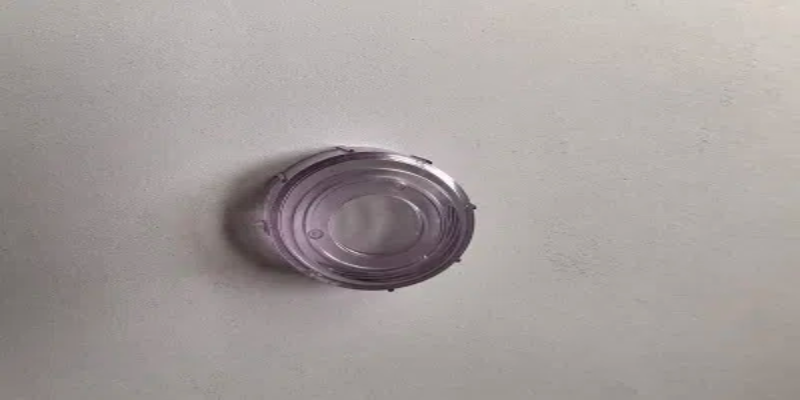
Online Resources
The internet is one of the most effective tools for identifying medical parts mold companies in your area. Start by searching through online directories and industry-specific databases that list medical parts mold companies based on location and specialties. Company websites are also valuable resources for learning more about a supplier’s services, capabilities, certifications (such as ISO 13485 and FDA registration), and customer reviews. Many medical parts mold companies also maintain a presence on professional forums and social media platforms, where they share case studies, industry news, and client feedback.
Trade Shows
Attending industry trade shows and conferences is another excellent way to connect with medical parts mold companies in your region. Events like MDM West, held annually in Anaheim, CA, offer an opportunity to meet local manufacturers in person, see product demonstrations, and discuss your project needs face-to-face. These trade shows often feature a wide range of exhibitors, from small local companies to large, global suppliers. By visiting booths, asking questions, and networking with industry professionals, you can get a firsthand look at the capabilities and expertise of local medical parts mold companies. In addition to MDM West, events like the Medical Design & Manufacturing (MD&M) series are also great opportunities to find local suppliers specializing in medical injection molding.
Customer Reviews and Testimonials
One of the most reliable ways to gauge the quality and reliability of medical parts mold companies is by reading customer reviews and testimonials. Feedback from previous clients provides valuable insights into a company’s performance, including their ability to meet deadlines, the quality of their products, and their customer service. Look for reviews on trusted platforms such as Google. Additionally, many medical parts mold companies will provide case studies or references from other clients in the healthcare industry. Talking to other professionals who have worked with the companies you’re considering can also give you a clearer picture of what to expect in terms of quality, communication, and compliance with industry standards.
By utilizing online resources, attending trade shows, and reviewing customer feedback, you can find the best medical parts mold companies near you. Whether you’re looking for a local partner for a specific project or a long-term manufacturing relationship, these strategies will help you make an informed decision and connect with a supplier that meets your requirements.
Specialization of Medical Parts Mold Companies in Medical Device Injection Molding
Medical device injection molding is a highly specialized field that requires advanced technology, precision, and strict adherence to regulatory standards. Companies that focus on medical device injection molding play a critical role in producing safe, functional, and reliable medical components. Below, we explore the areas of specialization that set medical parts mold companies apart in the field of medical device manufacturing.
Types of Medical Devices
Medical parts mold companies specializing in medical device injection molding produce components for a wide range of devices, each with unique requirements for precision, safety, and performance. These companies are experts in creating critical medical devices such as syringes, IV components, surgical instruments, and diagnostic tools. These parts often require tight tolerances and high levels of durability to ensure proper functionality in life-saving or life-supporting applications.
- Syringes and Drug Delivery Systems: Medical injection molding is used to create the intricate parts of syringes, insulin pens, and other drug delivery systems. These components must be manufactured with precision to ensure accurate dosages and prevent leaks or contamination.
- IV Components and Connectors: Medical parts mold companies often produce parts for IV sets, catheters, and other essential medical equipment used in hospitals and clinics. These parts must be sterile, durable, and able to withstand high pressure and fluid exposure without compromising the safety of the patient.
- Surgical Instruments: Many surgical tools and instruments, including forceps, scalpels, and clamps, are made using medical injection molding. These components must be lightweight, strong, and made from biocompatible materials to minimize the risk of infection or rejection during use.
By specializing in these high-precision applications, medical parts mold companies ensure that critical medical devices are produced to the highest standards of safety and functionality.
Advanced Molding Techniques
Medical device injection molding companies utilize advanced molding techniques to create complex components with high precision. These techniques enable the production of parts that are not only functional but also meet the specific needs of medical applications.
- Overmolding: Overmolding is a process where a second material is molded over an existing component, often combining materials with different properties to improve performance. This technique is commonly used for creating ergonomic grips for surgical tools or producing seals for drug delivery devices. Overmolding ensures better tactile handling, durability, and functionality.
- Multi-Shot Molding: This process involves injecting two or more materials into the same mold, creating multi-material parts with integrated functionality. Medical parts mold companies often use multi-shot molding for components like multi-material syringes or complex surgical instruments where different materials are required for various parts of the device. This technique allows for superior bonding between materials and a reduction in the need for secondary operations.
- Micro-Molding: Micro-molding is a technique used to create very small and intricate parts, often required for high-precision medical devices. This method is ideal for components used in diagnostic tools or micro-surgical instruments, where extremely tight tolerances and precise detailing are essential. Medical parts mold companies with expertise in medical micro molding can produce complex parts with dimensions as small as micrometers, ensuring the highest level of precision.
These advanced molding techniques enable medical device manufacturers to produce parts that are more complex, more durable, and capable of meeting the stringent demands of modern healthcare applications.
Regulatory Requirements
Medical device manufacturers are required to meet strict regulatory standards to ensure that their products are safe and effective for use in healthcare settings. Medical parts mold companies must adhere to these regulations, which include certifications like FDA registration, ISO 13485, and compliance with cleanroom standards.
- FDA Registration: Companies involved in medical injection molding must comply with FDA regulations for medical devices, ensuring that the devices are safe for use. FDA guidelines include strict requirements for device design, testing, manufacturing, and post-market surveillance. Medical parts mold companies that are FDA-registered demonstrate their commitment to producing safe and reliable medical components.
- ISO 13485: This international standard is specific to medical devices and outlines the requirements for a quality management system that ensures consistent quality in medical device manufacturing. Companies that hold ISO 13485 certification have demonstrated their ability to meet regulatory requirements and produce high-quality medical products.
- Cleanroom Standards: Many medical parts, particularly those used in sterile environments, must be produced in controlled environments. Cleanroom manufacturing ensures that particles, dust, and contaminants are minimized, maintaining the integrity and sterility of the medical device. Medical parts mold companies with cleanroom facilities ensure that their products meet the highest standards for sterility, making them suitable for critical medical applications.
By specializing in these regulatory requirements, medical parts mold companies ensure that medical devices are not only functional but also compliant with the necessary safety and quality standards required by the healthcare industry.
Medical device injection molding is a highly specialized area of manufacturing that demands expertise in precision molding techniques, regulatory compliance, and an in-depth understanding of medical device requirements. Medical parts mold companies that excel in these areas are essential partners in producing reliable, safe, and effective medical devices that meet the needs of both healthcare professionals and patients.
Comparing Medical Parts Mold Companies and Automotive Injection Molding
Medical molding and automotive injection molding are two distinct manufacturing processes, each with unique requirements and challenges. Although the industries differ significantly, there are key similarities in the technologies and techniques used. Below is a detailed comparison of these two fields, focusing on material requirements, tolerance levels, regulatory scrutiny, and how cross-industry expertise can be leveraged by medical parts mold companies.
Aspect | Medical Molding | Automotive Molding |
---|---|---|
Material Requirements | Medical-grade plastics such as biocompatible materials (e.g., PP, PEEK, ABS) to ensure safety and durability. | High-strength, cost-efficient materials such as thermoplastics (e.g., polypropylene, nylon) and composites for lightweight parts. |
Tolerance Levels | Extremely tight tolerances to ensure safety, functionality, and precision (micron-level accuracy). | While still important, tolerances are typically less strict than in medical molding, focusing on large-volume, cost-effective production. |
Regulatory Scrutiny | Must meet stringent FDA regulations, ISO 13485 certification, and cGMP standards. Products are often used in life-saving devices or diagnostic tools. | Largely focused on industry standards like ISO/TS 16949, with safety requirements but not as critical as in medical devices. |
Cleanroom Requirements | Manufacturing often takes place in ISO-classified cleanrooms to avoid contamination and maintain sterility. | Cleanroom requirements are less common, but parts must still meet specific safety and durability standards. |
Quality Assurance | Extensive testing and validation for sterility, biocompatibility, and mechanical properties to meet medical device regulations. | Emphasis on durability, weather resistance, and crash safety, with fewer biological or sterility concerns. |
Key Differences
The key differences between medical parts mold company and automotive molding revolve around the types of materials used, the level of precision required, and the regulatory environment. Medical molding demands stricter tolerances, higher-quality materials (e.g., biocompatible plastics), and compliance with health and safety standards like FDA regulations and ISO 13485. In contrast, automotive molding focuses on cost-effective production methods, where tolerances are important but not as stringent. Automotive parts are typically designed for durability and performance under harsh conditions but don’t require the same level of sterility or biocompatibility as medical devices.
Cross-industry Expertise
Some medical parts mold companies have cross-industry expertise, working in both medical and automotive injection molding sectors. They use their extensive experience in high-precision molding to adapt to the specific requirements of medical device manufacturing. These companies can bring valuable insights to medical device manufacturers, including efficient production methods and cost-saving techniques learned from automotive molding.
Innovation Transfer
Innovations from the automotive industry often influence advancements in medical molding. Techniques developed for automotive molding, such as precision tooling, efficiency improvements, and cost-saving methods, are frequently adapted by medical parts mold companies to meet the specific demands of medical device manufacturing.
- Precision Tooling: Automotive molding often requires complex tools and molds for mass production, a capability that translates well into medical molding, where precision is paramount. Advances in precision tooling from automotive production help medical device manufacturers achieve the tight tolerances needed for life-critical devices.
- Efficiency Improvements: The automotive industry’s focus on high-volume production and cycle time reduction has led to innovations that help medical manufacturers reduce lead times and lower production costs. Techniques like multi-shot molding and overmolding developed for automotive parts can be effectively used to enhance the functionality and production efficiency of medical devices.
- Cost-Saving Methods: In automotive molding, cost-saving methods are crucial due to the high volume of parts produced. Similarly, medical parts mold companies can apply some of these cost-effective strategies, such as optimized part design and material selection, to reduce the overall cost of manufacturing medical components while maintaining the required quality and regulatory standards.
While medical and automotive injection molding have their distinct requirements, there are significant overlaps in terms of technology and innovation. Medical parts mold companies that leverage cross-industry knowledge and innovations can benefit from advancements in automotive molding techniques, ultimately improving the precision, efficiency, and cost-effectiveness of medical device manufacturing.
How to Choose the Right Medical Parts Mold Company for Your Needs
Selecting the right medical parts mold companies for your medical device manufacturing needs is a critical decision that can impact both the quality of your products and the success of your business. The complexity of medical molding processes requires a partner who can meet stringent regulatory standards, provide precision, and deliver quality at scale. Here are the key factors to consider when choosing the best company for your needs.
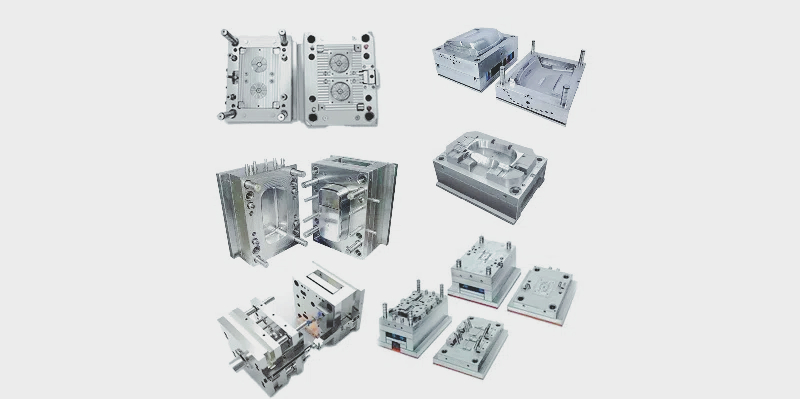
Experience and Expertise
One of the most important factors in selecting a medical parts mold company is its level of experience and expertise in the medical device industry. Medical injection molding is a specialized field that requires deep knowledge of both the technology and regulatory requirements. Companies with years of experience in medical molding are more likely to understand the unique challenges and demands of this sector, such as tight tolerances, material selection, and compliance with FDA regulations and ISO certifications.
Experienced manufacturers have the technical know-how to handle a wide range of medical devices, from simple consumables to complex diagnostic tools. They also bring valuable insights into process optimization and troubleshooting, which can help prevent costly delays or mistakes in the manufacturing process.
Customization Capabilities
Another critical aspect to consider when choosing a medical parts mold company is their ability to customize molds for your specific medical applications. The medical field often requires specialized molds for complex devices, which may involve intricate designs, multi-material molding, or even micro-molding. Whether you’re producing syringes, surgical instruments, or diagnostic equipment, you need a company that can tailor the medical mold design to meet the exact specifications of your product and align with medical molding requirements.
Customization capabilities also extend to the materials used. A reputable medical parts mold company will work with medical-grade materials that meet biocompatibility standards and other requirements essential for medical device safety. These companies should be able to adapt to evolving design requirements and ensure the molds are optimized for both functionality and cost-efficiency, while adhering to medical molding requirements for safety and compliance.
Quality Assurance
Quality is paramount in the medical device industry, and choosing a medical parts mold company that provides comprehensive quality assurance measures is essential. Look for companies that have certifications like ISO 13485, which demonstrates their adherence to quality management systems for medical devices. Additionally, ensure that the company complies with FDA regulations for medical device manufacturing and follows cleanroom standards to maintain the sterility and quality of the molds during production.
A strong focus on quality assurance helps minimize defects, reduce production costs, and ensure that your medical devices meet all the necessary safety and performance standards. Be sure to inquire about the company’s testing protocols and their ability to track and document the quality of every batch of molded parts.
Customer Service and Support
The level of customer service and support offered by medical parts mold companies can significantly affect the success of your medical molding project. Medical device manufacturing is a highly collaborative process, and it’s crucial to work with a partner who values communication and responsiveness. Look for companies that offer dedicated customer support and are proactive in addressing your concerns or design changes.
Moreover, choose a company that offers design collaboration and can work closely with your team to refine your product design, improve manufacturing processes, and solve any issues that arise during production. The ability to provide expert advice and support throughout the entire lifecycle of your project is a valuable asset that ensures smoother production runs and faster time-to-market for your medical devices.
When selecting the right medical parts mold company, prioritize experience, customization capabilities, robust quality assurance practices, and excellent customer service. These factors will help ensure that your medical device manufacturing is both efficient and compliant with the highest industry standards.
Process of Designing and Completing Medical Parts Injection Molding by Medical Parts Mold Companies
The process of designing and completing medical parts injection molding involves several essential steps that medical parts mold companies must carefully follow to ensure high-quality, reliable, and compliant products. These steps range from initial design and prototyping to final production and testing, with a strong emphasis on precision, regulatory compliance, and material selection. Below, we break down each step in the process, highlighting the key elements that medical parts mold companies must consider to ensure the successful manufacturing of medical devices.
Design and Product Development
The first step in the process of medical parts injection molding is design and product development. During this phase, medical parts mold companies work closely with the client to understand the functionality, materials, and regulatory requirements of the medical device being developed. The design must not only meet the functional needs of the product but also comply with the standards set by regulatory bodies, such as the FDA, to ensure patient safety.
The design process often involves creating 3D CAD (computer-aided design) models of the parts, which allow for detailed visualization and testing before physical production begins. This stage is critical for identifying any potential issues related to part geometry, manufacturability, or material selection. Prototypes may be created to evaluate the design before moving on to full-scale production.
Mold Design and Engineering
Once the product design is finalized, the next step is mold design and engineering. This phase involves the creation of the injection mold that will be used to produce the medical parts. Mold design is a highly technical process that requires medical parts mold companies to ensure that the mold is capable of producing the parts with the necessary precision and consistency.
The mold design includes choosing the right material for the mold, such as hardened steel or aluminum, and ensuring the mold has the required cavities, channels, and features needed for the production of the medical device. The company must also determine the optimal cooling system and venting design to minimize cycle time and prevent defects during production. Mold engineering is crucial for ensuring that the final part will meet all functional and regulatory standards.
Material Selection
Material selection is a key aspect of medical parts injection molding, as the material used must meet both the functional requirements of the device and regulatory standards for biocompatibility. During this phase, medical parts mold companies work with clients to choose the appropriate medical-grade plastics, such as polyethylene, polypropylene, polycarbonate, or silicone, depending on the product’s intended use.
The material chosen must ensure durability, strength, and resistance to sterilization processes, as many medical devices require frequent sterilization. The company must also ensure that the material is biocompatible, meaning it will not cause an adverse reaction when in contact with the human body. Additionally, the material must be lightweight and easy to handle, providing convenience in medical applications.
Prototype Development and Testing
After mold design and material selection, medical parts mold companies typically create a prototype of the medical device. Prototypes are essential for validating the design, mold, and material choices before mass production begins. During this stage, the prototype is carefully tested for accuracy, functionality, and compliance with industry regulations.
Prototyping allows for the identification of any potential issues, such as dimensional inaccuracies, surface defects, or material incompatibility, which could affect the device’s performance or safety. These tests ensure that the product meets the required quality standards before proceeding to full-scale manufacturing. If necessary, adjustments are made to the design or mold to correct any issues identified during testing.
Injection Molding Production
Once the design, mold, material, and prototype have been finalized and tested, the production phase begins. During injection molding production, medical parts mold companies inject molten plastic into the mold under high pressure, allowing it to cool and solidify into the final medical part. The process is repeated for each part, ensuring uniformity and precision throughout the production run.
The injection molding process is closely monitored to maintain tight tolerances and consistent quality. Parameters such as temperature, pressure, and injection speed are controlled to ensure that the final parts meet the required specifications. For medical devices, precision and consistency are critical to ensuring that every part functions as intended.
Quality Control and Regulatory Compliance
In the medical industry, quality control and regulatory compliance are of the utmost importance. Medical parts mold companies must implement rigorous quality control processes throughout the manufacturing process to ensure that each medical part meets both functional and safety standards. This may involve testing for dimensional accuracy, material properties, strength, and resistance to sterilization.
The company must also ensure that the products meet regulatory requirements set by governing bodies such as the FDA and ISO. Medical device manufacturers must maintain detailed records of the production process, including material certificates and inspection results, to demonstrate compliance with industry standards. This step ensures that the medical products are safe, effective, and legally marketable.
Post-Production Testing and Packaging
Once the medical parts are produced and meet quality control standards, the next step is post-production testing and packaging. Post-production testing involves a final round of testing to ensure that the medical device functions as expected under real-world conditions. This could include testing for strength, durability, and performance in clinical environments.
After successful testing, the parts are carefully packaged to ensure they remain sterile and safe for shipment. The packaging must also be compliant with medical industry standards, providing adequate protection during transportation and storage. This step is essential to ensure that the medical device reaches its destination in perfect condition and is ready for use in medical applications.
Final Delivery and Support
After successful production, testing, and packaging, the medical parts mold company delivers the finished product to the client or end customer. It is important that the company maintains open lines of communication with the client throughout the process to ensure that all requirements are met and to address any concerns promptly.
Additionally, medical parts mold companies often offer ongoing support for the products they manufacture. This may include maintenance of molds for future production runs, providing assistance with product modifications, or offering guidance on regulatory compliance. By providing comprehensive support, medical parts mold companies help ensure that the final product continues to meet industry standards and customer expectations.
The process of designing and completing medical parts injection molding is intricate and involves multiple steps, each critical to producing a high-quality, safe, and effective medical product. From initial design and prototyping to final delivery and support, medical parts mold companies must follow a precise, detailed approach to ensure that the medical devices they manufacture meet all necessary regulatory standards and functional requirements.
Why Medical Parts Mold Companies Need MedAccred Certification
MedAccred certification is an essential qualification for medical parts mold companies involved in the manufacturing of medical devices and components. This certification ensures that manufacturers comply with strict industry standards, such as ISO and FDA regulations, and provides a framework for continuous improvement in quality, safety, and performance. For medical parts mold companies, achieving MedAccred certification helps instill confidence in clients, streamline operations, and enhance their reputation within the competitive medical manufacturing sector. Below, we explore the key reasons why obtaining MedAccred certification is vital for these companies from various perspectives.
Ensuring Regulatory Compliance
One of the primary reasons medical parts mold companies need MedAccred certification is to ensure compliance with regulatory requirements. The medical device industry is highly regulated, with strict standards and guidelines set by governing bodies such as the U.S. Food and Drug Administration (FDA) and the European Medicines Agency (EMA). MedAccred certification is a recognized credential that demonstrates a company’s commitment to meeting these regulations.
By obtaining this certification, companies confirm that their processes adhere to the necessary regulatory guidelines, which is crucial for avoiding costly delays, fines, or product recalls. MedAccred certification assures clients and stakeholders that the medical parts produced meet safety, quality, and performance standards, which are essential for patient health and regulatory approval.
Enhancing Product Quality
MedAccred certification is a symbol of superior product quality. It requires medical parts mold companies to implement robust quality management systems (QMS) and to undergo regular audits to ensure compliance with industry standards. This certification helps companies refine their processes, reduce errors, and maintain consistent product quality over time.
For medical parts mold companies, MedAccred certification supports the establishment of a culture of continuous improvement. This leads to the production of more precise, durable, and reliable medical components, essential for the success and safety of medical devices. High-quality products are fundamental in the medical industry, where even the smallest defects can have severe consequences.
Building Client Trust and Confidence
For medical parts mold companies, trust and reputation are crucial in the competitive medical manufacturing industry. MedAccred certification serves as a third-party validation that the company meets the rigorous standards required for medical device manufacturing. This certification instills confidence in clients, knowing that the company adheres to internationally recognized quality and safety protocols.
Clients, especially those in the medical field, are more likely to choose a certified supplier over non-certified ones due to the added assurance of quality and compliance. MedAccred certification helps companies differentiate themselves from competitors and establishes long-term relationships with clients who rely on consistent, high-quality medical parts for their devices.
Streamlining Internal Processes
Obtaining MedAccred certification requires medical parts mold companies to streamline their internal processes and establish a systematic approach to quality control, production, and documentation. By following the certification guidelines, companies create more efficient operations that reduce waste, improve productivity, and minimize the risk of errors.
This streamlined approach not only enhances operational efficiency but also leads to cost savings. For instance, by reducing the need for rework and enhancing supply chain management, certified companies can lower manufacturing costs, which can then be passed on to customers in the form of competitive pricing.
Gaining a Competitive Edge
In the highly competitive field of medical device manufacturing, MedAccred certification provides a significant competitive advantage. Many medical device manufacturers prefer to work with certified suppliers because it ensures their components are of the highest quality and meet all necessary regulatory standards.
For medical parts mold companies, this certification can open doors to new business opportunities, including working with larger medical device companies or entering new markets where certification is a requirement. It enhances the company’s credibility and demonstrates its commitment to maintaining high standards, giving it an edge over competitors who may not be certified.
Facilitating International Market Access
MedAccred certification is recognized globally as a standard for quality and compliance in the medical manufacturing sector. For medical parts mold companies looking to expand their reach beyond local or regional markets, obtaining this certification can facilitate access to international markets. Many countries and regions, such as the European Union and North America, require or strongly prefer certification as part of their regulatory approval process.
Having MedAccred certification allows companies to demonstrate that their manufacturing processes are consistent with international standards, which can ease the approval process for medical products in foreign markets. This global recognition can help companies expand their customer base and grow their business internationally.
Fostering Continuous Improvement and Innovation
MedAccred certification is not a one-time achievement but a commitment to ongoing quality management and improvement. The certification process encourages medical parts mold companies to engage in continuous improvement by identifying areas for process optimization, reducing defects, and staying up-to-date with industry trends and technological advancements.
This commitment to innovation is essential in the fast-paced and ever-evolving medical industry. By maintaining MedAccred certification, companies demonstrate that they are dedicated to evolving and adapting to the latest standards and technologies, ensuring their products remain competitive and relevant in the marketplace.
MedAccred certification is an essential qualification for medical parts mold companies looking to ensure compliance, enhance product quality, build client trust, and remain competitive in the medical device industry. By adhering to the rigorous standards set by MedAccred, companies can streamline their operations, improve internal processes, and meet the demanding regulatory requirements of the medical field. This certification is not only a mark of excellence but also a key enabler of growth, enabling companies to access new markets and forge stronger, long-term client relationships.
FAQs about Medical Parts Mold Companies
The largest injection molding company in the world by revenue and global presence is Haitian International, a Chinese manufacturer with a revenue of over $2.5 billion. Founded in 1966, Haitian International is recognized for its advanced injection molding machines and wide range of products, including all-electric, hydraulic, hybrid, and vertical injection molding machines. The company has established a dominant position in the injection molding industry due to its innovative approach to machinery design, cost-efficiency, and commitment to producing high-quality, reliable products.
Although Haitian International is a leader in terms of size, other major players like ENGEL (Austria), Milacron (USA), and Arburg (Germany) also hold significant market shares globally. These companies are highly regarded for their technological advancements, sustainability initiatives, and specialization in diverse sectors, from medical molding to automotive manufacturing. Each of these companies has made substantial contributions to the injection molding industry, solidifying their positions as key industry leaders.
The market for medical injection molding is rapidly growing due to the increasing demand for high-quality, precise, and affordable medical devices. The global medical device industry is expected to reach USD 603 billion in 2023 and is projected to grow at a compound annual growth rate (CAGR) of 5% over the next six years. The medical injection molding market, in particular, is anticipated to see significant expansion, driven by technological advancements, the increasing aging population, and the rise in chronic diseases.
Medical injection molding is crucial for the production of medical devices such as syringes, catheters, diagnostic tools, and implantable devices. Molding allows for the cost-effective production of complex, high-precision parts in high volumes. Furthermore, the use of advanced materials like biocompatible plastics and the integration of automated systems to ensure high-quality standards (e.g., ISO 13485, FDA compliance) are contributing factors to the market’s growth. The shift towards minimally invasive surgeries, wearable health technologies, and personalized medicine is also increasing the demand for medical injection-molded parts.
Medical injection molding is used to create a wide range of medical products, thanks to its ability to produce high-precision, complex parts at scale. Some of the most common medical products made by injection molding include:
Syringes: Used in hospitals and clinics for administering vaccines, medications, and other injections. Injection molding ensures the precise design of the syringe barrel, plunger, and needle hubs.
Catheters: Essential for medical procedures such as urinary drainage, blood vessel access, and monitoring. Injection molding allows the production of flexible, biocompatible catheter tubes and components.
Diagnostic Tools: Components for medical diagnostic devices like blood glucose meters, pregnancy tests, and diagnostic cartridges. The precise molding of these small components is crucial for device accuracy and reliability.
Surgical Instruments: Precision parts for surgical tools, including handles, grips, and functional components. Injection molding ensures the exact specifications required for functionality and patient safety.
Implantable Devices: Parts for orthopedic implants, hearing aids, and pacemakers, among others. Injection molding is essential for producing durable, safe, and bio-compatible components that meet stringent regulatory standards.
Personal Protective Equipment (PPE): Items such as face shields, masks, and gloves. Injection molding provides a high-efficiency way to manufacture PPE in large quantities while maintaining quality control.
The cost of an injection mold for medical parts can vary significantly depending on several factors, such as mold complexity, material used, and the manufacturer’s location. Typically, the price range for an injection mold used in medical manufacturing falls between $5,000 and $100,000. Basic molds for simple medical components might cost around $5,000 to $10,000, while more intricate molds for complex medical devices or high-volume production can be significantly more expensive. The cost is influenced by factors like mold material (steel vs. aluminum), design complexity, and the required tolerance and finish quality for medical applications. It’s important to also factor in the ongoing maintenance costs and potential modifications required as product designs evolve. Medical molders may also offer custom solutions that can influence the overall price, especially for specialty or precision parts.
Calculating the mold injection cost involves several factors that include the mold design, material, and cycle time. The mold cost itself is one of the primary expenses and can range widely, depending on its complexity and the type of medical part being produced. In addition to the mold, you need to account for material costs, such as the type of polymer or plastic used in the injection process. Labor costs for the mold setup and the production process also contribute. To calculate the total cost, you must factor in the cycle time (how long it takes to inject and cool the part), the number of parts produced per cycle, and the overall number of cycles required. For medical parts, strict quality controls and testing add additional costs, particularly when meeting regulatory standards such as those imposed by the FDA.
Injection molds used in medical parts manufacturing can last for a significant number of cycles, typically between 100,000 and 1,000,000 cycles. The lifespan of a mold largely depends on the material used for the mold (steel tends to last longer than aluminum), the complexity of the part, and the care taken during production. Molds used for medical components, which often have high precision and stringent quality requirements, generally need to be maintained and refurbished periodically. Factors like material type, mold design, and production volume also play a role in determining how many times the mold can be used. Regular inspections and maintenance are crucial for ensuring that molds remain effective over time and continue to produce parts within the required tolerances for medical applications.
Injection molding can be highly profitable, especially when used for high-volume production of medical parts. The profitability of an injection molding business depends on several factors, including the cost of the mold, material costs, labor costs, and the volume of parts produced. Once a mold is designed and created, it can be used to produce thousands or even millions of parts with minimal additional investment, which increases profitability over time. In medical manufacturing, consistent, high-quality parts are in demand, and the precision required often leads to repeat business, contributing to higher profit margins. However, initial investment in tooling, quality control, and regulatory compliance can be substantial. Long-term profitability also depends on factors such as demand, operational efficiency, and market conditions. The ability to scale production and reduce per-part costs further enhances profitability.
Casting is often considered a more cost-effective method than injection molding for producing low-volume or complex parts, including in medical applications, but the comparison depends on the specific project. For small production runs, casting methods like sand casting or die casting can be less expensive because they typically require less complex tooling and have lower initial setup costs. However, for high-volume production, injection molding becomes more cost-effective due to its ability to produce parts quickly and at a lower cost per unit. In medical manufacturing, where high precision and consistent quality are paramount, injection molding is generally preferred for large-scale runs due to its repeatability and the ability to meet regulatory requirements. Ultimately, casting may be cheaper for prototypes or small batches, but injection molding is often the more economical choice for larger volumes.
Injection molding is generally cheaper than machining, particularly when producing large quantities of medical parts. Machining involves shaping material by removing portions from a workpiece, which can be time-consuming and expensive, especially when the parts are intricate or need tight tolerances. Conversely, injection molding allows for the mass production of highly consistent parts with minimal post-processing. The initial setup costs for injection molding can be higher due to the need for custom molds, but once the molds are in place, the cost per part drops significantly with higher volumes. In medical applications, where high precision and complex shapes are often required, injection molding allows for faster production of parts with less material waste compared to machining. Therefore, for large-volume runs of medical parts, injection molding is typically more economical.
While injection molding is often the preferred manufacturing method for medical parts, alternative processes may be better suited for certain applications. For example, 3D printing (additive manufacturing) can be advantageous for low-volume or highly customized parts, as it doesn’t require expensive molds and offers rapid prototyping. For high-precision metal parts, such as those used in implants, metal injection molding (MIM) or CNC machining may be better options. For parts requiring very detailed textures or unique surface finishes, casting techniques like die casting might be preferred over injection molding. Ultimately, the “better” option depends on the specific needs of the medical device, including production volume, material requirements, complexity, and cost constraints. Each method offers unique advantages based on the type of part and desired outcome.
For low-volume production or prototype medical parts, methods such as 3D printing (additive manufacturing) and casting can be cheaper than injection molding. 3D printing is particularly cost-effective for small batches of custom parts because it eliminates the need for molds and offers flexible designs. Investment casting, which involves creating a mold around a pattern that is later melted away, is another alternative that can be more affordable for low runs or when creating complex geometries. While these methods may not offer the same speed or consistency as injection molding in high-volume production, they can be a more economical solution for smaller projects or prototype development in the medical field.
The cheapest material to injection mold typically includes thermoplastics such as polystyrene (PS), polyethylene (PE), and polypropylene (PP). These materials are widely used in medical parts manufacturing due to their low cost, availability, and ease of processing. Polystyrene, for example, is inexpensive and commonly used for disposable medical devices like test tubes, while polypropylene is used for containers, syringes, and medical packaging due to its chemical resistance and cost-effectiveness. Polyethylene is also affordable and is used in medical packaging and basic medical components. While these materials are cost-effective, it is important to select the right material based on the specific medical part’s performance requirements, including biocompatibility, strength, and regulatory standards.
The future of injection molding, particularly in medical parts manufacturing, is expected to be shaped by advancements in technology, materials, and sustainability. As demand for medical devices continues to rise, there will be increased focus on precision, faster production times, and cost efficiency. The integration of automation, robotics, and AI into injection molding processes will improve production rates and reduce human error. Moreover, innovations in biocompatible and recyclable materials are likely to drive the development of more sustainable solutions. The growing trend towards personalization in medical devices may also lead to more flexible manufacturing processes, with injection molding adapting to produce small batches of custom components. Additionally, advancements in 3D printing and hybrid manufacturing could further complement traditional injection molding, expanding its versatility in medical applications.
Injection molds are expensive due to the high level of precision, complex design, and quality required, especially in the medical industry. Creating a mold involves detailed engineering, sometimes requiring intricate designs to ensure that parts are produced with exact tolerances. The materials used for making molds, such as high-grade steel, are costly, and the mold-making process itself requires skilled labor and advanced equipment. For medical parts, strict regulatory requirements, including FDA approvals, and the need for high levels of cleanliness and consistency, further increase the mold’s cost. Additionally, the design phase often involves multiple iterations and testing to meet the specific requirements of medical applications, driving up initial costs. The durability and lifespan of molds, essential for long-term production, also add to their price.
Injection molding tooling is expensive because it involves several high-cost factors, particularly in the medical industry. The tooling process requires the creation of molds that must withstand high pressures and temperatures over extensive production cycles. The use of durable materials like hardened steel or specialized alloys, which are essential for producing precise medical components, contributes significantly to the cost. Additionally, creating molds with exacting tolerances and fine details for medical applications requires advanced design, engineering, and prototyping, all of which take time and expertise. The complexity of molds, such as those used for medical devices with intricate features, further adds to the cost. Regulatory compliance, testing, and the need for consistency in every part produced also factor into the high price of injection molding tooling.
Contact our professional team now for a same-day quote and risk-free project evaluation. Benefit from ISO 8 cleanrooms, advanced machines, and 12-hour fast response in medical injection molding.