Medical parts mold factories play a crucial role in the healthcare industry, ensuring the production of high-quality, safe, and efficient medical components. These factories specialize in the precision manufacturing of medical parts through advanced techniques like injection molding, overmolding, and insert molding. By focusing on safety and regulatory compliance, they help meet the stringent requirements of the medical sector. Key players in the field have set high standards for the industry. Furthermore, medical product directories help businesses connect with reliable medical parts mold factories, making it easier for companies to find the right manufacturing partners. These factories are essential for the continuous innovation and advancement of medical technologies. Medical parts mold factories use advanced injection molding, overmolding, and insert molding, with FUJIU Medical Injection Mold offering precise, reliable manufacturing.
Low-Volume to High-Volume Production Capabilities
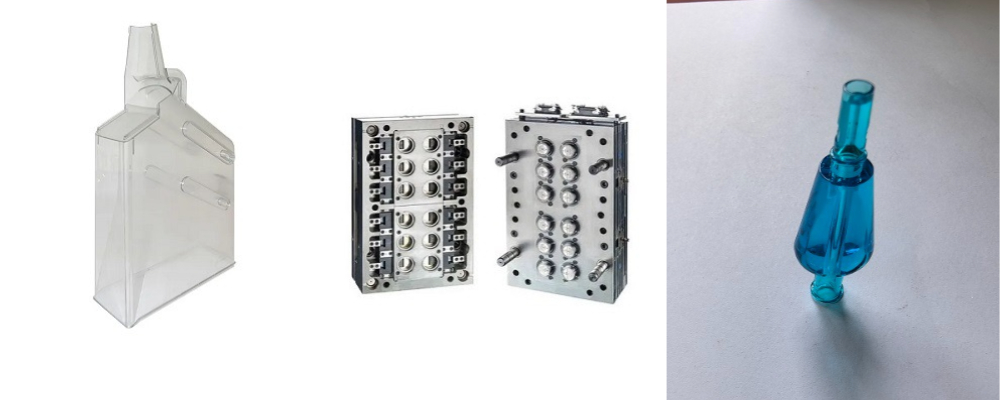
Attributes | Details |
---|---|
Place of Origin | Dongguan, Guangdong, China |
Brand Name | LY Medical Injection Mold |
Product Name | Medical Molding |
Technology | Injection Molding |
Processing Services | Molding, Cutting |
Color | Customized Color |
Size | Accept Customer's Design |
Shape | Customized Shape |
Service | One-Stop Service |
Feature | Environmentally Friendly |
Advantage | High Quality |
Certification | ISO9001:2008 |
Tolerance | +/-0.01mm / OEM |
OEM | Avaliable |
Selling Units | Single item |
Packing Details | According to Customer's Requirement |
Port | According to Customer's Requirement |
The Role of Medical Parts Mold Factories in Medical Manufacturing
Importance of Precision and Compliance with Medical Standards
Medical parts mold factories are at the heart of the medical manufacturing industry, ensuring that every part produced meets strict quality and safety standards. Precision mold medical components are particularly critical, as even small variations in size or function can lead to potential risks for patients. These factories are required to comply with industry regulations such as ISO 13485 and FDA standards, ensuring that the components they produce are safe, reliable, and capable of performing their intended functions. In the medical sector, compliance with these standards is non-negotiable, and medical parts mold factories must adhere to stringent testing and validation processes to guarantee product quality.
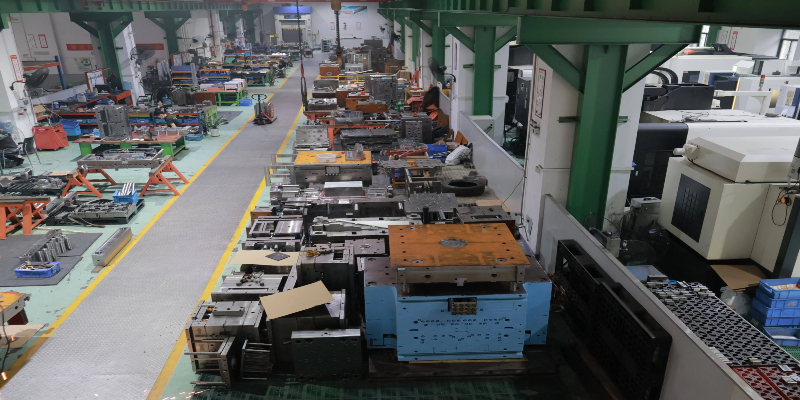
Overview of Processes: Injection Molding, Overmolding, and Insert Molding
Medical parts mold factories use a variety of advanced molding techniques to create high-precision medical components.
- Injection Molding: This is one of the most common methods used in medical manufacturing. It involves injecting molten plastic into a mold cavity under high pressure, allowing for high-volume production of complex shapes and detailed parts.
- Overmolding: In this process, a secondary layer of material is molded over an existing part, often to enhance the functionality or comfort of the component. For example, overmolding can be used for creating ergonomic handles for surgical instruments.
- Insert Molding: Insert molding involves placing metal or other inserts into the mold before injecting plastic. This technique is often used to combine plastic and metal components, such as in the production of components with embedded threads or electrical contacts.
These processes are crucial for producing medical parts with high accuracy and reliability, ensuring that they function as intended in critical medical applications.
Industries Served: Diagnostics, Surgical Instruments, and Pharmaceutical Packaging
Medical parts mold factories serve a wide range of industries within the healthcare sector. They are essential in producing components used in diagnostics, surgical instruments, and pharmaceutical packaging. In diagnostics, these factories manufacture parts for test kits, devices, and laboratory equipment that require high precision and reliability. For surgical instruments, the molding processes must meet high standards of durability, sterility, and functionality. Additionally, pharmaceutical packaging, which often requires tight seals and tamper-evident features, is another critical area where medical parts mold factories play a vital role. These factories ensure that the products meet not only performance standards but also regulatory requirements, contributing to the overall safety and efficiency of the medical industry.
Key Features of Medical Parts Mold Factories
Advanced Technology: Use of CNC Machines, EDM, and 3D Printing for Mold Production
Medical parts mold factories leverage cutting-edge technology to ensure the production of high-precision, high-quality components. One of the key technologies used is CNC (Computer Numerical Control) machining, which allows for precise control over the cutting and shaping of molds. CNC machines are essential for creating intricate details and ensuring that the molds meet the strict tolerances required in the medical industry. Another critical technology is EDM (Electrical Discharge Machining), which is ideal for creating complex, detailed mold features, especially in materials that are hard to machine with traditional methods.
In addition, 3D printing is becoming increasingly popular in the medical molding industry. This technology is particularly useful for rapid prototyping and creating intricate mold designs quickly. It enables manufacturers to test and refine designs before investing in the more expensive traditional molding processes. These advanced technologies ensure that medical parts mold factories can deliver precise, reliable, and efficient production of medical components.
Cleanroom Manufacturing: Ensures Sterility and Minimizes Contamination Risks
Cleanroom manufacturing is a key feature of medical parts mold factories, as it ensures that the parts produced are free from contaminants that could compromise the safety and functionality of medical devices. Cleanrooms are controlled environments where the concentration of airborne particles is minimized, and strict procedures are followed to maintain a sterile environment. This is especially important in the medical industry, where even the smallest contamination can lead to product failure or health risks for patients.
Medical parts mold factories that operate cleanrooms are equipped with HEPA (High-Efficiency Particulate Air) filters, controlled humidity, and temperature systems to maintain a pristine environment. These controlled conditions help prevent contamination during the production of medical components such as syringes, surgical tools, and diagnostic instruments. By utilizing cleanroom manufacturing, these factories ensure that the medical parts meet the stringent requirements for sterility and quality.
Regulatory Compliance: Adherence to ISO 13485 and FDA Standards
Medical parts mold factories must adhere to a wide range of regulatory standards to ensure the safety and reliability of the medical components they produce. One of the most important certifications is ISO 13485, which outlines the requirements for a comprehensive quality management system for plastic medical device manufacturers. Compliance with this standard is essential for ensuring that the products are consistently manufactured to meet regulatory requirements and that quality control is maintained throughout the production process.
In addition to ISO 13485, medical parts mold factories must also comply with FDA (Food and Drug Administration) regulations, particularly the FDA’s 21 CFR Part 820, which covers quality system regulations for medical devices. Adherence to these regulations ensures that the manufacturing processes, materials, and finished products meet the safety standards required for medical devices. By maintaining compliance with these rigorous standards, medical parts mold factories can ensure that the components they produce are safe for patient use and meet the necessary regulatory approvals for market distribution.
Why Choose Reliable Medical Parts Mold Factories?
Customization: Tailored Solutions for Specific Medical Applications
A reliable medical parts mold factory offers a significant advantage through the ability to provide customized solutions for a wide range of medical applications. Every medical device, whether it’s a diagnostic tool, surgical instrument, or implant, has its own set of requirements regarding shape, size, material, and functionality. A trusted mold factory works closely with clients to design and manufacture parts that meet these specific needs. This tailored approach, often involving machining medical parts, ensures that the medical components will perform optimally in their intended use. Customization also extends to design alterations, where mold factories use advanced technologies like 3D printing and CNC machining to adjust and refine parts quickly, ensuring a perfect fit and functionality for the end product. By choosing a medical parts mold factory with extensive customization capabilities, healthcare manufacturers can ensure their devices meet unique operational, regulatory, and design standards.
Cost-Optimization: High-Volume Production Reduces Costs
Cost efficiency is another compelling reason to choose a reliable medical parts mold factory. As the demand for medical devices increases, high-volume production becomes more cost-effective. Medical parts mold factories can leverage automation and advanced molding technologies to produce large quantities of components at a reduced cost per unit. By investing in high-precision molding equipment and optimized production processes, these factories can lower overhead and production costs, which is especially beneficial in industries that require large-scale manufacturing. Moreover, the economies of scale achieved in high-volume production allow manufacturers to offer competitive pricing while maintaining high standards of quality. This makes it easier for medical companies to produce cost-effective solutions without compromising on the performance and safety of their products.
Durability and Sterilization: Resistance to Harsh Conditions and Easy Sterilization
The durability and sterilization capabilities of medical components are essential when selecting a reliable medical parts mold factory. Medical products are often subjected to harsh conditions such as exposure to high temperatures, pressure, and chemicals. Therefore, components must be made from materials that are resistant to degradation and capable of withstanding these demanding environments. Medical parts mold factories specialize in using materials such as PEEK, polycarbonate, and silicone, which are known for their durability and ability to endure sterilization processes such as autoclaving or gamma radiation.
Furthermore, easy sterilization is a crucial factor in the design of medical parts. Many medical devices, especially those used in surgeries or diagnostics, must be thoroughly sterilized to ensure patient safety. A reliable medical parts mold factory uses advanced manufacturing techniques that ensure the parts are not only durable but also easy to sterilize without compromising their integrity. This guarantees that the components will remain safe and functional throughout their lifespan, which is vital in medical environments where hygiene and reliability are paramount.
Traceability: Critical for Regulatory Compliance and Safety Assurance
Traceability is another critical reason to choose a reputable medical parts mold factory. In the medical industry, tracking the lifecycle of every part is essential for regulatory compliance and safety assurance. Regulatory bodies like the FDA require that medical manufacturers implement systems to trace all components used in medical devices, ensuring they can be identified and tracked throughout their use. A reliable mold factory, such as a trusted medical plastic components manufacturer, provides thorough documentation and keeps detailed records of the materials, processes, and inspections used in the production of each component.
This traceability is essential not only for ensuring that the components meet all regulatory standards but also for maintaining a high level of safety in the event of a recall or quality issue. By choosing a medical parts mold factory with robust traceability systems in place, manufacturers can be confident that they are meeting stringent legal requirements while ensuring their customers’ safety and trust. This level of accountability and transparency enhances the credibility of the product and company, making traceability an indispensable feature in the medical device manufacturing process.
How to Find the Right Medical Parts Mold Factories
Use of Medical Product Directories to Identify and Evaluate Manufacturers
Finding the right medical parts mold factories requires thorough research and evaluation, and one of the best tools for this task is the use of medical product directories. These directories compile a comprehensive list of manufacturers, their specialties, and their qualifications. They serve as a valuable resource for businesses looking to identify mold factories that align with their specific needs. By browsing these directories, medical device companies can quickly find reliable manufacturers with expertise in producing high-quality medical parts. These directories also offer useful information about each company’s certifications, product offerings, and past projects, allowing potential clients to compare and assess various mold factories. Using a directory simplifies the search process and ensures that companies are considering reputable and qualified manufacturers that meet industry standards.
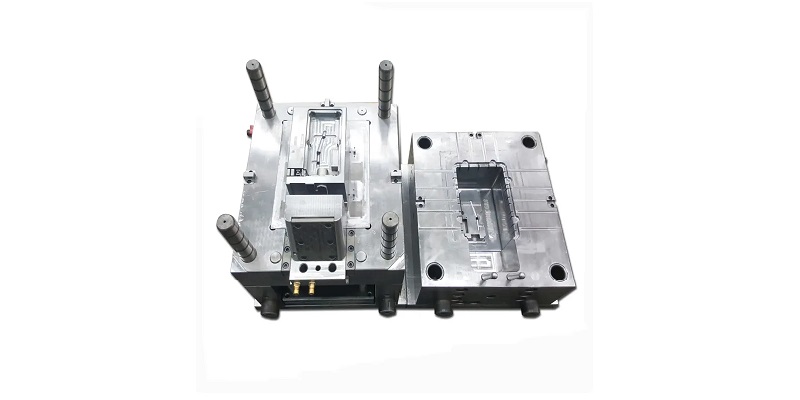
Key Factors to Consider
When selecting a medical parts mold factory, it is essential to consider several key factors to ensure the manufacturer meets your requirements and adheres to medical molding requirements. These considerations will help you assess whether the factory can provide the necessary precision, quality, and compliance with medical industry standards. The following are critical factors to evaluate:
Certification and Regulatory Compliance
The certification and regulatory compliance of a medical parts mold factory are fundamental when making your decision. Medical device manufacturing requires adherence to stringent regulations set by organizations such as the FDA (Food and Drug Administration) and international standards like ISO 13485. These certifications ensure that the mold factory maintains high standards of quality, safety, and precision, often supported by high precision tools for medical device manufacturing. A reliable factory will not only meet these regulations but also provide full documentation and transparency regarding its compliance. This guarantees that the parts produced are suitable for medical applications and can be trusted in environments where safety is paramount.
Technology and Cleanroom Capabilities
Another essential factor when choosing the right medical parts mold factory is the technology and cleanroom capabilities it possesses. The factory should be equipped with state-of-the-art equipment, such as CNC machines, EDM (electrical discharge machining), and 3D printing technology, to ensure the production of highly precise and complex medical components. Additionally, the cleanroom capabilities of the factory are critical for maintaining the sterility of medical parts, especially in industries where contamination control is essential, such as in the production of surgical tools, implants, and diagnostic equipment. A cleanroom ensures that the parts are manufactured in a controlled environment, minimizing the risk of contamination during production and handling.
Material Expertise and Production Capacity
Material expertise and production capacity are also important considerations when selecting a medical parts mold factory. The factory should have experience working with a variety of medical-grade materials such as PEEK, Polycarbonate, Silicone, and Polypropylene, each of which has specific properties needed for medical applications. Additionally, it’s important to evaluate the factory’s ability to handle your production volume, whether it is low-volume prototyping or high-volume mass production. A reputable medical parts mold factory should have the capacity to scale production while maintaining consistent quality and efficiency. This ensures that manufacturers can meet both small-scale and large-scale production needs, all while adhering to regulatory and quality standards.
By carefully evaluating these factors, businesses can confidently choose the right medical parts mold factory that aligns with their needs, ensuring that they receive high-quality, compliant, and reliable medical components for their products.
Materials and Precautions in Medical Parts Mold Factories: A Comprehensive Guide
Medical parts mold factories rely on various specialized materials in the injection molding process to produce high-quality, durable, and precise medical components. These materials must meet strict regulations for safety, biocompatibility, and functionality. The right material selection is essential for ensuring that medical devices are effective and safe for patient use. This answer will cover the types of materials used in medical injection molding, as well as the precautions taken when selecting medical-grade plastics, to provide a detailed understanding of how medical parts mold factories choose the best options for their manufacturing processes.
Types of Materials Used in Medical Parts Mold Factories
Medical parts mold factories use a range of materials tailored for different applications, including thermoplastics, thermosets, and elastomers. Each of these materials has unique properties that make them suitable for specific medical applications.
Medical-Grade Thermoplastics
Thermoplastics are the most common materials used in medical injection molding. They can be melted and re-molded multiple times without losing their properties, which is ideal for high-volume production. Common types of thermoplastics used include polycarbonate (PC), polypropylene (PP), polystyrene (PS), polyethylene (PE), and PPSU (polyphenylsulfone). These materials offer a balance of strength, flexibility, and durability, making them suitable for applications like syringes, IV connectors, and surgical tools.
Medical-Grade Thermosets
Thermosetting plastics are used for medical parts that require high resistance to heat and chemical exposure. These materials, like epoxy and phenolic, undergo a curing process that makes them rigid and durable. They are commonly used in applications like electrical components and certain diagnostic devices, where temperature stability and durability are critical.
Medical-Grade Elastomers
Elastomers such as silicone and thermoplastic elastomers (TPE) are used for parts requiring flexibility and elasticity. Silicone, in particular, is biocompatible, which makes it ideal for applications such as implants, seals, and gaskets. TPE is also used for flexible medical components like tubing and disposable medical gloves.
Precautions for Selecting Medical-Grade Plastics
Selecting medical-grade plastics for injection molding requires careful consideration of several factors, as the materials must meet rigorous standards of safety, effectiveness, and performance. The following are key precautions taken during material selection:
Biocompatibility
Medical-grade plastics must be biocompatible, meaning they should not cause adverse reactions when in contact with human tissues or fluids. This ensures that materials used in devices such as catheters or implants do not trigger immune responses or cause toxicity. Tests like cytotoxicity, irritation, and sensitization tests are conducted to assess biocompatibility.
Regulatory Compliance
Materials used in medical injection molding must comply with industry standards set by regulatory bodies such as the FDA and ISO. These standards ensure that the materials are safe for medical applications. It’s crucial for manufacturers to choose plastics that meet ISO 13485 (quality management for medical devices) and FDA approval for medical device manufacturing.
Sterilization Requirements
Medical components often need to be sterilized before use, which means the selected plastics must withstand processes like autoclaving, gamma radiation, or chemical sterilization without degrading. Therefore, materials must maintain their mechanical properties after sterilization to ensure the safety and functionality of the medical device.
Strength and Durability
The material must exhibit high strength and durability to withstand the rigors of use in medical applications. For example, surgical tools, drug delivery devices, and diagnostic instruments should be able to endure repetitive handling and environmental stress without breaking down.
Material Transparency
Certain medical applications, such as vials, syringes, and diagnostic devices, require transparent plastics for easy visibility. Materials like polycarbonate (PC) and polystyrene (PS) are commonly chosen for their optical clarity and ease of molding, ensuring the end product is functional and safe.
Cost and Availability
While medical-grade plastics must meet stringent technical and regulatory standards, cost-effectiveness is also an important consideration. Manufacturers often choose materials that offer the best balance of performance and affordability, especially when producing large quantities of medical parts for mass production.
In medical parts mold factories, the selection of materials for injection molding is crucial for ensuring the performance, safety, and regulatory compliance of medical devices. By carefully considering factors such as biocompatibility, sterilization compatibility, strength, and transparency, manufacturers can produce high-quality components that meet the demanding needs of the healthcare industry. Medical-grade thermoplastics, thermosets, and elastomers all offer distinct advantages, and precautions must be taken to ensure that the chosen materials adhere to industry standards and maintain the integrity of the final product.
Typical Applications of Injection Molding in Medical Parts Mold Factories
Medical parts mold factories play a crucial role in modern healthcare by producing high-precision, sterile, and biocompatible plastic components used in various medical applications. Injection molding is the preferred manufacturing method due to its ability to create complex geometries, maintain strict tolerances, and meet stringent medical standards. These factories manufacture a wide range of products, from disposable medical supplies to intricate implantable devices. Below, we explore the key application areas of injection molding in medical parts mold factories, categorized by their specific functions and significance in the medical industry.
Disposable Medical Devices and Consumables
Disposable medical components are widely used in hospitals and clinics to prevent cross-contamination and maintain patient safety. These parts must be produced in high volumes with strict quality control.
- Syringes and Needles: Plastic syringes, including their plungers and barrels, are produced using high-speed injection molding to ensure precision and leak-free performance.
- IV Tubing Connectors and Catheter Hubs: These connectors must be sterile, leak-proof, and biocompatible, making injection molding an ideal method for mass production.
- Blood Collection Tubes and Pipettes: Injection-molded plastic tubes and pipettes are used in laboratories and diagnostic centers to collect and store samples safely.
Surgical and Diagnostic Equipment Components
Injection molding is essential for manufacturing complex parts used in surgical instruments and diagnostic devices. These components require high durability, resistance to chemicals, and precise engineering.
- Surgical Instrument Handles: Handles for scalpels, forceps, and other surgical tools are often injection-molded for ergonomic grip and durability.
- Diagnostic Device Housings: Devices like glucose meters, blood analyzers, and ultrasound probe casings require precision molding to ensure durability and hygiene.
- Endoscopic Components: The housings and internal parts of endoscopic tools are made using high-performance plastics to withstand sterilization and repeated use.
Implantable and Biocompatible Medical Devices
For implantable medical devices, biocompatibility, sterilization resistance, and longevity are critical. Medical parts mold factories use advanced injection molding techniques to create these specialized components.
- Orthopedic Implants: PEEK and other medical-grade polymers are used for spinal implants and bone fixation devices due to their strength and biocompatibility.
- Dental Prosthetics and Aligners: Clear aligners, denture bases, and orthodontic components are precision-molded to fit patients’ needs perfectly.
- Drug Delivery Systems: Injection-molded components are used in insulin pens, inhalers, and auto-injectors to provide precise medication dosages.
Sterile Packaging and Medical Containers
Medical parts mold factories also manufacture sterile packaging and containers that protect medical instruments and pharmaceuticals from contamination.
- Blister Packs and Vials: These are used for packaging tablets, capsules, and liquid medications while ensuring sterility and ease of use.
- Sterilization Trays: Plastic sterilization trays are designed to hold surgical tools and medical instruments during autoclaving processes.
- Specimen Collection Containers: Urine cups, stool sample containers, and swab tubes are injection-molded for high-volume, contamination-free medical testing.
Wearable Medical Devices and Monitoring Systems
The rise of digital healthcare has increased the demand for injection-molded components in wearable medical technology.
- Blood Pressure Monitor Components: Plastic casings and internal components for blood pressure cuffs and monitoring devices are molded with precision.
- Hearing Aids and Cochlear Implant Casings: These require lightweight, durable, and comfortable materials for long-term patient wear.
- Continuous Glucose Monitoring (CGM) Sensors: Injection-molded housings protect the delicate electronic sensors that help diabetic patients track their blood sugar levels.
Medical parts mold factories utilize injection molding to produce a vast range of critical medical components, ensuring safety, precision, and cost-effectiveness. From disposable medical supplies and surgical tools to implantable devices and wearable technology, injection molding enables mass production while maintaining the highest quality standards. As medical technology advances, the demand for precision-molded medical parts will continue to grow, driving innovation in materials and manufacturing processes.
Advantages of Plastic Injection Molding in Medical Parts Mold Factories
Plastic injection molding offers numerous benefits when used in medical applications, especially when considering the high precision, volume, and compliance required in the healthcare industry. For medical parts mold factories, this manufacturing process is essential to meet the stringent standards of safety, quality, and functionality demanded by medical devices and components. This answer will explore the key advantages of plastic injection molding in medical applications, focusing on aspects such as precision, cost-effectiveness, scalability, material versatility, and regulatory compliance.
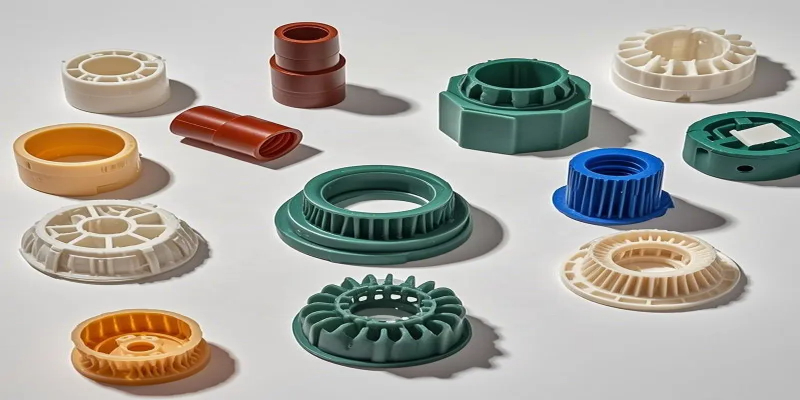
Precision and Accuracy in Medical Parts Mold Factories
One of the most significant advantages of plastic injection molding in medical parts mold factories is the exceptional precision and accuracy it provides. Injection molding allows for the production of parts with tight tolerances and complex geometries, which are crucial for medical devices that need to meet specific functional and safety standards. High-quality molds enable manufacturers to produce parts with consistency, ensuring that each component fits and functions precisely as intended, whether it’s a syringe, IV connector, or surgical tool.
Medical devices often have small and intricate parts, and injection molding can easily produce these at scale without compromising on quality. The use of advanced technologies like multi-cavity molds and precision-machined tools ensures that high-quality medical components are made with exacting standards. This capability helps in creating parts that are durable, reliable, and free from defects that could compromise patient safety.
Cost-Effectiveness and Efficiency
Plastic injection molding is an extremely cost-effective manufacturing process, especially for high-volume production runs. While the initial investment for creating molds can be expensive, the cost per unit decreases significantly as production volume increases. This makes it ideal for mass-producing medical devices like disposable syringes, diagnostic components, and surgical instruments. The efficiency of injection molding means that medical parts mold factories can produce thousands of parts in a relatively short time, significantly lowering the cost of production per item.
Moreover, the process itself is highly automated, reducing the need for extensive labor while maintaining high consistency in product quality. As a result, medical manufacturers can meet demand while keeping costs under control, ultimately passing the cost benefits onto consumers and healthcare providers. This makes injection molding a preferred method for mass-producing disposable medical components.
Scalability and Production Flexibility
Another key advantage of injection molding in medical parts mold factories is its scalability. Injection molding is well-suited to both small and large production runs, offering the flexibility to meet varying demand levels. Once the mold is created, it can be used to produce thousands to millions of identical parts, making it ideal for manufacturing medical devices with consistent quality and precision.
Medical parts mold factories can also modify the process to produce different sizes or variations of a medical component by using customized molds or altering the material used. This flexibility allows manufacturers to quickly adapt to changing needs in the healthcare sector and produce a wide range of medical devices using the same underlying process.
Material Versatility for Medical Parts
Injection molding allows for a wide range of material options, enabling medical parts mold factories to select the best material for each specific application. Medical-grade plastics, such as polycarbonate (PC), polypropylene (PP), and polyethylene (PE), offer the right balance of strength, flexibility, and biocompatibility for various medical devices. Additionally, plastics like silicone and thermoplastic elastomers (TPE) can be used for flexible medical components such as seals, gaskets, and implants.
This material versatility is essential for producing medical devices that must meet specific biocompatibility, chemical resistance, and sterilization requirements. With injection molding, manufacturers can choose materials that ensure both the functionality and safety of medical devices, meeting strict industry regulations and standards.
Regulatory Compliance and Quality Assurance
In the medical industry, products must comply with strict regulatory standards set by organizations such as the FDA and ISO to ensure patient safety. Plastic injection molding in medical parts mold factories is advantageous because the process is highly controlled, making it easier to adhere to these rigorous standards. The manufacturing process can be easily documented, and production records can be maintained to demonstrate compliance with quality assurance protocols.
Medical parts mold factories use advanced monitoring systems and quality control processes to ensure that the parts meet the exact specifications required. This includes testing for things like dimensional accuracy, strength, and sterilization compatibility. The precision of injection molding, combined with careful documentation and process control, helps ensure that medical parts meet the highest standards of quality, safety, and consistency.
Plastic injection molding provides numerous advantages for medical parts mold factories, making it an essential process for the production of high-quality, reliable medical components. From precise manufacturing and cost-efficiency to scalability and material versatility, the injection molding process is ideally suited for producing medical devices that meet the stringent demands of the healthcare industry. Moreover, injection molding ensures compliance with industry regulations, helping manufacturers produce safe and effective medical devices. With its ability to deliver precision, flexibility, and high-volume production, injection molding remains the preferred method for medical parts mold factories to meet the growing demands of the healthcare sector.
Why Do Medical Parts Mold Factories Attach Importance to MedAccred Certification?
Medical parts mold factories operate in a highly regulated industry where precision, quality, and compliance are critical. Any defect in molded medical components can lead to serious consequences, including product recalls, regulatory penalties, and risks to patient safety. To ensure that manufacturing processes meet the highest industry standards, many medical mold factories pursue MedAccred certification. This certification, issued by the Performance Review Institute (PRI), verifies that a factory’s injection molding and manufacturing processes comply with stringent medical quality requirements. Below, we explore why medical parts mold factories place significant importance on MedAccred certification through several key aspects.
Ensuring Compliance with Stringent Medical Industry Standards
MedAccred certification ensures that medical parts mold factories comply with globally recognized quality and safety standards. Regulatory bodies and medical device manufacturers require strict adherence to production protocols to avoid defects and maintain patient safety.
- Alignment with ISO and FDA Requirements: MedAccred certification complements international standards like ISO 13485 (Quality Management for Medical Devices) and FDA regulations, reinforcing compliance with the highest medical industry expectations.
- Standardized Manufacturing Processes: Certification ensures that injection molding procedures are consistently controlled and documented, reducing variability in production and improving product reliability.
- Risk Reduction in Production: By following MedAccred guidelines, factories can minimize risks such as contamination, material defects, and improper mold designs that could compromise medical device performance.
Gaining Trust and Recognition from Medical Device Manufacturers
Medical device companies prefer to partner with mold factories that hold MedAccred certification, as it demonstrates a commitment to high-quality manufacturing. This certification acts as a key differentiator in a competitive industry.
- Preferred Supplier Status: Many leading medical device manufacturers prioritize MedAccred-certified suppliers when sourcing molded components, ensuring their supply chain meets the highest standards.
- Increased Business Opportunities: Certification opens doors to new contracts with top-tier medical companies that require validated, traceable, and high-precision injection-molded components.
- Enhanced Reputation: MedAccred-certified factories gain credibility in the industry, reinforcing their position as reliable and trusted manufacturers of medical parts.
Improving Production Efficiency and Reducing Costs
While achieving MedAccred certification requires investment, it ultimately helps medical parts mold factories enhance their operational efficiency and reduce long-term manufacturing costs.
- Optimized Injection Molding Processes: The certification process includes audits that help factories refine their molding techniques, improving production efficiency and reducing material waste.
- Lower Defect and Scrap Rates: MedAccred-certified factories follow strict process controls, leading to fewer defective parts and reducing the costs associated with rework or recalls.
- Predictable and Consistent Output: Standardized production methods ensure consistency across batches, minimizing variations and ensuring product reliability.
Strengthening Patient Safety and Product Reliability
Patient safety is the top priority for medical device manufacturers, and MedAccred certification ensures that molded medical components meet the highest safety and performance standards.
- High-Precision Molding for Critical Components: Medical parts such as implantable devices, syringes, and IV connectors must meet exact specifications to function safely. MedAccred certification verifies that factories maintain precision in their molding processes.
- Biocompatibility Assurance: Certified factories follow strict material selection and handling procedures to ensure that all plastics used in medical molding are biocompatible and free from contamination.
- Failure Prevention: Certification reduces the likelihood of manufacturing defects that could lead to device malfunctions, protecting both patients and medical professionals.
Staying Competitive in a Regulated and Evolving Market
As the medical manufacturing industry evolves, staying ahead of regulatory changes and technological advancements is crucial. MedAccred certification helps mold factories remain competitive by ensuring they meet the latest industry requirements.
- Adapting to Changing Regulations: As global medical device standards evolve, MedAccred-certified factories stay compliant with new industry expectations, reducing the risk of non-compliance.
- Advancing with New Technologies: Certified factories are often better equipped to adopt innovative injection molding technologies, such as micro-molding for minimally invasive medical devices.
- Meeting the Demands of a Growing Industry: The demand for precision-molded medical components continues to rise, and MedAccred certification helps manufacturers position themselves as leaders in the field.
Medical parts mold factories place significant importance on MedAccred certification because it ensures compliance with industry regulations, builds trust with medical device manufacturers, improves production efficiency, enhances patient safety, and keeps them competitive in an evolving market. By obtaining this certification, medical mold factories demonstrate their commitment to high-quality manufacturing, regulatory compliance, and continuous process improvement—factors that are essential for success in the medical device industry.
The Medical Injection Molding Process in Medical Parts Mold Factories
The medical injection molding process plays a critical role in the manufacturing of medical devices, components, and packaging. In medical parts mold factories, injection molding is used to produce high-quality, precision parts that meet stringent industry regulations and safety standards. This manufacturing process is highly efficient, capable of producing thousands to millions of identical components with great accuracy and consistency. In this answer, we will explore the various stages of the medical injection molding process, including preparation, injection, cooling, and finishing, as well as key considerations for ensuring the production of safe and effective medical components.
Material Selection and Preparation
Before the injection molding process begins, material selection is one of the most important steps in producing medical-grade parts. Medical parts mold factories must choose plastics that are biocompatible, durable, and able to withstand the sterilization processes required for medical use. Common materials include polycarbonate (PC), polypropylene (PP), silicone, and PPSU (polyphenylsulfone).
Once the material is selected, it is then prepared for injection molding. The raw plastic, often in the form of pellets or granules, is fed into a hopper, where it is heated to a molten state. The exact temperature and processing conditions depend on the material being used and the specifications for the final product. Proper material preparation ensures that the molding process can proceed without defects and that the final product has the necessary mechanical properties.
Injection Phase
The injection phase is where the heated plastic is injected into a mold under high pressure. The process starts by filling the injection barrel with the molten material, where it is then pushed into a mold cavity. The mold is specifically designed to form the shape of the medical component, such as a syringe, catheter, or surgical instrument.
During this stage, the plastic flows into all parts of the mold, filling every cavity to form a precise and uniform part. The high pressure ensures that the material reaches all corners and crevices, allowing for intricate designs and small details that are often required in medical applications. The injection phase is typically very fast, often taking just a few seconds to a minute per cycle, depending on the size and complexity of the part.
Cooling Phase
Once the mold cavity is filled with molten plastic, the material begins to cool and solidify. Cooling is a critical part of the injection molding process because the shape and dimensional accuracy of the final medical component depend on how evenly and completely the plastic cools.
In medical parts mold factories, the cooling phase is carefully controlled to ensure that the material cools at a uniform rate to avoid warping or distortion. Cooling channels in the mold are used to regulate the temperature, and the cycle time for cooling is optimized based on the material being used and the part’s geometry. The time required for cooling can vary depending on the size of the part, with smaller parts typically cooling faster than larger ones. Once the part is sufficiently cooled, it becomes rigid and ready for the next phase.
Ejection and Post-Processing
After the component has cooled and solidified, it is time for the mold to be opened, and the part is ejected. The mold is separated, and the finished part is carefully removed from the mold cavity using automated ejection systems or manual tools. The mold design is typically equipped with ejector pins that push the part out without causing damage to the product.
However, the process doesn’t end here. Many medical parts require post-processing steps to ensure they meet strict standards. These processes may include:
- Trimming: Removing excess plastic or flashing from around the part.
- Polishing or surface treatment: Enhancing the appearance or functionality of the component, such as adding a smooth finish to prevent irritation during use.
- Sterilization: Certain parts may undergo sterilization, such as gamma radiation or autoclaving, to ensure they are safe for medical use.
Quality Control and Testing
One of the most critical steps in the medical injection molding process is quality control. Medical parts mold factories must ensure that each part meets stringent regulatory requirements and quality standards, such as FDA and ISO certifications. As such, extensive inspection and testing procedures are carried out at various stages of production.
This may include:
- Dimensional checks: Ensuring the parts meet tight tolerances and precise measurements.
- Visual inspection: Checking for defects like cracks, warping, or surface imperfections.
- Mechanical testing: Testing the strength, durability, and biocompatibility of the parts.
- Sterility testing: Ensuring the parts can be sterilized effectively and are free from contaminants.
Final Assembly and Packaging
In some cases, after the molding process is complete, the medical components undergo final assembly. Medical parts mold factories may incorporate additional processes, such as overmolding (molding additional materials onto the part) or insert molding (molding over pre-inserted components like metal or plastic inserts). After assembly, the parts are then packaged, typically in a cleanroom environment to ensure that the components remain sterile and safe for medical use.
The medical injection molding process is a highly specialized and efficient manufacturing method used in medical parts mold factories to create high-precision, safe, and reliable medical components. From material selection to post-processing and quality control, each step in the process ensures that the final product meets the high standards required for the medical industry. By carefully controlling every phase of the molding process, medical parts mold factories are able to produce components that are durable, biocompatible, and ready for use in medical applications worldwide.
FAQs about Medical Parts Mold Factories
BMP Medical’s headquarters is located in Lake Zurich, Illinois, United States. The company is well-positioned to serve medical device manufacturers across the country, offering a range of services that include the precision manufacturing of medical-grade components. BMP Medical operates a state-of-the-art facility that adheres to strict FDA and ISO 13485 regulations, ensuring that all products meet the highest standards of quality, safety, and performance. The company’s services include medical injection molding, design consultation, and packaging solutions for various medical applications, including diagnostic tools, surgical instruments, and pharmaceutical packaging. BMP Medical is a trusted partner for businesses in the medical field, providing them with reliable, precision-engineered solutions.
Medical molding is the process of manufacturing plastic components used in medical devices and related products, with a primary focus on ensuring precision, sterility, and compliance with regulatory standards. The process typically involves injection molding, where plastic material is injected into a mold to create the desired part shape. These molded parts are crucial for creating everything from diagnostic equipment to surgical tools and medical packaging. Medical molding requires specialized techniques and materials, such as biocompatible plastics like PEEK, polycarbonate, and silicone, which meet stringent health and safety regulations. Given the high stakes involved, medical molding processes are often carried out in cleanroom environments to avoid contamination, ensuring the parts are safe for medical use. This process plays a critical role in the healthcare industry by providing durable, reliable, and safe components that are essential for patient care.
The cost of a manufacturing mold can vary significantly based on several factors, including the complexity of the mold design, the materials used, and the production requirements. On average, a basic mold may cost anywhere from $1,000 to $12,000, especially for simpler designs. However, for more complex molds or those used for medical parts, the cost can range from $20,000 to $100,000 or more. Medical parts mold factories often deal with higher mold costs due to the precise requirements and specialized materials used, ensuring that the final components meet strict industry standards. Factors such as mold size, material selection, and whether the mold is designed for high-volume or low-volume production can also influence pricing. Molds for medical applications often require additional steps to ensure biocompatibility and compliance with regulatory standards, further adding to the cost. To determine the exact cost, it is advisable to consult with an experienced mold manufacturer who can assess the specifics of the project.
The global mold industry is a large and rapidly growing sector, with the plastic injection molding market alone valued at approximately $300 billion. This market continues to expand due to increasing demand for molded parts across various industries such as automotive, electronics, consumer goods, and particularly the medical sector. Medical parts mold factories play a significant role in this growth as the need for high-quality, precision-engineered medical components rises. As technology advances, particularly in areas like 3D printing and automation, the mold industry is evolving to meet the demands for faster production, reduced costs, and higher accuracy. The medical molding sector, in particular, is seeing increased demand due to the growing need for safe, durable, and sterile components used in medical devices, diagnostics, and packaging. The mold industry remains a critical element in global manufacturing, supporting the production of millions of parts and components used in everyday products and advanced medical devices.
Molds play a crucial role in pharmaceutical manufacturing, particularly in the production of medical devices and packaging components. Injection molds are used to create precise and sterile components such as syringes, inhalers, vials, IV connectors, and pill casings. These molds must meet stringent FDA and ISO regulations to ensure the highest standards of hygiene and safety. Medical-grade plastics like polypropylene and polycarbonate are commonly used because they are biocompatible, resistant to chemicals, and durable. Additionally, molds help in producing lab equipment, diagnostic components, and surgical tools with high accuracy and repeatability. Advanced mold technologies, such as multi-cavity and micro-molding, enable mass production of pharmaceutical parts with minimal waste. The pharmaceutical field also relies on silicone rubber molds for producing flexible components like gaskets and seals. The use of precise molding techniques ensures that medical products meet strict quality standards, reducing contamination risks and enhancing patient safety.
The global medical injection molding market has been experiencing steady growth due to the rising demand for disposable medical devices, minimally invasive surgical instruments, and pharmaceutical packaging. As of recent reports, the market size is valued at approximately $20 billion and is expected to grow at a CAGR of 5-7% over the next decade. The increasing need for high-volume production of precision medical components drives this expansion. North America and Europe lead the market due to their strong healthcare infrastructure and regulatory compliance requirements, while Asia-Pacific is emerging as a key player due to lower manufacturing costs and growing medical device exports. Factors such as advancements in material science, automation in molding processes, and the demand for customized medical components further contribute to market growth. The market’s expansion is also fueled by the increasing adoption of biodegradable and biocompatible materials for sustainable healthcare solutions.
Historically, molds have played a significant role in medicine, particularly in the development of antibiotics. The most famous example is Penicillium mold, which led to the discovery of penicillin by Alexander Fleming in 1928. This breakthrough revolutionized modern medicine by enabling the treatment of bacterial infections. Before this discovery, molds were used in traditional medicine across various cultures. Ancient Egyptians, for instance, used moldy bread to treat wounds and infections due to its natural antibacterial properties. Traditional Chinese medicine also recognized certain fungi for their healing properties, utilizing them for immune-boosting and anti-inflammatory purposes. Over time, researchers have explored other molds for their medicinal potential, leading to the development of additional antibiotics and antifungal medications. Today, molds continue to be studied for new pharmaceutical applications, including immunosuppressants and cholesterol-lowering drugs, demonstrating their enduring medical significance.
The cost of injection molding per hour varies based on machine size, complexity, and material selection. On average, the hourly rate for a standard injection molding machine ranges from $50 to $200, while high-precision medical-grade machines can cost $250 to $500 per hour. Factors influencing costs include mold complexity, cycle time, material choice (such as medical-grade plastics), and labor costs. Cleanroom molding, which is often required for medical applications, further increases expenses due to the need for contamination-free environments. Additionally, the cost of creating a medical injection mold can range from $5,000 to over $100,000, depending on design intricacies and material requirements. Despite these costs, injection molding remains a cost-effective method for mass-producing high-quality, standardized medical components. Companies often optimize production by using multi-cavity molds and automation to reduce per-unit costs, making large-scale manufacturing more economically viable.
Injection molding, particularly in the medical parts sector, is a highly profitable industry due to its ability to produce large volumes of precision components at low per-unit costs. Profitability depends on factors like initial tooling investment, production scale, and efficiency of operations. Medical injection molding is especially lucrative because it involves high-value, regulatory-compliant products such as surgical instruments, implants, and diagnostic devices. Companies that invest in automation, cleanroom facilities, and high-cavitation molds can significantly increase their profit margins by reducing labor costs and enhancing production efficiency. Additionally, recurring demand for disposable medical devices ensures consistent revenue streams. While the initial investment in molds and machinery is substantial, the long-term benefits outweigh the costs, with many manufacturers achieving 30-50% profit margins depending on the product type and market demand. As the healthcare industry continues to grow, injection molding businesses specializing in medical components are expected to remain highly profitable.
Yes, injection molding is generally cheaper than machining when producing medical parts in large quantities. While CNC machining is suitable for low-volume or highly customized components, injection molding becomes significantly more cost-effective for mass production. The primary advantage of injection molding is its ability to produce thousands to millions of identical parts at a low per-unit cost, whereas machining is a slower and more labor-intensive process. Medical injection molding also allows for complex geometries, tight tolerances, and high repeatability, making it ideal for disposable medical devices and intricate components like catheter tips and surgical handles. However, the upfront cost of mold fabrication can be high, ranging from $5,000 to $100,000+, depending on design complexity. Despite this, once the mold is made, the cost per part decreases significantly, making injection molding the preferred method for high-volume medical manufacturing compared to machining.
Injection molds are used for manufacturing a wide range of medical parts, ensuring high precision, durability, and sterility. They produce essential components such as syringes, IV connectors, catheters, surgical instruments, diagnostic devices, and pharmaceutical packaging. Medical-grade molds must meet strict regulatory standards like ISO 13485 and FDA approvals to ensure patient safety and product reliability. These molds are typically made from hardened steel or aluminum, allowing for high-volume production without compromising accuracy. In addition to traditional medical components, injection molds are used for micro-molding, producing ultra-small parts for minimally invasive surgeries and implantable devices. Multi-cavity and high-speed molding techniques further enhance production efficiency. The demand for single-use, contamination-free medical products has significantly increased, making injection molding a preferred method for manufacturing high-quality, sterile medical parts at scale. With advancements in biodegradable and antimicrobial materials, the role of injection molds in medical manufacturing continues to expand.
An injection molding job in a medical parts mold factory involves producing high-precision plastic components for medical applications, such as syringes, IV connectors, and surgical instrument housings. Workers in these jobs operate and maintain injection molding machines, ensuring that medical-grade plastics are heated, injected into molds, and cooled to form exact parts. These jobs require technical expertise in machine operation, mold design, and quality control. Due to strict medical standards, employees must follow FDA and ISO regulations to ensure the parts meet biocompatibility and sterility requirements. Engineers in these factories design and optimize molds to improve efficiency and minimize material waste. The industry also employs quality inspectors who use advanced testing methods to check for defects. With automation increasing in medical injection molding, many jobs now involve working with robotics and AI-driven inspection systems to maintain high precision and consistency.
In medical manufacturing, a mold is a custom-designed tool used to shape plastic into medical components through injection molding. Molds are typically made from high-grade stainless steel or aluminum and feature cavities that determine the final shape of the part. The mold is placed inside an injection molding machine, where heated medical-grade plastic, such as polycarbonate or PEEK, is injected under high pressure. Once cooled, the solidified plastic retains the mold’s shape and is ejected for further processing. In the medical field, molds must be engineered with extreme precision to ensure consistency, as even minor defects can impact the functionality and safety of medical devices. Advanced medical molds may also include multiple cavities for high-volume production, microfluidic channels for lab-on-a-chip devices, or specialized coatings to prevent contamination. Proper maintenance and sterilization of molds are crucial to maintaining the integrity of medical components.
Mold and cast manufacturing are both used in medical parts production, but they serve different purposes. Mold manufacturing, such as injection molding, is a high-precision process where molten plastic is injected into a metal mold to create detailed and complex medical components like drug delivery systems, inhalers, and prosthetic parts. This method ensures mass production with tight tolerances and consistent quality.
On the other hand, casting involves pouring liquid material (such as silicone or metal) into a mold, where it solidifies into shape. Casting is used for low-volume, custom medical parts, such as orthopedic implants or prosthetic sockets. It is preferred for materials that do not easily undergo injection molding, such as certain biocompatible alloys. While injection molding is faster and more cost-effective for mass production, casting is ideal for prototyping or specialized medical applications requiring unique geometries or material properties.
For medical parts mold factories, the best mold material depends on production volume, precision, and sterilization requirements. Stainless steel is the most common material for high-volume medical injection molding due to its durability, corrosion resistance, and ability to withstand repeated sterilization. Aluminum molds are also used, especially for prototyping or lower production runs, because they are cheaper and easier to machine, though they wear out faster than steel.
Some high-end medical applications use Nickel-based alloys for added strength and anti-bacterial properties. For microfluidic and bio-medical applications, specialized coatings such as diamond-like carbon (DLC) or Teflon coatings are applied to prevent contamination and ensure smooth part ejection. The material selection also depends on the type of plastic being molded—high-temperature plastics like PEEK require heat-resistant mold materials. Proper maintenance, cleaning, and precision engineering are crucial for long mold lifespan and consistent medical-grade parts.
Injection molding is a specific type of molding widely used in medical parts manufacturing. In injection molding, molten medical-grade plastic is injected under high pressure into a mold cavity to produce complex and high-precision parts, such as catheters, connectors, or surgical instruments.
“Molding” is a broader term that includes various techniques, such as compression molding, blow molding, and rotational molding, which may be used for different medical applications. For example, compression molding is used for rubber medical seals, while blow molding creates hollow parts like IV solution bottles.
Injection molding is preferred for high-precision medical components requiring sterility and consistency. It offers rapid production speeds, tight tolerances, and minimal waste. Other molding methods may be more suitable for low-volume production, flexible materials, or specific design requirements.
A mold is the physical tool or cavity used to shape a material into a specific form, while molding refers to the process of shaping that material. In medical injection molding, a mold is typically made of stainless steel and precisely engineered to produce components like syringe plungers or ventilator parts.
Molding, on the other hand, describes the process of injecting, compressing, or forming a material into a shape using the mold. In medical parts manufacturing, molding must meet strict regulatory standards to ensure biocompatibility and precision. The mold itself must be meticulously maintained, as even slight wear can affect the quality of the molded medical components.
In summary, a mold is the hardware (the tool), while molding is the process of using that tool to manufacture parts.
In medical injection molding, some of the hardest and most durable plastics include PEEK (Polyetheretherketone), Ultem (PEI – Polyetherimide), and PPSU (Polyphenylsulfone).
PEEK is one of the hardest and most heat-resistant plastics, often used in surgical implants, dental components, and high-stress medical devices. It can withstand repeated sterilization and has mechanical properties similar to bone, making it a preferred choice for orthopedic implants.
Ultem (PEI) is another high-strength, biocompatible plastic used for medical instrument housings and sterilization trays due to its ability to endure harsh cleaning chemicals.
PPSU is widely used in surgical instruments and sterilization trays, as it can withstand high-impact forces and temperatures above 200°C.
These materials are challenging to mold due to their high melting points and viscosity, requiring specialized high-temperature molds and advanced injection molding machines.
Injection molding for medical parts is expensive due to high mold fabrication costs, strict regulatory requirements, and precision demands.
Mold Costs: High-quality medical molds are made from durable materials like stainless steel and require precision machining, often costing tens of thousands of dollars.
Regulatory Compliance: Medical-grade plastics must meet FDA and ISO standards for biocompatibility, sterility, and performance, adding to material and testing costs.
Material Costs: High-performance plastics like PEEK, Ultem, and medical-grade silicones are more expensive than standard plastics due to their specialized properties.
Quality Control: Medical parts must be defect-free, requiring rigorous testing, cleanroom manufacturing, and automated inspection systems, all of which add costs.
Machine and Maintenance Costs: Injection molding machines for medical parts are advanced, requiring precise temperature and pressure control, as well as frequent maintenance to ensure accuracy.
Despite these high costs, injection molding remains cost-effective for large-scale medical production due to its efficiency, consistency, and ability to produce sterile, high-precision parts.
Contact our professional team now for a same-day quote and risk-free project evaluation. Benefit from ISO 8 cleanrooms, advanced machines, and 12-hour fast response in medical injection molding.