Precision medical machining refers to the process of manufacturing high-precision components used in medical devices. It plays a critical role in producing intricate parts that meet strict standards for quality, performance, and reliability in the medical industry. In addition to machining, medical injection molding is another key process used by manufacturers to create parts with tight tolerances, particularly for high-volume production.
A medical plastic molding trader also plays a vital role in ensuring these advanced techniques are utilized effectively, ensuring that parts are produced consistently and accurately to meet the stringent requirements for life-saving devices. In the healthcare industry, precision is essential due to the need for high-quality materials and tight tolerances in medical device manufacturing. A medical plastic components manufacturer must ensure that parts are not only functional but also safe for patients. Any discrepancies in manufacturing can affect device performance, potentially leading to patient safety issues. Precision machining ensures that components are consistent, reliable, and effective in critical medical applications. As a leading medical plastic components manufacturer, FUJIU Medical Injection Mold works closely with medical plastic molding traders to manufacture customized, high-quality parts for medical devices.
Low-Volume to High-Volume Production Capabilities
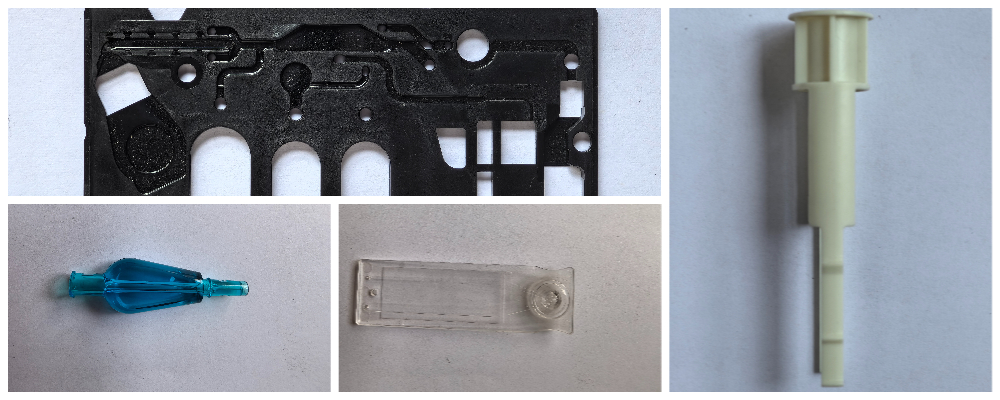
Attributes | Details |
---|---|
Place of Origin | Dongguan, Guangdong, China |
Brand Name | LY Medical Injection Mold |
Molding Mode | Plastic Injection Mold |
Product Name | Plastic Injection Medical Parts Plastic Injection Mold Medical |
Model | Customizable |
Product Material | Plastic |
Material | ABS, PP, PEEK, PC, PMMA, POM, etc. |
Surface Treatment | Original, Matte or Customized Surface Texture |
Color | White, Black, Gray or Customized Color |
Size | Customized Size |
Service | OEM/ODM Customization |
Packing | Plastic Bag Packaging or Packaging According to Customer Requirements |
Shipping | By Sea or Air According to Customer Requirements |
Core Capabilities of Precision Medical Machining by Medical Plastic Components Manufacturer
Material Handling and Expertise
A medical plastic components manufacturer must have a deep understanding of the materials used in medical machining. Common materials include stainless steel, titanium, Inconel, aluminum, plastics, and various alloys. Each material is selected based on the specific needs of the medical device it is intended for. For example, titanium is often used in implants and surgical tools due to its strength and biocompatibility, while plastics are commonly chosen for diagnostic equipment and disposable medical devices due to their versatility and cost-effectiveness. The right material ensures that the finished medical component meets the necessary performance, safety, and durability standards required in healthcare applications.
Machining Processes and Technologies
Medical plastic components manufacturers employ a variety of machining processes to achieve the precision required for medical devices.
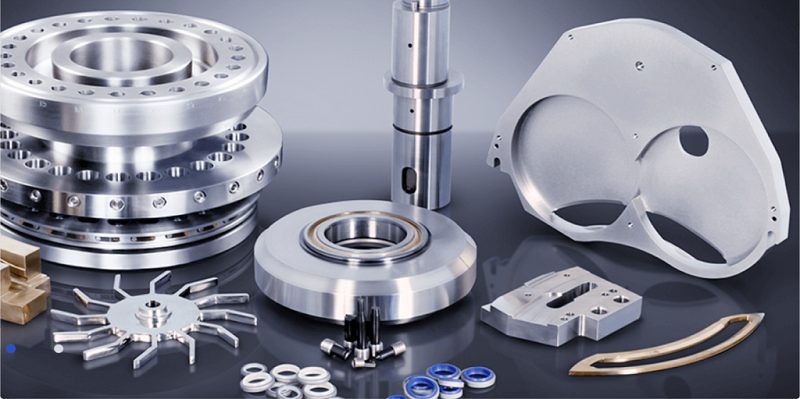
CNC Milling and Turning
These processes are essential for creating medical components with tight tolerances. CNC machines offer high accuracy and consistency, which are crucial for producing parts that fit precisely within complex medical systems, such as surgical instruments and diagnostic devices.
Swiss Machining
This process is ideal for producing small, intricate parts with very tight tolerances. Swiss machining is particularly effective for creating components like miniature gears and small, precise components found in cardiac devices, where accuracy is critical.
EDM (Electrical Discharge Machining)
EDM is used for precision cutting of complex geometries and hard metals. It’s especially valuable for medical components that require very fine details, such as those used in implants and surgical tools. EDM ensures that even the most intricate shapes are produced with high precision.
Multi-axis Machining
Multi-axis machines enable the creation of highly complex medical components that require multiple angles of machining. This technology is beneficial for the production of parts used in advanced medical devices, such as robotic surgery instruments or specialized diagnostic equipment, where detailed, multi-dimensional precision is necessary.
Injection Molding
Injection molding is one of the most widely used techniques for producing high-precision medical plastic components in large volumes. In this process, molten plastic is injected into a mold cavity under high pressure. The plastic then cools and solidifies, taking the shape of the mold. Injection molding is essential for producing components like syringes, blood collection tubes, connectors, and housings for medical devices.
Blow Molding
Medical blow molding is used to create hollow plastic parts, such as bottles, containers, and certain types of tubing, which are commonly used in the medical industry. In this process, a hollow tube of plastic is inflated inside a mold to form the desired shape. Blow molding is frequently used for manufacturing medical products like IV bottles, medical bags, and catheters.
Thermoforming
Thermoforming is a plastic manufacturing process where a plastic sheet is heated until it becomes soft and pliable, then molded into the desired shape using a mold or tool. This method is often used to create trays, packaging, or protective covers for medical devices. Medical applications for thermoforming include packaging for sterile instruments, custom trays for surgical tools, and components that require a specific shape for ease of use.
A medical plastic components manufacturer utilizes these advanced machining technologies to ensure the highest levels of precision and performance in their medical products. These capabilities are vital for producing safe and reliable devices that meet the stringent demands of the healthcare industry.
Notable Medical Components Manufactured by Precision Machining Companies and Medical Plastic Components Manufacturer
Examples of Medical Parts
A medical plastic components manufacturer plays a pivotal role in the production of a wide range of essential medical parts used across various healthcare applications. Some of the most common components include surgical instruments, diagnostic equipment like MRI and CT scanners, respiratory devices, and implants. Surgical instruments, such as scalpels, forceps, and surgical scissors, require precise machining to ensure that they are sharp, durable, and easy to handle in critical medical procedures. Diagnostic equipment, including parts of MRI and CT scanners, must meet stringent tolerances to ensure that images are accurate, providing essential information for diagnosis.
In addition to general medical devices, specialized components like catheters, ligation devices, and orthopedic implants are also produced using precision machining. Precision mold medical techniques are often employed to create parts like these, ensuring that they meet the exacting standards necessary for medical use. For instance, catheters need to be flexible yet strong, with precise measurements to ensure that they perform effectively during medical procedures. Likewise, orthopedic implants such as joint replacements and spinal devices must be manufactured to exact specifications for them to function properly inside the human body. Dental equipment, which includes tools like drills and scalers, also requires the fine-tuned accuracy provided by a medical plastic components manufacturer. Furthermore, miniature gears used in cardiac devices must be crafted with exceptional precision to maintain the integrity of the device and ensure its correct function.
High-Precision Components in Action
Precision machining ensures the reliability and safety of critical medical devices that are used in a variety of healthcare fields. For example, implants such as pacemakers, hip replacements, and dental implants rely on precision machining to guarantee that they fit perfectly within the body, minimizing the risk of complications. Additionally, diagnostic tools, including biopsy needles and endoscopic instruments, require extreme precision to avoid causing damage to delicate tissues or missing key diagnostic information.
A medical plastic components manufacturer ensures that all parts meet strict regulatory and quality standards, which are critical for the safe use of medical devices. Each component undergoes rigorous quality assurance testing, including dimensional checks, material testing, and functional verification, to ensure that the final product can withstand the demands of the medical environment. By maintaining these high standards, precision machining companies ensure that their components not only meet industry regulations but also deliver exceptional performance, contributing directly to the safety and effectiveness of medical procedures. These high precision medical components are vital for healthcare professionals to make accurate diagnoses, perform safe surgeries, and provide effective patient care.
The Role of Certifications and Quality Control in Medical Machining by Medical Plastic Components Manufacturer
Industry Certifications
- ISO 9001 & ISO 13485:
A plastic medical machined components manufacturer must obtain key certifications like ISO 9001 and ISO 13485 to ensure that their manufacturing processes meet high standards of quality and regulatory compliance. ISO 9001 sets general quality management guidelines, while ISO 13485 is specific to the medical device industry, ensuring that medical products are consistently produced with quality and safety in mind. - ITAR Compliance:
For manufacturers involved in the production of components that may have military or sensitive applications, ITAR compliance is crucial. It guarantees that the manufacturing of these components adheres to international security regulations, especially for items that may be used in sensitive healthcare applications. - FDA Guidelines:
Compliance with FDA guidelines is a must for any medical plastic components manufacturer. These regulations ensure that medical components meet the stringent requirements set by the U.S. Food and Drug Administration. Adhering to these guidelines ensures that the components are safe, effective, and ready for use in healthcare, from diagnostic equipment to surgical instruments.
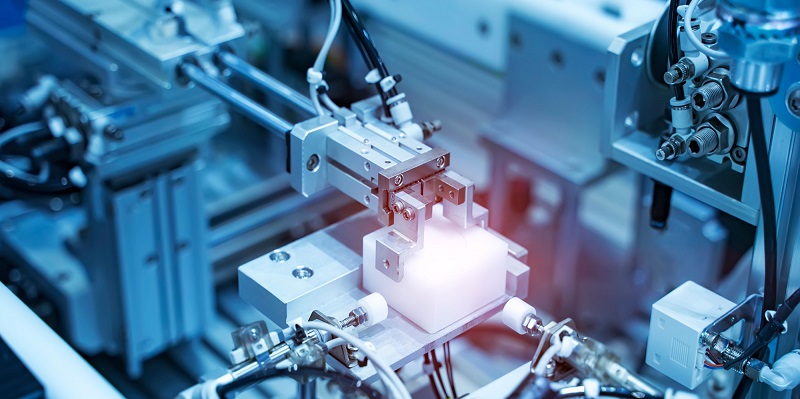
Quality Assurance and Testing
- Dimensional Checks:
One of the first steps in quality assurance is performing dimensional checks. This process ensures that the physical measurements of each part match the exact specifications outlined in the design, maintaining the tight tolerances necessary for medical applications. - Material Testing:
Material testing verifies the integrity of the raw materials used in the manufacturing process. For medical components, it’s critical that materials not only meet safety standards but are also durable and biocompatible to function correctly over time without causing harm to the patient. - Inspection Using Advanced Equipment:
Manufacturers use cutting-edge equipment, such as 3D scanning, coordinate measuring machines (CMM), and X-ray systems, to perform detailed inspections. This ensures that components are free of defects, ensuring both the safety and functionality of the parts. - Functional Testing:
Functional testing simulates real-world conditions to ensure that components perform as intended when used in medical devices. This step is crucial in confirming the reliability and performance of the parts in actual medical settings.
By following these rigorous testing and certification protocols, medical plastic components manufacturers ensure that every part is produced with the utmost precision, meets regulatory standards, and functions effectively in medical applications.
Benefits of Precision Medical Machining for the Healthcare Industry by Medical Plastic Components Manufacturer
Improved Patient Safety
- Better Fitting and Functionality:
One of the primary benefits of precision medical machining is that it ensures that medical components, such as implants, surgical instruments, and diagnostic devices, fit perfectly and function as intended. A medical plastic components manufacturer uses advanced machining techniques, such as CNC milling and turning, to produce components with tight tolerances and precise measurements. This high level of accuracy guarantees that each part meets the required specifications for safety and performance. For example, surgical instruments made with precise machining will fit seamlessly into their intended roles, reducing the risk of complications during procedures and ensuring better outcomes for patients. - Preventing Malfunctions and Ensuring Safety:
Precision machining significantly reduces the risk of malfunctions that could occur if components do not fit together properly or are manufactured with imperfections. The use of high-quality materials and exacting machining methods ensures that parts are durable, resistant to wear, and function as designed over the long term. For medical plastic components manufacturers, the ability to use top-grade plastics and other materials that meet biocompatibility standards is essential in preventing issues such as material degradation or harmful reactions when in contact with the human body. This level of quality control helps maintain patient safety, preventing device failure that could lead to serious health issues or even fatalities.
Cost Efficiency and Faster Turnaround
- Reducing Production Time and Costs:
Precision machining technologies, such as Swiss machining and multi-axis machining, enable medical plastic components manufacturers to produce medical components with greater efficiency. These advanced processes allow manufacturers to make high-quality parts in less time compared to traditional manufacturing methods. By optimizing the machining processes, a plastic injection molding medical parts manufacturer can reduce both production time and costs while maintaining the necessary standards of accuracy. This efficiency not only benefits the manufacturer but also lowers the overall cost for healthcare providers who rely on these components for medical devices. - Streamlined Production Methods:
The streamlined production processes made possible by precision machining also help meet the ever-growing demand for medical devices. With healthcare systems constantly requiring more innovative devices and solutions, it is crucial for manufacturer of injection-molded parts for medical devices to be able to deliver high-quality products within shorter lead times. Advanced machining techniques, along with improved medical device automation and production planning, enable manufacturers to produce components at a faster rate without compromising quality. This rapid turnaround helps ensure that critical medical devices, such as ventilators, surgical tools, or diagnostic equipment, are available when needed, thus supporting the overall healthcare system’s responsiveness to patient needs.
By combining improved safety, faster production, and cost savings, precision machining provides significant benefits for the healthcare industry. A medical component manufacturer can help improve patient outcomes by producing highly reliable, safe, and cost-effective medical components that are essential for modern healthcare.
What Is Medical Plastic Components Manufacturer
Plastic Medical Injection Part Molding Manufacturers
Plastic injection molding plays a crucial role in the manufacturing of medical components. Manufacturers of medical equipment using small plastic parts specialize in creating intricate and high-precision components required for medical devices. These parts often include customized precision medical apparatus components, ranging from tiny connectors, seals, and housings to larger components like surgical tools, catheters, and diagnostic equipment. By utilizing advanced injection molding technology, these manufacturers can produce high volumes of components with exceptional accuracy and efficiency.
Medical plastic parts exporter plays a key role in ensuring these high-quality components reach global markets, meeting industry standards for safety, durability, and performance. The process begins with injecting molten plastic material into a mold, which is then cooled and solidified to form the desired part. The ability to use a variety of plastic materials, including biocompatible and sterilizable plastics, makes this process ideal for medical applications. Plastic medical injection part molding manufacturers ensure that each component meets stringent industry standards for safety, durability, and performance. This manufacturing method is particularly advantageous for creating small, complex parts critical to the function of various medical devices.
Advantages of Injection Molding in Medical Equipment Manufacturing
- High Precision and Consistency:
One of the key benefits of using plastic injection molding in the manufacturing of medical components is the high level of precision it offers. The ability to create parts with tight tolerances ensures that small plastic components, such as connectors and valves, fit perfectly within medical devices. This precision is essential for maintaining the integrity and safety of medical equipment, particularly in devices where small plastic parts play a critical role in functionality. - Cost-Effective Production:
Injection molding allows plastic medical injection part molding manufacturers to produce large quantities of medical components at a lower cost compared to other methods. The speed and efficiency of the process help keep production costs down while maintaining the necessary quality standards. This cost-effectiveness is particularly beneficial for plastic medical device manufacturers who need to keep expenses manageable while producing reliable and safe devices. - Versatility in Material Choices:
Manufacturers of medical equipment using small plastic parts have access to a wide range of materials that can be used in the injection molding process. These materials can be chosen based on their specific properties, such as biocompatibility, strength, and resistance to sterilization. This versatility enables manufacturers to create parts that meet the unique requirements of various medical applications, ensuring that devices function properly and safely in different healthcare settings.
By utilizing plastic injection molding technology, medical plastic components manufacturercan produce high-quality, reliable, and cost-effective medical components that meet the rigorous demands of the healthcare industry. Whether it’s small plastic parts for complex devices or larger components for medical machinery, plastic medical injection part molding manufacturers are key players in ensuring the success of medical devices worldwide.
Factors To Consider When Choosing Medical Plastic Components Manufacturer
When selecting a medical device injection molding manufacturer, several key factors must be considered to ensure the company meets the specific requirements of the healthcare and pharmaceutical industries. These factors can help you make an informed decision, ensuring quality, efficiency, and compliance throughout the production process.
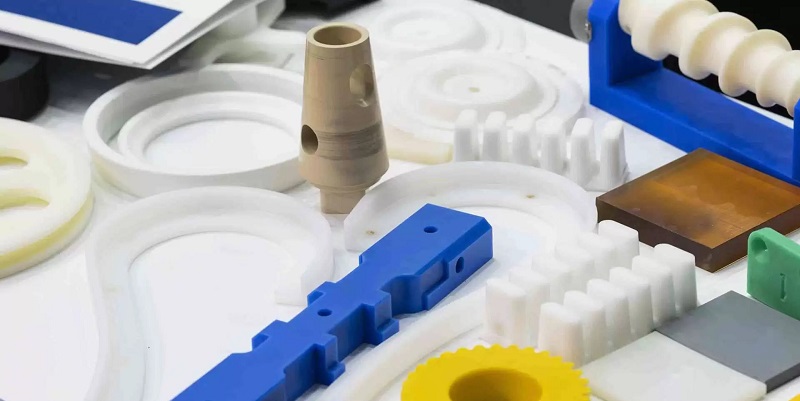
Industry Experience
The experience of a medical device component manufacturer is one of the most critical aspects to evaluate. A company with a proven track record in the medical industry is likely to deliver high-quality products that meet or exceed industry standards. Experience also ensures familiarity with the complexities of medical device manufacturing, from stringent regulatory compliance to the technical demands of molding precision components.
It’s also important to check whether the company uses high-quality machines and equipment that comply with FDA regulations. A background check can provide insight into the company’s experience and regulatory adherence.
Production Capacity and Volume
Another important consideration is the manufacturer’s production capacity. Depending on the volume of parts needed, you will want to choose a company that can handle your specific production requirements. A company with moderate production volume capabilities may be ideal for quick prototyping and low-to-mid volume runs (e.g., around 10,000 units), while high-volume manufacturers can produce large quantities, often exceeding 75,000 units, typically using smaller molds for efficiency.
Ensure the company can meet both your prototype needs and large-scale production demands, depending on your timeline and order volume.
Compliance with Industry Standards
Specification compliance is essential when choosing an injection molding company. Ensure the company operates cleanroom facilities that meet the required ISO class for medical manufacturing, particularly if the products will be used in sterile environments. It’s also crucial that all materials and processes adhere to FDA standards for medical device manufacturing.
Thoroughly verify the company’s certifications, suppliers, raw material sourcing, and inspection standards to ensure full compliance throughout the production lifecycle, from design to final delivery.
Cost Efficiency and Lead Times
Time and cost are critical factors in the success of any medical device project. When considering injection molding companies, it’s important to discuss lead times and any potential delays upfront. Considerations should include the time taken from initial product design to final delivery, as well as any possible setbacks due to design revisions, shipping, or manufacturing.
Make sure the company is transparent about pricing and provides a clear timeline to meet your production deadlines. This helps you avoid unexpected costs and delays during the product development process.
Material Capabilities and Application Suitability
A key consideration is whether the company can provide the right type of plastic resins required for your specific medical applications. The company should have the ability to source quality raw materials and offer a range of options that are compatible with their molding capabilities.
Additionally, it’s beneficial if the company offers a variety of services, making it a one-stop solution for all your manufacturing needs. This can help streamline logistics, reduce operational costs, and simplify transportation by sourcing all components from a single supplier.
When choosing a medical device injection molding company, evaluating the manufacturer’s experience, production capacity, specification compliance, cost efficiency, and material capabilities will help ensure that you partner with a company capable of delivering high-quality, compliant, and cost-effective solutions for your medical products.
Why Chose FUJIU Medical Injection Mold as Medical Plastic Components Manufacturer
Chose FUJIU Medical Injection Mold as Medical Plastic Components Manufacturer for several compelling reasons:
ISO Certified Expertise
With over 20 years of experience in the industry, FUJIU is a leader in ISO-certified medical injection molding. Expertise in precision mold manufacturing and deep knowledge of medical-grade plastics ensures that every product meets the strictest cleanliness and tolerance standards.
Comprehensive Full-Service Solutions
FUJIU offers end-to-end services, from product development and mold design to in-house tooling and secondary operations. This full-service capability makes them a one-stop partner, streamlining the production process and reducing the need for multiple suppliers.
Speed and Flexibility
The company’s agile supply chain is a major advantage. FUJIU is capable of rapidly adapting to changing customer needs, which helps shorten lead times and accelerate time-to-market. Ability to deliver fast samples, accommodate low minimum order quantities (MOQs), and maintain high-quality standards aligns with the fast-paced demands of the medical device industry.
Uncompromising Quality Assurance
FUJIU places a strong emphasis on quality control, backed by rigorous inspections and adherence to ISO certifications. This ensures that all medical components meet the highest industry standards, making them a reliable choice for critical applications where quality is paramount.
Advanced Technology
FUJIU use of state-of-the-art technology and equipment, including advanced ISO 8 cleanroom environments, ensures that every component is manufactured with precision and reliability. This technological edge is essential in the production of medical components where even the smallest deviation can affect performance.
Global Expertise and Cost-Effectiveness
FUJIU’s global reach, with expertise in sourcing, logistics, and project management, ensures smooth project execution no matter the location. Value-added supply chain and Design for Manufacturing (DFM) strategies help drive productivity while minimizing production costs.
FUJIU Medical Injection Mold offers quality custom solutions tailored to meet the unique needs of each medical device, ensuring precision, compliance with industry standards, and a focus on delivering high-performance, reliable components for healthcare applications.
FAQs about Medical Plastic Components Manufacturer
The medical industry utilizes a variety of plastics, each selected for its unique properties, such as biocompatibility, resistance to sterilization, and durability. Commonly used plastics in medical devices include polycarbonate (PC), which is known for its high impact resistance and optical clarity, making it ideal for surgical instruments, diagnostic equipment, and IV components. Polypropylene (PP) is another commonly used plastic due to its chemical resistance and heat tolerance, which makes it perfect for disposable items like syringes and medical packaging. Polyvinyl chloride (PVC) is widely used in blood bags, tubing, and catheters, as it is flexible and durable. Polystyrene (PS) is typically used in items like petri dishes and test tubes because of its clarity and ease of molding. Polyethylene (PE), a plastic with excellent moisture resistance and flexibility, is used in products such as gloves and catheters. Additionally, thermoplastic elastomers (TPE) combine the properties of rubber and plastic and are often used in components that require both flexibility and strength. These plastics are chosen to meet strict medical safety standards while ensuring the functionality and longevity of medical devices.
The largest manufacturer of medical supplies globally is Medtronic, a company headquartered in Ireland. Medtronic is a leader in the medical device sector, with a diverse range of products spanning across various medical fields, such as cardiac, neurological, diabetes care, and surgical solutions. Other significant players in the medical supplies industry include Johnson & Johnson, Siemens Healthineers, and GE Healthcare, all of which have a vast presence in medical device manufacturing. These companies are known for their innovation and manufacturing excellence in creating a wide array of medical equipment, from diagnostic imaging systems and surgical instruments to advanced monitoring devices. Medtronic, in particular, is recognized for its global impact, with operations in more than 150 countries and millions of patients benefiting from its medical technologies each year. The company’s products are central to improving patient care and health outcomes worldwide.
The legal manufacturer of a medical device is the company or entity responsible for the design, production, and marketing of the device. This entity holds responsibility for ensuring that the device complies with regulatory standards set by health authorities such as the U.S. Food and Drug Administration (FDA) and the European Medicines Agency (EMA). The legal manufacturer is also accountable for the device’s safety and efficacy, ensuring that it meets the required medical industry standards. This includes overseeing quality control processes, conducting clinical trials, and maintaining the records of production and distribution. While a contract manufacturer may be involved in producing the medical device, the legal manufacturer is the one that retains ultimate responsibility for the product’s regulatory compliance and safety. Additionally, the legal manufacturer must adhere to post-market surveillance requirements and address any issues that arise regarding the device’s performance after it has been released to the market.
Most medical devices are manufactured in countries with strong manufacturing infrastructure and advanced technology capabilities. The United States remains one of the largest producers of medical devices, with many leading companies like Medtronic, Johnson & Johnson, and Stryker headquartered there. These companies manufacture a wide variety of medical products, including diagnostic equipment, surgical instruments, and cardiac devices. Germany is another key hub for medical device manufacturing, particularly known for its high-quality standards and precision engineering in medical technology. Companies such as Siemens Healthineers and B. Braun are headquartered in Germany, producing a broad range of medical devices used globally. China has also become a significant player in the production of medical devices due to its lower manufacturing costs and strong industrial base, manufacturing both basic and complex medical supplies. Switzerland is renowned for its high-quality manufacturing, and major medical device companies like Roche and Novartis have a strong presence there, especially in diagnostic and imaging technologies. Lastly, Japan is known for its innovation in robotics and imaging devices, with companies like Olympus leading in the production of advanced medical devices. These regions collectively represent the major manufacturing bases for medical devices, meeting the growing global demand for healthcare products and solutions.
Starting a medical supply business involves several key steps to ensure regulatory compliance and a smooth market entry. Begin by researching the medical supply market to identify demand and competition. This will help you select a niche, such as surgical instruments, diagnostic equipment, or medical plastic components. Register your business and obtain the necessary licenses, such as a business license, FDA certifications, and any state-specific healthcare-related permits. Next, establish relationships with reliable suppliers and manufacturers who provide high-quality medical plastic components, ensuring they meet industry standards and certifications like ISO 13485. Consider investing in cleanroom facilities or partnering with companies that have such capabilities, as many medical devices require sterile conditions. Finally, create a marketing strategy to promote your products to healthcare facilities, hospitals, and other medical organizations, while emphasizing your product’s quality, reliability, and compliance with medical regulations.
Medical-grade polymers are specifically designed to meet the rigorous requirements for use in medical applications, and they are generally not toxic. These materials undergo extensive testing to ensure they do not release harmful chemicals when in contact with human tissue or fluids. However, the safety of a medical-grade polymer depends on the specific material and its compliance with regulatory standards such as FDA approval. Some polymers may be non-toxic, biocompatible, and hypoallergenic, making them suitable for medical applications like surgical implants, drug delivery systems, and medical device components. It’s important to choose polymers that are approved for medical use and that have undergone biocompatibility testing according to standards like ISO 10993. Any concerns regarding toxicity can typically be mitigated by ensuring the materials are properly certified and tested for specific medical purposes, including long-term safety for patients.
Medical-grade plastics are made from a variety of high-performance polymer resins that are specifically selected for their strength, durability, and biocompatibility. Common materials include polypropylene (PP), polyethylene (PE), polycarbonate (PC), polytetrafluoroethylene (PTFE), and medical-grade silicone. These materials are carefully chosen based on their ability to withstand harsh conditions, such as exposure to chemicals, high temperatures, and repeated sterilization. Medical-grade plastics are designed to be non-reactive and to ensure patient safety, making them ideal for products like syringes, surgical instruments, drug delivery systems, and medical device housings. The manufacturing process of medical-grade plastic components typically involves injection molding, extrusion, or blow molding, ensuring precise shapes and sizes. To meet industry standards, these plastics are tested for biocompatibility, and their production often occurs in regulated environments like cleanrooms to avoid contamination and maintain sterile conditions.
Contact our professional team now for a same-day quote and risk-free project evaluation. Benefit from ISO 8 cleanrooms, advanced machines, and 12-hour fast response in medical injection molding.