Medical plastic parts play a critical role in the healthcare industry, enabling the functionality, safety, and efficiency of medical devices. These components are essential in everything from diagnostic tools to life-saving surgical instruments. The versatility of plastics, combined with their ability to meet stringent regulatory standards, makes them indispensable in modern healthcare. A medical plastic components manufacturer plays a key role in producing these parts, ensuring they meet the precise specifications required for use in devices such as syringes, pacemakers, and diagnostic machines.
In this article, we will explore some of the top medical plastic parts companies, highlighting their contributions to the industry. We’ll delve into their expertise, capabilities, and the innovations they bring to medical plastics, helping to shape the future of healthcare. Medical plastic parts companies, like FUJIU Medical Injection Mold, offer high-quality, cost-effective components for medical devices with efficient large-volume production.
Low-Volume to High-Volume Production Capabilities
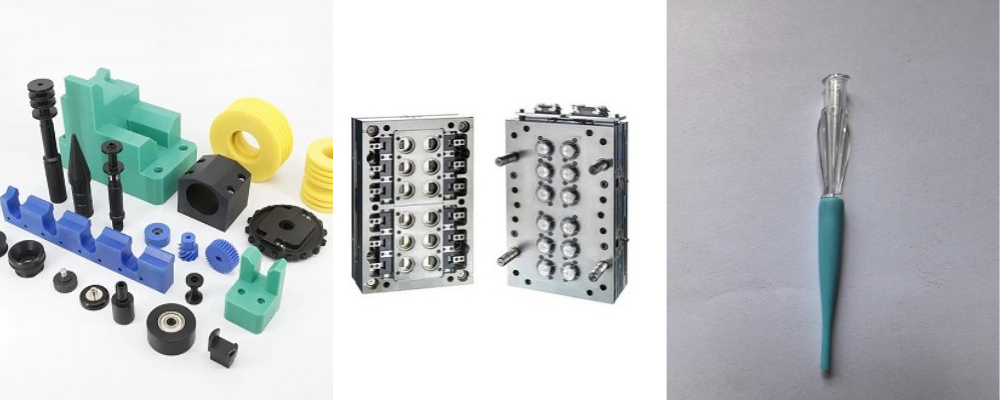
Attributes | Details |
---|---|
Place of Origin | Dongguan, Guangdong, China |
Brand Name | LY Medical Injection Mold |
Product Name | Medical Plastic Parts |
Processing Services | Molding, Cutting |
Color | Customized Color |
Size | Accept Customer's Design |
Shape | Customized Shape |
Service | One-Stop Service |
Feature | Environmentally Friendly |
Advantage | High Quality |
Certification | ISO9001:2008 |
Tolerance | 0.01mm |
OEM | Avaliable |
Selling Units | Single item |
Packing Details | According to Customer's Requirement |
Port | According to Customer's Requirement |
The Role of Medical Plastics in Healthcare
Medical plastic parts play a pivotal role in the manufacturing of a wide range of medical devices, from syringes and catheters to surgical instruments and implantable devices. These materials offer the unique combination of being lightweight, cost-effective, and versatile, making them essential for creating devices that are not only functional but also safe and efficient. In fact, medical plastics, such as OEM medical plastic parts, are integral to the overall success of the healthcare industry, facilitating the production of innovative, high-quality medical devices that improve patient outcomes.
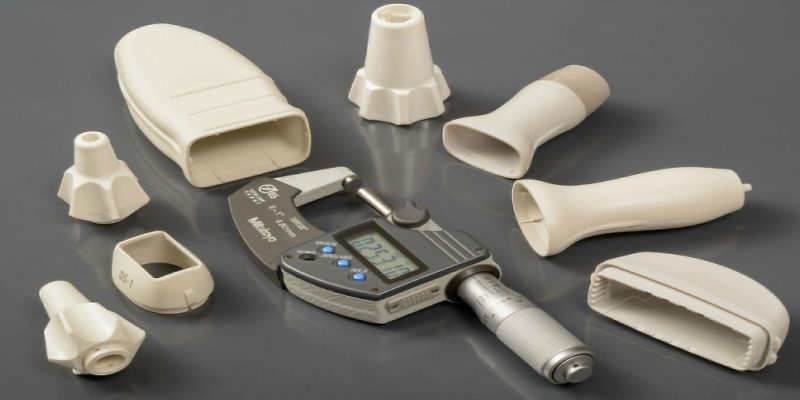
Significance of Medical Plastics in Manufacturing Medical Devices
Medical plastics are commonly used in the production of devices such as syringes, catheters, surgical instruments, and diagnostic tools. Their ability to be molded into precise shapes and sizes allows manufacturers to create devices with highly specific functions. For instance, syringes require materials that can withstand pressure and ensure accurate dosing, while catheters demand flexibility and biocompatibility. Prototypes medical molded plastic play a crucial role in testing these materials and designs, ensuring that each device meets the necessary functional and safety standards. The adaptability of medical plastics enables manufacturers to design devices that meet the functional and safety requirements of healthcare providers, thus playing a central role in patient care.
Benefits of Using Medical-Grade Plastics
Medical-grade plastics are widely regarded for their excellent properties, making them ideal for use in medical devices. Some of the key benefits include:
Biocompatibility: Ensuring Safety for Patients
One of the most important benefits of medical-grade plastics is their exceptional biocompatibility. This means that they are designed to interact safely with the human body without causing harmful reactions, such as inflammation or allergic responses. Materials like polyethylene, polypropylene, and polycarbonate are often chosen for their biocompatible properties, ensuring that medical devices made from these plastics are safe for prolonged use in contact with tissues, blood, or bodily fluids. This safety is critical in medical devices like surgical implants, catheters, and drug delivery systems, where direct or indirect contact with the human body is unavoidable.
Cost-Effectiveness: Affordable Healthcare Solutions
Medical-grade plastics are a cost-effective alternative to traditional materials like metals and ceramics, offering manufacturers a more economical solution for producing medical devices. The lower cost of plastic materials, coupled with their ability to be easily molded and shaped into complex forms, makes them an attractive option for a wide range of applications. This affordability not only helps reduce manufacturing costs but also makes healthcare products more accessible to a broader patient population. By utilizing medical plastics, healthcare providers can offer high-quality, functional devices at lower prices, improving access to essential treatments without compromising safety or performance.
Durability and Resistance: Handling Rigorous Medical Conditions
Medical-grade plastics are engineered to withstand the demanding conditions of healthcare environments. These materials exhibit exceptional durability, enabling them to endure physical stress, repeated use, and exposure to harsh chemicals without deteriorating. For instance, surgical tools, diagnostic devices, and implantable products require high resistance to wear and tear, corrosion, and sterilization methods, all of which medical-grade plastics can handle efficiently. Their robustness also ensures that these devices maintain their integrity throughout their service life, reducing the risk of malfunctions or failures during critical medical procedures.
Flexibility: Adapting to Patient Needs
Another significant advantage of medical-grade plastics is their flexibility, which is particularly important in applications such as tubing, IV components, and wound care dressings. These materials can be designed to provide the necessary level of flexibility and elasticity, allowing them to conform to various patient body types or conditions. For instance, plastic tubing used in intravenous therapy or respiratory equipment needs to be pliable and easily maneuverable to fit different anatomical structures and provide comfort during extended use. The flexibility of medical plastics makes them versatile in a wide range of applications, enhancing patient comfort and improving the overall effectiveness of medical treatments.
Lightweight: Reducing Patient Discomfort
Medical-grade plastics are notably lighter than metals, which can significantly enhance patient comfort, especially in devices that are worn or implanted for extended periods. The lightweight nature of plastics is a key benefit in the design of items such as prosthetics, braces, and orthopedic supports, where reduced weight can directly contribute to patient mobility and ease of use. By decreasing the overall weight of medical devices, plastics help improve user experience, reduce strain on the body, and facilitate better patient outcomes.
Sterilization and Cleanability: Ensuring Hygiene
Medical plastics are typically designed to be compatible with standard sterilization procedures, such as autoclaving or chemical sterilization, ensuring that they can be safely cleaned and reused without compromising their integrity. This is especially important for reusable medical devices like surgical instruments, dental tools, and diagnostic equipment, which must maintain a high level of hygiene to prevent infections and cross-contamination. The ability of medical-grade plastics to endure repeated sterilization processes without degrading ensures that devices can remain safe, functional, and hygienic over time, contributing to better patient outcomes and reducing the risk of healthcare-associated infections.
Transparency: Facilitating Monitoring and Diagnosis
Many medical-grade plastics are transparent or translucent, a feature that is particularly beneficial in devices that require visual monitoring or diagnosis. For example, plastic used in blood bags, infusion sets, or diagnostic containers allows healthcare professionals to monitor fluid levels, detect clots, or observe the condition of the contents without the need for additional procedures. Transparency not only enhances the usability of these devices but also improves the accuracy of medical procedures, as healthcare providers can easily observe and assess the situation in real time.
Design Versatility: Supporting Innovation
The versatility of medical-grade plastics allows for a wide range of design possibilities, enabling the creation of highly specialized, custom medical devices tailored to specific patient needs or medical procedures. Plastics can be molded into complex shapes and sizes, accommodating intricate design features that may be difficult to achieve with other materials. Whether for intricate surgical tools, ergonomic prosthetics, or compact diagnostic devices, medical-grade plastics support innovation by providing designers with more flexibility and freedom to develop cutting-edge solutions for modern healthcare challenges.
Chemical Resistance: Protecting Against Harsh Environments
Medical-grade plastics are often chosen for their chemical resistance, which ensures that they can maintain their performance in environments where exposure to a variety of chemicals, solvents, or bodily fluids is common. This resistance is particularly important for devices such as drug delivery systems, catheters, and laboratory equipment, where exposure to corrosive substances could otherwise degrade the device material over time. The ability of medical plastics to resist chemical reactions helps extend the life of the device, reduces the need for frequent replacements, and enhances the overall safety and reliability of medical treatments.
Regulatory Compliance: Meeting Strict Standards
Medical-grade plastics must meet rigorous regulatory standards set by organizations like the U.S. Food and Drug Administration (FDA) or the European Medicines Agency (EMA). These standards ensure that the plastics used in medical devices are safe, effective, and reliable for their intended use. Compliance with these regulations not only provides manufacturers with the confidence that their products are market-ready but also assures healthcare providers and patients that the devices they are using are of the highest quality. By adhering to stringent regulatory requirements, medical-grade plastics help ensure the continued safety and success of medical devices globally.
Industry Standards and Certifications
The medical device industry adheres to rigorous standards and certifications to ensure safety, efficacy, and compliance with regulatory bodies. These standards include:
- ISO 13485: This standard focuses on the quality management systems used by medical device manufacturers. Medical plastic parts companies must adhere to these regulations to ensure their products meet international safety and quality requirements.
- FDA Approvals: The U.S. Food and Drug Administration (FDA) oversees the safety of medical devices in the United States. For medical plastics used in devices, FDA approval is a crucial certification. Manufacturers must provide evidence that their materials are safe and effective for medical applications.
Medical plastic parts companies are essential to the healthcare industry. By producing high-quality, biocompatible, and cost-effective medical plastic components, these companies contribute significantly to improving patient care and enabling the innovation of medical technologies. The strict industry standards and certifications ensure that these materials meet the highest safety and performance criteria, making them indispensable in the production of medical devices.
FUJIU Medical Injection Mold: A Leading Innovator in Medical Plastic Parts Companies
At FUJIU Medical Injection Mold, we have established ourselves as a key player in the medical plastics industry, specializing in high-quality medical device manufacturing, medical injection molding, and assembly. Known for its commitment to regulatory compliance and cutting-edge technological advancements, we stand out as a leading innovator among medical plastic parts companies. This section delves into our company history, expertise, global presence, services, and future directions in medical plastics.
Company Overview
History and Growth of FUJIU Medical Injection Mold
Founded with a vision to provide high-precision medical plastic components, our company has grown significantly over the years, becoming one of the most respected medical plastic parts companies in the industry. Our success is attributed to its focus on innovation, quality, and efficiency. We have evolved to offer a wide range of services, including custom injection molding, precision mold medical solutions, and assembly for medical devices used in critical healthcare applications.
Key Areas of Expertise: Medical Device Manufacturing, Injection Molding, and Assembly
Our expertise lies in its ability to deliver both standard and complex medical plastic components for a variety of applications. We specializes in injection molding, a highly efficient manufacturing process that ensures precise, high-quality components that meet the rigorous requirements of the medical industry. Whether it’s for syringes, diagnostic tools, or surgical devices, our company deep knowledge of medical device manufacturing enables us to create products that prioritize patient safety and functionality.
Our Focus on Regulatory Compliance (FDA, ISO Certifications)
As one of the leading medical plastic parts companies, we places a strong emphasis on maintaining regulatory compliance. Our company is certified by the FDA for medical device manufacturing and follows ISO 13485 standards for quality management systems. These certifications ensure that our products meet the highest levels of safety, quality, and performance, meeting both domestic and international standards for medical device manufacturing.
FUJIU Medical Injection Mold Locations
Locations of Manufacturing Facilities in China and Internationally
Locations of Manufacturing Facilities in China and Internationally
Our company operates a number of state-of-the-art manufacturing facilities both in China and internationally, allowing us to serve a global market. One of our key facilities is our China medical plastic parts factory, which plays a crucial role in meeting the growing demand for medical plastic components. These manufacturing plants are strategically located to support both developed and emerging markets. With advanced capabilities in injection molding, we have the capacity to produce millions of precision medical plastic parts, ensuring timely delivery to clients worldwide.
Discussion of the Global Reach and Capabilities of FUJIU Medical Injection Mold
Our global presence extends beyond China, with manufacturing and assembly operations in key regions including North America, Europe, and Asia. This global footprint enables us to offer comprehensive solutions to medical device manufacturers across the world, providing the capability to address diverse needs in various medical sectors. By leveraging our China medical plastic parts expertise, alongside our international facilities, we remain a flexible and efficient supplier, capable of responding to large-scale demands without compromising quality.
FUJIU Medical Injection Mold Headquarters
Location and Significance of the Headquarters
Our headquarters are located in Shenzhen, China, a major hub for the global medical device industry. The strategic location of the headquarters enables our company to collaborate closely with other medical plastic parts companies, research institutions, and regulatory bodies to stay at the forefront of innovation. Shenzhen’s advanced infrastructure also supports our robust supply chain, ensuring that production and distribution are streamlined and efficient.
How Our HQ Supports Innovation and Industry-Leading Services
The headquarters plays a crucial role in driving our innovative spirit and continuous improvement. Our company’s R&D department is based at the headquarters, where engineers and designers work to develop cutting-edge solutions for the evolving needs of the healthcare industry. Our commitment to research and development ensures we remain a leader in medical plastics, providing advanced solutions that enhance the functionality, safety, and efficacy of medical devices.
Services and Capabilities
Medical Device Design and Prototyping
We offer comprehensive design and prototyping services, working closely with clients to create customized medical plastic parts. Our team of expert engineers and designers uses the latest CAD software, rapid prototyping technologies, and rapid injection molding medical techniques to turn concepts into functional prototypes. This ensures that designs meet both technical and regulatory specifications, providing fast, reliable, and cost-effective solutions for the medical industry.
Cleanroom Manufacturing and Injection Molding Capabilities
A core aspect of our offering is its cleanroom manufacturing capabilities. We operates fully equipped cleanrooms that meet ISO 13485 and ISO 14644 standards, ensuring the production of medical plastic parts in a contaminant-free environment. This capability is critical for the production of high-precision, medical-grade components, especially for devices used in sterile environments.
Custom Solutions for a Wide Range of Medical Applications
We provide tailored solutions for various medical applications, from injection-molded syringes to more complex diagnostic tools and surgical instruments. By offering flexibility and a wide range of custom options, we are able to address the specific needs of each client, ensuring that the final products align with the unique requirements of different medical sectors. With our expertise in medical molded plastics solutions, we can produce high-precision, durable components that meet the stringent quality standards essential in the healthcare industry.
Innovations and Future Directions
Commitment to Technological Advancements in Medical Plastics
Our company are deeply committed to staying at the cutting edge of medical plastics technology. We are investing heavily in automation, advanced injection molding machines, and materials science to improve production efficiency and product quality. Our company is also exploring new materials that offer enhanced performance, such as biocompatible plastics that can be used in long-term implantable devices.
How We are Addressing the Evolving Needs of the Healthcare Sector
As the healthcare sector continues to evolve, we remain agile and responsive to changing demands. Our company is focusing on developing innovative solutions for the emerging field of personalized medicine, where devices need to be customized for individual patients. Our company is also addressing the growing need for sustainable medical device production by exploring eco-friendly materials and processes that minimize waste and energy consumption.
At FUJIU Medical Injection Mold, we stand as a leading force among medical plastic parts companies. Through our commitment to quality, innovation, and customer service, we continue to be a vital player in the global healthcare sector, providing high-performance, medical-grade plastic components that enhance the safety, effectiveness, and reliability of medical devices worldwide.
Key Considerations When Choosing a Medical Plastic Parts Companies & Factory
When selecting a medical plastic parts company & factory, several critical factors must be considered to ensure that the chosen medica plastic parts supplier meets the stringent requirements of the healthcare industry. The following sections highlight key considerations when choosing medical plastic parts companies, ensuring they deliver high-quality, reliable, and compliant products for medical device manufacturing.
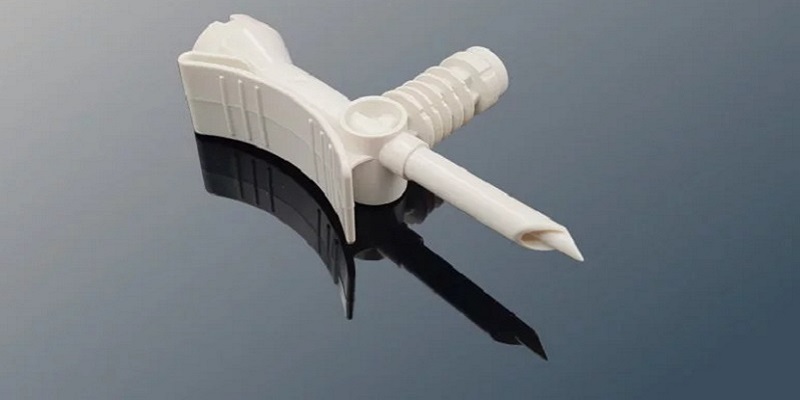
Importance of Selecting Companies with a Proven Track Record and FDA Compliance
Experience and industry reputation are crucial factors when choosing a medical plastic parts company. Medical parts mold companies with a proven track record in the medical device industry are more likely to understand the complex regulatory requirements and high standards of performance needed for medical components. An established reputation often reflects years of experience working with healthcare OEMs, ensuring the company can meet the demands of medical device manufacturers.
Additionally, selecting medical plastic parts companies that are FDA-compliant is a key consideration. FDA compliance ensures that the company adheres to the rigorous standards set forth for medical devices, particularly in terms of safety, biocompatibility, and quality control. FDA registration is often a prerequisite for companies involved in the production of medical devices, and it signals that the company has the necessary processes in place to maintain regulatory standards throughout the production lifecycle.
Overview of ISO, FDA, and Other Critical Standards in Medical Device Manufacturing
Compliance with relevant industry standards and certifications is one of the most important considerations when selecting a medical plastic parts company. Key certifications include ISO 13485, which outlines the requirements for a comprehensive quality management system in the design and manufacturing of medical devices. ISO 13485 certification ensures that the company follows a standardized approach to risk management, traceability, and quality assurance, which are critical in medical device production.
Other important certifications include FDA registration, which is required for companies manufacturing medical devices or components that will be sold in the U.S. market. Additionally, companies may hold certifications in environmental management (ISO 14001) or occupational health and safety (ISO 45001), which can be beneficial in demonstrating their overall commitment to quality and regulatory compliance.
In some cases, companies may also be required to meet specific standards for biocompatibility, such as ISO 10993, which ensures that medical plastic components are safe for contact with the human body.
Role of Customization, Prototyping, and Scalable Manufacturing Solutions
The capabilities and specializations of a medical plastic parts company are critical to meeting the unique needs of medical device manufacturers. A company with robust customization capabilities can tailor designs to specific requirements, ensuring that the plastic components are functional, reliable, and meet regulatory standards. When considering potential partners, medical plastic parts quotes can provide insight into the cost-effectiveness and competitive pricing, helping manufacturers make informed decisions.
Prototyping is another essential service that should be considered when choosing a medical plastic parts company. The ability to develop prototype medical equipment molds allows for early-stage testing, adjustments, and improvements, helping to ensure that the final product meets the desired specifications. A company with experience in rapid prototyping can significantly reduce development time and cost, providing clients with faster time-to-market for their medical devices.
In addition to customization and prototyping, scalability is another key factor. The medical plastic parts company should be capable of handling both small-batch and large-scale production runs. This ensures flexibility for companies at various stages of product development, from initial testing and prototype runs to full-scale commercial manufacturing.
Quality Assurance and Manufacturing Processes
Focus on Cleanroom Environments, Process Validation, and Precision Molding
When selecting medical plastic parts companies, it’s essential to consider their commitment to quality assurance and their manufacturing processes. Companies with expertise in cleanroom environments are often preferred, as these controlled spaces are necessary for manufacturing medical components that must remain free from contaminants. Cleanroom environments are particularly critical for the production of sterile medical devices, as even minor contamination can compromise the safety and effectiveness of the product.
Process Validation
Process validation is another key consideration. Medical plastic parts companies should conduct thorough process validation to ensure that their manufacturing processes consistently produce products that meet specified requirements. This includes validation of molding processes, material properties, and final product quality. For plastic injection molding medical parts companies, medical molding validation plays a pivotal role. By validating the molding process itself, companies can ensure that their production techniques are not only capable of meeting high standards for precision but also comply with regulatory guidelines, thus ensuring the final product’s safety, effectiveness, and consistency.
Finally, precision molding capabilities are essential for producing high quality medical plastic parts. Medical devices often require intricate designs and tight tolerances, which can only be achieved with advanced molding technologies. A medical plastic parts company with expertise in precision molding can deliver components with high dimensional accuracy and surface quality, ensuring that they function correctly within medical devices and comply with regulatory standards.
Choosing the right medical plastic parts company involves evaluating factors such as experience, regulatory compliance, capabilities, and commitment to quality. By considering these key considerations, manufacturers can ensure that their medical plastic components are of the highest quality, compliant with industry standards, and capable of supporting the development of safe and effective medical devices.
Key Injection Molding Processes Used by Medical Plastic Parts Companies
Medical plastic parts companies use a variety of specialized processes to produce high-quality, functional, and safe components for medical devices. These processes are designed to meet the specific requirements of the medical industry, including biocompatibility, precision, and durability. In the following, we will explore four essential injection molding techniques—implantable and bioresorbable molding, micromolding, secondary molding and insert molding, and silicone molding—that medical plastic parts companies commonly utilize to produce advanced medical components.
Implantable and Bioresorbable Molding
Medical plastic parts companies often manufacture implantable and bioresorbable components, which are crucial in medical applications like surgical implants or drug delivery systems. Implantable parts are designed to remain in the body permanently or for a specific period, while bioresorbable parts are engineered to degrade within the body after performing their function.
This process involves selecting plastics that are biocompatible and safe for long-term use within the human body. Materials such as polylactic acid (PLA), polycaprolactone (PCL), and polyglycolic acid (PGA) are commonly used for bioresorbable implants, as they safely degrade over time without causing harm. Medical plastic parts companies ensure that these parts meet stringent regulatory standards, making them critical for medical applications requiring precise, safe, and reliable performance.
Micromolding
Micromolding is a specialized injection molding technique used by medical plastic parts companies to create extremely small, precise components for applications like micro-surgical tools, drug delivery systems, and diagnostic devices. This process is essential for manufacturing high-precision medical parts that require tight tolerances and intricate features, such as fine threads or small cavities.
In micromolding, smaller molds and specialized equipment are used to inject molten plastic into miniature molds under controlled pressure, enabling the production of parts with exceptional accuracy and repeatability. The use of micromolding allows for the creation of compact, lightweight components that are critical in minimally invasive surgeries and diagnostic tools, where space and precision are crucial.
Secondary Molding and Insert Molding
Secondary molding and insert molding are processes that enable medical plastic parts companies to enhance the functionality of a single part by adding additional features or materials after the primary molding has taken place. Secondary molding often involves processes like overmolding, where a second material is added to the initial plastic part to enhance its properties, such as flexibility or grip.
Insert molding, on the other hand, involves placing pre-formed components, like metal parts or electronic circuits, into the mold before injection molding. This allows medical plastic parts companies to integrate various materials into a single component, creating a part with multi-material functionality, such as a plastic handle with a metal insert or a medical device housing with embedded sensors.
These techniques are often used for complex medical devices that require a combination of plastics and other materials to ensure performance and durability, such as surgical instruments or multi-functional diagnostic devices.
Silicone Molding
Silicone molding is a critical process for medical plastic parts companies when producing medical components that require flexibility, biocompatibility, and resistance to high temperatures or harsh chemicals. Silicone is used in a wide range of medical applications, including implants, catheters, seals, and gaskets, due to its superior properties such as hypoallergenic characteristics, flexibility, and durability.
The silicone molding process involves injecting liquid silicone rubber (LSR) into a mold cavity, where it solidifies into the desired shape. The resulting parts are highly customizable and can be produced with various levels of hardness, transparency, and color. This technique is ideal for creating flexible and soft medical parts that need to conform to body tissues or provide a comfortable interface with patients, such as flexible medical tubing or wearable devices.
By using silicone molding, medical plastic parts companies can meet the specific needs of the healthcare industry, producing reliable and high-performance components for critical medical applications.
These four injection molding processes—implantable and bioresorbable molding, micromolding, secondary molding and insert molding, and silicone molding—are key techniques that medical plastic parts companies use to ensure the production of high-quality, precise, and safe medical devices and components. Each process is tailored to meet the unique requirements of the medical industry, ensuring that devices function correctly and safely for patients.
Measures Taken by Medical Plastic Parts Companies to Ensure Product Consistency
In the medical industry, the consistency of plastic parts is paramount due to the critical nature of the devices they are used in. Medical plastic parts companies employ a range of stringent measures to ensure that every part produced meets high standards of quality, safety, and performance. These measures include robust quality control systems, strict adherence to regulatory guidelines, advanced manufacturing technologies, and continuous monitoring of production processes. The following outlines the key measures these companies take to ensure consistency in their medical plastic products.
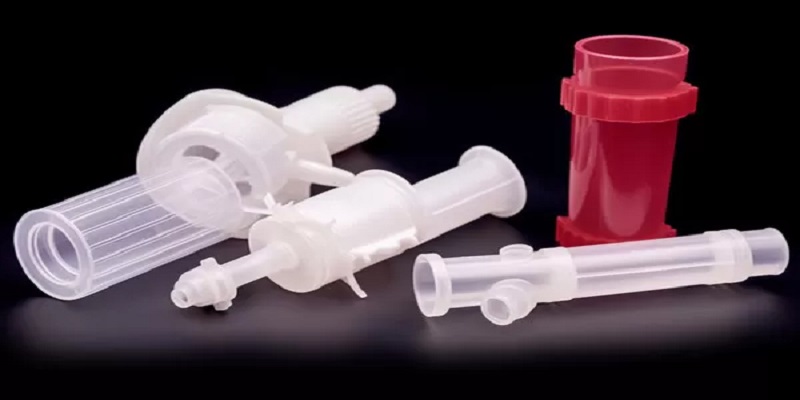
Quality Control Systems
The foundation of maintaining consistency in medical plastic parts lies in a rigorous quality control system. Medical plastic parts companies typically implement multi-tiered inspection processes, with checks occurring at various stages of production. The aim is to catch any defects early on, ensuring that only high-quality parts reach the market.
This process often includes visual inspections, dimensional checks, and functional testing. The companies also use automated inspection systems that leverage advanced technologies, such as machine vision, to detect minute defects that may be missed by the human eye. In addition to the physical inspection, companies may use non-destructive testing (NDT) methods to assess the integrity of the materials used, ensuring that every part is fit for purpose.
Compliance with Regulatory Standards
Medical plastic parts must adhere to a variety of regulations to ensure safety, performance, and consistency. Medical plastic parts companies are required to comply with national and international regulatory standards, such as those outlined by the FDA (Food and Drug Administration), ISO (International Organization for Standardization), and other health authorities.
To meet these regulatory standards, manufacturers follow strict guidelines in their design, production, and testing phases. This includes documentation of the entire production process, traceability of materials, and batch testing to ensure compliance with safety standards. Many companies also undergo regular audits by regulatory bodies to verify their adherence to these requirements, making it clear that product consistency is a top priority.
Advanced Manufacturing Techniques
To ensure the consistent production of high-quality medical plastic parts, many companies invest in cutting-edge manufacturing technologies. Techniques such as injection molding, extrusion, and blow molding are commonly used for precision and repeatability in medical plastic production. These processes are designed to maintain tight tolerances and ensure that each batch of parts is identical in size, shape, and performance.
Additionally, some companies use automated systems to reduce human error and increase the speed of production. Robotics and automated machinery allow for precise control over the manufacturing process, reducing variations in part quality and ensuring that consistency is maintained throughout large production runs.
Continuous Process Monitoring and Improvement
Medical plastic parts companies also employ continuous monitoring of their production processes to ensure consistency over time. This involves real-time data collection from production lines, which is analyzed to identify any deviations from the desired specifications. By using sensors and data analytics, companies can immediately address any issues that arise, preventing defects before they affect product quality.
Furthermore, companies often implement continuous improvement programs such as Six Sigma or Lean Manufacturing. These methodologies focus on identifying inefficiencies and minimizing variation in the manufacturing process. Regular process reviews and employee training ensure that all team members are aligned with the goal of maintaining high product consistency.
Supplier and Material Quality Management
The quality of raw materials is critical to ensuring consistency in the final product. Medical plastic parts companies establish strict supplier qualification processes to ensure that only high-quality materials are used in production. This includes auditing suppliers, testing materials before use, and ensuring that materials are sourced from trusted suppliers who comply with the necessary standards.
Material traceability is another essential practice. Companies track each batch of materials used in production to ensure that they meet the required specifications and can quickly trace the source of any issues that arise during the manufacturing process. This level of control ensures that the consistency of the final product is not compromised by variations in raw materials.
To ensure product consistency, medical plastic parts companies rely on a combination of quality control systems, regulatory compliance, advanced manufacturing techniques, continuous process monitoring, and effective supplier management. These measures work together to produce high-quality, reliable medical plastic parts that meet the stringent requirements of the healthcare industry. By focusing on these areas, companies can maintain the high standards necessary for medical devices and components, ultimately ensuring patient safety and performance.
How Medical Plastic Parts Companies Protect Their Intellectual Property Rights
In the highly competitive and regulated medical device industry, protecting intellectual property (IP) is essential for medical plastic parts companies to safeguard their innovations and maintain a competitive edge. IP protection ensures that companies retain control over their proprietary designs, technologies, and manufacturing processes, preventing unauthorized use or imitation by competitors. To achieve this, these companies employ a combination of legal, technical, and operational measures. The following sections outline the key strategies that medical plastic parts companies use to protect their intellectual property rights.
Patent Protection
One of the primary ways that medical plastic parts companies protect their intellectual property is through patenting their innovations. Patents provide legal protection for new inventions, such as unique designs or technologies used in the production of medical plastic parts, by granting the patent holder exclusive rights to use, manufacture, and sell the invention for a specified period.
Medical plastic parts companies typically file patents for novel aspects of their products, whether it’s a new material formulation, a manufacturing process, or a design feature. Filing for patents in multiple jurisdictions is common, especially in key markets like the United States, Europe, and Asia, to prevent competitors from using similar technologies without authorization. The patent process also acts as a deterrent to competitors who may otherwise attempt to replicate or reverse-engineer the company’s products. Additionally, patent protection allows companies to license their innovations, creating revenue streams while keeping control over how their intellectual property is used.
Trade Secrets and Confidentiality Agreements
In addition to patents, medical plastic parts companies often rely on trade secrets to protect their intellectual property. Trade secrets refer to proprietary knowledge or processes that give a company a competitive advantage but are not publicly disclosed. This could include unique formulations for medical-grade plastics, specialized manufacturing techniques, or internal design specifications.
To safeguard trade secrets, companies implement strict confidentiality measures. This includes non-disclosure agreements (NDAs) with employees, contractors, suppliers, and business partners. These legal contracts ensure that any sensitive information shared during collaborations or joint ventures remains confidential. Furthermore, companies may restrict access to critical information within the organization to a need-to-know basis and use encryption and secure systems to prevent unauthorized access.
Copyright Protection for Designs and Documentation
Medical plastic parts companies may also protect certain aspects of their intellectual property, such as product designs, technical drawings, and software, through copyright protection. While patents protect inventions, copyrights safeguard the expression of ideas, like visual designs or computer code, that are unique and original.
In the context of medical plastic parts companies, copyrighted materials can include 3D CAD models, blueprints for components, or the proprietary software used in the design and production of medical devices. By registering these works with the appropriate copyright offices, companies can prevent unauthorized reproduction or distribution of their creative materials. This legal protection adds an extra layer of security for the company’s innovative assets.
Trademarks for Brand Identity and Product Recognition
Trademarks are another key tool for protecting intellectual property rights in the medical plastic parts industry. A trademark, which could be a logo, name, slogan, or symbol, distinguishes the company’s products from those of competitors. By registering trademarks, companies can prevent other businesses from using similar marks that could confuse consumers or damage the brand’s reputation.
For medical plastic parts companies, trademarks help protect both the brand identity and the specific product lines that are associated with high quality and innovation. Trademarks can also cover product names or logos that are used on medical devices and their packaging, reinforcing the company’s unique market position. This form of IP protection can also be valuable for marketing and consumer trust.
IP Enforcement and Litigation
Even with strong IP protection in place, medical plastic parts companies must be proactive in enforcing their rights. This can involve monitoring the market for potential infringement and taking legal action when necessary. Companies may investigate competitors or third parties suspected of using their patented technologies, copyrighted designs, or trademarks without permission.
If an infringement is detected, companies may pursue various legal avenues, including cease-and-desist letters, negotiations, or litigation. While IP litigation can be costly and time-consuming, it is sometimes necessary to protect valuable assets. In some cases, companies may also consider alternative dispute resolution methods, such as arbitration or mediation, to resolve conflicts more efficiently.
Collaboration with IP Firms and Legal Counsel
To navigate the complex world of intellectual property law, medical plastic parts companies often work closely with specialized intellectual property law firms and legal experts. These professionals help guide the company through the process of filing patents, trademarks, and copyrights, ensuring that the IP is properly protected according to the relevant laws in each market.
Legal counsel also helps to identify and mitigate potential risks related to IP infringement and assists with enforcing IP rights if infringement occurs. By partnering with IP specialists, companies can develop a comprehensive strategy for safeguarding their innovations and effectively managing their IP portfolio.
Protecting intellectual property rights is a vital aspect of maintaining a competitive edge and safeguarding the innovations of medical plastic parts companies. Through a combination of patents, trade secrets, copyrights, trademarks, and legal enforcement strategies, these companies can prevent competitors from exploiting their proprietary technologies and designs. Additionally, ongoing collaboration with IP professionals ensures that the protection process remains robust, keeping intellectual property safe from infringement and reinforcing the company’s position in the market.
Challenges Faced by Medical Plastic Parts Companies and Their Solutions
Medical plastic parts companies operate in a complex and highly regulated industry, where challenges range from meeting stringent regulatory requirements to managing production efficiency and ensuring the quality of their products. These companies must navigate a variety of obstacles that can impact their ability to deliver reliable, safe, and innovative medical devices. In this section, we will explore some of the key challenges faced by medical plastic parts companies and the solutions they employ to address these issues effectively.
Regulatory Compliance and Certification
One of the biggest challenges for medical plastic parts companies is ensuring compliance with the strict regulations set by health authorities like the U.S. Food and Drug Administration (FDA), European Medicines Agency (EMA), and other national and international regulatory bodies. Medical devices and components must meet rigorous standards for safety, performance, and biocompatibility before they can be sold or used in medical applications.
Solution: To address regulatory compliance challenges, medical plastic parts companies often implement a robust quality management system (QMS) that aligns with global standards, such as ISO 13485, which specifically targets medical device manufacturing. These companies also dedicate resources to keeping up with evolving regulatory changes and conducting regular internal audits to ensure all processes and documentation meet required standards. Collaborating with regulatory consultants or experts can also streamline the approval process and minimize the risk of non-compliance.
Material Selection and Biocompatibility
The selection of materials used in medical plastic parts is a critical decision. The materials must not only be durable and cost-effective but also meet biocompatibility standards, as they may come into direct contact with the human body. Any failure to meet biocompatibility requirements could result in health risks, product recalls, or regulatory delays.
Solution: To mitigate these risks, medical plastic parts companies often work closely with material suppliers and testing laboratories to ensure that the plastics used in their products are biocompatible and meet all necessary standards, such as ISO 10993. Companies may also invest in advanced material research and development to create innovative, safer alternatives that meet both medical and functional requirements. Regular testing and validation of materials during the design and production phases also help ensure long-term performance and safety.
Maintaining Product Quality and Consistency
Ensuring consistent product quality is a significant challenge in medical plastic parts manufacturing. Variability in raw materials, machinery, or human error can lead to defects or inconsistencies that compromise the safety and effectiveness of medical devices.
Solution: Medical plastic parts companies often implement strict quality control measures, including automated inspection systems, in-process monitoring, and rigorous testing protocols. Techniques such as Statistical Process Control (SPC) and Six Sigma are commonly used to monitor production processes and minimize variability. By using precision manufacturing techniques, such as injection molding and automated assembly, companies can reduce the chances of defects and improve consistency in every batch produced.
Cost Control and Production Efficiency
The production of high-quality medical plastic parts can be expensive due to the need for advanced technologies, regulatory compliance, and material sourcing. Additionally, medical plastic parts companies often face pressure to reduce costs without sacrificing quality, which can be a challenge in a highly competitive market.
Solution: To address cost control challenges, companies often invest in automation and lean manufacturing practices to optimize production efficiency and reduce waste. By employing techniques such as design for manufacturability (DFM), companies can streamline their product designs to minimize production costs while maintaining the desired performance and quality. Strategic sourcing and supplier partnerships also allow for cost savings in materials and components, helping to manage overall production expenses.
Supply Chain Disruptions
The global nature of the medical device industry means that medical plastic parts companies are often reliant on suppliers from various regions. Supply chain disruptions, whether due to natural disasters, geopolitical issues, or global crises such as the COVID-19 pandemic, can lead to delays in production, shortages of materials, or increased costs.
Solution: To mitigate supply chain risks, medical plastic parts companies diversify their supplier base and maintain strong relationships with key partners. They may also invest in supply chain management software to track and manage inventory levels more effectively. In some cases, companies may keep safety stock of critical materials or components to ensure production can continue uninterrupted during unforeseen disruptions. Furthermore, adopting a just-in-time (JIT) inventory model helps minimize excess inventory costs and keeps the supply chain flexible.
Environmental and Sustainability Challenges
As environmental concerns grow, medical plastic parts companies are under increasing pressure to develop sustainable products and reduce the environmental impact of their manufacturing processes. Plastic waste, material sourcing, and energy consumption are key issues that need to be addressed to align with sustainability goals.
Solution: Medical plastic parts companies are increasingly focusing on developing biodegradable or recyclable medical plastics, reducing the environmental impact of their products. Some companies invest in eco-friendly manufacturing processes, such as using renewable energy sources or adopting energy-efficient equipment. Additionally, they collaborate with industry stakeholders to develop sustainable packaging solutions and reduce plastic waste through recycling programs. By adopting sustainable practices, companies can meet both regulatory requirements and consumer demand for environmentally responsible products.
Intellectual Property Protection
Protecting intellectual property (IP) is critical in a highly competitive industry where companies rely on proprietary technologies and designs. The risk of IP theft or infringement is particularly significant when companies collaborate with external partners, suppliers, or manufacturers.
Solution: To safeguard their intellectual property, medical plastic parts companies use a combination of legal tools, including patents, trademarks, copyrights, and trade secrets. Companies file patents for their innovative designs and technologies and sign non-disclosure agreements (NDAs) with partners and suppliers. Some companies also implement physical and digital security measures to protect their proprietary information and monitor the market for potential infringement. Working with intellectual property law experts can help companies develop an effective strategy for protecting and enforcing their rights.
Medical plastic parts companies face a wide range of challenges, from meeting regulatory requirements and maintaining product quality to managing costs and ensuring sustainability. However, by implementing strategic solutions such as advanced manufacturing technologies, robust quality management systems, diversified supply chains, and IP protection measures, these companies can navigate these challenges effectively. Innovation, collaboration, and ongoing process improvements will be key to overcoming obstacles and ensuring the long-term success of medical plastic parts manufacturers in a competitive and highly regulated market.
FAQs about Medical Plastic Parts Companies
When it comes to selecting the best medical-grade plastic, the decision depends on the specific requirements of the medical device being manufactured. Some of the most commonly used and trusted medical-grade plastics include Polycarbonate (PC), Polyethylene (PE), Polypropylene (PP), Polyvinyl Chloride (PVC), and Acrylonitrile Butadiene Styrene (ABS). Each of these materials has distinct advantages that make them ideal for medical applications:
Polycarbonate (PC) is known for its durability, transparency, and high impact resistance, making it ideal for devices like IV components, respiratory equipment, and surgical instruments.
Polyethylene (PE) and Polypropylene (PP) are both popular for medical packaging, as they offer chemical resistance, flexibility, and ease of sterilization.
Polyvinyl Chloride (PVC) is frequently used in medical tubing and disposable devices due to its versatility and ability to be easily molded into different shapes.
Acrylonitrile Butadiene Styrene (ABS) provides high strength and resistance to impact and is used in various medical devices such as diagnostic equipment and housings.
Ultimately, the “best” medical-grade plastic depends on factors like biocompatibility, strength, flexibility, chemical resistance, and ease of sterilization, all of which must be carefully considered by manufacturers to ensure the safety and effectiveness of the medical device.
BMP Medical, a leading provider of innovative solutions for the healthcare and medical device industries, is headquartered in Boca Raton, Florida, USA. The company has built a strong reputation for designing and manufacturing precision components used in various medical applications, including diagnostic equipment, drug delivery systems, and surgical instruments. BMP Medical’s headquarters serves as the central hub for its research, development, and production activities, where it focuses on meeting the stringent requirements of regulatory bodies such as the FDA and ISO. Their location in Boca Raton, a well-established medical device manufacturing area, allows the company to leverage a highly skilled workforce and stay close to its key clients in the healthcare and medical industries. The company’s strategic position also provides easy access to global markets, supporting its extensive network of operations both domestically and internationally.
As of recent estimates, there are approximately 10,000 to 15,000 medical device companies operating worldwide, with a significant concentration in countries like the United States, Germany, Japan, and Switzerland. These companies range from large multinational corporations to small startups specializing in niche medical technologies. The global medical device market is diverse, covering a wide array of products, from basic medical tools like syringes and bandages to advanced technologies like pacemakers, diagnostic imaging equipment, and robotic surgery systems. The number of companies in the medical device industry continues to grow as technological innovations and healthcare demands evolve, particularly in areas like telemedicine, personalized healthcare, and wearable medical devices. In the United States alone, the medical device industry is one of the largest sectors, with thousands of companies producing devices that are integral to patient care, disease management, and medical research.
One of the largest plastic companies globally is Dow Inc. Dow is a leading manufacturer of a wide variety of plastic materials, including polyethylene (PE), polypropylene (PP), polystyrene (PS), and many other polymers that are used across industries such as packaging, automotive, electronics, healthcare, and construction. Dow has a significant presence in the medical plastics sector, providing high-performance materials used in medical devices, drug packaging, and personal protective equipment (PPE). With its global reach and extensive research and development capabilities, Dow is one of the foremost suppliers of medical-grade plastics that meet stringent regulatory standards, including FDA approval for use in medical devices. Dow’s advanced polymer technologies enable manufacturers to create innovative, durable, and safe medical devices, contributing to the company’s leadership position in the global plastic manufacturing industry. With a commitment to sustainability and innovation, Dow continues to expand its capabilities, making it a key player in the plastics market.
The global plastic injection molding market was valued at approximately $290 billion in 2023, and it is projected to grow at a compound annual growth rate (CAGR) of around 5-6% over the next several years. This growth is driven by the increasing demand for high-quality, durable, and cost-effective plastic parts across various industries, including automotive, healthcare, electronics, consumer goods, and packaging. The medical plastic parts sector, specifically, is expanding as advancements in medical devices and healthcare applications require precision-manufactured components. The adoption of innovative materials, along with the trend toward automation and sustainability, is further bolstering the market. As medical device companies require more specialized components, the demand for medical-grade plastics within the injection molding industry is also expected to rise.
Injection molding can be highly profitable, particularly for companies that specialize in high-volume production runs and produce complex, high-precision parts. Profitability depends on factors such as the cost of materials, machine efficiency, labor costs, and the scale of production. Medical-grade plastic injection molding, in particular, offers lucrative opportunities due to the need for high-quality, sterile, and biocompatible components used in medical devices and equipment. However, initial investment in high-quality injection molding machinery, molds, and maintaining stringent quality standards for medical applications can be significant. Long-term profitability is achieved through economies of scale, repeat orders, and maintaining efficient production processes. Additionally, companies that can meet strict regulatory standards and deliver consistent, high-quality parts often secure long-term contracts, further enhancing profitability.
Yes, medical-grade plastics are designed and manufactured to meet strict safety and quality standards for use in healthcare environments. These plastics are biocompatible, meaning they are safe for use in contact with the human body. They must meet regulatory standards set by organizations such as the U.S. Food and Drug Administration (FDA), the European Medicines Agency (EMA), and other relevant health authorities. Medical-grade plastics undergo rigorous testing to ensure they do not cause adverse reactions, such as toxicity or irritation, when used in devices like surgical instruments, implants, or drug delivery systems. Examples of medical-grade plastics include polycarbonate, polyethylene, polypropylene, and PTFE (Teflon). Despite their safety, it is essential for manufacturers to follow proper sterilization procedures and ensure that the plastics do not degrade or leach harmful substances over time.
Medical-grade PVC (Polyvinyl Chloride) can be safe for medical applications when it is properly manufactured and meets the required regulatory standards. PVC is commonly used in medical devices such as blood bags, tubing, and catheters due to its flexibility, durability, and low cost. However, medical-grade PVC must be free from harmful plasticizers, phthalates, and other potentially toxic additives that can leach into the body during use. Manufacturers use non-toxic, medical-grade plasticizers to ensure safety. Additionally, PVC used in medical applications is subject to stringent regulatory testing and certifications by agencies like the FDA to ensure it does not cause adverse reactions. However, some studies have raised concerns about long-term exposure to certain plasticizers in PVC, so ongoing research into safer alternatives and manufacturing practices is important.
Medical-grade silicone is often considered superior for specific medical applications because of its flexibility, biocompatibility, and resistance to harsh environments (e.g., temperature extremes, moisture, and chemicals). It is non-toxic, hypoallergenic, and inert, making it ideal for implants, catheters, wound dressings, and prosthetics. Silicone is highly durable, and its ability to withstand sterilization processes (like autoclaving) makes it a preferred material in many medical devices. However, medical-grade silicone is more expensive than some other plastics, such as polyethylene or polypropylene, and it may not be suitable for all types of products. In comparison to PVC, silicone is generally seen as safer for prolonged human contact, and it does not contain potentially harmful plasticizers. While it is “better” in certain medical scenarios, the choice of material depends on the specific requirements of the application.
Plastic injection molding can be a rewarding and stable career, especially in the medical device and manufacturing industries. Skilled workers, such as mold makers, machine operators, and process engineers, are in demand due to the increasing reliance on plastic components for everything from consumer goods to medical devices. The industry offers opportunities for career growth, technical specialization, and innovation, particularly as automation and smart manufacturing practices become more prevalent. For those with an interest in precision manufacturing, problem-solving, and working with advanced materials, plastic injection molding can be both intellectually satisfying and financially rewarding. Additionally, as the demand for medical plastic parts continues to rise, professionals in this field are expected to have good job security and opportunities in diverse industries.
A plastic fabrication company specializes in the manufacturing and shaping of plastic materials into finished products or components. The company might use various processes such as injection molding, extrusion, thermoforming, and CNC machining to create custom plastic parts. In the context of medical plastic parts companies, these businesses focus on fabricating medical devices, instruments, and components that meet strict regulatory standards. Plastic fabrication companies may also offer design services, prototyping, and assembly of plastic components, working closely with clients to ensure the parts are functional, durable, and meet the necessary health and safety requirements. These companies often produce components for industries such as healthcare, automotive, electronics, and packaging, and can be involved in both large-scale and small-batch production.
A plastic injection company specializes in the process of creating plastic parts through injection molding. In this process, raw plastic materials are melted and injected into a mold to form precise and complex parts. These companies provide injection molding services to a wide range of industries, including medical, automotive, consumer products, and electronics. In the medical field, plastic injection companies manufacture components like surgical tools, implants, and diagnostic devices using medical-grade plastics that meet strict regulatory standards. These companies may also provide design and engineering services, mold design, prototyping, and post-production assembly. Their success depends on their ability to produce high-quality, consistent, and cost-effective parts, often at high volumes, while adhering to industry standards such as FDA regulations.
Medical-grade plastic is often referred to by its specific type or classification based on the material used and its intended application. Common medical-grade plastics include polycarbonate (PC), polyethylene (PE), polypropylene (PP), and medical-grade silicone. These materials are selected for their biocompatibility, durability, and resistance to sterilization methods. The term “medical-grade plastic” generally refers to any plastic that meets strict regulatory standards set by authorities like the FDA or European Medicines Agency (EMA) to ensure safety for use in medical devices and implants. Additionally, the term “medical-grade” implies that the plastic has passed rigorous testing for chemical stability, toxicity, and bio-safety to ensure it is suitable for direct or indirect contact with the human body.
Plastic injection molding and plastic extrusion are both processes used to manufacture plastic products, but they differ in how the plastic is formed and the types of products they produce. In injection molding, plastic pellets are melted and injected into a mold under high pressure to form a specific shape, typically used for creating complex, high-precision parts. This process is ideal for products with intricate details, like medical device components. In contrast, plastic extrusion involves forcing melted plastic through a die to create long, continuous shapes, such as pipes, sheets, or films. The extrusion process is typically used for creating products with uniform cross-sections and is often employed in industries such as construction and packaging. While both methods can produce medical-grade plastics, injection molding is more common for medical device manufacturing due to its ability to create detailed parts.
The fastest-growing medical device market is currently the orthopedic device sector, driven by an aging population, increasing incidence of joint-related disorders, and advancements in minimally invasive surgery technologies. Additionally, the diagnostic imaging and point-of-care testing markets are experiencing rapid growth, fueled by innovations in medical diagnostics and a focus on early disease detection. The biotechnology and implants markets, particularly those involving 3D-printed medical devices, are also expanding due to the demand for customized, patient-specific solutions. The rise of wearable medical devices, such as those used for monitoring chronic conditions like diabetes or heart disease, is contributing to the growth of the healthcare IoT sector. These trends are stimulating demand for high-quality, medical-grade plastic components used in everything from surgical instruments and implants to diagnostic equipment.
There isn’t a single “name” for injection plastics, as many types of plastics are used in the injection molding process. The choice of material depends on the intended application. Common plastics used in injection molding include polystyrene (PS), polyethylene (PE), polypropylene (PP), polycarbonate (PC), acrylonitrile butadiene styrene (ABS), nylon (PA), and polyvinyl chloride (PVC). For medical-grade parts, materials such as polycarbonate (PC), polyethylene (PE), polypropylene (PP), and medical-grade silicone are frequently used. These materials are chosen based on their specific properties, such as strength, flexibility, transparency, and biocompatibility, making them suitable for medical applications. Depending on the needs of the product being manufactured, the choice of injection plastic will vary.
The raw material for medical-grade plastic typically comes in the form of resin pellets made from high-quality polymers such as polycarbonate (PC), polyethylene (PE), polypropylene (PP), acrylonitrile butadiene styrene (ABS), polyvinyl chloride (PVC), or medical-grade silicone. These polymers are carefully selected for their biocompatibility, strength, durability, and ability to undergo sterilization processes. In some cases, specific additives or plasticizers are used to modify the properties of the material (e.g., to enhance flexibility or transparency), but these must be non-toxic and safe for use in medical environments. Raw materials for medical plastics are sourced from specialized suppliers who ensure the materials meet the stringent standards set by regulatory bodies such as the FDA, and they undergo rigorous testing to ensure safety and performance.
Various types of plastics are used in injection molding, depending on the product’s requirements. Common plastics for injection molding include polypropylene (PP), polyethylene (PE), acrylonitrile butadiene styrene (ABS), polycarbonate (PC), polyvinyl chloride (PVC), and nylon (PA). Polycarbonate is often used for high-clarity applications, such as medical device components. Polypropylene and polyethylene are commonly used for packaging and consumer goods, while ABS is favored for applications requiring toughness and impact resistance. Medical-grade plastics, such as medical-grade silicone or polycarbonate, are frequently used in the medical sector due to their biocompatibility, sterilization ability, and mechanical properties. The choice of plastic depends on the desired product attributes, including strength, flexibility, chemical resistance, and ease of processing.
Injection molding is used to create a wide variety of products, especially those requiring complex shapes and high precision. In the medical industry, common products made through injection molding include surgical instruments, implants, catheters, syringes, and diagnostic devices. Other sectors, such as automotive, electronics, consumer goods, and packaging, also rely heavily on injection molding for items like dashboards, housings for electronic devices, packaging containers, bottle caps, and toys. The process is ideal for producing high-volume, consistent, and durable parts, which makes it the preferred choice for manufacturing everything from small, intricate components to larger, more robust products. In the medical industry, the ability to manufacture sterile, custom-sized, and biocompatible parts is critical, making injection molding an essential method for producing medical plastic parts.
Contact our professional team now for a same-day quote and risk-free project evaluation. Benefit from ISO 8 cleanrooms, advanced machines, and 12-hour fast response in medical injection molding.