The medical plastics industry plays a crucial role in modern healthcare, providing essential materials for a wide range of medical devices and applications. Medical plastic parts factories specialize in producing precision medical components that meet stringent standards for safety, durability, and functionality. These factories utilize advanced manufacturing techniques to create parts used in everything from surgical instruments to implants, diagnostic tools, and packaging. Medical plastic parts exporter helps ensure that high-quality components are distributed globally, contributing to the reliability and effectiveness of medical devices in patient care. Medical plastic parts factories are essential in maintaining regulatory compliance, offering customization options, and delivering precision-engineered solutions that contribute to better health outcomes and medical advancements worldwide. FUJIU Medical Injection Mold is a top choice among medical plastic parts factories, specializing in high-quality, large-volume production of medical-grade components.
Overview of Medical Plastic Parts Factories
History and Reputation in the Medical Plastics Sector
- Evolution of the Industry: Medical plastic parts factories have developed over the years, transitioning from producing basic plastic components to advanced materials for complex medical devices.
- Key Role in Healthcare: These factories play a vital role in producing essential parts for a wide range of medical applications, including implants, surgical instruments, diagnostic devices, and drug delivery systems.
- Reputation for Reliability: The reputation of plastic medical parts factories is built on their ability to consistently produce high-quality, safe, and reliable components that meet the demanding needs of healthcare providers.
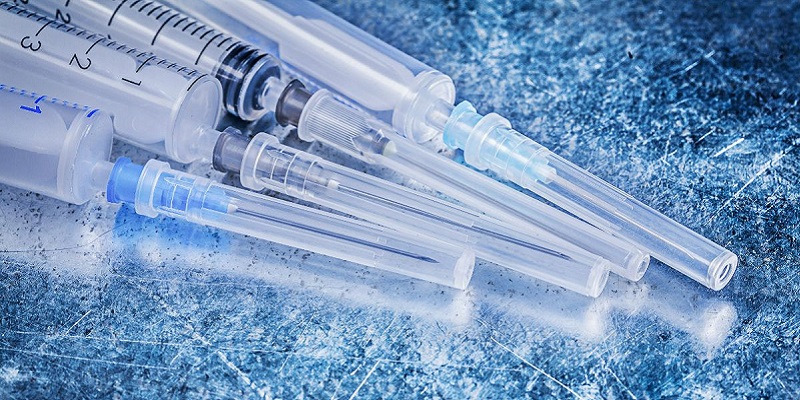
Commitment to Innovation, Quality, and Regulatory Compliance
- Continuous Technological Advancements: Medical plastic parts factory invests in new technologies to enhance the performance and safety of their products. They focus on developing innovative materials and manufacturing processes to meet evolving healthcare needs.
- Adherence to Quality Standards: These factories prioritize high manufacturing standards, ensuring their products meet strict guidelines for safety, reliability, and functionality.
- Regulatory Compliance: Compliance with FDA regulations, ISO standards, and other certifications is a key focus, as medical plastic parts factories must ensure their products are safe and effective for patient use.
Focus on Material Expertise and Manufacturing Capabilities
- Material Specialization: Plastic medical parts factory have in-depth expertise in working with advanced materials such as PEEK, PPSU, polycarbonate, and other biocompatible plastics that meet the stringent demands of medical applications.
- Advanced Manufacturing Techniques: These factories utilize cutting-edge manufacturing processes, such as injection molding, CNC machining, and cleanroom production, to produce precision components for plastic medical parts machining. These advanced techniques ensure the parts meet the stringent quality standards required for medical applications, delivering both accuracy and reliability.
- Customization and Flexibility: Medical plastic parts factories offer customized solutions for a variety of medical applications, ensuring that each component meets the specific needs of healthcare providers and manufacturers. They can handle both high-volume production runs and smaller, specialized orders.
Medical Plastic Parts Factories: Advanced Capabilities for Medical Applications
In-House Capabilities: Design Assistance, Rapid Prototyping, and Quality Control
- Design Assistance: Medical plastic parts factories provide comprehensive design assistance to help customers develop products that meet strict medical industry standards. Their in-house design teams work closely with plastic medical device manufacturers to optimize the functionality, manufacturability, and performance of plastic components. This support includes material selection, design for manufacturability (DFM) analysis, and ensuring the design complies with regulatory requirements.
- Rapid Prototyping: Many medical plastic parts factories offer rapid prototyping services, enabling manufacturers to quickly create and test prototype parts. This capability allows for faster design iterations, helping to shorten development timelines for new medical devices. Whether using 3D printing, injection molding, or CNC machining, these prototypes provide critical insights into form, fit, and function before committing to full-scale production.
- Quality Control: A critical aspect of medical plastic parts factories is their stringent quality control processes. These factories implement rigorous testing procedures to ensure every part meets the high-quality standards required for medical applications. From initial material inspection to final product testing, quality control is an integral part of the production cycle, helping to prevent defects and ensuring patient safety.
Focus on FDA Compliance, ISO Certifications, and Cleanroom Facilities
- FDA Compliance: Medical plastic parts factories adhere to the stringent requirements set by the FDA for manufacturing medical devices and components. Compliance with FDA regulations ensures that the materials used, as well as the processes employed in manufacturing, meet the necessary standards for safety, efficacy, and patient care. These factories follow Good Manufacturing Practices (GMP) to ensure every product is made with the highest degree of safety.
- ISO Certifications: Many medical plastic parts factories hold ISO certifications, such as ISO 13485, which is specific to medical devices. This certification confirms that the factory’s processes and systems meet international standards for quality management and regulatory compliance. These standards help ensure that products are consistently manufactured with precision and that the factory’s operations are continually improved to meet the evolving needs of the medical industry.
- Cleanroom Facilities: To meet the stringent requirements of medical applications, medical plastic parts factories often operate under cleanroom conditions. These controlled environments reduce the risk of contamination during the manufacturing process, which is crucial for producing components used in sensitive medical devices such as implants, syringes, and diagnostic equipment. Cleanroom facilities ensure that plastic parts are free from particles, dust, and other contaminants that could compromise their safety or functionality.
Customization Options to Meet Specific Medical Requirements
- Tailored Solutions: Manufacturers of medical plastic parts offer a broad range of customization services to cater to the specific demands of the healthcare industry. Through collaboration with medical device manufacturers, these companies create customized precision medical apparatus components that meet particular performance criteria, whether regarding shape, size, material, or durability. This tailored approach ensures that each component is designed to serve its specific purpose, whether for complex medical devices or specialized sterile packaging.
- Material Options: With a deep understanding of material science, medical plastic parts factories can source and process a variety of high-performance plastics, including biocompatible and sterilizable materials like PEEK, polycarbonate, and PPSU. These materials are selected based on factors such as biocompatibility, resistance to sterilization methods (e.g., autoclaving, gamma radiation), and durability under harsh conditions. Customization allows manufacturers to meet specific functional, aesthetic, and regulatory requirements.
- Precision Engineering: Customization in medical plastic parts factories often includes precision engineering capabilities that enable the creation of complex geometries and intricate features. With advanced manufacturing techniques such as medical injection molding, CNC machining, and overmolding, these factories can produce parts with tight tolerances, ensuring the highest level of accuracy and functionality for critical medical applications.
Medical plastic parts factories are equipped with the expertise, technology, and capabilities needed to meet the evolving demands of the healthcare industry. By offering design assistance, rapid prototyping, FDA compliance, ISO certifications, and highly customizable solutions, these factories are essential partners in the development of reliable, high-quality medical products.
Medical Plastic Parts Factories: Why Choose Medical Plastic Parts?
Key Reasons as a Manufacturing Partner for Medical Plastic Parts
- Expertise and Experience: Medical plastic parts factories, including medical parts mold factories, bring years of specialized experience to the table. Their deep understanding of the medical industry’s unique challenges allows them to provide solutions that meet stringent quality, safety, and regulatory requirements. As manufacturing partners, they offer valuable insights into material selection, design optimization, and production techniques, ensuring that the final products meet the needs of both the medical device manufacturers and end-users. This expertise makes them reliable and trusted partners for companies in the medical field.
- Regulatory Compliance and Certifications: Medical plastic parts factories are well-versed in navigating the complex regulatory landscape that governs the medical device industry. They ensure that their manufacturing processes comply with all relevant standards, such as ISO 13485 for quality management systems and FDA guidelines for medical devices. These factories often undergo rigorous audits to maintain their certifications, which assures medical companies that the parts produced are safe, reliable, and ready for market.
- State-of-the-Art Technology: To meet the high standards required by the medical industry, these factories utilize the latest manufacturing technologies, including advanced injection molding, 3D printing, and CNC machining. These technologies allow for the production of precise, complex parts that are integral to the function of medical devices. The use of cutting-edge equipment also ensures that parts can be manufactured quickly and efficiently, without compromising on quality.
Emphasis on Precision, Durability, and Cost-Efficiency in High-Volume and Low-Volume Production Runs
- Precision Manufacturing: Medical plastic parts factories are equipped with precision-engineering tools that enable them to produce components with extremely tight tolerances. Whether producing small, intricate parts or large, more robust components, these factories prioritize precision to ensure each part fits within the required specifications. Precision is crucial in medical applications where even the slightest deviation can impact the safety and effectiveness of the device. Medical plastic parts factories use advanced machinery and quality control methods to achieve the highest levels of accuracy.
- Durability and Performance: One of the key reasons to choose medical plastic parts factories is their focus on producing durable components. Medical devices often need to withstand extreme conditions such as high temperatures, sterilization processes, and long-term usage. These factories specialize in selecting the best materials and manufacturing techniques to ensure that each plastic part is strong, durable, and able to perform consistently over time. Durability is particularly important for parts used in critical applications like implants, surgical tools, and diagnostic equipment.
- Cost-Efficiency: Whether you need high-volume or low-volume production runs, medical plastic parts factories offer cost-effective solutions. For high-volume production, these factories utilize automated processes to reduce labor costs, optimize material usage, and increase efficiency. For low-volume runs or prototype parts, they offer flexible production capabilities, ensuring that the cost of producing fewer units remains competitive. The ability to provide cost-efficient solutions across different production volumes makes medical plastic parts factories valuable partners for medical device manufacturers, regardless of the size of the production run.
Meeting Strict Medical Industry Standards
- Quality Assurance: Medical plastic parts factories are committed to meeting the strictest industry standards for quality. To achieve this, they implement robust quality assurance protocols at every stage of the manufacturing process, from material selection to final inspection. These standards ensure that each part meets the required safety, performance, and regulatory criteria. By adhering to these rigorous quality checks, medical plastic parts factories provide peace of mind to their clients, knowing that the products they receive are reliable and safe for use in medical applications.
- Compliance with International Standards: In addition to meeting local regulations, many medical plastic parts factories also comply with international standards, which allows them to serve global markets. By adhering to internationally recognized certifications like ISO 13485 and following best practices in manufacturing, these factories ensure that their medical plastic parts are suitable for use in medical devices across the world. This global compliance is essential for manufacturers looking to expand their reach and market their products internationally.
Medical plastic parts factories provide critical support to the medical device industry by offering specialized expertise, precision, durability, and cost-effective production solutions. Whether you’re looking for high-volume manufacturing or customized, low-volume production, these factories deliver the necessary capabilities to meet the most demanding requirements. With a focus on quality, regulatory compliance, and technological innovation, they remain invaluable partners in the production of medical plastic components.
Medical Plastic Parts Factories: Medical Instrument Molding Parts Factory
Expertise in Medical Instrument Molding
- Specialized Knowledge: Medical plastic parts factories have deep expertise in molding parts that are crucial for medical devices. They understand the specific requirements and regulations surrounding medical instruments, which require high precision, durability, and sterility. These factories specialize in producing intricate and reliable components that play a critical role in the performance of medical instruments, from surgical tools to diagnostic equipment. Precision mold medical techniques are essential in ensuring the production of parts that meet the high standards of accuracy and reliability required in healthcare applications.
- Advanced Molding Techniques: These factories use state-of-the-art injection molding, compression molding, and other advanced techniques to produce complex and high-quality parts. Their experience with a wide range of materials, including biocompatible plastics and medical-grade polymers, ensures that the parts meet the necessary standards for safety and functionality. The molding process also allows for the production of parts with high accuracy and consistency, which is essential for the precision required in medical instruments.
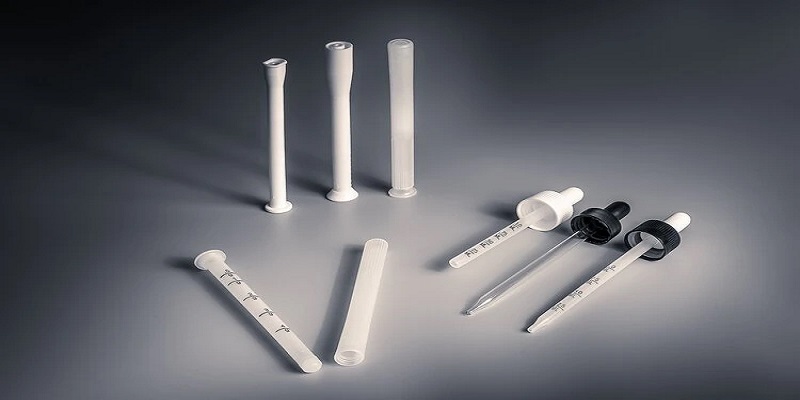
Meeting Medical Industry Standards
- Regulatory Compliance: Medical instrument molding parts factories are fully compliant with regulatory standards such as ISO 13485, FDA regulations, and GMP (Good Manufacturing Practices). This ensures that the parts produced for medical instruments meet the highest safety and quality standards. These factories are regularly audited to maintain their certifications and uphold their commitment to regulatory compliance.
- Custom Molding Solutions: Customization is key for many medical instruments, and these factories offer tailored molding solutions to meet the unique needs of specific medical devices. Whether producing ergonomic grips for surgical tools or specialized housings for diagnostic equipment, medical instrument molding parts factories work closely with manufacturers to create custom solutions that are functional, safe, and cost-effective.
High-Volume and Low-Volume Production Capabilities
- Scalable Production: Medical instrument molding parts factories offer both high-volume and low-volume production capabilities, depending on the customer’s needs. For high-volume production runs, these factories use automated processes that reduce costs and improve efficiency. For low-volume or prototype production, they provide flexibility and cost-effective solutions, allowing manufacturers to develop and test new medical instruments with a lower upfront investment.
- Efficient Turnaround Time: These factories prioritize efficient production cycles to meet the demands of the medical industry, where time-to-market can be critical. They work to ensure that parts are molded quickly without compromising on quality, helping manufacturers launch new instruments or update existing ones on time. Whether for a quick batch of prototype parts or large-scale production, medical instrument molding parts factories are equipped to meet tight deadlines.
High-Quality Materials for Medical Applications
- Material Selection: Choosing the right materials is crucial for medical instruments, as the parts must meet stringent requirements for strength, biocompatibility, and resistance to harsh sterilization processes. These factories offer a wide selection of medical-grade polymers, including thermoplastics, elastomers, and composites that can withstand the demanding environments of medical applications.
- Durability and Performance: Medical instruments must be durable and maintain their performance under various conditions. Molding parts made in these factories are designed to endure repeated sterilization, exposure to chemicals, and mechanical stress. This durability ensures that the instruments continue to perform as required throughout their lifecycle.
Medical instrument molding parts factories play a crucial role in the production of medical devices by offering specialized expertise, customized solutions, and high-quality materials. Their ability to meet regulatory standards, provide scalable production options, and maintain precise control over the molding process makes them invaluable partners for medical device manufacturers. Whether you need high-volume or custom-designed parts, these factories can provide the precision and reliability necessary for creating high-quality medical instruments.
Applications in the Medical Industry: Insights from Medical Plastic Parts Factories
Medical plastic parts produced by medical plastic parts factories play a crucial role in various aspects of the healthcare and medical industries. These parts are essential in ensuring the safety, functionality, and effectiveness of medical devices, diagnostic tools, and patient care products. From disposable items to high-precision components, medical plastics are used across a wide range of applications, enabling better treatment outcomes and improving the quality of care. In this section, we will explore the key areas where medical plastic parts are used, and how these materials contribute to the medical field.
Medical Device Components
Medical devices rely heavily on plastic parts for their construction. These devices must meet strict safety and performance standards, and plastic parts provide the necessary combination of durability, flexibility, and ease of sterilization.
Applications: Medical plastic parts factories produce a wide range of components used in devices such as pacemakers, infusion pumps, respiratory equipment, and diagnostic machines. These components include housings, seals, connectors, and control buttons, which are made from high-performance plastics like polycarbonate, ABS (Acrylonitrile Butadiene Styrene), and polyamide.
Plastics are ideal for medical devices because they can be molded into complex shapes, offering the versatility needed for intricate designs. Additionally, they are lightweight, which is crucial for portable devices. The ease of sterilization is also a major benefit, ensuring that the parts meet hygiene standards required in medical settings.
Packaging for Pharmaceuticals and Medical Products
Packaging for pharmaceuticals and medical products is another key application of medical plastic parts. Packaging must protect the contents, ensure sterility, and provide ease of use for patients and healthcare providers.
Applications: Medical plastic parts factories produce containers, vials, syringes, blister packs, and tubing used in the pharmaceutical industry. These packaging components are typically made from medical-grade plastics such as polyethylene (PE), polypropylene (PP), and polyethylene terephthalate (PET). These materials are chosen for their resistance to moisture, chemicals, and physical stress, ensuring the integrity of the medical products inside.
Medical packaging must also be capable of withstanding sterilization methods such as autoclaving or gamma irradiation, which further increases the demand for high-quality plastics. With innovations in packaging design, plastic packaging plays a vital role in reducing contamination risks and ensuring the safe delivery of medication.
Diagnostic and Laboratory Equipment
Diagnostic tools and laboratory equipment rely on medical plastic parts to function accurately and reliably. These tools require high precision and must be made from materials that can withstand frequent cleaning and sterilization.
Applications: Medical plastic parts factories manufacture components used in blood collection tubes, diagnostic test kits, centrifuges, microscopes, and lab trays. These components, made from materials like polystyrene and polypropylene, are durable, lightweight, and resistant to chemical reagents, making them ideal for medical diagnostic use.
The precise molding capabilities of medical plastic parts factories allow for the production of intricate, high-precision components that are critical for laboratory testing and diagnosis. The ability to sterilize these parts without degradation is a key factor in their use in medical laboratories.
Implants and Prosthetics
Medical plastic parts also play a significant role in the creation of implants and prosthetics, offering solutions that combine functionality, comfort, and biocompatibility. These parts need to meet the highest standards of safety and performance due to their direct interaction with the human body.
Applications: Medical plastic parts factories produce components for orthopedic implants, dental implants, hearing aids, and joint replacements. Materials such as medical-grade silicone, PEEK (polyetheretherketone), and UHMWPE (ultra-high-molecular-weight polyethylene) are commonly used in these applications due to their strength, flexibility, and biocompatibility.
For example, PEEK is often used in spinal implants and trauma devices because of its high strength and ability to mimic bone. Silicone is commonly used for flexible, skin-friendly implants, while UHMWPE is used for joint replacements due to its excellent wear resistance and durability.
Surgical Instruments and Tools
Surgical instruments and tools are another critical area where medical plastic parts are extensively used. These instruments must be precisely engineered for functionality and ease of use during medical procedures.
Applications: Medical plastic parts factories manufacture handles, tips, and components for a variety of surgical instruments, including scalpels, forceps, scissors, and surgical drapes. These parts are typically made from plastics like polypropylene, polycarbonate, and nylon, which provide the necessary strength, durability, and flexibility required during surgical procedures.
In addition to providing structural integrity, medical plastics also allow for lightweight and ergonomic designs, which are important for the comfort of medical professionals performing delicate operations. The plastic components used in surgical instruments must also withstand rigorous sterilization procedures to prevent infection.
Patient Care and Disposable Products
Medical plastic parts factories produce a wide range of disposable products that are essential for patient care. These products help to maintain hygiene, prevent infection, and ensure safety during medical procedures.
Applications: Disposable items like gloves, face masks, IV bags, syringes, and wound care dressings are produced by medical plastic parts factories. These products are typically made from materials like latex, polyethylene, or PVC, which offer flexibility, sterility, and comfort for short-term use.
These disposable products are critical in hospitals, clinics, and medical environments where hygiene is of utmost importance. By using medical-grade plastics, manufacturers ensure that these products are safe, effective, and free from contaminants, minimizing the risk of healthcare-associated infections.
Medical plastic parts factories are central to the production of a wide range of critical components used across the healthcare industry. From high-performance medical devices and diagnostic equipment to packaging, implants, and disposable products, medical-grade plastics play a vital role in ensuring patient safety, device functionality, and ease of use. These factories utilize advanced molding techniques and stringent quality controls to produce the components that support the ongoing development of medical technologies and improve patient outcomes globally.
Process Flows in Medical Plastic Parts Factories
When medical plastic parts factories produce medical injection molded parts, the process involves several carefully structured steps that ensure the final product meets all necessary quality, safety, and performance standards. From initial design to the final molded part, each step in the process must be meticulously executed to meet the stringent requirements of the medical industry. These steps include concept design, prototyping, tooling, injection molding, and post-processing, each playing a crucial role in the production of high-quality medical components. In this section, we will take a detailed look at these process flows and how they work together to produce reliable, precision medical plastic parts.
Initial Design and Concept Development
The first step in the production of medical injection molded parts is the design phase. During this phase, the concept of the medical part is developed, taking into account functional requirements, regulatory standards, and the intended use of the part. This process involves close collaboration between design engineers, medical professionals, and regulatory experts to ensure the product is both effective and compliant.
Process Details: The design team uses CAD (Computer-Aided Design) software to create 3D models of the medical part. These models provide a detailed representation of the part’s geometry, material requirements, and other specifications. Factors like biocompatibility, sterilization compatibility, and ease of use are incorporated into the design. The design phase also includes assessing the product’s manufacturability, ensuring that the part can be efficiently produced using injection molding techniques.
Prototyping and Testing
Once the initial design is completed, the next step is prototyping. Prototypes are created to validate the design and functionality of the medical plastic parts before full-scale production begins. This allows for early identification of any design flaws and helps refine the final product.
Process Details: The prototype is typically produced using rapid prototyping techniques, such as 3D printing or CNC machining, to quickly turn the digital design into a physical model. The prototype undergoes rigorous testing, including functional, durability, and biocompatibility tests, to ensure it meets medical industry standards. Testing may also involve sterilization trials to confirm the part can withstand the necessary sterilization processes used in medical environments. Feedback from this phase is used to make any necessary adjustments to the design before moving on to tooling.
Tooling and Mold Design
Once the design and prototype are finalized, the next step is tooling, which involves the creation of the molds used in the injection molding process. Tooling is one of the most critical stages in medical plastic parts factories because the quality and precision of the mold directly impact the quality of the final product.
Process Details: The mold is designed and manufactured based on the finalized CAD model of the part. The mold consists of two halves that will be used to form the plastic part when injected under high pressure. Materials used for creating the mold are usually high-grade steel or aluminum, chosen for their durability and precision. The tooling process involves CNC machining, electrical discharge machining (EDM), and other advanced techniques to create the intricate shapes and cavities required for the medical part. The mold design must also consider factors such as ease of part ejection, cooling efficiency, and mold longevity.
Injection Molding Process
Once the mold is ready, the medical plastic parts factory can begin the injection molding process, which involves injecting melted plastic into the mold under high pressure. This process is repeated to create large quantities of identical parts, each with consistent quality.
Process Details: The injection molding process begins by heating plastic pellets, which are typically medical-grade resins, to a molten state. This molten plastic is then injected into the mold using an injection molding machine, which applies high pressure to ensure the material fills every cavity of the mold. Once the plastic cools and solidifies, the mold is opened, and the newly formed part is ejected. The part is then checked for any defects, such as warping, air bubbles, or surface imperfections. The accuracy of the molding process is critical, as medical parts must meet strict dimensional tolerances to function properly.
Post-Processing and Quality Control
After the injection molding is completed, post-processing steps are essential to ensure the medical plastic parts meet all quality and functional requirements. This includes finishing processes such as trimming, cleaning, and assembly.
Process Details: Post-processing typically includes removing excess material, such as flash or sprues, that remains after molding. Some parts may require additional operations, such as ultrasonic welding, pad printing, or decorating, depending on their intended use. After the part is fully formed, it undergoes a series of quality control checks, which may include visual inspection, dimensional measurements, and functional testing to ensure that it meets the specified criteria for safety, durability, and performance. Medical plastic parts factories often employ automated inspection systems to detect even minor defects. In addition, biocompatibility and sterilization validation tests are performed to ensure the parts are safe for medical use.
Packaging and Sterilization
Finally, once the medical plastic parts have passed all quality control checks, they are packaged and prepared for delivery. Packaging plays a crucial role in maintaining the cleanliness and sterility of medical components, ensuring they remain safe for use in clinical environments.
Process Details: Medical parts are packaged in sterile containers or vacuum-sealed packaging to prevent contamination before they are used. Packaging must comply with the necessary standards for safety and traceability, including labeling, lot numbering, and sterilization documentation. If required, parts are also sterilized before packaging using methods such as gamma radiation, ethylene oxide, or autoclaving, depending on the material and the application. Proper packaging and sterilization ensure that the parts remain safe, functional, and ready for use by healthcare providers.
The process flow for producing medical injection molded parts in medical plastic parts factories involves a series of well-coordinated steps designed to ensure that each part meets the highest standards of quality and safety. From initial design and prototyping to molding, post-processing, and packaging, each stage is critical in creating reliable, functional, and biocompatible medical components. The meticulous approach taken by medical plastic parts factories ensures that medical devices, implants, packaging, and other plastic parts are ready for safe use in the healthcare industry, meeting the stringent regulatory requirements that govern the medical sector.
Medical Materials and Selection Criteria in Medical Plastic Parts Factories
When medical plastic parts factories produce medical injection molded parts, the choice of materials is crucial for ensuring the functionality, safety, and compliance of the parts. Medical devices and components must meet strict regulatory standards for biocompatibility, durability, and performance. The selection of medical-grade plastics involves considering factors such as the part’s intended use, the type of sterilization it will undergo, and its contact with the human body. This section will explore the types of materials commonly used in medical injection molding and the criteria for selecting the most appropriate materials for medical parts.
Common Medical Materials Used in Injection Molding
Medical plastic parts factories utilize a variety of medical-grade materials that are specifically designed to meet the rigorous standards of the healthcare industry. These materials must be non-toxic, biocompatible, and resistant to degradation, ensuring safety and performance in medical applications.
Material Examples:
- Polycarbonate (PC): Known for its strength and optical clarity, polycarbonate is often used in medical devices like housings for diagnostic equipment and surgical instruments. It is durable and can withstand sterilization methods such as autoclaving.
- Polypropylene (PP): This material is commonly used for products such as syringes, IV components, and medical packaging due to its resistance to chemicals, low moisture absorption, and ease of sterilization.
- Polyethylene (PE): Low-density polyethylene (LDPE) and high-density polyethylene (HDPE) are used for packaging, tubing, and disposable medical devices due to their flexibility, resistance to moisture, and biocompatibility.
- Polyvinyl Chloride (PVC): Medical-grade PVC is often used in flexible tubing, blood bags, and catheters. It is flexible, durable, and can be made clear for easy visibility, which is essential in medical settings.
- Silicone: A highly biocompatible material, silicone is commonly used in implants, seals, and gaskets. It is flexible, heat-resistant, and suitable for long-term use in the human body.
- PEEK (Polyetheretherketone): Used for high-performance applications such as spinal implants and surgical instruments, PEEK is biocompatible, strong, and resistant to high temperatures, making it ideal for advanced medical applications.
- Nylon (Polyamide): Known for its strength and wear resistance, nylon is used in surgical instruments, prosthetics, and orthopedic implants.
Factors to Consider When Choosing Materials for Medical Parts
Choosing the right material for medical injection molded parts is a complex process that involves several key considerations. The material must meet the specific requirements of the medical application while complying with regulatory standards. The selection is influenced by factors such as mechanical properties, biocompatibility, sterilization methods, and cost.
Factors to Consider:
- Biocompatibility: The material must be non-toxic and compatible with human tissue, ensuring it does not cause adverse reactions when in contact with the body. Materials undergo testing to meet ISO 10993 standards for biocompatibility.
- Mechanical Properties: Depending on the application, the material must have the right balance of strength, flexibility, and durability. For example, medical devices requiring high strength, like surgical tools, may use materials like polycarbonate or PEEK, while disposable devices may use more flexible materials like polyethylene.
- Sterilization Resistance: Many medical parts need to be sterilized to ensure they are free of pathogens. The selected material must be able to withstand sterilization methods such as autoclaving, gamma radiation, or ethylene oxide sterilization without degrading or losing its properties.
- Chemical Resistance: Medical parts may be exposed to various chemicals, including blood, medications, and disinfectants. Materials must be resistant to chemical degradation to ensure the integrity and safety of the part over time.
- Cost and Availability: While medical-grade materials are chosen for their safety and performance, cost is also a factor in mass production. Materials like polypropylene and polyethylene are often more cost-effective for disposable items, while high-performance materials like PEEK may be reserved for high-end, long-term implants.
- Regulatory Compliance: The material must comply with industry regulations such as FDA approval for medical devices and ISO 13485 certification for quality management systems. These certifications ensure that the materials are suitable for use in medical environments and meet global safety standards.
Application-Specific Material Choices
The choice of material also depends on the specific application of the medical part. Different materials are suited to different types of medical devices, and the functionality required by the device can dictate material selection.
Applications:
- Implants and Prosthetics: Materials like PEEK, titanium, and medical-grade silicone are often used for implants and prosthetics because they are durable, biocompatible, and resistant to wear and tear. These materials are designed for long-term contact with human tissue, making them ideal for joint replacements, dental implants, and spine surgery components.
- Diagnostic Tools: Polycarbonate and polypropylene are commonly used in diagnostic equipment like blood glucose monitors, thermometers, and diagnostic test kits. These materials offer clarity, chemical resistance, and strength, which are necessary for ensuring accurate readings and reliable performance.
- Surgical Instruments: Materials such as stainless steel and high-strength plastics like polycarbonate or nylon are commonly used for surgical instruments, ensuring they are strong, durable, and easy to sterilize. Materials need to withstand the mechanical stresses and sterilization cycles commonly encountered in surgical settings.
- Disposable Devices: For single-use medical products such as syringes, IV bags, and catheters, materials like polyethylene, polypropylene, and PVC are typically used due to their flexibility, low cost, and ability to be sterilized without degradation.
- Packaging: Medical packaging materials, including HDPE and PET, are designed to protect the sterility and integrity of the medical product. These materials need to be durable, chemically resistant, and capable of being sterilized to prevent contamination.
Material Sourcing and Quality Control
Once the appropriate material is chosen, medical plastic parts factories must ensure that the material is sourced from approved suppliers and undergoes strict quality control testing. The quality of the material is critical to ensuring that the final product meets all safety and regulatory standards.
Process Details:
- Supplier Certification: Medical plastic parts factories typically work with certified suppliers who provide materials that meet FDA and ISO standards. These suppliers must demonstrate that their materials are consistent, reliable, and compliant with regulatory requirements.
- Material Testing: Before being used in production, materials undergo testing for factors such as biocompatibility, mechanical properties, and sterilization resistance. Batch testing and traceability are also important to ensure that the materials are consistent and of the highest quality.
- Quality Assurance: Medical plastic parts factories implement strict quality control processes during material selection and production. This includes regular inspection, testing, and certification of incoming materials, as well as ongoing monitoring during the injection molding process to ensure product consistency and compliance with industry standards.
The selection of materials for medical injection molded parts is a critical aspect of the manufacturing process at medical plastic parts factories. The choice of material must take into account the intended application, biocompatibility, sterilization requirements, and cost, while also adhering to regulatory standards. By carefully considering these factors, manufacturers can ensure that medical plastic parts meet the stringent demands of the healthcare industry, ensuring safety, performance, and reliability.
Precision Technical Processes in Medical Plastic Parts Factories
Medical plastic parts factories utilize a range of advanced precision technical processes to produce high-quality medical injection molded parts. These processes ensure that medical components meet stringent requirements for accuracy, reliability, and safety, while also adhering to strict regulatory standards. Precision in manufacturing is critical in the medical industry, as even minor defects can lead to serious consequences. This section will explore the key technical processes and technologies used by medical plastic parts factories, detailing how they contribute to the production of accurate and functional medical devices, implants, packaging, and more.
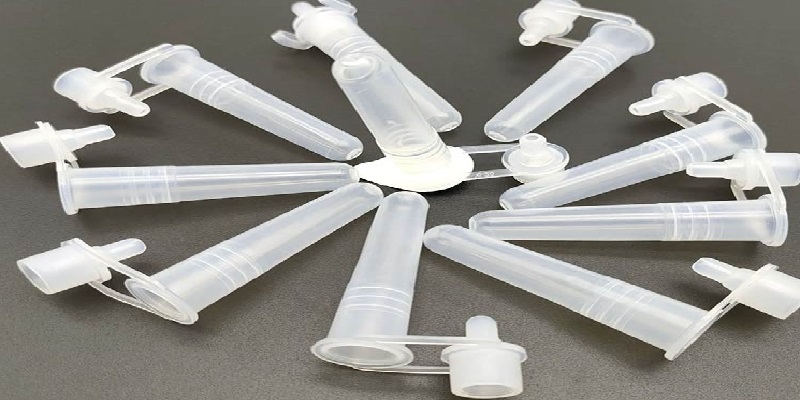
Computer Numerical Control (CNC) Machining for Molds
CNC machining is a highly precise technique used in the production of molds for medical injection molding. This technology allows for the accurate shaping of mold cavities, ensuring that each part produced will meet the necessary specifications.
Process Details:
CNC machines use computer-aided design (CAD) models to direct the machining process, creating highly detailed and intricate mold features with great accuracy. For medical plastic parts, the CNC machining process typically involves the use of hard metals like steel and aluminum, which are used to create the mold components. These molds are essential in ensuring that the injected plastic forms precisely to the desired shape and meets dimensional tolerances critical for medical applications. The precision offered by CNC machining is crucial for medical parts that require tight tolerances, such as surgical instruments, implants, and diagnostic devices.
CNC machines are also equipped with multi-axis capabilities, allowing for complex geometries and fine details to be produced with consistent quality. This precision ensures that the final injection-molded parts can be assembled accurately and function properly in medical applications.
Injection Molding with Multi-Cavity Molds
Multi-cavity molds are used to produce multiple parts in a single molding cycle, increasing efficiency and consistency during the manufacturing process. This technology is often employed by medical plastic parts factories to produce large volumes of identical medical components.
Process Details:
In multi-cavity injection molding, a single mold is designed with multiple cavities that allow for the simultaneous molding of several identical parts. This process reduces cycle time, increases production efficiency, and lowers per-part cost. Multi-cavity molds are particularly useful in the medical industry for producing large quantities of items such as syringes, IV components, and diagnostic tools.
The precision of multi-cavity molding is critical in the medical industry, as even slight variations in part dimensions could affect functionality or cause issues with device compatibility. High-quality injection molding machines, equipped with precise temperature control, pressure monitoring, and automated systems, are used to ensure uniformity across all cavities. This results in parts that are not only dimensionally accurate but also consistent in material properties and performance.
Hot Runner Systems for Consistent Flow
Hot runner systems are integral to ensuring the uniform distribution of molten plastic throughout the mold. These systems help to improve the quality and precision of the parts produced, particularly for medical devices that require intricate and uniform features.
Process Details:
In a hot runner system, the molten plastic is continuously heated in a manifold and delivered to the individual cavities of the mold via heated channels. This method keeps the plastic material at a consistent temperature and prevents it from cooling prematurely, ensuring a uniform flow of material into the mold cavities. The hot runner system reduces material waste and improves cycle time efficiency, as there is no need for cooling and reheating of the plastic in cold runners.
For medical plastic parts factories, hot runner systems are beneficial when producing complex parts with thin walls or delicate features that require precise control over the flow of material. This technology helps ensure that each part is molded with consistency and high quality, which is crucial for the functionality and safety of medical devices.
Precision Injection Molding with Gas-Assisted Molding
Gas-assisted injection molding is a technique used to create lightweight, hollow medical plastic parts with complex geometries, such as medical devices that require internal channels for fluid flow or air circulation.
Process Details:
In gas-assisted injection molding, nitrogen gas or another inert gas is injected into the molten plastic during the molding process. The gas creates a hollow section inside the part, allowing for the creation of lightweight structures without sacrificing strength or functionality. This technique is ideal for parts like medical connectors, handles, or devices with internal channels used for drainage, ventilation, or fluid transfer.
The advantage of this technology is that it allows for the reduction of material usage, minimizing waste while achieving desired part properties. The gas-assisted molding process also helps reduce cycle times and improve the dimensional stability of the final product. In medical plastic parts factories, this process is used to produce parts that must meet precise dimensional requirements while remaining lightweight and strong.
Precision Mold Flow Analysis
Mold flow analysis is a computational technique used to simulate the injection molding process and predict how molten plastic will flow through the mold. This technology is crucial in the design phase and helps to optimize the molding process, reducing defects and improving the precision of the final part.
Process Details:
Before physical production begins, mold flow analysis software is used to simulate how molten plastic will behave inside the mold. This allows engineers to identify potential issues, such as areas of the mold that may experience uneven cooling or excessive pressure, which could lead to defects such as warping or sink marks. By adjusting the mold design or process parameters, engineers can ensure a more uniform and precise molding process.
In medical plastic parts factories, mold flow analysis is especially important when producing complex medical devices or components that must meet strict regulatory standards. This technology helps minimize trial and error during the production phase, reducing the risk of defects and ensuring the highest quality parts for the medical industry.
Automated Quality Control and Inspection
To maintain the precision and reliability of the parts produced, medical plastic parts factories use advanced automated quality control and inspection technologies. These systems help to detect defects early in the production process, ensuring that only parts meeting exact specifications are delivered.
Process Details:
Automated inspection systems, such as vision systems and laser measurement tools, are used to perform detailed checks on the medical parts as they come off the production line. These systems can inspect various attributes, including dimensional accuracy, surface finish, and the presence of defects such as air bubbles, cracks, or surface blemishes. Vision systems use cameras to capture high-resolution images of the parts and compare them to pre-programmed specifications to ensure accuracy. Laser-based systems can measure the dimensions of the parts with micrometer precision, ensuring that they meet the tight tolerances required for medical devices.
Automated quality control technologies help reduce human error, increase throughput, and ensure that the final product is of the highest quality. In the medical industry, where precision is critical, these systems play an essential role in maintaining the safety and reliability of the parts produced.
Medical plastic parts factories employ a variety of precision technical processes to ensure the production of high-quality, reliable medical injection molded parts. From advanced CNC machining and multi-cavity molding to hot runner systems, gas-assisted molding, and mold flow analysis, these technologies help ensure that every part meets the exacting standards required by the medical industry. The use of automated quality control systems further enhances the precision and efficiency of the production process, ensuring that only the highest-quality medical components reach the market. These advanced manufacturing techniques are key to the development of safe, effective, and functional medical devices and components.
Handling Medical Waste Residues in Medical Plastic Parts Factories
In the production of medical injection molded parts, medical plastic parts factories inevitably generate various types of waste, including plastic scraps, packaging materials, defective parts, and residues from the molding process. These waste residues must be handled responsibly to minimize environmental impact and comply with local and international waste management regulations. Proper disposal and recycling procedures not only contribute to environmental sustainability but also ensure that the factory adheres to legal requirements concerning medical waste disposal. This section will explore the types of medical waste generated in medical plastic parts factories and provide a comprehensive guide to the appropriate methods for handling, treating, and disposing of these residues.
Types of Medical Waste Generated in Medical Plastic Parts Factories
Understanding the types of medical waste generated in the manufacturing process is crucial to determining the correct handling and disposal methods. Medical plastic parts factories produce different kinds of waste materials, each of which requires specific management strategies.
Types of Waste:
- Plastic Scraps and Defective Parts: These are the leftover plastic materials that result from the injection molding process, as well as defective parts that do not meet quality standards. These scraps are often in the form of runners, sprues, and parts with dimensional errors.
- Packaging Waste: Packaging materials such as plastic wrap, boxes, and containers used for shipping and storing materials may also contribute to medical waste. While not necessarily hazardous, these materials need to be disposed of properly to avoid cluttering landfills.
- Spent Materials: Some materials used in the manufacturing process, such as lubricants or release agents, can also result in waste that requires proper handling.
- Contaminated Parts: Occasionally, some medical plastic parts may be contaminated during production with chemicals, dust, or other substances. These parts need to be segregated and treated as hazardous waste in some cases.
The effective management of these waste types is crucial for maintaining a safe working environment and minimizing environmental impact.
Regulatory Framework for Medical Waste Disposal
Medical plastic parts factories must comply with a range of regulations governing the handling, treatment, and disposal of medical waste. These regulations ensure that waste does not pose a risk to human health, the environment, or public safety.
Key Regulations:
- The Resource Conservation and Recovery Act (RCRA): In many countries, including the United States, the RCRA governs the disposal of hazardous and non-hazardous waste. Medical plastic parts factories must ensure that their waste management practices align with these laws, particularly regarding the disposal of hazardous materials.
- Medical Waste Management Regulations: Medical plastic parts factories that handle items that come into direct contact with medical devices or biological materials may be subject to specific medical waste management regulations. These regulations define how contaminated waste should be segregated, labeled, and treated to prevent health risks.
- Local Environmental Standards: Many countries and local municipalities have specific environmental laws governing plastic waste and the disposal of manufacturing residues. Compliance with these local regulations ensures that medical plastic parts factories meet waste management standards and avoid environmental harm.
These regulatory frameworks are designed to ensure that medical waste is handled in a manner that protects human health and the environment, and they help guide the implementation of appropriate disposal practices.
Waste Segregation and Recycling
Waste segregation is a critical first step in the responsible handling of medical waste. By sorting waste into different categories, medical plastic parts factories can reduce contamination and facilitate recycling efforts.
Waste Segregation:
- Non-Hazardous Plastic Waste: Plastic scraps, defective parts, and packaging materials should be separated into designated bins for recycling. These non-hazardous materials, such as polypropylene (PP) and polyethylene (PE), can often be recycled into new products, minimizing waste and reducing the need for virgin plastic.
- Hazardous Waste: Any parts or materials that are contaminated with hazardous substances, such as chemicals or biological materials, must be segregated from non-hazardous waste and treated accordingly. This waste should be stored in specialized containers and handled by certified waste management professionals.
- Biodegradable and Compostable Materials: In some cases, packaging or other waste materials may be biodegradable or compostable. These should be kept separate from other waste streams for appropriate disposal.
Proper segregation is essential for ensuring that recyclable materials are not contaminated and that hazardous materials are disposed of safely and in compliance with regulations.
Recycling and Reuse of Medical Plastics
Recycling is one of the most sustainable ways to manage medical plastic waste. Many medical plastic parts factories adopt practices that allow for the reuse of plastic materials, either through direct recycling or reprocessing into new products.
Recycling Process:
- Closed-Loop Recycling: Medical plastic parts factories can implement closed-loop recycling systems where plastic scraps are directly recycled into new parts. This process reduces material costs and minimizes environmental impact. For example, unused plastic or defective parts can be reprocessed and used to produce non-critical parts.
- Partnership with Recycling Facilities: Some factories partner with specialized recycling facilities that process medical-grade plastics. These facilities ensure that the plastics are recycled into high-quality raw materials that can be used for new medical parts, packaging, or other applications.
- Reducing Material Waste: By optimizing production processes to minimize waste generation, medical plastic parts factories can reduce the amount of material that requires disposal. Techniques such as optimizing injection molding machine settings and using precise cutting methods can help reduce plastic scrap generation.
Recycling and reuse practices help to conserve natural resources, reduce waste, and lower production costs. In medical plastic parts factories, these practices are essential for creating a more sustainable manufacturing process.
Treatment and Disposal of Hazardous Waste
Some medical waste generated during the production of medical plastic parts may be classified as hazardous, particularly if it has been contaminated with toxic chemicals or biological materials. These types of waste require special handling and disposal methods to prevent harm to human health and the environment.
Treatment Methods:
- Incineration: Hazardous medical waste that cannot be recycled is often treated by incineration, a process that burns the waste at high temperatures to destroy harmful pathogens and chemicals. Incineration is a commonly used method for the disposal of contaminated or hazardous medical plastic waste.
- Chemical Treatment: Some waste, such as plastic parts contaminated with toxic substances, may require chemical treatment to neutralize harmful chemicals before disposal. This treatment ensures that the waste can be safely handled and disposed of.
- Licensed Disposal Facilities: For hazardous waste, medical plastic parts factories must work with licensed waste disposal companies that specialize in treating and safely disposing of hazardous materials. These facilities have the expertise and equipment to manage medical waste in accordance with legal requirements.
Proper treatment and disposal of hazardous waste are critical to ensuring compliance with environmental laws and protecting the safety of both the factory workers and the surrounding community.
Employee Training and Safety Measures
Employee training plays a crucial role in ensuring that medical plastic parts factories handle waste responsibly and in compliance with legal requirements. Factories must educate their staff on waste segregation, the identification of hazardous waste, and the proper procedures for disposal.
Training Programs:
- Waste Handling Protocols: Workers should be trained to identify, segregate, and handle medical waste safely. This includes understanding the difference between hazardous and non-hazardous materials and the proper storage and labeling practices for each.
- Safety Procedures: Factories should implement safety measures such as personal protective equipment (PPE), secure waste storage areas, and regular safety audits to ensure that employees are protected when handling waste.
- Environmental Responsibility: Training programs should also include education on the importance of sustainability and environmental responsibility, encouraging workers to actively participate in recycling and waste reduction efforts.
Well-trained employees are essential for ensuring that waste management processes are carried out effectively and safely.
The handling of medical waste residues in medical plastic parts factories is a critical aspect of ensuring environmental sustainability, regulatory compliance, and workplace safety. Through effective waste segregation, recycling, and proper disposal methods, factories can minimize their environmental impact while adhering to legal standards. By adopting responsible waste management practices, medical plastic parts factories not only contribute to a cleaner environment but also foster a culture of safety and responsibility that benefits both workers and the broader community.
FAQs about Medical Plastic Parts Factories
The medical industry relies on a variety of plastics to meet the specific needs of healthcare applications. Some of the most commonly used plastics include polycarbonate (PC), polypropylene (PP), polyethylene (PE), and polyvinyl chloride (PVC). Polycarbonate is often chosen for its high impact resistance and optical clarity, making it ideal for diagnostic equipment and surgical instruments. Polypropylene is known for its chemical resistance, low cost, and sterilization capabilities, commonly used in disposable medical products like syringes and specimen containers. Polyethylene is used for items requiring flexibility and durability, such as medical tubing, implants, and protective covers. PVC is versatile and can be made into both flexible and rigid forms, used in products like blood bags, catheters, and medical tubing. These plastics are specifically selected to meet stringent medical standards, ensuring that the materials are safe for patient use and capable of withstanding sterilization processes. The materials must also be non-toxic and biocompatible to prevent any adverse reactions when used in medical settings.
Medical equipment is produced in various regions around the world, with some areas emerging as leaders in manufacturing due to their advanced technology, skilled labor, and established healthcare standards. The United States is one of the largest manufacturers of medical devices, with many of the world’s leading companies such as Medtronic, Johnson & Johnson, and Abbott Laboratories based there. The U.S. has a well-regulated healthcare system with rigorous standards set by the FDA to ensure safety and effectiveness. In Europe, countries like Germany and Switzerland are known for their high-quality precision medical devices, with strong regulations in place to meet the demands of both the EU market and international clients. China, on the other hand, has become a major player in the manufacturing of medical equipment, especially for lower-cost products like diagnostic tools, PPE, and surgical instruments. Similarly, India plays an increasingly important role, particularly in the production of affordable medical devices and pharmaceutical manufacturing. The global nature of medical equipment manufacturing ensures that countries across North America, Europe, and Asia contribute to meeting the growing demand for healthcare technologies worldwide.
Plastic parts are manufactured through several specialized processes, each selected based on the type of plastic material and the complexity of the part. One of the most common methods is injection molding, where plastic pellets are melted and injected into a mold under high pressure. The plastic solidifies in the shape of the mold, making it ideal for creating intricate, high-volume parts such as medical device components, syringes, or IV connectors. Another method, extrusion, involves melting plastic and forcing it through a mold to create continuous shapes, such as tubes or sheets, which are often used for medical tubing or packaging. Blow molding is used for hollow parts like bottles or containers, where plastic is inflated inside a mold. CNC machining (Computer Numerical Control) allows for the precise shaping of plastic parts from solid blocks of material, ideal for prototyping or custom medical parts. Finally, thermoforming involves heating a plastic sheet and molding it over a form, commonly used for creating trays and packaging. These processes are crucial for producing high-quality, precise plastic parts used in medical applications, where reliability and safety are paramount.
Medical-grade plastics are materials that are specifically designed and manufactured to meet strict regulatory and safety standards for medical applications. These plastics are made from high-quality polymers that have undergone extensive testing to ensure they are safe for patient use. Some of the most common materials used to make medical-grade plastics include polyethylene (PE), polypropylene (PP), polycarbonate (PC), and polymethyl methacrylate (PMMA). Polyethylene, for example, is valued for its flexibility and resistance to chemicals, making it ideal for medical devices like implants and surgical tubing. Polypropylene is widely used in disposable medical devices due to its ability to withstand sterilization processes. Polycarbonate is used in medical instruments that require high impact resistance and optical clarity, such as surgical tools or diagnostic equipment. Polymethyl methacrylate is often used for intraocular lenses due to its transparency and rigidity. Medical-grade plastics are also tested for their biocompatibility, ensuring they do not cause adverse reactions in the body. The manufacturing of these plastics requires strict adherence to quality control procedures, and they must comply with standards set by regulatory agencies like the FDA and ISO to ensure the safety and reliability of medical devices and products.
Medical grade plastics, such as polyethylene (PE), polypropylene (PP), and polycarbonate (PC), are designed for specific medical uses, and in general, they do not release microplastics during normal use. However, wear and tear or improper disposal (e.g., in landfills or incinerators) can lead to degradation over time, potentially resulting in the release of microplastics into the environment. In medical devices, such as implants or surgical tools, plastic materials are carefully chosen for their durability and biocompatibility, which minimizes the risk of microplastic release under normal conditions. Nonetheless, the growing concern about plastic waste highlights the need for responsible recycling and disposal practices in medical plastic parts factories.
Medical grade silicone is a highly durable, flexible material used in various medical applications such as implants, tubing, and seals. It is less likely to release microplastics compared to conventional plastics since it does not degrade in the same way. However, like other materials, silicone could potentially degrade into smaller particles if exposed to harsh conditions over a long period. Silicone is typically biocompatible, and its use in medical devices ensures that it meets strict safety standards to avoid any harmful effects. Nonetheless, the management of silicone waste is critical to preventing environmental contamination.
To determine if plastic is medical grade, it must meet specific regulatory and quality standards, such as those set by the FDA (in the U.S.) or ISO 13485 for medical devices. Medical-grade plastics are non-toxic, biocompatible, and able to withstand sterilization processes. Certification by regulatory bodies, material testing (such as cytotoxicity tests), and compliance with Good Manufacturing Practices (GMP) are all key indicators that plastic is medical grade. Manufacturers of medical plastic parts undergo stringent quality control measures to ensure their products meet the required standards for safety and efficacy.
Medical grade plastic is made through a rigorous process that involves selecting high-quality, non-toxic polymers. These materials are carefully tested for biocompatibility, strength, and resistance to wear, heat, and chemicals. Manufacturing involves precise molding, extrusion, or injection molding techniques, followed by sterilization and cleaning processes to remove contaminants. Quality control checks, including cytotoxicity testing and biocompatibility assessments, are carried out to ensure that the material complies with safety standards. Medical plastic parts factories often use state-of-the-art equipment to ensure that all products are manufactured to meet the high standards required in the medical industry.
Medical grade silicone is manufactured through a process called “vulcanization,” which involves heating and curing silicone rubber to form a durable, flexible material. This process is typically carried out using a platinum-catalyzed or peroxide-catalyzed system, ensuring that the material remains non-toxic and biocompatible. The silicone is then molded into the desired shapes using injection molding or compression molding techniques. Throughout the manufacturing process, medical grade silicone undergoes strict quality control to ensure it meets the regulatory requirements for medical applications, such as ISO 10993 biocompatibility standards.
Plastic is widely used in the medical industry for a variety of applications due to its versatility, durability, and ease of molding into complex shapes. Common uses include medical device housings, syringes, drug delivery systems, IV bags, surgical instruments, and diagnostic tools. Medical-grade plastics such as polyethylene, polypropylene, and polycarbonate are specifically designed to meet regulatory requirements for biocompatibility, safety, and sterilization. In medical plastic parts factories, these plastics are shaped, sterilized, and tested to ensure they are suitable for patient contact, either for short-term or long-term use.
The medical industry produces a significant amount of plastic waste, primarily from single-use medical devices, packaging, and disposable products such as syringes, IV bags, gloves, and masks. Estimates suggest that the healthcare sector generates hundreds of thousands of tons of plastic waste annually. The majority of this waste is non-recyclable due to contamination, particularly in hospital settings. Efforts are being made to address this issue, including increased use of recyclable materials and advancements in sustainable packaging, but plastic waste remains a major environmental challenge for the medical industry.
High-Density Polyethylene (HDPE) is commonly used in the medical industry, particularly for medical packaging and products like bottles, drug containers, and certain surgical tools. However, not all HDPE is considered “medical grade.” For it to be medical grade, it must meet strict safety, biocompatibility, and regulatory standards, ensuring it is safe for patient use and can withstand sterilization. HDPE’s popularity in medical applications is due to its chemical resistance, strength, and ease of molding, which makes it a cost-effective material choice for many medical devices.
Medical grade polymers are specifically designed to be non-toxic, biocompatible, and safe for patient use. These materials undergo rigorous testing to ensure they do not cause adverse reactions when in contact with the body. For a polymer to be considered medical grade, it must meet strict regulatory standards, including those set by organizations like the FDA and ISO. Tests such as cytotoxicity, genotoxicity, and implantation studies are performed to confirm the material’s safety. While non-medical grade polymers can contain additives or impurities that may be harmful, medical-grade polymers are carefully regulated to ensure they are safe.
Yes, medical grade resin is specifically formulated to meet stringent regulatory standards for safety, biocompatibility, and performance. These resins undergo extensive testing to ensure they do not leach harmful substances into the body and are suitable for medical device applications. Medical grade resins are used in a wide variety of devices, including implants, diagnostic tools, and drug delivery systems. They are also designed to withstand repeated sterilization processes, ensuring they remain safe for long-term use. When properly processed and tested, medical grade resins are deemed safe for patient contact.
Medical grade Polyvinyl Chloride (PVC) is a form of PVC that has been specially formulated for use in medical applications. It must meet strict biocompatibility standards to ensure it is safe for use in patient care, especially in devices such as blood bags, catheters, and tubing. Medical grade PVC is flexible, durable, and resistant to chemicals, making it an ideal choice for many medical devices. Unlike standard PVC, medical grade PVC undergoes additional processing and testing to ensure it is free from harmful plasticizers and other additives that could be toxic or cause irritation.
The fastest growing medical device market is currently the market for wearable medical devices. These devices include fitness trackers, smartwatches with health monitoring features, and advanced medical wearables that track vital signs, glucose levels, and more. As the global demand for healthcare monitoring grows, driven by an aging population and increasing chronic conditions, wearable medical devices are expected to experience rapid growth. This trend has led to increased innovation in materials, including the use of medical-grade plastics and silicones, to create lightweight, durable, and comfortable devices for long-term wear.
The market for medical grade polymers is expected to grow significantly as the demand for medical devices, implants, and packaging increases. Medical grade polymers, including materials like polyethylene, polypropylene, silicone, and polycarbonate, are widely used in the production of medical components due to their versatility, durability, and biocompatibility. The global market for medical grade polymers is driven by factors such as advancements in medical technology, an aging population, and rising healthcare needs. Manufacturers are increasingly turning to these polymers for their ability to meet stringent safety standards while providing cost-effective solutions for mass production.
Plastic surgeons use a variety of medical-grade plastics, silicone, and polymers in both surgical tools and implants. For example, silicone is often used for breast implants due to its flexibility and biocompatibility. Polypropylene and polyethylene are commonly used in surgical meshes and implants, while surgical instruments may be made from medical-grade stainless steel or plastic composites. Medical-grade silicone and polymers are also used for facial implants, wound dressings, and prosthetics due to their ability to mimic natural tissue properties and their non-toxic, hypoallergenic nature.
Medicine containers, such as pill bottles, vials, and packaging, are typically made from plastics like high-density polyethylene (HDPE), polypropylene (PP), and polyethylene terephthalate (PET). These materials are chosen for their durability, resistance to moisture, and ability to maintain the integrity of the contents. HDPE and PP are often used for larger containers, while PET is commonly used for smaller, transparent vials and bottles. These materials are also FDA-approved and meet the necessary safety and compliance standards to ensure they are suitable for storing pharmaceuticals and medical products.
Contact our professional team now for a same-day quote and risk-free project evaluation. Benefit from ISO 8 cleanrooms, advanced machines, and 12-hour fast response in medical injection molding.