Medical precision components are highly specialized parts used in the manufacturing of medical devices. These components are designed with extreme accuracy to meet the rigorous demands of the healthcare industry. Medical injection molding is a key manufacturing process for producing these components, allowing for the creation of complex, precise shapes with high consistency. Precision is critical in medical device manufacturing because even the smallest deviation can impact the safety, effectiveness, and functionality of devices. Applications of China precision medical components span across various healthcare fields, from surgical tools that ensure precise operations to diagnostic devices like imaging systems, where accuracy is paramount. Additionally, they are used in implants, such as prosthetics and orthopedic devices, offering reliable performance and long-term durability. The development of medical precision components continues to advance healthcare by enhancing the quality and safety of essential tools and equipment. Medical precision components by FUJIU ensure device accuracy, supporting implants, surgical tools, orthopedic parts, wires, and springs.
Low-Volume to High-Volume Production Capabilities
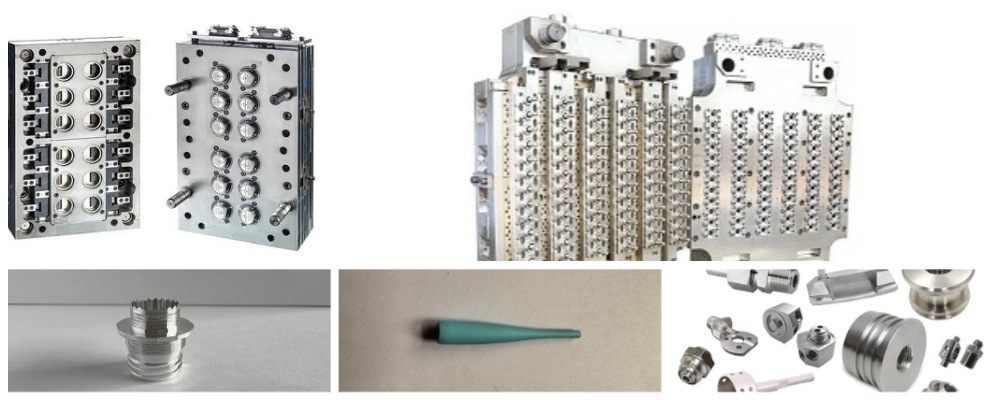
Attributes | Details |
---|---|
Place of Origin | Dongguan, Guangdong, China |
Brand Name | LY Medical Injection Mold |
Product Name | Medical Precision Components |
Application | Medical Industry |
CNC Machining or Not | CNC Machining |
Material | Aluminum, Brass, Bronze, Copper, Hardened Metal, Precious Metal, Stainless Steel, Steel Alloy |
Type | Broaching, Drilling, Etching/Chemical Processing, Laser Processing, Milling, Other Processing Services, Turning, Wire Cutting, Rapid Prototyping |
Is Micro-machining | Micro-machining |
Quality Control | 100% Inspection |
Machine | CNC Turning CNC Milling |
Process | CNC Machining + Deburring |
Drawing Format | 2D/(PDF/CAD)3D(IGES/STEP) |
Surface Treatment | Customer Requirement |
Item | OEM Precision Machining |
Color | Customized Color |
Size | Customized Size Acceptable |
Certification Standard | ISO9001 Certified |
Types of Medical Precision Components
Medical precision parts are essential for modern healthcare and medical technology, enabling the production of advanced medical devices and tools. These components ensure the accuracy, reliability, and safety needed for critical procedures. Below, we delve into six types of medical precision components, highlighting their applications and significance in the medical field.
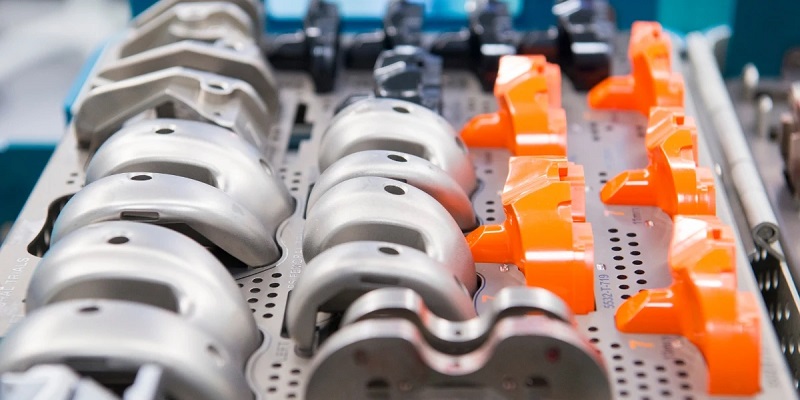
Mandrels and Cannulated Drills
Mandrels and cannulated drills are vital medical precision components used in minimally invasive procedures and orthopedic surgeries.
- Applications in Medical Procedures
These components are designed for precision and efficiency, often employed in surgical procedures such as joint replacements and spinal surgeries. Cannulated drills, for example, allow for the insertion of guidewires during orthopedic repairs, ensuring optimal accuracy. - Features and Benefits
Mandrels are precision-engineered to maintain dimensional stability and withstand high temperatures. Their customizable design allows compatibility with various surgical instruments, enhancing procedural outcomes.
Nitinol Orthopedic Staples
Nitinol orthopedic staples are another important category of precision medical components widely used in bone stabilization and alignment.
- Material Advantages
Nitinol, an alloy of nickel and titanium, offers superelasticity and shape memory, making it ideal for medical applications. These properties allow the staples to adapt to the body’s movements while maintaining their structural integrity. - Use Cases
Commonly used in orthopedic surgeries, Nitinol staples are integral to repairing fractures, stabilizing joints, and realigning bones. Their biocompatibility minimizes the risk of adverse reactions, making them highly reliable.
Orthopedic Pins and Screws
Orthopedic pins and screws are foundational precision medical components crucial for fracture fixation and implant procedures.
- Applications in Orthopedics
These medical plastic components secure broken bones and facilitate the healing process. They are commonly used in trauma surgeries to stabilize fractures or in joint reconstruction to anchor implants. - Features and Manufacturing
Orthopedic pins and screws are crafted with precision to ensure a perfect fit and high tensile strength. Materials such as stainless steel and titanium provide durability and biocompatibility, ensuring long-term functionality.
Precision CNC Components for the Medical Industry
The Role of Precision CNC Components for the Medical Industry
Precision CNC (Computer Numerical Control) machining plays a critical role in manufacturing medical devices and tools. These components are tailored to meet exacting medical standards, offering unmatched accuracy and consistency.
- Applications in Medical Device Production
Precision CNC components for the injection molding medical industry are used to create intricate surgical instruments, implantable devices, and diagnostic tools. For example, CNC machining produces detailed features like threading on orthopedic screws and complex shapes on implants. - Advantages in Medical Manufacturing
The ability to achieve micrometer-level accuracy ensures these components align with stringent regulatory requirements. Additionally, CNC technology allows customization, enabling manufacturers to produce patient-specific components.
Medical precision components, such as mandrels, cannulated drills, orthopedic staples, and screws, form the backbone of advanced healthcare solutions. Furthermore, the integration of technologies like CNC machining enhances the production of precision medical components, ensuring they meet the highest standards of quality and functionality. These innovations continue to drive progress in medical technology, improving patient outcomes worldwide.
CNC Medical Parts in Device Manufacturing with Medical Precision Components
CNC (Computer Numerical Control) machining has revolutionized the field of device manufacturing by enabling the production of highly accurate and reliable medical precision components. In addition to CNC machining, precision mold medical techniques are often used to create intricate shapes and structures required for medical components. With the growing demand for sophisticated medical devices, CNC technology ensures that components meet the stringent quality and safety requirements of the healthcare industry. Below, we explore how CNC machining drives innovation in medical component precision manufacturing and examine key techniques and examples.
How CNC Machining Revolutionizes Medical Precision
CNC machining transforms raw materials into intricate medical precision components, offering unmatched accuracy and repeatability. These components are essential for creating devices used in surgeries, diagnostics, and patient care. The precision achieved through CNC technology reduces manufacturing errors, ensuring components align perfectly with medical specifications.
Benefits in Medical Device Manufacturing:
- Micron-level Tolerances: Ensures compatibility and effectiveness in critical applications.
- Material Versatility: Processes materials like titanium, stainless steel, and high-performance plastics for diverse medical needs.
- Customization and Scalability: Enables both bespoke solutions for individual patients and large-scale production for healthcare facilities.
Key CNC Techniques for Medical Precision Components
5-Axis Milling
5-axis milling allows for the creation of complex geometries in a single setup, enhancing efficiency and precision. This technique is vital for manufacturing intricate medical components like joint replacements and surgical guides.
Wire and Sinker EDM (Electrical Discharge Machining)
EDM techniques are used for cutting hard materials and producing delicate, detailed parts. They are ideal for creating components like cardiac device casings or surgical instrument tips where precision is critical.
Micromachining specializes in producing miniature parts required for implants and diagnostic devices. Using ultra-fine tools, this technique ensures components meet the small-scale demands of modern medical technology.
Examples of CNC Medical Components
Surgical Instrument Components
CNC machining produces precision blades, handles, and endoscopic tool components, ensuring they meet high surgical standards for sterility and accuracy.
CNC technology creates components for pacemakers, defibrillators, and other cardiac devices, emphasizing durability and precise fit.
From orthopedic screws to dental implants, CNC machining ensures these critical components are biocompatible and dimensionally accurate.
CNC machining supports the production of laboratory tools like centrifuge rotors, pipettes, and diagnostic instrument parts, maintaining precision for research and testing.
Manufacturing Precision Medical Components
The Importance of Manufacturing Precision Medical Components
Manufacturing precision medical components involves cutting-edge technologies and meticulous quality control to meet healthcare’s exacting standards. This process ensures that every component is free of defects and performs its intended function flawlessly in life-critical scenarios.
Key Elements in Manufacturing Precision Medical Components
- Advanced Equipment: Leveraging CNC machines for consistent and repeatable results.
- Regulatory Compliance: Adhering to ISO 13485 and FDA guidelines for medical devices.
- Material Expertise: Selecting materials that meet medical-grade standards for biocompatibility and durability.
CNC machining plays an integral role in medical component precision manufacturing, facilitating the production of high-quality components necessary for life-saving devices. With techniques like 5-axis milling and micromachining, and applications ranging from surgical tools to laboratory equipment, CNC technology continues to push the boundaries of medical innovation.
Advanced Manufacturing Capabilities for Medical Precision Components
Advanced manufacturing capabilities have become the cornerstone of producing high-quality medical precision components. From prototyping to full-scale production, these capabilities ensure that components meet the rigorous demands of modern healthcare applications. Below, we explore the most innovative techniques, material selections, and specialized processes that make the production of precision components for medical a reality.
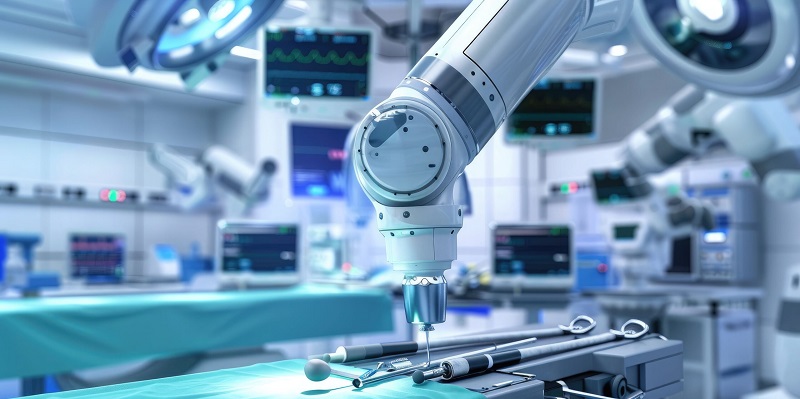
In-line Manufacturing and Process Optimization
In-line manufacturing streamlines the entire production process by integrating steps such as prototyping, rapid production, and finishing into one seamless workflow. This approach reduces lead times and ensures precision in every stage of manufacturing medical precision components.
Key Aspects of In-line Manufacturing:
- Prototyping: Advanced CNC technologies allow for the quick creation of prototypes that can be tested and refined before mass production.
- Rapid Production: High-speed machining enables the timely delivery of components, meeting critical timelines for healthcare providers.
- Flexible Finishing: Customizable finishing options such as polishing, coating, and engraving ensure components meet specific application requirements.
Quality Assurance Standards:
ISO 13485 certification is pivotal in maintaining the quality and safety of medical precision components. This certification ensures compliance with international plastic medical device manufacturing standards, addressing risk management and traceability.
Materials Used for Precision Components in Medical Applications
The selection of materials plays a critical role in ensuring the durability, biocompatibility, and functionality of precision components for medical devices.
Commonly Used Materials:
Titanium Grades:
Preferred for implants and surgical instruments due to their lightweight nature and exceptional biocompatibility.Corrosion-resistant, making them ideal for long-term use in the human body.
A versatile material used in surgical tools and fixtures, offering strength, sterility, and wear resistance.
High-Performance Alloys (Invar and Kovar):
Often used in diagnostic devices and precision measuring instruments, these alloys provide thermal stability and superior performance.
Medical Precision CNC Components: A Game-Changer in Healthcare
Specialized Techniques for Manufacturing Medical Precision CNC Components
Medical precision CNC components are vital in healthcare, requiring the most advanced machining techniques to meet exacting tolerances and complex geometries.
Precision CNC Equipment for Medical Components:
The use of precision CNC equipment for medical components ensures high levels of detail and repeatability. This equipment supports advanced techniques such as:
- Multi-axis milling for intricate shapes and surfaces.
- Micromachining for components used in minimally invasive surgeries.
- Wire EDM for delicate features and tight tolerances.
By employing these methods, manufacturers achieve superior precision and reliability, ensuring medical precision components meet the stringent demands of healthcare applications.
Precision CNC Equipment for Medical Components in Modern Manufacturing
The adoption of precision CNC equipment for medical components ensures consistency, efficiency, and scalability. Key benefits include:
- Automated Quality Control: Integrated sensors detect any deviations during production, guaranteeing flawless output.
- Scalability: CNC technology supports both small-batch and large-scale production without compromising quality.
- Innovation-Driven: CNC systems adapt to new designs and technologies, enabling the continuous improvement of medical device components.
The advanced manufacturing capabilities behind medical precision components have transformed the healthcare industry. With innovations in in-line manufacturing, the use of specialized materials, and the precision offered by cutting-edge CNC equipment, manufacturers ensure that every component meets the highest standards of performance and safety. These developments pave the way for the next generation of medical technologies, improving patient outcomes worldwide.
Key Players in Medical Component Manufacturing for Medical Precision Components
The manufacturing of medical precision components is a highly specialized field requiring expertise, advanced technology, and a commitment to quality. Several companies stand out as leaders in the industry, delivering precision components for medical devices that meet the stringent requirements of modern healthcare. Below, we explore key players and their contributions to precision medical component manufacturing.
The company’s history is deeply rooted in a family tradition of precision grinding. This legacy ensures a commitment to quality and innovation in every component produced. Their specialized knowledge in grinding and finishing allows them to achieve the exacting tolerances required in precision medical component manufacturing.
Innovations Driving the Future of Medical Precision Components
Precision Components for Medical Devices
Technologies continue to lead through innovation. By leveraging advanced manufacturing techniques and state-of-the-art materials, they are redefining the possibilities for precision components for medical devices. These companies play a crucial role in enhancing patient outcomes and driving technological advancements in healthcare.
Commitment to Quality in Precision Medical Component Manufacturing
The commitment to quality is evident in their adherence to strict standards, such as ISO 13485 certification. This ensures the reliability, safety, and performance of the medical precision components they produce, solidifying their standing as key players in the industry.
The success of precision medical component manufacturing depends on companies . Their dedication to innovation, quality, and precision has set a benchmark in the field, ensuring that medical precision components continue to meet the evolving demands of healthcare technologies. These leaders not only supply essential components but also drive the industry toward a future of enhanced medical solutions.
Applications of Medical Precision Components in Healthcare and Beyond
Medical precision components play an indispensable role in healthcare, contributing to a wide range of life-saving devices and equipment. Their precise engineering, high durability, and biocompatibility ensure reliability in critical applications. Medical injection molding applications are particularly important in this context, as they are used to create intricate and precise components such as surgical instruments, implants, and diagnostic tools. From orthopedic tools to diagnostic machines, the impact of these components extends beyond healthcare, influencing industries such as aerospace, robotics, and biotechnology.
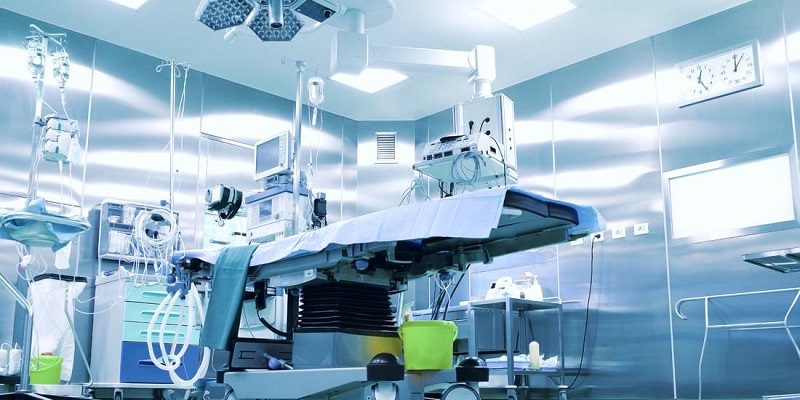
Orthopedic Devices: Precision for Healing
Orthopedic devices rely heavily on precision medical device components to deliver accurate and effective results. Components such as screws, staples, and pins are crucial for:
- Fracture Fixation: Precision-engineered screws and pins ensure proper alignment and stabilization of broken bones.
- Bone Reconstruction: Staples made from biocompatible materials like titanium provide long-lasting support in bone healing and reshaping surgeries.
- Joint Replacement: Custom-made components enable seamless integration with natural bone structures.
Minimally Invasive Tools: Reducing Patient Recovery Times
The evolution of minimally invasive surgical techniques demands medical precision components that are lightweight, durable, and meticulously crafted. Instruments like mandrels and cannulated drills are widely used for:
- Endoscopic Procedures: Allowing access to internal structures through small incisions.
- Orthopedic Surgery: Supporting precise drilling and implantation with minimal disruption to surrounding tissues.
These tools enhance surgical efficiency, reduce patient recovery times, and improve overall outcomes.
Diagnostic Equipment: Enhancing Medical Imaging
High-tech diagnostic equipment like CT and MRI scanners rely on precision medical device components to function accurately and consistently. Key applications include:
- Sensor Housing: Protecting delicate electronic components within imaging machines.
- Precision Gears and Bearings: Ensuring smooth operation and precise movements in scanning equipment.
- Component Mounting: Providing stable and accurate alignment for imaging sensors.
Surgical Instruments: Accuracy in the Operating Room
Surgical instruments require unmatched precision to ensure patient safety and optimal results. Examples include:
- Scalpels and Forceps: Manufactured with sharpness and durability to enhance surgical efficiency.
- Retractors: Designed to hold tissues firmly without causing unnecessary trauma.
- Custom Tools: Tailored for complex or unique surgical procedures to improve outcomes.
These medical precision components are essential for maintaining the high standards required in modern operating rooms.
Perform the Small Precision Inspection of Medical Device Components
Ensuring Quality through Rigorous Inspection
In the field of precision medical device components, inspection is a critical step to ensure reliability and performance. Advanced techniques are used to perform the small precision inspection of medical device components, which includes:
- Dimensional Analysis: Using high-precision measuring tools to verify component dimensions against design specifications.
- Material Testing: Ensuring that materials meet biocompatibility and durability requirements.
- Surface Quality Checks: Detecting and eliminating microscopic flaws that could compromise functionality.
These inspections not only enhance the quality of medical precision components but also extend their lifespan and safety in real-world applications.
Beyond Healthcare: Cross-Industry Applications
While healthcare remains the primary beneficiary of medical precision components, their applications extend to other advanced fields:
- Aerospace: High-precision components for aircraft engines and navigation systems.
- Robotics: Microcomponents for surgical robots and automation technologies. Medical device automation, which integrates these components, is playing an increasingly important role in enhancing the efficiency and accuracy of medical device manufacturing.
- Biotechnology: Specialized parts for lab equipment and genetic engineering tools.
The versatility of these components highlights their importance in driving innovation across multiple industries.
The applications of medical precision components span a wide range of critical functions in healthcare and beyond. Their precision, durability, and adaptability make them invaluable in orthopedic devices, minimally invasive tools, diagnostic equipment, and surgical instruments. By continuously advancing manufacturing and inspection techniques, these components will remain at the forefront of innovation, shaping the future of medicine and technology.
Ensuring Quality and Certification Standards for Medical Precision Components
Quality assurance is vital in the manufacturing of medical precision components, as these parts play a critical role in patient safety and healthcare outcomes. Achieving and maintaining the highest standards requires strict adherence to industry regulations, advanced inspection techniques, and a commitment to continuous improvement.
The Importance of ISO 13485 and FDA Registration
ISO 13485 certification and FDA registration are the cornerstones of quality management for manufacturers of medical precision components.
ISO 13485 Certification:
This internationally recognized standard ensures that manufacturers maintain stringent quality management systems tailored to medical devices. Key benefits include:
- Demonstrating compliance with global regulatory requirements.
- Enhancing process consistency and reducing defects.
- Building trust with healthcare providers and end-users.
FDA Registration:
For products distributed in the U.S., FDA registration is mandatory. It confirms that manufacturers of medical precision components meet all applicable safety and efficacy standards. This includes:
- Thorough documentation of manufacturing processes.
- Periodic audits and inspections to verify compliance.
Advanced Inspection Tools and Techniques
Ensuring the quality of medical precision components demands cutting-edge inspection technologies and methods. Precision is not optional—it’s a necessity in this field.
- Non-Destructive Testing (NDT):
This technique identifies internal defects without compromising the integrity of the component. Methods include X-ray inspection and ultrasonic testing. - Coordinate Measuring Machines (CMM):
These devices provide exact measurements to ensure components meet design specifications. CMMs are especially valuable for complex geometries. - Surface Roughness Analysis:
Advanced tools detect microscopic irregularities that could impact component performance, ensuring smooth finishes for applications like surgical tools. - Optical and Laser Inspection:
High-resolution imaging systems measure intricate details, enabling manufacturers to detect even the smallest deviations from specifications.
Continuous Improvement in Manufacturing Processes
The field of medical precision components demands relentless innovation and refinement of manufacturing processes. Key practices include:
- Lean Manufacturing:
Reducing waste and optimizing efficiency to ensure that production runs are cost-effective without compromising quality. - Statistical Process Control (SPC):
Using data-driven techniques to monitor and control production variables, minimizing errors and enhancing consistency. - Feedback Loops:
Incorporating feedback from healthcare providers and end-users to refine designs and improve functionality. - Advanced Automation:
Leveraging robotics and AI-powered systems to increase precision, reduce human error, and maintain uniformity in large-scale production.
The Role of Certifications in Building Trust
Certifications are more than compliance—they are a statement of quality and reliability. For manufacturers of medical precision components, obtaining and maintaining these certifications signals a commitment to excellence, patient safety, and regulatory adherence. This trust is critical in partnerships with medical device companies, healthcare institutions, and regulatory bodies.
Ensuring the quality of medical precision components involves a multifaceted approach, combining robust certification standards, advanced inspection techniques, and continuous improvement practices. By adhering to ISO 13485 and FDA requirements and leveraging state-of-the-art technology, manufacturers can guarantee the reliability and performance of their components, ultimately contributing to better patient care and innovation in healthcare.
How to Choose the Right Medical Precision Components Manufacturer?
Selecting the right medical precision components manufacturer is critical to ensuring high-quality, reliable medical devices. Here’s a detailed guide:
Expertise and Specialization
Look for a manufacturer with proven experience in medical applications. Specialization in producing precision components for devices, implants, and surgical instruments demonstrates their ability to meet the industry’s unique demands.
Compliance with Standards
Ensure the manufacturer adheres to medical industry regulations like ISO 13485, FDA standards, or CE certifications. These indicate quality management and compliance with safety protocols.
Technological Capabilities
Evaluate their technology and processes, such as CNC machining, injection molding, or laser cutting, which are essential for producing intricate, high-precision parts.
Material Selection
A reputable manufacturer offers biocompatible, durable materials tailored for specific applications, such as stainless steel, titanium, or medical-grade plastics.
Custom Design and Prototyping
Choose a partner that offers custom design services and rapid prototyping to meet your exact specifications and accelerate development cycles.
Reputation and Client References
Research their track record, customer reviews, and case studies. Positive feedback from other medical companies reflects reliability and quality.
Production Capacity and Scalability
Ensure the manufacturer can handle your volume requirements and scale production as demand grows.
By following these criteria, you can select a medical precision components manufacturer that ensures accuracy, compliance, and reliability for your medical products.
FUJIU Medical Injection Mold: Manufacturer of Medical Precision Components
FUJIU Medical Injection Mold, with its expertise in medical injection molding and precision mold solutions, stands out as a reliable medical precision components manufacturer. Its capabilities include working with a variety of medical-grade plastics, adhering to ISO-certified quality standards, and maintaining strict cleanliness and tolerance. With extensive material knowledge, the company ensures fast sampling, low MOQ, rapid delivery, and top-quality results. These features make FUJIU a trusted partner for producing high-precision components used in medical devices, implants, and surgical instruments, fulfilling every need in the healthcare industry.
Maintain and Care for Medical Precision Components
Proper maintenance and care of medical precision components are essential to ensure their longevity and reliability in critical applications. Here are key strategies:
Regular Cleaning and Sterilization
Follow the manufacturer’s guidelines for cleaning and sterilizing components. Use appropriate methods, such as autoclaving or chemical sterilization, to avoid damaging materials while maintaining sterility.
Inspection for Wear and Tear
Routinely inspect components for signs of wear, corrosion, or deformation. Early detection of defects can prevent failures during critical procedures.
Proper Storage
Store components in a clean, dry environment, protected from extreme temperatures, moisture, or contamination. Use dedicated storage cases to prevent physical damage.
Adherence to Usage Guidelines
Operate components within the specified limits for load, pressure, or temperature. Overuse or misuse can lead to premature failure.
Regular Calibration and Maintenance
For precision components in devices, ensure regular calibration and servicing to maintain accuracy and functionality.
Material-Specific Care
Be aware of the material properties of each component, such as susceptibility to corrosion in metals or degradation in plastics, and apply tailored maintenance practices.
Training and Handling Protocols
Train staff on proper handling techniques to minimize accidental damage. Mishandling can lead to reduced performance or complete failure.
By implementing these care practices, the service life of medical precision components can be significantly extended, ensuring their consistent performance and reliability in medical applications.
FAQs about Medical Precision Components
Genomics and Genetics: The study of genes and their functions helps identify genetic predispositions to certain diseases, allowing for more targeted and effective treatments.
Molecular Diagnostics: Techniques such as DNA sequencing, biomarker analysis, and other molecular diagnostics are used to identify unique disease profiles for each patient.
Big Data and Bioinformatics: Advanced computational tools are employed to analyze vast amounts of data from various sources, including electronic health records, clinical trials, and genetic databases.
Targeted Therapies: Treatments are developed based on the specific genetic and molecular makeup of a patient’s disease, leading to higher efficacy and reduced side effects.
Pharmacogenomics: This field studies how a person’s genes affect their response to drugs, allowing for personalized drug prescriptions that maximize efficacy and minimize adverse reactions.
Hardware: This includes the physical components of the device such as casings, tubing, sensors, and other mechanical parts. For example, in a blood pressure monitor, the cuff, gauge, and tubing are critical hardware components.
Software: Many medical devices are equipped with software that controls their functions and processes data. This software needs to be reliable, secure, and sometimes even capable of integrating with other healthcare systems.
Sensors and Actuators: Sensors collect data from the patient’s body or environment (e.g., glucose sensors, heart rate monitors), while actuators might be involved in administering treatment (e.g., insulin pumps).
Power Supply: Devices either plug into a power source or include batteries for portability and convenience. The power supply must be secure and reliable to ensure consistent operation.
User Interface: The interface includes screens, buttons, and other controls that allow healthcare providers or patients to interact with the device. An intuitive and user-friendly interface is crucial for proper operation.
Communications Modules: These allow the device to transmit data to other systems or devices, often via Bluetooth, Wi-Fi, or other wireless technologies. This component is essential for telemedicine and remote monitoring applications.
Compliance and Safety Features: Regulatory compliance, such as FDA approval, along with built-in safety features, ensures that the device can be used safely and effectively in a clinical setting.
Precision medicine integrates various components to deliver customized treatments based on an individual’s genetic, environmental, and lifestyle factors. Key components include:
Genomics: Genetic sequencing and analysis help identify mutations or markers linked to diseases.
Biomarkers: Biological indicators, such as proteins or DNA changes, guide diagnosis and therapy choices.
Diagnostics: Advanced imaging and laboratory tests ensure accurate disease identification.
Data Analytics: AI and machine learning analyze large datasets to predict outcomes and optimize care.
Medical Devices: Precision-engineered devices support tailored drug delivery or minimally invasive procedures.
Patient Monitoring: Wearable technology provides real-time data for continuous care.
For medical precision components, this involves high-accuracy parts used in diagnostic devices, surgical tools, and wearable health technologies, contributing to the effectiveness and reliability of precision medicine.
A Medtech OEM (Original Equipment Manufacturer) produces components, subsystems, or complete medical devices for healthcare companies. These manufacturers specialize in delivering high-quality, precision-engineered products that meet stringent regulatory standards. Their contributions range from diagnostic imaging systems to surgical instruments and wearable health devices.
In the context of medical precision components, Medtech OEMs ensure the seamless integration of complex, miniaturized parts into devices such as implantable pumps, catheters, or diagnostic sensors. They also provide custom components that align with specific medical applications, ensuring reliability, sterility, and compliance with healthcare standards. These OEMs are critical partners for medical device companies, enabling rapid prototyping, mass production, and innovation in Medtech solutions.
A medical device component refers to any part or subassembly that contributes to the functionality of a medical device. These components include:
Precision Mechanical Parts: Surgical instrument tips or catheter assemblies.
Electronic Components: Sensors, microchips, and batteries for monitoring devices.
Optical Components: Lenses or lasers used in diagnostic tools.
Materials: Specialized plastics or metals tailored for biocompatibility and durability.
Medical precision components play a vital role in ensuring the accuracy and reliability of devices such as diagnostic machines, minimally invasive tools, or wearable monitors. These components must meet strict medical standards, including ISO certifications, to guarantee safety and effectiveness in healthcare applications.
In healthcare, an OEM (Original Equipment Manufacturer) supplies products, components, or entire systems for medical applications under another company’s brand. These manufacturers create:
Precision Components for medical devices like implants or diagnostic tools.
Complete Systems, such as imaging equipment or laboratory analyzers.
Customized Solutions, designed to meet specific regulatory and functional needs.
OEMs support innovation and production for medical companies, enabling faster development and scalability of precision devices. In the context of medical precision components, healthcare OEMs ensure that parts meet exacting requirements for accuracy, sterility, and compliance, critical for patient safety and treatment success.
Precision components are highly accurate parts designed and manufactured to meet specific tolerances and functional requirements. In the medical field, these components include:
Miniature Gears and Bearings: Used in surgical instruments.
Microsensors: For patient monitoring devices.
Implantable Components: Such as stents or pacemaker electrodes.
These components are vital for medical devices where precision impacts performance and patient safety. Manufacturing involves advanced techniques like CNC machining, laser cutting, and cleanroom assembly to ensure exact specifications and regulatory compliance. Precision components support innovation in diagnostics, treatment, and patient monitoring.
OEM (Original Equipment Manufacturer) and ODM (Original Design Manufacturer) differ in their approach to product development:
OEMs produce components or devices based on a buyer’s design specifications. In healthcare, this might mean manufacturing custom surgical instruments or diagnostic machine parts.
ODMs design and manufacture complete products, offering turnkey solutions. They allow companies to market pre-designed medical devices under their own brand.
For medical precision components, an OEM focuses on producing parts that meet exacting requirements provided by healthcare firms, while an ODM delivers fully developed solutions ready for market. Both models are integral to the medical device supply chain.
Contact our professional team now for a same-day quote and risk-free project evaluation. Benefit from ISO 8 cleanrooms, advanced machines, and 12-hour fast response in medical injection molding.