Medical rubber molding plays a crucial role in the healthcare industry, providing high-quality, biocompatible rubber components that are essential for a wide range of medical devices. As medical technology advances, the demand for precision-engineered rubber parts continues to grow, ensuring the reliability and safety of various devices. Medical rubber molding is used in the production of critical products such as surgical tools, implants, seals, and gaskets, all of which must meet stringent regulatory standards. The use of medical-grade rubber materials ensures that these components are durable, flexible, and safe for patient use. With the right molding process, manufacturers can produce customized solutions that enhance the performance and longevity of medical devices, contributing significantly to patient care and safety. Medical rubber molding includes injection, compression, and transfer molding for medical devices. Fujiu Medical ensures precision with ISO Class 8 cleanroom molding.
Low-Volume to High-Volume Production Capabilities
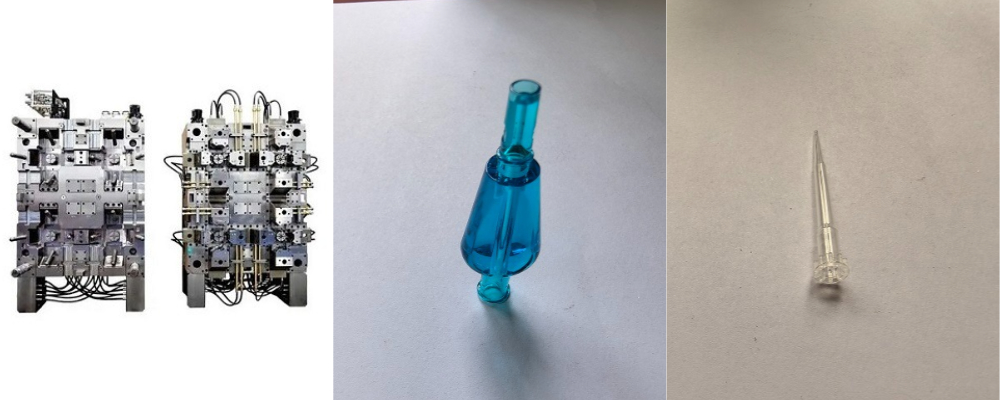
Attributes | Details |
---|---|
Place of Origin | Dongguan, Guangdong, China |
Brand Name | LY Medical Injection Mold |
Product Name | Medical Rubber Injection Mold |
Plastic Processing | Polypropylene, ABS, Polyvinyl Chloride, Polyethylene |
Process | Injection Molding |
Size | Customized Size |
Color | Customized Color |
Mold | Customizable Mold |
Shape | Customized Shapes |
Drawing Format | STEP/STP/IGS/x-t/STL/CAD/PDF/DWG, etc. |
Surface Treatment | Polishing |
Certification | CE, RoHS, ISO9001 |
Tolerance | 0.02mm-0.05mm |
Mold Life | 500000 shots |
Service | OEM |
Sales Unit | Single Item |
What is Medical Rubber Molding?
Medical rubber molding is a manufacturing process used to create high-quality, precise rubber components for medical devices and equipment. It involves shaping rubber materials using a variety of molding techniques to produce durable, biocompatible parts that meet strict regulatory standards. These rubber precision medical components are essential for the production of medical devices such as surgical tools, implants, gaskets, and seals. The process of medical rubber molding ensures that the rubber parts are not only functional but also safe for patient use, as they are designed to withstand the challenging environments often encountered in medical applications.
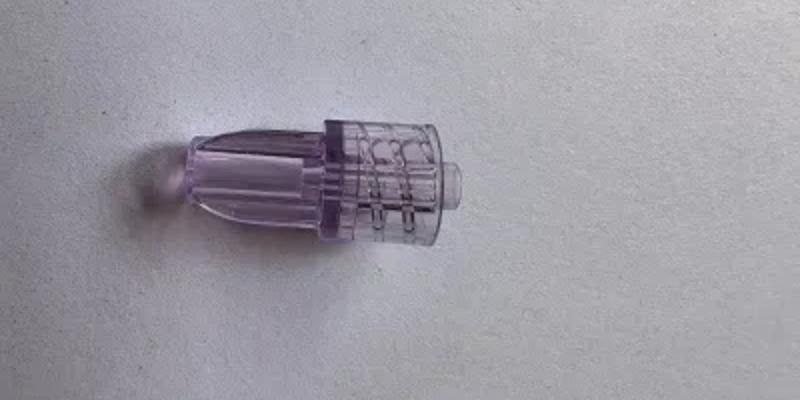
The Medical Rubber Molding Process
The process of medical rubber molding involves several key stages, including preparing the rubber material, shaping it into the desired form, and curing it to enhance its properties. Typically, medical-grade rubber materials like silicone, nitrile, and EPDM are used due to their excellent biocompatibility, flexibility, and durability. The raw rubber material is first compounded with additives to enhance its properties before being placed into a mold. Once in the mold, heat and pressure are applied to shape the rubber into the final product. The curing or vulcanization process bonds the rubber molecules, creating a strong, stable material that is resistant to wear, tear, and degradation.
This molding process can be adjusted depending on the specific requirements of the medical device, including factors such as the material’s elasticity, temperature resistance, and chemical compatibility. The choice of molding technique often depends on the complexity of the part, the material used, and the production volume needed.
Types of Medical Rubber Molding
There are several types of molding techniques commonly used in the medical industry. Each method offers specific advantages depending on the application and the characteristics of the final product. Below is an overview of the most common types of medical rubber molding:
Molding Type | Description | Advantages |
---|---|---|
Compression Molding | Rubber is placed into a heated mold and then compressed to form the desired shape. | Ideal for producing simple parts in high volumes; cost-effective for large runs. |
Injection Molding | Molten rubber is injected into a mold cavity under high pressure to form precise, complex shapes. | Provides high precision, excellent surface finish, and is highly repeatable; ideal for complex parts. |
Transfer Molding | Rubber is preheated and then transferred into a mold cavity where it is compressed and cured. | Best for creating complex, high-precision components with uniform material distribution. |
Overmolding | A secondary rubber material is molded over an existing component, often for added grip or flexibility. | Enhances the functionality of medical parts by combining different materials for performance. |
Why These Processes are Suitable for Medical Applications
Each type of medical rubber molding offers distinct advantages that make them well-suited for medical applications. For instance:
- Compression molding is often used for simple parts like gaskets or seals, which are essential in medical equipment to ensure proper sealing and prevent contamination. The ability to handle large production volumes with relatively lower costs makes this method ideal for producing high-demand components.
- Injection molding is highly precise, making it suitable for producing complex, intricate medical components such as surgical instruments, tubing, and connectors. It is particularly effective in ensuring that each part meets tight tolerances, which is critical for medical devices that require high levels of accuracy for patient safety.
- Transfer molding offers advantages in creating parts that require a uniform material distribution and high precision, which is crucial for critical medical components such as implants or flexible parts used in medical devices.
- Overmolding is beneficial for creating multi-material parts that require enhanced functionality, such as handles for surgical tools that need both a firm structure and a soft, ergonomic grip. This technique allows the integration of different materials, such as combining silicone with harder plastics or metals.
The suitability of these molding processes for medical applications is further enhanced by the use of medical-grade materials, which ensure that the molded rubber parts are biocompatible, durable, and able to withstand sterilization processes. Whether it’s sealing a medical container, creating flexible catheters, or producing gaskets for implants, medical rubber molding provides the versatility and reliability needed for the stringent requirements of the healthcare industry. By using precise and controlled molding techniques, manufacturers can create rubber components that perform reliably in critical medical environments, contributing to the overall safety and effectiveness of medical devices.
Types of Medical Rubber Molding
Medical rubber molding includes various techniques, each suited to different types of medical components, product requirements, and production volumes. The primary molding processes used in the medical industry—injection molding, compression molding, and overmolding/insert molding—are designed to meet the stringent quality standards required for medical devices and equipment. Let’s explore each of these molding processes in detail.
Injection Molding in Medical Rubber Molding
How Liquid Silicone Rubber Injection Molding Machines Work
Injection molding for medical rubber components typically involves the use of liquid silicone rubber (LSR), a versatile material known for its biocompatibility and flexibility. In this process, medical-grade silicone is heated to a liquid state and injected into precisely designed molds under high pressure. Once injected, the material is allowed to cure, taking the shape of the mold cavity. This results in highly precise and durable medical parts, including complex, intricate designs.
Advantages of Injection Molding in Medical Device Manufacturing
Injection molding is one of the most popular techniques for medical rubber molding, and for good reason. Some of its key advantages include:
- Precision: Injection molding allows for very tight tolerances, making it ideal for components that require high levels of accuracy. For medical devices where exact measurements are crucial for functionality and safety, this method provides superior control over the final product’s dimensions.
- Cost-Effectiveness: Once the initial mold is created, injection molding becomes highly cost-efficient for large-scale production runs. The automated nature of the process reduces labor costs, while the ability to produce high volumes of uniform parts further decreases the cost per unit.
- Consistency: Injection molding offers excellent reproducibility, ensuring that each part is identical to the next. This is particularly important in medical device plastic manufacturing, where even the smallest variations can affect the performance of the product.
Common Medical Products Made Using Injection Molding
Injection molding is used to produce a wide variety of medical rubber parts, including:
- Surgical instruments: Handles, grips, and non-slip components.
- Seals and gaskets: For medical equipment requiring airtight or liquid-tight seals.
- Catheters: Tubing for fluids and medical gases, often made from silicone or other elastomers.
- Implants: Joint replacements and other medical implants requiring biocompatible, flexible materials.
- Syringe parts: Pistons, seals, and diaphragms used in syringes and other disposable medical devices.
Compression Molding in Medical Rubber Molding
Benefits of Compression Molding for Producing Durable, Biocompatible Rubber Parts
Compression molding is another widely used method in medical rubber molding, particularly for producing parts that require durability, strength, and biocompatibility. In compression molding, rubber material is placed into an open mold cavity, and then heat and pressure are applied to mold the rubber into the desired shape. After the material has cooled and solidified, the mold is opened to release the finished part.
Some key benefits of compression molding include:
- Durability: Compression molding produces strong, long-lasting rubber parts. This is especially important for medical products that need to withstand wear, tear, and harsh conditions, such as seals for medical devices or gaskets for machines.
- Biocompatibility: Compression molding works well with various biocompatible materials, such as silicone and other elastomers, ensuring the safety and non-toxicity of medical components.
- Low Tooling Costs: Compared to injection molding, compression molding can be more cost-effective when producing small to medium production runs. This makes it a good choice for manufacturers who need to balance cost with performance for certain medical rubber products.
Common Medical Products Made Using Compression Molding
Compression molding is used to produce a variety of medical rubber parts, including:
- O-rings and seals: Ensuring airtight or liquid-tight seals for medical equipment.
- Gaskets: Used in valves, pumps, and other medical machinery.
- Protective covers: Rubber covers for medical equipment to prevent damage and contamination.
- Medical tubing: For fluids and gases, often used in oxygen masks or IV systems.
Overmolding and Insert Molding in Medical Rubber Molding
Process and Benefits of Overmolding and Insert Molding
Overmolding and insert molding are specialized techniques used in medical rubber molding to combine multiple materials, enhancing the functionality and performance of the final product.
- Overmolding involves molding a layer of rubber around a pre-existing component, often made of plastic or metal. This is commonly used when parts need to have both hard and soft elements, such as a surgical handle that combines a rigid frame with a soft, non-slip rubber grip.
- Insert molding is similar but involves placing an insert—typically a metal or plastic component—into the mold before the rubber is injected or compressed. The rubber material then bonds to the insert, creating a single, cohesive part.
Benefits of Overmolding and Insert Molding
- Enhanced Performance: By combining different materials in one part, these techniques improve the functionality of the component. For example, overmolding a rubber grip over a hard plastic body makes surgical tools more comfortable to use while maintaining their structural integrity.
- Increased Durability: Insert molding ensures that rubber parts are securely bonded to other materials, enhancing their strength and durability. This is crucial for components exposed to repetitive use or high stress, such as connectors and joints in medical devices.
- Customization: Overmolding allows for the creation of multi-material parts with different textures, colors, or hardness, which is especially useful for designing medical tools and devices that need to meet specific ergonomic or functional needs.
Common Medical Products Made Using Overmolding and Insert Molding
- Surgical instrument handles: Combining hard plastic or metal with a soft rubber grip for comfort and safety.
- Catheters: Providing flexibility and smooth surfaces with overmolded silicone tubing.
- Needle and syringe components: Combining elastomeric seals with rigid plastic to prevent leaks and improve functionality.
- Medical connectors: Ensuring a secure and reliable connection between various medical components, such as IV lines or respiratory equipment.
Each of these types of medical rubber molding—injection molding, compression molding, and overmolding/insert molding—offers unique advantages depending on the specific needs of the medical device. By selecting the appropriate molding process, manufacturers can produce high-quality, precise rubber components that are essential for the safe and effective operation of medical devices.
Double Shot Molding in Medical Rubber Molding
Double shot molding is an advanced technique used in medical rubber molding to create complex, multi-material medical components with enhanced functionality. This process allows manufacturers to mold two different materials or colors in a single production cycle, improving efficiency and product performance. In the medical industry, double shot molding is widely used for devices requiring soft-touch grips, multi-layer sealing, or integrated hard-soft material structures. Below, we explore the key aspects of double shot molding in medical rubber molding.
Process of Double Shot Molding
Double shot molding involves injecting two different materials into a mold in successive stages. The first material is molded into a base structure, and then a second rubber or plastic material is injected over or around it. This process ensures strong adhesion between the two layers without requiring adhesives or additional assembly.
Benefits in Medical Applications
Double shot molding enhances ergonomics, durability, and biocompatibility in medical devices. It enables seamless integration of soft and hard materials, improving grip and comfort for surgical instruments, respiratory masks, and catheters. The process also reduces contamination risks by eliminating assembly steps.
Common Medical Components Using Double Shot Molding
Medical devices benefiting from double shot molding include syringe plungers, multi-layer seals, catheter grips, and medical-grade handles. This method allows for precise control over texture and flexibility, ensuring safety and usability in healthcare environments.
By integrating double shot molding into medical rubber molding, manufacturers achieve high-quality, durable, and safe medical components with superior functionality.
Micro Molding in Medical Rubber Molding
Micro molding is a specialized technique within medical rubber molding that enables the production of extremely small, high-precision rubber components used in medical and pharmaceutical applications. As medical devices continue to miniaturize, the demand for micro-molded rubber parts has surged, requiring advanced molding processes capable of producing components with tight tolerances, biocompatibility, and consistent quality. This technique plays a crucial role in manufacturing intricate rubber components for catheters, seals, drug delivery systems, and implantable medical devices. Below, we explore the key aspects of micro molding in medical rubber molding, including its technology, applications, materials, and benefits.
Technology Behind Micro Molding in Medical Rubber Molding
Micro molding in medical rubber applications utilizes specialized injection molding machines designed to handle extremely small shot sizes with high precision and repeatability. Unlike traditional injection molding, micro molding involves sub-millimeter dimensions, requiring molds with ultra-fine cavity details and precision control over temperature, pressure, and material flow.
- Liquid Injection Molding (LIM): This is the most common method for micro-molding rubber components, particularly using liquid silicone rubber (LSR) due to its excellent flow properties and biocompatibility.
- Cold Runner Systems: These systems help reduce material waste, which is critical when dealing with costly medical-grade rubbers.
- Micro-Machining for Molds: Advanced CNC machining, EDM (electrical discharge machining), and laser etching are used to create intricate mold cavities that enable extremely detailed rubber micro-components.
Applications of Micro Molding in Medical Rubber Molding
Micro molding has revolutionized the production of small-scale, complex rubber parts used in various medical devices. These components require extreme precision to ensure functionality, reliability, and safety. Key applications include:
- Micro-Seals and Gaskets: Used in minimally invasive surgical tools, syringes, and medical pumps, where airtight sealing is critical.
- Catheter Components: Tiny molded parts help enhance flexibility and performance in cardiovascular and neurovascular catheters.
- Implantable Medical Devices: Micro-molded silicone and other rubber materials are used in pacemakers, drug-eluting stents, and hearing aids due to their biocompatibility.
- Lab-on-a-Chip (LOC) Devices: These diagnostic microfluidic devices use precisely molded rubber components to control fluid flow and chemical reactions.
Materials Used in Micro Molding for Medical Rubber Applications
Material selection is crucial in medical micro molding, as rubber components must meet strict biocompatibility and sterilization requirements. The most commonly used materials include:
- Liquid Silicone Rubber (LSR): Preferred for its low viscosity, high purity, chemical resistance, and ability to withstand sterilization.
- Thermoplastic Elastomers (TPEs): Used when flexibility and reusability are required, especially in wearable medical devices.
- Fluoroelastomers (FKM): Ideal for medical components exposed to aggressive chemicals or extreme temperatures.
- EPDM (Ethylene Propylene Diene Monomer): Used for seals and gaskets due to its excellent resistance to heat, ozone, and sterilization processes.
Benefits of Micro Molding in Medical Rubber Molding
Micro molding provides numerous advantages in medical rubber applications, particularly in precision manufacturing, material efficiency, and compliance with medical regulations. Some key benefits include:
- High Precision and Consistency: Advanced micro-molding techniques allow for repeatable, tight-tolerance production, crucial for medical applications.
- Material and Cost Efficiency: The process minimizes waste, especially when using expensive medical-grade rubber materials.
- Biocompatibility and Sterility: Medical rubber micro-components meet stringent FDA, ISO 10993, and USP Class VI standards for direct patient contact and implantable use.
- Scalability for High-Volume Production: Once the tooling is set up, micro molding enables mass production with minimal defects, ensuring cost-effective manufacturing.
- Supports Medical Device Miniaturization: As medical technology advances, smaller, more efficient rubber components are needed for portable and implantable devices.
Micro molding is a critical innovation in medical rubber molding, allowing for the precise, high-quality production of miniature rubber components used in advanced medical devices. The combination of specialized molding technology, high-performance rubber materials, and strict regulatory compliance ensures that micro-molded medical rubber parts meet the growing demands of the healthcare industry. As medical devices continue to shrink in size while increasing in complexity, micro molding will remain an essential manufacturing process for the future of medical technology.
Key Materials Used in Medical Rubber Molding
The choice of materials used in medical rubber molding is crucial in ensuring the safety, durability, and performance of medical devices. Different materials offer unique properties that make them suitable for specific medical applications. In this section, we will explore the most commonly used materials in medical rubber molding, including silicone rubber and other elastomers like nitrile, neoprene. We will also discuss the importance of compliance with industry standards such as FDA approval and USP Class VI certification.
Silicone Rubber in Medical Rubber Molding
Silicone Rubber is perhaps the most widely used material in medical rubber molding due to its exceptional biocompatibility, flexibility, and durability. This elastomer is highly favored in applications that require materials that can come into direct contact with the human body or bodily fluids, such as implants, catheters, and seals.
Key Properties of Silicone Rubber
- Biocompatibility: Silicone rubber is known for its excellent biocompatibility, meaning it does not cause harmful reactions when in contact with body tissues, making it ideal for medical devices that interact with patients.
- Flexibility and Durability: Silicone rubber is both flexible and durable, allowing it to maintain its shape and function over time. This makes it perfect for components like catheters and seals that must withstand bending, stretching, and repeated use.
- Temperature Resistance: Silicone rubber can withstand a wide range of temperatures, from low to high, without degrading, making it an excellent choice for sterilization processes like autoclaving.
- Chemical Resistance: Silicone rubber is resistant to a variety of chemicals, including acids, alkalis, and solvents, which makes it a good fit for medical devices exposed to various substances.
- Non-Toxicity: Silicone rubber is non-toxic, hypoallergenic, and free from harmful chemicals like BPA or phthalates, making it a safe option for medical applications.
Applications in Medical Rubber Molding
- Implants: Silicone rubber is commonly used in long-term and short-term implants due to its ability to endure body fluids and its minimal risk of causing immune reactions.
- Catheters: Flexible and smooth silicone rubber is often used to make catheters, as it is gentle on the body and reduces the risk of tissue damage.
- Seals and Gaskets: Silicone’s sealing properties make it ideal for use in medical devices that require a reliable barrier against liquids or gases, such as IV bags or dialysis machines.
Other Elastomers in Medical Rubber Molding
In addition to silicone, several other elastomers are used in medical rubber molding for specialized applications. These include nitrile, neoprene. Each of these materials has unique properties that make them suitable for particular medical applications.
Nitrile Rubber
- Properties: Nitrile rubber is a synthetic rubber that offers excellent resistance to oils, fuels, and other chemicals. It is also highly durable, making it resistant to wear and tear.
- Applications: Nitrile rubber is often used in medical gloves, seals, and gaskets, especially in environments where chemical resistance is required.
Neoprene Rubber
- Properties: Neoprene is known for its resistance to weathering, ozone, and a variety of chemicals. It also provides good flexibility and resilience.
- Applications: Neoprene is used in the production of medical devices like orthopedic supports, respiratory masks, and seals that need to resist chemical exposure and maintain flexibility.
Compliance with Industry Standards
In medical rubber molding, it’s not just about the material properties but also ensuring that the rubber parts meet the strict regulatory standards set for medical devices. Compliance with standards such as FDA approval and USP Class VI certification is critical to ensure that the rubber components are safe for use in medical applications.
- FDA Approval: The U.S. Food and Drug Administration (FDA) regulates medical devices and materials that come into contact with the human body. Medical rubber components, such as those made from silicone or nitrile, must be tested and approved by the FDA to ensure they meet safety standards. FDA approval guarantees that the materials do not conta At FUJIU Medical Injection Mold, we bring over 20 years of excellence as a third-generation, employee-owned factory. Every team member is a stakeful chemicals and are safe for their intended use in medical devices.
- USP Class VI Certification: The United States Pharmacopeia (USP) Class VI certification is a critical standard for materials used in medical devices. Class VI certification specifically addresses the biocompatibility of rubber materials and requires testing to ensure that the materials do not cause adverse reactions when in contact with human tissue. Rubber materials used in medical devices must meet these standards to ensure patient safety.
By using materials that are both high-performance and compliant with these standards, manufacturers ensure that their products are both effective and safe for medical use. Whether it’s silicone for catheters or nitrile for gloves, medical molding rubber uses materials that provide the reliability and biocompatibility necessary for patient care.
The materials used in medical rubber molding—such as silicone rubber, nitrile, neoprene—play a crucial role in ensuring the safety, effectiveness, and durability of medical devices. The choice of material depends on the specific needs of the application, such as flexibility, chemical resistance, or high-temperature performance. Additionally, compliance with standards like FDA approval and USP Class VI certification ensures that these materials are safe for use in medical devices that come into direct contact with the body.
Rubber Molding Medical Industry: Importance and Applications
The rubber molding medical industry plays a crucial role in the design, development, and production of high-quality medical components that are essential for the healthcare sector. As medical technologies continue to evolve, the demand for precision, reliability, and biocompatibility in medical devices has risen. Rubber molding processes are at the heart of this transformation, providing solutions that meet the stringent regulatory and functional requirements of the medical field.
Overview of the Rubber Molding Medical Industry and Its Critical Role in the Healthcare Sector
The rubber injection molding medical industry encompasses a wide range of molding processes that are specifically tailored to produce medical-grade components. These processes include compression molding, injection molding, transfer molding, and overmolding. The industry is deeply integrated into the production of a variety of medical devices, including surgical instruments, implants, seals, gaskets, and many other components. The ability to mold rubber into specific shapes and sizes with high precision makes it an indispensable method for manufacturing medical parts.
One of the critical aspects of the rubber molding medical industry is its focus on producing components that are not only effective in their functionality but also safe for patients. Medical-grade rubbers, like silicone, are chosen for their biocompatibility, flexibility, and durability, ensuring that the parts produced can withstand the physical demands of medical environments while maintaining patient safety.
The Significance of Medical Rubber Molding in Producing Reliable, High-Quality Components for Medical Devices
Medical rubber molding is essential for producing parts that are reliable, durable, and capable of performing under harsh medical conditions. For instance, components like gaskets and seals, used in surgical instruments or medical machinery, need to create tight, leak-proof seals to prevent contamination or malfunction. Rubber molding processes ensure that these parts are not only manufactured to precise specifications but are also able to meet regulatory standards such as FDA approvals and USP Class VI certification.
High-quality medical rubber components, such as seals, O-rings, and tubing, are designed to perform reliably in critical environments, from operating rooms to emergency medical equipment. In addition, many of these parts are subjected to strict sterilization procedures, such as autoclaving or chemical sterilization, which rubber materials can withstand without compromising performance or safety.
Moreover, the versatility of medical rubber molding allows for the production of components that can function across various applications in the medical field, from diagnostic devices to implantable products. For example, rubber molded components are often used in catheter production, where the material’s flexibility and biocompatibility are crucial for patient comfort and safety.
How Medical Rubber Molding Supports Innovation in the Medical Field
The rubber molding medical industry is a key enabler of innovation within the healthcare sector. As new medical technologies emerge, the need for specialized, custom-designed components grows. Medical rubber molding offers a unique combination of flexibility and precision that can meet these evolving demands. For example, in the development of new surgical tools, medical molds can be customized to create handles, grips, and functional parts that are ergonomically designed to improve the surgeon’s precision and comfort during procedures.
In the field of implants, medical rubber molding allows for the creation of components that are tailored to fit specific medical needs. For example, custom-made silicone implants used in reconstructive surgery or joint replacements benefit from the molding process’s ability to create smooth, seamless surfaces that are both biocompatible and durable. Similarly, rubber-molded components in drug delivery systems, such as insulin pumps, ensure the safe and controlled release of medication over time.
Another area where medical rubber molding contributes to innovation is in safety seals for medical devices. These seals play a crucial role in ensuring that devices like syringes, IV tubes, and drug vials are securely sealed to prevent contamination, leakage, or spoilage. Through advanced molding techniques, manufacturers can produce seals that are both functional and compliant with the highest standards of quality and performance.
By leveraging medical rubber molding, the healthcare industry can continue to innovate, offering more advanced, customized, and reliable medical solutions. As the demand for more personalized and minimally invasive medical treatments increases, the ability to produce tailored components that meet these specifications will be essential in driving further advancements in medical care.
This expanded section integrates the keyword “medical rubber molding” in each relevant part while detailing its role in the healthcare sector. The content highlights the industry’s importance, how it ensures high-quality products, and its support for medical innovation.
Medical Rubber Molding Applications
Medical rubber molding plays a critical role in the production of essential components for medical devices, ensuring that these devices meet the necessary standards for safety, durability, and functionality. The versatility of rubber materials, especially silicone, nitrile, and other elastomers, makes them ideal for a wide range of applications in the healthcare industry. In this section, we will explore some of the most common medical rubber molding applications, including surgical handles, gaskets and seals, tubing and connectors, and catheters and implants. We will also discuss the importance of high-quality molded rubber components in ensuring patient safety and device reliability.
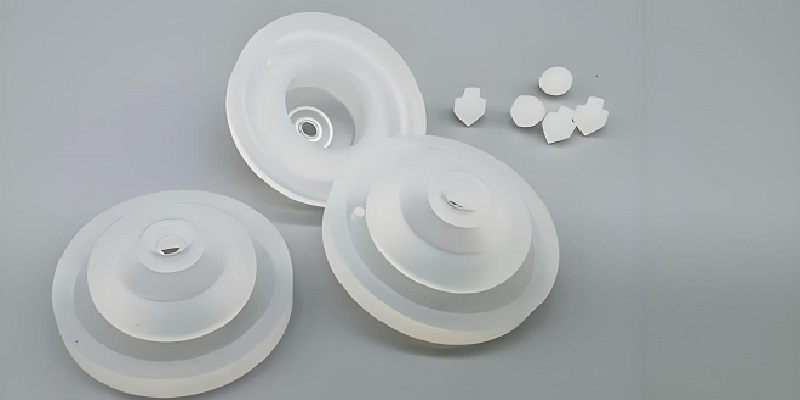
Common Applications in Medical Devices
Surgical Handles
Surgical handles are essential components of medical instruments such as scalpels, forceps, and other surgical tools. Medical rubber molding is widely used to produce ergonomic, non-slip handles that provide a secure grip during surgical procedures. Rubber materials like silicone and rubber blends offer comfort, flexibility, and durability, which are critical in ensuring that healthcare professionals can handle instruments with precision and safety.
- Benefits: Rubber molded surgical handles provide better ergonomics, reduce hand fatigue, and improve grip in both dry and wet conditions. Additionally, the materials used are typically biocompatible and resistant to sterilization processes like autoclaving, ensuring they remain safe and effective after repeated use.
- Applications: These handles are commonly used in tools such as scalpels, tweezers, and retractors, which require precision, comfort, and reliability in high-pressure, sterile environments.
Gaskets and Seals
Gaskets and seals are integral components in many medical devices, including oxygen tanks, pumps, IV sets, and fluid control systems. These components are responsible for preventing leaks and maintaining airtight or liquid-tight seals between different parts of the device. Medical rubber molding ensures that gaskets and seals are precisely molded to fit the required dimensions, ensuring functionality and safety.
- Benefits: Rubber molded gaskets and seals made from silicone or other elastomers are flexible, durable, and resistant to wear, tear, and degradation from exposure to harsh chemicals or high temperatures. The materials used also exhibit excellent sealing properties, making them perfect for maintaining sterility and preventing contamination in sensitive medical environments.
- Applications: These rubber components are widely used in medical devices such as pumps, syringes, infusion sets, blood filters, and sealing valves.
Tubing and Connectors
Medical tubing and connectors are essential for delivering fluids, gases, or medications within medical devices. Tubing systems are found in applications such as intravenous (IV) drip lines, respiratory systems, dialysis machines, and feeding tubes. Medical rubber molding is used to produce flexible, durable, and biocompatible tubing that can withstand bending, stretching, and exposure to body fluids or medications.
- Benefits: Rubber molded tubing and connectors are often made from materials like silicone, which is flexible, non-reactive, and easy to sterilize. These properties are essential when the tubing must be used in continuous medical treatments or when they come into direct contact with patients’ bodies.
- Applications: Common uses include IV catheters, oxygen masks, drainage tubes, and feeding tubes. Tubing is also used in dialysis machines, blood transfusion systems, and for the administration of medications in hospitals and clinics.
Catheters and Implants
Catheters and implants are some of the most critical medical components where medical rubber molding is heavily relied upon. Catheters, such as urinary, vascular, and intravenous catheters, are inserted into the body to administer fluids, deliver medication, or drain bodily fluids. Implants, such as joint replacements or pacemakers, require the use of flexible, biocompatible rubber materials to ensure they function optimally within the body over extended periods.
- Benefits: Rubber molded catheters are flexible, smooth, and biocompatible, which ensures that they can be inserted with minimal discomfort and can move with the body without causing damage to tissues. Medical-grade silicone is often the material of choice due to its non-reactivity, flexibility, and ability to withstand sterilization. Silicone’s ability to remain inert in the human body makes it suitable for both short-term and long-term implants.
- Applications: Common medical rubber molding applications include urinary catheters, endotracheal tubes, and vascular access catheters, as well as long-term implants like silicone breast implants, pacemaker leads, and prosthetic components.
The Importance of High-Quality Molded Rubber Components in Ensuring Patient Safety and Device Reliability
In medical rubber molding, quality is paramount. Since medical devices are designed to directly interact with the human body, it is critical that all molded rubber components are manufactured to the highest standards of safety and precision. High-quality medical rubber molding ensures that the parts meet biocompatibility requirements, regulatory standards, and function correctly in life-saving applications.
- Biocompatibility: Rubber materials must not cause adverse reactions in patients. Therefore, the rubber used in medical applications must be tested for biocompatibility, ensuring that it will not induce allergic reactions or toxicity when in contact with human tissues.
- Sterility: Many rubber components, such as catheters, gaskets, and surgical tools, need to be sterile or capable of being sterilized. The molding process ensures that parts are free of contaminants and can be safely used in sterile environments.
- Durability and Performance: Rubber components must be able to withstand mechanical stress, environmental factors like temperature and humidity, and repeated sterilization without degrading. Ensuring that these components are durable helps maintain the reliability and performance of medical devices over time, reducing the risk of device failure and improving patient outcomes.
High-quality molded rubber parts are not only crucial for the functionality of medical devices but also for patient safety. These components ensure that devices are reliable, safe, and effective, which is why the precision and quality control in medical rubber molding processes are so important.
Medical rubber molding is used in a variety of applications across the healthcare industry, including surgical handles, gaskets and seals, tubing and connectors, and catheters and implants. Each of these components requires high-quality materials and precise molding techniques to ensure patient safety and device reliability. As the demand for medical devices continues to grow, the importance of medical rubber molding in the production of reliable, durable, and biocompatible components will only increase.
Choosing the Right Medical Rubber Molding Factory
When it comes to selecting the right medical rubber molding factory, several key factors need to be considered to ensure that the manufacturer can meet the stringent requirements of the medical industry. Medical devices must adhere to rigorous standards for safety, performance, and reliability, so choosing a factory with the right capabilities is essential. In this section, we will explore the factors to consider when selecting a medical rubber molding factory and highlight some of the leading manufacturers in the industry.
Factors to Consider When Selecting a Medical Rubber Molding Factory
Experience and Expertise in the Medical Industry
One of the most important factors when choosing a medical rubber molding factory is its experience and expertise in the medical field. The medical device industry requires specialized knowledge of materials, regulations, and design requirements, and it is crucial that the factory has a deep understanding of these aspects.
- Experience: A factory with a proven track record in manufacturing medical rubber parts will be better equipped to handle the complexities of medical device molding. Experience in the industry allows manufacturers to anticipate challenges, ensure compliance with standards, and deliver high-quality products.
- Expertise: Companies that specialize in medical rubber molding should have in-depth knowledge of the different rubber materials used in medical applications, such as silicone, nitrile. They should also understand the specific needs of medical devices, such as biocompatibility, sterilization requirements, and durability.
Certifications and Compliance
Compliance with industry standards and certifications is crucial when choosing a medical rubber molding factory. These certifications ensure that the factory adheres to the necessary regulatory requirements and produces safe, reliable products for medical use.
- ISO 9001:2015 Certification: ISO 9001:2015 is a quality management standard that demonstrates a factory’s commitment to maintaining high-quality manufacturing processes. This certification is essential in ensuring that the medical rubber molding factory follows best practices for quality control and product consistency.
- FDA Compliance: The U.S. Food and Drug Administration (FDA) regulates the production of medical devices, including those made with molded rubber components. A factory that is FDA-compliant follows the necessary regulatory processes for ensuring the safety and effectiveness of its products.
- USP Class VI Certification: The United States Pharmacopeia (USP) Class VI certification is crucial for rubber materials used in medical applications. Class VI certification guarantees that the rubber materials meet the required biocompatibility standards for use in medical devices that come into direct contact with human tissue.
These certifications ensure that the factory is adhering to high standards of safety, quality, and compliance, which is especially important in the medical field where the stakes are high.
Ability to Provide Custom Molded Rubber Parts for Unique Applications
Medical devices often require customized parts that are tailored to specific applications, and a good medical rubber molding factory should have the ability to provide custom solutions. Custom molded rubber parts are often necessary for unique applications or for devices that have specialized design requirements.
- Custom Molding Capabilities: A reputable factory should be able to create rubber components that meet the exact specifications of your medical device. This may include custom shapes, sizes, and material properties that align with the functional requirements of the device.
- Material Selection: The factory should offer a variety of materials that can be customized to meet specific needs, whether it’s biocompatibility, flexibility, chemical resistance, or temperature tolerance.
- Tailored Solutions: Whether it’s for a specialized implant, custom surgical handle, or unique sealing component, a good medical rubber molding factory will be able to develop custom parts that meet the precise performance and regulatory requirements for the medical industry.
Capabilities for Prototyping and Design Validation
Prototyping and design validation are crucial steps in the development of medical devices. A medical rubber molding factory should have the capabilities to provide prototyping services, allowing manufacturers to test the functionality, fit, and performance of their rubber components before full-scale production.
- Prototyping Services: Rapid prototyping allows for quick iterations of designs and helps identify any issues early in the development process. This is especially important in plastic medical device manufacturing, where even small design flaws can have significant implications for safety and performance.
- Design Validation: A reliable medical rubber molding factory should offer design validation services to ensure that the molded rubber parts meet the required standards and function as intended in the final product. This includes evaluating factors such as material compatibility, dimensional accuracy, and long-term performance under real-world conditions.
Leading Medical Rubber Molding Manufacturers and Their Specialties
Several companies are recognized for their expertise in medical rubber molding and have earned a reputation for providing high-quality, compliant, and reliable products for the medical industry. Below are a few leading manufacturers and their specialties:
FUJIU Medical Injection Mold
- Specialties: At FUJIU Medical Injection Mold, we bring over 20 years of excellence as a third-generation, employee-owned factory. Every team member is a stakeholder, fueling our passion for innovation, quality, and collaboration. We specialize in OEM contract manufacturing for the medical device industry, producing high-precision plastic consumables for equipment and diagnostic kits. Our expertise extends to precision mold medical, where we utilize state-of-the-art techniques to create intricate, high-quality medical molds that meet the most stringent standards.
- Certifications: Achieved CMA certification for our ISO8-grade medical injection molding workshop and obtained ISO13485:2016 international medical quality management system certification.
- Strengths: From initial design to production, we partner with clients using advanced injection molding technologies. Equipped with Class 8 clean rooms and adhering to ISO 13485, FDA, and global standards, we ensure the highest quality control.
Precision Rubber Molding
- Specialties: Precision Rubber Molding focuses on medical-grade seals and gaskets, providing critical components for medical devices such as oxygen tanks, pumps, and infusion systems. Their ability to produce intricate, highly durable seals makes them a preferred choice for high-precision sealing applications.
- Certifications: ISO 13485, FDA-compliant, USP Class VI certified.
- Strengths: High-precision molded rubber parts, custom gaskets, and specialized sealing solutions.
Comprehensive Preparations for Customizing Medical Rubber Molding
When customizing medical rubber molding, users must conduct thorough preparations beyond simply selecting a qualified manufacturer. Proper planning ensures that the final product meets medical industry standards, functional requirements, and cost-efficiency goals. Medical rubber components, such as seals, gaskets, tubing, and surgical device grips, require precise material selection, detailed design specifications, regulatory compliance, and efficient production planning. Without adequate preparation, issues such as material incompatibility, design flaws, and production inefficiencies may arise, leading to delays or failures in medical applications. Below are the key areas users should focus on when preparing for medical rubber molding customization.
Defining Material and Performance Requirements
The choice of rubber material significantly impacts product durability, flexibility, and biocompatibility. Medical-grade rubber materials must withstand various environmental conditions, including repeated sterilization, exposure to bodily fluids, and mechanical stress. Users should work closely with manufacturers to define:
- Material Selection: Common medical rubber materials include:
- Liquid Silicone Rubber (LSR): Highly biocompatible, resistant to high temperatures, and ideal for implants, tubing, and seals.
- Nitrile Rubber (NBR): Excellent chemical resistance, commonly used for gloves, gaskets, and seals.
- EPDM (Ethylene Propylene Diene Monomer): Resistant to heat, steam, and UV, making it suitable for pharmaceutical tubing and gaskets.
- Fluorosilicone: Superior chemical resistance for critical medical sealing applications.
- Performance Requirements: Users must specify:
- Hardness and Flexibility: The rubber’s durometer rating should match the intended use (e.g., soft for catheter tips, firm for gaskets).
- Chemical and Temperature Resistance: The material must tolerate sterilization methods like autoclaving, gamma radiation, and ethylene oxide gas.
- Wear and Tear Resistance: Essential for long-term medical device performance.
Failing to define precise material needs may result in compatibility issues, affecting device safety and patient outcomes.
Creating a Detailed Design and Prototype
Before mass production, users must develop an accurate design and prototype to ensure proper fit, function, and manufacturability. The medical industry requires high-precision molding, and any design flaws could lead to defective or non-compliant products. Key preparation steps include:
- 3D CAD Design: Users should create detailed 3D models specifying:
- Exact dimensions, tolerances, and material thickness.
- Areas requiring reinforcement or flexibility based on function.
- Potential mold flow issues that could lead to defects like air bubbles or uneven curing.
- Prototype Development: Before mass production, prototype testing helps to:
- Identify design flaws or inefficiencies.
- Test the material’s performance under real-world medical conditions.
- Optimize the mold structure for better durability and cost-effectiveness.
Skipping this step may lead to increased costs due to rejected batches, excessive waste, and product failure in critical medical applications.
Ensuring Regulatory Compliance
Medical rubber components must meet stringent health and safety regulations to prevent contamination and ensure patient safety. Users should ensure that both the material and manufacturing process comply with:
- FDA (Food and Drug Administration) Standards: Rubber parts used in medical devices must be FDA-approved for biocompatibility and sterility.
- ISO 10993 Certification: Ensures that the material is safe for prolonged human contact (e.g., surgical tubing, implants).
- USP Class VI Certification: Required for rubber components used in pharmaceutical applications and direct-body contact devices.
- Cleanroom Manufacturing Standards (ISO Class 7 or 8): Ensures rubber components are produced in sterile, contamination-free environments.
Users should request material certifications, batch traceability reports, and compliance testing documentation from the manufacturer. Ignoring compliance checks could result in product recalls, legal liabilities, and patient safety risks.
Evaluating Production Feasibility and Cost
Beyond material selection and design, users must assess the manufacturing feasibility of their custom medical rubber components. Factors to consider include:
- Mold Tooling and Setup Costs:
- Medical rubber molding requires high-precision metal molds, which can be costly.
- The complexity of the design determines mold costs (multi-cavity molds increase production efficiency but require higher upfront investment).
- Production Volume Considerations:
- Injection Molding: Ideal for high-volume production of medical components like seals, gaskets, and tubing.
- Compression Molding: More cost-effective for low to medium-volume medical rubber parts.
- Transfer Molding: Suitable for complex medical components with embedded materials (e.g., multi-layer seals).
- Manufacturing Lead Time and Scalability:
- Users must confirm the production timeline and ensure the manufacturer can scale up production without compromising quality.
- Large-scale production should incorporate automated hands-free molding and cleanroom facilities to maintain precision and hygiene.
Without a clear understanding of costs and production capabilities, users risk exceeding their budget or encountering delays in critical medical supply chains.
Establishing a Strong Collaboration with the Manufacturer
Successful medical rubber molding projects require effective communication between the user and the manufacturer. Users should:
- Share Detailed Design and Functionality Requirements: Provide technical specifications to minimize errors in production.
- Clarify Quality Control Measures: Ensure the manufacturer has inspection and testing protocols in place for defect-free products.
- Request Trial Batches: Conduct initial test runs to evaluate mold performance, material quality, and consistency.
Establishing a long-term partnership with a trusted medical rubber molding manufacturer improves reliability, reduces risks, and ensures high-quality production.
Customizing medical rubber molding requires extensive preparation in material selection, design development, regulatory compliance, cost evaluation, and manufacturer collaboration. Failing to address these factors could lead to product failures, regulatory issues, or manufacturing inefficiencies. By carefully planning each aspect, users can ensure their custom medical rubber components meet the highest standards of safety, functionality, and durability, essential for success in the medical industry.
Custom Molded Rubber Parts for Medical Devices
Custom molded rubber parts play a crucial role in the design and functionality of medical devices. The medical rubber molding process allows manufacturers to create specialized components that meet the exacting standards of the healthcare industry. In this section, we will explore the benefits of custom molding in the medical sector, how custom molded rubber parts are made to fit specific requirements, and provide examples of common custom parts used in medical devices.
The Benefits of Custom Molding in the Medical Sector
Custom medical rubber molding offers several significant advantages when producing parts for medical devices. These benefits directly contribute to improved device performance, patient safety, and the overall functionality of medical products.
- Precision and Fit: Custom molding ensures that rubber components are produced with the highest level of precision, which is essential for devices that must function within strict tolerance parameters. Whether it’s a catheter, surgical tool, or diagnostic equipment, every component must fit seamlessly into the design to avoid failures and ensure optimal performance.
- Material Selection: Custom medical rubber molding allows manufacturers to select the best materials for specific applications. For example, some medical devices require biocompatible, durable, and flexible materials like medical-grade silicone, while others may require elastomers that resist chemicals or extreme temperatures. Custom molding ensures that the right material is used for each part, enhancing the safety and longevity of the device.
- Cost Efficiency: Although the initial costs for custom molds may be higher, custom molding in large production runs can actually help reduce overall costs. By minimizing waste and ensuring components are made to exact specifications, manufacturers can achieve cost savings in both material usage and assembly time.
- Regulatory Compliance: Custom medical rubber molding manufacturers understand the complex regulatory requirements that medical devices must meet. They ensure that each part is compliant with industry standards such as FDA regulations and USP Class VI certifications. This ensures that the molded parts are safe for use in medical applications and meet all necessary compliance benchmarks.
How Custom Molded Rubber Parts are Made to Fit Specific Medical Device Requirements
The process of creating custom molded rubber parts for medical devices involves several key steps to ensure that the parts meet the specific needs of the device. Below is an overview of how custom medical rubber molding is typically carried out:
- Design and Prototyping:
The first step is to design the custom rubber part based on the requirements of the medical device. Engineers and designers work closely with the medical device manufacturer to understand the functional needs of the part, its material requirements, and how it will interact with other components of the device. A prototype is often created to test the design before mass production begins. This allows for adjustments in the design if necessary and ensures that the part fits perfectly in the final device. - Material Selection:
After the design is finalized, the right material is selected for the rubber part. For medical devices, the material needs to be biocompatible, durable, and able to withstand sterilization processes. Common materials used in medical rubber molding include medical-grade silicone, nitrile rubber, EPDM. The choice of material is based on factors like flexibility, resistance to chemicals, heat tolerance, and the need for high precision. - Molding Process:
The molding process itself can vary depending on the type of part being produced. In medical rubber molding, common methods include compression molding, injection molding, and transfer molding. Each method involves the shaping of rubber under heat and pressure to form the desired part. In compression molding, the rubber is placed into a mold cavity and heated until it cures into the final shape. Injection molding involves injecting liquid rubber into a mold under pressure to form precise parts. The method selected depends on the complexity and size of the part, as well as the material used. - Post-Molding Processes:
After the part is molded, it often undergoes additional processes like trimming, quality checks, and cleaning. For medical devices, the parts may also need to be sterilized or undergo testing for biocompatibility and durability before they can be used in a final product. These additional steps ensure that each molded rubber part meets the highest standards for safety and performance.
Examples of Custom Parts: O-rings, Seals, Tubing, and Connectors
Custom molded rubber parts are used in a wide variety of medical devices, each serving a unique function. Some of the most common examples include:
O-rings
O-rings are circular rubber seals that are commonly used in medical devices to prevent leaks and ensure airtight or watertight seals. Custom molded O-rings are used in a variety of medical applications, such as in syringes, infusion pumps, and surgical instruments. They can be made from materials like silicone, nitrile, or EPDM, depending on the specific requirements of the device.
- Applications: Syringes, blood pressure cuffs, oxygen regulators, and other fluid-carrying devices.
Seals
Medical devices often require rubber seals to prevent the leakage of fluids or gases. These seals are critical for maintaining sterility, preventing contamination, and ensuring the proper functioning of the device. Custom molded rubber seals can be made in various shapes and sizes to meet the specific needs of medical devices.
- Applications: Surgical equipment, diagnostic tools, medical pumps, and implantable devices.
Tubing
Medical-grade rubber tubing is used in a wide range of devices, including catheters, infusion pumps, and respiratory equipment. Custom molded tubing can be designed to have the necessary flexibility, chemical resistance, and durability to perform safely and effectively in medical applications.
- Applications: IV lines, feeding tubes, drainage tubes, and oxygen delivery systems.
Connectors
Custom molded rubber connectors are used in medical devices to join different parts together, ensuring a secure and reliable connection. These connectors can be designed to meet specific size, shape, and performance requirements, and are often used in devices such as catheters, pumps, and diagnostic instruments.
- Applications: Catheter connectors, infusion set connectors, respiratory device connectors, and medical imaging equipment.
Custom molded rubber parts are essential in the medical sector, providing critical components that ensure the proper functionality and safety of medical devices. The medical rubber molding process allows for the creation of highly specialized, biocompatible parts that meet the stringent demands of the healthcare industry. Whether it’s O-rings, seals, tubing, or connectors, custom molded rubber parts play a vital role in enhancing the performance and reliability of medical devices, ultimately contributing to better patient outcomes. By choosing the right materials and manufacturing processes, plastic medical device manufacturers can ensure that their products meet both regulatory standards and the specific needs of their applications.
Pricing Considerations for Medical Rubber Molding
When it comes to medical rubber molding, pricing is influenced by several key factors that determine the overall cost of manufacturing. Understanding these factors can help medical device manufacturers make informed decisions about their molding processes, material choices, and production strategies. In this section, we will discuss the main elements that affect pricing and provide insights into how to obtain accurate quotes from medical rubber molding companies.
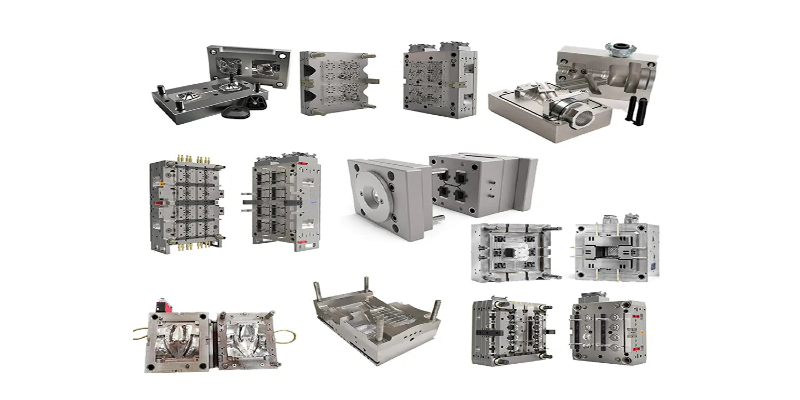
Key Factors Influencing Medical Rubber Molding Prices
Several factors can significantly impact the cost of medical rubber molding. These factors include the type of material used, the molding process chosen, and the production volume required. Each element plays a role in the overall cost structure, and understanding them can help manufacturers optimize their production costs.
Material Choice
The material selected for molding is one of the most important cost factors in the medical rubber molding process. Different types of rubber materials come with varying costs based on their properties, performance, and biocompatibility.
- Silicone Rubber: Medical-grade silicone is commonly used in medical rubber molding due to its excellent biocompatibility, flexibility, and durability. However, silicone is generally more expensive than other elastomers due to its specialized nature, particularly when it is required to meet stringent standards such as USP Class VI or FDA compliance.
- Other Elastomers: Materials like nitrile, neoprene are also used in medical applications, but they may be more cost-effective compared to silicone, depending on the intended use. These elastomers offer a range of properties, including chemical resistance, flexibility, and temperature tolerance, and may be chosen for specific applications based on their performance characteristics.
- Material Sourcing and Certification: Another consideration is the sourcing and certification of the materials. For instance, materials used in medical device production must often meet regulatory standards, such as FDA approval or USP Class VI certification, which can add to the material cost.
Molding Process
The molding process used for medical rubber molding significantly influences the price of the final product. Different molding techniques require different levels of expertise, equipment, and setup costs. Common molding methods in medical applications include:
- Injection Molding: This process is highly precise and efficient for producing large volumes of complex parts. However, injection molding typically requires expensive equipment and tooling, which can increase the upfront costs. The cost per part decreases with higher production volumes, making it more cost-effective for mass production.
- Compression Molding: In this process, rubber is placed in a heated mold and compressed to form the desired shape. Compression molding is more affordable than injection molding for smaller runs, making it an attractive option for low-volume production. However, it may not be as suitable for producing intricate or complex parts.
- Transfer Molding: This process is similar to compression molding but allows for more detailed designs and smaller tolerances. It is often used for applications where the part requires greater precision than what compression molding can offer, but the production volume is not as high as what injection molding would demand. The costs can be higher compared to compression molding but are often lower than injection molding.
- Overmolding and Insert Molding: These specialized processes combine different materials or parts during the molding process, which can add complexity and cost. While they offer significant advantages in terms of enhanced part performance, the tooling and setup costs are typically higher, making these processes more expensive than standard injection molding.
Production Volume
Production volume plays a crucial role in determining the overall cost of medical rubber molding. The scale of production often dictates whether a particular molding process is the most economical choice:
- High-Volume Runs: For large-scale production, medical injection molding processes are typically the most cost-effective. The initial tooling and setup costs can be high, but the cost per part decreases significantly as the volume increases. High-volume runs are ideal for producing large quantities of standardized parts, such as seals, O-rings, and connectors, for medical devices.
- Prototype Runs and Low-Volume Production: For prototypes or low-volume production, custom molding processes like compression or transfer molding may be more suitable. These methods generally have lower setup costs, but the cost per part may be higher compared to mass production methods. For manufacturers testing new designs or entering a new product line, prototype runs allow for quick iteration without committing to high-volume tooling expenses.
- Customization Needs: If the medical device requires highly specialized, custom-molded parts, the overall cost can increase. Customization often involves higher tooling costs, material expenses, and more extensive design work. This factor must be carefully considered when determining pricing for complex or unique medical rubber components.
How to Get an Accurate Quote from Medical Rubber Molding Companies
To obtain an accurate quote for medical rubber molding, manufacturers should provide detailed information to the molding factory. Here are some key aspects to consider when requesting a quote:
- Detailed Specifications: Provide the factory with detailed drawings or CAD files of the parts, including dimensions, material requirements, and specific performance characteristics (e.g., biocompatibility, temperature tolerance). The more information you can give, the more accurate the quote will be.
- Production Volume: Be clear about the quantity you need, as this will directly impact the pricing. High-volume runs may receive lower unit costs, while small batch or prototype runs will often have a higher price per part.
- Molding Process Preference: Specify which molding process you prefer or inquire about the most cost-effective option for your needs. Each molding method has its advantages, and a skilled molding factory can suggest the best process for your application.
- Material Selection: Clearly outline your material requirements, whether you’re looking for medical-grade silicone, elastomers, or other rubber materials. Ensure that the materials comply with relevant industry standards, such as FDA approval or USP Class VI certification.
- Tooling and Setup Costs: Ask for an estimate of the tooling and setup costs. These are typically a significant part of the initial investment for custom medical rubber molding. Larger production runs often allow for these costs to be spread out over more parts, reducing the cost per unit.
- Lead Times: Inquire about the lead times for production, including the time needed for prototyping, tooling, and mass production. Custom medical rubber molding projects can take several weeks or months depending on complexity and volume.
Understanding the factors that influence medical rubber molding prices is essential for medical device manufacturers who need to control costs while ensuring the quality and compliance of their products. Material choice, molding process, and production volume all play a significant role in determining the final cost of rubber components. By working closely with medical rubber molding companies and providing accurate information, manufacturers can obtain precise quotes and make cost-effective decisions that align with their production and design requirements.
FAQs about Medical Rubber Molding
Medical rubber refers to rubber materials specifically designed for use in medical devices and healthcare applications. Unlike regular rubber, medical rubber must meet strict regulatory standards, ensuring that it is safe, biocompatible, and durable enough for medical environments. These materials are often used in devices that come into contact with the human body, such as surgical tools, implants, catheters, seals, and gaskets.
Medical rubber can be made from various elastomers, such as silicone, nitrile, neoprene, and EPDM (ethylene propylene diene monomer). These materials are selected based on their unique properties like flexibility, chemical resistance, temperature stability, and biocompatibility. For example, silicone rubber is often chosen for its flexibility, low toxicity, and resistance to high temperatures, making it ideal for applications like medical implants, seals, and catheters.
To be classified as medical-grade rubber, these materials must pass extensive testing to ensure they do not cause adverse reactions when in contact with biological tissues. Additionally, they must meet regulatory standards set by authorities like the FDA and ISO to ensure patient safety and device reliability.
Medical molding is the process of creating rubber or plastic components used in medical devices through various molding techniques. This process allows manufacturers to produce parts that are both complex in design and precisely manufactured to meet stringent regulatory standards. Medical molding ensures that components such as seals, tubing, catheters, and surgical tools are made with high accuracy and durability, crucial for patient safety and the reliability of medical devices.
There are several types of molding techniques used in the medical industry, including injection molding, compression molding, transfer molding, and overmolding. Each of these methods has its advantages depending on the type of medical device, material requirements, and production volume. For example, injection molding is used for high-volume production and is known for producing precise parts, while compression molding is more cost-effective for low-volume runs.
Medical molding also focuses heavily on ensuring that materials used in the production process meet required biocompatibility standards and are free from contaminants. Because medical devices often come into direct contact with the human body, manufacturers must adhere to strict standards, such as FDA approval or USP Class VI certifications, to ensure the safety and efficacy of molded rubber components.
Medical grade silicone rubber is a specialized form of silicone rubber that is designed to meet the rigorous safety and performance standards required for medical applications. Silicone rubber, a synthetic elastomer made from silicon, oxygen, and other elements, is known for its excellent biocompatibility, flexibility, and durability. It can be used in a wide variety of medical devices, such as catheters, seals, gaskets, implants, and surgical tools.
What sets medical-grade silicone apart from other types of silicone is its high level of purity and its ability to withstand stringent testing for toxicity, irritancy, and long-term body compatibility. Medical-grade silicone must comply with FDA regulations, meet USP Class VI standards, and pass biocompatibility testing to ensure it will not cause adverse reactions when in contact with tissues or bodily fluids.
One of the main advantages of medical-grade silicone rubber is its resistance to extreme temperatures, which makes it ideal for use in sterilization processes such as autoclaving. It is also highly resistant to aging, UV light, and chemical exposure, making it durable over long periods. As a result, medical-grade silicone rubber is commonly used in applications such as implants, feeding tubes, and drug delivery systems.
Rubber molding is the process of shaping rubber materials into specific forms to create products used in a variety of industries, including automotive, consumer goods, and particularly healthcare. There are several different types of rubber molding processes, each suited to specific applications, material types, and production requirements. The main types of rubber molding include compression molding, injection molding, transfer molding, and overmolding.
Compression Molding: In this process, rubber is placed into a heated mold and compressed to take the shape of the mold cavity. It is ideal for producing large, simple parts or low-volume production runs.
Injection Molding: This technique involves injecting molten rubber into a mold under high pressure, ensuring precise shapes and high-quality finishes. It is commonly used for producing complex, small-to-medium-sized parts in high volumes.
Transfer Molding: Similar to compression molding, transfer molding involves pre-heating rubber and transferring it into a mold under pressure, but it allows for greater control over the molding process and more intricate designs.
Overmolding: Involves molding a layer of rubber over a substrate, such as metal or plastic, to create a part with enhanced functionality (e.g., a handle with better grip or a part that is more resistant to wear).
Rubber molding ensures that parts are produced with the necessary precision, durability, and quality for medical devices. These processes allow manufacturers to create critical medical components such as seals, gaskets, and O-rings, all of which must meet stringent safety and performance standards.
Silicone is a synthetic polymer known for its flexibility, heat resistance, and biocompatibility. However, not all silicone is suitable for medical applications. Medical-grade silicone is a specialized form that undergoes rigorous testing to ensure it meets strict biocompatibility and safety standards. It is designed to be non-toxic, hypoallergenic, and resistant to bacterial growth, making it safe for prolonged human contact.
Medical-grade silicone is used in devices such as catheters, implants, and prosthetics, while general silicone is commonly found in household items, automotive parts, and industrial applications. Unlike regular silicone, medical-grade variants comply with FDA and ISO 10993 standards, ensuring they are safe for medical use, including direct implantation into the body. The purification process for medical-grade silicone removes impurities and ensures it does not release harmful chemicals, making it ideal for healthcare settings.
Hospitals rely on a variety of rubber-based medical components to ensure patient care and safety. Four commonly used rubber goods in medical settings include:
Medical Seals and Gaskets – Used in medical devices and diagnostic equipment to prevent fluid or air leakage.
Catheters and Tubing – Made from medical-grade rubber or silicone for fluid drainage and medication delivery.
Surgical and Examination Gloves – Essential for infection control, these gloves provide a sterile barrier for healthcare professionals.
Respiratory Masks and Ventilator Components – Soft rubber parts help create airtight seals in respiratory devices used for patients with breathing difficulties.
These rubber goods are designed to be biocompatible, durable, and resistant to sterilization methods like autoclaving and chemical cleaning. The use of high-quality medical-grade rubber ensures patient safety and device reliability.
Industrial silicone is designed for applications that prioritize durability, flexibility, and resistance to extreme temperatures, making it suitable for construction, automotive, and electrical insulation. In contrast, medical silicone is formulated specifically for human use, ensuring biocompatibility and strict adherence to medical safety standards such as ISO 10993 and FDA regulations.
Medical silicone undergoes extensive testing for cytotoxicity, sensitization, and irritation to ensure it does not cause adverse reactions. It is free from harmful chemicals and additives that may be present in industrial-grade silicone. Additionally, medical silicone is produced in cleanroom environments to prevent contamination.
Industrial silicone, while durable, may contain fillers and processing agents that could be harmful if used in medical applications. Medical-grade silicone, on the other hand, is ultra-pure, making it safe for use in medical implants, prosthetics, and drug delivery systems.
Yes, 100% medical-grade silicone is considered safe for medical applications due to its biocompatibility, non-toxicity, and resistance to bacterial growth. It is extensively tested for safety and meets regulatory standards such as FDA approval and ISO 10993 compliance. Medical-grade silicone does not contain latex, phthalates, or BPA, making it hypoallergenic and ideal for sensitive applications.
This type of silicone is used in a variety of medical products, including implants, feeding tubes, and wound dressings. It is non-reactive, meaning it does not degrade or release harmful substances into the body. Additionally, medical-grade silicone is highly resistant to extreme temperatures, sterilization processes, and prolonged exposure to bodily fluids.
Because of its proven safety record, medical-grade silicone is widely used in both short-term and long-term medical applications, including surgical implants and prosthetic devices.
FDA-approved rubber refers to rubber materials that comply with the U.S. Food and Drug Administration (FDA) standards for medical and food-related applications. These rubbers must be non-toxic, non-reactive, and free from harmful chemicals such as BPA and phthalates.
FDA-approved rubber is often used in medical devices, pharmaceuticals, and food-processing equipment. Common types of FDA-compliant rubber include silicone, EPDM (ethylene propylene diene monomer), and natural rubber latex. These materials must pass stringent testing for chemical resistance, biocompatibility, and durability.
Medical rubber components like gaskets, tubing, and seals used in hospitals must be FDA-approved to ensure patient safety. These rubbers can withstand sterilization methods like autoclaving, gamma radiation, and chemical disinfectants. FDA-approved rubber ensures that medical devices remain safe and effective during use in hospitals, laboratories, and food-handling environments.
Medical-grade silicone offers several advantages that make it an ideal material for healthcare applications:
Biocompatibility – It is non-toxic, hypoallergenic, and does not cause adverse reactions when in contact with the human body.
Durability – Resistant to extreme temperatures, UV exposure, and chemicals, ensuring long-term functionality.
Sterilization Compatibility – Can be sterilized using autoclaving, gamma radiation, and chemical disinfectants without degrading.
Flexibility and Softness – Provides a comfortable and secure fit for medical devices such as prosthetics, catheters, and masks.
Non-Porous Surface – Inhibits bacterial growth, reducing the risk of infections in medical settings.
Regulatory Compliance – Meets strict FDA and ISO 10993 standards for safety and efficacy.
Due to these benefits, medical-grade silicone is widely used in implants, wound care products, and drug delivery systems.
The cost of medical-grade silicone varies depending on factors such as purity, processing methods, and specific applications. On average, medical-grade silicone costs between $50 and $500 per kilogram, depending on whether it is in liquid, gel, or solid form.
High-purity medical silicone used for implants and life-saving devices tends to be more expensive due to the stringent manufacturing processes and regulatory compliance involved. The price can also vary based on the supplier, region, and order quantity.
For manufacturers, bulk purchasing can reduce costs, but additional expenses like cleanroom production and FDA certification add to the final price. Custom-molded silicone components may also have higher costs due to specialized tooling and precision engineering.
Medical-grade plastic is commonly referred to as biocompatible polymer and includes materials such as:
Polycarbonate (PC) – Used in surgical instruments and medical housings.
Polyetheretherketone (PEEK) – Ideal for implants due to its strength and chemical resistance.
Polyvinyl Chloride (PVC) – Found in medical tubing and blood bags.
Polypropylene (PP) – Used for syringes, vials, and sterilizable containers.
Medical-Grade Silicone – Used in implants, prosthetics, and catheters.
These plastics meet strict medical regulations for biocompatibility and are designed for safe interaction with the human body.
The three primary types of molding used in medical rubber and plastic manufacturing are:
Injection Molding – Involves injecting liquid rubber or plastic into a mold cavity under high pressure. It is widely used for mass production of medical components like syringe plungers and tubing connectors.
Compression Molding – Uses heat and pressure to shape rubber or silicone into a mold. It is ideal for producing durable parts like gaskets and seals.
Transfer Molding – A hybrid of injection and compression molding where rubber is preheated and then forced into the mold, improving precision and reducing waste.
Each method is chosen based on the required precision, volume, and complexity of the medical component.
Rubber injection molding is a manufacturing process where liquid or semi-solid rubber is heated and injected into a mold under high pressure. This process ensures high precision, minimal waste, and faster production times, making it ideal for mass-producing medical rubber parts.
Medical-grade rubber injection molding is used to manufacture catheters, seals, gaskets, and O-rings. The process ensures consistency and durability while maintaining biocompatibility and FDA compliance. Rubber injection molding allows for complex designs and customization in medical device manufacturing.
Yes, natural rubber can be injection molded, but it requires specialized processing due to its unique properties. Unlike synthetic rubbers, natural rubber has high elasticity and resilience, making it more challenging to mold consistently. It needs precise temperature and pressure control to achieve optimal results.
In medical rubber molding, natural rubber is sometimes used for components like surgical gloves, tubing, and seals. However, it is less common than synthetic rubbers like silicone and nitrile, which offer better resistance to chemicals and sterilization processes.
The injection molding process for natural rubber involves heating it until it becomes flowable and then injecting it into a mold cavity under high pressure. After molding, the rubber undergoes vulcanization, a curing process that improves its strength and durability. While possible, manufacturers often prefer synthetic alternatives for more consistent and biocompatible medical applications.
The main difference between rubber and plastic injection molding lies in the material properties and processing methods. Plastic injection molding involves melting thermoplastic or thermosetting resins and injecting them into a mold, where they cool and solidify into a rigid shape. Rubber injection molding, on the other hand, deals with elastomers that remain flexible after molding and often require vulcanization or curing.
In medical applications, rubber molding is used for flexible, biocompatible parts like seals, gaskets, and tubing, while plastic molding is used for harder components like syringes, casings, and surgical tools. Rubber molding also involves a more complex curing process to ensure elasticity, whereas plastics simply harden upon cooling.
Overall, rubber molding produces softer, stretchable parts, while plastic molding creates rigid structures, both playing essential roles in medical device manufacturing.
Yes, silicone rubber can be injection molded using Liquid Silicone Rubber (LSR) molding. This process is ideal for medical rubber molding because silicone offers excellent biocompatibility, flexibility, and resistance to extreme temperatures.
Medical-grade silicone rubber injection molding is widely used for catheters, seals, implants, and respiratory masks. The process involves mixing two-part liquid silicone components, injecting them into a heated mold, and curing them rapidly. The result is high-precision medical components that are durable and safe for long-term contact with the human body.
Since medical-grade silicone is resistant to sterilization, does not degrade, and remains flexible, it is a preferred material in medical device manufacturing.
Yes, nitrile rubber (NBR) can be injection molded, making it a popular material for medical gloves, tubing, seals, and gaskets. Nitrile is known for its oil, chemical, and puncture resistance, making it ideal for medical and laboratory environments.
Injection molding nitrile rubber involves heating and injecting the rubber compound into a mold, followed by curing to enhance its elasticity and strength. Medical nitrile is commonly used for components that require flexibility, chemical resistance, and durability, such as O-rings in medical devices.
Compared to natural rubber, nitrile rubber is hypoallergenic, making it a safer alternative for people with latex allergies. Additionally, its resistance to sterilization processes like autoclaving and gamma radiation makes it ideal for single-use and reusable medical applications.
Elastomers used in medical injection molding include:
Silicone Rubber (LSR) – Biocompatible, flexible, and used for implants, seals, and tubing.
Nitrile Rubber (NBR) – Chemical-resistant, commonly used in gloves, gaskets, and seals.
Ethylene Propylene Diene Monomer (EPDM) – Heat-resistant, used in tubing and medical seals.
Fluorosilicone (FVMQ) – Resistant to harsh chemicals, used for high-performance seals.
Thermoplastic Elastomers (TPE/TPV) – Blend of rubber and plastic for flexible medical components.
These elastomers offer superior flexibility, sterilization resistance, and durability, making them essential for medical rubber molding applications.
In medical rubber molding, the most common mold types used are:
Single-Cavity Molds – Used for low-volume, precision medical parts like custom implants.
Multi-Cavity Molds – Ideal for mass production of medical tubing, gaskets, and seals.
Hot Runner Molds – Used to reduce material waste, common in high-precision medical molding.
Cold Runner Molds – More cost-effective for smaller production runs.
Medical rubber components require precision-engineered molds that ensure biocompatibility and dimensional accuracy for safety-critical applications.
The most common silicone used in medical rubber injection molding is Liquid Silicone Rubber (LSR). It is biocompatible, hypoallergenic, and resistant to extreme conditions, making it ideal for medical applications.
LSR is used in:
Medical tubing and catheters
Seals and gaskets for surgical devices
Respiratory masks and prosthetics
Implants and drug delivery systems
Medical-grade LSR is FDA-approved and ISO 10993 compliant, ensuring its safety for direct body contact and long-term implantation.
Molding is the manufacturing process of shaping materials into specific forms using molds. In the medical industry, this process is called medical rubber molding or medical injection molding when elastomers like silicone and nitrile are used.
Molding processes include:
Injection Molding – Fast, precise, and used for mass production.
Compression Molding – Used for durable medical rubber components.
Transfer Molding – A hybrid method for complex parts.
These methods help create high-quality, sterilizable, and biocompatible medical components.
A silicone rubber mold is a mold made from silicone elastomers used to shape medical-grade rubber parts. It is flexible, heat-resistant, and capable of producing high-precision medical components.
In medical rubber molding, silicone rubber molds are used to manufacture:
Medical implants
Custom prosthetics
Seals and gaskets for medical devices
These molds can withstand high temperatures, chemical exposure, and sterilization, making them ideal for medical device manufacturing.
A rubber baseboard is often referred to as rubber wall base or cove base molding. In medical settings, it is used for hygienic and protective purposes, ensuring easy cleaning and durability in hospitals, clinics, and laboratories.
Unlike traditional wood baseboards, rubber baseboards resist moisture, bacteria, and chemicals, making them ideal for infection-controlled environments.
Rubber compression molding is a process where preheated rubber is placed in a mold cavity and compressed under heat and pressure. This method is widely used for medical rubber molding to create durable, high-strength components like:
Seals and gaskets for medical equipment
Custom prosthetics and orthopedic supports
Medical-grade tubing
Compression molding is ideal for low to medium-volume production and is often used when precise material properties are required in biocompatible medical applications.
The most common material used in medical rubber injection molding is liquid silicone rubber (LSR) due to its exceptional biocompatibility, flexibility, and ability to withstand harsh sterilization processes. LSR is a two-part, platinum-cured elastomer that offers low toxicity, chemical resistance, and excellent durability, making it ideal for use in medical devices, seals, gaskets, syringe stoppers, catheters, and respiratory masks.
One of the biggest advantages of LSR is its ability to maintain its properties across a wide temperature range (-50°C to 250°C), ensuring it remains stable under various sterilization methods, including autoclaving, gamma irradiation, ethylene oxide (EtO) gas, and e-beam sterilization. Unlike organic rubbers, LSR does not degrade or leach harmful substances, making it safe for direct contact with human tissues and fluids.
In addition to LSR, other materials like thermoplastic elastomers (TPEs), fluoroelastomers (FKM), and EPDM (ethylene propylene diene monomer) are sometimes used, depending on the specific application. However, LSR dominates the medical rubber molding industry due to its superior hygienic properties, non-reactivity, and compliance with strict medical standards such as USP Class VI, ISO 10993, and FDA regulations.
The liquid injection molding (LIM) process used for LSR allows for high-precision, automated, and contamination-free production, ensuring that medical components meet the highest quality standards.
Injection molding of medical rubber involves several steps to ensure precision and sterility:
Material Selection – Medical-grade rubbers such as LSR, TPEs, or EPDM are chosen based on biocompatibility requirements.
Preparation – The rubber is preheated and mixed with curing agents.
Injection – The heated rubber is injected into a mold cavity under high pressure.
Curing – The rubber is vulcanized using heat to ensure shape retention.
Demolding & Finishing – The molded component is cooled, ejected, and inspected for defects.
Sterilization & Packaging – Parts are sterilized using autoclaving, gamma radiation, or ethylene oxide gas.
This process ensures consistent, high-quality medical components like syringe seals, gaskets, and stoppers.
Yes, EPDM (ethylene propylene diene monomer) rubber can be injection molded for medical applications, though it is less common than liquid silicone rubber (LSR). EPDM is valued for its chemical resistance, durability, and flexibility, making it suitable for medical seals, gaskets, and tubing. It withstands sterilization methods like autoclaving and gamma radiation, which is essential for medical devices. However, EPDM requires precise molding conditions due to its high viscosity. Advanced curing processes, such as peroxide curing, improve its performance in medical applications. While EPDM is a good choice for applications requiring weather and chemical resistance, LSR remains the preferred material due to its superior biocompatibility, softness, and ease of processing in medical molding.
Syringe components, such as plungers and seals, are typically made from butyl rubber, chlorobutyl rubber, bromobutyl rubber, and silicone rubber. Butyl rubber is highly impermeable to gases and chemicals, making it ideal for maintaining sterile drug storage. Silicone rubber is another common choice due to its biocompatibility, flexibility, and ability to withstand repeated use without degradation. Some syringe components may also use thermoplastic elastomers (TPEs) as an alternative for improved recyclability. Medical-grade rubbers for syringes must meet USP Class VI and ISO 10993 biocompatibility standards, ensuring that they do not interact with or contaminate pharmaceutical formulations.
Medical rubber injection molding commonly utilizes liquid silicone rubber (LSR), thermoplastic elastomers (TPEs), fluoroelastomers (FKM), and ethylene propylene diene monomer (EPDM). Among these, LSR is the most widely used due to its excellent biocompatibility, flexibility, and resistance to high temperatures and sterilization methods such as autoclaving and gamma radiation. TPEs are used for their ability to mimic rubber-like properties while being recyclable. EPDM is valued for its durability and resistance to chemicals, making it suitable for seals and gaskets. Medical-grade rubbers must be non-toxic, hypoallergenic, and free of leachables to ensure safety in healthcare applications. These materials undergo rigorous testing to meet FDA and ISO 13485 standards, ensuring their suitability for contact with human tissues, fluids, and pharmaceutical substances.
In the pharmaceutical industry, molding refers to the process of shaping rubber and elastomeric components used in drug delivery systems and medical devices. Key molded products include vial stoppers, syringe plungers, IV connectors, and seals for pharmaceutical packaging. These components must meet stringent regulatory standards such as USP Class VI and ISO 10993 for biocompatibility and sterility. Medical rubber molding in pharmaceuticals primarily uses liquid silicone rubber (LSR) and thermoplastic elastomers (TPEs) due to their high purity, chemical resistance, and ability to withstand sterilization. Precision molding ensures that pharmaceutical closures maintain airtight seals, preventing contamination and ensuring drug efficacy. The use of cleanroom molding environments minimizes the risk of particulate contamination. Advances in injection molding technology, including micro-molding for tiny pharmaceutical components, have further improved quality and functionality in drug delivery systems.
Molding and casting both shape materials, but they differ significantly in process and application. Molding involves injecting or pressing rubber into a mold cavity, where it takes the desired shape under heat and pressure. This technique is commonly used for medical rubber parts like syringe seals, catheters, and stoppers, ensuring precision and biocompatibility. Casting, on the other hand, typically involves pouring a liquid material (like silicone or polyurethane) into a mold, where it solidifies at room temperature without pressure. Casting is less common in medical rubber applications because it lacks the precision and repeatability required for high-volume manufacturing. Injection molding is preferred for medical rubber components due to its efficiency, consistency, and ability to meet strict regulatory standards. While casting is sometimes used for prototyping or custom medical devices, molding is the dominant technique for producing high-quality, sterile, and durable rubber medical components.
A mold is the physical tool or cavity used to shape the rubber material, while molding refers to the actual process of forming rubber components using a mold. In medical rubber manufacturing, molds are precision-engineered to create components with exact specifications, ensuring consistency in critical healthcare products like IV seals, syringe plungers, and medical-grade tubing. Molding involves multiple techniques, such as injection, compression, and transfer molding, depending on the material and product requirements. The mold itself is typically made from high-grade steel or aluminum and must withstand extreme temperatures and pressures without deforming. In contrast, molding is the controlled process where medical-grade rubbers such as silicone or EPDM are shaped into final parts under sterile conditions. The accuracy of the mold directly impacts the quality of the molded product, making precision engineering and maintenance essential for medical applications that require tight tolerances and biocompatibility.
Molding is a general term that refers to shaping materials into desired forms using a mold, while injection molding is a specific process where rubber or plastic is heated, injected into a mold cavity, and cooled to form a precise shape. In medical rubber applications, injection molding is preferred because it provides high accuracy, repeatability, and efficiency. This is essential for producing components such as syringe stoppers, seals, catheters, and gaskets that require tight tolerances and biocompatibility. Other molding techniques like compression molding and transfer molding are sometimes used but are less efficient for mass production. Injection molding ensures minimal waste and can be automated for high-volume production, making it cost-effective. Medical rubber injection molding often utilizes materials like liquid silicone rubber (LSR) and thermoplastic elastomers (TPE), which are safe for healthcare applications. The process also allows for customization and scalability while maintaining strict quality control standards.
Medical rubber molding presents several risks, particularly contamination, defects, and material degradation. Since medical applications demand high precision and biocompatibility, improper molding conditions can introduce defects such as flash, voids, or dimensional inconsistencies, potentially compromising the integrity of medical devices like syringes, seals, and gaskets. Additionally, microbial contamination during production can pose health hazards. Rubber formulations may also degrade under excessive heat, pressure, or exposure to certain sterilization methods, impacting performance and safety. Poor quality control during molding can result in inconsistencies that lead to device failure, affecting patient safety. To mitigate these risks, manufacturers implement stringent cleanroom environments, rigorous material testing, and precise process control. Advanced techniques such as liquid injection molding (LIM) help minimize defects and ensure consistency. The use of medical-grade rubbers like silicone and EPDM, along with compliance with FDA and ISO 13485 standards, is crucial for ensuring the reliability of molded medical components.
Contact our professional team now for a same-day quote and risk-free project evaluation. Benefit from ISO 8 cleanrooms, advanced machines, and 12-hour fast response in medical injection molding.